advertisement
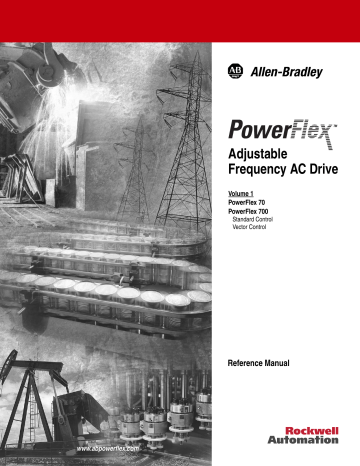
Accel Time
Chapter
2
Detailed Drive Operation
This chapter explains PowerFlex drive functions in detail. Explanations are organized alphabetically by topic. Refer to the Table of Contents for a listing of topics.
[Accel Time 1, 2]
The Accel Time parameters set the rate at which the drive ramps up its output frequency after a Start command or during an increase in command frequency (speed change). The rate established is the result of the programmed Accel Time and the Minimum and Maximum Frequency, as follows:
Maximum Speed
Accel Time
= Accel Rate (Hz./sec.)
Two accel times exist to allow the user to change acceleration rates “on the fly” via PLC command or digital input. The selection is made by programming [Accel Time 1] & [Accel Time 2] and then using one of the digital inputs ([Digital Inx Sel]) programmed as “Accel 2” (see
for further information). However, if a PLC is used, manipulate the bits of the command word as shown below.
(1
)
(1
)
(1
)
Bit #
0
15
0
Spd Ref ID 2 Decel 1 Accel 2
0 0 1 1 1 0
14 13 12 11 10 9 8
1
7
0
0
0
1
0
0
1
0
0
1
0
0
1
0
0
0
0
6
Accel 1
Accel 2
Decel 1
Decel 2
0
Re ver se d
Forwar Clear F ault
0 1 1 0
5 4 3 2 1
t
Star
0
0
Stop
1 =Condition True
0 =Condition False x =Reserved
The effectiveness of these bits or digital inputs can be affected by [Accel
Mask]. See
for more information.
Times are adjustable in 0.1 second increments from 0.0 seconds to 3600.0
seconds.
In its factory default condition, when no accel select inputs are closed and no accel time bits are “1,” the default acceleration time is Accel Time 1 and the rate is determined as above.
2-2
AC Supply Source Considerations
AC Supply Source
Considerations
PowerFlex drives are suitable for use on a circuit capable of delivering up to a maximum of 200,000 rms symmetrical amperes, 600V.
!
ATTENTION: To guard against personal injury and/or equipment damage caused by improper fusing or circuit breaker selection, use only the recommended line fuses/circuit breakers specified in
Tables
through
If a system ground fault monitor (RCD) is to be used, only Type B
(adjustable) devices should be used to avoid nuisance tripping.
Alarms
Alarms are indications of situations that are occurring within the drive or application that should be annunciated to the user. These situations may affect the drive operation or application performance. Conditions such as
Power Loss or Analog input signal loss can be detected and displayed to the user for drive or operator action.
There are two types of alarms:
•
Type 1 Alarms are conditions that occur in the drive or application that may require alerting the operator. These conditions, by themselves, do not cause the drive to “trip” or shut down, but they may be an indication that, if the condition persists, it may lead to a drive fault.
•
Type 2 Alarms are conditions that are caused by improper programming and they prevent the user from Starting the drive until the improper programming is corrected. An example would be programming one digital input for a 2-wire type control (Run Forward) and another digital input for a 3-wire type control (Start). These are mutually exclusive operations, since the drive could not determine how to properly issue a
“Run” command. Because the programming conflicts, the drive will issue a type 2 alarm and prevent Starting until the conflict is resolved.
Alarm Status Indication
[Drive Alarm 1]
[Drive Alarm 2]
Two 16 bit Drive Alarm parameters are available to indicate the status of any alarm conditions. Both Type 1 and Type 2 alarms are indicated.
A “1” in the bit indicates the presence of the alarm and a “0” indicates no alarm is present
Configuration
In order for a drive alarm to be annunciated to the “outside” world, it must first be “configured” or activated. Configuration parameters contain a configuration bit for each Type 1 alarm. Type 2 alarms are permanently configured to annunciate. The configuration word is a mirror image of the
Alarms
2-3
Drive Alarm word; that is, the same bits in both the Drive Alarm Word and the Alarm Configuration Word represent the same alarm.
Drive Alarm
1 1 1
Alarm Config
1 0 0
X X
Active
Alarm
Inactive
Alarm
Inactive
Alarm
The configuration bits act as a mask to block or pass through the alarm condition to the active condition. An active alarm will be indicated on the
LCD HIM and will cause the drive alarm status bit to go high (“1”) in the
Drive Status word (Bit 6, parameter 209). This bit can then be linked to a digital output for external annunciation. As default, all configuration bits are high (“1”). Note that setting a configuration bit to “0” to “mask” an alarm does not affect the status bit in the Drive Alarm parameter, only its ability to annunciate the condition.
Application
A process is being controlled by a PowerFlex drive. The speed reference to the drive is a 4-20 mA analog signal from a sensor wired to Analog Input 1.
The input is configured for mA by setting the corresponding bit in [Anlg In
Config] to “1”
320 [Anlg In Config]
Selects the mode for the analog inputs.
322
325
323
326 x
15 x
14 x
13 x
12 x
11 x
10 x
9
Bit #
Factory Default Bit Values x
8 x
7 x
6 x
5 x
4 x
3 x
2
0
1
A nalo
0
0
2 g In
A na log
In 1
1 =Current
0 =Voltage x =Reserved
Analog In Config
0 1
The input is scaled for 4-20 mA by setting [Analog In 1 Lo] to “4” mA and
[Analog In 1 Hi] to “20” mA.
2-4
Alarms
The signal is designated as the active speed reference by setting [Speed Ref
A Sel] to its factory default value of “1”
090 [Speed Ref A Sel]
Selects the source of the speed reference to the drive unless [Speed Ref
B Sel] or [Preset Speed 1-7] is selected.
Default:
Options:
(1)
See User Manual for DPI port locations.
2
16
17
18
19
12
13
14
15
20
21
22
8
9
10
11
1
2
3-6
7
“Analog In 2”
“Analog In 1”
“Analog In 2”
“Reserved”
“Pulse In”
“Encoder”
“MOP Level”
“Reserved”
“Preset Spd1”
“Preset Spd2”
“Preset Spd3”
“Preset Spd4”
“Preset Spd5”
“Preset Spd6”
“Preset Spd7”
“DPI Port 1”
(1)
“DPI Port 2”
(1)
“DPI Port 3”
(1)
“DPI Port 4”
(1)
“DPI Port 5”
(1)
117 thru
120
192 thru
194
213
272
273
320
361 thru
366
002
091 thru
093
101 thru
107
By setting Speed Ref A Hi to 60 Hz and Speed ref A Lo to 0 Hz, the speed reference is scaled to the application needs. Because of the Input scaling and link to the speed reference, 4 mA represents minimum frequency (0
Hz.) and 20 mA represents Maximum Frequency (60 Hz.)
Scale Block
P322
20mA
P325
4mA
P091
60 Hz
P092
0 HZ
The input is configured to recognize a loss of signal and react accordingly to the programming.
324
327
[Analog In 1 Loss]
[Analog In 2 Loss]
Selects drive action when an analog signal loss is detected. Signal loss is defined as an analog signal less than 1V or 2mA. The signal loss event ends and normal operation resumes when the input signal level is greater than or equal to 1.5V or 3mA.
Default:
Options:
5
6
3
4
0
1
2
0
0
“Disabled”
“Disabled”
“Disabled”
“Fault”
“Hold Input”
“Set Input Lo”
“Set Input Hi”
“Goto Preset1”
“Hold OutFreq”
091
092
The loss action is chosen as Hold Input, meaning that the last received signal will be maintained as the speed reference.
Alarms
2-5
Finally, a Digital Output relay is configured to annunciate an alarm by turning on a flashing yellow light mounted on the operator panel of the process control area.
380
384
388
[Digital Out1 Sel]
[Digital Out2 Sel]
Vector
[Digital Out3 Sel]
Selects the drive status that will energize a (CRx) output relay.
Default:
Options:
(1)
Contacts shown in User Manual are in drive powered state with condition present. Refer to “Fault” and “Alarm” information.
(2)
Vector Control Option Only.
1
4
4
12
13
14
15
8
9
10
11
6
7
4
5
1
2
3
20
21-
26
27
16
17
18
19
28
29
“Fault”
“Run”
“Run”
“Fault”
(1)
“Alarm”
(1)
“Ready”
“Run”
“Forward Run”
“Reverse Run”
“Auto Restart”
“Powerup Run”
“At Speed”
“At Freq”
“At Current”
“At Torque”
“At Temp”
“At Bus Volts”
“At PI Error”
“DC Braking”
“Curr Limit”
“Economize”
“Motor Overld”
“Power Loss”
“Input 1-6 Link”
“PI Enable”
(2)
“PI Hold”
(2)
“PI Reset”
(2)
381
385
382
386
383
002
001
003
004
218
012
137
157
147
053
048
184
While the process is normal and running from the analog input, everything proceeds normally. However, if the wire for the analog input should be severed or the sensor malfunction so that the 4-20mA signal is lost, the following sequence occurs:
1. The drive will sense the signal loss.
2. An active Type 1 Alarm is created and the last signal value is maintained as the speed reference.
3. The alarm activates the digital output relay to light the alarm light for the operator.
4. The operator uses the HIM to switch the drive to Manual Control (see
Auto/Manual).
5. The operator manually brings the process to a controlled stop until the signal loss is repaired.
2-6
Analog Inputs
Analog Inputs
Alarm Queue (PowerFlex 700 Only)
A queue of 8 parameters exists that capture the drive alarms as they occur. A sequential record of the alarm occurrences allows the user to view the history of the eight most recent events.
262
263
264
265
266
267
268
269
[Alarm 1 Code]
[Alarm 2 Code]
[Alarm 3 Code]
[Alarm 4 Code]
[Alarm 5 Code]
[Alarm 6 Code]
[Alarm 7 Code]
[Alarm 8 Code]
A code that represents a drive alarm.
The codes will appear in the order they occur (first 4 alarms in – first 4 out alarm queue). A time stamp is not available with alarms.
Default:
Min/Max:
Display:
Read Only
0/256
1
261
Possible Uses of Analog Inputs
The analog inputs provide data that can be used for the following purposes:
•
Provide a value to [Speed Ref A] or [Speed Ref B].
•
Provide a trim signal to [Speed Ref A] or [Speed Ref B].
•
Provide a reference when the terminal block has assumed manual control of the reference
•
Provide the reference and feedback for the PI loop. See
.
•
Provide an external and adjustable value for the current limit and DC braking level
•
Enter and exit sleep mode.
Analog Input Configuration
[Anlg In Config]
[Current Lmt Sel] allows an analog input to control the set point while [DC
Brk Levl Sel] allows an analog input to define the DC hold level used when
Ramp-to-Stop, Ramp-to-Hold, or Brake-to-Stop is active.
To provide local adjustment of a master command signal or to provide improved resolution the input to analog channel 1 or 2 can be defined as a trim input. Setting [Trim In Select] allows the selected channel to modify the commanded frequency by 10%.The speed command will be reduced by
10% when the input level is at [Anlg In x Lo] with it linearly increasing to
10% above command at [Anlg In xHi].
Feedback can be used to control an operation using the “Process PI”
(proportional-integral) feature of the control. In this case one signal, defined using [PI Reference Sel], provides a reference command and a second, defined using [PI Feedback Sel], provides a feedback signal for frequency compensation. Please refer to the
for details on this mode of operation.
Analog In 1 Lo
Analog In 1 Hi
Analog In 2 Lo
Analog In 2 Hi
Analog Input
1 Scale
Volts or mA
Cal Analog 1
Analog Input
2 Scale
Volts or mA
Cal Analog 2
Input/Output
Parameter
Processing
Selection/Control
Speed Ref A Sel Speed Ref B Sel Trim In Select TB Man Ref Sel PI Reference Sel PI Feedback Sel Current Lmt Sel DC Brk Levl Sel Sleep-Wake Ref
Ref A
Scale/Limit
Speed Ref A Lo
Speed Ref A Hi
Speed Ref B Lo
Speed Ref B Hi
Ref B
Scale/Limit
Trim
Scale/Limit
Trim Lo
Trim Hi
TB Manual
Scale/Limit
Trim Out Sel
Hz
+
Hz
Reference A
+
Hz
Reference B
Brake Level
Scale/Limit
Sleep Level
Compare
Hz
TB Manual
PI
Reference
Scale/Limit
%
PI Reference
PI Feedback
Scale/Limit
%
PI Feedback
Current Limit
Scale/Limit
% Rated
Current
Current Limit
% Rated
Current
DC Brake
Sleep/
Wake
Sleep/Wake
Sleep Level
Wake Level
Analog 1
Voltage
Analog 1
Current
ADC
Input/Output
Parameter
Processing
Selection/Control
Anlg In Config
0-10v
0-20mA
Unipolar
Cal 1
Current
Cal 1
Anlg In 1 Loss
Loss
Detect
Limit
0-10V
Anlg In Sqr Root
Loss
Detect
Limit
4-20mA
Square
Root
Cal Analog 1
Analog 2
Unipolar
Analog 2
Bipolar
Analog 2
Current
ADC
Anlg In Config
(voltage)
(current)
Analog In1 Value
Analog In 2 Lo
Analog In 2 Hi
0-10v
Note: If either of these parameters is < 0, input will go into bipolar mode, otherwise unipolar.
Unipolar
Cal 2
-10v - +10v
0-20mA
Bipolar
Cal 2
Current
Cal 2
Anlg In 2 Loss
Loss
Detect
Limit
0-10V
Loss
Detect
Limit
-10V to
10V
Limit
4-20mA
Anlg In Sqr Root
Square
Root
Cal Analog 2
Analog In2 Value
Analog Inputs
2-9
Scaling Blocks
[Analog In Hi]
[Analog In Lo]
A scaling operation is performed on the value read from an analog input in order to convert it to units usable for some particular purpose. The user controls the scaling by setting parameters that associate a low and high point in the input range (i.e. in volts or mA) with a low and high point in the target range (e.g. reference frequency).
Two sets of numbers may be used to specify the analog input scaling. One set (called the “input scaling points”) defines low and high points in terms of the units read by the input hardware, i.e. volts or mA.
The second set of numbers (called the “output scaling points”) used in the analog input scaling defines the same low and high points in units appropriate for the desired use of the input. For instance, if the input is to be used as a frequency reference, this second set of numbers would be entered in terms of Hz. For many features the second set of numbers is fixed. The user sets the second set for speed and reference trim.
An analog input or output signal can represent a number of different commands. Typically an analog input is used to control output frequency, but it could control frequency trim, current limit or act as a PI loop input.
An analog output typically is a frequency indication, but it could represent output current, voltage, or power. For this reason this document defines an analog signal level as providing a “command” value rather than a
“frequency.” However when viewing a command value it is presented as a frequency based on the [Minimum Speed] and [Maximum Freq] settings.
The 0-10 volt input scaling can be adjusted using the following parameters:
•
[Analog In x Lo]
•
[Analog In x Hi]
2-10
Analog Inputs
Configuration #1:
•
[Anlg In Config], bit 0 = “0” (Voltage)
•
[Speed Ref A Sel] = “Analog In 1”
•
[Minimum Speed] = 0 Hz
•
[Maximum Speed] = 60 Hz
•
[Speed Ref A Lo] = 0V
•
[Speed Ref A Hi] = 10V
This is the default setting, where minimum input (0 volts) represents
[Minimum Speed] of 0 Hz and maximum input (10 volts) represents
[Maximum Speed] of 60 Hz (it provides 6 Hz change per input volt).
8
6
4
2
12
10
0 6 12 18 24 30 36 42 48 54 60
Output Hertz
Scaling Block
[Speed Reference A Sel] = “Analog In 1”
[Analog In 1 Hi]
0V
[Analog In 1 Lo]
10V
[Speed Ref A Hi]
0 Hz
[Speed Ref A Lo]
60 Hz
Configuration #2:
•
[Anlg In Config], bit 0 = “0” (Voltage)
•
[Speed Ref A Sel] = “Analog In 1”
•
[Minimum Speed] = 0 Hz
•
[Maximum Speed] = 30 Hz
•
[Speed Ref A Lo] = 0V
•
[Speed Ref A Hi] = 10V
This is an application that only requires 30 Hz as a maximum output frequency, but is still configured for full 10 volt input. The result is that the resolution of the input has been doubled, providing only 3 Hz change per input volt (Configuration #1 is 6 Hz/Volt).
Analog Inputs
2-11
8
6
4
2
12
10
0 6 12 18 24 30 36 42 48 54 60
Output Hertz
Scaling Block
[Speed Reference A Sel] = “Analog In 1”
[Analog In 1 Hi]
0V
[Analog In 1 Lo]]
10V
[Speed Ref A Hi]
0 Hz
[Speed Ref A Lo]]
30 Hz
Configuration #3:
•
[Anlg In Config], bit 0 = “1” (Current)
•
[Speed Ref A Sel] = “Analog In 1”
•
[Minimum Speed] = 0 Hz
•
[Maximum Speed] = 60 Hz
•
[Speed Ref A Lo] = 4 mA
•
[Speed Ref A Hi] = 20 mA
This configuration is referred to as offset. In this case, a 4-20 mA input signal provides 0-60 Hz output, providing a 4 mA offset in the speed command.
20
16
12
8
4
0 6 12 18 24 30 36 42 48 54 60
Output Hertz
Scaling Block
[Speed Reference A Sel] = “Analog In 1”
[Analog In 1 Hi
4 mA
[Analog In 1 Lo]
20 mA
[Speed Ref A Hi]
0 Hz
[Speed Ref A Lo]
60 Hz
2-12
Analog Inputs
Configuration #4:
•
[Anlg In Config], bit 0 = “0” (Voltage)
•
[Speed Ref A Sel] = “Analog In 1”
•
[Minimum Speed] = 0 Hz
•
[Maximum Speed] = 60 Hz
•
[Speed Ref A Lo] = 10V
•
[Speed Ref A Hi] = 0V
This configuration is used to invert the operation of the input signal. Here, maximum input (10 Volts) represents [Minimum Speed] of 0 Hz and minimum input (0 Volts) represents [Maximum Speed] of 60 Hz.
10
8
6
4
2
0 6 12 18 24 30 36 42 48 54 60
Output Hertz
Scaling Block
[Speed Reference A Sel] = “Analog In 1”
[Analog In 1 Hi
10V
[Analog In 1 Lo]
0V
[Speed Ref A Hi]
0 Hz
[Speed Ref A Lo]
60 Hz
Configuration #5:
•
[Anlg In Config], bit 0 = “0” (Voltage)
•
[Speed Ref A Sel] = “Analog In 1”
•
[Minimum Speed] = 0 Hz.
•
[Maximum Speed] = 60 Hz
•
[Speed Ref A Lo] = 0V
•
[Speed Ref A Hi] = 5V
This configuration is used when the input signal is 0-5 volts. Here, minimum input (0 Volts) represents [Minimum Speed] of 0 Hz and maximum input (5 Volts) represents [Maximum Speed] of 60 Hz. This allows full scale operation from a 0-5 volt source.
Analog Inputs
2-13
4
3
2
1
6
5
0 6 12 18 24 30 36 42 48 54 60
Output Hertz
Scaling Block
[Speed Reference A Sel] = “Analog In 1”
[Analog In 1 Hi]
0V
[Analog In 1 Lo]
5V
[Speed Ref A Hi]
0 Hz
[Speed Ref A Lo]
60Hz
Square Root
[Anlg In Sqr Root]
For both analog inputs, the user can enable a square root function for an analog input through the use of [Analog In Sq Root]. The function should be set to enabled if the input signal varies with the square of the quantity
(i.e. drive speed) being monitored.
If the mode of the input is bipolar voltage (-10v to 10v), then the square root function will return 0 for all negative voltages.
The square root function is scaled such that the input range is the same as the output range. For example, if the input is set up as a unipolar voltage input, then the input and output ranges of the square root function will be 0 to 10 volts, as shown in figure below.
10
8
6
4
2
0 2 4 6
Input (Volts)
8 10
Signal Loss
[Analog In 1, 2 Loss]
Signal loss detection can be enabled for each analog input. The [Analog In x Loss] parameters control whether signal loss detection is enabled for each input and defines what action the drive will take when loss of any analog input signal occurs.
2-14
Analog Inputs
5
6
3
4
1
2
Value
0
One of the selections for reaction to signal loss is a drive fault, which will stop the drive. All other choices make it possible for the input signal to return to a usable level while the drive is still running.
•
Hold input
•
Set input Lo
•
Set input Hi
•
Goto Preset 1
•
Hold Output Frequency
Action on Signal Loss
Disabled (default)
Fault
Hold input (continue to use last frequency command.)
Set Input Hi - use [Minimum Speed] as frequency command.
Set Input Lo - use [Maximum Speed] as frequency command.
use [Preset 1] as frequency command.
Hold Out Freq (maintain last output frequency)
If the input is in current mode, 4 mA is the normal minimum usable input value. Any value below 3.2 mA will be interpreted by the drive as a signal loss, and a value of 3.8 mA will be required on the input in order for the signal loss condition to end.
4 mA
3.8 mA
3.2 mA
Signal Loss
Condition
End Signal Loss
Condition
If the input is in unipolar voltage mode, 2V is the normal minimum usable input value. Any value below 1.6 volts will be interpreted by the drive as a signal loss, and a value of 1.9 volts will be required on the input in order for the signal loss condition to end.
2V
1.9V
1.6V
Signal Loss
Condition
End Signal Loss
Condition
No signal loss detection is possible while an input is in bipolar voltage mode. The signal loss condition will never occur even if signal loss detection is enabled.
Analog Inputs
2-15
Trim
An analog input can be used to trim the active speed reference (Speed
Reference A/B). If analog is chosen as a trim input, two scale parameters are provide to scale the trim reference. The trim is a +/- value which is summed with the current speed reference. See also
.
•
[Trim In Select]
•
[Trim Out Select]
•
[Trim Hi]
•
[Trim Lo]
Value Display
Parameters are available in the Monitoring Group to view the actual value of an analog input regardless of its use in the application. Whether it is a current limit adjustment, speed reference or trim function, the incoming value can be read via these parameters.
The value displayed includes the input value plus any factory hardware calibration value, but does not include scaling information programmed by the user (i.e. [Analog In 1 Hi/Lo]). The units displayed are determined by the associated configuration bit (Volts or mA)
016
017
[Analog In1 Value]
[Analog In2 Value]
Value of the signal at the analog inputs.
Default:
Min/Max:
Display:
Read Only
0.000/20.000 mA
–/+10.000V
0.001 mA
0.001 Volt
Cable Selection
Important points to remember:
•
Always use copper wire.
•
Wire with an insulation rating of 600V or greater is recommended.
•
Control and signal wires should be separated from power wires by at least 0.3 meters (1 foot).
Important: I/O terminals labeled “–” or “Common” are not referenced to ground and are designed to greatly reduce common mode interference. Grounding these terminals can cause signal noise.
!
!
ATTENTION: Configuring an analog input for 0-20mA operation and driving it from a voltage source could cause component damage. Verify proper configuration prior to applying input signals.
ATTENTION: Hazard of personal injury or equipment damage exists when using bipolar input sources. Noise and drift in sensitive input circuits can cause unpredictable changes in motor speed and direction. Use speed command parameters to help reduce input source sensitivity.
2-16
Analog Inputs
Table 2.A Recommended Signal Wire
Signal Type Wire Type(s)
Analog I/O
Encoder/
Pulse I/O
Belden 8760/9460(or equiv.)
Belden 8770(or equiv.)
Less than or equal to 30 m (98 ft.) – Belden 9730 (or equiv.)
Greater than 30 m (98 ft.) –
Belden 9773(or equiv.)
Description
0.750 mm
2
(18AWG), twisted pair, 100% shield with drain
(1)
.
0.750 mm
2
(18AWG), 3 cond., shielded for remote pot only.
0.196 mm
2
(24AWG), individually shielded.
0.750 mm
2
(18AWG), twisted pair, shielded.
Minimum
Insulation Rating
300V,
60 degrees C
(140 degrees F)
EMC Refer to
EMC Instructions on page 2-40 for details.
Compliance
(1)
If the wires are short and contained within a cabinet which has no sensitive circuits, the use of shielded wire may not be necessary, but is always recommended.
Refer to
for recommended digital I/O control wire.
Terminal Designations & Wiring Examples
Refer to the appropriate PowerFlex User Manual for I/O terminal designations and wiring examples.
How [Analog Inx Hi/Lo] & [Speed Ref A Hi/Lo] Scales the Frequency
Command Slope with [Minimum/Maximum Speed]
Example 1:
Consider the following setup:
•
[Anlg In Config], bit 0 = “0” (voltage)
•
[Speed Ref A Sel] = “Analog In 1”
•
[Analog In1 Hi] = 10V
•
[Analog In1 Lo] = 0V
•
[Speed Ref A Hi] = 60 Hz
•
[Speed Ref A Lo] = 0 Hz
•
[Maximum Speed] = 45 Hz
•
[Minimum Speed] = 15 Hz
This operation is similar to the 0-10 volts creating a 0-60 Hz signal until the minimum and maximum speeds are added. [Minimum Speed] and
[Maximum Speed] limits will create a command frequency deadband.
Analog Inputs
2-17
[Analog In1 Hi]
10V
[Minimum Speed] [Maximum Speed]
Motor Operating Range
Frequency Deadband
0-2.5 Volts
Frequency Deadband
7.5-10 Volts
Command Frequency
[Analog In1 Lo]
0V
0 Hz
[Speed Ref A Lo]
15 Hz
Slope defined by (Analog Volts)/(Command Frequency)
45 Hz 60 Hz
[Speed Ref A Hi]
This deadband, as it relates to the analog input, can be calculated as follows:
1. The ratio of analog input volts to frequency (Volts/Hz) needs to be calculated. The voltage span on the analog input is 10 volts. The frequency span is 60 Hz.
10 Volts/60 Hz = 0.16667 Volts/Hz
2. Determine the frequency span between the Minimum and Maximum
Speed limits and Speed Ref A Hi and Lo.
[Speed Ref A Hi] – [Maximum Speed] = 60 – 45 = 15 Hz and . . .
[Minimum Speed] – [Speed Ref A Lo] = 15 – 0 = 15 Hz.
3. Multiply by the Volts/Hertz ratio
15 Hz x 0.16667 Volts/Hz = 2.5 Volts
Therefore the command frequency from 0 to 2.5 volts on the analog input will be 15 Hz. After 2.5 volts, the frequency will increase at a rate of
0.16667 volts per hertz to 7.5 volts. After 7.5 volts on the analog input the frequency command will remain at 45 Hertz.
Example 2:
Consider the following setup:
•
[Anlg In Config], bit 0 = “0” (voltage)
•
[Speed Ref A Sel] = “Analog In 1”
•
[Analog In1 Hi] = 10V
•
[Analog In1 Lo] = 0V
•
[Speed Ref A Hi] = 50hz
•
[Speed Ref A Lo] = 0hz
•
[Maximum Speed] = 45hz
•
[Minimum Speed] = 15hz
The only change from Example 1 is the [Speed Ref A Hi] is changed to 50
Hz.
2-18
Analog Inputs
[Analog In1 Hi]
10V
Frequency Deadband
0-3 Volts
[Minimum Speed]
Motor Operating Range
[Maximum Speed]
Frequency Deadband
9-10 Volts
Command Frequency
[Analog In1 Lo]
0V
0 Hz
[Speed Ref A Lo]
15 Hz
Slope defined by (Analog Volts)/(Command Frequency)
45 Hz 50 Hz
[Speed Ref A Hi]
The deadband, as it relates to the analog input, can be calculated as follows:
1. The ratio of analog input volts to frequency (Volts/Hertz) needs to be calculated. The voltage span on the analog input is 10 volts. The frequency span is 60 Hz.
10 Volts/50 Hz = 0.2 Volts/Hz
2. Determine the frequency span between the minimum and maximum speed limits and the Speed Ref A Hi and Lo.
[Speed Ref A Hi] – [Maximum Speed] = 50 – 45 = 5 Hz and . . .
[Minimum Speed] – [Speed Ref A Lo] = 15 – 0 = 15 Hz
3. Multiply by the volts/hertz ratio
5 Hz x 0.2 Volts/Hz = 1 Volt
15 Hz x 0.2 Volts/Hz = 3 Volts
Here, the deadband is “shifted” due to the 50 Hz limitation. The command frequency from 0 to 3 volts on the analog input will be 15 Hz. After 3 volts, the frequency will increase at a rate of 0.2 volts per hertz up to 9 volts. After
9 volts on the analog input the frequency command will remain at 45 Hz.
Analog Outputs
Analog Outputs
2-19
Explanation
Each drive has one or more analog outputs that can be used to annunciate a wide variety of drive operating conditions and values.
The user selects the source for the analog output by setting [Analog Outx
Sel].
342
345
[Analog Out1 Sel]
Vector
[Analog Out2 Sel]
Selects the source of the value that drives the analog output.
Default:
Options:
0 “Output Freq”
See Table
Options
[Analog Out1 Lo] Value
Param. 341 = Signed Param. 341 = Absolute
[Analog Out1 Hi] Value
7
8
9
10
11
12
13
14*
5
6
3
4
0
1
1*
2
15*
16*
17*
18*
“Output Freq”
“Command Freq”
“Commanded Spd”
“Output Amps”
“Torque Amps”
“Flux Amps”
“Output Power”
“Output Volts”
“DC Bus Volts”
“PI Reference”
“PI Feedback”
“PI Error”
“PI Output”
“%Motor OL”
“%Drive OL”
“CommandedTrq”
“MtrTrqCurRef”
“Speed Ref”
“Speed Fdbk”
“Pulse In Ref”
0 Volts
–100%
–100%
–100%
–100%
0%
0%
–800%
–[Maximum Speed]
–[Maximum Speed]
–[Maximum Speed]
0 Amps
–200% Rated
0 Amps
0 kW
0 Volts
–800%
–[Maximum Speed]
–[Maximum Speed]
–25200.0 RPM
* Vector Control Option Only
0%
0%
0%
0%
0 Volts
0%
0%
0%
0 Hz
0 Hz
0 Hz/RPM
0 Amps
0 Amps
0 Amps
0 kW
0 Volts
0%
0 Hz
0 Hz
0 RPM
+[Maximum Speed]
+[Maximum Speed]
+[Maximum Speed]
200% Rated
200% Rated
200% Rated
200% Rated
120% Rated Input Volts
200% Rated Input Volts
100%
100%
100%
100%
100%
100%
+800%
+800%
+[Maximum Speed]
+[Maximum Speed]
+25200.0 RPM
012
135
136
137
138
220
219
001
002
003
004
005
007
006
Configuration
The PowerFlex 70 standard I/O analog output is permanently configured as a 0 -10 volt output. The output has 10 bits of resolution yielding 1024 steps.
The analog output circuit has a maximum 1.3% gain error and a maximum
7 mV offset error. For a step from minimum to maximum value, the output will be within 0.2% of its final value after 12ms.
The PowerFlex 700 standard I/O analog output is permanently configured as a 0-10 volt output. The output has 10 bits of resolution yielding 1024 steps. The analog output circuit has a maximum 1.3% gain error and a maximum 100 mV offset error. For a step from minimum to maximum value, the output will be within 0.2% of its final value after 12ms.
Absolute (default)
Certain quantities used to drive the analog output are signed, i.e. the quantity can be both positive and negative. The user has the option of having the absolute value (value without sign) of these quantities taken before the scaling occurs. Absolute value is enabled separately for each analog output via the bitmapped parameter [Anlg Out Absolut].
Important: If absolute value is enabled but the quantity selected for output is not a signed quantity, then the absolute value operation will have no effect.
2-20
Analog Outputs
Scaling Blocks
The user defines the scaling for the analog output by entering analog output voltages into two parameters, [Analog Out1 Lo] and [Analog Out1 Hi].
These two output voltages correspond to the bottom and top of the possible range covered by the quantity being output. The output voltage will vary linearly with the quantity being output. The analog output voltage will not go outside the range defined by [Analog Out1 Lo] and [Analog Out1 Hi].
Analog Output Configuration Examples
This section gives a few examples of valid analog output configurations and describes the behavior of the output in each case.
Example 1 -- Unsigned Output Quantity
•
[Analog Out1 Sel] = “Output Current”
•
[Analog Out1 Lo] = 1 volt
•
[Analog Out1 Hi] = 9 volts
10V
[Analog Out1 Hi]
Analog
Output Voltage
Output Current vs.
Analog Output Voltage
Marker Lines
[Analog Out1 Lo]
0V
0% 200%
Output Current
Note that analog output value never goes outside the range defined by
[Analog Out1 Lo] and [Analog Out1 Hi]. This is true in all cases, including all the following examples.
Example 2 -- Unsigned Output Quantity, Negative Slope
•
[Analog Out1 Sel] = “Output Current”
•
[Analog Out1 Lo] = 9 volts
•
[Analog Out1 Hi] = 1 volts
10V
[Analog Out1 Lo]
Analog
Output Voltage
Output Current vs.
Analog Output Voltage
Marker Lines
[Analog Out1 Hi]
0V
0% 200%
Output Current
This example shows that you can have [Analog Out1 Lo] greater than
[Analog Out1 Hi]. The result is a negative slope on the scaling from original quantity to analog output voltage. Negative slope could also be applied to any of the other examples in this section.
Analog Outputs
2-21
Example 3 – Signed Output Quantity, Absolute Value Enabled
•
[Analog Out1 Sel] = “Output Torque Current”
•
[Analog Out1 Lo] = 1 volt
•
[Analog Out1 Hi] = 9 volts
•
[Anlg Out Absolut] set so that absolute value is enabled for output 1.
10V
[Analog Out1 Hi]
Analog
Output Voltage
Output Torque Current vs.
Analog Output Voltage
Marker Lines
[Analog Out1 Lo]
0V
– 200% 0%
Output Torque Current
200%
Example 4 – Signed Output Quantity, Absolute Value Disabled
•
[Analog Out1 Sel] = “Output Torque Current”
•
[Analog Out1 Lo] = 1 volt
•
[Analog Out1 Hi] set to 9 volts
•
[Anlg Out Absolut] set so that absolute value is disabled for output 1.
10V
[Analog Out1 Hi]
Analog
Output Voltage
[Analog Out1 Lo]
0V
– 200% 0%
Output Torque Current
200%
Output Torque Current vs.
Analog Output Voltage
Marker Lines
2-22
Analog Outputs
Filtering
Software filtering will be performed on the analog outputs for certain signal sources, as specified in
. “Filter A” is one possible such filter, and
it is described later in this section. Any software filtering is in addition to any hardware filtering and sampling delays.
Table 2.B Software Filters
Quantity
Output Frequency
Filter
No extra filtering
Commanded Frequency No extra filtering
Output Current Filter A
Output Torque Current
Output Flux Current
Output Power
Output Voltage
Filter A
Filter A
Filter A
No extra filtering
DC Bus Voltage
PI Reference
PI Feedback
PI Error
PI Output
Filter A
No extra filtering
No extra filtering
No extra filtering
No extra filtering
Analog output software filters are specified in terms of the time it will take the output of the filter to move from 0% to various higher levels, given an instantaneous step in the filter input from 0% to 100%. The numbers describing filters in this document should be considered approximate; the actual values will depend on implementation.
Filter A is a single pole digital filter with a 162ms time constant. Given a
0% to 100% step input from a steady state, the output of Filter A will take
500ms to get to 95% of maximum, 810 ms to get to 99%, and 910 ms to get to 100%.
Auto/Manual
Auto/Manual
2-23
The intent of Auto/Manual is to allow the user to override the selected reference (referred to as the “auto” reference) by either toggling a button on the programming terminal (HIM), or continuously asserting a digital input that is configured for Auto/Manual.
•
“Alt” Function on the HIM
By toggling the “Alt” and “Auto/Man” function on the HIM, the user can switch the speed reference back and forth between the active “Auto” source (per drive programming and inputs) and the HIM requesting the manual control. “Manual” switches the Reference Source to the HIM,
“Auto” switches it back to drive programming.
The HIM manual reference can be preloaded from the auto source by enabling the [Man Ref Preload] parameter. With the preload function enabled, when the HIM requests Manual control, the current value of the auto source is loaded into the HIM reference before manual control is granted. This allows the manual control to begin at the same speed as the auto source, creating a smooth transition. If the preload function is disabled, the speed will ramp to whatever manual reference was present in the HIM at the time manual control was granted.
•
Digital Input
By toggling the digital input programmed as Auto/Manual, the user can switch the speed reference back and forth between the active “Auto” source (per drive programming and inputs) and the designated Terminal
Block manual reference. When this digital input is asserted, the TB will attempt to gain exclusive control (Manual) of the reference. If granted control of the reference, the specific source for the reference is determined by the parameter TB manual reference select.
The TB manual reference is selected in [TB Man Ref Sel]. The choices for this parameter are:
– Analog Input 1
– Analog Input 2
– MOP Level
– Analog Input 3 (PF700 Only)
– Pulse Input (PF700 Only)
– Encoder input (PF700 Only)
– Releasing this input sends the control back to the Auto source.
General Rules
The following rules apply to the granting and releasing of Manual control:
1. Manual control is requested through a one-time request (Auto/Man toggle, not continuously asserted). Once granted, the terminal holds
Manual control until the Auto/Man button is pressed again, which releases Manual control (i.e. back to Auto mode).
2-24
Auto/Manual
2. Manual control can only be granted to the TB or to a programming terminal (e.g. HIM) if Manual control is not already being exercised by the TB or another programming terminal at the time.
3. Manual control can only be granted to a terminal if no other device has
Local control already asserted (i.e. no other device has ownership of the
Local control function).
4. A HIM (or TB) with Manual control active can have it taken away if another DPI port requests, and is granted Local control. In this case when Local control is released the drive will not go back to Manual control, Manual control must be again requested (edge based request, see
above). This is true for both the HIM and the TB (i.e. if the TB switch was in the Manual position it must be switched to Auto and back to
Manual to get Manual control again).
5. The status indicator (point LED on LED HIM & Text on LCD HIM) will indicate when that particular terminal has been granted Manual control, not the fact any terminal connected has Manual control and not the fact that the particular terminal has simply asked for Manual control.
6. When Manual control is granted, the drive will latch and save the current reference value prior to entering Manual. When Manual control is then released the drive will use that latched reference for the drive until another DPI device arbitrates ownership and changes the reference to a different value.
7. If a terminal has Manual control and clears its DPI reference mask
(disallows reference ownership), then Manual control will be released.
By extension, if the drive is configured such that the HIM can not select the reference (via reference mask setting), then the drive will not allow the terminal to acquire Manual control.
8. If a terminal has Manual control and clears its DPI logic mask (allowing disconnect of the terminal), then Manual control will be released. By extension if the drive is configured such that the HIM can be unplugged
(via logic mask setting), then the drive will not allow the terminal to acquire Manual control. The disconnect also applies to a DPI HIM that executes a soft “Logout.”
9. If a com loss fault occurs on a DPI that has Manual control, then Manual control will be released as a consequence of the fault (on that port which had Manual control).
10.There will be no way to request and hence no support of the Auto/
Manual feature on old SCANport based HIMs.
11.You can not acquire Manual control if you are already an assigned source for the DPI port requesting Manual.
12.When a restore factory defaults is performed Manual control is aborted.
Auto Restart (Reset/Run)
2-25
Auto Restart (Reset/
Run)
The Auto Restart feature provides the ability for the drive to automatically perform a fault reset followed by a start attempt without user or application intervention. This allows remote or “unattended” operation. Only certain faults are allowed to be reset. Certain faults (Type 2) that indicate possible drive component malfunction are not resettable.
Caution should be used when enabling this feature, since the drive will attempt to issue its own start command based on user selected programming.
Configuration
This feature is configured through two user parameters
174 [Auto Rstrt Tries]
Sets the maximum number of times the drive attempts to reset a fault and restart.
Default:
Min/Max:
Display:
0
0/9
1
!
ATTENTION: Equipment damage and/or personal injury may result if this parameter is used in an inappropriate application. Do Not use this function without considering applicable local, national and international codes, standards, regulations or industry guidelines.
175 [Auto Rstrt Delay]
Sets the time between restart attempts when [Auto Rstrt Tries] is set to a value other than zero.
Default:
Min/Max:
Display:
1.0 Secs
0.5/30.0 Secs
0.1 Secs
175
174
Setting [Auto Rstrt Tries] to a value greater than zero will enable the Auto
Restart feature. Setting the number of tries equal to zero will disable the feature.
The [Auto Rstrt Delay] parameter sets the time, in seconds, between each reset/run attempt.
The auto-reset/run feature provides 2 status bits in [Drive Status 2] – an active status, and a countdown status.
210 [Drive Status 2]
Present operating condition of the drive.
Read Only
Bit # x
15 x
14
0
13
D M oto r O verld req
R eg im
B us F it
C urr L
A uto ct
R st A
A uto
R st C td n
A
0
12
0
11
0
10
0
9
0
8 x
7
0
6
g uto
Tu ning
D
C
B rakin
Sto pp in
Jo g gg in
R g unn in g
A ctive
R ead y
0
5
0
4
0
3
0
2
0
1
0
0
1 =Condition True
0 =Condition False x =Reserved
209
The typical steps performed in an Auto-Reset/Run cycle are as follows:
1. The drive is running and an auto-resettable fault occurs, tripping the drive.
2. After the number of seconds in [Auto Rstrt Delay], the drive will automatically perform an internal Fault Reset, resetting the faulted condition.
2-26
Auto Restart (Reset/Run)
3. The drive will then issue an internal Start command to start the drive.
4. If another auto-resettable fault occurs the cycle will repeat itself up to the number of attempts set in [Auto Rstrt Tries].
5. If the drive faults repeatedly for more than the number of attempts set in
[Auto Rstrt Tries] with less than five minutes between each fault, the auto-reset/run is considered unsuccessful and the drive remains in the faulted state.
6. Aborting an Auto-Reset/Run Cycle (see
for details).
7. If the drive remains running for five minutes or more since the last reset/ run without a fault, or is otherwise stopped or reset, the auto-reset/run is considered successful. The entire process is reset to the beginning and will repeat on the next fault.
Beginning an Auto-Reset/Run Cycle
The following conditions must be met when a fault occurs for the drive to begin an auto-reset/run cycle.
•
The fault must be defined as an auto-resettable fault
•
[Auto Rstrt Tries] setting must be greater than zero.
•
The drive must have been running, not jogging, not autotuning, and not stopping, when the fault occurred. (Note that a DC Hold state is part of a stop sequence and therefore is considered stopping.)
Aborting an Auto-Reset/Run Cycle
During an auto-reset/run cycle the following actions/conditions will abort the reset/run attempt process.
•
Issuing a stop command from any source. (Note: Removal of a 2-wire run-fwd or run-rev command is considered a stop assertion).
•
Issuing a fault reset command from any source.
•
Removal of the enable input signal.
•
Setting [Auto Rstrt Tries] to zero.
•
The occurrence of a fault which is not auto-resettable.
•
Removing power from the drive.
•
Exhausting an Auto-Reset/Run Cycle
After all [Auto Rstrt Tries] have been made and the drive has not successfully restarted and remained running for five minutes or more, the auto-reset/run cycle will be considered exhausted and therefore unsuccessful. In this case the auto-reset/run cycle will terminate and an additional fault, “Auto Rstrt Tries” (Auto Restart Tries) will be issued if bit
5 of [Fault Config 1] = “1.”
Bus Regulation
Bus Regulation
2-27
[Bus Reg Gain]
[Bus Reg Mode A, B]
Some applications, such as the hide tanning shown here, create an intermittent regeneration condition. When the hides are being lifted (on the left), motoring current exists. However, when the hides reach the top and fall onto a paddle, the motor regenerates power back to the drive, creating the potential for a nuisance overvoltage trip.
When an AC motor regenerates energy from the load, the drive DC bus voltage increases unless there is another means (dynamic braking chopper/ resistor, etc.) of dissipating the energy.
Motoring Regenerating
Without bus regulation, if the bus voltage exceeds the operating limit established by the power components of the drive, the drive will fault, shutting off the output devices to protect itself from excess voltage.
Single Seq 500 S/s
0V Fault @V bus
Max
3
Drive Output Shut Off
2
1
Ch1
Ch3
100mV
500mV
Ch2 100mV M 1.00s
Ch3 1.47 V
With bus regulation enabled, the drive can respond to the increasing voltage by advancing the output frequency until the regeneration is counteracted.
This keeps the bus voltage at a regulated level below the trip point.
Since the same integrator is used for bus regulation as for normal frequency ramp operation, a smooth transition between normal frequency ramp operation and bus regulation is accomplished.
The regulator senses a rapid rise in the bus voltage and activates prior to actually reaching the internal bus voltage regulation set point Vreg. This is important since it minimizes overshoot in the bus voltage when bus regulation begins thereby attempting to avoid an over-voltage fault.
2-28
Bus Regulation
The bus voltage regulation set point (Vreg) in the drive is fixed for each voltage class of drive. The bus voltage regulation set points are identical to the internal dynamic brake regulation set points VDB's.
DB Bus
Motor Speed
Output Frequency
To avoid over-voltage faults, a bus voltage regulator is incorporated as part of the acceleration/deceleration control. As the bus voltage begins to approach the bus voltage regulation point (Vreg), the bus voltage regulator increases the magnitude of the output frequency and voltage to reduce the bus voltage. The bus voltage regulator function takes precedence over the other two functions. See
The bus voltage regulator is shown in the lower one-third of
inputs to the bus voltage regulator are the bus voltage, the bus voltage regulation set point Vreg, proportional gain, integral gain, and derivative gain. The gains are intended to be internal values and not parameters. These will be test points that are not visible to the user. Bus voltage regulation is selected by the user in the Bus Reg Mode parameter.
Operation
Bus voltage regulation begins when the bus voltage exceeds the bus voltage regulation set point Vreg and the switches shown in
move to the positions shown in
.
Table 2.C Switch Positions for Bus Regulator Active
SW 1
Bus Regulation Limit
SW 2
Bus Reg
SW 3
Open
SW 4
Closed
SW 5
Don’t Care
Current Limit Level
Bus Regulation
2-29
Figure 2.1 Bus Voltage Regulator, Current Limit and Frequency Ramp.
Current Limit
Derivative Gain
Block
Magnitude
Calculator
U Phase Motor Current
W Phase Motor Current
SW 3
PI Gain Block
I Limit,
No Bus Reg
Limit
0
SW 1
Acc/Dec Rate
No Limit
I Limit,
No Bus Reg
Jerk
Ramp
Jerk
Clamp
No Limit
SW 2
Bus Reg
Frequency Set Point
Maximum Frequency, Minimum Speed, Maximum Speed, Overspeed Limit
Frequency
Ramp
(Integrator)
+
+
+
Frequency Reference (to Ramp Control, Speed Ref, etc.)
Speed Control (Slip Comp, Process PI, etc)
Frequency
Reference
+
+
SW 5
Speed
Control
Mode
Frequency
Limits
Output Frequency
Bus Voltage Regulation Point, V reg
SW 4
PI Gain Block
Bus Reg On
Derivative
Gain Block
Bus Voltage (Vbus)
Bus Voltage Regulator
The derivative term senses a rapid rise in the bus voltage and activates the bus regulator prior to actually reaching the bus voltage regulation set point
Vreg. The derivative term is important since it minimizes overshoot in the bus voltage when bus regulation begins thereby attempting to avoid an over-voltage fault. The integral channel acts as the acceleration or deceleration rate and is fed to the frequency ramp integrator. The proportional term is added directly to the output of the frequency ramp integrator to form the output frequency. The output frequency is then limited to a maximum output frequency.
Bus voltage regulation is the highest priority of the three components of this controller because minimal drive current will result when limiting the bus voltage and therefore, current limit will not occur.
2-30
Bus Regulation
!
ATTENTION: The “adjust freq” portion of the bus regulator function is extremely useful for preventing nuisance overvoltage faults resulting from aggressive decelerations, overhauling loads, and eccentric loads. It forces the output frequency to be greater than commanded frequency while the drive's bus voltage is increasing towards levels that would otherwise cause a fault; however, it can also cause either of the following two conditions to occur.
1. Fast positive changes in input voltage (more than a 10% increase within 6 minutes) can cause uncommanded positive speed changes; however an “OverSpeed Limit” fault will occur if the speed reaches [Max Speed] + [Overspeed Limit]. If this condition is unacceptable, action should be taken to 1) limit supply voltages within the specification of the drive and, 2) limit fast positive input voltage changes to less than 10%. Without taking such actions, if this operation is unacceptable, the “adjust freq” portion of the bus regulator function must be disabled (see parameters 161 and 162).
2. Actual deceleration times can be longer than commanded deceleration times; however, a “Decel Inhibit” fault is generated if the drive stops decelerating altogether. If this condition is unacceptable, the “adjust freq” portion of the bus regulator must be disabled (see parameters 161 and 162). In addition, installing a properly sized dynamic brake resistor will provide equal or better performance in most cases.
Note: These faults are not instantaneous and have shown test results that take between 2 and 12 seconds to occur.
PowerFlex 70/700
The user selects the bus voltage regulator using the Bus Reg Mode parameters. The available modes include:
• off
• frequency regulation
• dynamic braking
• frequency regulation as the primary regulation means with dynamic braking as a secondary means
• dynamic braking as the primary regulation means with frequency regulation as a secondary means
The bus voltage regulation setpoint is determined off of bus memory (a means to average DC bus over a period of time). The following graph and tables describe the operation.
Table 2.D
Voltage Class DC Bus Memory DB On Setpoint
240 < 342V DC 375V DC
480
> 342V DC
< 685 VDC
Memory + 33V DC
750V DC
600
> 685 VDC
< 856 VDC
> 856 VDC
Memory + 65V DC
937V DC
Memory + 81V DC
DB Off Setpoint
On – 4V DC
On – 8V DC
On – 10V DC
Bus Regulation
2-31
880
815
750
685
650
DB Turn On
DB Turn Off ff
DB Turn O n
DB Turn O
Bus M em ory
509
453
320 360 460 484
AC Volts
528 576
If [Bus Reg Mode A], parameter 161 is set to “Dynamic Brak”:
The Dynamic Brake Regulator is enabled. The “blue” (upper) DB turn on and turn off curves apply. In “Dynamic Brak” mode adjust frequency control is turned off. See
If [Bus Reg Mode A], parameter 161 is set to “Both-Frq 1st”:
Both regulators enabled, the operating point of the Frequency Bus Voltage
Regulator is lower than that of the Dynamic Brake Regulator. The adjust frequency setpoint follows the “red” (lower) DB turn off curve (
If [Bus Reg Mode A], parameter 161 is set to “Adjust Freq”:
The Frequency Bus Voltage Regulator is enabled. The adjust frequency setpoint follows the “red” (lower) DB turn on curve. See
.
If [Bus Reg Mode A], parameter 161 is set to “Both-DB 1st”:
Both regulators enabled, the operating point of the Dynamic Brake
Regulator is lower than that of the Frequency Bus Voltage Regulator. The adjust frequency setpoint follows the “red” (lower) DB turn on curve(
Table 2.E
Voltage Class DC Bus Memory DB On Setpoint
240 < 342V DC Memory + 50V DC
480
> 342V DC
< 685V DC
375V DC
Memory + 33V DC
Memory + 100V DC
750 VDC
DB Off Setpoint
On – 4V DC
On – 8V DC
600
> 685V DC
< 856V DC
> 856V DC
Memory + 65V DC
Memory + 125V DC
937 VDC
Memory + 81V DC
On – 10V DC
2-32
Cable, Control
Cable, Control
For analog and encoder cable selection, see
. Digital input cable selection can be found on
Cable, Motor Lengths
The length of cable between the drive and motor may be limited by various application parameters. The 2 primary areas of concern are Reflected Wave and Cable charging.
The Reflected Wave phenomenon, also known as transmission line effect, can produce very high peak voltages on the motor due to voltage reflection.
Allen-Bradley drives have patented software that limits the voltage peak to
2 times the DC bus voltage or 1600 volts, whichever is greater. The software also reduces the number of occurrences. Note that many motors have inadequate insulation systems to tolerate high peaks. See
for more details.
Refer to
for measuring cable lengths when concerned about
Reflected Wave. The actual lead length for each motor must be measured or calculated based on the lead length for that motor only. Diagram A shows 2 motors, each 300 feet from the drive. Motor protection decisions are based on a 300 foot cable length (not 600). If the motors need protection at this distance, then both motors must be dealt with individually. In some cases, a single device placed at the drive output or near the motors may protect both motors. Diagram B shows 1 motor at 50 feet and one at 550 feet. It is likely that the motor that is close to the drive (50 feet) will not need protection, but the motor farther from the drive (550 feet) may. Again, each motor must be considered individually based on its distance from the drive.
Cable charging occurs because of the capacitance, phase-to-phase or phase-to-ground, inherent in the length of cable. The current that is used to charge the cable capacitance detracts from the overall current capability of the drive and reduces the availability of torque producing current for the motor. This can result in poor motor performance, motor stalls under full load and nuisance drive overcurrent tripping. In general, shielded cable has higher cable capacitance and will require higher cable charging current.
Refer to
for measuring cable lengths when concerned about
cable charging. In this case, it is the total amount of cable connected to the drive that must be considered. Diagram A shows 2 motors, each 300 feet from the drive. The drive must be capable of supplying enough current to charge the total length (600 feet) plus the needed current to produce desired torque in the motors. If a drive is unable to provide sufficient current for both cable charging and motor torque, then a larger drive with adequate current rating should be substituted. Diagram B shows 1 motor at 50 feet and one at 550 feet. Again, the drive must be capable of supplying enough current to charge the total length (600 feet), plus the current to produce desired torque in the motors. In fact, diagrams A, B, C and D will all require the same cable charging installation guidelines because they all have total cable lengths of 600 feet.
lists the maximum cable lengths recommended for PowerFlex drives.
Distances listed consider both reflected wave amplitude and cable charging
Cable, Motor Lengths
2-33
current. These distances are advisory only and are not intended to assure a trouble free installation. Differences in the cable chosen and other factors can affect maximum distance.
Figure 2.2 How to Measure Motor Cable Lengths Limited by Capacitance
B C D A
91.4 (300)
91.4 (300)
15.2 (50)
167.6 (550) 182.9 (600)
15.2 (50)
152.4 (500)
15.2 (50)
15
25
3
5
7.5
10
1
2
480V HP
Rating
0.5
All examples represent motor cable length of 182.9 meters (600 feet).
8
4
8
4
8
4
8
4
8
4
8
4
8
8
4
8
4
Carrier Freq.
(kHz)
4
25
NA
NA
NA
NA
NA
NA
25
NA
20
20
20
20
1000 volt motor
Shielded
50
Shielded
25
40
NA
NA
NA
20
NA
NA
NA
NA
NA
NA
25
25
NA
NA
NA
NA
20
20
20
20
PowerFlex 700 Maximum Motor Lead Lengths (in Feet)
75
NA
NA
NA
NA
NA
NA
75
NA
40
40
40
40
1200 volt motor
Unshielded Shielded
75 50
Shielded
220
75
NA
NA
NA
40
NA
NA
NA
220
NA
NA
NA
NA
NA
NA
40
40
NA
NA
NA
NA
50
40
50
40
NA
NA
NA
420
420
NA
NA
NA
NA
420
420
620
620
275
NA
NA
NA
NA
NA
NA
520
NA
620
520
620
420
220
NA
NA
NA
1488 volt motor
NEMA MG1-1998
Unshielded Shielded
320 220
Shielded
420
220
NA
NA
NA
420
NA
NA
NA
NA
NA
NA
420
420
NA
NA
NA
NA
420
420
620
620
NA
NA
NA
620
520
NA
NA
NA
NA
620
520
620
620
NA
NA
NA
NA
NA
NA
NA
NA
NA
NA
NA
NA
Unshielded
NA
NA
NA
NA
NA
NA
Notes
– 1000V motor is defined as one assembled without phase paper. 1200V motor is defined as one assembled with phase paper. 1488V motor meets NEMA MG 1-1998 section 31 standard where the insulation can withstand voltage spikes of 3.1 x rated motor voltage due to inverter operation (inverter duty motor). 1600V motor is a
1329R or 1329L. Operation at nominal line voltage. To increase the distance between the drive and the motor, some mitigation device needs to be added to the system (i.e. an RWR or Terminator).
– NA = Data Not Available at time of publication.
2-34
Cable, Motor Lengths
480V HP
Rating
0.5
1
2
3
5
7.5
10
15
20
4
6
8
10
6
8
10
2
2
4
8
10
4
6
10
2
6
8
2
4
4
6
8
10
6
8
10
2
2
4
Carrier
Freq.
(kHz)
6
8
10
2
4
8
10
4
6
10
2
6
8
2
4
NA
NA
NA
NA
NA
NA
NA
NA
NA
NA
NA
NA
NA
NA
NA
NA
NA
NA
NA
NA
NA
NA
NA
NA
NA
NA
NA
NA
NA
NA
NA
NA
NA
NA
NA
NA
NA
NA
NA
NA
NA
NA
NA
1000 Volt Motor
Shld.
(1)
Shld.
(2)
NA
NA
60
60
60
60
60
70
70
70
70
70
70
70
70
70
50
50
50
50
80
80
80
50
70
70
80
80
70
70
70
70
70
70
70
80
80
70
70
50
80
80
80
50
50
50
50
50
50
50
50
50
50
50
40
50
50
50
40
40
40
40
NA
NA
NA
NA
NA
NA
NA
NA
NA
NA
NA
NA
NA
NA
NA
NA
NA
NA
NA
NA
NA
NA
NA
NA
NA
NA
NA
NA
NA
NA
NA
40
40
40
40
40
40
40
40
40
40
40
40
40
40
40
40
40
40
40
40
30
30
30
30
40
40
40
30
1200 Volt Motor
Un-Shld.
Shld.
Shld.
40
40
NA
NA
175
175
NA
NA
NA
NA
175
175
175
275
NA
NA
NA
NA
NA
NA
NA
NA
275
250
250
240
250
250
250
200
300
300
300
300
280
280
280
300
220
220
280
280
220
220
220
220
400
400
600
400
200
160
160
300
600
400
400
300
300
300
300
PowerFlex 70 Maximum Motor Lead Lengths (in Feet) - No External Devices
80
80
80
80
80
80
80
60
80
80
80
60
60
60
60
NA
NA
NA
NA
NA
NA
NA
NA
NA
NA
NA
NA
NA
NA
NA
NA
NA
NA
NA
NA
NA
NA
NA
NA
NA
NA
NA
NA
NA
NA
NA
60
60
60
60
80
80
80
60
75
75
80
80
75
75
75
75
75
75
75
75
55
55
55
55
50
50
50
55
1488 Volt Motor
NEMA MG1-1998
Un-Shld.
Shld.
Shld.
60
60
NA
NA
175
175
NA
NA
NA
NA
175
175
175
275
NA
NA
NA
NA
NA
NA
NA
NA
275
250
250
250
250
250
250
250
400
400
400
300
400
300
300
400
400
400
450
400
250
425
400
425
600
600
600
600
600
600
600
300
600
600
600
400
400
400
400
600
600
560
500
600
600
580
600
580
550
600
600
400
600
600
600
500
400
400
400
300
280
260
240
Un-Shld.
150
150
150
150
150
350
600
480
600
600
600
600
600
520
600
600
600
600
600
600
560
500
400
600
600
600
600
340
380
600
600
600
600
600
560
440
NA
NA
NA
NA
NA
NA
NA
NA
NA
NA
NA
NA
NA
NA
NA
NA
NA
NA
NA
NA
NA
NA
NA
NA
NA
NA
NA
NA
NA
NA
NA
600
520
400
320
560
400
360
600
380
380
600
600
260
600
520
520
500
400
360
260
180
170
160
160
130
130
130
180
1600 Volt Motor
1329 R/L
Un-Shld.
Shld.
Shld.
150
130
NA
NA
175
175
NA
NA
NA
NA
175
175
175
275
NA
NA
NA
NA
NA
NA
NA
NA
275
250
250
250
250
250
250
250
400
400
400
300
400
300
300
400
400
400
450
400
250
425
400
425
600
600
600
600
600
600
600
300
600
600
600
400
400
400
400
(1)
(2)
Cable is Belden 295xx series or equivalent.
Cable is Alcatel C1202 or equivalent. Shielded cable with twisted conductors and no filler.
Notes
– 1000V motor is defined as one assembled without phase paper. 1200V motor is defined as one assembled with phase paper. 1488V motor meets NEMA MG 1-1998 section 31 standard where the insulation can withstand voltage spikes of 3.1 x rated motor voltage due to inverter operation (inverter duty motor). 1600V motor is a
1329R or 1329L. Operation at nominal line voltage. To increase the distance between the drive and the motor, some mitigation device needs to be added to the system (i.e. an RWR or Terminator).
– Shading indicates limited due to cable charging current.
– NA = Data Not Available at time of publication.
Cable, Power
Cable, Power
2-35
!
ATTENTION: National Codes and standards (NEC, VDE, BSI etc.) and local codes outline provisions for safely installing electrical equipment. Installation must comply with specifications regarding wire types, conductor sizes, branch circuit protection and disconnect devices. Failure to do so may result in personal injury and/or equipment damage.
A variety of cable types are acceptable for drive installations.
Unshielded
For many installations, unshielded cable or loose conductors are adequate, provided they can be separated from sensitive circuits. As an approximate guide, allow a minimum spacing of 0.3 meters (1 foot). Avoid long parallel runs. It is recommended that individual wires have XLPE insulation. As a minimum, any insulation must be at least 15 mils thick. Wire with PVC insulation (i.e. THHN, see more below) is acceptable if no moisture is present and the PVC insulation meets the 15 mil minimum. Recommended tray cable has XLPE for individual conductors and a PVC outer jacket.
Shielded/Armored
Shielded cable is recommended if sensitive circuits or devices are connected or mounted to the machinery driven by the motor.
Figure 2.3 Recommended Shielded Power Wire
Location
Standard
(Option 1)
Standard
(Option 2)
Class I & II;
Division I & II
Rating/Type
600V, 90
°
C (194
°
F)
XHHW2/RHW-2
Anixter
B209500-B209507,
Belden 29501-29507, or equivalent
Tray rated 600V, 90
°
C
(194
°
F) RHH/RHW-2
Anixter OLF-7xxxxx or equivalent
Tray rated 600V, 90
°
C
(194
°
F) RHH/RHW-2
Anixter 7V-7xxxx-3G or equivalent
Description
•
Four tinned copper conductors with XLPE insulation.
•
Copper braid/aluminum foil combination shield and tinned copper drain wire.
•
PVC jacket.
•
Three tinned copper conductors with XLPE insulation.
•
5 mil single helical copper tape (25% overlap min.) with three bare copper grounds in contact with shield.
•
PVC jacket.
•
Three bare copper conductors with XLPE insulation and impervious corrugated continuously welded aluminum armor.
•
Black sunlight resistant PVC jacket overall.
•
Three copper grounds on #10 AWG and smaller.
Based on field and internal testing, Rockwell Automation/Allen-Bradley has determined that conductors manufactured with Poly Vinyl Chloride
(PVC) wire insulation are subject to a variety of manufacturing inconsistencies which can lead to premature insulation degradation when used with IGBT drives that produce the reflected wave phenomena.
Flame-retardant heat-resistant thermoplastic insulation is the type of insulation listed in the NEC code for the THHN wire designation. This type of insulation is commonly referred to as PVC. In addition to manufacturing inconsistencies, the physical properties of the cable can change due to environment, installation and operation, which can also lead to premature insulation degradation. The following is a summary of our findings:
2-36
Cable, Power
Manufacturing Inconsistencies and their Effects on Cable Life
Due to manufacturing inconsistencies, the following conditions can exist:
•
PVC insulation material may have a dielectric constant ranging between
4 and 8 depending on the manufacturer. The higher the dielectric constant, the lower the dielectric strength (and voltage withstand to transients). A single IGBT drive output may have reflected wave transient voltage stresses of up to twice (2 per unit) the DC bus voltage between its own output wires. Multiple drive output wires in a single conduit or wire tray further increase output wire voltage stress between multi-drive output wires that are touching. Drive #1 may have a (+) 2 pu stress while drive #2 may simultaneously have a (–) 2 pu stress. Wires with dielectric constants (>4) cause the voltage stress to shift to the air gap between the wires that are barely touching. This electric field may be high enough to ionize the air surrounding the wire insulation and cause a partial discharge mechanism (corona) to occur. The electric field distribution between wires increases the possibility for corona which further produces ozone. This attacks the PVC insulation and produces carbon tracking, leading to the susceptibility of insulation breakdown.
•
Due to inconsistencies in manufacturing processes or wire pulling, air voids can also occur in the THHN wire between the nylon jacket and
PVC insulation. Because the dielectric constant of air is much lower than the dielectric constant of the insulating material, the transient reflected wave voltage may appear across the small air void capacitance. The
Corona Inception Voltage (CIV) for the air void may be reached which further produces ozone, which attacks the PVC insulation and produces carbon tracking, leading to the susceptibility of insulation breakdown as in the above case.
•
Asymmetrical construction of the insulation has also been observed for some manufacturers of PVC wire. A wire with a 15 mil specification was observed to have an insulation thickness of 10 mil at some points. The smaller the insulation thickness, the less voltage the wire can withstand.
Installation, Operation and Environmental Considerations
•
THHN jacket material has a relatively brittle nylon that lends itself to damage (i.e. nicks and cuts) when pulled through conduit on long wire runs. This issue is of even greater concern when the wire is being pulled through multiple 90 degree bends in the conduit. It is these nicks that may be a starting point for corona that leads to insulation degradation.
•
During operation, the conductor heats up and a “coldflow” condition may occur with PVC insulation at points where the unsupported weight of the wire may stretch the insulation. This has been observed at right angle bends where wire is dropped down to equipment from an above wireway. This “coldflow” condition produces thin spots in the insulation which lowers the cable’s voltage withstand capability.
•
The NEC 1996 code defines “dry, damp and wet” locations (7-31) and permits the use of heat-resistant thermoplastic wire in both dry and damp applications (Table 310-13). However, PVC insulation material is more susceptible to absorbing moisture than XLPE (Cross Linked
Polyethylene) insulation material (XHHN-2) identified for use in wet
Cable, Power
2-37
locations. Because the PVC insulating material absorbs moisture, the
Corona Inception Voltage insulation capability of the “damp” or “wet”
THHN was found to be less than 1/2 of the same wire when “dry”. For this reason, certain industries where water is prevalent in the environment have refrained from using THHN wire with IGBT drives.
Cable Recommendations for New & Existing Installations of IGBT Drives in Wet
Locations
•
Belden YR41709 cable is a PVC jacketed, shielded type TC with XLPE conductor insulation designed to meet NEC code designation XHHW-2
(wet locations per NEC 1996, Table 310-13). Based on Rockwell
Automation research, tests have determined the Belden YR41709 is notably superior to loose wires in dry, damp and wet applications and can significantly reduce capacitive coupling and common mode noise.
Other cable types for wet locations include those in the table above
summarizes the previous considerations and explanations.
Because applications can vary widely, the information in the flowchart is intended to be used only as a guideline in the decision-making process.
Figure 2.4 Wire Selection Flowchart
Selecting Wire to Withstand Reflected Wave Voltage for New and Existing Wire Installations in Conduit or Cable Trays
PVC
Conductor
Insulation
DRY
(Per NEC 7-31)
Conductor
Environment
230V
Insulation
Thickness
15 mil
400/460V
20 mil or > (1)
RWR or
Terminator
Reflected Wave
Reducer?
No RWR or
Terminator
< 50 ft.
Cable
Length
Single Drive,
Single Conduit or Wire Tray
> 50 ft.
# of
Drives in Same
Conduit or Wire
Tray
Multiple Drives in Single Conduit or Wire Tray
15 mil PVC
Not
Recommended
USE XLPE or > 20 mil
XLPE
WET
(Per NEC code Table 7-31)
575V
Reflected Wave
Reducer?
No RWR or Terminator
15 mil PVC
Not
Recommended
USE XLPE or > 20 mil
RWR or
Terminator
OK for < 600V AC
System
No RWR or
Terminator required
XLPE (XHHW-2)
Insulation for
<600V AC
System
No RWR or
Terminator
Required
(1) The mimimum wire size for PVC cable with 20 mil or greater insulation is 10 gauge.
See NEC Guidelines
(70-196 Adjustment Factors) for
Maximum Conductor Derating &
Maximum Wires in Conduit or Tray
2-38
Cable, Standard I/O
Cable, Standard I/O
For analog and encoder cable selection, see
. Digital input cable selection can be found on
CabIe Trays and
Conduit
Conduit must be magnetic steel and be installed so as to provide a continuous electrical path through the conduit itself.
Care must be taken when pulling wire to avoid nicking the wire.
Nylon-coated wire such as THHN or THWN is subject to insulation damage when it is pulled through conduit, particularly if 90º bends are present. Nicking can significantly reduce or remove the insulation. Water based lubricants should not be used with nylon coated wire such as THHN.
Important: Because of the nature of the drive PWM output and the reflected wave phenomenon, it is preferable to have each set of drive motor/power cables in an individual conduit. If this is not possible, do not route more than 3 sets of drive cables in one conduit. It is important that the allowable fill rates specified in the applicable national or local codes Not Be Exceeded.
!
ATTENTION: To avoid a possible shock hazard caused by induced voltages, unused wires in the conduit must be grounded at both ends. For the same reason, if a drive sharing a conduit is being serviced or installed, all drives using this conduit should be disabled. This will help minimize the possible shock hazard from
“cross coupled” motor leads.
When laying cable in cable trays, do not randomly distribute them. Cables for each drive should be bundled together and anchored to the tray (see
). A minimum separation of one cable width should be maintained between bundles to reduce overheating and cross-coupling.
Current flowing in one set of cables can induce a hazardous voltage and/or excessive noise on the cable set of another drive, even when no power is applied to the second drive. Dividers also provide excellent separation.
Figure 2.5 Cable Placement
Random Placement
Not Recommended
or
Bundled & Anchored to Tray
Recommended
For further information, refer to “Wiring and Grounding Guidelines for
PWM AC Drives,” publication DRIVES-IN001A-EN-P.
Carrier (PWM)
Frequency
Carrier (PWM) Frequency
2-39
See
page 1-4 for derating guidelines as they relate to carrier frequency.
In general, the lowest possible switching frequency that is acceptable for any particular application is the one that should be used. There are several benefits to increasing the switching frequency. Refer to
. Note the output current at 2 kHz and 4 kHz. The “smoothing” of
the current waveform continues all the way to 10 kHz.
Figure 2.6 Current at 2 kHz PWM Frequency
Figure 2.7 Current at 4 kHz PWM Frequency
The benefits of increased carrier frequency include less motor heating and lower audible noise. An increase in motor heating is considered negligible and motor failure at lower switching frequencies is very remote. The higher switching frequency creates less vibration in the motor windings and laminations thus, lower audible noise. This may be desirable in some applications.
Some undesirable effects of higher switching frequencies include derating ambient temperature vs. load characteristics of the drive, higher cable charging currents and higher potential for common mode noise.
A very large majority of all drive applications will perform adequately at
2-4 kHz.
2-40
CE Conformity
CE Conformity
EMC Instructions
CE Conformity
Conformity with the Low Voltage (LV) Directive and Electromagnetic
Compatibility (EMC) Directive has been demonstrated using harmonized
European Norm (EN) standards published in the Official Journal of the
European Communities. PowerFlex Drives comply with the EN standards listed below when installed according to the User and Reference Manuals.
CE Declarations of Conformity are available online at:
http://www.ab.com/certification/ce/docs .
Low Voltage Directive (73/23/EEC)
•
EN50178 Electronic equipment for use in power installations.
EMC Directive (89/336/EEC)
•
EN61800-3 Adjustable speed electrical power drive systems Part 3:
EMC product standard including specific test methods.
General Notes
•
If the adhesive label is removed from the top of the drive, the drive must be installed in an enclosure with side openings less than 12.5 mm (0.5
in.) and top openings less than 1.0 mm (0.04 in.) to maintain compliance with the LV Directive.
•
The motor cable should be kept as short as possible in order to avoid electromagnetic emission as well as capacitive currents.
•
Use of line filters in ungrounded systems is not recommended.
•
PowerFlex drives may cause radio frequency interference if used in a residential or domestic environment. The user is required to take measures to prevent interference, in addition to the essential requirements for CE compliance listed below, if necessary.
•
Conformity of the drive with CE EMC requirements does not guarantee an entire machine or installation complies with CE EMC requirements.
Many factors can influence total machine/installation compliance.
•
PowerFlex drives can generate conducted low frequency disturbances
(harmonic emissions) on the AC supply system. More information regarding harmonic emissions can be found in the PowerFlex Reference
Manual.
Essential Requirements for CE Compliance
Conditions 1-6 listed below must be satisfied for PowerFlex drives to meet the requirements of EN61800-3.
1. Standard PowerFlex CE compatible Drive.
2. Review important precautions/attention statements throughout the User
Manual before installing the drive.
3. Grounding as described on
CE Conformity
2-41
4. Output power, control (I/O) and signal wiring must be braided, shielded cable with a coverage of 75% or better, metal conduit or equivalent attenuation.
5. All shielded cables should terminate with the proper shielded connector.
6. Conditions in the appropriate table (
,
Table 2.F PowerFlex 70 – EN61800-3 EMC Compatibility
(1)
Frame Drive Description
A Drive Only
Drive with any Comm Option
Drive with ControlNet
B Drive Only
Drive with any Comm Option
Drive with ControlNet
C Drive Only
Drive with any Comm Option
Drive with ControlNet
D Drive Only
Drive with any Comm Option
Drive with ControlNet
Second Environment
Restrict Motor
Cable to
40 m (131 ft.)
✔
✔
✔
✔
✔
✔
✔
✔
✔
✔
✔
✔
Internal
Filter
Option
–
✔
✔
✔
–
–
–
–
–
–
–
–
External
Filter
✔
✔
✔
–
–
–
–
–
–
–
–
–
Input
Ferrite (2)
–
–
✔
–
–
✔
–
–
✔
–
–
✔
Table 2.G PowerFlex 70 – EN61800-3 First Environment Restricted Distribution
(1)
Frame Drive Description
A Drive Only
Drive with any Comm Option
Drive with ControlNet
B Drive Only
Drive with any Comm Option
Drive with ControlNet
C Drive Only
Drive with any Comm Option
Drive with ControlNet
D Drive Only
Drive with any Comm Option
Drive with ControlNet
First Environment Restricted Distribution
Restrict Motor
Cable to
12 m (40 ft.)
–
–
✔
✔
✔
✔
–
✔
✔
✔
✔
✔
Restrict Motor
Cable to
40 m (131 ft.)
✔
✔
✔
–
–
–
–
–
–
–
–
–
Internal
Filter
Option
–
–
–
✔
✔
✔
–
–
–
–
–
–
External
Filter
✔
✔
✔
–
–
–
–
–
–
–
–
–
–
–
✔
–
–
✔
Comm
Cable
Ferrite (2)
–
–
✔
–
–
✔
Common
Mode
Core (3)
–
–
–
–
✔
✔
✔
–
–
–
–
–
2
3
0
1
Table 2.H PowerFlex 700 EN61800-3 EMC Compatibility
(1)
Second Environment
Restrict Motor Cable to 30 m (98 ft.)
Any Drive and Option
✔
✔
✔
✔
First Environment Restricted Distribution
Restrict Motor Cable to 150 m (492 ft.)
Any Drive and Option
✔
✔
✔
✔
External Filter Required
✔
✔
✔
✔
2-42
Copy Cat
(1) External filters for First Environment installations and increasing motor cable lengths in Second Environment installations are available. Roxburgh models KMFA (RF3 for UL installations) and MIF or Schaffner FN3258 and FN258 models are recommended.
Refer to the following page and http://www.deltron-emcon.com and http://www.mtecorp.com (USA) or
http://www.schaffner.com, respectively.
(2) Two turns of the blue comm option cable through a Ferrite Core (Frames A, B, C Fair-Rite #2643102002, Frame
D Fair-Rite #2643251002 or equivalent).
(3) Refer to the 1321 Reactor and Isolation Transformer Technical Data publication, 1321-TD001x for 1321-Mxxx selection information.
Recommended Filters
(1)
Manufacturer Drive Type
Deltron
PowerFlex 70
Frame
A
B w/o Filter
B w/Filter
C
D
Manufacturer
Part Number
KMF306A
KMF310A
KMF306A
KMF318A
KMF336A
D w/o DC CM Capacitor KMF336A
PowerFlex 700 0
1
KMF318A
KMF325A
2 KMF350A
2 w/o DC CM Capacitor KMF350A
3 KMF370A
3 w/o DC CM Capacitor KMF370A
Schaffner
PowerFlex 70 A
B w/o Filter
B w/Filter
C
FN3258-7-45 –
FN3258-7-45 100
FN3258-7-45 –
FN3258-16-45 –
PowerFlex 700 0
1
D FN3258-30-47 0
D w/o DC CM Capacitor FN3258-30-47 –
FN3258-16-45 –
FN3258-30-47 –
200
176
150
150
–
–
150
–
Class
A
(Meters)
25
50
100
–
2 FN3258-42-47 50
2 w/o DC CM Capacitor FN3258-42-47 150
3 FN3258-75-52 100
3 w/o DC CM Capacitor FN3258-75-52 150
100
100
50
50
100
150
150
150
50
150
5
50
B
(Meters)
25
25
150
150
50
150
100
150
0
150
100
150
Manufacturer
Part Number
Class
A
(Meters)
–
–
MIF306
–
–
–
–
–
–
–
–
–
MIF330
–
MIF316
–
–
–
–
–
–
–
–
–
–
–
–
–
–
–
–
–
–
–
FN258-30-07 –
– –
–
–
–
–
–
–
–
–
–
–
–
–
–
–
–
–
150
–
100
–
150
–
–
–
B
(Meters)
–
–
–
–
–
–
–
–
150
–
(1) Use of these filters assumes that the drive is mounted in an EMC enclosure.
Copy Cat
Some PowerFlex drives have a feature called Copy Cat, which allows the user to upload a complete set of parameters to the LCD HIM. This information can then be used as backup or can be transferred to another drive by downloading the memory.
Generally, the transfer process manages all conflicts. If a parameter from
HIM memory does not exist in the target drive, if the value stored is out of range for the drive or the parameter cannot be downloaded because the drive is running, the download will stop and a text message will be issued. The user than has the option of completely stopping the download or continuing after noting the discrepancy for the parameter that could not be downloaded. These parameters can then be adjusted manually.
The LCD HIM will store a number of parameter sets (memory dependant) and each individual set can be named for clarity.
Current Limit
Current Limit
2-43
[Current Lmt Sel]
[Current Lmt Val]
[Current Lmt Gain]
There are 6 ways that the drive can protect itself from overcurrent or overload situations:
•
Instantaneous Overcurrent trip
•
Software Instantaneous Trip
•
Software Current Limit
•
Overload Protection IT
•
Heatsink temperature protection
•
Thermal Manager
1. Instantaneous Overcurrent - This is a feature that instantaneously trips or faults the drive if the output current exceeds this value. The value is fixed by hardware and is typically 250% of drive rated amps. The Fault code for this feature is F12 “HW Overcurrent.” This feature cannot be defeated or mitigated.
2. Software Instantaneous Trip - There could be situations where peak currents do not reach the F12 “HW Overcurrent” value and are sustained long enough and high enough to damage certain drive components. If this situation occurs, the drives protection scheme will cause an F36
“SW Overcurrent” fault. The point at which this fault occurs is fixed and stored in drive memory.
3. Software Current Limit - This is a software feature that selectively faults the drive or attempts to reduce current by folding back output voltage and frequency if the output current exceeds this value. The [Current Lmt
Val] parameter is programmable between approximately 25% and 150% of drive rating. The reaction to exceeding this value is programmable with [Shear Pin Fault]. Enabling this parameter creates an F63 “Shear
Pin Fault.” Disabling this parameter causes the drive to use Volts/Hz fold back to try and reduce load.
The frequency adjust or fold back operation consists of two modes. In the primary mode of current limit operation, motor phase current is sampled and compared to the Current Limit setting in the [Current Lmt
Val]. If a current “error” exists, error is scaled by an integral gain and fed to the integrator. The output of this integrator is summed with the proportional term and the active speed mode component to adjust the output frequency and the commanded voltage. The second mode of current limit operation is invoked when a frequency limit has been reached and current limit continues to be active. At this point, a current regulator is activated to adjust the output voltage to limit the current.
When the current limit condition ceases or the output voltage of the current regulator attempts to exceed the open loop voltage commands, control is transferred to the primary current limit mode or normal ramp operation.
2-44
Current Limit
4. Overload Protection I
2
T - This is a software feature that monitors the output current over time and integrates per IT. The base protection is
110% for 1 minute or the equivalent I
2
T value (i.e. 150% for 3 seconds, etc.). If the IT integrates to maximum, an F64 “Drive Overload” fault will occur. The approximate integrated value can be monitored via the
[Drive OL Count] parameter.
5. Heatsink Temperature Protection - The drive constantly monitors the heatsink temperature. If the temperature exceeds the drive maximum, a
“Heatsink OvrTemp” fault will occur. The value is fixed by hardware at a nominal value of 100 degrees C. This fault is generally not used for overcurrent protection due to the thermal time constant of the heatsink. It is an overload protection.
6. Thermal manager (see
Drive Overload on page 2-76 ).
Datalinks
Datalinks
2-45
Programmable
Controller
I/O Image Table
Output Image
Block Transfer
Logic Command
Analog Reference
WORD 3
WORD 4
WORD 5
WORD 6
WORD 7
Input Image
Block Transfer
Logic Status
Analog Feedback
WORD 3
WORD 4
WORD 5
WORD 6
WORD 7
A Datalink is one of the mechanisms used by PowerFlex drives to transfer data to and from a programmable controller. Datalinks allow a parameter value to be changed without using an Explicit Message or Block Transfer.
Datalinks consist of a pair of parameters that can be used independently for
16 bit transfers or in conjunction for 32 bit transfers. Because each Datalink consists of a pair of parameters, when enabled, each Datalink occupies two
16 or 32-bit words in both the input and output image tables, depending on configuration. A user enters a parameter number into the Datalink parameter. The value that is in the corresponding output data table word in the controller is then transferred to the parameter whose number has been placed in the Datalink parameter. The following example demonstrates this concept. The object of the example is to change Accel and Decel times “on the fly” under PLC control.
The user makes the following PowerFlex drive parameter settings:
Parameter 300 [Data In A1] = 140 (the parameter number of [Accel Time 1]
Parameter 301 [Data In A2] = 142 (the parameter number of [Decel Time 1]
Remote I/O
Communication
Module
Adjustable Frequency
AC Drive
Datalink A
Datalink A
Parameter/Number
Data In A1
Data In A2
300
301
Data Out A1
Data Out A2
310
311
In the PLC data Table, the user enters Word 3 as a value of 100 (10.0 Secs) and word 4 as a value of 133 (13.3 seconds). On each I/O scan, the parameters in the PowerFlex drive are updated with the value from the data table:
Accel Time P140 = 10.0 seconds (value from output image table Word 3)
Decel Time P142 = 13.3 seconds (value from output image table Word 4).
Any time these values need to be changed, the new values are entered into the data table, and the parameters are updated on the next PLC I/O scan.
2-46
Datalinks
Rules for Using Datalinks
1. 1. A Datalink consists of 4 words, 2 for Datalink x IN and 2 for Datalink x Out. They cannot be separated or turned on individually.
2. Only one communications adapter can use each set of Datalink parameters in a PowerFlex drive. If more than one communications adapter is connected to a single drive, multiple adapters must not try to use the same Datalink.
3. Parameter settings in the drive determine the data passed through the
Datalink mechanism
4. When you use a Datalink to change a value, the value is not written to the Non-Volatile Storage (EEprom memory). The value is stored in volatile memory (RAM) and lost when the drive loses power.
32-Bit Parameters using 16-Bit Datalinks
To read (and/or write) a 32-bit parameter using 16-bit Datalinks, typically both Datalinks (A,B,C,D) are set to the 32-bit parameter. For example, to read Parameter 09 - [Elapsed MWh], both Datalink A1 and A2 are set to
“9.” Datalink A1 will contain the least significant word (LSW) and Datalink
A2 the most significant word (MSW). In this example, the parameter 9 value of 5.8MWh is read as a “58” in Datalink A1
Datalink
A1
A2
Most/Least Significant Word Parameter
LSW 9
MSW 9
Data (decimal)
58
0
Regardless of the Datalink combination, x1 will always contain the LSW and x2 will always contain the MSW.
In the following examples Parameter 242 - [Power Up Marker] contains a value of 88.4541 hours.
Datalink
A1
A2
Most/Least Significant Word Parameter
LSW 242
-Not Used0
Data (decimal)
32573
0
Datalink
A1
A2
Most/Least Significant Word Parameter
-Not Used0
MSW 242
Data (decimal)
0
13
Even if non-consecutive Datalinks are used (in the next example, Datalinks
A1 and B2 would not be used), data is still returned in the same way.
Datalink
A2
B1
Most/Least Significant Word Parameter
MSW 242
LSW 242
Data (decimal)
13
32573
32-bit data is stored in binary as follows:
MSW 2
31
through 2
16
LSW 2
15
through 2
0
Example
Parameter 242 - [Power Up Marker] = 88.4541 hours
MSW = 13 decimal
= 1101 binary
= 2
16
+ 2
18
+ 2
19
= 851968
LSW = 32573
851968 + 32573 = 884541
DC Bus Voltage /
Memory
Decel Time
DC Bus Voltage / Memory
2-47
[DC Bus Voltage] is a measurement of the instantaneous value. [DC Bus
Memory] is a heavily filtered value or “nominal” bus voltage. Just after the pre-charge relay is closed during initial power-up bus pre-charge, bus memory is set equal to bus voltage. Thereafter it is updated by ramping at a very slow rate toward Vbus. The filtered value ramps at approximately 2.4V
DC per minute (for a 480V AC drive).
Bus memory is used as the base line to sense a power loss condition. If the drive enters a power loss state, the bus memory will also be used for recovery (i.e. pre-charge control or inertia ride through upon return of the power source) upon return of the power source. Update of the bus memory is blocked during deceleration to prevent a false high value caused by a regenerative condition.
[Decel Time 1, 2]
Sets the rate at which the drive ramps down its output frequency after a Stop command or during a decrease in command frequency (speed change). The rate established is the result of the programmed Decel Time and the
Minimum and Maximum Frequency, as follows:
Maximum Speed
Decel Time
= Decel Rate (Hz/sec)
Two decel times exist to allow the user to change rates “on the fly” via PLC command or digital input. The selection is made by programming [Decel
Time 1] & [Decel Time 2] and then using one of the digital inputs ([Digital
Inx Sel]) programmed as “Decel 2” (see
However, if a PLC is used, manipulate the bits of the command word as shown below.
(1
)
(1
)
(1
)
Bit #
0
15
0
Spd Ref ID 2 Decel 1 Accel 2
0 0 1 1 1 0
14 13 12 11 10 9 8
1
7
0
0
0
1
0
0
1
0
0
1
0
0
1
0
0
0
0
6
Accel 1
Accel 2
Decel 1
Decel 2
0
Re ver se d
Forwar Clear F ault
0 1 1 0
5 4 3 2 1
t
Star
0
0
Stop
1 =Condition True
0 =Condition False x =Reserved
The effectiveness of these bits or digital inputs can be affected by [Decel
Mask]. See
for more information.
Times are adjustable in 0.1 second increments from 0.0 seconds to 3600.0
seconds.
In its factory default condition, when no decel select inputs are closed and no time bits are “1,” the default deceleration time is [Decel Time 1] and the rate is determined as above.
2-48
Diagnostics
Diagnostics
Diagnostic Parameters – PF700 Vector Control Only
The following parameters can only be viewed when “2, Unused” is selected in parameter 196, [Param Access Lvl].
No. Parameter Name & Description
500 [KI Current Limit]
Current Limit Integral gain. This gain is applied to the current limit error signal to eliminate steady state current limit error.
A larger value increases overshoot during a step of motor current/load.
501 [KD Current Limit]
Current Limit Derivative gain. This gain is applied to the sensed motor current to anticipate a current limit condition. A larger value reduces overshoot of the current relative to the current limit value.
502 [Bus Reg ACR Kp]
This proportional gain, in conjunction with P160, adjusts the output frequency of the drive during a bus limit or inertia ride through condition. The output frequency is adjusted in response to an error in the active, or torque producing, current to maintain the active bus limit, or inertia ride through bus reference. A larger value of gain reduces the dynamic error of the active current.
503 [Jerk]
Values
Default:
Min/Max:
Units:
Default:
Min/Max:
Units:
Default:
Min/Max:
Units:
Default:
This parameter allows you to adjust the amount of S-Curve, or “Jerk” applied to the Acc/Dec rate. To enable the Jerk feature, bit 1 of P56 must be set high.
504 [Ln Ls Bus Reg Kp]
This proportional gain adjusts the active current command during an inertia-ride through condition, in response to a bus error. A larger value of gain reduces the dynamic error of the bus voltage as compared to the bus voltage reference.
505 [Ln Ls Bus Reg Kd]
Line Loss Bus Reg Kd is a derivative gain, which is applied to the sensed bus voltage to anticipate dynamic changes and minimize them. A larger value reduces overshoot of the bus voltage relative to the inertia-ride through bus voltage reference.
506 [Angl Stblty Gain]
Min/Max:
Units:
Default:
Min/Max:
Units:
Default:
Min/Max:
Units:
Default:
Angle Stability Gain adjusts the electrical angle to maintain stable motor operation.
An increase in the value increases the angle adjustment.
507 [Volt Stblty Gain]
Adjusts the output voltage to maintain stable motor operation. An increase in the value increases the output voltage adjustment.
508 [Stability Filter]
The Stability Filter coefficient is used to adjust the bandwidth of a low pass filter.
The smaller the value of this coefficient, the lower the bandwidth of the filter.
Min/Max:
Units:
Default:
Min/Max:
Units:
Default:
Min/Max:
Units:
900
2/30000
1
500
0/10000
1
500
0/10000
1
64
0/32767
1
128
0/32767
1
1750
0/32767
1
No. Parameter Name & Description
509 [Lo Freq Reg KpId]
This proportional gain adjusts the output voltage at very low frequency in response to the reactive, or d-axis, motor current. A larger value increases the output voltage change.
510 [Lo Freq Reg KpIq]
The proportional gain adjusts the output voltage at very low frequency in response to the active, or q-axis, motor current. A larger value increases the output voltage change.
511 [Cur Reg Ki]
This integral gain adjusts the output voltage in response to the q and d axis motor currents. A larger value increases the output voltage change.
512 [Cur Reg Kp]
This proportional gain adjusts the output voltage in response to the q and d axis motor currents. A larger value increases the output voltage change.
523 [Bus Utilization]
This value sets the drive output voltage limit as a percentage of the fundamental output voltage when operating in 6 step mode. Values above 95% increase harmonic content and jeopardize control stability. This output voltage limit is strictly a function of input line and resulting bus voltage.
524 [PWM Type Sel]
Values
Default:
Min/Max:
Units:
Default:
Min/Max:
Units:
Default:
Min/Max:
Units:
Default:
Min/Max:
Units:
Default:
Min/Max:
Units:
Default:
Allows selection of the active PWM type.
A value of 0 is default, and results in a change of PWM method at approximately
2/3 of rated motor frequency. If this is unacceptable for harmonic or audible reasons, a value of 1 disables the change.
536 [Flux Brake Ki]
Proportional gain for the Flux Regulator
Min/Max:
Units:
Default:
537 [Flux Brake Kp]
Integral gain for the Flux Regulator
Min/Max:
Units:
Default:
538 [Rec Delay Time]
TBD
Min/Max:
Units:
Default:
513 [PWM DAC Enable]
Reserved. Do Not Adjust
Min/Max:
Units:
Default:
Min/Max:
Units:
Default: 514
515
516
517
[DAC47-A]
[DAC47-B]
[DAC47-C]
[DAC47-D]
Reserved. Do Not Adjust
518 [Host DAC Enable]
Reserved. Do Not Adjust
Min/Max:
Units:
Default:
Min/Max:
Units:
32767
0/32767
1
32767
0/32767
1
95.0%
85.0/100.0%
0.1%
1000
1/30000
1
0
0/7432
1
Diagnostics
2-49
2-50
Diagnostics
s 519
520
521
522
No. Parameter Name & Description
[DAC55-A]
[DAC55-B]
[DAC55-C]
[DAC55-D]
Reserved. Do Not Adjust
525 [Torq Adapt Speed]
Values
Default:
Min/Max:
Units:
Default:
Selects the operating frequency/speed at which the adaptive torque control regulators become active as a percent of motor nameplate frequency.
526 [Torq Reg Enable]
Enables or disables the torque regulator
527 [Torq Reg Kp]
Proportional gain for the torque regulator
Min/Max:
Units:
Default:
Min/Max:
Units:
Default:
528 [Torq Reg Ki]
Integral gain for the torque regulator
529 [Torq Reg Trim]
Min/Max:
Units:
Default:
Min/Max:
Units:
Default:
Torque Regulator trim gain. A larger value increases the developed torque.
Typically used to compensate for losses between developed and shaft torque.
530 [Slip Reg Enable]
Enables or disables the slip frequency regulator.
531 [Slip Reg Kp]
Min/Max:
Units:
Default:
Min/Max:
Units:
Default:
Proportional gain for the slip frequency regulator.
532 [Slip Reg Ki]
Integral gain for the slip frequency regulator.
533 [Flux Reg Enable]
Enables or disables the flux regulator.
Min/Max:
Units:
Default:
Min/Max:
Units:
Default:
534 [Flux Reg Kp]
Proportional gain for the flux regulator.
Min/Max:
Units:
Default:
Min/Max:
Units:
Default: 535 [Flux Reg Ki]
Integral gain for the flux regulator.
539 [Freq Reg Kp]
Proportional gain for the Frequency
Regulator
540 [Freq Reg Ki]
Min/Max:
Units:
Default:
Min/Max:
Units:
Default:
Integral gain for the Frequency Regulator
[Hi Flux Reg Ki]
Min/Max:
Units:
Default:
TBD
[Hi Flux Reg Kp]
Min/Max:
Units:
Default:
TBD Min/Max:
Units:
0
0/7432
1
33.0%
0.0/100.0%
0.1%
0
0/1
1
32
0/32767
1
512
0/32767
1
1.0
0.5/1.5
0.1
0/1
1
400
0/32767
1
128
0/32767
1
0
0/1
1
160
0/32767
1
64
0/32767
1
0
Digital Inputs
Digital Inputs
2-51
Cable Selection
Important points to remember about I/O wiring:
•
Always use copper wire.
•
Wire with an insulation rating of 600V or greater is recommended.
•
Control and signal wires should be separated from power wires by at least 0.3 meters (1 foot).
Table 2.I Recommended Control Wire for Digital I/O
Type
Shielded
Wire Type(s)
Unshielded Per US NEC or applicable national or local code
Multi-conductor shielded cable such as Belden 8770(or equiv.)
Description
–
0.750 mm
2
(18AWG), 3 conductor, shielded.
Minimum Insulation
Rating
300V,
60 degrees C
(140 degrees F)
Wiring Examples
See User Manual.
There are 6 digital (discrete) inputs (numbered 1 through 6) available at the terminal block.
PowerFlex 70
Each digital input has a maximum response/pass through/function execution time of 25ms. For example, no more than 25ms should elapse from the time the level changes at the Start input to the time voltage is applied to the motor.
There is both hardware and software filtering on these inputs. The hardware provides an average delay of 12ms from the time the level changes at the input to the earliest time that the software can detect the change. The actual time can vary between boards from 7 to 17ms, but any particular board should be consistent to within 1% of its average value. The amount of software filtering is not alterable by the user.
PowerFlex 700
Each digital input has a maximum response/pass through/function execution time of 25ms. This means that, for example, no more than 25ms should elapse from the time the level changes at the Start input to the time voltage is applied to the motor.
Digital Input Configuration
Inputs are configured for the required function by setting a [Digital Inx Sel] parameter (one for each input). These parameters cannot be changed while the drive is running.
2-52
Digital Inputs
PowerFlex 700 Digital Input Selection
361
362
363
364
365
366
[Digital In1 Sel]
[Digital In2 Sel]
[Digital In3 Sel]
[Digital In4 Sel]
[Digital In5 Sel]
[Digital In6 Sel]
(11)
Default:
Default:
Default:
Default:
Default:
Default:
4
5
18
15
16
17
“Stop – CF”
“Start”
“Auto/ Manual”
“Speed Sel 1”
“Speed Sel 2”
“Speed Sel 3”
Selects the function for the digital inputs.
(1)
(2)
(3)
Speed Select Inputs.
3 2 1 Auto Reference Source
1
1
0
1
1
0
0
0
0
0
1
1
0
0
1
1
0
1
0
1
0
1
0
1
Reference A
Reference B
Preset Speed 2
Preset Speed 3
Preset Speed 4
Preset Speed 5
Preset Speed 6
Preset Speed 7
To access Preset Speed 1, set [Speed
Ref x Sel] to “Preset Speed 1”.
Type 2 Alarms - Some digital input programming may cause conflicts that will result in a Type 2 alarm.
Example: [Digital In1 Sel] set to “5,
Start” in 3-wire control and [Digital
In2 Sel] set to 7 “Run” in2-wire.
Refer to User Manual for information on resolving this type of conflict.
Vector Control Option Only.
3 2 1 Spd/Trq Mode
1
1
0
1
1
0
0
0
0
0
1
1
0
0
1
1
0
1
0
1
0
1
0
1
Zero Torque
Spd Reg
Torque Reg
Min Spd/Trq
Max Spd/Trq
Sum Spd/Trq
Absolute
Zero Trq
Options: “Not Used”
“Enable”
(8)(10)
“Clear Faults”(CF)
(4)
“Aux Fault”
“Stop – CF”
(10)
“Start”
(5)(9)
“Fwd/ Reverse”
(5)
“Run”
(6)(10)
“Run Forward”
(6)
“Run Reverse”
“Jog”
(5)
“Jog1”
(6)
(2)(5)
“Jog Forward”
(6)
“Jog Reverse”
(6)
“Stop Mode B”
“Bus Reg Md B”
“Speed Sel 1-3”
“Auto/ Manual”
(1)
(7)
“Local”
“Acc2 & Dec2”
“Accel 2”
“Decel 2”
“MOP Inc”
“MOP Dec”
“Excl Link”
“PI Enable”
“PI Hold”
“PI Reset”
“Pwr Loss Lvl”
“Precharge En”
“Spd/Trq Sel1-3”
“Jog 2”
(2)
(2,3)
25
26
27
28
29
30
31-33
34
21
22
23
24
15-17
18
19
20
11
12
13
14
7
8
9
10
5
6
3
4
0
1
2
(4)
When [Digital Inx Sel] is set to option 2 “Clear Faults” the Stop button cannot be used to clear a fault condition.
(5)
Typical 3-Wire Inputs - Requires that only 3-wire functions are chosen.
Including 2-wire selections will cause a type 2 alarm.
(6)
Typical 2-Wire Inputs - Requires that only 2-wire functions are chosen. Including 3-wire selections will cause a type 2 alarm. See User Manual for conflicts.
(7)
Auto/Manual - Refer to User Manual for details.
(8)
Opening an “Enable” input will cause the motor to coast-to-stop, ignoring any programmed Stop modes.
(9)
A “Dig In ConflictB” alarm will occur if a “Start” input is programmed without a
“Stop” input.
(10)
Refer to the Sleep-Wake Mode Attention statement on User Manual .
(11)
A dedicated hardware enable input is available via a jumper selection. Refer to User Manual for further information.
100
156
162
096
140
194
380
384
388
124
Digital Inputs
2-53
PowerFlex 70 Digital Input Selection
361
[Digital In1 Sel]
Default: 4
362
363
364
365
366
[Digital In2 Sel]
[Digital In3 Sel]
[Digital In4 Sel]
[Digital In5 Sel]
[Digital In6 Sel]
Selects the function for the digital inputs.
(1)
When [Digital Inx Sel] is set to option 2
“Clear Faults” the Stop button cannot be used to clear a fault condition.
(2)
Typical 3-Wire Inputs.
Requires that only 3-wire functions are chosen. Including 2-wire selections will cause a type 2 alarm.
(3)
Typical 2-Wire Inputs.
Requires that only 2-wire functions are chosen. Including 3-wire selections will cause a type 2 alarm.
(4)
Speed Select Inputs.
Default:
Default:
Default:
Default:
Default:
Options:
3 2 1 Auto Reference Source
1
1
1
1
0
0
0
0
0
0
1
1
0
0
1
1
0
1
0
1
0
1
0
1
Reference A
Reference B
Preset Speed 2
Preset Speed 3
Preset Speed 4
Preset Speed 5
Preset Speed 6
Preset Speed 7
To access Preset Speed 1, set [Speed
Ref A Sel] or [Speed Ref B Sel] to
“Preset Speed 1”.
Type 2 Alarms
Some digital input programming may cause conflicts that will result in a Type
2 alarm. Example: [Digital In1 Sel] set to 5 “Start” in 3-wire control and [Digital
In2 Sel] set to 7 “Run” in 2-wire.
Refer to Alarm Descriptions in the User
Manual for information on resolving this type of conflict.
(5)
Auto/Manual - Refer to User Manual for details.
(6)
Opening an “Enable” input will cause the motor to coast-to-stop, ignoring any programmed Stop modes.
(7)
A “Dig In ConflictB” alarm will occur if a
“Start” input is programmed without a
“Stop” input.
20
21
22
23
16
17
18
19
24
25
26
27
28
12
13
14
15
8
9
10
11
6
7
4
5
2
3
0
1
5
18
15
16
17
“Stop – CF”
(CF = Clear Fault)
“Start”
“Auto/ Manual”
“Speed Sel 1”
“Speed Sel 2”
“Speed Sel 3”
“Not Used”
“Enable”
(6)
“Clear Faults”
(1)
“Aux Fault”
“Stop – CF”
(2)
“Start”
(2)(7)
“Fwd/ Reverse”
(2)
“Run”
(3)
“Run Forward”
(3)
“Run Reverse”
(3)
“Jog”
(2)
“Jog Forward”
“Jog Reverse”
“Stop Mode B”
“Bus Reg Md B”
“Speed Sel 1”
(4)
“Speed Sel 2”
(4)
“Speed Sel 3”
(4)
“Auto/ Manual”
(5)
“Local”
“Acc2 & Dec2”
“Accel 2”
“Decel 2”
“MOP Inc”
“MOP Dec”
“Excl Link”
“PI Enable”
“PI Hold”
“PI Reset”
100
156
162
096
140
194
380
384
388
124
The available functions are defined in
2-54
Digital Inputs
Table 2.J Digital Input Function List
Input Function Name
Stop - CF
Run Forward
Run Reverse
Run
Start
Forward/Reverse
Jog
Jog Forward
Jog Reverse
Speed Select 3
Speed Select 2
Speed Select 1
Auto/Manual
Purpose
Stop drive
Clear Faults (open to closed transition)
Run in forward direction (2-wire start mode)
Run in reverse direction (2-wire start mode)
Run in current direction (2-wire start mode)
Start drive (3-wire start mode)
Set drive direction (3-wire mode only)
Jog drive
Jog in forward direction
Jog in reverse direction
Select which Speed reference the drive uses.
Accel 2
Decel 2
Accel 2 & Decel 2
MOP Increment
MOP Decrement
Stop Mode B
Bus Regulation Mode B
PI Enable
PI Hold
PI Reset
Auxiliary Fault
Local Control
Allows terminal block to assume complete control of Speed
Reference.
Select acceleration rate 1 or 2.
Select deceleration rate 1 or 2.
Select acceleration rate 1 and deceleration rate 1 or acceleration rate 2 and deceleration rate 2.
Increment MOP (Motor Operated Pot Function Speed ref)
Decrement MOP (Motor Operated Pot Function Speed ref)
Select Stop Mode A (open) or B (closed)
Select which bus regulation mode to use
Enable Process PI loop.
Hold integrator for Process PI loop at current value.
Clamp integrator for Process PI loop to 0.
Open to cause “auxiliary fault” (external string).
Allows terminal block to assume complete control of drive logic.
Clear Faults
Enable
Clear faults and return drive to ready status.
Open input causes drive to coast to stop, disallows start.
Exclusive Link Exclusive Link – digital input is routed through to digital output, no other use.
Power Loss Level (PowerFlex 700 only) Selects between using fixed value for power loss level and getting the level from a parameter
Precharge Enable (PowerFlex 700 only) If common bus configuration, denotes whether drive is disconnected from DC bus or not. Controls precharge sequence on reconnection to bus.
Input Function Detailed Descriptions
•
Stop - Clear Faults
An open input will cause the drive to stop and become “not ready”. A closed input will allow the drive to run.
If “Start” is configured, then “Stop - Clear Faults” must also be configured. Otherwise, a digital input configuration alarm will occur.
“Stop - Clear Faults” is optional in all other circumstances.
An open to closed transition is interpreted as a Clear Faults request. The drive will clear any existing faults. The terminal block bit must be set in the [Fault Mask] and [Logic Mask] parameters in order for the terminal block to clear faults using this input function.
Digital Inputs
2-55
If the “Clear Faults” input function is configured at the same time as
“Stop - Clear Faults”, then it will not be possible to reset faults with the
“Stop - Clear Faults” input.
•
Run Forward, Run Reverse
An open to closed transition on one input or both inputs while drive is stopped will cause the drive to run unless the “Stop - Clear Faults” input function is configured and open.
The table below describes the basic action taken by the drive in response to particular states of these input functions.
Run Forward Run Reverse Action
Open Open Drive stops, terminal block relinquishes direction ownership.
Open Closed
Closed Open
Drive runs in reverse direction, terminal block takes direction ownership.
Drive runs in forward direction, terminal block takes direction ownership.
Closed Closed Drive continues to run in current direction, but terminal block maintains direction ownership.
If one of these input functions is configured and the other one isn’t, the above description still applies, but the unconfigured input function should be considered permanently open.
The terminal block bit must be set in the [Start Mask], [Direction Mask], and [Logic Mask] parameters in order for the terminal block to start or change the direction of the drive using these inputs.
Important: Direction control is an “Exclusive Ownership” function (see
Owners). This means that only one control device (terminal block, DPI device, HIM, etc.) at a time is allowed to control direction at a time. The terminal block must become direction “owner” before it can be used to control direction.
If another device is currently the direction owner (as indicated by [Direction Owner]), it will not be possible to
start the drive or change direction by using the terminal block digital inputs programmed for both Run and
Direction control (i.e. Run/Fwd).
If one or both of these input functions is configured, it will not be possible to start or jog the drive from any other control device. This is true irrespective of the state of the [Start Mask], [Direction Mask], and
[Logic Mask] parameters.
•
Run
An open to closed transition on this input while drive is stopped will cause the drive to run in the currently selected direction unless the “Stop
- Clear Faults” input function is configured and open.
If this input is open, then the drive will stop.
The purpose of this input function is to allow a 2-wire start while the direction is being controlled by some other means.
2-56
Digital Inputs
The terminal block bit must be set in the [Start Mask] and [Logic Mask] parameters in order for the terminal block to start the drive using this input.
If the “Run” input function is configured, it will not be possible to start or jog the drive from any other control device. This is true irrespective of the state of the [Start Mask], [Direction Mask], and [Logic Mask] parameters.
The Effects of 2-Wire Start Modes on Other DPI Devices
The “Run/Stop” and “Run Fwd/Rev” start modes are also called
“2-wire” start modes, because they allow the drive to be started and stopped with only a single input and two wires. When a “2-wire” terminal block start mode is put into effect by the user, the drive can no longer be started or jogged from any other control device (i.e. HIM, network card, etc.). This restriction persists as long as one or more of
“Run”, “Run Forward”, and “Run Reverse” are configured. This is true even if the configuration is otherwise illegal and causes a configuration alarm. See
for typical 2 and 3-wire configurations.
•
Start
An open to closed transition while the drive is stopped will cause the drive to run in the current direction, unless the “Stop – Clear Faults” input function is open.
The terminal block bit must be set in the [Start Mask] and [Logic Mask] parameters in order for the terminal block to start or change the direction of the drive using these inputs.
If “Start” is configured, then “Stop - Clear Faults” must also be configured.
•
Forward/Reverse
This function is one of the ways to provide direction control when the
Start / Stop / Run functions of the drive are configured as 3 – wire control.
An open input sets direction to forward. A closed input sets direction to reverse. If state of input changes and drive is running or jogging, drive will change direction.
The terminal block bit must be set in the [Direction Mask] and [Logic
Mask] parameters in order for the terminal block to select the direction of the drive using this input function.
Important: Direction control is an “Exclusive Ownership” function (see
Owners). This means that only one control device (terminal block, DPI device, HIM, etc.) at a time is allowed to control direction at a time. The terminal block must become direction “owner” before it can be used to control direction.
If another device is currently the direction owner (as indicated by [Direction Owner]), it will not be possible to
Digital Inputs
2-57 start the drive or change direction by using the terminal block digital inputs programmed for both Run and
Direction control (i.e. Run/Fwd).
Important: Because an open condition (or unwired condition) commands
Forward, the terminal block seeks direction ownership as soon as this input function is configured, which may happen at power-up. In order for the terminal block to actually gain ownership, the masks must be set up correctly (see above) and no other device can currently have direction ownership. Once the terminal block gains direction ownership, it will retain it until shutdown, until the [Direction Mask] or [Logic Mask] bits for the terminal block are cleared, or until this input function is no longer configured
•
Jog
Jog is essentially a non-latched “run/start” command. An open to closed transition while drive is stopped causes drive to start (jog) in the current direction. When the input opens while drive is running (jogging), the drive will stop.
The drive will not jog while running or while the “Stop - Clear Faults” input is open. Start has precedence.
!
ATTENTION: If a normal drive start command is received while the drive is jogging, the drive will switch from jog mode to run mode. The drive will not stop, but may change speed and/or change direction.
The terminal block bit must be set in the [Jog Mask] and [Logic Mask] parameters in order for the terminal block to cause the drive to jog using this input function.
•
Jog Forward, Jog Reverse
An open to closed transition on one input or both inputs while drive is stopped will cause the drive to jog unless the “Stop - Clear Faults” input function is configured and open. The table below describes the actions taken by the drive in response to various states of these input functions.
Jog Forward Jog Reverse Action
Open Open Drive will stop if already jogging, but can be started by other means. Terminal block relinquishes direction ownership.
Open Closed
Closed Open
Drive jogs in reverse direction. Terminal block takes direction ownership.
Drive jogs in forward direction. Terminal block takes direction ownership.
Closed Closed Drive continues to jog in current direction, but terminal block maintains direction ownership.
If one of these input functions is configured and the other one isn’t, the above description still applies, but the unconfigured input function should be considered permanently open.
2-58
Digital Inputs
The drive will not jog while drive is running or while “Stop - Clear
Faults” input is open. Start has precedence
.
!
ATTENTION: If a normal drive start command is received while the drive is jogging, the drive will switch from jog mode to run mode. The drive will not stop, but may change speed and/or change direction.
The terminal block bit must be set in the [Jog Mask], [Direction Mask], and [Logic Mask] parameters in order for the terminal block to cause the drive to jog using these input functions.
Important: Direction control is an “Exclusive Ownership” function (see
Owners). This means that only one control device (terminal block, DPI device, HIM, etc.) at a time is allowed to control direction at a time. The terminal block must become direction “owner” before it can be used to control direction.
If another device is currently the direction owner (as indicated by [Direction Owner]), it will not be possible to
jog the drive or change direction by using the terminal block digital inputs programmed for both Run and
Direction control (i.e. Run/Fwd).
If another device is not currently the direction owner (as indicated by
[Direction Owner]) and the terminal block bit is set in the [Direction
Mask] and [Logic Mask] parameters, the terminal block becomes direction owner as soon as one (or both) of the “Jog Forward” or “Jog
Reverse” input functions is closed.
•
Speed select 1, 2, and 3
One, two, or three digital input functions can be used to select the speed reference used by the drive, and they are called the Speed Select input functions. The current open/closed state of all Speed Select input functions combine to select which source is the current speed reference.
There are 8 possible combinations of open/closed states for the three input functions, and thus 8 possible parameters can be selected. The 8 parameters are: [Speed Ref A Sel], [Speed Ref B Sel], and [Preset Speed
2] through [Preset Speed 7].
If the Speed Select input functions select [Speed Ref A Sel] or [Speed
Ref B Sel], then the value of that parameter further selects a reference source. There are a large number of possible selections, including all 7 presets.
If the input functions directly select one of the preset speed parameters, then the parameter contains a frequency that is to be used as the reference.
Digital Inputs
2-59
The terminal block bit must be set in the [Reference Mask] and [Logic
Mask] parameters in order for the reference selection to be controlled from the terminal block using the Speed Select inputs functions.
Important: Reference Control is an “Exclusive Ownership” function
(see
Owners on page 2-109 ). This means that only one
control device (terminal block, DPI device, HIM, etc.) at a time is allowed to select the reference source. The terminal block must become direction “owner” before it can be used to control direction. If another device is currently the reference owner (as indicated by [Reference Owner]), it will not be possible to select the reference by using the terminal block digital inputs, and the Speed Select Inputs will have no effect on which reference the drive is currently using.
Because any combination of open/closed conditions (or unwired condition) commands a reference source, terminal block seeks ownership of reference selection as soon as any of these input functions are configured, which may happen at power-up. In order for the terminal block to actually gain ownership, the masks must be set up correctly (see above) and no other device can currently have reference ownership.
Once the terminal block gains reference ownership, it will retain it until shutdown, until the [Reference Mask] or [Logic Mask] bits for the terminal block are cleared, or until none of the digital inputs are configured as Speed Select input functions.
The Speed Select input function configuration process involves assigning the functionality of the three possible Speed Select input functions to physical digital inputs. The three Speed Select inputs functions are called “Speed Select 1”, “Speed Select 2”, and “Speed
Select 3”, and they are assigned to physical inputs using the [Digital Inx
Sel] parameters.
The table below describes the various reference sources that can be selected using all three of the Speed Select input functions.
Speed Select 3 Speed Select 2 Speed Select 1 Parameter that determines Reference
Open Open Open [Speed Ref A Sel]
Open
Open
Open
Closed
Closed
Open
[Speed Ref B Sel]
[Preset Speed 2]
Open
Closed
Closed
Closed
Closed
Closed
Open
Open
Closed
Closed
Closed
Open
Closed
Open
Closed
[Preset Speed 3]
[Preset Speed 4]
[Preset Speed 5]
[Preset Speed 6]
[Preset Speed 7]
If any of the three Reference Select input functions are not configured, then the software will still follow the table, but will treat the unconfigured inputs as if they are permanently open.
As an example, the table below describes what reference selections can be made if “Speed Select 1” is the only configured input function. This
2-60
Digital Inputs configuration allows a single input to choose between [Speed Ref A Sel] and [Speed Ref B Sel].
Speed Select 1
Open
Closed
Selected Parameter that determines Reference
[Speed Ref A Sel]
[Speed Ref B Sel]
As another example, describes what reference selections can be made if the “Speed Select 3” and “Speed Select 2” input functions are configured, but “Speed Select 1” is not.
Speed Select 3 Speed Select 2 Selected Parameter that determines reference
Open Open [Speed Ref A Sel]
Open
Closed
Closed
Closed
Open
Closed
[Preset Speed 2]
[Preset Speed 4]
[Preset Speed 6]
•
Auto/Manual
The Auto/Manual facility is essentially a higher priority reference select.
It allows a single control device to assume exclusive control of reference select, irrespective of the reference select digital inputs, reference select
DPI commands, the reference mask, and the reference owner.
If the “Auto/Manual” input function is closed, then the drive will use one of the analog inputs (defined by [TB Man Ref Sel]) as the reference, ignoring the normal reference selection mechanisms. This mode of reference selection is called “Terminal Block Manual Reference
Selection Mode”.
If this input function is open, then the terminal block does not request manual control of the reference. If no control device (including the terminal block) is currently requesting manual control of the reference, then the drive will use the normal reference selection mechanisms. This is called “Automatic Reference Selection” mode.
The drive arbitrates among manual reference requests from different control devices, including the terminal block.
•
Accel 2 / Decel 2
The Acceleration/Deceleration Rate Control input functions (Acc/Dec input functions for short) allow the rate of acceleration and deceleration for the drive to be selected from the terminal block. The rates themselves are contained in [Accel Time 1], [Decel Time 1], [Accel Time 2], and
[Decel Time 2]. The Acc/Dec input functions are used to determine which of these acceleration and deceleration rates are in effect at a particular time.
The terminal block bit must be set in the [Accel Mask] and [Logic Mask] parameters in order for the acceleration rate selection to be controlled from the terminal block. The terminal block bit must be set in the [Decel
Mask] and [Logic Mask] parameters in order for the deceleration rate selection to be controlled from the terminal block.
There are two different schemes for using the Acc/Dec input functions.
Each one will be described in its own section.
Digital Inputs
2-61
•
Accel 2, Decel 2
In the first scheme, one input function (called “Accel 2”) selects between
[Accel Time 1] and [Accel Time 2], and another input function (called
“Decel 2”) selects between [Decel Time 1] and [Decel Time 2]. The open state of the function selects [Accel Time 1] or [Decel Time 1], and the closed state selects [Accel Time 2] or [Decel Time 2].
Important: Acc/Dec Control is an “Exclusive Ownership” function (see
Owners). This means that only one control device (terminal block, DPI device, HIM, etc.) at a time is allowed to select the Acc/Dec rates. The terminal block must become Acc/
Dec “owner” before it can be used to control ramp rates. If another device is currently the reference owner (as indicated by [Reference Owner]), it will not be possible to select the reference by using the terminal block digital inputs, and the
Speed Select Inputs will have no effect on which reference the drive is currently using.
Because any combination of open / closed conditions (or unwired condition) commands a reference source, the terminal block seeks accel ownership as soon as the “Accel 2” input function is configured, which may happen at power-up. In order for the terminal block to actually gain ownership, the masks must be set up correctly (see above) and no other device can currently have accel ownership. Once the terminal block gains accel ownership, it will retain it until shutdown, until the [Accel
Mask] or [Logic Mask] bits for the terminal block are cleared, or until
“Accel 2” is unconfigured.
For the “Decel 2” input function, deceleration rate selection ownership is handled in a similar fashion to acceleration rate selection ownership.
•
Acc2 & Dec2
In the second scheme, the “1” rates are combined (Acc and Dec) and the
“2” rates are combined. A single input function is used to select between
[Accel Time 1]/[Decel Time 1] and [Accel Time 2]/[Decel Time 2]. This input function is called “Acc 2 & Dec 2”.
If function is open, then drive will use [Accel Time 1] as the acceleration rate and [Decel Time 1] as the deceleration rate. If function is closed, then drive will use [Accel Time 2] as the acceleration rate and [Decel
Time 2] as the deceleration rate.
The same ownership rules as above apply.
•
MOP Increment, MOP Decrement
These inputs are used to increment and decrement the Motor Operated
Potentiometer (MOP) value inside the drive. The MOP is a reference setpoint (called the “MOP Value”) that can be incremented and decremented by external devices. The MOP value will be retained through a power cycle.
While the “MOP Increment” input is closed, MOP value will increase at rate contained in [MOP Rate]. Units for rate are Hz per second.
2-62
Digital Inputs
While the “MOP Decrement” input is closed, MOP value will decrease at rate contained in [MOP Rate]. Units for rate are Hz per second.
If both the “MOP Increment” and “MOP Decrement” inputs are closed,
MOP value will stay the same.
The terminal block bit must be set in the [MOP Mask] and [Logic Mask] parameters in order for the MOP to be controlled from the terminal block.
In order for the drive to use the MOP value as the current speed reference, either [Speed Ref A Sel] or [Speed Ref B Sel] must be set to
“MOP.”
•
Stop Mode B
This digital input function selects between two different drive stop modes. See also
.
If the input is open, then [Stop Mode A] selects which stop mode to use.
If the input is closed, then [Stop Mode B] selects which stop mode to use. If this input function is not configured, then [Stop Mode A] always selects which stop mode to use.
•
Bus Regulation Mode B
This digital input function selects how the drive will regulate excess voltage on the DC bus. See also
If the input is open, then [Bus Reg Mode A] selects which bus regulation mode to use. If the input is closed, then [Bus Reg Mode B] selects which bus regulation mode to use. If this input function is not configured, then
[Bus Reg Mode A] always selects which bus regulation mode to use.
•
PI Enable
If this input function is closed, the operation of the Process PI loop will be enabled.
If this input function is open, the operation of the Process PI loop will be disabled. See
Process PI Loop on page 2-121 .
•
PI Hold
If this input function is closed, the integrator for the Process PI loop will be held at the current value, which is to say that it will not increase.
If this input function is open, the integrator for the Process PI loop will be allowed to increase. See
.
•
PI Reset
If this input function is closed, the integrator for the Process PI loop will be reset to 0.
If this input function is open, the integrator for the Process PI loop will integrate normally. See
.
Digital Inputs
2-63
•
Auxiliary Fault
The “Aux Fault” input function allows external equipment to fault the drive. Typically, one or more machine inputs (limit switches, pushbuttons, etc.) will be connected in series and then connected to this input. If the input function is open, the software detects the change of state then the drive will fault with the “Auxiliary Input” (F2) fault code.
If the “Aux Fault” input function is assigned to a physical digital input, that input will be active regardless of any drive control masks. Also, the input will be active even if a device other than the terminal block gains complete local control of drive logic. See
If this input function is not configured, then the fault will not occur.
•
Local Control
The “Local Control” input function allows exclusive control of all drive logic functions from the terminal block. If this input function is closed, the terminal block has exclusive control (disabling all the DPI devices) of drive logic, including start, reference selection, acceleration rate selection, etc. The exception is the stop condition, which can always be asserted from any connected control device.
The drive must be stopped in order for the terminal block to gain complete local control.
Important: Local Control is an “Exclusive Ownership” function (see
Owners ). This means that only one control device (terminal
block, DPI device, HIM, etc.) at a time is allowed take local control. If another device is not currently the local owner (as indicated by [Local Owner]) and the terminal block bit is set in the [Local Mask] and [Logic Mask] parameters, the terminal block becomes local owner as soon as the “Local
Control” input function is closed.
•
Clear Faults
The “Clear Faults” digital input function allows an external device to reset drive faults through the terminal block. An open to closed transition on this input will cause the current fault (if any) to be reset.
If this input is configured at the same time as “Stop - Clear Faults”, then only the “Clear Faults” input can actually cause faults to be reset.
The terminal block bit must be set in the [Fault Mask] and [Logic Mask] parameters in order for faults to be reset from the terminal block.
•
Enable
If this input is closed, then the drive can run (start permissive). If open, the drive will not start.
If the drive is already running when this input is opened, the drive will coast and indicate “not enabled” on the HIM (if present). This is not considered a fault condition, and no fault will be generated.
2-64
Digital Inputs
This input is not used for a fast output power removal. The drive will not stop running until the software detects the open state of this input function.
If multiple “Enable” inputs are configured, then the drive will not run if any of the inputs are open.
•
Exclusive Link
This input function is used to activate the state of the input to control one of the drive’s digital outputs. See
.
If an Input is so configured, no function exists for the input until complementary Digital Output programming is done. If no outputs are programmed (linked), the input has no function.
This choice is made when the user wishes to link the input to the output, but desires that no other functionality be assigned to the input.
The state of any digital input can be “passed through” to a digital output by setting the value of a digital output configuration parameter ([Digital
Outx Sel]) to “Input n Link”. The output will then be controlled by the state of the input, even if the input is being used for a second function. If the input is configured as “Not used” input function, the link to the input is considered non-functional.
•
Power Loss Level (PowerFlex 700 only)
When the DC bus level in the drive falls below a certain level, a “power loss” condition is created in the drive logic. This input allows the user to select between two different “power loss” detection levels dynamically.
If the physical input is closed, then the drive will take its power loss level from [Power Loss Level]. If the physical input is open (de-energized), then the drive will use a power loss level designated by internal drive memory, typically 82% of nominal.
If the input function is not configured, then the drive always uses the internal power loss level. This input function is used in PowerFlex 700 drives only. In PowerFlex 70 drives, the power loss level is always internal and not selectable.
•
Precharge Enable (PowerFlex 700 only)
This input function is used to manage disconnection from a common DC bus.
If the physical input is closed, this indicates that the drive is connected to common DC bus and normal precharge handling can occur, and that the drive can run (start permissive). If the physical input is open, this indicates that the drive is disconnected from the common DC bus, and thus the drive should enter the precharge state (precharge relay open) and initiate a coast stop immediately in order to prepare for reconnection to the bus.
If this input function is not configured, then the drive assumes that it is always connected to the DC bus, and no special precharge handling will be done. This input function is used in PowerFlex 700 drive only. In
Digital Inputs
2-65
PowerFlex 70 drives, the drive assumes it is always connected to the DC bus.
Digital Input Conflict Alarms
If the user configures the digital inputs so that one or more selections conflict with each other, one of the digital input configuration alarms will be asserted. As long as the Digital Input Conflict exists, the drive will not
start. These alarms will be automatically cleared by the drive as soon as the user changes the parameters so that there is an internally consistent digital input configuration.
Examples of configurations that cause an alarm are:
•
User tries to configure both the “Start” input function and the “Run
Forward” input function at the same time. “Start” is only used in
“3-wire” start mode, and “Run Forward” is only used in “2-wire” run mode, so they should never be configured at the same time
•
User tries to assign a toggle input function (for instance “Forward/
Reverse”) to more than one physical digital input simultaneously.
•
These alarms, called Type 2 Alarms, are different from other alarms in that it will not be possible to start the drive while the alarm is active. It should not be possible for any of these alarms to occur while drive is running, because all configuration parameters are only changeable while drive is stopped. Whenever one or more of these alarms is asserted, the drive ready status will become “not ready” and the HIM will reflect a message signaling the conflict. In addition, the drive status light will be flashing yellow.
There are three different digital input configuration alarms. They appear to the user (in [Drive Alarm 2]) as “DigIn CflctA”, “DigIn CflctB”, and “DigIn
CflctC”.
“DigIn CflctA” indicates a conflict between different input functions that are not specifically associated with particular start modes.
The table below defines which pairs of input functions are in conflict.
Combinations marked with a “ ” will cause an alarm.
Important: There are combinations of input functions in
that will produce other digital input configuration alarms. “DigIn
CflctA” alarm will also be produced if “Start” is configured and
“Stop – Clear Faults” is not.
Table 2.K Input function combinations that produce “DigIn CflctA” alarm
Acc2/Dec2 Accel 2 Decel 2 Jog Jog Fwd Jog Rev Fwd/Rev
Acc2 / Dec2
Accel 2
Decel 2
Jog
Jog Fwd
Jog Rev
Fwd / Rev
2-66
Digital Inputs
“DigIn CflctB” indicates a digital Start input has been configured without a
Stop input or other functions are in conflict. Combinations that conflict are marked with a “ ” and will cause an alarm.
Table 2.L Input function combinations that produce “DigIn CflctB” alarm
Start Stop–CF Run Run Fwd Run Rev Jog Jog Fwd Jog Rev
Fwd/
Rev
Start
Stop–CF
Run
Run Fwd
Run Rev
Jog
Jog Fwd
Jog Rev
Fwd / Rev
“Digin CflctC” indicates that more than one physical input has been configured to the same input function, and this kind of multiple configuration isn’t allowed for that function. Multiple configuration is allowed for some input functions and not allowed for others.
The input functions for which multiple configuration is not allowed are:
Forward/Reverse
Speed Select 1
Speed Select 2
Speed Select 3
Run Forward
Run Reverse
Jog Forward
Jog Reverse
Run
Stop Mode B
Bus Regulation Mode B
Accel2 & Decel2
Accel 2
Decel 2
There is one additional alarm that is related to digital inputs: the “Bipolar
Cflct” alarm occurs when there is a conflict between determining motor direction using digital inputs on the terminal block and determining it by the polarity of an analog speed reference signal.
Note that the drive will assert an alarm when the user sets up a illegal configuration rather than refusing the first parameter value that results in such a configuration. This is necessary because the user may have to change several parameters one at a time in order to get to a new desired configuration, and some of the intermediate configurations may actually be illegal. Using this scheme, the user or a network device can send parameter updates in any order when setting up the digital input configuration.
The “Bipolar Cflct” alarm occurs when there is a conflict between determining motor direction using digital inputs on the terminal block and determining it by some other means.
When [Direction Mode] is “Bipolar”, the drive uses the sign of the reference to determine drive direction; when [Direction Mode] is “Reverse
Dis”, then the drive never permits the motor to run in the reverse direction.
In both of these cases, the terminal block inputs cannot be used to set
Digital Inputs
2-67
direction, so this alarm is asserted if any digital input function that can set motor direction is configured.
The “Bipolar Cflct” alarm will be asserted if both of the following are true:
•
One or more of the following digital input functions are configured:
“Forward/Reverse”, “Run Forward”, “Run Reverse”, “Jog Forward”,
“Jog Reverse”.
•
[Direction Mode] is set to “Bipolar” or “Reverse Dis”.
Digital In Status
This parameter represents the current state of the digital inputs. It contains one bit for each input. The bits are “1” when the input is closed and “0” when the input is open.
Digital In Examples
PowerFlex 70
shows a typical digital input configuration that includes “3-wire” start. The digital input configuration parameters should be set as shown.
Figure 2.8 Typical digital input configuration with “3-wire” start
Internal Power Source External Power Source
Digital In1 = Stop
Digital In2 = Start
Digital In3 = Forward/Reverse
Digital In4 = Jog
Digital In5 = Speed Select 1
Digital In6 = Enable
24V Common
Digital In Common
24V
Digital In1 = Stop
Digital In2 = Start
Digital In3 = Forward/Reverse
Digital In4 = Jog
Digital In5 = Speed Select 1
Digital In6 = Enable
24V Common
Digital In Common
24V
+24V Common
represents a typical digital input configuration that includes
“2-wire” start. The digital input configuration parameters should be set up as shown
Figure 2.9 Typical digital input configuration with “Run Fwd/Rev” start
Internal Power Source
Digital In1 = Run
Digital In2 = Clear Faults
Digital In3 = Forward/Reverse
Digital In4 = Jog
Digital In5 = Auxiliary Fault
Digital In6 = Enable
24V Common
Digital In Common
24V
External Power Source
Digital In1 = Run
Digital In2 = Clear Faults
Digital In3 = Forward/Reverse
Digital In4 = Jog
Digital In5 = Auxiliary Fault
Digital In6 = Enable
24V Common
Digital In Common
24V
+24V Common
2-68
Digital Outputs
Digital Outputs
Each drive provides digital (relay) outputs for external annunciation of a variety of drive conditions. Each relay is a Form C (1 N.O. – 1 N.C. with shared common) device whose contacts and associated terminals are rated for a maximum of 250V AC or 220V DC. The table below shows specifications and limits for each relay / contact.
Rated Voltage
Maximum Current
Maximum Power
Minimum DC Current
Switching Time
Initial State
Number of relays
(Standard I/O)
PowerFlex 70 PowerFlex 700
Resistive Load Inductive Load Resistive Load Inductive Load
250V AC
220V DC
250V AC
220V DC
240V AC
30V DC
240V AC
30V DC
3 A
AC - 50 VA
DC - 60 W
10
µ
A
8 ms
De-energized
2
1.5 A
AC - 25 VA
DC - 30 W
5 A
1200 VA
150W
10 mA
10 ms
De-energized
3.5 A
840 VA
105W
2 - Standard Control
3 - Vector Control
Configuration
The outputs may be independently configured via the following parameters to switch for various states of the drive.
PowerFlex 700 Digital Output Selection
380
384
388
[Digital Out1 Sel]
[Digital Out2 Sel]
Vector
[Digital Out3 Sel]
Selects the drive status that will energize a (CRx) output relay.
Default:
Options:
(1)
Contacts shown in User Manual are in drive powered state with condition present. Refer to “Fault” and “Alarm” information.
(2)
Vector Control Option Only.
1
4
4
12
13
14
15
8
9
10
11
6
7
4
5
1
2
3
20
21-
26
27
16
17
18
19
28
29
“Fault”
“Run”
“Run”
“Fault”
(1)
“Alarm”
(1)
“Ready”
“Run”
“Forward Run”
“Reverse Run”
“Auto Restart”
“Powerup Run”
“At Speed”
“At Freq”
“At Current”
“At Torque”
“At Temp”
“At Bus Volts”
“At PI Error”
“DC Braking”
“Curr Limit”
“Economize”
“Motor Overld”
“Power Loss”
“Input 1-6 Link”
“PI Enable”
(2)
“PI Hold”
(2)
“PI Reset”
(2)
002
001
003
004
218
012
137
157
147
053
048
184
381
385
389
382
386
390
383
Digital Outputs
2-69
PowerFlex 70 Digital Output Selection
380
384
[Digital Out1 Sel]
[Digital Out2 Sel]
Selects the drive status that will energize a (CRx) output relay.
Default:
Options:
(1)
Contacts shown on page 1-14 of the
User Manual are in drive powered state with condition not present. For functions such as “Fault” and “Alarm” the normal relay state is energized and
N.O. / N.C. contact wiring may have to be reversed.
1
4
20
21
22
23
16
17
18
19
24
25
26
12
13
14
15
8
9
10
11
6
7
4
5
1
2
3
“Fault”
“Run”
“Fault”
(1)
“Alarm”
(1)
“Ready”
“Run”
“Forward Run”
“Reverse Run”
“Auto Restart”
“Powerup Run”
“At Speed”
“At Freq”
“At Current”
“At Torque”
“At Temp”
“At Bus Volts”
“At PI Error”
“DC Braking”
“Curr Limit”
“Economize”
“Motor Overld”
“Power Loss”
“Input 1 Link”
“Input 2 Link”
“Input 3 Link”
“Input 4 Link”
“Input 5 Link”
“Input 6 Link”
002
001
003
004
218
012
137
157
147
053
048
184
381
385
389
382
386
390
383
The selections can be divided into three types of annunciation.
1. The relay changes state due to a particular status condition in the drive.
The following drive conditions or status can be selected to cause the relay activation:
Condition
Fault
Alarm
Ready
Description
A drive Fault has occurred and stopped the drive
A Drive Type 1 or Type 2 Alarm condition exists
The drive is powered, Enabled and no Start Inhibits exist. It is “ready” to run
Run The drive is outputting Voltage and frequency to the motor (indicates 3–wire control, either direction)
Forward Run The drive is outputting Voltage and frequency to the motor (indicates 2–wire control in Forward)
Reverse Run The drive is outputting Voltage and frequency to the motor (indicates 2–wire control in Reverse)
Reset/Run The drive is currently attempting the routine to clear a fault and restart the drive
Powerup Run The drive is currently executing the Auto Restart or “Run at Power Up” function
DC Braking The drive is currently executing either a “DC Brake” or a “Ramp to Hold” Stop command and the DC braking voltage is still being applied to the motor.
Current Limit The drive is currently limiting output current
Economize The drive is currently reducing the output voltage to the motor to attempt to reduce energy costs during a lightly loaded situation.
Mtr Overload The drive output current has exceeded the programmed [Motor NP FLA] and the electronic motor overload function is accumulating towards an eventual trip.
Power Loss The drive has monitored DC bus voltage and sensed a loss of input AC power that caused the DC bus voltage to fall below the fixed monitoring value (82% of
[DC bus Memory]
2-70
Digital Outputs
2. The relay changes state because a particular value in the drive has exceeded a preset limit.
The following drive values can be selected to cause the relay activation:
Condition
At Speed
Description
The drive Output Frequency has equalled the commanded frequency
The balance of these functions require that the user set a limit for the specified value. The limit is set into one of two parameters: [Dig Out1
Level] and [Dig Out2 Level] depending on the output being used. If the value for the specified function (frequency, current, etc.) exceeds the user programmed limit, the relay will activate. If the value falls back below the limit, the relay will deactivate.
381
385
389
[Dig Out1 Level]
[Dig Out2 Level]
Vector
[Dig Out3 Level]
Sets the relay activation level for options
10 – 15 in [Digital Outx Sel]. Units are assumed to match the above selection
(i.e. “At Freq” = Hz, “At Torque” = Amps).
Default:
Min/Max:
Units:
0.0
0.0
0.0/819.2
0.1
380
384
388
Notice that the [Dig Outx Level] parameters do not have units. The drive assumes the units from the selection for the annunciated value. For example, if the chosen “driver” is current, the drive assumes that the entered value for the limit [Dig Outx Level] is% rated Amps. If the chosen “driver” is Temperature, the drive assumes that the entered value for the limit [Dig Outx Level] is degrees C. No units will be reported to
LCD HIM users, offline tools, devices communicating over a network,
PLC’s, etc.
The online and offline limits for the digital output threshold parameters will be the minimum and maximum threshold value required for any output condition.
If the user changes the currently selected output condition for a digital output, then the implied units of the corresponding threshold parameter will change with it, although the value of the parameter itself will not.
For example, if the output is set for “At Current” and the threshold for
100, drive current over 100% will activate the relay. If the user changes the output to “At Temp”, the relay will deactivate (even if current >
100%) because the drive is cooler than 100 degrees C.
The following values can be annunciated
Value
At Freq
At Current
At Torque
At Temp
At Bus Volts
At PI Error
Description
The drive output frequency equals or exceeds the programmed Limit
The drive total output current exceeds the programmed Limit
The drive output torque current component exceeds the programmed Limit
The drive operating temperature exceeds the programmed Limit
The drive bus voltage exceeds the programmed Limit
The drive Process PI Loop error exceeds the programmed Limit
3. The relay changes state because a Digital Input link has been established and the Input is closed.
Digital Outputs
2-71
An Output can be “linked” directly to an Digital Input so that the output
“tracks” the input. When the input is closed, the Output will be energized, and when the input is open, the output will be de-energized.
This “tracking will occur if two conditions exist:
– The Input is configured for any choice other than “Unused”
– The Output is configured for the appropriate “Input x Link”
Note that the output will continue to track or be controlled by the state of the input, even if the input has been assigned a function (i.e. Start, Jog)
Output Time Delay
Each digital output has two user-controlled timers associated with it.
One timer (the ON timer) defines the delay time between a FALSE to TRUE transition (condition appears) on the output condition and the corresponding change in state of the digital output.
The second timer (the OFF timer) defines the delay time between a TRUE to FALSE transition (condition disappears) on the output condition and the corresponding change in the state of the digital output.
380
384
388
382
386
390
[Dig Out1 OnTime]
[Dig Out2 OnTime]
Vector
[Dig Out3 OnTime]
Sets the “ON Delay” time for the digital outputs. This is the time between the occurrence of a condition and activation of the relay.
383
387
391
[Dig Out1 OffTime]
[Dig Out2 OffTime]
Vector
[Dig Out3 OffTime]
Sets the “OFF Delay” time for the digital outputs. This is the time between the disappearance of a condition and de-activation of the relay.
Default:
Min/Max:
Units:
0.00 Secs
0.00 Secs
0.00/600.00 Secs
0.01 Secs
Default:
Min/Max:
Units:
0.00 Secs
0.00 Secs
0.00/600.00 Secs
0.01 Secs
380
384
388
Either timer can be disabled by setting the corresponding delay time to “0.”
Important: Whether a particular type of transition (False-True or
True-False) on an output condition results in an energized or de-energized output depends on the output condition.
If a transition on an output condition occurs and starts a timer, and the output condition goes back to its original state before the timer runs out, then the timer will be aborted and the corresponding digital output will not change state.
0
CR1 On Delay = 2 Seconds
Relay Activates
5
Current Limit Occurs
10
0
Relay Does Not Activate
CR1 On Delay = 2 Seconds
Cyclic Current Limit
(every other second)
5 10
2-72
Direction Control
Direction Control
Direction control of the drive is an exclusive ownership function. This means that only one device can be commanding/controlling direction at a time and that device can only command one direction or the other, not both.
Direction is defined as the forward (+) or reverse (–) control of the drive output frequency, not motor rotation. Motor wiring and phasing determines its CW or CCW rotation. The direction of the drive is controlled in one of four ways:
1. 2-Wire digital input selection such as Run Forward or Run Reverse
2. 3-Wire digital input selection such as Forward/Reverse, Forward or
Reverse (
3. Control Word bit manipulation from a DPI device such as a communications interface. Bits 4 & 5 control direction. Refer to the
Logic Command Word information in Appendix A of the PowerFlex 70 or 700 User Manual.
4. The sign (+/-) of a bipolar analog input.
Direction commands by various devices can be controlled using the
[Direction Mask]. See
page 2-97 for details on masks.
Refer to
and
more detail on the configuration and operating rules for direction control.
DPI
DPI
2-73
DPI is an enhancement to SCANport that provides more functions and better performance. SCANport was a CAN based, Master-Slave protocol, created to provide a standard way of connecting motor control products and optional peripheral devices together. It allows multiple (up to 6) devices to communicate with a motor control product without requiring configuration of the peripheral. SCANport and DPI both provide two basic message types called Client/Server (C/S) and Producer/Consumer (P/C). Client/Server messages are used to transfer parameter and configuration information in the background (relative to other message types). Producer/Consumer messages are used for control and status information. DPI adds a higher baud rate, brand specific enabling, Peer-to-Peer (P/P) communication, and
Flash Memory programming support. PowerFlex drives support the existing
SCANport and Drive Peripheral Interface (DPI) communication protocols.
Multiple devices of each type (SCANport or DPI) can be attached to and communicate with the drive at the same time. This communication interface is the primary way to interact with, and control the drive.
Client/Server
Client/Server messages operate in the background (relative to other message types) and are used for non-control purposes. The Client/Server messages are based on a 10ms “ping” event that allows peripherals to perform a single transaction (i.e. one C/S transaction per peripheral per time period). Message fragmentation (because the message transaction is larger than the standard CAN message of eight data bytes) is automatically handled by Client/Server operation. The following types of messaging are covered:
•
Logging in peripheral devices
•
Read/Write of parameter values
•
Access to all parameter information (limits, scaling, default, etc.)
•
User set access
•
Fault/Alarm queue access
•
Event notification (fault, alarm, etc.)
•
Access to all drive classes/objects (e.g. Device, Peripheral, Parameter, etc.)
Producer/Consumer operation overview
Producer/Consumer messages operate at a higher priority than Client/
Server messages and are used to control/report the operation of the drive
(e.g. start, stop, etc.). A P/C status message is transmitted every 5ms (by the drive) and a command message is received from every change of state in any attached DPI peripheral. Change of state is a button being pressed or error detected by a DPI peripheral. SCANport devices are slightly different in that those peripherals transmit command messages upon reception of a drive status message rather than on detection of a change of state. Producer/
2-74
DPI
Consumer messages are of fixed size, so support of message fragmentation is not required. The following types of messaging are covered:
•
Drive status (running, faulted, etc.)
•
Drive commands (start, stop, etc.)
•
Control logic parsing operations (e.g., mask and owner parameters)
•
Entering Flash programming mode
•
“Soft” login and logout of peripheral devices (enabling/disabling of peripheral control)
Peer-to-Peer operation
Peer-to-Peer messaging allows two devices to communicate directly rather than through the master or host (i.e. drive). They are the same priority as C/
S messages and will occur in the background. In the PowerFlex 70 drive, the only Peer-to-Peer functionality supports proxy operations for the LED
HIM. Since the PowerFlex 700 drive does not support an LED HIM, it will not support Peer-to-Peer proxy operations. The Peer-to-Peer proxy operation is only used so that the LED HIM can access parameters that are not directly part of the regulator board (e.g. DeviceNet baud rate, etc.). The
LED HIM is not attached to a drive through a CAN connection (as normal
DPI or SCANport devices are), so a proxy function is needed to create a
DPI message to access information in an off-board peripheral. If an LCD
HIM is attached to the PowerFlex 70 or 700 drive, it will be able to directly request off-board parameters using Peer-to-Peer messages (i.e. no proxy support needed in the drive). Because the PowerFlex 70 supports the LED
HIM, only 4 communication ports can be used. PowerFlex 700 drives can use all 6 communication ports because Peer-to-Peer proxy operations are not needed. All Peer-to-Peer operations occur without any intervention from the user (regardless whether proxy or normal P/P operation), no setup is required. No Peer-to-Peer proxy operations are required while the drive is in Flash mode.
All the timing requirements specified in the DPI and SCANport System,
Control, and Messaging specifications are supported. Peripheral devices will be scanned (“pinged”) at a 10ms rate. Drive status messages will be produced at a 5ms rate, while peripheral command messages will be accepted (by the drive) as they occur (i.e. change of state). Based on these timings, the following worst case conditions can occur (independent of the baud rate and protocol):
•
Change of peripheral state (e.g. Start, Stop, etc.) to change in the drive –
10ms
•
Change in reference value to change in drive operation – 10ms
•
Change in Datalink data value to change in the drive – 10ms
•
Change of parameter value into drive – 20ms times the number of attached peripherals
The maximum time to detect the loss of communication from a peripheral device is 500ms.
DPI
2-75
Table 2.M Timing specifications contained in DPI and SCANport
DPI
SCANport Host status messages only go out to peripherals once they log in. Peripherals time out if >500ms. If Peripheral receives incorrect status message type, Peripheral generates an error. Actual time dependent on number of peripherals attached. SCANport allows minimum rate of 5ms.
DPI
Host status messages only go out to peripherals once they log in and at least every
125ms (to all attached peripherals). Peripherals time out if >250ms. Actual time dependent on number of peripherals attached. Minimum time goal of 5ms (may have to be dependent on Port Baud Rate). DPI allows minimum 5ms status at 125k and
1ms status at 500k.
Host determines MUT based on number of attached peripherals. Range of values from 2 to 125ms. Minimum goal time of 5ms. DPI allows 2ms min at 500k and 5ms min at 125k.
SCANport No MUT.
DPI Peripheral command messages (including Datalinks) generated on change-of-state, but not faster than Host MUT and at least every 250ms. Host will time out if >500ms.
SCANport Command messages produced as a result of Host status message. If no command response to Host status within 3 status scan times, Host will time out on that peripheral.
DPI Peer messages requests cannot be sent any faster than 2x of MUT.
SCANport No Peer message support
DPI
SCANport Host waits at least 10ms for response to ping. Host cannot send more than 2 event messages (including ping) to a peripheral within 5ms. Peripherals typical response time is 1ms.
DPI
Host must ping every port at least every 2 sec. Peripherals time out if >3 sec. Host will wait maximum of 10ms (125k) or 5ms (500k) for peripheral response to ping.
Peripherals typical response time is 1ms. Peripherals only allow one pending explicit message (i.e. ping response or peer request) at a time.
Response to an explicit request or fragment must occur within 1 sec or device will time out (applies to Host or Peripheral). Time-out implies retry from beginning. Maximum number of fragments per transaction is 16. Flash memory is exception with 22 fragments allowed.
SCANport Assume same 1 sec time-out. Maximum number of fragments is 16
DPI During Flash mode, host stops ping, but still supports status/command messages at a
1 – 5 sec rate. Drive will use 1 sec rate. Data transfer occurs via explicit message as fast as possible (i.e. peripheral request, host response, peripheral request, etc.) but only between two devices.
SCANport No Flash mode support
The Minimum Update Time (MUT), is based on the message type only. A standard command and Datalink command could be transmitted from the same peripheral faster than the MUT and still be O.K. Two successive
Datalink commands or standard commands will still have to be separated by the MUT, however.
2-76
Drive Overload
Drive Overload
The drive thermal overload has two primary functions. The first requirement is to make sure the drive is not damaged by abuse. The second is to perform the first in a manor that does not degrade the performance, as long the drive temperature and current ratings are not exceeded.
The purpose of is to protect the power structure from abuse. Any protection for the motor and associated wiring is provided by a Motor Thermal
Overload feature.
The drive will monitor the temperature of the power module based on a measured temperature and a thermal model of the IGBT. As the temperature rises the drive may lower the PWM frequency to decrease the switching losses in the IGBT. If the temperature continues to rise, the drive may reduce current limit to try to decrease the load on the drive. If the drive temperature becomes critical the drive will generate a fault.
If the drive is operated in a low ambient condition the drive may exceed rated levels of current before the monitored temperature becomes critical.
To guard against this situation the drive thermal overload also includes an inverse time algorithm. When this scheme detects operation beyond rated levels, current limit may be reduced or a fault may be generated.
Operation
The drive thermal overload has two separate protection schemes, an overall
RMS protection based on current over time, and an IGBT junction thermal manager based on measured power module temperature and operating conditions. The drive may fold back current limit when either of these methods detects a problem.
Overall RMS Protection
The overall RMS protection makes sure the current ratings of the drive are not exceeded. The lower curve in
shows the boundary of normal-duty operation. In normal duty, the drive is rated to produce 110% of rated current for 60 seconds, 150% of rated current for three seconds, and
165% of rated current for 100 milliseconds. The maximum value for current limit is 150% so the limit of 165% for 100 milliseconds should never be crossed. If the load on the drive exceeds the level of current as shown on the upper curve, current limit may fold back to 100% of the drive rating until the 10/90 or 5/95 duty cycle has been achieved. For example, 60 seconds at
110% will be followed by 9 minutes at 100%, and 3 seconds at 150% will be followed by 57 seconds at 100%. With the threshold for where to take action slightly above the rated level the drive will only fold back when drive ratings are exceeded.
If fold back of current limit is not enabled in [Drive OL Mode], the drive will generate a fault when operation exceeds the rated levels. This fault can not be disabled. If current limit fold back is enabled then a fault is generated when current limit is reduced.
Drive Overload
2-77
Figure 2.10 Normal Duty Boundary of Operation
1.80
1.70
1.60
1.50
1.40
1.30
1.20
1.10
1.00
0.90
0.80
0.70
0.60
0.50
0.40
0.30
0.20
0.10
0.00
1.00
10.00
Time (Seconds)
100.00
1,000.00
2.25
2.00
1.75
1.50
1.25
1.00
0.75
0.50
0.25
0.00
1.00
The lower curve in
shows the boundary of heavy duty operation. In heavy duty, the drive is rated to produce 150% of rated current for 60 seconds, 200% for three seconds, and 220% for 100 milliseconds.
The maximum value for current limit is 200% so the limit of 220% for 100 milliseconds should never be crossed. If the load on the drive exceeds the level of current as shown on the upper curve, current limit may fold back to
100% of the drive rating until the 10/90 or 5/95 duty cycle has been achieved. For example, 60 seconds at 150% will be followed by 9 minutes at 100%, and 3 seconds at 200% will be followed by 57 seconds at 100%.
With the threshold for where to take action slightly above the rated level the drive will only fold back when drive ratings are exceeded.
Again, if fold back of current limit is not enabled in the [Drive OL Mode], the drive will generate a fault when operation exceeds the rated levels. This fault can not be disabled. If current limit fold back is enabled then a fault is generated when current limit is reduced.
Figure 2.11 Heavy Duty Boundary of Operation
2.50
10.00
100.00
Time (Seconds)
1000.00
10000.00
2-78
Drive Overload
Thermal Manager Protection
The thermal manager protection assures that the thermal ratings of the power module are not exceeded. The operation of the thermal manager can be thought of as a function block with the inputs and outputs as shown below.
Figure 2.12 Thermal Manager Inputs/Outputs
DTO Select
(Off,PWM,ILmt,Both)
PWM Frequency
(2 - 12 kHz)
Current Limit
(0 - 200%)
Temperature Analog Input
(Volts)
I_total
(Amps)
V_dc
(Volts)
Output Frequency
(0-400 Hz)
Drive
Thermal
Overload
DTO Fault
(On,Off)
Active PWM Frequency
(2 - 12 kHz)
Active Current Limit
(0 - 200%)
Drive Temperature
(x deg C)
IGBT Temperature
(x deg C)
KHz Alarm
(On, Off)
ILmt Alarm
(On, Off)
EE Power Board Data
The following is a generalization of the calculations done by the thermal manager. The IGBT junction temperature T
J
is calculated based on the measured drive temperature T
Drive
, and a temperature rise that is a function of operating conditions. When the calculated junction temperature reaches a maximum limit the drive will generate a fault. This fault can not be disabled. This maximum junction temperature is stored in EE on the power board along with other information to define the operation of the drive thermal overload function. These values are not user adjustable. In addition to the maximum junction temperature there are thresholds that select the point at which the PWM frequency begins to fold back, and the point at which current limit begins to fold back. As T
J
increases the thermal manager may reduce the PWM frequency. If T
J
continues to rise current limit may be reduced, and if T
J continues to rise the drive generates a fault.
The calculation of the reduced PWM frequency and current limit is implemented with an integral control.
PWM Frequency
PWM Frequency as selected by the user can be reduced by the thermal manager. The resulting Active PWM Frequency may be displayed in a test point parameter.
The active PWM frequency will change in steps of 2 kHz. It will always be less than or equal to the value selected by the user, and will not be less than the drives minimum PWM frequency. When drive temperature reaches the level where PWM frequency would be limited, the Drv OL Lvl 1 Alarm is turned on. This alarm will be annunciated even if the reduced PWM frequency is not enabled.
Drive Overload
2-79
Current Limit
Current Limit as selected by the user can be reduced by the thermal manager. The resulting active current limit may be displayed as a test point parameter.
The active current limit will always be less than or equal to the value selected by the user, and will not be less than flux current. When drive temperature reaches the level where current limit would be clamped, the
Drv OL Lvl 2 Alarm is turned on. This alarm will be annunciated even if reduced current limit is not enabled.
The active current limit is used during normal operation and during DC injection braking. Any level of current requested for DC injection braking is limited by the Active Current Limit.
Configuration
The [Drive OL Mode] allows the user to select the action(s) to perform with increased current or drive temperature. When this parameter is “Disabled,” the drive will not modify the PWM frequency or current limit. When set to
“Reduce PWM” the drive will only modify the PWM frequency. “Reduce
CLim” will only modify the current limit. Setting this parameter to
“Both-PWM 1st” the drive will modify the PWM frequency and the current limit.
DTO Fault
For all possible settings of [Drive OL Mode], the drive will always monitor the T j
and T
Drive
and generate a fault when either temperature becomes critical. If T
Drive
is less than –20
°
C, a fault is generated. With these provisions, a DTO fault is generated if the NTC ever malfunctions.
Temperature Display
The Drive’s temperature is measured (NTC in the IGBT module) and displayed as a percentage of drive thermal capacity in [Drive Temp]. This parameter is normalized to the thermal capacity of the drive (frame dependent) and displays thermal usage in % of maximum (100% = drive
Trip). A test point, “Heatsink temperature” is available to read temperature directly in degrees C, but cannot be related to the trip point since
“maximums” are only given in %. The IGBT temperature shown in
is used only for internal development and is not provided to the user.
2-80
Drive Ratings (kW, Amps, Volts)
Low Speed Operation
When operation is below 4 Hz, the duty cycle is such that a given IGBT will carry more of the load for a while and more heat will build up in that device.
The thermal manager will increase the calculated IGBT temperature at low output frequencies and will cause corrective action to take place sooner.
When the drive is in current limit the output frequency is reduced to try to reduce the load. This works fine for a variable torque load, but for a constant torque load reducing the output frequency does not lower the current (load).
Lowering current limit on a CT load will push the drive down to a region where the thermal issue becomes worse. In this situation the thermal manager will increase the calculated losses in the power module to track the worst case IGBT. For example, if the thermal manager normally provides
150% for 3 seconds at high speeds, it may only provide 150% for one second before generating a fault at low speeds.
If operating at 60Hz 120%, lowering the current limit may cause a fault sooner than allowing the drive to continue to operate. In this case the user may want to disable current limit fold back.
Drive Ratings (kW,
Amps, Volts)
Refer to
Fuses and Circuit Breakers on page 2-87
.
Economizer
(Auto-Economizer)
Refer to
Torque Performance Modes on page 2-178 .
Economizer mode consists of the sensorless vector control with an additional energy savings function.
When steady state speed is achieved, the economizer becomes active and automatically adjusts the drive output voltage based on applied load. By matching output voltage to applied load, the motor efficiency is optimized.
Reduced load commands a reduction in motor flux current. The flux current is reduced as long as the total drive output current does not exceed 75% of motor rated current as programmed in [Motor NP FLA], parameter 42. The flux current is not allowed to be less than 50% of the motor flux current as programmed in [Flux Current Ref], parameter 63. During acceleration and deceleration, the economizer is inactive and sensorless vector motor control performs normally.
Maximum Voltage
Motor Nameplate Voltage
Rated Flux Current
Increasing
Load
V total
Ir Voltage
0
0
Frequency
Reduced Flux Current, minimum of 50% of Rated Flux Current
Motor Nameplate
Frequency
Maximum
Frequency
Efficiency
Fan Curve
Fan
Efficiency
2-81
The following chart shows typical efficiency for PWM variable frequency drives, regardless of size. Drives are most efficient at full load and full speed.
100
95
90
85
80
75 vs. Speed vs. Load
10 20 30 40 50 60 70 80 90 100
% Speed/% Load
When torque performance (see
page 2-178 ) is set to Fan/Pump, the
relationship between frequency and voltage is shown in the following figure. The fan/pump curve generates voltage that is a function of the stator frequency squared up to the motor nameplate frequency. Above base frequency voltage is a linear function of frequency. At low speed the fan curve can be offset by the run boost parameter to provide extra starting torque if needed. No extra parameters are needed for fan/pump curve.
The pattern matches the speed vs. load characteristics of a centrifugal fan or pump and optimizes the drive output to those characteristics.
Maximum Voltage
Base Voltage
(Nameplate)
Run Boost
See
above.
Base Frequency
(Nameplate)
Maximum
Frequency
2-82
Faults
Faults
Faults are events or conditions occurring within and/or outside of the drive.
Theses events or conditions are (by default) considered to be of such significant magnitude that drive operation should or must be discontinued.
Faults are annunciated to the user via the HIM, communications and/or contact outputs. The condition that caused the fault determines the user response.
Once a fault occurs, the fault condition is latched, requiring the user or application to perform a fault reset action to clear the latched condition. If the condition that caused fault still exists when the fault is reset, the drive will fault again and the fault will be latched again.
When a Fault Occurs
1. The drive is set as faulted, causing the drive output to be immediately disabled and a “coast to stop” sequence to occur
2. The fault code is entered into the first buffer of the fault queue (see
“Fault Queue” below for rules).
3. Additional data on the status of the drive at the time that the fault occurred is recorded. Note that there is only a single copy of this information which is always related to the most recent fault queue entry
[Fault 1 Code], parameter 243. When another fault occurs, this data is overwritten with the new fault data. The following data/conditions are captured and latched into non-volatile drive memory:
– [Status 1 @ Fault], parameter 227 (drive condition at the time of the fault).
– [Status 2 @ Fault], parameter 228 (drive condition at the time of the fault).
– Alarm 1 @ Fault], parameter 229 (alarm condition at the time of the fault).
– Alarm 2 @ Fault], parameter 230 (alarm conditions at the time of the fault).
– Fault Frequency (drive output frequency at time of fault).
– Fault Motor Amps: (motor amps at time of fault).
– Fault Bus Volts: (unfiltered DC Bus volts at time of fault.)
Fault Queue
Faults are also logged into a fault queue such that a history of the most recent fault events is retained. Each recorded event includes a fault code
(with associated text) and a fault “time of occurrence.” The PowerFlex 70 drive has a four event queue and the PowerFlex 700 has an eight event queue.
Faults
2-83
A fault queue will record the occurrence of each fault event that occurs while no other fault is latched. Each fault queue entry will include a fault code and a time stamp value. A new fault event will not be logged to the fault queue if a previous fault has already occurred, but has not yet been reset. Only faults that actually trip the drive will be logged. No fault that occurs while the drive is already faulted will be logged.
The fault queue will be a first-in, first-out (FIFO) queue. Fault queue entry
#1 will always be the most-recent entry (newest). Entry 4 (8) will always be the oldest. As a new fault is logged, each existing entry will be shifted up by one (i.e. previous entry #1 will move to entry #2, previous entry #2 will move to entry #3, etc.). If the queue is full when a fault occurs, the oldest entry will be discarded.
The fault queue will be saved in nonvolatile storage at power loss, thus retaining its contents through a power off - on cycle.
Fault Code/Text [Fault Code 1-x]
The fault code for each entry can be read in its respective read-only parameter. When viewed with a HIM, only the fault code is displayed. If viewed via a DPI peripheral (communications network), the queue is not accessed through parameters, and a text string of up to 16 characters is also available.
Fault Time [Fault 1-8 Time]
PowerFlex drives have an internal drive-under-power-timer. The user has no control over the value of this timer, which will increment in value over the life of the drive and saved in nonvolatile storage. Each time the drive is powered down and then repowered, the value of this timer is written to
[Power Up Marker], parameter 242.
The time is presented in xxx.yyyy hours (4 decimal places). Each increment of 1 represents approximately 0.36 seconds. Internally it will be accumulated in a 32-bit unsigned integer with a resolution of 0.35 seconds, resulting in a rollover to zero every 47.66 years.
The time stamp value recorded in the fault queue at the time of a fault is the value of internal drive under power timer. By comparing this value to the
[PowerUp Marker], it is possible to determine when the fault occurred relative to the last drive power-up.
The time stamp for each fault queue entry can be read via the corresponding parameter. Time comparisons of one fault to the next and/or with [PowerUp
Marker] are only meaningful if they occur less than or equal to the rollover range.
Resetting or Clearing a Fault
A latched fault condition can be cleared by the following:
2-84
Faults
1. An off to on transition on a digital input configured for fault reset or stop/reset.
2. Setting [Fault Clear] to “1.”
3. A DPI peripheral (several ways).
4. Performing a reset to factory defaults via parameter write.
5. Cycling power to the drive such that the control board goes through a power-up sequence.
Resetting faults will clear the faulted status indication. If any fault condition still exists, the fault will relatch and another entry made in the fault queue.
Clearing the Fault Queue
Performing a fault reset does not clear the fault queue. Clearing the fault queue is a separate action.
Fault Configuration
The drive can be configured such that some fault conditions do not trip the drive. Configurable faults include those that are user inputs.
[Fault Config 1] is a bit-mapped 16 bit word enabling or disabling certain fault conditions (see below). Disabling a fault removes the effect of the fault condition and makes the event unknown to the user. If the bit is on, the fault is enabled. If the bit is off, the fault is not enabled.
x
15 x
14 x
13 x
12 x
11 x
10 x
9
Bit #
Factory Default Bit Values x
8 x
7
1
6
D A hib utR t st T ries
Sh ea r P in
M otor O verL d olta ge
U nderV
Po w er L
0
5
0
4
1
3 x
2
1
1
0
0
oss
1 =Enabled
0 =Disabled x =Reserved
Flying Start
Flying Start
2-85
The Flying Start feature is used to start into a rotating motor, as quick as possible, and resume normal operation with a minimal impact on load or speed.
When a drive is started in its normal mode it initially applies a frequency of
0 Hz and ramps to the desired frequency. If the drive is started in this mode with the motor already spinning, large currents will be generated. An overcurrent trip may result if the current limiter cannot react quickly enough. The likelihood of an overcurrent trip is further increased if there is a residual flux (back emf) on the spinning motor when the drive starts. Even if the current limiter is fast enough to prevent an overcurrent trip, it will take an unacceptable amount of time for synchronization to occur and for the motor to reach its desired frequency. In addition, larger mechanical stress is placed on the application, increasing downtime and repair costs while decreasing productivity.
In Flying Start mode, the drive’s response to a start command will be to identify the motor’s speed and apply a voltage that is synchronized in frequency, amplitude and phase to the back emf of the spinning motor. The motor will then accelerate to the desired frequency. This process will prevent an overcurrent trip and significantly reduce the time for the motor to reach its desired frequency. Since the motor is “picked up “smoothly at its rotating speed and ramped to the proper speed, little or no mechanical stress is present.
Configuration
Flying Start is activated by setting the [Flying Start En] parameter to
“Enable”
169 [Flying Start En]
Enables/disables the function which reconnects to a spinning motor at actual
RPM when a start command is issued.
Default:
Options:
0
0
1
“Disabled”
“Disabled”
“Enabled”
170
The gain can be adjusted to increase responsiveness. Increasing the value in
[Flying StartGain] increases the responsiveness of the Flaying Start Feature
169 170 [Flying StartGain]
Sets the response of the flying start function.
Default:
Min/Max:
Display:
4000
20/32767
1
Application Example
In some applications, such as large fans, wind or drafts may rotate the fan in the reverse direction when the drive is stopped. If the drive were started in the normal manner, its output would begin at zero Hz, acting as a brake to bring the reverse rotating fan to a stop and then accelerating it in the correct direction.
This operation can be very hard on the mechanics of the system including fans, belts and other coupling devices.
2-86
Flying Start
Cooling Tower Fans
Draft/wind blows idle fans in reverse direction. Restart at zero damages fans, breaks belts. Flying start alleviates the problem
Fuses and Circuit
Breakers
Fuses and Circuit Breakers
2-87
Tables
through
provide drive ratings (including continuous, 1
minute and 3 second) and recommended AC line input fuse and circuit breaker information. Both types of short circuit protection are acceptable for UL and IEC requirements. Sizes listed are the recommended sizes based on 40 degree C and the U.S. N.E.C. Other country, state or local codes may require different ratings.
Fusing
If fuses are chosen as the desired protection method, refer to the recommended types listed below. If available amp ratings do not match the tables provided, the closest fuse rating that exceeds the drive rating should be chosen.
•
IEC
– BS88 (British Standard) Parts 1 & 2
(1)
, EN60269-1, Parts 1 & 2, type gG or equivalent should be used.
•
UL – UL Class CC, T, RK1 or J must be used.
Circuit Breakers
The “non-fuse” listings in the following tables include both circuit breakers
(inverse time or instantaneous trip) and 140M Self-Protecting Motor
Starters. If one of these is chosen as the desired protection method, the following requirements apply.
•
IEC and UL
– Both types of devices are acceptable for IEC and UL installations.
(1) Typical designations include, but may not be limited to the following; Parts 1 & 2: AC, AD, BC, BD, CD, DD, ED,
EFS, EF, FF, FG, GF, GG, GH.
2-88
Fuses and Circuit Breakers
Table 2.N PF70 208/240 Volt AC Input Recommended Protection Devices
Drive
Catalog
Number
HP
Rating
Input
Ratings Output Amps
Dual
Element Time
Delay Fuse
ND HD Amps kVA Cont. 1 Min. 3 Sec. Min.
Max.
208 Volt AC Input
20AB2P2 A 0.5
0.33
2.9
20AB4P2 A 1 0.75
5.6
20AB6P8 B 2
20AB9P6 B 3
1.5
2
10
14
20AB015 C 5 3
20AB022 D 7.5
5
16
23.3
20AB028 D 10 7.5
29.8
240 Volt AC Input
1.1
2.5
2 4.8
3.6
7.8
5.1
11
2.7
5.5
10.3
12.1
5.8
17.5
19.2
8.3
25.3
27.8
10.7
32.2
37.9
3.7
7.4
13.8
16.5
26.6
37.9
50.6
20
30
40
6
10
15
20
35
50
70
6
10
15
25
20AB2P2 A 0.5
0.33
2.5
20AB4P2 A 1
20AB6P8 B 2
0.75
1.5
4.8
8.7
20AB9P6 B 3
20AB015 C 5
2
3
12.2
13.9
20AB022 D 7.5
5 19.9
20AB028 D 10 7.5
25.7
1.1
2.2
2 4.2
3.6
6.8
2.4
4.8
9
5.1
9.6
10.6
5.8
15.3
17.4
8.3
22
10.7
28
24.4
33
3.3
6.4
12
14.4
23.2
33
44
20
20
25
35
3
6
15
20
30
45
60
4.5
9
15
20
30
40
6
10
15
20
20
20
25
35
3
6
15
Non-Time
Delay Fuse
Min.
Max.
Circuit
Breaker
Amps
Motor
Circuit
Protector
Amps
140M Motor Starter with Adjustable Current Range
Available Catalog Numbers
8
15
25
35
60
80
110
10
17.5
30
40
70
100
125
15
15
25
35
60
80
110
15
15
30
40
70
100
125
15
30
30
50
3
7
15
30
30
50
7
7
15
30
140M-C2E-B40 140M-D8E-B40 –
140M-C2E-B63 140M-D8E-B63 –
140M-C2E-C10 140M-D8E-C10 140M-F8E-C10 –
140M-C2E-C16 140M-D8E-C16 140M-F8E-C16 –
–
–
140M-C2E-C20 140M-D8E-C20 140M-F8E-C20 –
140M-C2E-C25 140M-D8E-C25 140M-F8E-C25 140M-CMN-2500
– – 140M-F8E-C32 140M-CMN-4000
140M-C2E-B25 140M-D8E-B25 – –
140M-C2E-B63 140M-D8E-B63 – –
140M-C2E-C10 140M-D8E-C10 140M-F8E-C10 –
140M-C2E-C16 140M-D8E-C16 140M-F8E-C16 –
140M-C2E-C16 140M-D8E-C16 140M-F8E-C16 –
140M-C2E-C20 140M-D8E-C20 140M-F8E-C20 –
– – 140M-F8E-C32 140M-CMN-4000
Table 2.O PF70 400/480 Volt AC Input Recommended Protection Devices
Drive
Catalog
Number kW
(400V)
HP (480V)
Rating
Input
Ratings Output Amps
Dual
Element Time
Delay Fuse
ND HD Amps kVA Cont. 1 Min. 3 Sec. Min.
Max.
400 Volt AC Input
20AC1P3 A 0.37
0.25
1.6
20AC2P1 A 0.75
0.55
2.5
20AC3P5 A 1.5
1.1
4.3
20AC5P0 B 2.2
1.5
6.5
20AC8P7 B 4 3
20AC011 C 5.5
4
11.3
11
20AC015 C 7.5
5.5
15.1
20AC022 D 11 7.5
21.9
20AC030 D 15 11
480 Volt AC Input
30.3
1.1
1.3
1.8
2.1
3 3.5
4.5
5
7.8
8.7
9.9
7.6
11.5
13
10.4
15.4
17.2
15.2
22 24.2
21 30 33
1.4
2.4
4.5
5.5
13.2
17.4
23.1
33
45
1.9
3.2
6
7.5
15
15
20
30
40
3
4
6
10
17.5
25
30
45
60
3
6
6
10
20AD1P1 A 0.5
0.33
1.3
20AD2P1 A 1
20AD3P4 A 2
0.75
1.5
2.4
3.8
20AD5P0 B 3
20AD8P0 B 5
2
3
5.6
9.8
20AD011 C 7.5
5 9.5
20AD014 C 10 7.5
12.5
20AD022 D 15 10
20AD027 D 20 15
19.9
24.8
1.1
1.1
2 2.1
3.2
3.4
4.7
5
8.4
8
7.9
11
10.4
14
16.6
22
20.6
27
1.2
2.4
4.5
5.5
8.8
12.1
16.5
24.2
33
1.6
3.2
6
7.5
12
16.5
22
33
44
10
15
15
20
3
3
6
25
35
10
15
20
30
3
6
6
45
60
15
15
20
30
40
3
4
6
10
10
15
15
20
3
3
6
25
35
Non-Time
Delay Fuse
Min.
Max.
Circuit
Breaker
Amps
Motor
Circuit
Protector
Amps
140M Motor Starter with Adjustable Current Range
Available Catalog Numbers
20
30
40
50
4
8
12
80
100
30
45
60
80
120
5
8
12
20
20
30
40
50
15
15
15
80
100
30
40
60
80
120
15
15
15
20
15
15
15
20
3
3
7
30
50
15
15
20
30
50
3
7
7
15
140M-C2E-B16 – –
140M-C2E-B25 140M-D8E-B25 –
140M-C2E-B40 140M-D8E-B40 – –
140M-C2E-C10 140M-D8E-C10 140M-F8E-C10 –
–
–
140M-C2E-C16 140M-D8E-C16 140M-F8E-C16 –
140M-C2E-C16 140M-D8E-C16 140M-F8E-C16 –
140M-C2E-C16 140M-D8E-C16 140M-F8E-C16 –
140M-C2E-C25 140M-D8E-C25 140M-F8E-C25 140M-CMN-2500
– – 140M-F8E-C32 140M-CMN-4000
140M-C2E-B16 – –
140M-C2E-B25 140M-D8E-B25 –
140M-C2E-B40 140M-D8E-B40 –
140M-C2E-C63 140M-D8E-B63 – –
140M-C2E-C10 140M-D8E-C10 140M-F8E-C10 –
140M-C2E-C16 140M-D8E-C16 140M-F8E-C16 –
140M-C2E-C16 140M-D8E-C16 140M-F8E-C16 –
–
–
–
140M-C2E-C20 140M-D8E-C20 140M-F8E-C20 –
– – 140M-F8E-C25 140M-CMN-2500
Table 2.P PF70 600 Volt AC Input Recommended Protection Devices
Drive
Catalog
Number
HP
Rating
Input
Ratings Output Amps
Dual
Element Time
Delay Fuse
ND HD Amps kVA Cont. 1 Min. 3 Sec. Min.
Max.
600 Volt AC Input
20AE0P9 A 0.5
0.33
1.3
20AE1P7 A 1 0.75
1.9
20AE2P7 A 2
20AE3P9 B 3
1.5
2
3
4.4
20AE6P1 B 5 3
20AE9P0 C 7.5
5
7.5
7.7
20AE011 C 10 7.5
9.8
20AE017 D 15 10 15.3
20AE022 D 20 15 20
1.3
0.9
2 1.7
3.1
2.7
4.5
3.9
7.8
6.1
8 9
10.1
11
15.9
17
20.8
22
6.7
9.9
13.5
18.7
25.5
1.1
2
3.6
4.3
9.2
13.5
18
25.5
34
1.4
2.6
4.8
5.9
10
10
15
20
25
4
6
3
3
12
20
20
35
45
6
8
3
6
10
10
15
20
25
4
6
3
3
Non-Time
Delay Fuse
Min.
Max.
20
35
40
60
80
3.5
6
10
15
20
35
40
60
80
15
15
15
15
Circuit
Breaker
Amps
Motor
Circuit
Protector
Amps
140M Motor Starter with Adjustable Current Range
Available Catalog Numbers
15
15
15
30
30
7
7
3
3
140M-C2E-B16 – –
140M-C2E-B25 140M-D8E-B25 –
140M-C2E-B40 140M-D8E-B40 –
140M-C2E-C63 140M-D8E-B63 –
–
–
–
–
140M-C2E-C10 140M-D8E-C10 140M-F8E-C10 –
140M-C2E-C10 140M-D8E-C10 140M-F8E-C10 –
140M-C2E-C16 140M-D8E-C16 140M-F8E-C16 –
140M-C2E-C20 140M-D8E-C20 140M-F8E-C20 –
140M-C2E-C25 140M-D8E-C25 140M-F8E-C25 140M-CMN-2500
See
for Notes.
Fuses and Circuit Breakers
2-89
Table 2.Q PF700 208/240 Volt AC Input Recommended Protection Devices
Drive
Catalog
Number
HP
Rating
Input
Ratings Output Amps
Dual
Element Time
Delay Fuse
ND HD Amps kVA Cont. 1 Min. 3 Sec. Min.
Max.
208 Volt AC Input
20BB2P2 0 0.5
0.33 1.9
20BB4P2 0 1 0.75 3.7
20BB6P8 1 2
20BB9P6 1 3
1.5
2
6.8
9.5
0.7
2.5
1.3
4.8
2.4
7.8
3.4
11
2.8
5.6
10.4
12.1
20BB015 1 5 3
20BB022 1 7.5
5
15.7
5.7
17.5
19.3
23.0
8.3
25.3
27.8
20BB028 2 10 7.5
29.6
10.7 32.2
38
20BB042 3 15 10 44.5
16.0 48.3
53.1
20BB052 3 20 15 51.5
17.1 56
20BB070 4 25 20 78.2
64
86
20BB080 4 30 25
20BB104 5 – 30 84.7
28
92
92
117.3
138
86
117.3
156.4
175
40 –
20BB130 5 – 40
113
98
50 –
20BB154 6 60 50
122
20BB192 6 75 60
240 Volt AC Input
37.5 120
32.4 104
40.6 130
154
192
132
156
143
175
175
175
3.8
7.0
13.8
17
26.3
38
50.6
72.5
125
150
125
175
20
30
40
60
80
3
6
10
12
200
250
225
275
35
50
70
100
125
6
10
15
20
20BB2P2 0 0.5
0.33 1.7
20BB4P2 0 1
20BB6P8 1 2
0.75 3.3
1.5
5.9
0.7
2.2
1.4
4.2
2.4
6.8
2.4
4.8
9
20BB9P6 1 3
20BB015 1 5
2
3
8.3
3.4
9.6
10.6
13.7
5.7
15.3
16.8
20BB022 1 7.5
5 19.9
8.3
22
20BB028 2 10 7.5
25.7
10.7 28
24.2
33
20BB042 3 15 10 38.5
16.0 42
20BB052 3 20 15 47.7
18.2 52
20BB070 4 25 20
20BB080 4 30 25
70
80
20BB104 5 – 30 73
40 – 98
20BB130 5 – 40 98
50 – 122
20BB154 6 60 50
20BB192 6 75 60
28 80 120
37.3 104 115
37.3 104 156
47 130 143
154
192
46.2
63
78
105
160
175
175
175
63
80
105
136
3.3
6.4
12
14.4
23
33
44
100
125
125
175
12
20
25
35
3
5
10
50
60
175
225
225
275
20
30
50
60
6
8
15
90
100
20
30
40
60
80
3
6
10
12
12
20
25
35
3
5
10
50
60
Non-Time
Delay Fuse
Min.
Max.
125
150
125
175
100
125
125
175
300
400
400
500
350
475
400
500
70
100
125
175
200
10
17.5
30
40
10
15
25
35
60
80
100
150
200
300
350
300
375
300
300
300
375
70
100
125
175
200
15
15
30
40
15
15
25
35
60
80
100
150
200
Circuit
Breaker
Amps
Motor
Circuit
Protector
Amps
140M Motor Starter with Adjustable Current Range
Available Catalog Numbers
15
30
30
50
3
7
15
50
100
30
30
50
70
100
3
7
15
15
100
150
150
250
150
150
150
250
–
–
–
–
–
–
–
–
140M-C2E-B25 140M-D8E-B25 –
140M-C2E-B63 140M-D8E-B63 –
140M-C2E-C10 140M-D8E-C10 140M-F8E-C10 –
140M-C2E-C16 140M-D8E-C16 140M-F8E-C16 –
–
–
–
–
140M-C2E-C20 140M-D8E-C20 140M-F8E-C20 –
140M-C2E-C25 140M-D8E-C25 140M-F8E-C25 140M-CMN-2500
–
–
140M-F8E-C32 140M-CMN-4000
140M-F8E-C45 140M-CMN-6300
– – 140M-CMN-6300
–
–
140M-C2E-B25 140M-D8E-B25 – –
140M-C2E-B63 140M-D8E-B63 – –
140M-C2E-C10 140M-D8E-C10 140M-F8E-C10 –
140M-C2E-C10 140M-D8E-C10 140M-F8E-C10 –
140M-C2E-C16 140M-D8E-C16 140M-F8E-C16 –
140M-C2E-C25 140M-D8E-C25 140M-F8E-C25 140M-CMN-2500
– – 140M-F8E-C32 140M-CMN-4000
–
–
140M-F8E-C45 140M-CMN-6300
– 140M-CMN-6300
–
–
–
–
–
–
–
–
–
–
–
–
–
–
–
–
140M-CMN-9000
–
–
–
–
–
140M-CMN-9000
–
See
for Notes.
2-90
Fuses and Circuit Breakers
Table 2.R PF700 400/480 Volt AC Input Recommended Protection Devices
Drive
Catalog
Number kW
Rating
Input
Ratings Output Amps
Dual
Element Time
Delay Fuse
ND HD Amps kVA Cont. 1 Min. 3 Sec. Min.
Max.
400 Volt AC Input
20BC1P3 0 0.37 0.25 1.1
20BC2P1 0 0.75 0.55 1.8
20BC3P5 0 1.5
0.75 3.2
20BC5P0 0 2.2
1.5
4.6
0.77 1.3
1.3
2.1
2.2
3.5
3.2
5.0
1.4
2.4
4.5
5.5
1.9
3.2
6.0
7.5
20BC8P7 0 4 2.2
7.9
20BC011 0 5.5
4 10.8
5.5
7.5
8.7
11.5
9.9
13
13.2
17.4
20BC015 1 7.5
5.5
14.4
10.0 15.4
17.2
23.1
20BC022 1 11 7.5
20.6
14.3 22 24.2
33
20BC030 2 15 11 28.4
19.7 30
20BC037 2 18.5 15 35.0
24.3 37
20BC043 3 22 18.5 40.7
28.2 43
20BC056 3 30 22 53 36.7 56
20BC072 3 37 30 68.9
47.8 72
20BC085
4 – 37 68.9
47.8 72
45 – 81.4
56.4 85
20BC105 5 – 45 81.4
56.4 85
33
45
56
64
84
108
94
128
112
144
128
170
45
60
74
86
55 –
20BC125 5 – 45
100.5
91.9
69.6 105
63.7 96
116
144
55 –
20BC140 6 – 55
121.1
101
83.9 125
76 105
138
158
75 –
20BC170 6 – 75
136
136
20BC205
90 –
6 – 90
164
164
110 –
480 Volt AC Input
199
103
103
140
140
126 170
126 170
148 205
154
210
187
255
220
20BD1P1 0 0.5
0.33 0.9
20BD2P1 0 1
20BD3P4 0 2
0.75 1.6
1.5
2.6
0.7
1.1
1.4
2.1
2.2
3.4
20BD5P0 0 3
20BD8P0 0 5
2
3
3.9
6.9
3.2
5.0
5.7
8.0
20BD011 0 7.5
5 9.5
7.9
11
20BD014 1 10 7.5
12.5
10.4 14
20BD022 1 15 10 19.9
16.6 22
20BD027 2 20 15 24.8
20.6 27
20BD034 2 25 20 31.2
25.9 34
20BD040 3 30 25 36.7
30.5 40
20BD052 3 40 30 47.7
39.7 52
20BD065 3 50 40 59.6
49.6 65
20BD077 4 – 50 59.6
49.6 65
60 – 72.3
60.1 77
20BD096 5 – 60 72.3
60.1 77
75 – 90.1
74.9 96
116
106
20BD125 5 – 75 90.1
74.9 96
100 – 117 97.6 125
144
138
20BD156 6 – 100 131
125 – 147
20BD180 6 – 125 147
150 – 169
109
122
122
141
125
156
156
180
188
172
234
198
1.2
2.4
4.5
1.6
3.2
6.0
5.5
8.8
7.5
12
12.1
16.5
16.5
22
60
78
98
85
24.2
33
33 44
40.5
54
51 68
80
104
130
116
250
234
312
270
154
144
168
163
210
280
255
313
289
158
168
163
210
90
110
110
110
35
45
60
70
15
15
20
30
6
6
3
3
200
200
250
250
275
125
125
150
150
150
175
175
175
60
80
90
125
3
6
7
10
17.5
25
30
45
300
300
375
375
450
225
200
275
225
60
75
100
100
25
35
40
50
3
3
4
6
10
15
17.5
175
200
200
225
100
125
125
150
110
125
170
170
50
60
70
90
10
15
20
30
3
6
8
250
350
350
400
170
200
200
250
Non-Time
Delay Fuse
Min.
Max.
90
110
110
110
35
45
60
70
15
15
20
30
6
6
3
3
200
200
250
250
275
125
125
150
150
60
75
100
100
25
35
40
50
3
3
4
6
10
15
17.5
175
200
200
225
100
125
125
150
250
300
300
300
120
125
150
200
30
45
60
80
6
8
12
20
550
550
600
600
600
400
375
500
400
200
250
300
300
80
100
125
150
20
30
40
50
6
8
12
500
600
600
600
300
350
350
500
250
300
300
300
120
125
150
200
30
45
60
80
15
15
15
20
400
400
500
500
600
300
375
375
300
200
250
300
300
80
100
125
150
20
30
40
50
15
15
15
375
450
450
500
300
350
350
375
Circuit
Breaker
Amps
Motor
Circuit
Protector
Amps
140M Motor Starter with Adjustable Current Range
Available Catalog Numbers
70
100
100
100
30
50
50
50
7
15
15
20
3
3
7
250
250
250
250
100
125
125
150
100
150
150
150
50
50
60
100
15
15
20
30
7
7
3
3
250
250
250
250
400
150
150
250
150
–
–
–
–
–
–
–
–
–
–
–
–
–
–
–
–
–
140M-C2E-B16 – –
140M-C2E-B25 140M-D8E-B25 –
140M-C2E-B40 140M-D8E-B40 –
140M-C2E-B63 140M-D8E-B63 –
140M-C2E-C10 140M-D8E-C10 140M-F8E-C10 –
140M-C2E-C16 140M-D8E-C16 140M-F8E-C16 –
140M-C2E-C20 140M-D8E-C20 140M-F8E-C20 –
140M-C2E-C25 140M-D8E-C25 140M-F8E-C25 –
–
–
–
–
–
–
–
–
–
–
–
–
140M-F8E-C32 –
140M-F8E-C45 –
–
–
–
–
–
–
–
–
–
–
–
–
–
–
–
–
–
–
–
–
–
–
–
–
–
–
–
–
–
–
–
–
–
–
–
–
–
–
–
–
–
–
–
–
–
–
–
140M-C2E-B16 – –
140M-C2E-B25 – –
140M-C2E-B40 140M-D8E-B40 –
140M-C2E-C63 140M-D8E-B63 – –
140M-C2E-C10 140M-D8E-C10 140M-F8E-C10 –
140M-C2E-C16 140M-D8E-C16 140M-F8E-C16 –
140M-C2E-C16 140M-D8E-C16 140M-F8E-C16 –
–
–
–
–
–
–
–
140M-C2E-C25 140M-D8E-C25 140M-F8E-C25 140-CMN-2500
– – 140M-F8E-C32 140-CMN-4000
–
–
–
–
140M-F8E-C45 140-CMN-4000
140M-F8E-C45 140-CMN-4000
–
–
–
–
–
–
–
–
140M-CMN-6300
140M-CMN-9000
140M-CMN-9000
140M-CMN-9000
–
–
–
–
–
–
–
–
–
–
–
–
–
–
–
–
–
–
–
–
140M-CMN-9000
–
–
–
See
for Notes.
Grounding, General
2-91
Table 2.S PF700 600 Volt AC Input Recommended Protection Devices
Drive
Catalog
Number
HP
Rating
Input
Ratings Output Amps
Dual
Element Time
Delay Fuse
ND HD Amps kVA Cont. 1 Min. 3 Sec. Min.
Max.
600 Volt AC Input
20BE011 1 10 7.5
9.9
10.2 11
20BE017 1 15 10 15.4
16.0 17
20BE022 2 20 15 20.2
21.0 22
20BE027 2 25 20 24.8
25.7 27
20BE032 3 30 25 29.4
30.5 32
20BE041 3 40 30 37.6
39.1 41
20BE052 3 50 40 47.7
49.6 52
20BE062 4 60 50 62
20BE077 5 75 60 77
13.5
18.7
25.5
33
40.5
48
61.5
54
64
82
18
25.5
34
44
40
50
60
15
20
30
35
25
40
50
60
70
90
110
40
50
60
15
20
30
35
Non-Time
Delay Fuse
Min.
Max.
Circuit
Breaker
Amps
40
60
80
100
125
150
200
40
60
80
100
125
150
200
15
20
30
50
50
50
100
Motor
Circuit
Protector
Amps
140M Motor Starter with Adjustable Current Range
Available Catalog Numbers
–
–
–
–
–
–
–
–
–
–
–
–
–
–
–
–
–
–
–
–
–
–
–
–
–
–
–
–
–
–
–
–
–
–
–
–
Notes:
(1)
Minimum protection device size is the lowest rated device that supplies maximum protection without nuisance tripping.
(2)
Maximum protection device size is the highest rated device that supplies drive protection. For US NEC, minimum size is 125% of motor FLA. Ratings shown are maximum.
(3)
Circuit Breaker - inverse time breaker. For US NEC, minimum size is 125% of motor FLA. Ratings shown are maximum.
(4)
Motor Circuit Protector - instantaneous trip circuit breaker. For US NEC minimum size is 125% of motor FLA. Ratings shown are maximum.
(5)
Bulletin 140M with adjustable current range should have the current trip set to the minimum range that the device will not trip.
(6)
Manual Self-Protected (Type E) Combination Motor Controller, UL listed for 208 Wye or Delta, 240 Wye or Delta, 480Y/277 or 600Y/ 347. Not UL listed for use on
480V or 600V Delta/Delta systems.
(7)
The AIC ratings of the Bulletin 140M Motor Protector may vary. See publication 140M-SG001B-EN-P.
(8)
20BC085 current rating is limited to 45 degrees C ambient.
(9)
20BC205 current rating is limited to 40 degrees C ambient.
Grounding, General
Refer to “Wiring and Grounding Guidelines for PWM AC Drives,” publication DRIVES-IN001A-EN-P.
2-92
HIM Memory
HIM Memory
HIM Operations
See
Selecting a Language
See also
Language on page 2-96 . PowerFlex 700 drives support multiple
languages. When you first apply drive power, a language screen appears on the HIM. Use the Up or Down Arrow to scroll through the available languages. Press Enter to select the desired language. To switch to an alternate language, follow the steps below.
Step
1. Press ALT and then the Up Arrow (Lang).
The Language screen will appear.
2. Press the Up Arrow or Down Arrow to scroll through the languages.
3. Press Enter to select a language.
Key(s)
ALT
+
Example Displays
Speak English?
Parlez Francais?
Spechen Duetsch?
Plare Italiano?
Using Passwords
By default the password is set to 00000 (password protection disabled).
Logging in to the Drive
Step
1. Press the Up or Down Arrow to enter your password. Press Sel to move from digit to digit.
2. Press Enter to log in.
Key(s) Example Displays
Login: Enter
Password 9999
Logging Out
Step
You are automatically logged out when the User
Display appears. If you want to log out before that, select “log out” from the Main Menu.
Key(s)
To change a password
Step
1. Use the Up Arrow or Down Arrow to scroll to
Operator Intrfc. Press Enter.
Key(s)
2. Select “Change Password” and press Enter.
3. Enter the old password. If a password has not been set, type “0.” Press Enter.
4. Enter a new password (1- 65535). Press
Enter and verify the new password. Press
Enter to save the new password.
Example Displays
Example Displays
Operator Intrfc:
Change Password
User Display
Parameters
Password:
Old Code: 0
New Code: 9999
Verify: 9999
The User Display
The User Display is shown when module keys have been inactive for a predetermined amount of time. The display can be programmed to show pertinent information.
Input Devices
Input Devices
2-93
Setting the User Display
Step
1. Press the Up Arrow or Down Arrow to scroll to Operator Intrfc. Press Enter.
Key(s)
2. Press the Up Arrow or Down Arrow to scroll to User Display. Press Enter.
3. Select the desired user display. Press Enter.
Scroll to the parameter that the user display will be based on.
4. Press Enter. Set a scale factor.
Sel
5. Press Enter to save the scale factor and move to the last line.
6. Press the Up Arrow or Down Arrow to change the text.
7. Press Enter to save the new user display.
Example Displays
Operator Intrfc:
Change Password
User Display
Parameters
Setting the Properties of the User Display
The following HIM parameters can be set as desired:
•
User Display - Enables or disables the user display.
•
User Display 1 - Selects which user display parameter appears on the top line of the user display.
•
User Display 2 - Selects which user display parameter appears on the bottom line of the user display.
•
User Display Time - Sets how many seconds will elapse after the last programming key is touched before the HIM displays the user display.
Contactors
See
Motor Start/Stop Precautions on page 2-105
Circuit Breakers / Fuses
See
Fuses and Circuit Breakers on page 2-87
Filters, EMC
Refer to
2-94
Input Modes
Input Modes
The PowerFlex family of drives does not use a direct choice of 2-wire or
3-wire input modes, but allows full configuration of the digital I/O. As a means of defining the modes used, consider the following:
2-Wire Control
This input mode is so named because it only utilizes one device and 2 wires to control both the Start (normally referred to as
“RUN” in 2-wire) and Stop functions in an application.
•
A maintained contact device, such as a thermostat, for example, closes its contact to
Run the drive and opens to
Stop the drive
Run/Stop
PORT
MOD
NET A
NET B
PWR
STS
•
In other applications, the maintained device (such as a limit switch), can directly control both Run/Stop and direction control . . .
Run Forward
Run Reverse
PORT
MOD
NET A
NET B
PWR
STS
•
Or, a combination of the two may be desirable.
Run
Forward/Reverse
PORT
MOD
NET A
NET B
PWR
STS
3-Wire Control
This input mode utilizes 2 devices requiring 3 wires to control the
Start (proper term for 3-wire) and
Stop functions in an application.
In this case, momentary contact devices, such as pushbuttons are used.
•
A Start is issued when the
Start button is closed, but unlike 2-wire circuits, the drive does not Stop when the
Start button is released.
Instead, 3-wire control requires a Stop input to Stop the drive
•
Direction control is accomplished either with momentary inputs . . .
Start
Stop
Start
Stop
Forward
Reverse
•
Or, with a maintained input.
Start
Stop
Forward/Reverse
PORT
MOD
NET A
NET B
PORT
MOD
NET A
NET B
PORT
MOD
NET A
NET B
PWR
STS
PWR
STS
PWR
STS
Input Power
Conditioning
Jog
Input Power Conditioning
2-95
Refer to Chapter 2 of “Wiring and Grounding Guidelines for PWM AC
Drives,” publication DRIVES-IN001A-EN-P.
Also refer to
When a JOG command is issued by any of the controlling devices (terminal block digital input, communications adapter or HIM), the drive ouputs voltage and frequency to the motor as long as the command is present.
When the command is released, the drive output stops.
Whenever a jog command is present, the value programmed in parameter
100, [Jog Speed] becomes the active speed reference. Regardless of the
[Speed Mode] or [Feedback Select] setting, no modifications (i.e. no PI adder, no slip adder, no trim adder, etc.) will be made to the reference.
For PowerFlex 70 and PowerFlex 700 with Standard Control, the jog reference will always be a positive number limited between Minimum
Speed and Maximum Speed.
If [Direction Mode] = “Unipolar” the drive will jog using the Jog reference parameter value and will use the direction currently selected via the DPI commanded direction. When [Direction Mode] = “Bipolar” and a Jog command (with no direction) is asserted, the drive will jog using the Jog reference parameter (which is always positive or forward). To accommodate jogging with direction while in Bipolar mode (such as from a terminal block), the drive will allow Jog Fwd and Jog Rev to be configured as terminal block inputs. When these inputs are asserted, the drive will jog the requested direction. This still implies that a HIM can only jog in the forward direction when in Bipolar mode since they only transmit a Jog command with no direction via DPI.
For PowerFlex 700 drives with Vector Control, 2 independent Jog Speeds
(1 and 2) are provided. The jog reference is signed and limited between
Minimum Speed or Reverse Speed Limit (whichever is programmed)) and
Maximum Speed. In this control, the jog reference controls both speed and direction of the jog operation. If the programmed Jog Speed is negative the drive will jog in the reverse direction: if the Jog Speed value is positive, the drive will jog in the forward direction.
When a jog command is issued, exclusive control of speed and direction is given to the Jog function. If the master speed reference is bipolar and commanding reverse direction but the programmed Jog Speed is a positive value, the drive will jog in the forward direction, overriding the direction control of a bipolar speed reference.
2-96
Language
Language
PowerFlex drives are capable of communicating in 7 languages; English,
Spanish, German, Italian, French, Portuguese and Dutch. All drive functions and information displayed on an LCD HIM are shown in the selected language. The desired language can be selected several different ways:
•
On initial drive power-up, a language choice screen appears.
•
The language choice screen can also be recalled at any time to change to a new language. This is accomplished by pressing the “Alt” key followed by the “Lang” key.
•
The language can also be changed by selecting the [Language] parameter (201). Note that this parameter is not functional when using an LED HIM.
Masks
Masks
2-97
A mask is a parameter that contains one bit for each of the possible
Adapters. Each bit acts like a valve for issued commands. Closing the valve
(setting a bit's value to 0) stops the command from reaching the drive logic.
Opening the valve (setting a bit's value to 1) allows the command to pass through the mask into the drive logic.
276 [Logic Mask]
Determines which adapters can control the drive. If the bit for an adapter is set to
“0,” the adapter will have no control functions except for stop.
288 thru
297 x
15 x
14 x
13 x
12 x
11 x
10 x
9 x
8 x
7 x
6
Bit #
Factory Default Bit Values
277 [Start Mask]
Controls which adapters can issue start commands.
278 [Jog Mask]
Controls which adapters can issue jog commands.
279 [Direction Mask]
1
5
D
PI P ort
5
D
PI P ort
4
D
PI P
D ort
3
PI P ort
2
D
PI P ort
1
D ig ital In
1
4
1
3
1
2
1
1
1
0
1 =Control Permitted
0 =Control Masked x =Reserved
See
See
See
Controls which adapters can issue forward/reverse direction commands.
280 [Reference Mask]
Controls which adapters can select an alternate reference; [Speed Ref A, B Sel] or [Preset Speed 1-7].
281 [Accel Mask]
Controls which adapters can select
[Accel Time 1, 2].
282 [Decel Mask]
Controls which adapters can select
[Decel Time 1, 2].
283 [Fault Clr Mask]
Controls which adapters can clear a fault.
See
See
See
See
284 [MOP Mask]
Controls which adapters can issue MOP commands to the drive.
285 [Local Mask]
Controls which adapters are allowed to take exclusive control of drive logic commands (except stop). Exclusive
“local” control can only be taken while the drive is stopped.
See
See
Example: A customer's process is normally controlled by a remote PLC, but the drive is mounted on the machine. The customer does not want anyone to walk up to the drive and reverse the motor because it would damage the process. The local HIM (drive mounted Adapter 1) is configured with an operator's panel that includes a “REV” Button. To assure that only the PLC (connected to Adapter 2) has direction control, the
[Direction Mask] can be set as follows:
288 thru
297
288 thru
297
288 thru
297
288 thru
297
288 thru
297
288 thru
297
288 thru
297
288 thru
297
288 thru
297
2-98
Masks
Direction Mask
0 0 0 0 0 1 0 0
Adapter # X 6 5 4 3 2 1 0
This “masks out” the reverse function from all adapters except Adapter 2, making the local HIM (Adapter 1) REV button inoperable. Also see
MOP
MOP
2-99
The Motor Operated Pot (MOP) function is one of the sources for the frequency reference. The MOP function uses digital inputs to increment or decrement the Speed reference at a programmed rate.
The MOP has three components:
•
[MOP Rate] parameter
•
[Save MOP Ref] parameter
•
[MOP Frequency] parameter
MOP increment input
MOP decrement input
The MOP reference rate is defined in [MOP rate]. The MOP function is defined graphically below
MOP dec
MOP inc
MOP reference
MOP rate is defined in Hz/sec. The MOP reference will increase/decrease linearly at that rate as long as the MOP inc or dec is asserted via TB or DPI port (the MOP inputs are treated as level sensitive).
Both the MOP inc and dec will use the same rate (i.e. they can not be separately configured). The MOP rate is the rate of change of the MOP reference. The selected active MOP reference still feeds the ramp function to arrive at the present commanded speed/frequency (eg. is still based on the accel/decel rates). Asserting both MOP inc and dec inputs simultaneously will result in no change to the MOP reference.
[Save MOP Ref] is a packed boolean parameter with two bits used as follows:
Bit 0
0 = Don’t save MOP reference on power-down (default)
1 = Save MOP reference on power-down
If the value is “SAVE MOP Ref” when the drive power returns, the MOP reference is reloaded with the value from the non-volatile memory.
When the bit is set to 0, the MOP reference defaults to zero when power is restored. The MOP save reference parameter and the MOP rate parameter can be changed while the drive is running.
Bit 1
0 = Reset MOP reference when STOP edge is asserted
1 = Don’t reset MOP reference when STOP is asserted (default)
2-100
MOP
Important: The MOP reset only occurs on the stop edge and is not continuously cleared because the stop is asserted (this is always processed when a stop edge is seen, even if the drive is stopped). The reset only applies to the stop edge and not when a fault is detected.
In order to change the MOP reference (increment or decrement) a given DPI port must have the MOP mask asserted (and the logic mask asserted). In the case of the terminal block, if the MOP increment or MOP decrement function is assigned to a digital input, then the act of asserting either of those inputs will cause the TB to try and gain ownership of the MOP inc/ dec reference change.
Ownership of the MOP function can be obtained even if the MOP reference is not being used to control the drive. If ownership is granted, the owner has the right to inc/dec the MOP reference. Whether this reference is the active speed reference for the drive is separately selected via TB reference select, or Ref A/B select through DPI.
The MOP Frequency parameter is an output which shows the active value of the MOP reference in Hz x 10.
MOP handling with Direction Mode
If the Direction Mode is configured for “Unipolar,” then the MOP decrement will clamp at zero not allowing the user to generate a negative
MOP reference that is clamped off by the reference generation. When
Direction Mode = “Bipolar” the MOP reference will permit the decrement function to produce negative values. If the drive is configured for Direction
Mode = “Bipolar” and then is changed to “Unipolar”, the MOP reference will also be clamped at zero if it was less than zero.
Motor Nameplate
Motor Nameplate
2-101
[Motor NP Volts]
The motor nameplate base voltage defines the output voltage, when operating at rated current, rated speed, and rated temperature.
[Motor NP FLA]
The motor nameplate defines the output amps, when operating at rated voltage, rated speed, and rated temperature. It is used in the motor thermal overload, and in the calculation of slip.
[Motor NP Hz]
The motor nameplate base frequency defines the output frequency, when operating at rated voltage, rated current, rated speed, and rated temperature.
[Motor NP RPM]
The motor nameplate RPM defines the rated speed, when operating at motor nameplate base frequency, rated current, base voltage, and rated temperature. This is used to calculate slip.
[Motor NP Power]
The motor nameplate power is used together with the other nameplate values to calculate default values for motor parameters to and facilitate the commissioning process. This may be entered in horsepower or in kilowatts as selected in the previous parameter or kW for certain catalog numbers and
HP for others.
[Motor NP Pwr Units]
The rated power of the motor may be entered in horsepower or in kilowatts.
This parameter determines the units on the following parameter.
2-102
Motor Overload
Motor Overload
The motor thermal overload uses an IT algorithm to model the temperature of the motor. The curve is modeled after a Class 10 protection thermal overload relay that produces a theoretical trip at 600% motor current in ten
(10) seconds and continuously operates at full motor current.
Motor Overload Curve
100000
10000
Cold
Hot
1000
100
10
100 125 150 175 200
Full Load Amps (%)
225
250
Motor nameplate FLA programming is used to set the overload feature.
This parameter, which is set in the start up procedure, is adjustable from 0 -
200% of drive rating and should be set for the actual motor FLA rating.
Setting the correct bit in [Fault Config x] to zero disables the motor thermal overload. Most multimotor applications (using one drive and more than one motor) will require the MTO to be disabled since the drive would be unable to distinguish each individual motor’s current and provide protection.
Operation of the overload is based on three parameters; [Motor NP FLA],
[Motor OL Factor] and [Motor OL Hertz].
1. [Motor NP FLA] is the base value for motor protection.
2. [Motor OL Factor] is used to adjust for the service factor of the motor.
Within the drive, motor nameplate FLA is multiplied by motor overload factor to select the rated current for the motor thermal overload. This can be used to raise or lower the level of current that will cause the motor thermal overload to trip without the need to adjust the motor FLA. For example, if motor nameplate FLA is 10 Amps and motor overload factor is 1.2, then motor thermal overload will use 12 Amps as 100%.
Motor Overload
2-103
Changing Overload Factor
140
120
100
80
60
40
20
OL % = 1.20
OL % = 1.00
OL % = 0.80
0 10 20 30 40 50 60 70 80 90 100
% of Base Speed
3. [Motor OL Hertz] is used to further protect motors with limited speed ranges. Since some motors may not have sufficient cooling ability at lower speeds, the Overload feature can be programmed to increase protection in the lower speed areas. This parameter defines the frequency where derating the motor overload capacity should begin. As shown here, the motor overload capacity is reduced when operating below the motor overload Hz. For all settings of overload Hz other than zero, the overload capacity is reduced to 70% when output frequency is zero.
During DC injection the motor current may exceed 70% of FLA, but this will cause the Motor Thermal Overload to trip sooner than when operating at base speed. At low frequencies, the limiting factor may be the Drive Thermal Overload.
Changing Overload Hz
120
100
80
60
40
20
OL Hz = 10
OL Hz = 25
OL Hz = 50
0 10 20 30 40 50 60 70 80 90 100
% of Base Speed
2-104
Motor Overload
Duty Cycle for the Motor Thermal Overload
When the motor is cold motor thermal overload will allow 3 minutes at
150%. When the motor is hot motor thermal overload will allow 1 minute at
150%. A continuous load of 102% will not trip. The duty cycle of the motor thermal overload is defined as follows. If operating continuous at 100%
FLA, and the load increases to 150% FLA for 59 seconds and then returns to 100%FLA, the load must remain at 100% FLA for 20 minutes to reach steady state.
1 Minute 1 Minute
150%
100%
20 Minutes
The ratio of 1:20 is the same for all durations of 150%. When operating continuous at 100%, if the load increases to 150% for 1 second the load must then return to 100% for 20 seconds before another step to 150%
120
125
130
135
FLA%
105
110
115
140
145
150
291
244
209
180
934
619
456
357
Cold Trip
Time
6320
1794
122
94
74
60
667
375
240
167
Hot Trip
Time
5995
1500
170
175
180
185
FLA%
155
160
165
190
195
200
88
82
76
70
128
115
105
96
Cold Trip
Time
160
142
21
19
17
15
36
31
27
23
Hot Trip
Time
50
42
220
225
230
235
FLA%
205
210
215
240
245
250
46
44
41
39
58
54
51
48
Cold Trip
Time
66
62
7
7
8
8
11
10
10
9
Hot Trip
Time
14
12
Motor Start/Stop
Precautions
Motor Start/Stop Precautions
2-105
Input Contactor Precautions
!
!
ATTENTION: A contactor or other device that routinely disconnects and reapplies the AC line to the drive to start and stop the motor can cause drive hardware damage. The drive is designed to use control input signals that will start and stop the motor. If an input device is used, operation must not exceed one cycle per minute or drive damage will occur.
ATTENTION: The drive start/stop/enable control circuitry includes solid state components. If hazards due to accidental contact with moving machinery or unintentional flow of liquid, gas or solids exist, an additional hardwired stop circuit may be required to remove the AC line to the drive. An auxiliary braking method may be required.
Output Contactor Precaution
!
ATTENTION: To guard against drive damage when using output contactors, the following information must be read and understood. One or more output contactors may be installed between the drive and motor(s) for the purpose of disconnecting or isolating certain motors/loads. If a contactor is opened while the drive is operating, power will be removed from the respective motor, but the drive will continue to produce voltage at the output terminals. In addition, reconnecting a motor to an active drive (by closing the contactor) could produce excessive current that may cause the drive to fault. If any of these conditions are determined to be undesirable or unsafe, an auxiliary contact on the output contactor should be wired to a drive digital input that is programmed as “Enable.” This will cause the drive to execute a coast-to-stop (cease output) whenever an output contactor is opened.
Mounting
Refer to the Chapter 1 of the correct drive User Manual for mounting instructions and limitations. As a general rule, drives should be mounted on a metallic flat surface in the vertical orientation. If other orientations are being considered, contact the factory for additional data.
2-106
Output Current
Output Current
Output Devices
[Output Current]
This parameter displays the total output current of the drive. The current value displayed here is the vector sum of both torque producing and flux producing current components.
Drive Output Contactor
!
ATTENTION: To guard against drive damage when using output contactors, the following information must be read and understood. One or more output contactors may be installed between the drive and motor(s) for the purpose of disconnecting or isolating certain motors/loads. If a contactor is opened while the drive is operating, power will be removed from the respective motor, but the drive will continue to produce voltage at the output terminals. In addition, reconnecting a motor to an active drive (by closing the contactor) could produce excessive current that may cause the drive to fault. If any of these conditions are determined to be undesirable or unsafe, an auxiliary contact on the output contactor should be wired to a drive digital input that is programmed as “Enable.” This will cause the drive to execute a coast-to-stop (cease output) whenever an output contactor is opened.
Cable Termination
Voltage doubling at motor terminals, known as reflected wave phenomenon, standing wave or transmission line effect, can occur when using drives with long motor cables.
Inverter duty motors with phase-to-phase insulation ratings of 1200 volts or higher should be used to minimize effects of reflected wave on motor insulation life.
Applications with non-inverter duty motors or any motor with exceptionally long leads may require an output filter or cable terminator. A filter or terminator will help limit reflection to the motor, to levels which are less than the motor insulation rating.
Cable length restrictions for unterminated cables are discussed on
page 2-32 . Remember that the voltage doubling phenomenon occurs at dif-
ferent lengths for different drive ratings. If your installation requires longer motor cable lengths, a reactor or cable terminator is recommended.
Optional Output Reactor
Bulletin 1321 Reactors can be used for drive input and output. These reactors are specifically constructed to accommodate IGBT inverter applications with switching frequencies up to 20 kHz. They have a UL approved dielectric strength of 4000 volts, opposed to a normal rating of 2500 volts.
The first two and last two turns of each coil are triple insulated to guard against insulation breakdown resulting from high dv/dt. When using motor
Output Frequency
Output Power
Output Voltage
Output Frequency
2-107
line reactors, it is recommended that the drive PWM frequency be set to its lowest value to minimize losses in the reactors.
By using an output reactor the effective motor voltage will be lower because of the voltage drop across the reactor - this may also mean a reduction of motor torque.
[Output Frequency]
This parameter displays the actual output frequency of the drive. The output frequency is created by a summation of commanded frequency and any active speed regulator such as slip compensation, PI Loop, bus regulator.
The actual output may be different than the commanded frequency.
This parameter displays the output kW of the drive. The output power is a calculated value and tends to be inaccurate at lower speeds. It is not recommended for use as a process variable to control a process.
[Output Voltage]
This parameter displays the actual output voltage at the drive output terminals. The actual output voltage may be different than that determined by the sensorless vector or V/Hz algorithms because it may be modified by features such as the Auto-Economizer.
2-108
Overspeed Limit
Overspeed Limit
The Overspeed Limit is a user programmable value that allows operation at maximum speed but also provides an “overspeed band” that will allow a speed regulator such as encoder feedback or slip compensation to increase the output frequency above maximum Speed in order to maintain maximum
Motor Speed.
illustrates a typical Custom V/Hz profile. Minimum Speed
determines the lower speed reference limit during normal operation.
Maximum Speed determines the upper speed reference limit. The two
“Speed” parameters only limit the speed reference and not the output frequency.
The actual output at maximum speed reference is the sum of the speed reference plus “speed adder” components from functions such as slip compensation, encoder feedback or process trim.
The Overspeed Limit is added to Maximum Speed and the sum of the two
(Speed Limit) limits is output. This sum (Speed Limit) is compared to
Maximum Frequency and an alarm is initiated which prevents operation if the Speed Limit exceeds Maximum Frequency.
Figure 2.13 Typical V/Hz Curve for Full Custom (with Speed/Frequency Limits
Allowable Output Frequency Range -
Bus Regulation or Current Limit
Allowable Output Frequency Range - Normal Operation
1
Allowable Speed Reference Range
Maximum
Voltage
Motor NP
Voltage
Frequency Trim due to Speed
Control Mode
Overspeed
Limit
Break
Voltage
Start
Boost
Run
Boost
0 Minimum
Speed
Break
Frequency
Motor NP Hz Maximum
Speed
Output
Frequency
Limit
Maximum
Frequency
Frequency
Note 1: The lower limit on this range can be 0 depending on the value of Speed Adder
Owners
Owners
2-109
An owner is a parameter that contains one bit for each of the possible DPI or SCANport adapters. The bits are set high (value of 1) when its adapter is currently issuing that command, and set low when its adapter is not issuing that command. Ownership falls into two categories;
Exclusive
Only one adapter at a time can issue the command and only one bit in the parameter will be high.
For example, it is not allowable to have one Adapter command the drive to run in the forward direction while another Adapter is issuing a command to make the drive run in reverse. Direction Control, therefore, is exclusive ownership.
Non Exclusive
Multiple adapters can simultaneously issue the same command and multiple bits may be high.
288 [Stop Owner]
Adapters presently issuing a valid stop command.
Read Only 276 thru
285 x
15 x
14 x
13 x
12 x
11 x
10 x
9 x
8 x
7 x
6
0
5
D
PI P ort
5
D
PI P ort
4
D
PI P ort
3
D
PI P ort
2
D
PI P
1 ort
D ig ital In
0 0 0 0 1
1 =Issuing Command
4 3 2 1 0
0 =No Command x =Reserved
Bit #
289 [Start Owner]
Adapters that are presently issuing a valid start command.
290 [Jog Owner]
See [Stop Owner]
See [Stop Owner]
Adapters that are presently issuing a valid jog command.
291 [Direction Owner]
Adapter that currently has exclusive control of direction changes.
292 [Reference Owner]
Adapter that has the exclusive control of the command frequency source selection.
293 [Accel Owner]
Adapter that has exclusive control of selecting [Accel Time 1, 2].
See [Stop Owner]
See [Stop Owner]
See [Stop Owner]
See [Stop Owner] 294 [Decel Owner]
Adapter that has exclusive control of selecting [Decel Time 1, 2].
295 [Fault Clr Owner]
Adapter that is presently clearing a fault.
See [Stop Owner]
296 [MOP Owner]
Adapters that are currently issuing increases or decreases in MOP command frequency.
297 [Local Owner]
Adapter that has requested exclusive control of all drive logic functions. If an adapter is in local lockout, all other functions (except stop) on all other adapters are locked out and non-functional. Local control can only be obtained when the drive is not running.
See [Stop Owner]
See [Stop Owner]
276 thru
285
276 thru
285
276 thru
285
276 thru
285
140
276 thru
285
142
276 thru
285
276 thru
285
276 thru
285
276 thru
285
2-110
Owners
Conversely, any number of adapters can simultaneously issue Stop
Commands. Therefore, Stop Ownership is not exclusive.
Example:
The operator presses the Stop button on the Local HIM to stop the drive.
When the operator attempts to restart the drive by pressing the HIM Start button, the drive does not restart. The operator needs to determine why the drive will not restart.
The operator first views the Start owner to be certain that the Start button on the HIM is issuing a command.
Start Owner
0 0 0 0 0 0 0 0
Adapter # X 6 5 4 3 2 1 0
When the local Start button is pressed, the display indicates that the command is coming from the HIM.
Start Owner
0 0 0 0 0 0 1 0
Adapter # X 6 5 4 3 2 1 0
The [Start Owner] indicates that there is not any maintained Start commands causing the drive to run.
Stop Owner
0 0 0 0 0 0 0 1
Adapter # X 6 5 4 3 2 1 0
The operator then checks the Stop Owner. Notice that bit 0 is a value of “1,” indicating that the Stop device wired to the Digital Input terminal block is open, issuing a Stop command to the drive.
Until this device is reclosed, a permanent Start Inhibit condition exists and the drive will not restart.
Also refer to
and
Parameter Access
Level
PET
Parameter Access Level
2-111
The PowerFlex 70 allows the user to restrict the number of parameters that are viewable on the LCD or LED HIM. By limiting the parameter view to the most commonly adjusted set, additional features that may make the drive seem more complicated are hidden.
If you are trying to gain access to a particular parameter and the HIM skips over it, you must change the parameter view from “Basic” to “Advanced.”
This can be accomplished in two different ways:
•
Press “Alt” and then “View” from the HIM and change the view.
or
•
Reprogram Parameter 196 [Param Access Lvl] to “Advanced”.
Pulse Elimination Technique – See
Reflected Wave on page 2-132 .
2-112
Power Loss
Power Loss
Some processes or applications cannot tolerate drive output interruptions caused by momentary power outages. When AC input line power is interrupted to the drive, user programming can determine the drive’s reaction.
Terms
The following is a definition of terms. Some of these values are drive parameters and some are not. The description of how these operate is explained below
Term
Vbus
Vmem
Definition
The instantaneous DC bus voltage.
The average DC bus voltage. A measure of the “nominal” bus voltage determined by heavily filtering bus voltage. Just after the pre-charge relay is closed during the initial power-up bus pre-charge, bus memory is set equal to bus voltage. Thereafter it is updated by ramping at a very slow rate toward Vbus. The filtered value ramps at 2.4VDC
per minute (for a 480VAC drive). An increase in Vmem is blocked during deceleration to prevent a false high value due to the bus being pumped up by regeneration. Any change to Vmem is blocked during inertia ride through.
Vslew The rate of change of Vmem in volts per minute.
Vrecover The threshold for recovery from power loss.
Vtrigger The threshold to detect power loss.
PowerFlex 700
The level is adjustable. The default is the value in the PF700 Bus Level table. If “Pwr Loss
Lvl” is selected as an input function AND energized, Vtrigger is set to Vmem minus
[Power Loss Level].
Vopen is normally 60VDC below Vtrigger (in a 480VAC drive). Both Vopen and Vtrigger are limited to a minimum of Vmin. This is only a factor if [Power Loss Level] is set to a large value.
PowerFlex 70
This is a fixed value.
WARNING:
When using a value of Parameter #186 [Power Loss Level] larger than default, the customer must provide a minimum line impedance to limit inrush current when the power line recovers. The input impedance should be equal or greater than the equivalent of a
5% transformer with a VA rating 5 times the drive’s input VA rating.
Vinertia The software regulation reference for Vbus during inertia ride through.
Vclose The threshold to close the pre-charge contactor.
Vopen
Vmin
Voff
The threshold to open the pre-charge contactor.
The minimum value of Vopen.
The bus voltage below which the switching power supply falls out of regulation.
Table 2.T PF70 Bus Levels
Class
Vslew
Vrecover
Vclose
Vtrigger1
Vtrigger2
Vopen
Vmin
Voff 3
200/240 VAC
1.2 VDC
Vmem – 30V
Vmem – 60V
Vmem – 60V
Vmem – 90V
Vmem – 90V
204 VDC
?
400/480 VAC
2.4 VDC
Vmem – 60V
Vmem – 120V
Vmem – 120V
Vmem – 180V
Vmem – 180V
407 VDC
300 VDC
600/690 VAC
3.0 VDC
Vmem – 75V
Vmem – 150V
Vmem – 150V
Vmem – 225V
Vmem – 225V
509 VDC
?
Power Loss
2-113
700
650
600
550
500
450
Line Loss Mode = Decel
Recover
Close
Trigger
Open
400
350 400
AC Input Volts
Table 2.U PF700 Bus Levels
Class
Vslew
Vrecover
Vclose
Vtrigger1,2
Vtrigger1,3
Vopen
Vopen4
Vmin
Voff 5
200/240V AC
1.2 VDC
Vmem – 30V
Vmem – 60V
Vmem – 60V
Vmem – 90V
Vmem – 90V
153 VDC
153 VDC
–
450
Note 1:Vtrigger is adjustable, these are the standard values.
Line Loss Mode = Coast
550
500
450
400
350
300
700
650
600
Recover
Close
Trigger
Open
350 400
AC Input Volts
450
550
500
450
400
350
300
700
650
600
400/480V AC
2.4 VDC
Vmem – 60V
Vmem – 120V
Vmem – 120V
Vmem – 180V
Vmem – 180V
305 VDC
305 VDC
200 VDC
700
650
600
550
500
450
400
350
350
Line Loss Mode = Coast
Recover
Close
Trigger
Open
400
AC Input Volts
600/690V AC
3.0 VDC
Vmem – 75V
Vmem – 150V
Vmem – 150V
Vmem – 225V
Vmem – 225V
382 VDC
382 VDC
–
Line Loss Mode = Decel
Recover
Close
Trigger
Open
400
AC Input Volts
450
450
550
500
450
400
350
300
700
650
600
Line Loss Mode = Continue
Recover
Close
Trigger
Open
350 400
AC Input Volts
450
2-114
Power Loss
Restart after Power Restoration
If a power loss causes the drive to coast and power recovers the drive will return to powering the motor if it is in a “run permit” state. The drive is in a
“run permit” state if:
3 wire mode – it is not faulted and if all Enable and Not Stop inputs are energized.
2 wire mode – it is not faulted and if all Enable, Not Stop, and Run inputs are energized.
Power Loss Actions
The drive is designed to operate at a nominal bus voltage. When Vbus falls below this nominal value by a significant amount, action can be taken to preserve the bus energy and keep the drive logic alive as long as possible.
The drive will have three methods of dealing with low bus voltages:
•
“Coast” – Disable the transistors and allow the motor to coast.
•
“Decel” – Decelerate the motor at just the correct rate so that the energy absorbed from the mechanical load balances the losses.
•
“Continue” – Allow the drive to power the motor down to half bus voltage.
013
185
184 [Power Loss Mode]
Sets the reaction to a loss of input power.
Power loss is recognized when:
•
DC bus voltage is
≤
73% of [DC Bus
Memory] and [Power Loss Mode] is set to “Coast”.
•
DC bus voltage is
≤
82% of [DC Bus
Memory] and [Power Loss Mode] is set to “Decel”.
Default:
Options:
0
0
1
2
3
4
“Coast”
“Coast”
“Decel”
“Continue”
“Coast Input”
“Decel Input”
Coast
This is the default mode of operation.
The drive determines a power loss has occurred if the bus voltage drops below Vtrigger. If the drive is running the inverter output is disabled and the motor coasts.
The power loss alarm in [Drive Alarm 1] is set and the power loss timer starts.
The Alarm bit in [Drive Status 1] is set if the Power Loss bit in [Alarm
Config 1] is set.
The drive faults with a F003 – Power Loss Fault if the power loss timer exceeds [Power Loss Time] and the Power Loss bit in [Fault Config 1] is set.
The drive faults with a F004 – UnderVoltage fault if the bus voltage falls below Vmin and the UnderVoltage bit in [Fault Config 1] is set.
The pre-charge relay opens if the bus voltage drops below Vopen and closes if the bus voltage rises above Vclose
Power Loss
2-115
If the bus voltage rises above Vrecover for 20mS, the drive determines the power loss is over. The power loss alarm is cleared.
If the drive is in a “run permit” state, the reconnect algorithm is run to match the speed of the motor. The drive then accelerates at the programmed rate to the set speed.
Bus Voltage
680V
620V
560V
500V
407V
305V
Motor Speed
Power Loss
Output Enable
Pre-Charge
Drive Fault
480V example shown, see
Decel
This mode of operation is useful if the mechanical load is high inertia and low friction. By recapturing the mechanical energy, converting it to electrical energy and returning it to the drive, the bus voltage is maintained.
As long as there is mechanical energy, the ride through time is extended and the motor remains fully fluxed up. If AC input power is restored, the drive can ramp the motor to the correct speed without the need for reconnecting.
The drive determines a power loss has occurred if the bus voltage drops below Vtrigger.
If the drive is running, the inertia ride through function is activated.
The load is decelerated at just the correct rate so that the energy absorbed from the mechanical load balances the losses and bus voltage is regulated to the value Vinertia.
The Power Loss alarm in [Drive Alarm 1] is set and the power loss timer starts.
The Alarm bit in [Drive Status 1] is set if the Power Loss bit in [Alarm
Config 1] is set.
The drive faults with a F003 – Power Loss fault if the power loss timer exceeds [Power Loss Time] and the Power Loss bit in [Fault Config 1] is set.
The drive faults with a F004 – UnderVoltage fault if the bus voltage falls below Vmin and the UnderVoltage bit in [E238 Fault Config 1] is set.
2-116
Power Loss
The inverter output is disabled and the motor coasts if the output frequency drops to zero or if the bus voltage drops below Vopen or if any of the “run permit” inputs are de-energized.
The pre-charge relay opens if the bus voltage drops below Vopen.
The pre-charge relay closes if the bus voltage rises above Vclose
If the bus voltage rises above Vrecover for 20mS, the drive determines the power loss is over. The power loss alarm is cleared.
If the drive is still in inertia ride through operation, the drive immediately accelerates at the programmed rate to the set speed. If the drive is coasting and it is in a “run permit” state, the reconnect algorithm is run to match the speed of the motor. The drive then accelerates at the programmed rate to the set speed.
Bus Voltage
680V
620V
560V
500V
407V
305V
Motor Speed
Power Loss
Output Enable
Pre-Charge
Drive Fault
480V example shown, see
Half Voltage
This mode provides the maximum power ride through. In a typical application 230VAC motors are used with a 480VAC drive, the input voltage can then drop to half and the drive is still able to supply full power to the motor.
!
ATTENTION: To guard against drive damage, a minimum line impedance must be provided to limit inrush current when the power line recovers. The input impedance should be equal or greater than the equivalent of a 5% transformer with a VA rating
6 times the drive’s input VA rating.
The drive determines a power loss has occurred if the bus voltage drops below Vtrigger.
If the drive is running the inverter output is disabled and the motor coasts.
If the bus voltage drops below Vopen/Vmin (In this mode of operation
Vopen and Vmin are the same value) or if the Enable input is de-energized, the inverter output is disabled and the motor coasts. If the Not Stop or Run inputs are de-energized, the drive stops in the programmed manner.
Power Loss
2-117
The pre-charge relay opens if the bus voltage drops below Vopen/Vmin and closes if the bus voltage rises above Vclose.
The power loss alarm in [Drive Alarm 1] is set and the power loss timer starts. The Alarm bit in [Drive Status 1] is set if the Power Loss bit in
[Alarm Config 1] is set.
The drive faults with a F003 – Power Loss fault if the power loss timer exceeds [Power Loss Time] and the Power Loss bit in [Fault Config 1] is set.
The drive faults with a F004 – UnderVoltage fault if the bus voltage falls below Vmin and the UnderVoltage bit in [Fault Config 1] is set.
If the bus voltage rises above Vrecover for 20mS, the drive determines the power loss is over. The power loss alarm is cleared.
If the drive is coasting and if it is in a “run permit” state, the reconnect algorithm is run to match the speed of the motor. The drive then accelerates at the programmed rate to the set speed.
Bus Voltage
680V
620V
560V
365V
305V
Motor Speed
Power Loss
Output Enable
Pre-Charge
Drive Fault
480V example shown, see
Coast Input (PowerFlex700 Only)
This mode can provide additional ride through time by sensing the power loss via an external device that monitors the power line and provides a hardware power loss signal. This signal is then connected to the drive through the “pulse” input (because of its high-speed capability). Normally this hardware power loss input will provide a power loss signal before the bus drops to less than Vopen.
The drive determines a power loss has occurred if the “pulse” input is de-energized OR the bus voltage drops below Vopen. If the drive is running, the inverter output is disabled.
The Power Loss alarm in [Drive Alarm 1] is set and the power loss timer starts.
2-118
Power Loss
The Alarm bit in [Drive Status 1] is set if the Power Loss bit in [Alarm
Config 1] is set.
The drive faults with a F003 – Power Loss fault if the power loss timer exceeds [Power Loss Time] and the Power Loss bit in [Fault Config 1] is set.
The drive faults with a F004 – UnderVoltage fault if the bus voltage falls below Vmin and the UnderVoltage bit in [Fault Config 1] is set.
The pre-charge relay opens if the bus voltage drops below Vopen and closes if the bus voltage rises above Vclose.
If the “pulse” input is re energized and the pre-charge relay is closed, the drive determines the power loss is over. The power loss alarm is cleared.
If the drive is in a “run permit” state, the reconnect algorithm is run to match the speed of the motor. The drive then accelerates at the programmed rate to the set speed.
Decel Input (PF700 only)
This mode can provide additional ride through time by sensing the power loss via an external device that monitors the power line and provides a hardware power loss signal. This signal is then connected to the drive through the “pulse” input (because of its high-speed capability). Normally this hardware power loss input will provide a power loss signal before the bus drops to less than Vopen.
The drive determine a power loss has occurred if the “pulse” input is de-energized or the bus voltage drops below Vopen.
If the drive is running, the inertia ride through function is activated. The load is decelerated at just the correct rate so that the energy absorbed from the mechanical load balances the losses and bus voltage is regulated to the value Vmem.
If the output frequency drops to zero or if the bus voltage drops below
Vopen or if any of the “run permit” inputs are de-energized, the inverter output is disabled and the motor coasts.
The power loss alarm in [Drive Alarm 1] is set and the power loss timer starts. The Alarm bit in [Drive Status 1] is set if the Power Loss bit in
[Alarm Config 1] is set.
The drive faults with a F003 – Power Loss fault if the power loss timer exceeds [Power Loss Time] and the Power Loss bit in [E238 Fault Config 1] is set.
The drive faults with a F004 – UnderVoltage fault if the bus voltage falls below Vmin and the UnderVoltage bit in [Fault Config 1] is set.
The pre-charge relay opens if the bus voltage drops below Vopen and closes if the bus voltage rises above Vclose.
Power Loss
2-119
If power recovers while the drive is still in inertia ride through the power loss alarm is cleared and it then accelerates at the programmed rate to the set speed. Otherwise, if power recovers before power supply shutdown, the power loss alarm is cleared.
If the drive is in a “run permit” state, the reconnect algorithm is run to match the speed of the motor. The drive then accelerates at the programmed rate to the set speed.
2-120
Preset Frequency
Preset Frequency
There are 7 Preset Frequency parameters that are used to store a discrete frequency value. This value can be used for a speed reference or PI
Reference. When used as a speed reference, they are accessed via manipulation of the digital inputs or the DPI reference command. Preset frequencies have a range of plus/minus [Maximum Speed].
Process PI Loop
Process PI Loop
2-121
[PI Config]
[PI Control]
[PI Reference Sel]
[PI Setpoint]
[PI Feedback Sel]
[PI Integral Time]
[PI Prop Gain]
[PI Upper/Lower Limit]
[PI Preload]
[PI Status]
[PI Ref Meter]
[PI Feedback Meter]
[PI Error Meter]
[PI Output Meter]
The internal PI function provides closed loop process control with proportional and integral control action. The function is designed to be used in applications that require simple control of a process without external control devices. The PI function allows the microprocessor to follow a single process control loop.
The PI function reads a process variable input to the drive and compares it to a desired setpoint stored in the drive. The algorithm will then adjust the output of the PI regulator, changing drive output frequency to try and make the process variable equal the setpoint.
Proportional control (P) adjusts output based on size of the error (larger error = proportionally larger correction). If the error is doubled, then the output of the proportional control is doubled and, conversely, if the error is cut in half then the output of the proportional output will be cut in half. With proportional control there is always an error, so the feedback and the reference are never equal.
Integral control (I) adjusts the output based on the duration of the error.
(The longer the error is present, the harder it tries to correct). The integral control by itself is a ramp output correction. This type of control gives a smoothing effect to the output and will continue to integrate until zero error is achieved. By itself, integral control is slower than many applications require and therefore is combined with proportional control (PI).
Derivative Control (D) adjusts the output based on the rate of change of the error and, by itself, tends to be unstable. The faster that the error is changing, the larger change to the output. Derivative control is generally not required and, when it is used, is almost always combined with proportional and integral control (PID).
The PI function can perform a combination of proportional and integral control. It does not perform derivative control, however, the accel / decel control of the drive can be considered as providing derivative control.
2-122
Process PI Loop
There are two ways the PI Controller can be configured to operate.
•
Process Trim - The PI Output can be added to the master speed reference
•
Process Control - PI can have exclusive control of the commanded speed.
The selection between these two modes of operation is done in the [PI
Configuration] parameter.
Process Trim
Process Trim takes the output of PI regulator and sums it with a master speed reference to control the process. In the following example, the master speed reference sets the wind/unwind speed and the dancer pot signal is used as a PI Feedback to control the tension in the system. An equilibrium point is programmed as PI Reference, and as the tension increases or decreases during winding, the master speed is trimmed to compensate and maintain tension near the equilibrium point.
0 Volts
Equilibrium Point
[PI Reference Sel]
Dancer Pot
[PI Feedback Sel]
10 Volts
Master Speed Reference
When the PI is disabled the commanded speed is the ramped speed reference.
Slip Adder
Spd Ref
PI Ref
PI Fbk
Process PI
Controller
PI Disabled
Linear Ramp
& S-Curve
+
+
+
+
Slip
Comp
Open
Loop
Process
PI
Speed Control
Spd Cmd
Process PI Loop
2-123
When the PI is enabled, the output of the PI Controller is added to the ramped speed reference.
Slip Adder
Spd Ref
Linear Ramp
& S-Curve
+
+
+
+
Slip
Comp
Open
Loop
Process
PI
Spd Cmd
PI Ref
PI Fbk
Process PI
Controller
PI Enabled Speed Control
Exclusive Control
Process Control takes the output of PI regulator as the speed command. No master speed reference exists and the PI Output directly controls the drive output.
In the pumping application example below, the reference or setpoint is the required pressure in the system. The input from the transducer is the PI feedback and changes as the pressure changes. The drive output frequency is then increased or decreased as needed to maintain system pressure regardless of flow changes. With the drive turning the pump at the required speed, the pressure is maintained in the system.
Pump
Pressure
Transducer
Motor
PI Feedback
Desired Pressure
[PI Reference Sel]
However, when additional valves in the system are opened and the pressure in the system drops, the PI error will alter its output frequency to bring the process back into control.
When the PI is disabled the commanded speed is the ramped speed reference.
2-124
Process PI Loop
Slip Adder
Spd Ref
PI Ref
PI Fbk
Process PI
Controller
PI Disabled
Linear Ramp
& S-Curve
+
+
Slip
Comp
Open
Loop
Process
PI
Speed Control
Spd Cmd
When the PI is enabled, the speed reference is disconnected and PI Output has exclusive control of the commanded speed, passing through the linear ramp and s-curve.
Slip Adder
Spd Ref
Linear Ramp
& S-Curve
+
+
Slip
Comp
Open
Loop
Process
PI
Spd Cmd
PI Ref
Process PI
Controller
PI Fbk PI Enabled
Speed Control
Configuration
To operate the drive in PI regulator Mode, the speed regulation mode must be changed by selecting “Process PI” through the [Speed Control] parameter.
Three parameters are used to configure, control, and indicate the status of the logic associated with the Process PI controller; [PI Configuration], [PI
Control], and [PI Status]. Together these three parameters define the operation of the PI logic.
1. [PI Configuration] is a set of bits that select various modes of operation.
The value of this parameter can only be changed while the drive is stopped.
•
Exclusive Mode - see
•
Invert Error - This feature changes the “sign” of the error, creating a decrease in output for increasing error and an increase in output for decreasing error. An example of this might be an HVAC system with thermostat control. In Summer, a rising thermostat reading commands an increase in drive output because cold air is being blown. In Winter, a falling thermostat commands an increase in drive output because warm air is being blown.
The PI has the option to change the sign of PI Error. This is used when an increase in feedback should cause an increase in output.
PI Enabled
PI Output
Spd Cmd
Process PI Loop
2-125
The option to invert the sign of PI Error is selected in the PI
Configuration parameter.
PI_Config
.Invert
+
PI Ref Sel
–
PI_Config
.Sqrt
-
PI Fdbk Sel
PI Fbk
PI Error
•
Preload Integrator - This feature allows the PI Output to be stepped to a preload value for better dynamic response when the PI Output is enabled. Refer to diagram 2 below.
If PI is not enabled the PI Integrator may be initialized to the PI
Pre-load Value or the current value of the commanded speed. The operation of Preload is selected in the PI Configuration parameter.
PI_Config
.PreloadCmd
PI_Status
.Enabled
Preload Value PI Integrator
Spd Cmd
By default, Pre-load Command is off and the PI Load Value is zero, causing a zero to be loaded into the integrator when the PI is disabled.
As below shown on the left, when the PI is enabled the PI output will start from zero and regulate to the required level. When PI is enabled with PI Load Value is set to a non-zero value the output begins with a step as shown below on the right. This may result in the PI reaching steady state sooner, however if the step is too large the drive may go into current limit which will extend the acceleration.
PI Pre-load Value = 0
PI Pre-load Value
PI Pre-load Value > 0
2-126
Process PI Loop
Pre-load command may be used when the PI has exclusive control of the commanded speed. With the integrator preset to the commanded speed there is no disturbance in commanded speed when PI is enabled. After PI is enabled the PI output is regulated to the required level.
PI Enabled
Start at Spd Cmd
PI Output
Spd Cmd
Pre-load to Command Speed
When the PI is configured to have exclusive control of the commanded speed and the drive is in current limit or voltage limit the integrator is preset to the commanded speed so that it knows where to resume when no longer in limit.
•
Ramp Ref - The PI Ramp Reference feature is used to provide a smooth transition when the PI is enabled and the PI output is used as a speed trim (not exclusive control),.
When PI Ramp Reference is selected in the PI Configuration parameter, and PI is disabled, the value used for the PI reference will be the PI feedback. This will cause PI error to be zero. Then when the
PI is enabled the value used for the PI reference will ramp to the selected value for PI reference at the selected acceleration or deceleration rate. After the PI reference reaches the selected value the ramp is bypassed until the PI is disabled and enabled again. S-curve is not available as part of the PI linear ramp.
•
Zero Clamp - This feature limits the possible drive action to one direction only. Output from the drive will be from zero to maximum frequency forward or zero to maximum frequency reverse. This removes the chance of doing a “plugging” type operation as an attempt to bring the error to zero.
The PI has the option to limit operation so that the output frequency will always have the same sign as the master speed reference. The zero clamp option is selected in the PI Configuration parameter. Zero clamp is disabled when PI has exclusive control of speed command.
For example, if master speed reference is +10 Hz and the output of the PI results in a speed adder of –15 Hz, zero clamp would limit the output frequency to not become less than zero. Likewise, if master speed reference is –10 Hz and the output of the PI results in a speed adder of +15 Hz, zero clamp would limit the output frequency to not become greater than zero.
Process PI Loop
2-127
Spd Ref
PI Ref
PI Fbk
Linear
Ramp
& S-Curve
Process PI
Controller
Spd Ramp
+
+
PI Output
≥
0
PI_Config
.ZeroClamp
+32K
0
0
-32K
+32K
-32K
Spd Cmd
•
Feedback Square Root - This feature uses the square root of the feedback signal as the PI feedback. This is useful in processes that control pressure, since centrifugal fans and pumps vary pressure with the square of speed.
The PI has the option to take the square root of the selected feedback signal. This is used to linearize the feedback when the transducer produces the process variable squared. The result of the square root is normalized back to full scale to provide a consistent range of operation.
The option to take the square root is selected in the PI Configuration parameter.
100.0
75.0
50.0
25.0
0.0
-25.0
-50.0
-75.0
-100.0
-100.0
-75.0
-50.0
-25.0
0.0
25.0
Normalized Feedback
50.0
75.0
100.0
•
Stop Mode (PF700 Only). When Stop Mode is set to “1” and a Stop command is issued to the drive, the PI loop will continue to operate during the decel ramp until the PI output becomes more than the master reference. When set to “0,” the drive will disable PI and perform a normal stop. This bit is active in Trim mode only.
•
Anti-Wind Up (PF700 Only). When Anti-Windup is set to “1” the
PI loop will automatically prevent the integrator from creating an excessive error that could cause loop instability. The integrator will be automatically controlled without the need for PI Reset or PI Hold inputs.
2-128
Process PI Loop
2. [PI Control] is a set of bits to dynamically enable and disable the operation of the process PI controller. When this parameter is interactively written to from a network it must be done through a data link so the values are not written to EEprom.
•
PI Enable - The PI loop can be enabled/disabled. The Enabled status of the PI loop determines when the PI regulator output is part or all of the commanded speed. The logic evaluated for the PI Enabled status is shown in the following ladder diagram.
The drive must be in run before the PI Enabled status can turn on. The
PI will remain disabled when the drive is jogged. The PI is disabled when the drive begins a ramp to stop, except in the PowerFlex 700 when it is in Trim mode and the Stop mode bit in [PI Configuration] is on.
When a digital input is configured as “PI Enable,” the PI Enable bit of
[PI Control] must be turned on for the PI loop to become enabled.
If a digital input is not configured as “PI Enable” and the PI Enable bit in [PI Control] is turned on, then the PI loop may become enabled.
If the PI Enable bit of [PI Control] is left continuously, then the PI may become enabled as soon as the drive goes into run. If analog input signal loss is detected, the PI loop is disabled.
Running Stopping
DigInCfg
.PI_Enable
DigIn
.PI_Enable
PI_Control
.PI_Enable
Signal Loss
PI_Status
.Enabled
DigInCfg
.PI_Enable
PI_Control
.PI_Enable
•
PI Hold - The Process PI Controller has the option to hold the integrator at the current value so if some part of the process is in limit the integrator will maintain the present value to avoid windup in the integrator.
The logic to hold the integrator at the current value is shown in the following ladder diagram. There are three conditions under which hold will turn on.
– If a digital input is configured to provide PI Hold and that digital input is turned on then the PI integrator will stop changing. Note that when a digital input is configured to provide PI Hold that takes precedence over the PI Control parameter.
– If a digital input is not configured to provide PI Hold and the PI Hold bit in the PI Control parameter is turned on then the PI integrator will stop changing.
Process PI Loop
2-129
– If the current limit or voltage limit is active then the PI is put into hold.
DigInCfg
.PI_Hold
DigIn
.PI_Hold
PI_Status
.Hold
DigInCfg
.PI_Hold
Current Lmt or Volt Lmt
PI_Control
.PI_Hold
•
PI Reset – This feature holds the output of the integral function at zero. The term “anti windup” is often applied to similar features. It may be used for integrator preloading during transfer and can be used to hold the integrator at zero during “manual mode”. Take the example of a process whose feedback signal is below the reference point, creating error. The drive will increase its output frequency in an attempt to bring the process into control. If, however, the increase in drive output does not zero the error, additional increases in output will be commanded. When the drive reaches programmed Maximum
Frequency, it is possible that a significant amount of integral value has been “built up” (windup). This may cause undesirable and sudden operation if the system were switched to manual operation and back.
Resetting the integrator eliminates this windup.
NOTE: In the PowerFlex 70, once the drive has reached the programmable positive and negative PI limits, the integrator stops integrating and no further “windup” is possible.
3. [PI Status] parameter is a set of bits that indicate the status of the process PI controller
•
Enabled – The loop is active and controlling the drive output.
•
Hold – A signal has been issued and the integrator is being held at its current value.
•
Reset – A signal has been issued and the integrator is being held at zero.
•
In Limit – The loop output is being clamped at the value set in [PI
Upper/Lower Limit].
PI Reference and Feedback
The selection of the source for the reference signal is entered in the PI
Reference Select parameter. The selection of the source for the feedback signal is selected in the PI Feedback Select parameter. The reference and feedback have the same limit of possible options.
2-130
Process PI Loop
PF70 options include DPI adapter ports, MOP, preset speeds, analog inputs and PI setpoint parameter. In the PF700, options are expanded to also include additional analog inputs, pulse input, and encoder input.
The value used for reference is displayed in PI Reference as a read only parameter. The value used for feedback is displayed in PI Feedback as a read only parameter. These displays are active independent of PI Enabled.
Full scale is displayed as 100.00.
Refer to
Analog Input Configuration on page 2-6
.
PI Setpoint
This parameter can be used as an internal value for the setpoint or reference for the process. If [PI Reference Sel] points to this Parameter, the value entered here will become the equilibrium point for the process.
PI Output
The PI Error is then sent to the Proportional and Integral functions, which are summed together.
PI Gains
The PI Proportional Gain and the PI Integral Gain parameters determine the response of the PI.
The PI Proportional Gain is unitless and defaults to 1.00 for unit gain. With
PI Proportional Gain set to 1.00 and PI Error at 1.00% the PI output will be
1.00% of maximum frequency.
The PI Integral Gain is entered in seconds. If the PI Integral Gain is set to
2.0 seconds and PI Error is 100.00% the PI output will integrate from 0 to
100.00% in 2.0 seconds.
Positive and Negative Limits
The PI has parameters to define the positive and negative limits of the output PI Positive Limit, and PI Negative Limit. The limits are used in two places; on the integrator and on the sum of the Kp + Ki terms.
Providing an external source doesn't turn on Hold, the integrator is allowed to integrate all the way to Positive or Negative limit. If the integrator reaches the limit the value is clamped and the InLimit bit is set in the PI
Status parameter to indicate this condition.
The limits are entered in the range of 100.00.
PI Positive Limit must always be greater than PI Negative Limit.
Process PI Loop
2-131
If the application is Process Control, typically these limits would be set to the maximum allowable frequency setting. This allows the PI regulator to control over the entire required speed range.
If the application is Process Trim, large trim corrections may not be desirable and the limits would be programmed for smaller values.
PI PosLmt
PI NegLmt
PI Kp
PI Error
*
+
+
PI Output
*
PI_Status
.Hold
+
+
In Limit
PI Ki
Z
-1
Output Scaling
The output value produced by the PI is displayed as
±
100.00. Internally this is represented by
±
32767 which corresponds to maximum frequency.
PI_Config
.ZeroClamp
PI_Config
.Exclusive
PI_Status
.Enabled
Spd Ref
PI Pos Limit
PI Neg Limit
PI Kp
PI ExcessErr
*(PI Ref Sel)
PI_Status
.Enabled
PI_Config
.RampCmd
0
*(PI Fbk Sel)
PI_Config
.Sqrt
PI_Config
.Invert
PI Ki
PI_Status
.Hold
Preload Value
Spd Cmd
PI_Config
.PreloadCmd
PI_Status
.Enabled
PI Ref
Linear
Ramp
PI Cmd
+
-
-
Spd Cmd
PI_Config
.Exclusive
Current Limit or Volt Limit
PI Fbk
Figure 2.14 Process PI Block Diagram
abs
≥
PI Error
PI XS Error
*
*
+
+
+
+ z
-1
PI Output
Linear Ramp
& S-Curve
Spd Ramp
+
+
≥
0
+32K
-32K
+32K
0
0
-32K
Spd Cmd
Zclamped
In Limit
2-132
Reflected Wave
Reflected Wave
[Compensation]
The pulses from a Pulse Width Modulation (PWM) inverter using IGBTs are very short in duration (50 nanoseconds to 1 millisecond). These short pulse times combined with the fast rise times (50 to 400 nanoseconds) of the IGBT, will result in excessive over-voltage transients at the motor.
Voltages in excess of twice the DC bus voltage (650V DC nominal at 480V input) will occur at the motor and can cause motor winding failure.
The patented reflected wave correction software in the PowerFlex 70/700 will reduce these over-voltage transients from a VFD to the motor. The correction software modifies the PWM modulator to prevent PWM pulses less than a minimum time from being applied to the motor. The minimum time between PWM pulses is 10 microseconds. The modifications to the
PWM modulator limit the over-voltage transient to 2.25 per unit volts line-to-line peak at 600 feet of cable.
400 V Line = 540V DC bus x 2.25 = 1215V
480 V Line = 650V DC bus x 2.25 = 1463V
600 V Line = 810V DC bus x 2.25 = 1823 V
The software is standard and requires no special parameters or settings.
Inverter 500
V/div
0
<T
α
1670 Vpk
Motor
500
V/div
0
0 5 10 15 20 25 30
Time ( sec)
35 40 45 50
The above figure shows the inverter line-to-line output voltage (top trace) and the motor line-to-line voltage (bottom trace) for a 10 HP, 460V AC inverter, and an unloaded 10 HP AC induction motor at 60 Hz operation.
500 ft. of #12 AWG cable connects the drive to the motor.
Initially, the cable is in a fully charged condition. A transient disturbance occurs by discharging the cable for approximately 4ms. The propagation delay between the inverter terminals and motor terminals is approximately
1ms. The small time between pulses of 4ms does not provide sufficient time to allow the decay of the cable transient. Thus, the second pulse arrives at a point in the motor terminal voltage's natural response and excites a motor over-voltage transient greater than 2 pu. The amplitude of the double pulsed motor over-voltage is determined by a number of variables. These include
Reflected Wave
2-133
the damping characteristics of the cable, bus voltage, and the time between pulses, the carrier frequency, modulation technique, and duty cycle.
The plot below shows the per unit motor overvoltage as a function of cable length. This is for no correction versus the modulation correction code for varied lengths of #12 AWG cable to 600 feet for 4 and 8 kHz carrier frequencies. The output line-to-line voltage was measured at the motor terminals in 100 feet increments.
No Correction vs Correction Method at 4 kHz and 8 kHz Carrier
Frequencies - Vbus = 650, fe = 60 Hz
2.6
2.5
2.4
2.3
2.2
2.1
2
1.9
1.8
1.7
1.6
0
No Correction 4 kHz Carrier
Corrected 4 kHz Carrier
No Correction 8 kHz Carrier
Corrected 8 kHz Carrier
100 200 300 400
Cable Length (Feet)
500 600
Without the correction, the overvoltage increases to unsafe levels with increasing cable length for both carrier frequencies.
The patented modulation correction code reduces the overvoltage for both carrier frequencies and maintains a relatively flat overvoltage level for increasing cable lengths beyond 300 feet.
To determine the maximum recommended motor cable lengths for a particular drive refer to
Cable, Motor Lengths on page 2-32 .
Refer to:
www.ab.com/drives/techpapers/menu
for detailed technical papers.
2-134
Reset Meters
Reset Meters
The Elapsed kW Hour meter and/or Elapsed Time meter parameters are reset when parameter 200 is set to a value not equal to zero. After the reset has occurred, this parameter automatically returns to a value of zero.
200 [Reset Meters]
Resets selected meters to zero.
Default:
Options:
0
0
1
2
“Ready”
“Ready”
“MWh”
“Elapsed Time”
0 = Ready
1 = Reset kW Hour Meter
2 = Reset Elapsed Time Meter
Reset Run
Refer to
Auto Restart (Reset/Run) on page 2-25
.
RFI Filter Grounding
Refer to “Wiring and Grounding Guidelines for PWM AC Drives,” publication DRIVES-IN001A-EN-P.
S Curve
S Curve
2-135
The S Curve function of the PowerFlex family of drives allows control of the “jerk” component of acceleration and deceleration through user adjustment of the S Curve parameter. Jerk is the rate of change of acceleration and controls the transition from steady state speed to acceleration or deceleration and vice versa. By adjusting the percentage of S
Curve applied to the normal accel / decel ramps, the ramp takes the shape of an “S”. This allows a smoother transition that produces less mechanical stress and smoother control for light loads.
Linear Accel & Decel
Acceleration is defined as moving away from zero; deceleration is defined as moving toward zero. The linear acc / dec ramp is active when the S curve% is set to zero. The accel time and maximum frequency determine the ramp rate for speed increases while decel time and maximum frequency determine the ramp rate for speed decreases. Separate times can be set for accel and decel. In addition, a second set of accel and decel times is available. In this example Ta = 1.0 sec, Td = 2.0 sec and Maximum
Frequency is set to 60.0 Hz.
80.0
60.0
40.0
20.0
0.0
-20.0
-40.0
-60.0
-80.0
0.0
1.0
2.0
3.0
4.0
Seconds
5.0
6.0
7.0
8.0
S-Curve Selection
S-curve is enabled by defining the time to extend the acceleration and deceleration. The time is entered as a percentage of acceleration and deceleration time. In this case acceleration time is 2.0 seconds. The line on the left has s-curve set to 0%. The other lines show 25%, 50%, and 100%
S-curve. At 25% S-curve acceleration time is extended by 0.5 seconds (2.0
* 25%). Note that the linear portion of this line has the same slope as when s-curve is set to zero.
70.0
60.0
50.0
40.0
30.0
20.0
10.0
0.0
0.0
0.5
1.0
1.5
2.0
Seconds
2.5
3.0
3.5
4.0
2-136
S Curve
The acceleration and deceleration times are independent but the same
S-curve percentage is applied to both of them. With S-curve set to 50%, acceleration time is extended by 0.5 seconds (1.0 * 50%), and deceleration time is extended by 1.0 seconds (2.0 * 50%).
70.0
60.0
50.0
40.0
30.0
20.0
10.0
0.0
0.0
1.0
2.0
3.0
Seconds
4.0
5.0
6.0
Time to Max Speed
Note that S-curve time is defined for accelerating from 0 to maximum speed. With maximum speed = 60 Hz, Ta = 2.0 sec, and S-curve = 25%, acceleration time is extended by 0.5 seconds (2.0 * 25%). When accelerating to only 30 Hz the acceleration time is still extended by the same amount of time.
70.0
60.0
50.0
40.0
30.0
20.0
10.0
0.0
0.0
0.5
1.0
1.5
Seconds
2.0
2.5
3.0
Crossing Zero Speed
When the commanded frequency passes through zero the frequency will
S-curve to zero and then S-curve to the commanded frequency.
80.0
60.0
40.0
20.0
0.0
-20.0
-40.0
-60.0
-80.0
0.0
1.0
2.0
3.0
4.0
5.0
Seconds
Scaling Blocks
Scaling Blocks
2-137
The following graph shows an acceleration time of 1.0 second. After 0.75
seconds, the acceleration time is changed to 6.0 seconds. When the acceleration rate is changed, the commanded rate is reduced to match the requested rate based on the initial S-curve calculation. After reaching the new acceleration rate, the S-curve is then changed to be a function of the new acceleration rate.
70.0
60.0
50.0
40.0
30.0
20.0
10.0
0.0
0.0
1.0
2.0
3.0
4.0
5.0
Seconds
See
Scaling Blocks on page 2-9 and
2-138
Shear Pin Fault
Shear Pin Fault
This feature allows the user to select programming that will fault the drive if the drive output current exceeds the programmed current limit. As a default, exceeding the set current limit is not a fault condition. However, if the user wants to stop the process in the event of excess current, the Shear Pin feature can be activated. By programming the drive current limit value and enabling the electronic shear pin, current to the motor is limited, and if excess current is demanded by the motor, the drive will fault.
Configuration
The Shear Pin Fault is activated by setting Bit 4 of [Fault Config 1] to “1.”
238 [Fault Config 1]
Enables/disables annunciation of the listed faults.
x
15 x
14 x
13 x
12 x
11 x
10 x
9
Bit #
Factory Default Bit Values x
8 x
7
1
6
D
0
5
ib t utR ries in st T
Sh ear P
M oto r O verL d
U nd erV ge olta er L oss
Po w
0 1
x
1 0
1 =Enabled
4 3 2 1 0
0 =Disabled x =Reserved
The programmable current limit [Current Lmt Sel] should also set to identify the source of the current limit value. If “Cur Lim Val” is selected, then [Current Lmt Val] should be set to the required limit value.
147 [Current Lmt Sel]
Selects the source for the adjustment of current limit (i.e. parameter, analog input, etc.).
Default:
Options:
0
0
1
2
“Cur Lim Val”
“Cur Lim Val”
“Analog In 1”
“Analog In 2”
146
149
A separate fault (Shear Pin Fault, F63) dedicated to the Shear Pin feature, will be generated if the function is activated.
Application Example
In some applications, mechanical hardware can be damaged if the motor is allowed to develop excess torque. If a mechanical jam should occur, shutting down the system may be the only way to prevent damage. For example, a chain conveyor may be able to “hook” itself, causing a jam on the conveyor. Excess torque from the motor could cause chain or other mechanical damage.
By programming the Shear Pin feature, the user can cause the drive to fault, stopping the excess torque before mechanical damage occurs.
Skip Frequency
Skip Frequency
2-139
Figure 2.15 Skip Frequency
Frequency
Command
Frequency
Drive Output
Frequency
Skip + 1/2 Band
Skip Frequency
Skip – 1/2 Band
(A)
(B)
(A)
35 Hz
30 Hz
25 Hz
(B)
Time
Some machinery may have a resonant operating frequency that must be avoided to minimize the risk of equipment damage. To assure that the motor cannot continuously operate at one or more of the points, skip frequencies are used. Parameters 084-086, ([Skip Frequency 1-3]) are available to set the frequencies to be avoided.
The value programmed into the skip frequency parameters sets the center point for an entire “skip band” of frequencies. The width of the band (range of frequency around the center point) is determined by parameter 87, [Skip
Freq Band]. The range is split, half above and half below the skip frequency parameter.
If the commanded frequency of the drive is greater than or equal to the skip
(center) frequency and less than or equal to the high value of the band (skip plus 1/2 band), the drive will set the output frequency to the high value of the band. See (A) in
If the commanded frequency is less than the skip (center) frequency and greater than or equal to the low value of the band (skip minus 1/2 band), the drive will set the output frequency to the low value of the band. See (C) in
2-140
Skip Frequency
Skip Frequency Examples
The skip frequency will have hysteresis so the output does not toggle between high and low values. Three distinct bands can be programmed. If none of the skip bands touch or overlap, each band has its own high/low limit.
Max. Frequency
Skip Frequency 1
Skip Frequency 2
0 Hz
400 Hz.
If skip bands overlap or touch, the center frequency is recalculated based on the highest and lowest band values.
Skip Frequency 1
Skip Frequency 2
0 Hz
If a skip band(s) extend beyond the max frequency limits, the highest band value will be clamped at the max frequency limit. The center frequency is recalculated based on the highest and lowest band values.
400 Hz.
Max.Frequency
Skip
If the band is outside the limits, the skip band is inactive.
0 Hz
400 Hz.
Skip Band 1
Skip Band 2
Adjusted
Skip Band w/Recalculated
Skip Frequency
Adjusted
Skip Band w/Recalculated
Skip Frequency
Skip Frequency 1
Inactive
Skip Band
60 Hz. Max.
Frequency
0 Hz
Acceleration and deceleration are not affected by the skip frequencies.
Normal accel/decel will proceed through the band once the commanded frequency is greater than the skip frequency. See (A) & (B) in
This function affects only continuous operation within the band.
Sleep Mode
Sleep Mode
2-141
Operation
The basic operation of the Sleep-Wake function is to Start (wake) the drive when an analog signal is greater than or equal to the user specified [Wake
Level], and Stop (sleep) the drive when an analog signal is less than or equal to the user specified [Sleep Level]. Setting [Sleep-Wake Mode] to
“Direct” enables the sleep wake function.
Requirements
In addition to enabling the sleep function with [Sleep-Wake Mode], at least one of the following assignments must be made to a digital input: Enable,
Stop-CF, Run, Run Fwd or Run Rev, and the input must be closed. All normal Start Permissives must also be satisfied (Not Stop, Enable, Not
Fault, Not Alarm, etc.).
Conditions to Start/Restart
!
ATTENTION: Enabling the Sleep-Wake function can cause unexpected machine operation during the Wake mode. Equipment damage and/or personal injury can result if this parameter is used in an inappropriate application. Do Not use this function without considering the table below and applicable local, national & international codes, standards, regulations or industry guidelines.
Table 2.V Conditions Required to Start Drive
Input After Power-Up After a Drive Fault
Stop Stop Closed
Wake Signal
Reset by Stop-CF,
HIM or TB
Reset by Clear
Faults (TB)
Stop Closed
Wake Signal
New Start or Run Cmd.
Stop Closed
Wake Signal
Enable Enable Closed
Wake Signal
Run
Run For.
Run Rev.
Run Closed
Wake Signal
Enable Closed
Wake Signal
New Start or Run Cmd.
New Run Cmd.
Wake Signal
Enable Closed
Wake Signal
Run Closed
Wake Signal
After a Stop Command
HIM or TB
Stop Closed
Analog Sig. > Sleep Level
New Start or Run Cmd.
Enable Closed
Analog Sig. > Sleep Level
New Start or Run Cmd.
Wake Signal
(1)
(2)
(3)
(4)
(5)
(6)
When power is cycled, if all conditions are present after power is restored, restart will occur.
If all conditions are present when [Sleep-Wake Mode] is “enabled,” the drive will start.
The active speed reference is determined as explained in the User Manual. The Sleep/Wake function and the speed reference may be assigned to the same input.
Command must be issued from HIM, TB or network.
Run Command must be cycled.
Signal does not need to be greater than wake level.
2-142
Sleep Mode
Timers
Timers will determine the length of time required for Sleep/Wake levels to produce true functions. These timers will start counting when the Sleep/
Wake levels are satisfied and will count in the opposite direction whenever the respective level is dissatisfied. If the timer counts all the way to the user specified time, it creates an edge to toggle the Sleep/Wake function to the respective condition (sleep or wake). On power up, timers are initialized to the state that does not permit a start condition. When the analog signal satisfies the level requirement, the timers start counting.
Interactive functions
Separate start commands are also honored (including a digital input “start”), but only when the sleep timer is not satisfied. Once the sleep timer times out, the sleep function acts as a continuous stop. There are two exceptions to this, which will ignore the Sleep/Wake function:
1. When a device is commanding “local” control
2. When a jog command is being issued.
When a device is commanding “local” control, the port that is commanding it has exclusive start control (in addition to ref select), essentially overriding the Sleep/Wake function, and allowing the drive to run in the presence of a sleep situation. This holds true even for the case of Port 0, where a digital input start or run will be able to override a sleep situation.
Sleep / Wake Levels
Normal operation will require that [Wake Level] be set greater than or equal to [Sleep Level]. However, there are no limits that prevent the parameter settings from crossing, but the drive will not start until such settings are corrected. These levels are programmable while the drive is running. If
[Sleep Level] is made greater than [Wake Level] while the drive is running, the drive will continue to run as long as the analog input remains at a level that doesn’t trigger the sleep condition. Once the drive goes to sleep in this situation, it will not be allowed to restart until the level settings are corrected (increase wake, or decrease sleep). If however, the levels are corrected prior to the drive going to sleep, normal Sleep/Wake operation will continue.
Sleep Mode
2-143
Sleep Timer
Satisfied
Sleep Level
Satisfied
Wake Timer
Satisfied
Wake Level
Satisfied
Wake Level
Sleep Level
Analog Signal
Drive
Run
Sleep-Wake
Function
Sleep / Wake Sources
All defined analog inputs for a product shall be considered as valid Sleep/
Wake sources. The Sleep/Wake function is completely independent of any other functions that are also using the assigned analog input. Thus, using the same analog input for both speed reference and wake control is permitted.
Also, [Analog In x Hi] and [Analog In x Lo] parameters have no affect on the function. However, the factory calibrated result will be used. In addition, the absolute value of the calibrated result will be used, thus making the function useful for bipolar direction applications. The analog in loss function is unaffected and therefore operational with the Sleep/Wake function, but not tied to the sleep or wake levels.
Figure 2.16 Sleep/Wake Function
Wake Up
Go to Sleep
Start
Stop
Wake
Time
Example Conditions
Wake Time = 3 Seconds
Sleep Time = 3 Seconds
Sleep
Time
Wake
Time
Sleep
Time
2-144
Speed Control Speed Mode Speed Regulation
Speed Control
Speed Mode
Speed Regulation
The purpose of speed regulation is to allow the drive to adjust certain operating conditions, such as output frequency, to compensate for actual motor speed losses in an attempt to maintain motor shaft speed within the specified regulation percentage.
The [Speed Mode] parameter selects the speed regulation method for the drive, and can be set to one of 3 choices on the PowerFlex 70. Additional choices are available on the PowerFlex 700 (see
•
Open Loop - No speed control is offered
•
Slip Comp - Slip Compensation is active – approximately 5% regulation
•
Process PI – The PI Loop sets the actual speed based on process variables
0 “Open Loop” 080
Vector
[Feedback Select]
Selects the source for motor speed feedback.
“Open Loop” (0) - no encoder is present, and slip compensation is not needed.
“Slip Comp” (1) - tight speed control is needed, and encoder is not present.
“Encoder” (3) - an encoder is present.
“Encdless/Db” (4), Encoderless w/
Deadband - no encoder and operation below 1Hz/30 RPM is required. This will limit drive operation below a reference of
1Hz/30 RPM (clamping the speed and torque regulators to zero).
“Simulator” (5) - Simulates a motor for testing drive operation and interface checkout.
Standard
[Speed Mode]
Sets the method of speed regulation.
Default:
Options:
Default:
Options:
0
0
1
2
2
3
0
1
4
5
“Open Loop”
“Slip Comp”
“Reserved”
“Encoder”
“Encdless/Db”
“Simulator”
“Open Loop”
“Open Loop”
“Slip Comp”
“Process PI”
Open Loop
As the load on an induction motor increases, the rotor speed or shaft speed of the motor decreases, creating additional slip (and therefore torque) to drive the larger load. This decrease in motor speed may have adverse effects on the process. If the [Speed Mode] parameter is set to “Open Loop,” no speed control will be exercised. Motor speed will be dependent on load changes and the drive will make no attempt to correct for increasing or decreasing output frequency due to load.
Slip Compensation
As the load on an induction motor increases, the rotor speed or shaft speed of the motor decreases, creating additional slip (and therefore torque) to drive the larger load. This decrease in motor speed may have adverse effects on the process. If speed control is required to maintain proper process control, the slip compensation feature of the PowerFlex drives can be enabled by the user to more accurately regulate the speed of the motor without additional speed transducers.
Speed Control Speed Mode Speed Regulation
2-145
When the slip compensation mode is selected, the drive calculates an amount to increase the output frequency to maintain a consistent motor speed independent of load. The amount of slip compensation to provide is selected in [Slip RPM @ FLA]. During drive commissioning this parameter is set to the RPM that the motor will slip when operating with Full Load
Amps. The user may adjust this parameter to provide more or less slip.
As mentioned above, induction motors exhibit slip which is the difference between the stator electrical frequency, or output frequency of the drive, and the induced rotor frequency.
The slip frequency translates into a slip speed resulting in a reduction in rotor speed as the load increases on the motor. This can be easily seen by examining
Figure 2.17 Rotor Speed with/without Slip Compensation
0
0
Slip Compensation
Inactive
Load
Applied
No Load
0.5 p.u. Load
1.0 p.u. Load
1.5 p.u. Load
Slip Compensation
Active
Load
Applied
1.5 p.u. Load
1.0 p.u. Load
0.5 p.u. Load
Slip Compensation
Active
Load
Removed
Slip @
F.L.A.
Time
Without slip compensation active, as the load increases from no load to
150% of the motor rating, the rotor speed decreases approximately proportional to the load.
With slip compensation, the correct amount of slip compensation is added to the drive output frequency based on motor load. Thus, the rotor speed returns to the original speed. Conversely, when the load is removed, the rotor speed increases momentarily until the slip compensation decays to zero.
Motor nameplate data must be entered by the user in order for the drive to correctly calculate the proper amount of slip compensation. The motor nameplate reflects slip in the rated speed value at rated load. The user can enter the Motor Nameplate RPM, Motor Nameplate Frequency, the Motor
Nameplate Current, Motor Nameplate Voltage, and Motor Nameplate HP/ kW and during commissioning the drive calculates the motor rated slip frequency and displays it in [Slip RPM @ FLA]. The user can adjust the slip compensation for more accurate speed regulation, by increasing or decreasing [Slip RPM @ FLA] value.
2-146
Speed Control Speed Mode Speed Regulation
Internally, the drive converts the rated slip in RPM to rated slip in frequency. To more accurately determine the rated slip frequency in hertz, an estimate of flux current is necessary. This parameter is either a default value based on motor nameplate data or the auto tune value. The drive scales the amount of slip compensation to the motor rated current. The amount of slip frequency added to the frequency command is then scaled by the sensed torque current (indirect measurement of the load) and displayed.
Slip compensation also affects the dynamic speed accuracy (ability to maintain speed during “shock” loading). The effect of slip compensation during transient operation is illustrated in
operating at some speed and no load. At some time later, an impact load is applied to the motor and the rotor speed decreases as a function of load and inertia. And finally, the impact load is removed and the rotor speed increases momentarily until the slip compensation is reduced based on the applied load.
When slip compensation is enabled the dynamic speed accuracy is dependent on the filtering applied to the torque current. The filtering delays the speed response of the motor/drive to the impact load and reduces the dynamic speed accuracy. Reducing the amount of filtering applied to the torque current can increase the dynamic speed accuracy of the system.
However, minimizing the amount of filtering can result in an unstable motor/drive. The user can adjust the Slip Comp Gain parameter to decrease or increase the filtering applied to the torque current and improve the system performance.
Figure 2.18 Rotor Speed Response Due to Impact Load and Slip Com Gain
Impact Load
Removed
Impact Load
Applied
Increasing Slip
Comp Gain
Increasing Slip
Comp Gain
0
0
Time
Application Example - Baking Line
Rotor Speed
Reference
The diagram below shows a typical application for the Slip Compensation feature. The PLC controls the frequency reference for all four of the drives.
Drive #1 and Drive #3 control the speed of the belt conveyor. Slip compensation will be used to maintain the RPM independent of load changes caused by the cutter or dough feed. By maintaining the required
RPM, the baking time remains constant and therefore the end product is consistent.
With the Slip Compensation feature, the process will only require a new speed reference when the product is changed. The user will not have to tune the drive due to a different load characteristic.
Speed Control Speed Mode Speed Regulation
2-147
Dough Stress
Relief
CUTTERS
Cookie Line
OVEN
PowerFlex
Drive
#1
5/40
PowerFlex
Drive
#2
PowerFlex
Drive
#3
PowerFlex
Drive
#4
Process PI –
See
Encoder Feedback (PowerFlex 700 Vector Control Only)
This section is under construction. If further information is required, please contact factory.
2-148
Speed Reference
Speed Reference
Operation
The output frequency of the drive is controlled, in part, by the speed command or speed reference given to it. This reference can come from a variety of sources including:
•
HIM (local or remote)
•
Analog Input
•
Preset Speed Parameter
•
Jog Speed Parameter
•
Communications Adapter
•
Process PI Loop
•
Digital Input MOP
Selection
Binary Logic
Some references can be selected by binary logic, through digital inputs to the terminal block or bit manipulation of the Logic Command Word in a communications adapter. These sources are used when the drive is in
“Auto” mode. The default reference is from the source selected in [Speed
Ref A Sel], parameter 90. This parameter can be set to any one of the 22 choices. If the binary logic selection is zero, this will be the active speed reference.
Auto/Manual
Many applications require a “manual mode” where adjustments can be made and setup can be done by taking local control of the drive speed.
Typically, these adjustments would be made via a “local” HIM mounted on the drive. When all setup is complete, control of the drive frequency command is turned over to automatic control from a remote source such as a PLC, analog input etc.
The source of the speed reference is switched to one of two “manual” sources when the drive is put into manual mode:
1. Local HIM
2. Analog Input to terminal block
If the selection is the HIM, then the digital or analog speed control on the
HIM provides the reference.
If the switch to manual mode was made via a digital input, (parameters
361-366 set to “18, Auto/Manual”) then the source for the reference is defined in [TB Man Ref Sel], parameter 96. This can be either of the 2 analog inputs or the digital MOP.
When the drive is returned to automatic mode, the speed reference returns to the source selected by the binary logic. Also see
Speed Reference
2-149
Jog
When the drive is not running, pressing the HIM Jog button or a programmed Jog digital input will cause the drive to jog at a separately programmed jog reference. This speed reference value is entered in [Jog
Speed], parameter 100.
Figure 2.19 Speed Reference Selection
= Default
Trim
Auto Speed Ref Options
Speed Ref A Sel, Parameter 090
Speed Ref B Sel, Parameter 093
Preset Speed 2, Parameter 102
Preset Speed 3, Parameter 103
Preset Speed 4, Parameter 104
Preset Speed 5, Parameter 105
Preset Speed 6, Parameter 106
Preset Speed 7, Parameter 107
DPI Port Ref 1-6, See Parameter 209
Manual Speed Ref Options
HIM Requesting Auto/Manual
TB Man Ref Sel, Parameter 096
Jog Speed, Parameter 100
Speed Adders
PI Output
Slip Compensation
None
[Digital Inx Select]:
Speed Sel 3 2 1
Digital Input
Jog Command
[Speed Mode]:
2 "Process Pi"
1 "Slip Comp"
0 "Open Loop"
PI Exclusive Mode
[PI Configuration]:
Bit 0, Excl Mode = 0
0 0 0
0 0 1
0 1 0
0 1 1
1 0 0
1 0 1
1 1 0
1 1 1
DPI Command
Auto
Man
Drive Ref Rslt
Pure Reference to follower drive for
Frequency Reference
Mod Functions
(Skip, Clamp,
Direction, etc.)
Min/Max Speed
Commanded
Frequency
Acc/Dec Ramp and
S Curve
Post Ramp to follower drive for
Frequency Reference
Output Frequency
Scaling
Scaling applies only to references from analog inputs and reference sources selected in [Speed Ref x Sel], parameters 90/93.
Each analog input has its own set of scale parameters:
•
[Analog In x Hi] sets the maximum level on input to be seen (i.e. 10
Volts).
•
[Analog In x Lo] sets the minimum level on input to be seen (i.e. 0
Volts).
Each [Speed Ref x Sel] parameter has an additional set of scale parameters:
•
[Speed Ref x Hi] selects the reference value for the maximum input specified in [Analog In x Hi].
•
[Speed Ref x Lo] selects the reference value for the minimum input specified in [Analog In x Lo].
For example, if the following parameters are set:
[Analog In x Hi] = 10 V
[Analog In x Lo] = 0 V
[Speed Ref A Hi] = 45 Hz
[Speed Ref x Lo] = 5 Hz then the speed command for the drive will be linearly scaled between 45 Hz at maximum analog signal and 5 Hz at minimum analog signal. See additional examples under Analog Inputs on
2-150
Speed Reference
Polarity
The reference can be selected as either unipolar or bipolar. Unipolar is limited to positive values and supplies only the speed reference. Bipolar supplies both the speed reference AND the direction command: + signals = forward direction and – signals = reverse direction.
Trim
If the speed reference is coming from the source specified in [Speed Ref A
Sel] or [Speed Ref B Sel], the a trim signal can be applied to adjust the speed reference by a programmable amount. The source of the trim signal is made via [Trim In Sel], parameter 117 and can be any of the sources that are also used as references. [Trim Out Select], parameter 118 selects which of the references, A/B will be trimmed.
If the trim source is an analog input, two additional scale parameters are provide to scale the trim signal.
Figure 2.20 Trim
Trim Enable Select
Trim
A
B
Both
None
Reference A
Reference B
+
+
+
+
Trimmed
Reference A
Trimmed
Reference B
Min / Max Speed
[Max Speed]
Maximum and minimum speed limits are applied to the reference. These limits apply to the positive and negative references. The minimum speed limits will create a band that the drive will not run continuously within, but will ramp through. This is due to the positive and negative minimum speeds.
If the reference is positive and less than the positive minimum, it is set to the positive minimum. If the reference is negative and greater than negative minimum, it is set to the negative minimum. If the minimum is not 0, hysteresis is applied at 0 to prevent bouncing between positive and negative minimums. See below.
Speed Reference
2-151
Max Spd
Min Spd
Max Spd
Min Spd
– Min Spd
– Max Spd
Band
– Max Spd
Maximum frequency
The maximum frequency defines the maximum reference frequency. The actual output frequency may be greater as a result of slip compensation and other types of regulation. This parameter also defines scaling for frequency reference. This is the frequency that corresponds to 32767 counts when the frequency reference is provided by a network.
2-152
Start Inhibits
Start Inhibits
The [Start Inhibits] parameter indicates the inverted state of all start permissive conditions. If the bit is on (HI or 1), the corresponding permissive requirement has not been met and the drive is inhibited from starting. It will be updated continually, not only when a start attempt is made. See also
Start Permissives on page 2-153 .
Start Permissives
Start Permissives
2-153
Start permissives are conditions required to permit the drive to start in any mode – run, jog, auto-tune, etc. When all permissive conditions are met the drive is considered ready to start. The ready condition is available as the
drive ready status.
Permissive Conditions
1. No faults can be active.
2. No type2 alarms can be active.
3. The TB Enable input (if configured) must be closed.
4. The DC bus precharge logic must indicate it is a start permissive.
5. All Stop inputs must be negated (See special Digital Inputs Stops
Configuration issues below).
6. No configuration changes (parameters being modified) can be in-progress.
If all permissive conditions are met, a valid start, run or jog command will start the drive. The status of all inhibit conditions, except for item
above, are reflected in the output parameter Start Inhibits. The configuration change condition is a transient (short-term) condition and not directly user controlled. It is therefore not reflected in the Start Inhibits parameter.
Note that the Start Inhibits conditions do not include any of the functionality imposed by the DPI logic such as owners, masks, local control, etc.
2-154
Start-Up
Start-Up
Start-Up Routines
PowerFlex drives offer a variety of Start Up routines to help the user commission the drive in the easiest manner and the quickest possible time.
PowerFlex 70 Drives have the S.M.A.R.T Start routine and a Basic assisted routine for more complex setups. PowerFlex 700 drives have both of the above plus an advanced startup routine.
S.M.A.R.T. Start
During a Start Up, the majority of applications require changes to only a few parameters. The LCD HIM on a PowerFlex 70 drive offers S.M.A.R.T.
start, which displays the most commonly changed parameters. With these parameters, you can set the following functions:
S - Start Mode and Stop Mode
M - Minimum and Maximum Speed
A - Accel Time 1 and Decel Time 1
R - Reference Source
T - Thermal Motor Overload
To run a S.M.A.R.T. start routine:
Step
1. Press ALT and then Esc (S.M.A.R.T).
The S.M.A.R.T. start screen appears.
2. View and change parameter values as desired. For HIM information, see
Appendix B.
3. Press ALT and then Sel (Exit) to exit the S.M.A.R.T. start.
Key(s)
ALT
ALT
Esc
Example LCD Displays
S.M.A.R.T. List
Start Mode
Stop Mode
Minimum Speed
Sel
Basic Start Up
The Basic Start Up routine leads the user through the necessary information in a simple question and answer format. The user can make the choice to execute or skip any section of the routine. Below is a complete flow chart of the routine.
Start-Up
2-155
7. Done
/Exit
Startup previously aborted?
No
0-0
PowerFlex 70
StartUp .
This routine is to help setup a drive for basic applications.
Parameter access through other menus may be necessary to setup advanced features.
Enter
0-1
PowerFlex 70
StartUp .
Complete these steps in order:
1. Input Voltage
2. Motr Dat/Ramp
3. Motor Tests
4. Speed Limits
5. Speed Control
6. Strt,Stop,I/O
7. Done / Exit
Figure 2.21 PowerFlex 70 & 700 Standard Control Option Startup
HIM
Main Menu:
<Diagnostics>
Parameter
Device Select
Memory Storage
StartUp
Preferences
Startup
Drive active?
Esc
Yes
0-2
PowerFlex 70
StartUp .
The drive must be stopped to proceed. Press
Esc to cancel.
Abort
Any state
Basic Start Up (Top Level)
'Esc' key
No
Stop
Yes
0-3
PowerFlex 70
StartUp .
Make a selection
Abort
<Backup>
Resume
StartUp Menu
Resume
Backup
Go to previous state
Go to Backup screen for previous state
Backup
Startup Menu
1. Input
Voltage
2. Motor
Dat/Ramps
3. Motor
Tests
4. Speed
Limits
5. Speed
Control
6. Strt,Stop,
I/O
Go to 1-0
Go to 2-0
Go to 3-0
Go to 4-0
Go to 5-0
Go to 6-0
2-156
Start-Up
Backup
Figure 2.21 PowerFlex 70 & 700 Standard Control Option Startup (1)
Basic Start Up (Input Voltage)
1-0
StartUp
1. Input Voltage
This step should be done only when "alternate voltage" is needed (see user manual). It will reset all drive parameters with specific choice of Volts and Hz.
Enter
Backup
Rated Volts
>300?
Backup
1-1
StartUp
1. Input Voltage
Enter choice for
Input Supply
400V, 50 Hz
<480V, 60 Hz>
Yes
Enter
1-3
StartUp
1. Input Voltage
Reset all parameters to their defaults?
<Yes>
No
Enter
Yes
1-4
StartUp
1. Input Voltage
Clear fault to continue.
No
1-2
StartUp
1. Input Voltage
Enter choice for
Input Supply
208V, 60 Hz
<240V, 60 Hz>
Fault Clear
No
Go to 0-1 (2)
Start-Up
2-157
Figure 2.21 PowerFlex 70 & 700 Standard Control Option Startup (2)
Basic Start Up (Motor Data/Ramp)
2-0
StartUp
2. Motr Dat/Ramp
Use motor nameplate data and required ramp times for the following steps.
Enter
2-1
StartUp
2. Motr Dat/Ramp
Enter choice for
Mtr NP Pwr Units
Enter
2-2
StartUp
2. Motr Dat/Ramp
Enter value for
Motor NP Power
123.4 kW xxx.x <> yyy.y
Enter
2-3
StartUp
2. Motr Dat/Ramp
Enter value for
Motor NP FLA
+456.78 Amps xxx.xx <> yyy.yy
Enter
2-4
StartUp
2. Motr Dat/Ramp
Enter value for
Motor NP Volts
123.4 Volt xxx.x <> yyy.y
Enter
2-5
StartUp
2. Motr Dat/Ramp
Enter value for
Motor NP Hertz
60.0 Hz x.x <> y.y
Enter
2-6
StartUp
2. Motr Dat/Ramp
Enter value for
Motor NP RPM
+456 RPM xxx <> yyy
2-7
StartUp
2. Motr Dat/Ramp
Enter choice for
Stop Mode A
Backup
Enter
Enter
Backup
Stop Mode A
= "DC Brake" or
"Ramp to
Hold"?
Yes
2-8
StartUp
2. Motr Dat/Ramp
Enter value for
DC Brake Level
1.0 Amps
0.0 < 30.0 Amps
Enter
Backup
Stop Mode A
= "DC
Brake"?
Yes
2-9
StartUp
2. Motr Dat/Ramp
Enter value for
DC BrakeTime
1.0 Secs
0.0 < 90.0 Secs
No
2-10
StartUp
2. Motr Dat/Ramp
Enter choice for
DB Resistor Type
None
Internal
External
No
Enter
2-11
StartUp
2. Motr Dat/Ramp
Enter value for
Accel Time 1
6.0 Secs
0.0 < 60.0 secs
Enter
Enter
2-12
StartUp
2. Motr Dat/Ramp
Enter value for
Decel Time 1
6.0 Secs
0.0 < 60.0 secs
Enter
2-13
StartUp
2. Motr Dat/Ramp
Enter value for
S Curve %
0 %
0 < 100 %
None - Bus Reg Mode A = Adj Freq.
Intenal - Bus Reg Mode A = Both, DB 1st.
External - Bus Reg Mode A = Both, DB 1st.
Enter Go to 0-1 (3)
2-158
Start-Up
Enter/
Backup
Figure 2.21 PowerFlex 70 & 700 Standard Control Option Startup (3)
3-0
Startup
3. Motor Tests
This section optimizes torque performance and tests for proper direction.
3-4
Startup
B. Directn Test
Press Jog or Start to begin.
Basic Start Up (Motor Tests)
Direction
Test
Enter
Startup
3. Motor Tests
Complete these steps in order:
<A. Auto Tune>
B. Directn Test
C. Done
3-1
Done
Auto Tune
Startup
A. AutoTune
Rotate Tune only with no load and low friction.
Static Tune when load or friction are present.
3-2
Enter
3-3
Startup
A. AutoTune
Make a selectioon
<Rotate Tune>
Static Tune
Go to 0-1 (4)
3-8
Startup
A. Auto Tune.
Static Tune will energize motor with no shaft rotation. Press
Start to begin.
Static
Tune
Rotate
Tune
Startup
A. Auto Tune
Rotate Tune will energize motor, then cause shaft rotation. Press
Start to begin.
3-9
Enter/
Backup
3-12
Startup
3. Motor Tests
Test aborted due to user stop.
Clear fault to continue.
Fault Clear
Start
3-5
Startup
B. Directn Test
Is direction of motor forward?
<Yes>
No
Enter/
Backup
Yes
(stops drive)
3-6
Startup
B. Directn Test
Test complete.
No
(stops drive)
3-7
Startup
B. Directn Test
Press Enter.
Then power down and swap 2 output wires to motor.
Start
3-10
Startup
A. Auto Tune
Executing test.
Please wait....
Start
Rotate/Static
Tune complete
(stops drive)
3-11
Startup
A. Auto Tune
Test complete.
Stop or Esc
(stops drive)
Fault
3-13
Startup
3. Motor Tests
Test aborted!
Clear the fault.
Check motor data settings. Verify load is removed.
Start-Up
2-159
4-0
StartUp
4. Speed Limits
This section defines min/max speeds, and direction method
Figure 2.21 PowerFlex 70 & 700 Standard Control Option Startup (4)
Basic Start Up (Speed Limits)
Backup
Enter
4-1
StartUp
4. Speed Limits
Disable reverse operation?
Yes
<No>
No
4-2
StartUp
4. Speed Limits
Enter choice for
Direction Method
<Fwd/Rev Command>
+/- Speed Ref
Yes
4-3
StartUp
4. Speed Limits
Enter value for
Maximum Speed
+60.00 Hz xxx.xx <> yyy.yy
Enter
Enter
Backup
MaxSpd + OSL
> MaxFreq?
Yes
4-5
StartUp
4. Speed Limits
Maximum Freq and
Overspeed Limit will be changed to support your
Maximum Speed.
No
Backup
4-4
StartUp
4. Speed Limits
Enter value for
Minimum Speed
+5.78 Hz xxx.xx <> yyy.yy
Enter
4-6
StartUp
4. Speed Limits
Rejecting this change will prevent starting
Accept
Reject
Accept
MaxSpd + OS
Lmt > 400Hz?
Reject
MaxFreq = MaxSpd
+ OS Limit
No
OS Limit =
MaxFreq - MaxSpd
MaxFreq = 400Hz
Enter
Yes
Go to 0-1 (5)
2-160
Start-Up
Figure 2.21 PowerFlex 70 & 700 Standard Control Option Startup (5)
Basic Start Up (Speed Control)
5-0
StartUp
5. Speed Control
This section defines a source from which to control speed.
5-2
Adapter
StartUp
5. Speed Control
Enter choice for
Comm Adapter
Port 5-internal
Port 2-external
Port 3-external
Enter
Go to 0-1 (6)
Enter
5-3
StartUp
5. Speed Control
Enter choice for
Remote HIM
Port 2 (common)
Port 3
5-4
StartUp
5. Speed Control
Enter value for
Preset Speed 1
5.0 Hz
xxx.x < yyy.y
5-5
StartUp
5. Speed Control
Enter value for
Preset Speed 2
10.0 Hz
xxx.x < yyy.y
5-6
StartUp
5. Speed Control
Enter value for
Preset Speed 3
15.0 Hz
xxx.x < yyy.y
5-7
StartUp
5. Speed Control
Enter value for
Preset Speed 4
20.0 Hz
xxx.x < yyy.y
5-1
StartUp
5. Speed Control
Enter choice for
Speed Control
<Analog Input>
Comm Adapter
Local HIM-Port 1
Remote HIM
Preset Speeds
MOP
Remote
HIM
Enter
Preset
Speeds
Local HIM-
Port 1
Go to 0-1 (6)
MOP
Analog Input
5-14
StartUp
5. Speed Control
Digital Inputs
5 & 6 will be set to MOP Inc &
MOP Dec.
Enter
5-15
StartUp
5. Speed Control
Save MOP speed at power down ?
<Yes>
No
5-11
StartUp
5. Speed Control
Note: Factory default settings provide preset speed operation from the digital inputs, unless you change their function.
Enter
5-16
StartUp
5. Speed Control
Save MOP speed at stop ?
<Yes>
No
Enter/
Backup
Preset
Speed 1
Preset
Speed 2
Enter
5-12
StartUp
5. Speed Control
Make a selection .
<Preset Speed 1>
Preset Speed 2
Preset Speed 3
Preset Speed 4
Preset Speed 5
Preset Speed 6
Preset Speed 7
Done
Preset
Speed 3
Preset
Speed 4
Preset
Speed 5
Preset
Speed 6
Done
Preset
Speed 7
Enter
5-17
PF70 StartUp
5. Speed Control
Enter value for
MOP Rate
5.0 Hz xx.x < yy.y
Enter
Go to 0-1 (6)
5-8
StartUp
5. Speed Control
Enter value for
Preset Speed 5
25.0 Hz
xxx.x < yyy.y
5-9
StartUp
5. Speed Control
Enter value for
Preset Speed 6
30.0 Hz
xxx.x < yyy.y
5-10
StartUp
5. Speed Control
Enter value for
Preset Speed 7
35.0 Hz
xxx.x < yyy.y
Enter
Enter
5-22
StartUp
5. Speed Control
The next two parameters link a low speed with a low analog value.
5-23
Enter
StartUp
5. Speed Control
Enter value for
Analog In 1 Lo
0.0 V
xxx.x < yyy.y
Enter
5-24
StartUp
5. Speed Control
Enter value for
Speed Ref A Lo
0.0 Hz
xxx.x < yyy.y
Enter
5-19
StartUp
5. Speed Control
The next two parameters link a high speed with a high analog value.
5-20
Enter
StartUp
5. Speed Control
Enter value for
Analog In 1 Hi
10.0 V
xxx.x < yyy.y
Enter
5-21
StartUp
5. Speed Control
Enter value for
Speed Ref A Hi
60.0 Hz
xxx.x < yyy.y
5-13
StartUp
5. Speed Control
Enter choice for
Input Signal
Analog Input 1
Analog Input 2
5-18
Analog
Input 1
StartUp
5. Speed Control
Enter choice for
Signal Type
Voltage
Current
Analog
StartUp
5. Speed Control
Enter choice for
Signal Type
Voltage
Current
5-25
Enter
5-29
StartUp
5. Speed Control
The next two parameters link a low speed with a low analog value.
5-30
Enter
StartUp
5. Speed Control
Enter value for
Analog In 2 Lo
0.0 V
xxx.x < yyy.y
Enter
5-31
StartUp
5. Speed Control
Enter value for
Speed Ref A Lo
0.0 Hz
xxx.x < yyy.y
Enter
5-26
StartUp
5. Speed Control
The next two parameters link a high speed with a high analog value.
5-27
Enter
StartUp
5. Speed Control
Enter value for
Analog In 2 Hi
10.0 V
xxx.x < yyy.y
Enter
5-28
StartUp
5. Speed Control
Enter value for
Speed Ref A Hi
60.0 Hz
xxx.x < yyy.y
Start-Up
2-161
Figure 2.21 PowerFlex 70 & 700 Standard Control Option Startup (6)
6-0
StartUp
6. Strt,Stop,I/O
This section defines I/O functions including start and stop from digital ins
Backup
Enter
6-3
StartUp
A. Dig Inputs
Digital Inputs
1-4 will be set to defaults.
Yes
Enter
6-1
StartUp
6. Strt,Stop,I/O
Complete these steps in order:
<A. Dig Inputs>
B. Dig Outputs
C. Anlg Outputs
D. Done
A. Dig Inputs
6-2
StartUp
A. Dig Inputs
Make a selection
<Easy Configure>
Custom Configure
Easy Configure
DigIn 5,6 = MOP
Inc, Dec?
No
Enter
Dir Mode =
Reverse
Disable?
Yes
6-6
Backup
6-4
StartUp
A. Dig Inputs
Digital Inputs
1-6 will be set to defaults.
No
StartUp
A. Dig Inputs
Enter choice for
Control Method
<3-wire>
2-wire
Yes
C. Anlg
Outputs
D. Done
B. Dig
Outputs
Go to 6-29
Custom Configure
Backup
Dir Mode =
Bipolar?
6-7
StartUp
A. Dig Inputs
Digital Input 1 will be set to
Not Used.
2-wire
Enter
6-8
StartUp
A. Dig Inputs
Digital Input 2 will be set to
Run/Stop.
Enter
3-wire
6-9
StartUp
A. Dig Inputs
Digital Input 1 will be set to
Stop.
Enter
6-10
StartUp
A. Dig Inputs
Digital Input 2 will be set to
Start.
Enter
Go to 6-1 (B)
Go to 0-1 (7)
Go to 6-24
Go to 6-1 (B)
Done
6-17
StartUp
A. Dig Inputs
Make a selection
<Digital Input 1>
Digital Input 2
Digital Input 3
Digital Input 4
Digital Input 5
Digital Input 6
Done
No
No
6-5
StartUp
A. Dig Inputs
Is reverse required from digital inputs?
<Yes>
No
Yes
StartUp
A. Dig Inputs
Enter choice for
Control Method
<3-wire>
2-wire
6-11
Enter
6-12
2-wire
StartUp
A. Dig Inputs
Digital Input 1 will be set to
Run Forward.
6-13
Enter
StartUp
A. Dig Inputs
Digital Input 2 will be set to
Run Reverse.
Enter
Enter/
Backup
Basic Start Up (Start,Stop,I/O)
Digital In 1
Digital In 2
Digital In 3
Digital In 4
Digital In 5
Digital In 6
3-wire
6-14
StartUp
A. Dig Inputs
Digital Input 3 will be set to Fwd/
Reverse.
Enter
6-15
StartUp
A. Dig Inputs
Digital Input 1 will be set to
Stop.
6-16
Enter
StartUp
A. Dig Inputs
Digital Input 2 will be set to
Start.
6-18
StartUp
A. Dig Inputs
Enter choice for
Digital In1 Sel
6-19
StartUp
A. Dig Inputs
Enter choice for
Digital In2 Sel
6-20
StartUp
A. Dig Inputs
Enter choice for
Digital In3 Sel
6-21
StartUp
A. Dig Inputs
Enter choice for
Digital In4 Sel
6-22
StartUp
A. Dig Inputs
Enter choice for
Digital In5 Sel
6-23
StartUp
A. Dig Inputs
Enter choice for
Digital In6 Sel
2-162
Start-Up
Go to 6-1 (C)
Figure 2.21 PowerFlex 70 & 700 Standard Control Option Startup (7)
Basic Start Up (Start,Stop,I/O [2])
Done
6-24
StartUp
B . Dig Outputs
Make a selection
<Digital Out 1>
Digital Out 2
Done
6-29
StartUp
C. Anlg Outpts
Enter choice for
Analog Out 1 Sel
Digital
Out 1
Digital
Out 2
6-25
StartUp
B. Dig Outputs
Enter choice for
Digital Out 1 Sel
6-27
StartUp
B. Dig Outputs
Enter choice for
Digital Out 2 Sel
Enter
6-30
StartUp
C. Anlg Outpts
Enter value for
Analog Out 1 Hi
No
Enter
Enter
Digital Out 1 Sel
= ENUM choice that uses
"Level"?
Yes
6-26
StartUp
B. Dig Outputs
Enter value for
Dig Out 1 Level
Backup
Enter
Backup
Digital Out 2 Sel
= ENUM choice that uses
"Level"?
Yes
StartUp
B. Dig Outputs
Enter value for
Dig Out 2 Level
No
Enter
Enter
6-31
StartUp
C. Anlg Outpts
Enter value for
Analog Out 1 Lo
Enter
Go to 6-1 (D)
Start-Up
2-163
Figure 2.22 PowerFlex 700 Vector Control Option Startup
For first time powerup...
Select:
<English>
Francais
Espanol
Deustch
Italiano
Flux Vector Start Up (Top Level)
HIM
Main Menu:
<Diagnostics>
Parameter
Device Select
Memory Storage
Start-Up
Preferences
Start-Up/Continue
(disallow Start/Jog)
Abort
(allow Start/Jog)
Esc
(allow Start/Jog)
'Esc' key
0-0
Start-Up/Restart
(disallow Start/Jog)
PowerFlex 700
Start-Up .
Startup consists of several steps to configure a drive for basic applications.
Drive active?
0-2
PowerFlex 700
Start-Up .
The drive must be stopped to proceed. Press
ESC to cancel.
Yes
No
Go to Abort-
Resume state
Yes
Done/Exit
(allow Start/Jog)
Backup
0-4
Drive active?
No
PowerFlex 700
Start-Up .
Make a selection
<1.SMART>
2.Basic
3.Detailed
4.More Info
STOP
(Stops the Drive)
Basic/
Detailed
SMART
Go to 8-1 (SMART
Start)
First time into
Startup??
Yes
Go to 1-1 (Motor
Control)
No
0-5
PowerFlex 700
Start-Up .
SMART startup programs 11 key drive parameters for fast setup .
Basic startup programs basic drive functions and options. .
Detailed startup programs motor data, reference; ramps; limits; & analog/digital
I/O.
No
Yes
0-3
PowerFlex 700
Start-Up .
Make a selection
Abort
<Backup>
Resume
Start-Up Menu
Startup
Menu
Drive active?
Any state
(except 0-2)
Resume/Esc
Backup
Go to previous state
Go to Backup screen for previous state
Basic
0-1
PowerFlex 700
Start-Up .
Complete these steps in order:
<1.Motor Control>
2.Motr Data/Ramp
3.Motor Tests
4.Speed Limits
5.Speed/Trq Cntl
6.Start/Stop/I/O
7.Done/Exit
Detailed
PowerFlex 700
Start-Up .
Complete these steps in order:
<1.Motor Control>
2.Motr Data/Ramp
3.Motor Tests
4.Speed Limits
5.Speed/Trq Cntl
6.Start/Stop/I/O
7.Appl Features
8.Done/Exit
0-1
Motor Control
Motor Dat/Ramp
Motor Tests
Speed Limits
Speed/Torque Control
Strt/Stop/ I/O
Appl Features
Done/Exit
Go to 1-0
Go to 2-0
Go to 3-0
Go to 4-0
Go to 5-0
Go to 6-0
Go to 7-0
Go to HIM
Main Menu
2-164
Start-Up
Figure 2.22 PowerFlex 700 Vector Control Option Startup (1)
Flux Vector Start Up (Motor Control Select)
1-0
1-1
B
Start-Up
1. Motor Control
This section selects the type of Motor Control the drive will use.
1-3
1-2
B
Start-Up
SVC
Enter choice of
Speed Units
<Hz>
RPM
Start-Up
SVC
Enter choice for
Slip Comp
<Enable>
Disable
Start-Up
1. Motor Control
Make a selection
<1.SVC>
2.V/Hz
3.Flux Vector
4.More info
SVC- Set
#53= 0
Flux
Vector
1-6
Start-Up
Flux Vector
NOTE! An Encoder is required for the Flux Vector
Control option.
B
More info
Frequency
1-7
Start-Up
Flux Vector
Enter value for
Encoder PPR
1024
B
1-8
B
1-17
Start-Up
1.Motor Control
Use SVC for applications requiring speed regulation.
Use V/Hz control for Fan/Pump and other V/Hz applications.
Use Flux Vector for applications requiring Torque control or tight speed regulation.
B = Basic mode
1-18
Start-Up
V/Hz
Select a V/Hz control option:
<1.V/Hz-Fan/Pump>
2.V/Hz-Cust/Std.
3.More info
Fan/Pump-Set #53=3
1-19
Start-Up
V/Hz
Enter choice for
Slip Comp
<Enable>
Disable
Disable
Set #80=0
Disable
Set #80=0
1-4
Start-Up
SVC
Control selected is SVC with no Slip Comp
Enable
Set #80=1
1-5
B
Start-Up
SVC
Control selected is SVC with
Slip Comp
1-12
Min Torque/
Speed -
Set #88 =3
Torque path
1-10
Start-Up
Flux Vector
Select Torque
Regulate option:
<1.Torque Regul.>
2.Min Torque/Spd
3.Max Torque/Spd
4.Sum Torque/Spd
5.Absolute
Start-Up
Flux Vector
Control selected is Torque/FOC
Min Torque/Speed
Start-Up
Flux Vector
Enter choice of
Speed Units
<Hz>
RPM
Start-Up
Flux Vector
Enter choice of
Regulation
<Speed>
Torque
Max
Trq/Speed -
Set #88 = 4
1-13
Start-Up
Flux Vector
Control selected is Torque/FOC
Max Torque/Speed
1-9
Speed path-
Set #88 to 1
Absolute-
Set #88
= 6
Trq
Regulate
Set #88
= 2
Sum Trq/Speed-
Set #88 = 5
1-14
Start-Up
Flux Vector
Control selected is Torque/FOC
Torque Regulate
1-11
Start-Up
Flux V ector
Control selected is FOC Speed
Regulate.
1-15
Start-Up
Flux Vector
Control selected is Torque/FOC
Sum Torque/Speed
More info
1-31
V/Hz
Custom/Std.
Start-Up
V/Hz
Define Custom
V/Hz curve?
<Yes>
No
1-32
Yes
B
Standardset params #54
& 69-72 to default values
1-20
Start-Up
V\Hz
Control selected is Standard V/Hz
Enable
Set #80=1
1-21
Start-Up
V/Hz
Control selected is Fan/Pump with Slip Comp
Start-Up
V/Hz
Control selected is Fan/Pump no Slip Comp
1-22
B
1-16
Start-Up
Flux Vector
Control selected is Torque/FOC
Absolute
1-30
Start-Up
V/Hz
The Fan/Pump option selects a predefined V/Hz curve.
The Custom/Std.
option allows you to define a
V/Hz curve or select a default
V/Hz curve.
Start-Up
V/Hz
Control selected is V/Hz/Custom no Slip Comp.
1-23
Start-Up
V/Hz
Enter choice for
Slip Comp
<Enable>
Disable
Set #80 to selection made
1-24
Start-Up
V/Hz
Enter value for
Run Boost
10V xx.x < yy.y
Start-Up
V/Hz
Enter value for
Start Boost
10.0 V
x.xxxx < y.yyyy
1-25
Start-Up
V/Hz
Enter value for
Break Voltage
10.0 Hz
x.x < y.y
1-27
Start-Up
V/Hz
Enter value for
Break Frequency
10.0 Hz
x.xxxx < y.yyyy
Start-Up
V/Hz
Enter value for
Max Voltage
10.0 V
x.x < y.y
1-26
1-28
Start-Up
V/Hz
Control selected is V/Hz/Custom with Slip Comp.
1-29
Go to 0-1
2. Motr Dat/Ramp
Start-Up
2-165
Figure 2.22 PowerFlex 700 Vector Control Option Startup (2)
Flux Vector Start Up (Motor Dat/Ramp)
B
2-0
Start-Up
2. Motr Dat/Ramp
Use motor nameplate data and required ramp times for the following steps.
B
Enter
2-1
Start-Up
2. Motr Dat/Ramp
Enter choice for
Power Units
<HP>
Killowatt
B
Enter
2-2
Start-Up
2. Motr Dat/Ramp
Enter value for
Motor NP Power
123.4 kW xxx.x <> yyy.y
B
Enter
2-3
Start-Up
2. Motr Dat/Ramp
Enter value for
Motor NP FLA
+456.78 Amps xxx.xx <> yyy.yy
B
Enter
2-4
Start-Up
2. Motr Dat/Ramp
Enter value for
Motor NP Volts
123.4 Volt xxx.x <> yyy.y
B
Enter
2-5
Start-Up
2. Motr Dat/Ramp
Enter value for
Motor NP Hertz
60.0 Hz x.x <> y.y
B
Enter
2-6
Start-Up
2. Motr Dat/Ramp
Enter value for
Motor NP RPM
+456 RPM xxx <> yyy
B = Basic mode
2-14
Start-Up
2. Motr Dat/Ramp
Enter value for
Motor Poles
12 xx <> yy
2-7
Start-Up
2. Motr Dat/Ramp
Enter Stop Mode:
1.Coast
<2.Ramp>
3.Ramp to Hold
4.DC Brake
Enter
Use formula:
Poles= 120 * NP Hz
NP RPM as Motor Poles parameter value.
Stop Mode A =
"DC Brake" or
"Ramp to Hold"?
2-8
Yes
Start-Up
2. Motr Dat/Ramp
Enter value for
DC Brake Level
1.0 Amps
0.0 < 30.0 Amps
Enter
No
No
Enter
Stop Mode A =
"DC Brake"?
2-9
Yes
Start-Up
2. Motr Dat/Ramp
Enter value for
DC BrakeTime
1.0 Secs
0.0 < 90.0 Secs
Backup
2-10
Start-Up
2. Motr Dat/Ramp
Enter choice for
DB Resistor type
<None>
Internal
External
Enter
2-11
Start-Up
2. Motr Dat/Ramp
Enter value for
Accel Time 1
6.0 Secs
0.0 < 60.0 secs
Enter
2-12
Start-Up
2. Motr Dat/Ramp
Enter value for
Decel Time 1
6.0 Secs
0.0 < 60.0 secs
2-13
Enter
Start-Up
2. Motr Dat/Ramp
Enter value for
S Curve %
0 %
0 < 100 %
Enter
Note: Depending on selection, set parameter
#161 (Bus Reg Mode A):
None - Bus Reg Mode A = Adj Freq.
Intenal - Bus Reg Mode A = Both, DB 1st.
External - Bus Reg Mode A = Both, DB 1st.
Note: If Stop Mode A = COAST, then skip 2-10.
Note: Default should be NONE.
B
Note: If Stop Mode A = COAST, then skip 2-12. If in Quick/Basic mode, then exit Motor Data/Ramp.
B
Note:
- For V/Hz mode, only states 2-0 thru 2-6 & 2-14 are displayed.
- For V/Hz mode, configure Stop Mode A as Coast to Stop.
- Going from state 2-7 to 2-10 directly sets the DC Brake Level/Time parameters to their default value.
Go to 0-1 (3. Motor
Tests)
2-166
Start-Up
Figure 2.22 PowerFlex 700 Vector Control Option Startup (3)
3-0
Start-Up
3. Motor Tests
This section optimizes motor performance and tests for proper direction.
3-22
Start-Up
3. Motor Tests
Select source of
Start/Stop
<Digital Inputs>
Local HIM-Port1
Remote HIM-Port2
If Digital Inputs:- Set
#361/2 to START/STOP resp.
If Local HIM:- Set
#361/2 to Not Used &
#90 to 18
3-21
Start-Up
C.Inertia Test
V/Hz Control does not require an Inertia Test.
V/Hz
Flux Vector Start Up (Motor Tests)
Start-Up
C.Inertia Test
Sensrls Vector does not require an Inertia Test.
3-25
Go to 0-1 (4.Speed
Limits)
SV
Enter/
Backup
5 Hz.
- State 3-4 allows
Start/Jog
3-4
Backup
3-1
Start-Up
3. Motor Tests
Complete these steps in order:
<A. Directn Test>
B. Auto Tune
C. Inertia Test
D. Done
D. Done
Motor
Cntl
Sel?
3-5
Start-Up
A. Directn Test
Motor rotation correct for application?
<Yes>
No
3-6
If YES & positive encoder counts..
(stops drive)
Start-Up
A. Directn Test
Test complete.
Press <ENTER>
If YES & negative encoder counts..
(stops drive)
If NO..
(stops drive)
Start-Up
A. Directn Test
Startup will automatically reverse the
MotorLeads.
3-7
3-8
Note: States 3-8
& 3-9 allow Start.
Start-Up
B. Auto Tune.
Static Tune will energize motor with no shaft rotation. Press
START to begin.
3-9
No
Start-Up
B. Auto Tune
Caution: Rotate
Tune will cause shaft rotation.
Press START to begin.
FOC?
Yes
3-16
Start-Up
B. Auto Tune
Enter value for
Autotune Torque
6.0 % xxx.x <> yyy.y
3-17
Start-Up
A. Directn Test
Power down and swap encoder leads.
Go to State 3-18
Start-Up
B. Auto Tune
Rotate Tune done. Press
ENTER to continue with
Inertia Test.
3-24
Go to State 3-4
Yes
Start (disallow
Start/Jog)
3-10
Start (disallow
Start/Jog)
Start-Up
B. Auto Tune
Executing test.
Please wait...
Rotate/Static Tune complete
(stops drive)
FOC
Mode?
Stop or Esc
(stops drive)
Fault
(stops drive)
3-11
No
Note:
Direction
Test
Start Inhibit
Note:
- Fix Jog/Reference to param != 0
No
Start-Up
A. Directn Test
Press Jog or Start to begin.
Start/Jog
(disallow Start/Jog)
Yes
Start-Up
3. Motor Tests
Cannot start due to open Stop input or other
[Start Inhibits]
Press Enter.
Enter
Enter
3-14
- The Motor Tests are NOT executed while in V/Hz mode.
B. Auto Tune
Yes
Static
Tune
C. Inertia Test
Start Inhibit param != 0
Note: Set #61
(Autotune) to '2' or
'1' depending on selection
No
3-2
Start-Up
B. AutoTune
IMPORTANT!!
Use Rotate Tune if no load/low friction/Flux
Vector mode.
Else use Static
Tune. For special applications, see reference maual.
3-3
Start-Up
B. AutoTune
Make a selectioon
Static Tune
<Rotate Tune>
Rotate Tune
Start-Up
B. Auto Tune
Test complete.
Press <ENTER>
3-12
Start-Up
3. Motor Tests
Test aborted due to user stop.
Clear fault to continue.
FOC
Start-Up
C. Inertia Test
Connect load to motor for
Inertia Test.
3-18
3-19
Start-Up
C. Inertia Test
Caution:Inertia
Test causes shaft rotation.
<START> to begin
Start-Up
C. Inertia Test
Executing test.
Please wait...
Go to 3-1
3-20
3-15
Start-Up
C. Inertia Test
Enter value for
Speed Desired BW
60.0 RPM xxx.x <> yyy.y
Start-Up
C. Inertia Test
Test complete.
Press <ENTER>
3-23
3-13
Start-Up
3. Motor Tests
Test aborted!
Clear the fault.
Check motor data settings. Verify load is removed.
Go to 3-1
Fault
(stops drive)
Stop or ESC
(stops drive)
Go to 3-1
Start-Up
2-167
Figure 2.22 PowerFlex 700 Vector Control Option Startup (4)
Flux Vector Start Up (Speed Limits)
4-0
Start-Up
4. Speed Limits
This section defines min/max speeds and direction method
4-1
Start-Up
4. Speed Limits
Enter value for
Maximum Speed
+60.00 Hz xxx.xx <> yyy.yy
B
B
4-2
Start-Up
4. Speed Limits
Enter value for
Minimum Speed
+5.78 Hz xxx.xx <> yyy.yy
B
FOC
Mode?
No
Go to 0-1 (5.
Speed Control)
Yes
4-3
Start-Up
4. Speed Limits
Enter value for
Rev Speed Lim
+5.78 Hz xxx.xx <> yyy.yy
B
2-168
Start-Up
Figure 2.22 PowerFlex 700 Vector Control Option Startup (5)
5-0
Start-Up
5. Speed Control
This section selects the speed/torque control source.
Note:
- Only Analog and Local HIM are displayed in 5-1 for Basic mode.
5-1
Flux
Vector
Mode?
No
5-2
Comm Adapter write to #90 (Ref A
Sel) selection
Start-Up
Comm Adapter
Make a selection
<Port 5-internal>
Port 2-common
Port 3-external
Port 4-external
Go to 0-1 (6.Strt/
Stop/I/O)
Remote
HIM -write to #90 (Ref
A Sel) selection
Start-Up
5. Speed Control
Choose source of Reference:
<1.Analog Input>
2.Preset Speed 1
3.Digital Inputs
4.Comm Adapter
5.Local HIM
6.Remote HIM
7.MOP
Digital
Inputs
Yes
Speed
Preset
Speed - Set param #90
(Ref A Sel) to '11'
5-3
Start-Up
Remote HIM
Make a selection
<Port 2 (common)>
Port 3
Port 4
5-4
5-5
5-6
5-7
Start-Up
5. Speed Control
Enter value for
Preset Speed 1
5.0 Hz
xxx.x < yyy.y
Start-Up
5. Speed Control
Enter value for
Preset Speed 2
10.0 Hz
xxx.x < yyy.y
Start-Up
5. Speed Control
Enter value for
Preset Speed 3
15.0 Hz
xxx.x < yyy.y
Start-Up
5. Speed Control
Enter value for
Preset Speed 4
20.0 Hz
xxx.x < yyy.y
5-8
Start-Up
5. Speed Control
Enter value for
Preset Speed 5
25.0 Hz
xxx.x < yyy.y
5-9
Start-Up
5. Speed Control
Enter value for
Preset Speed 6
30.0 Hz
xxx.x < yyy.y
5-10
Start-Up
5. Speed Control
Enter value for
Preset Speed 7
35.0 Hz
xxx.x < yyy.y
5-11
Start-Up
5. Speed Control
Note: Factory default settings provide preset speed operation from the digital inputs.
Enter/
Backup
Preset
Speed 1
Preset
Speed 2
Preset
Speed 3
Preset
Speed 4
Set params: #90 (Ref A
Sel) to Anlg In 1; #93 (Ref
B Sel) to Preset Spd 1;
#364-66 (Digital In 4-6) to Speed Sel 1, 2, 3.
Preset
Speed 5
Preset
Speed 6
Preset
Speed 7
Start-Up
C. Anlg Inputs
Enter choice for
Reference::
<Speed>
Torque
Local HIM- Port 1-
Set param #90
(Ref A Sel) to '18'
5-35
Start-Up
5. Speed Control
Enter value for
Preset Speed 1
5.0 Hz
xxx.x < yyy.y
5-12
Start-Up
5. Speed Control
Select a Preset
Speed:
<1.Preset Speed 1>
2.Preset Speed 2
3.Preset Speed 3
4.Preset Speed 4
5.Preset Speed 5
6.Preset Speed 6
7.Preset Speed 7
8.Done
Go to 0-1
(6. Strt/Stop/I/O)
Go to 0-1 (6. Strt/
Stop/I/O)
Done
5-33
Start-Up
5. Speed Control
Configure other
Spd References?
<Yes>
No
No
Note :
- For V/Hz mode, the MOP option in 5-1 is NOT displayed, screens 5-14 thru 5-17 and 5-18 thru 5-31 are also NOT displayed.
5-34
Analog Input
MOP - Set
Param #90
(Ref A Sel) to '9'
Yes
Torque
Upon "Enter", write to bit '0' of param #194
(Save MOP Ref)
5-16
Start-Up
5. Speed Control
Save MOP speed at Stop ?
<Yes>
No
Enter
Upon "Enter", write to bit '1' of param #194
(Save MOP Ref)
5-17
Go to 5-1
Flux Vector Start Up (Speed/Torque Control)
Go to 6-49
5-14
Start-Up
5. Speed Control
Digital Inputs
5 & 6 will be set to MOP Inc &
MOP Dec.
5-15
Start-Up
5. Speed Control
Save MOP speed at power down ?
<Yes>
No
PF70 Start-Up
5. Speed Control
Enter value for
MOP Rate
5.0 Hz xx.x < yy.y
Enter
Enter
V/Hz
Mode?
5-21
Start-Up
5. Speed Control
Enter value for
Speed Ref A Hi
60.0 Hz
x.x < y.y
5-22
Start-Up
5. Speed Control
The next two steps scale a low speed with a low analog value.
5-23
Start-Up
5. Speed Control
Enter value for
Analog In 1 Lo
0.0 V
x.xxxx < y.yyyy
5-24
Start-Up
5. Speed Control
Enter value for
Speed Ref A Lo
0.0 Hz
x.x < y.y
5-32
Start-Up
5. Speed Control
Verify high/low speeds with high/low analog signals.
5-13
Start-Up
5. Speed Control
Enter choice for
Input Signal
<Analog Input 1>
Analog Input 2
Set #90 to
Analog Input 1
Set #90 to
Analog Input 2
5-18
Start-Up
5. Speed Control
Enter choice for
Signal Type
<Voltage>
Current
5-25
Start-Up
5. Speed Control
Enter choice for
Signal Type
<Voltage>
Current
Set bit 0 of #320 to '0'
(for Volts) & '1' (for Amps)
No-If AIn 1 Hi/Lo value out of range, set to min of Signal type selected
5-19
Start-Up
5. Speed Control
The next two steps scale a high speed to a high analog value.
5-20
Start-Up
5. Speed Control
Enter value for
Analog In 1 Hi
10.0 V
x.xxxx < y.yyyy
Yes
Set bit 1 of #320 to '0'
(for Volts) & '1' (for Amps)
V/Hz
Mode?
No-If AIn 2 Hi/Lo value out of range, set to min of Signal type selected.
5-26
Start-Up
5. Speed Control
The next two steps scale a high speed to a high analog value.
5-27
Start-Up
5. Speed Control
Enter value for
Analog In 2 Hi
10.0 V
x.xxxx < y.yyyy
5-28
Start-Up
5. Speed Control
Enter value for
Speed Ref A Hi
60.0 Hz
x.x < y.y
5-29
Start-Up
5. Speed Control
The next two steps scale a low speed with a low analog value.
5-30
Start-Up
5. Speed Control
Enter value for
Analog In 2 Lo
0.0 V
x.xxxx < y.yyyy
5-31
Start-Up
5. Speed Control
Enter value for
Speed Ref A Lo
0.0 Hz
x.x < y.y
Start-Up
2-169
Figure 2.22 PowerFlex 700 Vector Control Option Startup (6)
B
6-0
Start-Up
6. Strt,Stop,I/O
This section defines I/O functions including Start and Stop.
6-1
A. Dig Inputs
6-2
B
Start-Up
A. Dig Inputs
Digital Input
Config options:
<Easy Configure>
Custom Configure
More info
Start-Up
6. Strt,Stop,I/O
Complete these steps in order:
<A.Dig Inputs>
B.Dig Outputs
C.Analog Outputs
D.Done
B. Dig
Outputs
C.Analog
Output
D. Done
Custom Configure
Yes
6-3
Start-Up
A. Dig Inputs
Digital Inputs
1-4 will be set to defaults.
Easy Configure
DigIn 5,6 = MOP
Inc, Dec?
No
6-4
Start-Up
A. Dig Inputs
Digital Inputs
1-6 will be set to defaults.
B
More info
6-26
Start-Up
A. Dig Inputs
Easy Configure asks questions before writing to digital ins.
Custom Configure allows you to program each digital input(s)
Backup
Go to 6-27
Go to 6-49
Go to 0-1 (7. Application
Features)
6-19 Start-Up
A. Dig Inputs
Select a Digital
Input:
<1.Digital In 1>
2.Digital In 2
3.Digital In 3
4.Digital In 4
5.Digital In 5
6.Digital In 6
7.Done
6-5
B
Start-Up
A. Dig Inputs
Is REVERSE required from digital inputs?
<Yes>
No
Done
Go to 6-1 (B.Dig
Outputs)
Flux Vector Start Up (Strt,Stop,I/O)
B = Basic mode
Enter/
Backup
Digital In 1
Digital In 2
Digital In 3
Digital In 4
Digital In 5
Digital In 6
6-20
Start-Up
A. Dig Inputs
Enter choice for
Digital In1 Sel
6-21
Start-Up
A. Dig Inputs
Enter choice for
Digital In2 Sel
6-22
Start-Up
A. Dig Inputs
Enter choice for
Digital In3 Sel
6-23
Start-Up
A. Dig Inputs
Enter choice for
Digital In4 Sel
6-24
Start-Up
A. Dig Inputs
Enter choice for
Digital In5 Sel
6-25
Start-Up
A. Dig Inputs
Enter choice for
Digital In6 Sel
No
Backup
B
Start-Up
A. Dig Inputs
2 wire control uses a contact that acts as both STOP (Open)
& Run (Closed).
3 wire control uses 2 contacts; one for START
& one for STOP.
6-6
Yes
B
Start-Up
A. Dig Inputs
2 wire control uses a contact that acts as both STOP (Open)
& Run (Closed).
3 wire control uses 2 contacts; one for START
& one for STOP.
6-7
6-8
Start-Up
A. Dig Inputs
Enter choice for
Control Method
<3 wire>
2 wire
More info
B
6-9
Start-Up
A. Dig Inputs
Digital In1 set to Not Used.
Digital In2 set to Run/Stop.
2-wire
B
More
Info..
3-wire
Start-Up
A. Dig Inputs
Digital In1 set to Stop.
Digital In2 set to Start.
B 6-11
6-13
Start-Up
A. Dig Inputs
Enter choice for
Control Method
<3 wire>
2 wire
More info
B
6-14
2-wire
Start-Up
A. Dig Inputs
Digital In1 set to Run Forward.
Digital In2 set to Run Reverse.
B
More
Info..
3-wire
B
6-16
Start-Up
A. Dig Inputs
Digital Input 3 will be set to Fwd/
Reverse.
B
Start-Up
A. Dig Inputs
Digital In1 set to Stop.
Digital In2 set to Start.
6-17
6-10
Start-Up
A. Dig Inputs
Digital Inputs configured for
2-wire control no reversing
B
Start-Up
A. Dig Inputs
Digital Inputs configured for
3-wire control no reversing.
B
6-12 6-15
Start-Up
A. Dig Inputs
Digital Inputs configured for
2-wire control with reversing.
B B
Start-Up
A. Dig Inputs
Digital Inputs configured for
3-wire control with reversing.
6-18
Note:
- For V/Hz mode, states 6-3 - 6-5, & 6-11 - 6-16 are not displayed.
Go to 6-1 (B. Dig
Outputs)
2-170
Start-Up
Figure 2.22 PowerFlex 700 Vector Control Option Startup (7)
No
6-28
Start-Up
B. Dig Outputs
Enter choice for
Digital Out 1 Sel
Digital Out 1
6-27
Start-Up
B. Dig Outputs
Make a selection
<Digital Out 1>
Digital Out 2
Digital Out 3
Done
6-30
Digital Out 2
Start-Up
B. Dig Outputs
Enter choice for
Digital Out 2 Sel
Done
Digital Out 1
Sel = ENUM choice that uses "Level"?
6-29
Yes
Start-Up
B. Dig Outputs
Enter value for
Dig Out 1 Level
Digital Out 2
Sel = ENUM choice that uses "Level"?
Yes
6-31
Start-Up
B. Dig Outputs
Enter value for
Dig Out 2 Level
No
6-49
Start-Up
C.Analog Outputs
Make a selection
<Anlgl Out 1>
Anlg Out 2
Done
Analog 1
6-50
Start-Up
C.Analog Outputs
Enter choice for
Analog Out 1 Sel
Output Freq
6-51
Start-Up
C.Analog Outputs
Enter choice for
Signal Type
<Voltage>
Current
6-52
Start-Up
C.Analog Outputs
Enter value for
Analog Out 1 Hi
10.000 Volt x.xxxx < y.yyyy
6-53
Start-Up
C.Analog Outputs
Enter value for
Analog Out 1 Lo
0.0 Volt x.xxxx < y.yyyy
Go to 6-1 (D.
Done)
Analog 2
6-54
Start-Up
C.Analog Outputs
Enter choice for
Analog Out 2 Sel
Output Amps
6-55
Start-Up
C.Analog Outputs
Enter choice for
Signal Type
<Voltage>
Current
6-56
Start-Up
C.Analog Outputs
Enter value for
Analog Out 2 Hi
10.000 Volt x.xxxx < y.yyyy
6-57
Start-Up
C.Analog Outputs
Enter value for
Analog Out 2 Lo
0.0 Volt x.xxxx < y.yyyy
Go to 6-1 (C.Anlg
Inputs)
Digital Out 3
Start-Up
B. Dig Outputs
Enter choice for
Digital Out 3 Sel
6-32
Digital Out 3
Sel = ENUM choice that uses "Level"?
Yes
6-33
Start-Up
B. Dig Outputs
Enter value for
Dig Out 3 Level
No
Flux Vector Start Up (Start,Stop,I/O [2])
6-34
Start-Up
C. Anlg Inputs
Enter choice for
Input Signal
<Analog Input 1>
Analog Input 2
6-35
Anlg 1
Start-Up
Enter choice for
Signal type:
<Voltage>
Current
6-36
Torque Ref-
Anlg 1
Start-Up
C. Anlg Inputs
The next two steps scale a high torque with a high analog value.
6-37
Start-Up
C. Anlg Inputs
Enter value for
Analog In 1 Hi
10.0 V
x.xxxx < y.yyyy
6-38
Start-Up
C. Anlg Inputs
Enter value for
Torque Ref A Hi
100.0 %
x.x < y.y
6-39
Start-Up
C. Anlg Inputs
The next two steps scale a low torque with a low analog value.
6-40
Start-Up
C. Anlg Inputs
Enter value for
Analog In 1 Lo
10.0 V
x.xxxx < y.yyyy
6-41
Start-Up
C. Anlg Inputs
Enter value for
Torque Ref A Hi
100.0 %
x.x < y.y
Anlg 2
6-42
Start-Up
C. Anlg Inputs
Enter choice for
Signal type:
<Voltage>
Current
Torque Ref-
Anlg 2
6-43
Start-Up
C. Anlg Inputs
The next two steps scale a high torque with a high analog value.
6-44
Start-Up
C. Anlg Inputs
Enter value for
Analog In 2 Hi
10.0 V
x.xxxx < y.yyyy
Start-Up
C. Anlg Inputs
Enter value for
Torque Ref A Hi
100.0 %
x.x < y.y
6-45
6-46
Start-Up
C. Anlg Inputs
The next two steps scale a low torque with a low analog value.
Start-Up
C. Anlg Inputs
Enter value for
Analog In 2 Lo
10.0 V
x.xxxx < y.yyyy
6-47
6-48
Start-Up
C. Anlg Inputs
Enter value for
Torque Ref A Hi
100.0 %
x.x < y.y
Go to 6-1 (D.Anlg
Outputs)
Start-Up
2-171
Figure 2.22 PowerFlex 700 Vector Control Option Startup (8)
Flux Vector Start Up (Application Functions)
7-0
Start-Up
7.Appl. Features
This allows programming of additional drive features.
7-1 Start-Up
7.Appl Features
Make a Selection
<Flying Start>
Auto Restart
Done
Process PI
7-2
Start-Up
7.Appl Features
Enter choice for
PI Reference
1
Analog In 1
7-3
Start-Up
7.Appl Features
Enter choice for
PI Feedback
1
Analog In 1
7-4
Start-Up
7.Appl Features
Enter value for
PI Setpoint
50.0%
xx.x < yy.y
7-5
Start-Up
7.Appl Features
Enter value for
PI Upper Limit
60.0 Hz
xx.x < yy.y
7-6
Start-Up
8.Appl Features
Enter value for
PI Lower Limit
-60.0 Hz
xx.x < yy.y
7-7
Start-Up
8.Appl Features
Enter value for
PI Integral Time
2.0 Secs x.x < y.y
7-8
Start-Up
8.Appl Features
Select other PI options in parameter #124.
Auto
Restart
Flying
Start
No
7-3
Start-Up
7.Appl Features
Enable Flying
Start?
<Yes>
No
7-2
Yes
Start-Up
7.Appl Features
Enter value for
Flying StartGain
4000 xxx < yyyy
7-4
Start-Up
7.Appl Features
Set Auto Restart
Tries to Zero to disable the function.
7-5
Start-Up
7.Appl Features
Enter value for
Auto Rstrt Tries
0 xxx < yyyy
Go to 7-1 (Auto
Restart)
Go to 7-1 (Done)
Auto Restart tries = 0?
Yes
No
7-6
Start-Up
7.Appl Features
Enter value for
Auto Rstrt Delay
1.0 Secs xx.x < yy.y
Go to 0-1 (8. Done/
Exit)
2-172
Start-Up
Figure 2.22 PowerFlex 700 Vector Control Option Startup (9)
Flux Vector Start Up (S.M.A.R.T.)
8-4
Start-Up
SMART
Enter value for
Maximum Speed
60.0 Hz
8-5
Start-Up
SMART
Enter value for
Accel Time 1
10.0 Secs
8-6
Start-Up
SMART
Enter value for
Decel Time 1
10.0 Secs
8-7
Start-Up
SMART
Enter value for
Speed Ref A Sel
Analog In 2
8-8
Start-Up
SMART
Enter value for
Motor NP FLA
0.8 Amps
8-9
Start-Up
SMART
Enter value for
Motor OL Hertz
10.0 Hz
8-10
Start-Up
SMART
Enter value for
Motor OL Factor
1.0
8-11
Start-Up
SMART
SMART Startup is now complete.
8-0
Start-Up
SMART
Enter choice of
Speed units:
<Hz>
RPM
8-1
Start-Up
SMART
Enter value for
Digital In 2 Sel
5
Start
8-2
Start-Up
2. Motr Dat/Ramp
Enter choice for
Stop Mode A
Coast
<Ramp>
Ramp to Hold
DC Brake
8-3
Start-Up
SMART
Enter value for
Minimum Speed
0.0 Hz
Start-Up
2-173
Figure 2.22 PowerFlex 700 Vector Control Option Startup (10)
1-0
Start-Up
1. Motor Control
This section selects the type of Motor Control the drive will use.
1-1
Start-Up
1. Motor Control
Enter choice of
Control:
<Speed>
Torque
More info
Flux Vector Start Up (Motor Control Select)
1-2
Start-Up
Torque
Is an encoder present?
<Yes>
No
Torque Speed
Start-Up
Speed
Is an encoder present?
<Yes>
No
1-11
Torque- No
Torque-
Yes
1-12
YES-Speed path-
Set #88 to 1
1-3
1-4
Start-Up
Torque-FOC
An Encoder is required for the
Torque Control option. Select another Motor
Control option or install an encoder.
Start-Up
Speed-SVC
Enter value for
Encoder PPR
1024
1-5
Torque path
Start-Up
Speed-SVC
Control selected is FOC Speed
Regulate.
1-6
Min Torque/
Speed -
Set #88 to 3
Start-Up
Torque-FOC
Control selected is Torque/FOC
Min Torque/Speed
1-7
Start-Up
Torque-FOC
Control selected is Torque/FOC
Max Torque/Speed
Start-Up
Torque-FOC
Select Torque
Regulate option:
<Torque Regulate>
Min Torque/Speed
Max Torque/Speed
Sum Torque/Speed
Absolute
Max
Trq/Speed -
Set #88 to 4
Trq
Regulate
Set #88 to 2
Absolute-
Set #88 to 6
Sum Trq/Speed-
Set #88 to 5
1-9
Start-Up
Torque-FOC
Control selected is Torque/FOC
Sum Torque/Speed
Start-Up
Torque-FOC
Control selected is Torque/FOC
Absolute
1-8
1-10
NO
1-13
Start-Up
Frequency-V/Hz
Select Motor
Control Mode
<SVC-common>
V/Hz
More info
V/Hz
1-25
Start-Up
Speed-SVC
Control selected is Speed/SVC with Slip Comp
Start-Up
Torque-FOC
Control selected is Torque/FOC
Torque Regulate
1-14
Start-Up
Frequency-V/Hz
Select Motor
Control Mode
<V/Hz-Fan/Pump>
V/Hz-Custom
V/Hz-Multi Motor
SV-No regulation
Sensorless
Vector - set param #53 to '0' & #80 to '0'
1-16
Start-Up
Frequency-V/Hz
Control selected is Frequency/SV no Slip Comp
1-17
Fan/Pump -
Set param
#53 to '3' &
#80 to '0'
Start-Up
Frequency-V/Hz
Control selected is Freq/Fan/Pump no Slip Comp
V/Hz
Custom/Multi
Motor - Set param #53 to '2'
& #80 to '0'
1-15
Start-Up
Frequency-V/Hz
Select V/Hz
Parameters.
<Standard V/Hz>
Custom V/Hz
1-18
Standard
Start-Up
Frequency-V/Hz
Control selected is Freq/V/Hz.
Start-Up
Speed-SVC
Enter value for
Max Voltage
10.0 V
x.x < y.y
Go to 1-1
Start-Up
Speed-SVC
Use Speed-SVC for applications requiring speed regulation.
Start-Up
Speed-SVC
Enter choice of
Speed Units
<V/Hz>
RPM
Custom
1-19
Start-Up
Frequency-V/Hz
Enter value for
Run Boost
10V xx.x < yy.y
1-20
Start-Up
Frequency-V/Hz
Enter value for
Start Boost
10.0 V
x.xxxx < y.yyyy
1-21
Start-Up
Frequency-V/Hz
Enter value for
Break Voltage
10.0 Hz
x.x < y.y
1-22
Start-Up
Frequency-V/Hz
Enter value for
Break Frequency
10.0 Hz
x.xxxx < y.yyyy
1-23
Start-Up
Frequency-V/Hz
Enter value for
Max Voltage
10.0 V
x.x < y.y
1-24
Start-Up
Frequency-V/Hz
Control selected is Freq/Custom.
Go to 0-1
2. Motr Dat/Ramp
2-174
Stop Modes
Stop Modes
[Stop Mode A, B]
[DC Brake Lvl Sel]
[DC Brake Level]
[DC Brake Time]
1. Coast to Stop - When in Coast to Stop, the drive acknowledges the Stop command by shutting off the output transistors and releasing control of the motor. The load/motor will coast or free spin until the mechanical energy is dissipated.
Output Voltage
Output Current
Motor Speed
Time
Coast Time is load dependent
Stop
Command
2. Dynamic Braking is explained in detail in the PowerFlex Dynamic
Braking Selection Guide, presented in
3. DC Brake is selected by setting [Stop Mode A] to a value of “3.” The user can also select the amount of time the braking will be applied and the magnitude of the current used for braking with [DC Brake Time] and
[DC Brake Level]. This mode of braking will generate up to 40% of rated motor torque for braking and is typically used for low inertia loads.
When in Brake to Stop, the drive acknowledges the Stop command by immediately stopping the output and then applying a programmable DC voltage [DC Brake Level] to 1 phase of the motor.
The voltage is applied for the time programmed in [DC Brake Time].
After this time has expired, all output ceases. If the load is not stopped, it will continue to coast until all energy is depleted (A on the diagram below). If the time programmed exceeds the needed time to stop, the drive will continue to apply the DC hold voltage to the non-rotating motor (B on the diagram below). Excess motor current could cause motor damage. The user is also cautioned that motor voltage can exist long after the Stop command is issued. The right combination of Brake
Level and Brake Time must be determined to provide the safest, most efficient stop (C on the diagram below).
Output Voltage
Output Current
Motor Speed
DC
Hold Level
Time
Stop
Command
(B)
DC Hold Time
(C) (A)
Stop Modes
2-175
4. Ramp To Stop is selected by setting [Stop Mode x]. The drive will ramp the frequency to zero based on the deceleration time programmed into
[Decel Time 1/2]. The “normal” mode of machine operation can utilize
[Decel Time 1]. If the “Machine Stop” mode requires a faster deceleration than desired for normal mode, the “Machine Stop” can activate [Decel Time 2] with a faster rate selected. When in Ramp to
Stop, the drive acknowledges the Stop command by decreasing or
“ramping” the output voltage and frequency to zero in a programmed period (Decel Time), maintaining control of the motor until the drive output reaches zero. The output transistors are then shut off.
The load/motor should follow the decel ramp. Other factors such as bus regulation and current limit can alter the decel time and modify the ramp function.
Ramp mode can also include a “timed” hold brake. Once the drive has reached zero output hertz on a Ramp-to-Stop and both parameters [DC
Hold Time] and [DC Hold Level] are not zero, the drive applies DC to the motor producing current at the DC Hold Level for the DC Hold
Time.
Output Voltage
Output Current
Motor Speed
Output Current
Output Voltage
DC
Hold
Level
DC Hold Time
Time
Stop
Command
Zero
Command
Speed
Motor speed during and after the application of DC depends upon the combination of the these two parameter settings, and the mechanical system. The drive output voltage will be zero when the hold time is finished.
The level and uniformity of the DC braking offered at zero speed may not be suitably smooth for many applications. If this is an application requirement, a vector control drive, motion control drive or mechanical brake should be used.
The drive output voltage will be zero when the hold time is finished
2-176
Stop Modes
5. Ramp To Hold is selected by setting [Stop Select x]. The drive will ramp the frequency to zero based on the deceleration time programmed into [Decel Time 1/2]. Once the drive reaches zero hertz, a DC Injection holding current is applied to the motor. The level of current is set in [DC
Brake Level].
In this mode, the braking is applied Continuously. [DC Hold Time] has no effect in this mode. Braking will continue until one of the following events occur:
– The Enable Input is opened, or . . .
– A Start command is re-issued.
Again, caution must be exercised to not overheat the motor by applying excess voltage and/or for excess time, particularly if the motor is not rotating.
Output Voltage Output Voltage
Output Current
Motor Speed
Output Current
Motor Speed
Output Current
Output Voltage
DC
Hold Level
Time
Stop
Command
Zero
Command
Speed
Re-issuing a
Start Command
Test Points
Thermal Regulator
234
236
235
237
32
[Testpoint 1 Sel]
[Testpoint 2 Sel]
Selects the function whose value is displayed value in [Testpoint x Data].
These are internal values that are not accessible through parameters.
See Testpoint Codes and Functions on page 4-10 for a listing of available codes and functions.
[Testpoint 1 Data]
[Testpoint 2 Data]
The present value of the function selected in [Testpoint x Sel].
Default:
Min/Max:
Display:
Default:
Min/Max:
Display:
499
0/999
1
Read Only
0/65535
1
Table 2.W Testpoint Codes and Functions
4
5
2
3
0
1
Code Selected in
[Testpoint x Sel]
6
7
8-99
Function Whose Value is
Displayed in [Testpoint x Data]
DPI Error Status
Heatsink Temperature
Active Current Limit
Active PWM Frequency
Lifetime MegaWatt Hours
Lifetime Run Time
Lifetime Powered Up Time
Lifetime Power Cycles
Reserved for Factory Use
See
Test Points
2-177
2-178
Torque Performance Modes
Torque Performance
Modes
[Torque Perf Mode] selects the output mode of the drive. The choices are:
•
Custom Volts/Hertz
Used in multi-motor or synchronous motor applications.
•
Fan/Pump Volts/Hertz
Used for centrifugal fan/pump (variable torque) installations for additional energy savings.
•
Sensorless Vector
Used for most general constant torque applications. Provides excellent starting, acceleration and running torque.
•
Sensorless Vector w/Economizer
Used in constant torque applications that have significant “idle” time
(time spent at greatly reduced load) to offer additional energy conservation.
The following table shows the performance differences between V/Hz and
Sensorless Vector.
Torque Mode
Speed Regulation/accuracy (w/ slip compensation)
Operating Speed Range (w/slip compensation)
Dynamic Speed Accuracy
(speed response to a 95% step load change)
Velocity Bandwidth (w/slip compensation and no encoder)
Minimum setting of velocity bandwidth/slip compensation
Fan/Pump and
Custom V/Hz SVC
0.5% 0.5%
40:1
0.5% base speed
10 rad/s
0.1 rad/s
80:1
0.5% base speed
20 rad/s (50 rad/s desired)
0.1 rad/s
Volts/Hertz
Volts/Hertz operation creates a fixed relationship between output voltage and output frequency. The relationship can be defined in two ways.
1. Fan/Pump
When this option is chosen, the relationship is 1/X
2
. Therefore; for full frequency, full voltage is supplied and for 1/2 rated frequency,
1/4 voltage is applied, etc. This pattern closely matches the torque requirement of a variable torque load (centrifugal fan or pump – load increases as speed increases) and offers the best energy savings for these applications.
Maximum Voltage
Base Voltage
(Nameplate)
Run Boost
Base Frequency
(Nameplate)
Maximum
Frequency
Torque Performance Modes
2-179
2. Custom
Custom Volts/Hertz allows a wide variety of patterns using linear segments. The default configuration is a straight line from zero to rated voltage and frequency. This is the same volts/hertz ratio that the motor would see if it were started across the line. As seen in the diagram below, the volts/hertz ratio can be changed to provide increased torque performance when required. The shaping takes place by programming 5 distinct points on the curve:
– Start Boost - Used to create additional torque for breakaway from zero speed and acceleration of heavy loads at lower speeds
– Run Boost - Used to create additional running torque at low speeds.
The value is typically less than the required acceleration torque. The drive will lower the boost voltage to this level when running at low speeds (not accelerating). This reduces excess motor heating that could be caused if the higher start / accel boost level were used.
– Break Voltage/Frequency - Used to increase the slope of the lower portion of the Volts / hertz curve, providing additional torque.
– Motor Nameplate Voltage/Frequency - sets the upper portion of the curve to match the motor design. Marks the beginning of the constant horsepower region
– Maximum Voltage/Frequency - Slopes that portion of the curve used above base speed.
Maximum Voltage
Base Voltage
(Nameplate) Voltage
Break Voltage
Start/Accel Boost
Run Boost
Break
Frequency
Base Frequency
(Nameplate)
Maximum
Frequency
2-180
Torque Performance Modes
Sensorless Vector
Sensorless Vector technology consists of a basic V/Hz core surrounded by excellent current resolution (the ability to differentiate flux producing current from torque producing current), a slip estimator, a high performance current limiter (or regulator) and the vector algorithms.
SPEED REF.
+
+
FREQUENCY REF.
Current
Limit
ELEC. FREQ.
CURRENT FEEDBACK - TOTAL
TORQUE I EST.
Current
Resolver
CURRENT FEEDBACK
V/Hz Control
V/Hz
V REF.
Voltage
Control
GATE
SIGNALS
Inverter Motor
TORQUE I EST.
Flux
Vector
Control
V VECTOR
SLIP FREQUENCY
Slip
Estimator
The algorithms operate on the knowledge that motor current is the vector sum of the torque and flux producing components. Values can be entered to identify the motor values or an autotune routine can be run to interrogate and identify the motor values (see
Autotune on page 2-181 ). Early versions
required feedback, but today, performance is sensorless. It offers high breakaway torque, exceptional running torque, a wider speed range than V/
Hz, higher dynamic response and a fast accel “feed forward” selectable for low inertia loads (adaptive current limit).
Sensorless vector is not a torque regulating technology. It does NOT independently control the flux and torque producing currents. Therefore, it cannot be used to regulate torque (torque follower).
In sensorless vector control, the drive maintains a constant flux current up to base speed, allowing the balance of the drive available current to develop maximum motor torque. By manipulating output voltage as a function of load, excellent motor torque can be generated.
Maximum Voltage
Base Voltage
(Nameplate)
Ir Voltage ve
Apppro ximate Full Load Cur
Apppro ximate No Load Cur ve
Base Frequency
(Nameplate)
Maximum
Frequency
Torque Performance Modes
2-181
Autotune
The purpose of Autotune is to identify the motor flux current and stator resistance for use in Sensorless Vector Control and Economizer modes. The result of the flux current test procedure is stored in the parameter [Flux
Current]. The product of [Flux Current] and the result of the stator resistance test procedure will be stored in the parameter [IR Voltage Drop].
There are two options for autotuning:
•
Static - the motor shaft will not rotate during this test.
•
Dynamic - the motor shaft will rotate during this test.
The static test determines only stator resistance, while the dynamic
Autotune procedure determines both the stator resistance and motor flux current.
[IR Voltage Drop] is used by the IR Compensation procedure to provide additional voltage at all frequencies to offset the voltage drop developed across the stator resistance. An accurate calculation of the [IR Voltage
Drop] will ensure higher starting torque and better performance at low speed operation.
If it is not possible or desirable to run the Autotune tests, there are two other methods for the drive to determine the [IR Voltage Drop] and [Flux Current] parameters. One method retrieves the default parameters stored in the power
EEprom, and the other method calculates them from the user-entered motor nameplate data parameters.
If the stator resistance and flux current of the motor are known, the user can calculate the voltage drop across the stator resistance and directly enter these values into the [Flux Current] and [IR Voltage Drop] parameters.
The user must enter motor nameplate data into the following parameters for the Autotune procedure to obtain accurate results:
[Motor NP Volts]
[Motor NP Hertz]
[Motor NP Power]
In addition to the motor nameplate parameters, the user must also enter a value in the [Autotune] parameter to determine which Autotune tests to perform.
The following options for the [Autotune] parameter are as follows:
0 = Ready
1 = Static Tune
2 = Rotate Tune
3 = Calculate
The procedure to identify the motor flux current, stator resistance, and IR voltage drop is started with the [Autotune] parameter. The tests are initiated after a value is entered (1 for static or 2 for dynamic) into this parameter and the start button is pressed. When the tests are finished, the [Autotune] parameter is set to 0 (ready), the drive is stopped, and the Autotune procedure is complete.
2-182
Torque Performance Modes
If any errors are encountered during the Autotune process drive parameters are not changed, the appropriate fault code will be displayed in the fault queue, and the [Autotune] parameter is reset to 0. If the Autotune procedure is aborted by the user, the drive parameters are not changed and the
[Autotune] parameter is reset to 0.
The following conditions will generate a fault during an Autotune procedure:
•
Incorrect stator resistance measurement
•
Incorrect motor flux current measurement
•
Load too large
•
Autotune aborted by user
When the drive is initially powered up, the [Autotune] parameter is defaulted to a value of 3(calculate). With this setting, any changes made by the user to motor nameplate HP, Voltage, Frequency, or Power activates a new calculation, which will update the [IR Voltage Drop] and [Flux
Current] parameters. This calculation is based on a typical motor with those nameplate values. The Autotune parameter will not be reset to zero after this calculation is performed; calculations will continue to be performed every time motor nameplate values are changed.
Flux Current
[Flux Current Ref]
The test to identify the motor flux current requires the load to be uncoupled from the motor to find an accurate value. If this is not possible and the no load current is know then the value can be entered into the flux current parameter and this step in the drive commissioning can be skipped. If it is not possible to uncouple the load and the no load current is not known, then a value of zero is entered into flux and this step in the drive commissioning can be skipped.
This parameter displays only the flux producing component of output current. It displays the amount of current that is out of phase with the output voltage. This current is reactive current and is used to produce flux in the motor.
Flux Up
[Flux Up Mode]
AC induction motors require flux to be established before controlled torque can be developed. To build flux in these motors, voltage is applied to them.
PowerFlex drives have two methods to flux the motor.
Torque Performance Modes
2-183
The first method is a normal start. During a normal start, flux is established as the output voltage and frequency are applied to the motor. While the flux is being built, the unpredictable nature of the developed torque may cause the rotor to oscillate even though acceleration of the load may occur. In the motor, the acceleration profile may not follow the commanded acceleration profile due to the lack of developed torque.
Figure 2.23 Accel Profile during Normal Start - No Flux Up
Frequency
Reference
Rated Flux
Stator
Rotor
0
Oscillation due to flux being established
Time
The second method is Flux Up Mode. In this mode, DC current is applied to the motor at a level equal to the lesser of the current limit setting, drive rated current, and drive DC current rating. The flux up time period is based on the level of flux up current and the rotor time constant of the motor.
The flux up current is not user adjustable.
Figure 2.24 Flux Up Current versus Flux Up Time
Flux Up Current = Maximum DC Current
Rated Flux
Current
Rated Motor Flux
Motor Flux
T1
T2
T3
T4
Flux Up Time
[Flux Up Time]
Once rated flux is reached in the motor, normal operation begins and the desired acceleration profile is achieved.
2-184
Torque Performance Modes
Figure 2.25 Rated Flux Reached
Flux Up
Voltage
Motor Flux
Flux Up
Ir Voltage - SVC
Greater of IR Voltage or
Voltage Boost - V/Hz
Normal
Operation
Stator Voltage
Rotor Speed
Motor Flux
Stator Freq
Time
Torque Current
This parameter displays only the torque producing component of output current. It displays the amount of current that is in phase with the output voltage. This current is real current and is used to produce torque in the motor.
IR Drop Volts
[IR Voltage Drop]
The test to identify the IR drop of the drive and motor does not require the load to be uncoupled from the motor and should be run even if the flux current identification procedure is skipped.
Troubleshooting
Troubleshooting
2-185
See also
.
Power Up Marker
Copy of factory “drive under power” timer at the last power-up of the drive.
Used to provide relevance of Fault 'n' Time values with respect to the last power-up of the drive.
This value will rollover to 0 after the drive has been powered on for more than the hours shown in the Range field (approximately 47.667 years).
2-186
Unbalanced or Ungrounded Distribution Systems
Unbalanced or
Ungrounded
Distribution Systems
Unbalanced Distribution Systems
This drive is designed to operate on three-phase supply systems whose line voltages are symmetrical. Surge suppression devices are included to protect the drive from lightning induced overvoltages between line and ground.
Where the potential exists for abnormally high phase-to-ground voltages (in excess of 125% of nominal), or where the supply ground is tied to another system or equipment that could cause the ground potential to vary with operation, suitable isolation is required for the drive. Where this potential exists, an isolation transformer is strongly recommended.
Ungrounded Distribution Systems
All drives are equipped with an MOV (Metal Oxide Varistor) that provides voltage surge protection and phase-to-phase plus phase-to-ground protection which is designed to meet IEEE 587. The MOV circuit is designed for surge suppression only (transient line protection), not continuous operation.
With ungrounded distribution systems, the phase-to-ground MOV connection could become a continuous current path to ground. Energy ratings are listed below. Exceeding the published phase-to-phase or phase-to-ground energy ratings may cause physical damage to the MOV.
Three-Phase
AC Input
R
S
T
Ground
Joules (J)
Joules (J)
Joules (J)
Joules (J)
1 2 3 4
Phase-to-Phase MOV Rating
Includes 2 Phase-Phase MOVs
Phase-to-Ground MOV Rating
Includes Phase-Phase & Phase-Ground MOVs
Device Rating (V AC)
Phase-Phase Total
Phase-Ground Total
240 480/600
160J 320J
220J 380J
240/480 600
280J 320J
360J 410J
240/480 600
280J 300J
360J 370J
PowerFlex drives contain protective MOVs and common mode capacitors that are referenced to ground. To guard against drive damage, these devices should be disconnected if the drive is installed on an ungrounded distribution system where the line-to-ground voltages on any phase could exceed 125% of the nominal line-to-line voltage. Refer to your PowerFlex
User Manual for details.
Also refer to “Wiring and Grounding Guidelines for PWM AC Drives,” publication DRIVES-IN001A-EN-P.
User Sets
User Sets
2-187
After a drive has been configured for a given application the user can store a copy of all of the parameter settings in a specific EEPROM area known as a
“User Set.” Up to 3 User Sets can be stored in the drives memory to be used for backup, batch “switching” or other needs. All parameter information is stored. The user can then recall this data to the active drive operating memory as needed. Each User Set can also be identified with a programmable name, selected by the user for clarity.
Two operations are available to manage User Sets, “Save To User Set” and
“Restore From User Set.” The user selects 1, 2, or 3 as the area in which to store data. After data is successfully transferred, “Save User Set” returns to a value of 0. To copy a given area back into the active EEprom memory, the user selects Set 1, 2, or 3 for “Restore User Set.” After data is successfully transferred, “Restore User Set” returns to a value of 0. When shipped from the factory all user sets have the same factory default values. Reset Defaults does not effect the contents of User Sets.
Important: User Sets can only be transferred via the HIM. No provisions exist for control via digital I/O or communications module.
Figure 2.26 User Sets
Reset Defaults
PowerBoard
EEprom
Factory
Default Data
Drive Rating & Motor
Parameters
1
Reset
Active EE
Non Drive Rating & Motor
Parameters
Flash Memory
SaveUserSet
400V
Default Data
2
1 User Set 1
Save
User set
480V
Default Data
3
Active EE 2 User Set 2
Restore
User set
3 User Set 3
RestoreUserSet
Load
Application
Set
Flash Memory
Application Set
2-188
Voltage class
Voltage class
PowerFlex drives are sometimes referred to by voltage “class.” This class identifies the general input voltage to the drive. This general voltage includes a range of actual voltages. For example, a 400 Volt Class drive will have an input voltage range of 380-480VAC. While the hardware remains the same for each class, other variables, such as factory defaults, catalog number and power unit ratings will change. In most cases, all drives within a voltage class can be reprogrammed to another drive in the class by resetting the defaults to something other than “factory” settings. The
[Voltage Class] parameter can be used to reset a drive to a different setup within the voltage class.
As an example, consider a 480 volt drive. This drive comes with factory default values for 480V, 60 Hz with motor data defaulted for U.S. motors
(HP rated, 1750 RPM, etc.) By setting the [Voltage Class] parameter to
“low Voltage” (this represents 400V in this case) the defaults are changed to
400V, 50 Hz settings with motor data for European motors (kW rated, 1500
RPM, etc.). Refer to
Watts Loss
Watts Loss
2-189
The following table lists watts loss data for PowerFlex drives running at full load, full speed and a factory default PWM Frequency of 4 kHz.
PowerFlex 70
For PowerFlex 70 drives, Internal Watts are those dissipated by the control structure of the drive and will be dissipated into the cabinet regardless of mounting style. External Watts are those dissipated directly through the heatsink and will be outside the cabinet for flange mount and inside the cabinet for panel mount.
Table 2.X PowerFlex 70 Watts Loss at Full Load/Speed, 4kHz
(1)
Voltage Normal Duty HP Internal
480 0.5
17.9
1
2
19.5
21.6
3
5
7.5
10
24.0
28.2
27.8
32.0
240V
2
3
5
7.5
10
15
20
0.5
1
34.2
42.9
19.2
20.5
22.6
25.4
33.2
34.2
48.1
305.4
432.9
12.2
30.7
44.6
67.3
141.3
205.7
270.4
External
11.5
27.8
43.6
64.6
99.5
140.0
193.3
339.6
475.8
31.4
51.2
67.2
92.7
174.5
239.9
318.5
Total
29.4
47.3
65.2
88.6
127.7
167.8
225.3
PowerFlex 700
PowerFlex 700 drives are offered in panel mount versions only. At this time, no method exists for venting outside of a secondary enclosure. This requires enclosure sizing for total watts. see
(1) Includes HIM.
2-190
Watts Loss
Table 2.Y PowerFlex 700 Watts Loss at Full Load/Speed, 4kHz
(1)
Voltage
480V
40
50
60
75
100
15
20
25
30
3
5
7.5
10
1
2
ND HP
0.5
117
148
210
241
332
99
91
102
103
46
87
79
84
Internal
42
44
45
226
303
339
357
492
568
764
906
1143
46
78
115
134
External
11
19
31
326
394
441
459
610
717
974
1146
1475
93
164
194
218
Total
53
63
76
(1) Includes HIM and Standard I/O Board.
advertisement
Related manuals
advertisement
Table of contents
- 5 Specifications & Dimensions
- 5 PowerFlex 70/700 Specifications
- 7 Input/Output Ratings
- 7 Heat Dissipation
- 8 Derating Guidelines
- 11 PowerFlex 70 Dimensions
- 17 PowerFlex 700 Dimensions
- 25 Detailed Drive Operation
- 25 Accel Time
- 26 AC Supply Source Considerations
- 26 Alarms
- 30 Analog Inputs
- 43 Analog Outputs
- 47 Auto/Manual
- 49 Auto Restart (Reset/ Run)
- 51 Bus Regulation
- 56 Cable, Control
- 56 Cable, Motor Lengths
- 59 Cable, Power
- 62 Cable, Standard I/O
- 62 CabIe Trays and Conduit
- 63 Carrier (PWM) Frequency
- 64 CE Conformity
- 66 Copy Cat
- 67 Current Limit
- 69 Datalinks
- 71 DC Bus Voltage / Memory
- 71 Decel Time
- 72 Diagnostics
- 75 Digital Inputs
- 92 Digital Outputs
- 96 Direction Control
- 97 DPI
- 100 Drive Overload
- 104 Drive Ratings (kW, Amps, Volts)
- 104 Economizer (Auto-Economizer)
- 105 Efficiency
- 105 Fan Curve
- 105 Fan
- 106 Faults
- 109 Flying Start
- 111 Fuses and Circuit Breakers
- 115 Grounding, General
- 116 HIM Memory
- 116 HIM Operations
- 117 Input Devices
- 118 Input Modes
- 119 Input Power Conditioning
- 119 Jog
- 120 Language
- 121 Masks
- 123 MOP
- 125 Motor Nameplate
- 126 Motor Overload
- 129 Motor Start/Stop Precautions
- 129 Mounting
- 130 Output Current
- 130 Output Devices
- 131 Output Frequency
- 131 Output Power
- 131 Output Voltage
- 132 Overspeed Limit
- 133 Owners
- 135 Parameter Access Level
- 135 PET
- 136 Power Loss
- 144 Preset Frequency
- 145 Process PI Loop
- 156 Reflected Wave
- 158 Reset Meters
- 158 Reset Run
- 158 RFI Filter Grounding
- 159 S Curve
- 161 Scaling Blocks
- 162 Shear Pin Fault
- 163 Skip Frequency
- 165 Sleep Mode
- 168 Speed Control Speed Mode Speed Regulation
- 172 Speed Reference
- 176 Start Inhibits
- 177 Start Permissives
- 178 Start-Up
- 198 Stop Modes
- 201 Test Points
- 201 Thermal Regulator
- 202 Torque Performance Modes
- 209 Troubleshooting
- 210 Unbalanced or Ungrounded Distribution Systems
- 211 User Sets
- 212 Voltage class
- 213 Watts Loss
- 215 Dynamic Brake Selection Guide
- 219 Table of Contents
- 221 Section 1
- 221 Understanding How Dynamic Braking Works
- 225 Section 2
- 225 Determining Dynamic Brake Requirements
- 237 Section 3
- 237 Evaluating the Internal Resistor
- 245 Section 4
- 245 Selecting An External Resistor
- 253 Appendix A