- Home
- Domestic appliances
- Climate control
- Temperature & humidity sensors
- YASKAWA
- P7B Drive Bypass
- Manual
advertisement
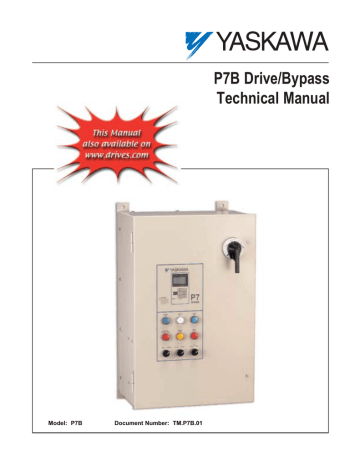
Model: P7B Document Number: TM.P7B.01
P7B Drive/Bypass
Technical Manual
Quick Reference for Bypass Parameters
b2-01 b2-02 b2-03 b2-04 b2-09 b3-01 b3-02 b1-02 b1-03 b1-04 b1-07 b1-08 b1-11 b1-12 b3-03 b3-05 b3-14 b4-01 b4-02 b5-01 b5-02 b5-03
A2-17
A2-18
A2-19
A2-20
A2-21
A2-22
A2-23
A2-24
A2-10
A2-11
A2-12
A2-13
A2-14
A2-15
A2-16
A2-25
A2-26
A2-27
A2-28
A2-29
A2-30
A2-31
A2-32 b1-01
Parameter
Number
A1-00
A1-01
A1-03
A1-04
A1-05
A2-01
A2-02
A2-03
A2-04
A2-05
A2-06
A2-07
A2-08
A2-09
Factory
Setting
0
2
0
0
0
See Table 2 of the bypass schematic
0.5
50
5.0
0
0
2
120
0
0
1
1
1
0
1
2
5
0
0
2
0.2
1
0
User
Setting
d2-03 d3-01 d3-02 d3-03 d3-04 d4-01 d4-02
E1-01
C6-05 d1-01 d1-02 d1-03 d1-04 d1-17 d2-01 d2-02
C2-01
C2-02
C4-01
C4-02
C6-02
C6-03
C6-04 b8-06
C1-01
C1-02
C1-03
C1-04
C1-09
C1-11 b5-26 b5-27 b5-28 b5-29 b5-30 b8-01 b8-04 b8-05 b5-19 b5-20 b5-21 b5-22 b5-23 b5-24 b5-25
Parameter
Number
b5-04 b5-06 b5-07 b5-08 b5-09 b5-10 b5-11 b5-12 b5-13 b5-14 b5-15 b5-16 b5-17 b5-18
E1-03
E1-04
0
10.0
6.0
0
40
6
100
0
0
0
0
0
1
0
10
208, 240V or
480V
0.2
0.2
1
200 kVA Dep.
kVA Dep.
kVA Dep.
30
30
10
0
0
60
60
0
60
0
1
0
1 kVA Dep.
20
0
0
0
1
0
0
1
0
0
0
0
0
0
1
0
1
Factory
Setting
100
100
0
0
0
F
60
User
Setting
H4-01
H4-02
H4-03
H4-04
H4-05
H4-06
H4-07
H4-08
H5-01
H5-02
H5-03
H5-04
H5-05
H5-06
H5-07
H5-08
H5-09
L1-01
L1-02
L1-03
L1-04
Parameter
Number
E1-05
E1-06
E1-07
E1-08
E1-09
E1-10
E1-11
E1-12
E1-13
E2-01
E2-03
E2-05
F6-01
F6-02
F6-03
F6-05
H1-01
H1-02
H1-03
H1-04
H1-05
H2-01
H2-02
H3-02
H3-03
H3-08
H3-09
H3-10
H3-11
H3-12
H3-13
See Table 2 of the bypass schematic
4
6
0
3B
See Table 2 of the bypass schematic
0
See Table 2 of the bypass schematic
See Table 2 of the bypass schematic
100
0
0.3
See Table 2 of the bypass schematic
0
3
1
0
0
1F
3
2
100
0
8
50
0
3
1
1
8
0
2
5
1
Factory
Setting
240V or 480V
60
3
18
1.5
10.8
0
0
0 kVA Dep.
kVA Dep.
kVA Dep.
3
0
1
0
70
User
Setting
o2-07 o2-08 o2-09 o2-10 o2-12 o2-14 o2-15 o1-07 o1-08 o2-01 o2-02 o2-03 o2-04 o2-05 o2-06 o3-01 o3-02
T1-02
T1-04 n3-03 n3-04 o1-01 o1-02 o1-03 o1-05 o1-06
L8-15
L8-18
L8-19 n1-01 n1-02 n3-01 n3-02
L8-01
L8-02
L8-03
L8-06
L8-09
L8-10
L8-11
L8-12
L4-06
L5-01
L5-02
L5-03
L6-01
L6-02
L6-03
Parameter
Number
L1-05
L2-01
L2-02
L2-03
L2-04
L2-05
L3-01
L3-02
L3-04
L3-05
L3-06
L4-01
L4-02
L4-05
0
0
0
0
0
1
1
1
0
2
3
0 kVA Dep.
1
1
0
1 kVA Dep.
kVA Dep.
0
3
0
1
40
6
1
1
1
20
1
1
5
150
1
0
300
45
0
95
4
5
80
10
0
600
6
15
10
120
0
2
0
190
1
120
1
1
Factory
Setting
0.2
2
0.1
0.1
0.3
User
Setting
Warnings and Cautions
This Section provides warnings and cautions pertinent to this product, that if not heeded, may result in personal injury, fatality, or equipment damage. Yaskawa is not responsible for consequences of ignoring these instructions.
WARNING
YASKAWA manufactures component parts that can be used in a wide variety of industrial applications. The selection and application of YASKAWA products remain the responsibility of the equipment designer or end user. YASKAWA accepts no responsibility for the way its products are incorporated into the final system design. Under no circumstances should any
YASKAWA product be incorporated into any product or design as the exclusive or sole safety control. Without exception, all controls should be designed to detect faults dynamically and fail safely under all circumstances. All products designed to incorporate a component part manufactured by YASKAWA must be supplied to the end user with appropriate warnings and instructions as to that part’s safe use and operation. Any warnings provided by YASKAWA must be promptly provided to the end user. YASKAWA offers an express warranty only as to the quality of its products in conforming to standards and specifications published in the YASKAWA manual. NO OTHER WARRANTY, EXPRESS OR IMPLIED, IS OFFERED.
YASKAWA assumes no liability for any personal injury, property damage, losses, or claims arising from misapplication of its products.
WARNING
•
Read and understand this manual before installing, operating, or servicing this Drive. All warnings, cautions, and instructions must be followed. All activity must be performed by qualified personnel. The Drive must be installed according to this manual and local codes.
•
Do not connect or disconnect wiring while the power is on. Do not remove covers or touch circuit boards while the power is on.
•
Before servicing, disconnect all power to the equipment. The internal capacitor remains charged even after the power supply is turned off. Status indicator LEDs and Digital Operator display will be extinguished when the DC bus voltage is below
50 VDC. To prevent electric shock, wait at least five minutes after all indicators are OFF and measure DC bus voltage level to confirm safe level.
•
Do not perform a withstand voltage test on any part of the unit. This equipment uses sensitive devices and may be damaged by high voltage.
•
The Drive and Bypass unit is not suitable for circuits capable of delivering more than the specified RMS symmetrical amperes. Install adequate branch short circuit protection per applicable codes. Refer to the specification. Failure to do so may result in equipment damage and/or personal injury.
•
Do not connect unapproved LC or RC interference suppression filters, capacitors, or overvoltage protection devices to the output of the Drive. These devices may generate peak currents that exceed Drive specifications.
•
To avoid unnecessary fault displays caused by contactors or output switches placed between Drive and motor, auxiliary contacts must be properly integrated into the control logic circuit.
•
YASKAWA is not responsible for any modification of the product made by the user; doing so will void the warranty. This product must not be modified.
•
Verify that the rated voltage of the Drive and Bypass unit matches the voltage of the incoming power supply before applying power.
•
To meet CE directives, proper line filters and proper installation are required.
i
WARNING
•
Some drawings in this manual may be shown with protective covers or shields removed, to describe details. These must be replaced before operation.
•
Observe electrostatic discharge procedures when handling circuit cards to prevent ESD damage.
•
The equipment may start unexpectedly upon application of power. Clear all personnel from the Drive, motor, and machine area before applying power. Secure covers, couplings, shaft keys, and machine loads before energizing the Drive and Bypass unit.
•
Please do not connect or operate any equipment with visible damage or missing parts. The operating company is responsible for any injuries or equipment damage resulting from failure to heed the warnings in this manual.
!
Intended Use
Drives and Bypass Units are intended for installation in electrical systems or machinery.
For use in the European Union, the installation in machinery and systems must conform to the following product standards of the Low Voltage Directive:
EN 50178, 1997-10, Equipping of Power Systems with Electronic Devices
EN 60201-1, 1997-12 Machine Safety and Equipping with Electrical Devices
Part 1: General Requirements (IEC 60204-1:1997)/
EN 61010, 1997-11Safety Requirements for Information Technology Equipment
(IEC 950:1991 + A1:1992 + A2:1993 + A3:1995 + A4:1996, modified)
CE certification per EN 50178 can be achieved using the line filters specified in this manual and following the appropriate installation instructions.
!
Other
The Drive and Bypass unit is suitable for use on a circuit capable of delivering not more than 100,000 RMS symmetrical amperes, 240Vac maximum (240V Class) and 480Vac maximum (480V Class).
This manual is for reference only and subject to change without notice.
ii
Introduction
This Section describes the applicability of the Manual
!
Product Description
The P7 Bypass unit provides a means of bypassing the Drive while allowing the motor to operate at full speed, directly from the AC line. It incorporates an AC Drive and three contactor Bypass arrangement in a single UL listed enclosure. The three electrically interlocked IEC rated contactors isolate the Drive when operating in Bypass mode.
Control logic provides industry standard Hand/Off/Auto functions and safety circuit interlocks in both drive and Bypass operating modes.
Bypass components include: a fused 120 VAC control circuit transformer, an input Motor Circuit Protector (MCP) circuit breaker/disconnect, motor overload relay, selector switches and indicating lights.
The P7 Drive, a component of the P7 Bypass package, is a Pulse Width Modulated Drive for 3-Phase AC induction motors.
This type of Drive is also known as an Adjustable Frequency Drive, Variable Frequency Drive, AC Drive, AFD, ASD, VFD, and Inverter. In this manual, the P7 Drive will be referred to as the “Drive”.
The Drive is a variable torque AC drive, designed specifically for HVAC applications, including fans, blowers and pumps. A new benchmark for size, cost, performance, benefits, and quality, the Drive includes numerous built-in features such as network communications, H/O/A, PI, parameter storage and copy functions.
The Drive has communications for the popular protocols: DeviceNet, Profibus, Ethernet, etc. An optional L
ON
W
ORKS® interface card is also available.
The LCD keypad/operator is equipped with Hand/Off/Auto functions, copy feature, 7 language choices, and 5 lines of display with 16 characters per line. User parameter settings can be recovered at any time via “User Initialization”. Optional
DriveWizard software allows upload/download, as well as graphing and monitoring of drive parameters from a PC for ease of drive management.
Built-in PI eliminates the need for closed loop output signals from a building automation system. It includes feedback display, inverse, square root and differential control functions, and maintains setpoint for closed loop control of fans and pumps for pressure, flow, or temperature regulation.
This manual is applicable to P7 Drives defined by model numbers of CIMR-P7U_ _ _ _ contained within Bypass units defined by model numbers of P7B_ _ _ _.
This manual is subject to change as product improvements occur. The latest version of the manual can be obtained from the
Yaskawa website www.drives.com
. The date shown on the rear cover is changed when revisions are made. The latest version of Drive software is also shown.
Introduction iii
This manual may describe trademarked equipment, which is the property of other companies. These trademarks are the property of the registered owner companies and may include the following:
PROFIBUS
®
and PROFIBUS-DP
®
are registered trademarks of PROFIBUS Nutzerorganization e.v.
DeviceNet is a registered trademark of ODVA (Open DeviceNet Vendor Association, Inc.)
Modbus
®
, trademark of Schneider Automation, Inc.
L
ON
W
ORKS
®
, trademark of Echelon Corporation
Other Documents and Manuals are available to support special use or installation of this product. These documents may be provided with the product or upon request or downloaded from www.drives.com. Documents may include the following:
TM.P7.02.Programming … Manual included on CD ROM with product
DriveWizard … Software and Manual…Included on CD ROM with product
Option Instructions … Included on CD ROM with product
!
Definitions of Acronyms and Abbreviations
AC
AIC
CB
CIMR
CN
CPT
CPU
DIP
FLA
Alternating Current
Amps Interrupting Capacity
Circuit Breaker
Control Induction Motor Rotation
Connector
Control Power Transformer
Central Processing Unit
Dual Inline Package
Full Load Amperes
FVFF Forced Ventilated, inlet Filter, outlet Filter
HOA Hand/Off/Auto
HP Horsepower
IEC
IGV
IPM
KVA
LED
International Electrotechnical Commission
Inlet Guide Vanes
Intelligent Power Module
Kilo Volt Amperes
Light Emitting Diode
PI
SFS
TB
THD
VA
VAC
VAV
LRA
MCP
MTBF
NC
NEC
NEMA
NO
OLR
PCB
Locked Rotor Amperes
Motor Circuit Protector
Mean Time Between Failures
Normally Closed
National Electrical Code
National Electrical Manufacturers Association
Normally Open
Over Load Relay
Printed Circuit Board
Proportional plus Integral control action
Terminal Block
Total Harmonic Distortion
Volt Amperes
Volts Alternating Current
Variable Air Volume
!
Terminology in This Manual
“Standard” or “Configured” options - are available with standard lead times
“Engineered” or “Custom” options - are available only with extended lead times
Introduction iv
!
Resources Available
Document Number
TM.P7.01
TM.P7.02
TM.AFD.14
TM.AFD.12
IG.AFD.20
IG.AFD.50
CD.AFD7.01
Document
DriveWizard
®
Software
Table of Resources
Manuals, Installation Guides, and CD’s
Description
Drive User Manual
Drive Programming Manual
DeviceNet Technical Manual
Profibus Technical Manual
LONWORKS
®
Option Installation Guide
3-15 PSI Pressure Transducer Installation Guide
CD ROM for Drives
Software
Description
DriveWizard
®
Software Version 5.3 or later
Introduction v
Notes:
Introduction vi
Table of Contents
Table of Contents vii
Table of Contents viii
Table of Contents ix
Notes:
Table of Contents x
Chapter 1
Physical Installation
This chapter describes the checks required upon receiving and the installation process for a Drive and Bypass unit.
Bypass Model Number and Enclosure Style .................................. 2
Enclosure Data ............................................................................... 4
Confirmations upon Delivery .......................................................... 7
Receiving Checks ...................................................................... 7
Bypass Nameplate Information .................................................. 7
Bypass Unit Enclosures ............................................................. 8
Bypass Product Options ................................................................. 9
Bypass Component Descriptions ................................................. 11
Bypass Unit Front Control Panel ............................................ 11
Exterior and Mounting Dimensions .............................................. 17
Bypass Unit 30 HP and Below, 480 VAC;
15 HP and Below, 208V/240V ................................................. 17
Bypass Unit 30 HP and Below, 480 VAC;
15 HP and Below, 208V/240V With Add-On Box ................... 18
Bypass Unit 40 HP to 100 HP, 480 VAC;
20 HP to 40 HP, 208V/240V .................................................... 19
Bypass Unit 40 HP to 100 HP, 480 VAC;
20 HP to 40 HP, 208V/240V With Add-On Box ........................ 20
Bypass Unit 125 HP to 250 HP, 480 VAC;
50 HP to 125 HP, 208V ............................................................ 21
Dimensions and Weights ......................................................... 22
Checking and Controlling Installation Site .................................... 24
Installation Site ........................................................................ 24
Controlling the Ambient Temperature ...................................... 25
Protecting the Bypass Unit from Foreign Matter ...................... 25
Installation Orientation and Enclosure Considerations ............ 26
Physical Installation 1 - 1
Bypass Model Number and Enclosure Style
The Bypass covers two voltage ranges: 208-240 VAC and 480 VAC. Ratings applicable are from 1/2 to 500 HP.
Voltage
208 VAC
240 VAC
Table 1.1 Bypass
Bypass
Base Model Number
HP
NEMA 1
*NEMA 12
FVFF
P7BVD002
P7BVD003
P7BVD004
P7BVD007
P7BVD010
P7BVD016
P7BVD024
P7BVD030
P7BVD046
P7BVD059
P7BVD074
P7BVD088
P7BVD114
P7BVD143
P7BVD169
P7BVD211
P7BVD273
P7BVD343
P7BVD396
P7BVA002
P7BVA003
P7BVA004
P7BVA006
P7BVA009
P7BVA015
P7BVA022
P7BVA028
P7BVA042
P7BVA054
P7BVA068
P7BVA080
P7BVA104
P7BBD002
P7BBD003
P7BBD004
P7BBD007
P7BBD010
P7BBD016
P7BBD024
P7BBD030
P7BBD046
P7BBD059
P7BBD074
P7BBD088
P7BBD114
P7BBD143
P7BBD169
P7BBD211
P7BBD273
P7BBD343
P7BBD396
P7BBA002
P7BBA003
P7BBA004
P7BBA006
P7BBA009
P7BBA015
P7BBA022
P7BBA028
P7BBA042
P7BBA054
P7BBA068
P7BBA080
P7BBA104
0.5
0.75
1
2
3
5
7.5
10
15
20
25
30
40
50
60
75
100
125
150
0.5
0.75
1
2
3
5
7.5
10
15
20
25
30
40
Bypass
Continuous
Output
Current
(Amps)
2.4
3.5
4.6
7.5
10.6
16.7
24.2
30.8
46.2
59.4
74.8
88
114
143
169
211
273
343
396
2.2
3.2
4.0
6.8
9.6
15.2
22
28
42
54
68
80
104
Uses
Basic Drive
Model Number
CIMR-P7U2075
CIMR-P7U2090
CIMR-P7U2110
CIMR-P7U22P2
CIMR-P7U22P2
CIMR-P7U22P2
CIMR-P7U22P2
CIMR-P7U22P2
CIMR-P7U23P7
CIMR-P7U25P5
CIMR-P7U27P5
CIMR-P7U2011
CIMR-P7U2015
CIMR-P7U2018
CIMR-P7U2022
CIMR-P7U2030
CIMR-P7U22P2
CIMR-P7U22P2
CIMR-P7U22P2
CIMR-P7U22P2
CIMR-P7U22P2
CIMR-P7U23P7
CIMR-P7U27P5
CIMR-P7U27P5
CIMR-P7U2011
CIMR-P7U2015
CIMR-P7U2018
CIMR-P7U2022
CIMR-P7U2030
CIMR-P7U2037
CIMR-P7U2045
CIMR-P7U2055
Physical Installation 1 - 2
Voltage
230 VAC
480 VAC
Bypass
Base Model Number
NEMA 1
Table 1.1 Bypass (Continued)
*NEMA 12
FVFF
HP
Bypass
Continuous
Output
Current
(Amps)
P7BVA130
P7BVA154
P7BVA192
P7BVA248
P7BVA312
P7BVA360
P7BVB001
P7BVB001
P7BVB002
P7BVB003
P7BVB004
P7BVB007
P7BVB011
P7BVB014
P7BVB021
P7BVB027
P7BVB034
P7BVB040
P7BVB052
P7BVB065
P7BVB077
P7BVB096
P7BVB124
P7BVB156
P7BBA130
P7BBA154
P7BBA192
P7BBA248
P7BBA312
P7BBA360
P7BBB001
P7BBB001
P7BBB002
P7BBB003
P7BBB004
P7BBB007
P7BBB011
P7BBB014
P7BBB021
P7BBB027
P7BBB034
P7BBB040
P7BBB052
P7BBB065
P7BBB077
P7BBB096
P7BBB124
P7BBB156
50
50
60
75/100
125
150
0.5
0.75
1
2
3
5
7.5
10
15
20
25
30
40
50
60
75
100
125
130
154
192
248
312
360
1.1
1.6
2.1
3.4
4.8
7.6
11
14
21
27
34
40
52
65
77
96
124
156
Uses
Basic Drive
Model Number
CIMR-P7U2037
CIMR-P7U2037
CIMR-P7U2045
CIMR-P7U2075
CIMR-P7U2075
CIMR-P7U2090
CIMR-P7U42P2
CIMR-P7U42P2
CIMR-P7U42P2
CIMR-P7U42P2
CIMR-P7U42P2
CIMR-P7U43P7
CIMR-P7U45P5
CIMR-P7U47P5
CIMR-P7U4011
CIMR-P7U4011
CIMR-P7U4015
CIMR-P7U4018
CIMR-P7U4030
CIMR-P7U4030
CIMR-P7U4037
CIMR-P7U4045
CIMR-P7U4055
CIMR-P7U4075
P7BVB180
P7BVB240
P7BBB180
P7BBB240
150
200
180
240
CIMR-P7U4090
CIMR-P7U4110
P7BVB302 P7BBB302 250 302 CIMR-P7U4160
* The Nema 12 FVFF Enclosure is ventilated and filtered with gaskets. UL does not recognize NEMA 12 ventilated enclosures, therefore, for UL purposes, these units are designated NEMA 1.
Physical Installation 1 - 3
Enclosure Data
Table 1.2 208V Enclosure Data
Input
Volts
208
HP
1
3
5
7.5
10
15
0.5
0.75
1
2
40
50
60
75
20
25
30
100
125
150
Drive
Model
CIMR-
Bypass
2
Model
Number
P7U22P21A P7B_D002
P7U22P21A P7B_D003
P7U22P21A P7B_D004
P7U22P21A P7B_D007
P7U22P21A P7B_D010
P7U23P71A P7B_D016
P7U27P51A P7B_D024
P7U27P51A P7B_D030
P7U20111A P7B_D046
P7U20151A P7B_D059
P7U20181A P7B_D074
P7U20221A P7B_D088
59.4
74.8
88.0
P7U20301A P7B_D114 114.0
P7U20370A P7B_D143 143.0
P7U20450A P7B_D169 169.0
P7U20550A P7B_D211 211.0
P7U20750A P7B_D273
P7U20900A P7B_D343
273.0
343.0
P7U21100A P7B_D396
NEC
FLA
10.6
16.7
24.2
30.8
46.2
2.4
3.5
4.6
7.5
396.0
OL
110%
1 min
11.7
18.4
26.6
33.9
50.8
2.6
3.8
5.1
8.2
65.3
82.3
96.8
125.4
157.3
185.9
232.1
300.3
377.3
435.6
653
746
939
1340
1523
1762
2244
3003
3296
141
202
273
365
578
Heat
3
Loss
Watts
Enclosure Dimensions
4
NEMA 1 & NEMA 12 -FVFF
H W D inches
68
68
78
110
29.48 19.06 13.66
Weight
5 of
Assembly
Enclosure Dimensions w/Add-on
4
NEMA 1 & NEMA 12-FVFF
H W D inches
Weight
5 of
Assembly
+Add-on
Box
Electrical
Schematic
115 lbs
43.35 19.06 13.66
156 lbs
Dimension Drawing
S-5542
6
127 lbs
Dimension Drawing
S-5543
164 lbs
P7B-00
4029
40.48 25.63 14.66
Note 1: Horsepower rating is based on a standard NEMA B 4-pole motor.
Dimension Drawing
S-5544
Dimension Drawing
S-5550
7
84.00 25.63 26.25
9
8
208 lbs
221 lbs
847 lbs
943 lbs
1214 lbs
1330 lbs
1423 lbs
55.35 25.63 14.66
Dimension Drawing
S-5545
NOT REQUIRED
291 lbs
307 lbs
Note 2: The underscore position in these model numbers codes for the enclosure type: V = NEMA1, B = NEMA12 FVFF.
Note 3: Heat loss is the amount of heat dissipated by the drive at full load with all standard options available inside the enclosure. Drive heat sink losses are
included in the heat loss data. Heat loss data is for the enclosure without the add-on enclosure.
Note 4: Height dimension (H) excludes the mounting screw tabs. Depth dimension (D) excludes MCP disconnect handle.
Note 5: This data represents the total weight with all possible standard options. Weight could be less depending on the options specified.
Note 6: All standard options are available in this size enclosure except options E (RFI Filter) and K (5% Output Reactor). Options E and K require the add-on enclosure.
Note 7: All options are available in this size enclosure except E (RFI Filter), R (3% Line Reactor), and K (5% Output Reactor). Only option E combined with either option R or option K can be installed in the add-on enclosure. Options R and K together require an increase in the size of the P7 Bypass Enclosure.
Contact the factory if all three options are required. Options D (2 Motor “OR”) or A (2 Motor “AND”) for 30 Hp and 40 Hp require the next size enclosure.
Note 8: Heat sink mounted externally varies the depth dimension depending on the drive size. Depth will not exceed dimension shown.
Note 9: All options are available in this size enclosure except options D (2 Motor “OR”) or A (2 Motor “AND”) for 75 Hp and 100 Hp require the next size enclosure.
Physical Installation 1 - 4
Table 1.3 240/230V Enclosure Data
Input
Volts
240
230
HP
1
15
20
25
30
5
7.5
10
0.5
0.75
1
2
3
40
50
60
75
100
125
150
Drive
Model
CIMR-
Bypass
2
Model
Number
P7U22P21A P7B_A002
P7U22P21A P7B_A003
P7U22P21A P7B_A004
P7U22P21A P7B_A006
P7U22P21A P7B_A009
P7U23P71A P7B_A015
P7U25P51A P7B_A022
P7U27P51A P7B_A028
P7U20111A P7B_A042
P7U20151A P7B_A054
P7U20181A P7B_A068
P7U20221A P7B_A080
P7U20301A P7B_A104
P7U20370A P7B_A130
P7U20370A P7B_A154
P7U20450A P7B_A192
P7U20750A P7B_A248
P7U20750A P7B_A312
P7U20900A P7B_A360
NEC
FLA
16.7
24.2
30.8
46.2
59.4
74.8
88.0
2.4
3.5
4.4
7.5
10.6
15.2
22.0
28.0
42.0
54.0
68.0
80.0
2.2
3.2
4.0
6.8
9.6
104.0
130.0
154.0
192.0
248.0
312.0
360.0
OL
110%
1 min
114.4
143.0
169.4
211.2
272.8
343.2
396.0
1340
1523
1544
1860
3003
3045
202
273
365
578
653
746
939
Heat
3
Loss
Watts
Enclosure Dimensions
4
NEMA 1 & NEMA 12 -FVFF
H W D inches
68
68
78
110
141
29.48 19.06 13.66
Weight
5 of
Assembly
Enclosure Dimensions w/Add-on
4
NEMA 1 & NEMA 12-FVFF
H W D inches
Weight
5 of
Assembly
+Add-on
Box
Electrical
Schematic
115 lbs
43.35 19.06 13.66
156 lbs
3440
Note 1: Horsepower rating is based on a standard NEMA B 4-pole motor.
Dimension Drawing
S-5542
6
40.48 25.63 14.66
Dimension Drawing
S-5544
7
84.00 25.63 26.25
Dimension Drawing
S-5550
9
8
127 lbs
208 lbs
221 lbs
847 lbs
943 lbs
1214 lbs
1330 lbs
1423 lbs
Dimension Drawing
S-5543
55.35 25.63 14.66
Dimension Drawing
S-5545
NOT REQUIRED
164 lbs
291 lbs
307 lbs
P7B-00
Note 2: The underscore position in these model numbers codes for the enclosure type: V = NEMA1, B = NEMA12 FVFF.
Note 3: Heat loss is the amount of heat dissipated by the drive at full load with all standard options available inside the enclosure. Drive heat sink losses are included in the heat loss data. Heat loss data is for the enclosure without the add-on enclosure.
Note 4: Height dimension (H) excludes the mounting screw tabs. Depth dimension (D) excludes MCP disconnect handle.
Note 5: This data represents the total weight with all possible standard options. Weight could be less depending on the options specified.
Note 6: All standard options are available in this size enclosure except options E (RFI Filter) and K (5% Output Reactor). Options E and K require the add-on enclosure.
Note 7: All options are available in this size enclosure except E (RFI Filter), R (3% Line Reactor), and K (5% Output Reactor). Only option E combined with either option R or option K can be installed in the add-on enclosure. Options R and K together require an increase in the size of the P7 Bypass Enclosure.
Contact the factory if all three options are required. Options D (2 Motor “OR”) or A (2 Motor “AND”) for 30 Hp and 40 Hp require the next size enclosure.
Note 8: Heat sink mounted externally varies the depth dimension depending on the drive size. Depth will not exceed dimension shown.
Note 9: All options are available in this size enclosure except options D (2 Motor “OR”) or A (2 Motor “AND”) for 75 Hp and 100 Hp require the next size enclosure.
Physical Installation 1 - 5
Table 1.4 480V Enclosure Data
Input
Volts
480
HP
1
100
125
150
200
40
50
60
75
250
300
350
400
450
15
20
25
30
5
7.5
10
0.5
0.75
1
2
3
Drive
Model
CIMR-
Bypass
2
Model
Number
P7U42P21A P7B_B001
P7U42P21A P7B_B001
P7U42P21A P7B_B002
P7U42P21A P7B_B003
P7U42P21A P7B_B004
P7U43P71A P7B_B007
P7U45P51A P7B_B011
P7U47P51A P7B_B014
P7U40111A
P7U40111A
P7B_B021
P7B_B027
P7U40151A P7B_B034
P7U40181A P7B_B040
NEC
FLA
P7U40301A P7B_B052
P7U40301A P7B_B065
P7U40371A P7B_B077
P7U40451A P7B_B096
52.0
65.0
77.0
96.0
57.2
71.5
84.7
105.6
P7U40551A P7B_B124 124.0
136.4
P7U40750A P7B_B156 156.0
171.6
P7U40900A P7B_B180 180.0
198.0
P7U41100A P7B_B240 240.0
264.0
P7U41600A P7B_B302 302.0
332.2
P7U41850A P7B_B361 361.0
397.1
P7U41850A P7B_B414 414.0
455.4
P7U42200A P7B_B477 477.0
524.7
P7U42200A P7B_B515 515.0
566.5
8.4
12.1
15.4
23.1
29.7
37.4
44.0
1.2
1.8
2.3
3.7
5.3
7.6
11.0
14.0
21.0
27.0
34.0
40.0
1.1
1.6
2.1
3.4
4.8
OL
110%
1 min
4225
4425
4451
5099
5154
1749
2032
2486
2955
1040
1045
1197
1357
155
217
318
404
408
485
618
Heat
3
Loss
Watts
Enclosure Dimensions
4
NEMA 1 & NEMA 12 -FVFF
H W D inches
57
57
62
89
121
29.48 19.06 13.66
Weight
5 of
Assembly
Enclosure Dimensions w/Add-on
4
NEMA 1 & NEMA 12-FVFF
H W D inches
Weight
5 of
Assembly
+Add-on
Box
Electrical
Schematic
115 lbs
43.35 19.06 13.66
156 lbs
Dimension Drawing
S-5542
6
127 lbs
142 lbs
Dimension Drawing
S-5543
164 lbs
189 lbs
40.48 25.63 14.66
Dimension Drawing
S-5544
Dimension Drawing
S-5550
TBD
7
84.00 25.63 26.25
9
8
203 lbs
232 lbs
241 lbs
943 lbs
1240 lbs
1352 lbs
TBD
55.35 25.63 14.66
Dimension Drawing
S-5545
NOT REQUIRED
281 lbs
319 lbs
332 lbs
P7B-00
500 P7U43000A P7B_B590 590.0
649.0
7329
Note 1: Horsepower rating is based on a standard NEMA B 4-pole motor.
Note 2: The underscore position in these model numbers codes for the enclosure type: V = NEMA1, B = NEMA12 FVFF.
Note 3: Heat loss is the amount of heat dissipated by the drive at full load with all standard options available inside the enclosure. Drive heat sink losses are included in the heat loss data. Heat loss data is for the enclosure without the add-on enclosure.
Note 4: Height dimension (H) excludes the mounting screw tabs. Depth dimension (D) excludes MCP disconnect handle.
Note 5: This data represents the total weight with all possible standard options. Weight could be less depending on the options specified.
Note 6: All standard options are available in this size enclosure except options E (RFI Filter) and K (5% Output Reactor). Options E and K require the add-on enclosure.
Note 7: All options are available in this size enclosure except E (RFI Filter), R (3% Line Reactor), and K (5% Output Reactor). Only option E combined with either option R or option K can be installed in the add-on enclosure. Options R and K together require an increase in the size of the P7 Bypass Enclosure.
Contact the factory if all three options are required. Options D (2 Motor “OR”) or A (2 Motor “AND”) for 75 Hp and 100 Hp require the next size enclosure.
Note 8: Heat sink mounted externally varies the depth dimension depending on the drive size. Depth will not exceed dimension shown.
Note 9: All options are available in this size enclosure except options D (2 Motor “OR”) or A (2 Motor “AND”) for 200 Hp and 250 Hp require the next size enclosure.
Physical Installation 1 - 6
Confirmations upon Delivery
!
Receiving Checks
Check the following items as soon as the Drive and Bypass unit is delivered.
Item
Has the correct model of Bypass unit been delivered?
Table 1.5 Checks
Method
Check the model number on the nameplate on the right side of the Bypass unit.
Reconcile with packing slip and/or order information.
Is the Bypass unit damaged in any way?
Inspect the entire exterior of the Bypass unit to see if there are any dents, scratches or other damage resulting from shipping.
Are any screws or other components loose?
Use a screwdriver or the appropriate tool to check for tightness.
If you find any irregularities in the above items, contact the shipping company, the distributor or representative you purchased the Bypass unit from or your Yaskawa office immediately.
The Bypass unit is thoroughly tested at the factory. Any damages or shortages evident when the equipment is received must be reported immediately to the commercial carrier that transported the material. Shipping damage is not covered by the Yaskawa warranty. After unpacking and inspecting for damage, verify that internal wire connections have not come loose during shipment by spot checking wire terminations with a screwdriver or the appropriate tool.
Bypass unit storage must be in a clean and dry location. Maintain the factory packaging and provide covering as needed to protect the Bypass unit from construction site dirt, water, debris and traffic prior to and during construction.
!
Bypass Nameplate Information
A nameplate is attached to the right side of the enclosure and the inside of the door of each Bypass unit.
The nameplate shown below is an example for a standard Bypass unit.
Volts: 480
Phase: 3
Volts: 0-480
Phase: 3
A.C. INPUT
Hz: 50/60
Amps: 71.6
A.C. OUTPUT
Hz: 0-60
Amps: 65
Serial No: 4W033727440-0002
Model No: P7BVB065R
Type: P7 BYPASS
W.D.: P7B-00
Inst. Manual: TM.P7B.01,CD.AFD7.01
UNPN0001
Fig 1.1 Bypass Nameplate
(Example)
Physical Installation 1 - 7
"
Drive Nameplate Information
A nameplate is also attached to the right side of the Drive inside the Bypass enclosure. The following nameplate is an example for a standard Drive.
Drive Model Number
CIMR-P7U2011
Drive Enclosure and
Revision Code
Input Power Specifications
Output Power Specifications
Weight
Serial Number
UL File Number
Fig 1.2 Drive Nameplate
(Example)
"
Bypass Unit Model Numbers
The model number on the nameplate of the Bypass unit indicates the enclosure, voltage, Drive rated current and options of the
Bypass unit in alphanumeric codes.
BASE NUMBER
P 7 B V B 0 9 6
OPTIONS
- - - R - - S - - L
P7 Bypass Configuraton
V
B
Enclosure
NEMA 1
NEMA 12
D
A
B
Voltage
208V
230/240V
480V
Current
NEC Rated Amps
(Ex.: "096" = 96A)
-
D
A
Motor Control
1 Motor (Standard)
2 M otor "OR"
2 Motor "AND"
-
N
E
Input Filter
None (Leave Blank)
Cap Filter
RFI Filter
-
F
Input Fuses
None (Leave Blank)
Fuses
(1) 3% and 5% Bus Reactors are only available as an option on Drives up to
25HP at 208V and 30HP at 480V; larger Drives have a Bus Reactor as standard
(2) 3% Input Reactor, when combined with the standard Bus Reactor (available on drives above 25HP at 208V and 30HP at 480V), yields a total of 5% input impedance
Fig 1.3 Bypass Unit Model Number
-
G
Communications
Not Enabled (Leave Blank)
DeviceNet
H
Profibus
L LonWorks
Q Ethernet
V Modbus (Internal)
-
M
4-20mA Output
None (Leave Blank)
4-20mA Output
-
P
3-15 PSI Transducer
None (Leave Blank)
3-15 PSI Transducer
-
S
Speed Pot
None (Leave Blank)
Speed Pot
-
W
Custom Nameplates
None (Leave Blank)
Custom Nameplates
-
K
Load Reactor
None (Leave Blank)
5% Load Reactor
Z
R
-
X
Line Impedance
None (Leave Blank)
3% Bus Reactor (1)
5% Bus Reactor (1)
3% Input Reactor (2)
!
Bypass Unit Enclosures
All Bypass units are intended for non-hazardous locations. Various enclosure types are provided to protect against the application environmental conditions:
Nema Type 1 Enclosures
are constructed for indoor use to provide a degree of protection against incidental contact with enclosed electrical equipment and falling dust or dirt.
NEMA Type 12 FVFF Enclosures.
NEMA provides for both non-ventilated and ventilated NEMA 12 enclosures. When ventilated, a suffix to the type number defines the ventilation method. A NEMA 12 FVFF enclosure has Forced Ventilation with inlet air Filter and outlet air Filter. The internal pressure is positive with respect to the ambient pressure. UL does not recognize NEMA 12 ventilated enclosures, therefore, these enclosures are designated NEMA 1 for UL purposes.
Physical Installation 1 - 8
Bypass Product Options
Option A - Two motor “AND” control: Allows the operation of two motors from one Drive or Bypass. Pump #1 “AND” pump #2 are operated at the same speed via the output from one Drive or Bypass. The motors are always operated simultaneously therefore, no transfer switch is involved. With the 2 motor “AND” option, motor OverLoad Relays and fuses are provided for each motor and the Drive’s internal motor overload function is disabled.
The two motors can be of different capacity if this capacity difference was considered in the ordering process. The factory needs to know the FLA value of each motor controlled in order to select the correct motor overload devices and fuses.
(Specifying different capacity motors results in longer, non-standard lead times).
Option D - Two motor “OR” control: A MTR #1/AUTO/MTR #2 selector switch is provided to allow local or remote motor operation selection, between two identical motors, for control by either the Drive or the Bypass (for example, Pump #1 “OR”
AUTO “OR” Pump #2). In the AUTO position, a customer supplied contact closure at TB1 terminals 23 and 24 can switch between the two motors. The two motors must be the same horsepower and current draw.
Option E - RFI/EMI Filter: Filters to further attenuate possible VFD generated noise. Radio frequency interference/electro magnetic interference filters reduce conducted noise on the Drive input power leads and therefore, radiated noise from those leads. This option is installed on the input power side of the Drive, between the input contactor and the Drive.
Option F - Drive Input Fuses: Fuses capable of protecting semiconductor devices, rated at 200 kAIC are connected to the line side of the Drive, between the input contactor and the Drive, to protect the Drive semiconductors when motor or output conductor short circuit faults occur.
Option G - Serial Communication, DeviceNet: An option card that provides DeviceNet protocol for network communication.
Option H - Serial Communication, Profibus: An option card that provides Profibus protocol for network communication.
Option K - 5% Output Reactor: Employed on the output side of the Drive for reduction of peak voltages applied to the driven motor. In long Drive to motor lead length situations, high carrier frequency and reflected waves can cause high voltage spikes at the motor. An output reactor provides motor protection in these long motor lead length situations. This option is installed on the output power side of the Drive, between the output contactor and the Drive.
Option L - Serial Communication, Echelon LonWorks: An isolated RS-422/485 circuit board provides LonTalk protocol for network communication. This option plugs into the CN2 connection on the Drive control circuit board.
Option M - 4 to 20 mA Output: Provides two programmable 0 to 10 VDC analog outputs or two programmable 4 to 20 mA analog outputs.
Option N - Input Capacitive Network Radio Frequency Interference Filter: Electronic equipment can be sensitive to low levels of voltage distortion and electrical noise. This passive wye-delta capacitve filter is intended for installation on the VFD input in order to protect other sensitive electronic loads, it provides attenuation of conducted RFI and EMI.
Option P - Pressure to Electrical Transducer: This transducer is employed when converting a pneumatic signal to an electrical signal for use as the Drive speed command input. The need for this option comes up on retrofit applications when the pneumatic signal that formerly controlled the pneumatic actuator on Inlet Guide Vanes (IGV), for example, is now to be used to control the fan speed via the Drive. This option is wired to Drive terminals +V, A2 and AC, parameters H3-10 and
H3-11 are used for final field calibration of this input if there is jobsite variation from the typical 3 to 15 PSIG pneumatic signal input range.
Physical Installation 1 - 9
Option Q - Serial Communication, Ethernet: An option card that provides Modbus TCP protocol for network communication.
Option R - 3% Input Line Reactor: Employed on the input side of the Drive for Total Harmonic Distortion (THD) suppression. A line reactor also minimizes the potential for Drive input diode damage from line transients and reduces voltage peaks on the DC bus capacitors. This option is installed on the input power side of the Drive, between the input contactor and the
Drive.
Option S - Speed Potentiometer: A door mounted single turn potentiometer for manual control of Drive output and motor speed. This option is wired to Drive terminals +V, A1 and AC and is used as the local speed command input to the Drive instead of the keypad up and down arrows. Parameters for use of this option in conjunction with other input signals are detailed in Table 5.2.
Option V - Embedded Serial Communication, Modbus: A no cost option. The Drive in a Bypass unit is capable of Modbus network communication via the standard RS-422/485 terminals.
Option W - Engraved Plastic Nameplate: An enclosure identification nameplate to carry the controlled equipment “tag number”.
Option X - 3% DC Bus Reactor: Attenuates harmonic distortion by limiting the rate of rise of the input current. The bus reactor is wired to the Drive (+1) and (+2) DC bus terminals to provide the equivalent impedance of a 3% input reactor. This option is only used on the low end of the horsepower range where DC bus reactors are not a standard Drive component (25 HP and below @ 208 VAC, 25 HP and below @ 240 VAC, and 30 HP and below @ 480 VAC.)
Option Z - 5% DC Bus Reactor: Attenuates harmonic distortion by limiting the rate of rise of the input current. The bus reactor is wired to the Drive (+) and (-) DC bus terminals to provide the equivalent impedance of a 5% input reactor. This option is only used on the low end of the horsepower range where DC bus reactors are not a standard Drive component
(25 HP and below @ 208 VAC, 25 HP and below @ 240 VAC, and 30 HP and below @ 480 VAC.)
Physical Installation 1 - 10
Bypass Component Descriptions
!
Bypass Unit Front Control Panel
The external appearance, component names, and terminal arrangement of the Bypass unit is shown in Figures 1.4 through 1.8.
MCP
Disconnect
Keypad
Operator
Indicating Lights
Selector Switches
P7
Fig 1.4 E7 Bypass Unit Appearance
"
Keypad Operator
In a Bypass unit the keypad operator is mounted flush with the hinged door of the enclosure. The addition of a HAND/
OFF/AUTO selector switch for the Bypass logic circuit makes the Hand, Off and Auto keys on the standard Drive keypad operator redundant. In this Bypass configuration the keypad Hand, Off and Auto keys are disabled in the Drive firmware and a mask (membrane) is placed over the keypad operator to cover these keys, avoiding the potential for confusion. The membrane over the Drive keypad is non-removable on these Bypass units (In order to use the keypad copy function on a Bypass unit - order a separate keypad.
"
Indicating Lights
On the enclosure door just below the digital operator are six 22 mm, 24 VAC LED indicating lights for: “Control Power”,
“Drive Run”, “Bypass Run”, “Motor OL/Safeties Fault “Drive Fault” and “Smoke Purge”. LED type indicating lights are provided to improve the reliability well beyond that of incandescent bulbs. LED’s have a MTBF of 100K hours, eliminating any need for “push to test” type pilot lights.
Physical Installation 1 - 11
"
HAND/OFF/AUTO Selector Switch
A three position rotary switch employed to control the source of the motor start and speed commands in either the Drive or
Bypass operating modes.
Hand Position – Drive Mode: The Drive input and output contactors are energized and the Drive is given a run command.
Operation is via the local speed input from the keypad or optional speed potentiometer.
Hand Position – Bypass Mode: The Bypass contactor is energized causing the motor to run at full speed directly across-theline.
Off Position: No power is applied to the Bypass circuit. The Drive input and output contactors are energized and the Drive is stopped (run command removed). The Off position takes precedence over a serial communication run command.
Auto Position – Drive Mode: The Drive input and output contactors are energized. The Drive is enabled to receive a run command contact closure and speed input analog signal from a separate source.
Auto Position – Bypass Mode: The motor full speed across-the-line run/stop is controlled by a customer supplied contact closure, energizing the Bypass contactor.
The H/O/A switch must be in the AUTO position if serial communication is to be used for Drive run, stop and speed control.
"
DRIVE/BYPASS Selector Switch
A two position rotary switch selecting motor operation from the Drive or directly across-the-line. When transferring from
Drive operation to Bypass operation, the logic circuit will require the Bypass unit to stop the motor before completing the transfer to full speed across-the-line operation.
"
NORMAL/TEST Selector Switch
A two position rotary switch, test position is used to energize the Drive input contactor while operating in the Bypass mode
(via the HAND or AUTO switch position). In Drive mode switching from NORMAL to TEST position will remove the power from the Drive and the motor will stop. In Bypass mode the test position powers the Drive for programming or other
“tests” while keeping it isolated from the motor.
"
MCP Motor Circuit Protector Circuit Breaker/Disconnect
Electrically located on the input power side of the Bypass unit, the MCP adjustable, instantaneous trip circuit breaker provides protection from short circuits for the motor power cables. The Bypass three phase input power connection is made to the input terminals of the MCP. The door mounted rotary operating mechanism is a convenient means of disconnecting the Bypass unit from line power for equipment maintenance. The MCP must be in the OFF position in order to open the enclosure door.
Service and troubleshooting personnel are provided with a means to defeat this door interlock. The rotary handle provides trip indication and can be padlocked in the OFF position.
CAUTION
Only qualified service personnel should use the defeator feature.
Defeator
Fig 1.5 MCP Handle Positions – RESET/LOCK, OFF, TRIP, ON Shown in the “ON” position
Physical Installation 1 - 12
"
Internal Bypass Panel
Fig 1.6 MCP Handle Positions – Shown OFF, With Padlock
Customer Wiring
Terminal Strip (TB1)
PCB A2
Drive
Line
Connections
Digital Operator
Motor Circuit
Protector
Load
Connections
Overload
Relay
PCB A3
Control Power
Transformer
Input
Contactor
(K1)
Fig 1.7 Internal Bypass Panel
Bypass
Contactor
(K3)
Output
Contactor
(K2)
Physical Installation 1 - 13
TB1 Label Defining
Customer Control
Circuit Connection
Points
TB1 with Terminal Numbers
Printed on the PCB
Fig 1.8 Control Terminal Strip
Slide Switches for switch selectable functions (Auto
Transfer, Remote Transfer and
Smoke Purge) are behind this ribbon cable connector. See
Fig. 1.9 for details.
"
Contactors
The Bypass is a “3 contactor Bypass” circuit employing IEC rated contactors in an electrically interlocked arrangement to allow mutually exclusive operation in Drive or Bypass modes. To minimize enclosure space requirements, they are mounted in a 3 contactor assembly.
The control logic and “soft start” characteristic of the Drive limit the Drive input and output contactors to motor FLA current or less. For this reason, the Drive input and output contactors have lower current ratings than the Bypass contactor. The Bypass contactor is exposed to motor inrush current (LRA) when starting the motor across-the-line and therefore requires a higher current rating.
"
OverLoad Relay
The OverLoad Relay (OLR) is mounted to the contactor assembly or back panel (depending on rating), just above the Bypass contactor (see Figure 1.7). Electrically on the output power side of the Bypass unit, the adjustable thermal OLR provides overload protection for the motor in both the Drive and Bypass operating modes. The Bypass three phase output power connection to the motor is made to the output terminals of the overload relay. The OLR is set up in the factory to be a manual reset device, requiring operator attention if an overload trip-out is experienced.
"
Control Power Transformer
A Control Power Transformer (CPT) is provided to power the Bypass 120 VAC control circuit. The VA capacity is determined by the control circuit and optional functions specified for the unit. 100 VA of extra transformer capacity for customer control logic is provided in the standard unit and additional capacity is available as an “engineered” or “custom” option. The CPT primary is fused in both legs, the secondary is fused when required by NEC (above 350 VA). One side of the transformer secondary is grounded to the Bypass enclosure.
"
Relay and Selector Switch Logic
Operating elements such as indicating lights and selector switches, as well as the control relay logic, have been incorporated into a PCB assembly to eliminate the potential for loose wires after shipment and to control factory costs.
The operating elements are located on PCB A3, mounted to the inside of the enclosure door and ribbon cable connected to the control relay logic PCB A2.
The control relay logic PCB A2 is mounted to the left hand side of the enclosure and contains the control circuit field wiring terminal strip (TB1).
"
Drive/Bypass logic interlocks explained
The Bypass 120 VAC relay logic circuit is interconnected with the Drive multi-function digital input terminals and multifunction digital output terminals to allow a single customer interface to control both Drive and Bypass circuits. Some of these terminals are therefore not available for other field use.
Physical Installation 1 - 14
Drive Multi-function input terminals:
Terminal S
1
receives the Drive run command from the 120 VAC relay logic circuit.
Terminal S
3
receives the Drive run enable signal from the 120 VAC relay logic circuit.
Terminal S
5
receives the Drive local/remote command from the 120 VAC relay logic circuit via the HAND/OFF/
AUTO and NORMAL/TEST selector switch.
Drive Multi-function output terminals:
Terminals M
1
and M
2
are a normally open Drive run relay contact used to communicate the Drive operational mode to the 120 VAC relay logic circuit.
Terminals M
3
and M
4
are a normally open serial com. run status relay contact used to communicate the Drive operational state to the 120 VAC relay logic circuit.
Terminals M
A
and M
C
are a normally open Drive fault relay contact used to communicate the Drive fault status to the
120 VAC relay logic circuit.
"
PCB Jumpers explained
The S101 “Berg pin” jumper on the control relay logic PCB A2 is not for field use. It is employed only in the factory to enable the 2 motor “OR” configured option. It is removed when this option is present and must be in place when this option is not part of the unit specification (See Figure 1.9).
The S102 “Berg pin” jumper on the control relay logic PCB A2 is not for field use. It is employed only in the factory to enable the Run/Stop Push Button (3 wire control) configured option. It is removed when this option is present and must be in place when this option is not part of the unit specification (See Figure 1.9).
TB1 terminals 1 and 2 are jumpered (J1) as the unit is shipped from the factory. If a customer supplied series circuit of NC safety devices is to be used, this jumper is removed and the safety circuit connected between terminals 1 and 2.
TB1 terminals 5 and 6 are jumpered (J2) as the unit is shipped from the factory. If a customer supplied Drive NO enabling contacts are to be used (such as a damper end switch or occupied cycle timer), this jumper is removed and the enabling contacts wired between terminals 5 and 6.
Physical Installation 1 - 15
"
Switch Selectable Functions:
The slide switches used to select these functions are located on the relay controller Printed Circuit Board (PCB) A2
(See Figure 1.9). The factory default is for these functions to be de-selected.
Smoke Purge: When enabled (switch S105) this function allows a contact closure, between terminals 17 and 18 of
TB1, to transfer motor operation to bypass for a maximum capacity smoke control function. When in smoke purge mode, during emergency fire/smoke situations, the motor overloads and safety interlock circuit are overridden to shift the priority to protecting people rather than equipment.
Auto Transfer to Bypass: If enabled (switch S103), the P7 Bypass unit will automatically transfer the motor operation from Drive to Bypass in the event of a Drive fault. When the Drive fault condition has cleared, this function is reset by moving the H/O/A switch to the OFF position, waiting for the keypad to go blank, then switching back to the
DRIVE position.
IMPORTANT
Before selecting this function in fan applications, care must be taken to ensure that the duct-work is designed to handle the pressure resulting from full speed operation with the VAV terminal unit dampers at minimum position or closed.
Remote Transfer to Bypass: When selected (switch S104) this function allows a contact closure from a separate source, between terminals 25 and 26 of TB1, to transfer motor operation from Drive mode to Bypass mode. This remote tranfer to Bypass function overrides the DRIVE/BYPASS manual switch.
Slide Switches
Fig 1.9 Printed Circuit Board A2
PCB Jumpers
Physical Installation 1 - 16
Exterior and Mounting Dimensions
!
Bypass Unit 30 HP and Below, 480 VAC; 15 HP and Below, 208V/240V
Ø0.50(4PLS)
(Ø12.7)
MIN. 6
(152.4)
0.75
(19)
32.00
(812.8)
FWD REV SEQ REF
AUTO
ALARM
RUN
Monitor
MENU
ESC
DATA
ENTER
STOP
RESET
P7
BYPASS
RUN
CONTROL
POWER ON
DRIVE
RUN
MOTOR OL/
SAFETIES FAULT
SMOKE
PURGE
DRIVE
FAULT
TEST NORMAL BYPASS DRIVE HAND
OFF
AUTO
29.48
(748.8)
0.75
(19)
1.29
(32.8)
MIN. 1.50
(3.81)
16.50
(419.1)
19.06
(484.1)
2.37
(60.2)
RECOMMENDED
CONDUIT
ENTRANCE AREA
TOP, BOTTOM
AND SIDE
MIN. 6
(152.4)
13.66
(347)
2.50
(63.5)
DIMENSIONS IN INCHES (MM), FOR REFERENCE ONLY
Fig 1.10 Enclosure 1 for up to 30HP, 480 VAC
NEMA 1 and NEMA 12 FVFF Enclosures
Physical Installation 1 - 17
TOP VIEW
!
Bypass Unit 30 HP and Below, 480 VAC; 15 HP and Below, 208V/240V
With Add-On Box
16.50
(419.1)
19.06
(484.1)
1.29
(32.8)
0.75
(19)
Ø0.50(4PLS)
(Ø12.7)
MIN. 6
(152.4)
44.60
(1132.8)
32.00
(812.8)
FWD REV SEQ
AUTO
REF ALARM
RUN
Monitor
MENU
ESC
DATA
ENTER
STOP
RESET
P7
BYPASS
RUN
CONTROL
POWER ON
DRIVE
RUN
MOTOR OL/
SAFETIES FAULT
SMOKE
PURGE
DRIVE
FAULT
TEST NORMAL BYPASS DRIVE HAND
OFF
AUTO
12.60
(317.5)
0.75
(19)
MIN. 1.50
(3.81)
13.50
(342.9)
29.48
(748.8)
43.35
(1,101.2)
13.87
(3.81)
5.37
(136.4)
2.37
(60.2)
RECOMMENDED
CONDUIT
ENTRANCE AREA
TOP, BOTTOM
AND SIDE
9.1
(231.1)
3.375
(85.7)
13.66
(347)
2.50
(63.5)
TOP VIEW
DIMENSIONS IN INCHES (MM), FOR REFERENCE ONLY
Fig 1.11 Enclosure 1, with Options Extension, for up to 30HP, 480 VAC
NEMA 1 and NEMA 12 FVFF Enclosures
Physical Installation 1 - 18
!
Bypass Unit 40 HP to 100 HP, 480 VAC; 20 HP to 40 HP, 208V/240V
Ø0.50 (4PLS)
(Ø12.7)
MIN. 6
(152.4)
0.75
(19)
43.00
(1092.2)
FWD REV SEQ REF
AUTO
ALARM
RUN
Monitor
MENU
ESC
DATA
ENTER
RESET
STOP
P7
BYPASS
RUN
CONTROL
POWER ON
DRIVE
RUN
MOTOR OL/
SAFETIES FAULT
SMOKE
PURGE
DRIVE
FAULT
TEST NORMAL BYPASS DRIVE HAND
OFF
AUTO
40.48
(1028.2)
0.75
(19)
1.32
(33.5)
MIN. 1.50
(3.81)
23.00
(584.2)
23.00
(584.2)
2.37
(60.2)
RECOMMENDED
CONDUIT
ENTRANCE AREA
TOP, BOTTOM
AND SIDE
MIN. 6
(152.4)
14.66
(372.4)
3.50
(88.9)
DIMENSIONS IN INCHES (MM), FOR REFERENCE ONLY
Fig 1.12 Enclosure 2, for 40HP to 100HP, 480 VAC
NEMA 1 and NEMA 12 FVFF Enclosures
Physical Installation 1 - 19
TOP VIEW
!
Bypass Unit 40 HP to 100 HP, 480 VAC; 20 HP to 40 HP, 208V/240V
With Add-On Box
1.32
(33.5)
0.75
(19)
23.00
(584.2)
25.63
(651)
Ø0.50 (4PLS)
(Ø12.7)
MIN. 6
(152.4)
43.00
(1092.2)
56.60
(1437.6)
FWD REV SEQ
AUTO REF ALARM
RUN
Monitor
MENU ESC
DATA
ENTER
STOP
RESET
P7
BYPASS
RUN
CONTROL
POWER ON
DRIVE
RUN
MOTOR OL/
SAFETIES FAULT
SMOKE
PURGE
DRIVE
FAULT
TEST NORMAL BYPASS DRIVE HAND
OFF
AUTO
40.48
(1028.2)
55.35
(1431.3)
13.60
(345.4)
0.75
(19)
14.87
(377.7)
MIN. 1.50
(3.81)
18.00
(457.2)
7.44
(189)
2.37
(60.2)
RECOMMENDED
CONDUIT
ENTRANCE AREA
TOP, BOTTOM
AND SIDE
9.1
(231.1)
4.375
(111.1)
14.66
(372.4)
3.50
(88.9)
TOP VIEW
DIMENSIONS IN INCHES (MM), FOR REFERENCE ONLY
Fig 1.13 Enclosure 2, with Options Extension, for up to 40HP to 75HP, 480 VAC
NEMA 1 and NEMA 12 FVFF Enclosures
Physical Installation 1 - 20
!
Bypass Unit 125 HP to 250 HP, 480 VAC; 50 HP to 125 HP, 208V
THIS DIMENSION IS 23.50 IF
A MA FRAME CIRCUIT
BREAKER IS USED
EYEBOLTS ARE
REMOVABLE
MIN. 10.00
(254)
P7
15.00
(381)
CIRCUIT
BREAKER
HANDLE
LOCATION
84.00
(2133.6)
1.70
(43.2)
42.00
(1066.8)
37.75
(958.8)
20.00
(508)
RECOMMENDED
CONDUIT
ENTRANCE AREA
TOP AND BOTTOM
MIN. SPACE REQ'D TO OPEN DOOR
35.50
(901.7)
3.00
(76.2)
13.00
(330.2)
20.00
(508)
.62
(15.8)
(4 PLS)
1.38
(35.1)
1.00
(25.4)
35.00
(889)
1.00
(25.4)
10.00
(254)
TOP VIEW
FOR BOTTOM CONDUIT ENTRY, DUE TO POSSIBLE INTERFERENCE WITH OPTIONAL EQUIPMENT MOUNTED
INTERNALLY, VERIFY SPECIFIC REQUIREMENTS WITH THE FACTORY.
DIMENSIONS IN INCHES (MM), FOR REFERENCE ONLY
Fig 1.14 Enclosure F1, for 125HP to 250HP, 480 VAC
NEMA 1 and NEMA FVFF 12 Enclosures
Physical Installation 1 - 21
5.00
(127)
12.00
(304.8)
COVER PLATE
3.00
(76.2)
!
Dimensions and Weights
Rated
Input
Voltage
208V
240V
230V
343
396
2.2
3.2
4.0
6.8
9.6
59.4
74.8
88
114
143
169
211
273
2.4
3.5
4.6
7.5
10.6
16.7
24.2
30.8
46.2
130
154
192
248
312
360
15.2
22
28
42
54
68
80
104
Continuous
Output
Current (Amps)
1
2
3
125
150
1/2
3/4
50
60
75
100
20
25
30
40
1/2
5
7.5
10
15
3/4
1
2
3
50
60
75
100
125
150
20
25
30
40
5
7.5
10
15
Nominal
HP
(1)
Table 1.6 Bypass Dimensions and Weights
Bypass
_ _ _
_
NEMA 1 and NEMA 12
Dimensions inches (mm)
Height
(2)
Width Depth
Wall
Mounting
Dimensions
H x W
Drawing
Number
Drawing
Number
(w/ Add-on
Box)
(3)
D343
D396
A002
A003
A004
A006
A009
D059
D074
D088
D114
D143
D169
D211
D273
D002
D003
D004
D007
D010
D016
D024
D030
D046
A130
A154
A192
A248
A312
A360
A015
A022
A028
A042
A054
A068
A080
A104
32.00
(812.8)
43.00
(1092.2)
84.00
(2133.6)
32.00
(812.8)
43.00
(1092.2)
84.00
(2133.6)
19.06
(484.1)
25.63
(651.0)
37.75
(958.9)
19.06
(484.1)
25.63
(651.0)
37.75
(958.9)
16.03
(407.2)
17.03
(432.6)
21.7
(551.2)
16.03
(407.2)
17.03
(432.6)
21.7
(551.2)
30.5 x 16.5
(774.7) x
(419.1)
41.5 x 23.0
(1054.1 x
584.2)
Floor Mount
W x D
35.0 x 13.0
(889 x 330.0)
30.5 x 16.5
(774.7) x
(419.1)
41.5 x 23.0
(1054.1 x
584.2)
Floor Mount
W x D
35.0 x 13.0
(889 x 330.0)
S-5542
S-5544
S-5550
S-5542
S-5544
S-5550
S-5543
S-5545
N/A
S-5543
S-5545
N/A
Weight
(lbs)
(4)
115
127
208
115
127
208
221
847
943
1214
1330
1376
221
847
943
1214
1330
1423
(1) Horsepower rating is based on standard NEMA B 4-pole motor design
(2) Height dimension includes the mounting screw tabs.
(3) Add-on box adds 13.6 inches to Height dimension and 91 lbs. Max. to total
(4) Data represents the total weight of the Drive with all possible standard options, not shipping weight.
Physical Installation 1 - 22
Rated
Input
Voltage
480V
40
52
65
77
14
21
27
34
1.1
1.6
2.1
3.4
4.8
7.6
11
96
124
156
180
240
302
Continuous
Output
Current (Amps)
B002
B003
B004
B007
B011
B014
B021
B027
B034
B040
B052
B065
B077
B096
B124
B156
B180
B240
B302
Table 1.6 Bypass Dimensions and Weights (Continued)
Nominal
HP
(1)
Bypass
_ _ _
_
NEMA 1 and NEMA 12
Dimensions inches (mm)
Height
(2)
Width Depth
Wall
Mounting
Dimensions
H x W
30
40
50
60
10
15
20
25
1/2
3/4
1
2
3
5
7.5
75
100
125
150
200
250
B001
32.00
(812.8)
43.00
(1092.2)
84.00
(2133.6)
19.06
(484.1)
25.63
(651.0)
37.75
(958.9)
16.03
(407.2)
17.03
(432.6)
21.7
(551.2)
30.5 x 16.5
(774.7) x
(419.1)
41.5 x 23.0
(1054.1 x
584.2)
Floor Mount
W x D
35.0 x 13.0
(889 x 330.0)
Drawing
Number
Drawing
Number
(w/ Add-on
Box)
(3)
S-5542
S-5544
S-5550
S-5543
S-5545
N/A
Weight
(lbs)
(4)
115
127
142
203
232
241
943
1240
1352
(1) Horsepower rating is based on standard NEMA B 4-pole motor design
(2) Height dimension includes the mounting screw tabs.
(3) Add-on box adds 13.6 inches to Height dimension and 91 lbs. Max. to total
(4) Data represents the total weight of the drive with all possible standard options, not shipping weight.
Physical Installation 1 - 23
Checking and Controlling Installation Site
Install the Bypass unit as described below and maintain the specified operating conditions.
!
Installation Site
Location of the Bypass unit is important to achieving proper performance and design operating life. Install the Bypass unit as close as possible to the motor. The NEMA type 1 & 12 enclosed units should be installed in an area where it will be protected from: Direct sunlight, rain or moisture, corrosive gasses or liquids, vibration and dust or metallic particles. The ambient air available for cooling the unit should be 104° F (40° C) or less.
Wall mount units require a minimum 6 inch clearance above and below, to achieve adequate heat sink cooling. When the addon box is employed for optional equipment, no additional bottom clearance is required.
No side clearance is required for cooling because the cooling air flow is in and out of the enclosure door at the front surface of the unit (do not block the air flow louvers). Clearance for the opening swing of the enclosure door should be considered when placing these units. The door is hinged on the left and must open through at least a 90 degree swing with a 120 to 180 degree swing being preferable (minimum clearance is 1.5”).
Floor mounted units require a minimum clearance of 10 inches above the enclosure to allow for air flow over the heat sink fins.
Install the Bypass unit under the following conditions in UL pollution degree 1 & 2 environments. This excludes wet locations where surfaces may become conductive due to moisture and contaminant loading.
Type
NEMA Type 1 & 12
Table 1.7 Installation Site
Ambient Operating Temperature
14 to 104
°
F (-10 to + 40
°
C) 95% RH or -
Humidity less (no -
Plenum Rated condensation) Yes
Observe the following precautions when mounting the Bypass unit.
•
Install the Bypass unit in a clean location that is free from oil mist and dust.
•
Install the Bypass unit in an environment where metal shavings, oil, water, or other foreign matter will not get into the
Bypass enclosure.
•
Install the Bypass unit in a location free from radioactive materials.
•
Install the Bypass unit in a location free from harmful gasses and liquids.
•
Install the Bypass unit in a location without excessive vibration.
•
Install the Bypass unit in a location free from chlorides.
•
Install the Bypass unit in a location not in direct sunlight.
•
Install the Bypass unit on a non-combustible surface.
Physical Installation 1 - 24
!
Controlling the Ambient Temperature
To enhance the reliability of operation, the Bypass unit should be installed in an environment free from extreme temperature variations. Do not store this Technical Manual or any other documents on the top surface of the Bypass unit, they may cover the heat sink cooling air discharge opening and cause the unit to overheat.
If the Bypass unit is installed in an enclosure (such as an electrical control box in an air handling unit), use a cooling fan or air conditioner to maintain the Bypass unit internal air temperature below 113
°
F (45
°
C).
!
Protecting the Bypass Unit from Foreign Matter
During Bypass unit installation and project construction, it is possible to have foreign matter, such as metal shavings or wire clippings, fall inside the Bypass unit. To prevent foreign matter from falling into the Bypass unit, place a temporary cover over the unit.
Always remove the temporary cover from the Bypass unit before start-up. Otherwise, ventilation will be reduced, causing the
Bypass unit to overheat.
Physical Installation 1 - 25
!
Installation Orientation and Enclosure Considerations
Install the Bypass unit vertically so as not to reduce the cooling efficiency. When installing the Bypass unit, always provide the recommended installation clearances to allow normal heat dissipation.
When preparing to mount the unit, lift it by the base (or lifting rings when provided), never by the enclosure door. For effective cooling and proper maintenance, the wall mounted units must be installed on a flat non-flammable vertical surface using four mounting screws.
To mount units employing the add-on box, a hex head mounting screw and socket wrench will be required for the lower left mounting hole location. See Figure 1.15.
For all units, the MCP handle should be in the OFF position to open the enclosure door. The wall mount units have two full turn fasteners, CCW to open, that require a flat blade screwdriver to open the enclosure door.
Mounting
Holes
Mounting
Holes
Fig 1.15 Add-on Options Box
Physical Installation 1 - 26
Chapter 2
Electrical Installation
This chapter describes wiring and the electrical installation process for a Drive and
Bypass unit.
Termination Configuration - Power Wiring ..................................... 2
Field Wiring, Pressure Wire Connector, Wire Type, Range and Tightnening Torque Specifications ..................................... 3
Cable Length between Drive and Motor .................................... 4
Grounding ................................................................................. 5
Wire Routing ............................................................................. 6
Drive Main Circuit Configurations 208-240 VAC ....................... 7
Drive Main Circuit Configurations 480 VAC .............................. 8
Control Wiring ................................................................................ 9
Bypass Field Control Wire Landing ........................................... 9
Annunciation Contacts .............................................................. 9
Damper Control Circuit ............................................................ 10
Customer Supplied Run/Stop circuit: ...................................... 10
Safety Interlock Circuit: ........................................................... 10
Customer Supplied Interlock Circuit
(Drive and Bypass enable input): ............................................ 10
Switch Selectable Functions: .................................................. 10
Bypass Relay Controller PCB ................................................. 11
Drive Speed Control Circuit Wiring .......................................... 12
Drive Terminal Block Configuration ......................................... 13
Wiring Checks ......................................................................... 14
Control Circuit Wiring Precautions .......................................... 14
Bypass Control Circuit Terminal Functions ............................. 15
DIP Switch S1 ......................................................................... 16
Shunt Connector CN15 ........................................................... 17
Field Wiring Diagram ............................................................... 18
Wiring Diagram ............................................................................ 20
Logic Diagram .............................................................................. 22
Electrical Installation 2 - 1
Termination Configuration - Power Wiring
The Circuit Breaker/MCP is located in the upper right hand side of the Bypass unit. The Bypass three phase input power connection is made to the input terminals of the MCP. See Figure 2.1 and 2.2 for representative examples.
Input Power
Motor
Connections Ground Lug
Input Power
Ground Lug
Fig 2.1 Typical Input Power Connection,
Wall Mount Unit
Fig. 2.2 Typical Input and Output Power
Connections, Floor Mount Unit
The OverLoad Relay (OLR) is mounted to the contactor assembly or back panel (depending on rating), just above the bypass contactor. The Bypass three phase output power connection to the motor is made to the output terminals of the OverLoad
Relay. See Figure 2.3 for representative examples.
Motor Connections
Motor Connections
Overload Relay
Fig 2.3 Typical Output Power Connection, Wall Mount Units
Electrical Installation 2 - 2
!
Field Wiring, Pressure Wire Connector, Wire Type, Range and Tightnening
Torque Specifications
D002
D003
D004
D007
D010
D016
D024
D030
D074
D088
D114
D143
D169
D211
D273
D343
D396
BYPASS MODEL NO.
BASE NUMBER
208V
_ _ _ _ -XXXX
240V
*
480V
A002 B001
A003
A004
D046
D059
A006
A009
A015
A022
A028
A042
A054
A068
A080
A104
A130
A154
A192
A248
A312
A360
B034
B040
B052
B065
B077
B096
B002
B003
B004
B007
B011
B014
B021
B027
B124
B156
B180
B240
B302
B361
B414
B477
B515
B590
MFG.
PART
NUMBER
FAL36003
FAL36007
FAL36015
FAL36030
FAL36050
FAL36100
KAL36150
KAL36250
LAL36400
MAL36600
MAL36800
CUSTOMER A.C. LINE WIRING
CURRENT
RATING
(AMPS)
3
7
CIRCUIT BREAKER
WIRE SIZE
RANGE
(AWG)
14 - 4
14 - 4
15
30
50
100
150
250
400
600
800
14 - 4
12 - 4
12 - 1/0
12 - 1/0
4 - 350 kcmil
4 - 350 kcmil
1 x (1-600 kcmil)
2 x (1-250 kcmil)
(1-3) x (3/0-500 kcmil)
(1-3) x (3/0-500 kcmil)
TIGHTENING
TORQUE
(LB.-IN.)
35
35
35
35
80
80
250
250
375
2 x 375
(1-3) x 300
(1-3) x 300
BYPASS MODEL NO.
BASE NUMBER
208V 240V
*
480V
D002 A002 B001
STANDARD BYPASS OVERLOAD RELAY
MFG.
PART
NUMBER
LR2 D13
WIRE SIZE
RANGE
(AWG)
18 - 10
TIGHTENING
TORQUE
(LB.-IN.)
15
CUSTOMER A.C. MOTOR WIRING
OR, WITH OPTION A OVERLOAD RELAYS
MFG.
PART
NUMBER
LR2 D13
WIRE SIZE
RANGE
(AWG)
18 - 10
TIGHTENING
TORQUE
(LB.-IN.)
15
D003
D004
D007
D010
D016
D024
D030
A003
A004
A006
A009
A015
A022
A028
B002
B003
B004
B007
B011
B014
B021
B027
B034
B040
LR2 D15
LR2 D15
LR2 D15
LR2 D25
LR2 D35
18 - 10
18 - 10
18 - 10
14 - 6
10 - 1/0
15
15
15
15
75
LR2 D15
LR2 D15
LR2 D15
LR2 D15
18 - 10
18 - 10
18 - 10
18 - 10
D046
D059
D074
D088
D114
D143
D169
D211
D273
D343
D396
A042
A054
A068
A080
A104
A130
A154
A192
A248
A312
A360
B052
B065
B077
B096
B124
B156
B180
B240
B302
B361
LR2 D35
LR2 D35
LR2 D35
LR2 D35
LR2 D35
LR2 D3563
LR9 F5567
LR9 F5569
LR9 F5569
LR9 F5569
LR9 F5571
LR9 F5571
LR9 F7575
LR9 F7575
LR9 F7579
LR9 F7579
LR9 F7579
10 - 1/0
10 - 1/0
10 - 1/0
10 - 1/0
10 - 1/0
10 - 1/0
6 - 3/0
6 - 3/0
6 - 3/0
6 - 3/0
6 - 300 kcmil
6 - 300 kcmil
2 x (6-300 kcmil)
2 x (6-300 kcmil)
2 x (6-300 kcmil)
2 x (6-300 kcmil)
2 x (6-300 kcmil)
200
200
200
200
275
275
2 x 500
2 x 500
2 x 500
2 x 500
2 x 500
75
75
75
75
75
100
LR2 D15
LR2 D25
LR2 D25
LR2 D35
LR2 D35
LR2 D35
LR2 D35
LR2 D35
LR9 F5567
LR9 F5569
LR9 F5569
LR9 F5569
LR9 F5571
LR9 F5571
18 - 10
14 - 6
14 - 6
10 - 1/0
10 - 1/0
10 - 1/0
10 - 1/0
10 - 1/0
6 - 3/0
6 - 3/0
6 - 3/0
6 - 3/0
6 - 300 kcmil
6 - 300 kcmil
B414
B477
B515
B590
LR9 F7581
LR9 F7581
LR9 F7581
3 x (6-300 kcmil)
3 x (6-300 kcmil)
3 x (6-300 kcmil)
3 x 500
3 x 500
3 x 500
LR9 F7575
LR9 F7575
2 x (6-300 kcmil)
2 x (6-300 kcmil)
*
The fourth underscore position in these model numbers codes for the enclosure type: V = NEMA1, B = NEMA12 FVFF.
15
15
15
15
75
75
200
200
200
200
275
275
15
15
15
75
75
75
2 x 500
2 x 500
FOR 0 TO 100 AMPS, USE 60 -75 C COPPER WIRE, AND ABOVE 100 AMPS, USE 75 C COPPER WIRE.
D074
D088
D114
D143
D169
D211
D273
D343
D396
BYPASS MODEL NO.
BASE NUMBER
208V
_ _ _ _ -XXXX
240V
*
480V
D002 A002 B001
D003
D004
D007
D010
D016
D024
D030
A003
A004
A006
A009
A015
A022
A028
D046
D059
A042
A054
A068
A080
A104
B034
B040
B052
B065
B077
B096
B124
B002
B003
B004
B007
B011
B014
B021
B027
A130
A154
A192
A248
A312
A360
B156
B180
B240
B302
B361
B414
B477
B515
B590
CUSTOMER EARTH GROUND WIRING
WIRE SIZE
RANGE
(AWG)
14 - 10
GROUND LUG
TIGHTENING
TORQUE
(LB.-IN.)
35
4 - 2/0
LC1 D18
6 - 4
LC1 D25
LC1 D32
LC1 D40
LC1 D50
LC1 D65
LC1 D80
LC1 D115
LC1 D150
LC1 F185
LC1 F265
LC1 F330
LC1 F400
LC1 F500
LC1 F630
8
18 - 8
18 - 8
14 - 6
10 - 3
10 - 3
10 - 3
10 - 2
8 - 250 kcmil
8 - 250 kcmil
6 - 3/0
6 - 300 kcmil
6 - 300 kcmil
4 - 500 kcmil
2 x (2-600 kcmil)
3 x (2-600 kcmil)
40
45
120
OR, WITH OPTION D A.C. CONTACTORS
MFG.
PART
NUMBER
LC1 D09
WIRE SIZE
RANGE
(AWG)
18 - 10
TIGHTENING
TORQUE
(LB.-IN.)
7
15
2 x 500
3 x 500
45
100
100
100
200
275
275
500
15
20
45
45
IMPORTANT
Determine the wire size for the main circuit so that line voltage drop is within 2% of the rated voltage. Line voltage drop is calculated as follows:
Line voltage drop(V) =
√
3 x wire resistance (
Ω
/km) x wire length (m) x current (A) x 10
-3
WARNING
Prior to removing any protective cover or wiring any part of the Drive, remove all power sources, including main input power and control circuit power. Wait a minimum of 5 minutes after power removal, before removing any cover. The charge lamp located within the Drive should be off prior to working inside. Even if the charge lamp is off, one must measure the AC input, output, and DC Bus potential to insure safe levels prior to resuming work. Failure to adhere to this warning may result in personal injury or death.
Electrical Installation 2 - 3
!
Cable Length between Drive and Motor
The Bypass unit should be installed as close as possible to the motor to minimize the length of load side power cable needed between the Drive and the motor. If the cable between the Drive and the motor is long, the high-frequency leakage current will increase, causing the Drive output current to increase as well. This may affect peripheral devices. To prevent this, reduce cable length, or if necessary, adjust the carrier frequency (set in C6-02) as shown in Table 2.1.
The line side power cables, load side power cables and the control wiring should all be run in a separate conduit. Careful attention to this recommended design practice will avoid many potential motor and Drive related problems.
Motor Cable Length
Table 2.1 Motor Cable Length vs. Carrier Frequency (C6-02)
164 ft. (50m) maximum 328 ft. (100m) maximum More than 328 ft.(100m)
Carrier Frequency 15kHz maximum 10kHz maximum 5kHz maximum
(See the limitations on carrier frequency, based on Drive capacity and model number in Appendix B).
Electrical Installation 2 - 4
!
Grounding
"
Drive and Motor Ground Wire Landing
The Drive ground lug (terminal ) is connected to the enclosure. The enclosure ground lug must be connected to earth ground. See Figures 2.1 and 2.2.
The Drive has a second ground lug to accept the motor ground lead. See Figure 2.9.
"
Ground Wiring Precautions
Observe the following precautions when connecting the ground wire:
1.
208-240 VAC Drives should have a ground connection with resistance of less than 100
Ω
..
2.
480 VAC Drives should have a ground connection with resistance of less than 10
Ω
..
3.
Do not share the ground wire with other devices, such as large-current electrical equipment.
4.
Always use a ground wire that complies with technical standards on electrical equipment and minimize the length of the ground wire. Leakage current flows through the Drive. Therefore, if the distance between the ground rod and the ground terminal is too long, potential on the ground terminal of the Drive will become unstable.
5.
When using more than one Drive, be careful not to loop the ground wire.
OK NO
Fig 2.4 Ground Wiring Examples
For grounding connection to earth ground see Figures 2.1 and 2.2.
"
Control Circuit Ground Terminals
The removable Drive control terminal card provides two ground terminals (marked TB3 and TB4) to accept the control wire shield connection. The control wire shield should be connected on this end only, the opposite end should be isolated with electrical tape.
IMPORTANT
Grounding of the Bypass enclosure and motor is required for proper system operation.
Electrical Installation 2 - 5
!
Wire Routing
The following Figures indicate suggested wire entry and bending areas for representative wall mount enclosures.
Control circuit wiring
Motor connection
Input power
Control circuit wiring
Motor connection
Input power
Typical Enclosure 2
Fig 2.5 Wall Mount Enclosures
Typical Enclosure 2
Electrical Installation 2 - 6
!
Drive Main Circuit Configurations 208-240 VAC
The main circuit configurations of the Drive are shown in Tables 2.2 and 2.3.
Table 2.2 Drive Main Circuit Configurations
208-240 VAC
CIMR-_ _ _ 20P4 to 2018
(1/2 Hp to 25 Hp)
CIMR-_ _ _ 2022 and 2030
(30 Hp to 40 Hp)
Note
1
{
Notes
1 & 3
{
Power supply
Control circuits
Power supply
Control circuits
CIMR-_ _ _ 2037 to 2110
(50 Hp to 150 Hp)
Notes
1 & 3
{
---
Power supply
Control circuits
Note1. Input fuses or molded case circuit breakers are required for proper branch circuit protection for all Drives. Failure to use recommended fuses/circuit breakers (See Appendix E) may result in damage to the wiring, Drive and/or personal injury.
2. Control power is supplied internally from the main circuit DC power supply for all Drives.
3. Consult your Yaskawa representative before using 12-pulse rectification.
Electrical Installation 2 - 7
!
P7 Drive Main Circuit Configurations 480 VAC
Table 2.3 Drive Main Circuit Configurations
480 VAC
CIMR-_ _ _ 40P4 to 4018
(1/2 Hp to 30 Hp)
CIMR-_ _ _ 4030 to 4055
(40 Hp to 100 Hp)
Note
1
{
Notes
1 & 3
{
Power supply
Control circuits
Power supply
Control circuits
Notes
1 & 3
{
CIMR-_ _ _ 4075 to 4160 and CIMR-_ _ _ 4185 to 4300
(125 Hp to 500 Hp)
3
Power supply
Control circuits
---
Note1. Input fuses or molded case circuit breakers are required for proper branch circuit protection for all Drives. Failure to use recommended fuses/circuit breakers (See Appendix E) may result in damage to the wiring, Drive and/or personal injury.
2. Control power is supplied internally from the main circuit DC power supply for all Drives.
3. Consult your Yaskawa representative before using 12-pulse rectification.
Electrical Installation 2 - 8
Control Wiring
!
Bypass Field Control Wire Landing
The Bypass field control wiring is terminated on the relay control PCB A2, Terminal block TB1. The terminal designations are labeled on the door, adjacent to PCB A2 (see Figure 2.6). Route the control wiring as shown in Figure 2.5.
TB1 terminals 1 and 2 are jumpered (J1) as the unit is shipped from the factory. If a customer supplied series circuit of NC safety devices is to be used, this jumper is removed and the safety circuit connected between terminals 1 and 2.
TB1 terminals 5 and 6 are jumpered (J2) as the unit is shipped from the factory. If customer supplied Drive NO enabling contacts (open = Drive disabled, closed = Drive enabled) are to be used (such as a damper end switch or occupied cycle timer), this jumper is removed and the enabling contacts wired between terminals 5 and 6.
Fig 2.6 TB1 Control Terminal Locations, All Models
!
Annunciation Contacts
Contacts for customer use are provided and wired to TB1 as follows for use as annunciators of Bypass unit operation. All are 1 amp at 120 VAC contacts.
Table 2.4 Annunciation Contacts
Function
Motor OL/Safeties Fault
Type
Form C
Bypass Run
Drive Run
Drive Fault
Form A
Form A
Form C
Electrical Installation 2 - 9
TB1 Terminals
14-15-16
9-10
7-8
11-12-13
!
Damper Control Circuit
TB1 terminals 19 and 20 are provided to power a customer supplied 120 VAC relay, electric actuator or electro-pneumatic solenoid air valve employed to control a pneumatic damper actuator, typically for outdoor air intake damper interlock. The power rating of the connected device should be no more than 40 VA continuous and 70 VA inrush. An off command (from the
H/O/A switch) or a safety device trip-out will immediately de-energize these terminals. At the same time the Drive will begin the ramp to stop process (in Drive mode with the default stopping method). In some air handling unit applications operation during the ramp to stop time with the dampers closed may be problematic. Over pressurization of ducts or trip-out on high DC bus voltage, due to overhauling of the load by other fans in the system, are possible outcomes. One solution is to reprogram the stopping method in parameter b1-03 to “coast to stop” eliminating the potential for both of these problems.
!
Customer Supplied Run/Stop circuit:
A control terminal block position (TB1, terminals 3 and 4) is provided to connect the Normally Open (NO) Run/Stop contact from a separate source or other remote controller for auto mode control.
There must be continuity between these terminals in order for the motor to run.
!
Safety Interlock Circuit:
A control terminal block position (TB1, terminals 1 and 2) is provided to connect the series circuit of Normally Closed (NC) safety devices such as: freeze up thermostats, smoke/fire sensors, high pressure limits, temperature limits or vibration detectors.
There must be continuity between these terminals in order for the motor to run.
!
Customer Supplied Interlock Circuit (Drive and Bypass enable input):
A control terminal block position (TB1, terminals 5 and 6) is provided to connect Normally Open (NO) enabling contacts such as: damper end switches or occupied cycle timers.
There must be continuity between these terminals in order for the motor to run.
!
Switch Selectable Functions:
The slide switches used to select these functions are located on the relay controller Printed Circuit Board (PCB) A2
(See Figure 1.9). The factory default is for these functions to be de-selected.
Smoke Purge: When enabled (switch S105) this function allows a contact closure, between terminals 17 and 18 of TB1, to transfer motor operation to bypass for a maximum capacity smoke control function. When in smoke purge mode, during emergency fire/smoke situations, the motor overloads and safety interlock circuit are overridden to shift the priority to protecting people rather than equipment.
Remote Transfer to Bypass: When selected (switch S104) this function allows a contact closure from a separate source, between terminals 25 and 26 of TB1, to transfer motor operation from Drive mode to bypass mode. This remote tranfer to bypass function overrides the Drive/Bypass manual switch.
Electrical Installation 2 - 10
!
Bypass Relay Controller PCB
TB1
ON PCB A2
9
8
7
11
10
13
12
16
15
14
4
3
2
1
6
5
21
20
24
23
26
25
22
19
18
17
(L1)
Fig 2.7 Bypass Control Circuit Inputs and Outputs
Customer provided contact closure inputs must have a minimum rating of 0.1 amp at 120 VAC.
Electrical Installation 2 - 11
!
Drive Speed Control Circuit Wiring
The auto mode speed reference (speed command) field wiring connection is made directly to Drive terminals A2 (signal positive), AC (signal common) and G (shield). Keep this lead length as short as possible to maintain signal quality. Insulated twisted shielded pair wire (2 conductor # 18 ga, Belden 8760 or equivalent) is required. Do not run these wires in the same conduits as other AC power or control wires. The shield must be connected on this end only, stub and isolate the other end. The signal employed is 4 to 20 mA with parameter H3-08 set for “2: 4 - 20 mA”. For 0 to 10 VDC, parameter H3-08 is set for
“0: 0 - 10 VDC” and the P7 control board DIP switch S1-2 must be in the OFF position. (See Figure 2.11)
For remote operation, keep the length of the control wiring to 50 m or less. Separate the control wiring from high-power lines
(input power, motor leads or relay sequence circuits) to reduce induction from peripheral devices.
When setting speed commands from an external speed potentiometer (and not from a Digital Operator), use shielded twistedpair wires and ground the shield to terminal E(G), as shown in Figure 2.8. Terminal numbers and wire sizes are shown in
Table 2.5.
External frequency reference
E (G)
Shield terminal
0 to +10 V
Speed setting power supply, +15 V 20 mA
Master speed reference, 0 to +10 V (20 k
Ω
)
Master speed reference, 4 to 20 mA (250
Ω
)/0 to +10 V (20 k
Ω
)
P = Wire Pair
Fig 2.8 Analog Input Terminal Configuration on Drive
Electrical Installation 2 - 12
!
Drive Terminal Block Configuration
The wiring terminals are shown in Figure 2.9.
Control circuit terminals
Ground terminal
E(G)
SN SC SP A1 A2 +V AC -V MP AC RP R+ R-
S1 S2 S3 S4 S5 S6 S7 FM AC AM IG S+ S-
M5 M6 MA MB MC
M3 M4 M1 M2 E(G)
Main circuit terminals
Charge indicator
Ground terminal
Models CIMR-_ _ _2018 (25 HP, 208V)/
4018 (30 HP, 480V) and smaller
E(G)
SN SC SP A1 A2 +V
S1 S2 S3 S4 S5
AC
S6 S7
-V MP AC RP R+ R-
FM AC AM IG S+ S-
M5 M6 MA MB MC
M3 M4 M1 M2 E(G)
Control circuit terminals
Charge indicator
Main circuit terminals
Ground terminal
Ground terminal
Models CIMR-_ _ _2022 (30 HP, 208V)/
4030 (40 HP, 480V) and larger
Fig 2.9 Drive Terminal Configuration
Electrical Installation 2 - 13
Terminals
Table 2.5 Terminal Numbers and Wire Sizes (Same for all Bypass Units)
Terminal
Screws
Tightening
Torque lb.-in.
(N•m)
Possible
Wire Sizes
AWG
(mm
2
)
Recommended
Wire Size
AWG
(mm
2
)
Wire Type
DRIVE
TERMINALS:
FM, AC, AM, SC, SN,
SP, A1, A2, +V, S1, S2,
S3, S4, S5, S6, S7, MA,
MB, MC, M1, M2, M3,
M4, MP, R+, R-, S+,
S-, IG
Phoenix type *3
TB1 ON PCB A2
TERMINALS:
TB1-1 through TB1-26
4.2 to 5.3
(0.5 to 0.6)
Stranded wire:
26 to 16
(0.14 to 1.5)
18
(0.75)
• Shielded, twisted-pair wire
*1
• Shielded, polyethylene-covered, vinyl sheath cable
E(G) M3.5
7.0 to 8.8
(0.8 to 1.0)
20 to 14
(0.5 to 2
*2
)
12
(1.25)
*1. Use shielded twisted-pair cables to input an external speed command.
*2. We recommend using straight solderless terminals on digital inputs to simplify wiring and improve reliability.
*3. We recommend using a thin-slot screwdriver with a 3.5 mm blade width.
!
Wiring Checks
After all wiring is completed, perform the following checks:
1.
Is all wiring correct?
2.
Have all wire clippings, screws or other foreign material been removed from the Drive and Bypass enclosure?
3.
Are all terminal screws tight?
!
Control Circuit Wiring Precautions
Observe the following precautions when wiring control circuits:
1.
Separate control wiring from power/motor wiring and other high-power lines.
2.
Separate wiring for control circuit terminals for digital outputs from wiring to other control circuit terminals.
3.
If using an optional external power supply, it should be a UL Listed Class 2 power supply source.
4.
Use twisted-pair or shielded twisted-pair cables for control circuits to prevent operating faults. Prepare cable ends as shown in Figure 2.10.
5.
Connect the shield wire to terminal E(G).
6.
Insulate the shield with tape to prevent contact with other signal lines and equipment.
Shield sheath
Insulation
Do not connect here.
Connect to shield sheath terminal E(G) at Drive
Insulate with tape
Fig 2.10 Preparing the Ends of Shielded Twisted-Pair Cables
Electrical Installation 2 - 14
!
Bypass Control Circuit Terminal Functions
The functions of the control circuit terminals are shown in Table 2.6.
Type
Digital input signals
Analog input signals
(Drive)
Digital output signals
Analog
output signals
(Drive)
TB1-10
TB1-11
TB1-12
TB1-13
TB1-14
TB1-15
TB1-16
No.
TB1-3
TB1-4
TB1-1
TB1-2
TB1-5
TB1-6
TB1-17
TB1-18
TB1-23
TB1-24
TB1-25
TB1-26
+V
A1
A2
AC
E(G)
Table 2.6 Bypass Control Circuit Terminals
Signal Name
Auto Mode run/stop command
NC Safety Circuit
Customer Supplied Interlock
Smoke Purge
2 Motor “OR”
Remote Transfer
+15 VDC power output
Analog Input or Speed Command
Multi-function analog input
Analog input common
Shield wire, optional ground line connection point
Function
Run when CLOSED; stopped when OPEN.
Fault when OPEN
Enable Drive when Closed
*Transfer to Bypass when Closed
*Transfer to Motor 2 When Closed
*Transfer to Bypass when Closed
+15 VDC power supply for analog Transmitters
0 to +10 VDC/100%
4 to 20 mA/100%
0 to +10 VDC/100% (H3-08)
Function set by
H3-09.
–
–
TB1-7
Running on Drive
TB1-8
CLOSED During Operation
TB1-9
Running on Bypass
Drive Fault
Motor Overload or
Safety Circuit Fault
11/12 CLOSED During Fault Condition
12/13 OPEN During Fault Condition
14/15 CLOSED During Fault Condition
15/16 OPEN During Fault Condition
FM Multi-function analog output
Frequency Output
0 to +10 VDC/100% frequency
Multi-function analog monitor 1
Function set by
H4-01
AC Analog output common –
AM Multi-function analog output
Current Monitor
0 to +10 VAC/100%
Drive's rated current
Multi-function analog monitor 2
Function set by
H4-04
* Switch Selectable Options
Signal Level
Dry
Contacts
+15 VDC
(Max. current: 20 mA)
0 to +10 V(20 k
Ω
)
4 to 20 mA(250
Ω
)
0 to +10 V(20k
Ω
)
–
–
Dry contacts
Contact capacity:
1 A max. at 250 VAC
1 A max. at 30 VDC
0 to +10 VDC max. ±5%
2 mA max.
Electrical Installation 2 - 15
Type
RS-485/
422
(Drive)
Control
Power
Output
No.
R+
R-
S+
S-
IG
TB1-19
TB1-20
TB1-21
TB1-22
Table 2.6 Bypass Control Circuit Terminals (Continued)
Signal Name Function
Communication input
For 2-wire RS-485, short R+ to S+
and R- to S-.
Communication output
Signal common -
Damper Control Pneumatic Control Interface
Customer Use Power Customer control Devices
!
DIP Switch S1
DIP Switch S1 is described in this section. The functions of DIP switch S1 are shown in Table 2.7.
Signal Level
Differential input, optical isolation
Differential input, optical isolation
-
40VA@120V
100VA@120V
O
S1
1
1
2
Terminating resistance
DIP Switch S1-1 located on terminal board.
Fig 2.11 DIP Switch S1 Location
Name
S1-1
S1-2
Function
Table 2.7 DIP Switch S1
RS-485 and RS-422 terminating resistance
Input signal for analog input A2
Setting
OFF: No terminating resistance (Factory default)
ON: Terminating resistance of 110
Ω
OFF: 0-10 VDC (internal resistance: 20 K
Ω
)
ON: 4-20 mA (internal resistance: 250
Ω
) (Factory default)
Electrical Installation 2 - 16
!
Shunt Connector CN15
The shunt connector CN15 is described in this section. Shunt connector along with parameters H4-07 and H4-08 select the signal range of the analog output terminals FM and AM.
Shunt connector CN15 is only available when the optional Terminal Card with the 4-20mA Analog Output Monitor is installed. See Chapter 7 for installation of the optional Terminal Card.
The function of various shunt connector CN15 configurations is shown in Table 2.8.
Fig 2.12 Shunt Connector CN15 Location
CN15
Table 2.8 Shunt Connector CN15 Configuration Options
Analog Output Monitor Configurations
Voltage Output (0-10 VDC) for terminals FM-AC (CH1) and AM-AC (CH2)
Current Output (4-20mA) for terminals FM-AC (CH1) and AM-AC (CH2)
Voltage Output (0-10 VDC) for terminals FM-AC (CH1)
Current Output (4-20mA) for terminals AM-AC (CH2)
Current Output (4-20mA) for terminals FM-AC (CH1)
Voltage Output (0-10 VDC) for terminals AM-AC (CH2)
The software configuration for the analog output monitor signal type is listed below:
Parameter
No.
H4-07
H4-08
Parameter Name
Digital Operator Display
Terminal FM Signal Level
Selection
AO Level Select1
Terminal AM Signal Level
Selection
AO Level Select2
0: 0 - 10 V
2: 4-20 mA
0: 0 - 10 V
2: 4-20 mA
Description
Setting
Range
0 or 2
Factory
Setting
0
Menu
Location
Programming
0 or 2 0 Programming
Electrical Installation 2 - 17
!
Field Wiring Diagram
Use these diagrams to document your field wiring. We suggest copying this page based on your installation needs.
Fig 2.13 Field Wiring Diagram
Electrical Installation 2 - 18
Notes:
Electrical Installation 2 - 19
Wiring Diagram
FROM
CUSTOMER'S
A.C. LINES
GND LUG
EG
EARTH
GROUND
SEE
NOTE 1
CB1
L1
(1)
L2
(2)
L3
(3)
(SEE
TABLE 3
FOR CB1
AMPERE
RATINGS)
CG1
1L1
(4)
(5)
1L2
(6)
OPTION R
3% INPUT
REACTOR
L1
A1
A2
1L3
B1 C1
B2 C2
(L1)
K1
(T1)
(L2)
(T2)
(L3)
(T3) (1)
(2)
(1)
F3
(2)
(1)
F4
(2)
F5
OPTION F
DRIVE
INPUT
FUSES
MANUAL
SPEED POT
OPTION S
TO A2
OPTION N
DELTA-WYE
CAPACITIVE
INPUT FILTER
A5
(GRN) (YEL) (YEL) (YEL)
E
TO DRIVE
TERMINAL
L1 L2 L3
OPTION X
OR
OPTION Z
DC BUS
CHOKE
L3
L1
L2
+1
+2
+1
+2
REMOVE JUMPER
FOR
DC BUS CHOKE
OPTIONS X OR Z
CN1 CN2
L12/1.22
L11/1.23
L13/1.24
TO CABINET
DOOR MOUNTED
DRIVE KEYPAD
(B)
WITHOUT
OPTION P
(R)
(W)
CONTROL
BOARD
A1
+V
MANUAL REF. IN
0-10VDC
(20K OHM)
+15VDC
20mA MAX.
AC
ANALOG
COM.
CN2
A6
L1
(R)
L2
(S)
L3
(T)
OPTION G, H, L, or Q
SEE THE
APPROPRIATE
TECHNICAL
MANUAL FOR
NETWORK
CONNECTIONS
P7
DRIVE
A1
STD. AUTO MODE SPEED REFERENCE
+
ISOLATED
AUTO MODE
SPEED
REFERENCE
4-20MADC
0R
0-10VDC
(SEE
TABLE 2)
-
SHIELD
SEE
NOTE 5
0R
L15/1.32
L14/1.31
WITH OPTION P
3-15 PSI PRESSURE TRANSDUCER
OPTION P
A4
4-20MA
OUTPUT
3-14.5 PSI
PNEUMATIC
SIGNAL
3-15 PSI
FOLLOWER
A2
VCC +V
WITH
OPTION S
PART NO.
UTC000038
J2 +V
COM.
AC
AC
L14/1.21
L15/1.20
(B)
(R)
A2
AC
E
A2
+V
AC
A2
AUTO REF. IN
(AS SET
BY H3-08)
AC
ANALOG
COM.
E
(G) TB3
SHIELD
EG
OPTION N
GREEN
LEAD WIRE
(U)
T1
DIP SWITCH S1
OFF
ON
1
OFF
ON
2
TERMINAL
BOARD
(V)
T2
PG1
SEE
NOTE 1
(L1)
K2
(T1)
(L2) (L3)
(T2) (T3)
(W)
T3
L4
L1/A1
GND1
E L2
L1/A2
L2/B1
LINE
L3/C1
GND2
PE
LOAD
L2/B2 L3/C2
OPTION E
INPUT
RFI
FILTER
MA
MA
DRIVE
FAULT
MB
MC
MC
MA
M1
DRIVE
RUNNING
M2
M2
M3
M3
SERIAL
COMM. RUN
M4
M4
S1
RUN
FWD
S1
BYPASS DRIVE
ENABLE
S3
FAULT RESET S4
S1
S5
HAND/AUTO S5
COM.
SN
SEQ. COM.
SC
JUMPER
+24V
SP
SN
A1 B1 C1
A2 B2 C2
(L3) (L2) (L1)
L1/1.04
K3
(T3) (T2) (T1)
L3/1.14
L4/1.15
L5/1.16
L6/1.17
L7/1.18
L8/1.20
L9/1.21
OPTION K
5% LOAD
REACTOR
2 MOTOR
"AND"
OPTION A
STD.
(2)
SEE
NOTE 2
(2)
S11
(1)
(1) (1)
F9
(2)
(1)
F8
(2)
F7
(4)
(3)
(6)
(5)
JUMPER
(96)
(95)
(1)
(2)
SEE
NOTE 2
(96)
(2)
(95)
S12
(1)
(1)
F12
(2)
(4)
(3)
(1)
F11
(2)
(6)
(5)
F10
(96)
(95)
(2) (4)
(1) (3)
(6)
SEE
NOTE 2
S10
(5)
SEE
NOTE 2
(2)
S10
(1)
(4)
(3)
(6)
(5)
(L1)
K4
(T1)
4T1
(L2)
(T2)
4T2
(L3)
(T3)
4T3
(L1)
K5
(T1)
(L2) (L3)
(T2) (T3)
(96)
(95)
TO A2
(T2)
(T1) (T3)
A.C. MOTOR #1
TO A2
(T2)
(T1) (T3)
A.C. MOTOR #2
L1/1.04
L2/1.07
TO A2
(T2)
(T1) (T3)
A.C. MOTOR
(T1)
(T2)
(T3)
A.C. MOTOR #1
(T2)
(T1) (T3)
A.C. MOTOR #2
2 MOTOR
"OR"
OPTION D
Electrical Installation 2 - 20
1L1
1L2
DG1 EG1 PG2
SEE
NOTE 1
INPUT
CONTACTOR
104
OUTPUT
CONTACTOR
128
111
BYPASS
CONTACTOR
112
109
MANUAL
SPEED POT
OPTION S
F1
A
F2
B
100
(X2)
MA
L1
1
CN102A
(A2)
(A2)
K1
K2
K3
L2/1.39
(A1)
(A1)
100
2
111
3
112
4
114
(61)
K3
113
(62)
114
5
6
116
(61)
K2
115
(62)
116
7
8
(A1)
L3/1.14
MC
1
CN102B
L4/1.16
MA
M2
2
M3
L5/1.17
3
M4
L6/1.18
4
CONTROL TRANSFORMER
T1
(X1)
PG2
PG2
TB1
26
25
24
23
22
21
20
19
18
17
F6
(1) (2)
SEE NOTE 6
CONTROL TRANSFORMER PRIMARY CONNECTIONS
INPUT
VOLTS
208
230/240
460/480
REMOTE TRANSFER
TO BYPASS CONTACT
(CLOSED=BYPASS)
MIN. RATING:
0.1A,120VAC
OPTION D
MOTOR #1/MOTOR #2
SELECT CONTACT
(CLOSED=MOTOR #2)
MIN. RATING:
0.1A,120VAC
120VAC,1 PHASE
100VA MAX. POWER
FOR CUSTOMER USE
CUSTOMER TO
PROVIDE FUSING
(BUSSMANN FNQ-R-1.25
IS RECOMMENDED)
120VAC DAMPER
SOLENOID 40VA MAX.
SMOKE PURGE
CONTACT
(CLOSED=PURGE)
MIN. RATING:
0.1A,120VAC
TERMINALS
A B
(H1) (H2)
(H1)
(H1)
(H4)
(H4)
JUMPER
LOCATION
NONE
(H1) TO (H3)
(H2) TO (H4)
(H2) TO (H3)
CABINET DOOR OPERATOR PANEL
PART NUMBER UOPN0001
BYPASS
RUN
DRIVE
KEYPAD
CN1
BYPASS OPERATOR
INTERFACE PCB
A3
PART NUMBER UTC000037-2
CONTROL
POWER ON
DRIVE
RUN
L7/1.20
S1
5
BYPASS RELAY
CONTROLLER PCB
CN103 CN203
DS205 DS201 DS204
6
A2
L8/1.23
S5
7
MOTOR OL/
SAFETIES FAULT
SMOKE
PURGE
DRIVE
FAULT
A3
CN204
1
2
3
CN205
1
2
SN
L9/1.24
8 DS202 DS206 DS203
3
TO A1 L12/1.17
(W)
CN102C
13
TB1
16
TO A1
OR A4
L11/1.18
L13/1.19
(B)
(R)
12
14
15
14
MOTOR
OVERLOAD
OR
CUSTOMER
SAFETIES
FAULT
TEST NORMAL
S203
BYPASS DRIVE
S201
HAND
OFF
AUTO
CN207
1
S202
2
6
4
5
7
8
13
12
11
10
9
DRIVE
FAULT
BYPASS
RUN
CONTACTS
FOR
CUSTOMER
USE
RATED:
1A, 120VAC
MAX.
CUSTOMER
MUST PROVIDE
PROPER
SHORT CIRCUIT
PROTECTION
AND MEANS OF
DISCONNECT.
1
CN206A
2
B1,B3,B5
CABINET
BLOWER(S)
(IF REQUIRED)
1
CN206B
2
B2,B4,B6
CABINET
BLOWER(S)
(IF REQUIRED)
3
MOTOR #1
CONTACTOR
138
135
133
MOTOR #2
CONTACTOR
138
136
131
2 MOTOR
"OR"
OPTION D
K4
121
(61)
K5
(62)
122
(A2)
(1)
RC4
K5
(A1)
(2)
(A2)
(1)
RC5
(A1)
(2)
K4
(13) (14)
K5
123
(61)
K4
(62)
124
100
1
2
(13) (14)
3
1
2
3
9
10
11
S103
DISABLE
(TOP)
ENABLE
(BOTTOM)
AUTO-TRANSFER TO BYPASS
S104
DISABLE
(TOP)
ENABLE
(BOTTOM)
REMOTE TRANSFER TO BYPASS
S105
DISABLE
(TOP)
ENABLE
(BOTTOM)
SMOKE PURGE
8
7
DRIVE
RUN
6
5
JUMPER
J2
4
3
2
1
JUMPER
J1
FOR INSERTION OF NORMALLY
OPEN BLDG. AUTOMATION SYSTEM
INTERLOCK, OR NORMALLY
OPEN DAMPER END SWITCH
SEE NOTE 4
AUTO MODE
RUN/STOP
CONTACT
(CLOSED = RUN)
FOR INSERTION OF NORMALLY
CLOSED CUSTOMER SAFETY
CONTACTS
SEE NOTE 3
(B)
(W)
(R)
MA
125
126
(B)
(W)
(R)
TO A1
CONTROL BOARD
CN1
MANUAL SPEED POT
OPTION S
1
MANUAL SPEED POT
ASSEMBLY
PART NO. URSN0001
R1 MAX. SPEED TRIM
POT PCB
R2
MANUAL
SPEED
R1
2
3
2.5K
OHM
2 MOTOR "OR"
OPTION D
MTR #1
AUTO
MTR #2
(1L3)
(1R1) S1
- INDICATES COMPONENTS NOT SUPPLIED BY YASKAWA.
- INDICATES CUSTOMER WIRING.
SEE SHEET 2 FOR NOTES AND TABLES.
00X
(1L4)
0XX
(1R2)
Items within dashed line boxes are optional equipment
Electrical Installation 2 - 21
Logic Diagram
FROM
CUSTOMERS
A.C. LINES
L1
1
L2
L3
2
3
CB1
4
5
6
EARTH
GROUND
1L1
1L2
1L3
K1
MANUAL SPEED POT OPTION S
R2
MAX. SPEED
TRIM
1
CN204
R1
MANUAL
SPEED
2.0K
2
CN204
1
2
2.5K
3 CN204
3
CN103/
CN203
20
CN103/
CN203 21
CN103/
CN203 22
CN102C
CN102C
CN102C
12
+V
13
A1
AC
14
STANDARD AUTO MODE
SPEED REFERENCE INPUT
ISOLATED
AUTO MODE
SPEED
REFERENCE
4-20MADC
(WITH
PARAMETER
H3-08=1)
0R
0-10VDC
(WITH
PARAMETER
H3-08=0, AND
CONTROL
BOARD DIP SWITCH
S1-2 OFF)
+
-
SEE SH.3,
NOTE 5
SHIELD
A2
AC
G
+V +15 V
A1
MANUAL REF. IN
0 TO 10VDC
(20k ohm)
AC ANALOG COM.
A2
AUTO REF. IN
(AS SET BY
PARAMETER H3-08)
AC
ANALOG COM.
G
(G) TB3
SHIELD
(E)
E
L1
(R)
L2
(S)
A1
P7
L3
(T)
(U)
T1
(V)
T2
(W)
T3
RUN FWD S1
S1
CN102B
5
(3)
K110
(5) (5)
K116
(1) (4)
K119
(6)
BYPASS DRIVE
ENABLE
S3
S1
SEQ. COM
JUMPER
+24V
SC
SP
FAULT RESET S4
HAND/AUTO S5
S5
CN102B
7
RY1
DRIVE
RUNNING
RY2
COM.
SN
SN
CN102B
8
MA
M1
M2
M2
M3
M3
SERIAL
COMM. RUN
RY3
M4
M4
MA
MA
RY3
MB
DRIVE
FAULT
MC
MC
L1/2.10
L2/2.10
L3/2.18
L4/2.18
L5/2.06
L6/2.06
(3)
(1)
K122
ALSO
(3)
(5)
SHOWN
IN CONTROL
RELAY LOGIC
CIRCUIT
K2
- INDICATES COMPONENTS NOT SUPPLIED BY YASKAWA
(L1)
S12
(T1)
(L2)
(T2)
(L3)
(T3)
SEE
SH. 2
(T1)
(T2)
(T3)
A. C. MOTOR *
Electrical Installation 2 - 22
OPTION D
CN102C
11
REMOVE THE
BYPASS RELAY
PCB JUMPER
S101
(1)
S101
(2)
3
K4
1
CN102C
3
K5
2
CN102C
K125
9
(1)
K125
(5)
10
(3) (5)
CN102B
(NOT USED)
K123
6
(1) (5)
K3
1L1
1L2
1
MA
F1
2
F2
F6
1
1 2
PRESENT ONLY
WITH 350VA,
OR GREATER
2
MA
CN102A
1
(X1)
CONTROL TRANSFORMER
T1
RV101
(X2)
(X2)
GND
100
CN102A
(1) (2)
L7
/2.01
/2.01
/2.40
L8
/2.01
/2.01
/2.40
TO SHEET 2
DAMPER CONTROL AND 120 VOLT POWER
K104
(5)
K114
(5)
K116
(3)
(6)
K118
(4)
(5) (3)
(1)
(5)
K111
(3)
TB1
19
2
H N
DAMPER ELECTRIC
PNEUMATIC SOLENOID
TB1
21
TB1
22
TB1
100
20
120VAC, 1PH., 60HZ.
FOR CUSTOMER USE
CUSTOMER MUST PROVIDE PROPER
SHORT CIRCUIT PROTECTION
K108
2 MOTOR "OR" OPTION D
CN205
1
(5)
K125
(3)
(6)
K108
(2)
CN102C
1
122
K5
121
K4
(A1) (A2)
(MTD. ON PANEL)
RC4
CN102C
3
(6)
K125
(4)
(6)
MA
(4)
MTR#1
AUTO
MTR#2
OOX
125
S1
MTR#1
AUTO
MTR#2
OXX
S1
126
CN102C
2
CN205
3
124
CN103/
CN203 18
CN205
2
CN103/
CN203 19
TB1
23
K4 K5
123
(A1) (A2)
(MTD. ON PANEL)
RC5
R123
K125
1
C117
2
TB1
(7) (2) (7) (8)
MOTOR SELECT
(CLOSED = MTR#2)
24
MOTOR #1
CONTACTOR
MOTOR #2
CONTACTOR
MOTOR SELECT
CONTROL RELAY
(2) FORM C
CN102C
MA
6
(MTD. SEPARATELY
ON CABINET DOOR)
STOP
119
CN103/
CN203 23
CN207
119
(MTD. SEPARATELY
ON CABINET DOOR)
RUN
120
CN207
2
CN103/
CN203 24
S3
S2
CN207
CN102C
7
119
(6)
K6
120
(10)
CN102C
3
CN103/
CN203
8
25
1
RUN/STOP ENGINEERED OPTION
(OPERATIONAL ONLY IN THE HAND MODE)
K6
120 100
(13) (14)
(MTD. ON PANEL)
RC28
RUN/STOP
CONTROL RELAY
Electrical Installation 2 - 23
L7/1.06
120VAC FROM SHEET 1 L8/1.06
CN103/
CN203 26
MA
(96)
S12
(95)
111
CN102A
L7/1.06
(2)
K109
(6)
R113
R114
CN103/
CN203
CN103/
CN203
5
6
DS201
W
(1) (2)
(1)
DS202
R
(2)
CN103/
CN203
CN103/
CN203
CN103/
CN203
CN103/
CN203
3
4
1
2
CONTROL
POWER ON
MOTOR OVERLOAD/
CUSTOMER SAFETIES FAULT
K104
MA
MA
L5/1.27
L1/1.23
L6/1.29
L2/1.24
MC
M2
CN102B
CN102B
1
2
R101
R115
R102
1
C101
2
(7)
K105
(8)
CN103/
CN203
(7) (8)
7
(1)
DS203
R
(2)
K106
1
C102
2
(7)
K107
(8)
(7) (8)
K108
DRIVE FAULT RELAY
(2) FORM A
(1) FORM C
DRIVE FAULT
DRIVE RUN RELAY
(2) FORM A
(2) FORM A
TB1 TB1
3
1
JUMPER
2
CUSTOMER
SAFETY INTERLOCKS
(5)
K117
(1)
(5)
K119
(3) (1)
(6)
K113
K107
K113
(3)
(3)
(4)
(4)
K117
(6)
(5)
(5)
(6)
K115
(4)
(6)
K119
(4)
(1)
AUTO TRANSFER
TO BYPASS
S103
(TOP)
DISABLE
(BOTTOM)
ENABLE
(1) (2)
(FACTORY SETTING
IS "DISABLE")
(6)
(1)
K114
(3)
(4)
REMOTE TRANSFER
TO BYPASS
S104
(TOP)
DISABLE
(BOTTOM)
ENABLE
(1) (2)
(FACTORY SETTING
IS "DISABLE")
K120
K121
(5)
(5)
(5)
TB1
CN102B
CN102C
K115
3
3
4
M3
TB1
AUTO MODE
RUN/STOP CONTACT
(CLOSED = RUN)
L3/1.25
L4/1.26
REMOVE JUMPER
FOR RUN/STOP PB OPTION
M4
CN102B
4
4
117
K123
(2)
S102
K6
(1)
118
(11) (7)
CN102C
5
(6)
K104
(4)
(1) (4)
(2)
(1)
(4)
(6)
K124
K124
K110
(6)
(5)
(6)
(4)
K120
(6)
(6)
K124
(6)
(1)
K124
(3)
(4)
(5) (3)
K106
(2)
CN103/
CN203
CN103/
CN203
13
12
CN103/
CN203
11
CN102A
K106
5
113
(5) (3)
CN102A
7
115
R103
TB1 TB1
5
JUMPER
6
BAS INTERLOCK/
DAMPER END
SWITCH
(CLOSED =
DAMPER OPEN)
1
C103
2
(7)
K109
(8)
(7) (8)
K110
(7)
R104
1
K111
(8)
C104
2
(1) FORM C
MOTOR OVERLOAD/
CUSTOMER SAFETIES
FAULT RELAY
(1) FORM A, (1) FORM C
RUN RELAY
(2) FORM A
(7) (8)
CN206A 1
R112
CN102A
R120
1 2
C115
4
112
(A1)
K1
1
100
2
(A2)
B1,B3,B5
C111
CN206A 2
CN206B 1
B2,B4,B6
CN206B 2
DAMPER OPTION
CONTROL RELAY
(1) FORM A
INPUT CONTACTOR
CABINET BLOWER(S)
(360VA. MAX.
TOTAL FOR
ALL BLOWERS
COMBINED)
K3
R116
K2
CN102A
CN103/
CN203
CN102A
R105 C105
8
6
114
(A1)
K2
1
100
2
(A2)
DS204
G
(1) (2)
116
8
R106
(A1)
K3
100
(A2)
C106
1
K112
2
OUTPUT CONTACTOR
DRIVE
RUN
BYPASS CONTACTOR
R107
CN103/
CN203 9
R108
R109
1
C107
2
(7) (8)
(1)
DS205
B
(2)
K113
1
C108
2
(7)
K114
(8)
BYPASS PILOT RELAY
(1) FORM A
BYPASS
RUN
AUTO TRANSFER
RELAY
(2) FORM A
TB1
25
(4)
K121
(6)
REMOTE TRANSFER
TO BYPASS CONTACT
(CLOSED = BYPASS)
TB1
26
R110
(7) (8)
(2) FORM A
221, 228
C109 (7)
K115
(8)
1 2
K116
(2) FORM A
113, 118
(7) (8)
(2) FORM A
REMOTE TRANSFER
RELAY
L8/1.06
Electrical Installation 2 - 24
CN103 XX
L7/1.06
SMOKE PURGE
S105
(TOP)
DISABLE
(BOTTOM)
ENABLE TB1
(1) (2)
(FACTORY SETTING
IS "DISABLE")
17
TB1
SMOKE PURGE
CONTACT
(CLOSED = PURGE)
18
BYPASS
DRIVE
OX
(1R3)
S201 S201
(1R4)
(NORMALLY OPEN (NO))
HAND
OFF
AUTO
(1L3)
S202
OOX
(1L4)
(NORMALLY OPEN (NO))
HAND
OFF
AUTO
XOO
(1R3)
S5 S202
(1R4)
(NORMALLY OPEN (NO))
TEST
NORMAL
OX
(1R3)
S6 S203
(1R4)
(NORMALLY OPEN (NO))
TB1
BYPASS RELAY PCB UTC000036 CONNECTORS
CN102A
XX
XX
- CUSTOMER CONNECTION POINT ON 26 POINT, 1 PIECE PHOENIX
CONNECTOR. TORQUE WIRE CONNECTIONS TO 4.4 POUND-INCH.
- 8 POINT MOLEX HEADER.
USED TO CONNECT THE PANEL HARNESS TO THE BYPASS RELAY PCB.
CN102B
CN102C
XX
XX
- 8 POINT MOLEX HEADER.
USED TO CONNECT THE PANEL HARNESS TO THE BYPASS RELAY PCB.
- 14 POINT, 1 PIECE PHOENIX CONNECTOR.
USED TO CONNECT PANEL MOUNTED OPTIONS TO THE BYPASS
RELAY PCB.
- 26 POINT RIBBON CABLE HEADER.
USED TO CONNECT TO THE CABINET DOOR MOUNTED OPERATOR
PCB CONNECTOR CN203.
CN103/
CN203 14
CN103/
CN203 15
CN103/
CN203 16
CN103/
CN203 17
L8/1.06
R111
R122
K117
1
C110
2
(7)
K118
(8)
CN103/
CN203
(7) (8)
10
(1)
DS206
A
(2)
R117
1
C112
2
(7)
K119
(8)
R118
1
C113
2
(7)
K120
(8)
R119
R121
K121
1
C114
2
(7)
K122
(8)
(7) (8)
K123
1
C116
2
(7)
K124
(8)
(7) (8)
SMOKE PURGE
RELAY
(2) FORM A
(1) FORM A
SMOKE PURGE
BYPASS-DRIVE
CONTROL RELAY
(1) FORM A,
(1) FORM C
AUTO MODE
CONTROL RELAY
(2) FORM A
HAND MODE
CONTROL RELAY
(2) FORM A
(1) FORM A
TEST-NORMAL
CONTROL RELAY
(2) FORM A
(1) FORM C
OPERATOR PCB UTC000037-2 CONNECTORS
CN203
CN204
XY
- 26 POINT RIBBON CABLE HEADER.
USED TO CONNECT TO THE BYPASS RELAY PCB CONNECTOR CN103.
CN205
CN206A
CN206B
CN207
X
X
X
X
X
- 3 POINT, 2 PIECE PHOENIX CONNECTOR.
USED TO CONNECT THE OPTIONAL CABINET DOOR MOUNTED MANUAL
SPEED POT TO THE OPERATOR PCB/PANEL.
- 3 POINT, 2 PIECE PHOENIX CONNECTOR.
USED TO CONNECT THE OPTIONAL CABINET DOOR MOUNTED 2 MOTOR
"OR" SELECTOR SWITCH TO THE OPERATOR PCB/PANEL.
- 2 POINT, 2 PIECE PHOENIX CONNECTOR.
USED TO CONNECT THE OPTIONAL CABINET DOOR MOUNTED BLOWER(S)
TO THE OPERATOR PCB/PANEL.
- 2 POINT, 2 PIECE PHOENIX CONNECTOR.
USED TO CONNECT THE OPTIONAL CABINET DOOR MOUNTED BLOWER(S)
TO THE OPERATOR PCB/PANEL.
- 3 POINT, 2 PIECE PHOENIX CONNECTOR.
USED TO CONNECT THE OPTIONAL CABINET DOOR MOUNTED PARTS (AND
THE "HAND" MODE RUN AND STOP PUSHBUTTONS) TO THE
OPERATOR PCB/PANEL.
(3)
K107
(5)
RUN AND FAULT CONTACT ANNUNCIATION
RATED: 1AMP, 120VAC MAX.
K112 K105 K105
(3) (5) (3)
K105
(5) (5)
K105
(1)
(4) (6) (6) (2)
(3)
K109
(5)
TB1 7
DRIVE RUN
TB1 8 TB1 9
BYPASS RUN
TB1 10 TB1 11 TB1 12
DRIVE FAULT
(5)
K109
(1)
TB1 13 TB1 14 TB1 15 TB1
MOTOR OVERLOAD OR
CUSTOMER SAFETIES FAULT
16
Electrical Installation 2 - 25
Notes:
Electrical Installation 2 - 26
Chapter 3
Control Panel
This chapter describes the displays and functions of the Control Panel.
Digital Operator and Control Panel Display .................................... 2
Digital Operator Keys ................................................................. 3
Drive Mode Indicators ................................................................ 4
Control Panel Indicator Lights .................................................... 5
Drive Main Menus .......................................................................... 8
Main Menu Structure ................................................................. 9
DRIVE - Operation Menu ......................................................... 10
QUICK - Quick Setting Menu .................................................. 13
ADV- Programming Menu ....................................................... 14
VERIFY - Modified Constants (Parameters) Menu ................. 15
A.TUNE - Auto-Tuning Menu .................................................. 15
Example of Changing a Parameter .............................................. 16
Digital Operator 3 - 1
Digital Operator and Control Panel Display
The various items included on the Digital Operator Display and Control Panel are described below.
Menu Display
See Table 3.12
Key Descriptions
See Table 3.1
Blue
{
-DRIVE- Rdy
Frequency Ref
U101 = 60.00Hz
- - - - - - - - - - - - - - - - - - - - - - - - - - - - -
U1-02= 60.00Hz
U1-03= 10.05A
P7
Drive Mode Indicators
See Table 3.2
Ready Display
Drive can operate when a drive command is input
Data Display
Displays monitor data, parameter numbers and settings
1 line x 13 characters
3 lines x 16 characters
RUN & STOP Indicators
See Tables 3.4 and 3.5
White Green
Indicating Lights
Red
Amber
Red
Selector Switches
Fig 3.1 P7 Bypass Control Panel Component Names and Functions
Digital Operator 3 - 2
!
Digital Operator Keys
The names and functions of the Digital Operator Keys are described in Table 3.1.
Table 3.1 Digital Operator Keys
Key Name Function
MENU Key Scrolls from one of the five main menus to the next.
ESCAPE Key Returns to the display before the DATA/ENTER key was pressed.
MONITOR Key Selects the monitor (-DRIVE-) mode from any display location.
INCREASE Key Increases parameter numbers and set values. Used to move to the next item or data.
DECREASE Key
Decreases parameter numbers and set values. Used to move to the previous item or data.
SHIFT/RESET Key
Selects the digit to be changed. The selected digit will blink. Also resets the Drive when a fault has occurred.
DATA/ENTER Key Pressed to enter menus and parameters as well as to set values.
Digital Operator 3 - 3
!
Drive Mode Indicators
The definition of the Drive mode indicators are shown in Table 3.2.
Indicator
FWD
Table 3.2 Drive Mode Indicators
Definition
Lit when a forward run command is input. Also lit when the Drive is in “Hand” Mode.
REV Lit when a reverse run command is input.
AUTO SEQ Lit when set up for remote run command, see Table 3.3.
AUTO REF Lit when set up for remote speed command, see Table 3.3.
ALARM Lit when a fault has occurred and flashing when an alarm has occurred.
"
Drive AUTO Sequence (SEQ) and AUTO Reference (REF) indicators
The Bypass operates differently than a stand alone Drive with regard to these two indicators. The Bypass control logic interfaces with the Drive via terminals that would be used, in a Drive only installation, for the AUTO Sequence (Run Command), and
AUTO Reference (Speed Command).
Since these terminals are active and the appropriate parameters configured for the Bypass unit operation (see Tables 5.1 and
5.2), the AUTO Sequence and AUTO Reference LED’s will be lit even when the H/O/A is in HAND position (local control), providing both the run and speed command from the local control panel. The control signals are “Local” to the Drive and
Bypass unit, but “Remote” (AUTO) from the Drive itself.
Table 3.3 AUTO Sequence (SEQ) and Reference (REF) Indicator
Hand Mode
On
Auto Mode
On
Digital Operator 3 - 4
"
Drive Run Indicator
The status of the “RUN” indicator is shown in Table 3.4 when the Drive is either in the “Hand” or “Auto” mode.
Table 3.4 RUN Indicator
Indicator Status
On
Blinking
Off
Description
Drive is running
Drive is decelerating to a stop
Drive is stopped
"
Drive Stop Indicator
The status of the “STOP” indicator is shown in Table 3.5 when the Drive is either in the “Hand” or “Auto” mode.
Indicator Status
On
Blinking
Off
Table 3.5 STOP Indicator
Description
Drive is decelerating to a stop or stopped
Drive is in a run condition but the speed command is zero
Drive is running
!
Control Panel Indicator Lights
"
Control Power Indicator
Table 3.6 Control Power Indicator
Indicator Status
On
Off
Condition
3 Phase Power is applied to the Bypass unit and the control power transformer is functioning.
3 Phase Power is disconnected from the Bypass unit or a control power transformer fuse has cleared.
"
Drive Run Indicator
Indicator Status
On
Off
Table 3.7 Drive Run Indicator
Condition
The Drive has been given a run command in hand or auto mode and the Bypass circuit is de-energized.
The Drive has no run command in either the hand or auto modes. The unit may be operating in Bypass mode.
Digital Operator 3 - 5
"
Bypass Run Indicator
Indicator Status
On
Off
Table 3.8 Bypass Run Indicator
Description
The Bypass has been given a run command in the HAND or AUTO mode.
Or, the operation has been remotely transferred to Bypass using the switch selectable “Remote Transfer to Bypass” feature (S104) via a customer supplied contact closure at terminals TB1-25 and TB1-26.
Or, the operation has been automatically transferred to Bypass after a
Drive fault condition via the switch selectable “Auto Transfer to
Bypass” feature (S103).
Or, the operation has been transferred to Bypass using the switch-selectable “Smoke Purge” feature (S105) via a contact closure at terminals
TB1-17 and TB1-18.
The motor is running at full speed across-the-line and the Drive is deenergized.
The Bypass has no run command in either the HAND or AUTO modes.
The unit may be operating in Drive mode.
"
Motor OL/Safeties Fault Indicator
Indicator Status
On
Off
Table 3.9 Motor OL/Safeties Fault Indicator
Description
The motor overload (S10) has tripped OFF de-energizing both the
Drive and Bypass Circuits.
Or, the NC “motor safety circuit” connected to terminals TB1-1 and
TB1-2 has an open circuit condition.
The motor overload (S10) and NC “motor safety circuit” are satisfied.
Digital Operator 3 - 6
"
Drive Fault Indicator
Indicator Status
On
Off
"
Smoke Purge Indicator
Table 3.10 Drive Fault Indicator
Description
The Drive has tripped OFF due to an internal Drive fault.
The Drive is ready for operation, or operating normally.
Indicator Status
On
Off
Table 3.11 Smoke Purge Indicator
Description
The Smoke Purge function has been selected by closing switch S105 on
PCB A2 and the building fire control system has closed a contact between terminals TB1-17 and TB1-18.
Smoke Purge is not active, the Drive & Bypass are operating normally.
Digital Operator 3 - 7
Drive Main Menus
The Drive’s parameters and monitoring functions are organized into groups called menus that make it easier to read and set parameters. The Drive is equipped with five menus. The five menus and their primary functions are shown in Table 3.12 and are directly available by pressing the MENU key.
Main Menu
- DRIVE -
Operation
- QUICK -
Quick Setting
- ADV -
Programming
- VERIFY -
Modified Constants
(Parameters)
- A.TUNE -
Auto-Tuning
Table 3.12 Drive Main Menus
Primary Function(s)
The Drive can be run in this menu. Also called the “Monitor” menu.
Use this menu for monitoring values such as frequency reference or output current, displaying fault history or displaying the fault traces.
The Drive can be programmed in this menu.
Use this menu to set/read the most commonly used parameters.
The Drive can be programmed in this menu.
Use this menu to set/read every parameter.
The Drive can be programmed in this menu.
Use this menu to set/read the parameters that have been modified from their factory default settings.
For Bypass units Auto-Tuning can only be accomplished through the DriveWizard software. A free download from www.drives.com.
The Drive can be programmed in this menu.
Use this menu to auto-tune the Drive in order to utilize the bi-directional speed search feature.
Digital Operator 3 - 8
!
Main Menu Structure
The menu selection display will appear when the MENU key is pressed from a monitor or setting display. While viewing the menu selection display, press the MENU key repeatedly to scroll between the menu selections.
MENU
-DRIVE-
** Main Menu **
- - - - - - - - - - - - - -
Operation
MENU
-DRIVE-
** Main Menu **
- - - - - - - - - - - - - -
Quick Setting
MENU
-DRIVE-
** Main Menu **
- - - - - - - - - - - - - -
Programming
MENU
-DRIVE-
** Main Menu **
- - - - - - - - - - - - - -
Modified Consts
1
MENU
-DRIVE-
** Main Menu **
- - - - - - - - - - - - - -
Auto-Tuning
MENU
Press the DATA/ENTER key to enter the desired menu selection.
1
Modified Consts = Modified Parameters
Digital Operator 3 - 9
!
- DRIVE - Operation Menu
This menu is used for setting a speed command or monitoring values such as output frequency and output current. It is also used for displaying the fault history and the fault traces. The Drive may be limited to this menu in order to accept a run
command, see parameter b1-08 in Chapter 5 and Table 5.1.
"
U1 Monitor Parameter List
Follow the key operations below to access the Operation Menu.
x1
-DRIVE-
** Main Menu **
- - - - - - - - - - - - - -
Operation
-DRIVE- Rdy
Frequency Ref
U101 = 0.00Hz
- - - - - - - - - - - - - - - - - - - -
U1-02= 0.00Hz
U1-03= 0.00A
Use and keys to scroll through the U1 “Monitor” parameter list.
Monitor Parameters
U1-01 Frequency Ref
U1-02 Output Freq
U1-03 Output Current
U1-06 Output Voltage
U1-07 DC Bus Voltage
U1-08 Output kWatts
U1-10 Input Term Sts
U1-11 Output Term Sts
U1-12 Int Ctl Sts 1
U1-13 Elapsed Time
U1-14 FLASH ID
U1-15 Term A1 Level
U1-16 Term A2 Level
U1-18 Mot SEC Current
U1-20 SFS Output
U1-24 PI Feedback
U1-28 CPU ID
U1-29 kWh
U1-30 MWh
U1-34 OPE Detected
U1-36 PI Input
U1-37 PI Output
U1-38 PI Setpoint
U1-39 Transmit Err
U1-40 FAN Elapsed Time
U1-51 Auto Mode Fref
U1-52 Hand Mode Fref
U1-53 PI Feedback 2
Digital Operator 3 - 10
"
U2 Fault Trace Parameter List
After viewing the “Monitor” parameter list, in order to view the “Fault Trace” parameter list, follow the example below.
-DRIVE- Rdy
Monitor
U1 -01= 0.00Hz
- - - - - - - - - - - - - - - - - - - -
U1-02= 0.00Hz
U1-03= 0.00A
-DRIVE- Rdy
Fault Trace
U2 -01= None
- - - - - - - - - - - - - - - - - - - -
U2-02= None
U2-03= 0.00Hz
-DRIVE- Rdy
Current Fault
U201 = None
- - - - - - - - - - - - - - - - - - - -
U2-02= None
U2-03= 0.00Hz
Use and keys to scroll through the U2 “Fault Trace” parameter list.
Fault Trace Parameters
U2-01 Current Fault
U2-02 Last Fault
U2-03 Frequency Ref
U2-04 Output Freq
U2-05 Output Current
U2-07 Output Voltage
U2-08 DC Bus Voltage
U2-09 Output kWatts
U2-11 Input Term Sts
U2-12 Output Term Sts
U2-13 AC Drive Status
U2-14 Elapsed Time
Digital Operator 3 - 11
"
U3 Fault History Parameter List
After viewing the “Fault Trace” parameter list, in order to view the “Fault History” parameter list, follow the example below.
-DRIVE- Rdy
Fault Trace
U2 -01= None
- - - - - - - - - - - - - - - - - - - -
U2-02= None
U2-03= 0.00A
-DRIVE- Rdy
Fault History
U3 -01= None
- - - - - - - - - - - - - - - - - - - -
U3-02= None
U3-03= None
-DRIVE- Rdy
Last Fault
U301 = None
- - - - - - - - - - - - - - - - - - - -
U3-02= None
U3-03= None
Use and keys to scroll through the U3 “Fault History” parameter list.
Fault History Parameters
U3-01 Last Fault
U3-02 Fault Message 2
U3-03 Fault Message 3
U3-04 Fault Message 4
U3-05 Elapsed Time 1
U3-06 Elapsed Time 2
U3-07 Elapsed Time 3
U3-08 Elapsed Time 4
U3-09 Fault Message 5
U3-10 Fault Message 6
U3-11 Fault Message 7
U3-12 Fault Message 8
U3-13 Fault Message 9
U3-14 Fault Message 10
U3-15 Elapsed Time 5
U3-16 Elapsed Time 6
U3-17 Elapsed Time 7
U3-18 Elapsed Time 8
U3-19 Elapsed Time 9
U3-20 Elapsed Time 10
Digital Operator 3 - 12
!
- QUICK - Quick Setting Menu
This menu is used to set/read a limited set of parameters in the Drive. Follow the key operations below to access the Quick Setting Menu.
x2
-QUICK-
** Main Menu **
- - - - - - - - - - - - - -
Quick Setting
-QUICK-
Reference Source
- - - - - - - - - - - - - - - - - - - -
B1-01= 1
*1*
Terminals
“1”
Use and keys to scroll through the “Quick Setting” parameter list.
Parameter
Number
L6-03
L8-11 o1-01 o1-05 o1-07 o1-08 o2-03 o2-05 o2-08 o3-02
L2-01
L2-02
L4-05
L4-06
L5-01
L5-03
L6-01
L6-02 d2-02
E1-01
E2-01
F6-01
H3-02
H3-03
H3-10
H3-11
A1-00 b1-01 b1-02 b1-03 b1-04 b5-XX b8-01
C1-01
C1-02 d2-01
Parameter Name
Language Selection
Frequency Reference Selection
Run command Selection
Stopping Method Selection
Reverse Operation Selection
PI Mode Parameters
Energy Savings Control Selection
Acceleration Time 1
Deceleration Time 1
Frequency Reference Upper Limit
Frequency Reference Lower Limit
Input Voltage Setting
Motor Rated Current
Operation Selection After Communication Error
Terminal A1 Gain Setting
Terminal A1 Bias Setting
Terminal A2 Gain Setting
Terminal A2 Bias Setting
Momentary Power Loss Detection Selection
Momentary Power Loss Ride-thru Time
Frequency Reference Loss Detection Selection
Frequency Reference Level at Loss Frequency
Number of Auto Restarts Attempts
Maximum Restart Time After Fault
Torque Detection Selection 1
Torque Detection Level 1
Torque Detection Time 1
Heatsink Cooling Fan Operation Delay Time
User Monitor Selection
LCD Brightness Adjustment
Second Line User Monitor Selection
Third Line User Monitor Selection
User Parameter Default Value
Frequency Operation Time Selection
Cumulative Operation Time Selection
Read Allowed Selection
Digital Operator 3 - 13
!
- ADV- Programming Menu
This menu is used to set/read every parameter in the Drive. Follow the key operations below to access the Programming
Menu.
-ADV-
** Main Menu **
- - - - - - - - - - - - - -
Programming x3
-ADV-
Initialization
- - - - - - - - - - - - - - - - - - - -
A1 -00= 0
Select Language
Use , see Appendix A.
, and keys to scroll through the “Programming” parameter group list. For a complete parameter list
Parameter Group Functions
A1 Initialization
A2 User Parameters b1 Sequence b2 DC Braking b3 Speed Search b4 Delay Timers b5 PI Control b8 Energy Saving
C1 Accel/Decel
C2 S-Curve Acc/Dec
C4 Torque Comp
C6 Carrier Freq d1 Preset Reference d2 Reference Limits d3 Jump Frequencies d4 Sequence d6 Field-Weakening
E1 V/F Pattern
E2 Motor Setup
F6 Com OPT Setup
H1 Digital Inputs
H2 Digital Outputs
H3 Analog Inputs
H4 Analog Outputs
H5 Serial Com Setup
L1 Motor Overload
L2 PwrLoss Ridethru
L3 Stall Prevention
L4 Ref Detection
L5 Fault Restart
L6 Torque Detection
L8 Hdwe Protection n1 Hunting Prev n3 High Slip o1 Monitor Select o2 Key Selections o3 COPY Function
Digital Operator 3 - 14
!
- VERIFY - Modified Constants (Parameters) Menu
This menu is used to set/read only those parameters that have been modified from the Drive’s original factory default settings.
Follow the key operations below to access the Modified Constants (Parameters) Menu.
-VERIFY-
** Main Menu **
- - - - - - - - - - - - - -
Modified Consts x4
Note 1: If there are not any parameters that have been modified from their original factory default settings, then the display will state “None Modified”. Otherwise, use the “increase” and “decrease” keys to scroll through the “Modified
Constants” (Parameters) list.
!
- A.TUNE - Auto-Tuning Menu
For P7 Bypass units Auto-Tuning can only be accomplished through the DriveWizard software. A free download from www.drives.com.
This menu is used to auto-tune the Drive in order to utilize the bi-directional speed search feature. Follow the key operations below to access the Auto-Tuning Menu.
-A.TUNE-
** Main Menu **
- - - - - - - - - - - - - -
Auto-Tuning x5
-A.TUNE-
Mtr Rated Power
- - - - - - - - - - - - - - - - - - - -
T102 = 0.40kW
(0.00~650.00)
“0.40kW”
Use and keys to scroll through the “Auto-Tuning” parameter list.
Auto-Tuning Parameters
T1-02 Mtr Rated Power
T1-04 Rated Current
Digital Operator 3 - 15
Example of Changing a Parameter
Table 3.13 provides an example of how to change parameter “C1-02” (Deceleration Time 1) from 30 sec to 40 sec.
Step
Number
Table 3.13 Changing a Parameter in the Programming Menu
Digital Operator Display Description
1
-DRIVE- Rdy
Frequency Ref
U101 = 0.00Hz
- - - - - - - - - - - - - - - - - - - -
U1-02= 0.00Hz
U1-03= 0.00A
The Drive is first powered up.
2
-DRIVE-
** Main Menu **
- - - - - - - - - - - - - -
Operation
Press the MENU key to scroll to “Operation” menu.
3
4
5
6
7
-QUICK-
** Main Menu **
- - - - - - - - - - - - - -
Quick Setting
-ADV-
** Main Menu **
- - - - - - - - - - - - - -
Programming
-ADV-
Initialization
- - - - - - - - - - - - - - - - - - - -
A1 -01= 0
Select Language
-ADV-
Accel/Decel
- - - - - - - - - - - - - - - - - - - -
C1 -01= 1.0sec
Accel Time 1
-ADV-
Accel Time 1
- - - - - - - - - - - - - - - - - - - -
C101 = 30.0sec
(0.0~6000.0)
“30.0sec”
Press the MENU key to scroll to “Quick Setting” menu.
Press the MENU key to scroll to “Programming” menu.
Press the DATA/ENTER key to enter “Programming” menu.
Press the INCREASE key until C1-01 (Accel/Decel) is displayed.
Press the SHIFT/RESET key to move flashing digit to the right.
Digital Operator 3 - 16
Step
Number
Table 3.13 Changing a Parameter in the Programming Menu (Continued)
Digital Operator Display Description
8
-ADV-
Decel Time 1
- - - - - - - - - - - - - - - - - - - -
C102 = 30.0sec
(0.0~6000.0)
“30.0sec”
Press the INCREASE key to display C1-02 (Decel Time 1).
9
10
11
12
13
-ADV-
Decel Time 1
- - - - - - - - - - - - - - - - - - - -
C1-02= 0 030.0sec
(0.0~6000.0)
“30.0sec”
-ADV-
Decel Time 1
- - - - - - - - - - - - - - - - - - - -
C1-02= 0 0 30.0sec
(0.0~6000.0)
“30.0sec”
-ADV-
Decel Time 1
- - - - - - - - - - - - - - - - - - - -
C1-02= 00 3 0.0sec
(0.0~6000.0)
“30.0sec”
-ADV-
Decel Time 1
- - - - - - - - - - - - - - - - - - - -
C1-02= 00 4 0.0sec
(0.0~6000.0)
“30.0sec”
-ADV-
Entry Accepted
Press the DATA/ENTER key to access setting display.
Press the SHIFT/RESET key to move the flashing digit to the right.
Press the SHIFT/RESET key to move the flashing digit to the right.
Press the INCREASE key to increase the set data.
Press the DATA/ENTER key to enter the set data. “Entry Accepted” is displayed for 1.0 sec after the data setting has been confirmed.
14
15
16
-ADV-
Decel Time 1
- - - - - - - - - - - - - - - - - - - -
C102 = 30.0sec
(0.0~6000.0)
“30.0sec”
-DRIVE-
** Main Menu **
- - - - - - - - - - - - - -
Operation
-DRIVE- Rdy
Frequency Ref
U101 = 0.00Hz
- - - - - - - - - - - - - - - - - - - -
U1-02= 0.00Hz
U1-03= 0.00A
The monitor display for C1-02 returns.
Press the MENU key to scroll to “Operation” menu.
Press the DATA/ENTER key to enter “Operation” menu.
Digital Operator 3 - 17
Notes:
Digital Operator 3 - 18
Chapter 4
Start Up and Operation
This chapter describes the procedures to prepare for and conduct the P7B Drive and Bypass unit start up.
Start Up Introduction ...................................................................... 2
Bypass Start Up Preparation .......................................................... 3
Bypass Unit Start Up Procedure .................................................... 4
Bypass Operation Description......................................................... 8
Selector Switch Functions ......................................................... 9
Switch Selectable Functions .................................................... 10
Contact Closure Inputs and Outputs ....................................... 10
Start Up and Operation 4 - 1
Start Up Introduction
In order to provide you with the most reliable Drive and Bypass unit available, and to avoid any extra costs related to loss or reduction of warranty coverage, an authorized Yaskawa service representative should complete this start up procedure. Please complete the checklist in this document and maintain it in a secured location. Should you have a need to contact Yaskawa in the future, technical service personnel may request information from this document.
CAUTION
Procedures within this document assume that start up is being accomplished by a Yaskawa authorized service person who has training on the product and is capable of working through the detailed steps with power applied to the Bypass unit while the enclosure door is open.
Start Up and Operation 4 - 2
BYPASS START UP PREPARATION
! 1. Review this Bypass Technical Manual and any option instructions and schematics shipped with the Drive and Bypass unit.
! 2. Verify that the model numbers and voltage ratings are as specified in the purchase order by matching the nameplate data for each unit to the purchase order.
! 3. Verify that the unit has been installed in accordance with Chapter 1, Receiving and Mechanical Installation and
Chapter 2, Electrical Installation.
! 4. Inspect the security of the supply line power, ground connections and all control circuit connections as identified in
Chapter 2, Electrical Installation.
Double check all the power wires and motor wires.
Verify that the electrical supply power lines are connected to the input circuit breaker and that the motor leads are connected to the output terminals of the overload relay. Ensure that all connections are tight, loose wire connections may cause intermittent problems or overheating. Factory connections sometimes come loose during shipment.
! 5. Review the installer’s “as wired” schematic. Determine if a driven motor “safety circuit” is connected. This is a series circuit of NC contacts from devices such as a smoke/fire sensor, freeze-up thermostat or high static pressure limit switch. Verify that these customer emergency contacts are properly terminated in the Bypass safety shutdown circuit.
These contacts should be wired between terminal TB1-1 and TB1-2. No field programming is required.
Verify that all other field installed wires are correctly terminated (included the shields).
! 6. Verify that the motor is wired for the application voltage. Record the motor nameplate information:
Voltage _____________________________ Full Load Amps (FLA) _________________________________
(or Rated Load Amps (RLA)
! 7. Verify that the input voltage matches the Bypass unit rating.
! 8. Verify that the motor rated full load amps (FLA) does not exceed the rated output current of the Drive and Bypass controlling it. When multiple motors are simulaneously operated by the Drive, the sum of all motor FLA values must be less than or equal to that of the Drive and Bypass controlling them.
! 9. Record any other connections to the Bypass unit, by terminal number to determine if special programming of any of the following is required. (see Chapter 5 for programming details).
• Multi-function Digital Inputs
• Multi-function Digital Outputs
• Analog Outputs
• Differential PI control
! 10. Verify that the customer supplied logic is ready for the start, stop and speed command functions.
Start Up and Operation 4 - 3
BYPASS UNIT START UP PROCEDURE
(Please review “Bypass Start Up Preparation” on page 4-3)
! 1. Before applying power, make sure that the following conditions are met:
• The DRIVE/BYPASS switch is in the DRIVE position.
• The HAND/OFF/AUTO switch is in the OFF position.
• The NORMAL/TEST switch is in the NORMAL position. [Note: If the TEST position is selected while the
DRIVE/BYPASS switch is in the DRIVE position, the fault code “UV, DC Bus Undervolt” will be briefly displayed and the Drive will shut down. TEST mode is only available when in the BYPASS position.]
• The VAV terminal unit dampers, in supply fan applications, are open to prevent duct flexing or damage in a full speed, across the line starting situation.
• The electro-mechanical motor OverLoad Relay (OLR) (S10) is adjusted to equal the Full Load Amps (FLA) value from the motor nameplate.
The OLR is mounted to the contactor assembly or back panel (depending on rating), just above the Bypass contactor.
See Figure 4.1. Electrically on the output power side of the Bypass unit, the adjustable thermal OLR provides overload protection for the motor in both the Drive and Bypass operating modes. The OLR is set up in the factory to be a manual reset device, requiring operator attention if an overload trip-out is experienced.
OverLoad Relay
Adjustment Dial
Reset Button
Bypass Contactor
Fig 4.1 Typical Motor Overload and Contactors
IMPORTANT
To maintain overcurrent, short-circuit, and ground-fault protection, the manufacturer’s instructions for setting the motor OLR must be followed.
! 2. Apply power to the Drive and Bypass package. Ensure that all three phases are present and that the input voltage is correct for the system being set up. The CONTROL POWER ON, STOP and AUTO SEQ and REF LEDs on the control panel should be ON and the display will be in the “-DRIVE-/Operation” menu showing the active speed command. [Note: If the MOTOR OL/SAFETIES FAULT light is ON, press the reset button on the motor OLR (S10) and check the “safety device” circuit between terminals TB1-1 and TB1-2.].
Start Up and Operation 4 - 4
! 3. Various menus are directly available by pressing the MENU key (see Chapter 3). When in the “-DRIVE-/Operation” menu, the Drive can accept a run command from local (Hand mode) or remote (Auto mode) sources. Press the MENU key until the “-ADV-/Programming” menu is displayed. From here, any of the parameters can be accessed and changed using the
"
,
#
, and DATA/ENTER keys. See Appendix A for a list of programmable features. The
“-VERIFY-/Modified Consts” menu can be used to review or modify only those parameters that have been changed from the Drive’s default values. Using the
"
,
#
, and DATA/ENTER keys as needed, verify that the parameters are correct for the Drive and installation conditions. See the Factory Parameter Settings printed in Table 1 and Table 2 on page 2 of the Schematic Diagram that was shipped with the unit. Consider any additional parameter settings that may be needed by this specific application.
The Factory Parameter Settings table documents Drive parameter settings, required to interface with the Bypass logic circuit, that have been established at the factory and stored in a dedicated location in memory as “User
Initialization” values (think of it as a “back-up file”). If additional parameters are set to the specific needs of the application project, and the system operation has been checked and verified, then the “User Initialization” values should be stored in memory again by selecting and entering “1: Set Default” in parameter o2-03.
When there is a need for re-initialization of the “user” parameters (re-setting to the “User Initialization” values) of the
Bypass unit, then a “User Initialization” function should be carried out by selecting “1110: User Initialize” in parameter A1-03. This will re-establish the drive set-up required for the Bypass application and any “user” parameter values that have been stored.
The factory parameter settings required to interface with the bypass logic circuit have also been stored in the digital keypad memory. If there is a need for re-initialization (re-setting to a known factory starting point for trouble-shooting purposes) of the Bypass unit, then the “back-up file” in the digital keypad memory can be copied to the drive. In parameter o3-01 select “2: OP->INV WRITE” to carry out the copy function.
Table 1 of the schematic is also used to document parameters that have been factory set to typical values for fan and pump applications. These parameters may be changed to meet the needs of the specific application. In Table 5.1 of this manual shading is used to distinguish between settings required by the Bypass logic and those that may be changed.
! 4. From the “-ADV-/Programming” menu, go to parameter E1-01 and select the nominal input voltage that the Drive will receive in this specific application. The overall voltage classification of the Drive cannot be changed by this parameter.
However, the input voltage should be adjusted within the range available for the given voltage “class” of the Drive to match the input voltage level normally found on the jobsite. For example, 480 VAC class Drives may be employed on nominal three phase voltage distribution systems of: 380, 400, 415, 440, 460 or 480 VAC. The factory default values may need to be changed to meet the needs of the application distribution voltage.
! 5. From the “-ADV-/Programming” menu, go to parameter E2-01 and enter the Motor rated current. Set this parameter to the Full Load Amps (FLA) rating shown on the motor nameplate. This is essential for proper Drive operation and motor overload protection.
! 6. If the unit being started has the Speed Potentiometer option, proceed directly to step 7. Otherwise, press the
MONITOR key to return to the “-DRIVE-/Operation” menu. The AUTO SEQ and REF LEDs and the STOP and
CONTROL POWER ON LEDs on the control panel should be ON at this time.
To start the motor in Drive mode, move the HAND/OFF/AUTO switch to HAND. The DRIVE RUN LED will turn
ON and the Drive will ramp up to “6 HZ”. Verify that motor rotation is correct. [Note: In Bypass packages, the Drive is programmed at the factory for 5 seconds of DC injection braking at start (to stop a rotating motor when switching from BYPASS to DRIVE), expect to see this delay each time the Drive is started.]
If the direction of motor rotation is wrong, turn the HAND/OFF/AUTO switch to OFF; and turn the Power OFF!
Wait for the Red CHARGE LED (near the Drive power terminals) to go out. When it does, swap the wires in the motor junction box for T1 & T2 or on the output terminals of the motor OLR (S10). Tighten the terminal lugs, reapply the power, turn to HAND and re-check the rotation direction.
Start Up and Operation 4 - 5
! 7. If a Speed Potentiometer option is present, turn the Speed Potentiometer fully counterclockwise to ensure that the local speed command is zero. If necessary, press the MONITOR key to return to the “-DRIVE-/Operation” menu. The
AUTO SEQ and REF LEDs and the STOP and CONTROL POWER ON LEDs on the control panel should be ON at this time.
To start the motor in Drive mode, move the HAND/OFF/AUTO switch to HAND, then rotate the Speed Potentiometer clockwise to establish a speed command in the 6 to 10 Hz range. The DRIVE RUN LED will turn ON and the
Drive will ramp up to this setting. Verify that motor rotation is correct. [Note: In Bypass packages the Drive is programmed at the factory for 5 seconds of DC injection braking at start (to stop a rotating motor when switching from BYPASS to DRIVE), expect to see this delay each time the Drive is started.]
If the direction of motor rotation is wrong, turn the HAND/OFF/AUTO switch to OFF; and turn the Power OFF!
Wait for the Red CHARGE LED (near the Drive power terminals) to go out. When it does, swap the wires in the motor junction box for T1 & T2 or on the output terminals of the motor OLR (S10). Tighten the terminal lugs, reapply the power, turn to HAND; and re-check the rotation direction.
! 8. With correct motor rotation, press the MONITOR key, if necessary, to return to the “-DRIVE-/Operation” menu.
Using the
"
,
#
, and DATA/ENTER keys, manually run the Drive throughout its entire operating range, while observing operation. If excessive vibration of the driven load is noted at specific input frequencies, the Jump
Frequency function may be used to eliminate this vibration, by programming d3-01 through d3-04.
! 9. Determine whether the remote speed command is a 0-10 VDC or a 4-20 mA signal. The positive side of the signal should be connected to terminal A2 of the Drive terminal strip. The COMMON of the remote speed command signal should be connected to terminal AC of the Drive. See the connection diagram on page 1 of the Bypass schematic. [Note: The factory default is 4-20 mA, to change to 0 to 10 VDC adjust parameter H3-08 to “0: 0-10VDC” and move Drive DIP switch S1-2, on the Drive terminal PCB to the OFF position.]
! 10. Observe if the remote speed command can achieve the minimum and maximum speeds desired. If not, perform the following (see Chapter 5):
For 0-10 VDC input at Terminal A2
1. With no input, adjust the Bias (H3-11 setting) until an output of “0.0 Hz” is obtained.
2. With full scale input, adjust the Gain (H3-10 setting) until an output of “60.0 Hz” (or other desired maximum frequency) is obtained.
For 4-20 mA input at Terminal A2
1. With 4 mA input, adjust Bias (H3-11 setting) until an output of “0.0 Hz” is obtained.
2. With 20 mA input, adjust Gain (H3-10 setting) until an output of “60.0 Hz” (or other desired maximum frequency) is obtained.
! 11. Turn the HAND/OFF/AUTO switch to AUTO, then request a run command and speed reference signal from the building automation system to confirm remote (auto) operation.
! 12. In preparation for testing the Bypass, observe the trip setting of the circuit breaker (CB1). The trip point is factory set at the lowest possible setting and must be adjusted for each application. This breaker will trip due to inrush current and load inertia unless it is reset!
• For fan applications adjust the trip setting to ten times motor FLA.
• For pump applications adjust the trip setting to six times motor FLA.
If circuit breaker tripping is experienced at these settings during motor starting on Bypass, increase the setting gradually until the motor can be started without circuit breaker tripping.
Start Up and Operation 4 - 6
Adjustment Dial Label
Trip Setting
Adjustment Dial
MCP
Fig 4.2 Typical MCP Circuit Breaker
IMPORTANT
To maintain overcurrent, short-circuit, and ground-fault protection, the manufacturer’s instructions for setting the instantaneous-trip circuit breaker must be followed.
! 13. Turn the HAND/OFF/AUTO switch to OFF and the DRIVE/BYPASS switch to BYPASS. The Drive will ramp the motor to zero speed, then the Drive will be de-energized and control transferred to Bypass mode. Be prepared to monitor the rotation direction of the motor in Bypass operation. “Bump” the HAND/OFF/AUTO switch to the
HAND position and quickly back to OFF. Check the motor rotation. Do not allow the motor to continue operating in
BYPASS until rotation is correct!
If the rotation direction in Bypass is correct, skip the rest of this step. If not, carry out the following corrections:
1.
Turn OFF the incoming power feed to the Drive. Since the correct rotation in Drive mode was previously established, do not change any output wires at the motor.
2.
Instead, verify that power to the circuit breaker is OFF. Then swap L1 & L2 on the input side of the circuit breaker/disconnect switch (CB1). This will affect rotation in Bypass operation only. Once connections are complete and tight, reapply the incoming power and repeat the previous step to re-check the rotation direction in
Bypass mode.
! 14. Run the motor in Bypass by placing the HAND/OFF/AUTO switch in HAND. Record all the phase voltages and currents at this time.
! 15. Select the OFF position of the HAND/OFF/AUTO switch and place the BYPASS/DRIVE switch in DRIVE. Turn to the HAND position and scroll the Speed Command to “60 HZ” operation. Monitor the voltages and currents in each of the output phases at full speed to make sure the voltages are balanced and the currents are within the motor nameplate rating during accel, stable speed, and decel.
! 16. If this application requires the Drive to operate in PI mode, see Chapter 5.
! 17. For fan applications, with the HAND/OFF/AUTO switch set to AUTO, have the building automation system give the
Drive a run command and a speed command. Put the BYPASS/DRIVE switch into BYPASS and let the load speed up and stabilize. Then move the switch to DRIVE. Observe if the DC braking is enough to stop the fan in the time period set in parameter b2-03 (5 sec factory setting). If not, set this parameter to its maximum setting, which is 10.0 seconds.
If this is not enough, slowly increase the braking current setting (parameter b2-02) but do not go above 90% to protect the Drive output devices.
Start Up and Operation 4 - 7
Bypass Operation Description
(For manual switch positions, control inputs and switch selectable functions.)
The Bypass has two modes of operation: Bypass and Drive. When in the Bypass mode the connected motor is run directly from the incoming AC line, whereas in Drive mode the motor is run from the Drive output. The DRIVE/BYPASS switch located on the front panel determines operating mode. Within each operating mode are two methods of control; HAND and
AUTO. The HAND/OFF/AUTO switch on the front panel determines this control method.
Table 4.1 provides a look at various combinations of the control panel selector switch positions, control inputs to TB1 and the status of the switch selectable options.
A
A
A
A
H
H
H
H
A
A
A
O
H
H
H
H
H
O
A
A
A
H
H
H
A
A
D
D
D
D
B
B
B
D
D
D
D
B
B
B
B
D
D
D
D
B
D
D
D
D
D
N
N
N
T
N
T
N
N
N
N
T
N
T
N
N
N
N
N
N
N
N
N
N
N
N
Selector Switches
H/O/A D/B N/T
X
X
X
X
X
X
X
X
X
X
X
X
Table 4.1 Bypass Inputs and Operating Mode
Contact Closure Inputs Switch Selectable Functions
Auto Xfer Remote Xfer Smoke Purge
Run
TB1
3 & 4
Enable
TB1
5 & 6
Safety
TB1
1 & 2
S103
DRV
FLT
S104
TB1
25 & 26
S105
TB1
17 & 18
X
0
X
X
X
X
0
X
0
0
0
0
0
0
0
0
0
0
0
0
0
X
0
X
X
X
X
0
X
X
X
0
X
X
X
0
X
X
0
X
X
X
X
0
0
0
0
X
X
0
X
0
0
0
0
X 0
0
0
X
0
0
0
0
0
0
0
X
X
X
X
X
X
X
X
X
X
X
X
X
X
0
X
X
X
X
X
X
X
0
X
X
X
X
X
0
X
X
X
X
X
X
X
0
X
Operating Mode
Result
None
Drive
None
None
None
Bypass
Bypass*
None
None
Drive
None
None
None
Bypass
Bypass*
None
None
Drive
Bypass
Bypass
Bypass
Bypass
Drive
Bypass
Bypass
Bypass
Note: A blank cell indicates the input can be in any of the possible positions.
* = Drive energized, output contactor open.
Table 4.1 Definitions:
H/O/A = Hand/Off/Auto
D/B = Drive/Bypass
N/T = Normal/Test
DRV FLT = Drive Fault Contacts
TB = Terminal Block
S10X = Slide Switch Number
X = Closed Contacts or Enabled
0 = Open Contacts or Disabled
Start Up and Operation 4 - 8
For additional influences on the Drive behavior in Drive operating mode, consult Table 5.1 and Table 5.2. These tables explain the settings of Drive parameters required by the Bypass logic (Table 5.1) and those that are also dependent upon the control options present on the unit (Table 5.2). For Example: In the second line of Table 5.2, for a Bypass equipped with no options and switch S1-2 in the off position, the hand mode speed command is based on the setting of d1-02 and the auto mode speed command signal is 0-10VDC.
$
Selector Switch Functions
Operating in HAND position - Drive mode:
The Drive can be operated locally from the control panel by first placing the DRIVE/BYPASS switch in DRIVE. Then placing the HAND/OFF/AUTO switch in the HAND position gives the front panel control of the Drive operation.
Moving the switch to HAND also provides the run command to the Drive. When placed into HAND mode the Drive begins running at the hand mode speed command.
Operating in AUTO position - Drive mode:
The Drive can be operated remotely by placing the DRIVE/BYPASS switch in DRIVE. Then placing the HAND/OFF/
AUTO switch in the AUTO position gives a remote device (separate source or DDC) control of the Drive. In the AUTO position the Drive will look for a run command contact closure at terminals TB1-3 and TB1-4 on the relay PCB A2.
Speed command signal level and source is determined by the parameter settings and the options present in the unit, see
Tables 5.1 and 5.2. The AUTO speed command must be wired directly to the Drive terminals A2 and AC, not the control terminal block TB1. Consult Figures 2.7 and 2.8 in Chapter 2, Electrical Installation for correct configuration of the speed command (analog frequency reference).
Operating in HAND position - Bypass mode:
The Bypass can be operated locally from the front control panel by placing the DRIVE/BYPASS switch in BYPASS. In
BYPASS mode the Bypass contactor coil can be energized manually by placing the HAND/OFF/AUTO switch in
HAND position. In Bypass mode, moving the HAND/OFF/AUTO switch to HAND causes the motor to run at full speed, directly “across the line”.
Operating in AUTO position - Bypass mode:
The Bypass can be operated remotely by placing the DRIVE/BYPASS switch in BYPASS and the HAND/OFF/AUTO switch in AUTO. In the AUTO position the Bypass will look for a run command contact closure at terminals TB1-3 and
TB1-4 on the relay PCB A2, to control the run/stop status of “across the line” full speed motor operation.
Operating in TEST position - Bypass mode:
TEST position is used to energize the Drive input contactor while operating in the Bypass mode. The only valid use of the
TEST position is in Bypass mode. In Drive mode, switching from NORMAL to TEST position will remove the Drive run command and the motor will stop. In Bypass mode, the test position powers the Drive for programming or other
“tests” while keeping it isolated from the motor.
Start Up and Operation 4 - 9
$
Switch Selectable Functions
The switch selectable functions, Smoke Purge, Auto Transfer and Remote Transfer represent various methods of transferring from the Drive mode of operation to the Bypass mode. They may be enabled in any combination from none of them to all of them. See Table 4.1 for a summary of some common combinations of these switch selectable inputs.
Smoke Purge: When enabled (switch S105) this function allows a contact closure between terminals TB1-17 and TB1-18 to transfer motor operation to Bypass for a maximum capacity smoke control function. When in smoke purge mode, during emergency fire/smoke situations, the motor overloads and safety interlock circuit are overridden to shift the priority to protecting people rather than equipment. [Note: Smoke purge overrides all other control inputs and selector switches.
Smoke purge operation can only be terminated by opening the contact closure at terminals TB1-17 and TB1-18 or by opening the Circuit Breaker (CB1).]
Auto Transfer to Bypass: When enabled (switch S103), the Bypass unit will automatically switch into Bypass mode on a
Drive fault. After clearing the Drive fault condition, the function resets by moving the HAND/OFF/AUTO switch to the
OFF position and waiting for the keypad to go blank. CAUTION: Before selecting this function in fan applications, care must be taken to ensure that the ductwork is designed to handle the pressure resulting from full speed operation with the
VAV terminal unit dampers at minimum position or closed.
Remote Transfer to Bypass: When enabled (switch S104), this function allows a customer supplied contact closure, between terminals TB1-25 and TB1-26, to transfer motor operation from Drive mode to Bypass mode. This remote transfer to Bypass function overrides the DRIVE/BYPASS manual switch. An open contact causes operation in Drive mode and a closed contact results in Bypass mode.
$
Contact Closure Inputs and Outputs
Customer Safety Interlocks Input: Terminals TB1-1 and TB1-2 are used as a Drive or Bypass override from the NC contacts of the customer’s safety device series circuit. Anytime all the safety device contacts are closed, the Drive or Bypass will operate. When any one of these contacts open, the Drive or Bypass will immediately stop operating. This input is momentary, when a customer safety device contact re-closes, the Drive or Bypass will return to operation.
Auto Mode Run/Stop Contact Input: TB1-3 and TB1-4 are input terminals used for the Run/Stop command when in the
AUTO mode. When these input contacts close, the unit will begin running. When the contacts reopen, the unit will cease running.
Customer Supplied Interlock or Drive Enable Input: An open contact at TB1-5 and TB1-6 will override the run command, preventing Drive or Bypass operation until these input contacts are closed. For example this input could insure that the system dampers achieve an operating position before the fan is started in order to protect the ductwork from over pressure.
Drive Run Contact Output: Terminals TB1-7 and TB1-8 are an output contact that closes whenever the motor is running in
Drive mode. If the Drive is receiving a run command, but a fault condition occurs, this contact will not be closed.
Bypass Run Contact Output: Terminals TB1-9 and TB1-10 are an output contact that closes whenever the motor is running in
Bypass mode. If the Bypass is receiving a run command, but a fault condition occurs, this contact will not be closed.
Drive Fault Contact Output: Terminals TB1-11, TB1-12 and TB1-13 are a Form C set of output relay contacts, NO and NC that are activated when the Drive is in a fault condition.
Start Up and Operation 4 - 10
Motor Overload or Customer Safeties Fault Contact Output: Terminals TB1-14, TB1-15 and TB1-16 are a Form C set of output relay contacts, N.O. and N.C. that are activated when one of the N.C. contacts of the Customer Safety device input series circuit or the motor overload relay contacts is opened.
120VAC Damper Actuator Output: Output terminals TB1-19 and TB1-20 are provided to energize a damper actuator circuit or solenoid air valve, typically for outdoor air intake dampers. When the motor is stopped, the output voltage is removed in order to close the dampers. Whenever the Drive or Bypass is running, the terminals output 120VAC to power a 40VA damper actuator circuit.
120VAC Control Power Output: Output terminals TB1-21 and TB1-22 are provided to energize additional, customer defined control logic circuits. A maximum of 100VA control power is available, the user must provide the short circuit protection.
Optional Two Motor “OR” Selection Input: Terminals TB1-23 and TB1-24 are used only when the “Two Motor OR option” is part of the unit. These input terminals are used for choosing between motor 1 or motor 2 when the optional
MOTOR 1/AUTO/MOTOR 2 selector switch is in the AUTO position.
Start Up and Operation 4 - 11
Notes:
Start Up and Operation 4 - 12
Chapter 5
Programming
This Manual contains descriptions of all parameters in the Drive that may be useful in
Bypass applications. Parameters are listed in alpha-numerical order. Parameter number and name, along with a detailed description and its settings are described on the following pages.
Bypass Basic Programming Parameters ........................................ 2
Discussion of Table 5.2 Option-Dependent Bypass
Parameter Settings: ................................................................... 5
A1 Initialization .......................................................................... 9 b1 Sequence ........................................................................... 11 b2 DC Braking ......................................................................... 16 b3 Speed Search ..................................................................... 18 b5 PI Function ......................................................................... 22 b8 Energy Savings .................................................................. 37
C1 Accel/Decel ........................................................................ 38 d1 Preset References .............................................................. 39 d2 Reference (Speed Command) Limits .................................. 41 d3 Jump Frequencies .............................................................. 42 d4 Sequence ........................................................................... 43
E1 V/f Pattern .......................................................................... 44
E2 Motor Setup ........................................................................ 50
F6 Com OPT Setup
(Applies only to the LonWorks® option) .............................. 51
H1 Digital Inputs ...................................................................... 52
H2 Digital Outputs .................................................................... 57
H3 Analog Inputs ..................................................................... 58
L2 Momentary Power Loss Ride-thru Function ....................... 64
L3 Stall Prevention ................................................................... 65
L4 Speed Command Loss Detection ....................................... 68
L5 Fault Restart ....................................................................... 69
L6 Torque Detection ................................................................ 71
L8 Hardware Protection ........................................................... 73 o1 Monitor Configuration ......................................................... 75 o2 Key Selections .................................................................... 79 o3 Digital Operator Copy Function .......................................... 82
T1 Auto-Tuning ........................................................................ 85
Programming 5 - 1
Bypass Basic Programming Parameters
The basic Drive programming for a Bypass unit is different from that of a Drive installation without the Bypass option.
Several Drive parameters have been programmed at the factory to meet the needs of the Bypass logic circuit. See Table 5.1 below, the highlighted parameters are required by the Bypass logic circuit.
PARAMETER
NUMBER b1-01 b1-07 b1-08 b2-03 d1-01 d1-02 d1-04
E1-01
F6-01
H1-01
H1-02
H1-03
H2-02
H3-02
H3-08
Table 5.1 Bypass Parameter Settings
SETTING
For
Bypass
Drive
Default
1 SEE
TABLE
5.2
1 0
UNITS
N/A
N/A
DESCRIPTION
Frequency Reference Selection – Selects the speed command input source
1
5.0
10.0
6.0
40.0
208,
240 or
480
3
0
0.0
0.0
0.0
0.0
240 or
480
1
N/A
SEC
HZ
HZ
HZ
VOLT
S
N/A
Local/Remote Run Selection – Determines acceptability of a remote run command when switching from hand (local) mode to auto (remote) mode
Run Command Selection During Programming –
Selects if run command is accepted in DRIVE Operation menu only or in all menus.
DC Injection Braking Time At Start – Sets the braking time at Drive start, to stop a coasting motor before starting
Frequency Reference 1 – Hand Mode Speed Reference, used with serial communication, see Table 5.2 and H1-03
Frequency Reference 2 – Hand Mode Speed Reference, used without serial communication, see Table
5.2 and H1-03
Frequency Reference 4 – Speed Reference, used with serial communication loss and H5-04 = “4: Run at d1-04”
Input Voltage Setting – Set to the nominal Voltage
Setting for the incoming line
70 24
14
N/A
N/A
Operation Selection After Communication Error –
Selects the serial com error response, alarm and continue operation
Terminal S3 Function Selection – Set for Drive run enable
Terminal S4 Function Selection – Set for fault reset or Frequency Reference 1
SEE
TABLE
5.2
SEE
TABLE
5.2
3B
3
A
N/A
N/A
Terminal S5 Function Selection – Set For Frequency
Reference 1 or Serial Communication
100.0
%
Terminals M3 - M4 Function Selection – Set for serial communication run command
Terminal A1 Gain Setting SEE
TABLE
5.2
SEE
TABLE
5.2
2 N/A Terminal A2 Signal Level –Signal selection, 0 to 10
VDC (Drive control board switch S1-2 off) or 4 to 20 mA (Drive control board switch S1-2 on)
KEYPAD DISPLAY
For Bypass Setting
Reference Source /
Terminals
LOC/REM RUN Sel /
Accept Extrn RUN
RUN CMD at PRG /
Enabled
Dcinj Time@Start /
(0-10)
Reference 1 / (0-60)
Reference 2 / (0-60)
Reference 4 / (0-60)
Input Voltage / (range)
Com Bus Flt Sel / Alarm
Only
Terminal S3 Sel / Drive
Enable
Terminal S4 Sel / Multi-
Step Ref 1
Terminal S5 Sel / Multi-
Step Ref 1
Term M3-M4 Sel / Com
RUN Command
Terminal A1 Gain /
(0-1000)
Term A2 Signal / 0-10
VDC
Programming 5 - 2
PARAMETER
NUMBER
H3-09
H3-13
L4-05
L5-01
L5-03 o2-02 o2-03 o2-15 o3-02
SETTING
For
Bypass
Drive
Default
2 SEE
TABLE
5.2
SEE
TABLE
5.2
0
0 1
10.0
600
0
1
0
1
0
180
1
0
1
0
Table 5.1 (Continued)Bypass Parameter Settings
UNITS
N/A
N/A
N/A
N/A
SEC
N/A
N/A
N/A
DESCRIPTION
Terminal A2 Function Selection – Selects how this input will be used by the Drive
Master Frequency Reference Terminal Selection –
Determines which terminal (A1 or A2) will be the main speed reference source.
Frequency Reference Loss Detection Selection –
Determines Drive response to loss of the frequency speed command
Number of Re-start Attempts – Sets the number of times the Drive will perform an automatic re-start
Maximum Restart Time After Fault – If not successfully started after this time, restart attempts stop and
Drive faults
OFF Key Function During Auto Run - Enables or disables the Off key.
User Initialization - Factory set parameter for user default values.
Hand Key Function Selection - Enables or disables the Hand and Auto keys.
Read Allowed Selection – Enables or disables keypad copy functions
KEYPAD DISPLAY
For Bypass Setting
Terminal A2 Sel / Aux
Reference
TA1/A2 Select / Main
Fref TA1
Ref Loss Sel / Stop
Num of Restarts / (0-10)
Max Restart Time /
(.5-600.0)
Oper STOP Key /
Disabled
Hand Key / Disabled
Read Allowable /
Enabled
Shaded Areas = Parameter settings required by the Bypass logic
The shaded Bypass Parameter Settings in Table 5.1 document Drive parameter settings, required to interface with the Bypass logic circuit, that have been established at the factory and stored in a dedicated location in the memory as “User Initialization” values (think of it as a “back-up file”).
Table 5.1 is also used to document parameters that have been factory set, for convenience, to typical values for fan and pump applications. These parameters may be changed to meet the needs of the specific application.
If additional parameters are set to the specific needs of the application project, and the system operation has been checked and verified, then the “User Initialization” values should be stored in memory again by selecting and entering “1: Set Default” in parameter o2-03.
When there is a need for re-initialization of the “user” parameters (re-setting to the “User Initialization” values) of the Bypass unit, then a “User Initialization” function should be carried out by selecting “1110: User Initialize” in parameter A1-03. This will re-establish the drive set-up required for the Bypass application and any “user” parameter values that have been stored.
The factory parameter settings required to interface with the bypass logic circuit have also been stored in the digital keypad memory. If there is a need for re-initialization (re-setting to a known factory starting point for trouble-shooting purposes) of the Bypass unit, then the “back-up file” in the digital keypad memory can be copied to the drive. In parameter o3-01 select
“2: OP->INV WRITE” to carry out the copy function.
Programming 5 - 3
Options
Table 5.2 Option Dependent Bypass Parameter Settings
Parameters Effected by Options Specified and
Settings
Resulting Hand Speed
Command Source b1-
01
H1-
02
H1-
03
H3-
02
H3-
08
H3-
09
H3-
13
Drive PCB
Switch S1
1 2 d1-
01
Keypad d1-
02 d1-
04
Resulting Auto Speed
Command Signal
Terminal A2
Speed
Pot.
4-20 mA
0-10
VDC
3-15
PSIG
Serial Com
#
Run Speed
X None
None
P
P and S 1
S 1
S
G, H, Q,
V
G, H, Q,
V
G, H, Q,
V and P
G, H, Q,
V and S
L
1
0
0
0
1
L
0
0
L and P
L and S
1* 14* 3*
1
1
14
14
3
3
0
1
14
14
14
14
3
3
3
@
@
14
14
@
3
@
14
3
3
3
0.0
0.0
0.0
100*
100
100
6C 0.0
6C
6C
6C
6C
6C
6C
6C
0.0
0.0
100
0.0
0.0
0.0
100
2*
0
2
2
2
0
2
0
2
2
2
0
2
2
2
2
2*
2
0
0
0
2
2
2
2
2
2
2
1 Off* On*
1 Off Off
1 Off On
1 Off On
1 Off On
1 Off Off
0* Off On
0 Off Off
0 Off On
0 Off On
0
0
0
0
On On
On Off
On On
On On
X
X
X
X
X
X
X
X
X
X
X
X
X
X
X
X
X
X
X
X
X
X
X
X
X
X
X
X
X
X
X
X
X
X
X
X
X
X
X
Definitions:
L = LonWorks Option Card
S = Speed Potentiometer
V = Native Protocol (Modbus)
P = Pneumatic Pressure Transducer (3-15 PSIG)
G = DeviceNet Option Card
H = Profibus Option Card
Q = Ethernet Option Card
Parameter Reference: b1-01: Speed Command Input Source
0: Operator
1: Terminals
H1-02: Terminal S4 Function Selection
3: Multi-step Ref 1
14: Fault Reset
H1-03: Terminal S5 Function Selection
3: Multi-step Ref 1
6C: Com/Inv Sel 2
H3-02: Terminal A1 Gain Setting
H3-08: Terminal A2 Signal Level
0: 0 - 10 VDC
2: 4 - 20 mA
H3-09: Terminal A2 Function Selection
0: Frequency Bias
2: Aux Reference
* = The Drive factory default
# = The H/O/A switch must be in the AUTO position to allow serial com. to control the Drive.
@ = Jumpers required from S5 to S6 and S4 to SN
H3-13: Master Frequency Reference Terminal Selection d1-01: d1-02: d1-04:
0: Main Fref TA1
1: Main Fref TA2
Frequency Reference 1
Frequency Reference 2
Frequency Reference 4
Note: Hand mode run/stop for Drive and Bypass is always via the front control panel HAND/OFF/AUTO switch.
Programming 5 - 4
!
Discussion of Table 5.2 Option-Dependent Bypass Parameter Settings:
Drive Parameter Settings for Various Combinations of Bypass and Options
Notes:
See Appendix D, Communications, for additional information on serial communication.
Hand mode run/stop for Drive and Bypass is always via the front control panel HAND/OFF/AUTO switch.
The HAND/OFF/AUTO switch must be in AUTO position if serial communication is to be used to control the Drive.
For "monitoring only" of Drive parameters and operation, via serial communication, the user needs only to set-up the
H5-0X "Serial Com Setup" parameters. All other parameters may remain as they were factory programmed for the
Bypass unit and options.
Option L, LonWorks serial communication always requires DIP switch S1-1 (terminating resistor) to be ON.
"
Options - None; Bypass with no options:
Hand mode speed command from Keypad/Operator.
Auto mode speed command input signal, 4-20 mA applied to Drive terminal A2.
Auto mode run/stop contact closure for Drive and Bypass applied to terminals TB1-3 and TB1-4.
Significant
Parameter Setting b1-01 = 1: Terminals (default)
H3-13 = 1: Main Fref TA2
H3-08 = 2: 4-20 mA (default)
H3-02 = 0.0
H3-09 = 0: Frequency Bias
H1-03 = 3: Multi-Step Ref 1
(default)
Result
Speed command source = Terminals
Specific speed command source = Terminal A2
Terminal A2 is programmed for 4-20 mA (Note – Control PCB DIP switch S1-2 must also be ON)
Terminal A1 gain = 0.0 (To insure no stray signal level at this unused terminal)
Terminal A2 function is set to “bias” the terminal A1 input. Terminal A1 is not used, therefore the A2 “bias” signal becomes the speed command.
A terminal S5 input contact closure selects d1-02 (keypad) as a preset speed. This input contact is closed when H/O/A = Hand.
"
Options - None; Bypass with no options:
Hand mode speed command from Keypad/Operator.
Auto mode speed command input signal, 0-10 VDC applied to Drive terminal A2.
Auto mode run/stop contact closure for Drive and Bypass applied to terminals TB1-3 and TB1-4.
Significant
Parameter Setting b1-01 = 1: Terminals (default)
H3-13 = 1: Main Fref TA2
H3-08 = 0: 0-10 VDC
H3-02 = 0.0
H3-09 = 0: Frequency Bias
H1-03 = 3: Multi-Step Ref 1
(default)
Result
Speed command source = Terminals
Specific speed command source = Terminal A2
Terminal A2 is programmed for 0-10 VDC (Note – Control PCB DIP switch S1-2 must also be OFF)
Terminal A1 gain = 0.0 (To insure no stray signal level at this unused terminal)
Terminal A2 function is set to “bias” the terminal A1 input. Terminal A1 is not used, therefore the A2 “bias” signal becomes the speed command.
A terminal S5 input contact closure selects d1-02 (keypad) as a preset speed. This input contact is closed when H/O/A = Hand.
Programming 5 - 5
"
Options - P "Pneumatic Pressure Transducer"; Bypass with pneumatic input for speed control:
Hand mode speed command from Keypad/Operator.
Auto mode speed command input signal from the pneumatic transducer, or 4-20 mA applied to Drive terminal A2.
Auto mode run/stop contact closure for Drive and Bypass applied to terminals TB1-3 and TB1-4.
Significant
Parameter Setting b1-01 = 1: Terminals (default)
H3-13 = 1: Main Fref TA2
H3-08 = 2: 4-20 mA (default)
H3-02 = 0.0
H3-09 = 0: Frequency Bias
H1-03 = 3: Multi-Step Ref 1
(default)
Result
Speed command source = Terminals
Specific speed command source = Terminal A2
Terminal A2 is programmed for 4-20 mA (Transducer output is 4-20 mA) (Note
– Control PCB DIP switch S1-2 must also be ON)
Terminal A1 gain = 0.0 (To insure no stray signal level at this unused terminal)
Terminal A2 function is set to “bias” the terminal A1 input. Terminal A1 is not used, therefore the A2 “bias” signal becomes the speed command.
A terminal S5 input contact closure selects d1-02 (keypad) as a preset speed.
This input contact is closed when H/O/A = Hand.
"
Options - P and S "Pneumatic Pressure Transducer" and "Speed Pot."; Bypass with pneumatic input and speed potentiometer for speed control:
Hand mode speed command from speed potentiometer.
Auto mode speed command input signal from the pneumatic transducer, or 4-20 mA applied to Drive terminal A2.
Auto mode run/stop contact closure for Drive and Bypass applied to terminals TB1-3 and TB1-4.
Significant
Parameter Setting b1-01 = 1: Terminals (default)
H3-13 = 1: Main Fref TA2
Result
Speed command source = Terminals
Main speed command source = Terminal A2 and the Aux speed command source
= Terminal A1
H3-08 = 2: 4-20 mA (default) Terminal A2 is programmed for 4-20 mA (Transducer output is 4-20 mA) (Note
– Control PCB DIP switch S1-2 must also be ON)
H3-09 = 2: Aux Reference (default) Aux Terminal (A1) function is set to be a speed command input.
H1-03 = 3: Multi-Step Ref 1
(default)
A terminal S5 input contact closure selects Aux Terminal (A1) as a preset speed.
This input contact is closed when H/O/A = Hand.
"
Options - S "Speed Pot."; Bypass with speed potentiometer for speed control:
Hand mode speed command from speed potentiometer.
Auto mode speed command input signal, 4-20 mA applied to Drive terminal A2.
Auto mode run/stop contact closure for Drive and Bypass applied to terminals TB1-3 and TB1-4.
Significant
Parameter Setting b1-01 = 1: Terminals (default)
H3-13 = 1: Main Fref TA2
Result
Speed command source = Terminals
Main speed command source = Terminal A2 and the Aux speed command source
= Terminal A1
H3-08 = 2: 4-20 mA (default) Terminal A2 is programmed for 4-20 mA (Note – Control PCB DIP switch S1-2 must also be ON)
H3-09 = 2: Aux Reference (default) Aux Terminal (A1) function is set to be a speed command input.
H1-03 = 3: Multi-Step Ref 1
(default)
A terminal S5 input contact closure selects Aux Terminal (A1) as a preset speed.
This input contact is closed when H/O/A = Hand.
Programming 5 - 6
"
Options - S "Speed Pot."; Bypass with speed potentiometer for speed control:
Hand mode speed command from speed potentiometer.
Auto mode speed command input signal, 0-10 VDC applied to Drive terminal A2.
Auto mode run/stop contact closure for Drive and Bypass applied to terminals TB1-3 and TB1-4.
Significant
Parameter Setting
Result b1-01 = 1: Terminals (default)
H3-13 = 1: Main Fref TA2
Speed command source = Terminals
Main speed command source = Terminal A2 and the Aux speed command source = Terminal A1
H3-08 = 0: 0-10 VDC Terminal A2 is programmed for 0-10 VDC (Note –
Control PCB DIP switch S1-2 must also be OFF)
H3-09 = 2: Aux Reference (default) Aux Terminal (A1) function is set to be a speed command input.
H1-03 = 3: Multi-Step Ref 1 (default) A terminal S5 input contact closure selects Aux Terminal (A1) as a preset speed. This input contact is closed when H/O/A = Hand.
"
Options - G, H, L, Q, or V "Serial Communications"; Bypass with serial communication for control:
Hand mode speed command from Keypad/Operator.
Auto mode speed command input signal from serial communication.
Auto mode run/stop command for Drive from serial communication.
Auto mode run/stop contact closure for Bypass applied to terminals TB1-3 and TB1-4.
Significant
Parameter Setting b1-01 = 0: Operator
H1-03 = 6C: Com/Inv Sel 2
Result
Speed command source = Keypad/Operator (d1-01)
A terminal S5 input contact closure allows b1-01 to select d1-01 (keypad) as a preset speed. An open contact selects serial com for speed command and run/ stop. This input contact is closed when H/O/A = Hand.
"
Options - G, H, L, Q, or V "Serial Communications"; Bypass with serial communication for run/stop control and speed monitoring:
Hand mode speed command from Keypad/Operator.
Auto mode speed command input signal, 0-10 VDC applied to Drive terminal A2.
Auto mode run/stop command for Drive from serial communication.
Auto mode run/stop contact closure for Bypass applied to terminals TB1-3 and TB1-4.
Significant
Parameter Setting
Result b1-01 = 0: Operator
H3-08 = 0: 0-10 VDC
Speed command source = Keypad/Operator (d1-01)
Terminal A2 is programmed for 0-10 VDC (Note – Control PCB DIP switch
S1-2 must also be OFF)
H3-09 = 2: Aux Reference (default) Terminal A2 function is set to be a speed command input. This setting also gives terminal A2 priority over d1-02 for “preset speed 2”, see Programming
Manual.
H1-02 = 3: Multi-Step Ref 1
S4 must be jumpered to SN
H1-03 = 6C: Com/Inv Sel 2
A terminal S4 input contact closure selects A2 as “preset speed 2” speed input.
The S4 input is jumpered to SN, therefore it is always closed.
A terminal S5 input contact closure allows b1-01 to select d1-01 (keypad) as a preset speed. An open contact selects serial com for the run/stop command
(the serial com speed command is overridden by the preset speed above). This input contact is closed when H/O/A = Hand.
H1-04 = 4: Multi-Step Ref 2 (default)
S6 must be jumpered to S5
A terminal S6 input contact closure selects d1-04 (keypad) as a speed input.
When open, the speed command is determined by “preset speed 2”. This input contact is closed when H/O/A = Hand.
Programming 5 - 7
"
Options - G, H, L, Q, or V and P "Serial Communications" and "Pneumatic Pressure Transducer"; Bypass with serial communication for run/stop control and speed monitoring, with pneumatic input for speed control:
Hand mode speed command from Keypad/Operator.
Auto mode speed command input signal from the pneumatic transducer, or 4-20 mA applied to Drive terminal A2.
Auto mode run/stop command for Drive from serial communication.
Auto mode run/stop contact closure for Bypass applied to terminals TB1-3 and TB1-4.
Significant
Parameter Setting b1-01 = 0: Operator
H3-08 = 2: 4-20 mA (default)
H3-09 = 2: Aux Reference (default)
H1-02 = 3: Multi-Step Ref 1
S4 must be jumpered to SN
H1-03 = 6C: Com/Inv Sel 2
H1-04 = 4: Multi-Step Ref 2 (default)
S6 must be jumpered to S5
Result
Speed command source = Keypad/Operator (d1-01)
Terminal A2 is programmed for 4-20 mA (Transducer output is 4-20 mA)
(Note – Control PCB DIP switch S1-2 must also be ON)
Terminal A2 function is set to be a speed command input. This setting also gives terminal A2 priority over d1-02 for “preset speed 2”, see
Programming Manual.
A terminal S4 input contact closure selects A2 as “preset speed 2” speed input. The S4 input is jumpered to SN, therefore it is always closed.
A terminal S5 input contact closure allows b1-01 to select d1-01 (keypad) as a preset speed. An open contact selects serial com for the run/stop command (the serial com speed command is overridden by the preset speed above). This input contact is closed when H/O/A = Hand.
A terminal S6 input contact closure selects d1-04 (keypad) as a speed input. When open, the speed command is determined by “preset speed 2”.
This input contact is closed when H/O/A = Hand.
"
Options - G, H, L, Q, or V and S "Serial Communications" and "Speed Pot."; Bypass with serial communication for control, with hand mode speed potentiometer:
Hand mode speed command from speed potentiometer.
Auto mode speed command input signal from serial communication.
Auto mode run/stop command for Drive from serial communication.
Auto mode run/stop contact closure for Bypass applied to terminals TB1-3 and TB1-4.
Significant
Parameter Setting b1-01 = 1: Terminals (default)
H3-13 = 0: Main Fref TA1 (default)
H1-03 = 6C: Com/Inv Sel 2
Result
Speed command source = Terminals
Specific speed command source = Terminal A1
A terminal S5 input contact closure allows b1-01 to select terminals and the speed pot. as the speed command. An open contact selects serial com for speed command and run/stop. This input contact is closed when H/O/A
= Hand.
Programming 5 - 8
!
A1 Initialization
The initialization group contains parameters associated with initial setup of the Drive. Parameters involving the display language, access levels, initialization and password are located in this group.
"
A1-00 Select Language
Setting
0
1
4
5
6
2
3
Description
English (factory default)
Japanese
Deutsch
Francais
Italiano
Espanol
Portugues
The setting of parameter A1-00 determines which international language the Drive will use to display non-numerical text. The
A1-00 parameter will not be changed by an Initialization of the Drive (A1-03= “1110: User Initialize”, “2220: 2-Wire Initial”, or “3330: 3-Wire Initial”).
If the Drive is accidentally set to a language unfamiliar to the operator, locating the parameter to change the operator language can be done by performing the following:
1. Press the MENU key until the “-ADV-” MENU is shown in the upper left corner of the digital operator.
2. Press the DATA/ENTER key to enter the programming menu. The first parameter shown is A1-00 (Select Language).
3. Press the DATA/ENTER key again and use the INCREASE and DECREASE arrow keys to choose the preferred language from the list below:
0 : English
1 : Japanese
2 : Deutsch (German)
3 : Francais (French)
4 : Italiano (Italian)
5 : Español (Spanish)
6 : Portugu s (Portuguese)
"
A1-01 Access Level Selection
Setting
0
1
2
Description
Operation Only
User Level
Advanced Level (factory default)
A1-01 can be used to allow access to and permission to change all Drive parameters. If the Drive is programmed for Operation
Only (A1-01= “0: Operation Only”), then only the OPERATION and the PROGRAMMING menus are accessible. Within the
PROGRAMMING menu only parameters A1-01 and A1-04 are adjustable.
Programming 5 - 9
If A1-01 is configured for Advanced Access (A1-01= “2: Advanced Level”), then all menus and all parameters are shown. If the
Access Level Selection is set to Advanced, all parameters should be adjustable unless:
1. The Drive parameters are password protected (A1-04) which will prevent access to A1-00 through A1-03 and all A2 parameters.
2. A digital input has been configured as a Program Lockout (H1-0X= 1B) is active.
3. During serial communication writing, if a parameter change is also attempted via the digital operator, a
“BUSY - WRITE PROTECTED” message will display. Parameter change will not be possible from the digital operator until an
Enter command is received via the serial communication to finish the serial writing process.
"
A1-03 Initialize Parameters
Setting
0
1110
2220
3330
Description
No Initialize (factory default)
User Initialize
2-Wire Initialize
3-Wire Initialize
The Drive can be set back to one of three default states via the A1-03 parameter.
1. User Initialization – 1110: The modified Drive parameters are returned to the values selected as user settings. User settings are stored when parameter o2-03= “1: Set Defaults”.
2. 2-Wire Initialization – 2220: The Drive parameters are returned to factory default values with digital inputs S1 and S2 configured as Forward Run and Reverse Run, respectively.
3. 3-Wire Initialization – 3330: The Drive parameters are returned to factory default values with digital inputs S1, S2, and S5 configured as Run, Stop, and Forward/Reverse respectively.
After an initialization is performed, parameter A1-03 will automatically be set back to 0.
S1
FWD Run/Stop
Stop switch
(NC contact)
Operation switch
(NO contact)
S2
REV Run/Stop
SN
S3 or S5
Run command
(run on momentary close)
Stop command
(stop on momentary open)
Forward/reverse command
(multi-function input)
Sequence input common
3-wire control
Fig 5.1 2 & 3-Wire Control Wiring Examples
IMPORTANT
Some parameters are unaffected by either the 2-Wire or 3-Wire initialization. The following parameters will not be reset when parameter A1-03=2220 or 3330:
A1-00
E1-03 o2-04 o2-09
Language Selection
V/f Pattern Selection kVA Selection
Initialization Specification Selection
Programming 5 - 10
"
A1-04 Password Entry
Setting Range: 0 to 9999
Factory Default: 0
If parameters A1-01 through A1-03 and all of the A2 parameters are locked (unchangeable) they can be unlocked by entering the correct password number into A1-04.
Once the correct password number is entered and the specified parameters are unlocked, a 2-Wire or 3-Wire initialization will reset the password to 0000.
"
A1-05 Select Password
Setting Range: 0 to 9999
Factory Default: 0
When the value set into A1-04 does NOT match the value set into A1-05, parameters A1-01 thru A1-03 and A2-32 cannot be changed. All other parameters determined by A1-01 can be changed. Parameter A1-05 can be accessed by displaying parameter
A1-04, then press and hold the RESET key along with the MENU key simultaneously.
!
b1 Sequence
The Sequence Group contains parameters associated with starting and stopping the Drive. Parameters involving the Run
Command, Speed Reference location, Stopping Method and Hand/Auto changeover are located in this group.
"
b1-01 Reference (Speed Command) Source Selection
This is one of the special parameter settings required by the Bypass logic circuit. See Table 5.1.
The addition of serial communication to the Drive and Bypass unit, after shipment to the job site, would be the only reason for changing this parameter. See Table 5.2 for the parameter settings required to enable serial communication in the field.
Setting
0
1
2
3
Description
Operator - Digital Preset Speed d1-01
Terminals - Analog Input Terminal A1 (or Terminal A2, see Parameter H3-13)
Serial Com - RS-485 Terminals R+, R-, S+ and S-
Option PCB - Option Board connected at 2CN
In order to run the Drive and motor with the BYPASS/DRIVE switch in the DRIVE position: the Drive must receive a Run command and a speed command. Parameter b1-01 specifies from where the speed command is received when the Drive is in the
AUTO mode. Switching into the AUTO mode can be done by turning the Hand/Off/Auto selector switch to AUTO while the
Drive is stopped.
IMPORTANT
If a Run command is input to the Drive but no corresponding speed command is input, the Run indicator on the digital operator will turn on and the STOP indicator on the digital operator will blink.
Programming 5 - 11
If you want the Drive to follow the speed command set by the digital operator: Use the HAND mode by turning the
HAND/OFF/AUTO selector switch to HAND. The speed command can then be entered into the U1-01 monitor parameter in the
“-DRIVE-” Menu.
If you want the Drive to follow an AUTO analog speed command: Connect a 0 – 10 VDC speed command signal between terminals A1 and AC or a 4 – 20 mA speed command signal to terminals A2 and AC. Select the AUTO position of the Hand/
Off/Auto switch.
If you want the Drive to receive the speed command from serial communication: Set the parameter indicated in Table 5.2 for the desired serial communication option. Connect the RS-485/422 serial communications cable to terminals R+, R-, S+, and S- on the control I/O terminal block. The HAND/OFF/AUTO selector switch must be in the AUTO position.
"
b1-02 Run Source
Setting
0
1
2
3
Description
Operator
Terminals (factory default)
Serial Com
Option PCB
To successfully operate the Drive or Bypass and motor remotely, an external run command must be received by the Drive and
Bypass unit. Parameter b1-02 specifies from where the run command for the Drive will be accepted.
This parameter is by default set to “1: Terminals.” This setting is required by the Bypass logic circuit.
To issue a run command from the control panel: Turn the Hand/Off/Auto switch to the HAND position.
To issue a run command from a remote source: Turn the Hand/Off/Auto switch to the AUTO position. A contact closure between terminals TB1-3 and TB1-4 will control the Drive or Bypass start and stop operation.
To issue a run command via serial communication: Set the parameters indicated in Table 5.2 for the desired serial communication option. Connect the RS-485/422 serial communication cable to R+, R-, S+, and S- on the removable terminal block.
"
b1-03 Stopping Method
There are four methods of stopping the Drive when the Run command is removed.
Setting
0
1
2
3
Description
Ramp to Stop (factory default)
Coast to Stop
DC Injection to Stop
Coast w/Timer
“0:Ramp to stop”: When the Run command is removed, the Drive will decelerate the motor to 0 rpm. The rate of deceleration is determined by the active deceleration time. The factory default Decel Time is in parameter C1-02.
Programming 5 - 12
When the output frequency has dropped below the DC Injection Start Frequency in b2-01 (Default = 0.5HZ) DC current will be injected in the motor at a level determined by b2-02 (50% Default). The DC Injection condition will occur for the time specified by b2-04 (0.0 Default), to establish the end point of the ramp. DC injection can be used to insure the motor is at zero rpm prior to the Drive shutting off.
Run Command
ON
(CLOSED)
OFF
(OPEN)
100 % b2-01
Output Frequency
Deceleration Time (C1-02)
0 %
TIME
Fig 5.2 Deceleration to Stop
DC Injection Brake
| b2-04 |
The actual deceleration time can be determined by the following formula
Time to Stop
=
Output Freq.
at time of stop command
Maximum Frequency (E1 04)
×
Setting of active Decel Time (C1 -
02 or C1-04)
If S-Curve characteristics are specified by the Drive programming, they will add to the total time to stop.
1:Coast to stop: When the Run command is removed, the Drive will turn off its output and the motor will coast (uncontrolled deceleration). The friction of the driven equipment will eventually overcome any residual inertia of the system and the rotation will stop.
Run Command
ON
(CLOSED)
OFF
(OPEN)
100 %
Output Frequency
0 %
Motor Speed
Drive Output Frequency Interrupted
TIME
Fig 5.3 Coast to Stop
IMPORTANT
After a stop is initiated, a subsequent Run commands input before the Minimum Baseblock Time (L2-03) has expired, will be ignored.
Programming 5 - 13
2:DCInj to Stop: When the Run command is removed, the Drive will Baseblock (turn off its output) for the Minimum Baseblock Time (L2-03). Once the Minimum Baseblock Time has expired, the Drive will inject DC current into the motor windings to lock the motor shaft. The stopping time will be reduced as compared to Coast to Stop. The level of DC Injection current is set by parameter b2-02 (50% Default). The DC Injection brake time is determined by the set value in b2-04 and the output frequency at the time the Run command is removed.
DC Injection Brake Time
=
(b2 04)
×
10
×
Output Frequency
Maximum Frequency (E1 04)
Run Command
ON
(CLOSED)
OFF
(OPEN) b2-04 x 10
100 %
Output Frequency
0 %
Drive Output Voltage Interrupted
Minimum Baseblock
Time (L2-03)
DC Injection Brake
DC Injection Brake Time b2-04
Fig 5.4 DC Injection Braking to Stop b2-04
10%
100% (Maximum
Output Frequency)
IMPORTANT
If an overcurrent (OC) fault occurs during DCInj to Stop, lengthen the Minimum Baseblock Time (L2-03) until the fault no longer occurs.
3:Coast w/Timer: When the Run command is removed, the Drive will turn off its output and the motor will coast to a stop. If a
Run command is input before time T (Operation Wait Time) expires, the Drive will not run and the Run command will need to be cycled before operation can occur
.
The time T (Operation Wait Time) is determined by the output frequency when the
Run command is removed and the active deceleration time (C1-02).
Ignored
Run Command
Run Command
ON
(CLOSED)
OFF
(OPEN)
Deceleration
Time (C1-02)
100 %
Output Frequency
0 %
Drive Output
Voltage
Interrupted
(C1-02)
Fig 5.5 Coast to Stop with Timer
Minimum
Baseblock
Time (L2-03)
Minimum
Output
Frequency
100% (Maximum
Output
Frequency)
Output Frequency at Stop Command Input
Programming 5 - 14
"
b1-04 Reverse Operation
Setting
0
1
2
3
Description
Reverse Enabled
Reverse Disabled (factory default)
Exchange Phase
ExchgPhs, Rev Dsbl
For some applications reverse motor rotation is not applicable and may even cause problems (e.g., air handling units, pumps, etc.). Setting parameter b1-04 to 1 or 3 will cause the Drive to ignore any inputs for reverse operation. Setting parameter b1-04 to either 2 or 3 will change the motor shaft rotation when a Forward Run command is given by exchanging the order of the output phasing.
The factory default setting of parameter b1-04 is “1: Disabled”. When b1-04= “1: Disabled”, reverse operation is prohibited and no exchanging of output phasing occurs.
"
b1-07 Local/Remote Run Selection
Setting
0
1
Description
Cycle Extern Run
Accept Extrn Run (factory default)
When the Drive is switched between the Local (Hand) mode (the digital operator) to the Remote (Auto) mode by the Hand/
Off/Auto selector switch, there is the possibility that a Run command is already present (i.e. a contact closure between terminals TB1-3 and TB1-4. Parameter b1-07 determines whether the Drive will:
Ignore the external Run command until it is removed and re-instated (b1-07= “0: Cycle Extern Run”)
OR
Accept the already present Run command and immediately begin acceleration to the commanded speed
(b1-07= “1: Accept Extrn Run”).
IMPORTANT
When switching from local mode to Auto mode when b1-07= “1:Accept Extrn Run” the Drive may start unexpectedly if the Run command is already applied. Be sure all personnel are clear of rotating machinery and electrical connections prior to switching between local mode and Auto mode.
"
b1-08 Run Command Selection During Programming
Setting
0
1
Disabled
Enabled (factory default)
Description
As a convenience to the user, the Drive will respond to a Run input even when the digital operator is being used to adjust parameters. If it is necessary that external Run commands not be recognized while the Drive is being programmed, set b1-08= “0: Disabled”.
Programming 5 - 15
"
b1-11 Drive Delay Time Setting
Setting Range: 0 to 600 Seconds
Factory Default: 0 Seconds
If a time is set into parameter b1-11, the Drive will delay executing any run command until the b1-11 time has expired.
During Drive delay time execution, the digital operator will display:
DDLY
Waiting to RUN
Both the ALARM and Run indicators will blink while the Drive waits to execute the Run command.
!
b2 DC Braking
The DC Braking Group contains parameters associated with the DC injection braking feature. Parameters involving the starting frequency, current level, braking time, and motor pre heat current level are located here.
"
b2-01 DC Injection Braking Start Frequency
Setting Range: 0.0 to 10.0 Hz
Factory Default: 0.5 Hz
Parameter b2-01 sets the output frequency where the Drive begins DC Injection during Ramp to stop. in order to lock the rotor of the motor and established the end point of the ramp. If b2-01 < E1-09 (Minimum Frequency), then DC Injection begins at E1-09.
Parameter b2-01 also determines the output frequency that the Drive must be at or below before a Zero Speed condition is considered true. This affects any digital output configured as a Zero Speed signal (H2-0x= “1: Zero Speed”).
Output Frequency
| b2-04
| b2-01 t ime
DC injection
Fig 5.6 DC Injection Braking During Stopping
"
b2-02 DC Injection Braking Current
Setting Range: 0 to 100%
Factory Default: 50%
The level of DC Injection Braking Current affects the strength of the magnetic field attempting to lock the motor shaft.
Increasing the level of current will increase the amount of heat generated by the motor windings and should only be increased to the level necessary to hold the motor shaft. DC Injection current is set in percentage of Drive rated output current. Drive rated output current is stated on the Drive nameplate.
Programming 5 - 16
"
b2-03 DC Injection Braking Time at Start b2-04 DC Injection Braking Time at Stop
Setting Range: 0.00 to 10.00 Seconds
Factory Default: b2-03 = 5.00 Seconds b2-04 = 0.00 Seconds b2-03 is one of the special parameter settings required by the Bypass logic circuit. See Table 5.1.
The Drive can be programmed to automatically DC Inject for a predetermined amount of time prior to accelerating to speed
(b2-03) and/or at the end of a Ramp to stop (b2-04). Parameter b2-03 can be used to stop a rotating motor prior to attempting acceleration (i.e. a wind milling fan). If DC Injection braking at start or Speed Search is not enabled, attempting to Drive a spinning motor may cause nuisance tripping.
Parameter b2-04 can be used to resist any residual motion of the load after the deceleration has finished.
DC injection
Output Frequency b2-03 b2-04
Fig 5.7 DC Injection Braking During Starting and Stopping
Parameter b2-04 also serves the function of affecting the length of time DC Injection to stop (b1-03= “2: DC Injection to
Stop”) will occur.
"
b2-09 Motor Pre-Heat Current
Setting Range: 0 to 100%
Factory Default: 0%
A DC current can be circulated within the motor windings while the motor is stopped. The current will produce heat within the motor and prevent condensation. Parameter b2-09 determines the percentage of Drive rated output current that will be used for the motor pre-heat function. This function can be useful in applications where the motor sits for extended periods of time in humid conditions. Motor pre-heating can only be initiated by closing a digital input programmed as a Motor Pre-heat Input
(H1-0x= 60). Check with the motor manufacturer to determine the maximum acceptable current level the motor can withstand when stopped. Be sure not to exceed the motor manufacturers recommended level.
Programming 5 - 17
!
b3 Speed Search
The Speed Search function allows the Drive to determine the speed of a motor shaft that is being driven by rotational inertia.
Speed Search will allow the Drive to determine the speed of the already rotating motor and begin to ramp the motor to a set speed without first having to bring it to a complete stop. When a momentary loss of supply power is experienced, the Drive output is turned off. This results in a coasting motor. When power returns, the Drive can determine the speed of the coasting motor and start without requiring it to be brought to minimum speed. Speed Search can be programmed to always be active by setting b3-01 or it can be commanded by remote contact closure by setting a digital input.
There are two forms of Speed Search in the Drive, the speed estimation method and the current detection method.
IMPORTANT
When setting the Drive for remote Speed Search input, via a contact closure, the method of Speed Search is determined by the setting of b3-01. If b3-01= ”0: SpdsrchF Disable” then the remote input will initiate speed estimation method, and if b3-01= ”2: SpdsrchI Disable”, then the remote input will start the current detection method.
Parameters L2-03 and L2-04 also affect the current detection method of Speed Search operation.
"
b3-01 Speed Search Selection
Setting
0
1
2
3
Description
SpdsrchF Disable
SpdsrchF Enable
SpdsrchI Disable (factory default)
SpdsrchI Enable
Speed Estimation: Method (b3-01= 0 or 1)
The speed estimation method will calculate the speed using measurements of residual motor fields. The speed estimation version is bi-directional and will determine both the motor speed and direction. To enable speed estimation Speed Search at start, set b3-01= “1: SpdsrchF Enable”.
IMPORTANT
If the speed estimation method of Speed Search is to be used, then Auto-tuning must be performed prior to using Speed Search. If the length of cable between the Drive and motor is ever changed after Auto-tuning then Auto-tuning should be performed again.
IMPORTANT
The speed estimation mode cannot be used when there are multiple motors operated by one Drive or the motor is two or more frames smaller than the standard size motor per the Drive capacity.
Programming 5 - 18
AC power supply
Output frequency
ON OFF
Start using speed detected
Set frequency reference
Output current
10 ms
Minimum baseblock time (L2-03) x 0.75 *1
Minimum baseblock time (L2-03) x 0.75*1
*2
*1 Baseblock time may be reduced by the output frequency
immediately before the baseblock.
minimum Speed Search Wait Time (b3-05).
Fig 5.8 Speed Search (Estimated Speed Method) after momentary power loss where the power loss time is less than the minimum baseblock time
AC power supply
Output frequency
ON OFF
Start using speed detected
Set frequency reference
Output current
10 ms
Minimum baseblock time
(L2-03)
Speed Search Wait Time
(b3-05)
Note: If the frequency immediately before the baseblock is low or the power supply break time is long, operation may be the same as the search in case 1.
Fig 5.9 Speed Search (Estimated Speed Method) after momentary power loss where the power loss time exceeds the minimum baseblock time
Current Detection Method (b3-01=2 or 3):
The current detection method starts searching from a predetermined frequency while monitoring the Drive output current to determine when the rotor speed and the Drive output speed (frequency) match.
The current detection version is not bi-directional. To enable current detection Speed Search at start set b3-01= “3: SpdscrhI enable” and program any digital input equal to Speed Search 1 (H1-0x= 61) or Speed Search 2 (H1-0x= 62). Speed Search 1 will start searching from the max. frequency (E1-04) and ramp down to meet the rotor speed. Speed Search 2 will start searching from the set frequency and ramp down to meet the rotor speed.
IMPORTANT
If a UV1 fault occurs when current detection Speed Search is attempted, increase the setting of L2-04.
IMPORTANT
If an OC fault occurs when Speed Search is attempted after power loss recovery, increase the setting of L2-03.
Programming 5 - 19
Run command
OFF ON
Maximum output frequency or set frequency
Output frequency
Deceleration time set in b3-03
Set frequency reference b3-02
Speed search current level
Output current
Minimum baseblock time
*
(L2-03)
Fig 5.10 Speed Search (Current Detection Method) at Startup
AC power supply
Output frequency
ON OFF
Output frequency before power loss
Deceleration time set in b3-03
Set frequency reference b3-02 speed search operating current
Output current
*1 Baseblock time may be reduced by the output frequency
immediately before baseblock.
*2 After AC power supply recovery, motor waits for the minimum
Minimum baseblock time (L2-03)
*1
*2
Fig 5.11 Speed Search (Current Detection Method) after momentary power loss where the power loss time is less than the minimum baseblock time
AC power supply
ON OFF Output frequency before power loss
Set frequency reference
Output frequency b3-02
Speed search operating time
Output current
Speed search wait time (b3-05)
Minimum baseblock time
(L2-03)
Fig 5.12 Speed Search (Current Detection Method) after momentary power loss where the power loss time exceeds the minimum baseblock time
Setting of b3-01
2
3
0
1
Automatic Speed Search for all RUN commands and momentary power loss
No
Yes - Speed Estimation
No
Yes - Current Detection
Speed Search Method
Used for Multi-function inputs
Speed Estimation
Current Detection
Programming 5 - 20
"
b3-02 Speed Search Deactivation Current
Setting Range: 0 to 200% of Drive rated output current
Factory Default: 120% of Drive rated output current
When using the current detection method of Speed Search, parameter b3-02 sets the current level that will determine when the search is complete and the rotor and output speeds match. When the output frequency is higher than the actual rotor speed the slip causes the current to be high. As the output frequency is lowered, the closer it comes to the rotor speed, the lower the current draw will be. When the output current drops below the level as set in b3-02 (100% = Drive Rated Current) the output frequency stops decreasing and normal operation resumes.
"
b3-03 Speed Search Deceleration Time
Setting Range: 0.1 to 10.0 Seconds
Factory Default: 2.0 Seconds
Parameter b3-03 sets the deceleration ramp used by the current detection method of Speed Search when searching for the motor’s rotor speed. Even if Speed Search 2 is selected, for Speed Search at start, the time entered into b3-03 will be the time to decelerate from maximum frequency (E1-04) to minimum frequency (E1-09).
"
b3-05 Speed Search Delay Time
Setting Range: 0.0 to 20.0 Seconds
Factory Default: 0.2 Seconds
In cases where an output contactor is used between the Drive and the motor, extra waiting time is provided after power returns and before Speed Search is performed. This extra time allows for the contactor to operate. When Speed Search at start is used, b3-05 will serve as the lower limit of the Minimum Baseblock Time (L2-03).
"
b3-14 Bi-Directional Speed Search Selection
Setting
0
1
Description
Disabled
Enabled (factory default)
The b3-14 parameter can be used to turn off the bi-directional capabilities of the Speed Estimation form of Speed Search. By turning off the bi-directional capability, the speed search will only try to match the speed in the last known direction.
Programming 5 - 21
!
b5 PI Function
The capability to accept an analog signal as feedback for a PI (Proportional + Integral) control function is built into the Drive.
D1-04
D1-02
D1-01
Option Card b1-01
4
3
Frequency Reference using multi-step command
Frequency reference
(U1-01)
Reg. 0Fh, bit 1
1
1 b5-20 b5-18
Scaling
PI Differential
1
Fdbk. H3-09=16
0
0
0 b5-01=0
PI control is OFF under the following conditions:
- b5-01=0
- During JOG command input
ON
ON
Enable / Disable reverse operation when PI output is negative
+
Upper limit
Fmax x109%
+
0 b5-11
1
Lower limit 0
Upper limit
Fmax x109%
1
0
2
Sleep function selection b5-21
+
b5-16
Delay
Timer b5-15
Sleep Level
Sleep Function
RUN on/off
Serial Com
1 0
PI Differential
Fdbk. H3-09=16
1
Terminal A1
MEMOBUS Reg. 06H
PI target value
Constant b5-19
Terminal A1
Terminal A2
2
PI SFS cancel
H1-xx=34
1
0
PI SFS b5-17
Scaling o1-03
PI Set Point
(U1-38)
Scaling b5-20 b5-01=3 b5-01=1
PI Input
(U1-36)
OFF
Lower limit
Fmax x109%
SFS
2
Output frequency
Sleep function selection b5-21
0
+
b5-22
PI Snooze Level b5-23
Delay
Timer
PI
Snooze
PI Snooze Function
0
1
PI Differential
Fdbk. H3-09=16
0
1
H3-09=B
PI Feedback 2
(U1-46)
+
-
1
0 b5-28
0
1
PI Differential
Fdbk. H3-09=16
PI SFS cancel
H1-xx=34
1
PI SFS b5-17
1 0
H3-09=16
+
PI Input
0
+
-
PI Feedback
(U1-24) b5-20
Scaling
H1-xx=35
0
Z -1
1
I-time b5-03
0
P
1/t
Proportional gain b5-02
1
Integral Hold
H1-xx=31
Sleep function selection b5-21
2
+
+
I - limit b5-04
Z -1
0
1
+ +
Integral Reset
H1-xx=30
PI Snooze Function b5-29
0
+
1
0 or 1
+
-
PI
Wake Up
P
PI Differential
Fdbk. H3-09=16 b5-24
PI Wake Up Level
PI offset
(b5-07)
PI Limit b5-06
PI delay time b5-08
1/t
0
Z -1
1
PI Output
Characteristic b5-09
1
PI Differential
Fdbk. H3-09=16
+
+
0 b5-07
PI offset
PI Output
Gain b5-10
1 0 b5-30
PI output monitor
(U1-37)
Fig 5.13 PI Block Diagram
Bypass units are shipped with the parameters in Table 5.1 and Table 5.2 pre-established.
To add PI control to a Bypass unit; observe the control options that are included in the unit by review of the model number on the nameplate (inside of door and external lower right side) as well as the option codes and model number description in
Chapter 1. Then revise the parameter settings indicated in Table 5.3 and 5.4 for a line of data, in Table 5.4, with the same
(or similar) combination of options. This will add the logic required for PI control to that required for Bypass control.
Table 5.3 includes parameters that are the same regardless of control options specified while Table 5.4 provides detail on the option dependent parameters.
Programming 5 - 22
PARAMETER
NUMBER b1-01 b5-01
H1-03
H1-04
H3-02
H3-08
H3-09
H3-13 o1-03 o1-06 o1-08
SETTING
Table 5.3 PI Control Parameter Settings in Bypass Units
Bypass & PI
Control
Bypass
Default
UNITS DESCRIPTION
SEE TABLE
5.4
1
19
SEE TABLE
5.2
0
SEE TABLE
5.2
4 SEE TABLE
5.4
100
SEE TABLE
5.4
SEE TABLE
5.2
SEE TABLE
5.2
KEYPAD DISPLAY
For Bypass Setting
N/A Frequency Reference Selection – Selects the speed command input source
N/A PI Mode Selection – Enables PI mode
Reference Source / Terminals
PI Mode Setting / PI Mode
Terminal S5 Sel / PI Disable N/A Terminal S5 Function Selection – Set for PI
Disable, turn off PI controller
N/A Terminal S6 Function Selection – Set for various operating modes
% Terminal A1 Gain Setting
Terminal S6 Sel / Com/Inv Sel 2, for example
Terminal / (0-1000)
B
1
1
1
24
SEE TABLE
5.2
SEE TABLE
5.2
0
0
3
N/A Terminal A2 Signal Level – Signal selection,
0 to 10 VDC (Drive control board switch
S1-2 off) or 4 to 20 mA (Drive control board switch S1-2 on)
N/A Terminal A2 Function Selection – Selects how this input will be used by the Drive
Term A2 Signal / 0-10 VDC
Terminal A2 Sel / PI Feedback
TA1/A2 Select / Main Fref TA2 N/A Master Frequency Reference Terminal
Selection – Determines which terminal (A1 or A2) will be the main speed reference source.
% Digital Operator Display Selection – Set for percent
Display Scaling / (0-39999)
N/A User Monitor Selection Mode – Enables a custom display for PI Control monitoring
N/A Third Line User Monitor Selection – Display
PI Feedback
Monitor Mode Sel / 1: 3 Non
Selectable
3rd Monitor Sel / 24: PI Feedback
"
Digital Operator and Control Panel Display for PI Control
In Table 5.3, the o1-0X parameter listed setup the Drive display to indicate 3 variables for PI control as in Figure 5.14 when the HAND/OFF/AUTO switch is in AUTO.
FWD REV SEQ
AUTO
REF ALARM
- - - - - - - - - - - - - - - - - - - - - - - - - - - - -
RUN
Monitor
MENU
ESC
DATA
ENTER
STOP
RESET
Fig 5.14 Drive Display for PI Control, AUTO Mode
PI SETPOINT
OUTPUT
PI FEEDBACK
Programming 5 - 23
When the HAND/OFF/AUTO switch is transfered to the HAND position, the display will automatically change to indicate the speed command, as in Figure 5.15.
FWD REV SEQ
AUTO
REF ALARM
- - - - - - - - - - - - - - - - - - - - - - - - - - - - -
RUN
Monitor
MENU
ESC
DATA
ENTER
STOP
RESET
SPEED COMMAND
OUTPUT
FEEDBACK
Fig 5.15 Drive Display for PI Control, HAND Mode
Options
None
None
S
S
S
G, H, Q or V 2
G, H, Q or V 0
G, H, Q or V 0
L 0
V and S
L and S
0
1*
1
1
1
1
Table 5.4 Option Dependent Drive PI Control Parameters in Bypass Units
Parameters Effected by Options Specified b1-01 H1-04 H3-08
Drive PCB
Switch S1
1 2
Resulting Hand
Speed Command
Source
Keypad
U1-01
Speed
Pot.
Auto: PI
Feedback
Terminal A2
4-20 mA
0-10
VDC
TB1
3&4
Auto:
Run/Stop
Serial
#
Auto: PI Setpoint
Keypad
U1-01
Serial
#
Speed
Pot.
0 4* 2* Off On* X X X X
4
4
4
6D
@
6E
@
6C
@
6C
@
6C
@
6C
@
6C
@
2
2
0
0
0
0
2
0
0
0
Off* Off
Off Off
Off On
Off Off
Off Off
Off Off
Off On
On On
Off Off
On Off
X
X
X
X
X
X
X
X
X
X
X
X
X
X
X
X
X
X
X
X
X
X
X
X
X
X
X
X
X
X
X
X
X
X
X
X
X
X
X
X
Definitions:
L = LonWorks Option Card
S = Speed Potentiometer
V = Native Protocol (Modbus)
G = DeviceNet Option Card
H = Profibus Option Card
Q = Ethernet Option Card
Parameter Reference: b1-01: Speed Command Input Source
0: Operator
1: Terminals
H1-04: Terminal S6 Function Selection
6C: Com/Inv Sel 2
6D: Auto Mode Selection
6E: Hand Mode Selection
4: Multi-Step Ref 2
Note:
* = The factory default
# = The H/O/A switch must be in the AUTO position
to allow serial com. to control the Drive.
@ = Jumpers required from S5 to S6
H3-08: Terminal A2 Signal Level
0: 0 - 10 VDC
2: 4 - 20 mA
Hand mode run/stop for Drive and Bypass is always via the front control panel HAND/OFF/AUTO switch.
Programming 5 - 24
"
Discussion of Table 5.4 Options Dependent, PI Control Bypass Parameter Settings:
Typical Drive Parameter Settings for PI Control with Various Combinations of Bypass and Control Options
Notes:
For project specific PI control tuning see the PI Control (b5-XX) parameters in this chapter. Tables 5.3 and 5.4 provide the basic configuration for PI Control from a Drive in an E7 Bypass unit. The b5-XX parameters are defaulted to a good starting point for most HVAC applications. Final adjustment to some of the b5-XX parameters for the project at hand may be required.
Hand mode run/stop for Drive and Bypass is always via the front control panel HAND/OFF/AUTO switch.
Options - None;
Bypass with PI Control and no options:
Hand mode speed command from Keypad/Operator.
Auto mode PI Setpoint from Keypad/Operator.
Auto mode PI Feedback input signal, 4-20 mA applied to Drive terminal A2.
Auto mode run/stop contact closure for Drive and Bypass applied to terminals TB1-3 and TB1-4.
Significant
Parameter Setting b1-01 = 0: Operator b5-01 = 1: Enable
H1-03 = 19: PI Disable
H3-08 = 2: 4-20 mA (default)
H3-09 = B: PI Feedback
H3-13 = 1: Main Fref TA2
Result
Speed command (Hand) and PI setpoint (Auto) sourced = Keypad/Operator (U1-01)
Enable PI mode of operation
A terminal S5 input contact closure disables PI mode. This input contact is closed when H/O/A = Hand.
Terminal A2 is programmed for 4-20 mA (Note – Control PCB DIP switch S1-2 must also be ON)
Terminal A2 function is set to provide PI feedback for closed loop control
Terminal A2 (the feedback terminal) serves as the main input
Options - None;
Bypass with PI Control and no options:
Hand mode speed command from Keypad/Operator.
Auto mode PI Setpoint from Keypad/Operator.
Auto mode PI Feedback input signal, 0-10 VDC applied to Drive terminal A2.
Auto mode run/stop contact closure for Drive and Bypass applied to terminals TB1-3 and TB1-4.
Significant
Parameter Setting b1-01 = 0: Operator b5-01 = 1: Enable
H1-03 = 19: PI Disable
H3-08 = 0: 0-10 VDC
H3-09 = B: PI Feedback
H3-13 = 1: Main Fref TA2
Result
Speed command (Hand) and PI setpoint (Auto) source = Keypad/Operator (U1-01)
Enable PI mode of operation
A terminal S5 input contact closure disables PI mode. This input contact is closed when H/O/A = Hand.
Terminal A2 is programmed for 0-10 VDC (Note – Control PCB DIP switch S1-2 must also be OFF)
Terminal A2 function is set to provide PI feedback for closed loop control
Terminal A2 (the feedback terminal) serves as the main input
Programming 5 - 25
Options - S
"Speed Pot."; Bypass with PI Control and speed potentiometer for speed control and setpoint:
Hand mode speed command from speed potentiometer.
Auto mode PI Setpoint from speed potentiometer.
Auto mode PI Feedback input signal, 0-10 VDC applied to Drive terminal A2.
Auto mode run/stop contact closure for Drive and Bypass applied to terminals TB1-3 and TB1-4.
Significant
Parameter Setting b1-01 = 1: Terminals (default) b5-01 = 1: Enable
H1-03 = 19: PI Disable
H3-08 = 0: 0-10 VDC
H3-09 = B: PI Feedback
H3-13 = 1: Main Fref TA2
Result
Speed command (Hand) and PI setpoint (Auto) source = Terminals
Enable PI mode of operation
A terminal S5 input contact closure disables PI mode. This input contact is closed when H/O/A = Hand.
Terminal A2 is programmed for 0-10 VDC (Note – Control PCB DIP switch S1-2 must also be OFF)
Terminal A2 function is set to provide PI feedback for closed loop control
Terminal A2 (the feedback terminal) serves as the main input
Options - S
"Speed Pot."; Bypass with PI Control and speed potentiometer for speed control:
Hand mode speed command from speed potentiometer.
Auto mode PI Setpoint from Keypad/Operator.
Auto mode PI Feedback input signal, 0-10 VDC applied to Drive terminal A2.
Auto mode run/stop contact closure for Drive and Bypass applied to terminals TB1-3 and TB1-4.
Significant
Parameter Setting b1-01 = 1: Terminals (default) b5-01 = 1: Enable
H1-03 = 19: PI Disable
H1-04 = 6D: Auto Mode Sel
S6 must be jumpered to S5
H3-08 = 0: 0-10 VDC
H3-09 = B: PI Feedback
H3-13 = 1: Main Fref TA2
Result
Speed command (Hand) and PI setpoint (Auto) source = Terminals
Enable PI mode of operation
A terminal S5 input contact closure disables PI mode. This input contact is closed when H/O/A = Hand.
A terminal S6 input contact opening (H/O/A = Auto) puts the Drive in “Hand” mode to source the PI Setpoint from the Keypad/Operator (overrides b1-01). A terminal S6 input contact closure (H/O/A = Hand) puts the Drive in “Auto” mode to allow b1-01 to determine the speed command source. This input is jumpered to S5, therefore the contact is closed when H/O/A = Hand.
Terminal A2 is programmed for 0-10 VDC (Note – Control PCB DIP switch S1-2 must also be OFF)
Terminal A2 function is set to provide PI feedback for closed loop control
Terminal A2 (the feedback terminal) serves as the main input
Programming 5 - 26
Options - G, H, L, Q, or V
"Serial Communications"; Bypass with PI Control and serial communication for Setpoint input:
Hand mode speed command from Keypad/Operator.
Auto mode PI Setpoint input signal from serial communication.
Auto mode run/stop contact closure for Drive and Bypass applied to terminals TB1-3 and TB1-4.
Significant
Parameter Setting b1-01 = 2: Serial Com b5-01 = 1: Enable
H1-03 = 19: PI Disable
H1-04 = 6E: Hand Mode Sel
S6 must be jumpered to S5
H3-08 = 0: 0-10 VDC
H3-09 = B: PI Feedback
H3-13 = 1: Main Fref TA2
Result
Speed command (Hand) and PI setpoint (Auto) source = Serial Communication
Enable PI mode of operation
A terminal S5 input contact closure disables PI mode. This input contact is closed when H/O/A = Hand.
A terminal S6 input contact opening (H/O/A = Auto) puts the Drive in “Auto” mode to allow b1-01 to determine the PI Setpoint source. A terminal S6 input contact closure (H/O/A = Hand) puts the Drive in “Hand” mode to source the speed command from the Keypad/Operator (overrides b1-01). This input is jumpered to
S5, therefore the contact is closed when H/O/A = Hand.
Terminal A2 is programmed for 0-10 VDC (Note – Control PCB DIP switch S1-2 must also be OFF)
Terminal A2 function is set to provide PI feedback for closed loop control
Terminal A2 (the feedback terminal) serves as the main input
Options - G, H, L, Q, or V
"Serial Communications"; Bypass with PI Control and serial communication for run/stop control and Setpoint input:
Hand mode speed command from Keypad/Operator.
Auto mode PI Setpoint input signal from serial communication.
Auto mode run/stop command for Drive from serial communication.
Auto mode run/stop contact closure for Bypass applied to terminals TB1-3 and TB1-4.
Significant
Parameter Setting b1-01 = 0: Operator b5-01 = 1: Enable
H1-03 = 19: PI Disable
Result
Speed command source = Keypad/Operator (U1-01)
Enable PI mode of operation
A terminal S5 input contact closure disables PI mode. This input contact is closed when H/O/A = Hand.
H1-04 = 6C: Com/Inv Sel 2 S6 must be jumpered to S5
A terminal S6 input contact opening (H/O/A = Auto) selects serial com for both the run/stop command and speed command. A terminal S6 input contact closure
(H/O/A = Hand) allows b1-01 to select Keypad/Operator as the speed command source. This input is jumpered to S5, therefore the contact is closed when
H/O/A = Hand.
H3-08 = 2: 4-20 mA (default)
H3-09 = B: PI Feedback
Terminal A2 is programmed for 4-20 mA (Note – Control PCB DIP switch S1-2 must also be ON)
Terminal A2 function is set to provide PI feedback for closed loop control
H3-13 = 1: Main Fref TA2 Terminal A2 (the feedback terminal) serves as the main input
Programming 5 - 27
Options - G, H, L, Q, or V
and S "Serial Communications" and "Speed Pot."; Bypass with PI Control and serial communication for run/stop control and Setpoint input, with hand mode speed potentiometer:
Hand mode speed command from speed potentiometer.
Auto mode PI Setpoint input signal from serial communication.
Auto mode run/stop command for Drive from serial communication.
Auto mode run/stop contact closure for Bypass applied to terminals TB1-3 and TB1-4.
Significant
Parameter Setting b1-01 = 1: Terminals (default) b5-01 = 1: Enable
H1-03 = 19: PI Disable
Result
Speed command (Hand) and PI setpoint (Auto) source = Terminals
Enable PI mode of operation
A terminal S5 input contact closure disables PI mode. This input contact is closed when H/O/A = Hand.
H1-04 = 6C: Com/Inv Sel 2 S6 must be jumpered to S5
A terminal S6 input contact opening (H/O/A = Auto) selects serial com for both the run/stop command and speed command. A terminal S6 input contact closure
(H/O/A = Hand) allows b1-01 to select Keypad/Operator as the speed command source. This input is jumpered to S5, therefore the contact is closed when
H/O/A = Hand.
H3-08 = 0: 0-10 VDC
H3-09 = B: PI Feedback
Terminal A2 is programmed for 0-10 VDC (Note – Control PCB DIP switch S1-2 must also be OFF)
Terminal A2 function is set to provide PI feedback for closed loop control
H3-13 = 1: Main Fref TA2 Terminal A2 (the feedback terminal) serves as the main input
Programming 5 - 28
The analog feedback to the Drive for the PI control is via the A2 terminal. The Drive must be programmed
(H3-09= “B: PI Feedback”) to use terminal A2 as feedback for the PI functionality of the Drive.
The PI setpoint can be configured to come from one of many different inputs or parameters. The table below describes the options for originating the PI setpoint.
06H
D1-01
Table 5.5 PI Setpoint Options
The PI Setpoint will be read from:
Parameter b5-19
Modbus Register
Terminal A1
Serial Com.
Option PCB
If these conditions are true
Status of b5-18
Status of
Modbus
Register
0Fh bit 1
Status of b1-01
= 1
= 0
= 0
= 0
= 0
= 0
N/A
ON
OFF
OFF
OFF
OFF
N/A
N/A
= 0
= 1
= 2
= 3
In some situations there are two feedback inputs. The Drive can be programmed to maintain a set differential between two analog signals. If input A2 is configured as a “PI Differential Mode” (H3-09= “16: PI Differential”), then the Drive will maintain a set difference between the measurements read on inputs A1 and A2. This differential setpoint is programmed by parameter (b5-07).
"
b5-01 PI Mode
Setting
0
1
3
Description
Disabled (factory default)
Enabled
Fref+PI
The Drive can be used as a stand-alone PI controller. If PI functionality is selected by parameter b5-01, the Drive will adjust its output to cause the feedback from a transmitter to match the PI setpoint (b5-19). The setting of b5-01 will determine whether
PI functionality is disabled (b5-01= “0: Disabled”), enabled (b5-01= “1: Enabled”), or enable with the output of the
PI function used to trim a Speed Command (b5-01= “3: Fref+PI”).
"
b5-02 Proportional Gain Setting
Setting Range: 0.00 to 25.00
Factory Default: 2.00
The proportional gain will apply a straight multiplier to the calculated difference (error) between the PI Setpoint and the measured transmitter feedback at terminal A2. A large value will tend to reduce the error but may cause instability
(oscillations) if too high. A small value may allow to much offset between the setpoint and feedback (See Figure 5.14 on following page).
"
b5-03 Integral Time Setting
Setting Range: 0.0 to 360.0 Seconds
Factory Default: 5.0 Seconds
Programming 5 - 29
The Integral factor of PI functionality is a time-based gain that can be used to eliminate the error (difference between the setpoint and feedback at steady state). The smaller the Integral Time set into b5-03, the more aggressive the Integral factor will be. To turn off the Integral Time, set b5-03= 0.00.
Setpoint
Offset
Setpoint
Zero offset with
Integral Action
Feedback Feedback
No Integral
TIME
With Integral
Fig 5.16 PID Feedback Response Characteristics
TIME
"
b5-04 Integral Limit Setting
Setting Range: 0.0 to 100.0%
Factory Default: 100.0%
On some applications, especially those with rapidly varying loads, the output of the PI function may have large oscillations. To suppress these oscillations, a limit can be applied to the integral factor by programming b5-04.
"
b5-06 PI Output Limit
Setting Range: 0.0 to 100.0%
Factory Default: 100.0%
Places a cap on the output of the PI function. Limiting the PI function may help to prevent large overshoots in the Drive’s response to error (the difference between the setpoint and the feedback).
"
b5-07 PI Offset Adjustment
Setting Range: -100.0% to +100.0%
Factory Default: 0.0%
The PI Offset Adjustment parameter has two different uses. Parameter b5-07 serves different functions depending on whether it is used on a standard PI loop or a Differential PI loop.
Parameter b5-07 causes an offset to be applied to the output of the PI function in a non-differential PI loop. Every time the PI output is updated, the offset (b5-07) is summed with the PI output. This can be used to artificially kick-start a slow starting PI loop.
If the Drive is configured for Differential PI Regulation (H3-09= “16: PI Differential”), then this parameter is the target setpoint for the differential to be maintained between the signal measured on analog input A1 and the signal measured on analog input A2.
Programming 5 - 30
"
b5-08 PI Primary Delay Time Constant
Setting Range: 0.00 to 10.00 Seconds
Factory Default: 0.00 Seconds
Acts as a time based filter that lowers the responsiveness of the PI function, but also makes the function more stable when the setpoint varies rapidly or when the feedback is noisy.
"
b5-09 PI Output Level Selection
Setting
0
1
Description
Normal Output (direct acting) (factory default)
Reverse Output (reverse acting)
Normally, the output of the PI function causes an increase in motor speed whenever the measured feedback is below the setpoint. This is referred to as direct acting response. However, if b5-09= “1: Reverse Output”, the output of the PI function causes the motor to slow down when the feedback is below the setpoint. This is referred to as reverse acting response.
"
b5-10 PI Output Gain Setting
Setting Range: 0.0 to 25.0
Factory Default: 1.0
Applies a multiplier to the output of the PI function. Using the gain can be helpful when the PI function is used to trim the
Speed Command. Increasing b5-10 causes the PI function to have a greater regulating affect on the speed command.
"
b5-11 PI Reverse Selection
Setting
0
1
Description
0 Limit (factory default)
Reverse
Parameter b5-11 determines whether reverse operation is allowed while using PI control (b5-01
≠
0). The factory default setting will not allow the Drive to run in reverse. This parameter does not need to be changed from factory default for a majority of
HVAC applications. (Refer also to b5-09).
"
b5-12 PI Feedback Reference Missing Detection Selection
Setting
0
1
2
Description
Disabled (factory default)
Alarm
Fault
Loss of feedback can cause problems to a PI application. The Drive can be programmed to turn on a digital output whenever a loss of feedback occurs. Feedback Loss Detection is turned on by b5-12. When b5-12= “1: Alarm”, the Drive acknowledges the loss of feedback without stopping or turning on the fault output (MA-MB). If b5-12= “2: Fault”, the Drive coasts to a stop and turns on the fault output if the feedback is determined to be lost.
Programming 5 - 31
"
b5-13 PI Feedback Loss Detection Level
Setting Range: 0 to 100%
Factory Default: 0%
"
b5-14 PI Feedback Loss Detection Time
Setting Range: 0.0 to 25.0 Seconds
Factory Default: 1.0 Seconds
The Drive interprets feedback loss whenever the feedback signal drops below the value of b5-13 and stays below that level for at least the time set into b5-14. See Figure 5.15 below for timing details.
Measured
Feedback b5-13
T T
TIME
T = b5-14
ON (CLOSED) t OFF (OPEN)
Fig 5.17 Loss of PI Feedback Feature
"
b5-15 Sleep Function Start Level
Setting Range: 0.0 to 200.0 Hz
Factory Default: 0.0 Hz
"
b5-16 Sleep Delay Time
Setting Range: 0.0 to 25.5 Seconds
Factory Default: 0.0 Seconds
The Sleep Function can be programmed to prevent running the Drive when the PI loop output or the speed command is so low that no usable work is being done and/or equipment damage may result. The Sleep Function can be Enabled by entering a value in parameter b5-15. If the Drive’s output drops below the level set by the Sleep Function Start Level (b5-15) and remains there at least as long as the delay time determined by the Sleep Delay Time (b5-16), then the Drive’s internal Run command drops out and the Drive output ceases. Though the Drive’s output has ceased, all other Drive functions continue. Once the Drive’s theoretical output returns to a level above the Sleep Function Start Level (b5-15) and remains above that level for at least the
Sleep Delay Time (b5-16), the internal Run command returns and the Drive output begins again. The b5-16 Delay Time prevents oscillation about the sleep level. Note: The sleep function can be used even if the P1 function is disabled
(b5-01 = “0: Disabled”).
t
Upper Limit d2-01
Sleep Level b5-15
Fig 5.18 Sleep Function Response
Programming 5 - 32
"
b5-17 PI Accel/Decel Time
Setting Range: 0.0 to 25.5 Seconds
Factory Default: 0.0 Seconds
This is a soft start function that is applied to the PI setpoint analog input. Instead of having nearly instantaneous changes in signal levels, there is a programmed ramp applied to level changes. When changing setpoints the error can be limited by gradually ramping the setpoint through the use of parameter b5-17.
"
b5-18 PI Setpoint Selection
Setting
0
1
Description
Disabled (factory default)
Enabled
In order to use parameter b5-19 as the PI Setpoint, set parameter b5-18= “1: Enabled”. If b5-18= “0: Disabled” the PI Setpoint will either be:
• Modbus Register 06H (If Register 0FH bit 1 is high)
• The active speed command (i.e. Determined by the setting of b1-01). See Table 1 “Setpoint Options”
"
b5-19 PI Setpoint Value
Setting Range: 0.00 to 100.00%
Factory Default: 0.00%
Parameter b5-19 is for a PI Setpoint value. When b5-18= “1: Enabled”, the value of b5-19 will take precedent over any other PI setpoint unless the Drive is set up for Differential Feedback, in which case, b5-18 and b5-19 have no affect on the PI function.
"
b5-20 PI Setpoint Display Scaling
Setting
0
1
3
3
Hz (factory default)
%
RPM (Synchronous)
Engineering Units
Description
The PI Setpoint Display Scaling value (b5-20) is a scaling factor that is applied to the monitor display for both the PI Setpoint
(U1-38) and the PI Feedback (U1-24).
Table 5.6 PI Setpoint Display Scaling Options
If b5-20 is:
0
1
2 through 39
(enter the # of motor poles)
40 through 39999
U1-24 and U1-38
Display Increments.
0.01 Hz
0.00%
0 RPM
Engineering Units
Programming 5 - 33
If the monitors seem more natural in terms of percentage, set b5-20= 1. If the monitors are easier to work with when displaying the equivalent synchronous RPM, set b5-20= [the number of motor poles].
If another engineered unit, such a fpm or cfm, is desired, set b5-20= xxxxx where
X X X X X
Digit 5 Digit 4 Digit 3 Digit 2 Digit 1
Digits 1 through 4 set the desired number to be displayed at 100% speed.
Digit 5 determines the number of decimal places
If Digit 5 = 0 number format is XXXX
If Digit 5 = 1 number format is XXX.X
If Digit 5 = 2 number format is XX.XX
If Digit 5 = 3 number format is X.XXX
For example:
If b5-20= 10425 then at 100% output the digital operator would display 42.5 for monitor U1-38 or U1-24.
"
b5-21 Sleep Source
Setting
0
1
2
Description
SFS Input (Output of PI block)
PI Setpoint (factory default)
Snooze
Parameter b5-21 selects the sleep function characteristic action:
When b5-21= “0: SFS Input” the sleep function start level (b5-15) is compared to the Drive’s output (Speed Command after PI block). This is the setting that should be used for open loop or closed loop control.
It is also possible to have the sleep function start level (b5-15) compared to the Drive input or setpoint. For this special application set b5-21= “1: PI Setpoint”.
When b5-21= “2: Snooze” a variation of the sleep function called “Snooze” is enabled, see parameter b5-22 to b5-27.
IMPORTANT
The sleep function can be used even if the PI function is disabled (b5-01= ”0: Disabled”).
Programming 5 - 34
"
b5-22 PI Snooze Level
Setting Range: 0 to 100%
Factory Default: 0%
"
b5-23 PI Snooze Delay Time
Setting Range: 0 to 3600 Seconds
Factory Default: 0 Seconds
"
b5-24 PI Snooze Deactivation Level
Setting Range: 0 to 100%
Factory Default: 0%
The Snooze Function is a variation on the Sleep Function. The Snooze function must be selected by setting parameter b5-21= “2: Snooze”. Once the Snooze Function is selected, the Drive monitors the output frequency. If the output frequency drops below the PI Snooze Level (b5-22), and stays below that level for at least the PI Snooze Delay Time (b5-23), the Drive output shuts off. This is different from the Sleep Function because it is the feedback that must drop below the PI Snooze
Deactivation Level (b5-24) before normal Drive output will begin again. See Figure 5.19 on the following page.
"
b5-25 PI Setpoint Boost Setting
Setting Range: 0 to 100%
Factory Default: 0%
Just before the Snooze Function is activated, the PI Setpoint can be temporarily increased to create an overshoot of the intended PI Setpoint. The temporary boost is determined by the PI Setpoint Boost Setting (b5-25). Once the temporary boost level is reached (or the PI Maximum Boost Time (b5-26) is exceeded), the Drive output shuts off (snoozes) and the intended PI
Setpoint returns. From this point on, the Snooze Function operates normally and the Drive output returns when the feedback level drops below b5-24. See Figure 5.19 on the following page.
Programming 5 - 35
"
b5-26 PI Maximum Boost Time
Setting Range: 0 to 3600 Seconds
Factory Default: 0 Seconds
Associated with the Snooze Function. In cases where the temporary PI Setpoint (intended PI setpoint + PI Setpoint Boost) cannot be reached within the PI Maximum Boost Time (b5-26), the Setpoint Boost is interrupted and the Drive output is turned off.
b5-26
PI Output
PI Output
PI Setpoint
PI Setpoint
PI Feedback
PI Feedback b5-23 b5-22 b5-24 t
t
t b5-23
Snooze
Function
OFF
ON
OFF
TIME
Either PI
Feedback boosted setpoint value reaches the new or the maximum boost boosted setpoint time b5-26 is reached. value or the maximum boost time is reached .
Fig 5.19 Snooze Function Operation
"
b5-27 PI Snooze Feedback Level
Setting Range: 0 to 100%
Factory Default: 60%
This is a second method of initiating the Snooze Function. If the PI feedback level exceeds the PI Snooze Feedback Level
(b5-27), then the Drive output shuts off. Once the PI feedback drops below the PI Snooze Deactivation Level (b5-24) then normal Drive and PI operation return.
"
b5-28 PI Feedback Square Root Function Activation
Setting
0
1
Description
Disabled (factory default)
Enabled
If b5-28= “1: Enabled”, the square root of the PI feedback is compared to the PI Setpoint in order to determine appropriate
Drive output to properly regulate the system. This is helpful in cases where the measured feedback is pressure but the PI loop needs to regulate flow.
Programming 5 - 36
"
b5-29 PI Square Root Gain
Setting Range: 0.00 to 2.00
Factory Default: 1.00
A multiplier applied to the square root of the feedback.
"
b5-30 PI Output Square Root Monitor Selection
Setting
0
1
Description
Disabled (factory default)
Enabled
If the PI Function is regulating the flow of a closed loop system by using a pressure feedback, it may be convenient to view the square root of the PI output using monitor U1-37.
!
b8 Energy Savings
The energy savings function improves overall system operating efficiency by operating the motor at its highest efficiency. This
is accomplished by continuously monitoring the motor load and adjusting the motor terminal voltage so that the motor always operates near its rated slip frequency. A motor is most efficient when operating near rated slip conditions.
"
b8-01 Energy Savings Selection
Setting
0
1
Description
Disabled (factory default)
Enabled
When the Energy Savings function is enabled (b8-01= “1: Enabled”), the Drive reduces the output voltage to the motor below
the voltage value specified by the programmed V/f pattern whenever the motor load is light. Since torque is reduced during this voltage reduction, the voltage has to return to normal levels when the load returns. The energy savings is realized through improved motor efficiency. The reduced output voltage causes increased rotor slipping even with a light load. A motor is most efficient when operating fully loaded (i.e. operating at rated slip).
"
b8-04 Energy Saving Coefficient Value
Setting Range: 0.0 to 655.0
Factory Default: Model Dependent
Parameter b8-04 is used in maximizing motor efficiency. The factory setting will be Drive capacity dependent but can be adjusted in small amounts while viewing the kW monitor (U1-08) and running the Drive to minimize the output kW. A larger value typically results in less voltage to the motor and less energy consumption. Too large a value will cause the motor to stall.
Programming 5 - 37
!
C1 Accel/Decel
"
C1-01 Acceleration Time 1
C1-02 Deceleration Time 1
C1-03 Acceleration Time 2
C1-04 Deceleration Time 2
Setting Range: 0.0 to 6000.0 Seconds
Factory Default: 30.0 Seconds
C1-01 (Acceleration Time 1) sets the time to accelerate from zero to maximum speed (E1-04). C1-02 (Deceleration Time 1) sets the time to decelerate from maximum speed to zero. C1-01 and C1-02 are the factory default active accel/decel “pair”. Another accel/decel pair (C1-03 and C1-04) exists that can be activated by a multi-function digital input (H1-0x= 7), or specified by a switch over frequency as programmed in parameter C1-11.
Note: In fan applications employing duct high pressure safety limit switches, it may be necessary to further adjust the deceleration time to avoid high pressure limit trips due to damper closure as the system is shut down (an alternate solution in this situation is to set parameter b1-03 to “Coast to Stop”).
"
C1-09 Fast Stop Time
Setting Range: 0.0 to 6000.0 Seconds
Factory Default: 10.0 Seconds
A special deceleration parameter is available for use with emergency or fault operations. Parameter C1-09 will set a special deceleration that can be operated by closing a digital input configured as H1-0x= 15 or H1-0x= 17. A digital input configured as H1-0x= 15 will look for a switch closure before initiating the Fast Stop operation. A digital input configured as
H1-0x= 17 will look for the switch opening before initiating the Fast Stop operation.
Unlike a standard deceleration time, once the Fast Stop operation is initiated even momentarily, the Drive cannot be re-operated until the deceleration is complete, the Fast Stop input is cleared, and the Run command is cycled.
Programming 5 - 38
!
d1 Preset References
"
d1-01 Frequency Reference 1 d1-02 Frequency Reference 2 d1-03 Frequency Reference 3 d1-04 Frequency Reference 4
Setting Range: 0.00 to E1-04 Value
Factory Default: d1-01 = 10.00 Hz d1-02 = 6.00 Hz d1-03 = 0.00 Hz d1-04 = 40.00 Hz d1-01, d1-02 and d1-04 are special parameter settings required by the Bypass logic circuit. See Table 5.1.
d1-04 d1-03
Output
Speed d1-02 d1-01 d1-17 t
Closed
Open
RUN
Multi-step
Reference 1 Input
Multi-step
Reference 2 Input
Jog Input
Fig 5.20 Preset Reference Timing Diagram example
"
d1-17 Jog Frequency Reference
Setting Range: 0.00 to E1-04 Value
Factory Default: 6.00 Hz
Closed
Open
Closed
Open
Closed
Open
The Drive can be programmed to utilize digital inputs to change between four presets speeds and a jog speed. It is a two-step process to set the Drive up for preset speeds. First, d1-01 through d1-04 and d1-17 must be programmed with the desired preset speeds and the desired jog speed, respectively. Next, up to three of the Drive’s digital inputs (Terminals S3 through S7) need to be programmed (via parameters H1-01 to H1-05) and wired (to normally open contacts) as Multi-step Speed Reference 1, Multi-step
Speed Reference 2, and Jog Frequency.
Table 5.7 Preset Speed Truth Table
Preset Speed
Terminal
programmed as Multi-step
Reference 1
OFF
Terminal programmed as Multi-step
Reference 2
OFF 1
2
3
ON
OFF
OFF
ON
4 ON ON
5 -
*
The Jog Frequency input is given priority over the multi-step speeds.
Terminal programmed as Jog
Reference
OFF
OFF
OFF
OFF
ON*
Details
Frequency Reference 1 (d1-01) or analog input A1
Frequency Reference 2 (d1-02) or analog input A2
Frequency Reference 3 (d1-03)
Frequency Reference 4 (d1-04)
Jog Frequency (d1-17)
Programming 5 - 39
As shown in Table 5.6, it is possible to use analog inputs in place of Frequency Reference 1 and Frequency
Reference 2.
#
If b1-01= “1: Terminals” then the analog input A1 will be used instead of Frequency Reference 1 for the first preset speed.
If b1-01= “0: Operator”, then Frequency Reference 1 will be used.
#
If H3-09= “2: Aux Reference” then the analog input A2 will be used instead of Frequency Reference 2 for the second preset speed. If H3-09
≠
2 then Frequency Reference 2 will be used.
IMPORTANT
The programming of d1-01 through d1-04 and d1-17 will be affected by the setting of o1-03. The programming of these parameters will be in the units specified by Display Scaling parameter (o1-03).
Programming 5 - 40
!
d2 Reference (Speed Command) Limits
"
d2-01 Frequency Reference Upper Limit
Setting Range: 0.0 to 110.0%
Factory Default: 100.0%
"
d2-02 Frequency Reference Lower Limit
Setting Range: 0.0 to 110.0%
Factory Default: 0.0%
The use of parameters d2-01 and d2-02 places limitations on the speed command that the Drive will accept. The parameters are set in units of percentage of the maximum frequency (E1-04) and provide limits on any remote speed command input. By entering upper or lower frequency limits, the Drive programmer can prevent operation of the Drive above or below levels that may cause resonance, equipment damage or discomfort (see also parameter d3-0X). For example, limits may be needed to prevent low speed operation of: cooling tower fans with gear boxes, pumps with pressure dependent seals or AHUs with minimum delivery requirements.
Internal Speed Command d2-01 d2-01
Operating
Range
Frequency Reference Upper Limit
Frequency Reference Lower Limit
Set Speed Command
Note: See also the “Sleep” function in Figure 5.19 for alternate “lower limit” implementation.
Fig 5.21 Frequency Reference Upper and Lower Limit Effects on the Speed Command
Programming 5 - 41
!
d3 Jump Frequencies
"
d3-01 Jump Frequency 1 d3-02 Jump Frequency 2 d3-03 Jump Frequency 3
Setting Range: 0.0 to 200.0 Hz
Factory Default: 0.0 Hz
"
d3-04 Jump Frequency Width
Setting Range: 0.0 to 20.0 Hz
Factory Default: 1.0 Hz
In order to avoid continuous operation at a speed that causes resonance in driven machinery, the Drive can be programmed with jump frequencies that will not allow continued operation within specific frequency ranges. If a speed is commanded that falls within a dead band, or Jump Frequency, the Drive will clamp the frequency reference just below the dead band and only accelerate past it when the commanded speed rises above the upper end of the dead band, for increasing references. Similarly, the Drive will clamp the frequency reference just above the dead band and only decelerate past it when the command speed falls below the lower end of the dead band, for decreasing references.
d3-03 d3-03 d3-02 d3-04 d3-01 d3-04
User Frequency
Reference
Fig 5.22 Jump Frequency Characteristics d3-04
Setting the center point of the dead band with the d3-01 through d3-03 parameters and setting the width of the dead band with parameter d3-04 determines the dead band characteristics. The programmer can set up to three Jump Frequencies. If multiple
Jump Frequencies are programmed the following rule applies: d3-01
< = d3-02
<
= d3-03
Programming 5 - 42
!
d4 Sequence
"
d4-01 MOP Reference Memory
Setting
0
1
Description
Disabled (factory default)
Enabled
The Drive offers the capacity to change the speed command much the way a Motor Operated Potentiometer (MOP) would.
Using programmed digital inputs configured as MOP Increase (H1-0x= 10) and MOP Decrease (H1-0x= 11), the Drive will increase the speed command whenever the MOP Increase input is closed and decrease the speed command whenever the MOP
Decrease is closed. The speed command will remain constant whenever both inputs are open or closed.
Parameter d4-01 determines whether the last speed command, before the Run command was removed, is remembered even if the power is cycled to the Drive. If d4-01= “0: Disabled”, then when a new Run command is issued the Drive’s speed command will be 0 rpm. If d4-01= “1: Enabled”, then the speed command will be the last commanded speed before the Run command was removed.
Programming 5 - 43
!
E1 V/f Pattern
"
E1-01 Input Voltage Setting
Setting Range: 155.0V to 255.0V (208V/240V Models)
310.0V to 510.0V (480V Models)
Factory Defaults: 208.0V (208V Models)
240.0V (240V Models)
480.0V (480V Models)
Set the Input Voltage parameter (E1-01) to the nominal voltage of the connected AC power supply. This parameter adjusts the levels of some protective features of the Drive (i.e. Overvoltage, Stall Prevention, etc.). E1-01 also serves as the Maximum/
Base Voltage used by the Preset V/Hz curves (E1-03= 0 to D).
"
E1-03 V/f Pattern Selection
A
B
8
9
5
6
7
Setting
0
1
2
3
4
C
D
F
FF
Description
50 Hz
60 Hz Saturation
50 Hz Saturation
72 Hz
50 Hz VT1
50 Hz VT2
60 Hz VT1
60 Hz VT2
50 Hz HST1
50 Hz HST2
60 Hz HST1
60 Hz HST2
90 Hz
120 Hz
Custom V/f (factory default, with parameter values per setting 1)
Custom w/o limit
The Drive operates utilizing a set V/f pattern to determine the appropriate output voltage level for each commanded speed.
There are 14 different preset V/f patterns to select from with varying voltage profiles, saturation levels (frequency at which maximum voltage is reached), and maximum frequencies.
There are also settings for Custom V/f patterns that will allow the programmer to manually set (“Customize”) the V/f pattern using parameters E1-04 through E1-13.
Using parameter E1-03, the programmer can select one of the preset V/f patterns or chose between a custom V/F pattern with an upper voltage limit (E1-03= “F: Custom V/F”) and a custom V/f pattern without a voltage limit (E1-03= “FF: Custom w/o limit”).
Programming 5 - 44
Specifications E1-03
50Hz
60Hz Saturation
50Hz Saturation
72Hz
0
1
F
2
3
Table 5.8 Preset V/f Patterns
V/f Pattern *1 Specifications E1-03
230
(V)
17
10
0 1.3 2.5
0
50
(Hz)
230
(V)
17
10
0 1.5 3.0
2
1
F
50 60
(Hz)
230
(V)
3
50Hz
High
Starting
Torque 1
60Hz
High
Starting
Torque 2
High
Starting
Torque 1
High
Starting
Torque 2
8
9
A
B
90Hz C
50Hz
60Hz
Variable
Torque 1
Variable
Torque 2
Variable
Torque 1
Variable
Torque 2
4
5
6
7
17
10
0 1.5 3.0
60 72
(Hz)
230
(V)
5
57
40
10
9
0 1.3
25
4
50
(Hz)
230
(V)
7
57
40
10
9
0 1.5
30
6
60
(Hz)
120Hz D
V/f Pattern *1
230
(V)
9
28
22
15
13
0 1.3 2.5
8
50
(Hz)
230
(V)
B
28
22
17
13
0 1.5 3.0
A
230
(V)
C
60
(Hz)
17
10
0 1.5 3.0
230
(V)
D
17
10
0 1.5 3.0
60 90
(Hz)
60 120
(Hz)
If one of the custom V/f patterns is selected, then parameters E1-04 through E1-13 will determine the V/F pattern.
IMPORTANT
When a factory Initialization is performed, the setting of E1-03 is unaffected but the settings of E1-04 through
E1-13 are returned to their factory default settings.
"
E1-04 Maximum Output Frequency
Setting Range: 0.0 to 120.0 Hz
Factory Default: 60.0 Hz
Programming 5 - 45
"
E1-05 Maximum Output Voltage
Setting Range: 0.0 to 255.0V (208V/240V Models)
0.0 to 510.0V (480V Models)
Factory Defaults: 208.0V (208V Models)
240.0V (240V Models)
480.0V (480V Models)
"
E1-06 Base Frequency
Setting Range: 0.0 to 200.0 Hz (settings above 120.0 Hz are currently not supported)
Factory Default: 60.0 Hz
"
E1-07 Mid Output Frequency A
Setting Range: 0.0 to 200.0 Hz (settings above 120.0 Hz are currently not supported)
Factory Default: 3.0 Hz
"
E1-08 Mid Output Voltage A
Setting Range: 0.0 to 255.0V (208V/240V Models)
0.0 to 510.0V (480V Models)
Factory Defaults: 18.0V (208V Models)
18.0V (240V Models)
18.0V (480V Models)
"
E1-09 Minimum Output Frequency
Setting Range: 0.0 to 200.0 Hz (settings above 120.0 Hz are currently not supported)
Factory Default: 1.5 Hz
"
E1-10 Mid Output Voltage
Setting Range: 0.0 to 255.0V (208V/240V Models)
0.0 to 510.0V (480V Models)
Factory Defaults: 10.8V (208V Models)
10.8V (240V Models)
10.8V (480V Models)
"
E1-11 Mid Output Frequency B
Setting Range: 0.0 to 200.0 Hz (settings above 120.0 Hz are currently not supported)
Factory Default: 0.0 Hz
"
E1-12 Mid Output Voltage B
E1-13 Base Voltage
Setting Range: 0.0 to 255.0V (208V/240V Models)
0.0 to 510.0V (480V Models)
Factory Defaults: 0.0V (208V Models)
0.0V (240V Models)
0.0V (480V Models)
Programming 5 - 46
To set up a custom V/f pattern, program the points shown in the diagram below using parameters E1-04 through E1-13. Be sure that the following condition is true:
E1-09
≤
E1-07
≤
E1-06
≤
E1-11
≤
E1-04
Max Voltage E1-05
Mid Voltage B E1-12
Base Voltage E1-13
Mid Voltage A E1-08
Min Voltage E1-10
Min
Freq
Mid
E1-11
Base
Freq
Mid
Freq B
A
E1-04
Max
Freq
Frequency
Fig 5.23 Custom V/f Pattern Programming Curve
Increasing the voltage in the V/f pattern increases the available motor torque. However, when setting a custom V/f pattern, increase the voltage gradually while monitoring the motor current, to prevent:
• Drive faults as a result of motor over-excitation
• Motor overheating or excessive vibration
Table 5.8 is for 240V class units only. For 480V class units, multiply the voltage values by 2.
Table 5.9 V/f Pattern Default Settings for Drive Capacity 0.5 to 2 HP for 240V Class
Parameter
No.
Name Unit
E1-03 V/f Pattern Selection —
E1-04
E1-05
E1-06
E1-07
E1-08
E1-09
E1-10
E1-11
Max Output Frequency
Max Output Voltage
Base Frequency
Mid Output Frequency A
Mid Output Voltage A
Min Output Frequency
Mid Output Voltage
Mid Output Frequency B
E1-12
E1-13
Mid Output Voltage B
Base Voltage
For 480V class units, the value is twice that of 240V class units.
V
V
V
Hz
V
Hz
Hz
V
Hz
V
0
50.0
240.0
50.0
2.5
17.2
1.3
10.3
0
0
0
1
60.0
240.0
60.0
3.0
17.2
1.5
10.3
0
0
0
2
60.0
240.0
50.0
3.0
17.2
1.5
10.3
0
0
0
Factory Setting
3 4
72.0
50.0
240.0
240.0
60.0
3.0
50.0
25.0
17.2
1.5
10.3
0
0
0
40.2
1.3
9.2
0
0
0
5 6 7
50.0
60.0
60.0
240.0
240.0
240.0
50.0
25.0
60.0
30.0
60.0
30.0
57.5
1.3
10.3
0
0
0
40.2
1.5
9.2
0
0
0
57.5
1.5
10.3
0
0
0
Programming 5 - 47
Table 5.9 V/f Pattern Default Settings for Drive Capacity 0.5 to 2 HP for 240V Class (Continued)
Parameter
No.
E1-03
Name
V/f Pattern Selection
Unit
— 8 9 A
Factory Setting
B C D E
E1-04 Max. Output Frequency Hz
E1-05
E1-06
E1-07
E1-08
E1-09
E1-10
E1-11
Max. Output Voltage
Base Frequency
Mid. Output Frequency A
Mid. Output Voltage A
Min. Output Frequency
Mid. Output Voltage
Mid Output Frequency B
E1-12
E1-13
Mid Output Voltage B
Base Voltage
For 480V class units, the value is twice that of 240V class units.
V
V
V
Hz
V
Hz
V
Hz
V
50.0
240.0
50.0
2.5
21.8
1.3
12.6
0
0
0
50.0
240.0
50.0
2.5
27.6
1.3
14.9
0
0
0
60.0
240.0
60.0
3.0
21.8
1.5
12.6
0
0
0
60.0
90.0
120.0
240.0
240.0
240.0
60.0
3.0
60.0
3.0
60.0
3.0
27.6
1.5
17.2
0
0
0
17.2
1.5
10.3
0
0
0
0
0
17.2
1.5
10.3
0
F
180.0
60.0
240.0
240.0
60.0
3.0
60.0
3.0
17.2
1.5
10.3
0
0
0
0
0
17.2
1.5
10.3
0
Table 5.10 V/f Pattern Default Settings for Drive Capacity 3 to 75 HP for 240V Class
Parameter
No.
Name Unit
E1-03 V/f Pattern Selection —
E1-04
E1-05
E1-06
E1-07
E1-08
E1-09
E1-10
Max. Output Frequency
Max. Output Voltage
Base Frequency
Mid. Output Frequency A
Mid. Output Voltage A
Min. Output Frequency
Mid. Output Voltage
E1-11
E1-12
Mid Output Frequency B
Mid Output Voltage B
Hz
V
E1-13 Base Voltage V
For 480V class units, the value is twice that of 240V class units.
V
V
Hz
V
Hz
V
Hz
0
50.0
240.0
50.0
2.5
16.1
1.3
8.0
0
0
0
1
60.0
240.0
60.0
3.0
16.1
1.5
8.0
0
0
0
2
60.0
240.0
50.0
3.0
16.1
1.5
8.0
0
0
0
Factory Setting
3
0
0
0
4 5
72.0
50.0
50.0
240.0
240.0
240.0
60.0
50.0
50.0
3.0
16.1
1.5
8.0
25.0
40.2
1.3
6.9
25.0
57.5
1.3
8.0
0
0
0
0
0
0
6 7
0
0
0
60.0
60.0
240.0
240.0
60.0
60.0
30.0
40.2
1.5
6.9
30.0
57.5
1.5
8.0
0
0
0
Programming 5 - 48
Table 5.10 V/f Pattern Default Settings for Drive Capacity 3 to 40 HP for 240V (Continued)
Parameter
No.
Name Unit
E1-03 V/f Pattern Selection —
E1-04 Max. Output Frequency Hz
E1-05
E1-06
E1-07
E1-08
E1-09
E1-10
E1-11
E1-12
Max. Output Voltage
Base Frequency
Mid. Output Frequency A
Mid. Output Voltage A
Min. Output Frequency
Mid. Output Voltage
Mid Output Frequency B
Mid Output Voltage B
E1-13 Base Voltage
For 480V class units, the value is twice that of 240V class units.
Hz
V
Hz
V
V
V
Hz
V
V
8
50.0
9
50.0
1.3
10.3
0
0
0
240.0
240.0
50.0
50.0
2.5
20.7
2.5
26.4
1.3
12.6
0
0
0
A
Factory Setting
B C D E F
60.0
60.0
90.0
120.0
180.0
60.0
1.5
10.3
0
0
0
240.0
240.0
240.0
240.0
240.0
240.0
60.0
60.0
60.0
60.0
60.0
60.0
3.0
20.7
3.0
26.4
3.0
16.1
3.0
16.1
3.0
16.1
3.0
16.1
1.5
14.9
0
0
0
1.5
8.0
0
0
0
1.5
8.0
0
0
0
1.5
8.0
0
0
0
0
0
1.5
8.0
0
Table 5.11 V/f Pattern Default Settings for Drive Capacity 50 to 150 HP for 230V
Parameter
No.
Name
E1-03 V/f Pattern Selection
E1-04
E1-05
E1-06
E1-07
E1-08
E1-09
E1-10
Max. Output
Frequency
Max. Output Voltage
Max. Voltage
Frequency
Mid. Output
Frequency A
Mid. Output
Voltage A
Min. Output
Frequency
Mid. Output
Voltage
E1-11
E1-12
Mid Output Frequency B
Mid Output Voltage B
E1-13 Base Voltage
For 480V class units, the value is twice that of 240V class units.
Unit
–
Hz
V
Hz
V
V
Hz
V
Hz
V
V
0
50.0
240.0
50.0
2.5 3.0
13.8
1.3 1.5
6.9
0
0
0
1
60.0
240.0
60.0
13.8
6.9
0
0
0
2
60.0
240.0
50.0
3.0
13.8
1.5
6.9
0
0
0
Factory Setting
3
72.0
240.0
60.0
3.0
13.8
1.5
6.9
0
0
0
4
50.0
240.0
50.0
25.0
40.2
1.3
5.7
0
0
0
5
50.0
240.0
50.0
57.5
6
60.0
240.0
60.0
40.2
1.3 1.5
6.9
0
0
0
5.7
0
0
0
7
60.0
240.0
60.0
30.0
57.5
1.5
6.9
0
0
0
Programming 5 - 49
Table 5.11 V/f Pattern Default Settings for Drive Capacity 100 to 150 HP for 230V (Continued)
Parameter
No.
Name Unit
E1-03 V/f Pattern Selection – 8
E1-04
E1-05
E1-06
E1-07
E1-08
E1-09
E1-10
E1-11
Max. Output
Frequency
Max. Output Voltage
Base
Frequency
Mid. Output
Frequency A
Mid. Output
Voltage A
Min. Output
Frequency
Mid. Output
Voltage
Mid Output Frequency B
Hz
V
Hz
V
V
Hz
V
Hz
50.0
240.0
50.0
2.5
17.2
1.3
8.0
0
E1-12
Mid Output Voltage
B
V 0
E1-13 Base Voltage V
For 480V class units, the value is twice that of 240V class units.
0
9
50.0
240.0
50.0
2.5
23.0
1.3
10.3
0
0
0
A
60.0
240.0
60.0
3.0
17.2
1.5
8.0
0
0
0
Factory Setting
B
60.0
240.0
60.0
3.0
23.0
1.5
12.6
0
0
0
C
90.0
240.0
60.0
3.0
13.8
1.5
6.9
0
0
0
D
120.0
240.0
60.0
3.0
13.8
1.5
6.9
0
0
0
E
180.0
240.0
60.0
3.0
13.8
1.5
6.9
0
0
0
0
0
0
1.5
6.9
F
60.0
240.0
60.0
3.0
13.8
!
E2 Motor Setup
"
E2-01 Motor Rated Current
Setting Range: Model Dependent (see appendix B)
Factory Default: Model Dependent
The Motor Rated Current parameter (E2-01) is necessary information for the Drive motor protection function. The motor overload protection parameter L1-01 is enabled by default. In addition, motor rated current is used by the torque compensation function to insure optimum torque production. Set E2-01 to the full load amps (FLA) value stamped on the motor’s nameplate. During Auto-tuning, it is required for the operator to enter the motor rated current in parameter T1-04 on the
Auto-Tuning menu. If the Auto-tuning operation completes successfully, the value entered into T1-04 will be also written into
E2-01.
For applications employing a Drive that is oversized for the motor, E2-01 may be set as low as 10% of the Drive output current rating. The ampere value in E2-01 however, must always be greater than the “No Load Current” value in parameter E2-03 or an OPE02 error will be displayed.
Programming 5 - 50
"
E2-03 No Load Current
Setting Range: Model Dependent (see appendix B)
Factory Default: Model Dependent
Set E2-03 to the motor no-load current at rated voltage and rated frequency. Consult the motor manufacturer for the proper value if the no load current is not stated on the motor nameplate.
!
F6 Com OPT Setup
(Applies only to the LonWorks
®
option)
"
F6-01 Operation Selection After Communication Error
Setting
0
1
2
3
Description
Ramp to Stop
Coast to Stop
Fast-Stop
Alarm Only (factory default)
If a serial communication option board is attached to the Drive at the 2CN connector, the Drive will automatically monitor the card for any type of communication errors. F6-01 is applicable no matter whether a run command or speed command is coming via the option board, digital operator, or terminal input. The setting of F6-01 determines whether the communication error is seen as a fault or an alarm. If F6-01= “3: Alarm Only”, then the fault output is not energized upon a communication error. All other settings of F6-01 cause the fault output to energize. The setting of F6-01 does not apply to any of the embedded communication protocols used at the RS-485/422 terminals on the removable terminal board. (See parameters H5-0X)
"
F6-02 Option PCB External Fault Detection Selection
Setting
0
1
Description
Always Detected (factory default)
Detected only during operation
"
F6-03 Option PCB External Fault Stopping Method
Setting
0
1
2
3
Description
Ramp to Stop
Coast to Stop (factory default)
Fast-Stop
Alarm Only
If an external fault is received from the LonWorks
® or other communication option card, the settings of F6-02 and F6-03 will determine the Drive operation in reaction to the fault signal. Parameter F6-02 will determine if the external fault is always recognized (F6-02= “0: Always Detected”) or only recognized when the Run command is active (F6-02= “1: Detected only during operation”).
Once the fault is recognized, parameter F6-03 will determine the operation of the Drive. If parameter F6-03 is set to anything other then “3”, the Drive will fault and a stopping sequence is begun. If F6-03= “3: Alarm Only”, then the external fault is treated like an alarm. Operation will continue and an EF0 fault will flash on the digital operator.
Programming 5 - 51
"
F6-05 Current Scaling via Communication Option PCB
Setting
0
1
Description
A Display (factory default)
100%/8192 (Drive Rated Current)
A communication option card can read the Drive’s DPRAM to access the current monitor. The format of the current reading in the DPRAM will be determined by parameter F6-05.
F6-05= “0: A Display” $ Current is a decimal number corresponding to actual Amperes
F6-05= “1: 100%/8192 (Drive Rated Current)” $ Current reading is a number where
8192 = 100% of Drive rated output current
!
H1 Digital Inputs
"
H1-01 Terminal S3 Function Selection
H1-02 Terminal S4 Function Selection
H1-03 Terminal S5 Function Selection
H1-04 Terminal S6 Function Selection
H1-05 Terminal S7 Function Selection
Setting Range: 0 to 6E
Factory Default: H1-01= “70: Bypass Drv Envl” This is one of the special parameter settings required by the Bypass logic circuit. See Table 5.1.
H1-02= This is one of the special parameter settings required by the Bypass logic circuit. See Table 5.2
H1-03= This is one of the special parameter settings required by the Bypass logic circuit. See Table 5.2.
H1-04= “4: Multi-Step Ref 2” (2 Wire)
“3: Multi-Step Ref 1” (3 Wire)
H1-05= “6: Jog Freq Ref ” (2 Wire)
“4: Multi-Step Ref 2” (3 Wire)
Programming 5 - 52
The Drive has five multi-function contact digital inputs. By programming parameters H1-01 through H1-05, the user can assign specific functions to each input. Below is a table with a complete list of all of the digital input functions. The programming manual has a more detailed description of each of the functions.
13
14
15
17
F
10
11
12
18
19
1B
Parameter setting
0
1
4
6
2
3
9
A
C
7
8
Function
3-Wire Control
Local/Remote Selection
Option/Inv Selection 1
Multi-step Reference 1
Multi-step Reference 2
Jog Frequency Reference 1
Multi-Accel/Decel 1
External Baseblock N.O.
External Baseblock N.C.
Accel/Decel Ramp Hold
Terminal A2 Enable
Terminal Not Used
MOP Increase
MOP Decrease
Forward Jog
Reverse Jog
Fault Reset
Fast Stop N.O.
Fast Stop N.C.
Timer Function
PI Disable
Program Lockout
Table 5.12 Digital Input Functions
69
6A
6B
6C
62
64
67
68
6D
6E
70
Parameter setting
1C
1D
1E
20-2F
30
31
34
35
36
60
61
Function
Trim Control Increase
Trim Control Decrease
Reference Sample Hold
External Fault
Integral Reset
Integral Hold
PI Soft Start Cancel
PI Input Characteristic
Option/Inv Selection 2
Motor Pre-heat
Speed Search 1
Speed Search 2
Speed Search 3
Communications Test Mode
High Slip Braking
Jog Frequency Reference 2
Drive Enable (Cycle Run)
Com/Inv Selection
Com/Inv SEL 2
Auto Mode @ Close
Hand Mode @ Close
Drive Enable (Accept Run)
Following are descriptions of only those parameters that are required for Bypass operations and PI control.
"
Function: Multi-step Ref 1
Setting: 3
"
Function: Multi-step Ref 2
Setting: 4
The Drive can be programmed to step through four preset speeds and a jog. It is also possible to mix in the analog inputs as speed references that can be chosen in place of the first and second preset frequency references. The selection of which preset speed will be the active speed command is determined by the status of the digital inputs set for Multi-step Ref 1 (H1-0x= 3) and
Multi-step Ref 2 (H1-0x= 4). Changing the active speed command via the Multi-step References can be done while the Drive is running.
Programming 5 - 53
The following table details which reference is active based on the status of the Multi-step Ref 1 and Multi-step Ref 2 inputs:
Table 5.13 Digital Input Functions
Preset Speed
1
2
3
4
5
Terminal
Programmed as Multi-step
Reference 1
OFF
ON
OFF
ON
-
Terminal
Programmed as Multi-step
Reference 2
OFF
OFF
ON
ON
-
*
The Jog Frequency input is given priority over the multi-step speeds.
Terminal
Programmed as
Jog Reference
OFF
OFF
OFF
OFF
ON*
Details
Frequency Reference 1 (d1-01) or analog input A1
Frequency Reference 2 (d1-02) or analog input A2
Frequency Reference 3 (d1-03)
Frequency Reference 4 (d1-04)
Jog Frequency (d1-17)
The determination of whether the Preset Speed 1 will be the Frequency Reference 1 (d1-01 or the analog input A1) is determined by the status of b1-01. If b1-01= “1: Terminals”, the value of the input to A1 will determine the commanded speed when Preset Speed 1 is selected. If b1-01
≠
1, the setting of d1-01 will determine the commanded speed when Preset Speed 1 is selected.
The determination of Preset Speed 2 is made much the same way as Preset Speed 1 except that the setting of parameter H3-09 decides whether the analog input A2 or d1-02 is Preset Speed 2. If H3-09= “2: Aux Reference”, the value of the input to A2 will determine the commanded speed when Preset Speed 2 is selected. If H3-09
≠
2, the setting of d1-02 will determine the commanded speed when Preset Speed 2 is selected.
"
Function: Fault Reset
Setting: 14
Whenever the Drive detects a fault condition, the fault output contact will close and the Drive’s output will shut OFF causing the motor to coast (specific stopping methods can be selected for some faults such as L1-04 for motor overheat). Once the Run command is removed, the fault can be reset by either the RESET key on the digital operator or by closing a digital input configured as a Fault Reset (H1-0x= 14).
"
Function: PI Disable
Setting: 19
When the PI Function has been enabled by b5-01 (PI Mode Selection), it can be indefinitely disabled by closing a digital input configured as a PI Disable input (H1-0x= 19). When disabled, the Drive operates as a standard Drive that does not have PI enabled.
"
Function: Com/Inv Sel 2
Setting: 6C
The Com/Inv Selection function allows the user to switch the origin of the Run and speed command between the Drive’s terminals and the RS-485/422 port (and the embedded communication protocols) on the removable terminal board. When a digital input is programmed for the Com/Inv Selection function (H1-0x= 6B) that input will function as follows:
Programming 5 - 54
Option/Inv Function Input Status
OPEN
CLOSED
Table 5.14
Run and Speed Command Source
From the control circuit and analog input terminals
From Serial Com port (R+,R-,S+, and S-) (embedded protocols)
To switch the command source between the serial communication port and the control circuit terminals be sure to program the following parameters:
• Set b1-01 (Frequency Reference Selection) to 1 (Terminals).
• Set b1-02 (Run Command Selection) to 1 (Terminals).
• Set H1-0x (Input Terminal Function Selection) to 6B or 6C.
The Com/Inv Sel 2 function will operate the same way except the logic is reversed. When a digital input is programmed for the
Com/Inv Selection function (H1-0x= 6C) that input will function as follows:
Option/Inv Function Input Status
OPEN
CLOSED
Table 5.15
Run and Speed Command Source
From Serial Com port (R+, R-, S+, and S-) (embedded protocols)
From the control circuit and analog input terminals
IMPORTANT
Switching the Reference and Run sources can only be done while the Drive is stopped.
"
Function: Auto Mode Sel
Setting: 6D
"
Function: Hand Mode Sel
Setting: 6E
This effects the speed command (reference) input only. The Auto Mode Selection (H1-0x= 6D) and the Hand Mode Selection
(H1-0x= 6E) allows use of a digital input to toggle between the Auto and Hand operational modes for speed control. The Auto
Mode Selection and Hand Mode Selection cannot both be programmed simultaneously. If both 6D and 6E are programmed together, an OPE03 fault will occur.
The 6D setting for digital input defines the speed command (or setpoint) source as the keypad/operator for an open contact and allows b1-01 to determine the speed command source for a closed contact. Setting 6D has no effect on the run command.
Input Contact Status
OPEN
CLOSED
Speed Command or PI Setpoint Source
Keypad/operator (override b1-01)
Determined by b1-01
Programming 5 - 55
The 6E setting for digital input defines the speed command (or setpoint) source as the keypad/operator for an closed contact and allows b1-01 to determine the speed command source for a open contact.
Input Contact Status
OPEN
CLOSED
Speed Command or PI Setpoint Source
Determined by b1-01
Keypad/operator (overrides b1-01)
Programming 5 - 56
!
H2 Digital Outputs
"
H2-01 Terminal M1-M2 Function Selection
H2-02 Terminal M3-M4 Function Selection
Setting Range: 0 to 3B
Factory Default: H2-01= “0: During Run 1”
H2-02= “3B: Run Src Com/Opt”
H2-02 is one of the special parameter settings required by the Bypass logic circuit. See Table 5.1.
The Drive has two multi-function outputs. By programming parameters H2-01 and H2-02, the user can assign specific functions to each output. Below is a table with a complete list of all of the digital output functions. Refer to the Programming
Manual for a more detailed description of each of the functions.
Parameter setting
0
1
2
3
9
A
B
7
8
C
E
4
5
6
Table 5.16 Digital Output Functions
Function
During Run1
Zero Speed
F
REF
/F
OUT
Agree 1
F
REF
/Set Agree 1
Frequency Detect 1
Frequency Detect 2
Drive Ready
DC Bus Undervoltage
Baseblock 1
Option Reference
Remote Operation
Torque Detect 1 N.O.
Loss of Reference
Fault
Parameter
Setting
F
10
11
12
1F
20
38
39
3A
3B
17
1A
1E
Function
Terminal Not Used
Minor Fault
Reset Cmd Active
Timer Output
Torque Detect 1 N.C.
Reverse Direction
Restart Enabled
Overload (OL1)
OH Pre-alarm
Drive Enable
Drive Waiting
Frequency Reduced, OH
Run from Serial Com
Programming 5 - 57
!
H3 Analog Inputs
"
H3-02 Terminal A1 Gain Setting
Setting Range: 0.0 to 1000.0%
Factory Default: 100.0%
H3-02 is one of the special parameter settings required by the Bypass logic circuit, depending on the options provided. See
Table 5.2.
The addition of another input signal on terminal A1 to the Drive and Bypass unit, after shipment to the job site, would be the only reason for changing this parameter.
For example, in variable air volume AHUs with a “volume matching” control strategy, P1 differential control is employed with feedback signals connected to both terminals A1 and A2.
"
H3-03 Terminal A1 Bias Setting
Setting Range: -100.0% to +100.0%
Factory Default: 0.0%
In order to have the Drive properly interpret an analog input, it may be necessary to apply a gain and/or a bias to the signal.
The analog inputs have a resolution of 10 bits (1024 steps). Using the factory default settings for the analog input’s gain and bias, the 0-10Vdc or 4-20mA signal at the analog input will yield a 0-100% speed command span.
Gain = 100%
Bias = 0%
0V
4mA
10V
20mA
Fig 5.24 Output Frequency as Commanded Via Analog Input
If a different span of analog input signal is desirable, it will be necessary to adjust the gain, the bias, or both to allow the analog input level to generate the desired frequency command. Adjustment of the gain setting will change the speed command that is equivalent to the maximum analog input (10Vdc or 20mA). If, for instance, the gain is increased to 200%, then 10Vdc or
20mA will be equivalent to a 200% speed command and 5 VAC or 12mA will be equivalent to a 100% Speed Command.
Since the Drive output is limited by the maximum frequency parameter (E1-04), 0-5Vdc or 4-12mA will now be equivalent to
0-100% speed command span.
Programming 5 - 58
Gain =200%
100%
Bias = 0%
0V
4mA
5V
12mA
10V
20mA
Fig 5.25 Output Frequency as Commanded via Analog Input with Increased Gain Setting
Adjustment of the bias setting will likewise adjust the speed command that is equivalent to the minimum analog input level
(0Vdc or 4mA). If, for instance, the bias is set to –25%, then 0Vdc or 4mA will be equivalent to a –25% speed command.
Since the minimum speed command is 0% an analog input of 2.5 to10Vdc or 8 to 20mA will now be equivalent to 0-100% speed command span.
Gain = 100%
0V
4mA
Bias = -25%
2.5V
8mA
10V
20mA
Fig 5.26 Output Frequency with Reduced Bias Setting
As a further example, for an inverse-acting speed command, set the bias= 100% and the gain= 0%. The minimum analog input level (0Vdc or 4mA) will produce a 100% speed command and the maximum analog input level (10Vdc or 20mA) will produce a 0% speed command.
0V
4mA
10V
20mA
Analog Input Signal
Analog Input Level
Fig 5.27 Output Frequency with Inverted Gain and Bias Settings
Programming 5 - 59
"
H3-08 Terminal A2 Signal Level
Setting
0
2
0 - 10VDC
4 - 20mA (Default)
Description
H3-08 is one of the special parameter settings required by the Bypass logic circuit. See Table 5.2.
The H3-08 parameter (Terminal A2 Signal Level) allows the programmer to specify the signal that will be applied to the A2 analog input. The A2 analog input can accept either a 0–10 Vdc or 4-20 mA signal as a reference. The Drive also has a DIP switch (S1) on the removable terminal board that must be set for the proper reference signal into the A2 analog input. The
S1-2 dipswitch setting determines the internal resistance of the A2 input while parameter H3-08 determines how the Drive interprets the measured signal.
O
S1
1
1
2
Terminating resistance
DIP Switch S1-1 located on terminal board.
Fig 5.28 DIP Switch S1
Name
S1-1
S1-2
Table 5.17 DIP Switch S1
Function
RS-485 and RS-422 terminating resistance
Input method for analog input A2
Setting
OFF: No terminating resistance (Factory default)
ON: Terminating resistance of 110
Ω
OFF: 0 to 10 V (internal resistance: 20 k
Ω
)
ON: 4 to 20 mA (internal resistance: 250
Ω
) (Factory default)
Programming 5 - 60
"
H3-09 Terminal A2 Function Selection
H3-09 is one of the special parameter settings required by the Bypass logic circuit. See Table 5.2.
Setting
0
2
B
D
E
16
1F
Frequency Bias
Aux Reference
PI Feedback
Frequency Bias 2
Motor Temperature
PI Differential
Not Used
Description
The A2 analog input can be programmed to perform many different functions. The setting of parameter H3-09 determines which of the following functions the A2 analog input will perform.
Function: Aux Reference
Setting: 2
In order for the A2 analog input to be used as the master Speed Command, parameter H3-09 must be set for Aux Reference
(H3-09= “2: Aux Reference”). Once A2 is configured as an auxiliary reference, it can be selected as the master Speed
Command by setting H3-13= “1: Main Fref TA2”. If H3-09= 2, terminal A2 analog input will become the speed command when a digital input programmed for Multi-Step Ref 1 (H1-0x= 3) is selected by a contact closure.
Function: PI Feedback
Setting: B
Configuring the A2 analog input as PI Feedback (H3-09= “B: PI Feedback”) is a requirement of setting the Drive up for PI operation. The A2 analog input is the only source for feedback for PI operation though the setpoint can come from a number of different sources (refer to the section covering the PI parameters for more information regarding specifying the setpoint source. PI parameters are listed in section b5).
Parameters H3-10 (Terminal A2 Gain) and H3-11 (Terminal A2 Bias) can be used to configure the A2 analog input to match the signal from the Feedback Transmitter.
The U1-24 monitor (PI Feedback) can be used to check the PI Feedback level with the digital operator.
Function: PI Differential
Setting: 16
Normal PI operation will adjust the Drive output in order to match the measured feedback value to a desired setpoint. When PI is operated in the differential mode, however, the Drive output is adjusted in order to maintain a desired differential between two feedback signals.
When the A2 analog input is configured as a PI Differential (H3-09= “16: PI Differential”), the A1 analog input becomes the other PI Differential input. The desired differential is set by parameter b5-07 (PI Differential Setpoint) and can be set so that
A2 is held less than A1 (b5-07 <0) or A2 is held greater than A1 (b5-07>0).
When PI Differential operation is chosen, the A1 feedback level can be monitored by U1-24 (PI Feedback) and the A2 feedback level can be monitored by U1-53 (PI Feedback2).
Programming 5 - 61
"
H3-10 Terminal A2 Gain Setting
Setting Range: 0.0 to 1000.0%
Factory Default: 100.0%
"
H3-11 Terminal A2 Bias Setting
Setting Range: -100.0% to +100.0%
Factory Default: 0.0%
Parameters H3-10 and H3-11 perform the same function for the A2 analog input that parameters H3-02 and H3-03 perform for the A1 analog input. Please refer to the parameter description for H3-02 and H3-03 for information about H3-10 and
H3-11.
These parameters could be used for final calibration of a factory or field installed pressure to electric transducer input connected to terminal A2 and AC. This field calibration may be needed if there is a job site variation from the typical 3 to 15
PSIG pneumatic signal input range.
"
H3-12 Analog Input Filter Time Constant
Setting Range: 0.0 to 2.00 Seconds
Factory Default: 0.30 Seconds
An analog input filter can be used to prevent erratic Drive control when a “noisy” analog reference is used. Parameter H3-12 sets the time constant for a first order filter that will be applied to both the A1 and A2 analog inputs. The Drive operation becomes more stable the longer the time programmed, but it becomes less responsive to rapidly changing analog signals.
Analog
Input
Filter
Noisy input signal
Fig 5.29 Analog Input Filter Time Constant Effect on “Noisy” Signal
Programming 5 - 62
"
H3-13 Master Frequency Reference Terminal Selection
Setting
0
1
Description
Main Fref= A1 (factory default)
Main Fref= A2
H3-13 is one of the special parameter settings required by the Bypass logic circuit. See Table 5.2.
Parameter H3-13 allows the programmer to select which analog input will serve as the Speed Command input when “Terminals” are selected as the Auto Mode Speed source (b1-01= “1: Terminals”), or Terminal is selected as the reference source for the Hand mode (b1-12= “1: Terminals”). For the A2 analog input to be an effective selection for the H3-13 parameter, parameter H3-09 must be configured as Aux Reference (H3-09= “2: Aux Reference”).
If H3-09
≠
2, then the A1 analog input will be used regardless of the setting of parameter b1-12.
Programming 5 - 63
!
L2 Momentary Power Loss Ride-thru Function
When momentary power loss recovery is enabled (L2-01
≠0), a speed search is executed to catch the potentially spinning motor shaft. This speed search will occur regardless of the setting of b3-01 “Speed Search Selection”.
"
L2-01 Momentary Power Loss Detection Selection
Setting
0
1
2
Description
Disabled
PwrL Ride Thru t
CPU Power Active (factory default)
"
L2-02 Momentary Power Loss Ride-Thru Time
Setting Range: 0.0 to 25.5 Seconds
Factory Default: Model Dependent
The Drive allows different responses to momentary power losses. The setting of L2-01 determines whether the Drive attempts to restart after a short loss of incoming AC power and for what length of time this capability remains active.
If L2-01= “0: Disabled”, the Drive detects a UV1 fault 15ms after power loss and automatic restarting is disabled. The Drive cannot restart until the external run command is removed and the UV1 fault is reset.
If L2-01= “1: PwrL Ride Thru t”, the Drive restarts without the UV1 fault if power is returned within the time specified in
L2-02, the Momentary Power Loss Ride-thru Time. During the power loss but before the fault trip, the digital operator will display a UV alarm. If L2-02 is set for a time longer than the control power supply can be sustained, a UV1 fault will not occur and the Drive restarts upon the return of AC power. The time that the control power supply can be maintained varies with
Drive size. The larger the Drive, the greater the potential ride-thru time.
If L2-01= “2: CPU Power Active”, the Drive ignores L2-02 and attempts a restart as long as the control power supply is still able to maintain a minimal voltage level. In effect, setting L2-01= “2: CPU Power Active” (factory default) is programming the Drive for maximum Power Loss Ride-thru. An equivalent setting is L2-01= “1: PwrL Ride Thru t”, with L2-02 set to a time longer than the control power supply can be maintained after power is lost.
Note:
The run command must be held during power loss for any power loss ride-thru capability to be possible. It is for this reason that 3-wire control is not recommended for use with the Momentary Power Loss function.
Programming 5 - 64
!
L3 Stall Prevention
"
L3-01 Stall Prevention Selection During Accel
Setting
0
1
2
Description
Disabled
General Purpose (factory default)
Intelligent
"
L3-02 Stall Prevention Level During Accel
Setting Range: 0 to 200% of Drive rated output current
Factory Default: 120% of Drive rated output current
The stall prevention during acceleration function adjusts the acceleration time in order to prevent OC fault trips during acceleration. If L3-01= “0: Disabled”, stall prevention is disabled. If the load is large enough and the acceleration time short enough the Drive may fault and stop.
If L3-01= “1: General Purpose”, then the standard stall prevention function is enabled. When the output current exceeds the level set by the L3-02 parameter, the Drive will discontinue accelerating and maintain speed. If, during acceleration, the output current comes within 15% of the level set by parameter L3-02, the acceleration time is lengthened. Once the output current level has dropped below the L3-02 level, acceleration will begin again with the acceleration rate reaching the programmed rate once again 15% below the L3-02 level.
-15%
Stall level during acceleration
Output Current
Time
Output frequency
Output frequency is controlled to prevent the motor stalling.
Time
Fig 5.30 Detailed Time Chart for Stall Prevention During Acceleration
If L3-01= “2: Intelligent”, the intelligent stall prevention is enabled. The active acceleration time is ignored and the Drive will attempt to accelerate as quickly as possible without exceeding the L3-02 output current level.
IMPORTANT
Stall Prevention during Acceleration is not effective when the output frequency is less than 6Hz.
Programming 5 - 65
The following figure demonstrates acceleration when L3-01= “1: General Purpose”.
Output
Frequency a - Set accel time b - Accel time is extended
t
L3-02
Output
Current
Fig 5.31 Time Chart for Stall Prevention During Acceleration
The L3-02 parameter is set as a percentage of the Drive rated output current. If the motor capacity is small compared to the
Drive’s capacity, or if the motor stalls during acceleration, lower the set value of L3-02.
"
L3-04 Stall Prevention Selection During Decel
Setting
0
1
2
3
Description
Disabled
General Purpose (factory default)
Intelligent
Stall prev w/R
The stall prevention during deceleration function adjusts the deceleration time in order to prevent OV fault trips during deceleration. If L3-04= “0: Disabled”, stall prevention is disabled and if the load is large and the deceleration time short enough the Drive may fault and stop.
If L3-04= “1: General Purpose”, then the standard stall prevention function is enabled. If, during deceleration, the DC Bus voltage exceeds the stall prevention level (see table below), the Drive will discontinue decelerating and maintain speed. Once the DC Bus voltage has dropped below the stall prevention level, the deceleration will continue down to the Speed Command level. See figure below.
480 VAC
Table 5.18 Stall Prevention During Decel
Drive Voltage
240 VAC
E1-01
≥
400 VAC
E1-01
<
400 VAC
Stall Prevention Level during Deceleration
(V)
380
760
660
If L3-01= “2: Intelligent”, the intelligent stall prevention is enabled. The active deceleration time is ignored and the Drive will attempt to decelerate as quickly as possible without causing the DC Bus voltage to exceed the stall prevention level.
The following figure demonstrates acceleration when L3-04= “1 General Purpose”.
Programming 5 - 66
a - Set decel time b - Decel time is extended
Output
Frequency
DC Bus
Voltage
t
a b
380/660/760 Vdc
t
TIME
Fig 5.32 Time Chart for Stall Prevention During Deceleration
"
L3-05 Stall Prevention Selection During Running
Setting
0
1
2
Description
Disabled
Decel Time 1 (factory default)
Decel Time 2
"
L3-06 Stall Prevention Level During Running
Setting Range: 30 to 200% of Drive rated output current
Factory Default: 120% of Drive rated output current
The Stall Prevention During Running function will attempt to avoid a Drive OC fault occurrence while the Drive is operating at a constant speed. If L3-05= “0: Disabled”, the Drive may fault if the load increases sufficiently to cause the output current to reach the OC fault level (180% of Drive rated output current).
If L3-05= “1: General Purpose”, the Drive is outputting a constant speed, and the Drive’s output current level exceeds the level set by parameter L3-06 for more than 100 ms the Drive will begin to decelerate at the rate specified by parameter C1-02. The
Drive will continue to decelerate until the output current level drops below the L3-06 level (less a 2% hysteresis). Once the output current drops below the L3-06 – 2% level the Drive will begin to accelerate at the currently active acceleration rate
(either C1-01 or C1-03).
If L3-05= “2: Decel Time 2”, the Drive will function as described above except C1-04 will be used instead of C1-02 as the deceleration rate used when the output current exceeds L3-06 for more than 100 ms.
The following figure demonstrates acceleration when L3-05
≠
0.
Output
Frequency a
- Decel time
C1-02 or C1-04.
C1-02 or C1-04 b
– Active accel time b - Active Accel time
t
a a b b
Output
Current
L3-06
t
TIME
Fig 5.33 Time Chart for Stall Prevention Level During Running
The L3-06 parameter is set as a percentage of the Drive rated output current. If the Drive still faults when L3-05
≠
0, then either lower the L3-06 or adjust the C1-02 or C1-04 settings for a quicker deceleration.
Programming 5 - 67
!
L4 Speed Command Loss Detection
"
L4-05 Frequency Reference Loss Detection Selection
Setting
0
1
Description
Disabled (factory default)
Enabled @ % of PrevRef
"
L4-06 Frequency Reference at Loss of Frequency Reference
Setting Range: 0.0 to 100.0% of previous speed command
Factory Default: 80.0% of previous speed command
The Drive can be configured to compensate for the loss of its external speed command. An external speed command is considered lost if it drops 90% of its value in 400mS or less.
100%
Frequency
Reference
T
10%
t
T = 400mS
Output
Frequency
Fig 5.34 Loss of Frequency Reference Timing Diagram
TIME
L4-06
t
To enable Frequency loss detection, set L4-05= “1: Enabled @ % of PrevRef”. If Frequency Reference Loss Detection is enabled and the reference is lost, the Drive continues to operate at the speed commanded by parameter L4-06. When the speed command returns, the Drive again follows the speed command.
Setting H2-01/H2-02= “C: Loss of Ref”, configures a digital output as a Frequency Reference Loss indication only when
L4-05= “1: Enabled @ % of PrevRef”.
Programming 5 - 68
!
L5 Fault Restart
"
L5-01 Number of Auto Restart Attempts
Setting Range: 0 to 10
Factory Default: 10
"
L5-02 Auto Restart Operation Selection
Setting
0
1
Description
No Flt Relay (factory default)
Flt Relay Active
"
L5-03 Maximum Restart Time After Fault
Setting Range: 0.5 to 600.0 Seconds
Factory Default: 600.0 Seconds
All major faults will cause the Drive to stop. For some faults it is possible to configure the Drive to attempt a restart automatically. After the fault occurs, the Drive baseblocks for L2-03 seconds. After the baseblock is removed the Drive checks if a fault condition still exists. If no fault condition exists the Drive will attempt to restart the motor. If the restart is successful, the Drive performs a Speed Search (Regardless of the status of b3-01 “Speed Search Selection”) from the set speed command and the Auto Restart Attempts count is increased by one. Even if the restart fails the restart count is increased by one as long as the Drive attempted to rotate the motor. The restart count will not be incremented if the restart is not attempted due to a continuing fault condition (i.e. an OV fault). The Drive waits L5-03 seconds before attempting another restart.
Run t
OV
OC
OC
Fault
Attempts trying each
L5-03 seconds successful try but failed successful t
L2-03 L2-03 L2-03 t
1
2
3
Count
Voltage remains high for a long time, then reset (1) and run
Drive trips on OC, resets (2) and tries again but motor still shorted, trips again.
OC condition gone, resets (3) and runs.
Fig 5.35 Automatic Restart Timing Diagram
The auto restart count is reset back to 0 if any of the following occur:
• No further faults for ten minutes after the last retry.
• The Drives power is turned off (the Drive must be without power long enough to let control power dissipate).
• The SHIFT/RESET key is pushed after the last reset attempt.
Programming 5 - 69
The setting of parameter L5-02 determines whether the fault output (MA-MB) will be closed during an auto restart attempt.
The setting of L5-02 can be important when interfacing the Drive with other equipment.
The following faults will allow the Auto Restart function to initiate:
• OC (Overcurrent)
• LF (Output Open Phase)
• PF (Input Phase Loss)
• PUF (DC Bus Fuse)
• OL1 (Motor Overload)
• OL3 (Overtorque)
• OL2 (Drive Overload)
• OV (DC Bus Overvoltage)
• GF (Ground Fault)
• UV1 (DC Bus Undervoltage)
• OH1 (Overheat)
In order for auto restart after a UV1 fault, Momentary Power Loss Ride-thru must be enabled (L2-01= “1: PwrL Ride Thru t”, or “2: CPU Power Active”). Setting H2-01 or H2-02 equal to “1E” configures a digital output as “Restart Enabled” to signal if an impending auto restart is possible.
Programming 5 - 70
!
L6 Torque Detection
"
L6-01 Torque Detection Selection 1
Setting
0
1
4
5
2
3
6
7
8
Description
Disabled (factory default)
OL@SpdAgree - Alm
OL At Run -Alm
OL@SpdAgree - Flt
OL At Run - Flt
UL@SpdAgree - Alm
UL at Run - Alm
UL@SpdAgree - Flt
UL At Run - Flt
"
L6-02 Torque Detection Level 1
Setting Range: 0 to 300% of Drive rated output current
Factory Default: 15% of Drive rated output current
"
L6-03 Torque Detection Time 1
Setting Range: 0.0 to 10.0 Seconds
Factory Default: 10.0 Seconds
The Drive can be programmed to indicate when either an overtorque or an undertorque conditions exist. A digital output must be programmed for “Torque Detection”, (H2-01/H2-02= “B: Trq Det 1 N.O.” or “17: Trq Det 1 N.C.). A warning of an overtorque condition can indicate a jam and an undertorque condition can indicate a broken belt, no water in a pump, or other loss of load.
To configure Torque Detection requires the following decisions:
1.
Do you wish to check for an overtorque condition or an undertorque condition?
2.
Do you wish to check for the torque condition whenever the Drive is running or only at speed agree? Nuisance detection during acceleration, when variable torques are normally required, can be avoided.
3.
Do you want the Drive to fault if the torque condition is detected or only alarm and continue operation?
The following table can help choose the proper setting for Torque Detection Selection 1 to get the wanted results.
Table 5.19 L6-01 Setting Choices
L6-01
Setting
Overtorque Undertorque
6
7
4
5*
8
2
3
0
1 X
X
X
X
X
X
X
X
*Suggested settings for Loss of Load indication
Fault Alarm
Torque Detection Disabled
X
X
X
X
X
X
Always
Detected
X
X
X
X
Only Detected @
Spd Agree
X
X
X
X
Programming 5 - 71
After selecting the proper detection scheme the Torque Detection Level (L6-02) must be specified. If the current level read by the output current transformers rises above (overtorque) or drops below (undertorque) this level, and remains there for at least the Torque Detection Time (L6-03), then the Torque Detection Function will change the state of any digital output configured for Torque Detection (H2-01/H2-02= “B: Trq Det 1 N.O.”, or “17: Trq Det 1 N.C.”).
*
*
Torque detection level -10%
L6-03 t
L6-03
CLOSED
TIME
Closed
Open
* When the output current drops below the Torque Detection Level by
approximately 10% of the Drive’s rated output current the digital output is reset.
Fig 5.36 Over Torque Detection
*
Torque detection level 10%
*
L6-02 t
L6-03
L6-03
Closed
TIME
* When the output current rises above the Torque Detection Level by
approximately 10% of the Drive’s rated output current the digital output is reset.
Fig 5.37 Under Torque Detection
Programming 5 - 72
!
L8 Hardware Protection
"
L8-01 Internal Dynamic Braking Resistor Protection Selection
Setting
0
1
Description
Not Provided (factory default)
Provided
This parameter is not applicable for Drive operation.
"
L8-02 Overheat Pre-Alarm Level
Setting Range: 50 to 130 o
C
Factory Default: 95 o
C
"
L8-03 Overheat Pre-Alarm Operation Selection
Setting
0
1
2
3
4
Description
Ramp to Stop (Decel Time C1-02)
Coast to Stop
Fast-Stop (Decel Time C1-09)
Alarm Only
OH Alarm and Reduce (factory default)
The Drive is capable of warning the operator of an impending heatsink over-temperature fault via an OH pre-alarm. The level at which the pre-alarm will activate is determined by the setting of parameter L8-02. Measurement of the heatsink temperature is done with several strategically mounted thermistors. If any of the heatsink thermistors measure a temperature in excess of the setting of
L8-02, the Drive will fault (OH2) and either: ramp to stop using the C1-02 deceleration rate (L8-03= “0: Ramp to Stop”), coast to stop (L8-03= “1: Coast to Stop”), ramp to stop using the C1-09 fast stop deceleration rate (L8-03= “2: Fast-Stop”), alarm (OH) and continue running (L8-03 = “3: Alarm Only”), alarm (OH) and continue running but at a reduced speed (L8-03= “4: Alarm &
Reduce”). If L8-03= 4: Alarm and Reduce, the Drive will continue to run but will reduce the speed to the level determined by parameter L8-19. Refer to the description for parameter L8-19.
If a digital output is configured for OH Prealarm (H2-01= “20: OH PreAlarm”), it will close whenever the heatsink temperature is greater than the L8-02 level no matter what the setting is of L8-03.
"
L8-10 Heatsink Cooling Fan Operation Selection
Setting
0
1
Description
Fan On-Run Mode (factory default)
Fan Always On
Programming 5 - 73
"
L8-11 Heatsink Cooling Fan Operation Delay Time
Setting Range: 0 to 300 Seconds
Factory Default: 300 Seconds
Parameters L8-10 and L8-11 allow the Drive programmer to customize the heatsink cooling fan operation. Parameter L8-10 determines whether the cooling fans are always ON whenever the Drive is powered (L8-10= “1: Fan Always On”) or if the cooling fans are only ON when the Drive is in a Run condition (L8-10= “0: Fan On-Run Mode”).
Parameter L8-11 is a delayed OFF for the cooling fan if L8-10= “0: Fan On-Run Mode”. When the cooling fans are set to turn
OFF when the Run command is removed, parameter L8-11 will cause the fans to continue cooling the Drive for the amount of time programmed into L8-11 after the Run command is actually removed. The Drive can be programmed to allow the cooling fan to run for up to 5 minutes (factory default) after the run command is removed.
Both parameters are intended to extend fan life while still providing sufficient cooling for proper Drive operation.
Run
Command
ON (CLOSED) t
Heatsink Fan
RUN
L8-11
TIME
ON (CLOSED) t
Fig 5.38 Heatsink Cooling Fan Operation Timing Diagram
"
L8-19 Overheat Frequency Reference Reduction Level
Setting Range: 0.0 to 100.0% of maximum frequency
Factory Default: 20.0% of maximum frequency
When the heatsink temperature reaches the OH Pre-alarm level (L8-02) and the Overheat Pre-Alarm Operation Selection parameter is set for Alarm and Reduce (L8-03= “4: OH Alarm & Reduce”), the L8-19 parameter sets the amount of speed decrease that will be applied to the Speed Command in order to lower the heatsink temperature. The decrease in speed will lower the current being switched and conducted by the heat producing output transistors of the Drive.
Parameter L8-19 is set in percentage of maximum frequency (E1-04).
Programming 5 - 74
!
o1 Monitor Configuration
"
o1-01 User Monitor Selection
Setting Range: 6 to 53
Factory Default: 6
34
36
37
38
20
24
28
39
40
51
52
53
Setting
6
7
8
10
11
12
13
14
15
16
18
Description
Output Voltage (factory default)
DC Bus Voltage
Output Power
Input Terminal Status
Output Terminal Status
Drive Operation Status
Cumulative Operation Time
Software Number
Terminal A1 Input Voltage
Terminal A2 Input Voltage
Motor Secondary Current (I q
)
Output Frequency After Soft Start
PI Feedback Value
CPU Number
First Parameter Causing an OPE
PI Input
PI Output
PI Setpoint
Memobus Communication Error Code
Heatsink Cooling Fan Operation Time
Auto Mode Frequency Reference Value
Hand Mode Frequency Reference Value
PI Feedback 2 Value
Programming 5 - 75
"
o1-02 Power-On Monitor
Setting
1
2
3
4
Description
Frequency Reference (factory default)
Output Frequency
Output Current
User Monitor (set by o1-01)
When the Drive is powered up, three monitors are displayed on the digital operator. The first and largest monitor is the
“Power-On” monitor. The factory default “Power-On monitor” is Speed Command (U1-01). Below the Speed Command monitor are the next two sequential monitors, Output Frequency (U1-02) and Output Current (U1-03). Pressing the
INCREASE key once scrolls the monitors to show the User Monitor as selected by o1-01. The factory default for o1-01 is the
Output Voltage monitor (U1-06).
The active monitor displayed when the Drive is powered on can be changed to either be U1-01 (Speed Command), U1-02
(Output Frequency), U1-03 (Output Current), or the User Monitor. Whichever monitor is selected as the Power-On top monitor, the two monitors displayed below it are the next two sequential monitors. See example below.
Active Monitor
Active Monitor Title
Output Frequency
Output Current
Next two sequential monitors
For example, if the Drive needs to display the Elapsed Timer as the Power-On monitor, then o1-01 must be set to “13” and o1-02 must be set to “4”. The next time Drive power is cycled, the digital operator displays U1-13 (Elapsed Time), U1-14
(Flash ID), and U1-15 (Term AI Level).
Active Monitor
-DRIVE- Rdy
Elapsed Time
U1-13= 2
H
- - - - - - - - - - - - - - - - - - - - - - - - - - - - -
U1-14= 03010
U1-16= 51.2%
Flash ID
Term AI Level
Active Monitor Title
Next two sequential monitors
Programming 5 - 76
"
o1-03 Digital Operator Display Scaling
Setting
0
1
2 - 39
40 - 39999
Description
Hz (factory default)
%
RPM (Enter the # of Motor Poles)
User Display
Parameter o1-03 allows the programmer to change the units in which the speed monitors and some speed parameters are displayed. The o1-03 parameter will change the units of the following:
• U1-01 (Frequency Reference Monitor)
• U1-02 (Output Frequency Monitor)
• U1-20 (Output Frequency after Soft Start)
• d1-01 through d1-17 (Preset Frequency References and Jog Reference)
The table below details how the setting of o1-03 will affect the way the listed monitors and parameters will be displayed.
Table 5.20 Display Scaling
If o1-03 is:
0
1
The frequency format is
0.01 Hz
0.00%
2 through 39
(enter the # of motor poles)
0 RPM
40 through 39999 Engineering Units
The factory default setting (o1-03= “0”) sets the Drive up to display the affected monitors and parameters in terms of hertz
(Hz).
If the speeds seem more natural in terms of percentage of maximum, set o1-03= “1”. If the speeds are easier to work with when displaying the equivalent synchronous motor RPM, set o1-03= [the number of motor poles]. If another engineered unit, such as fpm or gpm, is desired, set o1-03= xxxx where:
X X X X X
Digit 5 Digit 4 Digit 3 Digit 2 Digit 1
Digits 1 through 4 set the desired number to be displayed at 100% speed.
Digit 5 determines the number of decimal places in the displayed number.
If Digit 5 = 0 number format is XXXX
If Digit 5 = 1 number format is XXX.X
If Digit 5 = 2 number format is XX.XX
If Digit 5 = 3 number format is X.XXX
For example:
If o1-03= 10425, then at full speed the digital operator will display “42.5”. Configuring parameter o1-03 for displaying in terms of an engineering unit is only appropriate if the actual display units have a linear relationship with the actual output speed.
Programming 5 - 77
"
o1-05 LCD Contrast Adjustment
Setting Range: 0 to 5
Factory Default: 3
The contrast setting of the LCD display of the digital operator can be adjusted by the setting of parameter o1-05. The higher the number programmed into o1-05, the darker the background will become. Set o1-05 to the value that makes the LCD the easiest to view at the normal viewing distance and angle.
"
o1-06 User Monitor Selection Mode
Setting
0
1
Description
3 Mon Sequential (factory default)
3 Mon Selectable
"
o1-07 Second Line User Monitor
Setting Range: 1 to 53
Factory Default: 2
"
o1-08 Third Line User Monitor
Setting Range: 1 to 53
Factory Default: 3
Normally the monitors shown directly below the active monitor are the next two sequential monitors. If o1-06 (User Monitor
Selection Mode) is set to “1: 3 Mon Selectable”, those two monitors are locked as specified by parameters o1-07 and o1-08 and will not change as the top parameter is scrolled with the INCREASE and DECREASE keys.
Active Monitor
-DRIVE- Rdy
PI Feedback
U1-24= 64.55%
- - - - - - - - - - - - - - - - - - - - - - - - - - - - -
U1-37= 0.00%
U1-38= 2.50%
PI Output
PI Setpoint
Active Monitor Title
For Example:
The Display above showing PI Feedback, PI Output and PI Setpoint would be useful when setting up a PI Control Loop.
Programming 5 - 78
!
o2 Key Selections
"
o2-03 User Parameter Default Value
Setting
0
1
2
No Change
Set Defaults
Clear All
Description
The Drive gives the option of configuring any and all of the programming parameters and then saving the parameters as “User
Initialization Values”. After configuring the Drive, set parameter o2-03= “1: Set Defaults”, to save the parameters to a User
Initialization memory location. Once this has been done, the “Initialize Parameters” parameter (A1-03) will offer the choice of
“1110:User Initialize”. Choosing A1-03= “1110: User Initialized”, will reset all modified parameters back to what they were the last time they were saved using o2-03.
The choice of setting A1-03= “1110: User Initialized”, is unavailable until first setting the User Initialization parameters using o2-03. Once a User Initialization is set (saved), it can be cleared by setting o2-03= “2: Clear All”. After clearing the User
Initialization parameters, the choice of “1110: User Initialize” is no longer a available in A1-03.
"
o2-05 Frequency Reference Setting Method Selection
Setting
0
1
Description
Disabled
Enabled (factory default)
The factory default setting of the Frequency Reference Setting Method parameter (o2-05= “1: Enabled”) dictates that when setting a Speed Command via the digital operator (“Hand” mode), it is not necessary to press the DATA/ENTER key before the Drive will begin to accelerate or decelerate to the new set speed. This is referred to as MOP (Motor Operated
Potentiometer) type functionality. When o2-05= “1: Enabled”, the speed command is stored to memory 5 seconds after the
INCREASE or DECREASE keys are released.
When o2-05= “0: Disabled”, the digital operator INCREASE and DECREASE keys will change the speed command but the
Drive will not accelerate or decelerate to the new speed command until the DATA/ENTER key is pressed. In order to change the Speed Command in the HAND mode, U1-01 must be the top monitor and then the ENTER key must be pressed in order to access the Speed Command function. This in not to be confused with pressing the ENTER key in order to achieve a change in speed using the INCREASE and DECREASE keys, which is the subject of parameter o2-05.
Programming 5 - 79
"
o2-06 Operation Selection when Digital Operator is Disconnected
Setting
0
1
Description
Disabled
Enabled (factory default)
Leaving o2-06 enabled will cause the Drive to fault, when the digital operator is removed, even if it’s not outputting to the motor. The reset key on the digital operator will need to be pressed after reconnecting the digital operator to reset the fault and continue normal operation.
If o2-06 = “0: Disabled” then the Drive will not fault if the digital operator is disconnected, but the Drive will discontinue motor operation. If full Drive operation is required while the digital operator is removed set o2-06 = “0: Disabled” and o2-15 = “0: Disabled” (Hand Key Function). If both o2-06 and o2-15 are disabled then the digital operator can be disconnected without disturbing Drive operation.
"
o2-07 Cumulative Operating Time Setting
Setting Range: 0 to 65535 Hours
Factory Default: 0 Hours
"
o2-08 Cumulative Operation Time Selection
Setting
0
1
Description
Power-On Time
Running Time (factory default)
The Drive features an Elapsed Timer monitor that records in units of hours. The Elapsed Timer monitor is U1-13. Parameter o2-08 programs this function to either accumulate elapsed hours based on time the Drive is powered (o2-08= “0: Power-On
Time”) or time the Drive is running (o2-08= “1: Running Time”). The Drive is considered “running” anytime there is an active run command or when the Drive is outputting voltage (i.e. including during deceleration).
-DRIVE- Rdy
Elapsed Time
U1-13= 0H
- - - - - - - - - - - - - - - - - - - - - - - - - - - - -
U1-14= 03010
U1-15= 34.1%
Parameter o2-07 allows manual adjustment of the Elapsed Timer, primarily to accommodate maintenance or control board replacement in the event of damage. To reset the Elapsed Timer back to zero, set o2-07= 0.
Programming 5 - 80
"
o2-10 Cumulative Cooling Fan Operation Time Setting
Setting Range: 0 to 65535 Hours
Factory Default: 0 Hours
The elapsed time of heatsink cooling fan operation is tracked by the U1-40 monitor. Much like the o2-07 parameter can be used to adjust or reset the Drive operation elapsed timer, parameter o2-10 can be used to adjust the time displayed by the
U1-40 monitor in the event of fan replacement.
-DRIVE- Rdy
FAN Elapsed Time
U1-40= 152H
- - - - - - - - - - - - - - - - - - - - - - - - - - - - -
U1-51= 52.33%
U1-52= 57.60%
"
o2-12 Fault Trace / Fault History Clear Function
Setting
0
1
Description
Disabled (No Effect) (factory default)
Enabled
The operator can clear the Fault Trace (U2) and Fault History logs by setting o2-12= “1: Enabled”. Clearing the Fault Trace and Fault History logs erases all the information.
"
o2-14 kWh User Monitor Initialization
Setting
0
1
Description
Disabled (No Change) (factory default)
Clear All
The kWh monitors (U1-29 and U1-30) track the power usage of the Drive and are not reset by powering down the Drive. To reset the monitors back to zero, set o2-14= “1: Clear all”.
Programming 5 - 81
!
o3 Digital Operator Copy Function
"
o3-01 Copy Function Selection
The membrane over the Drive keypad also makes the keypad non-removable on Bypass units. In order to use the keypad copy function on a Bypass unit - order a separate keypad, part number CDR001115 and obtain locally a standard CAT 5
Ethernet cable.
Note: The copy function is disabled when serial communication is active.
Setting
0
1
2
3
Description
COPY SELECT (factory default)
INV
→
OP READ
OP
→
INV WRITE
OP
↔
INV VERIFY
"
o3-02 Read Allowed Selection
Setting
0
1
Description
Disabled
Enabled (factory default)
The digital operator has parameter COPY capabilities via built in non-volatile memory. The digital operator can READ all of the parameters in the Drive and store them for later WRITE back to the Drive or into a Drive with the same product code and software number. In order to read the parameter values and store them in the digital operator, select o3-02= “1: Enabled”. If you attempt to READ the data, which overwrites any previously stored data, without first setting o3-02= “1: Enabled”, you will get the following error:
-ADV-
PRE
READ IMPOSSIBLE
After setting o3-02= “1: Enabled”, it is possible to store parameter values in the digital operator by setting o3-01=1
(INV
→
OP READ).
A successful READ of the parameter values will display:
-ADV-
READ
READ COMPLETE
Programming 5 - 82
An error may occur while saving the parameter values to the digital operator’s memory. If an error is displayed, press any key to cancel the error display and return to parameter o3-01. To COPY parameter values into a Drive, set o3-01= “2: OP->INV
WRITE”. During the writing of the parameter values into the Drive the digital operator will display:
-ADV-
COPY
OP
→
INV COPYING
A successful COPY of the parameter values will display:
-ADV-
COPY
COPY COMPLETE
An error may occur while writing the parameter values to the Drive. If an error is displayed, press any key to cancel the error display and return to parameter o3-01.
It is possible to compare the parameter values stored in the digital operator with the parameter values currently in the Drive by using the VERIFY function. This VERIFY function should not be confused with the “-VERIFY-“ that is displayed on the digital operator when viewing the “Modified Constants” menu. To VERIFY the parameter values in the Drive as compared with those stored in the digital operator, set o3-01= “3: OP<-->INV VERIFY”. During the comparing of the parameter values into the Drive the digital operator will display:
-ADV-
VERIFY
DATA VERIFYING
A successful VERIFY of the parameter values will display:
-ADV-
VERIFY
VERIFY COMPLETE
Programming 5 - 83
If all the parameter values stored in the digital operator do not match those programmed in the Drive, the digital operator displays the following:
-ADV-
VYE
VERIFY ERROR
The digital operator will not display which parameters did not match, only that the verification found discrepancies in some parameter values.
NOTE:
In order to properly use the COPY or VERIFY functions, the following Drive specifications must be identical between the Drive that the parameters were read from and the Drive that the parameters are to be written to:
• Model Number (e.g. CIMR-P7U2015)
• Software Number (e.g. 1010 also known as FLASH ID)
Yaskawa offers DriveWizard™ software that can also READ, COPY, and VERIFY Drive parameter values. DriveWizard™ lists all discrepancies between the Drive and a pre-saved parameter file when verifying is performed.
To use
DriveWizard first select o2-15= “0: Disabled” and select o2-06= “0: Disabled” then remove the digital operator/keypad and attach the DriveWizard cable in its place.
Programming 5 - 84
!
T1 Auto-Tuning
Auto-Tuning can only be accomplished through the DriveWizard software. Available by download from www.drives.com.
"
T1-02 Motor Rated Power
Setting Range: 0.00 to 650.00 kW
Factory Default: Model Dependent
"
T1-04 Motor Rated Current
Setting Range: Model Dependent
Factory Default: Model Dependent
Auto tuning is recommended to achieve optimum performance. In addition, the Drive requires Line-To-Line Resistance auto-tuning before it can properly perform the Estimated Speed Search method. This method of speed search allows for bi-directional speed search. The T1 parameters are found under the Auto-Tuning menu.
"
Auto-Tuning Using DriveWizard
DriveWizard is a PC software program designed to provide the tools necessary to handle Drive installation as well as parameter record keeping and maintenance. As such it provides an Auto-Tuning method for Drives in Bypass units. The
Auto-Tuning function “tunes” the Drive setup to the characteristics of the specific motor to which it is applied. Auto-Tuning is essential if bi-directional Speed Search is required and enabled for the application.
DriveWizard can be obtained either through CD or www.Drives.com. Follow the installation procedures provided with the software.
With the DriveWizard software loaded onto a PC, connect a standard CAT 5 Ethernet cable from the PC’s RS-232 port (with a
DB-9 to CAT 5 adaptor) to the digital operator/keypad port on the Drive. Before disconnecting the digital operator/keypad from the Drive, set parameter o2-06 (“Oper Detection”) to “0:disabled”. This will allow the Drive to continue running with the digital operator/keypad removed.
Start DriveWizard and setup the PC communications by setting the appropriate communications port and Baud rate. Typical settings are Com Port 1 and 9600 Baud.
Once the communications port is set, connect to the Drive by clicking on the pull-down menu “Inverter” and selecting
“Connect.” [This can also be done by typing Ctrl+C on your keyboard, or by clicking on the yellow icon resembling two puzzle pieces.] This will upload all of the current parameters in the Drive to the computer as a working parameter file.
At this point the parameters can be saved as a backup file if desired. [DriveWizard is a third method of saving the complete parameter list and user settings. In addition to the “User Parameters” (o2-03) and “Keypad Copy” (o3-01) functions discussed in this chapter, DriveWizard can be employed to maintain a downloadable list of the Drive parameter set up on a PC, for backup or transfer to other drives.]
Auto-Tuning is performed by selecting the Auto-Tuning function from the “Inverter” pull-down menu. DriveWizard will ask you to verify that the motor is in a safe operating condition, and then ask you to enter two parameters. DriveWizard will ask you to fill in parameters T1-02 “Mtr Rated Power” and T1-04 “Rated Current”. After this data has been entered, click on the
“Load” button to enter these values into the Drive memory. The “Start” button will become available, click on “Start” to begin the auto-tuning process. While Auto-Tuning is running the Drive output current and frequency will be displayed, the flashing green light indicates DriveWizard is communicating with the Drive. When complete, DriveWizard will have auto-tuned the
Drive, adjusted several motor related parameters and the Drive will be ready for optimum performance for bi-directional Speed
Search and other functions.
Programming 5 - 85
Notes:
Programming 5 - 86
Chapter 6
Diagnostics & Troubleshooting
This chapter describes diagnostics and troubleshooting for the Drive.
Bypass Diagnostics ........................................................................ 2
Troubleshooting the Bypass Printed Circuit Boards .................. 2
Drive Diagnostics ........................................................................... 3
Fault Detection .......................................................................... 4
Alarm Detection ....................................................................... 10
Operator Programming Errors (OPE) ...................................... 13
Auto-Tuning Faults .................................................................. 14
Digital Operator COPY Function Faults ................................... 15
Drive Troubleshooting .................................................................. 16
If Parameter Cannot Be Set .................................................... 16
If the Motor Does Not Operate ................................................ 17
The Direction of the Motor Rotation is Reversed ..................... 18
If the Motor Does Not Put Out Torque or
If Acceleration is Slow ............................................................. 18
If the Motor Operates at a Higher Speed
Than the Speed Command ...................................................... 18
If the Motor Overheats ............................................................. 19
If Peripheral Devices Like PLCs or Others are Influenced by
Starting or Running Drive ......................................................... 19
If the Ground Fault Interrupter Operates When the Drive is Run ....................................................................... 20
If There is Mechanical Vibration .............................................. 20
If the Motor Rotates Even When Drive Output is Stopped ....... 21
If Zero Volts is Detected When a Motor is Started, or Stalls .... 21
If Output Frequency Does Not Rise to Frequency Reference . 21
Drive Main Circuit Test Procedure ................................................ 22
Drive Date Stamp Information ...................................................... 26
Diagnostic & Troubleshooting 6 - 1
Bypass Diagnostics
!
Troubleshooting the Bypass Printed Circuit Boards
In order to check the two circuit boards (PCB A2 and A3 on the schematic diagram in Chapter 2) based on the following table, it is assumed that they are assembled and wired in the unit and all the Bypass functions were working properly prior to the fault.
11
12
13
14
2
3
No.
1
4
5
8
9
6
7
10
Fault Description Possible Cause Corrective Procedure
No lights, some/no contactors pick up
No. 1 but fuses are not blown
No. 2 but power has no problem
No. 3 but Operator (A3) board and ribbon cable OK
Power light on, contactors do not pick up
No. 5 but fuses are not blown
No. 6 but TB1 connections are secure
No. 7 but wiring and contactors OK
Contactor/blowers pick up with delay
Some options do not work anymore
Any light off but functions are right
User functions on TB1 terminals 7 to 16 faulty
Auto/Remote/Purge
Functions faulty
Drive/Damper Solenoid does not operate
Control circuit fuses are blown
Power/wiring is disrupted to cabinet and/or transformer
The Ribbon cable and/or Operator
(A3) board are faulty
The wiring to Relay (A2) board is loose/Relay board faulty
Control circuit fuses are blown
Check for any short circuits before replacing the fuses
Check the power to the control transformer/cabinet
Check for the cause/shorting before ordering replacement
Inspect the wiring/connectors to relay board before ordering replacement
Check for any short circuits/wiring before replacing the fuses
User connections to TB1 are disrupted
The contactors/wiring are faulty/disrupted
The wiring to Relay (A2) board is loose/Relay board faulty
Bad connection/relays, loose circuit boards
Loose wiring/connectors on Relay
(A2) and/or Operator (A3) boards
Inspect connections to TB1
Inspect contactors and check the power at the contactor
Inspect the wiring/connectors to relay
(A2) board before ordering replacement
Check TB1 wiring/PCB ribbon cable sockets before ordering replacement
Inspect the Relay (A2) board wiring/connectors/jumpers
Bad light module, loose Operator
(A3) board/cable
Bad user wiring, shorting to TB1 terminals, bad relays
Loose wiring on TB1, bad switches of Relay (A2) board
Loose wiring on Drive terminals, incomplete TB1 connections
Read 8-12 VAC voltage on Operator board light pins before ordering replacement
Check the wiring and terminals on TB1 before ordering replacement
Inspect wiring/Relay board switches,
TB1 inputs before ordering replacement
Inspect Drive wiring, TB1 connections
Diagnostic & Troubleshooting 6 - 2
Drive Diagnostics
Drives Technical Support in USA and Canada
Technical Support for Inverters and Drives is available by phone as follows:
Normal: Monday through Friday during the hours of 8 a.m. to 5:00 p.m. C.S.T.
Emergency: After normal hours, 7 days a week including weekends and holidays
To contact Drives Technical Support, please call 1-800-YASKAWA (927-5292).
From the menu, dial 2 for Inverter and Drive Products, then 5 for Technical Support.
Drives Technical Support can also be reached by e-mail at [email protected]
.
Support information, such as technical manuals, FAQs, instruction sheets and software downloads are available at our website, www.drives.com
.
When calling for technical support, please have the following materials available:
•
The appropriate Technical Manual in hand because the support associate may refer to this.
•
Complete nameplate information from the Drive and the motor.
(Confirm that Drive Nameplate Output amps is equal to or greater than Motor Nameplate amps)
• Α list with your parameter settings.
•
A sketch of the electrical power train, from AC line to motor, including filters and disconnects.
Field Service, Start Up Assistance, Factory Repair, Replacement Parts, and Other Support
Contact Drives Technical Support for help with any of these needs.
Technical Training
Training is conducted at Yaskawa training centers, at customer sites, and via the internet.
For information, visit www.drives.com
or call 1-800-YASKAWA (927-5292).
From the phone menu, dial 2 for Inverter and Drive Products, then 4 for Product Training.
Support in Other Countries
Yaskawa is a multi-national company with offices and service representation around the world.
To obtain support, always contact the local distributor first for guidance and assistance.
Contact the closest Yaskawa office listed for further assistance.
Diagnostic & Troubleshooting 6 - 3
!
Fault Detection
When the Drive detects a fault, the fault information is displayed on the digital operator, the fault contact closes, and the motor coasts to stop. (However, a fault with selectable stopping method will operate according to the stopping method selected.)
• If a fault occurs, take appropriate action according to the table by investigating the cause.
• To restart, reset the fault with any of the following procedures:
• Turn ON the fault reset signal.
• Set “14: Fault Reset” to a multi-function digital input (H1-01 to H1-05).
• Press the RESET key of the digital operator.
• Shut off the Drive input power once, and then turn on again.
WARNING
The Run Command (Start Command) needs to be removed prior to resetting a fault. Resetting a fault by removing and reapplying power to the Drive while the Run Command is applied, may cause the Drive to start unexpectedly. Therefore, make sure all personnel are clear from the Drive, motor, and machine prior to resetting the Drive.
Table 6.1 Fault Displays and Processing
Digital
Operator Display
Description Cause
BUS
Option Com Err
CE
Memobus Com Err
Option Communication Error
After initial communication was established, the connection was lost.
Modbus Communication Error
Control data was not received correctly for two seconds.
CPF00
COM-ERR(OP&INV)
Operator Communication Fault 1
Transmission between the Drive and the digital operator cannot be established within 5 seconds after supplying power.
Connection is broken, master has stopped communicating.
Connection is broken, master has stopped communicating.
Digital operator cable not securely connected, digital operator defective, control board defective.
..
CPF01
COM-ERR(OP&INV)
CPF02
BB Circuit Err
CPF03
EEPROM Error
External RAM of CPU is defective.
Operator Communication Fault 2
After communication started with the digital operator, a communication fault occurred for 2 seconds or more.
Baseblock Circuit Fault
Baseblock circuit fault at power-up
EEPROM Fault
EEPROM fault, check sum not valid
Control circuit damage.
Digital operator cable not securely connected, digital operator defective, control board defective.
Gate array hardware failure during power-up.
Noise or spike on the control circuit input terminals.
Corrective Action
Check all connections, verify all user-side software configurations.
Check all connections, verify all user-side software configurations.
Remove the digital operator once and then reinstall it.
Cycle power off and on to the
Drive.
Replace the Drive.
Remove the digital operator once and then reinstall it.
Cycle power off and on to the
Drive.
Replace the Drive.
Perform a factory initialization.
Cycle power off and on to the
Drive.
Replace the control board.
Perform a factory initialization
Cycle power off and on to the
Drive.
Replace the control board.
Diagnostic & Troubleshooting 6 - 4
Table 6.1 Fault Displays and Processing
Digital
Operator Display
Description Cause Corrective Action
CPF04
Internal A/D Err
CPF05
External A/D Err
CPF07
RAM-Err
CPF08
WAT-Err
CPF09
CPU-Err
CPU Internal A/D Converter Fault
CPU External A/D Converter Fault
ASIC Internal RAM Fault
(RAM)
Watchdog Timer Fault
(WAT)
CPU-ASIC Mutual Diagnosis Fault
(COY)
Noise or spike on the control circuit input terminals.
Perform a factory initialization.
Cycle power off and on to the
Drive.
Replace the control board.
Perform a factory initialization.
Noise or spike on the control circuit input terminals.
Cycle power off and on to the
Drive.
Replace the control board.
- - -
Control circuit damage
- - -
Control circuit damage
- - -
Control circuit damage
Cycle power off and on to the
Drive.
Replace the Drive.
Cycle power off and on to the
Drive.
Replace the Drive.
Cycle power off and on to the
Drive.
Replace the Drive.
CPF10
ASIC-Err
ASIC Version Fault
(ASIC)
Control circuit damage Replace the Drive.
CPF20
Option A/D Error
CPF21
Option CPU Down
CPF22
Option Type Err
Option Card Fault
Option card connector connection fault.
Option card A/D converter fault.
Remove all inputs to the option board.
Perform a factory initialization.
Cycle power off and on to the
Drive.
Replace the option board.
Replace the Control board.
Self-diagnosis Fault of Communication
Option Card
Communication Option Card Code Number
Fault
Noise or spike on the communication line, defective option board.
Perform a factory initialization.
Cycle power off and on to the
Drive.
Replace the option board.
Unrecognizable option board is connected to the control board.
Replace the control board.
Remove any option boards.
Cycle power off and on to the
Drive.
Perform a factory initialization.
Replace the option board.
Replace the control board.
Diagnostic & Troubleshooting 6 - 5
Table 6.1 Fault Displays and Processing
Digital
Operator Display
Description Cause Corrective Action
CPF23
Option DPRAM Err
EF0
Opt External Flt
Communication Option Card
Interconnection Fault
Communication Option Card External Fault
Remove power to the Drive.
An option board is not correctly connected to the control board or an option board that is not made for the Drive is attached to the control board.
Connect the option board once more.
Perform a factory initialization.
Cycle power off and on to the
Drive.
Replace the option board.
An external fault condition exists.
Replace the control board.
Check for an external condition.
Verify the parameters.
Verify communication signal.
EF3
Ext Fault S3
EF4
Ext Fault S4
EF5
Ext Fault S5
EF6
Ext Fault S6
EF7
Ext Fault S7
External Fault at Terminal S3
External Fault at Terminal S4
External Fault at Terminal S5
External Fault at Terminal S6
An external fault condition exists connected to a multifunction digital input.
Eliminate the cause of an external fault condition.
FBL
Feedback Loss
GF
Ground Fault
External Fault at Terminal S7
PI Feedback Loss
This fault occurs when PI Feedback Loss
Detection is programmed to fault.
(b5-12 = 2) and the
PI Feedback < PI Feedback Loss Detection
Level (b5-13) for the PI Feedback Loss
Detection Time (b5-14).
Remove the fault from a multifunction digital input.
PI Feedback source
(e.g. transducer, sensor, building automation signal) is not installed correctly or is not working.
Verify Drive is programmed to receive the PI Feedback source signal.
Check to ensure the PI Feedback source is installed and working properly.
Output Ground Fault
Drive output grounding current has exceeded 50% of the Drive rated output current.
Motor lead is shorted to ground, DCCT defective.
Remove the motor and run the
Drive without the motor.
Check the motor for a phase to ground short.
Check the output current with a clamp on meter to verify the
DCCT reading.
Diagnostic & Troubleshooting 6 - 6
Table 6.1 Fault Displays and Processing
Digital
Operator Display
Description Cause Corrective Action
OC
Over Current
OH1
Heatsnk MAX Temp
OH3
Motor Overheat 1
OH4
Motor Overheat 2
OL1
Motor Overloaded
OL2
Inv Overloaded
Overcurrent
Drive output current exceeded the overcurrent detection level (approximately
180% of Drive rated output current).
Cooling Fin/Cooling Fin Fan Overheat
The temperature of the Drive cooling fin exceeded the temperature programmed in parameter L8-02.
Drive Internal Cooling Fan
Motor Overheating Alarm
The Drive stops or continues operation according to the setting of L1-03.
Motor Overheating Fault
The Drive stops operation according to the setting of L1-04.
Motor Overload
Designed to protect the motor
Fully adjustable from parameter E2-01
Drive Overload
Designed to protect the Drive
Shorted Drive output phase to phase, shorted motor, locked rotor, load too heavy, accel/ decel time too short, contactor on the Drive output is opened and closed, a special motor or a motor with a FLA rating larger than Drive rated output current.
Remove the motor and run the
Drive without the motor.
Check the motor for a phase-tophase short.
Check the Drive for a phase-tophase short at the output.
Verify C1-01 and C1-02 are set correctly.
Check load conditions.
Cooling fan(s) are not working, high ambient temperature, a heat source is too close to the Drive.
Check for dirt build-up on the fans and cooling fins.
Reduce the ambient temperature around the Drive.
Remove the heating unit.
Recheck the cycle time and the size of the load.
Overheating of motor as measured by motor thermistor.
Recheck the accel/decel time
(C1-01 and C1-02).
Recheck the V/F pattern (E1-01 thru E1-13).
Recheck the motor rated current value (E2-01).
Recheck the cycle time and the size of the load.
Overheating of motor as measured by motor thermistor.
Recheck the accel/decel time
(C1-01 and C1-02).
Recheck the V/F pattern (E1-01 thru E1-13).
Recheck the motor rated current value (E2-01).
The load is too large. The cycle time is too short at the accel/decel time.
Recheck the cycle time and the size of the load as well as the times set in C1-01 and C1-02.
The voltage of the V/F pattern is high.
Review the V/F pattern parameters, E1-01 thru E1-13.
Motor rated current setting is improper.
The load is too large. The cycle time is too short at the accel/decel time.
Check the motor rated current value in E2-01.
Recheck the cycle time and the size of the load as well as the times set in C1-01 and C1-02.
The voltage of the V/F pattern is high.
Review the V/F pattern parameters, E1-01 thru E1-13.
The size of the Drive is small.
Change to a larger size Drive.
Diagnostic & Troubleshooting 6 - 7
Table 6.1 Fault Displays and Processing
Digital
Operator Display
Description Cause Corrective Action
OL3
Overtorque Det 1
OPR
Oper Disconnect
OV
DC Bus Overvolt
PF
Input Pha Loss
PUF
DC Bus Fuse Open
RH
DynBrk Resistor
Overtorque Detection 1
Drive output current > L6-02 for more than the time set in L6-03
Motor is overloaded.
Ensure the values in L6-02 and
L6-03 are appropriate.
Check application/machine status to eliminate fault.
Digital Operator Connection Fault
The Drive will stop if the digital operator is removed when the Drive is commanded to run through the digital operator.
The digital operator is not attached or the digital operator connector is broken.
High input voltage at R/L1,
S/L2 and T/L3.
Attach the digital operator.
Check the digital operator connector.
Verify the setting of o2-06.
Check the input circuit and reduce the input power to within specifications.
DC Bus Overvoltage
208-240VAC: Trip point is
480VAC: Trip point is
≥
≥
400Vdc
800Vdc
The deceleration time is set too short.
Power factor correction capacitors are being used on the input to the Drive.
Extend the time in C1-02.
Remove the power factor correction capacitors.
Open phase on the input of the
Drive.
Check the input voltage.
Loose terminal screws at
R/L1, S/L2 or T/L3.
Input Phase Loss
Drive input power supply has an open phase or has a large imbalance of input voltage.
Momentary power loss occurred.
Input voltage fluctuation too large.
Tighten the terminal screws.
Check the input voltage.
Check the input voltage.
DC Bus Fuse
Detects if the DC bus fuse has opened
Dynamic Braking Resistor
The protection of the dynamic braking resistor based on setting of L8-01
Parameter L8-06 value is set incorrectly.
Shorted output transistor(s) or terminals.
Adjust L8-06 according to your application. The higher the value the less sensitive it becomes.
Remove power from the Drive.
Disconnect the motor.
Perform the checks without power in Table 6.6.
Replace the shorted component(s).
Replace the defective fuse.
Overhauling load, extended dynamic braking duty cycle, defective dynamic braking resistor.
Verify dynamic braking duty cycle.
Monitor DC bus voltage.
Replace dynamic braking resistor.
Diagnostic & Troubleshooting 6 - 8
Table 6.1 Fault Displays and Processing
Digital
Operator Display
Description Cause Corrective Action
RR
DynBrk Transistr
UL3
Undertorq Det 1
UV1
DC Bus Undervolt
UV2
CTL PS Undervolt
UV3
MC Answerback
Dynamic Braking Transistor
The dynamic braking transistor failed.
Undertorque Detection 1
Drive output current < L6-02 for more than the time set in L6-03
DC Bus Undervoltage
The DC bus voltage is
≤
L2-05
208-240VAC: Trip point is
≤
190Vdc
480VAC: Trip point is
≤
380Vdc
Control Power Supply Undervoltage
Undervoltage of the control circuit when running.
Soft Charge Circuit Fault
The pre-charge contactor opened while the
Drive was running.
Shorted dynamic braking transistor, high DC bus voltage, defective dynamic braking resistor.
Motor is underloaded.
Cycle power off and on to the
Drive.
Replace defective dynamic braking transistor or resistor.
..
Monitor DC bus voltage.
Ensure the values in L6-02 and
L6-03 are appropriate.
Check application/machine status to eliminate fault.
Low input voltage at R/L1,
S/L2 and T/L3
Check the input circuit and increase the input power to within specifications.
The acceleration time is set too short.
Extend the time in C1-01.
Voltage fluctuation of the input power is too large.
Check the input voltage.
Cycle power off and on to the
Drive.
External load connected pulling down the Drive power supplies.
Repair or replace the Power PCB/
Gate Drive PCB.
Remove all control wiring and test Drive.
Contacts on the soft charge contactor are dirty and the soft charge contactor does not function mechanically.
Cycle power off and on to the
Drive.
Check the condition of the soft charge contactor.
Repair or replace the Power PCB/
Gate Drive PCB.
WARNING
Some features within the PI function group cause the Drive to shut down momentarily (e.g. Sleep Function,
Snooze Function, Feedback Loss feature etc.) Upon recovery from the conditions that activate these features, the Drive may start unexpectedly. Therefore, when enabling these features take appropriate measures to notify personnel working with this equipment that unexpected starting may occur.
Diagnostic & Troubleshooting 6 - 9
!
Alarm Detection
Alarms are Drive protection functions that does not operate the fault contact. The Drive will automatically return to its original status once the cause of the alarm has been removed.
During an alarm condition, the Digital Operator display flashes and an alarm output is generated at the multi-function outputs
(H2-01 to H2-02) if programmed.
When an alarm occurs, take appropriate corrective action according to the table below.
Table 6.2 Alarm Displays and Processing
Digital
Operator Display
Description Cause Corrective Action
BUS
Option Com Err
Option Communication Error
After initial communication was established, the connection was lost.
Connection is broken, master has stopped communicating.
Check all connections, verify all user side software configurations.
CALL
SI-F/G ComCall
EF
External Fault
EF0
Opt External Flt
(Flashing)
Serial communication transmission error
Communication has not yet been established.
Connection not made properly, user software not configured to the proper baud rate or configuration.
Check all connections, verify all user side software configurations.
Both the forward and the reverse run commands are input simultaneously for 500mS or more. This alarm stops the motor.
An external forward and reverse command are input simultaneously.
Check external sequence logic.
Communication Option Card External Fault
An external fault condition exists.
Check for an external condition.
Verify the parameters.
Verify communication signal.
EF3
Ext Fault S3
(Flashing)
EF4
Ext Fault S4
(Flashing)
EF5
Ext Fault S5
(Flashing)
EF6
Ext Fault S6
(Flashing)
EF7
Ext Fault S7
(Flashing)
DNE
Drive not Enable
(Flashing)
External Fault at Terminal S3
External Fault at Terminal S4
External Fault at Terminal S5
External Fault at Terminal S6
External Fault at Terminal S7
The Drive does not have the enable command when the run command is applied.
An external fault condition exists connected to a multi-function digital input.
The Run command has been applied prior to the enable signal.
Eliminate the cause of an external fault condition.
Remove the fault from a multifunction digital input.
Apply the enable command before applying the run command.
Diagnostic & Troubleshooting 6 - 10
Table 6.2 Alarm Displays and Processing (Continued)
Digital
Operator Display
Description Cause Corrective Action
FBL
Feedback Loss
PI Feedback Loss
This fault occurs when PI Feedback Loss
Detection is programmed to fault.
(b5-12 = 2) and the
PI Feedback < PI Feedback Loss Detection
Level (b5-13) for the PI Feedback Loss
Detection Time (b5-14)
PI Feedback source
(e.g. transducer, sensor, building automation signal) is not installed correctly or is not working.
Verify Drive is programmed to receive the PI Feedback source signal.
Check to ensure the PI Feedback source is installed and working properly.
Check the motor for a phase-tophase short.
Check the Drive for a phase-to phase short at the output.
OH
Heatsnk Overtemp
(Flashing)
Cooling Fin/Cooling Fin Fan Overheat
The temperature of the Drive cooling fin exceeded the temperature programmed in parameter L8-02.
Drive Internal Cooling Fan
OH2
Over Heat 2
(Flashing)
Cooling fan(s) are not working, high ambient temperature, a heating unit in close proximity to Drive is present.
Verify C1-01 and C1-02 are set correctly.
Check load conditions.
Check for dirt build-up on the fans and cooling fins.
Reduce the ambient temperature around the Drive.
Remove the heating unit.
Drive overheat pre-alarm signal is input from a multi-function digital input terminal.
An external overheat condition exists connected to one of the multi-function input terminals
S3, S4, S5, S6 or S7.
Check for an external condition.
Verify the program parameters
H1-01 thru H1-05.
OH3
Motor Overheat 1
(Flashing)
Motor Overheating Alarm
The Drive stops or continues operation according to the setting of L1-03.
Overheating of motor
Recheck the cycle time and the size of the load.
Recheck the accel/decel time
(C1-01 and C1-02).
Recheck the V/F pattern (E1-01 thru E1-13).
Recheck the motor rated current value (E2-01).
Check the digital operator connector.
Verify the setting of o2-06.
Diagnostic & Troubleshooting 6 - 11
Table 6.2 Alarm Displays and Processing (Continued)
Digital
Operator Display
Description Cause Corrective Action
OV
DC Bus Overvolt
(Flashing)
UL3
Undertorq Det 1
(Flashing)
UV
DC Bus Undervolt
(Flashing)
UV2
CTL PS Undervolt
UV3
MC Answerback
High input voltage at R/L1,
S/L2 and T/L3.
Check the input circuit and reduce the input power to within specifications.
DC Bus Overvoltage
208-240VAC: Trip point is
≥
400Vdc
480VAC: Trip point is
≥
800Vdc
The deceleration time is set too short.
Extend the time in C1-02.
Undertorque Detection 1
Drive output current < L6-02 for more than the time set in L6-03
Power factor correction capacitors are being used on the input to the Drive.
Remove the power factor correction capacitors.
Motor is underloaded.
Ensure the values in
L6-02 and L6-03 are appropriate.
Check application/machine status to eliminate fault.
Low input voltage at R/L1, S/L2 and T/L3.
Check the input circuit and increase the input power to within specifications.
DC Bus Undervoltage
The DC bus voltage is
≤
L2-05
208-240VAC: Trip point is
≤
190Vdc
480VAC: Trip point is
≤
380Vdc
The acceleration time is set too short.
Voltage fluctuation of the input power is too large.
Extend the time in C1-01.
Check the input voltage.
Control Power Supply Undervoltage of the control circuit when running
External load connected pulling down the Drive power supplies.
Cycle power off and on to the
Drive.
Repair or replace the Power PCB/
Gate Drive PCB.
Soft Charge Circuit Fault
The pre-charge contactor opened while the
Drive was running.
Contacts on the soft charge contactor are dirty and the soft charge contactor does not function mechanically.
Cycle power off and on to the
Drive.
Check the condition of the soft charge contactor.
Diagnostic & Troubleshooting 6 - 12
!
Operator Programming Errors (OPE)
An Operator Programming Error (OPE) occurs when an inapplicable parameter is set or an individual parameter setting is inappropriate.
The Drive does not operate until the parameter is set correctly. (Alarm output and fault contact do not operate.)
If an OPE occurs, change the appropriate parameter by checking the cause shown in Table 6.3.
Table 6.3 OPE Error and Fault Displays
Digital Operator
Display
Description Cause
Corrective
Action
OPE01 kVA Selection t
OPE02
Limit
OPE03
Terminal
Drive kVA setting error
Constant data out of range
Multi-function input selection fault
The control board was replaced and the kVA parameter is set incorrectly.
Parameter set above the allowable range
Enter the correct kVA setting (o2-04) by referring to the Drive model number in Appendix B.
Verify the program settings.
Duplicate functions are selected, up/down commands or trim control increase/decrease are not set simultaneously. Speed search from maximum frequency and set frequency are set simultaneously.
Verify program settings
(H1-01~H1-05).
OPE05
Sequence Select
OPE10
V/f Ptrn Setting
Run command is selected through serial communication at 2CN but option board is not installed.
V/f data setting fault
Serial communication option board is not installed, option board is installed incorrectly. The run command selection parameter
B1-02 is set to 3 and option board is not installed.
Verify that the board is installed.
Remove power to the Drive and connect the option board once more.
V/f parameter settings are not set correctly.
Check parameters (E1-04 ~ E1-11).
A minimum frequency/voltage value may be set higher than the maximum frequency/voltage.
OPE11
CarrFrq/On-Delay
Carrier frequency data setting fault
Carrier frequency proportional gain
C6-05 > 6 and C6-04 > C6-03.
Upper/lower limit error of C6-03 to
5.0kHz
Parameter setting incorrect.
ERR
EEPROM R/W Err It does not match at EEPROM write.
• Power supply is turned OFF.
• Parameter is reset repeatedly.
Check the program settings and correct the errors.
• Cycle power off and on to Drive.
• Do a factory initialization (A1-03).
Diagnostic & Troubleshooting 6 - 13
!
Auto-Tuning Faults
Auto-tuning faults are shown below. When the following faults are detected, the fault is displayed on the digital operator and the motor coasts to a stop during operation. The fault contact is not activated.
Digital Operator Display
Table 6.4 Auto-Tuning Displays and Processing
Probable Cause
Er - 01
Fault
Er - 02
Minor Fault
Er - 03
STOP key
Er - 04
Resistance
Er - 12
I-det. Circuit
Er - 13
Leakage Inductance Fault
End - 3
Data Invalid
Corrective Action
• There is an error in the data input for autotuning.
• There is an error in the relationship between the motor output and the motor rated current.
• Check input data.
• Check Drive and motor capacity.
• Check motor rated current.
A minor fault is detected during auto-tuning.
• Check input data.
• Check wirings and around the machine.
• Check the load.
The STOP key is pressed during auto-tuning, and the auto-tuning is interrupted.
–
Auto-tuning is not completed within the specified time.
The auto-tuning result became other than the parameter set range.
• Check input data.
• Check motor wiring.
• If a motor and a machine are connected, disconnect the motor from the machine.
• Current flow exceeded the motor rated current.
• Current detection value symbol was reversed.
• Any of U/TI, V/T2, and W/T3 has open-phase.
• Check current detection circuit, wiring and mounting procedure.
Auto-tuning did not finish within the set time.
Tuning result became other than the parameter setting range.
• Check motor wiring.
Rated current set value is set too high.
• Check input data (especially, motor output current and motor rated current value).
Diagnostic & Troubleshooting 6 - 14
!
Digital Operator COPY Function Faults
These faults can occur occurred during the operator COPY function. Fault content is displayed on the operator. An error during the COPY function does not activate the fault contact output or alarm output.
Function
READ
Function
COPY
Function
Verify
Function
Table 6.5 Digital Operator COPY Function Faults
Digital Operator Display Probable Causes
PRE
READ IMPOSSIBLE
IFE
READ DATA ERROR
RDE
DATA ERROR
CPE
ID UNMATCHED
VAE
INV. KVA UNMATCH
CRE
CONTROL UNMATCHED
CYE
COPY ERROR
CSE
SUM CHECK ERROR
VYE
VERIFY ERROR
Corrective Action o3-01 was set to 1 to write a parameter when the Digital Operator was write-protected (o3-02 = 0).
Set o3-02 to 1 to enable writing parameters with the Digital Operator.
The read data length does not agree.
The write data is incorrect.
• Repeat the Read.
• Check the Digital Operator cable.
• Replace digital operator.
An attempted write of a parameter to
EEPROM on the Digital Operator failed.
• A low Inverter voltage has been detected.
• Repeat the read.
• Replace Digital Operator.
The Drive product code or software number is different.
Use COPY function for the same product code and software number.
The capacity of the Drive being copied and the capacity in the Digital Operator are different.
Use COPY function for the same Drive capacity.
The control method of the Drive being copied and the control method in the
Digital Operator are different.
Use the COPY function for the same control method.
The parameter written to the Drive was compared with the parameter in the Digital
Operator and they were different.
COPY retest.
The checksum in the Drive parameter area was compared with the checksum in the
Digital Operator parameter area and they were different.
Retry the copy.
The set value of the digital operator and the
Drive do not match.
Retry Verify function.
After COPY is retested, verify it is retested.
Diagnostic & Troubleshooting 6 - 15
Drive Troubleshooting
Due to parameter setting errors, faulty wiring, etc., the Drive and motor may not operate as expected when the system is started up. If this occurs, use this section as a reference and apply the appropriate measures.
If a fault is displayed on the digital operator, refer to Fault Detection, Table 6.1.
!
If Parameter Cannot Be Set
Use the following information if a Drive parameter cannot be set.
"
The display does not change when the INCREASE and DECREASE keys are pressed.
The following causes are possible.
The Drive is operating (Drive mode).
There are some parameters that cannot be set during operation. Remove the run command and then set the parameters.
Parameter write enable is input.
This occurs when "parameter write enable" (set value: 1B) is set for a multi-function digital input terminal (H1-01 to H1-05).
If the parameter write enable input is OFF, the parameters cannot be changed. Turn it ON and then set the parameters.
Passwords do not match. (Only when a password is set.)
If the parameter A1-04 (Password) and A1-05 (Password Setting) numbers are different, the parameters for the initialize mode cannot be changed. Enter the correct password in A1-04.
If you cannot remember the password, display A1-05 (Password Setting) by pressing the Shift/Reset Key and the MENU Key simultaneously while in the A1-04 display. Reset the password and input the reset password in parameter A1-04.
"
OPE01 through OPE11 is displayed.
The set value for the parameter is wrong. Refer to Operator Programming Errors in this chapter and correct the setting.
"
CPF00 or CPF01 is displayed.
This is a Digital Operator communications error. The connection between the Digital Operator and the Drive may be faulty.
Remove the Digital Operator and then re-install it.
Diagnostic & Troubleshooting 6 - 16
!
If the Motor Does Not Operate
Use the following information if the motor does not operate.
"
Ensure the digital operator is securely connected to the Drive.
"
The motor does not operate when the HAND key on the Digital Operator is pressed.
The following causes are possible:
The Speed Command (Frequency Reference) is too low.
If the Speed Command (frequency reference) is set below the frequency set in E1-09 (Minimum Output Frequency), the Drive will not operate.
Raise the Speed Command to at least the minimum output frequency.
"
The motor does not operate when an external run command is input.
The following causes are possible.
The Drive is not in Drive mode.
If the Drive is not in Drive mode, it will remain in ready status and will not start. Press the MENU key once and press the
DATA/ENTER key. The Drive is now in Drive mode.
The Speed Command is too low.
If the Speed Command is set below the frequency set in E1-09 (Minimum Output Frequency), the Drive will not operate.
Raise the Speed Command to at least the minimum output frequency.
Diagnostic & Troubleshooting 6 - 17
"
The motor stops during acceleration or when a load is connected.
The load may be too high. The Drive has a stall prevention function and an automatic torque boost function, but the motor responsiveness limit may be exceeded if acceleration is too rapid or if the load is too great. Lengthen the acceleration time
(CI-01) or reduce the load. Also consider increasing the motor size.
"
The motor only rotates in one direction.
"Reverse run prohibited" may be selected. If b1-04 (Prohibition of Reverse Operation) is set to 1 (reverse run prohibited), the
Drive will not receive reverse run commands. This is the default to use both forward and reverse operation, set b1-04 to 0, and operate in Auto mode.
!
The Direction of the Motor Rotation is Reversed
If the motor rotates in the wrong direction, the motor output wiring is incorrect. When the Drive U/T1, V/T2, and W/T3 terminals are properly connected to the motor, the motor operates in a forward direction when a forward run command is received. The forward direction depends on the manufacturer and the motor type, so be sure to check the specifications.
The direction of rotation can be reversed by switching any two wires among U/TI, V/T2, and W/T3.
!
If the Motor Does Not Put Out Torque or If Acceleration is Slow
Use the following information if the motor does not output torque or if acceleration is too slow.
"
The stall prevention level during acceleration is too low.
If the value set for L3-02 (Stall Prevention Acceleration Level) is too low, the acceleration time will be too long. Check to be sure that the set value is suitable.
"
The stall prevention level during running is too low.
If the value set for L3-06 (Stall Prevention Level during Running) is too low, the motor speed and torque will be limited.
Check to be sure that the set value is suitable.
!
If the Motor Operates at a Higher Speed Than the Speed Command
Use the following information if the motor operates at a higher speed than the Speed Command.
"
A signal is being input to the Speed Command (current) terminal A2.
If a preset frequency reference is selected, the preset reference takes priority over the normal reference.
If the PI mode of operation is enabled, the Drive output frequency will change to regulate the process variable to the desired setpoint. Then, the Drive speed may go to maximum.
Diagnostic & Troubleshooting 6 - 18
!
If the Motor Overheats
Take the following steps if the motor overheats.
"
The load is too high.
If the motor load is too high and the motor is used when the effective torque exceeds the motor's rated torque, the motor will overheat. Reduce the load amount by either reducing the load or increasing the acceleration/deceleration times. Also consider increasing the motor size.
"
The ambient temperature is too high.
The motor rating is determined by a particular ambient operating temperature range. The motor will overheat if it is run continuously at the rated torque in an environment where the maximum ambient operating temperature rating is exceeded.
Lower the motor's ambient temperature to within its acceptable range.
"
The withstand voltage between the motor phases is insufficient.
When the motor is connected to the Drive output, Voltage surges are generated by standing waves that can occur with certain combinations of Drive carrier frequency and motor cable length. Normally the maximum surge voltage is three times the
Drive's input power supply voltage (i.e., 1200VAC for a 480VAC). Be sure to use a motor with a withstand voltage between the motor phases that is greater than the maximum surge voltage. In particular, when using a 480VAC Drive, use an inverterduty (NEMA MG1, Parts 30 & 31) motor. Motor protection filter can also be an effective measure.
!
If Peripheral Devices Like PLCs or Others are Influenced by Starting or Running
Drive
"
If noise is generated by Drive switching, implement the following countermeasures:
1.
Change the Drive's Carrier Frequency Selection (C6-02) to lower the carrier frequency. This will help to reduce the amount of internal switching.
2.
Install an Input Noise Filter at the Drive's input power terminals.
3.
Use metal conduit. Electric waves can be shielded by metal, so encase the Drive and power wires in metal.
4.
Ground the Drive and motor.
5.
Separate main circuit wiring from control wiring.
Diagnostic & Troubleshooting 6 - 19
!
If the Ground Fault Interrupter Operates When the Drive is Run
The Drive performs internal switching, so there is a certain amount of leakage current. This may cause an external ground fault interrupter to operate and cut off the power supply. Whenever possible, use a ground fault interrupter with a high leakage detection level (i.e., a sensitivity current of 200 mA or greater per unit, with an operating time of 0.1 s or more), or one that incorporates high frequency countermeasures (i.e., one designed for use with Drives). It will also help to change the Drive's
Carrier Frequency Selection (C6-02) to lower the carrier frequency. In addition, remember that the leakage current increases as the cable is lengthened.
!
If There is Mechanical Vibration
Use the following information when there is mechanical vibration.
"
The application is making unusual sounds.
The following causes are possible.
There may be resonance between the mechanical system's natural frequency and the carrier frequency.
This is characterized by the motor running with no noise generation, but the machinery vibrates with a high-pitched whine. To prevent this type of resonance, adjust the carrier frequency with parameters C6-02 to C6-05.
There may be resonance between an applications characteristic frequency and the output frequency of the Drive.
To prevent this from occurring, use the jump frequency functions in parameters d3-01 to d3-04, or have the driven motor and load balanced to reduce vibration.
"
Oscillation and hunting are occurring with V/f control.
The gain adjustment may be insufficient. Reset the gain to a more effective level by raising the value of C4-02 (Torque
Compensation Primary Delay Time Parameter) and then lowering the setting of n1-02 (Hunting Prevention Gain).
"
Oscillation and hunting are occurring with PI control.
If there is oscillation or hunting during PI control, check the oscillation cycle and individually adjust P and I parameters.
• Disable integral (I) control
• Reduce the proportional gain (P) until hunting stops
• Reintroduce the integral function, starting with long integral time values, to eliminate the P offset
Diagnostic & Troubleshooting 6 - 20
!
If the Motor Rotates Even When Drive Output is Stopped
If the motor rotates even when the Drive is stopped, the DC injection braking may be insufficient. If the motor continues operating at low speed, without completely stopping after a stop has been executed, it means that the DC injection braking is not decelerating the motor enough. Adjust the DC injection braking as follows:
•
Increase the parameter b2-04 (DC Injection Braking (initial excitation) Time at Stop) setting.
•
Increase the parameter b2-02 (DC Injection Braking Current) setting.
!
If Zero Volts is Detected When a Motor is Started, or Stalls
Generation of 0 V (main circuit voltage) and stalling can occur if a motor is turning when it is started and the DC injection braking is insufficient.
This can be prevented by slowing motor rotation by DC injection braking before starting. Increase parameter b2-03
(DC injection braking time at start) setting.
!
If Output Frequency Does Not Rise to Frequency Reference
Use the following information if the output frequency does not rise to the Speed Command.
"
The Speed Command is within the jump frequency range.
When the jump frequency function is used, the output frequency does not change within the jump frequency range. Check to be sure that the Jump Frequency (parameters d3-01 to d3-03) and Jump Frequency Width (parameter d3-04) settings are suitable.
"
The frequency reference upper limit has been reached.
The output frequency upper limit is determined by the following formula:
Freq Ref Upper Limit = Maximum Output Frequency (E1-04)
×
Frequency Reference Upper Limit (d2-01) / 100
Check to be sure that the parameter E1-04 and d2-01 settings are suitable.
Diagnostic & Troubleshooting 6 - 21
Drive Main Circuit Test Procedure
WARNING
Prior to removing any protective cover or wiring any part of the Drive, remove all power sources, including main input power and control circuit power. Wait a minimum of 5 minutes after power removal, before removing any cover. The charge lamp located within the Drive should be off prior to working inside. Even if the charge lamp is off, one must measure the AC input, output, and DC Bus potential to insure safe levels prior to resuming work. Failure to adhere to this warning may result in personal injury or death.
Before attempting any troubleshooting checks, make sure that the three-phase power is disconnected and locked out. With power removed from the unit, the DC bus capacitors will stay charged for several minutes. The Charge LED in the Drive will glow red until the DC bus voltage is below 10Vdc. To ensure that the DC bus is completely discharged, measure between the positive and negative bus with a DC voltmeter set to the highest scale.
Check
Measure DC Bus Voltage
Input Diodes
(D1-D12 or Q1)
Table 6.6 Main Circuit Test Procedure
Procedure
1. Set the digital multi-meter to its highest VDC scale.
2. Measure between
⊕
1 and (-) for the following check:
Place the positive (red) meter lead on
⊕
1.
Place the negative (black) meter lead on (-).
3. If the measured voltage is < 10Vdc, it is safe to work inside the Drive.
If not, wait until the DC Bus has completely discharged.
The input diodes rectify or transform the three-phase input AC voltage into a DC voltage.
1. Set a digital multi-meter to the Diode Check setting.
2. Place the positive (red) meter lead on terminal R/L1.
Place the negative (black) meter lead on terminal
⊕
1.
Expected reading is about 0.5 Volts.
3. Place the positive (red) meter lead on terminal S/L2.
Place the negative (black) meter lead on terminal
⊕
1.
Expected reading is about 0.5 Volts.
4. Place the positive (red) meter lead on terminal T/L3.
Place the negative (black) meter lead on terminal
⊕
1.
Expected reading is about 0.5 Volts.
5. Place the positive (red) meter lead on terminal R/L1.
Place the negative (black) meter lead on terminal (-).
Expected reading is OL displayed.
6. Place the positive (red) meter lead on terminal S/L2.
Place the negative (black) meter lead on terminal (-).
Expected reading is OL displayed.
7. Place the positive (red) meter lead on terminal T/L3.
Place the negative (black) meter lead on terminal (-).
Expected reading is OL displayed.
8. Place the positive (red) meter lead on terminal (-).
Place the negative (black) meter lead on terminal R/L1.
Expected reading is about 0.5 Volts.
9. Place the positive (red) meter lead on terminal (-).
Place the negative (black) meter lead on terminal S/L2.
Expected reading is about 0.5 Volts.
10. Place the positive (red) meter lead on terminal (-).
Place the negative (black) meter lead on terminal T/L3.
Expected reading is about 0.5 Volts.
Diagnostic & Troubleshooting 6 - 22
Check
Input Diodes
(D1-D12 or Q1)
Soft Charge Resistor Check
(R1, R2, 6PCB)
Soft Charge Contactor
(K1)
DC Bus Fuse
(F1)
Table 6.6 Main Circuit Test Procedure (Continued)
Procedure
11. Place the positive (red) meter lead on terminal
⊕
1.
Place the negative (black) meter lead on terminal R/L1.
Expected reading is OL displayed.
12. Place the positive (red) meter lead on terminal
⊕
1.
Place the negative (black) meter lead on terminal S/L2.
Expected reading is OL displayed.
13. Place the positive (red) meter lead on terminal
⊕
1.
Place the negative (black) meter lead on terminal T/L3.
Expected reading is OL displayed.
The soft charge resistor works in conjunction with the soft charge contactor to slowly charge the DC bus capacitors to minimize the inrush current when power is applied to the Drive.
1. Conduct a visual inspection. Check for physical damage.
2. Set a digital multi-meter to the R x 1 scale.
3. If the resistor is damaged, the measured value will be infinite ohms.
The purpose of the soft charge contactor is to bypass the soft charge resistor after the DC bus voltage has reached its normal operating level.
1. Conduct a visual inspection. Check for physical damage.
2. Set a digital multi-meter to the R x 1 scale.
3. On Drives with a board-mounted contactor, verify that each contact resistance measures infinite ohms.
4. On Drives without a board-mounted contactor, press the plunger in, and verify that each contact measures zero ohms.
5. On Drives without a board-mounted contactor, release the plunger, and verify that the resistance is the ohmic value of the soft charge resistor.
6. On Drives with a board-mounted contactor, verify that the contactor coil measures about
300 ohms. The coil can be tested by applying the appropriate voltage to verify the contacts change states.
7. On Drives without a board-mounted contactor, verify that the 230VAC contactor coil measures about 175 ohms. The coil can be tested by applying the appropriate voltage to verify the contacts change states.
8. On Drives without a board-mounted contactor, verify that the 24Vdc auxiliary coil measures about 2.2M ohms. The coil can be tested by applying the appropriate voltage to verify the contacts change states.
The DC bus fuse is located in the negative portion of the DC Bus. The DC bus fuse is used to protect the main circuit components if the output transistors short. If the DC bus fuse is open, at least one of the output transistors has failed. When a transistor fails, there is a short between the positive and negative portions of the DC Bus. The DC bus fuse does not protect the transistors, but protects the rest of the main circuit from the high current present during a short. Never replace the DC bus fuse without first checking all of the output transistors.
1. Set a digital multi-meter to the R x 1 scale.
2. Place one lead of the multi-meter on one side of the fuse and place the other lead of the multi-meter on the other side of the fuse.
3. If the fuse is good, the measured value will be zero ohms.
If the fuse is bad, the measured value will be infinite ohms.
Diagnostic & Troubleshooting 6 - 23
Check
Output Transistors
(Q1-Q12)
Control Power Fuse
Table 6.6 Main Circuit Test Procedure (Continued)
Procedure
The output transistors are used to switch the DC bus voltage to allow current to flow to the motor.
1. Set a digital multi-meter to the Diode Check setting.
2 Place the positive (red) meter lead on terminal U/T1.
Place the negative (black) meter lead on terminal
⊕
1.
Expected reading is about 0.5 Volts.
3 Place the positive (red) meter lead on terminal V/T2.
Place the negative (black) meter lead on terminal
⊕
1.
Expected reading is about 0.5 Volts.
4 Place the positive (red) meter lead on terminal W/T3.
Place the negative (black) meter lead on terminal
⊕
1.
Expected reading is about 0.5 Volts.
5 Place the positive (red) meter lead on terminal U/T1.
Place the negative (black) meter lead on terminal (-).
Expected reading is OL displayed.
6. Place the positive (red) meter lead on terminal V/T2.
Place the negative (black) meter lead on terminal (-).
Expected reading is OL displayed.
7 Place the positive (red) meter lead on terminal W/T3.
Place the negative (black) meter lead on terminal (-).
Expected reading is OL displayed.
8 Place the positive (red) meter lead on terminal (-).
Place the negative (black) meter lead on terminal U/T1.
Expected reading is about 0.5 Volts.
9 Place the positive (red) meter lead on terminal (-).
Place the negative (black) meter lead on terminal V/T2.
Expected reading is about 0.5 Volts.
10 Place the positive (red) meter lead on terminal (-).
Place the negative (black) meter lead on terminal W/T3.
Expected reading is about 0.5 Volts.
11. Place the positive (red) meter lead on terminal
⊕
1.
Place the negative (black) meter lead on terminal U/T1.
Expected reading is OL displayed.
12. Place the positive (red) meter lead on terminal
⊕
1.
Place the negative (black) meter lead on terminal V/T2.
Expected reading is OL displayed.
13. Place the positive (red) meter lead on terminal
⊕
1.
Place the negative (black) meter lead on terminal W/T3.
Expected reading is OL displayed.
All Drives have a Control Power Fuse. The fuse is located on either the Power PCB (3PCB) or the Gate Drive PCB (3PCB). The Control Power Fuse protects the primary switching mode power supply.
1. Set a digital multi-meter to the R x 1 scale.
2. Place one lead of the multi-meter on one side of the fuse and place the other lead of the multi-meter on the other side of the fuse.
3. If the fuse is good, the measured value will be zero ohms.
If the fuse is bad, the measured value will be infinite ohms.
Diagnostic & Troubleshooting 6 - 24
Check
24Vdc Cooling Fans
(Heat Sink & Internal)
230/240VAC Cooling Fans
(Heat Sink)
Cooling Fan Fuse
Table 6.6 Main Circuit Test Procedure (Continued)
Procedure
The Heat Sink & Internal Cooling Fans cool the heat sink as well as the output transistor modules of the Drive.
1. Conduct a visual inspection to ensure the fan turns freely.
2. If there is no physical evidence that the fan is bad, the fan motor can be checked with a digital mutli-meter.
3. Set the digital multi-meter to the R x 1 scale.
4. Measure across the fan motor terminals. If zero ohms are measured, conclude that the fan motor is shorted. If infinite ohms are measured, conclude that the fan motor is burned open.
5. If the fan is not working, then disconnect the fan and apply 24Vdc to the fan to test the motor.
The Heat Sink Cooling Fans cool the heat sink to remove heat from the Drive.
1. Conduct a visual inspection to ensure the fan turns freely.
2. If there is no physical evidence that the fan is bad, the motor can be checked with a digital mutli-meter.
3. Set a digital multi-meter to the R x 1 scale.
4. Measure across the fan motor terminals. If the fan motor is good, the measured value should be about 500 ohms. If zero ohms are measured, conclude that the fan motor is shorted. If infinite ohms are measured, conclude that the fan motor is burned open.
If the fan is not working, then disconnect the fan and apply 230/240VAC to the fan to test the motor.
Large Drive units contain a Cooling Fan Fuse. It is located on either the Gate Drive Board
(3PCB) or the Tap Change Board (8PCB). If the Cooling Fan Fuse is open, then the
230/240VAC cooling fans may be defective.
1. Set a digital multi-meter to the R x 1 scale.
2. Place one lead of the multi-meter on one side of the fuse and place the other lead of the multi-meter on the other side of the fuse.
3. If the fuse is good, the measured value will be zero ohms.
If the fuse is bad, the measured value will be infinite ohms.
Diagnostic & Troubleshooting 6 - 25
Drive Date Stamp Information
This information is used to determine when a Drive was built to see if it is within its warranty period. The date stamp is located on the lower right side of the Drive.
Fig 6.1 Date Stamp Location
PRD
INSP2
YEA Production
Manufacture Date
Inspector Number
Diagnostic & Troubleshooting 6 - 26
Chapter 7
Maintenance
This chapter describes basic maintenance and inspection of the Drive and Bypass unit. Please refer to these instructions to ensure that the Drive receives the proper maintenance to maintain overall performance.
Maintenance ................................................................................... 2
Periodic Inspection .................................................................... 2
Preventive Maintenance ............................................................ 3
Replacing Control Panel indicating lights or selector switches .. 4
Replacing The Relay Controller PCB: ....................................... 5
Drive Heatsink Cooling Fan Replacement ................................. 6
Removing and Mounting the Drive Control Terminal Card ........ 8
Removing and Replacing the Drive in a Bypass Unit ..................... 9
Drive Replacement .................................................................... 9
Maintenance 7 - 1
P7B Maintenance
!
Periodic Inspection
Check the following items during periodic maintenance.
•
The motor should not be vibrating or making unusual noises.
•
•
•
There should be no abnormal heat generation from the Drive and Bypass or motor.
The ambient temperature should be within the Drive and Bypass specification of -10
°
C to 40
°
C (14
°
F to 104
°
F).
The output current value shown in parameter U1-03 should not be higher than the motor rated current for an extended period
•
of time.
The cooling fan in the Drive and Bypass should be operating normally.
Always turn OFF the input power before beginning inspection. Confirm that the digital operator and indicator lights on the front panel have all turned OFF, and then wait an additional five minutes before beginning the inspection. Be sure not to touch terminals immediately after the power has been turned off. Doing so can result in electric shock. Please refer to Warnings on page i.
Item
External terminals, mounting bolts, connectors, etc.
Cooling fins
Bypass Operator
Interface PCB
Bypass Relay
Controller PCB
Control PCB
Terminal PCB
Power PCB
Gate Drive PCBs
Contactors
Input Diodes
Output Transistors or IPMs
DC bus capacitors
Table 7.1 Periodic Inspections With no Power Applied
Inspection Corrective Action
Are all screws and bolts tight?
Tighten loose screws and bolts firmly.
Are connectors tight?
Are the fins dirty or dusty?
Is there any conductive dirt or oil mist on the
PCBs?
Reconnect the loose connectors.
Clean off any dirt and dust with an air gun using clean and dry air at a pressure between 55-85 psi.
Clean off any dirt and dust with an air gun using clean and dry air at a pressure between 55-85 psi.
Replace the boards if they cannot be made clean.
Is there any conductive dirt or oil mist on the modules or components?
Clean off any dirt and dust with an air gun using clean and dry air at a pressure between 55-85 psi.
Are there any irregularities, such as
discoloration or odor?
Replace the capacitors or Drive.
Apply power to the Drive and Bypass, then conduct the following inspection.
Item
Cooling fan(s)
Table 7.2 Periodic Inspections With Power Applied
Inspection Corrective Action
Is there any abnormal noise or vibration, or has the total operating time exceeded 20,000 hours.
Check U1-40 for elapsed cooling fan operation time.
Replace Cooling Fan.
Maintenance 7 - 2
!
Preventive Maintenance
Inspection Points
General
Item
Environment
Equipment
AC Power Supply
Table 7.3 Preventive Maintenance
Check Points
Ambient Temperature
Humidity
Dust
Harmful Gas
Oil Mist
Abnormal vibration or noise
Conductors & Wire
Connections
Main circuit & control voltage
Loose lugs, screws & wires
Hot spots on parts
Corrosion
Bent conductors
Breakage, cracking or discoloration
Check spacing
AC Power Circuit &
Devices
Control Circuits
Cooling System
Keypad/Front Panel
Display
Transformers & Reactors
Terminal Blocks
DC Bus Capacitors
Relays & Contactors
Soft Charge Resistors
Operation
Cooling Fans/Fins & Heatsink
Digital Operator and
Front Panel
Discoloration or Noise
Loose, damaged
Leakage
Ruptures, broken, expansion
Capacitance & insulation resistance
Noisy
Contact discoloration
Cracked
Discoloration
Speed reference voltage/current
I/O contact operation
Relay logic
Abnormal fan noise
Loose connectors
Free of accumulation
LEDs
Monitor display values
Key and selector switch functionality
Clean
Every 3-6 Months
"
"
"
"
"
"
"
Yearly
"
"
"
"
"
"
"
"
"
"
"
"
"
"
"
"
"
"
"
"
"
"
"
"
If the Drive is used under the following conditions, it may be necessary to inspect more often:
•
High ambient temperatures, humidity or altitudes above 3,300 feet
•
Frequent starting and stopping
•
Fluctuations of the AC power supply or load
•
Excessive vibration and/or shock loading
•
Poor environment, including dust, metal particles, salt, sulfuric acid, chlorine
Maintenance 7 - 3
!
Replacing Control Panel indicating lights or selector switches
Control panel pilot lights are modular, replaceable LEDs with a MTBF of 100,000 hours. LED type indicating lights are provided to improve the reliability well beyond that of incandescent bulbs.
To remove and replace the LEDs, remove 9 screws from the “Bypass Operator Interface PCB A3” located on the inside of the enclosure door mounted Operator Panel.
PCB Mounting
Screws, 9 places
Fig 7.1 Removing PCB A3
PCB A3 will then lift off, exposing the LEDs and selector switch assemblies. Remove the ribbon cable connection from
CN203 as well as marking and disconnecting the terminations from CN204, CN205, CN206 and CN207, if required, to gain access to the LED side of the circuit board A3.
To replace an individual LED, slide a small blade screwdriver beside the LED module and the retaining tabs on the socket that is soldered to the circuit board, see Figure 7.2.
Maintenance 7 - 4
Twist the screwdriver just sufficiently to release the retainers while “rocking” the LED module in the socket.
Care must be exercised to avoid breaking off the delicate retaining tabs. If retaining tabs break off, then the complete PCB A3 should be replaced (see appendix F for part numbers).
LED Module
LED Socket
LED Module Retaining Tabs
Fig 7.2 Removing an LED
The new LED module (see appendix F for part numbers) is simply pushed firmly into the same location on the socket until the retainers snap into place. Then reassemble the PCB A3 to the operator panel on the inside of the enclosure door, using the 9 screws previously removed.
This procedure is also employed to replace the Selector Switch modules on the “Bypass Operator Interface PCB A3”.
!
Replacing The Relay Controller PCB:
The Bypass controller relays are not individually replaceable, the “Bypass Relay Controller PCB A2” assembly must be replaced (see appendix F for part numbers). The “Bypass Relay Controller PCB A2” is located on the left hand side of the wall mount enclosure, adjacent to the door hinge.
To remove PCB A2, disconnect the ribbon cable connectors at CN102 A, CN102 B and CN103. Mark and disconnect the wires from TB CN102 C as well as marking and disconnecting all field wiring from terminal block TB1.
Remove the 5 nuts securing the circuit board to the side wall of the enclosure, lift out and replace the “Bypass Relay Controller
PCB A2” assembly with a new one (see appendix F for part numbers).
Maintenance 7 - 5
!
Drive Heatsink Cooling Fan Replacement
#
Drive Models CIMR-
_ _ _
20P4 thru 2018 (25 HP@208V/240V) and 40P4 thru 4018
(30 HP@480V)
IMPORTANT
If the Drive is mounted with the heatsink external to the enclosure, as it is in Bypass units, the cooling fan can only be replaced by removing the Drive from the enclosure. See “Removing and Replacing the Drive” in this chapter.
A cooling fan is attached to the bottom of the Drive.
If the Drive is installed using the mounting holes on the back of the Drive heatsink, the cooling fan can be replaced without removing the Drive from the enclosure panel.
#
Removing the Drive Heatsink Cooling Fan
1.
Always turn OFF the input power before removing and installing the heatsink cooling fan.
2.
Press in on the right and left sides of the fan cover in the direction of arrows “1” and then pull the fan out in the direction of arrow “2”.
3.
Pull out the cable connected to the fan from the fan cover and disconnect the power connector. See Figure 7.3.
4.
Open the fan cover on the left and right sides in the direction of arrows “3” and remove the fan cover from the fan.
3
3
Power
Connector
Fig 7.3 Cooling Fan Replacement Procedure
#
Installing the Drive Heatsink Cooling Fan
1. Attach the fan cover to the cooling fan. Be sure that the air flow direction indicated by the arrows above faces into the
Drive.
2. Connect the power connector securely and place the power connector and cable into the fan cover.
3. Mount the fan cover on the Drive. Be sure that the tabs on the sides of the fan cover click into place on the Drive.
Maintenance 7 - 6
#
Drive Models CIMR-
_ _ _
2022 thru 2110 (30 HP and above @ 208V/240V) and 4030 thru 4300 (40 HP and above @ 480V)
A cooling fan assembly is attached to the top inside the Drive. The cooling fan assembly includes the heat sink cooling fans and the internal cooling fan. The cooling fan(s) can be replaced without removing the Drive from the enclosure panel.
#
Removing the Drive Cooling Fan Assembly
1.
Always turn OFF the input power before removing and installing the heatsink cooling fan assembly.
2.
Remove the terminal cover, Drive cover, Digital Operator, and front cover from the front of the Drive.
3.
Remove the Control PCB bracket (if necessary) to which the cards are mounted. Remove all cables connected to the
Control PCB and remove the cooling fan power connector from the fan board (13 PCB) positioned near the top of the
Drive.
4.
Remove the cooling fan power connectors from the gate Drive board (3PCB) positioned at the back of the Drive.
5.
Remove the fan assembly screws and pull out the fan assembly from the Drive.
6.
Remove the cooling fan(s) from the fan assembly.
#
Mounting the Drive Cooling Fan Assembly
After attaching a new cooling fan, reverse the above procedure to attach all of the components.
When attaching the cooling fan to the mounting bracket, be sure that the air flow goes toward the top of the Drive.
Control PCB bracket
Control PCB
Air flow direction
Fan cover
Connector
Gate driver
Fig 7.4 Cooling Fan Assembly Replacement Procedure
Maintenance 7 - 7
!
Removing and Mounting the Drive Control Terminal Card
The terminal card can be removed and mounted without disconnecting the control wiring.
IMPORTANT
Always confirm that input power is removed and the Charge LED is not lit before removing or mounting the terminal card.
#
Removing the Drive Terminal Card
1. Remove the terminal cover on the Drive.
2. Remove the Digital Operator and front cover on the Drive.
3. Remove the wires connected to FE and NC on the terminal card.
4. Loosen the mounting screws on the left and right sides of the terminal card until they are free. It is not necessary to remove the mounting screws completely. They are captive and self-rising.
5. Pull the terminal card out in the direction of the block arrow.
#
Mounting the Drive Terminal Card
Reverse the removal procedure to mount the terminal card.
Confirm that the terminal card and the Control PCB properly meet at connector CN8 before insertion.
The connector pins may be bent if the terminal card is forced into place, possibly preventing correct Drive operation.
CN8
FE NC
Mounting Screw
Fig 7.5 Terminal Card Removal Procedure
Maintenance 7 - 8
Mounting Screw
Removing and Replacing the Drive in a Bypass Unit
!
Drive Replacement
If possible, save the existing drive programming by copying it to the memory in the keypad/operator via parameter o3-01.
When it has been determined that a Drive fault requires a Drive replacement (see Chapter 6), there are several steps required before the Bypass will be operable again. First, a new Drive must be ordered. Begin by determining the model number Drive that is in the Bypass assembly.
Drive Model Number:_____________________________
Warranty status determines whom you should contact to obtain a new Drive.
For a Bypass unit that is still under warranty, begin by contacting Yaskawa Technical Support: 1-800-YASKAWA (927-5292), dial 2 for Inverter and Drive Products, then 5 for technical support. Technical support may also be reached through e-mail at
A Yaskawa distributor should be contacted to replace a Drive that is no longer under warranty.
When the Drive arrives, verify that the Drive is the correct model number.
#
Removing the Drive
Before installing the new Drive, the old Drive must be removed from the Bypass assembly. As a safety precaution, disconnect the AC power line coming into the main Bypass circuit breaker to ensure that no power is in the Bypass unit.
Check the Drive DC Bus voltage to be sure it is at a safe level before working inside the Bypass enclosure. DC Bus voltage can be monitored by the CHARGE status indicator LED, near the power terminals. Be sure the LED is extinguished before proceeding. Another method is to measure the DC voltage across terminals “+1” and “-” on the power terminal block.
Terminal for DC
Bus Voltage
Fig 7.6 Drive Power Terminal Block
DC Bus CHARGE Status
Indicator LED
Maintenance 7 - 9
Disconnect the cable from the Drive to the front panel mounted Digital Operator at the Drive end of the cable.
If a LonWorks option card is present, leave all the wires connected to the option card, disconnect the option card ground wire at the Drive end and remove the option card from the Drive.
Leave the field control wiring connected to the removable control terminal card and remove the control terminal card from the
Drive. Two captive screws on either side of the terminal card must be loosened, the ground wire removed from terminal FE, and the terminal card must be separated from the control circuit board by sliding the terminal card off its Connector (CN8). Do this carefully by pulling down evenly on both sides of the terminal card. See also page 7-9 for detailed instructions.
Connector
CN8
Terminal
FE
Captive
Mounting
Screw
Captive
Mounting
Screw
Fig 7.7 Removable Control Terminal Card
The power terminal block for the three phase input and output power connections is not removable. All connections to the power terminal block must be removed. Do not overlook the Drive ground wire. It is behind other wiring and will probably be removed last. Observe the wire and terminal markings for all power wires, to ensure correct re-wiring to the new Drive. The wires are labeled from the factory, but re-label any wires where labels may no longer be legible. Refer to Chapter 2 Electrical
Installation and the schematic diagram that was shipped with the original Bypass unit.
Once all wiring has been disconnected from the Drive, the Drive is ready to be removed from the enclosure.
Drives located in Bypass units are mounted differently than stand alone drives. A Drive in a Bypass unit is mounted such that the heat sink is external to the enclosure. Mounting brackets are located on the top and bottom of the Drive, between the Drive and the Drive’s heat sink. These brackets are bolted to the reinforced Bypass back panel with the heat sink projecting through an opening in the back panel and reinforcing frame.
Drive Top Bracket
Fig 7.8 Drive Top Mounting Bracket
Maintenance 7 - 10
Drive Bottom Bracket
Fig 7.9 Drive Bottom Mounting Bracket
Reinforcing
Frame
Bypass Enclosure
Back Panel
Fig 7.10 Back Panel and Reinforcing Frame
To free the Drive, remove the bolts from the Drive mounting brackets (remove the bottom first). When free, pull the Drive through the front of the Bypass enclosure by guiding the heat sink back through the opening in the back panel.
With the Drive out of the Bypass assembly, remove the mounting brackets from the old Drive by removing the bolts affixing the mounting brackets to the Drive. Attach the mounting brackets to the new Drive using the bolts from the old Drive.
#
Installing the Replacement Drive
Place the new Drive into the Bypass by sliding the heat sink through the opening in the rear of the Bypass enclosure. Line up the holes on the mounting brackets with the holes in the reinforcing frame of the Bypass assembly. Use the mounting bolts previously removed to re-affix the Drive to the Bypass back panel.
When the new Drive has been mounted in the Bypass enclosure, reconnect all power wiring and verify by checking the Bypass schematic.
Re-mount the control terminal card to the Drive by sliding the terminal card into the connector (CN8) on the control circuit board. Re-fasten the captive screws to the control PCB. Consult page 7-9 for detailed instructions.
Re-mount any option card, and re-connect all wiring from the option card to the Drive. Be sure to re-connect the ground wire to the Drive.
With the Drive replacement complete, return power to the Bypass unit. Locate the start-up procedure for the Bypass in
Chapter 4 and follow the complete start-up procedure.
Maintenance 7 - 11
#
Programming the Replacement Drive
Replacement drives come from the factory with standard factory default parameter settings. They are not “Bypass ready” and the parameters in the replacement Drive will need to be modified for Bypass compatibility.
Several approaches to this may be available:
1.
The digital operator/keypad from the old Drive may contain a copy of the parameter settings for this application. See parameter o3-01 in Chapter 5 for instructions.
2.
The customer may have a file of parameter settings for the PC software “DriveWizard” which can be used to download these values to the Drive. Information and instructions for DriveWizard are available at www.drives.com.
3.
Page 2 of the Bypass Schematic has a table of Drive “Factory Parameter Settings” for Bypass applications of drives. The
Bypass schematic was delivered as part of the original Bypass assembly and is re-produced in Chapter 2 of this manual.
These settings can be manually entered into the new Drive after setting the access level in parameter A1-01 to advanced
(“2: Advanced Level”).
Using one of these methods, load the Drive with the Bypass “factory default” settings and verify correct Bypass operation.
Maintenance 7 - 12
Appendix A
Parameters
This appendix lists all the parameter numbers and names, along with a description of each. Also, below the parameter name in bold type is the abbreviated name as it appears on the digital operator display/keypad.
Parameter List ................................................................................ 2
Monitor List ................................................................................... 26
Fault Trace List ............................................................................. 28
Fault History List ........................................................................... 29
Parameters A - 1
Parameter List
Table 1: Parameter List
Parameter
No.
Parameter Name
Digital Operator Display
A1-00
!
A1-01
!
A1-03
A1-04
A1-05
Language Selection
Select Language
Access Level Selection
Access Level
Initialize Parameters
Init Parameters
Password 1
Enter Password
Password 2
Select Password
Description
Initialization
Language selection for digital operator display.
0: English
1: Japanese
2: Deutsch
3: Francais
4: Italiano
5: Espanol
6: Portugues
*Not returned to factory setting by initialization
This setting determines which parameters are accessible.
0: Operation Only
1: User Level
2: Advanced Level
Used to return all parameters to their factory or user setting.
0: No Initialize
1110: User Initialize (The user must set their own parameter default values and then parameter o2-03 must be set to “1” to save them. If the parameter values are changed after o2-03 is set to “1”, the user default values can be restored by setting A1-03 to 1110.)
2220: 2-Wire Initial
3330: 3-Wire Initial
When the value set into A1-04 does NOT match the value set into
A1-05, parameters A1-01 thru A1-03 and A2-01 thru A2-32 cannot be changed. All other parameters as determined by A1-01 can be changed. Parameter A1-05 can be accessed by pressing the MENU key while holding the RESET key.
User Parameters
A2-01
User Parameter 1
User Param 1
A2-02
User Parameter 2
User Param 2
Setting
Range
Factory
Setting
0 to 6
0 to 2
0 to
3330
0 to 9999
0 to 9999
0
2
0
0
0
–
–
Menu
Location
Quick Setting
Programming
Programming
Programming
Programming
Programming
Programming
A2-03
User Parameter 3
User Param 3
Selects the parameters to be available in the User Access Level
(A1-01 = 1). These are the only parameters accessible for the user level. These parameters are not related to the User Initialize function.
A2-04
User Parameter 4
User Param 4
A2-05
User Parameter 5
User Param 5
A2-06
User Parameter 6
User Param 6
!Denotes that parameter can be changed when the Drive is running.
b1-01 to o3-02
–
–
–
–
Programming
Programming
Programming
Programming
Parameters A - 2
Table 1: Parameter List (Continued)
Parameter
No.
A2-07
A2-08
A2-09
A2-10
A2-11
A2-12
A2-13
A2-14
A2-15
A2-16
A2-17
A2-18
A2-19
A2-20
A2-21
A2-22
A2-23
A2-24
A2-25
A2-26
A2-27
A2-28
A2-29
A2-30
A2-31
A2-32
Parameter Name
Digital Operator Display
User Parameter 7
User Param 7
User Parameter 8
User Param 8
User Parameter 9
User Param 9
User Parameter 10
User Param 10
User Parameter 11
User Param 11
User Parameter 12
User Param 12
User Parameter 13
User Param 13
User Parameter 14
User Param 14
User Parameter 15
User Param 15
User Parameter 16
User Param 16
User Parameter 17
User Param 17
User Parameter 18
User Param 18
User Parameter 19
User Param 19
User Parameter 20
User Param 20
User Parameter 21
User Param 21
User Parameter 22
User Param 22
User Parameter 23
User Param 23
User Parameter 24
User Param 24
User Parameter 25
User Param 25
User Parameter 26
User Param 26
User Parameter 27
User Param 27
User Parameter 28
User Param 28
User Parameter 29
User Param 29
User Parameter 30
User Param 30
User Parameter 31
User Param 31
User Parameter 32
User Param 32
Description
Selects the parameters to be available in the User Access Level
(A1-01 = 1). These are the only parameters accessible for the user level. These parameters are not related to the User Initialize function.
Setting
Range b1-01 to o3-02
–
–
–
–
–
–
–
–
–
–
–
–
–
–
–
–
–
–
–
–
–
Factory
Setting
–
Menu
Location
Programming
–
–
–
–
Programming
Programming
Programming
Programming
Programming
Programming
Programming
Programming
Programming
Programming
Programming
Programming
Programming
Programming
Programming
Programming
Programming
Programming
Programming
Programming
Programming
Programming
Programming
Programming
Programming
Parameters A - 3
Table 1: Parameter List (Continued)
Parameter
No.
b1-01 b1-02 b1-03 b1-04 b1-07 b1-08 b1-11 b1-12 b2-01 b2-02 b2-03 b2-04
Parameter Name
Digital Operator Display
Description
Frequency Reference
Selection
Reference Source
Run Command Selection
Run Source
Stopping Method Selection
Stopping Method
Reverse Operation Selection
Reverse Oper
Local/Remote Run Selection
LOC/REM RUN Sel
Sequence
Selects the speed command (frequency reference) input source.
0: Operator - Digital preset speed d1-01
1: Terminals - Analog Input Terminal A1 (or Terminal A2 see parameter H3-13)
2: Serial Com - RS-485 terminals R+, R-, S+ and S-
3: Option PCB - Option board connected at 2CN
Selects the run command input source.
0: Operator - "Hand" and "Off" keys on digital operator
1: Terminals - Contact Closure on Terminal S1
2: Serial Com - RS-485 terminals R+, R-, S+ and S-
3: Option PCB - Option board connected at 2CN
Selects the stopping method when the run command is removed.
0: Ramp to Stop
1: Coast to Stop
2: DC Injection to Stop
3: Coast w/Timer (A new run command is ignored if input before the time in C1-02 expires.)
Determines the forward rotation of the motor, and if reverse operation is disabled.
0: Reverse Enabled
1: Reverse Disabled
2: Exchange Phase - Change direction of forward motor rotation.
3: ExchgPhs, Rev Dsbl - Change direction of forward motor rotation and disable reverse operation.
0: Cycle Extern RUN - If the run command is closed when switching from hand(local) mode to auto(remote) mode, the
Drive will not run.
1: Accept Extrn RUN - If the run command is closed when switching from hand(local) mode to auto(remote) mode, the
Drive WILL run.
0: Disabled - Run command accepted only in the operation menu.
1: Enabled - Run command accepted in all menus
(except when b1-02 = 0).
Run Command Selection
During Program
RUN CMD at PRG
Drive Delay Time Setting
Wait to Run Time
After a run command, Drive output will start after this delay time.
Hand Frequency Reference
Selection
HAND Fref Source
DC Injection Braking Start
Frequency
DCInj Start Freq
DC Injection Braking
Current
DCInj Current
DC Injection Braking Time at
Start
DCInj Time @ Start
Selects the speed command input source in hand mode.
0: Operator - Digital preset speed d1-01
1: Terminals - Analog Input Terminal A1 (or Terminal A2 see parameter H3-13)
DC Braking
Sets the frequency at which DC injection braking starts when ramp to stop (b1-03 = 0) is selected. If b2-01< E1-09, DC Injection braking starts at E1-09.
Selects the DC injection braking current as a percentage of the
Drive rated current.
Sets the time length of DC injection braking at start in units of 1 second.
DC Injection Braking Time at
Stop
DCInj Time @ Stop
When b1-03 = 2 actual DC Injection time is calculated as follows: b2-04 * 10 * Output Frequency / E1-04. When b1-03 = 0, this parameter determines the amount of time DC Injection is applied to the motor at the end of the decel ramp. This should be set to a minimum of 0.50 seconds when using HSB. This will activate DC injection during the final portion of HSB and help ensure that the motor stops completely.
b2-09
Motor Pre-Heat Current
Preheat Current
Motor Pre-heat current in % of Drive rated current. This is used to keep the motor warm to prevent condensation and is used in conjunction with a digital input (data = 60).
Setting
Range
0 to 3
0 to 3
0 to 3
0 to 3
0 or 1
0 or 1
0 to 600
0 or 1
0.0 to 10.0
0 to 100
0.00 to
10.00
0.00 to
10.00
0 to100
Factory
Setting
1
1
0
1
0
0
0sec
0
0.5Hz
50%
0.00sec
0.00sec
0%
Menu
Location
Quick Setting
Quick Setting
Quick Setting
Quick Setting
Programming
Programming
Programming
Programming
Programming
Programming
Programming
Programming
Programming
Parameters A - 4
Table 1: Parameter List (Continued)
Parameter
No.
Parameter Name
Digital Operator Display
Description b3-01
Speed Search Selection
SpdSrch at Start
Speed Search
Enables/disables and selects the speed search function at start.
0: SpdsrchF Disable - Speed search at start is disabled
(estimated speed method is used at other times)
1: SpdsrchF Enable - Speed search is enabled
(estimated speed method)
2: SpdsrchI Disable - Speed search at start is disabled
(current detection method is used at other times)
3: SpdscrhI Enable - Speed search is enabled
(current detection method)
Estimated Speed Method:
Actual motor speed and direction is estimated, then the motor is ramped from that speed to the commanded speed.
Current Detection Method:
Current level is monitored while output frequency is ramped down. b3-02 b3-03 b3-05 b3-14
Speed Search Deactivation
Current
SpdSrch Current
Speed Search Deceleration
Time
SpdSrch Dec Time
Speed Search Delay Time
Search Delay
Bidirectional Speed Search
Selection
Bidir Search Sel
Used only when b3-01 = 3. Sets the speed search operation current as a percentage of Drive rated current.
Used only when b3-01 = 3. Sets the deceleration time during speed search.
Delays the speed search operation after a momentary power loss to allow time for an external output contactor to re-energize.
0: Disabled
1: Enabled b4-01 b4-02 b5-01
Timer Function ON-Delay
Time
Delay-ON Timer
Timer Function OFF-Delay
Time
Delay-OFF Timer
PI Mode Setting
PI Mode
Delay Timers
Used in conjunction with a multi-function digital input and a multifunction digital output. This sets the amount of time between when the digital input is closed, and the digital output is energized.
Used in conjunction with a multi-function digital input and a multifunction digital output. This sets the amount of time the output stays energized after the digital input is opened.
PI Control
This parameter enables / disables the closed loop (PI) controller.
0: Disabled
1: Enabled (commanded speed becomes PI setpoint)
3: Fref+PI b5-02
!
b5-03
!
b5-04
!
b5-06
!
b5-07
!
Proportional Gain Setting
P Gain
Integral Time Setting
PI I Time
Integral Limit Setting
PI I Limit
PI Output Limit
PI Limit
PI Offset Adjustment
PI Offset
Sets the proportional gain of the PI controller.
Sets the integral time for the PI controller. A setting of zero disables integral control.
Sets the maximum output possible from the integrator. Set as a % of fmax.
Sets the maximum output possible from the entire PI controller.
Set as a % of fmax.
Sets the amount of offset of the output of the PI controller. Set as a
% of fmax.
The PI Offset Adjustment parameter has two different uses. Parameter b5-07 serves different functions depending on whether it is used on a standard PI loop or a Differential PI loop.
1: Parameter b5-07 causes an offset to be applied to the output of the PI function in a non-Differential PI loop. Every time the PI output is updated, the offset is summed with the PI output. This can be used to artificially kick-start a slow starting PI loop.
2: If the Drive is configured for Differential PI Regulation
(H3-09=16), then the PI Offset is the targeted maintained differential between the signal measured on analog input A1 and the signal measured on analog input A2.
b5-08
!
PI Primary Delay Time
Constant
PI Delay Time
Sets the amount of time for a filter on the output of the PI controller.
b5-09
PI Output Level Selection
Output Level Sel
Determines whether the PI controller will be direct or reverse acting.
0: Normal Output (direct acting)
1: Reverse Output (reverse acting)
!Denotes that parameter can be changed when the Drive is running.
Parameters A - 5
Setting
Range
0 to 3
0 to 200
0.1 to 10.0
0.0 to
20.0sec
0 or 1
0.0 to
3000.0
0.0 to
3000.0
0, 1, 3
0.00 to
25.00
0.0 to 360.0
0.0 to
100.0
0.00 to
100.0
–100.0 to
+100.0
0.00 to
10.00
0 or 1
Factory
Setting
2
120%
2.0sec
0.2sec
1
0.0sec
0.0sec
0
2.00
5.0sec
100%
100.0%
0.0%
0.00sec
0
Menu
Location
Programming
Programming
Programming
Programming
Programming
Programming
Programming
Quick Setting
Quick Setting
Quick Setting
Quick Setting
Quick Setting
Quick Setting
Quick Setting
Quick Setting
Table 1: Parameter List (Continued)
Parameter
No.
b5-10
Parameter Name
Digital Operator Display
PI Output Gain Setting
Output Gain
b5-11
PI Output Reverse Selection
Output Rev Sel
Description
Sets the output gain of the PI controller.
0: 0 limit (when PI output goes negative Drive stops)
1: Reverse (when PI goes negative Drive reverses)
0 limit automatic when reverse prohibit is selected using b1-04 b5-12 b5-13 b5-14 b5-15 b5-16 b5-17 b5-18 b5-19
Setting
Range
0.0 to 25.0
Factory
Setting
1.0
Menu
Location
Quick Setting
0 or 1
PI Feedback Reference
Missing Detection Selection
Fb los Det Sel
0: Disabled
1: Alarm
2: Fault
0 to 2
PI Feedback Loss Detection
Level
Fb los Det Lvl
PI Feedback Loss Detection
Time
Fb los Det Time
Sleep Function Start
Level
Sleep Level
Sleep Delay Time
Sleep Time
PI Accel/Decel Time
PI Acc/Dec Time
PI Setpoint Selection
PI Setpoint Sel
PI Setpoint Value
PI Setpoint
Sets the PI feedback loss detection level as a percentage of maximum frequency (E1-04).
Sets the PI feedback loss detection delay time in terms of seconds.
Sets the sleep function start frequency.
Sets the sleep function delay time in terms of seconds.
Applies an accel/decel time to the PI setpoint reference.
0: Disabled
1: Enabled
*Depends on b5-20.
0 to 100
0.0 to 25.5
0.0 to 200.0
0.0 to 25.5
0.0 to 25.5
0 or 1
0.00 to
100.00
0
0
0%
1.0sec
0.0Hz
0.0sec
0.0sec
0
0.00%
Quick Setting
Quick Setting
Quick Setting
Quick Setting
Quick Setting
Quick Setting
Quick Setting
Quick Setting
Quick Setting b5-20 b5-21
PI Setpoint Display Scaling
Setpoint Scaling
Set display/setting unit of b5-19.
PI Sleep Input Source
PI Sleep Source
PI Snooze Level
Snooze Level
Input Source Selection for Sleep function Mode.
0: PI Input
1: PI Setpoint
2: Snooze
Sets the PI snooze function start level as a percentage of maximum frequency (E1-04).
0 to 39999
0 to 2
0 to 100 b5-22
!
b5-23 b5-24
PI Snooze Delay Time
Snooze Delay Time
Sets the PI snooze function delay time in terms of seconds.
PI Snooze Deactivation Level
Wake-Up Level
When the PI feedback drops below this level, normal PI operation starts again. Set as a percentage of maximum frequency (E1-04).
0 to 3600
0 to 100 b5-25 b5-26
PI Setpoint Boost Setting
Setpoint Boost
PI Maximum Boost Time
Max Boost Time
Temporary increase of PI setpoint to create an overshoot of the intended PI setpoint.
Sets a time limitation for reaching temporarily boosted PI setpoint
(intended PI setpoint + b5-25).
b5-27
PI Snooze Feedback Level
Snooze Feedback
PI snooze mode will be activated when PI feedback is above this level. Set as a percentage of maximum frequency (E1-04).
b5-28 b5-29
PI Feedback Square Root
Function Selection
PI Feedback SqRt
PI Square Root Gain
PI Fb SqRt Gain
0: Disabled
1: Enabled
A multiplier applied to the square root of the feedback.
b5-30
Output Square Root
Monitor Selection
PI Out Moni SqRt
0: Disabled
1: Enabled
!Denotes that parameter can be changed when the Drive is running.
0 to 100
0 to 3600
0 to 100
0 or 1
0.00 to 2.00
0 or 1
1
1
0%
0sec
0%
0%
0sec
60%
0
1.00
0
Quick Setting
Quick Setting
Quick Setting
Quick Setting
Quick Setting
Quick Setting
Quick Setting
Quick Setting
Quick Setting
Quick Setting
Quick Setting
Parameters A - 6
Table 1: Parameter List (Continued)
Parameter
No.
Parameter Name
Digital Operator Display
b8-01 b8-04 b8-05 b8-06
C1-01
!
C1-02
!
C1-03
!
C1-04
!
Description
Energy Saving Control
Selection
Energy Save Sel
Energy Saving Coefficient
Value
Energy Save COEF
Power Detection Filter Time
kW Filter Time
Search Operation Voltage
Limit
Search V Limit
Energy Saving
Energy Savings function enable/disable selection
0: Disabled
1: Enabled
Used to fine-tune the energy savings function.
Accel / Decel
Sets the time to accelerate from zero to maximum frequency.
Acceleration Time 1
Accel Time 1
Deceleration Time 1
Decel Time 1
Acceleration Time 2
Accel Time 2
Deceleration Time 2
Decel Time 2
Sets the time to decelerate from maximum frequency to zero.
Sets the time to accelerate from zero to maximum frequency when selected via a multi-function input.
Sets the time to decelerate from maximum frequency to zero when selected via a multi-function input.
C1-09
Fast Stop Time
Fast Stop Time
Sets the time to decelerate from maximum frequency to zero for the "Fast Stop" function.
C1-11
Accel/Decel
Switch Frequency
Acc/Dec SW Freq
Sets the frequency for automatic switching of accel / decel times.
Fout < C1-11: Accel/Decel Time 2
Fout >= C1-11: Accel/Decel Time 1
Multi-function input "Multi-Acc/Dec 1" has priority over C1-11.
S-Curve Acc/Dec
Setting
Range
Factory
Setting
0 or 1
0.0 to
655.00
0 to 2000
0 to 100
0.0
to
6000.0
0.0
to
6000.0
0.0 to
200.0
0 kVA
Dependent
Programming
20ms Programming
0%
30.0sec
30.0sec
30.0sec
30.0sec
10.0sec
0.0Hz
Menu
Location
Quick Setting
Programming
Quick Setting
Quick Setting
Programming
Programming
Programming
Programming
S-curve is used to further soften the starting ramp.
The longer the S-curve time, the softer the starting ramp.
C2-01
S-Curve Characteristic at
Accel Start
SCrv Acc @ Start
0.00 to
2.50
0.20sec
Programming
Run command
ON
Output frequency
C2-02
OFF
C2-02
S-Curve Characteristic at
Accel End
SCrv Acc @ End
C2-01
0.00 to 2.50
0.20sec
Programming
Time
!Denotes that parameter can be changed when the Drive is running.
Parameters A - 7
Table 1: Parameter List (Continued)
Parameter
No.
Parameter Name
Digital Operator Display
C4-01
!
C4-02
Torque Compensation Gain
Torq Comp Gain
Torque Compensation
Primary Delay Time
Torq Comp Time
Description
Setting
Range
Torque Comp
This parameter helps to produce better starting torque. It determines the amount of torque or voltage boost based upon motor current and motor resistance.
This parameter adjusts a filter on the output of the torque compensation function. Increase to add torque stability, decrease to improve torque response.
0.00 to 2.50
0 to 10000
Factory
Setting
1.00
200ms
Menu
Location
Programming
Programming
C6-02
Carrier Frequency Selection
CarrierFreq Sel
Carrier Freq
Carrier frequency sets the number of pulses per second of the output voltage waveform.
0: Low Noise (Carrier frequency is randomly moduled for lower audible noise)
1: Fc = 2.0 kHz
2: Fc = 5.0 kHz
3: Fc = 8.0 kHz
4: Fc = 10.0 kHz
5: Fc = 12.5 kHz
6: Fc = 15.0 kHz
F: Program (Determined by the settings of C6-03 thru C6-05)
C6-03
C6-04
Carrier Frequency Upper
Limit
CarrierFreq Max
Carrier Frequency Lower
Limit
CarrierFreq Min
Carrier Frequency Proportional Gain
CarrierFreq Gain
Maximum carrier frequency allowed when C6-02 = F.
Minimum carrier frequency allowed when C6-02 = F.
C6-05 d1-01
!
d1-02
!
d1-03
!
d1-04
!
Frequency Reference 1
Reference 1
Frequency Reference 2
Reference 2
Frequency Reference 3
Reference 3
Frequency Reference 4
Reference 4
Sets the relationship of output frequency to carrier frequency when
C6-02 = F.
Preset Reference
Digital preset speed command 1. Used when b1-01 = 0 and when in "hand" mode. Setting units are affected by o1-03.
Digital preset speed command 2. Selected via multi-function input terminals. Setting units are affected by o1-03.
Digital preset speed command 3. Selected via multi-function input terminals. Setting units are affected by o1-03.
Digital preset speed command 4. Selected via multi-function input terminals. Setting units are affected by o1-03.
d1-17
!
Jog Frequency Reference
Jog Reference
Speed command used when a jog is selected via multi-function input terminals. Setting units are affected by o1-03.
!Denotes that parameter can be changed when the Drive is running.
0 to F kVA
Dependent
Programming
0.4 to 15.0
kHz kVA
Dependent
Programming
0.4 to 15.0
kHz kVA
Dependent
Programming
0 to 99
0.00 to
E1-04
Value
0.00 to
E1-04
Value
0
0.00Hz
0.00Hz
0.00Hz
0.00Hz
6.00Hz
Programming
Programming
Programming
Programming
Programming
Programming
Parameters A - 8
Table 1: Parameter List (Continued)
Parameter
No.
Parameter Name
Digital Operator Display
d2-01 d2-02 d2-03 d3-01 d3-02 d3-03 d3-04 d4-01 d4-02
Description
Setting
Range
Frequency Reference Upper
Limit
Ref Upper Limit
Frequency Reference Lower
Limit
Ref Lower Limit
Master Speed Reference
Lower Limit
Ref1 Lower Limit
Reference Limits
Determines maximum speed command, set as a percentage of parameter E1-04. If speed command is above this value, actual
Drive speed will be limited to this value. This parameter applies to all speed command sources.
Determines minimum speed command, set as a percentage of parameter E1-04. If speed command is below this value, actual
Drive speed will be set to this value. This parameter applies to all speed command sources.
Determines the minimum speed command, set as a percentage of parameter E1-04. If speed command is below this value, actual
Drive speed will be set to this value. This parameter only applies to analog inputs A1 and A2.
Jump Frequencies
0.0 to 110.0
0.0 to 110.0
0.0 to 110.0
Jump Frequency 1
Jump Freq 1
Jump Frequency 2
Jump Freq 2
Jump Frequency 3
Jump Freq 3
Jump Frequency Width
Jump Bandwidth
MOP Ref Memory
Trim Control Level
Trim Control Lvl
These parameters allow programming of up to three prohibited frequency points for eliminating problems with resonant vibration of the motor / machine. This feature does not actually eliminate the selected frequency values, but will accelerate and decelerate the motor through the prohibited bandwidth.
0.0 to 200.0
This parameter determines the width of the deadband around each selected prohibited frequency point. A setting of "1.0" will result in a deadband of +/- 1.0 Hz.
Sequence
0: Disabled
1: Enabled
Set the percentage of maximum speed to be added or subtracted via multi-function inputs.
0.0 to 20.0
0 or 1
0 to 100
Factory
Setting
100.0%
0.0%
0.0%
0.0Hz
0.0Hz
0.0Hz
1.0Hz
0
10%
Menu
Location
Quick Setting
Quick Setting
Programming
Programming
Programming
Programming
Programming
Programming
Programming
Parameters A - 9
E1-11
E1-12
E1-13
Mid Output Frequency B
Mid Frequency B
Mid Output Voltage B
Mid Voltage B
Base Voltage
Base Voltage
Table 1: Parameter List (Continued)
Parameter
No.
Parameter Name
Digital Operator Display
E1-01
E1-03
E1-04
E1-05
E1-06
E1-07
E1-08
E1-09
E1-10
Description
Setting
Range
V/F Pattern
Input Voltage Setting
Input Voltage
Set to the nominal voltage of the incoming line.
155 to 255.0
(240V)
310 to 510.0
(480V)
V/F Pattern Selection
V/F Selection
0: 50Hz
1: 60 Hz Saturation
2: 50 Hz Saturation
3: 72 Hz
4: 50 Hz VT1
5: 50 Hz VT2
6: 60 Hz VT1
7: 60 Hz VT2
8: 50 Hz HST1
9: 50 Hz HST2
A: 60 Hz HST1
B: 60 Hz HST2
C: 90 Hz
D: 120 Hz
E: 180 Hz
F: Custom V/F
FF: Custom w/o limit
Maximum Output Frequency
Max Frequency
Maximum Output Voltage
Max Voltage
Output voltage (V)
VMAX
(E1-05)
VBASE
(E1-13)
Base Frequency
Base Frequency
Mid Output Frequency A
Mid Frequency A
VA
(E1-08)
Mid Output Voltage A
Mid Voltage A
Minimum Output Frequency
Min Frequency
Mid Output Voltage
Min Voltage
VMIN
(E1-10)
FMIN FA FBASE FMAX
(E1-09) (E1-07) (E1-06) (E1-04)
Frequency (Hz)
To set V/f characteristics in a straight line, set the same values for
E1-07 and E1-09. In this case, the setting for E1-08 will be disregarded.
Always ensure that the four frequencies are set in the following manner:
E1-04 (FMAX)
≥
E1-06 (FA) > E1-07 (FB)
≥
E1-09 (FMIN)
0 to FF
0.0 to
200.0
0 to 255.0
(240V)
0 to 510.0
(480V)
0.0 to
200.0
0.0 to 200.0
0 to 255.0
(240V)
0 to 510.0
(480V)
0.0 to 200.0
0 to 255.0
(240V)
0 to 510.0
(480V)
Factory
Setting
240V
480V
F
60.0Hz
240V
480V
60.0Hz
3.0Hz
18.0VAC
1.5Hz
10.8VAC
Menu
Location
Quick Setting
Programming
Programming
Programming
Programming
Programming
Programming
Programming
Programming
Set only when V/f is finely adjusted at rated output range.
Adjustment is not normally required.
0.0 to
200.0
0 to 255.0
(240V)
0 to 510.0
(480V)
0 to 255.0
(240V)
0 to 510.0
(480V)
0.0Hz
0.0VAC
0.0VAC
Programming
Programming
Programming
Parameters A - 10
Table 1: Parameter List (Continued)
Parameter
No.
Parameter Name
Digital Operator Display
E2-01
E2-03
E2-05
F6-01
F6-02
F6-03
F6-05
Description
Motor Setup
Setting
Range
Factory
Setting
Menu
Location
Motor Rated Current
Motor Rated FLA
Set to the motor nameplate full load amps.
No-Load Current
Sets the magnetizing current of the motor.
Motor Line-to-Line
Resistance
Term Resistance
Operation Selection after
Communication Error
Com Bus Flt Sel
Phase to phase motor resistance, normally set by the autotuning routine.
Com OPT Setup
Sets the stopping method for option PCB communications error
(BUS fault). Active only when a communications option PCB is installed and when b1-01 or b1-02 = 3.
0: Ramp to Stop
1: Coast to Stop
2: Fast-Stop
3: Alarm Only
Input Level of External Fault from Communication Option
Card
EF0 Detection
Stopping Method for
External Fault from
Communication Option Card
EF0 Fault Action
Current Monitor Display Unit
Selection
Current Unit Sel
0: Always detected
1: Detected only during operation
0: Ramp to Stop
1: Coast to Stop
2: Fast-Stop
3: Alarm Only
0: A Display
1: 100%/8192 (Drive Rated Current)
10% to
200% kVA
Dependent
Quick Setting kVA
Dependent
0.000 to
65.000
kVA
Dependent
9.842
Ω
Programming
Programming
0 to 3
0 or 1
0 to 3
0 or 1
1
0
1
0
Quick Setting
Programming
Programming
Programming
Parameters A - 11
Parameter
No.
Parameter Name
Digital Operator Display
H1-01
Terminal S3 Function
Selection
Terminal S3 Sel
H1-02
Terminal S4 Function
Selection
Terminal S4 Sel
Table 1: Parameter List (Continued)
Description
Digital Inputs
Setting
Range
Factory
Setting
Menu
Location
0: 3-wire control
FWD/REV selection for 3-wire sequence
1: Local/Remote Sel
Hand/Auto Selection - Closed = Hand, Open = Auto
2: Option/Inv Sel
Selects source of speed command and sequence
Closed = Option Card, Open = b1-01 & b1-02
3: Multi-Step Ref 1
Closed = speed command from d1-02 or Aux Terminal
Open = speed command determined by b1-01
4: Multi-Step Ref 2
Closed = speed command from d1-03 or d1-04
Open speed command determined by b1-01
6: Jog Freq Ref
Closed = speed command from d1-17
Open = speed command determined by b1-01
7: Multi-Acc/Dec 1
Closed = Accel & Decel Ramps determined by C1-03 & C1-04
Open = Accel & Decel Ramps determined by C1-01 & C1-02
8: Ext BaseBlk N.O.
Closed = Output transistors forced off, Open = Normal operation
9: Ext BaseBlk N.C.
Closed = Normal Operation, Open = Output transistors forced
off
A: Acc/Dec RampHold
Closed = Acceleration suspended and speed held, Open =
Normal Operation
C: Term A2 Enable
Closed = Terminal A2 is active, Open = Terminal A2 is disabled
F: Term Not Used
Terminal has no effect
10: MOP Increase
Closed = Speed Command Increases, Open = Speed Command
Held.
Must be set in conjunction with MOP Decrease and b1-02 must be set to 1.
11: MOP Decrease
Closed = Speed Command Decreases, Open = Speed Command
Held.
Must be set in conjunction with MOP Increase and b1-02 must
be set to 1.
(Continued on next page)
0 to 6E
0 to 6E
24 Programming
14 Programming
Parameters A - 12
Table 1: Parameter List (Continued)
Parameter
No.
Parameter Name
Digital Operator Display
H1-03
Terminal S5 Function
Selection
Terminal S5 Sel
Description
12: Forward Jog
Closed = Drive runs forward at speed command entered into parameter d1-17.
13: Reverse Jog
Closed = Drive runs in reverse at speed command entered into parameter d1-17.
14: Fault Reset
Closed = Resets the Drive after the fault and the run
command have been removed.
15: Fast-Stop N.O.
Closed = Drive decelerates using C1-09, regardless of run command status.
17: Fast-Stop N.C.
Closed = Normal operation
Open = Drive decelerates using C1-09, regardless of run command status.
18: Timer Function
Input for independent timer, controlled by b4-01 and b4-02.
Used in conjunction with a multi-function digital output.
19: PI Disable
Turns off the PI controller, and PI setpoint becomes speed command.
1B: Program Lockout
Closed =All parameter settings can be changed.
Open = Only speed command at U1-01 can be changed.
1C: TrimCtl Increase
Closed = Increase motor speed by value in d4-02.
Open = Return to normal speed command.
Not effective when using d1-01 thru d1-04 as a speed command.
Must be used in conjunction with Trim Ctrl Decrease.
1D: Trim Ctl Decrease
Closed = Decrease motor speed by value in d4-02.
Open = Return to normal speed command.
Not effective when using d1-01 thru d1-04 as speed command.
Must be used in conjunction with Trim Ctrl Increase.
Setting
Range
Factory
Setting
Menu
Location
0 to 6E
3: 2-wire
0: 3-wire
Programming
Parameters A - 13
Parameter
No.
Parameter Name
Digital Operator Display
H1-04
Terminal S6 Function
Selection
Terminal S6 Sel
H1-05
Terminal S7 Function
Selection
Terminal S7 Sel
Table 1: Parameter List (Continued)
Description
Digital Inputs
Setting
Range
Factory
Setting
Menu
Location
1E: Ref Sample Hold
Analog speed command is sampled then held at time of input closure.
20: External fault, Normally Open, Always Detected, Ramp To
Stop
21: External fault, Normally Closed, Always Detected, Ramp To
Stop
22: External fault, Normally Open, During Run, Ramp To Stop
23: External fault, Normally Closed, During Run, Ramp To Stop
24: External fault, Normally Open, Always Detected, Coast To
Stop
25: External fault, Normally Closed, Always Detected, Coast To
Stop
26: External fault, Normally Open, During Run, Coast To Stop
27: External fault, Normally Closed, During Run, Coast To Stop
28: External fault, Normally Open, Always Detected, Fast-Stop
29: External fault, Normally Open, Always Detected, Fast-Stop
2A: External fault, Normally Open, During Run, Fast-Stop
2B: External fault, Normally Closed, During Run, Fast-Stop
2C: External fault, Normally Open, Always Detected, Alarm Only
2D: External fault, Normally Closed, Always Detected, Alarm
Only
2E: External fault, Normally Open, During Run, Alarm Only
2F: External fault, Normally Closed, During Run, Alarm Only
34: PI SFS Cancel
36: Option/Inv Sel 2 Selects source of speed command and
sequence
Closed = b1-01 & b1-02, Open = Option Card
60: Motor Preheat Applies current to create heat to avoid
condensation.
Closed = Apply amount of current as set in parameter b2-09
61: Speed Search 1
When closed as a run command is given, Drive does a speed
search starting at maximum frequency (E1-04).
(Current detection)
62: Speed Search 2
When closed as a run command is given, Drive does a speed
search starting at speed command. (Current detection).
64: Speed Search 3
67: Com Test Mode - Used to test RS-485/422 interface.
68: High Slip Braking - Closed = Drive stops using High Slip
Braking regardless of run command status.
69: Jog2 - Closed = Drive runs at speed command entered into
parameter d1-17.
Direction determined by fwd/rev input. 3-wire control Only.
6A: Drive Enable - Closed = Drive will accept run command.
Open = Drive will not run. If running, Drive will stop per b1-03.
6B: Com/Inv Sel - Selects source of speed command and sequence
Closed = Serial Communication (R+,R-,S+,S-), Open = b1-01
& b1-02
6C: Com/Inv Sel 2
6D: Auto Mode Sel - Hand/Auto Selection - Closed = Auto,
Open = Hand
6E: Hand Mode Sel - Hand/Auto Selection - Closed = Hand,
Open = Auto
70: Bypass Drv Enbl
0 to 6E
0 to 6E
4: 2-wire
3: 3-wire
Programming
6: 2-wire
4: 3-wire
Programming
Parameters A - 14
Table 1: E7 User Parameter List (Continued)
Parameter
No.
Parameter Name
Digital Operator
Display
H2-01
H2-02
Description
Digital Outputs
Setting
Range
Factory
Setting
Menu
Location
Terminal M1-M2 Function
Selection
Term M1-M2 Sel
Terminal M3-M4 Function
Selection
Term M3-M4 Sel
0: During RUN 1 = Closed when a run command is input
or the Drive is outputting voltage.
1: Zero Speed = Closed when Drive output frequency is less
than Fmin (E1-09)
2: Fref/Fout Agree 1 = Closed when Drive output speed
equals the speed command within the bandwidth of
L4-02.
3: Fref/Set Agree 1 = Closed when the Drive output speed
and the speed command are equal to the value in L4-01
within the bandwidth of L4-02.
4: Freq Detect 1 = Closed when the Drive output speed is
less than or equal to the value in L4-01, with hysteresis
determined by L4-02.
5: Freq Detect 2 = Closed when the Drive output speed
is greater than or equal to the value in L4-01, with
hysteresis determined by L4-02.
6: Inverter Ready = Closed when the Drive is not in a fault
state, and not in program mode.
7: DC Bus Undervolt = Closed when the DC bus voltage
falls below the UV trip level (L2-05)
8: Base Blk 1 = Closed when the Drive is not outputting
voltage.
9: Option Reference = Closed when the speed command is
coming from the digital operator.
A: Remote/Auto Oper = Closed when the run command is
coming from the digital operator.
B: Trq Det 1 N.O. - Closes when the output current exceeds
the value set in parameter L6-02 for more time than is set
in parameter L6-03.
C: Loss of Ref - Closes when the Drive has detected a loss
of analog speed command.
Speed command is considered lost when it drops 90% in
0.4 seconds.
Parameter L4-05 determines Drive reaction to a loss of
speed command.
E: Fault - Closes when the Drive experiences a major fault.
F: Not Used
10: Minor Fault - Closes when Drive experiences a minor fault or alarm.
11: Reset Cmd Active - Closes when the Drive receives a reset command from terminals or serial comms.
12: Timer Output - Output for independent timer, controlled
by b4-01 and b4-02.
Used in conjunction with a multi-function digital input.
17: Trq. Det 1 N.C. - Opens when the output current
exceeds the value set in parameter
L6-02 for more time than is set in parameter L6-03.
1A: Reverse Dir - Closes when the Drive is running in the reverse direction.
1E: Restart Enabled - Closes when the Drive is performing
an automatic restart.
Automatic restart is configured by parameter L5-01.
1F: Overload (OL1) - Closes before a motor overload
occurs. (90% of OL1 time)
20: OH Prealarm - Closes when the Drive’s heatsink
temperature exceeds the setting
of parameter L8-02.
38: Drive Enable - Closes when the Drive enable input is active.
39: Waiting to Run - Closes during the time after a run command is issued, but the Drive is not running due to the time set in parameter b1-10.
3A: OH Freq Reduce
3B: Run Src Com/Opt
0 to 3B
0 to 3B
0
A
Programming
Programming
Parameters A - 15
Table 1: Parameter List (Continued)
Parameter
No.
Parameter Name
Digital Operator Display
Description
Analog Inputs
H3-02
!
H3-03
!
H3-08
H3-09
Terminal A1 Gain Setting
Terminal A1 Gain
Terminal A1 Bias Setting
Terminal A1 Bias
Terminal A2 Signal Level
Selection
Term A2 Signal
Aux Terminal Function Selection
Terminal A2 Sel
Sets the speed command when 10V is input, as a percentage of the maximum output frequency (E1-04).
Sets the speed command when 0V is input, as a percentage of the maximum output frequency (E1-04).
Selects the signal level of terminal A2.
0: 0 - 10VDC (switch S1-2 must be in the off position)
2: 4 - 20 mA (switch S1-2 must be in the on position)
Selects what effect the aux terminal has on the Drive.
0: Frequency Bias - 0 - 100% bias
2: Aux Reference
B: PI Feedback
D: Frequency Bias 2 - 0 - 100% bias
E: Motor Temperature - See parameters L1-03 & L1-04
16: PI Differential
1F: Not Used
H3-10
!
H3-11
!
Terminal A2 Gain Setting
Terminal A2 Gain
Terminal A2 Bias Setting
Terminal A2 Bias
Sets the percentage when 10V (20mA) is input.
Sets the percentage when 0V (4mA) is input.
H3-12
Analog Input Filter Time Constant
Filter Avg Time
Used to "smooth" out erratic or noisy analog input signals.
H3-13
Master Frequency Reference
Terminal Selection
TA1/A2 Select
Determines which terminal will be the main reference source.
0: Main Fref TA1 - Terminal TA1 is the main speed command and Terminal TA2 is the Aux speed
command.
1: Main Fref TA2 - Terminal TA2 is the main speed command and Terminal TA1 is the Aux speed command.
Only effective when H3-09 is set to 2 "Aux Reference".
!Denotes that parameter can be changed when the Drive is running.
Setting
Range
Factory
Setting
0.0 to
1000.0
–100.0 to
+100.0
0 or 2
0 to 1F
0.0 to
1000.0
–100.0 to
+100.0
0.00 to
2.00
0 or 1
100.0%
0.0%
2
2
100.0%
0.0%
0.30sec
0
Menu
Location
Quick Setting
Quick Setting
Programming
Programming
Quick Setting
Quick Setting
Programming
Programming
Parameters A - 16
Table 1:
Parameter List (Continued
)
Parameter
No.
Parameter Name
Digital Operator Display
Description
Analog Outputs
H4-01
H4-02
!
H4-03
!
H4-04
Terminal FM Monitor Selection
Terminal FM Sel
Terminal FM Gain Setting
Terminal FM Gain
Terminal FM Bias Setting
Terminal FM Bias
Terminal AM Monitor Selection
Terminal AM Sel
Selects which monitor will be output on terminals FM and AC.
1: Frequency Ref (100% = max. output frequency)
2: Output Freq (100% = max. output frequency)
3: Output Current (100% = Drive rated current)
6: Output Voltage (100% = 230V or 100% = 460V)
7: DC Bus Voltage (100% = 400V or 100% = 800V)
8: Output kWatts (100% = Drive rated power)
15: Term A1 Level
16: Term A2 Level
18: Mot SEC Current (100% = Motor rated secondary current)
20: SFS Output (100% = max. output frequency)
24: PI Feedback
31: Not Used
36: PI Input
37: PI Output (100% = max. output frequency)
38: PI Setpoint
51: Auto Mode Fref (100% = max. output frequency)
52: Hand Mode Fref (100% = max. output frequency)
53: PI Feedback 2
NOTE: 100% = 10V DC output * FM gain setting
(H4-02).
Sets terminal FM output voltage (in percent of 10V) when selected monitor is at 100% output.
Sets terminal FM output voltage (in percent of 10V) when selected monitor is at 0% output.
Selects which monitor will be output on terminals AM and AC.
1: Frequency Ref (100% = max. output frequency)
2: Output Freq (100% = max. output frequency)
3: Output Current (100% = Drive rated current)
6: Output Voltage (100% = 230V or 100% = 460V)
7: DC Bus Voltage (100% = 400V or 100% = 800V)
8: Output kWatts (100% = Drive rated power)
15: Term A1 Level
16: Term A2 Level
18: Mot SEC Current (100% = Motor rated secondary current)
20: SFS Output (100% = max. output frequency)
24: PI Feedback
31: Not Used
36: PI Input
37: PI Output (100% = max. output frequency)
38: PI Setpoint
51: Auto Mode Fref (100% = max. output frequency)
52: Hand Mode Fref (100% = max. output frequency)
53: PI Feedback 2
NOTE: 100% = 10V DC output * AM gain setting
(H4-05).
H4-05
!
Terminal AM Gain Setting
Terminal AM Gain
Sets terminal AM output voltage (in percent of 10V) when selected monitor is at 100% output.
!Denotes that parameter can be changed when the Drive is running.
Setting
Range
Factory
Setting
Menu
Location
1 to 53
0.0 to
1000.0
–110.0 to
110.0
1 to 53
0.0 to
1000.0
2
100.0%
0.0%
8
50.0%
Programming
Programming
Programming
Programming
Programming
Parameters A - 17
Table 1:
Parameter List (Continued
)
Parameter
No.
Parameter Name
Digital Operator Display
Description
H4-06
!
H4-07
Terminal AM Bias Setting
Terminal AM Bias
Terminal FM Signal Level
Selection
AO Level Select1
Analog Outputs
Sets terminal AM output voltage (in percent of 10V) when selected monitor is at 0% output.
0: 0 - 10 VDC
2: 4-20 mA*
H4-08
H5-01
H5-02
H5-03
H5-04
H5-05
H5-06
H5-07
Terminal AM Signal Level
Selection
AO Level Select2
Drive Node Address
Serial Com Adr
Communication Speed Selection
Serial Baud Rate
Communication Parity Selection
Serial Com Sel
Stopping Method after
Communication Error
Serial Fault Sel
Communication Error Detection
Selection
Serial Flt Dtct
Drive Transmit Wait Time
Transmit WaitTIM
RTS Control Selection
RTS Control Sel
0: 0 - 10 VDC
2: 4-20 mA*
* An analog output of 4 - 20 mA can not be used with the standard terminal board. Therefore an optional terminal board (with shunt connector CN15) is needed.
Serial Com Setup
Selects Drive station node number (address) for terminals R+, R-, S+, S-.*
Note: An address of “0” disables serial com.
Selects the baud rate for terminals R+, R-, S+ and S-.*
0: 1200 Baud
1: 2400 Baud
2: 4800 Baud
3: 9600 Baud
4: 19200 Baud
Selects the communication parity for terminals R+, R-,
S+ and S-.*
0: No Parity
1: Even Parity
2: Odd Parity
Selects the stopping method when a communication error is detected.
0: Ramp to Stop
1: Coast to Stop
2: Fast-Stop
3: Alarm Only
4: Runn at D1-04
Enables or disables the communications timeout detection function.
0: Disabled - A communications loss will NOT cause a communications fault.
1: Enabled - If communications are lost for more than the time specified in parameter H5-09, a communications fault will occur.
Sets the time from when the Drive receives data to when the Drive sends data.
Enables or disables “request to send” (RTS) control:
0: Disabled (RTS is always on)
1: Enabled (RTS turns on only when sending)
Selects the communication protocol.
0: Memobus (Modbus) H5-08
Communication Protocol Selection
Protocol Select
H5-09
Communication Error
Detection Time
CE Detect Time
Determines how long communications must be lost before a fault is annunciated. Works in conjunction with parameters H5-05 and H5-04.
!Denotes that parameter can be changed when the Drive is running.
* After these parameters are changed, Drive power must be cycled before the changes will take effect.
Setting
Range
–110.0 to
110.0
0 or 2
0 or 2
0 to FF(hex,
H5-08 dependent)
0 to 4
0 to 2
0 to 3
0 or 1
5 to 65
0 or 1
0
0.0 to 10.0
Factory
Setting
0.0%
0
0
1F
3
0
3
1
5ms
1
0
2.0sec
Menu
Location
Programming
Programming
Programming
Programming
Programming
Programming
Programming
Programming
Programming
Programming
Programming
Programming
Parameters A - 18
Parameter
No.
L1-01
L1-02
L1-03
L1-04
L1-05
L2-01
L2-02
L2-03
L2-04
L2-05
Table 1:
Parameter List (Continued
)
Parameter Name
Digital Operator Display
Motor Overload Protection
Selection
MOL Fault Select
Motor Overload Protection
Time
MOL Time Const
Motor Overheat Alarm Operation
Selection
Mtr OH Alarm Sel
Motor Overheat Fault Operation
Selection
Mtr OH Fault Sel
Setting
Range
0 to 1
0.1 to 20.0
0 to 3
0 to 2
Factory
Setting
1
8.0min
3
1
Motor Temperature Input Filter
Time
Mtr Temp Filter
Delay Time applied to motor temperature analog input
(H3-09=E) for filtering purposes.
0.00 to
10.00
0.20sec
Momentary Power Loss Detection
Selection
PwrL Selection
Momentary Power Loss Ride-thru
Time
PwrL Ridethru t
Momentary Power Loss Minimum Base Block Time
PwrL Baseblock t
PwrLoss Ridethru
Enables and disables the momentary power loss function.
0: Disabled - Drive trips on (UV1) fault when power is lost.
1: PwrL Ride Thru t - Drive will restart if power returns within the time set in L2-02.*
2: CPU Power Active - Drive will restart if power returns prior to internal power supply shut down.*
* In order for a restart to occur, the run command must be maintained throughout the ride thru period.
Determines the power loss ride-thru time. This value is dependent on the capacity of the Drive. Only effective when L2-01 = 1.
Used to allow the residual motor voltage to decay before the Drive output turns back on. After a power loss, if L2-03 is greater than L2-02, operation resumes after the time set in L2-03.
0 to 2
0.0 to
25.5sec
0.1 to 5.0sec
2 kVA
Dependent kVA
Dependent
Momentary Power Loss Voltage
Recovery Ramp Time
PwrL V/F Ramp t
Undervoltage Detection
Level
PUV Det Level
Description
Motor Overload
Enables or disables the motor thermal overload protection.
0: Disabled
1: Std Fan Cooled (Enabled)
Determines how much time will elapse prior to a motor overload fault (OL1), when motor amps exceed the value set in parameter E2-01 by 10%. Actual (OL1) trip time will vary depending on severity of overload.
Operation selection when the motor temperature analog input (H3-09=E) exceeds the OH3 alarm level (1.17V)
0: Ramp to Stop
1: Coast to Stop
2: Fast-Stop
3: Alarm Only
Stopping method when the motor temperature analog input (H3-09=E) exceeds the OH4 level (2.34V).
0: Ramp to Stop
1: Coast to Stop
2: Fast-Stop
The time it takes the output voltage to return to the preset V/f pattern after speed search (current detection mode) is complete.
Sets the Drive's DC Bus undervoltage trip level. If this is set lower than the factory setting, additional AC input reactance or DC bus reactance may be necessary.
0.0 to 5.0sec
Voltage
Class
Dependent kVA
Dependent
Voltage
Class
Dependent
Menu
Location
Programming
Programming
Programming
Programming
Programming
Quick Setting
Quick Setting
Programming
Programming
Programming
Parameters A - 19
Table 1:
Parameter List (Continued
)
Parameter
No.
L3-01
L3-02
L3-04
L3-05
L3-06
Parameter Name
Digital Operator Display
Stall Prevention Selection During
Accel
StallP Accel Sel
Stall Prevention Level During
Accel
StallP Accel Lvl
Stall Prevention Selection During
Decel
StallP Decel Sel
Stall Prevention Level During
Decel
StallP Run Sel
Stall Prevention Level During
Running
StallP Run Level
Description
Stall Prevention
0: Disabled (Motor accelerates at active acceleration,
C1-01 or C1-03. The motor may stall if load is too heavy or accel time is too short.)
1: General Purpose (When output current exceeds L3-
02 level, acceleration stops. It starts to accelerate at current value recovery.)
2: Intelligent (The active acceleration rate, C1-01 or C1-
02, is ignored. Acceleration is completed in the shortest amount of time w/o exceeding the current value set in L3-02.
This function is enabled when L3-01 is “1” or “2”.
Drive rated current is 100%. Decrease the set value if stalling occurs at factory setting.
0: Disabled (The Drive decelerates at the active
deceleration rate, C1-02 or C1-04. If the load is too large or the deceleration time is too short, an OV fault may occur.)
1: General Purpose (The Drive decelerates at the active deceleration rate, C1-02 or C1-04, but if the main circuit DC bus voltage reaches the stall prevention level the output frequency will clamp. Deceleration will continue once the DC bus level drops below the stall prevention level.)
2: Intelligent (The active deceleration rate is ignored and the Drive decelerates as fast as possible w/o hitting OV fault level.)
3: Stall prev w/R (When using a dynamic braking resistor, be sure to set L3-04 to either “0” or “3”.
Setting “3” will yield a quicker deceleration rate than
“0”.)
0: Disabled (Drive runs a set frequency.) A heavy load may cause the Drive to trip on an OC fault.
1: Decel Time 1 (In order to avoid stalling during heavy loading, the Drive will start to decelerate at Decel time 1 (C1-02) if the output current exceeds the level set by L3-06. Once the current level drops below the
L3-06 level the Drive will accelerate back to its set frequency at the active acceleration rate.)
2: Decel Time 2 (Same as setting 1 except the Drive decelerates at Decel Time 2 (C1-04).)
For 6Hz or less frequency, stall prevention function during run is disabled regardless of L3-05 set.
This function is enabled when L3-05 is “1” or “2”.
Drive rated current is set as 100%.
Normally, changing the setting is not required.
Decrease the set value if stalling occurs at factory setting.
Setting
Range
0 to 2
0 to 200
0 to 3
0 to 2
30 to 200
Factory
Setting
1
120%
1
1
120%
Menu
Location
Programming
Programming
Programming
Programming
Programming
Parameters A - 20
Parameter
No.
L4-01
L4-02
L4-05
L4-06
L5-01
L5-02
L5-03
L6-01
L6-02
L6-03
Parameter Name
Digital Operator Display
Speed Agreement Detection Level
Spd Agree Level
Speed Agreement Detection Width
Spd Agree Width
Frequency Reference Loss
Detection Selection
Ref Loss Sel
Frequency Reference Level at
Loss Frequency
Fref at Floss
Number of Auto Restart Attempts
Num of Restarts
Auto Restart Operation Selection
Restart Sel
Maximum Restart Time After
Fault
Max Restart Time
Torque Detection Selection 1
Torq Det 1 Sel
Torque Detection Level 1
Torq Det 1 Lvl
Torque Detection Time 1
Torq Det 1 Time
Table 1:
Parameter List (Continued
)
Description
Ref Detection
L4-01 and L4-02 are used in conjunction with the multi-function outputs, (H2-01and H2-02) as a setpoint and hysteresis for a contact closure.
Determines how the Drive will react when the frequency reference is lost.
0: Disabled - Drive will not run at the frequency reference
1: Enabled @ % of PrevRef - Drive will run at a percentage (L4-06) of the frequency reference level at the time frequency reference was lost.
If Frequency Reference loss function is enabled
(L4-05=1) and Frequency Reference is lost, then the
Drive will run at reduced frequency reference determined by L4-06. New Fref=Fref at time of loss L4-06.
Fault Restart
Determines the number of times the Drive will perform an automatic restart.
Determines if the fault contact activates during an automatic restart attempt.
0: No Flt Relay - fault contact will not activate during an automatic restart.
1: Flt Relay Active - fault contact will activate during an automatic restart.
If the restart fails (or is not attempted due to a continuing fault condition, e.g. an OV fault) the Drive waits L5-03 seconds before attempting another restart.
Torque Detection
Determines the Drive's response to an overtorque / undertorque condition. Overtorque and Undertorque are determined by the settings in parameters L6-02 and
L6-03.
0: Disabled
1: OL@SpdAgree - Alm (Overtorque Detection only active during Speed Agree and Operation continues after detection)
2: OL At RUN - Alm (Overtorque Detection is always active and operation continues after detection)
3: OL@SpdAgree - Flt (Overtorque Detection only active during Speed Agree and Drive output will shut down on an OL3 fault.)
4: OL At RUN - Flt (Overtorque Detection is always active and Drive output will shut down on an OL3 fault.)
5: UL@SpdAgree - Alm (Undertorque Detection is only active during Speed Agree and operation continues after detection.)
6: UL at RUN - Alm (Undertorque Detection is always active and operation continues after detection.)
7: UL @ SpdAgree - Flt (Undertorque Detection only active during Speed Agree and Drive output will shut down on an OL3 fault.)
8: UL At RUN - Flt (Undertorque Detection is always active and Drive output will shut down on an OL3 fault.)
Sets the overtorque/undertorque detection level as a percentage of Drive rated current.
Sets the length of time an overtorque / undertorque condition must exist before being recognized by the
Drive. OL3 is then displayed.
Setting
Range
0.0 to 200.0
0.0 to 20.0
0 or 1
0 to 100.0%
0 to 10
0 or 1
0.5 to 600.0
0 to 8
0 to 300
0.0 to 10.0
Factory
Setting
0.0Hz
2.0Hz
1
80.0%
0
0
180.0sec
0
15%
10.0sec
Menu
Location
Programming
Programming
Quick Setting
Quick Setting
Quick Setting
Programming
Quick Setting
Quick Setting
Quick Setting
Quick Setting
Parameters A - 21
Parameter
No.
L8-01
L8-02
L8-03
L8-06
L8-09
L8-10
L8-11
L8-12
L8-15
L8-18
L8-19
Parameter Name
Digital Operator Display
Internal Dynamic Braking Resistor Protection Selection
DB Resistor Prot
Overheat Pre-Alarm Level
OH Pre-Alarm Lvl
Overheat Pre-Alarm Operation
Selection
OH Pre-Alarm Sel
Input Phase Loss Detection Level
Ph Loss In Lvl
Output Ground Fault Detection
Selection
Ground Fault Sel
Heatsink Cooling Fan Operation
Selection
Fan On/Off Sel
Heatsink Cooling Fan Operation
Delay Time
Fan Delay Time
Ambient Temperature Setting
Ambient Temp
OL2 Characteristic Selection at
Low Speeds
OL2 Sel @ L-Spd
Soft CLA Selection
Soft CLA Sel
OH Frequency Reference
Reduction Level
Fref During OH
Table 1:
Parameter List (Continued
)
Description
Hdwe Protection
0: Not Provided
1: Provided
When the cooling fin temperature exceeds the value set in this parameter, an overheat pre-alarm (OH) will occur.
Drive Operation upon OH Pre Alarm Detection.
0: Ramp to Stop (Decel Time C1-02).
1: Coast to Stop
2: Fast-Stop (Decel Time = C1-09).
3: Alarm Only
*0 to 2 is recognized as fault detection, and 3 is recognized as alarm. (For the fault detection, the fault contact operates.)
4: OH Alarm & Reduce (Continue operation and reduce output frequency by L8-19)
Monitors the DC Bus current ripple and activates when one of the input phases is lost (PF).
Enables and disables Drive output ground fault detection.
0: Disabled
1: Enabled
Controls the Heatsink Cooling Fan Operation.
0: Fan On-Run Mode (Fan will operate only when
Drive is running and for L8-11 seconds after RUN is removed).
1: Fan Always On (Cooling fan operates whenever
Drive is powered up.)
When L8-10=0 this parameter sets a delay time for
Cooling Fan de-energization after the run command is removed.
When the Drive is installed in an ambient temperature exceeding its rating, Drive overload (OL2) protection level is reduced.
This parameter assists in protecting the output transistor junctions from overheating when output current is high and output frequency is low.
0: Disabled
1: Enabled (L8-18 is active)
Enables and disables current limit “A”
0: Disabled
1: Enabled.
Sets the amount of frequency reference reduction when an Overheat Pre-alarm (OH) is detected.
Setting
Range
0 or 1
50 to 130
0 to 4
0.0 to 25.0
0 or 1
0 or 1
0 to 300
45 to 60°C
0 or 1
0 or 1
0.0
to
100.0
Factory
Setting
0
95°C
4
5.0%
1
0
300sec
45°C
1
1
20.0%
Menu
Location
Programming
Programming
Programming
Programming
Programming
Programming
Quick Setting
Programming
Programming
Programming
Programming
Parameters A - 22
Parameter
No.
n1-01 n1-02 n3-01 n3-02 n3-03 n3-04 o1-01
!
o1-02
Parameter Name
Digital Operator Display
Hunting Prevention Selection
Hunt Prev Select
Hunting Prevention Gain Setting
Hunt Prev Gain
High-Slip Braking Deceleration
Frequency Width
HSB Decel Width
High-Slip Braking Current Limit
HSB Current Ref
High-Slip Braking Dwell Time at
Stop
HSB DwelTim@ Stp
High-Slip Braking Overload Time
HSB OL Time
User Monitor Selection
User Monitor Sel
User Monitor Selection After
Power-Up
Power-On Monitor
Table 1:
Parameter List (Continued
)
Description
Hunting Prev
0: Disabled (Hunting prevention function disabled.)
1: Enabled (Hunting prevention function enabled.)
If the motor vibrates while lightly loaded, hunting prevention may reduce the vibration. There is a loss of responsiveness if hunting prevention is enabled.
Gain setting for the Hunting Prevention Function.
If the motor vibrates while lightly loaded and n1-01=1, increase the gain by 0.1 until vibration ceases.
If the motor stalls while n1-01=1 decrease the gain by
0.1 until the stalling ceases.
HighSlip
Sets how aggressively the Drive decreases the output frequency as it stops the motor. If overvoltage (OV) faults occur during HSB, this parameter may need to be increased.
Sets the maximum current to be drawn during a HSB stop. Higher n3-02 settings will shorten motor stopping times but cause increased motor current, and therefore increased motor heating.
Sets the amount of time the Drive will dwell at E1-09
(Minimum Frequency). If this time is set too low, the machine inertia can cause the motor to rotate slightly after the HSB stop is complete and the Drive output is shut off.
Sets the time required for a HSB Overload Fault to occur when the Drive output frequency does not change for some reason during a HSB stop. Normally this does not need to be adjusted.
Monitor Select
Selects which monitor will be displayed upon power-up when o1-02 = 4.
Selects which monitor will be displayed upon power-up.
1: Frequency Ref
2: Output Freq
3: Output Current
4: User Monitor (set by o1-01)
Setting
Range
0 or 1
0.00 to 2.50
1 to 20
100 to 200
0.0 to 10.0
30 to 1200
6 to 53
1 to 4 o1-03
Digital Operator Display Selection
Display Scaling
Sets the units of the Frequency References (d1-01 through d1-17) and the Frequency Reference Monitor
(U1-01).
0: Hz
1: % (100%. = E1-04)
2 to 39: RPM. (Enter the number of motorpoles.)
40 to 39999: User display
Desired set/display value is set at Max. output frequency.
4 digit number.
The number of digits from the right the decimal point is displayed.
Example: If “200.0 is displayed at Max. output frequency, set “12000”.
0 to 39999
Factory
Setting
1
1.00
5%
150%
1.0sec
40sec
6
1
0
Menu
Location
Programming
Programming
Programming
Programming
Programming
Programming
Quick Setting
Programming
Programming
Parameters A - 23
Parameter
No.
Parameter Name
Digital Operator Display
Table 1:
Parameter List (Continued
)
Description
Setting
Range
Factory
Setting
Menu
Location o1-05
LCD Brightness Adjustment
LCD Contrast
Set Value
5
3
1
Description
LCD display becomes dark.
Standard setting
LCD display becomes light.
0 to 5 3 Quick Setting o1-06 o1-07 o1-08
User Monitor Selection Mode
Monitor Mode Sel
Second Line User Monitor
Selection
2nd Monitor Sel
Third Line User Monitor
Selection
3rd Monitor Sel
Selects the "U1" monitors displayed on the 4th and 5th lines of the digital operator display.
0: 3 Mon Sequential (Displays the next 2 sequential U1
monitors.)
1: 3 Mon Selectable (Displays U1 monitors set by o1-07
and o1-08.)
Sets the "U1" monitor always displayed on the 4th line of the digital operator display. Effective only when o1-
06 = 1.
Sets the "U1" monitor always displayed on the 5th line of the digital operator display. Effective only when o1-06 = 1.
Key Selections
0 or 1
1 to 53
1 to 53 o2-01
Local/Remote Key Function
Selection
Local/Remote Key
Has no function when HOA operator (Part# JVOP-162) is connected.
o2-02 o2-03
OFF Key Function During Auto
Run
Oper STOP Key
User Parameter Default Value
User Defaults
Determines if the off key on the digital operator will stop the Drive when Drive is operating from external terminals or serial communications.
0: Disabled
1: Enabled
Allows storing of current parameter values as a User
Initialization Selection at parameter A1-03.
0: No Change (No user parameter set active).
1: Set Defaults (Saves current parameter settings as user initialization. A1-03 now allows selecting <1110> for user initialization.
2: Clear All (Clears the currently saved user initialization. A1-03 no longer allows selecting
<1110>.
Sets the kVA of the Drive. Enter the number based on
Drive Model #. Use the """" portion of the
CIMR-E7"""" Model Number.
o2-04
Drive/kVA Selection
Inverter Model #
o2-05
Frequency Reference Setting
Method Selection
Operator M.O.P.
Reference Appendix 2
Determines if the Data/Enter key must be used to input a frequency reference from the digital operator.
0: Disabled - Data/Enter key must be pressed to enter a frequency reference.
1: Enabled - Data/Enter key is not required. The frequency reference is adjusted by the up and down arrow keys on the digital operator without having to press the data/enter key.
o2-06
Operation Selection when Digital
Operator is Disconnected
Oper Detection
Determines if the Drive will stop when the digital operator is removed.
0: Disabled - The Drive will not stop when the digital operator is removed.
1: Enabled - The Drive will fault (OPR) and coast to stop when the operator is removed.
o2-07
Cumulative Operation Time
Setting
Elapsed Time Set
Sets the initial value of the elapsed operation timer.
!Denotes that parameter can be changed when the Drive is running.
0 or 1
0 to 2
0 to FF
0 or 1
0 or 1
0 to 65535
0
2
3
1
0 kVA
Dependent
Programming
1
1
0H
Programming
Quick Setting
Quick Setting
Programming
Quick Setting
Quick Setting
Programming
Programming
Parameters A - 24
Parameter
No.
o2-08 o2-09 o2-10 o2-12 o2-14 o2-15 o3-01 o3-02
T1-02
T1-04
Parameter Name
Digital Operator Display
Cumulative Operation Time
Selection
Elapsed Time Run
Initialization Specification
Selection
Init Mode Sel
Cumulative Cooling Fan
Operation Time Setting
Fan ON Time Set
Fault Trace/Fault History Clear
Function
FLT Trace Init
kWh User Monitor (U1-29)
Initialization
kWH MonitorClear
Hand Key Function Selection
Oper Hand Key
Copy Function Selection
Copy Function Sel
Read Allowed Selection
Read Allowable
Motor Rated Power
Mtr Rated Power
Motor Rated Current
Rated Current
Table 1:
Parameter List (Continued
)
Description
Sets how time is accumulated for the elapsed timer
(o2-07).
0: Power-On Time (Time accumulates whenever Drive is powered).
1: Running Time (Time accumulates only when Drive is running)
Determines parameter values after a Drive initialization
(A1-03) is executed. This should always be set to "1"
American Spec.
1: American spec
2: European spec
4: PV-A spec
5: PV-E spec
Sets the initial value of the heatsink fan operation time.
Clears the fault memory contained in the U2 and U3 monitors.
0: Disabled (no effect).
1: Enabled - resets U2 and U3 monitors, and returns o2-12 to zero.
Used to reset the kilowatt Hour monitor to zero
0: Disabled (no change).
1: Clear all - Resets U1-29 to zero and returns o2-14 to zero.
Enables or disables the "Hand" key on the digital operator.
0: Disabled
1: Enabled
COPY Function
This parameter controls the copying of parameters to and from the digital operator.
0: COPY SELECT (no function)
1: INV -> OP READ - All parameters are copied from the Drive to the digital operator.
2: OP -> INV WRITE - All parameters are copied from the digital operator into the Drive.
3: OP<-->INV VERIFY - Parameter settings in the
Drive are compared to those in the digital operator.
NOTE: When using the copy function, the Drive model number and software number (U1-14) must match or an error will occur.
Enables and disables all digital operator copy functions.
0: Disabled - No digital operator copy functions are allowed.
1: Enabled - Copying allowed
Auto-Tuning
Sets the motor rated power in kW.
NOTE: If motor power is given in horsepower, power in kW can be calculated using the following formula: kW = Hp * 0.746
Sets the motor rated current. (Used only during an autotune).
Setting
Range
0 or 1
1 to 5
0 to 65535
0 or 1
0 or 1
0 or 1
0 to 3
0 to 1
0.00 to
650.00
kVA
Dependent
Factory
Setting
1
1
0H
0
0
1
0
0
Menu
Location
Quick Setting
Programming
Programming
Programming
Programming
Programming
Programming
Quick Setting kVA
Dependent kVA
Dependent
Auto-Tuning
Auto-Tuning
Parameters A - 25
Monitor List
Parameter
No.
U1-01
U1-02
U1-03
U1-06
U1-07
U1-08
U1-10
Table 2: Monitor List
Parameter Name
Digital Operator Display
Frequency Reference
Frequency Ref
Output Frequency
Output Freq
Output Current
Output Current
Output Voltage
Output Voltage
DC Bus Voltage
DC Bus Voltage
Output Power
Output kWatts
Input Terminal Status
Input Term Sts
Description
Monitor
Frequency reference (speed command) monitor when in auto mode, frequency reference (speed command) setting location when in hand mode. Units changeable via o1-03.
Output frequency (speed) monitor. Units changeable via o1-03.
Output current monitor
Displays Drive output voltage
Displays DC Bus Voltage
Displays Drive output power
Displays Drive input terminal status
0 0 0 0 0 0 0 0
1: FWD. run
(Terminal S1) is ON.
1: REV. run
(Terminal S2) is ON.
1: Multi-function input 1
(Terminal S3) is ON.
1: Multi-function input 2
(Terminal S4) is ON.
1: Multi-function input 3
(Terminal S5) is ON.
1: Multi-function input 4
(Terminal S6) is ON.
1: Multi-function input 5
(Terminal S7) is ON.
U1-11
Output Terminal Status
Output Term Sts
Output terminal ON/OFF Check
0 0 0 0 0 0 0 0
1: Multi-function Contact 1 output 1 (Terminal M1-M2) is ON.
1: Multi-function Contact 2 output 1 (Terminal P1) is
ON.
1: Multi-function contact output 3 (Terminal P2) is ON.
Not used
1: Fault output
(Terminal Ma/AB-MC) is
ON.
U1-12
Drive Operation Status
Int Ctl Sts 1
0 0 0 0 0 0 0 0
1: During running
1: During zero speed
1: During reverse
1: During reset signal input
1: During speed agree
1: Drive operation ready
1: During fault detection
(Minor fault)
1: During fault detection
(Major fault)
Parameters A - 26
Table 2: Monitor List (Continued)
Parameter
No.
U1-13
U1-14
U1-15
U1-16
U1-18
U1-20
U1-24
U1-28
U1-29
U1-30
U1-34
U1-36
U1-37
U1-38
Parameter Name
Digital Operator Display
Description
Monitor
Cumulative Operation Time
Elapsed Time
Software Number
FLASH ID
Terminal A1 Input Voltage
Term A1 Level
Terminal A2 Input Voltage
Term A2 level
Motor Secondary Current (I q
Mot SEC Current
)
Output Frequency After Soft Start
SFS Output
PI Feedback Value
PI Feedback
CPU Number
CPU ID
kWh
kWh Lo 4 Digits
MWh
kWh Hi 5 Digits
First Parameter Causing an OPE
OPE Detected
PI Input
PI Input
PI Output
PI Output
PI Setpoint
PI Setpoint
Displays total operating or power-on time of the Drive.
Displays Drive's software number.
Displays the input voltage on Terminal A1, as a percentage of
10V DC.
Displays the input current (or voltage) on Terminal A2, as a percentage of 20mA (or 10 V DC).
Displays the amount of current being used by the motor to produce torque (Iq).
Displays the frequency reference (speed command) after the accel and decel ramps.
Displays the feedback signal when PI control is used.
Displays control board hardware revision.
Displays the accumulated kWh.
Displays the accumulated MWh.
Displays the parameter number causing an "OPE" fault.
Displays the "error" in the PI regulator. (U1-36 = PI Setpoint -
PI Feedback).
Displays the output of the PI as a percentage of maximum frequency (E1-04).
Displays the setpoint of the PI regulator (U1-38 = PI reference
+ PI bias).
U1-39
Memobus Communication Error
Code
Transmit Err
0 0 0 0 0 0 0 0
1: CRC error
1: Data length error
Not used. Always 0.
1: Parity error
1: Overrun error
1: Fleming error
1: Timeover
Not used. Always 0 .
U1-40
U1-51
U1-52
U1-53
Heatsink Cooling Fan Operation
Time
FAN Elapsed Time
Auto Mode Frequency Reference
Value
Auto Mode Fref
Hand Mode Frequency Reference
Value
HAND Mode Fref
PI Feedback 2 Value
PI Feedback 2
Displays total operating time of the heatsink cooling fan.
Displays the frequency reference (speed command) when in auto mode.
Displays the frequency reference (speed command) when in hand mode, or displays Terminal A2 when differential mode is selected.
Displays PI feedback 2 value.
Parameters A - 27
Fault Trace List
Table 3: Fault Trace List
Fault Trace
U2-01
U2-02
U2-03
U2-04
U2-05
U2-07
U2-08
U2-09
U2-11
U2-12
U2-13
Current Fault
Current Fault
Previous Fault
Last Fault
Frequency Reference at Most Recent Fault
Frequency Ref
Output Frequency at Most Recent Fault
Output Freq
Output Current at Most Recent Fault
Output Current
Output Voltage at Most Recent Fault
Output Voltage
DC Bus Voltage at Most Recent Fault
DC Bus Voltage
Output Power at Most Recent Fault
Output kWatts
Input Terminal Status at Most Recent Fault. The format is the same as for U1-10.
Input Term Sts
Output Terminal Status at Most Recent Fault. The format is the same as for U1-11.
Output Term Sts
Drive Operation Status at Most Recent Fault. The format is the same as for U1-12.
Inverter Status
U2-14 Cumulative Operation Time at Most Recent Fault
Elapsed time
(Note) Fault trace is not executed at CPF00, CPF
0
1, CPF03, UVI and UV2.
Parameters A - 28
Fault History List
Table 4: Fault History List
Fault Trace
U3-01
U3-02
U3-03
U3-04
U3-05
U3-06
U3-07
U3-08
U3-09
U3-10
U3-11
U3-12
U3-13
U3-14
U3-15
U3-16
U3-17
U3-18
U3-19
U3-20
Most Recent Fault
Last Fault
2 nd
Most Recent Fault
Fault Message 2
3 rd
Most Recent Fault
Fault Message 3
4 th
Most Recent Fault
Fault Message 4
Cumulative Operation Time at Most Recent Fault
Elapsed Time 1
Cumulative Operation Time at 2 nd
Most Recent Fault
Elapsed Time 2
Cumulative Operation Time at 3 rd
Most Recent Fault
Elapsed Time 3
Cumulative Operation Time at 4 th
Most Recent Fault
Elapsed Time 4
5 th
Most Recent Fault
Fault Message 5
6 th
Most Recent Fault
Fault Message 6
7 th
Most Recent Fault
Fault Message 7
8 th
Most Recent Fault
Fault Message 8
9 th
Most Recent Fault
Fault Message 9
10 th
Most Recent Fault
Fault Message 10
Cumulative Operation Time at 5 th
Most Recent Fault
Elapsed Time 5
Cumulative Operation Time at 6 th
Most Recent Fault
Elapsed Time 6
Cumulative Operation Time at 7 th
Most Recent Fault
Elapsed Time 7
Cumulative Operation Time at 8 th
Most Recent Fault
Elapsed Time 8
Cumulative Operation Time at 9 th
Most Recent Fault
Elapsed Time 9
Cumulative Operation Time at 10 th
Most Recent Fault
Elapsed Time 10
(Note) Faults such as CPF00, CPF01, CPF02, CPF03, UV1, and UV02 are not stored in fault history.
Parameters A - 29
Notes:
Parameters A - 30
Appendix B
Capacity Related Parameters
This appendix lists the parameters affected by the Drive Capacity setting of o2-04.
Drive Capacity ................................................................................ 2
Parameters Affected by o2-04 ........................................................ 3
Capacity Related Parameters B - 1
Drive Capacity
Parameter o2-04 sets the Drive capacity according to the model number. Parameter o2-04 will need to be adjusted when replacing a control board.
If a Control PCB is changed, the first time the Drive is powered up, parameter o2-04 must be set to the appropriate value listed in Table B.1 for the Drive model number. After properly setting parameter 02-04, a 2-wire or 3-wire initialization must be performed by setting parameter A1-03=2220 or A1-03=3330, respectively.This will automatically program the values of all other parameters listed in Table B.2 to the factory settings for that particular Drive rating.
.
Voltage
208-240VAC
208-230VAC
480VAC
Table B.1 Drive Capacity Selection
Model Number
CIMR-P7U20P4 o2-04 Setting
0
CIMR-P7U20P7
CIMR-P7U21P5
1
2
CIMR-P7U22P2
CIMR-P7U23P7
CIMR-P7U25P5
CIMR-P7U27P5
CIMR-P7U2011
CIMR-P7U2015
CIMR-P7U2018
CIMR-P7U2022
CIMR-P7U2030
9
A
7
8
B
5
6
3
4
CIMR-P7U2037
CIMR-P7U2045
CIMR-P7U2055
CIMR-P7U2075
CIMR-P7U2090
CIMR-P7U2110
CIMR-P7U40P4
CIMR-P7U40P7
CIMR-P7U41P5
CIMR-P7U42P2
CIMR-P7U43P7
CIMR-P7U45P5
CIMR-P7U47P5
CIMR-P7U4011
CIMR-P7U4015
CIMR-P7U4018
CIMR-P7U4030
CIMR-P7U4037
27
28
29
2A
22
23
24
26
2C
2D
10
11
20
21
E
F
C
D
CIMR-P7U4045
CIMR-P7U4055
CIMR-P7U4075
CIMR-P7U4090
CIMR-P7U4110
CIMR-P7U4160
CIMR-P7U4185
CIMR-P7U4220
CIMR-P7U4300
32
34
35
36
2E
2F
30
31
37
Capacity Related Parameters B - 2
5
7.5
10
15/20
25
30
40/50
60
75
75
75/100
125
150
0.5/0.75
1
1.5/2
3
Nominal Hp
0.5/0.75
1
1.5/2
3
20
25
30
40
5
7.5
10
15
50
60
100
125
150
200
250
300/350
400/450
500+
!
Parameters Affected by o2-04
The factory setting of the following parameters may change when the Drive capacity is changed.
Table B.2 Parameters Affected by o2-04
Parameter Number
Parameter Name
Digital Operator Display
b8-04
C6-02
E2-01
E2-03
Energy Saving Coefficient Value
Energy Save COEF
Carrier Frequency Selection
CarrierFreq Sel
Motor Rated Current
Motor Rated FLA
Motor No Load Current
No-Load Current
E2-05
L2-02
L2-03
L2-04
L8-02
L8-06 o2-04
Motor Line-to-Line Resistance
Term Resistance
Momentary Power Loss Ride-thru Time
PwrL Ridethru t
Momentary Power Loss Minimum Base Block Time
PwrL Baseblock t
Momentary Power Loss Voltage Recovery Ramp Time
PwrL V/F Ramp t
Overheat Pre-Alarm Level
OH Pre-Alarm Lvl
Input Phase Loss Detection Level
Ph Loss In Lvl
Drive/kVA Selection
Inverter Model #
Capacity Related Parameters B - 3
The following tables detail the factory default settings for the parameters that are affected by the setting of parameter o2-04.
Drive Model
CIMR-_ _ _
Table B.3 208/240VAC Drives
Nominal
Hp
Factory
Default for b8-04
Factory
Default for
C6-02
Factory
Default for
E2-01
Factory
Default for
E2-03
Factory
Default for
E2-05
Factory
Default for
L2-02
Factory
Default for
L2-03
Factory
Default for
L2-04
Factory
Default for
L8-02
Factory
Default for
L8-06
P7U20P4
P7U20P7
P7U21P5
P7U22P2
P7U23P7
P7U25P5
P7U27P5
0.5/0.75
2
1.5/2
3
5
7.5
10
288.2
223.7
169.4
156.8
122.9
94.75
72.69
10kHz
10kHz
10kHz
8kHz
10kHz
15kHz
15kHz
1.9
3.3
6.2
8.5
14.0
19.6
26.6
P7U2011
P7U2015
P7U2018
P7U2022
P7U2030
P7U2037
15
20
25
30
40
50
70.44
63.13
57.87
51.79
46.27
38.16
8kHz
10kHz
10kHz
10kHz
10kHz
5kHz
39.7
53.0
65.8
77.2
105.0
131.0
P7U2045
P7U2055
P7U2075
60
75
75/100
35.78
31.35
23.10
5kHz
8kHz
2kHz
160.0
190.0
260.0
44.0
45.6
72.0
P7U2090 125 20.65
2kHz
P7U2110 150 18.12
2kHz
Note: b8-04 = Energy Savings Coefficiant
C6-02 = Carrier Frequency
E2-01 = Motor Rated Current
E2-03 = Motor No-Load Current
E2-05 = Motor Line-to-Line Resistance
L2-02 = Momentary Power Loss Ride-Thru Time
L2-03 = Momentary Power Loss Minimun Base Block Time
L2-04 = Momentary Power Loss Voltage Recovery Ramp Time
L8-02 = Overheat Pre-Alarm Level
L8-06 = Input Phase Loss Detection Level
260.0
260.0
72.0
72.0
11.2
15.2
15.7
18.5
21.9
38.2
1.2
1.8
2.8
3.0
4.5
5.1
8.0
0.6
0.1
0.1
0.1
0.1
0.3
0.3
0.6
0.6
0.6
0.6
0.3
0.3
0.3
0.3
0.3
0.3
0.3
1.2
1.2
1.3
1.5
1.7
0.8
0.9
1.0
1.0
1.1
1.1
0.1
0.2
0.3
0.4
0.5
0.6
0.7
2.0
2.0
2.0
2.0
2.0
1.0
2.0
2.0
2.0
2.0
2.0
0.1
0.1
0.2
0.3
0.5
1.0
1.0
0.230
0.138
0.101
0.079
0.064
0.039
0.030
0.022
0.023
0.023
0.023
9.842
5.156
1.997
1.601
0.771
0.399
0.288
90
°
C
100
°
C
90
°
C
90
°
C
95
°
C
100
°
C
105
°
C
110
°
C
100
°
C
95
°
C
95
°
C
95
°
C
95
°
C
100
°
C
95
°
C
95
°
C
95
°
C
95
°
C
20
17
16
18
20
21
17
15
24
20
18
5
7.5
10
12
12
10
17
Capacity Related Parameters B - 4
Drive Model
CIMR-_ _ _
Nominal
Hp
Table B.4 480VAC Drives
Factory
Default for b8-04
Factory
Default for
C6-02
Factory
Default for
E2-01
Factory
Default for
E2-03
Factory
Default for
E2-05
Factory
Default for
L2-02
Factory
Default for
L2-03
Factory
Default for
L2-04
Factory
Default for
L8-02
Factory
Default for
L8-06
P7U40P4
P7U40P7
P7U41P5
P7U42P2
P7U43P7
P7U45P5
P7U47P5
P7U4011
P7U4015
P7U4018
P7U4030
P7U4037
P7U4045
P7U4055
P7U4075
0.5/0.75
1
1.5/2
3
5
7.5
10
15/20
25
30
40/50
60
75
100
125
576.40
447.40
338.80
313.60
245.80
189.50
145.38
140.88
126.26
115.74
92.54
76.32
71.56
67.20
46.20
15kHz
15kHz
15kHz
15kHz
15kHz
15kHz
15kHz
8kHz
10kHz
10kHz
8kHz
8kHz
8kHz
5kHz
5kHz
P7U4090
P7U4110
P7U4160
150
200
250
38.91
36.23
30.13
8kHz
5kHz
5kHz
156.0
190.0
270.0
P7U4185
P7U4220
300/350
400/450
30.57
27.13
2kHz
2kHz
310.0
370.0
P7U4300 500+ 21.76
2kHz 500.0
Note: b8-04 = Energy Savings Coefficiant
C6-02 = Carrier Frequency
E2-01 = Motor Rated Current
E2-03 = Motor No-Load Current
E2-05 = Motor Line-to-Line Resistance
L2-02 = Momentary Power Loss Ride-Thru Time
L2-03 = Momentary Power Loss Minimun Base Block Time
L2-04 = Momentary Power Loss Voltage Recovery Ramp Time
L8-02 = Overheat Pre-Alarm Level
L8-06 = Input Phase Loss Detection Level
52.3
65.6
79.7
95.0
130.0
130.0
1.0
1.6
3.1
4.2
7.0
13.3
19.9
26.5
32.9
40.0
49.0
70.0
81.0
96.0
130.0
7.8
10.9
19.1
22.0
24.0
36.0
0.6
0.8
1.4
1.5
2.3
2.6
4.0
5.6
7.6
2.0
2.0
2.0
2.0
2.0
2.0
0.1
0.1
0.2
0.3
0.5
1.0
1.0
2.0
2.0
2.0
2.0
2.0
2.0
2.0
2.1
0.403
0.269
0.155
0.122
0.088
0.092
38.198
22.459
10.100
6.495
3.333
1.595
1.152
0.922
0.550
0.056
0.046
0.029
0.025
0.020
0.014
0.6
0.6
0.6
0.6
1.0
1.0
0.3
0.3
0.3
0.3
0.3
0.3
0.3
0.3
0.3
1.0
1.0
1.0
1.0
1.0
1.0
1.0
1.1
1.1
1.2
1.2
1.3
0.1
0.2
0.3
0.4
0.5
0.6
0.7
0.8
0.9
1.5
1.7
1.8
0.7
0.8
0.9
17
20
20
20
20
16
10
12
10
5
7.5
10
20
23
17
16
16
14
15
15
15
95
°
C
98
°
C
85
°
C
85
°
C
90
°
C
90
°
C
98
°
C
108
°
C
95
°
C
95
°
C
95
°
C
90
°
C
95
°
C
95
°
C
90
°
C
95
°
C
100
°
C
108
°
C
95
°
C
100
°
C
95
°
C
Capacity Related Parameters B - 5
Notes:
Capacity Related Parameters B - 6
Appendix C
Specifications
This appendix details the standard Drive Specifications.
Standard Drive and Bypass Specifications ..................................... 2
208-240 VAC ............................................................................. 2
480 VAC ..................................................................................... 3
All Voltages ................................................................................ 4
Specifications C - 1
Standard Drive and Bypass Specifications
The standard Drive and Bypass specifications are listed in the following tables.
!
208-240 VAC
Bypass Model Number P7B_ *
208V
Motor HP
240V
Bypass rated output current (A)
Drive Model Number CIMR-P7U
Drive rated output capacity (kVA)
Drive rated output current (A)
Drive max. output voltage (V)
Drive max. output frequency (Hz)
Rated voltage (V)
Rated frequency (Hz)
Rated input current (A)
Allowable voltage fluctuation
Allowable frequency fluctuation
Table C.1 208-240VAC Drive and Bypass Specifications
D003
0.5/0.75
0.5/0.75
3.5
20P4
1.4
3.6
D004
1
1
4.6
20P7
1.8
4.6
D007
1.5/2
1.5/2
7.5
21P5
D010
3
3
10.6
22P2
D016
5
5
16.7
23P7
D024
7.5
7.5
24.2
25P5
D030
10
10
30.8
27P5
D046 D059
15
15
46.2
2011
20
20
59.4
2015
D074
25
25
74.8
2018
3.0
7.8
4.1
10.8
6.4
16.8
8.8
23.0
12.0
31.0
18.0
46.2
23.0
59.4
29.0
74.8
3-phase; 200, 208, 220, 230, or 240VAC (Proportional to input voltage)
120 Hz
3-phase, 200/208/220/230/240VAC, 50/60 Hz
4.3
5.5
9.4
13 20 24 37
+ 10%, - 15%
±5%
53 70 89
D088
30
30
88
2022
34.0
88.0
98
D114
40
40
114
2030
44.0
115.0
120
Built-in DC Reactor
Measures for power supply harmonics
12-Pulse
Rectification
Optional
Not possible
Bypass Model Number P7B_ *
208V
Motor HP
Bypass rated output current (A)
230V
Drive Model Number CIMR-P7U
Drive rated output capacity (kVA)
Drive rated output current (A)
Drive max. output voltage (V)
Drive max. output frequency (Hz)
Rated voltage (V)
Rated frequency (Hz)
Rated input current (A)
Allowable voltage fluctuation
Allowable frequency fluctuation
Table C.2 208-230VAC Drive and Bypass Specifications
D143
50
50/60
143
2037
62.0
162.0
D169
60
75
169
2045
D211
75
-
211
2055
D273
100
100/125
273
2075
D343
125
150
343
2090
73.0
192.0
82
215
120.0
312.0
140.0
360.0
3-phase; 200, 208, 220, 230, or 240VAC (Proportional to input voltage)
120 Hz
3-phase, 200/208/220/230/240VAC, 50/60 Hz
180 212 237 350
+ 10%, - 15%
±5%
396
Possible
D396
150
-
396
2110
160.0
415.0
457
DC Reactor
Measures for power supply harmonics
12-Pulse
Rectification
Built-in
Possible
Note: The maximum applicable motor output is given for a standard 4-pole motor. When selecting the actual motor and Drive, be sure that the Bypass and
Drive's rated output current is equal to, or greater than, the motor's rated current.
A phase-shifting transformer is required on the power supply for 12-pulse rectification.
* Only 208V model numbers are shown.
Specifications C - 2
!
480 VAC
Bypass Model Number P7B_ *
Motor HP (460V)
Bypass rated output current (A)
Drive Model Number CIMR-P7U
Drive rated output capacity (kVA)
Drive rated output current (A)
Drive max. output voltage (V)
Drive max. output frequency (Hz)
Rated voltage (V)
Rated frequency (Hz)
Table C.3 480VAC Drive and Bypass Specifications
B001
0.5/0.75
1.6
40P4
1.4
1.8
B002
1
2.1
40P7
1.6
2.1
B003
1.5/2
3.4
41P5
2.8
B004
3
4.8
42P2
4.0
B007
5
7.6
43P7
5.8
B011
7.5
11
45P5
9.5
B014
10
14
47P5
13.0
B021/B027
15/20
21/27
4011
21.0
B034
25
34
4015
26.0
3.7
5.3
7.6
12.5
17.0
27.0
3-phase; 380, 400, 415, 440, 460, or 480VAC (Proportional to input voltage.)
34.0
120 Hz
3-phase, 380, 400, 415, 440, 460 or 480VAC, 50/60 Hz
Rated input current (A) 2.2
2.5
4.4
6.4
9.0
15 20 33 40
B040
30
40
4018
30.0
40.0
48
Allowable voltage fluctuation + 10%, - 15%
Allowable frequency fluctuation ±5%
DC Reactor
Measures for power supply harmonics
12-pulse
Rectification
Optional
Not possible
Bypass Model Number P7B_ *
Motor HP (460V)
Bypass rated output current (A)
Drive Model Number CIMR-P7U
Drive rated output capacity (kVA)
Drive rated output current (A)
Drive max. output voltage (V)
Drive max. output frequency (Hz)
Max. voltage (V)
Rated frequency (Hz)
Rated input current (A)
Table C.3 480VAC Drive Specifications (Continued)
B052/B065
40/50
52/65
4030
51.0
67.2
B077
60
77
4037
59.0
B096
75
96
4045
73.0
B124
100
124
4055
95.0
B156
125
156
4075
120.0
B180
150
180
4090
140.0
B240
200
240
4110
180.0
B302 – – –
250 300/350 400/450 500+
302
4160
230.0
4185
315.0
4220
390.0
515.0
77.0
96.0
125.0
156.0
180.0
240.0
304.0
414.0
3-phase, 380, 400, 415, 440, 460 or 480VAC (Proportional to input voltage)
120 Hz
4300
510.0
675.0
3-phase, 380, 400, 415, 440, 460, or 480VAC, 50/60 Hz
74 85 106 134 172 198 264 334 456 567 743
Allowable voltage fluctuation + 10%, - 15%
Allowable frequency fluctuation ±5%
DC Reactor Built-in
Measures for power supply harmonics
12-Pulse
Rectification
Possible
Note: The maximum applicable motor output is given for a standard 4-pole motor. When selecting the actual motor and Drive, be sure that the Bypass and
Drive's rated output current is equal to, or greater than, the motor's rated current.
A 3-wire phase-shifting transformer is required on the power supply for 12-pulse rectification.
Specifications C - 3
!
All Voltages
All Models
Control method
Speed range
Speed control accuracy
Frequency accuracy
(temperature characteristics)
Frequency setting resolution
Table C.4 Common Drive Specifications
Specification
Sine wave PWM
V/f control
40:1
±2 to 3% (77
°
F ± 50
°
F) (25
°
C ± 10
°
C)
Digital references: ± 0.01% (14
°
F to 104
°
F) (-10
°
C to +40
°
C)
Analog references: ±0.1% (77
°
F ± 50
°
F) (25
°
C ±10
°
C)
Digital references: 0.01 Hz
Analog references: 0.025/50 Hz (10 bit with sign)
0-10 Vdc, 4-20 mA
Frequency setting signal
(Speed Command)
Acceleration/Deceleration time
Main Drive control functions
Main Bypass control functions
Motor protection
Fuse blown protection
Overload capacity and maximum current
Overvoltage protection
Undervoltage protection
Momentary power loss ride thru
Cooling fin overheating
Stall prevention
Grounding protection
Charge indicator
Enclosure Type
Ambient operating temperature
Ambient operating humidity
Storage temperature
Application site
Altitude
Vibration
0.0 to 6000.0 s (2 selectable combinations of independent acceleration and deceleration settings)
Restarting for momentary power loss, bi-directional speed search, overtorque detection, 5 preset speeds,
acceleration/deceleration time changes, S-curve acceleration, 3-wire sequence, auto-tuning, cooling fan ON/OFF control, torque compensation, jump frequencies, upper and lower limits for frequency references, DC braking for starting and stopping, high-slip braking, PI control (with sleep function), energy-saving control, Modbus communications (RS-
485/422, 19.2 kbps maximum), fault reset, and copy function
Provides an alternate connection for the motor to line power for operation at full speed only, directly from line power.
Three electrically interlocked IEC rated contactors isolate the Drive when operating in Bypass mode. Control logic circuit provides Hand/Off/Auto functions and safety circuit interlocks. Includes fused 120VAC control transformer, motor circuit protector/disconnect, motor overload relay, selector switches and indicating lights.
Protection by electronic thermal overload relay
Stops for fuse blown
110% of rated output current for 60 seconds
208-240VAC: Stops when main-circuit DC voltage is above 410 V
480VAC: Stops when main-circuit DC voltage is above 820 V
208-240VAC: Stops when main-circuit DC voltage is below 190 V
480VAC: Stops when main-circuit DC voltage is below 380 V
Power Interuptions of 15 ms or more
By selecting the momentary power loss method, operation can be continued if power is restored within 2 s
Protection by thermistor
Stall prevention during acceleration, deceleration, or running
Protection by electronic circuits. (50% of inverter rated current)
Lit when the main circuit DC voltage is approx. 50 Vdc or more
Enclosed wall-mounted type (NEMA 1): CIMR-P7U20P4 thru 2030 and 40P4 thru 4055
Open chassis type (IP00): CIMR-P7U2022 thru 2110 and 4030 thru 4300
14
°
F to 104
°
F (-10
°
C to 40
°
C) NEMA 1 type
14
°
F to 113
°
F (–10
°
C to 45
°
C) Open chassis type
95% max. (with no condensation)
68
°
F to 140
°
F (- 20
°
C to + 60
°
C) short-term temperature during transportation
Indoor (no corrosive gas, dust, etc.)
3300 ft. (1000 m), higher altitudes by derate
10 to 20 Hz, 32 ft/sec
2
(9.8 m/s
2
) max.; 20 to 50 Hz, 6.5 ft/sec
2
(2 m/s
2
) max.
Specifications C - 4
Appendix D
Communication
This appendix details the specifications, connections, and programming of the Drive for Modbus communications.
The H/O/A switch must be in the AUTO position if serial communication is to be used for P7 Drive run, stop and speed control.
Using Modbus Communication ...................................................... 2
Modbus Communication Configuration ...................................... 2
Communication Specifications ................................................... 2
Communication Connection Terminal ........................................ 3
Procedure for Setting Up Communication ................................. 3
Modbus Function Code Details ...................................................... 7
Reading/Holding Register Contents (03H) ................................ 7
Write In Single Holding Register (06H) ...................................... 7
Loopback Test (08H) ................................................................. 8
Write In Several Holding Registers (10H) .................................. 8
Modbus Data Tables ....................................................................... 9
Reference Data .......................................................................... 9
Monitor Data ............................................................................ 10
Modbus Self-Diagnosis ................................................................ 14
Communications D - 1
Using Modbus Communication
Serial communication can be performed with Direct Digital Controllers (DDCs) or similar devices using the Modbus protocol.
!
Modbus Communication Configuration
Modbus communication is configured using 1 master (PLC) and a maximum of 31 slaves. Serial communication between master and slave is normally initiated by the master and responded to by the slaves.
The master performs serial communication with one slave at a time. Consequently, the slave address of each slave must be initially set, so that the master can perform serial communication using that address. Slaves receiving commands from the master perform the specified functions, and send a response back to the master.
Master
Slaves
P7
P7
P7
Fig D. 1 Example of Connections between Master and Drive
!
Communication Specifications
The Modbus communication specifications are shown below:
Interface
Item
Communications Cycle
Communications Parameters
Communications Protocol
Table D.1 Modbus Communication Specifications
Specifications
RS-422, RS-485
Asynchronous (Start-stop synchronization)
Number of Connectable Units
Baud rate: Select from 1200, 2400, 4800, 9600, and 19200 bps.
Data length: 8 bits fixed
Parity:
Stop bits:
Select from even, odd, or none.
1 bit selected
Modbus
31 units max.
Communications D - 2
!
Communication Connection Terminal
Modbus communication uses the following terminals: S+, S-, R+, and R-. The terminating resistance must be turned ON only if the Drive is at the very end of the Serial Communication chain. Set the terminating resistance by turning ON pin 1 of switch
S1.
RS-422A or RS-485
Switch
O
F
F
S1
1
1
2
Terminating resistance
DIP Switch S1-1 located on terminal board.
Terminating resistance (1/2W, 110 Ohms)
Fig. D.2 Communication Connection Terminals and Terminating Resistance
IMPORTANT
1. Separate the communication cables from the main circuit cables and control circuit wiring.
2. Use shielded cables for the communication cable, and use proper shield clamps.
3. When using RS-485 communication, connect S+ to R+, and S- to R-, on the control circuit terminal board. See Fig. D-3 below.
4. Shield at one end only.
Fig. D.3 RS-485 Communication Connection
!
Procedure for Setting Up Communication
Use the following procedure to perform communication with the PLC.
1. Turn OFF the input to the Drive power and connect the communication cable between the PLC and the Drive.
2. Turn ON the input power to the Drive.
3. Set the required communication parameters (H5-01 to H5-09) using the Digital Operator.
4. Turn OFF the input to the Drive power, and check that the Digital Operator display has completely disappeared.
5. Turn ON the input power to the Drive once again.
6. Perform communication with the PLC.
Communications D - 3
"
Related Parameters
Table D.2 Serial Communication Related Parameters
Parameter
No.
Parameter Name
Digital Operator Display
Description
Setting
Range b1-01 b1-02
H5-01
H5-02
H5-03
H5-04
H5-05
H5-06
H5-07
Frequency Reference
Selection
Reference Source
Run Command Selection
Run Source
Drive Node Address
Serial Com Adr
Communication Speed Selection
Serial Baud Rate
Communication Parity Selection
Serial Com Sel
Stopping Method after
Communication Error
Serial Fault Sel
Communication Error Detection
Selection
Serial Flt Dtct
Drive Transmit Wait Time
Transmit WaitTIM
RTS Control Selection
RTS Control Sel
Selects the speed command (frequency reference) input source.
0: Operator - Digital preset speed d1-01
1: Terminals - Analog Input Terminal A1
(or Terminal A2 see parameter H3-13)
2: Serial Com - RS-485 terminals R+, R-, S+ and S-
3: Option PCB - Option board connected at 2CN
Selects the run command input source.
0: Operator - "Hand" and "Off" keys on digital operator
1: Terminal - Contact Closure on Terminal S1
2: Serial Com - RS-485 terminals R+, R-, S+ and S-
3: Option PCB - Option board connected at 2CN
Selects Drive station node number (address) for terminals R+, R-, S+, S-.*
* Set H5-01 to 0 to disable Drive responses to
Modbus communications.
Selects the baud rate for terminals R+, R-, S+ and S-*.
0: 1200 Baud
1: 2400 Baud
2: 4800 Baud
3: 9600 Baud
4: 19200 Baud
Selects the communication parity for terminals R+,
R-, S+ and S-.*
0: No Parity
1: Even Parity
2: Odd Parity
Selects the stopping method when a communication error is detected.
0: Ramp to Stop
1: Coast to Stop
2: Fast-Stop
3: Alarm Only
4: Run at D1-04
Enables or disables the communications timout detection function.
0: Disabled - A communications loss will NOT cause a communications fault.
1: Enabled - If communications is lost for more than the time specified in parameter H5-09, a communications fault will occur.
Sets the time from when the Drive receives data to when the Drive sends data.
Enables or disables request to send (RTS) control:
0: Disabled
1: Enabled
Selects the communication protocol.
0: Modbus H5-08
H5-09
Communication Protocol
Selection
Protocol Select
Communication Error
Detection Time
CE Detect Time
Determines how long communications must be lost before a fault is annunciated. Works in conjunction with parameters H5-05 and H5-04.
* After these parameters are changed Drive power must be cycled before the changes will take effect.
0 to 3
0 to 3
0 to FF
(H5-08 dependent)
0 to 4
0 to 2
0 to 3
0 or 1
5 to 65
0 or 1
0.0 to 10.0
Factory
Setting
Chapter
Ref #
Menu
Location
1
1
1F
3
0
3
1
5ms
1
0
2.0sec
Quick
Setting
Quick
Setting
Programming
Programming
Programming
Programming
Programming
Programming
Programming
Programming
Programming
Modbus communication can perform the following operations regardless of the settings in b1-01 and b1-02:
1.
Monitoring operation status of the Drive
2.
Setting and reading Drive parameters
3.
Resetting faults
4.
Input multi-function commands
IMPORTANT
An OR operation is performed between the multi-function command input from the DDC and the command input from multi-function digital input terminals S3 to S7.
Communications D - 4
"
Message Format
In Modbus communication, the master sends commands to the slave, and the slave responds. The message format is configured for both sending and receiving as shown below. The length of the data packets is changed by the command
(function) contents.
Slave address
Function code
Data
Error check
Fig. D.4 Message Format
The space between messages must support the following:
DDC to Drive
Command message
Drive to DDC
Response message
DDC to Drive
Command message
Time (Seconds)
24 bits long
H5-06 setting
24 bits long
5 ms min.
Fig. D.5 Message Spacing
Slave Address
Set the Drive address from 0 to 32. If 0 is selected, commands from the master will be broadcast (i.e., the Drive will not return responses).
Function Code
The function code specifies commands. There are four function codes, as shown below.
Function Code
(Hexadecimal)
03H
06H
08H
10H
Table D.3 Modbus Function Codes
Command Message
Function
Min.
(Bytes)
Max.
(Bytes)
Reading/Holding Register Contents
Write In Single Holding Register
Loopback Test
Write In Several Holding Registers
8
8
8
11
* Minimum bytes for a normal Response Message (error response message is always 5 bytes).
8
41
8
8
Response Message
Min.*
(Bytes)
Max.
(Bytes)
8
8
7
8
37
8
8
8
Data
Configure consecutive data by combining the storage register address (test code for a loopback address) and the data the register contains. The data length changes depending on the command details.
Communications D - 5
Error Check
Errors are detected during communication using CRC-16. Perform calculations using the following method:
1. The factory setting for CRC-16 communication is typically zero, but when using the Modbus system, set the factory setting to one (e.g., set all 16 bits to 1).
2. Calculate CRC-16 using MSB as slave address LSB, and LSB as the MSB of the final data.
3. Calculate CRC-16 for response messages from the slaves and compare them to the CRC-16 in the response messages.
Communications D - 6
Modbus Function Code Details
!
Reading/Holding Register Contents (03H)
Read the contents of the storage register only for specified quantities. The addresses must be consecutive, starting from a specified address. The data content of the storage register are separated into higher 8 bits and lower 8 bits.
The following table shows message examples when reading status signals, error details, data link status, and frequency references from the slave 2 Drive.
Command Message
Slave Address
Function Code
Start
Address
Higher
Lower
Quantity
CRC-16
Higher
Lower
Higher
Lower
02H
03H
00H
20H
00H
04H
45H
F0H
Response Message
(During Normal Operation)
Slave Address
Function Code
02H
03H
Data quantity
1st storage register
Higher
Lower
Next storage register
Next storage register
Next storage register
Higher
Lower
Higher
Lower
Higher
Lower
Higher
CRC-16
Lower
08H
00H
65H
00H
00H
00H
00H
01H
F4H
AFH
82H
Fig. D.6 Function Code 03H Message Example
Response Message
(During Error)
Slave Address
Function Code
02H
83H
Error code
Higher
CRC-16
Lower
03H
F1H
31H
!
Write In Single Holding Register (06H)
Command Message
Slave Address
Function Code
Register
Address
Upper
Lower
Setting
Data
CRC-16
Upper
Lower
Upper
Lower
01H
06H
00H
01H
00H
03H
98H
0BH
Response Message
(During Normal Operation)
Slave Address
Function Code
01H
06H
Register
Address
Setting
Data
CRC-16
Upper
Lower
Upper
Lower
Upper
Lower
00H
01H
00H
03H
98H
0BH
Fig. D.7 Function Code 06H Message Example
Response Message
(During Error)
Slave Address
80H + Function Code
01H
86H
Error code
Upper
CRC-16
Lower
21H
82H
78H
Communications D - 7
!
Loopback Test (08H)
The loopback test returns the command message directly as the response message without changing the contents to check the communications between the master and slave. Set user-defined test code and data values.
The following table shows a message example when performing a loopback test with the slave 1 Drive.
Command Message
Slave address
Function code
Test Code
Higher
Lower
Data
CRC-16
Higher
Lower
Higher
Lower
01H
08H
00H
00H
A5H
37H
DAH
8DH
Response Message
(During Normal Operation)
Slave address
Function code
Test Code
Higher
Lower
Data
CRC-16
Higher
Lower
Higher
Lower
01H
08H
00H
00H
A5H
37H
DAH
8DH
Fig. D.8 Function Code 08H Message Example
Response Message
(During Error)
Slave address
Function code
Error Code
Higher
CRC-16
Lower
01H
89H
01H
86H
50H
!
Write In Several Holding Registers (10H)
Write the specified data to the registers from the specified addresses. The written data must be consecutive, starting from the specified address in the command message: Higher 8 bits, then lower 8 bits, in storage register address order.
The following table shows an example of a message when a forward run command has been set at a speed command of
60.0 Hz in the slave 1 Drive by the PLC.
Command Message
Slave Address
Function Code
Start
Address
Higher
Lower
Quantity
Higher
Lower
No. of data
Higher
Lead data
Lower
Higher
Next data
Lower
Higher
CRC-16
Lower
01H
10H
00H
01H
00H
02H
04H
00H
01H
02H
58H
63H
39H
Response Message
(During Normal Operation)
Slave Address
Function Code
01H
10H
Start
Address
Quantity
CRC-16
Higher
Lower
Higher
Lower
Higher
Lower
00H
01H
00H
02H
10H
08H
Response Message
(During Error)
Slave Address
Function Code
01H
90H
Error code
Higher
CRC-16
Lower
02H
CDH
C1H
* No. of data = 2 x (quantity)
Fig. D.9 Function Code 10H Message Example
IMPORTANT
Set the number of data specified using command messages as quantity of specified messages x 2. Handle response messages in the same way.
Communications D - 8
Modbus Data Tables
The data tables are shown below. The types of data are as follows: Reference data, monitor data and broadcast data.
!
Reference Data
The reference data table is shown below. Reference data can be read and written to.
Register No.
0000H
Table D.4 Reference Data
Contents
Reserved
Frequency reference
Bit 0 Run/stop command 1: Run 0: Stop
Bit 1
Bit 2
Bit 3
Bit 4
Forward/reverse operation 1: Reverse 0: Forward
External fault 1: Fault (EFO)
Fault reset
ComNet
1: Reset command
0001H Bit 5
Bit 6
Bit 7
Bit 8
ComCtrl
Multi-function digital input command 3
Multi-function digital input command 4
Multi-function digital input command 5
Bit 9
Bit A
Multi-function digital input command 6
Multi-function digital input command 7
Bits B to F Not used
Frequency reference (Set units using parameter o1-03) 0002H
0003H to 0005H Not used
0006H
0007H
0008H
PI Setpoint
Analog output 1 setting (-11 V = 726 to 11 V = 726)
→
10V = 660
Analog output 2 setting (-11 V = 726 to 11 V = 726)
→
10V = 660
Multi-function contact output setting
Bit 0 Digital output 1 (Terminal M1-M2) 1: ON 0: OFF
0009H
Bit 1
Bit 2
Bits 3 to 5 Not used
Bit 6 Set fault contact (terminal MA-MC) output using bit 7. 1: ON 0: OFF
Bit 7
Digital output 2 (Terminal M3-M4) 1: ON 0: OFF
Not Used
Fault contact (terminal MA-MC)
Bits 8 to F Not used
1: ON 0: OFF
000AH to 000EH Not used
Reference selection settings
Bit 0
Bit 1
Not used
Input PI setpoint 1: Enabled 0: Disabled
000FH
Bits 3 to B Not used
C Broadcast data terminal S5 input 1: Enabled 0: Disabled
D
E
Broadcast data terminal S6 input 1: Enabled 0: Disabled
Broadcast data terminal S7 input 1: Enabled 0: Disabled
F Not used
Note: Write 0 to all unused bits. Also, do not write data to reserved registers.
Communications D - 9
!
Monitor Data
The following table shows the monitor data. Monitor data can only be read.
Register No.
0020H
0021H
0022H
0023H
0024H
0025H
0026H
0027H
0028H
0029H
002AH
Table D.5 Monitor Data
Contents
Drive status
Bit 0
Bit 1
Bit 2
Bit 3
Bit 4
Bit 5
Bit 6
Operation 1: Operating 0: Stopped
Reverse operation 1: Reverse operation 0: Forward operation
Drive startup complete 1: Completed 0: Not completed
Fault 1: Fault
Data setting error 1: Error
Multi-function digital output 1 (terminal M1 - M2) 1: ON 0: OFF
Multi-function digital output 2 (terminal M3 - M4) 1: ON 0: OFF
Not used
Not used
Bit 7
Bits 8 to F
Fault details
Bit 0
Bit 1
Bit 2
Bit 3
Bit 4
Bit 5
Bit 6
Bit 7
Bit 8
Bit 9
Bit A
Bit B
Bit C
Bit D
Bit E
Bit F
Data link status
Bit 0
Bit 1
Bit 2
Bit 3
Overcurrent (OC) Ground fault (GF)
Main circuit overvoltage (OV)
Drive overload (OL2)
Drive overheat (OH1, OH2)
Not used
Fuse blown (PUF)
PI feedback reference lost (FbL)
External error (EF, EFO)
Hardware error (CPF)
Motor overload (OL1) or overtorque 1 (OL3) detected
PG broken wire detected (PGO), Overspeed (OS), Speed deviation (DEV)
Main circuit undervoltage (UV) detected
Main circuit undervoltage (UV1), control power supply error (UV2), inrush prevention circuit error (UV3), power loss
Missing output phase (LF)
Modbus communications error (CE)
Operator disconnected (OPR)
Bit 4
Bits 5 to F
Frequency reference
Output frequency
Output voltage reference U1-06
Output current U1-03
Output power
Torque reference
U1-08
U1-09
Not used
Not used
Writing data
Not used
Not used
Upper and lower limit errors
Data integrity error
Not used
U1-01
U1-02
Communications D - 10
Register No.
Table D.5 Monitor Data (Continued)
Contents
002BH
002CH
002DH
Sequence input status
Bit 0
Bit 1
Bit 2
Input terminal S1 1: ON 0: OFF
Input terminal S2 1: ON 0: OFF
Multi-function digital input terminal S3 1: ON 0: OFF
Multi-function digital input terminal S4 1: ON 0: OFF Bit 3
Bit 4
Bit 5
Bit 6
Bit 2
Bit 3
Bit 4
Bit 5
Multi-function digital input terminal S5 1: ON 0: OFF
Multi-function digital input terminal S6 1: ON 0: OFF
Multi-function digital input terminal S7 1: ON 0: OFF
Not used Bits 7 to F
Drive status
Bit 0
Bit 1
Bit 6
Bit 7
Bit 8
Bit 9
Bit A
Bit B
Bit C
Bit D
Bit E
Bit F
Operation
Zero speed
1: Operating
1: Zero speed
Frequency agree
Desired frequency agree
Frequency detection 1
Frequency detection 2
Drive startup completed
1: Matched
1: Matched
1: Output frequency
≤
L4-01
1: Output frequency
≥
L4-01
1: Startup completed
Low voltage detection 1: Detected
Baseblock
Frequency reference mode
Run command mode
Overtorque detection
Frequency reference lost
Retrying error
1: Drive output baseblock
1: Not communication 0: Communication
1: Not communication 0: Communication
1: Detected
1: Lost
1: Retrying
Error (including Modbus communications time-out) 1:Error occurred
Modbus communications time-out 1: Timed out
Multi-function digital output status
Bit 0 Multi-function digital output 1 (terminal M1-M2) 1: ON 0: OFF
Multi-function digital output 2 (terminal M3-M4): 1: ON 0: OFF
Not used
Not used
002EH - 0030H Not used
Bit 1
Bit 2
Bits 3 to F
0031H Main circuit DC voltage
0032H - 0037H Not used
0038H
0039H
PI feedback level (Input equivalent to 100%/Max. output frequency; 10/1%; without sign)
PI input level (±100%/±Max. output frequency; 10/1%; with sign)
003AH
003BH
003CH
PI output level (±100%/±Max. output frequency; 10/1%; with sign)
CPU software number
Flash software number
Communication error details
003DH
Bit 0
Bit 1
Bit 2
Bit 3
Bit 4
Bit 5
Bit 6
Bits 7 to F
CRC error
Invalid data length
Not used
Parity error
Overrun error
Framing error
Time-out
Not used
003EH
003FH
KVA setting
Control method
Note: Communication error details are stored until an error reset is input (errors can be reset while the Drive is operating).
Communications D - 11
"
Broadcast Data
The following table shows the broadcast data. Broadcast data can be written to.
Table D.6 Broadcast Data
Register
Address
Contents
0001H
Operation signal
Bit 0
Bit 1
Bits 2 and 3
Bit 4
Bit 5
Bits 6 to B
Bit C
Run command 1: Operating 0: Stopped
Reverse operation command 1: Reverse 0: Forward
Not used
External error 1: Fault (set using H1-01)
Error Fault 1: Reset command (set using H1-02)
Not used
Multi-function digital input terminal S5 input
Bit D
Bit E
Multi-function digital input terminal S6 input
Multi-function digital input terminal S7 input
0002H
Bit F Not used.
Frequency reference 30000/100%
Note: Bit signals not defined in the broadcast operation signals use local node data signals continuously.
"
Enter Command
When writing parameters to the Drive from the PLC using Modbus communication, the parameters are temporarily stored in the constant data area in the Drive. To enable these parameters in the parameter data area, use the Enter command.
There are two types of Enter commands:
1. Enter commands that enable parameter data in RAM
2. Enter commands that write data to EEPROM (non-volatile memory) in the Drive at the same time as enabling data in RAM.
The following table shows the Enter command data. Enter command data can only be written.
The Enter command is enabled by writing 0 to register number 0900H or 0901H.
Register No.
0900H
0910H
Table D.7 Enter Command
Contents
Write parameter data to EEPROM
Parameter data is not written to EEPROM, but refreshed in RAM only.
IMPORTANT
The maximum number of times you can write to EEPROM using the Drive is 100,000. Do not frequently execute Enter commands (0900H) written to EEPROM.
The Enter command registers are write-only. Consequently, if reading these registers, the register address will become invalid (Error code: 02H).
Communications D - 12
"
Error Codes
The following table shows Modbus communication error codes.
Error
Code
Table D.8 Error Codes
Contents
01H
02H
03H
21H
22H
23H
24H
Function code error
A function code other than 03H, 08H, or 10H has been set by the PLC.
Invalid register number error
• The register address you are attempting to access is not recorded anywhere.
• With broadcast sending, a start address other than 0000H, 0001H, or 0002H has been set.
Invalid quantity error
• The number of data packets being read or written is outside the range of 1 to 16.
• In write mode, the number of data packets in the message is not No. of packets x 2.
Data setting error
• Upper limit or lower limit error has occurred in the control data or when writing parameters.
• When writing parameters, the parameter setting is invalid.
Write mode error
• Attempting to write parameters to the Drive during run.
• Attempting to write via Enter commands during run.
• Attempting to write parameters other than A1-00 to A1-05, E1-03, or 02-04 when a
CPF03 (defective EEPROM) fault has occurred.
• Attempting to write read-only data.
Writing during main circuit undervoltage (UV) fault
• Writing parameters to the Drive during UV (main circuit undervoltage) alarm.
• Writing via Enter commands during UV (main circuit undervoltage) alarm.
Writing error during parameters processing
Attempting to write parameters while processing parameters in the Drive.
"
Slave Not Responding
In the following cases, the slave will ignore the write function.
•
When a communication error (overrun, framing, parity, or CRC-16) is detected in the command message.
•
When the slave address in the command message and the slave address in the Drive do not agree.
•
When the data that configures the message and the data time length exceed 24 bits.
•
When the command message data length is invalid.
IMPORTANT
If the slave address specified in the command message is 0, all slaves execute the write function, but do not return response messages to the master.
Communications D - 13
Modbus Self-Diagnosis
The Drive has a built-in function for self-diagnosing the operations of serial communication interface circuits. The self-diagnosis function connects the communication parts of the send and receive terminals, receives the data sent by the
Drive, and checks if communication is being performed normally.
Perform the self-diagnosis function using the following procedure.
1.
Turn ON the power supply to the Drive, and set parameter H1-05 (Terminal S7 Function Selection) to 67 (Com Test
Mode).
2.
Turn OFF the power supply to the Drive.
3.
Perform wiring according to the following diagram while the power supply is turned OFF.
4.
Turn ON the terminating resistance. (Turn ON pin 1 on DIP switch 1.)
5.
Turn ON the power supply to the Drive again.
Fig. D.10 Communication Terminal Connection for Self -Diagnosis Function
6.
During normal self-diagnostic operation, the Digital Operator displays the frequency reference value. If an error occurs, a
CE (Modbus communication error) alarm will be displayed on the Digital Operator, the fault contact output will be turned
ON, and the Drive operation ready signal will be turned OFF.
Communications D - 14
Appendix E
Peripheral Devices
This appendix describes recommended branch short circuit protection and peripheral devices.
General Peripheral Devices ........................................................... 2
Magnetic Contactor ................................................................... 2
AC and DC reactor .................................................................... 2
Noise filter ................................................................................. 2
Peripheral Devices E - 1
General Peripheral Devices
The following peripheral devices may be required to be mounted between the AC main circuit power supply and the Drive input terminals R/L1, S/L2, and T/L3.
CAUTION
Never connect a general LC/RC noise filter to the DriveDrive output circuit.
Never connect a phase-advancing capacitor to the input or output sides, or a surge suppressor to the output side of the Drive. When magnetic contactor is installed between the Drive and the motor, never turn it on or off during operation.
For more details on peripheral devices, contact the manufacturer.
!
Magnetic Contactor
Mount a surge protector on the coil. When using a magnetic contactor to start and stop the Drive, do not exceed one start per hour.
!
AC and DC reactor
Install a reactor to connect to a power supply transformer of large capacity (600 kVA or more) or to improve the power factor on the power supply side.
4000
AC or D C
Reactor Required
600
AC or D C
Reactor Not Required
0 60
Fig E.1 Connected Drive (kVA)
400
!
Noise filter
Use a noise filter exclusively for the Drive if radio noise generated from the Drive causes other control devices to malfunction.
Peripheral Devices E - 2
Appendix F
Replacement Parts
This appendix lists the primary parts that may be needed to maintain or service the Drive and Bypass unit.
Primary Parts - 208/230/240 VAC .................................................. 2
Primary Parts - 480 VAC ................................................................ 3
Bypass Replacement Parts ............................................................. 4
Spare Parts F - 1
Primary Parts - 208/230/240VAC
Drive Model
CIMR-P7U
20P4
20P7
2018
2022
2030
2037
2045
2055
2075
2090
2110
21P5
22P2
23P7
25P5
27P5
2011
2015
Nominal
Hp
0.5/0.75
1
1.5/2
3
5
25
30
40
7.5
10
15
20
50
60
75
75/100
125
150
Power PCB
(3PCB)
ETP617012
ETP617012
Table F.1 208-240VAC Primary Parts
Gate Drive PCB
(3PCB)
N/A
N/A
Control PCB
(1PCB)
ETC618021-S3010
ETC618021-S3010
ETP617022
ETP617032
ETP617042
ETP617052
N/A
N/A
N/A
N/A
ETC618021-S3010
ETC618021-S3010
ETC618021-S3010
ETC618021-S3010
ETP617062 N/A
ETP617422 N/A
N/A
ETC618021-S3010
ETC618021-S3010
ETC617032 ETC618021-S3010
N/A
N/A
N/A
N/A
N/A
N/A
N/A
N/A
N/A
ETC617042
ETC617053
ETC617063
ETC617073
ETC617083
ETC617093
ETC617103
ETC617113
ETC617531
ETC618021-S3010
ETC618021-S3010
ETC618021-S3010
ETC618021-S3010
ETC618021-S3010
ETC618021-S3010
ETC618021-S3010
ETC618021-S3010
ETC618021-S3010
Terminal PCB
(2PCB)
ETC618141
ETC618141
ETC618141
ETC618141
ETC618141
ETC618141
ETC618141
ETC618141
ETC618141
ETC618141
ETC618141
ETC618141
ETC618141
ETC618141
ETC618141
ETC618141
ETC618141
ETC618141
Diode Module
Inside the Power Module
Inside the Power Module
Inside the Power Module
Inside the Power Module
Inside the Power Module
Inside the Power Module
Inside the Power Module
SID003113 (D1)
SID003114 (D1,D2)
SID003113 (D1,D2)
SID003130 (D1,D2)
SID003115 (D1,D2)
SID003115 (D1,D2)
SID003116 (D1,D6)
SID003116 (D1,D6)
SID003108 (D1,D12)
Drive Model
CIMR-P7U
20P4
20P7
2018
2022
2030
2037
2045
2055
2075
2090
2110
21P5
22P2
23P7
25P5
27P5
2011
2015
Nominal
Hp
0.5/0.75
1
1.5/2
3
5
25
30
40
7.5
10
15
20
50
60
75
75/100
125
150
Table F.1 208-240VAC Primary Parts (Continued)
Power Module Transistor Module DC Bus Fuse Heat Sink Fan
STR001297 (Q1)
STR001297 (Q1)
STR001299 (Q1)
STR001301 (Q1)
STR001303 (Q1)
STR001304 (Q1)
STR001278 (Q1)
N/A
N/A
N/A
N/A
N/A
N/A
N/A
N/A
N/A
N/A
N/A
Inside the Power Module
Inside the Power Module
Inside the Power Module
Inside the Power Module
Inside the Power Module
Inside the Power Module
Inside the Power Module
STR001315 (Q1)
STR001315 (Q1)
STR001320 (Q1)
STR001314 (Q1)
STR001323 (Q1)
STR001293 (Q1-Q3)
STR001335 (Q1-Q3)
STR001335 (Q1-Q3)
STR001349 (Q1-Q6)
STR001338 (Q1-Q6)
STR001351 (Q1-Q12)
FU-002029 (F1)
FU-002029 (F1)
FU-002029 (F1)
FU-002030 (F1)
FU-002031 (F1)
FU-002099 (F1)
FU-002107 (F1)
FU-002108 (F1)
FU-002108 (F1)
FU-002109 (F1)
FU-002110 (F1)
FU-002110 (F1)
FU-002102 (F1)
FU-000925 (F1)
FU-000938 (F1)
FU-000926 (F1)
FU-002105 (F1)
FU-002106 (F1)
N/A
N/A
N/A
N/A
FAN001066 (B1)
FAN001066 (B1)
FAN001066 (B1,B2)
FAN001066 (B1,B2)
FAN001065 (B1,B2)
FAN001065 (B1,B2)
FAN001039 (B1,B2)
FAN001039 (B1,B2)
FAN001049 (B1,B2)
FAN001049 (B1,B2)
FAN001052 (B1,B2)
FAN001056 (B1,B2)
FAN001056 (B1,B2)
FAN001056 (B1,B2)
Internal Fan
N/A
N/A
N/A
N/A
N/A
N/A
N/A
FAN001043 (B3)
N/A
FAN001043 (B3)
N/A
N/A
FAN001053 (B4)
FAN001053 (B4)
FAN001054 (B4)
FAN001054 (B4)
FAN001054 (B4)
FAN001054 (B4)
Spare Parts F - 2
Primary Parts - 480VAC
Drive Model
CIMR-P7U
40P4
40P7
41P5
42P2
43P7
45P5
47P5
4011
4015
4018
4030
4037
4045
4055
4075
4090
4110
4160
4185
4220
4300
Nominal
Hp
0.5/0.75
1
1.5/2
3
5
7.5
10
15/20
25
30
40/50
60
75
100
125
150
200
250
300/350
400/450
500+
Power PCB
(3PCB)
Table F.2 480VAC Primary Parts
Gate Drive PCB
(3PCB)
N/A
N/A
N/A
N/A
N/A
N/A
N/A
N/A
N/A
N/A
ETP617082
ETP617082
ETP617092
ETP617102
ETP617112
ETP617132
N/A
N/A
N/A
N/A
N/A
N/A
ETP617142
ETP617152
N/A
N/A
ETP617162 N/A
ETP617172 N/A
N/A ETC617151
ETC617161
ETC617171
ETC617181
ETC617190
ETC617200
ETC617210
ETC617230
ETC617240
ETC617250
ETC617260
Control PCB
(1PCB)
ETC618021-S3010
ETC618021-S3010
ETC618021-S3010
ETC618021-S3010
ETC618021-S3010
ETC618021-S3010
ETC618021-S3010
ETC618021-S3010
ETC618021-S3010
ETC618021-S3010
ETC618021-S3010
ETC618021-S3010
ETC618021-S3010
ETC618021-S3010
ETC618021-S3010
ETC618021-S3010
ETC618021-S3010
ETC618021-S3010
ETC618021-S3010
ETC618021-S3010
ETC618021-S3010
Terminal PCB
(2PCB)
ETC618141
ETC618141
ETC618141
ETC618141
ETC618141
ETC618141
ETC618141
ETC618141
ETC618141
ETC618141
ETC618141
ETC618141
ETC618141
ETC618141
ETC618141
ETC618141
ETC618141
ETC618141
ETC618141
ETC618141
ETC618141
Diode Module
Inside the Power Module
Inside the Power Module
Inside the Power Module
Inside the Power Module
Inside the Power Module
Inside the Power Module
Inside the Power Module
Inside the Power Module
SID003112 (D1,D2)
SID003112 (D1,D2)
SID000605 (D1,D2)
SID000605 (D1,D2)
SID003117 (D1,D2)
SID003117 (D1,D2)
SID003109 (D1,D6)
SID003119 (D1,D6)
SID003119 (D1,D6)
SID003131 (D1,D6)
SID003119(D1,D12)
Drive Model
CIMR-P7U
40P4
4011
4015
4018
4030
4037
4045
4055
40P7
41P5
42P2
43P7
45P5
47P5
4075
4090
4110
4160
4185
4220
4300
Nominal
Hp
10
15/20
25
30
60
75
100
125
150
0.5/0.75
1
1.5/2
3
5
7.5
10
200
250
300/350
400/450
500+
Table F.2 480VAC Primary Parts (Continued)
Power Module Transistor Module
STR001298 (Q1)
STR001298 (Q1)
STR001298 (Q1)
Inside the Power Module
Inside the Power Module
Inside the Power Module
STR001298 (Q1)
STR001300 (Q1)
Inside the Power Module
Inside the Power Module
STR001302 (Q1) Inside the Power Module
STR001279 (Q1) Inside the Power Module
N/A
N/A
N/A
N/A
N/A
N/A
N/A
STR001280 (Q1)
STR001318 (Q1)
STR001318 (Q1)
STR001324 (Q1)
STR001316 (Q1-Q3)
STR001317 (Q1-Q3)
STR001317 (Q1-Q3)
N/A
N/A
N/A
N/A
N/A
N/A
N/A
STR001294 (Q1-Q3)
STR001336 (Q1-Q6)
STR001336 (Q1-Q6)
STR001322 (Q1-Q3)
STR001339 (Q1-Q12)
STR001341 (Q1-Q12)
STR001342 (Q1-Q12)
DC Bus Fuse
FU-002029 (F1)
FU-002029 (F1)
FU-002029 (F1)
FU-002029 (F1)
FU-002031 (F1)
FU-002031 (F1)
FU-002032 (F1)
FU-002037 (F1)
FU-002038 (F1)
FU-002038 (F1)
FU-002039 (F1)
FU-002040 (F1)
FU-002040 (F1)
FU-002101 (F1)
FU-002112 (F1)
FU-002113 (F1)
FU-002114 (F1)
FU-000895 (F1)
FU-000895 (F1)
FU-002116 (F1)
FU-002117 (F1)
Heat Sink Fan
N/A
N/A
N/A
FAN001066 (B1)
FAN001066 (B1)
FAN001066 (B1)
FAN001066 (B1,B2)
FAN001066 (B1,B2)
FAN001065 (B1,B2)
FAN001065 (B1,B2)
FAN001039 (B1,B2)
FAN001044 (B1,B2)
FAN001044 (B1,B2)
FAN001044 (B1,B2)
FAN001052 (B1,B2)
FAN001052 (B1,B2)
FAN001056 (B1,B2)
FAN001056 (B1,B2)
FAN001056 (B1,B4)
FAN001056 (B1,B4)
FAN001082 (B1,B5)
Internal Fan
N/A
N/A
N/A
N/A
N/A
N/A
N/A
FAN001043 (B3)
N/A
FAN001043 (B3)
N/A
N/A
N/A
N/A
FAN001054 (B4)
FAN001054 (B4)
FAN001054 (B4)
FAN001054 (B4)
FAN001054 (B6,B7)
FAN001054 (B6,B7)
FAN001054 (B6,B7)
Spare Parts F - 3
Bypass Replacement Parts
480 P7U42P2VA
P7U42P2VA
P7U42P2VA
P7U42P2VA
P7U42P2VA
P7U42P2VA
P7U43P7VA
P7U45P5VA
P7U47P5VA
P7U4011VA
P7U4011VA
P7U4015VA
P7U4018VA
P7U4030QA
P7U4030QA
P7U4037QA
P7U4045QA
P7U4055QA
P7U4055QA
P7U4075QA
P7U40900A
P7U41100A
P7U41600A
P7U41850A
P7U41850A
P7U42200A
P7U42200A
P7U43000A
240
230
P7U22P2VA
P7U22P2VA
P7U22P2VA
P7U22P2VA
P7U22P2VA
P7U22P2VA
P7U23P7VA
P7U25P5VA
P7U27P5VA
P7U2011VA
P7U2015VA
P7U2018VA
P7U20221A
P7U20301A
P7U20370A
P7U20370A
P7U20450A
P7U20750A
P7U20750A
P7U20900A
INPUT
VOLTS
Drive
MAIN P/N
CIMR-
208 P7U22P2VA
P7U22P2VA
P7U22P2VA
P7U22P2VA
P7U22P2VA
P7U22P2VA
P7U23P7VA
P7U27P5VA
P7U27P5VA
P7U2011VA
P7U2015VA
P7U2018VA
P7U20221A
P7U20301A
P7U20301A
P7U20370A
P7U20450A
P7U20550A
P7U20750A
P7U20900A
P7U21100A
60
75
100
125
150
40
40
50
20
25
30
7.5
10
15
2
3
5
0.5
0.75
1
1.5
NEC
NOM.
HP
P7
BYPASS
BASE NO.
P7B_XXXX
D059
D074
D088
D114
D114
D143
D169
D211
D273
D343
D396
D002
D003
D004
N/A
D007
D010
D016
D024
D030
D046
Motor Circuit Protector
SQ. D
PART
NO.
FAL3600712M
YASK.
PART
NO.
50188255
FAL3600712M
FAL3600712M
FAL3601513M
50188255
50188255
50188256
FAL3601513M
FAL3601513M
FAL3603015M
FAL3605016M
FAL3605016M
FAL3610018M
50188256
50188256
50188250
50188251
50188251
50188252
FAL3610018M
KAL3615026M
KAL3615026M
KAL3625032M
KAL3625032M
KAL3625032M
50188252
50188260
50188260
50188267
50188267
50188267
KAL3625032M
LAL3640036M
LAL3640036M
50188267
50188275
50188275
MAL3660036M UCB000061
MAL3660036M UCB000061
Table F.3 Bypass Replacement Parts
139
111
112
113
114
84
85
138
139
139
139
96
97
83
95
95
95
Input Contactor
YASK.
P/N
5P32-
92
SQ. D
P/N (K1)
LC1-
D0901F7
92
92
95
D0901F7
D0901F7
D1801F7
D1801F7
D1801F7
D1801F7
D2501F7
D3201F7
D5011F7
D6511F7
D8011F7
D11500F7
D15000F7
D15000F7
D15000F7
D15000F7
F265F7
F330F7
F400F7
F500F7
139
111
111
112
113
84
85
138
139
139
139
96
97
83
95
95
95
Output Contactor
YASK.
P/N
5P32-
92
SQ. D
P/N (K2)
LC1-
D0901F7
92
92
95
D0901F7
D0901F7
D1801F7
D1801F7
D1801F7
D1801F7
D2501F7
D3201F7
D5011F7
D6511F7
D8011F7
D11500F7
D15000F7
D15000F7
D15000F7
D15000F7
F265F7
F265F7
F330F7
F400F7
111
112
113
114
114
84
85
138
139
139
110
96
97
83
95
95
95
Bypass Contactor
YASK.
P/N
5P32-
92
SQ. D
P/N (K3)
LC1-
D0901F7
Overload Relay
SQ. D
PART (S10)
NO.
LR2-D1307
YASK.
P/N
5P37-
148
92
92
95
D0901F7 LR2-D1508
D0901F7 LR2-D1510
D1801F7 LR2-D1512
174
175
176
D1801F7 LR2-D1512
D1801F7 LR2-D1516
D1801F7 LR2-D1521
D2501F7 LR2-D1522
D3201F7 LR2-D2553
D5011F7 LR2-D3557
176
178
179
180
181
185
D6511F7 LR2-D3559
D8011F7 LR2-D3563
D11500F7 LR9-F5567
D15000F7 LR9-F5569
D15000F7 LR9-F5569
F185G6 LR9-F5569
F265F7
F330F7
F400F7
F500F7
F500F7
LR9-F5571
LR9-F7575
LR9-F7575
LR9-F7579
LR9-F7579
246
247
247
248
248
186
188
244
245
245
245
300D3
300D3
300D3
300D3
500D3
500D3
500D3
500D3
500D3
750D3
750D3
Control Transformer
SQ. D
P/N
TF-
300D3
YASK.
PART
NO.
50210414
CPT Primary Fuses
YASKAWA
PART NO.
5P17-0359
BUSSMANN
PART NO.
FNQ-R-4
300D3
300D3
300D3
50210414 5P17-0359
50210414 5P17-0359
50210414 5P17-0359
FNQ-R-4
FNQ-R-4
FNQ-R-4
300D3
300D3
300D3
300D3
300D3
300D3
50210414
50210414
5P17-0359
50210414 5P17-0359
50210414 5P17-0359
5P17-0359
50210414 5P17-0359
50210414 5P17-0359
FNQ-R-4
FNQ-R-4
FNQ-R-4
FNQ-R-4
FNQ-R-4
FNQ-R-4
50210414 5P17-0359
50210414 5P17-0359
50210414 5P17-0359
50210414 5P17-0359
50210416 5P17-0360
50210416 5P17-0360
50210416 5P17-0360
50210416 5P17-0360
50210416 5P17-0360
FNQ-R-4
FNQ-R-4
FNQ-R-4
FNQ-R-4
FNQ-R-5
FNQ-R-5
FNQ-R-5
FNQ-R-5
FNQ-R-5
50210417 5P17-0361 FNQ-R-7 1/2
50210417 5P17-0361 FNQ-R-7 1/2
FAL3600311M
FAL3600712M
FAL3600712M
FAL3601513M
FAL3601513M
FAL3601513M
FAL3603015M
FAL3605016M
FAL3605016M
FAL3610018M
FAL3610018M
FAL3610018M
KAL3615026M
KAL3615026M
KAL3625032M
KAL3625032M
KAL3625032M
LAL3640036M
50188260
50188260
50188267
50188267
50188267
50188275
MAL3660036M UCB000061
MAL3660036M UCB000061
50188254
50188255
50188255
50188256
50188256
50188256
50188250
50188251
50188251
50188252
50188252
50188252
FAL3600311M
FAL3600311M
FAL3600712M
FAL3600712M
FAL3600712M
FAL3600712M
FAL3601513M
FAL3601513M
FAL3603015M
FAL3605016M
FAL3605016M
FAL3605016M
FAL3610018M
FAL3610018M
FAL3610018M
FAL3610018M
KAL3615026M
KAL3625032M
KAL3625032M
KAL3625032M
KAL3625032M
LAL3640036M
50188267
50188275
LAL3640036M 50188275
MAL3660036M UCB000061
MAL3660036M UCB000061
MAL3680040M UCB000072
MAL3680040M UCB000072
MAL3680040M UCB000072
50188251
50188252
50188252
50188252
50188252
50188260
50188267
50188267
50188267
50188254
50188254
50188255
50188255
50188255
50188255
50188256
50188256
50188250
50188251
50188251
B034
B040
B052
B065
B077
B096
B124
B124
B156
B007
B011
B014
B021
B027
B001
B001
B002
N/A
B003
B004
B180
B240
B302
B361
B414
B477
B515
B590
A015
A022
A028
A042
A054
A068
A002
A003
A004
N/A
A006
A009
A080
A104
A130
A154
A192
A248
A312
A360
25
30
40
50
60
75
100
100
125
5
7.5
10
15
20
0.5
0.75
1
1.5
2
3
150
200
250
300
350
400
450
500
15
20
25
5
7.5
10
0.5
0.75
1
1.5
2
3
60
75
100
30
40
50
125
150
93
93
83
84
85
138
139
139
110
95
95
95
96
97
92
92
92
92
92
92
111
112
113
114
114
114
115
115
D4011F7
D4011F7
D5011F7
D6511F7
D8011F7
D11500F7
D15000F7
D15000F7
D15000F7
D0901F7
D0901F7
D0901F7
D0901F7
D0901F7
D0901F7
D1801F7
D1801F7
D1801F7
D2501F7
D3201F7
D15000F7
F265F7
F330F7
F400F7
F400F7
F500F7
F500F7
F500F7
83
84
85
95
96
97
95
95
95
92
92
92
85
138
139
110
111
112
113
114
D0901F7
D0901F7
D0901F7
D1801F7
D1801F7
D1801F7
D1801F7
D2501F7
D3201F7
D5011F7
D6511F7
D8011F7
D8011F7
D11500F7
D15000F7
D15000F7
F265F7
F265F7
F330F7
F330F7
93
93
83
84
85
138
139
139
139
95
95
95
96
97
92
92
92
92
92
92
139
111
112
113
113
114
114
114
83
84
85
95
96
97
95
95
95
92
92
92
85
138
139
139
111
111
112
112
D4011F7
D4011F7
D5011F7
D6511F7
D8011F7
D11500F7
D15000F7
D15000F7
D15000F7
D0901F7
D0901F7
D0901F7
D0901F7
D0901F7
D0901F7
D1801F7
D1801F7
D1801F7
D2501F7
D3201F7
D15000F7
F265F7
F330F7
F400F7
F500F7
F500F7
F500G7
F500F7
D0901F7
D0901F7
D0901F7
D1801F7
D1801F7
D1801F7
D1801F7
D2501F7
D3201F7
D5011F7
D6511F7
D8011F7
D8011F7
D11500F7
D15000F7
D15000F7
F265F7
F265F7
F330F7
F400F7
93
93
83
84
85
138
139
139
139
95
95
95
96
97
92
92
92
92
92
92
139
111
112
113
114
114
114
114
83
84
85
95
96
97
95
95
95
92
92
92
85
138
139
139
111
111
112
113
184
184
186
187
188
244
245
245
246
176
178
179
180
181
146
146
148
174
174
175
246
247
248
248
249
249
249
249
179
180
181
185
186
187
148
174
174
176
176
177
188
245
245
246
246
247
248
248
D0901F7 LR2-D1307
D0901F7 LR2-D1508
D0901F7 LR2-D1508
D1801F7 LR2-D1512
D1801F7 LR2-D1512
D1801F7 LR2-D1514
D1801F7 LR2-D1521
D2501F7 LR2-D1522
D3201F7 LR2-D2553
D5011F7 LR2-D3557
D6511F7 LR2-D3559
D8011F7 LR2-D3561
D8011F7 LR2-D3563
D11500F7 LR9-F5569
D15000F7 LR9-F5569
F185G6
F265F7
F330F7
F400F7
F500F7
LR9-F5571
LR9-F5571
LR9-F7575
LR9-F7579
LR9-F7579
F265F7
F330F7
F400F7
F500F7
F500F7
F500F7
F630F7
F630F7
D0901F7 LR2-D1306
D0901F7 LR2-D13X6
D0901F7 LR2-D1307
D0901F7 LR2-D1508
D0901F7 LR2-D1508
D0901F7 LR2-D1510
D1801F7 LR2-D1512
D1801F7 LR2-D1516
D1801F7 LR2-D1521
D2501F7 LR2-D1522
D3201F7 LR2-D2553
D4011F7 LR2-D3555
D4011F7 LR2-D3555
D5011F7 LR2-D3559
D6511F7 LR2-D3561
D8011F7 LR2-D3563
D11500F7 LR9-F5567
D15000F7 LR9-F5569
D15000F7 LR9-F5569
F185G6 LR9-F5571
LR9-F5571
LR9-F7575
LR9-F7579
LR9-F7579
LR9-F7581
LR9-F7581
LR9-F7581
LR9-F7581
300D1
300D1
300D1
300D1
300D1
300D1
300D1
300D1
300D1
300D1
300D1
300D1
300D1
300D1
500D1
500D1
500D1
500D1
500D1
750D1
5P58-1010 5P617-0391 FNQ-R-3 1/2
5P58-1010 5P617-0391 FNQ-R-3 1/2
5P58-1010 5P617-0391 FNQ-R-3 1/2
5P58-1010 5P617-0391 FNQ-R-3 1/2
5P58-1010 5P617-0391 FNQ-R-3 1/2
5P58-1010 5P617-0391 FNQ-R-3 1/2
5P58-1010 5P617-0391 FNQ-R-3 1/2
5P58-1010 5P617-0391 FNQ-R-3 1/2
5P58-1010 5P617-0391 FNQ-R-3 1/2
5P58-1010 5P617-0391 FNQ-R-3 1/2
5P58-1010 5P617-0391 FNQ-R-3 1/2
5P58-1010 5P617-0391 FNQ-R-3 1/2
5P58-1010 5P617-0391 FNQ-R-3 1/2
5P58-1010 5P617-0391 FNQ-R-3 1/2
50210407 5P17-0360 FNQ-R-5
50210407 5P17-0360
50210407 5P17-0360
50210407 5P17-0360
FNQ-R-5
FNQ-R-5
FNQ-R-5
50210407 5P17-0360 FNQ-R-5
50210405 5P17-0361 FNQ-R-7 1/2
300D1
300D1
300D1
300D1
300D1
300D1
300D1
500D1
500D1
300D1
300D1
300D1
300D1
300D1
300D1
300D1
300D1
300D1
300D1
300D1
500D1
500D1
500D1
750D1
750D1
750D1
1000D1
1000D1
5P58-1010 5P17-0356 FNQ-R-1 1/2
5P58-1010 5P17-0356 FNQ-R-1 1/2
5P58-1010 5P17-0356 FNQ-R-1 1/2
5P58-1010 5P17-0356 FNQ-R-1 1/2
5P58-1010 5P17-0356 FNQ-R-1 1/2
5P58-1010 5P17-0356 FNQ-R-1 1/2
5P58-1010 5P17-0356 FNQ-R-1 1/2
5P58-1010 5P17-0356 FNQ-R-1 1/2
5P58-1010 5P17-0356 FNQ-R-1 1/2
5P58-1010 5P17-0356 FNQ-R-1 1/2
5P58-1010 5P17-0356 FNQ-R-1 1/2
5P58-1010 5P17-0356 FNQ-R-1 1/2
5P58-1010 5P17-0356 FNQ-R-1 1/2
5P58-1010 5P17-0356 FNQ-R-1 1/2
5P58-1010 5P17-0356 FNQ-R-1 1/2
5P58-1010 5P17-0356 FNQ-R-1 1/2
5P58-1010 5P17-0356 FNQ-R-1 1/2
5P58-1010 5P17-0356 FNQ-R-1 1/2
50210407 5P17-0357 FNQ-R-2 1/2
50210407 5P17-0357 FNQ-R-2 1/2
50210407 5P17-0357 FNQ-R-2 1/2
50210407 5P17-0357 FNQ-R-2 1/2
50210407 5P17-0357 FNQ-R-2 1/2
50210405 5P617-0391 FNQ-R-3 1/2
50210405 5P617-0391 FNQ-R-3 1/2
50210405 5P617-0391 FNQ-R-3 1/2
5P58-1011 5P17-0360 FNQ-R-5
5P58-1011 5P17-0360 FNQ-R-5
Spare Parts F - 4
Table F.3 Bypass Replacement Parts
CPT Secondary Fuses
YASKAWA
PART NO.
N/A
N/A
N/A
N/A
N/A
N/A
N/A
N/A
N/A
N/A
N/A
N/A
N/A
N/A
5P617-0392
BUSSMANN
PART NO.
N/A
N/A
N/A
N/A
N/A
N/A
N/A
N/A
N/A
N/A
N/A
N/A
N/A
N/A
Drive Input Fuses - Option F
Semiconductor Fuses F3, F4, F5 (QTY. 3)
YASKAWA
PART NO.
UFU000025
BUSSMANN
PART NO.
FWH-5A14F
YASKAWA
PART NO.
UFU000062
Fuse Block F3, F4, F5
PART NUMBER QTY.
BUSSMANN SHAWMUT REQ'D.
70308 1
5P17-0422 FWH-10A14F UFU000062
5P17-0422 FWH-10A14F UFU000062
UFU000028 FWH-15A14F UFU000062
UFU000028 FWH-15A14F UFU000062
UFU000029 FWH-25A14F UFU000062
UFU000032
5P617-0385
5P17-0363
5P17-0260
5P17-0261
FWH-40B
FWH-50B
FWH-70B
FWH-100B
FWH-125B
UFU000035 FWH-175B
5P17-0245 FWH-200B
UFU000052 FWX-225A
FNQ-R-7 UFU000052 FWX-225A
5P19-0104
5P19-0104
5P19-0104
5P19-0104
5P19-0105
5P19-0105
5P19-0105
5P19-0106
5P19-0106
1BS101
1BS101
1BS101
1BS101
1BS102
1BS102
1BS102
1BS103
1BS103
70308
70308
70308
70308
70308
1
1
1
1
1
3
3
3
3
3
3
3
3
3
5P617-0392
5P617-0392
FNQ-R-7
FNQ-R-7
UFU000055
UFU000055
FWX-300A
FWX-300A
5P19-0106
5P19-0106
1BS103
1BS103
3
3
5P617-0392
5P617-0392
5P617-0392
5P617-0392
FNQ-R-7
FNQ-R-7
FNQ-R-7
FNQ-R-7
UFU000057
UFU000044
UFU000061
UFU000061
FWX-400A
FWH-500A
FWX-700A
FWX-700A
5P19-0106
UFU000063
UFU000065
UFU000065
1BS103
1BS104
BH3145
BH3145
3
3
3
3
DC Bus Choke
3% - Option X
YASKAWA
PART NO.
MTE
P/N
5% - Option Z
YASKAWA
PART NO.
MTE
P/N
3% Reactor-Option R
YASKAWA
PART
NUMBER
MTE
PART
NUMBER
5% Reactor-Option K
YASKAWA
PART
NUMBER
URX000041 4RB002 5P620-0109 4RB003
5P620-0111 9RB003 URX000041 4RB002
5P620-0017 RL-00401 URX000080
5P620-0017 RL-00401 5P620-0132
URX000046 12RB004 5P620-0111 9RB003 5P620-0024 RL-00801 5P620-0017
5P652-0213 12RB003 URX000046 12RB004 5P620-0024 RL-00801 5P620-0133
URX000048 18RB003 5P652-0213 12RB003 5P620-0024 RL-00801 5P620-0133
URX000052 25RB003 5P652-0213 12RB003 5P620-0136 RL-01801 5P620-0134
URX000053 25RB004 URX000052 25RB003 URX000083 RL-02501 5P620-0136
5P620-0120 32RB001 URX000055 32RB002 URX000083 RL-02501 5P620-0139
MTE
PART
NUMBER
URX000059 50RB001 URX000061 50RB003 5P620-0044 RL-03501 5P620-0049
URX000059 50RB001 URX000059 50RB001 5P620-0141 RL-05501 5P620-0142
URX000068 80RB002 URX000073 92RB002 5P620-0143 RL-08001 5P620-0144
URX000085 RL-10001 5P620-0143
URX000085 RL-10001 5P620-0013
5P620-0064 RL-13001 5P620-0013
5P620-0064 RL-13001 5P620-0013
5P620-0069 RL-16001 5P620-0070
5P620-0075 RL-20001 5P620-0146
5P620-0080 RL-25001 5P620-0147
5P620-0085 RL-32001 5P620-0148
URX000087 RL-40001 5P620-0090
URX000088 RL-50001 5P620-0094
RFI Filter - Option E
NEW
SAP
PART NO.
MTE/SCHAFFNER
PART
NUMBER
UFI000035
UFI000035
UFI000035
UFI000035
UFI000035
UFI000036
UFI000036
UFI000037
UFI000039
UFI000039
UFI000041
UFI000041
UFI000042
UFI000042
UFI000042
UFI000043
RF3-0010-4
RF3-0010-4
RF3-0010-4
RF3-0010-4
RF3-0010-4
RF3-0018-4
RF3-0018-4
RF3-0025-4
RF3-0050-4
RF3-0050-4
RF3-0090-4
RF3-0090-4
RF3-0130-4
RF3-0130-4
RF3-0130-4
RF3-0150-4
UFI000044
UFI000044
RF3-0330-4
RF3-0330-4
UFI000044 RF3-0330-4
UFI000032 FS5972-600-99
UFI000032 FS5972-600-99
N/A
N/A
N/A
N/A
N/A
N/A
5P617-0392
5P617-0392
N/A
N/A
N/A
N/A
N/A
N/A
N/A
N/A
5P617-0392
5P617-0392
5P617-0392
5P617-0392
N/A
N/A
N/A
N/A
UFU000025 FWH-5A14F UFU000062
5P17-0422 FWH-10A14F UFU000062
5P17-0422 FWH-10A14F UFU000062
UFU000028 FWH-15A14F UFU000062
N/A
N/A
N/A
N/A
N/A
N/A
N/A
N/A
N/A
N/A
FNQ-R-7
FNQ-R-7
UFU000028 FWH-15A14F UFU000062
5P17-0338 FWH-20A14F UFU000062
UFU000031
UFU000032
5P17-0288
UFU000034
5P17-0261
5P17-0279
FWH-35B
FWH-40B
FWH-60B
FWH-90B
FWH-125B
FWH-150B
UFU000035 FWH-175B
5P17-0245 FWH-200B
UFU000036
UFU000055
FWH-250A
FWX-300A
5P19-0104
5P19-0104
5P19-0104
5P19-0104
5P19-0105
5P19-0105
5P19-0105
5P19-0105
5P19-0106
5P19-0106
1BS101
1BS101
1BS101
1BS101
1BS102
1BS102
1BS102
1BS102
1BS103
1BS103
FNQ-R-7 UFU000057 FWX-400A 5P19-0106 1BS103
FNQ-R-7 UFU000044 FWH-500A UFU000063 1BS104
FNQ-R-7 5P17-0265 FWH-600A UFU000063 1BS104
FNQ-R-7 UFU000061 FWX-700A UFU000065 BH3145
N/A
N/A
N/A
N/A
N/A
N/A
N/A
N/A
N/A
N/A
N/A
N/A
N/A
N/A
N/A
N/A
N/A
N/A
5P617-0392
5P617-0392
5P617-0392
5P617-0392
5P617-0392
5P617-0392
N/A
N/A
N/A
N/A
N/A
N/A
N/A
N/A
UFU000023
UFU000024
UFU000025
UFU000026
5P17-0422
FWH-3A14F
FWH-4A14F
FWH-5A14F
FWH-6A14F
UFU000062
UFU000062
UFU000062
UFU000062
FWH-10A14F UFU000062
UFU000027 FWH-12A14F UFU000062
5P17-0338 FWH-20A14F UFU000062
UFU000029 FWH-25A14F UFU000062
N/A
N/A
N/A
N/A
N/A
N/A
N/A
N/A
N/A
N/A
FNQ-R-7
FNQ-R-7
FNQ-R-7
FNQ-R-7
UFU000030 FWH-30A14F UFU000062
5P617-0385
5P17-0363
5P617-0347
5P17-0260
5P17-0260
5P17-0261
5P17-0279
5P17-0245
5P617-0348
5P617-0348
UFU000040
UFU000040
UFU000042
FWH-50B
FWH-70B
FWH-80B
FWH-100B
FWH-100B
FWH-125B
FWH-150B
FWH-200B
FWH-225A
FWH-225A
FWH-350A
FWH-350A
170M5608
5P19-0104
5P19-0104
5P19-0104
5P19-0104
5P19-0104
5P19-0105
5P19-0105
5P19-0105
5P19-0106
5P19-0106
5P19-0106
5P19-0106
1BS101
1BS101
1BS101
1BS101
1BS101
1BS102
1BS102
1BS102
1BS103
1BS103
1BS103
1BS103
UFU000064 170H3004
FNQ-R-7 UFU000045
FNQ-R-7 5P17-0265
170M6608
FWH-600A
UFU000064 170H3004
UFU000063 1BS104
70308
70308
70308
70308
70308
70308
70308
70308
70308
5P617-0392
5P617-0392
FNQ-R-7 UFU000046 FWH-700A UFU000065 BH3145
FNQ-R-7 UFU000046 FWH-700A UFU000065 BH3145
5P17-0395 FNQ-R-10 UFU000048 FWH-1000A
5P17-0395 FNQ-R-10 UFU000048 FWH-1000A
USE BUS BAR
USE BUS BAR
70308
70308
70308
70308
70308
70308
3
3
3
3
3
3
3
3
3
3
3
3
3
3
1
1
1
1
1
1
URX000041 4RB002 5P620-0109 4RB003 URX000080 RL-00204 5P620-0131
5P620-0111 9RB003 URX000041 4RB002 5P620-0017 RL-00401 5P620-0132
5P620-0111 9RB003 URX000044 9RB004
5P652-0213 12RB003 5P620-0111 9RB003
5P620-0017
5P620-0024
RL-00401
RL-00801
5P620-0132
5P620-0133
5P652-0213 12RB003 URX000046 12RB004 5P620-0024 RL-00801 5P620-0133
URX000048 18RB003 5P652-0213 12RB003 5P620-0134 RL-01201 5P620-0135
URX000052 25RB003 URX000048 18RB003 5P620-0136 RL-01801 5P620-0137
URX000053 25RB004 URX000052 25RB003 URX000083 RL-02501 5P620-0138
5P620-0120 32RB001 URX000055 32RB002 5P620-0044 RL-03501 5P620-0139
URX000059 50RB001 URX000060 50RB002 5P620-0140 RL-04501 5P620-0142
URX000068 80RB002 URX000070 80RB004 5P620-0141 RL-05501 5P620-0142
URX000068 80RB002 URX000073 92RB002 5P620-0143 RL-08001 5P620-0144
URX000085 RL-10001 5P620-0143
5P620-0064 RL-13001 5P620-0013
5P620-0064 RL-13001 5P620-0013
5P620-0069 RL-16001 5P620-0070
5P620-0075 RL-20001 5P620-0146
5P620-0080 RL-25001 5P620-0147
5P620-0085 RL-32001 5P620-0148
URX000087 RL-40001 5P620-0090
3
3
3
3
3
3
1
3
1
1
1
1
1
1
1
1
3
3
3
3
3
3
3
3
3
3
URX000039 2RB004 URX000039 2RB004 URX000078 RL-00104 URX000077
URX000039 2RB004 URX000039 2RB004 5P620-0131 RL-00201 5P620-0014
URX000042 4RB004 URX000039 2RB004
5P620-0109 4RB003 URX000042 4RB004
5P620-0131
5P620-0132
RL-00201
RL-00402
5P620-0014
URX000081
5P620-0109 4RB003 URX000042 4RB004
URX000044 9RB004 URX000044 9RB004
5P620-0132 RL-00402 URX000081
5P620-0025 RL-00803 5P620-0018
URX000046 12RB004 URX000044 9RB004 5P620-0133 RL-00802 5P620-0025
5P652-0213 12RB003 URX000046 12RB004 5P620-0135 RL-01202 5P620-0031
5P652-0216 18RB004 URX000049 18RB005 5P620-0137 RL-01802 5P620-0035
URX000056 32RB003 URX000054 25RB005 5P620-0138 RL-02502 5P620-0040
URX000055 32RB002 URX000056 32RB003 5P620-0139 RL-03502 5P620-0045
URX000061 50RB003 URX000061 50RB003 5P620-0139 RL-03502 5P620-0045
URX000061 50RB003 URX000061 50RB003 5P620-0049 RL-04502 5P620-0012
5P620-0142 RL-05502 URX000084
5P620-0144 RL-08002 5P620-0057
5P620-0145 RL-10002 5P620-0061
5P620-0145 RL-10002 5P620-0061
5P620-0013 RL-13002 5P620-0065
5P620-0013 RL-13002 5P620-0065
5P620-0070 RL-16002 URX000086
5P620-0146 RL-20002 5P620-0076
5P620-0147 RL-25002 5P620-0081
5P620-0148 RL-32002 5P620-0086
5P620-0090 RL-40002 5P620-0091
5P620-0094 RL-50002 URX000089
5P620-0094 RL-50002 URX000089
5P620-0098 RL-60002 URX000091
5P620-0098 RL-60002 URX000091
UFI000035
UFI000035
UFI000035
UFI000035
UFI000035
UFI000035
UFI000036
UFI000037
UFI000039
UFI000039
UFI000041
UFI000041
UFI000041
UFI000042
UFI000043
UFI000044
RF3-0010-4
RF3-0010-4
RF3-0010-4
RF3-0010-4
RF3-0010-4
RF3-0010-4
RF3-0018-4
RF3-0025-4
RF3-0050-4
RF3-0050-4
RF3-0090-4
RF3-0090-4
RF3-0090-4
RF3-0130-4
RF3-0150-4
RF3-0330-4
UFI000044
UFI000044
RF3-0330-4
RF3-0330-4
UFI000032 FS5972-600-99
UFI000032 FS5972-600-99
UFI000035
UFI000035
UFI000035
UFI000035
UFI000035
UFI000035
UFI000035
UFI000036
UFI000036
UFI000037
UFI000039
UFI000039
UFI000039
UFI000041
UFI000041
UFI000041
RF3-0010-4
RF3-0010-4
RF3-0010-4
RF3-0010-4
RF3-0010-4
RF3-0010-4
RF3-0010-4
RF3-0018-4
RF3-0018-4
RF3-0025-4
RF3-0050-4
RF3-0050-4
RF3-0050-4
RF3-0090-4
RF3-0090-4
RF3-0090-4
UFI000042
UFI000043
UFI000043
UFI000044
RF3-0130-4
RF3-0150-4
RF3-0150-4
RF3-0330-4
UFI000044
UFI000044
RF3-0330-4
RF3-0330-4
UFI000044 RF3-0330-4
UFI000032 FS5972-600-99
UFI000032 FS5972-600-99
UFI000032 FS5972-600-99
UFI000032 FS5972-600-99
UFI000033 FS5972-800-99
Spare Parts F - 5
Table F.4 Bypass Common Replacement Parts
Part Description
W1 AND W2 CABINET FAN
W1 AIR FILTER
W2 AIR FILTER
F1 CABINET FAN
F1 FILTER
DIGITAL OPERATOR
OPERATOR INTERGFACE PCB A3
22mm, selector SW, 2 pos., maintained
22mm, selector SW, 3 pos.,maintained
22mm, pilot light head for LED, WHITE
22mm, pilot light head for LED, GREEN
22mm, pilot light head for LED, RED
22mm, pilot light head for LED, AMBER
22mm, pilot light head for LED, BLUE
22mm, Body/Collar
22mm, PCB contact block 1 N.O., standard
22mm, PCB light module, LED, 24V, WHITE
22mm, PCB light module, LED, 24V, GREEN
22mm, PCB light module, LED, 24V, RED
Relay controller PCB A2
Cabinet door operator panel
W1 = Wall mount enclosure 1
W2 = Wall mount enclosure 2
F1 = Floor mount enclosure 1
Part Number
UFN000005
UFL00001-1
UFL00001-2
5P16-0012
UFL00001-3
CDR001115
UTC000037-2
USW000071
USW000072
USD000038
USD000039
USD000037
USD000040
USD000041
UBM-0006
UMC000080
USD000043
USD000044
USD000042
UTC00036
UOPN0001
Spare Parts F - 6
A
A. TUNE.................................................................. 3-7, 3-14
AC Reactor ....................................................................... E-4
Accel/Decel
Parameters .................................................................A-7
Switch Frequency ........................................... 5-19, A-7
Time .........................................................................5-19
Acceleration
Stall Prevention Level during ....................... 6-16, A-20
Time................................................................ 5-19, A-7
Troubleshooting............................. 6-5, 6-10, 6-12, 6-16
Access Level ................................................................... A-2
ADV .........................................................................3-7, 3-13
Alarm Displays & Processing............................................6-8
ALARM Indicator .............................................................3-4
Altitude ............................................................................ C-4
Ambient Temperature – See Temperature
Analog Inputs
Bias................................................................ 5-26, A-16
Connection Diagram.................................................2-16
Control Circuit Terminals.........................................2-13
Gain ............................................................... 5-26, A-15
Parameters ...............................................................A-16
Troubleshooting....................................................... 6-15
Analog Outputs
Bias ............................................................... A-17, A-18
Connection Diagram................................................ 2-16
Control Circuit Terminals........................................ 2-13
Gain ........................................................................ A-17
Parameters .................................................... A-17, A-18
APOGEE FLN ............................................. iii, iv, A-18, D-1
ASIC Faults ...................................................................... 6-3
AUTO
Key .............................................................................3-3
Mode...........................................................................3-3
REF Indicator ..................................................... 3-4, 3-5
SEQ Indicator .................................................... 3-4, 3-5
Auto Restart.....................................................................5-31
Count Reset ..............................................................5-31
Faults Covered..........................................................5-31
Max. Restart Time After Fault .................................5-31
Number of Attempts .................................................5-31
Auto-Tuning
Fault Displays and Processing..................................6-12
How to ......................................................................5-39
Line-to-Line Resistance .................................5-39, A-11
Menu..................................................................3-7, 3-14
Motor Rated Current .............................................A-25
Motor Rated Power .................................................A-25
B
Base Block
After Fault................................................................ 5-31
Circuit Fault ............................................................... 6-2
Minimum Time ......................................................... 5-6
Basic Programming...............................................5-1 to 5-40
Baud Rate .........................................................6-8, D-2, D-4
Bias Adjustments ...............................5-26, 5-27, A-16, A-18
Braking
DC Injection – See DC Injection Braking
High-Slip................................................................. A-23
Branch Short Circuit Protection................................ E-2, E-3
C
Cable Length ...................................................................2-11
Capacitors – See DC Bus Capacitors
Capacity, Rated Output ............................................C-2, C-3
Capacity Related Parameters .......................................... B-1
Carrier Frequency
Error ......................................................................... 6-11
Lower Limit ............................................................. A-8
Parameters................................................................. A-8
Proportional Gain ......................................................A-8
Selection ....................................................................A-8
Upper limit ............................................................... A-8
Vs. Cable Length ..................................................... 2-11
Characteristic Frequency – See Oscillation
Charge Indicator (LED) .......................... i, 1-6, 2-2, 4-5, C-4
Circuit Breakers ................................................2-9, E-2, E-3
Clearances – See Installation, Physical
Coast to Stop ..................................................................... 5-5
Coast w/Timer................................................................... 5-6
Com OPT Setup Parameters............................................A-11
Communications – Also see Modbus Communications and
Serial Communications
Errors (CPF)............................................. 6-2 to 6-4, 6-8
Parameters............................................................... A-18
Component Names.....................................................1-5, 1-6
Connections
Preventive Maintenance............................................. 7-3
Connectors
Inspection................................................................... 7-2
Sizing ............................................................... 2-3 to 2-7
Contactors
Magnetic ...................................................................E-4
Soft Charge – See Soft Charge Contactor
Control
Characteristics............................................................C-4
Index - 1
Circuit
Connection Diagram......................................... 2-16
Terminal Configuration ................................... 2-12
PCB
Method ............................................................... C-4
Inspecting ........................................................... 7-2
Spare Parts ...................................................F-2, F-3
Power Fuse .............................................................. 6-22
Terminal Functions .................................................. 2-13
Wiring .............................................................. 2-12
Precautions ....................................................... 2-17
Cooling
Fan – See Fan
Fins
Inspecting ........................................................... 7-2
Preventive Maintenance ..................................... 7-3
COPY Function......................................................5-37, 5-38
Faults .......................................................................6-13
Read Allowed Selection .......................5-37, 6-13, A-25
Selection ........................................................ 5-37, A-25
Covers
Protective ................................................1-5 to 1-7, 1-11
Removing and Attaching ............................... 1-13, 1-14
CPU Faults ........................................................................6-3
Critical Frequency Rejection – See Jump Frequency
Current
DC Injection Braking ................................................5-6
Maximum Output ..................................................... C-4
Monitor ........................................................ 2-13, A-11
Motor Rated (FLA)........................4-7, 5-26, 6-12, A-11
Rated Output .................................................... C-2, C-3
D
DATA/ENTER Key ........................................................ 3-3
Data Length – See Modbus Communications
Date Stamp Information..................................................6-24
DC Braking – See DC Injection Braking
DC Bus Capacitors
Inspecting................................................................... 7-2
Preventive Maintenance ............................................7-3
DC Bus Fuse
Checking .................................................................. 6-21
Fault ...........................................................................6-6
Spare Parts ......................................................... F-2, F-3
DC Bus Voltage
Checking ..................................................................6-20
Overvoltage ................................................6-6, 6-9, C-4
Safety ............................................................................. i
Undervoltage ..................... 5-26 to 5-30, 6-7, 6-10, C-4
DC Injection Braking
Current....................................................................... 5-6
Parameters ................................................................ A-4
Start Frequency.......................................................... 5-5
Time at Start ............................................................. A-4
Time at Stop............................................................... 5-6
DC Reactor (See also Specifications)........................2-8, E-4
DCInj to Stop.................................................................... 5-6
DDLY Waiting to RUN – See Drive Delay
Deadband, Prohibited Frequency – See Jump Frequency and
Frequency Limits
Deceleration
Coast to Stop ............................................................. 5-5
Coast w/ Timer .......................................................... 5-6
DCInj to Stop............................................................. 5-6
Indicators ................................................................... 3-6
Ramp to Stop ............................................................. 5-5
Stall Prevention during ............................................A-20
Time ................................................................ 5-19, A-7
Troubleshooting..................................................6-6, 6-9
DECREASE Key .............................................................. 3-3
Troubleshooting....................................................... 6-14
Delay Timer Parameters .................................................. A-5
Diagnostics — See Troubleshooting
Digital Inputs
Connection Diagram................................................ 2-16
Control Circuit Terminals........................................ 2-13
Parameters ...............................................................A-12
Sinking/Sourcing Terminals ..................2-13, 2-15, 2-16
Troubleshooting.............................................. 6-14, 6-15
Digital "Motor Operated Pot” – See MOP
Digital Operator ............................................................... 3-1
Data Display .............................................................. 3-2
Display Selection (Display Scaling) .......................A-23
Drive Operation when Disconnected ......................A-24
Faults/Errors ..............................................6-2, 6-6, 6-14
Keys........................................................................... 3-3
LCD Brightness Adjustment ...................................A-24
Lights – See Indicators
Mode Indicators......................................................... 3-4
Mode Selection ......................................................... 3-3
Monitor Selection (At Power-up) – See Monitor
Preventive Maintenance ............................................ 7-3
Removing and Attaching.............................1-14 to 1-16
Write-protected – See COPY Function, Read Allowed
Digital Outputs
Connection Diagram................................................ 2-16
Control Circuit Terminals........................................ 2-13
Parameters ...............................................................A-15
“Restart Enable” ...................................................... 5-31
Index - 2
Dimensions ..........................................................1-7 to 1-10
Diodes, Input – See Input Diodes
Diode Module
Resistance Test .............................................. 6-20, 6-21
Spare Parts......................................................... F-2, F-3
DIP Switch S1 ................................................................ 2-14
Displaying Faults – See Fault History, Fault Trace
“Down Arrow” Key – See DECREASE Key
DRIVE – See Operation Menu
Drive Delay Time ..................................................... 5-7, A-4
Drive Mode, Troubleshooting ........................................ 6-15
DriveWizard Software................................................iv, 5-39
E
EEPROM
Enter Command.......................................................D-11
Fault/Error .............................................. 6-2, 6-11, 6-13
Maximum Number of Writes ................................. D-11
Elapsed Timer Function ................................................. 5-37
Monitor......................................................... 5-37, A-27
Parameters .................................................... A-24, A-25
EMC
Compatibility........................................................... 2-19
Filters....................................................................... 2-20
Enclosed wall-mounted type .......................... 1-2 to1-4, C-4
Enclosure Style ...............................................1-2 to1-4, C-4
Energy Saving
Parameters ................................................................A-7
Selection ......................................................... 5-19, A-7
Environment – See Installation Site
ESC Key .......................................................................... 3-3
External Faults (EF) ..................................................6-4, 6-8
External Fault Inputs ..............................................2-13, 6-4
F
Factory Repair ...........................................Inside Back Cover
Fan
Checking ................................................................. 6-23
Cumulative Operation Time Setting .......................A-25
Fuse, Checking ........................................................6-23
Heatsink Cooling Fan
Operation Delay Time............................ 5-34, A-22
Operation Selection..................................... A-22
Replacement Method ..................................7-5, 7-6
Spare Parts.................................................. F-2, F-3
Inspecting ....................................................7-2, 7-3
Internal, Spare Parts ................................... F-2, F-3
Troubleshooting................................................ 6-19
Fast-Stop Time ................................................................. A-7
Faults
Clearing .................................................................. A-25
Covered by Auto Restart ......................................... 5-30
Digital Output Signal............................................... 2-13
Effect on Drive Operation ....................................... 5-31
History .................................................3-9 to 3-11, A-29
Listing of.................................................................... 6-2
Reset .......................................................................... 3-3
Trace ....................................................3-9 to 3-11, A-28
Feedback (PI Function)................................................... 5-15
Differential................................................................. 5-9
Loss Detection Level ....................................... 5-15, A-6
Loss Detection Time........................................ 5-15, A-6
Reference Missing Detection Selection.......... 5-15, A-5
Square Root Function Activation ....................5-19, A-6
Field Service ............................................. Inside Back Cover
FLA, Motor .......................................... 4-6, 5-25, 6-12, A-11
Flash ID ..........................................................................A-27
Forward Run/Stop Command ................................ 2-13, 2-16
Programming ............................................. 5-3, 5-4, A-4
Frequency Detection Multi-function Output – See Digital
Outputs
Frequency, Output
Accuracy .................................................................... C-4
Allowable Fluctuation – See Specifications
Carrier – See Carrier Frequency
Command Selection – See Speed Command
Jump ................................................................ 6-19, A-9
Lower Limit .............................................5-19,5-20, A-9
Max. Output .........................................5-19, 5-20, A-10
(Also see Specifications)
Meter (Analog Monitor) – See Analog Outputs
Mid Output ............................................................. A-10
Minimum Output .......................................... 6-15, A-10
Monitor (U1-02) ......................................................A-26
Prohibited – See Jump Frequency and Frequency Limits
Rated – See Specifications
Setting Resolution......................................................C-4
Setting Signal.............................................................C-4
Troubleshooting ....................................................... 6-19
Upper Limit ............................................5-19, 6-19, A-9
Frequency Reference
Analog Input .................................2-13, 2-16, A-4, A-15
At Loss of Frequency Reference ..............................5-30
Bias ....................................................5-26 to 5-29, A-16
Drift ......................................................................... 5-16
Gain ...................................................5-26 to 5-29, A-16
Jog ..........................................................2-13, 2-16, A-8
Loss Detection ......................................................... 5-30
Index - 3
Setting Method Selection (MOP).................. 5-36, A-24
Source (b1-01)............... 2-12, 2-13, 2-16, 3-3, 3-5, A-4
Frequency References 1 thru 4 – See Preset Speeds
Full Load Amps (FLA) ........................ 4-7, 5-26, 6-12, A-11
Fuse Blown Protection .....................................................C-4
FWD Indicator.................................................................. 3-4
G
Gain Adjustments ....................................... 5-26, 5-27, A-16
Gate Drive PCBs
Inspecting ..................................................................7-2
Spare Parts......................................................... F-2, F-3
Ground Fault (GF)...................................................5-31, 6-5
Ground Fault Interrupter (GFI) ....................................... E-4
Troubleshooting ...................................................... 6-18
Grounding ...................................................................... 2-11
Protection ..................................................................C-4
Shield Wire.............................................................. 2-13
H
HAND
Frequency Reference Selection.........................3-4, A-4
Indicators........................................................... 3-4, 3-5
Key ............................................................................ 3-4
Function Selection .......................................... A-25
Mode ......................................................................... 3-4
Troubleshooting ...................................................... 6-15
Hardware Protection Parameters ....................................A-22
Harmonics, Power Supply ...................................... C-2, C-3
Heatsink – See Cooling Fins
Heatsink Fan – See Fan, Heatsink Cooling
High-Slip Braking ..........................................................A-23
H/O/A (Hand/Off/Auto) – See Digital Operator
Horsepower, converting to kW........................................5-39
Humidity..........................................................................1-11
Ambient Operating....................................................C-4
Hunting Prevention
Parameters ...............................................................A-23
Troubleshooting ...................................................... 6-18
I
IEC IP00 – See Open Chassis
IEC IP20 – See Enclosed wall-mounted type
IGBT (Transistor Module)
Inspecting ...................................................................7-2
Resistance Test ............................................6-20 to 6-22
Spare Parts..........................................................F-2, F-3
INCREASE Key ...............................................................3-3
Troubleshooting ....................................................... 6-14
Indicators, Mode .....................................................3-4 to 3-6
Initial Start-up ......................................................4-1 to 4-10
Initialization
Mode Selection ................................................. 5-2, 5-36
Parameters ................................................................ A-2
Specification Selection ................................... 5-2, A-25
Input
Diodes, Inspecting ..................................................... 7-2
Fuses .......................................................... 2-9, E-2, E-3
Multi-function Terminals – See Analog Inputs and
Digital Inputs
Phase Loss Detection Level............................. 6-6, A-22
Terminal Status (U1-10) ........................................ A-26
Voltage ................................................... A-10, C-2, C-3
Setting..............................................4-5, 5-15, A-10
Inputs
Analog – See Analog Inputs
Digital – See Digital Inputs
Frequency Reference – See Frequency Reference
Inspection
Periodic ...................................................................... 7-2
Receiving ................................................................... 1-3
Installation
Electrical ................................................................... 2-1
Physical ..................................................................... 1-1
Adverse Conditions ............................................ 7-3
Orientation & Clearances ................................. 1-12
Site............................................................ 1-11, C-4
Integral Limit (PI) ........................................................... 5-13
Interference ........................................................ 2-19 to 2-21
IPM (Intelligent Power Module)
Inspecting................................................................... 7-2
Spare Parts ......................................................... F-2, F-3
J
Jog Frequency Reference ..............................2-13, 2-16, A-8
Jump Frequency ...............................................................A-9
Troubleshooting ....................................................... 6-19
K
Keypad — See Digital Operator kVA
Auto-Tuning ............................................................ 5-39
Error................................................................ 6-11, 6-13
Parameters Affected by .............................................B-2
Selection ................................................................. A-23
Index - 4
kW, Converting from HP................................................5-39 kWH User Monitor Initialization ..................................A-25
L
Lamps, Indicator – See Indicators, Mode
Language Selection ..................................................5-2, A-2
LCD Display– See Digital Operator, Data Display
Lights – See Indicators, Mode
Line-borne Interference – See Interference
Line-to-Line Resistance, Motor ........................... 5-39, A-11
LonWorks ................................................................. 5-3, 5-5
M
Main Circuit
Terminals ...........................................................2-2, 2-8
Test Procedure ......................................................... 6-20
Wire Sizes and Connectors ..............................2-3 to 2-7
Wiring Diagrams .................................... 2-9, 2-10, 2-11
Main Menu
Functions ................................................................... 3-7
Structure .................................................................... 3-8
Maintenance ...........................................................7-1 to 7-8
Mass, Drive .............................................................1-4, 1-10
Master Frequency Reference Terminal Selection ......... A-16
Master/Auxiliary Switch ............................................... 2-13
Master/Slave – See Modbus Communications Configuration
Mechanical Oscillation .................................................. 6-18
Mechanical Resonance ...................................................6-18
MENU Key .....................................................................3-3
Menu Trees, Digital Operator ..........................................3-8
Metasys.........................................................iii, iv, A-18, D-1
Meters – See Analog Outputs
Modbus Communications .........................A-18, D-1 to D-13
(Also see Serial Communications)
Baud Rate...........................................6-8, D-2, D-4
Terminals...........................................................2-13
Mode Selection ................................................................ 3-3
Model Number ................................................................. 1-4
Modified Constants Menu .......................................3-7, 3-14
Molded Case Circuit Breaker (MCCB) ........................... E-4
Momentary Power Loss Ride-thru ............... 5-29, A-19, C-4
Monitor
Configuration ........................................................... 5-21
Parameter List .......................................3-9, A-26, A-27
Power-On Monitor ........................................ 5-35, A-22
User Monitor .......................................5-35, A-23, A-24
MONITOR Key................................................................ 3-3
MOP (Motor Operated Pot) Function ............................ 5-36
Reference Memory.................................................... A-9
Index - 5
Motor
Auto-Tuning
Fault Displays & Processing ............................6-12
How to .............................................................. 5-39
Line-to-Line Resistance ........................ 5-39, A-11
Menu..........................................................3-7, 3-14
Motor Rated Current ........................................A-25
Motor Rated Power ......................................... A-25
Direction .......................................................... 4-7, 6-16
No-Load Current (NLA) .........................................A-11
Output, Maximum Applicable – See Specifications
Parameters ...............................................................A-11
Pre-Heat Current...................................................... A-4
Protection......................................................... 5-16, C-4
Overheat .......................................................... A-19
Overload .................................................. A-19, C-4
Rated Current (FLA) ................... 4-6, 5-26, 6-12, A-11
Rated Voltage ............................................................ 4-3
Speed (U1-02) .........................................................A-26
Stopping Method Selection ................ 4-7, 5-5, 5-6, A-4
Temperature Input Filter Time................................ A-19
Troubleshooting ........................................... 6-15 to 6-19
Wiring ......................................................... .......... 2-13
Mounting Drive – See Installation, Physical
Mounting, Inspecting ........................................................ 7-2
Multi-function Analog Inputs – See Analog Inputs
Multi-function Analog Outputs – See Analog Outputs
Multi-function Digital Inputs – See Digital Inputs
Multi-function Digital Outputs – See Digital Outputs
Multi-step Speed Reference (Preset Speed)............ 2-13, A-8
N
Nameplate Information ..............................................1-3, 1-4
NEMA Type 1 ....................................................1-2, 1-4, 1-5
Noise
Electrical .....................................................2-19 to 2-21
Fan .................................................................... 7-2, 7-3
Filter ........................................................................ E-4
Mechanical...............................................................6-18
No-Load Current (NLA) ................................................A-11
O
OFF Key ...........................................................................3-4
Function during Auto Run ...................................... A-24
Off-delay Timer .............................................................. A-5
On-delay Timer ................................................................A-5
Open Chassis......................................................1-2, 1-4, 1-5
Operation
Menu ..................................................................3-7, 3-9
Status (U1-12) .........................................................A-26
Operator Programming Errors (OPE)..............................6-11
Option
Card Faults .........................................................6-3, 6-4
Communication Error Selection.............................. 5-26
Options (Peripheral Devices) ...........................................E-4
Orientation, Drive........................................................... 1-12
Oscillation
Mechanical .............................................................. 6-18 with PI control......................................................... 6-18 with V/f control ....................................................... 6-18
Output
Current Monitor (U1-03).........................................A-26
Frequency – See Frequency, Output
Ground Fault Detection Selection ...........................A-22
Monitors ....................................................... A-26, A-27
Phase Loss ................................................................. 6-9
Power Monitor (U1-08)...........................................A-26
Power Ratings – See Specifications, Standard Drive
Terminal Status Monitor (U1-11)............................A-26
Transistors (IGBT)
Inspecting ...........................................................7-2
Spare Parts .................................................F-2, F-3
Testing..................................................6-20 to 6-22
Voltage Monitor (U1-06).........................................A-26
Outputs, Analog – See Analog Outputs
Outputs, Digital – See Digital Outputs
Over Current (OC)........................................... 5-6, 5-30, 6-5
Overheat (OH)
Alarms/Faults .....................................................6-9, 6-5
Cooling Fin (Heatsink)...............................6-5, 6-9, C-4
Drive....................................................................... A-22
Motor........................................................6-5, 6-9, A-19
Parameters .................................................... A-19, A-22
Pre-Alarm........................................................6-9, A-22
Overload
Alarms/Faults ...................................................5-30, 6-6
Capacity..................................................................... C-4
Drive.......................................................................... 6-6
Motor............................................................... 6-6, A-18
Overtorque – See Torque Detection
Protection ....................................................... A-19, C-4
Overtorque – See Torque Detection
Overvoltage Protection......................................6-6, 6-9, C-4
DC Bus – See DC Bus Voltage
P
Parameters
Accel/Decel (C1-01 – C1-11) ...................................A-7
Analog Inputs (H3-02 – H3-13) ..............................A-16
Analog Outputs (H4-01 – H4-08)................. A-17, A-18
Auto-Tuning (T1-02 – T1-04) ................................ A-25
Capacity Related........................................................B-1
Carrier Freq (C6-02 – C6-05) ................................... A-8
Com OPT Setup (F6-01 – F6-05) ........................... A-11
COPY Function (o3-01 – o3-02) ............................ A-25
DC Braking (b2-01 – b2-09) ....................................A-4
Delay timers (b4-01 – b4-02) ...................................A-5
Digital Inputs (H1-01 – H1-05) ................. A-12 to A-14
Digital Outputs (H2-01 – H2-02) ........................... A-14
Energy Saving (b8-01 – b8-06) ................................ A-7
Example of Changing .....................................3-15, 3-16
Factory Reset (Initialize) ......................................... A-2
Fault Restart (L5-01 – L5-03) .................................A-21
Hdwe Protection (L8-01 – L8-19) .......................... A-22
High Slip (n3-01 – n3-04) ...................................... A-23
Hunting Prevention (n1-01 – n1-02) ...................... A-23
Initialization (A1-00 – A1-05).................................. A-2
Jump Frequencies (d3-01 – d3-04) ........................... A-9
Key Selections (o2-01 – o2-15).................... A-24, A-25
Listing of ..................................................... A-1 to A-29
Modified – See Modified Constants
Monitor Select (o1-01 – o1-08) .................... A-23, A-24
MOP/Trim Control (d4-01 – d4-02) ..........................A-9
Motor Overload (L1-01 – L1-05) ............................A-19
Motor Setup (E2-01 – E2-05) ................................. A-11
PI Control (b5-01 – b5-30) ............................... A-5, A-6
Preset Reference (d1-01 – d1-17) ............................. A-8
Programming ................................................ 5-1 to 5-40
PwrLoss Ridethru (L2-01 – L2-05) ........................ A-19
Ref Detection (L4-01 – L4-06)................................A-21
Reference Limits (d2-01 – d2-03) ............................ A-9
S-Curve Acc/Dec (C2-01 – C2-02) ...........................A-7
Sequence (b1-01 – b1-12)..........................................A-4
Serial Com Setup (H4-06 – H4-08) ........................ A-18
Setting and Reading................................................. 3-13
Speed Search (b3-01 – b3-05) ...................................A-5
Stall Prevention (L3-01 – L3-06) ............................A-20
Torque Comp (C4-01 – C4-02)................................. A-8
Torque Detection (L6-01 – L6-03) ..........................A-21
Troubleshooting .......................................................6-14
User (A2-01 – A2-32)....................................... A-2, A-3
V/f Pattern (E1-01 – E1-13) ....................................A-10
Parity – See Modbus Communications
Index - 6
Parts
Ordering Replacement ...................... Inside Back Cover
Replacement Guidelines ............................................7-4
Spare ......................................................... F-1to F-3
Password
Setting ................................................................ A-2
PCB
Troubleshooting ................................................6-14
Control
Inspecting.....................................................7-2
Spare Parts ........................................... F-2, F-3
Gate Drive
Inspecting.....................................................7-2
Spare Parts ........................................... F-2, F-3
Power
Inspecting.....................................................7-2
Spare Parts ........................................... F-2, F-3
Terminal
Inspecting.....................................................7-2
Removing and Mounting .............................7-7
Spare Parts ...........................................F-2, F-3
Peripheral Devices
AC and DC reactor ........................................... E-4
Ground Fault Interrupter .................................... E-4
Magnetic Contactor........................................... E-4
Molded-case circuit breaker (MCCB) ............... E-2
Noise filter ........................................................ E-4
Phase-advancing capacitor................................. E-4
Troubleshooting ................................................6-17
Phase Loss Detection
Input .........................................................6-6, A-22
Output ................................................................6-9
Phase-to-Phase Short .................................. 6-5, 6-9
Physical Installation –See Installation, Physical
PI Feedback Loss .......................................................6-4
PI Function
Accel/Decel Time .....................................5-16, A-6
Block Diagram .................................................... 5-8
Feedback ..........................................................5-10
Differential...................................................5-9
Loss Detection Level ........................ 5-15, A-6
Loss Detection Time..........................5-15, A-6
Reference Missing Detection ............5-15, A-5
Square Root Function Activation ......5-14, A-6
Integral Limit Setting.................................. 5-9, A-5
Integral Time Setting .................................. 5-9, A-5
Maximum Boost Time ..............................5-17, A-6
Offset Adjustment .................................... 5-15, A-5
Output ............................................................ 5-10
Gain Setting ....................................... 5-15, A-5
Level Selection .................................. 5-15, A-5
Limit .................................................. 5-14, A-5
Square Root Monitor ......................... 5-18, A-6
Parameters ................................................ A-5, A-6
Primary Delay Time Constant .................. 5-15, A-5
Setpoint .................................................... 5-16, A-6
Boost Setting .....................................5-17, A-6
Display Scaling.................................5-16, A-6
Selection ............................................ 5-16, A-6
Value ..................................................5-16, A-6
Sleep
Delay Time ....................................... 5-15, A-6
Function.................................................... 5-15
Function Start Level .......................... 5-15, A-6
Input Source ...................................... 5-15, A-6
Snooze
Deactivation Level ........................... 5-17, A-6
Delay Time ........................................ 5-17, A-6
Feedback Level..................................5-18, A-6
Function..................................................... 5-17
Level .................................................. 5-13, A-6
Square Root Gain...................................... 5-14, A-6
PI Mode ............................................................. 5-9, A-5
PI Monitors
Feedback (U1-24)..................................5-13, A-27
Output Square Root (U1-37) .................. 5-18, A-27
Setpoint (U1-38) ..................................... 5-13, A-27
PLC (Programmable Logic Controller)
Serial Com. Using Modbus Protocol .................D-2
Troubleshooting ................................................ 6-17
Plenum Rated ........................................................... 1-11
Potentiometer (Connection) .....................................2-16
Power
Detection Filter Time......................................... A-7
Input, +15Vdc ..........................................2-13, 2-16
Loss Ride-thru .................. 5-26 to 5-30, A-19, C-4
Module Spare Parts..................................... F-2, F-3
PCB
Inspecting .................................................... 7-2
Spare Parts ........................................... F-2, F-3
Supply Specifications .................................C-2, C-3
Power Factor Correction Capacitors..........................6-6
Pre-Operation Considerations .............i to iv; Ch. 1, 2, 4
Preset Speeds ........................................................... A-8
Preventive Maintenance............................................. 7-3
Index - 7
Programming
Basic.............................................................. 5-1 to 5-40
Error (OPE) ............................................................. 6-11
Menu ................................................................3-7, 3-13
Proportional Gain (PI)............................................ 5-13
Protective
Functions .................................................................. C-4
Structure ................................................................... C-4
PWM Frequency — see Carrier Frequency
Q
QUICK – See Quick Setting Menu
Quick Setting Menu ....................................................... 3-12
R
RAM...............................................................................D-11
Ramp to Stop .................................................................... 5-5
Rated Current, Motor .......................... 4-6, 5-25, 6-12, A-11
Rdy – See Ready Display
Reactors, Preventive Maintenance ................................... 7-3
READ ..............................................................................5-37
Ready Display ..................................................................3-2
Receiving ......................................................................... 1-3
REF Indicator ...........................................................3-4, 3-5
Reference Limits (Also see Frequency) ...... 5-19, 6-19, A-9
Reference Selection
AUTO........................................................................ 3-3
HAND .......................................................................3-4
Reference Source.............................................. 5-2, 5-3, A-4
Relays, Preventive Maintenance ...................................... 7-3
Replacement Parts – Also see Spare Parts Ordering..............
.................................................................. Inside Back Cover
RESET Key – See SHIFT/RESET Key
Resistance, Motor Line-to-Line .......................... 5-40, A-11
Resonance....................................................................... 5-15
REV Indicator .................................................................3-4
Reverse Operation ....................................................5-6, A-4
Prohibiting............................................... 5-6, 6-16, A-4
Reverse Run/Stop command .........................2-13, 2-16, A-4
Ride-thru, Momentary Power Loss . 5-26 to 5-31, A-19, C-4
"Right Arrow" Key – See SHIFT/RESET Key
RS-485/422 .......................................................................5-4
Communication Wiring.............................................D-3
Control Circuit Terminals ....................................... 2-13
Parameters ...............................................................A-18
Terminating Resistance ...................................2-14, D-3
RTS Control Selection....................................................A-18
Run Command
During Program ........................................................ A-4
External, Troubleshooting ....................................... 6-15
Selection ...................................... 3-3, 3-5, 4-6, 5-3, A-4
Source ........................................................................ 5-3
RUN Indicator................................................................... 3-6
Running
Signal ....................................................................... 2-13
Stall Prevention during ............................................A-20
S
Scaling Display
Digital Operator ...................................................... A-23
PI Setpoint ....................................................... 5-16, A-6
S-Curve Characteristic at Accel End...............................................................A-7 at Accel Start............................................................ A-7
Search Operation Voltage Limit....................................... A-7
SEQ ............................................................................ 3-4, 3-5
Sequence Parameters ....................................................... A-4
Serial Communications - See also Modbus Communications
Address ..................................................................... D-4
Baud Rate ..........................................................6-8, D-4
Drive Node Address ..................................................D-4
Parameters ...................................................... A-18, D-4
Run Command ........................................................... 5-4
Self-Diagnosis Function ..........................................D-13
Serial Number ................................................................... 1-3
Setpoint (PI Function)..................................................... 5-16
Boost Setting.................................................... 5-17, A-6
Display Scaling................................................ 5-16, A-6
Selection .......................................................... 5-16, A-6
Value ................................................................ 5-16, A-6
SHIFT/RESET Key ................................................. 3-3, 5-19
Shield Wire Grounding .......................................... 2-13, 2-17
Shipping Damage.............................................................. 1-3
Short Circuit Protection, Branch............................... E-2, E-3
Sinking/Sourcing Mode ................................2-13, 2-15, 2-16
Skip Frequency –– See Jump Frequency and Frequency
Limits
Slave – See Modbus Communication Configuration
Sleep Function – See PI Function, Sleep
Snooze Function – See PI Function, Snooze
Soft Charge Contactor
Alarm .......................................................................6-10
Checking .................................................................. 6-21
Fault ...........................................................................6-7
Preventive Maintenance ............................................ 7-3
Index - 8
Soft Charge Resistor
Checking ..................................................................6-21
Preventive Maintenance ............................................ 7-3
Soft CLA Selection ........................................................A-22
Soft Start — see S-Curve
Software Number ...........................................................A-27
Spare Parts ............................................................. F-1 to F-3
SPEC .........................................................................1-3, 1-4
Specifications
Design ....................................................................... 1-4
General ......................................................................C-4
Selection ..................................................................A-25
Standard Drive
208-240Vac ....................................................... C-2
480Vac............................................................... C-3
Nameplate .......................................................... 1-3
Speed
Agreement .............................................................. A-21
Control Accuracy ......................................................C-4
Range........................................................................ C-4
Speed Command – See also Frequency Reference
0-10Vdc.....................................................................4-9
4-20mA ..................................................................... 4-9
Limits ...................................................................... 5-19
Loss Detection......................................................... 5-30
Selection ..................................................... 4-6, 5-2, 5-3
Setting Selection...................................................... 5-36
Signal Polarity ...........................................................4-9
Troubleshooting .............................................6-15, 6-16
Speed Reference, Multiple (Multi-step Speed Operation) –
See Preset Speeds
Speed Search ................................................................. 5-30
Auto-Tuning ........................................................... 5-39
Parameters ................................................................ A-5
Stall Prevention
Parameters .............................................................. A-20
Specifications ........................................................... C-4
Troubleshooting .......................................................6-16
Start-up ..................................................................4-1 to 4-9
Assistance.......................................... Inside Back Cover
Benchmark data.........................................................4-8
Preparation for........................................................... 4-2
Procedure................................................................... 4-5
Station Address (Modbus Control) ..................................D-4
Stop bits – See Modbus Communications
STOP Indicator ................................................................ 3-6
Stop Method Selection (OH) .........................................A-22
Stopping Method ...................................... 4-7, 5-5, 5-6, A-4
Coast to Stop ............................................................. 5-5
Coast w/Timer ........................................................... 5-6
DcInj to Stop.............................................................. 5-6 for External Fault from OPT Card .......................... A-11
Ramp to Stop ............................................................. 5-5
Stopping Method at Error (Modbus Control) – See Modbus
Communications
Storage Temperature ........................................................ C-4
Surge Suppressor ..............................................................E-4
Switching Frequency, Accel/Decel ...............5-18, 5-19, A-7
T
Technical Support ..................................... Inside Back Cover
Technical Training ....................................Inside Back Cover
Temperature
Ambient Operating .......................................... 1-11, C-4
Ambient, Setting ..................................................... A-22
Effect on Frequency Accuracy ................................. C-4
Storage ..................................................................... C-4
Troubleshooting .......................................................6-17
Terminal PCB
Inspecting................................................................... 7-2
Removing and Mounting ........................................... 7-7
Spare Parts ......................................................... F-2, F-3
Terminals
Terminal A1 .....................................2-13, 2-16, 5-26, A-16
Terminal A2 ...............................2-13, 2-16, 5-28, 5-29, A-16
Terminal AM .................................... 2-13, 2-16, A-17, A-18
Terminal FM ............................................... 2-13, 2-16, A-17
Terminal M1-M2 ........................................ 2-13, 2-16, A-15
Terminal M3-M4 Function Selection ......... 2-13, 2-16, A-15
Terminal R+, R-, S+, S- .................................2-13, 2-16, D-3
Terminal S1, S2...............................................2-13, 2-16, 5-4
Terminals S3 – S7 ..........................2-13, 2-16, A-12 to A-14
Arrangement .............................................................. 1-6
Configuration............................................................. 2-2
Connections ............................................................. 2-16
Control Circuit ................................................ 2-12, 2-16
Main Circuit ..................................................2-3 to 2-11
Inspecting ........................................................... 7-2
Wiring ....................................................... 2-3 to 2-7
Preventive Maintenance ............................................ 7-3
Screw Sizes .....................................................2-3 to 2-7
Terminating Resistance...........................................2-14, D-3
Three-Wire Operation ....................................................... 5-4
Troubleshooting ....................................................... 6-15
Timers, Delay...................................................................A-5
Timers, Elapsed.....................................................5-36, A-25
Torque Compensation
Parameters ................................................................A-8
Troubleshooting .......................................................6-16
Index - 9
Torque Detection
Faults .........................................................................6-6
Level ..............................................................5-32, 5-33
Nuisance .................................................................. 5-20
Parameters .............................................................. A-21
Selection ........................................................5-32, 5-33
Time ..............................................................5-32, 5-33
Torque Output................................................................. 6-16
Transformers, Preventive Maintenance............................ 7-3
Transistor Module
Inspecting .................................................................. 7-2
Resistance Test ............................................6-20 to 6-22
Spare Parts..........................................................F-2, F-3
Trim Control Level ......................................................... A-9
Troubleshooting ...................................................6-1 to 6-24
Two-Wire Operation......................................................... 5-3
Troubleshooting ......................................................6-15
Twelve-pulse rectification ................................2-9, C-2, C-3
U
U1 Monitor List............................................3-9, A-26, A-27
U2 Fault Trace List............................................... 3-10, A-28
U3 Fault History List............................................3-11, A-29
UL File Number ........................................................1-3, 1-4
Undertorque Detection (UL) ...........................................5-32
Alarm/Fault ......................................................6-7, 6-10
Parameters .............................................................. A-21
Undervoltage (UV)
Alarm/Fault ...................................................... 6-7, 6-10
Detection Level ......................................................A-19
Protection ..................................................................C-4
"Up Arrow" Key – See INCREASE Key
Up/Down Function – See MOP
User Initialization ........................................................... 5-36
User Parameter Default Value....................... 5-36, A-24
User Parameters .............................................. A-2, A-3
User Monitor ..............................................5-35, 5-36, A-23
Voltage
Allowable fluctuation ...................... 6-7, 6-10, C-2, C-3
Base ........................................................................ A-10
Drop Calculation........................................................ 2-7
Input – See Input Voltage
Maximum Output ..............................................C-2, C-3
Rating, Drive ............................................ 1-4, C-2, C-3
Related Parameters ................................................. A-10
W
Warranty.......................................................................... 6-24
Watchdog Timer................................................................ 6-3
Weight – See Mass, Drive
Wire
Clamping Torque .............................................2-3 to 2-7
Gauge – See Wire Size
Length – See Cable Length
Size ................................................................. 2-3 to 2-7
Wiring – See also Electrical Installation
Control Circuit ....................................................... 2-12
Diagrams ................................................................ 2-16
Distances – See Cable Length
Field Diagram .......................................................... 2-18
Ground ............................................................ 2-11, 2-21
Main Circuit
Input/Output ............................................ 2-9, 2-10
Terminals .................................................. 2-3 to 2-7
Shielded Twisted-Pair Wires ................................... 2-17
Sinking/Sourcing ..................................................... 2-15
Three-Wire Control..................................................2-16
Two-Wire Control ................................................... 2-16
Z
Zero speed signal ........................................................... A-14
V
Ventilation – See Installation Site
VERIFY Function .......................................................... 5-38
Error ...............................................................5-39, 6-13
VERIFY Menu – See Modified Constants Menu
V/f Pattern
Faults/Errors ..................................................... 6-5, 6-11
Parameters ...............................................................A-10
Vibration, Maximum ........................................................ C-4
Index - 10
P7B Drive/Bypass
YASKAWA ELECTRIC AMERICA, INC.
Drives Division
16555 W. Ryerson Rd., New Berlin, WI 53151, U.S.A.
Phone: (800) YASKAWA (800-927-5292) Fax: (262) 782-3418
Internet: http://www.drives.com
YASKAWA ELECTRIC AMERICA, INC.
Chicago-Corporate Headquarters
2121 Norman Drive South, Waukegan, IL 60085, U.S.A.
Phone: (800) YASKAWA (800-927-5292) Fax: (847) 887-7310
Internet: http://www.yaskawa.com
MOTOMAN INC.
805 Liberty Lane, West Carrollton, OH 45449, U.S.A.
Phone: (937) 847-6200 Fax: (937) 847-6277
Internet: http://www.motoman.com
YASKAWA ELECTRIC CORPORATION
New Pier Takeshiba South Tower, 1-16-1, Kaigan, Minatoku, Tokyo, 105-0022, Japan
Phone: 81-3-5402-4511 Fax: 81-3-5402-4580
Internet: http://www.yaskawa.co.jp
YASKAWA ELETRICO DO BRASIL COMERCIO LTDA.
Avenida Fagundes Filho, 620 Bairro Saude Sao Paolo-SP, Brasil CEP: 04304-000
Phone: 55-11-5071-2552 Fax: 55-11-5581-8795
Internet: http://www.yaskawa.com.br
YASKAWA ELECTRIC EUROPE GmbH
Am Kronberger Hang 2, 65824 Schwalbach, Germany
Phone: 49-6196-569-300 Fax: 49-6196-888-301
MOTOMAN ROBOTICS AB
Box 504 S38525, Torsas, Sweden
Phone: 46-486-48800 Fax: 46-486-41410
MOTOMAN ROBOTEC GmbH
Kammerfeldstrabe 1, 85391 Allershausen, Germany
Phone: 49-8166-900 Fax: 49-8166-9039
YASKAWA ELECTRIC UK LTD.
1 Hunt Hill Orchardton Woods Cumbernauld, G68 9LF, Scotland, United Kingdom
Phone: 44-12-3673-5000 Fax: 44-12-3645-8182
YASKAWA ELECTRIC KOREA CORPORATION
Paik Nam Bldg. 901 188-3, 1-Ga Euljiro, Joong-Gu, Seoul, Korea
Phone: 82-2-776-7844 Fax: 82-2-753-2639
YASKAWA ELECTRIC (SINGAPORE) PTE. LTD.
Head Office: 151 Lorong Chuan, #04-01, New Tech Park Singapore 556741, Singapore
Phone: 65-282-3003 Fax: 65-289-3003
TAIPEI OFFICE (AND YATEC ENGINEERING CORPORATION)
10F 146 Sung Chiang Road, Taipei, Taiwan
Phone: 886-2-2563-0010 Fax: 886-2-2567-4677
YASKAWA JASON (HK) COMPANY LIMITED
Rm. 2909-10, Hong Kong Plaza, 186-191 Connaught Road West, Hong Kong
Phone: 852-2803-2385 Fax: 852-2547-5773
BEIJING OFFICE
Room No. 301 Office Building of Beijing International Club,
21 Jianguomanwai Avenue, Beijing 100020, China
Phone: 86-10-6532-1850 Fax: 86-10-6532-1851
SHANGHAI OFFICE
27 Hui He Road Shanghai 200437 China
Phone: 86-21-6553-6600 Fax: 86-21-6531-4242
SHANGHAI YASKAWA-TONJI M & E CO., LTD.
27 Hui He Road Shanghai 200437 China
Phone: 86-21-6533-2828 Fax: 86-21-6553-6677
BEIJING YASKAWA BEIKE AUTOMATION ENGINEERING CO., LTD.
30 Xue Yuan Road, Haidian, Beijing 100083 China
Phone: 86-10-6232-9943 Fax: 86-10-6234-5002
SHOUGANG MOTOMAN ROBOT CO., LTD.
7, Yongchang-North Street, Beijing Economic & Technological Development Area,
Beijing 100076 China
Phone: 86-10-6788-0551 Fax: 86-10-6788-2878
YEA, TAICHUNG OFFICE IN TAIWAIN
B1, 6F, No.51, Section 2, Kung-Yi Road, Taichung City, Taiwan, R.O.C.
Phone: 886-4-2320-2227 Fax:886-4-2320-2239
YEA Document Number: TM.P7B.01 10/1/03 Software Version: 1010
Data subject to change without notice. Yaskawa Electric America, Inc.
advertisement
Related manuals
advertisement
Table of contents
- 14 Bypass Model Number and Enclosure Style
- 16 Enclosure Data
- 19 Confirmations upon Delivery
- 21 Bypass Product Options
- 23 Bypass Component Descriptions
- 29 Exterior and Mounting Dimensions
- 36 Checking and Controlling Installation Site
- 40 Termination Configuration - Power Wiring
- 47 Control Wiring
- 58 Wiring Diagram
- 60 Logic Diagram
- 66 Digital Operator and Control Panel Display
- 72 Drive Main Menus
- 80 Example of Changing a Parameter
- 84 Start Up Introduction
- 85 Bypass Start Up Preparation
- 86 Bypass Unit Start Up Procedure
- 90 Bypass Operation Description
- 96 Bypass Basic Programming Parameters
- 182 Bypass Diagnostics
- 183 Drive Diagnostics
- 196 Drive Troubleshooting
- 202 Drive Main Circuit Test Procedure
- 206 Drive Date Stamp Information
- 208 Maintenance
- 215 Removing and Replacing Drive in a Bypass Unit
- 220 Parameter List
- 244 Monitor List
- 246 Fault Trace List
- 247 Fault History List
- 250 Drive Capacity
- 256 Standard Drive and Bypass Specifications
- 260 Using Modbus Communication
- 265 Modbus Function Code Details
- 267 Modbus Data Tables
- 272 Modbus Self-Diagnosis
- 274 General Peripheral Devices
- 276 Primary Parts - 208/230/240VAC
- 277 Primary Parts - 480VAC
- 278 Bypass Replacement Parts