- Industrial & lab equipment
- Welding System
- ESAB
- m3® Plasma Integrated Gas Control (IGC) System - ICH
- Instruction manual
Torch Connections. ESAB m3® Plasma Integrated Gas Control (IGC) System - ICH, m3® plasma Integrated Gas Control
Add to My manuals190 Pages
advertisement
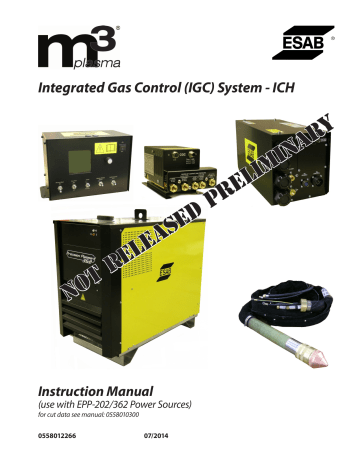
InstallatIon
Torch Connections
Torch hook-up requires the connection of power cables / coolant hoses, pilot arc cable and chassis ground. On the PT-36 torch, the coolant hoses from the RAS box to the torch also carry electrode power.
The pilot arc cable is connected inside the arc starter box. The pilot arc cable also has a green/yellow wire that is connected to a grounding stud.
Power Cable /
Coolant Connections
Pilot Arc Connection
Ground
Stud
Pilot
Arc Cable
Chassis
Ground
Wire
Power Cable /
Coolant
PG Hose
SG Hose
86
InstallatIon
Connection of Torch to Plasma System
DANGER
Electric Shock Can Kill!
• Disconnect primary power source before making any adjust ments.
• Disconnect primary source before doing maintenance on system components.
• Do not touch front-end torch parts (nozzle, retaining cup, etc.) without turning primary power off.
Ground Stud
Ground cable
Power cables
Pilot Arc cable
Connection to the Remote Arc Starter Box
The PT-36 has two water cooled power cables which must be connected to the negative output from the power supply. The right handed 7/16-20 fitting is on the cable supplying coolant to the torch. The left handed 7/16-20 fitting is on the cable returning coolant from the torch. Both of these cables have a green/yellow wire to be connected to the ground stud shown above.
The pilot arc cable is connected to the arc starter box (see Installation section). The pilot arc cable also has a green/yellow wire that is connected to a grounding stud.
87
InstallatIon
Mounting Torch to Machine
DANGER
CLAMPING ON TORCH BODY MAY CAUSE DANGEROUS CURRENT
TO FLOW THROUGH MACHINE CHASSIS.
Mount torch on insulated sleeve here
DO NOT mount on steel torch body here
•
Do not mount on stainless steel torch body.
•
Torch body is electrically insulated, however high frequency start current may arc through to find a ground.
•
Clamping near torch body may result in arcing between body and machine.
•
When this arcing occurs, torch body may require non-warranty replacement.
•
Damage to machine components may result.
•
Clamp only on insulated torch sleeve (directly above label) not less than 1.25" (31.75mm) from the torch end of the sleeve.
Placement of ICH
The ICH should be located close to the operator for easy access.
Connect required CAN cables between ICH and other CAN nodes, such as EPP-202/362 Power Source, B4 lifter, if applicable. CAN connection is always made from left to right, if one node is removed from CAN bus, all nodes on the right need to be shifted to left. After connecting all CAN nodes, a terminator is required. Leave all unused
CAN ports open.
Connect DB37 cable to port “CNC” on ICH. The other side of DB37, is connected to the customer’s CNC via a male DB37 connector. An optional breakout board may be used. A DB37 to free end cable is also available.
Connect power from ICH to PDB and B4 lifter, if applicable. Make sure the power switch on ICH is off.
Connect power to ICH box.
88
InstallatIon
Placement of CGC
The CGC regulates the plasma gas and shield gas. For optimum performance, it should always be placed close to torch. According to the material being cut, the customer needs to select and connect the correct inlet gases. Inline filters are embedded into the inlet fittings. Please make sure all inlet gases meet the pressure and flow requirements.
Connect 24V AC/DC power from PDB, then connect CAN cable to ICH.
Plasma
Shield
Air Curtain
Gas
Argon
O2/H35/F5
N2/Air
N2/Air
Air
Gas &
Pressure
Air (85psi / 5.9bar)
Process
Nitrogen
(125psi / 8.6bar)
Oxygen
(125psi / 8.6bar)
Pressure
125 psi (8.6 bar), 200 SCFH (5.7 SCMH)
125 psi (8.6 bar) for O2, 75 psi (5.2 bar) for H35/F5, 255 SCFH (7.2 SCMH)
125 psi (8.6 bar), 255 SCFH (7.2 SCMH)
125 psi (8.6 bar), 353 SCFH (10.0 SCMH)
80 psi (5.5 bar), 1200 SCFH (34.0 SCMH)
Maximum Gas Flow Rates - CFH (CMH)
With PT-36 Torch
269
(7.6)
385
(10.9)
66
(1.9)
Gas Purity
Clean, Dry, Oil Free
Filtered to 25 microns
99.99%, Filtered to 25 microns
99.5%, Filtered to 25 microns
Placement of PDB
The PDB should be placed on the deck as it is used for supplying power to the CGC.
89
InstallatIon
Individual Component Connections
Part numbers and lengths for the cables shown below are provided on the following page.
PDB front ICH back
A
B
CGC front
C
PDB back
“A” - Power cable from ICH to PDB (115/230V)
Part Number Length Part Number Length
0560947962 1m (3.3’) 0560947088 5m (16’)
0560946776
0560947964
0560947087
2m (6.4’)
3m (10’)
4m (13’)
0560947089
0560947090
6m (19’)
7m (23’)
90
“C” - Power cable PDB to CGC (24 VAC/DC)
Part Number Length Part Number Length
0560947079 1.5m (5’) 0560947064 8m (26’)
0560947080
0560947061
0560947081
0560947062
0560947063
3m (10’)
4m (13’)
5m (16’)
6m (19’)
7m (23’)
0560947065
0560947082
0560946780
0560947066
0560947083
9m (30’)
10m (33’)
12.8m (42')
15m (49’)
20m (66’)
“B” - CAN cable from ICH to CGC
Part Number Length Part Number Length
0558008464 1m (3.3’) 0558008473 10m (33’)
0558008465
0558008466
0558008467
0558008468
0558008469
0558008470
0558008471
0558008472
2m (6.5’)
3m (10’)
4m (13’)
5m (16’)
6m (19’)
7m (23’)
8m (26’)
9m (30’)
0558008474
0558008475
0558008476
0558008477
0558008478
0558008479
0558008809
0558008480
11m (36’)
12m (39’)
13m (43’)
14m (46’)
15m (49’)
20m (66’)
25m (82')
36m (118')
InstallatIon
ACC Component Connections
A
Compressed Air
Part Number
0560947067
0560947075
0560947076
0560947068
0560947077
0560947069
0560946782
Part Number
0558004841
0558004842
0558004843
0558004844
0558004845
0558006865
0558008502
“A” - Cable from ACC to PDB
Length Part Number
0.5m (1.7’)
1.5m (5’)
0560947070
0560947071
3m (10’)
4m (13’)
5m (16’)
6m (19’)
6.1m (20')
0560947072
0560947078
0560947073
0560947074
0560946758
“B” - Air Curtain hose from ACC to CGC
Length Part Number
1.4m (4.75’)
1.8m (6’)
3.7m (12’)
4.6m (15.25’)
5.3m (17.25’)
6.1m (20’)
7.0m (23’)
0558004846
0558008503
0558008504
0558008505
0558008506
0558008507
B
Length
7m (23’)
8m (26’)
9m (30’)
10m (33’)
15m (49’)
20m (66’)
25m (82')
Length
7.6m (25’)
8.0m (26.25’)
9.1m (30’)
10.1m (33')
11.0m (36.25’)
11.9m (39.5’)
91
InstallatIon
Component Placement Example
5
6 alternative mounting location
8
6
7
2
1
4
3
92
3
4
5
6
7
8
1
2
Components
CNC
Interface Control Hub (ICH)
PT-36 Torch
B4 Lift
Combined Gas Control (CGC)
Remote Arc Starter Box (RAS)
Power Supply
Power Distribution Box (PDB)
InstallatIon
DANGER
Hydrogen explosion hazard! Read the following before attempting to cut with a water table.
A hazard exists whenever a water table is used for plasma arc cutting. Severe explosions have resulted from the accumulation of hydrogen beneath the plate being cut. Thousands of dollars in property damage has been caused by these explosions. Personal injury or death could result from such an explosion. The best available information indicates that three possible sources of hydrogen exists in water tables:
1. Molten Metal Reaction
Most of the hydrogen is liberated by a fast reaction of molten metal from the kerf in the water to form metallic oxides. This reaction explains why reactive metals with greater affinity for oxygen, such as aluminum and magnesium, release greater volumes of hydrogen during the cut than does iron or steel. Most of this hydrogen will come to the surface immediately, but some will cling to small metallic particles. These particles will settle to the bottom of the water table and the hydrogen will gradually bubble to the surface.
2. Slow Chemical Reaction
Hydrogen may also result from the slower chemical reactions of cold metal particles with the water, dissimilar metals, or chemicals in the water. The hydrogen gradually bubbles to the surface.
3. Plasma Gas
Hydrogen may come from the plasma gas. At currents over 750 amps, H-35 is used as cut gas. This gas is 35% hydrogen by volume and a total of about 125 cfh of hydrogen will be released.
Regardless of the source, the hydrogen gas can collect in pockets formed by the plate being cut and slats on the table, or pockets from warped plate. There can also be accumulation of hydrogen under the slag tray or even in the air reservoir, if these are part of the table design. The hydrogen, in the presence of oxygen or air, can then be ignited by the plasma arc or a spark from any source.
4. Follow these practices to reduce hydrogen generation and accumulation:
A. Clean the slag (especially fine particles) from the bottom of the table frequently. Refill the table with clean water.
B. Do not leave plates on the table overnight or a weekend.
C. If a water table has been unused for several hours, vibrate it in some way before the first plate is laid in position.
This will allow accumulated hydrogen in the refuse to break loose and dissipate before it is confined by a plate on the table. This might be accomplished by laying the first plate onto the table with a slight jolt, then raising the plate to permit hydrogen to escape before it is finally set down for cutting.
D. If cutting above water, install fans to circulate air between the plate and the water surface.
E. If cutting underwater, agitate the water under the plate to prevent accumulation of hydrogen. This can be done by aerating the water using compressed air.
F. If possible, change the level of the water between cuts to dissipate accumulated hydrogen.
G. Maintain pH level of the water near 7 (neutral). This reduces the rate of chemical reaction between water and metals.
93
InstallatIon
WARNING
Possible explosion hazard from plasma cutting aluminum-lithium alloys!
Aluminum-Lithium (Al-Li) alloys are used in the aerospace industry because of 10% weight savings over conventional aluminum alloys. It has been reported that molten Al-Li alloys can cause explosions when they come into contact with water. Therefore, plasma cutting of these alloys should not be attempted in the presence of water. These alloys should only be dry cut on a dry table. Alcoa has determined that "dry" cutting on a dry table is safe and gives good cutting results.
DO NOT dry cut over water. DO NOT water injection cut.
The following are some of the Al-Li alloys currently available:
Alithlite (Alcoa)
Alithally (Alcoa)
2090 Alloy (Alcoa)
X8090A (Alcoa)
X8092 (Alcoa)
X8192 (Alcoa)
Navalite (U. S. Navy)
Lockalite (Lockheed)
Kalite (Kaiser)
8091 (Alcan)
For additional details and information on the safe use from the hazards associated with these alloys, contact your aluminum supplier.
WARNING
Oil And Grease Can Burn Violently!
• Never use oil or grease on this torch.
• Handle torch clean hands only on clean surface.
• Use silicone lubricant only where directed.
• Oil and grease are easily ignited and burn violently in the presence of oxygen under pressure.
WARNING
Hydrogen explosion hazard.
Do Not Cut Underwater With H-35! Dangerous buildup of hydrogen gas is possible in the water table.
Hydrogen gas is extremely explosive. Reduce the water level to 4 inches minimum below the workpiece.
Vibrate plate, stir air and water frequently to prevent hydrogen gas buildup.
94
Spark hazard.
WARNING
Heat, spatter, and sparks cause fire and burns.
• Do not cut near combustible material.
• Do not cut containers that have held combustibles.
• Do not have on your person any combustibles (e.g. butane lighter).
• Pilot arc can cause burns. Keep torch nozzle away from yourself and others when activating plasma process.
• Wear correct eye and body protection.
• Wear gauntlet gloves, safety shoes and hat.
• Wear flame-retardant clothing that covers all exposed areas.
• Wear cuffless trousers to prevent entry of sparks and slag.
InstallatIon
Preparing to Cut
•
Select an appropriate condition from the Cut Data manual (SDP File) and install recommended torch front-end parts (nozzle, electrode, etc.) See Cut Data manual to identify parts and settings.
•
Position torch over material at desired start location.
•
See Power Source Manual for proper settings.
•
See Description and Installation sections for gas control and startup procedures.
Mirror Cutting
When mirror cutting, a reverse swirl gas baffle and reverse diffuser are required. These reverse parts will “spin” the gas in the opposite direction, reversing the “good” side of the cut.
Reverse 4 x .032 Baffle
Reverse 8 x .047 Baffle
P/N 0558002534
P/N 0558002530
Reverse Diffuser P/N 0004470115
Cut Quality
Causes affecting cut quality are interdependent. Changing one variable affects all others. Determining a solution may be difficult. The following guide offers possible solutions to different undesirable cutting results. To begin select the most prominent condition:
•
Cut Angle, negative or positive
•
Cut Flatness
•
Surface Finish
•
Dross
•
Dimensional Accuracy
Usually the recommended cutting parameters will give optimal cut quality, occasionally conditions may vary enough that slight adjustments will be required. If so:
•
Make small incremental adjustments when making corrections.
•
Adjust Arc Voltage in 5 volt increments, up or down as required.
•
Adjust cutting speed 5% or less as required until conditions improve.
95
InstallatIon
CAUTION
Before attempting ANY corrections, check cutting variables with the factory recommended settings/consumable part numbers listed in
Cut Data manual.
Cut Angle
Negative Cut Angle
Top dimension is greater than the bottom.
•
Misaligned torch
•
Bent or warped material
•
Worn or damaged consumables
•
Standoff low (arc voltage)
•
Cutting speed slow (machine travel rate)
Part
Part
Positive Cut Angle
Top dimension is less than the bottom dimension.
•
Misaligned torch
•
Bent or warped material
•
Worn or damaged consumables
•
High standoff High (arc voltage)
•
Cutting speed fast
•
Current high or low. (See Cut Data manual for recommended current level for specific nozzles).
Drop
Part
Drop Part
96
InstallatIon
Cut Flatness
Top And Bottom Rounded. Condition usually occurs when material is .25" thick (6.4mm) or less.
•
High current for given material thickness.
(See Cut Data manual for proper settings).
Drop Part
Top Edge Undercut
•
Standoff low (Arc Voltage).
Drop Part
97
InstallatIon
Surface Finish
Process Induced Roughness
Cut face is consistently rough. May or may not be confined to one axis.
•
Incorrect Shield Gas mixture (See Cut Data manual).
•
Worn or damaged consumables.
Machine Induced Roughness
Can be difficult to distinguish from Process Induced
Roughness. Often confined to only one axis. Roughness is inconsistent.
•
Dirty rails, wheels and/or drive rack/pinion.
•
Carriage wheel adjustment.
Top View
Cut Face
Process
Induced
Roughness or
Machine
Induced
Roughness
Dross
Dross is a by-product of the cutting process. It is the undesirable material that remains attached to the part. In most cases, dross can be reduced or eliminated with proper torch and cutting parameter setup. Refer to Cut Data manual.
High Speed Dross
Material weld or rollover on bottom surface along kerf. Difficult to remove. May require grinding or chipping. “S” shaped lag lines.
•
Standoff high (arc voltage).
•
Cutting speed fast.
Lag Lines
Cut Face
Rollover
Side View
Lag Lines
Cut Face
Slow Speed Dross
Forms as globules on bottom along kerf. Removes easily.
•
Cutting speed slow.
Globules
Side View
98
CAUTION
InstallatIon
Recommended cutting speed and arc voltage will give optimal cutting performance in most cases. Small incremental adjustments may be needed due to material quality, material temperature and specific alloy. The operator should remember that all cutting variables are interdependent. Changing one setting affects all others and cut quality could deteriorate. Always start at the recommended settings.
Top Dross
Appears as splatter on top of material. Usually removes easily.
•
Cutting speed fast
•
Standoff high (arc voltage)
Intermittent Dross
Appears on top or bottom along kerf. Non-continuous. Can appear as any kind of dross.
•
Possible worn consumables
Other Factors Affecting Dross;
•
Material temperature
•
Heavy mill scale or rust
•
High carbon alloys
Side View
Splatter
Cut Face
CAUTION
Before attempting ANY corrections, check cutting variables with the factory recommended settings/consumable part numbers listed in the Cut Data manual.
Dimensional Accuracy
Generally using the slowest possible speed (within approved levels) will optimize part accuracy. Select consumables to allow a lower arc voltage and slower cutting speed.
NOTICE
Recommended cutting speed and arc voltage will give optimal cutting performance.
Small incremental adjustments may be needed due to material quality, material temperature and specific alloy. The operator should remember that all cutting variables are interdependent. Changing one setting affects all others and cut quality could deteriorate. Always start at the recommended settings. Before attempting ANY corrections, check cutting variables with the factory recommended settings/consumable part numbers listed in the Cut Data manual.
99
advertisement
Related manuals
advertisement
Table of contents
- 11 Safety
- 13 Safety - English
- 17 Safety - Spanish
- 21 Safety - French
- 25 System Diagrams
- 27 System Diagrams
- 28 Base System + AHC + WIC + ACC (all options)
- 29 Descriptions
- 31 Power Supplies
- 31 380/400V Power Supplies
- 31 460/575V Power Supplies
- 32 380/400V Power Supplies
- 32 460/575V Power Supplies
- 33 Interface Control Hub (ICH)
- 33 Specifications
- 33 ICH Mounting Dimensions
- 34 CNC Direct Board
- 35 Combined Gas Control (CGC)
- 35 Specifications
- 36 Connections
- 39 CGC Flow Diagram
- 40 Combined Gas Control Plumbing Schematic
- 41 Combined Gas Control Electrical Schematic
- 42 CGC Mounting Dimensions
- 42 CGC Bottom View
- 43 Troubleshooting
- 43 Replacement Parts
- 44 Power Distribution Box (PDB)
- 44 Specifications
- 44 PDB Mounting Dimensions
- 45 PDB Mounting Plate Dimensions
- 45 PDB Schematic
- 46 Remote Arc Starter (RAS)
- 46 Specifications
- 47 Remote Arc Starter Connections
- 49 RAS Box Mounting Dimensions
- 49 RAS Box Mounting Plate Dimensions
- 50 Air Curtain Control (ACC)
- 50 Specifications
- 51 ACC Mounting Dimensions
- 51 ACC Component Connections
- 52 Water Injection Control (WIC)
- 52 Specifications
- 53 Automatic Height Control (AHC)
- 53 Specifications
- 54 B4 Mounting Dimensions
- 55 Hoses and Cables
- 59 Specifications
- 59 PT-36 Mechanized Plasmarc Cutting Torch
- 60 Package Options Available
- 60 Optional Accessories
- 61 PT-36 Torch Consumable Kits
- 63 Recommended Regulators
- 63 Replacement Parts
- 65 Installation
- 67 Grounding
- 67 Introduction
- 68 Grounding Overview
- 69 Basic Layout
- 70 Elements of a Ground System
- 70 Plasma Current Return Path
- 71 Plasma System Safety Ground
- 74 Rail System Safety Ground
- 75 Earth Ground Rod
- 75 Ground Rod
- 75 Soil Resistivity
- 76 Utility Power Electrical Ground
- 77 Multiple Ground Rods
- 78 Machine Grounding Schematic
- 79 Check upon receipt
- 79 Before Installation
- 79 Placement of Power Supply
- 79 Input Power Connection
- 79 Input Conductors
- 80 Input Connection Procedure
- 81 Output Connection Procedure
- 82 Interface Cables/Connections
- 83 Placement of RAS Box
- 83 Connections on the RAS Box
- 86 Torch Connections
- 87 Connection of Torch to Plasma System
- 87 Connection to the Remote Arc Starter Box
- 88 Mounting Torch to Machine
- 95 Preparing to Cut
- 100 Placement of ICH
- 89 Placement of CGC
- 89 Placement of PDB
- 90 Individual Component Connections
- 91 ACC Component Connections
- 92 Component Placement Example
- 101 Operation
- 103 Interface Control Hub
- 105 ICH Operation
- 105 ICH Connectors
- 106 Display Screens
- 106 Editing a Parameter on the Display
- 109 Setup Descriptions
- 110 Communication Options
- 111 Station Options
- 113 Digital I/O
- 113 Digital Inputs
- 113 Digital Outputs
- 114 Modes of Operation:
- 114 Remote Interface without Serial Communication
- 116 Operation sequence with ESAB supplied plasma lifter:
- 118 Operation sequence with customer supplied plasma lifter:
- 119 Remote Interface with Serial Communication
- 120 Local Interface - Diagnostics Only
- 121 Operation sequence:
- 123 Interface Wiring Descriptions
- 123 Interface Wiring
- 129 Maintenance/Troubleshooting
- 131 ICH Maintenance/Troubleshooting
- 131 Communication Problems
- 131 Digital Input Problems
- 131 Digital Output Problems
- 131 Gas Problems
- 131 Power Supply Problems
- 132 Error Messages on the ICH Display
- 134 Module Errors
- 135 Module Errors
- 136 Process Errors
- 137 Process Errors
- 138 Process Errors
- 139 Process Errors
- 140 Torch Front End Disassembly
- 143 Torch Front End Assembly
- 144 Torch Front End Assembly using the Speedloader
- 145 Torch Front End Disassembly (for Production Thick Plate)
- 148 Torch Front End Assembly (for Production Thick Plate)
- 150 Torch Body Maintenance
- 151 Torch Body Removal and Replacement
- 153 Reduced Consumable Life
- 154 Checking for Coolant Leaks
- 155 Appendix
- 157 ESAB Serial Communication Interface
- 157 Introduction
- 157 System Requirements
- 158 Installation
- 160 Operation
- 171 ICH Serial Communication Protocol
- 171 Commands
- 178 ICH Communication Errors
- 178 ICH Login Sequence
- 179 ICH Communication Error Messages
- 182 ICH Parameter Loading
- 183 Replacement Parts
- 185 General
- 185 Ordering