advertisement
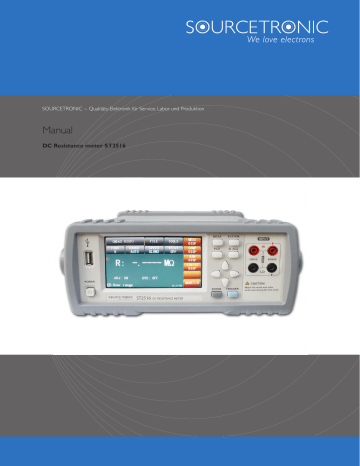
SOURCETRONIC − Qualitäts-Elektronik für Service, Labor und Produktion
Manual
DC Resistance meter ST2516
ST2516 Series Operation Manual
Contents
Contents
ST2516 Series Operation Manual
Compare Mode and SETTINGS of ABS & Percent Error .................................... 13
Edge Mode and Settings of Its Relevant Values ............................................... 16
<TC/∆t SETUP> (
ST2516)................................................................................... 19
ersion (∆t)
................................................................................. 20
Contents
ST2516 Series Operation Manual
Measurement Parameters and Notations ........................................................ 31
Basic Accuracy for Resistance Measurement ................................................... 33
Accuracy for Resistance Tested at Low Current Mode ..................................... 34
Accuracy for Temperature Measurement (Pt500) ........................................... 34
Accuracy for Temperature Measurement (Analog Input) ................................ 34
FUNCtion Subsystem Commands ..................................................................... 39
Contents
ST2516 Series Operation Manual
APERture Subsystem Commands ..................................................................... 43
TEMPerature Subsystem Commands(ST2516) ................................................. 46
COMParator Subsystem Commands ................................................................ 49
Contents
ST2516 Series Operation Manual
Declaration
The descriptions contained in this manual may not cover all information about this instrument.
Introductions to the improvements of the instrument in performance, function, internal structure, outer appearance, accessories, packing material, etc. are subject to change without notice. If you find any inconformity of this manual with our instruments, please contact us for further consultation by the address listed on the cover.
Contents
ST2516 Series Operation Manual
1) Introduction to Instrument, Unpacking and
Installing
Thank you for your purchase and use of our products! This chapter will introduce the basic instrument performance, which is followed by notes of unpacking and installing.
1.1
Introduction to Instrument
ST2516 adopts 32 bits CPU and high density SMD technology. 24 bits, 4.3-inch and touch LCD screen brings ease for your eyes and convenience to your operation. The maximum 0.05% accuracy and minimum 1 µΩ resolution shore up its leading role in testing relay contact resistance, interconnecting resistance, conductor resistance, PCB resistance and welding-hole resistance. Temperature compensation and conversion functions make your tests be free from the effect of the environment temperature. The offset voltage compensation has effectively eliminated the electromotive force of the DUT and its contact potential difference. For the contact influence of the thermoelectricity on DUT, its elimination is achieved; especially when the resistance changes with the temperature greatly, better test results will be achieved. With statistic analysis function, the instrument can make statistic analysis for a large number of test data.
ST2516 series is a powerful test tool for all kinds of resistor design, detection, quality control and production. Automation on production lines can be greatly improved by the realization of ultra-high test speed and the signal output of 3 compare results through HANDLER interface.
With multiple output data display, comparison mode and bin comparator, ST2516 series can meet different test requirements of different resistor manufacturers. The prominent performance makes the test results come up to IEC and IML standard.
1.2
Unpacking
Inspect the shipping container for damage after unpacking it. It is not recommended to power on the instrument in the case of a damage container.
If the contents in the container do not conform to the packing list, notify us or your dealer.
1.3
Power Connection
1) Power supply: 90V-125V, 190V-250V
2) Power supply frequencies: 50Hz and 60Hz
3) Power supply power range: ≤30VA
1
ST2516 Series Operation Manual
4) L (line wire), N (neutral wire) and E (earth ground wire) of the power supply input socket should correspond to the power plug of the instrument.
5) The instrument has been specially designed for decreasing noise jamming caused by the input in AC power terminal, but it is also recommended to use it in the environment of low noise. If noises cannot be avoided, install a power source filter please.
WARNING: To avoid injury to personnel and damage to the instrument resulting from electric shock, do sure that the earth ground wire is safely grounded.
There is selector switch between 110V and 220V voltage besides the power interface on the rear panel. Please switch correctly.
1.4
Fuse
The fuse is a standard configuration, so use the included custom fuse please.
1.5
Environment
1) Do not store or use the instrument where it could be exposed to many dusts, great vibration, direct sunshine and corrosive gas.
2) The instrument should operate under the temperature ranging from 0 humidity of no greater than 80%. For high accuracy, use the instrument in the environment above mentioned.
3) For high accuracy, do not block the left air vent so as to ensure good ventilation.
4) The instrument has been specially designed for decreasing noise jamming caused by the AC power input, but it is also recommended to use it in the environment of low noise. If noise cannot be avoided, install a power filter please.
5) If the instrument will not be used for a long time, please place it in the original or a similar packing box. The environment temperature should be kept in the range of 5 the relative humidity should not be greater than 85%. The box should be located in an airy room where it could be exposed corrosive impurities and direct sunlight.
6) Test leads on the instrument that are connected to DUTs should be kept away from strong electromagnetic fields to avoid interference.
1.6
Use of Test Fixture
Only use the test fixture or cable made by our company, because the use of other test fixtures or cables may result in incorrect measurement results.
In addition, for good contact of DUT and fixture, keep the test fixture or cable and pins of DUT clean.
Connect the test fixture or cable to HI and LO terminals on the instrument front panel. Ensure the color and arrow conformity of the test fixture with that of sockets on panels, thus to avoid abnormal measurement.
2
ST2516 Series Operation Manual
1.7
Warm-up
1) For accurate measurement, the warm-up time should not be less than 30 minutes.
2) Do not turn on or off the instrument frequently. This may cause internal data confusion.
1.8
Other Features
1) Consumption: ≤ 30VA
2) Dimensions (W*H*D): 235mm*105mm*360mm; this dimension is the final packaging size.
3) Weight: Approx. 3.6kg
3
ST2516 Series Operation Manual
2) Introduction to Front and Rear Panels
This chapter will describe the basic operation of ST2516. Before using the instrument, please read this chapter carefully.
2.1
Introduction to Front Panel
Figure 2-1 shows the front panel of ST2516.
1 2 3 4 5 6 7
POWER
MEAS SYSTEM
FILE 0 ADJ
INPUT
HI
DRIVE SENSE
LO
ENTER TRIGGER
! CAUTION:
Match the arrow and color while connecting the test leads.
ST2516
DC RESISTANCE METER
12 11 10 9 8
Figure 2-1 Front Panel
1) USB interface
HOST interface of USB
2) LCD and touch screen
480*272 dot-matrix, 24-bit, 4.3-inch TFT and touch LCD is used for measurement setup and result display.
3) [MEAS]
Press [MEAS] to enter into the MEAS DISP page.
4) [FILE]
Press [FILE] to enter into the page of internal and external File Manage.
5) [SYSTEM]
Press [SYSTEM] to enter into the SYSTEM SETUP page.
6) [0 ADJ]
Press [0 ADJ] to execute correction function.
7) Test terminals (INPUT)
4-terminal test terminal is used to measure DUT by a 4-terminal test cable.
4
ST2516 Series Operation Manual
The color and arrow of the test cable should correspond to that of socket on panel, thus to avoid abnormal measurement.
8) [TRIGGER]
When the trigger mode is set as MANU (manual), pressing this key can trigger the instrument manually.
9) [ENTER]
Press this key to terminate and store input data.
10) Universal Arrow Keys
There are four arrow keys: up, down, left and right arrow keys.
11) Trademark and Model
Show instrument trademark and model.
12) POWER
It is the power switch.
2.2
Introduction to Rear Panel
Figure 2-2 shows the rear panel of ST2516.
1 2 3
RS-232C TEMP.INPUT
RS-232C
DEVICE HANDLER
~
RATING
110V/60Hz
~
220V/50Hz
FUSE
T2AL
T1AL
S/N:
R6-513-00003
7 6 5 4
Figure 2-2 Rear Panel
1) RS232C Serial Interface
It realizes serial communication of the instrument with PC .
2) TEMP.INPUT
There are two kinds of temperature signal input: Pt500 and Analog Input.
3) Fuse socket and Power Socket
Fuse will be placed in this socket to protect the instrument; be used to input AC power.
5
ST2516 Series Operation Manual
4) Nameplate
It shows the instrument model.
5) Ground Terminal
This terminal connects the instrument chassis thus to protect or shield ground connection.
6) HANDLER Interface
Through HANDLER interface, an automatic test system can be conveniently constructed to realize auto test. ST2516 series will output bin comparator result signals and handshake signals by this interface, meanwhile, external trigger signal will also be sent to the instrument by it.
7) USB Interface
PC can remotely control ST2516 series through USB DEVICE.
2.3
Display Zone
ST2516 series adopts 24-bit 4.3-inch LCD touch screen with a resolution of 480*272. The display screen is divided into the following zones, as shown in figure 2-3.
Figure 2-3 Display zone
1.
Page name
This zone shows the current page name.
2.
FILE
In this zone, file manage can be executed such as File Manage, Screen Copy.
3.
TOOLS
This zone can set some short-cut functions.
4.
Soft keys
This zone displays the function menu corresponding to the cursor-located zone.
5.
Result display
This zone displays the measurement result such as resistance and temperature.
6.
Prompt information
6
ST2516 Series Operation Manual
This zone displays all prompt information.
7.
Function zone
This zone is used to change the measurement mode and measurement parameters.
2.4
Introduction to Buttons on Front Panel
2.4.1
[MEAS]
Press <MEAS> to enter into display homepage. Selectable functions in this page are shown as follows:
<MEAS DISP>
<COMP DISP>
<BIN DISP>
<STATIS DISP>
< >
<MORE 1/2>
<MEAS SETUP>
<TC/∆t SETUP> (ST2516)
<BIN SETUP>
<SYSTEM SETUP>
< >
<MORE 2/2>
2.4.2
[SYSTEM]
Press the [SYSTEM] button to enter into the <SYSTEM SETUP> page; the following soft keys will be displayed:
<MEAS DISP>
<COMP DISP>
<BIN DISP>
<STATIS DISP>
< >
<MORE 1/2 >
<MEAS SETUP>
<TC/∆t SETUP> (ST2516)
<BIN SETUP>
<SYSTEM SETUP>
< >
<MORE 2/2 >
7
ST2516 Series Operation Manual
2.5
Simple Operation
Simple operation steps for ST2516:
Use [MEAS], [SYSTEM] or [FILE] or soft keys to enter into the page required to enter. (Refer
to figure 3-1)
Use arrow buttons ( [←] [↑] [→] [↓] ) to move the cursor to desired zone.
When the cursor is moved to a soft key zone, press ENTER to confirm the selection. If it is required to input a number or a file name, use the keyboard to input and press ENTER to finish entry. You can use arrow buttons to select a number or a letter.
ST2516 touch screen operation is much easier. Just use your finger to touch the corresponding function on the screen and then the corresponding work will be done.
NOTE: DO NOT use acute units or nails to touch the screen. Doing so will cause damage to the screen, our company shall not be liable to this case.
2.6
Starting Up
Ensure the power earth (ground) wire is grounded, plug into a 3-wire power socket. Press down the power switch on the bottom left corner of the front panel, the instrument will be started up and a boot screen will be displayed.
Figure 2-4 shows the boot screen of ST2516, indicating product information such as instrument trademark, model and version.
Figure 2-4 ST2516 Boot Screen
If the password protection is enabled, you will be asked to input your password. After inputting your password, press [ENTER] to enter into the main menu page.
NOTE: This series of products have enabled password protection and the default password is
2516. You can reset the password by yourself. Refer to the password function on <SYSTEM
SETUP> page for more details.
8
ST2516 Series Operation Manual
3) Basic Operation
3.1
<MEAS DISP>
Touch the screen or press down [MEAS], the <MEAS DISP> page will be displayed in the screen shown as figure 3-1.
Figure 3-1 Measure Display
The following measurement parameters can be set on this page.
Measurement function ( FUNC R-T )
Resistance range ( RANGE AUTO )
Measurement speed ( FAST SLOW1 )
Measurement temperature ( TC/∆t )
File manage ( FILE )
Other tools ( TOOLS )
Soft keys (used to enter into operation pages)
The following test conditions are displayed in the measurement result/condition display area on this page. These conditions can be set on the tool function page of <MEAS SETUP> or
<MEAS DISP> page.
0 ADJ (ON/OFF):
ON: turn on the function of SHORT zero clearing (self-calibration function)
OFF: turn off the function
OVC (ON/OFF): compensation of the offset voltage, i.e. compensation of the measurement error due to thermoelectromotive force on the DUTs. (ST2516/ST2516A)
3.1.1
Measurement Functions
Measurable parameters on ST2516 are as follows:
9
ST2516 Series Operation Manual
R (Resistance)
R-T (Resistance and temperature)
T (Temperature)
LPR (resistance test at low current mode)
LPR-T (Temperature and resistance test at low current mode)
----------------------------------------------------------------------------------------------------------------------
Note: Settings and modifications of all functions can be taken by the following steps:
1.
Touch the corresponding function zone and then select the desired soft keys.
2.
Use arrow buttons and [ENTER] button to set and modify the corresponding function.
----------------------------------------------------------------------------------------------------------------------
Setting steps for measurement function:
You use buttons or touch the screen to select FUNC , available soft keys will be displayed in the right soft key zone.
R
R-T (ST2516)
T (ST2516)
LPR
LPR-T (ST2516)
3.1.2
Measurement Range
There are two resistance modes: resistance measurement mode and resistance measurement at low voltage mode. Measure and display two types of parameters: resistance parameters and temperature parameters.
ST2516 has 9 DC resistance ranges: 20mΩ, 200mΩ, 2Ω, 20Ω, 200 Ω , 2kΩ, 20kΩ, 2 00kΩ, 2 MΩ
ST2516A has 7 DC resistance ranges: 200mΩ , 2Ω , 20Ω , 200Ω , 2kΩ , 20kΩ , 200k Ω
ST2516B has 7 DC resistance ranges: 20mΩ , 200mΩ , 2Ω , 20Ω , 200Ω , 2kΩ , 20kΩ
ST2516, ST2516A, ST2516B has 4 DC low voltage resistance ranges: 2Ω, 20Ω, 200Ω, 2KΩ
ST2516 The testing range of temperature (PT500): -10
The testing range of temperature (Analog): 0 to 2V
℃ to 99.9℃.
Operation steps for setting measurement ranges:
1) Touch the range zone, the following soft keys will be displayed.
AUTO Set the range mode as AUTO.
HOLD Switch the range mode from AUTO to HOLD. When the range mode is set as HOLD, the range will be locked at the current measurement range which is displayed in the RANG
zone.
↑ (+) Increase the range.
↓ (-) Decrease the range.
2) Touch the corresponding soft key to select the required range.
10
ST2516 Series Operation Manual
3.1.3
Measurement Speed
ST2516 displays the measurement result as a 5-digit number in the decimal point floating mode.
The measurement result of the speed is shown as a 4-digit number with one digit after the decimal point.
1) Touch the speed zone, the following soft keys will be displayed.
FAST
MED
SLOW1
SLOW2
2) Use above soft keys to modify the speed.
3.1.4
File Manage
1 ) Touch FILE , the following soft keys will be displayed.
File Manage: Touch this key to enter into the file operation page.
Screen Copy : Touch this key to capture the current screen and save it to a U disk in image format. Before a U disk is inserted, the save function will be disabled.
Save Data OFF: Touch this key, this key will turn to <Save Data ON> and each measurement result will be continuously saved to the .CSV file in U disk. Before a U disk is inserted, the save function will be disabled. Press the key again, this key will turn to <Save Data OFF> and the measurement result will not be saved. When switching between ON and OFF once, a new .CSV file will be created in a U disk. The measurement data can be analyzed by opening the file through the computer.
2) As for File Manage, please refer to 4.2 for details.
3.1.5
Tools
Operation steps for setting tools:
Touch TOOLS , the following soft keys will be displayed in the soft key zone.
Display (ON/OFF): Display the measurement result or not. ON is to display, OFF is not to display.
0 ADJ (ON/OFF): OFF is to turn off the function of short correction, while ON is to turn on
the function of short correction.
0 ADJ: Execute short correction. In this process, please ensure the test terminals have been correctly shorted. Only by doing this, unexpected measurement errors could be avoided.
NOTE:
SPEED : In SLOW2, SLOW1, MED or FAST mode, the measurement result is a 5-digit number.
SAVE : Once SAVE DATA OFF is selected, you must press SAVE DATA ON to terminate or the saved data will be lost.
SHORT : When this key is used to take short correction, the test fixture should be correctly
11
ST2516 Series Operation Manual connected. If not, the deducted data will be wrong, and further it will cause result errors. The correct connection is shown as the following figure.
3.2
<COMP DISP>
Touch <MEAS DISP> or press [MEAS] to select the COMP DISP soft key to enter into the <COMP
DISP> page shown as figure 3-2.
<COMP DISP>
COMP
OFF
COMP MODE
ABS
FILE
HIGH
225.000
R: 499.76
COMP: HI
Ω
TOT:0
HI :0
IN :0
LO :0
TOOLS
LOW
63.0000
MEAS
DISP
COMP
DISP
BIN
DISP
STATICS
DISP
MORE 1/2
11:36:54
Figure 3-2
The following parameters can be set on this page:
FILE
TOOLS
COMP ON/OFF
COMP MODE
NOM (nominal value)
Low limit (%)
12
ST2516 Series Operation Manual
3.2.1
File Manage
1) Touch FILE , the following soft keys will be displayed:
File manage: Touch this soft key to enter into the file manage page.
Screen copy: Touch this key to save the current screen page to a U disk. If no U disk is found, this function will be disabled.
Save Data OFF: Touch this key, this key will turn to <Save Data ON> and each measurement result will be continuously saved to the .CSV file in U disk. Before a U disk is inserted, the save function will be disabled. Press the key again, this key will turn to <Save Data OFF> and the measurement result will not be saved. When switching between ON and OFF once, a new .CSV file will be created in a U disk. The measurement data can be analyzed by opening the file through the computer.
2) Refer to 4.2 for more details about FILE MANAGE .
3.2.2
Tools
Touch <TOOLS> , the following soft keys will be displayed.
DISP (ON/OFF): ON is to display the measurement result and OFF is not to.
BEEP (NG/GD/OFF): NG: The beeper will sound when the measurement result is not
consistent with the setting value. GD: The beep will sound when the measurement result conforms to the setting value. OFF: Turn off the beeper.
COUNT (ON/OFF): ON : Start count; OFF: Stop count.
COUNT CLEAR : Clear the count numbers of TOT, IN, HI and LO and start count from zero.
DISP MODE NORMAL: press the key, DISP Mode DEV will be displayed. The value of deviation △ will be displayed in the main display interface and the display range is
-99.9~999.9%. Press the key again and DISP MODE NORMAL will be displayed.
NOTE: △ ={( measured resistance value - nominal resistance)/ nominal resistance} x 100%
3.2.3
COMP (ON/OFF)
COMP (ON/OFF): ON indicates the compare function has been turned on. Only when the compare function is in ON mode, count and beep function can be enabled.
OFF is to turn off this function.
3.2.4
Compare Mode and SETTINGS of ABS & Percent Error
You can set the compare mode and concerned values by touching the screen or pressing keyboard. There are two compare modes: ABS and %.
Compare modes:
1) ABS (high and low limits)
In this mode, you can set low and high limits. The instrument will take comparison between the
13
ST2516 Series Operation Manual tested values and the set ones so as to judge the DUT is HI or LO or IN. The set upper limit value should be equal or larger than the lower limit value.
2) % (percent error)
In this mode, you can set the nominal value and the percent error. If you set the nominal value as
100 and percent as 10, the set value should be 100±10%. The instrument will take comparison between the tested values and the set ones so as to judge the DUT is HI or LO or IN. The nominal value is the base value in bias display mode.
3.3
<BIN DISP>
Touch <MEAS DISP> or press [MEAS]. Then select the soft key BIN DISP to enter into <BIN DISP> shown as figure 3-3.
BIN
ON
<BIN DISP>
BIN BEEP
NG
FILE
NG COLOR
RED
R: 479.67
Ω
BIN:
TOOLS
GD COLOR
GREEN
MEAS
DISP
COMP
DISP
BIN
DISP
STATIS
DISP
11:36:54
MORE 1/2
Figure 3-3 Bin display
The following parameters can be set on <BIN DISP>.
FILE
1) File Manage: Touch this key to enter into the file manage page.
2) Screen Copy: Touch this key to save the current screen page to an external U disk. If no U disk is found, this function will be disabled.
3) Save Data OFF: Touch this key, this key will turn to <Save Data ON> and each measurement result will be continuously saved to the .CSV file in U disk. Before a U disk is inserted, the save function will be disabled. Press the key again, this key will turn to <Save Data OFF> and the measurement result will not be saved. When switching between ON and OFF once, a
new .CSV file will be created in a U disk. The measurement data can be analyzed by opening the file through the computer.
TOOLS
DISP (ON/OFF): ON is to display the result while OFF is not to.
BIN
BIN ON/OFF: ON is to turn on bin compare display while OFF is to turn off.
BIN BEEP ON/OFF
OFF is to turn off the bin beep function.
14
ST2516 Series Operation Manual
NG: Bin beep function is ON. When one of the bin comparator results is not consistent with the bin setting, the beep will sound.
GD: Bin beep function is ON. When the bin comparator results are consistent with bin setting, the beep will sound.
NG Color
OFF : no display. GREY : When the corresponding bin comparator result is different from the bin setting, the corresponding bin will be displayed in grey; RED : When the corresponding bin comparator result is different from the bin setting, the corresponding bin will be displayed in red; GREEN : When the corresponding bin comparator result is different from the bin setting, the corresponding bin will be displayed in green.
GD Color
OFF : When the corresponding bin comparator result conforms to the bin setting, there is no display. GREY : When the corresponding bin comparator result conforms to the bin setting, the corresponding bin will be displayed in grey; RED : When the corresponding bin comparator result conforms to the bin setting, the corresponding bin will be displayed in red;
GREEN : When the corresponding bin comparator result conforms to the bin setting, the corresponding bin will be displayed in green.
---------------------------------------------------------------------------------------------------------
NOTE: NG is the abbreviation of not good while GD is the abbreviation of good.
---------------------------------------------------------------------------------------------------------
3.4
STATIS DISP
Touch the main menu or press [MEAS]. And then touch the soft key STATIS DISP to enter into the
<STATIS DISP> page shown as figure 3-4.
Figure 3-4 Statistic display
The function of this page is to count measurement data. It is workable to analyze the average
15
ST2516 Series Operation Manual value of results for multiple measurements, the PASS/FAIL rate and some engineering coefficients.
Details are as below.
3.4.1
Edge Mode and Settings of Its Relevant Values
Touch this key, two modes is available: ABS (high and low limits) and % (percent error mode).
When ABS is selected, the adjacent two items on the same line will be high and low limits. Touch them to set the values. When % is selected, the two items on the same line will be nominal value and percent. Touch them to set the values.
3.4.2
Status ON/OFF
Status ON/OFF:
(1) When ON is selected, except the trigger button, no other keys and buttons could be enabled.
The instrument makes a statistic at every trigger.
(2) When OFF is selected, the statistic function will be turned off and other keys and buttons is available.
3.4.3
Parameters of Statistic Analysis
1)
2)
3)
4)
X
: Average value. Corresponding formula: x =
∑ n x
σ
: Population Standard Deviation. Corresponding formula:
σ
=
∑ x 2 − nx
2 n
( =
σ
n ) s
: Sample Standard Deviation. Corresponding formula: s =
∑ x 2 − nx
2 n − 1
C p : Process Capability Index (Dispersion). Corresponding formula:
C
p
=
|
( =
σ
n − 1 )
6
s
|
5) : Process Capability Index (Deviation). Corresponding formula:
=
|
− −
6
s
+ −
2 |
---------------------------------------------------------------------------------------------------------------------------------
NOTE: Explanations for variables in formulas from 1) to 5): n
: The total measurement times that a sample is used to make statistic analysis, which corresponds to the value of TIMES. x
: Measurement results of each sample measurement. The data are saved in the
16
ST2516 Series Operation Manual instrument buffer memory.
Hi
: Upper limit value, used to be compared, corresponds to the value of UPPER limit.
Lo
: Lower limit value, used to be compared, corresponds to the value of LOWER limit.
When
C p , > 1.33, the working capacity is ideal.
When 1.33
≥
C p , > 1.00 , the working capacity is qualified.
When 1.00
≥
C p ,
C K
, the working capacity is insufficient.
---------------------------------------------------------------------------------------------------------------------------------
6) Hi (num): Be used to add up times that the measurement result exceeds the upper limit value.
7) Lo (num): Be used to add up times that the measurement result is less than the lower limit value.
8) In (num): Be used to add up times that the measurement result passes.
9) Max: Be used to display the maximum measurement result among all measurement results.
10) MaxIndex: Be used to display the test serial corresponding to the maximum measurement result.
11) Min: Be used to display the minimum measurement result among all measurement results.
12) MinIndex: Be used to display the test serial corresponding to the minimum measurement result.
3.4.4
TOOLS
CLEAR: Clear all parameters obtained from last statistic.
TRIGGER: Trigger the instrument to execute a measurement.
3.4.5
FILE
1) File Manage: Touch this key to enter into the file manage page.
2) Screen copy: Touch this key to save the current screen page to an external U disk. If no U disk is found, this function will be disabled.
3) Save Data OFF: Touch this key, this key will turn to <Save Data ON> and each measurement result will be continuously saved to the .CSV file in U disk. Before a U disk is inserted, the save function will be disabled. Press the key again, this key will turn to <Save Data OFF> and the measurement result will not be saved. When switching between ON and OFF once, a new .CSV file will be created in a U disk. The measurement data can be analyzed by opening the file through the computer.
NOTE: Before switching from statistics interface to other interface, please firstly set the statistics
17
ST2516 Series Operation Manual status as OFF.
3.5
<MEAS SETUP>
Touch the main menu. And then touch the soft key MEAS SETUP to enter into the MEAS SETUP page shown as figure 3-5.
<MEAS SETUP>
FUNC
R-T
TRIG DELAY
AUTO
0 ADJ
ON
RANGE
AUTO
AVERAGE
56
OVC
OFF
FILE
TRIG
INT
SPEED
MEAS
SETUP
TC/ Δ t
SETUP
BIN
SETUP
SYSTEM
SETUP
11:36:54
MORE 2/2
Figure 3-5 Measurement Setup
On this page, the following parameter can set:
FUNC R-T : Touch this key to select the required parameter.
RANGE AUTO : Touch this key, the following soft keys will be displayed: AUTO (automatically set the resistance range), HOLD (lock the resistance range), ↑ (increase the range), ↓
(decrease the range). Touch the corresponding soft key to set the range mode.
TRIG INT : Touch this key, the following soft keys will be displayed in the soft key zone: INT
(auto measurement mode), MAN (manual measurement mode), EXT (external trigger mode),
BUS (BUS trigger mode).
TRIG DELAY : Touch this key, the following soft keys will be displayed: AUTO , MANUAL ,
INPUT .
NOTE : The setting of manual measurement delay time is determined by inputting. Range:
0ms—9.99ms. If the delay time is set as 0ms, the detection for wrong measurement cannot be executed. Therefore, it is recommended to set the delay time being more than 1ms.
AVERAGE : Touch this key, a numeric keyboard will pop up. Input the average number ranging from 1 to 255. The larger the average number is set, the better the accuracy will be obtained but the longer time it will cost to display the result.
SPEED MED : This mode is usually applied in 4-terminal measurement. Touch this key,
SLOW1, SLOW2, FAST and MED will be selectable. In SLOW1 and SLOW2 mode, the noise is lower; in FAST mode, noise suppression is needed. FAST is high speed measurement.
0 ADJ: Touch this key to select ON or OFF . ON is to turn on the short correction function while OFF is to turn off.
OVC: Touch this key to select ON or OFF . ON is to turn on the compensation voltage while
OFF is to turn off.
18
ST2516 Series Operation Manual
ST2516B has no OVC function.
3.6
<TC/∆t SETUP> (ST2516)
Touch the main menu. And then touch the soft key TC/∆t SETUP to enter into the TC/∆t setup page shown as figure 3-6.
<
TC/
FUNC
R t0( ℃ )
20.0
t1( ℃ )
23.0
T1( ℃ )
0.0
Δ T SETUP>
TC/
Δ
t
OFF
α
t0 ( ppm)
3390 k
236.0
V2(v)
1.00
FILE
T.SENS
Pt
R1(
Ω
)
100.00
V1(v)
0.00
T2( ℃ )
500.0
MEAS
SETUP
TC/
Δ t
SETUP
BIN
SETUP
SYSTEM
SETUP
11:36:54
MORE 2/2
Figure 36 TC/∆t setup
3.6.1
Temperature Correction (TC)
Temperature correction (TC) : By this function, the resistance tested under the current environment temperature will be converted to a resistance value under the user-set environment temperature. For instance, a resistor is tested as 100Ω under 20 ℃ . If user sets the temperature as 10 ℃ , after correction, the value will be disp layed as 96.22Ω. This is realized by formulary conversion.
Formula: Rt=Rt0*{1+ ɑt0*(t -t0)}
Rt Resistance measured under the current environment temperature
Rt0 Resistance after correction t0 Preset temperature t Current environment temperature ɑ t0
Temperature coefficient of the material
For example: A resistor is measured as 100Ω under 20
3930ppm), the resistance under 10
𝑹𝒕𝟎
=
𝐑𝐭
𝟏+
𝛂 𝐭𝟎
∗
(
𝐭−𝐭𝟎
)
=
℃ will be 96.22Ω.
100
1+
(
3930 x 10
−6 )
x
(
20−10
)
=96.22Ω
19
ST2516 Series Operation Manual
NOTE: Before measurement, it is necessary to warm up the instrument and the probe for about half an hour. The temperature sensor should be placed to the DUT as close as possible but cannot contact it. After the displayed result comes to be stable, you can read or record the result.
3.6.2 Temperature conversion (∆t)
Temperature conversion (∆t) : Basically, resistors have heat effect. Temperature conversion represents the temperature difference between the resistor and the environment.
Formula:
R
R
2 (
+ − +
)
∆ t is the temperature increment. t1 is the temperature at the start of resistance measurement. ta is the environment temperature.
R1 is the resistance at the start of contact.
R2 is the resistance after the display is stable.
K is the variance ration of the environment temperature coefficient when the conductor is at
0 ℃ .
For example
When R1 is 2 00mΩ, t1 is 20 ℃ and k is 235.
Δ t =
𝐑𝟐
𝐑𝟏
(k + t1) –(k + ta)=
𝟐𝟏𝟎 𝐱𝟏𝟎 −𝟑
𝟐𝟎𝟎 𝐱𝟏𝟎 −𝟑
(235 + 20) –(235+25)=7.75
℃
The temperature after the resistance is stable is calculated as the following formula: 𝑡
𝑅
= ta +Δt = 25 +7.75 = 32.75
℃
Where, k =
1
α t0
- t0, if α t0
= 3930ppm, k is 234.5
NOTE: Conductivity and temperature coefficient of metal and alloy
Metallic material
Annealed copper
Metal
[%]
Copper>99.9
Material density
(x 10 3 )
[kg/ m 3 ]
8.89
Conductivity
1.00 to 1.02
Hard-drawn copper Copper>99.9 8.89 0.96 to 0.98
0.85 to 0.88 Cadmium copper Cadmium: 0.7 to
1.2
8.94
Silver copper Silver: 0.03 to 0.1 8.89
Chromium copper Chromium: 0.4 to 8.89
0.8
0.96 to 0.98
0.40 to 0.50
0.80 to 0.85
3930
20
30
Temperature coefficient
(20 ℃ )
[ppm]
3810 to 3970
3370 to 3850
3340 to 3460
20
ST2516 Series Operation Manual
Anti-corrosion alloy Nickel: 2.5 to 4.0
Silicon: 0.5 to 1.0
Soft aluminum
Hard-drawn
Aluminum>99.5
Aluminum>99.5 aluminum
Aluminum alloy Silicon: 0.4 to 0.6
Magnesium: 0.4 to
0.5
Aluminum: 99.2 to
98.9
---
2.7
2.7
---
0.25 to 0.45
0.63 to 0.64
0.60 to 0.62
0.50 to 0.55
980 to 1770
42
40
36
NOTE: Calculating the conductivity and the temperature coefficient of the copper wire:
Diameter [mm]
0.01 to 0.26
0.26 to 0.50
0.50 to 2.00
2.00 to 8.00
(Conductivity)
0.98
0.993
1.00
1.00 copper (conductivity)
0.93
0.94
0.96
0.97
Hard-drawn copper
(Conductivity)
---
0.96
0.96
0.97
(
Temperature coefficient ( α t
) varies with environment temperature and material conductivity. It is supposed that the temperature coefficient of a material at 20 , its temperature coefficient
α
α ct ct
) at t
=
1
α 20
1 x c
+ ( t−20 )
℃ will be as the following expression:
3.6.3
Types of Temperature Sensor
There are two temperature input types: Pt and Analog Input.
PT500
Touch the T.SENS
soft key to select the temperature input type. Select PT and the input type of the temperature is platinum resistor temperature sensor. At this time, standard configuration of
“PT500 temperature sensor” should be inserted in the temperature measurement input terminal.
Analog Input
Touch the T.SENS
soft key to select the temperature input type. AnLG_In is analog input(the input voltage is 0-2V) and the corresponding forma is :
T2−T1
V2−V1
*(Input Voltage) +
T1V2 – T2V1
V2−V1
-----------------------------------------------------------------------------------------------------------------------------
21
ST2516 Series Operation Manual
NOTE: V1 and V2 range from 00.00V to 02.00V while T1 and T2 range from -99.9
℃ to 999.9
℃ .
3.6.4
Parameter Setting
t0: Touch this key, the numeric keyboard will pop up and you can input the reference temperature (-10-99.9
℃
α t0
: Touch this key, the numeric keyboard will pop up and you can input the reference temperature (-999999-999999).
R1: Touch this key, the numeric keyboard will pop up and input the set resistance value
(0-2M Ω ). t1: Touch this key, the numeric keyboard will pop up and input the set temperature value
(-10-99.9
℃ ). k: Touch this key, a numeric keyboard will pop up and you can input the reciprocal of the temperature coefficient (0-9999).
V1: Touch this key, a numeric keyboard will pop up and you can input the set voltage value
(0-2V).
T1: Touch this key, a numeric keyboard will pop up and you can input the set temperature value( 100-999.9
℃ ).
V2: Touch this key, a numeric keyboard will pop up and you can input the set voltage value
(0-2V).
T2: Touch this key, a numeric keyboard will pop up and you can input the set temperature value ( 100-999.9
℃ ).
T C/∆t: Touch this key, OFF , TC and ∆ t will be displayed in the soft key zone. Touch the corresponding key to choose.
T.SENS: Touch this key, Pt and AnaLG_In will be displayed in the soft key zone. Touch the corresponding key to choose.
3.6.5
File
1) File manage: Touch this key to enter into the file manage page.
2) Screen copy: Touch this key to save the screen page to an external U disk. If no U disk is found, the function will be disabled.
3.7
<BIN SETUP>
Touch the main menu. And then touch MORE 1/2 to select BIN SETUP , and the corresponding Bin
Setup page will be displayed as figure 3-7:
22
ST2516 Series Operation Manual
Figure 3-7 Bin Setup
On this page you can set all parameters concerned with the bin comparator. There are 3 groups of parameters (high and low limits, nominal value, %) can be set.
The following parameters can be set on this page:
BIN : Touch 1, 2, 3 below the bin, a Delete soft key will be displayed which can be used to
clear the high and low limits, nominal value, % of the bin.
STATE : Display the bin state as ON or OFF. When ON is set, the corresponding bin in the display zone will be shown as lighted circle. When OFF is set, the corresponding bin is shown as a horizontal line.
TOOLS: Touch TOOLS, the following soft keys will be displayed: MODE, BEEP and CLEAR.
Touch MODE to select ABS (Absolute value error mode) or % (percentage error) and correspondingly high and low limits, nominal value, %. Press the touch key of the corresponding bin, a numeric keyboard will pop up and you can set the relevant parameters of the values. There are three bin beep modes: OFF, GD and NG. CLEAR can clear the setting parameters of all the three bins.
23
ST2516 Series Operation Manual
4) System Setup and File Manage
4.1
System Setup
Entering the system setup page, you can press [SYSTEM] or touch MORE2/2 on any display page to select system setup function as shown in figure 4-1.
<SYSTEM SETUP>
Touch Tone
OFF
Bus Mode
RS232C
Handler VCC
INT
Language
Chinese
Baud Rate
9600
LCD Style
DEFAULT
FILE TOOLS
Password
OFF
AC Freq
50Hz
MEAS
SETUP
TC/ Δ t
SETUP
BIN
SETUP
SYSTEM
SETUP
Time
: 13-02-08 09:21:19
MORE 2/2
Figure 4-1 System Setup
On this page, the following functions can be set: TouchTone, Language, Password, Bus Mode,
Baud Rate, AC Freq, Handler VCC, LCD Style and Time.
4.1.1
TouchTone
The function is used to control the touch tone.
Steps for setting the touch tone
Touch TouchTone , the following soft keys will be displayed:
ON
Touch this key to turn on the touch tone.
OFF
Touch this key to turn off the touch tone.
You can touch soft keys to set corresponding functions.
4.1.2
Language
The function is used to set the language.
Steps for setting the language
Touch Language , the following soft keys will be displayed:
English
24
ST2516 Series Operation Manual
Touch this soft key to set the language as English.
Chinese
Touch this soft key to set the language as Chinese.
You can touch soft keys to set corresponding functions.
4.1.3
Password
The function is used to set the password.
Steps for setting the password
Touch Password , the following soft keys will be displayed:
OFF
Touch this key to turn off the password protection function. This function would be disabled only when the preset password is correctly input.
LOCK SYSTEM
Touch this key to enable the password function. Please input the password which will be required to be input when opening a file or starting up the instrument.
LOCK FILE
It is necessary to input the password if this function is enabled.
MODIFY
Touch this key to modify the password.
Steps for modify the password:
Touch MODIFY , a numeric keyboard will pop up then you should input the original password and press [ENTER] to confirm. Input the new password when the numeric keyboard is shown once again and press [ENTER] to confirm. Then the numeric keyboard will be displayed for the third time, please input the new password. Press [ENTER] to finish the password modification.
NOTE: The default password is 2516.
4.1.4
Bus Mode
Touch this zone to select the communication interface.
Steps for setting the bus mode
1) Touch Bus Mode , the following soft keys will be displayed:
RS232C
USBTMC
USBVCOM
2) Touch RS232C to select the RS232C interface.
3) Touch USBTMC to select the USBTMC interface. The instrument communicates with PC through the USB interface on the rear panel.
4) Touch USBVCOM to select the USBVCOM interface. The instrument communicates with PC through the USB interface on the rear panel.
25
ST2516 Series Operation Manual
4.1.5
Baud Rate
Touch this key, the following six baud rates is selectable:
9600
19200
28800
38400
96000
115200
4.1.6
AC Freq
ST2516 supplies two power supply frequencies: 50Hz and 60Hz . Please select the correct frequency so as to eliminate the influence of the power noise on the instrument.
4.1.7
Handler VCC
Press the Handler VCC, the following six baud rates is selectable:
EXT
INT
Press EXT, external power supply is selected.
Press INT, internal power supply is selected.
4.1.8
LCD Style
Press LCD Style, the following six baud rates is selectable:
DEFAULT
CLASSIC
Press DEFAULT, default style interface is selected.
Press CLASSIC, classic style interface is selected.
4.1.9
Setting Time and Date
Set the time.
For example: 9 o’clock 21 minute and 19 second a.m. on February 8, 2013 will be shown as
13-02-08 09:21:19.
Operations are as follows: Touch the time zone to be modified, the following items will be displayed.
↑↑ ( + + )
Touch this key, the time will increase rapidly by 5.
↑ ( + )
26
ST2516 Series Operation Manual
Touch this key, the time will increase by 1.
↓ ( )
Touch this key, the instrument will decrease by 1.
↓↓ ( - )
Touch this key, the instrument will decrease rapidly by 5.
<<
Touch this key, the cursor under the time will move left.
>>
Touch this key, the cursor under the time will move right.
4.2
<File Manage>
ST2516 series can save parameters that are set by user to the internal non-volatile memory in the file format. User can load the file to use these parameters instead of resetting.
This section will introduce the information about the function of Save/Recall.
Notation Explanation:
E: Abbreviation of External, representing external memory, like U disk.
I: Abbreviation of Internal, representing internal memory, like internal Flash of ST2516.
4.2.1
Introduction to Save/Recall
By the function of save/recall, user can save measurement results and configuration information to ST2516 internal Flash or external U disk; meanwhile user can recall data from ST2516 internal
Flash or external U disk.
Introduction to Methods and Applications of Save
The table below shows the applicable save methods and applications: save method type file format recall application
(internal Flash)
(external U disk) data save (external U disk) screen save (external
U disk)
Yes
Yes
Save the current configuration to internal Flash.
Save the current configuration to a U disk.
*.CSV No Save measurement results to a U disk.
*.gif No Save the screen information to a U disk.
Table 4-1 Methods and Applications of Save
4.2.2
Structure of File Folder/File in a U Disk
Before saving data to a U disk, you are recommended to save it into a file and folder that have existed in the memory as shown in table 4-2. If you want to save the configuration file into a file folder in PC,
27
ST2516 Series Operation Manual you should enter into the folder on the instrument and then take relative file operations.
Folder
CSV
STA
IMAGE
Maximum Amount of File
999
999
20
Description
Including measurement result, like *.CSV file.
Including configuration data, like *.STA file.
Including screen information, like *.gif file.
Table 4-2 Folder in U disk
----------------------------------------------------------------------------------------------------------------------------
NOTE: CSV and STA folders might be automatically generated when a U disk is connected.
----------------------------------------------------------------------------------------------------------------------------
Structure of Folder/File in a U disk is shown in figure 4-2.
E:(U disk)
\STA
2516001.STA
2516002.STA
2516003.STA
2516999.STA
\CSV
2516001.CSV
2516002.CSV
2516003.CSV
2516999.CSV
\IMAGE
2516001.GIF
2516002.GIF
2516003.GIF
2516999.GIF
……
Figure 4-2 file structure in a U disk
When using a U disk on ST2516, you should pay special attention to the following points:
1. Use a U disk with the USB2.0 interface.
2. The U disk file system should be FAT16 or FAT32. FAT16 or FAT32 standard should be used to format the U disk. If the U disk memory exceeds 512M, it is recommended to use FAT32 standard to format the disk.
3. Before a U disk is connected to ST2516, you are recommended to save the data on it and
Sourcetronic will not be liable for the data loss.
4. In order to rapidly save the instrument data to a U disk, it is not recommended to store too many files or folders.
28
ST2516 Series Operation Manual
Operation Procedures
Touch FILE in any page and select File Manage to enter into the internal file page (or directly press the FILE button on the front panel) as shown in below figure.
Touch [Inter File] and [External File] to respectively display files stored in the internal FLASH and the external U disk. Touch [Exit] to exit the file manage page.
Figure 4-3 External file page
Figure 4-4 External file page
Four files’ information will be displayed in the internal file page or the external file page, including file names and time of being saved.
Operations of the internal file and the external file are similar. Take internal file operations as an example to describe the specific procedures of file operations.
29
ST2516 Series Operation Manual
Operations on file are as follows:
Touch the file name to be edited (If the file name does not exist in the current page, you can touch [Page 1] and select [ Previous Page ] and [ Next Page ] to toggle between file pages, and then select the desired file.), the following items will be displayed.
Load
Touch this key, if the file name that the cursor locates is not empty, [YES] and [NO] will be displayed in the soft key zone. When [YES] is selected, the instrument will load the
setup data in the file; when [NO] is selected, the current operation will be cancelled.
Save
Touch this key, [YES] and [NO] will be displayed in the soft key zone. When [NO] is selected, the current operation of save file will be cancelled; when [YES] is selected, the numerical keyboard will pop up and then you can input the file name and press [ENTER]
to finish inputting. Thus the current settings in all pages will be saved to the file. (NOTE:
When storing a file, if the inputting file number has already existed, the save operation will overwrite the original file.)
Delete
Touch “Delete”, if “YES” is selected, the instrument will delete the file that the cursor locates.
Copy to E :
Touch “Copy to E”. The instrument will copy the file the cursor locates or the selected file to a U disk.
Select
Touch “Select”, the file the cursor locates will be selected. ST2516 can simultaneously copy several files to a U disk.
Touch “Select” once again, the selected file will be cancelled from selection.
Save Measurement Results
In the “MEAS DISP” page, touch “FILE” and select “Start Save” to save measurement results to a
U disk. Touch “Stop Save”, the instrument will stop saving measurement results.
Save Screen Information:
Touch “FILE” and select “Screen Save” to store the current screen information to a U disk.
Operations of External File and Folder
Operations of external file are similar to that of internal file.
30
ST2516 Series Operation Manual
5) Performance Index
5.1
Measurement Function
5.1.1
Measurement Parameters and Notations
R : Resistance T: Temperature
LPR: Low current mode
5.1.2
Measurement Groups
Five measurement groups are available:
ST2516: R, R-T, T, LPR, LPR-T
ST2516A, ST2516B: R, LPR
5.1.3
Range
Range Mode: AUTO, MANU (HOLD, UP, DOWN)
5.1.4
Trigger
Internal, Manual, External, BUS
Internal: Continuously test a DUT and then output and display the result.
Manual: Press the “TRIGGER” button on the panel, the instrument will test a DUT once and display the result. This mode keeps in waiting mode when it is not used.
External: Test a DUT once and display the result when the instrument receives an external “start up” signal from the footswitch of HANDLER interface on the rear panel.
BUS: The measurement of the instrument will be triggered through the communication interface.
5.1.5
Mode of Test Terminal
4-terminal measurement mode
DRIVE HI : Current-drive high terminal DRIVE LO: Current-drive low terminal
SENSE HI : Voltage-sense high terminal SENSE LO : Voltage-sense low terminal
31
ST2516 Series Operation Manual
5.1.6
Resistance Measurement Time
When OVC is OFF, measurement time= 5ms +t1 (50 Hz) / 5ms+t1 (60 Hz) FAST
20ms+t1 (50 Hz) / 16.6ms+t1 (60 Hz) MED
110ms+t1 (50 Hz) / 110ms+t1 (60 Hz) SLOW
450ms +t1 (50 Hz) / 450ms+t1 (60 Hz) SLOW
When OVC is OFF, measurement time= 10 ms + t+t1 (50 Hz) / 10ms + t+t1 (60 Hz) FAST
40ms + t+t1 (50 Hz) / 33ms + t+t1 (60 Hz) MED
220ms + 9* t+t1 (50 Hz) / 220 ms + 11* t+t1 (60 Hz) SLOW
900ms + 39*t+t1 (50 Hz) /900 ms + 47*t+t1 (60 Hz) SLOW
NOTE: t is the measurement waiting time, t1 is the data processing time, approximately is 5ms.
More detailed information about time parameters, please refer to Chapter 7 “Handler Interface”.
5.1.7
Average
Range from 1 to 255, programmable: this value reflects the measurement times from measuring resistance to measuring display.
5.2
Test Signal
5.2.1
Current range
ST2516: Current range: 1μA -- 1A
ST2516A: Current range: 10 μA – 100mA
ST2516B: Current range: 100 μA -- 1A
5.2.2
Output Voltage of Open Circuit
Output voltage of open circuit: 0.7V, 3V, 40mV
5.2.3
Maximum Display Range
Parameter
R
LPR
T
Measurement Display Range
1u Ω –- 2 MΩ
0.1m
Ω —2.1k
Ω
-99.9
℃ -- 999.9
℃
32
ST2516 Series Operation Manual
5.3
Measurement Accuracy
Checking the measurement accuracy should be taken under the following circumstances: a . Warm-up time should be more than 30 minutes. b . Correctly short the test cables, turn 0 ADJ to ON and perform short calibration by pressing the touch key or 0 ADJ panel.
The correct short of the test cable is as follows:
5.3.1
Basic Accuracy for Resistance Measurement
ST2516
Range
Current
OCV
Resolution
Accuracy
Temperature coefficient
ST2516A
Range
Current
OCV
Resolution
Accuracy
Temperature coefficient
ST2516B
Range
Current
OCV
20mΩ
1A
1µΩ
200mΩ 2Ω 20Ω 200Ω 2kΩ 20kΩ 200k
Ω
100mA 100mA 10mA 1mA 100µA 100µA 10µA
0.7V 3V
10µΩ 100µΩ 1mΩ 10mΩ 100mΩ 1Ω 10Ω
0.1%+3 0.05%+2 0.05%+2
300ppm 100ppm
200mΩ
100mA 100mA 10mA 1mA 100µA 100µA 10µA
0.7V 3V
10µΩ 100µΩ 1mΩ 10mΩ 100mΩ 1Ω
300ppm
20mΩ
1A
2Ω
200mΩ
100mA 100mA 10mA
0.7V
20Ω 200Ω
2Ω
0.05%+2
20Ω
2kΩ
100ppm
200Ω
1mA
3V
20kΩ 200kΩ
2kΩ
100µA
10Ω
20kΩ
100µA
33
2MΩ
1µA
100Ω
0.2%+2
Resolution
Accuracy
Temperature coefficient
ST2516 Series Operation Manual
1µΩ 10µΩ 100µΩ 1mΩ 10mΩ 100mΩ
0.1%+3 0.1%+2
300ppm 100ppm
1Ω
5.3.2
Accuracy for Resistance Tested at Low Current Mode
ST2516, ST2516A, ST2516B
Range 2Ω
Current
OCV
10mA
Resolution
Accuracy
100µΩ
Temperature coefficient
20Ω
1mA
40mV
1mΩ
0.2%+5
200ppm
200Ω
100µA
10mΩ
2kΩ
10µA
100mΩ
5.3.3
Accuracy for Temperature Measurement (Pt500)
ST2516
Temperature range
Resolution
Accuracy in six months
Accuracy in one year
-10.0 to 39.9
0.1
±
±
℃
0.30%Rd
0.45%Rd
*1: accuracy=0.3%*measured value ±0.5
℃
℃
±
±
0.5
0.8
℃
℃
*1
40.0 to 99.9
℃
0.1
℃
± 0.30%Rd ± 1.0
℃
± 0.45%Rd ± 1.5
℃
5.3.4
Accuracy for Temperature Measurement (Analog Input)
ST2516
Input voltage range 0 to 2V
Temperature range display
Resolution
-99.9
℃ to 999.9
℃
1mV
Accuracy ±1%Rd ± 3mV
Accuracy= 1%* ( T
R
– T
0V
) + 0.3%*( T
1V
− T
0V
)
T
1V
T
0V
: The temperature measured under input voltage of 1V.
: The temperature measured under input voltage of 0V.
T
R
: The current measured temperature.
-------------------------------------------------------------------------------------------------------------------------------
Note: Rd is the digit reading of measuring instrument; Fs is the full range.
-------------------------------------------------------------------------------------------------------------------------------
34
ST2516 Series Operation Manual
6) Remote Control
6.1
RS232C Connection
RS-232 standard, also called as asynchronous serial communication standard, has already been widely used for data communication between computers, computer and external equipment. RS is the English abbreviation of Recommended Standard; 232, the standard number. This standard is issued by EIA in 1969, which rules to send one bit in a data line every time.
As most serial interfaces, the serial interface of ST2516 is also not strictly based on RS-232 standard but only uses the smallest subset of this standard. The signals are listed in the following table.
Signal
Transmitted Data
Received Data
Signal Ground Common
Code
TXD
RXD
GND
Connector Pin Number
2
3
5
Table 6-1 RS-232 Signal and Pin Connector
The reason is that the use of three lines is much more inexpensive and much simpler than that of five lines or six lines, which is the biggest advantage of using serial interface for communication.
The connection of the instrument with PC is shown in figure 6-1.
TXD(2) (3) RXD
PC
( Controller ) RXD(3) (2) TXD ST2516
GND(5) (5) GND
Figure 6-1 Connection of the instrument with PC
Figure 6-1 shows that the serial interface pin definition of this instrument is different from that of
9 pin connector used in the computer. User can purchase the serial interface cable from our company.
RS232 interface characterizes with a baud rate ranging from 9600 to 115200, no parity, 8-bit data bit, 1-bit stop bit.
The instrument commands comply with the SCPI standard. When a command string is
35
ST2516 Series Operation Manual transmitted to the instrument, it is required to send LF (hexadecimal: 0AH) as the terminating character. Each time the maximum receivable number of SPCI command string is 2kB.
For result data formats transmitted to a PC from the instrument, see Commands Reference.
6.2
USBTMC Remote Control System
USB (Universal Serial Bus) remote control system controls the instrument through the USB interface. This connection conforms to USBTMC-USB488 and USB2.0 protocols.
6.2.1
System Configuration
Connect USB interfaces on PC and ST2516 through a USB cable.
6.2.2
Install the Driver
When ST2516 is first connected to a PC through a USB cable, the prompt information –Found
New Hardware will show on the right bottom of the computer desktop, as is shown below:
Click “NEXT”, dialogue 6-11 will pop up. Choose “Install the software automatically
(recommended)”.
When the installation of driver is finished, user can see “usb test and measurement device” in the device manager of PC, as is shown in the following figure.
36
ST2516 Series Operation Manual
When user is using USBTMC interface, labview software can be used to access the instrument.
6.3
USBCDC Virtual Serial Port
When “USBCDC” is selected, the USB interface can be configured as a virtual serial port (VCom).
6.3.1
System Configuration
Connect PC and ST2516 to the USB interface through a USB cable.
6.3.2
Installing Driver
Methods of installing USBCDC driver are the same with that of installing USBTMC driver. When the installation of driver is finished, user can see “USB VCom Port” in the PC device manager, as is shown in figure 6-13.
Figure 6-13 VCom Display of PC Device Manager
Now, USB VCom Port acts as a serial port. When PC has no serial port, the communication software based on this serial port can be used as USB virtual serial port.
37
ST2516 Series Operation Manual
7) SCIP Command Reference
1. Data Conventions of This Manual
NR1 : integer, for example:123
NR2 : fixed number, for example: 12.3
NR3 : floating number, for example: 12.3E+5
NL : CR character , integer: 10
^END : EOI (end) signal of IEEE-488 bus.
7.1
ST2516 Subsystem Commands
●DISPlay ●TRIGger ● COMParator ●APERture ●SYSTem
●FUNCtion ●FET Ch? ● TEMPerature ●STATistical ● BIN
7.1.1
DISPlay Subsystem Commands
DISPlay subsystem commands are mainly used to set the instrument display page.
The :DISPlay? query returns to the current page.
Command Tree:
The :PAGE command sets the display page.
The DISPlay:PAGE? qurey returns to the current page.
Command Syntax: DISPlay:PAGE <page name>
Functions of <page name> are as follows :
MEASurement Set the display page to the basic measurement.
COMPare Set the display page to compare.
BIN Set the display page to bin.
MSETup Set the display page to measurement setup.
BSETup Set the display page to bin setup.
38
ST2516 Series Operation Manual
TSETup Set the display page to temperature setup. (ST2516)
STATistics Set the display page to statistics.
SYSTem Set the display page to system setup.
FLISt Set the display page to (internal) file list.
For example: WrtCmd(“DISP:PAGE MEAS”); Set the display page to basic measurement.
Query syntax: DISPlay:PAGE?
Return format: <page name><NL^END>
Functions of <page name> are as follows:
MEAS Set the display page to the basic measurement.
COMP Set the display page to compare.
BIN Set the display page to bin.
MSET
BSET
Set the display page to measurement setup.
Set the display page to bin setup.
TSET Set the display page to temperature setup. (ST2516)
STAT Set the display page to statistics.
SYST Set the display page to system setup.
FLISt Set the display page to (internal) file list.
The :STATe command is used to set whether the measurement display page has refreshed the display results.
Command syntax:
ON ( 0 )
DISPlay:STATe
OFF ( 1 )
Query syntax: DISPlay:STATe?
Return format: <NR1><NL^END>
<NR1> are as follows:
1
2
The :LINE command sets the current measurement topic as a substring with up to 20 characters.
The DISPlay:LINE? query returns the current measurement topic. The character string of the measurement topic can be shown in the file list page and be saved as the file name.
Command Syntax: DISPlay:LINE”<string>”
Where:
<string> can be a ASCII character string (up to 20 characters).
For example: WrtCmd(“DISP:LINE ”Resistor meas””);
Query syntax: DISPlay:LINE?
Return format: <string><NL^END>
7.1.2
FUNCtion Subsystem Commands
FUNCtion subsystem commands are mainly used to set “function”, “range”, “measurement
39
ST2516 Series Operation Manual pattern”, “self-calibration mode”, etc.. The DISPlay:PAGE? qurey returns to the current page.
Command Tree:
The :IMPedance command sets the “function” parameters.
The FUNCtion:IMPedance? query returns to the current “function” parameters.
Command Syntax: FUNCtion:IMPedance <function>
Details are as follows:
R Set “function” as R.
RT Set “function” as R-T. (ST2516)
T Set “function” as T. (ST2516)
LPR Set “function” as LPR.
LPRT Set “function” as LPR-T. (ST2516)
For example: WrtCmd(“FUNC:IMP RT”); Set “function” as R-T .
Query syntax: FUNCtion:IMPedance?
Return Format: <function><NL^END>
If the current “function” is R-T, it will returns to RT.
The :IMPedance:RES:RANGe command sets the instrument range in common resistance measurement pattern.
The FUNCtion:IMPedance:RES:RANGe? query returns to the current range parameters in common resistance measurement pattern.
Command Syntax: FUNCtion:IMPedance:RANGe <value>
Where, <value> can be the impedance of the tested LCR component or the specific range values. Its data format is NR1, NR2, NR3, <value> = 0 to 2E+6.
For example: WrtCmd(“FUNC:IMP:RES:RANG 123”); Set the instrument range in common
40
ST2516 Series Operation Manual resistance measurement pattern as 200Ω.
Query syntax: FUNCtion:IMPedance: RES:RANGe?
Return format: <value><NL^END>
Where, <value> can be:
ST2516 : 20.000E-3, 200.00E-3, 2000.0E-3, 20.000E+0, 200.00E+0,
2000.0E+0, 20.000E+3, 200.00E+3,2. 0000E+6
ST2516A : 200.00E-3, 2000.0E-3, 20.000E+0, 200.00E+0,
2000.0E+0, 20.000E+3, 200.00E+3
ST2516B : 20.000E-3, 200.00E-3, 2000.0E-3, 20.000E+0, 200.00E+0,
2000.0E+0, 20.000E+3
The :IMPedance:RES:RANGe:AUTO command sets the range auto selection mode in common resistance measurement pattern.
The FUNCtion:IMPedance:RANGe:AUTO? query returns to the current range mode.
Command syntax:
ON (1)
:IMPedance:RES:RANGe:AUTO
OFF (0)
Where,
Character 1 (integer:49) means ON.
Character 0 (integer: 48) means OFF.
For example: WrtCmd(“FUNC:IMP:RES:RANG:AUTO ON”); Set the range mode in common resistance measurement pattern as AUTO.
Query syntax: FUNCtion:IMPedance:RES:RANGe:AUTO?
Return format: <NR1><NL^END>
<NR1> = 1 or 0
The:IMPedance:LPR:RANGe command sets the instrument range in resistance tested at low voltage measurement pattern.
The FUNCtion :IMPedance:LPR:RANGe? query returns to the current range parameter in resistance tested at low voltage measurement pattern.
Command syntax: FUNCtion:IMPedance:LPR:RANGe <value>
Where, <value>can be the impedance of the tested LCR component or the specific range values. Its data format is NR1, NR2, NR3, <value> = 0 to 2000.
For example: WrtCmd(“FUNC: IMP:LPR:RANG 15”); Set the instrument range in resistance tested at low voltage measurement pattern as 20Ω.
Query syntax: FUNCtion:IMPedance:LPR:RANGe?
Return format: <value><NL^END>
Where , <value> can be :
2000.00E-3, 20.0000E+0, 200.000E+0, 2000.00E+0
41
ST2516 Series Operation Manual
The :IMPedance:LPR:RANGe:AUTO command sets the auto selection mode of range in resistance tested at low voltage measurement pattern.
The FUNCtion :IMPedance:LPR:RANGe:AUTO? query returns to the current range mode.
Command syntax:
ON (1)
:IMPedance:LPR:RANGe:AUTO
OFF (0)
Where:
Character 1 (integer:49) means ON.
Character 0 (integer: 48) means OFF.
For example: WrtCmd(“FUNC:IMP:LPR:RANG:AUTO ON”); Set the range in resistance tested at low voltage measurement pattern as AUTO.
Query syntax: FUNCtion:IMPedance:LPR:RANGe:AUTO?
Return format: <NR1><NL^END>
<NR1> = 1 or 0
The :ADJust command is used to execute or clear 0 ADJ.
Clear 0 ADJ data
Command syntax: FUNCtion: ADJust:CLEAr
Execute 0 CAJ operation
Command syntax: FUNCtion: ADJust?
Returned value: <0 or 1><NL^END>
0: it indicates that the 0CAJ has completed successfully and open 0 CAJ after the completion.
1: it indicates that the measured value of resistance exceeds 400 dgt, namely operation failed.
The :OVC command sets the instrument offset voltage compensation state.
The :OVC? Query returns to the current setstate.(ST2516/ST52516A)
Command syntax:
ON (1)
:OVC
OFF (0)
Where,
Character 1 (integer:49) means ON.
Character 0 (integer: 48) means OFF.
For example: WrtCmd(“FUNCtion:OVC ON”); Set the instrument offset voltage compensation state as “ON”.
Query syntax: FUNCtion: FUNCtion:OVC?
Return format: <NR1><NL^END>
42
ST2516 Series Operation Manual
<NR1> = 1 or 0
1: the offset voltage compensation state is “ON”.
0: the offset voltage compensation state is “OFF”.
7.1.3
APERture Subsystem Commands
The APERture subsystem commands are mainly used to set the measurement speed and the average times used in measurement.
The APERture? query returns to the current measurement speed and average times used in measurement.
Command Tree:
The :APERture command sets the instrument measurement speed.
The :APERture? query returns to the current measurement speed.
Command syntax:
Command syntax: APER <FAST, MEDium, SLOW1 or SLOW2>
For example: WrtCmd(“APERture SLOW1”); Set the instrument self-calibration mode as SLOW.
Query syntax: APERture?
Return format: <FAST , MEDium , SLOW1 or SLOW2> <NL^END>
The :APERture:AVERage command sets the instrument average times used in measurement.
The :APERture:AVERage? query returns to the current average times.
Command syntax:
Command syntax: APER:AVERage <value>
Where, <value> = 1 to 255
For example: WrtCmd(“APERture:AVER 10”); Set nstrument average times used in measurement as 10.
Query syntax: APERture:AVERture?
Return format: < NR1> <NL^END>
7.1.4
TRIGger Subsystem Commands
The TRIGger subsystem commands set the instrument trigger source and the delay time after triggering, and triggers instrument measurement.
Command Tree:
43
ST2516 Series Operation Manual
The :IMMediate command triggers a measurement.
Command syntax: TRIGger[:IMMediate]
For example : WrtCmd(“TRIG”);
The :SOURce command sets the mode of trigger source.
The :SOURce? query returns to the current mode of trigger source.
Command syntax:
TRIGger:SOURce <INTernal, MANual, EXTernal or BUS>
Where,
INTernal Be automatically triggered by the instrument and be the defaut setting of the instrument.
MANual Be triggered by pressing the TRIGGER button on the panel.
EXTernal Be triggered by the HANDLER interface.
BUS Be triggered by the RS232 interface or the GPIB interface.
For example: WrtCmd(“TRIG:SOUR BUS”);
Query syntax: TRIGger:SOURce?
Return format: <INTernal, MANual, EXTernal or BUS> <NL^END>
The :DELay command sets the insreument measurement delay time after triggering.
The TRIGger:DELay? query returns to the current delay time.
Command syntax:
TRIGger:DELay <delay value>
Where, <delay value> = 0 to 9.999 [in seconds]
For example: WrtCmd(“TRIG:DEL 0.5”); Set the delay time as 0.5S.
Query syntax: TRIGger:DELay?
Return format: <NR2><NL^END>
The :DELay:AUTO command sets the instrument measurement delay mode after triggering.
The :DELay:AUTO? query returns to the current delay mode status.
Command syntax:
TRIGger:DELay:AUTO ON(1)
OFF(0)
44
ST2516 Series Operation Manual
Where, ON Set the measurement delay mode as automatic “ON”
OFF Set the measurement delay mode as automatic “OFF”
For example: WrtCmd(“TRIG:DEL:AUTO ON”); Set the delay mode as automatic “ON”.
Query syntax: TRIG:DEL:AUTO?
Return format: <NR1><NL^END>
<NR1> = 1 or 0
1: the measurement delay mode is automatic “ON”.
0: the measurement delay mode is automatic “OFF”.
7.1.5
FETCH? Subsystem Commands
The FETCh? Subsystem commands are used to get the last measurement result and the setup of the mode.
Command Tree:
The [:IMP]? query returns ST2516’s last measurement result to its output buffer.
Query syntax: FETCh[:IMP]?
The data got from the commands can be divided into three types according to different functions and display page.
1. On the measurement display page, compare display interface, bin display page and statistical interface and the measurement function is one-parameter mode (functions are R, T, LPR):
Data format: <primary parameter>, <system status>;
<primary parameter>= the measured value of the current parameter and the format is NR3
(when the temperature conversion function is enabled and on the measurement display interface, the primary parameter is the temperature incrementΔT), when existing outran ge or measurement error, the returned value is “+9.90000E+37”.
System status : -1 No data in the buffer zone.
0 Ordinary measurement data.
+1 Measurement status error.
2.
On the measurement display page, compare display interface, bin display page and statistical interface and the measurement function is two-parameter mode (functions are R-T , LPR-T):
Data format: <primary parameter>, <secondary parameter>, <system status>;
<primary parameter>= the measurement of the current primary parameter and the format is NR3
(when the temperature conversion function is enabled and on the measurement display interface, the primary parameter is the temperature incrementΔT), when existing outrange or measurement error, the returned value is “+9.90000E+37”.
45
ST2516 Series Operation Manual
<secondary parameter>= the measurement of the current secondary parameter and the format is NR3, when existing outrange or measurement error, the returned value is “+9.90000E+37”.
The system status is the same as above.
3.
There is no return value for other display page.
The FETCh:AUTO command sets the automatic mode switch to send each measurement result to its output buffer.
Command syntax: FETCh:AUTO ON(1)
OFF(0)
For example: WrtCmd(“FETC:AUTO ON”); namely opening the automatic sending mode of each measurement result.
7.1.6
TEMPerature Subsystem Commands (ST2516)
TEMPerature subsystem commands set the instrument trigger source and the delay time after triggering, and triggers instrument measurement.
Command Tree:
The :TEMPerature:CORRect:STATe command sets “ON” and “OFF” of the instrument temperature correction function.
The :TEMPerature:CORRect:STATe? query returns to the current state of the temperature correction function.
Command syntax:
:TEMPerature:CORRect:STATe <ON(1) or OFF(0)>
For example: WrtCmd(“:TEMPerature:CORRect:STATe ON”); Set the instrument temperature correction function as “ON”.
NOTE: Turning the temperature correction function on will stop the temperature conversion function!
46
ST2516 Series Operation Manual
Query Syntax: :TEMPerature:CORRect:STATe?
Return format: <NR1><NL^END>
<NR1> = 1 or 0
1: the instrument temperature correction function is “ON”.
0: the instrument temperature correction function is “OFF”.
The :TEMPerature:CORRect:PARameter command sets the “reference temperature” and
“temperature coefficient” of the instrument temperature correction function.
The :TEMPerature:CORRect:PARameter? query returns to the current “reference temperature” and “temperature coefficient”.
Command syntax:
:TEMPerature:CORRect:PARameter<Reference Temp.>,<Temp. Coefficient>
Where, <Reference Temp.> = -10.0 to 99.9(NR2) means “reference temperature”, unit: ℃
<Temp. Coefficient> = -99999 to 99999(NR1) means “temperature coefficient”, unit : ppm/ ℃
For example: WrtCmd(“:TEMP:CORR:PAR 25,3390”); Set the instrument “reference temperature” and “temperature coefficient” as 25 ℃ and 3390 ppm/℃ respectively.
Query Syntax: :TEMPerature:CORRect:PARameter?
Return format: <Reference Temp.>,<Temp. Coefficient><NL^END>
Where, the format and unit of <Reference Temp.>,<Temp. Coefficient> are the same as above.
The :TEMPerature:CONversion:DELTa:STATe command sets “ON” and “OFF” of the instrument temperature conversion function.
The :TEMPerature:CONversion:STATe? query returns to the current state of the temperature conversion function.
Command syntax:
:TEMPerature: CONversion: DELTa:STATe <ON(1) or OFF(0)>
For example: WrtCmd(“:TEMPerature:Conversion: :DELTa:STATe ON”); Set the instrument temperature conversion function as “ON”.
NOTE: Turning the temperature conversion function on will stop the temperature correction function!
Query Syntax: :TEMPerature:CONversion:DELTa:STATe?
Return format: <NR1><NL^END>
<NR1> = 1 or 0
1: the temperature conversion function of the instrument is “ON”.
0: the temperature conversion function of the instrument is “OFF”.
The :TEMPerature:CONversion:DELTa:PARameter command sets the “initial resistance” , ”initial temperature” and ”constant k” of the instrument temperature conversion function.
The :TEMPerature:CONversion:DELTa:PARameter? query returns to the current “initial
47
ST2516 Series Operation Manual resistance” , ”initial temperature” and ”constant k”.
Command syntax:
:TEMPerature:CONversion:DELTa:PARameter<Initial resistance>,<Initial temperature>,
<Constant>
Where, < Initial resistance> = 0 to 110.000E+6(NR3) means “initial resistance”, unit: Ω
< Initial temperature> = -10.0 to 99.9(NR2) means ”initial temperature”, unit: ℃
< Constant > = -999.9 to 999.9(NR2) means ”constant k”, unit: ℃
For example: WrtCmd(“:TEMP:CON:DELT:PAR 100,20,235”); Set the instrument “initial resistance” , ”initial temperature” and ”constant k” as 100Ω , 20 ℃ and 235℃ respectively.
Query Syntax: :TEMPerature:CORRect:STATe:PARameter?
Return format: <Initial resistance>,<Initial temperature>,<Constant><NL^END>
Where, the format and unit of <Initial resistance>,<Initial temperature>,<Constant> are the same as above.
The :TEMPerature:SENSor command sets the input mode selection of the instrument temperature sensor.
The :TEMPerature:SENSor? query returns to the current input mode of the temperature sensor.
Command syntax:
:TEMPerature:SENSor <PT or ANALog>
Where, PT : Using PT500 as the input signal of the temperature sensor
ANALog: Using analog voltage signal as the input signal of the temperature sensor
Query Syntax: :TEMPerature:SENSor?
Return format: < PT or ANAL ><NL^END>
The :TEMPerature:PARameter command sets the parameter setting when using analog voltage signal as the input signal of the temperature sensor.
The :TEMPerature:PARameter? query returns to the current parameter setting.
Query Syntax:
:TEMPerature:PARameter <V1>,<T1>,<V2>,<T2>
Where, <V1> = 0 to 2.00 (NR2) means “reference voltage1“, unit: V
<T1> = -99.9 to 999.9 (NR2) means “reference temperature1“, unit: ℃
<V2> = 0 to 2.00 (NR2) means “reference voltage2“, unit: V
<T2> = -99.9 to 999.9 (NR2) means “reference temperature2“, unit: ℃
For example: WrtCmd(“:TEMP: PAR 0,0,1,500”); Set the“reference voltage1“ , “reference temperature1“ , “reference voltage2“ and “reference temperature2“ of the instrument as 0V, 0 ℃
1V and 500 ℃ respectively.
Query Syntax: :TEMPerature:PARameter?
Return format: the format and unit of <V1>,<T1>,<V2>,<T2><NL^END> are the same as above.
48
ST2516 Series Operation Manual
7.1.7
COMParator Subsystem Commands
COMParator subsystem commands are used to set the compare function of the insturment, including the setup of comparator switch, beeper mode, limit mode and other compare parameters.
Command Tree:
The :COMParator[:STATe] command sets the state of instrument comparator function.
The :COMParator[:STATe]? query returns to the current comparator state.
Command syntax:
:COMParator[:STATe] <ON(1) or OFF(0)>
For example, WrtCmd(“:COMP:STAT ON”); Set the comparator function of the instrument as
“ON”.
Query Syntax: :COMParator:STATe?
Return format: <NR1><NL^END>
<NR1> = 1 or 0
1: the current comparator function of the instrument is “ON”
0: the current comparator function of the instrument is “OFF”
The :COMParator:BEEPer command sets the comparator beeper mode of the instrument.
The :COMParator:BEEPer? query returns to the current beeper mode.
Command syntax:
:COMParator:BEEPer <OFF, HL or IN>
Where, OFF : the comparator beeper function is “OFF”
HL : it beeps when the comparative result is not qualified
49
ST2516 Series Operation Manual
IN : it beeps when the comparative result is qualified
For example, WrtCmd(“:COMP:BEEP IN”); Set the comparator beeper mode as IN.
Query Syntax: :COMParator:BEEPer?
Return format: <OFF, HL or IN><NL^END>
The :COMParator:MODE command sets the comparator limit mode of the instrument.
The :COMParator:MODE? query returns to the current limit mode.
Command syntax:
COMParator:MODE < ATOLerance or PTOLerance >
Where, ATOLerance : set the limit mode of the instrument as absolute tolerance mode
PTOLerance : set the limit mode of the instrument as proportional tolerance mode
For example, WrtCmd(“COMP:MODE ATOL”); Set the limit mode of the instrument as absolute tolerance mode.
Query Syntax: COMParator:MODE?
Return format: <ATOL or PTOL><NL^END>
The :COMParator:UPPer command sets the upper threshold of the instrument comparator function.
The :COMParator:UPPer? query returns to the current upper threshold.
Command syntax:
Where,
COMParator:UPPer < Upper threshold >
< Upper threshold > = 0 to 2.2E+6 (NR3) the upper threshold of the comparator function unit: “Ω”
For example, WrtCmd(“COMP:UPP 2000”); Set the the upper threshold of the instrument compara tor function as 2000Ω.
NOTE: The upper threshold must be greater than or equal to the lower threshold.
Query Syntax: COMParator:UPPer?
Return format: the format and unit of < Upper threshold ><NL^END> are the same as above.
The :COMParator:LOWer command sets the lower threshold of the instrument comparator function.
The :COMParator: LOWer? query returns to the current lower threshold.
Command syntax:
COMParator: LOWer< Lower threshold >
Where,
< Lower threshold > = 0 to 2.2E+6 (NR3) the lower threshold of the comparator function unit: “Ω”
For example: WrtCmd(“COMP:LOW 1800”); Set the the lower threshold of the instrument comparator function as 18 00Ω.
NOTE: The lower threshold must be less than or equal to the upper threshold.
50
ST2516 Series Operation Manual
Query Syntax: COMParator: LOWer?
Return format: the format and unit of < Lower threshold ><NL^END> are the same as above.
The :COMParator:REFerence command sets the reference resistance of the instrument comparator function.
The :COMParator:REFerence? query returns to the current reference resistance.
Command syntax:
COMParator: REFerence<Reference Resistance>
Where,
< Reference Resistance > = 0 to 2.2E+6 (NR3) the reference resistance of the comparator functio n unit: ” Ω”
For example: WrtCmd(“COMP:REF 20E+3”); Set the reference resistance of the instrument comparator fun ction as 20kΩ.
Query Syntax: COMParator: REFerence?
Return format: the format and unit of < Reference Resistance ><NL^END> are the same as above.
The :COMParator:PERCent command sets the tolerance of the instrument comparator function.
The :COMParator:PERCent? query returns to the current tolerance.
Command syntax:
COMParator:PERCent<Tolerance(%)>
Where, < Tolerance(%) > = 0 to 99.999 (NR2) the tolerance of the comparator function unit: ”%”
For example: WrtCmd(“COMP:PERC 10”); Set the tolerance of the instrument comparator function as 10%.
Query Syntax: COMParator: PERCent?
Return format: the format and unit of < Tolerance(%) ><NL^END> are the same as above.
The :COMParator:RESult command querys the last comparator result of the instrument.
Query Syntax: COMParator: RESult?
Return format: < HI, IN, LO, OFF or ERR> <NL^END>
Where,
HI: it indicates that the measurement result is greater than the upper boundary of the comparator
IN: it indicates that the measurement result is between the upper and lower boundary of the comparator
LO: it indicates that the measurement result is less than the lower boundary of the instrument
OFF: it indicates that the comparator function is “OFF”
ERR: it indicates that the comparator function is “ON”, but there exists the measurement error.
51
ST2516 Series Operation Manual
The :COMParator: COUNter:STATe command sets the counter state of instrument comparator interface.
The :COMParator: COUNter:STATe? query returns to the current counter state.
Command syntax:
:COMParator: COUNter :STATe <ON(1) or OFF(0)>
For example, WrtCmd(“:COMP:COUN: STAT ON”); Set the counter function of the instrument comparator interface as “ON”.
Query Syntax: :COMParator:COUNter: STATe?
Return format: <NR1><NL^END>
<NR1> = 1 or 0
1: the current counter function of the instrument comparator interface is “ON”
0: the current counter function of the instrument comparator interface is “OFF”
The :COMParator:COUNter:CLEAr command is used to clear the counter value of the instrument comparator interface.
7.1.8
BIN Subsystem Commands
BIN subsystem commands sets the bin comparator function of the instrument, including bin status switch, beeper mode, limit mode, enable mask and other bin parameters.
Command Tree:
The :BIN[:STATe] command sets the state of the instrument comparator.
The :BIN[:STATe]? query returns to the current state of the bin comparator.
Command syntax:
:BIN[:STATe] <ON(1) or OFF(0)>
For example : WrtCmd(“:BIN:STAT ON”); Set the bin comparator function as “ON”.
52
ST2516 Series Operation Manual
Query Syntax: :BIN:STATe?
Return format: <NR1><NL^END>
<NR1> = 1 or 0
1: the current bin comparator function of the instrument is ”ON”
0: the current bin comparator function of the instrument is ”OFF”
The :BIN:BEEPer command sets the beeper mode of the instrument bin comparator.
The :BIN:BEEPer? query returns to the current bin beeper mode.
Command syntax:
:BIN:BEEPer <OFF, NG or GD>
Where, OFF : the bin beeper is “OFF”
NG : it beeps when one or more bin comparator results are not qulified
GD : it beeps when all the bin comparator results are qulified
For example: WrtCmd(“:BIN:BEEP GD”); Set the comparator beeper mode as GD.
Query Syntax: BIN:BEEPer?
Return format: <OFF, NG or GD><NL^END>
The :BIN:MODE command sets the limit mode of the instrument bin comparator function.
The :BIN:MODE>? query returns to the current limit mode.
Command syntax:
BIN:MODE < ATOLerance or PTOLerance >
Where, ATOLerance : set the bin limit modeas absolute tolerance mode
PTOLerance : set the bin limit mode as proportional tolerance mode
For example: WrtCmd(“BIN:MODE ATOL”); Set the bin limit mode as absolute tolerance mode.
Query Syntax: BIN:MODE?
Return format: <ATOL or PTOL><NL^END>
The :BIN:COLOr:NG command sets the color of the display mark when the bin comparator result is “NG”.
The :BIN:COLOr:NG? query returns to the color of the display mark when the bin comparator result is “NG”.
Command syntax:
BIN:COLOr:NG <OFF, GRAY, RED or GREEN>
Where,
OFF : when the bin comparator result is “NG”, no result mark will be displayed
GRAY : when the bin comparator result is “NG”, set the color of the result mark as
GRAY
RED : when the bin comparator result is “NG”, set the color of the result mark as
RED
GREEN : when the bin comparator result is “NG”, set the color of the result mark as
GREEN
53
ST2516 Series Operation Manual
For example: WrtCmd(“BIN:COLOr:NG GRAY”); Set the color of the result mark as GRAY when the bin comparator result is “NG”.
Query Syntax: BIN:COLOr:NG?
Return format: <OFF, GRAY, RED or GREEN><NL^END>
The :BIN:COLOr:GD command sets the color of the display mark when the bin comparator result is “GD”.
The :BIN:COLOr:GD? query returns to the color of the display mark when the bin comparator result is “GD”.
Command syntax:
BIN:COLOr:GD <OFF, GRAY, RED or GREEN>
Where,
OFF : when the bin comparator result is “GD”, no result mark will be displayed
GRAY : when the bin comparator result is “GD”, set the color of the result mark as
GRAY
RED : when the bin comparator result is “GD”, set the color of the result mark as
RED
GREEN : when the bin comparator result is “GD”, set the color of the result mark as
GREEN
For example: WrtCmd(“BIN:COLOr:GD RED”); Set the color of the result mark as RED when the bin comparator result is “GD”.
Query Syntax: BIN:COLOr:GD?
Return format: <OFF, GRAY, RED or GREEN><NL^END>
The :BIN:UPPer command sets the upper threshold of the instrument specific bin.
The :BIN:UPPer? query returns to the upper threshold of the specific bin.
Command syntax:
BIN:UPPer <Bin NO.>,< Upper threshold >
Where, <Bin NO.> = 1 to 3(NR1) specified bin no., namely specific bin
< Upper threshold > = 0 to 2.2E+6 (NR3) the upper threshold of the specific bin unit: “Ω”
For example: WrtCmd(“BIN:UPP 1,2000”); Set the upper threshold of bin 1 as 2000Ω.
NOTE: The upper threshold of the same bin should be greater than or equal to the lower threshold!
Query Syntax: BIN:UPPer?<Bin NO.>
Return format: the format and unit of < Upper threshold ><NL^END> are the same as above.
--------------------------------------------------------------------------------------------------------------
Note: If the upper threshold does not exist, the returned value is “+9.90000E+37”
The : BIN:LOWer command sets the lower threshold of the instrument specific bin.
The : BIN:LOWer? query returns to the lower threshold of the specific bin.
54
ST2516 Series Operation Manual
Command syntax:
BIN: LOWer <Bin NO.>,< Lower threshold >
Where, <Bin NO.> = 1 to 3(NR1) specified bin no., namely specific bin
< Lower threshold > = 0 to 2.2E+6 (NR3) the lower threshold of the specific bin unit: “Ω”
For example: WrtCmd(“BIN:LOW 1,1800”); Set the lower threshold of bin 1 as 18 00Ω.
NOTE: The lower threshold of the same bin should be less than or equal to the upper threshold!
Query Syntax: BIN:LOWer?<Bin NO.>
Return format: the format and unit of < Lower threshold ><NL^END> are the same as above.
Note: If the lower threshold does not exist, the returned value is “+9.90000E+37”
The : BIN:REFerence command sets the reference resistance of the instrument specific bin.
The : BIN:REFerence? query returns to the current reference resistance of the specific bin.
Command syntax:
BIN: REFerence <Bin NO.>,<Reference Resistance>
Where,
<Bin NO.> = 1 to 3(NR1) specified bin no., namely specific bin
< Reference Resistance > = 0 to 2.2E+6 (NR3) the reference resistance of the specific bin unit: “Ω”
For example: WrtCmd(“BIN:REF 1,20E+3”); Set the reference resistance of bin 1 as 20kΩ.
Query Syntax: BIN: REFerence?<Bin NO.>
Return format: the format and unit of < Reference Resistance ><NL^END> are the same as above.
Note: If the reference resistance does not exist, the returned value is “+9.90000E+37”
The : BIN:PERCent command sets the tolerance of the instrument specific bin.
The : BIN:PERCent? query returns to the current tolerance of the specific bin.
Command syntax:
BIN:PERCent <Bin NO.>,<Tolerance(%)>
Where,
<Bin NO.> = 1 to 3(NR1) specified bin no., namely specific bin
< Tolerance(%) > = 0 to 99.999 (NR2) the tolerance of the specific bin unit: “%”
For example: WrtCmd(“BIN:PERC 1,10”); Set the tolerance of bin 1 as 10%.
Query Syntax: BIN: PERCent?<Bin NO.>
Return format: the format and unit of < Tolerance(%) ><NL^END> are the same as above.
Note: If the tolerance does not exist, the returned value is “+9.90000E+37”
The : BIN:ENABle command sets the enable mask of the bin function.
The : BIN:ENABle? query returns to the current enable number of the bin function.
Command syntax:
55
ST2516 Series Operation Manual
BIN: ENABle <Enable Mask>
Where,
<Enable Mask> = 0 to 7(NR1) enable mask (decimal system)
Transfer some bit to 1, namely hold the corresponding bin enable
Bit No. 2 1 0
BIN NO. BIN3 BIN2 BIN1
For example: WrtCmd(“BIN:ENAB 6”); Set the enable mask from BIN2 to BIN3.
Query Syntax: BIN:ENABle?
Return format: the format and unit of < Enable Mask ><NL^END> are the same as above.
The :BIN:RESult command querys the last bin comparator result of the instrument.
Query Syntax: BIN:RESult?
Return format: < NR1> <NL^END>
Where,
< NR1> = 0 to 7
When the judging result of some bin is “GD”, transfer the corresponding bit to 1
Bin Number 2 1 0
BIN NO. BIN3 BIN2 BIN1
For example: when < NR1> = 4, only the judging result of BIN3 is “GD’.
7.1.9
STATistics Subsystem Commands
Statistics subsystem commands are used to set the statistics funtion of the instrument, including statistics state switch, statistics limit, limit mode and statistics data clear.
Command Tree:
56
ST2516 Series Operation Manual
The :STATistic [:STATe] command sets the statistics state of the instrument.
The :STATistic [:STATe]? query returns to the current statistics state.
Command syntax:
: STATistics [:STATe] <ON(1) or OFF(0)>
For example: WrtCmd(“:STAT:STAT ON”); Set the statistics function as “ON”.
Query Syntax: : STATistics[:STATe]?
Return format: <NR1><NL^END>
<NR1> = 1 or 0
1: the current statistics function of the instrument is ”ON”
0: the current statistics function of the instrument is ”OFF”
The :STATistics:MODE command sets the limit mode of the instrument statistics function.
The :STATistics:MODE? query returns to the current limit mode.
Command syntax:
STATistics:MODE < ATOLerance or PTOLerance >
Where, ATOLerance: set the limit mode of the instrument statistics function as absolute tolerance mode
57
ST2516 Series Operation Manual
PTOLerance : set the limit mode of the instrument statistics function as proportional tolerance mode
For example: WrtCmd(“STAT:MODE ATOL”); Set the limit mode of the instrument as absolute tolerance mode.
NOTE: If the statistics function of the instrument is “ON”, ingore this command!
Query Syntax: STATistics:MODE?
Return format: <ATOL or PTOL><NL^END>
The :STATistics:UPPer command sets the upper threshold of the instrument statistics function.
The :STATistics:UPPer? query returns to the current upper threshold.
Command syntax:
Where,
STATistics:UPPer < Upper threshold >
< Upper threshold > = 0 to 2.2E+6 (NR3) the upper threshold of the statistics function unit: “Ω”
For example: WrtCmd(“COMP:UPP 200”); Set the upper threshold of the statistics function as
200Ω.
NOTE: The upper threshold should be greater than or equal to the lower threshold!
If the statistics function of the instrument is “ON”, ingore this command!
Query Syntax: STATistics:UPPer?
Return format: the format and unit of < Upper threshold ><NL^END> are the same as above.
The :STATistics:LOWer command sets the lower threshold of the instrument statistics function.
The :STATistics:LOWer? query returns to the current lower threshold.
Command syntax:
Where,
STATistics: LOWer< Lower threshold >
< Lower threshold > = 0 to 2.2E+6 (NR3) the lower threshold of the statistics function unit: “Ω”
For example: WrtCmd(“STAT:LOW 180”); Set the lower threshold of the statistics function as
18 0Ω.
NOTE: The lower threshold should be less than or equal to the upper threshold!
If the statistics function of the instrument is “ON”, ingore this command!
Query Syntax: STATistics:LOWer?
Return format: the format and unit of < Lower threshold ><NL^END> are the same as above.
The :STATistics:REFerence command sets the reference resistance of the instrument statistics function.
The :STATistics:REFerence? query returns to the current reference resistance.
Command syntax:
STATistics: REFerence<Reference Resistance>
58
ST2516 Series Operation Manual
Where,
< Reference Resistance > = 0 to 2.2E+6 (NR3) the reference resistance of the statistics function unit: “Ω”
For example: WrtCmd(“STAT:REF 20E+3”); Set the reference resistance of the instrument statistics function as 20kΩ.
NOTE: If the statistics function of the instrument is “ON”, ingore this command!
Query Syntax: STATistics: REFerence?
Return format: the format and unit of < Reference Resistance ><NL^END> are the same as above.
The :STATistics:PERCent command sets the tolerance of the instrument statistics function.
The :STATistics:PERCent? query returns to the tolerance.
Command syntax:
STATistics:PERCent<Tolerance(%)>
Where,
< Tolerance(%) > = 0 to 99.999 (NR2) the tolerance of the statistics function unit: “%”
For example: WrtCmd(“STAT:PERC 10”); Set the tolerance of the instrument statistics function as
10%.
NOTE: If the statistics function of the instrument is “ON”, ingore this command!
Query Syntax: STATistics:PERCent?
Return format: the format and unit of < Tolerance(%) ><NL^END> are the same as above.
The :STATistics:CLEAr command is used to clear the statistics results (all kinds of statistics).
NOTE: If the statistics function of the instrument is “ON”, ingore this command!
The :STATistics:NUMBer command is used to query the statistics numbers of statistics results.
Query Syntax: :STATistics:NUMBer?
Return format: <Total statistics numbers (NR1), valid statistics numbers (NR1)>
For example: WrtCmd(“:STAT:NUMB?”)
Returned value: 1256, 1243
The : STATistics:MEAN command is used to query the mean of the statistics results.
Query Syntax: :STATistics:MEAN?
Return format: <Mean (NR3) >
NOTE: When the valid statistics numbers >= 1, it will returns to the valid value or
“+9.90000E+37”.
For example: WrtCmd(“:STAT:MEAN?”)
Returned value: 1.240E+01
The : STATistics:MAXimum command is used to query the maximum of the statistics results.
Query Syntax: :STATistics:MAXimum?
59
ST2516 Series Operation Manual
Return format: <Maximum (NR3), the corresponding data serial number of the maximum data
(NR1)>
NOTE: When the valid statistics numbers >= 1, it will returns to the valid value or
“+9.90000E+37, 0”.
For example: WrtCmd(“:STAT:MAX?”)
Returned value: 1.2450E+01, 5
The : STATistics:MINimum command is used to query the minimum of the statistics results.
Query Syntax: : STATistics:MINimum?
Return format: <Minimum (NR3), the corresponding data serial number of the minimum data
(NR1)>
NOTE: When the valid statistics numbers >= 1, it will returns to the valid value or
“+9.90000E+37, 0”.
For example: WrtCmd(“:STAT:MIN?”)
Returned value: 1.2350E+01, 8
The : STATistics:COUNt command is used to query the statistics compare results.
Query Syntax: : STATistics:COUNt?
Return format: <HI count (NR1)>, <IN count (NR1)>, < LO count (NR1)>, <measurement error count (NR1)>
For example: WrtCmd(“:STAT:COUNt?”)
Returned value: 12, 246, 78, 5
The :STATistics:DEViation command is used to query the statistics standard deviation.
Query Syntax: : STATistics:DEViation?
Return format: < σ n (NR3)>
For example: WrtCmd(“:STAT:DEV?)
Returned value: 0.0159E-3
The :STATistics:VARiance command is used to query the statistics sample variance.
Query Syntax: : STATistics:VARiance?
Return format: <sn (NR3)>
For example: WrtCmd(“:STAT:VAR?”)
Returned value: 0.0159E-3
The :STATistics:CP command is used to query the Process Capability Index (CP).
Query Syntax: :STATistics:CP?
Return format: <Cp (NR2)>, <Cpk (NR2)>
For example: WrtCmd(“:STAT:CP?”)
Returned value: 0.86, 0.14
60
ST2516 Series Operation Manual
7.1.10
SYSTem Subsystem Commands
SYSTem subsystem commands are used to set the system function of the instrument, including the beeper switch, parameters save, output mode of measurement state error, parameter setting reset and so on.
Command tree:
The :SYSTem:BEEPer:STATe command sets the beeper switch state of the instrument.
The :SYSTem:BEEPer:STATe? qury returns to the current beeper state.
Command syntax :
:SYSTem:BEEPer:STATe <ON(1) or OFF(0)>
For example: WrtCmd(“:SYST:BEEP:STAT ON”); Set the save state of the instrument as “ON”.
Query Syntax: :SYST:BEEP:STAT?
Return format: <NR1><NL^END>
<NR1> = 1 or 0
1: the current beeper state of the instrument is “ON”
0: the current beeper state of the instrument is “OFF”
The :SYSTem:LFRequency command sets the line frequency of the instrument.
The :SYSTem:LFRequency? query returns to the current line frequency.
Command syntax :
:SYSTem:LFRequency <50 or 60>
For example: WrtCmd(“:SYST:LFR 50”); Set the line frequency of the instrument as 50 Hz.
Query Syntax: :SYST: LFRequency?
Return format: <NR1><NL^END>
<NR1> = 50 or 60
50: the current line frequency of the instrument is “50Hz”
60: the current line frequency of the instrument is “60Hz”
61
ST2516 Series Operation Manual
The :SYSTem:SAVE command is used to save the current parameter setting.
Command syntax :
:SYSTem:SAVE <Table NO.1 to 30>, <File name>
Where,
<Table NO.1 to 30> = 1 to 30 (NR1), the serial number of file to be saved
<File name> the filename to be saved (no need with suffix.STA, the length of the file name should be no more than 15 characters)
For example: WrtCmd(“:SYST:SAVE 9 filename”); Save the current parameter setting of the instrument to No.9 file and set the name of the file as “filename”.
The :SYSTem:LOAD command is used to load the parameter setting file saved.
Command syntax :
:SYSTem:LOAD <Table NO.1 to 30>
Where,
<Table NO.1 to 30> = 1 to 30 (NR1) the serial number of file saved
For example: WrtCmd(“:SYST:LOAD 9”); load No.9 file of parameter setting file saved.
NOTE: The file to be loaded must have been saved, otherwise ignore this command!
The :SYSTem:EXTVCC command sets the VCC of the instrument Handler interface.
The :SYSTem:EXTVCC? query returns to the current VCC of the instrument Handler interface.
Command syntax :
:SYSTem:EXTVCC INTernal
EXTernal
Where, INTernal : set the VCC of the instrument Handler interface as “INTernal”
EXTernal : set the VCC of the instrument Handler interface as “EXTernal”
For example: WrtCmd(“:SYST:EXTVCC INT”); Set the VCC of the instrument Handler interface as
“INTernal”.
Query Syntax: :SYSTem:EXTVCC?
Return format: <INT or EXT><NL^END>
INTernal: the current VCC of the instrument Handler interface is “INTernal”
EXTernal: the current VCC of the instrument Handler interface is “EXTernal”
The :SYSTem:RESet command is used to reset the parameter setting to factory default.
Command syntax :
:SYSTem:RESet
For example: WrtCmd(“:SYSTem:RES”); namely finish the parameter reset of the instrument.
Other Commands:
The *RST command resets the instrument.
Command syntax: *RST
For example: WrtCmd(“*RST”);
62
ST2516 Series Operation Manual
The *TRG command triggers the measurement and then sends the result to the output buffer.
Command syntax: *TRG
For example: WrtCmd(“*TRG”);
NOTE: ”*trg” will be valid when :INIT:CONT ON and trig:sour bus commands are enabled.
The *IDN? query returns ST2516’s identification string.
Query syntax: *IDN?
Return format: <manufacturer>,<model>,<firmware><NL^END>
Where,
<manufacturer> Name of Manufacturer ( Sourcetronic)
<model> Instrument Model (ST2516)
<firmware> Firmware Version (VER1.0.0)
For example: WrtCmd(“*IDN?”);
63
ST2516 Series Operation Manual
8) Handler Interface
ST2516 DC Resistance Meter equips with a Handler interface which is mainly used to output the sorting result. When the instrument is applied to an automatic component sorting test system, this interface will output the handshake signal and the sorting result output signal. The sorting result output corresponds to the comparison result output of the current comparator bin.
Terminals and Their Descriptions:
Terminal number
Terminal name
Description
1 START Measurement trigger signal, falling edge is valid. When the instrument holds in the external trigger mode and this signal is valid, the instrument will trigger a measurement.
4
5
2
3
6
PASS2
FAIL
+5V
EXT_VCC
PASS1
The low bin 2 comparison result output signal will be valid.
The low bin comparison result output signal will be valid.
Internal +5V power output.
When the “Handler” power supply is set as “External”, the terminal is external power source and the voltage ranges from +5V to +30V; when the “Handler” power supply is set as “Internal”, the terminal is internal power source.
The low bin 1 comparison result output signal will be valid.
7
8
9
Sequence chart
PASS3
EOC
The low bin 3 comparison result output signal will be valid.
Measurement end signal. The low output signal will be valid.
EXT_GND When the “Handler” power supply is set as “External”, the terminal is external GND; when the “Handler” power supply is set as “Internal”, the terminal is internal GND.
NOTE: P1/P2/P3 is PASS1/PASS2/PASS3 signal.
64
ST2516 Series Operation Manual
Time t1: trigger pulse width t2: measurement time at one time t3: sampling time of one measurement
Minimum value
1ms t3+t4
1 Sampling Time
Maximum value
---
---
--- t4: data processing and display time of one measurement t5: end of sampling to control output time t6: measurement delay time
Display “ON”: 22ms
Display “OFF”: 5ms
2ms
---
---
See the setup for measurement delay
---
When OVC is OFF: Sampling Time = 5ms (50 Hz) / 5ms(60 Hz) Fast
20 ms (50 Hz) / 16.6ms(60 Hz) Medium
110 ms (50 Hz) / 110ms(60 Hz) Slow
450 ms (50 Hz) / 450ms(60 Hz) Slow
When OVC is ON: Sampling Time = 10 ms + t6 (50 Hz) / 10ms + t6 (60 Hz) Fast
40 ms + t6 (50 Hz) / 33ms + t6 (60 Hz) Medium
220 ms + 9* t6 (50 Hz) / 220 ms + 11* t6 (60 Hz) Slow
900 ms + 39*t6(50 Hz) / 900 ms + 47*t6(60 Hz) Slow
Electrical Characteristics
65
ST2516 Series Operation Manual
9) Package Contents and Warranty
9.1
Package Contents
Following items should be contained in the package.
N
S u ee e m
1 rr r ii i aa bb a ll ee l e rr r
N a m ee e
ST2516 series DC Resistance Meter
Q u
1 aa a n tt t ii i tt t yy y
2
3
4
5
ST26050A 4-terminal test cable
Three-Wire power line
PT500
Fuse of 2A
1
1
1
2
6 Operation Manual 1
7
8
9
Manufacturer Certificate
Test Report
Warranty Card
1
1
1
Verify that you have received all above items and any optional accessories you may have ordered.
If anyone is missing, please contact our company or operating division without delay.
9.2
Marks
The following marks can be seen on each instrument panel and nameplate: a.
Manufacturer name and trademark b.
Product name and model c.
Product number and date d.
the License for Manufacturing Measurement Instruments and its number e.
Marks for test terminal
9.3
Package
The instrument, generally wrapped in a plastic bag, should be packed in a strong packing box that could resist dust, vibration and moisture. Accessories, spare parts, operation manual and manufacturer certificates, etc. should also be included in it.
66
ST2516 Series Operation Manual
9.4
Shipping
In the shipment, the instrument should be handled with care and some precautions must be taken to resist moisture and water.
9.5
Storage
The instrument should be stored in an airy room where the environment temperature ranges from 5 ℃ to 40 ℃ , relative humidity is not greater than 85% and the air contains no detrimental impurities that might corrode the instrument.
9.6
Warranty
This instrument is warranted against defects in material and workmanship for a period of one years from the date of shipment. You should supply us with the warranty card before you enjoy the free maintenance service. This warranty does not apply in the event of misuse or abuse of the product or as a result of unauthorized alterations or repairs. We will, without charge, repair or replace, at its option, defective product or component parts.
The maintenance for this instrument should be performed by professional maintenance personnel. Do not substitute the internal components unauthorized when maintaining. In order to ensure the measurement accuracy, the instrument must be measured and corrected after maintenance. You should bear the maintenance expense for damages caused by unauthorized repairing or substituting components.
67
www.sourcetronic.com
SOURCETRONIC GMBH
Fahrenheitstrasse 1
28359 Bremen
Germany
T +49 421 2 77 99 99
F +49 421 2 77 99 98 [email protected]
www.sourcetronic.com
skype: sourcetronic
advertisement
Related manuals
advertisement
Table of contents
- 7 Introduction to Instrument, Unpacking and Installing
- 7 Introduction to Instrument
- 7 Unpacking
- 7 Power Connection
- 8 Environment
- 8 Use of Test Fixture
- 9 Warm-up
- 9 Other Features
- 10 Introduction to Front and Rear Panels
- 10 Introduction to Front Panel
- 11 Introduction to Rear Panel
- 12 Display Zone
- 13 Introduction to Buttons on Front Panel
- 13 [MEAS]
- 13 [SYSTEM]
- 14 Simple Operation
- 14 Starting Up
- 15 Basic Operation
-
15
- 15 Measurement Functions
- 16 Measurement Range
- 17 Measurement Speed
- 17 File Manage
- 17 Tools
-
18
- 19 File Manage
- 19 Tools
- 19 COMP (ON/OFF)
- 19 Compare Mode and SETTINGS of ABS & Percent Error
-
20
- 21 STATIS DISP
- 22 Edge Mode and Settings of Its Relevant Values
- 22 Status ON/OFF
- 22 Parameters of Statistic Analysis
- 23 TOOLS
-
24
- 25 ST2516)
- 25 Temperature Correction (TC)
- 27 Types of Temperature Sensor
- 28 Parameter Setting
-
28
- 30 System Setup and File Manage
- 30 System Setup
- 30 TouchTone
- 30 Language
- 31 Password
- 31 Bus Mode
- 32 Baud Rate
- 32 AC Freq
- 32 Handler VCC
- 32 LCD Style
- 32 Setting Time and Date
-
33
- 33 Introduction to Save/Recall
- 33 Structure of File Folder/File in a U Disk
- 37 Performance Index
- 37 Measurement Function
- 37 Measurement Parameters and Notations
- 37 Measurement Groups
- 37 Range
- 37 Trigger
- 37 Mode of Test Terminal
- 38 Resistance Measurement Time
- 38 Average
- 38 Test Signal
- 38 Current range
- 38 Output Voltage of Open Circuit
- 38 Maximum Display Range
- 39 Measurement Accuracy
- 39 Basic Accuracy for Resistance Measurement
- 40 Accuracy for Resistance Tested at Low Current Mode
- 40 Accuracy for Temperature Measurement (Pt500)
- 40 Accuracy for Temperature Measurement (Analog Input)
- 41 Remote Control
- 41 RS232C Connection
- 42 USBTMC Remote Control System
- 42 System Configuration
- 42 Install the Driver
- 43 USBCDC Virtual Serial Port
- 43 System Configuration
- 43 Installing Driver
- 44 SCIP Command Reference
- 44 ST2516 Subsystem Commands
- 44 DISPlay Subsystem Commands
- 45 FUNCtion Subsystem Commands
- 49 APERture Subsystem Commands
- 49 TRIGger Subsystem Commands
- 51 FETCH? Subsystem Commands
- 52 TEMPerature Subsystem Commands(ST2516)
- 55 COMParator Subsystem Commands
- 58 BIN Subsystem Commands
- 62 STATistics Subsystem Commands
- 67 SYSTem Subsystem Commands
- 70 Handler Interface
- 72 Package Contents and Warranty
- 72 Package Contents
- 72 Marks
- 72 Package
- 73 Shipping
- 73 Storage
- 73 Warranty