advertisement
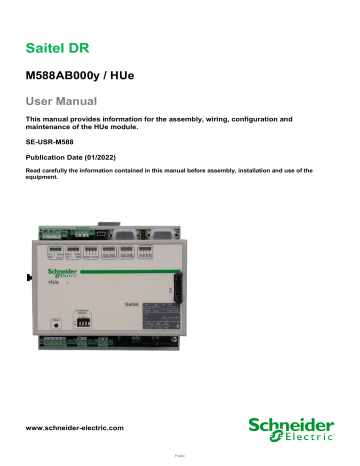
Saitel DR
M588AB000y / HUe
User Manual
This manual provides information for the assembly, wiring, configuration and maintenance of the HUe module.
SE-USR-M588
Publication Date (01/2022)
Read carefully the information contained in this manual before assembly, installation and use of the equipment. www.schneider-electric.com
Public
10/01/2022
Change Control
User Manual – HUe
Rev
01
02
03
04
05
06
Date
14-01-2019 Initial edition
Description
08-08-2019 • The supervision point TEMP is not available for HUe.
• Information about safety is included according the standard 60950-1.
02-03-2020 • Included information about Bluetooth connection.
• Included information about PTP, PRP and HSR.
• New certification according to the RED European Directive.
23-06-2020 • Included some safety boxes.
• Correct the ‘ Serial communication ports’ figure.
• Structure updated.
• Add wiring recommendations.
25-09-2020 • Included RSTP and BOND1 protocols information.
• Updated Easergy Builder version.
10-01-2022 • Removed information about Bluetooth port.
• Updated RoHS 3 directive
• Included note for HUe in a RS-485 bus.
• Removed sensitive information and new rules for inclusive language have been applied.
• Included reference to "Client SPA-Bus".
General Information
The Saitel platform and all its components have been developed in accordance to the requirements for a quality management system, complying with the ISO 9001:2015 Norm.
SE-USR-M588
06 / 10-01-2022
HUe – User Manual_EN_06.pdf
Permanent throughout its validation period + 3 years after its cancellation.
Document nº:
Revision/Date:
File:
Retention period:
Reference Documents
User Manual
Easergy Builder User Manual webApp User Manual
IEC101 User Manual
IEC104 User Manual
IEC103 User Manual
Modbus User Manual
ISaGRAF® User Manual
DNP User Manual
SOE User Manual
IEC61850 User Manual - Ed1
IEC61850 User Manual - Ed2
EOL Instructions
FTE-MSS-S856
FTE-WPP-S856
FTE-I1D-S854
FTE-I4D-S854
FTE-I3D-S854
FTE-MBD-S854
FTE-ISD-S854
FTE-DNP-S854
FTE-SOE-S854
FTE-IEC61-1-S854
FTE-IEC61-2-S854
FTE-EOLI-M588
Document Code
Pag 2
User Manual – HUe
Software Version in this Manual
10/01/2022
The information in this manual is valid for the software versions listed below. This information is also valid for later versions, although some parameters may change slightly:
Module
Baseline
Easergy Builder Tool
11.06.16
Version
1.7.9
Pag 3
10/01/2022
Content
User Manual – HUe
3 PHYSICAL MOUNTING & INSTALLING ............................................................... 23
4 CONFIGURATION & MAINTENANCE ................................................................... 38
6 TECHNICAL SPECIFICATIONS TABLE ............................................................... 89
Pag 4
1 Safety & Health
Public
10/01/2022
Content
User Manual – HUe
Pag 6
User Manual – HUe
1.1 Introduction
10/01/2022
1.1.1 Information of Safety
Important information
Read these instructions carefully and look at the equipment to become familiar with the equipment before trying to install, operate, service or maintain it. This manual includes different types of messages associated with situations that have different level of risk for people and / or for the equipment.
This symbol indicates "DANGER" or "WARNING". This symbol informs of an electrical risk that will cause personal injuries if the instructions are not followed.
This symbol is associated to a safety alert. It is used to warn of possible personal injury hazards. The user must follow all instructions or messages associated to this symbol to avoid possible injuries.
DANGER
DANGER indicates a hazardous situation which, if not avoided, will result in death or serious injury.
WARNING
WARNING indicates a hazardous situation which, if not avoided, could result in death or serious injury.
NOTICE
NOTICE is used to address practices not related to physical injury. The safety alert symbol shall not be used with this signal word.
To Keep in Mind
Electrical equipment should be installed, operated, serviced, and maintained only by qualified personnel. No responsibility is assumed by Schneider Electric for any consequences arising out of the use of this material.
A qualified person is who fulfill the requirements in section 1.2 .
1.1.2 Presentation
This manual provides information for an appropriate handling, commissioning and testing. This chapter about Safety also includes descriptions of the labels on the equipment.
Documentation for equipment ordered from Schneider Electric is dispatched separately from manufactured goods and may not be received at the same time. Therefore, this guide is provided in order to printed information (which may be present on the equipment) is fully understood by the recipient.
The technical data in this safety guide is typical only, see the technical data section of the user manual for specific details of a particular equipment.
Pag 7
10/01/2022 User Manual – HUe
Before carrying out any work on the equipment the user should be familiar with the contents of this Safety guide, the ratings on the equipment’s rating label and the user manual.
THE SAFETY SECTION MUST BE READ BEFORE STARTING ANY WORK ON
THE EQUIPMENT.
1.2 Introduction to Safety
The information in this chapter is provided in order to the equipment is properly installed and handled maintaining it in a safety condition. It is assumed that everyone who will be associated with the equipment will be familiar with the contents of that Safety section.
When electrical equipment is in operation, high voltages will be present in certain parts of the equipment. Failure to observe warning notices, an incorrect or not appropriate use may endanger personnel and equipment and also cause personal injury or physical damage.
WARNING
Before working with the terminal of connection, the equipment must be switched off and disconnected of the power supply.
Proper and safe operation of the equipment depends on appropriate shipping and handling, proper storage, installation and commissioning, and on careful operation, maintenance and servicing. For this reason, only qualified personnel may work on or operate the equipment.
Qualified personnel are individuals who:
• Have read and understood the information on the device and its user manual.
• Are familiar with the installation, commissioning, and operation of the equipment and of the system to which it is being connected.
• Are able to safely perform switching operations in accordance with accepted safety engineering practices and are authorized to energize and de-energize equipment and to isolate, ground, and label it.
• Are trained in the care and use of safety apparatus in accordance with safety engineering practices.
• Are trained in emergency procedures (first aid).
It is necessary to consider that the documentation of the equipment collects the instructions for its installation, set up and operation. However, the manuals could not cover all the possible circumstances neither include specific information on all the details.
In case of questions or specific problems, contact with his sales office of Schneider Electric or with the customer care center and request the necessary information.
Pag 8
User Manual – HUe
1.3 Symbols and Labels on the Equipment
10/01/2022
Before the equipment is installed or commissioned, the user must understand the following symbols, which may be used on the equipment or referred to in the user documentation:
Table 1 – Symbols
Symbol Associated Text Description
Possibility of electric shock
Caution, read the manual.
Possibility of electric chock
Protective earth connection
International Electrotechnical Commission (IEC) symbol associated to a DANGER or WARNING message indicating that there is an electrical risk. Failure to follow these instructions could cause damage to people or death.
Symbol associated with a risk alert. The user must read the manual before handling the equipment.
American National Standards Institute (ANSI) symbol associated to a DANGER or WARNING message indicating that there is an electrical risk. Failure to follow these instructions could cause damage to people or death.
Associated symbol to the protective ground connection.
Functional earth connection
Associated symbol to the functional ground connection.
CE Mark
Electronic equipment. Special instructions must be followed for disposed.
This symbol indicates that the equipment has been developed in compliance with all applicable European Directives.
This symbol indicates that, at the end of its life, this module must be disposed according to the
WEEE Directive (Waste Electrical and Electronic
Equipment).
Compliant with
RoHS.
Direct Voltage
The equipment has been designed and manufactured according to RoHS Directive
(Restriction of Hazardous Substances).
Symbol of direct voltage (V
DC
).
Alternate Voltage Symbol of alternate voltage (V
AC
).
1.4 Installation, Setup and Operation
There are several acquisition blocks in Saitel DR that use high voltages (> 50 V). The user is responsible to check that the characteristics of each equipment are adapted and convenient for his installation. The user should read the instructions of installation before proceeding to the use or maintenance of the equipment.
Not following these instructions can be dangerous for the people and the equipment.
Pag 9
10/01/2022 User Manual – HUe
DANGER
Devices that handle dangerous tensions are marked with a sticker on the front label (size: 12,5 mm). This label must be visible all the time while the module is installed on the DIN rail.
The following products handle high voltages:
• HU_AF : Advanced head unit with acquisition (P/N M503xx3x0x and P/N M503xx4x0x). For other part numbers, depending on the voltage handled by the equipment connected to the digital outputs (voltage > 50 V), this module must be marked with an electric risk label. It will not be marked on factory.
• AB_DI : Digital inputs module (P/N: M55520000x, M55530000x and M55540000x).
• AB_DIDO : Input and output digital module (P/N M5722x000x, M5723x000x and M5724x000x).
For other part numbers, depending on the voltage handled by the equipment connected to the digital outputs (voltage > 50 V), this module must be marked with an electric risk label. It will not be marked on factory.
• AB_AC : Direct measurements module (P/N M562x0000x).
• AB_DO : This module does not handle high voltages. This module must be labeled with an electric risk label when some equipment that manage voltage higher than 50 V are connected to digital outputs.
It is recommended to install the RTU inside a cabinet with a key. This cabinet only should be opened by a qualified person.
WARNING
If this type of cabinet is not available, a barrier must be installed in order to avoid an accidental contact with these dangerous elements. This barrier should only be able to be uninstalled using a special tool.
If the barrier has to be removed in order to access to equipment, personnel responsible for the task must be sure that the barrier is installed again when the task is finished.
While the RTU is accessible for a user, all people must follow all instructions to prevent electrical risk or discharges.
Not following these instructions can give like result that the equipment do not work properly or even can damage to the people or equipment .
An electrical risk symbol with enough size must be included on the cabinet’s door or on the barrier .
The following image shows an example:
Figure 1 - Barrier of protection for elements with high voltages
Pag 10
User Manual – HUe 10/01/2022
NOTICE
Terminals will not be accessible to the user directly once it has made the installation of the equipment. The cabinet will have to remain closed with key or the screen of installed protection.
The cabinet or installation must have a general switch placed just in the cable entry of the
installation (see paragraph 1.7.1 ).
For the cleaning of the equipment, it is recommended to remove the power and to use only a dry cloth by the surface when it detects excessive presence of dust or any element deposited on the surface.
WARNING
Do not use liquid products of cleanliness due to the presence of active parts.
Because of the variety of uses of the product, the managers of the application and use of this controller device will have to take the measures to the fulfillment of all the safety requirements and provision of each application. These requirements are according to the applicable laws, regulations, codes and standard.
1.5 Earthing
WARNING
Before energizing the equipment, it has to be earthed properly such as it indicates in the
When installing the equipment, ground is the first thing that should be connected and the last one that should be disconnected.
Saitel can be earthed for two distinct needs:
• For purposes of electrical safety (Protective Earth, PE).
• Improve the behavior in Electromagnetic Compatibility (EMC) and derive perturbations to earth
(functional Earth).
1.5.1 Electrical Safety
Only qualified personnel, with knowledge about hazards associated with electrical equipment is allowed to install Saitel DR. In general, the installation will be following IEC 61010-1 recommendations in order to be compliant with this norm.
The modules must be installed on a metallic DIN Rail which is fixed on a metallic surface. This metallic surface must have an M4 screw marked with this symbol.
According to the norm IEC 61010-1, the ground of the cabinet or installation must be connected to this screw .
Saitel DR modules have a metallic enclosure offering protection for isolation faults.
WARNING
All electronic equipment with high voltage must be disconnected before dismounting a module from the DIN rail.
A dedicated connection with green/yellow wire should be used to have electric continuity to the installation protective earth. Use a wire with adequate section according to IEC 61010.
Pag 11
10/01/2022
Figure 2 – Yellow and green cable for earthing
User Manual – HUe
The design and installation of the cabinet is responsible for compliance with all the existing international and national electrical codes concerning protective grounding of any equipment.
WARNING
According to Electrical Safety:
• The screw for ground must be exclusive for this use.
• The power voltage must be supplied by a power supply that offers double or reinforced insulation against high voltages (higher than 50 V).
1.5.2 Functional Earth (EMC)
In this case the main rule is that the connection has to be done with wires of the lower possible length to the shield or earth connection nearest. In this case the section of the driver is less notable, moreover, it is advised of the use of flat wires or flexible conductive bands for a good behavior EMC.
NOTICE
The DIN rail must have terminals of earthing (of yellow and green color) necessary to connect the terminals of PE (if it is present).
Figure 3 –Terminal for functional earth (EMC)
All Saitel DR modules with power or polarization connector have an exclusive terminal for earthing
EMC. These modules are HUe, HU_B, HU_A, HU_AF, XU, AB_DO, AB_DIDO and AB_SER with external polarization.
It must be connected as follows:
Figure 4 – Example of earthing for EMC
Pag 12
User Manual – HUe
1.6 Handling Electronic Components
10/01/2022
Like any electronic equipment, Saitel is susceptible to receive electrostatic discharges during the handling. It is necessary to take the usual measures to minimize this risk, since serious damage to the equipment can be caused, which may not be detected immediately but which may affect the reliability of the product.
WARNING
The enclosure should ONLY be removed by authorized use and ONLY when is strictly necessary because this action has a risk for the equipment. The following precautions will be taken:
• Before removing the enclosure, the operator be equipotential with the equipment. The operator must have a grounding bracelet and the device must be connected to ground as well
• Avoid touching the electronic. The board must be always manipulated for the edges.
• If the equipment has to be passed between two persons, both must be equipotential.
• Put the module always on an antistatic surface or on a surface equipotential with the operator.
• During the storage and transport, the module will remain in the packaging.
Not following these instructions can give like result that the equipment do not work properly or even can damage the people or equipment.
1.7 Technical Specifications for Safety
1.7.1 Protective Elements
The cabinet's engineering and installation must include a general automatic switch next to the cables' input in the cabinet; once the door is opened, high voltages must be interrupted inside. This switch must be located at a place which is not accessible by a third person while the operator is using the boards in the cabinet.
Moreover, the installation will incorporate a circuit breaker of 5A next to the cabinet protecting it from possible overcurrent in the power supply.
Both switches will be labeled with the symbol O as "Off" and I as “On”.
WARNING
The connection / disconnection switch must be installed in a fixed element (for example the wall of the cabinet) and it must not break any earthing wire.
1.7.2 Environmental Conditions
The protection degree of the equipment is IP20.
WARNING
This equipment has been designed ONLY for indoor use.
If it is necessary for his use in some external surroundings, it has to mount in a cabinet or specific accommodation that contributes at least a degree of protection IP54, protected against the dust and water.
Pag 13
10/01/2022 User Manual – HUe
The electronic cards of the modules will be able to be tropicalized or not according to the manufacturing option. The tropicalized used is the AVR80, of the company ABchimie. It can consult all the technical information of this type of finishing in http://www.abchimie.com
.
Other data to consider about the environmental are:
• Altitude until 2000 m.
• Operation temperature range: Between -40 ºC and 70 ºC. (IEC 60068-2-1 and IEC 60068-2-2).
WARNING
According to the standard 60950-1, all electrical safety tests have been done in an environmental temperature range of -40 ºC to 60 ºC. For higher temperature (> 60 ºC), the module must be handled with care since the metal surface could reach a dangerous temperature for the user.
• Maximum relative humidity of 95%. (IEC 60068-2-30)
• Degree of pollution II. (IEC 60255-5)
• Overvoltage transitory until levels of Category III. (IEC 60255-5)
1.7.3 Storage Conditions
The continuous exhibition to some high levels of humidity during the storage can cause damages to the electronic components and reduce the useful life of the equipment.
Recommended relative humidity for storage conditions: lower than 50%.
Before the installation of an electrical equipment, it is recommended to leave the necessary time for the acclimatization of the environmental temperature.
1.8 Technical Label
Each Saitel product includes a technical label with the following information:
Figure 5 – Technical label
NOTICE
The “Technical data” includes a zone with relevant information about the input and output voltage in the module. Any voltage greater than 50 V must be considered as a high voltage.
Pag 14
User Manual – HUe
1.9 Packing and Unpacking
10/01/2022
All Saitel modules are packaged separately in their own carton box and shipped inside outer packaging. Use special care when unpacking the equipment. Do not use force.
NOTICE
Our products leave our factory in closed, sealed original packaging. If at receipt of the delivery the transport packaging is open or the seal is broken, the confidentiality and authenticity of the information contained in the products cannot be ensured.
The design revision and manufacturing options can be determined using the P/N included in the packaging label on packaging.
After unpacking the equipment, inspect it visually to be sure it is in proper mechanical condition.
If the product needs to be shipped, the original packaging must be used, including foams and the carton box. If the original packaging is no longer available, make sure that the packaging used is according to ISO 2248 specifications for a drop height of 1 m.
1.10 Decommissioning and Disposal
This symbol, means that, at the end of its life cycle, the product must not be disposed together with habitual residues. To avoid any possible damage to the environment or to the human health that represents the uncontrolled elimination of residues, please, separate the battery (if there is one) of the other elements, and each one must be recycled according to the local regulation .
Pag 15
10/01/2022
2 General Description of HUe
User Manual – HUe
Pag 16
User Manual – HUe
Content
10/01/2022
Pag 17
10/01/2022
2.1 Saitel DR Platform
User Manual – HUe
Saitel DR is a hardware platform by Schneider Electric. It consists of a set of equipment which have been specifically designed for real-time control and automation applications. Saitel DR is a high-technology platform which serves Schneider Electric’s business areas.
On this hardware platform, the Baseline Software Platform is installed. This software is used in
Saitel families (Saitel DP and Saitel DR) and other Schneider Electric products.
Other features identifying Saitel DR are:
• A DIN rail is used for the mechanical installation.
• The communication between the controls units integrated in a distributed system is mainly established by Ethernet.
• The terminal blocks for field-connection are completely built into acquisition blocks.
Figure 6 – Saitel DR
Saitel DR’s design has been optimized to meet the most demanding requirements of multiple sectors:
• Safety and reliability requirements for power, gas and water supply, as well as sewage treatment plants, etc.
• Compliance with electric safety, electromagnetic compatibility, and environmental standards.
• Centralized monitoring and control of geographically-distributed systems which support hierarchical data acquisition and sharing networks.
• Local monitoring and control with data sharing capabilities of plant-distributed equipment.
• Quick troubleshooting, including the possibility of using programmable automation execution.
NOTICE
Please, note Saitel DR does not support hot-swapping, that is, module replacements during operation.
2.2 HUe Functions in the ITB
HUe is a high-performance CPU developed by Schneider Electric within the Saitel DR family. HUe performs the control functions for the complete system, centralizes the information acquired by other modules, and executes the programmable logic control, communication protocols and userspecific applications.
The communication with the acquisition modules in the ITB is established by an internal high-speed bus that makes the system highly reliable even in noisy environments.
Pag 18
User Manual – HUe
Figure 7 – Communication between HUe and ABs
10/01/2022
HUe controls and manages the following functions:
ITB Controller
This block controls the operation of both the HU and the ABs connected to the HU through the bus.
These functions include:
• Operation mode monitoring. It performs functions as hardware and software Watchdog control, the states control of the ABs and the HU and the provision of diagnostic information about the
ITB status through the LED indicators and several log files. These files can be consulted by a user with sufficient privileges through SFTP or webApp.
• Interface with the operator through the console, webApp (for supervision and maintenance) and Easergy Builder (for configuration).
• Firmware upgrade by SFTP or webApp (using MNT port) or USB 2.0 port.
ITB Configuration
HUe maintains and manages the information that supports the real-time database, coreDb. In this database, the I/O signals are related to the communication protocols signals. The configuration is based on XML files that are generated with the Easergy Builder tool. These files are generated on a PC and sent to the CPU via an SFTP connection through the MNT port.
ITB Synchronization
Up to two different synchronization sources can be configured. In this configuration is included the priority level for each source, so there will be a primary and a secondary source. If both sources are active, only the primary source will synchronize the system.
NOTICE
The primary source is used to synchronize the ITB, if available. Otherwise, the secondary source is used.
The available synchronization sources are:
• A GPS connected to the COM1 port. The time received from the GPS is used to set the system’s clock and the RTC.
• An SNTP source through Ethernet. HUe can be used as SNTP server and client.
• Protocol : Most telecontrol protocols allow synchronizing to secondary devices.
• Console : The user can set the system's time manually from the console terminal.
• IRIG-B : HUe can be used as a server and/or a client. The communication always will be made with IRIG-B compliant devices.
Pag 19
10/01/2022 User Manual – HUe
NOTICE
If the HUe is configured as IRIG-B server an AB_SER module must be included in the ITB. The
IRIG-B signal will be send to client devices through the COM ports of this module. More information in the AB_SER user manual.
If the synchronization source is not configured, the console device will always be created by default. The console operates as the lowest priority when other source is configured.
ITB Communications
The HUe configuration includes information about definition and parameterization of communications:
• Controlling and controlled station IEC101.
• Controlling and controlled station IEC104.
• Master station and outstation DNP 3.0.
• Controlling station IEC103.
• Client and server Modbus.
• Client IEC61850, Edition 1 and 2.
• Server IEC61850, Edition 2.
• Client SPA-Bus (only available for 11.06.16 and later)
I/O Acquisition
HUe manages the information exchange with the ABs. Its main functions include:
• Processing I/O information, which offers an added value to the information exchanged with the
ABs.
• Accessing the internal bus to exchange information with the ABs.
• The HUe module has 4 digital inputs that can be used as 4 general-purpose digital inputs or as
2 specific-purpose digital inputs and 2 general-purpose digital inputs (more details below in this manual).
Real-Time DataBase (RTDB)
The core of the Baseline Software Platform is the real-time database or coreDb. It is a real-time database which stores not only the information acquired from field devices, but also the information about the status of HUe and ABs included in the ITB. coreDb also relates the acquisition signals to the communication protocol signals. This database is generated in the CPU by using the configuration information.
The information which is received from field in real time is processed, stored in the RTDB and then related to the communication protocols signals of the ITB, which function is to transfer that information to the primary device.
Pag 20
User Manual – HUe
Figure 8 – coreDb operation example
10/01/2022 coreDb can also have as a source of information the result of a logic, which can be implemented by a third-party software such as ISaGRAF® or within the database itself with an internal device of the type "Formula".
Consult more information about this functionality in the Easergy Builder user manual.
Cybersecurity
The HUe module is supplied with a standard security policy, complemented with the definition of an
RBAC model (Role-Based Access Control). This model is defined and managed through a special tool, CAE (EcoStruxure™ Cybersecurity Admin Expert.
2.3 Interfaces
The HUe module is a high-performance CPU, which offers superior performance to other Saitel DR
CPUs. It includes the Baseline Software Platform based on Linux operating system and with an integrated cybersecurity brick.
Figure 9 – HUe front view
The main features of this module are:
• Power input between 24 and 48 V
DC
, with tolerance of 20%.
• A reset button integrated allowing the user to reset the module mechanically.
• It implements a security mechanism for data in memory (NVRAM) allowing to keep the information for some time if the power is temporarily down.
• 4 general-purpose digital inputs.
• Synchronization using: IRIG-B input, PPS signal (through a GPS), console or SNTP.
• A watchdog isolated output is available and can be used according to the requirements of the system.
Pag 21
10/01/2022 User Manual – HUe
• A copper Fast-Ethernet port for configuration and maintenance (10/100BaseT).
• Two additional Fast-Ethernet ports, which can be copper (10/100BaseT) or fiber optic
(100BASE-FX) depending on the mounting options.
• Two RS-232 non-isolated communication ports. COM1 allows modem control but COM2 does not.
• One RS-485 isolated communication port.
• One console port using a miniUSB connector.
• One USB 2.0 connector for software upgrading.
• SD slot.
2.4 Hardware Architecture
The HUe module is composed by two or three electronic boards, depending on the manufacturing options.
Figure 10 – Electronic boards in HUe
These electronic boards and the metallic enclosure makeup the HUe module.
This information is shown in the technical label on the module with the Part Number (P/N):
Figure 11 – Part Number description
If the module is manufactured without optic fiber, only two boards will be mounted.
Ordering options:
• (Ax) Version of the microprocessor: Lite / Pro.
• (Bx) Power supply. The module can be powered with 24 V
DC
or 48 V
DC
, both ±20%.
Pag 22
User Manual – HUe
3 Physical Mounting & Installing
10/01/2022
Pag 23
10/01/2022
Content
User Manual – HUe
3 PHYSICAL MOUNTING & INSTALLING ............................................................... 23
P OWER S UPPLY R EQUIREMENTS ................................................................... 25
M OUNT AND D ISMOUNT P ROCEDURES ............................................................ 25
IRIG-B AND W ATCHDOG O UTPUT .................................................................. 32
Pag 24
User Manual – HUe
3.1 ITB Installation
10/01/2022
3.1.1 Handling Modules
Please note the following precautions to avoid electrostatic damages:
• Never touch the pins of the bus connector.
• Keep the module in its packaging box when unused.
WARNING
Electrostatic discharges may damage semi-conducive devices within the module.
3.1.2 HUe Location in the ITB
The HUe module must always be the first module in the ITB, that is, it must be mounted in the first position of the first DIN rail, being the bus initiator in the ITB.
The HU can only be found in the second position of the DIN rail, if the ITB requires processing redundancy. In this configuration, there is a main DIN rail in which two redundant HU modules are installed and connected to the acquisition ITB by means of an Ethernet network; the system’s bus is not used in this case.
NOTICE
In order to minimize the adverse effects of noise and heat, it is recommended to install the ITB’s head unit as far as possible from other modules handling alternating current and high voltages.
3.1.3 Power Supply Requirements
To calculate the ITB’s power supply requirements, the power consumption of each module must be considered. The modules’ power consumptions must be added plus a safety margin (min. 20%).
Each row in the ITB is powered independently thought the HUe (first row) or XU (second and following rows) module.
In order to avoid ITB overload, the power supply performance should also be considered (typically,
70-90%).
The power consumption data is detailed in the technical specifications table of each module’s user manual and in the technical label on the equipment.
3.1.4 Mount and Dismount Procedures
WARNING
It is important to assure that handling is always done while the ITB elements are unpowered.
Saitel DR modules have a DIN-rail bracket at the rear side that allows mounting on a DIN rail.
Figure 12 – Mount bracket on DIN rail
The mounting procedure is described below:
• Switch off the power supply.
• Attach the module’s rear bracket on the upper DIN rail.
Pag 25
10/01/2022 User Manual – HUe
• Press the lower front panel gently until a click confirms that the bracket is fit on the rail.
• Verify the module is anchored firmly to the rail, although lateral movement is possible.
Figure 13 – Saitel DR module on a DIN rail
The module is dismounted from the DIN rail as follows:
• Switch off the power supply.
• If necessary, disconnect the bridge(s) connecting the module to the system bus.
• Holding the module by the front panel, push the upper metal tab downward. The user can also pull the tab down using for example a screwdriver as shown:
• Pressing the tab, remove the module from the lower DIN rail.
• Once detached, the module can be removed easily.
3.2 Wiring HUe
3.2.1 Wiring Recommendations
The following table shows several wiring recommendations for signals, communications and power:
Type
Power
Digital Inputs
RS-485
IRIG-B
Watchdog
7 mm
7 mm
7 mm
7 mm
7 mm
1.5-2.5 mm²
15-13 AWG
1.5 mm²
15 AWG
1.5 mm²
15 AWG
1.5 mm²
15 AWG
1.5 mm²
15 AWG
0.5 Nm
0.5 Nm
0.5 Nm
0.5 Nm
0.5 Nm
Copper
Copper
Copper, shielded
Copper
Copper
The following section describes each HUe interface, including functionality and wiring when it is required.
Pag 26
User Manual – HUe
NOTICE
Follow all wiring recommendation for EMC included in Saitel DR Platfom user manual.
10/01/2022
3.2.2 Power and Reset
Figure 14 – Power and reset
The power supply input terminal is located in the upper left area. There is a DC/DC converter, next to the filtering electronic components, which is used to power both the HUe module itself and all the
AB modules assembled on the same row.
NOTICE
The maximum power to be supplied to the rest of modules in the same row by the HUe module is 10 W. If the modules to be assembled on the ITB require a higher power, then, the ITB must be divided into several rows, always observing the above-mentioned maximum power allowed for each row.
A Reset button is included in this block allowing the user to reset all the ITB.
Power Wiring
The POWER connector must be used as power input. The input voltage range is 24 to 48 V
DC
, with a tolerance of ±20%.
WARNING
For safety reasons, the use of ferrules on power input cables is recommended to avoid possible short-circuits.
From left to right, the connecting order must be functional Earth, negative and positive terminal.
WARNING
For safety reasons, before connecting the aerial terminal to the module, it is recommended:
• To check that the voltage between the positive and negative poles does not exceed the
maximum operating voltage (see the technical table in chapter 6).
• To check that the polarity has not been inverted according to the label on the terminal.
Pag 27
10/01/2022
3.2.3 Digital Inputs
Figure 15 – General-purpose digital inputs
User Manual – HUe
HUe has 4 digital inputs located in the lower left, only configurable as single inputs. These signals are useful to inform the operator about some controlled malfunction in the system. For example, the cabinet door is open (the appropriated wired must be done).
The digital inpus 1 and 2 can be used for the following purposes:
• Digital input 1 : This signal provides the HUe module with information about the digital inputs’ polarization status of the ABs installed in the ITB. When the signal is active, the polarization of all digital signals is correct. If the signal is disabled, the HU will understand that there is a polarization fault.
• Digital input 2 : If this signal is enabled, the HUe module will interpret that the ITB is working in
LOCAL mode, whereas if it is disabled, the ITB is operating in REMOTE mode. When the ITB is in LOCAL mode the commands are disabled.
To use these two signals with the purpose described above, they must be defined in the database following the instructions included in paragraph 4.5.1 of this manual.
WARNING
Before doing any local operation, for safety reasons, the operator MUST :
• To be sure that the "Local" LED on HUe is lit.
• To be sure that the secondary relays are de-energized.
Digital Inputs Wiring
Use AUX DI terminal in order to use the general-purpose digital inputs. These signals are selfpolarized, that is, they do not need an external polarization source.
These digital inputs are designed for internal use within the cabinet where the HUe module is installed.
WARNING
These signals must not be connected to equipment that are outside the cabinet. Failing this instruction could modify EMC behavior of the equipment.
The following figure illustrates how each input receives the polarization through the common:
WARNING
These digital inputs are internally polarized. Please, DO NOT CONNECT to other power supply.
Failure to observe this instruction can result in equipment damage.
Pag 28
User Manual – HUe
3.2.4 Serial Communications
Figure 16 – Serial communication ports
10/01/2022
• COM1 and COM2 : non-isolated RS-232 communication ports for general-purpose. Both ports use male DB-9 connector.
• CON : Console port with miniUSB connector.
• RS-485 : Isolated TS-485 communication port.
RS-232 Communications Wiring (COM1 and COM2)
All modem signals are available in COM1 port. COM2 only uses RTS and CTS signals. The maximum speed in both ports is 115200 bps.
Following tables show the pinout for both connectors:
Table 2 – Pinout of COM1
7
8
5
6
9
3
4
1
2
Pin Description
DCD – Data Carrier Detect
Rx – Data Reception
Tx – Data Transmission
DTR – Data Terminal Ready
GND – Ground
DSR - Data Set Ready
RTS – Request to Send
CTS – Clear to Send
RI – Call indicator
Table 3 – Pinout of COM2
7
8
5
6
9
3
4
1
2
Pin Description
Not connected
Rx – Data Reception
Tx – Data transmission
Not connected
GND – Ground
Not connected
RTS – Request to Send
CTS – Clear to Send
Not connected
Pag 29
I/O
O
I
-
I
I
O
O
I
I
I/O
O
I
-
-
-
O
-
-
I
10/01/2022 User Manual – HUe
NOTICE
COM1 can receive a pulse per second signal (PPS) through pin 8, so it must be used as the
GPS input, if required. The input PPS signal must be valid for RS-232 levels.
The validated GPS devices to be connected to the COM1 port are GPS35 (Garmin) and GPS16
(Garmin).
Some GPS devices don’t allow to use PPS signal.This operation mode implies that the synchronization accuracy will be lower. It can produce a desviation of up to 10 ms in the generation of the signal.
NOTICE
When using a GPS synchronization device, it is always advisable to wire the PPS signal to achieve the highest accuracy in the synchronization.
WARNING
The installer should check that the cable connected to each COMx port is correct. It is also recommended to use identification tags on the cables to avoid errors.
Redundancy Wiring (COM1 and COM2)
For redundant system, both HUe can be connected using COM1 and COM2 ports. The following pinout must be considered (other pins should not be connected):
Figure 17 –Pinout of the cable for redundancy
Console Port Wiring (CON)
The following table shows the pinout of the miniUSB port for the console:
3
4
1
2
5
Table 4 – Pinout of the console port
Pin Name
-
Data -
Data +
Mode detection
Ground
Wire color
White
Green
-
Black
Pag 30
I/O
Not connected
O
I
Not connected
Ground
User Manual – HUe
RS-485 Wiring (RS-485)
10/01/2022
This terminal block is used to communicate with other equipment through a 2-wire RS-485 communication (Half-Duplex). The figure below shows the pinout of this terminal:
WARNING
The connector RS-485 of HUe includes a termination resistor that cannot be disabled, so HUe only can be installed as first and last device on the RS-485 bus. In this case, the termination resistor included in any other element in the bus must be disabled.
VERY IMPORTANT: Three HUe device cannot be installed as part of the same RS-485 bus.
The relationship between this 3-poles terminal and the SM_SER’s DB9 connector is the following:
Table 5 – 2-wire RS-485 to DB9
HUe connector DB9 connector
A
B
Ground
Pin 9 (Y)
Pin 8 (Z)
Pin 5
3.2.5 Ethernet Communications
Figure 18 –Ethernet communication ports
• MNT : Fast-Ethernet port (10/100BaseT) for maintenance purpose. It uses a RJ-45 connector.
• LAN1 and LAN2 : Fast-Ethernet communication ports using copper or fiber optic depending on the manufacturing options. o Copper ports allow 10/100 BaseT IEEE 1588, with a RJ-45 connector. o Fiber optic ports allow 100Base-FX with SFP connectors.
WARNING
The installer should check that the cable connected to each Ethernet port is correct. It is also recommended to use identification tags on the cables to avoid errors.
Ethernet Wiring – Copper ports
The pinout for RJ-45 connector is the following:
Pag 31
10/01/2022
Table 6 – Pinout of the copper ports
User Manual – HUe
7
8
5
6
3
4
1
2
Pin Name Description TIA/EIA 568A TIA/EIA 568B
BI_DA+ Bi-directional pair A+ (TX) White/Green White/Orange
BI_DA- Bi-directional pair A- (TX) Green Orange
BI_DB+ Bi-directional pair B+ (RX) White/Orange White/Green
BI_DC+ Bi-directional pair C+ Blue Blue
BI_DC- Bi-directional pair C- White/Blue White/Blue
BI_DB- Bi-directional pair B- (RX) Orange Green
BI_DD+ Bi-directional pair D+ White/Brown White/Brown
BI_DD- Bi-directional pair D- Brown Brown
TIA/EIA 568A and TIA/EIA 568B are two color codes used for wiring eight-position RJ45 modular plugs. Both are allowed under the ANSI/TIA/EIA wiring standards. The only difference between both codes is that the orange and green pairs are interchanged.
WARNING
Each network segment cable length may be up to 100 m.
Ethernet Wiring – Fiber Optic Ports
If fiber optic is selected in manufacturing options for LAN1 and LAN2, they have to mount a SFP transceiver with LC connector. These transceivers aren’t included with HUe.
The following figure shows two connectors which could be used in LAN1 and LAN2:
The following models are recommended:
• Models: HFBR-57E0PZ and HFBR-57E0APZ . According the manufacturer datasheets: o Full compliance with the optical performance requirements of 100Base-FX version of
IEEE802.3u. o Operates with 62.5/125 μm and 50/125 μm multimode fiber , with a LED light source of 1300 nm. o Maximum link length: 2 km. o Operating temperature: From -40 ºC to +85 ºC (only HFBR-57E0APZ)
3.2.6 IRIG-B and Watchdog Output
Figure 19 –IRIG-B and WD output connectors
Pag 32
User Manual – HUe
IRIG-B Wiring
10/01/2022
This terminal block is used to receive an IRIG-B claqsignal (non modulated TTL - 5V) which can be used by the CPU to synchronize the ITB. The input impedance is 600 Ohm.
The connector for IRIG-B has the following pinout:
HUe can be set as an IRIG-B client and/or server, according the standards IRIG-B002, 003, 006 and 007.
Watchdog Wiring (WD)
A watchdog output (identified as WD and labeled as B5) is available in HUe for system monitoring.
It is implemented as follows:
• solid-state relay (normally open)
• supporting a maximum voltage of 250 V.
• current of 200 mA.
The relay status depends on the FAIL_RTU supervision signal. A normal value of this signal is 0, and value 1 is associated to the detection of a controlled malfunction in the system.
WARNING
The watchdog output is not designed to be wired as a field output. This output was designed to be connected to a local device inside the same cabinet. The connection wire must be shorter than 3 meters.
3.3 Compact-Flash Card
Figure 20 – Slot for SD card and USB connector
The slot for the SD card is located on the left side of the module. This card can be used for mass storage of data, for example, the event log or configuration files.
The slot for the Compact-Flash card is located on the left side of the module. This card can be used for mass storage of data, for example, the event log.
The following Compact Flash card have been validated (both with capacity of 512 MB):
• Swissbit manufacturer, model SFCF0512H1BK1MT-I-MS-553-SMA.
• Apacer manufacturer, model AP-CF512ME3NR-ETNRQ.
If necessary, to extract the compact flash card, use the ejector located at right of the slot.
NOTICE
For P/N E7 and later, this ejector is not mounted. To extract the compact flash card, use an appropiate tool, for example a tweezers for electronic.
Pag 33
10/01/2022 User Manual – HUe
If the CF ejector is not available for the module and there is some problem to access the card, the enclosure can be removed allowing access to the card:
WARNING
Turn off all power supplying this equipment before working on or inside it. Consider all sources of power, including the possibility of back feeding.
3.4 Expansion
Through a flat ribbon connector, the CPU starts the data and power bus, expanding it to the other modules.
Figure 21 – Expansion bus connector
NOTICE
Before disconnecting the secondary devices from the bus (disconnecting the flat ribbon) the ITB must be unpowered.
3.5 Configuration Switches
There are 4 configuration switches on the front of the module. They are numbered 1 to 4 from the left to the right.
Figure 22 – Configuration switches
Pag 34
User Manual – HUe
This group of switches allows:
• Restoring the manufacturing default configuration.
10/01/2022
• Enabling the automatic execution of the addressing procedure (AAP).
• Executing the AAP automatically when the ITB starts.
As is indicated on the label, the switch is in position ON if is up and OFF when is down.
These switches can be used as follow:
• Switch 4 : It restores the factory IP configuration. If switch 4 is ON when HUe starts, the network configuration will be restored for all Ethernet ports. If the network configuration file
(netConfig.xml) exists, it will be renamed to old_netConfig.xml. The default IP addresses are
• Switch 3 : It enables or not the automatic execution of the AAP: o On : Enabled. When the ITB starts, the AAP procedure is automatically executed. o Off : Disabled. The AAP procedure has to be executed with a command if it is required. This command may be executed depending on the position of switch 2.
• Switch 2 : It allows or not the execution of AAP: o On : Allowed. The AAP can be executed. o Off : Not allowed. The AAP cannot be executed either automatically or manually.
• Switch 1 : Reserved. It must be in OFF position.
3.6 LED Indicators
There are 24 light indicators (LED) on the front of the module:
Figure 23 – LED indicators
The information by the LED indicators includes:
• General status of the module ( On , Bat , Local and Sync )
• Configuration and acquisition status ( Run , Fail , DIO and RED )
• Status of the 4 general-purpose digital inputs ( Digital Input x ).
• Transmission/Reception in COM1, COM2, CON and RS-485 ports ( Tx and Rx ).
• Communications in the Ethernet ports LAN1 ( ETH1 ) and LAN2 ( ETH2 ).
NOTICE
There is not a LED associated to the MNT port.
HUe’s LED provide the following information to the operator:
Pag 35
10/01/2022
On
LED
Bat
Local
Sync
Run
Fail
DIO
RED.
Digital
Inputs x
Tx
Rx
User Manual – HUe
ïƒ Blink
Table 7 – LED indicators
ïƒ On ïƒ Off
Status Description Recommended action
Powered.
Unpowered.
The supercapacitor is discharged. While this led is on, the system cannot keep the data in memory if a power down occurs.
Normal state. If the supercapacitor is fully charged, data in memory can be kept for 8 hours (at 25 ºC) if a power down occurs.
RTU in LOCAL mode. Digital outputs are disabled in the ITB.
RTU in REMOTE mode.
The system uses an external synchronization source.
Any external synchronization source is being used.
RTU operative, with configuration or not.
-
Connect the module to a power supply according to the input voltage of the module.
Switch 1 must be turned OFF. The led will turn off when the supercapacitor is loaded.
RTU not operative.
RTU not configured or with errors.
A correct configuration is loaded in the CPU.
Use Easergy Builder and load a configuration without errors in the CPU.
There is at least one module in Fail status in the ITB.
Use the console tool in order to check if the message “CONF OK” is shown. The supervision signal DOING_WELL must be defined in coreDb and set to 1.
All modules in the ITB are OK.
Redundant system. This CPU is in HOT status.
Identify the module with problems and perform the recommended actions. More information in the user manual of the module in fail status.
Redundant system. This CPU is in
STANDBY status.
Non redundant system or configuration.
The digital input x is activated.
The digital input x is deactivated or not defined in coreDb.
The port COMx/CON/RS485 is transferring.
The port COMx/CON/RS485 is not transferring.
The port COMx/CON/RS485 is receiving.
The port COMx/CON/RS485 is not receiving.
Pag 36
User Manual – HUe
LED Status
Li
Ac
Description
The port ETHx has a physical connection.
The port ETHx has not a physical connection.
There is a channel activity through the ETHx port.
There is not a channel activity through the
ETHx port.
10/01/2022
Recommended action
Pag 37
4 Configuration & Maintenance
Public
User Manual – HUe
Content
10/01/2022
4 CONFIGURATION & MAINTENANCE ................................................................... 38
N ETWORK C ONFIGURATION (IP / R OUTER / F IREWALLS ) .................................. 43
C REATING A RTU B ASED ON HU E .................................................................. 54
C ONFIGURING A R EDUNDANT RTU ................................................................. 55
R EADING THE C ONFIGURATION FROM THE HU ................................................ 55
C REATE A N EW C ONFIGURATION ................................................................... 55
C ONFIGURING HU E C OMMUNICATION C HANNELS ............................................ 57
C ONFIGURING HU E L INK C ONFIGURATION ...................................................... 58
L OCAL A CQUISITION C ONFIGURATION ........................................................... 68
G ENERAL P URPOSE D IGITAL I NPUTS ............................................................ 69
T RANSFERRING THE C ONFIGURATION TO THE RTU ....................................... 70
Pag 39
10/01/2022
4.1 Getting Started
User Manual – HUe
HUe is supplied with a basic configuration, which will help us have a first contact with the system.
To get started, the following data should be known:
Default IP Addresses
Table 8 – Default IP addresses
Port
LAN1
LAN2
MNT
Description
Operating system's eth0 port.
Operating system's eth1 port.
Operating system's eth2 port. This is the maintenance dedicated port.
IP Subnet Mask
10.1.1.1 255.0.0.0
192.168.1.1 255.255.255.0
192.168.2.1 255.255.255.0
User
In accordance to the policy provided with the CAE tool, the default users which can log into the system are:
Table 9 – Default users
User Level
Operator
Engineer
Installer
Viewer
Administrator
User
Operator
Engineer
Installer
Viewer
Password
Operator1!
Engineer1!
Installer1!
Viewer1!
SecurityAdmin Security1!
Description
This user can view most of the system's information (data, syslog, events, settings…) It can write to coreDb, but it does NOT have access to security parameters.
This user can view and modify all the system information, except for the security parameters. It can also access the operating system's console, although it cannot execute Saitel commands.
This user can view and modify all the system information, except for the security parameters.
In the console, it can only access the BLMon application and Saitel commands.
This user level can read coreDb settings and data and can connect to webApp. It cannot make changes to settings or to the coreDb data.
This user level is only used to define and modify the security parameters and user permissions.
NOTICE
It is recommended to use Engineer user to perform configuration tasks with Easergy Builder and Installer user to use the console.
It is possible to execute console commands with the Engineer user as follow:
Activate the command terminal with: tty > /tmp/BLCMD
Execute the command: echo "claqVersion" > /tmp/BLCMD
This command provides the software version installed on the ITB modules.
Pag 40
User Manual – HUe 10/01/2022
When working with the HUe module, the user will need to prepare the working environment, in terms of installing the adequate tools, making the software files available, in case the CPU needs to be upgraded, and so on.
There are certain tasks that the user must be familiar with before using Saitel DR, such as:
• Installing and using Easergy Builder: This manual describes specific operations to be
performed with this tool (see Chapter 5 in this manual). For detailed information about the use
of Easergy Builder, please refer to “Easergy Builder User Manual”.
• Using webApp: For detailed information about the use of the web server, please refer to
“webApp User Manual”.
• Operating Saitel DR modules: For further information about the wiring, configuration, and use of the modules which be included in an ITB, please refer to their respective user manual.
4.1.1 Using the Console
The material below is required to use the console:
• A HUe M588 Module.
• A console cable if a USB cable is used. For connecting to the HUe, the cable must have a miniUSB connector (for further information about the CON port and its pinout, please refer to
section 3.2.4 in this manual).
• Software for serial channel connection. In the examples of this user manual, PuTTY is used, which is a free-license software that can be used in most PC’s running on Microsoft®
Windows® and several UNIX® platforms.
Connection
Connect the cable between the CON port (miniUSB connector) in the HUe to a PC serial port (one of the USB ports can be used).
Switch on the HUe module and execute PuTTY (or another commercial software).
Working with the Console
When the COMx port is identified, connect the console port to the PC and open a console session with the following parameters:
Figure 24 - Putty configuration
When the connection is established, the CPU requests a valid user:
Pag 41
10/01/2022
Figure 25 – HUe login
User Manual – HUe
The commands that can be executed in the console will depend on the logged-in user permissions.
In order to execute the usual actions with this tool, it is recommend using Installer user with
Installer1!
password.
Figure 26 - Login session
For a complete list of all BLMon commands and its actions, please refer to section 5.9.1 in this manual.
4.1.2 File System
The file system in the HUe module is available through a secure connection, such as SFTP (SSH –
File Transfer Protocol). In the following examples, Filezilla software was used.
The file structure is available using Linux commands too.
The files constituting the Baseline Software Platform are installed in a non-volatile memory which is accessible by the user. The file system is structured as follows:
• /mnt/bf : Flash memory. This is a general-purpose memory. It stores ISaGRAF®, web server, and other application's files.
• /mnt/flash : Main memory. It stores user applications of Baseline Platform, for example, the software for the Device Drivers and their configuration files.
• /mnt/nflash : Auxiliary memory assembled on a NAND flash memory.
• /nvRam : Non-volatile SRAM memory. Memory used for data storage (i.e. Event log).This memory has a power fail protection by means of a supercapacitor, which is capable of retaining data for 8 hours.
• /mnt/sd1 : Memory for mass data storage in a SD memory card. The board needs to be inserted in the slot on the module’s side panel. The /mnt/sd1 folder is listed in the file system when the card is inserted in this slot. If the card is not inserted, then the folder will not be displayed in the file system.
• /mnt/usb1 : Memory for mass data storage in a pen drive. When the device is connected to a
USB port, the /mnt/usb1 folder is listed in the file system, and its content will be available. If there is no pen drive connected to this port, the folder is not displayed in the file system.
Pag 42
User Manual – HUe 10/01/2022
NOTICE
The host USB port can be used to update Baseline. Connect a pen drive containing new
Baseline file to be installed (for example, “Baseline_11.06.02.tar.gz”) and, then, click Reset on the equipment.
IMPORTANT : For the update to be successful, there should only be one file
Baseline_XX.XX.XX.tar.gz on the pen drive.
4.1.3 Network Configuration (IP / Router / Firewalls)
The configuration windows will depend on whether the configuration is for a redundant RTU or not; two or more tabs will be displayed in the network settings and environment variables screen.
If the RTU is not redundant, only the following tabs are visible: “ Network ” and “ Environment
Variables A ”. If the RTU is redundant, the corresponding configuration tabs for each CPU are visible, that is “ Network – CPU A ”, “ Network - CPU B ”, “ Environment Variables A ”, and
“ Environment Variables B ”, where A is the main CPU and B is the secondary CPU.
Network Interfaces
Figure 27 – Network interface settings
Routers
The network settings in the CPU can be read by clicking . Then, they can be modified and sent to the RTU by clicking ). All changes will be effective in the next reboot.
To add new network interfaces, remove one of the existing interfaces or change their respective parameters, use the , , and buttons respectively.
All the network interfaces integrated in the HUe can be set as DHCP client, so “ IP Address ” and
“ Subnet Mask ” fields are ignored. These data are automatically assigned by a DHCP server through the network.
NOTICE
HUe cannot be set as a DHCP server.
It is possible to configure a Parallel Redundancy Protocol (PRP) logical interface. This interface allows two physical ports to be used as a single port, that is, both ports will have the same MAC address and the same IP address.
NOTICE
When a PRP interface is defined, LAN ports are not available to be defined.
To define interfaces in different networks, a device that gives us access to different networks must be configured. Each device is configured in the “ Routers ” tab, in which each respective IP address is indicated. The figure below illustrates an example with two external subnets.
Pag 43
10/01/2022
Figure 28 – Using routers to configure subnets
User Manual – HUe
Define the following settings in Easergy Builder:
Figure 29 - Router settings
The Destination IP and Destination Mask fields are related to the IP addresses to be reached from the router. The Router IP is the device's IP address in the main network.
A default IP address and mask can be defined (i.e., 0.0.0.0 and 0.0.0.0) in order to access external networks. With these settings, any device connected to the router from the CPU could be reach.
Firewall
As with network interfaces, use the buttons on the right to add, remove or edit a router.
The network ports (MNT, LAN1, and LAN2) have the Firewall tab with the following parameters:
• Defining an allowlist : A pool of IP addresses which will access the CPU through this port.
Subnet mask must be 255.255.255.255.
• Defining a blocklist : A pool of IP addresses which CANNOT access the CPU through this port.
• Blocking a TCP or UDP port in the interface.
In this case, no device can connect to this network interface using the specified port.
Pag 44
User Manual – HUe
To manage the firewall rules for each port, select it from the list and click .
Figure 30 - Edit firewall rules
10/01/2022
The configuration of Firewalls in the system is not required. If the network interface does not have
Firewall settings, then no restrictions or capabilities are associated to use this feature.
To define an allowlist or blocklist, select the Type ("White list" or "Black list") and indicate the pool of addresses to be included ( IP Address / Subnet Mask ).
To block a port, select “Blocked port” in Type field and then, indicate the port number and type
(TCP or UDP).
The firewall rules are defined in the order below:
• Firstly, indicate the Forwarding state.
• Secondly, close the ports.
• Thirdly, include addresses in the blocklist.
• Fourthly, include addresses in the allowlist.
With this configuration, make sure that the information received from one port or one address will be accepted or rejected in accordance to this rule ordering. When a rule matches, the information is accepted or rejected. If no rule matches, then communication is enabled
It is also possible to forward a packet received through an Ethernet port with the IP Address belonging to another port's subnet. This is known as Packet Forwarding between Ethernet ports.
To use this feature, check the “ Forwarding ” box.
This feature is disabled by default for all ports.
4.1.4 Environment Variables
There are multiple environment variables defined in Baseline Software Platform which should be known in order to configure our system according to our requirements. These variables are defined in the “main_cfg.xml” in /mnt/flash file, which is managed and edited by means of Easergy Builder tool, as shown below.
The environment variables that must be defined with default values are:
• CONFIG_DIR :(Default value:/mnt/flash/cfgFiles/).This is the folder in which configuration files are stored. The CPU may have several projects stored in different associated configuration folders. The system will load the project whose configuration folder is associated with the value of this variable. If necessary, use an external storage device for these configuration folders (SD card o USB pen drive).
• BIN_DIR :(Default value:/mnt/bf/).Alternative path for application or binary files. The default directory in which application files are stored is /mnt/flash.If these files are not in this folder, the system will search in an alternative file path, as indicated in BIN_DIR.
Pag 45
10/01/2022 User Manual – HUe
• SLOT : In a redundant system, it is necessary to define the type of CPU. It will have the value A in the main CPU, the one that is initialized HOT by default, and B for the secondary CPU.
• WEB_IS_REMOTE :(It does not apply with HUe).
When a redundant HUe is configured, two tabs are available; the first is associated to the CPU A and the second is associated to CPU B. The figure below illustrates the variable definition in a redundant CPU:
Figure 31 - Variable definition in a redundant CPU
In this tab, the values can be changed and sent to the CPU by clicking ; new values will be applied in the next CPU initialization. Using button , the current values for these parameters in the RTU are read.
4.2 Cybersecurity
The HUe module implements a standard security policy and a default RBAC model (Role-based access control). This model is defined and managed by a special tool, i.e. CAE (EcoStruxure™
Cybersecurity Admin Expert). Based on this model, authorized users can create and manage other system's users. Moreover, the CPU includes a firewall.
The RBAC model implemented in the HUe module complies with the IEC 62351-8 standard.
4.2.1 CAE and RBAC
CAE is the tool designed to administer the security policy and define access restrictions for the system and/or communication interfaces.
A key aspect of this RBAC model is that every access is controlled by means of roles; each role is defined as a set of permissions and privileges. Permissions are assigned to users by means of roles; they can also inherit roles though a hierarchy.
The RBAC model provides the HUe module with:
• Secure connections for local and remote maintenance: HTTPS and SSH.
• Secure file transfer protocol: SFTP.
• Firewall capability.
Default RBAC model is detailed in further sections in this manual, including:
• List of objects.
• List of roles (users)
• Allocation of each role to each object's permission.
It is not necessary to modify the RBAC module supplied with the equipment, if it fulfils the system's requirements.
Pag 46
User Manual – HUe
Otherwise, use the CAE tool for:
• Creating a user database
10/01/2022
• Defining the roles
• Managing the RBAC model in each device centrally.
4.2.2 Users
During the engineering phase, CAE must be used to redefine or change the access restrictions for the system, including the access rights and responsibilities.
In the basic model supplied with HUe, the SecurityAdmin user is the only user with sufficient privileges to administer Saitel cybersecurity (please, see table below).It means that it is the only user which is able to administer and/or modify the passwords and roles being assigned to the users.
Table 10 – Default users
User Password Role
Viewer
Operator
Engineer
Installer
SecurityAdmin
SecAud
RbacMnt
Viewer1!
Operator1!
Engineer1!
Installer1!
Security1!
Secaud1!
Rbacmnt1!
VIEWER
OPERATOR
ENGINEER
INSTALLER
SECADM
SECAUD
RBACMNT
Once access levels are defined in the RBAC model, the HUe web server (webApp) can be used to add or remove users, modify passwords and assign one or several predefined functions to the users or modify them.
WARNING
When users are modified, if new RBAC configuration is uploaded from CAE, all changes here will be overwritten.
In webApp, use Maintenance tab in order to manage the users:
Figure 32 – Managing users in HUe
Pag 47
10/01/2022 User Manual – HUe
For further information, please refer to webApp User Manual.
NOTICE
For security reasons, these users’ password must be changed when the system is initialized.
4.2.3 Roles
Role-based-access-control (RBAC) is a control mechanism that defines the roles and privileges assigned to each role. These privileges are defined in accordance to some objects and actions that the user can act upon:
The table below illustrates the actions allowed for each object. Depending on the roles assigned to the logged-in user in the system, a specific action is allowed or not for an object:
Table 11 – Default roles
Object Description Actions Privilege
CONF_DB
CONF_SYS
FIRMWARE
Configuration files in coreDb.
Configuration files in the system.
Directory in which Baseline executables and libraries are contained (excluding the smAutoLoad file).
WEBSERVICE Web server.
SSH
SSH and SFTP connection to the operating system.
OSSHELL
BLMON
Operating system's console.
SYSLOG
Baseline Console.
System's Log File (Baseline).It includes the log file both for the system and SOE
(sequence of events), but it does not include the cybersecurity log.
Reading
Writing
Reading
Writing
Reading
Writing
Viewing
Access
Access
Access
Access
Reading
Writing
CONFDB_READ
CONFDB_WRITE
CONFSYS_READ
CONFSYS_WRITE
FIRMWARE_READ
FIRMWARE_WRITE
FIRMWARE_VIEW
WEBSERVICES_ACCESS
SSH_ACCESS
OSSHELL_ACCESS
BLSHELL_ACCESS
SYSLOG_READ
SYSLOG_WRITE
RBAC
RBAC_LOG
RESET
DATA
Configuration of the model associated to cybersecurity brick.
Log file for the cybersecurity brick.
System reset.
Access to the information about coreDb points.
Reading
Writing
Reading
Access
Reading
Writing
RBAC_READ
RBAC_WRITE
RBACLOG_READ
RESET_ACCESS
DATA_READ
DATA_WRITE
The table below illustrates the privileges associated each role defined in the RBAC model for the
HUe module. For users and roles management the SecurityAdmin user must be used to login in webApp.
Pag 48
User Manual – HUe
Table 12 – User’s privileges
10/01/2022
Roles
Privilege
CONF_DB
CONFDB_WRITE
CONFSYS_READ
CONFSYS_WRITE
FIRMWARE_VIEW
FIRMWARE_READ
FIRMWARE_WRITE
WEBSERVICES_ACCESS
SSH_ACCESS
OSSHELL_ACCESS
BLSHELL_ACCESS
SYSLOG_READ
SYSLOG_WRITE
RBAC_READ
RBAC_WRITE
RBACLOG_READ
RESET_ACCESS
DATA_READ
DATA_WRITE
√
√
√
√
√
√
√
√
√
√
√
√
√
√
√
√
√
√
√
√
√
√
√
√
√ √ √
√
√
√
√
√
√
√
√ √
√
√
√
√
√
√
√
√
√ √
√
√
√
√
4.2.4 Security Event Log
The HUe module contains an event log which is exclusively used for cybersecurity. This file registers the following data:
• Events associated with the connections to the CPU.
• Modifications made to the cybersecurity policy.
This file is only accessible by a user with the adequate rights to cybersecurity options. It can be viewed and downloaded from webApp, by clicking Diagnostics ïƒ Cybersecurity menu.
Pag 49
10/01/2022
Figure 33 – Cybersecurity log
User Manual – HUe
4.3 ITB Addressing (AAP)
Inside the ITB, each acquisition block or communication block must be identified with a number.
This number is assigned with Easergy Builder when configuring the local acquisition (please see
Once the local acquisition is defined with the configuration tool and it is transferred to the RTU, it is necessary to define these modules’ runtime addressing. To do so, execute a so-called Automatic
Addressing Procedure (AAP) that creates a table in the memory in which the acquisition blocks assembled physically on the ITB are associated to an address and a type. The physical components on the system must match the configuration in Easergy Builder.
NOTICE
For AAP execution, at least one configuration needs to be loaded in the RTU; it must match the configuration loaded in the modules that are physically installed on the ITB. For further information about how to define and load a configuration to the RTU by using Easergy Builder,
The Automatic Addressing Procedure (AAP) must be performed every time the ITB morphology changes, that is, every time a module is added, deleted or replaced.
The AAP procedure can be executed both automatically and manually.
Automatic Execution
For a forced execution of the AAP when the ITB is reset, switches 2 and 3 in the HUe must be set
to ON (please, see section 0).After resetting the HUe module, an AAP procedure is executed,
displaying the information about the modules that are installed and configured.
The figure shown below illustrates an example of the messages generated by the console when
AAP procedure is completed:
Pag 50
User Manual – HUe
Figure 34 - Welcome view
10/01/2022
In this case, there is an AB_AI module with the address 1 and an AB_DI module with the address
2.
If any of these acquisition blocks which was configured previously with Easergy Builder is not properly addressed (the “SUCCESSFUL!” message is not shown in the console), the module's
RUN led DOES NOT flash and the DIO led on HUe module remains lit.
Manual Execution
The user can force the module addressing at any time.
Log into the console with the Installer user and in BLMon prompt, execute the “ claqStartAAP ” command to route the acquisition AB and the “ MUX_startAAP ” command for the communication
AB.
NOTICE
To execute the AAP procedure, the switch 2 must be set to ON.
If switch 3 is also set to ON, the entire procedure is performed automatically. Otherwise, follow these steps:
• When executing the claqStartAAP or MUX_startAAP command, the following message appears. Upon the execution, the screen will display each module's information (type, assigned address, and serial number).
• The user will need to verify that all necessary modules are displayed with the text
“ SUCCESSFUL!
” next to them.
• To complete the procedure, the user will need to execute the claqTableAck command to confirm that the information is correct. In this case, the addressing information is stored permanently. If the information is not correct, execute the claqTableNack command in order to indicate that there was an addressing problem and that the information being displayed must be ignored
NOTICE
Only after executing the claqTableAck command, the information will be recorded permanently.
4.4 Local Acquisition
Local acquisition means how the system treats the HUe information received from field devices through acquisition blocks (AB).
This manual describes the configuration of the local acquisition signals in general terms, with no comprehensive information about the configuration of each AB. This chapter explains how information is processed by the CPU once it is received from each module.
For more detailed information about each AB, please refer to the corresponding user manual.
Pag 51
10/01/2022 User Manual – HUe
With respect to the ITB architecture, there are two types:
• Centralized Local Acquisition : All modules are installed in the same ITB, in which only one
HUe module is installed (or two if the configuration is redundant).The ITB may have more than one row of modules, but only the first row may have a CPU.
• Distributed Local Acquisition : There are several acquisition ITB's reporting information to a single ITB. In this case, the system is configured as if all AB modules are installed in the same physical ITB.
More information in the Saitel DR Platform user manual.
4.5 Treatment of Local Acquisition Signals
The claq Device is responsible for the treatment and configuration of the local acquisition signals in
Easergy Builder. This Device is created by default in any configuration of Saitel DR.
For further information about how configuring ITB and how signals are added automatically in coreDb, please refer to Easergy Builder User Manual.
4.5.1 General-Purpose Digital Inputs
The HUe module integrates 4 digital inputs in the lower part, which are configurable only as simple signals. These signals are useful to inform the operator about the controlled faults occurred.
The digital inputs 1 and 2 can be used for the following purpose:
• Digital 1 : It informs the HUe module about the polarization of the digital signals of the AB's installed in the ITB. When the signal is active, the polarization of all digital input is correct. If there are inactive, the HUe module will understand that a problem with the polarization has occurred. To use this signal for this purpose, the supervision signal POL_OK_ABDI must be defined.
• Digital 2 :Depending on its on/off state, the HUe module will understand that the ITB is operating in LOCAL or REMOTE respectively. In LOCAL mode, the command execution will be disabled. To use this signal, the supervision signal LOCALREMOTE must be defined in coreDb.
Clicking the graph on the HUe figure, it lights up in green and the 4 general-purpose digital Inputs available in the module are displayed.
For each signal, the following parameters should be defined:
• Type : Type of digital input. Only DI_ISIM (simple digital input) is available for these digital signals in the HUe module.
• Inverse : It indicates if the signal is inverted ( Y ) or not ( N ).
• TF (ms) :Filtering time to be used for the digital filtering. Expressed in milliseconds, it can range between 0 and 255.
• TM (ms*10) :Memory time to be considered for change memory. The indicated value is expressed with 10-ms intervals, and it can range between 0 and 255.
• NChat and TChat : They have no effect on these signals and cannot be configured.
For this type of signals, “Digital Filtering” and “Change Memory” should be considered. Both concepts are explained in Saitel DR Platform user manual.
Pag 52
User Manual – HUe
4.5.2 Field Signals
10/01/2022
HUe doesn’t have field signals but it is in charge of to do the treatment of the information received from AB modules. HUe execute the following function depending on the type of signal:
• Digital inputs o Digital filtering o Change memory o Settling Time o Anti-Chattering o Inversion o Edge Configuration for Counters
• Digital outputs o Pulse time o SBO Command Lock
• Analog Inputs o Input Range o Out-of-Range Detection o Digital Filtering o Scaling to Engineering Units o Cancellation of Values Close to Zero o Range Checking o Change Threshold
• Analog Outputs o Reset Value o Maintenance o Scaling to Field Values o Output range Configuration
Consult Saitel DR user manual for all information about how HUe executes these functions.
4.6 Working with HUe in Easergy Builder
NOTICE
To perform the operations described in this chapter, the user must be familiar with the Easergy
Builder tool. Otherwise, please, refer to the tool's user manual.
Pag 53
10/01/2022
4.6.1 Creating a RTU Based on HUe
User Manual – HUe
Press button or right-click on the RTU tree to add a new RTU by entering the required information in following fields:
Figure 35 – New RTU
• Name : RTU's name. The name cannot be longer than 64 characters and it cannot contain the following symbols:\, /, :, *, ?, “, <, > o |.The tree hierarchy will display a RTU identified with that name.
• Description : RTU's description. This field is optional and can be 128 characters long.
• AB_SER : Number of the communication modules installed in the RTU. These modules are not shown in Easergy Builder, even though its communication channels are available for use.
• Redundancy: This field must be checked when the RTU is controlled by two redundant CPU’s.
• Define default acquisition : If this box is checked, every time a configuration is created for this
RTU, a set of default acquisition modules will be associated. These selectable modules are specified below.
The previous parameters are assigned as default values in each Configuration created for this
RTU.
For example, if “Define default acquisition” box is checked, all the acquisition modules included in this RTU will also be included in its corresponding Configurations.
Figure 36 – Configuring the ITB
This default configuration can be hanged by clicking the button next to the ITB figure.
Build the ITB using the buttons on the upper part of the screen, having in account:
• The Addr field is the number associated to an acquisition block inside the ITB. This number must be unique for each AB and will be used to identify both the AB and its points. The user can change the associated address by selecting the module and using the buttons.
Selecting “ Auto Address ” box, when reordering the modules physically or when modifying the
ITB, all addresses are reassigned automatically. The address 1 is assigned to the closest AB to the HUe module. If the “ Automatic Address ” is unchecked, the modules retain the assigned address ignoring the changes made to the ITB.
• The Automatic Addressing Procedure ( AAP ) must be performed every time the ITB structure changes, that is, every time a module is added, deleted or replaced from the ITB. These procedure can be launched both manually, using the Console or Easergy Builder, or
automatically by using the switch 3 in the HUe module (more information in section 0in this
manual).
The RTU is ready for creating the different configurations. For more information about SOE, please, consult the SOE user manual.
Pag 54
User Manual – HUe
4.6.2 Configuring a Redundant RTU
For a redundant ITB, the following consideration must be considered:
10/01/2022
• Field Redundancy must be marked.
• IP CPU A and IP CPU B must be indicated. These IP addresses are used for communications with Easergy Builder.
• In tab Network – CPU A and Network – CPU B, IP addresses for ETH1 and ETH2 for CPU A and CPU B should be indicated.
• In tab Environment Variables A and Environment Variables B, the environment variables to be created in each CPU should be indicated. The environment variable SLOT is mandatory and must be different for each CPU. In CPU A, SLOT must be A and in CPU B, SLOT must be B.
More information about redundant configuration in the Easergy Builder User Manual.
4.6.3 Reading the Configuration from the HU
If the HU module was not built-in from the factory the configuration in the HU should be read and loaded in Easergy Builder. Then, the necessary modifications can be done and sent to the CPU.
NOTICE
It is recommend backing up the original configuration in the RTU in order to restore the CPU to its original state at any time. To back up the security configuration, select the RTU from the tree and generate an EBR file by clicking the button. This file will include all the settings for that
RTU. To save a copy of the configuration, select the specific configuration from the tree and click the same button. In this case, an EBC file is generated, which only includes the selected configuration.
To load the existing configuration in the HU, it’s necessary to follow next steps from the Easergy
Builder Workspace.
• In the RTU tree, the RTU to which the new configuration will be associated has to be selected.
If there is no configuration, a new one has to be loaded. The HU needs to have configured an
IP address so it’s possible to communicate with it.
• Once the “Read Configuration” button ( ) is pressed, the user would need to introduce a user and password.
• It’s necessary to choose the information to be loaded: “Network”, “Environment Variables” and/or “Configuration”.
In case that “Configuration” has been chosen, it will be necessary to choose a name for it. After that, the configuration would appear available in the RTU tree. If “Environment Variables” and
“Network” were selected, the RTU will take the values defined in the HU that is being read.
4.6.4 Create a New Configuration
To create a new configuration for the HUe, select the RTU from the tree and right-click it, or click the button.
Figure 37 – New configuration
Type the new configuration's name.
Pag 55
10/01/2022 User Manual – HUe
If “ Create defined RTU acquisition points ” box is checked, all local acquisition points will be included in coreDb for each acquisition blocks included in the default configuration associated to the RTU.
For example, if a HUe has an associated ITB that includes an AB_DI module, an AB_AI module, and another AB_DO module, after selecting the “Create acquisition points defined in the RTU” field when creating a new configuration, the following points will be created in coreDb:
• 16 digital inputs in Status table.
• 8 analog inputs in Analog table.
• 8 digital outputs in Command table.
• The supervision points of each acquisition block.
When the operation completes, the new configuration will be listed in the RTU trees. Double-click on it and the Easergy Builder tool enters Configuration mode. Now the new configuration can be edited.
Figure 38 - Configuration mode
By right-clicking on the configuration name, a contextual menu is displayed:
Figure 39 – Contextual menu for Configuration
This menu allows:
• Add, remove or modify a configuration.
• Create a template with the information associated to this configuration.
• Change the name or description of the Device (description field allows 128 characters maximum).
Pag 56
User Manual – HUe
4.6.5 Editing the Configuration
10/01/2022
The figure below illustrates the Easergy Builder environment when editing for a HUe CPU:
Figure 40 – Editing a configuration
The user needs to be familiar with the use of Easergy Builder, since this user manual only refers to certain aspects directly affecting the configuration of the HUe module.
4.6.6 Communications
The default configuration does not include any communication Device, since this functionality depends on how the RTU will be used in the system. Communication Devices available for the
HUe module are:
• Controlling and controlled station IEC101
• Controlling and controlled station IEC104
• Master station and outstation DNP 3.0.
• Controlling station IEC103.
• Client and server Modbus.
• IEC61850. Client (Editions 1 and 2) and server (Edition 2)
• Client SPA-bus (only available for 11.06.16 and later).
Each Device has a dedicated user manual which detail all configuration parameters.
4.6.7 Configuring HUe Communication Channels
The Easergy Builder Manual describes general operations that are necessary to know to create and edit the communication channels available in the CPU and communications modules.
In Configuration mode, select Channels tab in order to access channel management window.
Figure 41 - Module management window
Pag 57
10/01/2022
Figure 42 – Channel configuration window
User Manual – HUe
Configuration channels are shown in tab “Channels”.
Once created and loaded in the CPU, these channels’ parameters can be read and modify through webApp.
NOTICE
The CON port cannot be used for communications, and that is why it is not necessary to include it in the channel list.
The communication ports available in HUe are:
• Ethernet Ports. Each port use for communications must be defined as a TCP or UDP channel.
• Serial ports (ASYNC): o COM1 (GPS input). o COM2 o RS-485
Apart from those, depending on the number of AB_SER modules in the ITB, the serial channels for these modules are also listed:AB_SERx-COM1..AB_SERx-COM4, being x the AB_SER module number.
NOTICE
It RTS control is AUTO for a specific channel:
• In COM1 and COM2, the hardware will control RTS and CTS signals. CAUTION! If the CTS signal is not received, then there is no transmission.
• For RS-485, the control for the RTS signal and the changes between the transmission and reception modes would be controlled by the hardware IT IS HIGHLY RECOMMENDED!!
Please refer to the Easergy Builder manual to obtain further details about how to create and define parameters for communication channels.
4.6.8 Configuring HUe Link Configuration
Some Devices support double channel management. This functionality can be different depending on the protocol in use. A link is the association of two channels; can also be considered as a double channel.
To configure a channel, in the window displayed above, select “Link” and indicate the two channels that will be associated to create the link; the operation mode and the link test time can be also defined:
Pag 58
User Manual – HUe
Figure 43 – Link configuration window
10/01/2022
4.6.9 Synchronization
The factory configuration does not include a defined Synchronization Device. The configuration source is defined in Easergy Builder. webApp only allows changing the configuration once it has been previously defined with Easergy Builder.
For HUe, two synchronization channels can be defined: a primary channel and a secondary channel, which will be used when the primary channel is not available.
Figure 44 - Synchronization configuration
The synchronization sources to be used with HUe are:
• PROTOCOL : Time is received through a user-specific protocol. Most telecontrol protocols enable secondary devices to be synchronized.
• SNTP : The remote unit will operate as a SNTP client; therefore, two parameters should be indicated: the SNTP server's IP address and the synchronization period through that server.
• IRIG : The time received from the IRIG device is used to set the system’s clock and RTC. The configurable formats are: IRIG-B002, IRIG-B003, IRIG-B006, and IRIG-B007.
NOTICE
If the HUe is configured as IRIG-B server, an AB_SER module witn external polarization
(M56720000yZZ) must be included in the firt row of the ITB. The IRIG-B signal is sent to the client devices through COM ports of this AB_SER.
• GPS : GPS35 and GPS16 of Garmin have been validated.
• PTP : As indicated in the IEEE-1588 standard, a primary device PTP will synchronize the accessible secondary PTP devices through one or multiple Ethernet interfaces. This functionality for Hue is available in version 11.06.08 and later.
• Console , using the commands: o thmShow : It displays the states of the synchronization devices and the information about current time and date. o thmConsoleSetTime “YY:MM:DD:HH:NN:SS” :It configures the date and time manually.
Pag 59
10/01/2022 User Manual – HUe
Moreover, the HUe module can be configured as a Simple Network Time Protocol (SNTP) server, as a primary PTP device or as an IRIG-B server.
The synchronization module allows the time zone and summer/winter (day light saving) calendars to be configured.
Figure 45 - Time configuration
For further details about synchronization configuration, please refer to the Easergy Builder user manual.
4.6.9.1 Configuring PTP in HUe
NOTICE
UDP port is unavailable when PTP port is configured.
PTP Client (Precise Time Protocol)
According to IEEE-1588 terminology, when the RTU is synchronized by an external PTP device, the RTU works in “Ordinary Clock" mode (OC). If the RTU is a PTP server, then it works in
“Boundary clock” mode (BC).
NOTICE
The RTU can be configured a PTP client or a PTP server, but not both at the same time.
The following information is required:
Figure 46 – Configuring synchronization with a PTP device
• Port: Select the physical port for synchronization with the PTP device.
• domainNumber: Value of the "domain" attribute of the local clock. The default value is 0.
• Announce messages period: Average time interval between "Announce messages". Value in seconds, as a base two logarithm. The default value is 1, that is, 2 seconds.
Pag 60
User Manual – HUe 10/01/2022
• Max. Announce messages lost : Maximum number of lost messages before considering a time-out in the reception. The default value is 3.
• Delay req period : Minimum allowed time interval between "Delay_Req" messages. It is specified, in seconds, as a base two logarithm. The default value is 0, that is, 1 second.
• Sync period : Average time interval between synchronization messages. A shorter interval can improve the accuracy of the local clock. It is specified, in seconds, as a base two logarithm.
The default value is 0, that is, 1 second.
• Pdelay req period : Minimum allowed time interval between "Pdelay_Req" messages. It is specified, in seconds, as a base two logarithm. The default value is 0, that is, 1 second.
• delay mode : Delay determination mechanism. The possible values are: o P2P. Peer-to-Peer. (available in version 11.06.08 and later).
• net transport : network transport mechanism. Possible values are: o IEEE_802_3. IEEE 802.3 network transport (available in version 11.06.08 and later).
• vlan tagging : It selects whether the PTP frames should include their VLAN tagging (IEEE
802.1Q). Only can be select when “Net transport” is IEEE 802.3.
• ID : ID of the vlan. From 0 to 4095. It is only available if vlan_tagging is selected.
• Priority : Priority of the vlan. From o to 7.
PTP Server
Select tabs Synchronization server - PTP and configure the following parameters:
Figure 47 – Configuring the RTU as PTP server
The information for each field is detailed in the previous paragraph. Other fields are available for
PTP Servers:
• Clock Class : Denotes the traceability of the time or frequency distributed by the grandmaster clock. Default value is 127.
• Priority 1 : A configurable designation that a clock belongs to an ordered set of clocks from which a primary device is selected, through the “Best Master Clock algorithm”. Values can range from 0 to 255 (lower values take preference). Default value is 128.
• Priority 2 : A user configurable designation that provides finer grained ordering among otherwise equivalent clocks. Values can range from 0 to 255 (lower values take preference).
Default value is 128.
NOTICE
An RTU cannot be OC (Ordinary clock) and BC at the same time. If it is synchronized by a PTP device, it can't be configured as PTP server.
Pag 61
10/01/2022
4.6.10 Using Formulas
User Manual – HUe coreDb signals can be associated to a series of functions such as: mathematic operations, logical operations or event triggering. All these functions are implemented and controlled by the Formula
Device available in Easergy Builder.
The Easergy Builder user manual includes all the details about the use of this Device, as well as available functions.
4.6.11 PLC Configuration
The HUe module integrates the use of ISaGRAF®, that is, a logic programming tool working under the IEC 61131-3 environment to develop PLC programs.
ISaGRAF® is a third party tool consisting of two parts:
• Runtime: Control and execution environment for logic programs. The license is included as part of the Baseline Software Platform installed in the HUe module.
• Workbench: Development environment. It is installed in a PC, and needs to be purchased for the project, since it requires an additional license that is not included as part of our software platform.
The logic programming languages include:
• SFC : Sequential Function Chart
• FBD : Function Block Diagram
• LD : Ladder Diagram
• ST : Structured Text
• IL : Instruction List
To let ISaGRAF® interact with coreDb, a Device of this type needs to be defined in Easergy
Builder.
For detailed information about the use of ISaGRAF® inside Saitel, please refer to the Device user manual.
4.6.12 Supervision
The Supervision Device is a default Device in Easergy Builder. The Device is used to monitor the status of CPU's components and generates information about other components in the RTU.
Double click the “Supervision” Device in the tree to see a complete list of all the concepts available for monitorization in this type of CPU:
Figure 48 – Supervision signals
Pag 62
User Manual – HUe 10/01/2022
In this window, check or uncheck the available supervision points to be used for that RTU.
NOTICE
It is highly recommend configuring the Supervision; besides, it is essential in redundant configurations. The CPU itself cannot be arbitrated autonomously with the other CPU in redundant systems, so there must be some supervision in charge of this Device.
For redundant configurations, most of the supervision points are also available with “_A” and “_B” suffixes in order to provide CPU-related information. For example, the points PS1_V, PS1_V_A, and PS1_V_B are available for power supply voltage. Regardless which CPU is in online mode, the information about both CPUs is shown.
If points are not available with _A and _B suffixes in a redundant configuration, it means that only values for the online CPU are available, for example, DOING_WELL.
The information generated by the supervision is complemented with control and diagnostic information that is generated by each Device.
The table below shows the supervision points available for HUe:
Table 13 – Supervision points
Point
COLD_RST_CNT
COM_CTS
CPU_USAGE
DAY
DB_UPDATE
DOING_WELL
FAIL_CONF
FAIL_PLC
FAIL_RTU
FAIL_SER1 ...FAIL_SER4 Status
FAIL_SYNC1
Table
Status
Analog
Analog
Status
Status
Status
Status
Status
Status
Type
Source
Source
Source
Source
Destination
Source
Source
Source
Source
Source
Pag 63
Description
Cold start-up counter.
Reserved use. Do not configure.
Level of CPU used.
Current day.
1 ïƒ The system is redundant and it is configured as “Hot data”. The data has been correctly updated.
1 ïƒ The source to which the point is associated is operating properly. Value “1” must be set as initial value. This signal is generally set with an ISaGRAF® point in order to control that PLC is operating properly.
The value “1” indicates a problem in the configuration.
It is used with ISaGRAF®.
1 ïƒ There is not a program in the PLC or the program has been stopped.
1 ïƒ The CPU state is anomalous.0 ïƒ There are no configuration errors (FAIL_CONF = 0); the value of DOING_WELL = 1 and all the tasks controlled by the watchdog are working properly. When the value for FAIL_RTU is “0”, pulses for RTS and DTR are generated. If a task doesn’t reply to the watchdog, the value for FAIL_RTU will change to 1.
1 ïƒ There is a problem in the corresponding module (FAIL_SER1 indicates a problem in module 1, and so on).The number of points to be configured will depend on the number of communication modules included in the configuration.
1 ïƒ Synchronization problem in the main synchronization source.
10/01/2022
Point
FAIL_SYNC2
FAIL_SYNCDESV
FAIL_SYNCHW
HOUR
LAQ_FAIL
LINK:LAN1
LINK:LAN2
LINK:MNT
LOCALREMOTE
LOCALREMOTE:I
LOCALREMOTE:W
MEM_USAGE
MINUTE
MONTH
NODE_A
NODE_B
ONLINE
PLC_WARNING
POL_OK_ABDI
Status
Status
Status
Analog
Analog
Analog
Status
Status
Status
Status
Table
Status
Status
Status
Analog
Status
Status
Status
Status
Type
Source
Source
Source
Source
Source
Source
Source
Source
Status
Source
Source
Source
Source
Source
Source
Source
Source
Source
Source
Source
User Manual – HUe
Description
1 ïƒ Synchronization problem in the secondary synchronization source.
1 ïƒ There is a delay of at least 3 seconds.
1 ïƒ Hardware problem in the synchronization source.
Current hour.
1 ïƒ Problem detected in the local acquisition.
At least one acquisition module is out of service or with error.
Link status in LAN1 port.
Link status in LAN2 port.
Link status in MNT port.
Value of Digital signal 2 in HUe.
1 ïƒ The system is in local mode (no commands can be executed on the digital signals).
0 ïƒ The system is operating in remote mode.
This is the usual state of the RTU.
(*) See note at the end of the table.
INVERTED value of Digital signal 2 in HUe.
0 ïƒ The system is in local mode (no commands can be executed on the digital signals).
1 ïƒ The system is operating in remote mode.
This is the usual state of the RTU.
(*) See note at the end of the table.
This signal will show the state of the system put by HMI.
RAM memory usage in %.
Current minute.
Current month.
1 ïƒ CPU configured as A (Main).
1 ïƒ CPU configured as B (Secondary).
In a redundant system, 1 ïƒ CPU is HOT.
It is used with ISaGRAF®.
1 ïƒ There are ISaGRAF® points that are not mapped in coreDb.
1 ïƒ The polarization for digital inputs is correct.
0 ïƒ The polarization is not correct or the point has not been defined in coreDb, If the point is not defined in coreDb, then the polarization of digital inputs is not supervised.
Pag 64
User Manual – HUe
Point
RED_I_STATE
RED_IT_FAIL
Table
Status
Status
Status
Status
Type
Source
Source
Source
Source
10/01/2022
Description
LOCAL state of RTU redundancy, that is, the
CPU on which the Supervision controller is operating.
1 ïƒ The local CPU status is HOT or
STANDBY.
0 ïƒ The local CPU status is in FAIL status.
GENERAL status of the redundancy in the
RTU.
1 ïƒ The redundant CPU status is in FAIL status.
0 ïƒ The redundant CPU status is HOT or
STANDBY.
1 ïƒ The main line of the RCAP protocol does not work properly.
1 ïƒ The secondary line of the RCAP protocol does not work properly.
RED_VIA1_FAIL
RED_VIA2_FAIL
RESET_RTU
SECOND
WARN_BAT
WDAY
Analog
Status
Analog
Source
Source
Source
Current second.
1 ïƒ The backup supercapacitor is disconnected.
Day of the week, considering; 0-Sunday, 1-
Monday, .., 6:Saturday)
Current year. YEAR Analog Source
WARNING
(*) Please do not define LOCALREMOTE and LOCALREMOTE:I simultaneously in coreDb.
Otherwise, the behavior would be unpredictable.
4.6.13 Redundancy
As it was explained previously, the system has two redundant CPU’s, there are certain differences in the configuration of, for example, environment variables and supervision points. Moreover, the configuration also must indicate how redundancy will be implemented both in physical terms
(control mechanism) and functional terms (data redundancy mode).
The environment variables A and environment variables B table must be correctly configured in dbRED tab (coreDb) to indicate which CPU will act as primary and which as redundancy
NOTICE
The dbRED section is only available in Easergy Builder for redundant CPUs.
Control Mechanism
For HUe there is redundancy only through the RCAP protocol (Redundancy Control Asynchronous
Protocol). It consists of a redundant channel between the two HUe modules that is switched when required by means of a Schneider Electric proprietary protocol.
To implement this control mechanism, up to two different channels can be used, which are used redundantly to obtain a fault-tolerant redundancy control:
Pag 65
10/01/2022 User Manual – HUe
• Through network ports, IP addresses for CPU A and CPU B should be defined.
• Through a serial channel. The serial port to be used in both CPUs should be defined.
Mode
4.6.13.1
There are two different modes to implement redundancy:
• Cold redundancy : The databases in both CPU's are NOT synchronized. When switching, the other CPU will initialize with its own database using default values.
• Hot redundancy : A high-speed communication channel (Ethernet) must be defined between the two CPU’s to keep the database updated in the backup CPU. When switching, the redundant CPU will initialize with updated values.
NOTICE
When using the “Hot redundancy” mode, the names of the points in both databases must be identical, that is, it is very important to use the SAME Easergy Builder configuration in both
CPU’s.
The backup CPU's database is updated when exceptions are thrown (i.e. only the modified points are updated), except for the initialization after which the entire database is updated. The
DB_UPDATE supervision point allows us to monitor the process.
Additional IP’s
A list of IP addresses can be defined related to the HOT CPU. These addresses are dynamically associated, so that in redundant systems they can always communicate with the online CPU at the time.
NOTICE
When a static IP address and a virtual address is defined for the same device in the same subnet, a warning console message will be displayed to inform about an anomalous situation
(sup_redAddIPs: dev xxx ip x.x.x.x subnetMask xxxxxxxx).
The message is an operating system warning, even though it will not cause a malfunction.
PRP (Parallel Redundancy Protocol), HSR (Highly-available Seamless Redundancy), BOND
(Bonding) and RSTP (Rapid Spanning Tree Protocol) protocols allow using two physical ports as a unique logical port, with a same MAC address and IP.
NOTICE
If PRP, HSR, BOND or RSTP interfaces are defined, the associated LAN ports will be not available to define.
HUe can use PRP, HSR, BOND and RSTP protocols as detailed in the following sections.
Configuring PRP
This protocol is based on the use of two independent networks at all levels, LAN A and LAN B, and sending the same message at the same time on both networks.
The device must send through each of its two network interfaces, a frame with the same MAC and the same IP through a different port in both networks.
In this case two switches are required, one for network A and one for network B. In HUe the network A (LAN(A)) for PRP is always the interfaces labelled as LAN2.
Click on “add new interfaces” and select PRP.
Pag 66
User Manual – HUe
Figure 49 – Configuring PRP
10/01/2022
4.6.13.2 Configuring HSR
HSR is a redundancy protocol, like PRP. It is based on a redundancy in the device, a Layer 3 network frame, is converted into 2 identical HSR frames and sent by the 2 ports of the device to a ring topology network, in opposite directions. The devices linked in this ring network are called
DANH (Double Attached Node implementing HSR).
One difference from PRP is that there is only one LAN with a mandatory ring topology in the HSR protocol.
Click on “add new interfaces” and select HSR.
Figure 50 – Configuring HSR
4.6.13.3 Configuring RSTP
This is a second OSI layer network protocol that ensures a loop-free topology for Ethernet networks. RSTP (IEEE 802.1w) is an evolution of STP (Spanning Tree Protocol; IEEE 802.1D).
This protocol monitoring each link state. If an active link goes down, RSTP active the redundant links and reconfigure the network topology.
Click on “add new interfaces” and select RSTP.
Pag 67
10/01/2022
Figure 51 - Configuring RSTP
User Manual – HUe
4.6.13.4 Configuring BOND1
This is a method of combining (joining) two or more network interfaces together into a single interface. It will increase the network throughput, bandwidth and will give redundancy.
If one interface is down or unplugged, the other one will keep the network traffic up and alive.
Click on “add new interfaces” and select BOND1.
Figure 52 – Configuring BOND1
4.6.14 Local Acquisition Configuration
As mentioned before, the local acquisition Device for Saitel DR is named “ claq ” and it is created by default for each Saitel DR configuration.
Figure 53 - Configuring local acquisition for Saitel DR
For HUe the following types of modules can be configured:
Pag 68
User Manual – HUe
Figure 54 - Available Saitel DR modules in Easergy Builder
10/01/2022
Back in the local acquisition configuration, several options are possible:
•
•
•
button, to add a new module.
button, to remove a module.
buttons, to change the address of the modules.
• button, to create in coreDb acquisition and diagnostics points for all included modules.
More information in section claq in the manual of the different acquisition modules.
4.6.15 General Purpose Digital Inputs
HUe has 4 digital inputs located in the lower left, only configurable as single inputs. These signals are useful to inform the operator about a general problem in the system. All signals can be configured for a general-purpose, but Digital 1 and 2 can be used with the following purpose too:
• Digital 1 : This signal provides the HU module with information about the digital inputs’ polarization status of the ABs installed in the ITB. When the signal is active (1), the polarization of all digital signals is correct. If the signal is disabled (0), the HU will understand that there is a problem with polarization.
In order for the CPU to interpret the value of Digital 1 in this way, the supervision signal
POL_OK_ABDI must be included in coreDb.
• Digital 2 : Depending on this signal is active or not, the CPU will understand that the ITB is in
LOCAL mode (signal is 1) or in REMOTE mode (signal is 0). In order for the CPU to interpret the value of Digital 2 in this way, the supervision signal LOCALREMOTE or LOCALREMOTE:I must be included in coreDb.
WARNING
(*) Please do not define LOCALREMOTE and LOCALREMOTE:I simultaneously in coreDb.
Otherwise, the behavior would be unpredictable.
If LOCALREMOTE is defined, when Digital 2 is 1 ïƒ LOCALREMOTE is 1, the ITB is in LOCAL mode, so the commands are not enabled in the digital output modules. If the Digital 2 signal is 0 ïƒ
LOCALREMOTE is 0, the ITB is in REMOTE mode, which will be the normal operating state.
If LOCALREMOTE:i point is defined, this signal inverts the value of Digital 2.
The REMOTE mode is the default mode when neither LOCALREMOTE nor LOCALREMOTE:I are included in coreDb.
To configure these signals, click on claq Device, and select the module HUe on the ITB. The HUe module lights up in green and the 4 general-purpose digital Inputs available in the module are displayed.
Pag 69
10/01/2022
Figure 55 - Configure signals Easergy Builder
User Manual – HUe
For each signal, the following parameters must be defined:
• Type : Type of digital input. Only DI_ISIM (simple digital input) is available for the four digital inputs of the HUe module.
• Invert : It indicates if the signal is inverted ( Y ) or not ( N ).
• TF (ms) : Filtering time to be used for the digital filtering. Expressed in milliseconds, it can range between 0 and 255.
• TM (ms*10) : Memory time to be considered for change memory. The indicated value is expressed with 10-ms intervals, and it can range between 0 and 255.
• NChat and TChat : They have no effect on these signals and cannot be configured.
For this type of signals, “Digital Filtering” and “Change Memory” must be configured. Both concepts are explained in further details below.
4.6.16 Transferring the Configuration to the RTU
To transfer the configuration from Easergy Builder (in the PC) to the CPU, if configuration mode is active, select button . If Workspace mode is active select button . Then,
Easergy Builder requests to confirm the project save operation. Press “ Yes ” and the log window will display the information about the operation progress.
Finally, reset the RTU and, if no problem occurs, the console will display the information about the initialization progress of operating system and then the application. If everything is correct, the message “CONF OK” should be shown in the console.
Pag 70
5 Advanced Operations
Public
10/01/2022 User Manual – HUe
Content
M ONITORING AND S YNCHRONIZATION C OMMANDS .......................................... 83
Pag 72
User Manual – HUe
5.1 Baseline Update
10/01/2022
There are several ways to update the baseline installed in the HUe; using a SFTP client (for example, Filezilla), using webApp (HUe web-based tool), or using a USB pen drive connected to the USB Host port.
5.1.1 Required Material
The following elements are required:
• An Ethernet cable connecting the PC with the MNT port in HUe. This wired connection is only necessary when transferring the update file through SFTP or webApp. If using a pen drive, it would not be necessary.
• A file with the new Baseline to be installed. It will be a compressed file with a name like
“Baseline_11.06.02.tar.gz”.
The file's name containing the image must have a specific syntax:
• It must start with "Baseline_", (no case sensitivity).
• It must finish with the ".tar.gz" extension
The following names are valid, for example: BaseLine_11.04.00.tar.gz, Baseline_10.tar.gz, and
BASELINE_9.3.0.tar.gz.
5.1.2 Using SFTP
An FTP client (supporting SFTP) must be available in the PC, and the ethernet cable must be connected to the MNT port. Both the CPU and our PC must be in the same subnet.
Check the connection using a ping command in a command prompt:
Once the connection is verified, open the FTP client software and establish connection with the
CPU using the SFTP protocol and Installer (user) and Installer1! ( password).
When connection is established, move to the folder /mnt/flash and transfer the Baseline file from the PC.
Pag 73
10/01/2022
Figure 56 – SFTP connection
User Manual – HUe
When loading is completed, press the Reset button on the CPU. If the console is available, the message on it will show how the installation is in progress.
Once installed, the compressed file including the Baseline image is deleted.
Finally, reboot the system and Baseline is updated.
5.1.3 Using an USB Device
To upgrade the system using the USB port, copy the file to the root folder in the USB device, connect it to the CPU and reboot the HUe.
During Linux initialization, the USB drive is installed in /mnt/usb1 and, if the file with a Baseline image is detected, the implementation is executed automatically.
There is a slight difference after the installation with respect to the previous section:
• To allow using the same USB device to deploy a baseline in different CPUs, the target image is not deleted from the /mnt/usb1 device.
• Since the /mnt/usb1 image is not deleted, the system does not reboot. Thus, any "autoinstallation" of the same image is prevented. After the file is automatic copied from the
/mnt/usb1 device, it is recommended to remove the USB device and reboot the system manually.
The priority order for the update procedure is:
• File in USB drive
• File in /mnt/bf
• File in /mnt/flash
Pag 74
User Manual – HUe
5.1.4 Using webApp
10/01/2022
To use a web browser to upgrade the system, such as Chrome, connect the PC to the MNT port using the correct IP address.
NOTICE
Considering that the connection must be secure, the protocol HTTPS must be indicated in the address bar, i.e. "https://192.168.0.254".
Figure 57 – webApp login
Log in with the “Installer” user and the webApp main screen appears:
Figure 58 - webApp main screen
In the lower area, identified with factory information, there is information about the current Baseline version.
To install a new baseline, in the main menu, click: Maintenance ïƒ Software . Press button “ Install new software ”. The following information is shown:
Figure 59 – Firmware upgrade using webApp
Pag 75
10/01/2022 User Manual – HUe
• Drag and drop the file in the designated area or search for it using the “ Select file ” button (Step
1).
• Click the “ Load ” button (Step 2).
• Next, confirm that the software file is correct (Step 3).
• Click the “ Install new firmware ”, and the software file will be sent to the CPU to install the new firmware (Step 4).
• Then, reboot the CPU (Step 5).
• Finally, the user will need to log in again and the CPU will be ready with the new software version.
5.2 AB Software Update
All
Module
Position
AB_DI
AB_AI
AB_DO
AB_AO
AB_DIDO
Apart from the software installed in the HUe, both the acquisition blocks and the communication blocks have a software to be updated.
To update the software on the ITB modules, the required elements are:
• A console connection with HUe.
•
Information about the correct addressing in all ITB modules (please, see section 4.3 ).
• The appropriate software files for each type of module.
Once Baseline is installed in the HUe module, the /mnt/flash directory will include all the files required to update any of the modules in the ITB. If other software version is required, copy the appropriate file to the folder /mnt/flash using SFTP.
NOTICE
Only Installer can be used to execute update commands in the console.
The table below shows the file to be used for each type of module and the command to be executed by the operator in the console.
Table 14 – Software update file for ITB modules
*.bin
File
<Module type>.bin
AB_DI.bin
AB_AI.bin
AB_DO.bin
AB_AO.bin
AB_DIDO.bin
Command claqUpgrade all claqUpgrade <position> claqUpgrade all AB_DI claqUpgrade all AB_AI claqUpgrade all AB_DO claqUpgrade all AB_AO claqUpgrade all AB_DIDO
Description
It updates all the acquisition AB addressed in the ITB. The adequate file will be sent for each AB module.
It updates the acquisition AB with the <position> address, using the adequate file for its type.
It updates all the AB_DI modules installed in the ITB.
It updates all the AB_AI modules installed in the ITB.
It updates all the AB_DO modules installed in the ITB.
It updates all the AB_AO modules installed in the ITB.
It updates all the AB_DIDO modules installed in the ITB.
Pag 76
User Manual – HUe
Module
AB_AC
File abaca.t00
AB_AC/LPVT
AB_AC_A.bin abaca2.t00
AB_MIO
AB_SER
AB_SER
AB_AC2.bin
AB_MIO.bin
AB_SER.bin
AB_SER.bin
Command claqDSPUpgrade all claqUpgrade all AB_AC_A claqDSPUpgrade all claqUpgrade all AB_AC2 claqUpgrade all AB_MIO
MUX_upgrade “all”
MUX_upgrade “<position>”
10/01/2022
Description
It updates the DSP in all the AB_AC modules installed in the ITB.
It updates the firmware in all the
AB_AC modules installed in the ITB.
It updates the DSP in all the
AB_AC/LPVT modules installed in the ITB.
It updates the firmware in all the
AB_AC/LPVT modules installed in the ITB.
It updates all the AB_MIO modules installed in the ITB.
It updates the firmware in all the
AB_SER modules installed in the
ITB.
It updates the AB_SER module with the <position> address in the ITB.
5.3 Operating System Update (Linux)
NOTICE
Only users with advanced knowledge about the equipment should perform the tasks described in this section.
The operating system update is executed, if required, during Baseline installation, but only if the currently installed version is older than the version to be uploaded.
Finally, reboot the system and the baseline is updated.
NOTICE
To downgrade the system (install a previous version of the baseline, including the operating system), the name of the file used must content the suffix “_KFD.tar.gz”.
5.4 Console Commands
The HUe operating system offers a high-priority command console to help with certain monitoring and diagnostic tasks.
The connection to this console from the PC is established through the CON port. The section 4.1.1
in this manual describes how access the command console.
Have into account:
• The use of the command console must be restricted only to expert operators in the system.
• The command execution in the console must return a “0” character when outputted. If it returns other values, then there has been a problem in the execution. It is usually caused by parameters with the wrong format.
Pag 77
10/01/2022 User Manual – HUe
• When executing a command for any controller, it must be saved into the memory to solve this problem, that is, the controller must be included in the configuration loaded in the CPU from
Easergy Builder.
NOTICE
Only the Device controllers included in the current configuration will be loaded into the memory.
Then, the commands available in the console for the Installer user are displayed below, using the following convention:
• (No parameters) :The command must be executed directly, with no additional parameter.
• <XX> :Required parameter. It must be replaced with the XX value. The symbols <> MUST NOT be included.
• [YY] :Optional argument. If using the argument, it must be replaced with the YY value. The characters [] MUST NOT be included.
5.4.1 BLMon
When accessing the console with the Installer user (recommended), the BLMon menu is directly shown. The commands in this menu are executed on the operating system's prompt. Most commands shown below are NOT available for the rest of the users.
The BLMon menu includes the following commands:
Table 15 - List of BLMon commands
Command a
Use
It displays the list of the commands available to obtain information about the local acquisition. This chapter includes more information about these commands.
Pag 78
User Manual – HUe
Command b
Use
It displays the version of the Baseline software being executed.
10/01/2022 e c f h o s m l
This command is similar to “ baselineShowVer ”.
It starts the monitoring of the system events.
All the events occurred will be shown in the console.
It starts the monitoring of a communication channel.
It displays the channels configured selectable by the user. If “Enter” is pressed instead of a channel number, the command is aborted.
This command is similar to “ chanSniffOn ”.
It finishes the monitoring of the communication links.
This command is similar to “ chlnSniffOff ”.
Using this command, detailed information about the system's commands is shown.
Apart from BLMon commands, the user has other commands to be executed in the prompt.
Type the desired “ FUNCTION_HELP :” command to view the following information.
Use “ a ” to see a list of the available commands .
It displays the BLMon menu.
It starts the monitoring of a communication link.
It is similar to the “c” command but for a link (association between two communication channels).
This command is similar to “ chlnSniffOn ”.
It finishes the supervision of all the channels being monitored.
This command is similar to “ chanSniffOff ”.
It displays the coreDb and configuration status.
Pag 79
10/01/2022
Command t
User Manual – HUe
Use
It displays the information about the configuration and the current synchronization status. u v p
This command is similar to “ thmShow ”.
It finishes the monitoring of the system events.
It displays the current version of the operating system.
This command is similar to “ version ”.
It displays the processes being executed.
This command is similar to the operating system’s command, “ ps -eTcl ”.
Pag 80
User Manual – HUe
Command i
10/01/2022
Use
It displays the configuration of all network interfaces.
NOTICE!! Please note that the physical name shown for each interface has the following relationship with the Ethernet ports’ names:
Port's name (Front label) Physical name (Linux)
MNT eth2
LAN1 eth0
LAN2 eth1 coreDbShowVer coreDbShowState
This command is similar to “ ifconfig ” and “ route ”.
5.4.2 General Commands
Table 16 - List of general commands
Command coreDbShowEvents
Parameters / Description
(No parameters)
It starts the monitoring of the system events.
It is similar to the e of BLMon.
(No parameters)
It shows the version of coreDb for the Baseline in the CPU.
(No parameters)
It displays the coreDb and configuration status.
It is similar to the s of BLMon.
Pag 81
10/01/2022
Command Parameters / Description
User Manual – HUe coreDbUnShowEvents (No parameters)
It finishes the monitoring of the system events.
It is similar to the u of BLMon. baselineShowVer (No parameters)
It displays the version of the controllers loaded into the application. Please note that if a controller is not used in the current configuration, it will not be loaded into the memory.
5.4.3 Communications
Table 17 - List of communication commands
Command chanShowVer
Parameters / Description
(No parameters)
It displays information about the channel controller. chanSniffOff dnpeShowVer
(No parameters)
It deactivates the transparent mode for ALL channels.
(No parameters)
It displays information about the controller of the DNP (outstation) protocol. dnpmShowVer chlnSniffOff chlnSniffOn
(No parameters)
It displays information about the controller of the DNP (master station) protocol.
(No parameters)
It deactivates the transparent mode for ALL links
<Link_Name>
It activates the transparent mode for the specified link. Use I command of BLMon to execute this command more easily.
Example ïƒ chlnSniffOn Link1
The operation is the same as for chanSniffOn, but for a link instead of a channel.
Pag 82
User Manual – HUe
Command chanSniffOn
10/01/2022
Parameters / Description
<Channel_Name>
It activates the transparent mode for the specified channel. Use c command of BLMon to execute this command more easily.
Example ïƒ chanSniffOn Channel1
This transparent mode can be activated for more than one channel at the same time.
Each message will indicate the related channel.
For this example, messages from channel1 and Channel485HUe are shown.
5.4.4 Monitoring and Synchronization Commands
Table 18 - List of monitoring and synchronization commands
Command Parameters / Description supCpuUsage supShowVer
(No parameters)
It shows the instantaneous usage of the CPU.
(No parameters)
It displays the software version of the supervision controller (sup) included in the
Baseline. thmConsoleSetTime <AA>:<MM>:<DD>:<HH><mm>:<SS>
It sets the system date and time.
<AA>: Year
<MM>: Month
<DD>: Day
<HH>: Hour
<mm>: Minute
<SS>: Second thmShow (No parameters)
It displays the information about the configuration and the current synchronization status. It is similar to the t of BLMon. thmShowVer (No parameters)
It displays the software version of the synchronization controller (thm) included in the
Baseline.
Pag 83
10/01/2022
5.4.5 Local Acquisition Commands
Table 19 - List of local acquisition commands
Command claqSniffOn
User Manual – HUe
Parameters / Description
[0|1] <Node Address>
0:Link layer
1:Application Layer
<Node Address> AB you request information from
It displays the communications of the link or application layer in the local acquisition data bus. Only the messages associated to the specified node in the second parameters are displayed.
Example of the link message: claqHelp (No parameters)
It displays a brief explanation of the list of commands available to interact with the
Local Acquisition Device and how they can be used. claqSniffOff claqStartAAP claqTableAck
(No parameters)
It finishes the local acquisition data bus.
(No parameters)
It starts the ITB addressing. All module addresses are recalculated.
To execute this addressing procedure, the configuration switch 2 must be set to ON.
For further information, please refer to section 4.3
(No parameters)
It confirms the information displayed by the claqStartAAP command so that it is stored permanently in the ITB addressing table.
For further information, please refer to section 4.3
Pag 84
User Manual – HUe
Command claqTableNack claqShowMod
10/01/2022
Parameters / Description
(No parameters)
It rejects the information displayed by the claqStartAAP command. The ITB addressing table is not updated.
For further information, please refer to section 4.3
<AB address>
It displays the value of all input and diagnostic signals of the module. It does NOT show the value of the output signals. claqTableShow (No parameters)
It shows the ITB addressing table. claqShowEvents (No parameters)
It activates the event monitoring. claqUnShowEvents (No parameters)
It deactivates the event monitoring. claqForceOut <Signal’s coordinate> <Value>
It forces a digital output to a value. Where:
<Signal’s coordinate>: Local acquisition coordinate of the signal.
<Value>: Value to which the signal should be forced. claqForceOutNTimes <Signal’s coordinate> <Number > <Time>
It forces a digital output a number of times. Where:
<Signal’s coordinate>: Local acquisition coordinate of the signal.
<Number>: Number of times the signal will be forced.
<Time>: How often (in ms) the signal will be forced. Maximum: 999 ms. claqReboot claqResetBusInfo
<AB address>
Reboot an AB. If the command does not work, the message " fun_Reboot: Unable to reboot AB module 3 " is shown. It is recommended to wait a few seconds and retry.
(No parameters)
Set to zero the counter of bus errors. claqShowInfoEmerOn (No parameters)
It allows that emergency information is shown.
Pag 85
10/01/2022
Command Parameters / Description
User Manual – HUe claqShowInfoEmerOff (No parameters)
It hides that emergency information is shown. claqShowVer (No parameters)
It displays the software version of the local acquisition controller (claq) included in the
Baseline. claqShow (No parameters)
It shows the status of the ITB and the status of each addressed module. claqVersion claqGetMIT
The ITB can be in any of the following status:
• BOOT_HU : Initial status after a boot of the ITB.
• CHECK_LAQ : Local acquisition wasn’t configured.
• READY_HU : The information in the addressing table is compatible with the loaded configuration.
• RUN_AB_LIST : HUe is asking for information of the status of each AB module.
• WAIT_HU_AAP : Error detected in the addressing procedure. Information in the addressing table is not compatible with the loaded configuration. An AAP procedure must be executed.
• WAIT_END_AAP : The CPU is waiting for a validation of the addressing table
(claqTableAck command).
Each AB can be in the following status:
• START_HU_IDP : The AB needs to be identified by the. An AAP must be executed.
• STOP_HU_AB : Problem in the addressing procedure. The AB module did not answer the request for information from the HU.
• VERIFIED_HU_IDP : The AB was addressed correctly and is waiting for the configuration.
• START_HU_AB : The AB was configured correctly and is waiting for go to the normal work status (RUN_HU_AB).
• RUN_HU_AB : Normal work status. It is sharing data with the CPU.
(No parameters)
Information about the firmware version installed in each of the AB.
<AB address>
Information about the tests carried out in the factory. This information includes: Type of module, S/N of the module and boards, P/N of the module and boards, date on which the firmware were downloaded and its version.
Pag 86
User Manual – HUe
Command claqFileVersion claqDSPUpgrade claqUpgrade
10/01/2022
Parameters / Description
<File>
It shows information about the software version of a file (.bin). The name of the file must include the full path. For example:
[all AB_AC | all AB_AC2 | <Address>]
This command updates the DSP firmware included in the AB_AC and AB_AC_LPVT
(AB_AC2) modules. The file ".t00" with the necessary software must be available in folder "/mnt/flash" of the CPU.
It can be used as follows: all AB_AC : Update the DSP in all AB_AC modules. all AB_AC2 : Update the DSP in all AB_AC_LPVT modules.
<Address> : Update the module AB_AC or AB_AC_LPVT with this address. If the module with this address in not an AB_AC or AB_AC_LPVT modules, the following message is shown “ Node to flash should be an AB_AC or AB_AC2 ”.
[all | all <Type of module> | <Address>]
This command is used to update the software of the AB modules installed in the ITB.
The ".bin" file (s) with the necessary software must be available in folder "/mnt/flash".
It can be used as follows: all : Update all modules in the ITB (included in the addressing table). all <Type of module> : Update all the ITB modules that are of the indicated type. For example: claqUpgrade all AB_DI.
<Address> : Update only the module with this address. For example: claqUpgrade 1.
Pag 87
10/01/2022
Command claqCheckUpgrade
User Manual – HUe
Parameters / Description
(No parameters)
It makes a comparison between the software files in folder "/mnt/flash" (version to install) and the software installed in each module (currently installed). For example: claqJtag
If a module is included in the addressing table, but it is not installed in the ITB, the following message will be displayed: “ Module not available ”.
<File>
Be careful using this command, it can block the AB modules in the ITB!! On this situation, each blocked AB need to be sent to the repair service!!
It restores the software of a module when it is not addressed in the ITB. This command must be used when the claqUpdate command does not work and only for users with great knowledge of the system.
<File>: File’s name, including the path. For example:
claqJtag /mnt/flash/AB_MIO.bin.
When this command is executed, the user must BE SURE of:
• The module has a bootLoader.
• Only the AB module to be restored must be connected in the ITB.
• The File must be the same time of the AB to be restored. For example, for an
AB_MIO module, the file must be AB_MIO.bin
Pag 88
6 Technical Specifications Table
Public
10/01/2022
Hardware Specifications
Processing unit
External RTC
RTC accuracy
FLASH memory (NOR)
FLASH memory (NAND)
Static RAM memory
Dynamic RAM memory (DDR3)
Assurance for static RAM
Autonomy in power down
Consumption
Weight
Dimensions
Coating
Protection degree
Range of temperature
Sitara™ AM3356BZCZD60
Technology: ARM® Cortex™-A8
Data bus: 32-bits
Clock frequency: Up to 720 MHz
DS3232 controlled by I2C
±2 ppm (0°C to +40°C)
±3.5 ppm (-40°C to +85°C)
32 MB
256 MB
2 MB
256 MB
Integrated supercapacitor
Up to 8 hours (+25 ºC)
5 W Maximum
600 g
134 mm x 129 mm x 60 mm
AVR80 (Depending on P/N)
IP20
Operation: From -40º C to +70º C (See warning note below)
Storage: From -40º C to +125º C
User Manual – HUe
WARNING
According to the standard 60950-1, all electrical safety tests have been done in an environmental temperature range of -40 ºC to 60 ºC. For higher temperature (> 60 ºC), the module must be handled with care since the metal surface could reach a dangerous temperature for the user.
Interfaces
Power supply (POWER)
Console port (CON)
Serial port (RS-485)
Serial port (COM1)
Serial port (COM2)
USB port
SD card
Voltage range 24 – 48 VDC (±20%)
3-pole terminal block
Wire: 2.5 mm² (13 AWG)
Mini-USB connector
RS-485 communications
3-pole connector, with isolation
Wire: 1.5 mm² (15 AWG)
RS-232 communications
Male DB9 connector, without isolation
Modem control (full)
GPS port
RS-232 communications
Male DB9 connector, without isolation
Modem control (only RTS and CTS)
2.0 (Host)
Up to 32 GB
Pag 90
User Manual – HUe
Interfaces
Auxiliary digital inputs (AUX DI)
IRIG-B
External watchdog (WD)
Ethernet port (MNT)
Ethernet ports (LAN1 and LAN2)
(Copper)
Ethernet ports (LAN1 and LAN2)
(Fiber Optic)
5-pole terminal block with isolation
4 digital inputs for general purpose
2-pole terminal block with isolation
1.5 mm² (15 AWG)
Non-modulated TTL 5V
Input impedance 600 Ohm
Maximum capacity of current: 20 mA
2-pole terminal block with isolation
1.5 mm² (15 AWG)
Fast-Ethernet 10/100BaseT
RJ-45 connector
Fast-Ethernet 10/100BaseT
RJ-45 connector
Fast-Ethernet 100Base-FX
Recommended transceivers for FO:
• HFBR-57E0PZ (From 0º C to +70º C)
• HFBR-57E0APZ (From -40º C to +85º C)
Internal bus (power, data, synchronization, …) Communication with other modules
Software
Operating System
External synchronization
IRIG-B
Discrimination time for events
Watchdog software
Security control
RTLinux
GPS
IRIG-B
Protocol
Console
PTP
TTL input signal
Protocols: IRIG-B002, IRIG-B003, IRIG-B006 and IRIG-B007
1 ms
Internal
Cybersecurity brick included
Embedded firewall
Secured interfaces
User management based on a RBAC model
Ordering Options
10/01/2022
Pag 91
10/01/2022
Cybersecurity
Based on IEC62351
IEC62443
Security Engine SEC 3.3.2 (XOR acceleration)
Supported cryptographic algorithms 3DES, AES, MD5/SHA, RSA/ECC, & FIPS (determinist generator)
Processing
Security protocols
Single pass encryption and authentication
SSL 3.0, SSL 3.1 / TLS 1.0
CE Mark
Standards, Directives and harmonized norms.
Electric Safety
Environmental tests
User Manual – HUe
LVD – Low Voltage Directive
EMC – Electromagnetic Compatibility
RoHS
Directive 2014/35/EU
Directive 2014/30/EU
Directive 2015/863/EU
WEEE – Waste Electrical and Electronic
Equipment
Directive 2012/19/EU
General requirements
IEC 60950-1:2005 + CORR:2006 + A1:2009 + A2:2013
EN 60950-1:2006 + A11:2009 + A1:2010 + AC:2011 + A12:2011+ A2:2013
UNE EN 60950-1:2007 + A11:2009 + CORR:2007 + A1:2011 + A12:2011 + AC:2012 + A2:2014
Cold - EN 60068-2-1:2007
Dry heat - EN 60068-2-2:2007
Damp heat - EN 60068-2-30:2005
-40ºC during 16h
+70ºC during 16h
25-60ºC with 95%RH during 24h
Tests according to
Emission
Immunity
EMC Directive
EN 60870-2-1 (1996)
IEC/TS 61000-6-5 (2015)
Radiated emissions
EN 55022:2006 + A1:2007
Conducted emissions
EN 55022:2006 + A1:2007
Radiated emission.
EN 55032 (2015) / AC (2016-07)
Conducted emission on power leads
EN 55032 (2015) / AC (2016)
Electrostatic discharges (ESD)
EN 61000-4-2:2009
Radiated, radio-frequency, electromagnetic field
EN 61000-4-3:2006 + A2:2010
Fast transients common mode
EN61000-4-4:2012
Surges, line to line and line to ground
EN 61000-4-5:2006
From 30 to 1000 MHz (Class A)
From 0.15 to 30 MHz (Class A)
From 30 to 6000 MHz (Class A)
From 0.15 to 30 MHz (Class A)
By air ±8 kV and by contact ±4 and ±6 kV (Level 3)
From 80 to 6000 MHz (Level 3).
Power port: ±4 kV, 5kHz / ±0.5 kV, 5kHz.
Communications ports: ±4 kV and ±0.5 kV 5kHz /
±4 kV 2.5kHz.
I/O ports: ±4 kV 5kHz (Level 4).
Power: ±4 kV symmetric and asymmetric (Level 4)
Power: ±4 kV, 5kHz.
Communications: ±4 kV CM, ±2 kV DM (Level 4).
±0.5 kV,±1 kV (symmetrical)
±0.5 kV,±1 kV,±2 kV (asymmetrical)
I/O: ±4 kV CM, ±2 kV DM
RF common mode
EN 61000-4-6:2014
Power frequency magnetic field
EN 61000-4-8:2010.
Pag 92
10 V
RMS
0.15-80MHz 80% AM (Level 3).
100 A/m, 1000 A/m 3s (Level 4).
User Manual – HUe
EMC Directive
Power frequency common mode disturbances
EN 61000-4-16:1998
Damped oscillatory wave
EN 61000-4-18:2007 + A1:2010
10/01/2022
30V 50Hz, 300V 50Hz 1s (Level 4).
Power, communications and I/O:
1kV DM, 2.5kV CM (Level 4), (f=1MHz)
Pag 93
10/01/2022
Index of Figures
User Manual – HUe
Pag 94
User Manual – HUe 10/01/2022
Pag 95
10/01/2022
Index of Tables
User Manual – HUe
Pag 96
User Manual – HUe
Glossary
A
A : Ampere.
AAP : Automatic Addressing Procedure.
AB : Saitel DR Acquisition Block.
AB_AC : Direct measurements Acquisition Block.
AB_AI : Analog Inputs Acquisition Block.
AB_AO : Analog Outputs Acquisition Block.
AB_DI : Digital Inputs Acquisition Block.
AB_DIDO: Digital Inputs and Outputs Acquisition Blocks.
AB_DO: Digital Outputs Acquisition Blocks.
AB_MIO: Multiple Inputs and Outputs Acquisition Block.
AB_SER: Communication module for expansion.
AC: Alternate Current.
AI: Analog Input.
AO: Analog Output.
AWG: American Wire Gauge .
B
Bps : Bits per second .
C
ºC: Celsius degree.
COM: Communication port.
CPU: Central Processing Unit.
CTS: Clear to Send.
D
DC : Direct Current.
DI : Digital Input.
DIN : Deutsches Institut für Normung.
DO : Digital Output.
DRAM : Dynamic Random Access Memory.
E
EMC: ElectroMagnetic Compatibility.
EPROM : Erasable Programmable Read Only Memory
Pag 97
10/01/2022
10/01/2022
F
FTP : File Transfer Protocol.
G g : Gram.
GPS : Global Positioning System.
H
HMI : Human-Machine Interface.
HU : Head Unit. Saitel DR CPU.
HU_A : Saitel DR Advanced Head Unit.
HU_AF : Saitel DR Advanced Head Unit with acquisition.
HU_B : Saitel DR Basic Head Unit.
HUe : Saitel DR High-Performance Head Unit.
Hz : Hertz.
I
IED : Intelligent Electronic Device.
I/O : Input / Output.
IRIG : Inter Range Instrumentation Group.
IRIG-B : Mode B of the standard IRIG.
ISO 9001 : International standard for Quality Systems.
ITB : Intelligent Terminal Block.
K
KB : Kilobyte. kHz : Kilohertz.
L
LAN : Local Area Network.
LED: Light Emitting Diode.
M mA: Milliampere.
MHz: Megahertz.
MB: Megabyte.
Mbps: Megabits per second. m : Meter. mm: Millimeter. ms : Millisecond.
Pag 98
User Manual – HUe
User Manual – HUe
N
N/A : Non-Application.
P
PC : Personal Computer.
PPS : Pulses per Second.
PS : Power Supply.
PWR : Power.
R
RAM : Random Access Memory.
RS-232 : Communication standard.
RS-485 : Multipoint differential Bus.
RTDB : Real Time DataBase.
RTS : Request To Send.
RTU : Remote Terminal Unit.
Rx : Reception
S s : Second.
SCADA : Supervisory Control And Data Acquisition.
SFTP : Secure File Transfer Protocol.
SNTP : Simple Network Time Protocol.
SRAM : Static Random Access Memory.
SSH : Secure SHell.
T
TCP/IP : Transmission Control Protocol/Internet Protocol.
TU : Terminal Unit.
Tx : Transmission.
V
VAC : Volt of Alternate Current.
VDC : Volt of Direct Current.
W
W : Watt.
X
XU: Expansion Unit.
Pag 99
10/01/2022
Schneider Electric
C/ Charles Darwin s/n
Parque Científico y Tecnológico de la Cartuja
Seville, Spain
©2022 All rights reserved. The information contained in this document is confidential and is owned by Schneider Electric. It cannot be copied or distributed in any way, unless there is express written authorization by Schneider Electric.
Although this information was verified at the time of publication, may be subject to change without notice.
SE-USR-M588-06 01/2022
Pag 100
Printed in:
Wednesday, January 19, 2022
advertisement