- Home
- Domestic appliances
- Climate control
- Temperature & humidity sensors
- YASKAWA
- P7B Drive Bypass
- Manual
advertisement
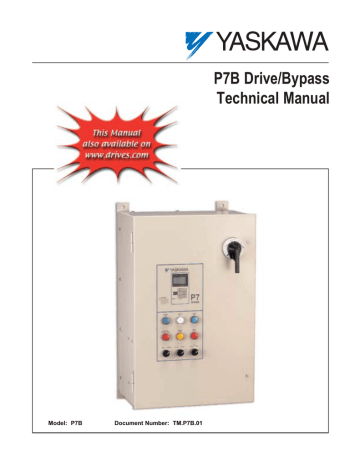
Bypass Basic Programming Parameters
The basic Drive programming for a Bypass unit is different from that of a Drive installation without the Bypass option.
Several Drive parameters have been programmed at the factory to meet the needs of the Bypass logic circuit. See Table 5.1 below, the highlighted parameters are required by the Bypass logic circuit.
PARAMETER
NUMBER b1-01 b1-07 b1-08 b2-03 d1-01 d1-02 d1-04
E1-01
F6-01
H1-01
H1-02
H1-03
H2-02
H3-02
H3-08
Table 5.1 Bypass Parameter Settings
SETTING
For
Bypass
Drive
Default
1 SEE
TABLE
5.2
1 0
UNITS
N/A
N/A
DESCRIPTION
Frequency Reference Selection – Selects the speed command input source
1
5.0
10.0
6.0
40.0
208,
240 or
480
3
0
0.0
0.0
0.0
0.0
240 or
480
1
N/A
SEC
HZ
HZ
HZ
VOLT
S
N/A
Local/Remote Run Selection – Determines acceptability of a remote run command when switching from hand (local) mode to auto (remote) mode
Run Command Selection During Programming –
Selects if run command is accepted in DRIVE Operation menu only or in all menus.
DC Injection Braking Time At Start – Sets the braking time at Drive start, to stop a coasting motor before starting
Frequency Reference 1 – Hand Mode Speed Reference, used with serial communication, see Table 5.2 and H1-03
Frequency Reference 2 – Hand Mode Speed Reference, used without serial communication, see Table
5.2 and H1-03
Frequency Reference 4 – Speed Reference, used with serial communication loss and H5-04 = “4: Run at d1-04”
Input Voltage Setting – Set to the nominal Voltage
Setting for the incoming line
70 24
14
N/A
N/A
Operation Selection After Communication Error –
Selects the serial com error response, alarm and continue operation
Terminal S3 Function Selection – Set for Drive run enable
Terminal S4 Function Selection – Set for fault reset or Frequency Reference 1
SEE
TABLE
5.2
SEE
TABLE
5.2
3B
3
A
N/A
N/A
Terminal S5 Function Selection – Set For Frequency
Reference 1 or Serial Communication
100.0
%
Terminals M3 - M4 Function Selection – Set for serial communication run command
Terminal A1 Gain Setting SEE
TABLE
5.2
SEE
TABLE
5.2
2 N/A Terminal A2 Signal Level –Signal selection, 0 to 10
VDC (Drive control board switch S1-2 off) or 4 to 20 mA (Drive control board switch S1-2 on)
KEYPAD DISPLAY
For Bypass Setting
Reference Source /
Terminals
LOC/REM RUN Sel /
Accept Extrn RUN
RUN CMD at PRG /
Enabled
Dcinj Time@Start /
(0-10)
Reference 1 / (0-60)
Reference 2 / (0-60)
Reference 4 / (0-60)
Input Voltage / (range)
Com Bus Flt Sel / Alarm
Only
Terminal S3 Sel / Drive
Enable
Terminal S4 Sel / Multi-
Step Ref 1
Terminal S5 Sel / Multi-
Step Ref 1
Term M3-M4 Sel / Com
RUN Command
Terminal A1 Gain /
(0-1000)
Term A2 Signal / 0-10
VDC
Programming 5 - 2
PARAMETER
NUMBER
H3-09
H3-13
L4-05
L5-01
L5-03 o2-02 o2-03 o2-15 o3-02
SETTING
For
Bypass
Drive
Default
2 SEE
TABLE
5.2
SEE
TABLE
5.2
0
0 1
10.0
600
0
1
0
1
0
180
1
0
1
0
Table 5.1 (Continued)Bypass Parameter Settings
UNITS
N/A
N/A
N/A
N/A
SEC
N/A
N/A
N/A
DESCRIPTION
Terminal A2 Function Selection – Selects how this input will be used by the Drive
Master Frequency Reference Terminal Selection –
Determines which terminal (A1 or A2) will be the main speed reference source.
Frequency Reference Loss Detection Selection –
Determines Drive response to loss of the frequency speed command
Number of Re-start Attempts – Sets the number of times the Drive will perform an automatic re-start
Maximum Restart Time After Fault – If not successfully started after this time, restart attempts stop and
Drive faults
OFF Key Function During Auto Run - Enables or disables the Off key.
User Initialization - Factory set parameter for user default values.
Hand Key Function Selection - Enables or disables the Hand and Auto keys.
Read Allowed Selection – Enables or disables keypad copy functions
KEYPAD DISPLAY
For Bypass Setting
Terminal A2 Sel / Aux
Reference
TA1/A2 Select / Main
Fref TA1
Ref Loss Sel / Stop
Num of Restarts / (0-10)
Max Restart Time /
(.5-600.0)
Oper STOP Key /
Disabled
Hand Key / Disabled
Read Allowable /
Enabled
Shaded Areas = Parameter settings required by the Bypass logic
The shaded Bypass Parameter Settings in Table 5.1 document Drive parameter settings, required to interface with the Bypass logic circuit, that have been established at the factory and stored in a dedicated location in the memory as “User Initialization” values (think of it as a “back-up file”).
Table 5.1 is also used to document parameters that have been factory set, for convenience, to typical values for fan and pump applications. These parameters may be changed to meet the needs of the specific application.
If additional parameters are set to the specific needs of the application project, and the system operation has been checked and verified, then the “User Initialization” values should be stored in memory again by selecting and entering “1: Set Default” in parameter o2-03.
When there is a need for re-initialization of the “user” parameters (re-setting to the “User Initialization” values) of the Bypass unit, then a “User Initialization” function should be carried out by selecting “1110: User Initialize” in parameter A1-03. This will re-establish the drive set-up required for the Bypass application and any “user” parameter values that have been stored.
The factory parameter settings required to interface with the bypass logic circuit have also been stored in the digital keypad memory. If there is a need for re-initialization (re-setting to a known factory starting point for trouble-shooting purposes) of the Bypass unit, then the “back-up file” in the digital keypad memory can be copied to the drive. In parameter o3-01 select
“2: OP->INV WRITE” to carry out the copy function.
Programming 5 - 3
Options
Table 5.2 Option Dependent Bypass Parameter Settings
Parameters Effected by Options Specified and
Settings
Resulting Hand Speed
Command Source b1-
01
H1-
02
H1-
03
H3-
02
H3-
08
H3-
09
H3-
13
Drive PCB
Switch S1
1 2 d1-
01
Keypad d1-
02 d1-
04
Resulting Auto Speed
Command Signal
Terminal A2
Speed
Pot.
4-20 mA
0-10
VDC
3-15
PSIG
Serial Com
#
Run Speed
X None
None
P
P and S 1
S 1
S
G, H, Q,
V
G, H, Q,
V
G, H, Q,
V and P
G, H, Q,
V and S
L
1
0
0
0
1
L
0
0
L and P
L and S
1* 14* 3*
1
1
14
14
3
3
0
1
14
14
14
14
3
3
3
@
@
14
14
@
3
@
14
3
3
3
0.0
0.0
0.0
100*
100
100
6C 0.0
6C
6C
6C
6C
6C
6C
6C
0.0
0.0
100
0.0
0.0
0.0
100
2*
0
2
2
2
0
2
0
2
2
2
0
2
2
2
2
2*
2
0
0
0
2
2
2
2
2
2
2
1 Off* On*
1 Off Off
1 Off On
1 Off On
1 Off On
1 Off Off
0* Off On
0 Off Off
0 Off On
0 Off On
0
0
0
0
On On
On Off
On On
On On
X
X
X
X
X
X
X
X
X
X
X
X
X
X
X
X
X
X
X
X
X
X
X
X
X
X
X
X
X
X
X
X
X
X
X
X
X
X
X
Definitions:
L = LonWorks Option Card
S = Speed Potentiometer
V = Native Protocol (Modbus)
P = Pneumatic Pressure Transducer (3-15 PSIG)
G = DeviceNet Option Card
H = Profibus Option Card
Q = Ethernet Option Card
Parameter Reference: b1-01: Speed Command Input Source
0: Operator
1: Terminals
H1-02: Terminal S4 Function Selection
3: Multi-step Ref 1
14: Fault Reset
H1-03: Terminal S5 Function Selection
3: Multi-step Ref 1
6C: Com/Inv Sel 2
H3-02: Terminal A1 Gain Setting
H3-08: Terminal A2 Signal Level
0: 0 - 10 VDC
2: 4 - 20 mA
H3-09: Terminal A2 Function Selection
0: Frequency Bias
2: Aux Reference
* = The Drive factory default
# = The H/O/A switch must be in the AUTO position to allow serial com. to control the Drive.
@ = Jumpers required from S5 to S6 and S4 to SN
H3-13: Master Frequency Reference Terminal Selection d1-01: d1-02: d1-04:
0: Main Fref TA1
1: Main Fref TA2
Frequency Reference 1
Frequency Reference 2
Frequency Reference 4
Note: Hand mode run/stop for Drive and Bypass is always via the front control panel HAND/OFF/AUTO switch.
Programming 5 - 4
!
Discussion of Table 5.2 Option-Dependent Bypass Parameter Settings:
Drive Parameter Settings for Various Combinations of Bypass and Options
Notes:
See Appendix D, Communications, for additional information on serial communication.
Hand mode run/stop for Drive and Bypass is always via the front control panel HAND/OFF/AUTO switch.
The HAND/OFF/AUTO switch must be in AUTO position if serial communication is to be used to control the Drive.
For "monitoring only" of Drive parameters and operation, via serial communication, the user needs only to set-up the
H5-0X "Serial Com Setup" parameters. All other parameters may remain as they were factory programmed for the
Bypass unit and options.
Option L, LonWorks serial communication always requires DIP switch S1-1 (terminating resistor) to be ON.
"
Options - None; Bypass with no options:
Hand mode speed command from Keypad/Operator.
Auto mode speed command input signal, 4-20 mA applied to Drive terminal A2.
Auto mode run/stop contact closure for Drive and Bypass applied to terminals TB1-3 and TB1-4.
Significant
Parameter Setting b1-01 = 1: Terminals (default)
H3-13 = 1: Main Fref TA2
H3-08 = 2: 4-20 mA (default)
H3-02 = 0.0
H3-09 = 0: Frequency Bias
H1-03 = 3: Multi-Step Ref 1
(default)
Result
Speed command source = Terminals
Specific speed command source = Terminal A2
Terminal A2 is programmed for 4-20 mA (Note – Control PCB DIP switch S1-2 must also be ON)
Terminal A1 gain = 0.0 (To insure no stray signal level at this unused terminal)
Terminal A2 function is set to “bias” the terminal A1 input. Terminal A1 is not used, therefore the A2 “bias” signal becomes the speed command.
A terminal S5 input contact closure selects d1-02 (keypad) as a preset speed. This input contact is closed when H/O/A = Hand.
"
Options - None; Bypass with no options:
Hand mode speed command from Keypad/Operator.
Auto mode speed command input signal, 0-10 VDC applied to Drive terminal A2.
Auto mode run/stop contact closure for Drive and Bypass applied to terminals TB1-3 and TB1-4.
Significant
Parameter Setting b1-01 = 1: Terminals (default)
H3-13 = 1: Main Fref TA2
H3-08 = 0: 0-10 VDC
H3-02 = 0.0
H3-09 = 0: Frequency Bias
H1-03 = 3: Multi-Step Ref 1
(default)
Result
Speed command source = Terminals
Specific speed command source = Terminal A2
Terminal A2 is programmed for 0-10 VDC (Note – Control PCB DIP switch S1-2 must also be OFF)
Terminal A1 gain = 0.0 (To insure no stray signal level at this unused terminal)
Terminal A2 function is set to “bias” the terminal A1 input. Terminal A1 is not used, therefore the A2 “bias” signal becomes the speed command.
A terminal S5 input contact closure selects d1-02 (keypad) as a preset speed. This input contact is closed when H/O/A = Hand.
Programming 5 - 5
"
Options - P "Pneumatic Pressure Transducer"; Bypass with pneumatic input for speed control:
Hand mode speed command from Keypad/Operator.
Auto mode speed command input signal from the pneumatic transducer, or 4-20 mA applied to Drive terminal A2.
Auto mode run/stop contact closure for Drive and Bypass applied to terminals TB1-3 and TB1-4.
Significant
Parameter Setting b1-01 = 1: Terminals (default)
H3-13 = 1: Main Fref TA2
H3-08 = 2: 4-20 mA (default)
H3-02 = 0.0
H3-09 = 0: Frequency Bias
H1-03 = 3: Multi-Step Ref 1
(default)
Result
Speed command source = Terminals
Specific speed command source = Terminal A2
Terminal A2 is programmed for 4-20 mA (Transducer output is 4-20 mA) (Note
– Control PCB DIP switch S1-2 must also be ON)
Terminal A1 gain = 0.0 (To insure no stray signal level at this unused terminal)
Terminal A2 function is set to “bias” the terminal A1 input. Terminal A1 is not used, therefore the A2 “bias” signal becomes the speed command.
A terminal S5 input contact closure selects d1-02 (keypad) as a preset speed.
This input contact is closed when H/O/A = Hand.
"
Options - P and S "Pneumatic Pressure Transducer" and "Speed Pot."; Bypass with pneumatic input and speed potentiometer for speed control:
Hand mode speed command from speed potentiometer.
Auto mode speed command input signal from the pneumatic transducer, or 4-20 mA applied to Drive terminal A2.
Auto mode run/stop contact closure for Drive and Bypass applied to terminals TB1-3 and TB1-4.
Significant
Parameter Setting b1-01 = 1: Terminals (default)
H3-13 = 1: Main Fref TA2
Result
Speed command source = Terminals
Main speed command source = Terminal A2 and the Aux speed command source
= Terminal A1
H3-08 = 2: 4-20 mA (default) Terminal A2 is programmed for 4-20 mA (Transducer output is 4-20 mA) (Note
– Control PCB DIP switch S1-2 must also be ON)
H3-09 = 2: Aux Reference (default) Aux Terminal (A1) function is set to be a speed command input.
H1-03 = 3: Multi-Step Ref 1
(default)
A terminal S5 input contact closure selects Aux Terminal (A1) as a preset speed.
This input contact is closed when H/O/A = Hand.
"
Options - S "Speed Pot."; Bypass with speed potentiometer for speed control:
Hand mode speed command from speed potentiometer.
Auto mode speed command input signal, 4-20 mA applied to Drive terminal A2.
Auto mode run/stop contact closure for Drive and Bypass applied to terminals TB1-3 and TB1-4.
Significant
Parameter Setting b1-01 = 1: Terminals (default)
H3-13 = 1: Main Fref TA2
Result
Speed command source = Terminals
Main speed command source = Terminal A2 and the Aux speed command source
= Terminal A1
H3-08 = 2: 4-20 mA (default) Terminal A2 is programmed for 4-20 mA (Note – Control PCB DIP switch S1-2 must also be ON)
H3-09 = 2: Aux Reference (default) Aux Terminal (A1) function is set to be a speed command input.
H1-03 = 3: Multi-Step Ref 1
(default)
A terminal S5 input contact closure selects Aux Terminal (A1) as a preset speed.
This input contact is closed when H/O/A = Hand.
Programming 5 - 6
"
Options - S "Speed Pot."; Bypass with speed potentiometer for speed control:
Hand mode speed command from speed potentiometer.
Auto mode speed command input signal, 0-10 VDC applied to Drive terminal A2.
Auto mode run/stop contact closure for Drive and Bypass applied to terminals TB1-3 and TB1-4.
Significant
Parameter Setting
Result b1-01 = 1: Terminals (default)
H3-13 = 1: Main Fref TA2
Speed command source = Terminals
Main speed command source = Terminal A2 and the Aux speed command source = Terminal A1
H3-08 = 0: 0-10 VDC Terminal A2 is programmed for 0-10 VDC (Note –
Control PCB DIP switch S1-2 must also be OFF)
H3-09 = 2: Aux Reference (default) Aux Terminal (A1) function is set to be a speed command input.
H1-03 = 3: Multi-Step Ref 1 (default) A terminal S5 input contact closure selects Aux Terminal (A1) as a preset speed. This input contact is closed when H/O/A = Hand.
"
Options - G, H, L, Q, or V "Serial Communications"; Bypass with serial communication for control:
Hand mode speed command from Keypad/Operator.
Auto mode speed command input signal from serial communication.
Auto mode run/stop command for Drive from serial communication.
Auto mode run/stop contact closure for Bypass applied to terminals TB1-3 and TB1-4.
Significant
Parameter Setting b1-01 = 0: Operator
H1-03 = 6C: Com/Inv Sel 2
Result
Speed command source = Keypad/Operator (d1-01)
A terminal S5 input contact closure allows b1-01 to select d1-01 (keypad) as a preset speed. An open contact selects serial com for speed command and run/ stop. This input contact is closed when H/O/A = Hand.
"
Options - G, H, L, Q, or V "Serial Communications"; Bypass with serial communication for run/stop control and speed monitoring:
Hand mode speed command from Keypad/Operator.
Auto mode speed command input signal, 0-10 VDC applied to Drive terminal A2.
Auto mode run/stop command for Drive from serial communication.
Auto mode run/stop contact closure for Bypass applied to terminals TB1-3 and TB1-4.
Significant
Parameter Setting
Result b1-01 = 0: Operator
H3-08 = 0: 0-10 VDC
Speed command source = Keypad/Operator (d1-01)
Terminal A2 is programmed for 0-10 VDC (Note – Control PCB DIP switch
S1-2 must also be OFF)
H3-09 = 2: Aux Reference (default) Terminal A2 function is set to be a speed command input. This setting also gives terminal A2 priority over d1-02 for “preset speed 2”, see Programming
Manual.
H1-02 = 3: Multi-Step Ref 1
S4 must be jumpered to SN
H1-03 = 6C: Com/Inv Sel 2
A terminal S4 input contact closure selects A2 as “preset speed 2” speed input.
The S4 input is jumpered to SN, therefore it is always closed.
A terminal S5 input contact closure allows b1-01 to select d1-01 (keypad) as a preset speed. An open contact selects serial com for the run/stop command
(the serial com speed command is overridden by the preset speed above). This input contact is closed when H/O/A = Hand.
H1-04 = 4: Multi-Step Ref 2 (default)
S6 must be jumpered to S5
A terminal S6 input contact closure selects d1-04 (keypad) as a speed input.
When open, the speed command is determined by “preset speed 2”. This input contact is closed when H/O/A = Hand.
Programming 5 - 7
"
Options - G, H, L, Q, or V and P "Serial Communications" and "Pneumatic Pressure Transducer"; Bypass with serial communication for run/stop control and speed monitoring, with pneumatic input for speed control:
Hand mode speed command from Keypad/Operator.
Auto mode speed command input signal from the pneumatic transducer, or 4-20 mA applied to Drive terminal A2.
Auto mode run/stop command for Drive from serial communication.
Auto mode run/stop contact closure for Bypass applied to terminals TB1-3 and TB1-4.
Significant
Parameter Setting b1-01 = 0: Operator
H3-08 = 2: 4-20 mA (default)
H3-09 = 2: Aux Reference (default)
H1-02 = 3: Multi-Step Ref 1
S4 must be jumpered to SN
H1-03 = 6C: Com/Inv Sel 2
H1-04 = 4: Multi-Step Ref 2 (default)
S6 must be jumpered to S5
Result
Speed command source = Keypad/Operator (d1-01)
Terminal A2 is programmed for 4-20 mA (Transducer output is 4-20 mA)
(Note – Control PCB DIP switch S1-2 must also be ON)
Terminal A2 function is set to be a speed command input. This setting also gives terminal A2 priority over d1-02 for “preset speed 2”, see
Programming Manual.
A terminal S4 input contact closure selects A2 as “preset speed 2” speed input. The S4 input is jumpered to SN, therefore it is always closed.
A terminal S5 input contact closure allows b1-01 to select d1-01 (keypad) as a preset speed. An open contact selects serial com for the run/stop command (the serial com speed command is overridden by the preset speed above). This input contact is closed when H/O/A = Hand.
A terminal S6 input contact closure selects d1-04 (keypad) as a speed input. When open, the speed command is determined by “preset speed 2”.
This input contact is closed when H/O/A = Hand.
"
Options - G, H, L, Q, or V and S "Serial Communications" and "Speed Pot."; Bypass with serial communication for control, with hand mode speed potentiometer:
Hand mode speed command from speed potentiometer.
Auto mode speed command input signal from serial communication.
Auto mode run/stop command for Drive from serial communication.
Auto mode run/stop contact closure for Bypass applied to terminals TB1-3 and TB1-4.
Significant
Parameter Setting b1-01 = 1: Terminals (default)
H3-13 = 0: Main Fref TA1 (default)
H1-03 = 6C: Com/Inv Sel 2
Result
Speed command source = Terminals
Specific speed command source = Terminal A1
A terminal S5 input contact closure allows b1-01 to select terminals and the speed pot. as the speed command. An open contact selects serial com for speed command and run/stop. This input contact is closed when H/O/A
= Hand.
Programming 5 - 8
!
A1 Initialization
The initialization group contains parameters associated with initial setup of the Drive. Parameters involving the display language, access levels, initialization and password are located in this group.
"
A1-00 Select Language
Setting
0
1
4
5
6
2
3
Description
English (factory default)
Japanese
Deutsch
Francais
Italiano
Espanol
Portugues
The setting of parameter A1-00 determines which international language the Drive will use to display non-numerical text. The
A1-00 parameter will not be changed by an Initialization of the Drive (A1-03= “1110: User Initialize”, “2220: 2-Wire Initial”, or “3330: 3-Wire Initial”).
If the Drive is accidentally set to a language unfamiliar to the operator, locating the parameter to change the operator language can be done by performing the following:
1. Press the MENU key until the “-ADV-” MENU is shown in the upper left corner of the digital operator.
2. Press the DATA/ENTER key to enter the programming menu. The first parameter shown is A1-00 (Select Language).
3. Press the DATA/ENTER key again and use the INCREASE and DECREASE arrow keys to choose the preferred language from the list below:
0 : English
1 : Japanese
2 : Deutsch (German)
3 : Francais (French)
4 : Italiano (Italian)
5 : Español (Spanish)
6 : Portugu s (Portuguese)
"
A1-01 Access Level Selection
Setting
0
1
2
Description
Operation Only
User Level
Advanced Level (factory default)
A1-01 can be used to allow access to and permission to change all Drive parameters. If the Drive is programmed for Operation
Only (A1-01= “0: Operation Only”), then only the OPERATION and the PROGRAMMING menus are accessible. Within the
PROGRAMMING menu only parameters A1-01 and A1-04 are adjustable.
Programming 5 - 9
If A1-01 is configured for Advanced Access (A1-01= “2: Advanced Level”), then all menus and all parameters are shown. If the
Access Level Selection is set to Advanced, all parameters should be adjustable unless:
1. The Drive parameters are password protected (A1-04) which will prevent access to A1-00 through A1-03 and all A2 parameters.
2. A digital input has been configured as a Program Lockout (H1-0X= 1B) is active.
3. During serial communication writing, if a parameter change is also attempted via the digital operator, a
“BUSY - WRITE PROTECTED” message will display. Parameter change will not be possible from the digital operator until an
Enter command is received via the serial communication to finish the serial writing process.
"
A1-03 Initialize Parameters
Setting
0
1110
2220
3330
Description
No Initialize (factory default)
User Initialize
2-Wire Initialize
3-Wire Initialize
The Drive can be set back to one of three default states via the A1-03 parameter.
1. User Initialization – 1110: The modified Drive parameters are returned to the values selected as user settings. User settings are stored when parameter o2-03= “1: Set Defaults”.
2. 2-Wire Initialization – 2220: The Drive parameters are returned to factory default values with digital inputs S1 and S2 configured as Forward Run and Reverse Run, respectively.
3. 3-Wire Initialization – 3330: The Drive parameters are returned to factory default values with digital inputs S1, S2, and S5 configured as Run, Stop, and Forward/Reverse respectively.
After an initialization is performed, parameter A1-03 will automatically be set back to 0.
S1
FWD Run/Stop
Stop switch
(NC contact)
Operation switch
(NO contact)
S2
REV Run/Stop
SN
S3 or S5
Run command
(run on momentary close)
Stop command
(stop on momentary open)
Forward/reverse command
(multi-function input)
Sequence input common
3-wire control
Fig 5.1 2 & 3-Wire Control Wiring Examples
IMPORTANT
Some parameters are unaffected by either the 2-Wire or 3-Wire initialization. The following parameters will not be reset when parameter A1-03=2220 or 3330:
A1-00
E1-03 o2-04 o2-09
Language Selection
V/f Pattern Selection kVA Selection
Initialization Specification Selection
Programming 5 - 10
"
A1-04 Password Entry
Setting Range: 0 to 9999
Factory Default: 0
If parameters A1-01 through A1-03 and all of the A2 parameters are locked (unchangeable) they can be unlocked by entering the correct password number into A1-04.
Once the correct password number is entered and the specified parameters are unlocked, a 2-Wire or 3-Wire initialization will reset the password to 0000.
"
A1-05 Select Password
Setting Range: 0 to 9999
Factory Default: 0
When the value set into A1-04 does NOT match the value set into A1-05, parameters A1-01 thru A1-03 and A2-32 cannot be changed. All other parameters determined by A1-01 can be changed. Parameter A1-05 can be accessed by displaying parameter
A1-04, then press and hold the RESET key along with the MENU key simultaneously.
!
b1 Sequence
The Sequence Group contains parameters associated with starting and stopping the Drive. Parameters involving the Run
Command, Speed Reference location, Stopping Method and Hand/Auto changeover are located in this group.
"
b1-01 Reference (Speed Command) Source Selection
This is one of the special parameter settings required by the Bypass logic circuit. See Table 5.1.
The addition of serial communication to the Drive and Bypass unit, after shipment to the job site, would be the only reason for changing this parameter. See Table 5.2 for the parameter settings required to enable serial communication in the field.
Setting
0
1
2
3
Description
Operator - Digital Preset Speed d1-01
Terminals - Analog Input Terminal A1 (or Terminal A2, see Parameter H3-13)
Serial Com - RS-485 Terminals R+, R-, S+ and S-
Option PCB - Option Board connected at 2CN
In order to run the Drive and motor with the BYPASS/DRIVE switch in the DRIVE position: the Drive must receive a Run command and a speed command. Parameter b1-01 specifies from where the speed command is received when the Drive is in the
AUTO mode. Switching into the AUTO mode can be done by turning the Hand/Off/Auto selector switch to AUTO while the
Drive is stopped.
IMPORTANT
If a Run command is input to the Drive but no corresponding speed command is input, the Run indicator on the digital operator will turn on and the STOP indicator on the digital operator will blink.
Programming 5 - 11
If you want the Drive to follow the speed command set by the digital operator: Use the HAND mode by turning the
HAND/OFF/AUTO selector switch to HAND. The speed command can then be entered into the U1-01 monitor parameter in the
“-DRIVE-” Menu.
If you want the Drive to follow an AUTO analog speed command: Connect a 0 – 10 VDC speed command signal between terminals A1 and AC or a 4 – 20 mA speed command signal to terminals A2 and AC. Select the AUTO position of the Hand/
Off/Auto switch.
If you want the Drive to receive the speed command from serial communication: Set the parameter indicated in Table 5.2 for the desired serial communication option. Connect the RS-485/422 serial communications cable to terminals R+, R-, S+, and S- on the control I/O terminal block. The HAND/OFF/AUTO selector switch must be in the AUTO position.
"
b1-02 Run Source
Setting
0
1
2
3
Description
Operator
Terminals (factory default)
Serial Com
Option PCB
To successfully operate the Drive or Bypass and motor remotely, an external run command must be received by the Drive and
Bypass unit. Parameter b1-02 specifies from where the run command for the Drive will be accepted.
This parameter is by default set to “1: Terminals.” This setting is required by the Bypass logic circuit.
To issue a run command from the control panel: Turn the Hand/Off/Auto switch to the HAND position.
To issue a run command from a remote source: Turn the Hand/Off/Auto switch to the AUTO position. A contact closure between terminals TB1-3 and TB1-4 will control the Drive or Bypass start and stop operation.
To issue a run command via serial communication: Set the parameters indicated in Table 5.2 for the desired serial communication option. Connect the RS-485/422 serial communication cable to R+, R-, S+, and S- on the removable terminal block.
"
b1-03 Stopping Method
There are four methods of stopping the Drive when the Run command is removed.
Setting
0
1
2
3
Description
Ramp to Stop (factory default)
Coast to Stop
DC Injection to Stop
Coast w/Timer
“0:Ramp to stop”: When the Run command is removed, the Drive will decelerate the motor to 0 rpm. The rate of deceleration is determined by the active deceleration time. The factory default Decel Time is in parameter C1-02.
Programming 5 - 12
When the output frequency has dropped below the DC Injection Start Frequency in b2-01 (Default = 0.5HZ) DC current will be injected in the motor at a level determined by b2-02 (50% Default). The DC Injection condition will occur for the time specified by b2-04 (0.0 Default), to establish the end point of the ramp. DC injection can be used to insure the motor is at zero rpm prior to the Drive shutting off.
Run Command
ON
(CLOSED)
OFF
(OPEN)
100 % b2-01
Output Frequency
Deceleration Time (C1-02)
0 %
TIME
Fig 5.2 Deceleration to Stop
DC Injection Brake
| b2-04 |
The actual deceleration time can be determined by the following formula
Time to Stop
=
Output Freq.
at time of stop command
Maximum Frequency (E1 04)
×
Setting of active Decel Time (C1 -
02 or C1-04)
If S-Curve characteristics are specified by the Drive programming, they will add to the total time to stop.
1:Coast to stop: When the Run command is removed, the Drive will turn off its output and the motor will coast (uncontrolled deceleration). The friction of the driven equipment will eventually overcome any residual inertia of the system and the rotation will stop.
Run Command
ON
(CLOSED)
OFF
(OPEN)
100 %
Output Frequency
0 %
Motor Speed
Drive Output Frequency Interrupted
TIME
Fig 5.3 Coast to Stop
IMPORTANT
After a stop is initiated, a subsequent Run commands input before the Minimum Baseblock Time (L2-03) has expired, will be ignored.
Programming 5 - 13
2:DCInj to Stop: When the Run command is removed, the Drive will Baseblock (turn off its output) for the Minimum Baseblock Time (L2-03). Once the Minimum Baseblock Time has expired, the Drive will inject DC current into the motor windings to lock the motor shaft. The stopping time will be reduced as compared to Coast to Stop. The level of DC Injection current is set by parameter b2-02 (50% Default). The DC Injection brake time is determined by the set value in b2-04 and the output frequency at the time the Run command is removed.
DC Injection Brake Time
=
(b2 04)
×
10
×
Output Frequency
Maximum Frequency (E1 04)
Run Command
ON
(CLOSED)
OFF
(OPEN) b2-04 x 10
100 %
Output Frequency
0 %
Drive Output Voltage Interrupted
Minimum Baseblock
Time (L2-03)
DC Injection Brake
DC Injection Brake Time b2-04
Fig 5.4 DC Injection Braking to Stop b2-04
10%
100% (Maximum
Output Frequency)
IMPORTANT
If an overcurrent (OC) fault occurs during DCInj to Stop, lengthen the Minimum Baseblock Time (L2-03) until the fault no longer occurs.
3:Coast w/Timer: When the Run command is removed, the Drive will turn off its output and the motor will coast to a stop. If a
Run command is input before time T (Operation Wait Time) expires, the Drive will not run and the Run command will need to be cycled before operation can occur
.
The time T (Operation Wait Time) is determined by the output frequency when the
Run command is removed and the active deceleration time (C1-02).
Ignored
Run Command
Run Command
ON
(CLOSED)
OFF
(OPEN)
Deceleration
Time (C1-02)
100 %
Output Frequency
0 %
Drive Output
Voltage
Interrupted
(C1-02)
Fig 5.5 Coast to Stop with Timer
Minimum
Baseblock
Time (L2-03)
Minimum
Output
Frequency
100% (Maximum
Output
Frequency)
Output Frequency at Stop Command Input
Programming 5 - 14
"
b1-04 Reverse Operation
Setting
0
1
2
3
Description
Reverse Enabled
Reverse Disabled (factory default)
Exchange Phase
ExchgPhs, Rev Dsbl
For some applications reverse motor rotation is not applicable and may even cause problems (e.g., air handling units, pumps, etc.). Setting parameter b1-04 to 1 or 3 will cause the Drive to ignore any inputs for reverse operation. Setting parameter b1-04 to either 2 or 3 will change the motor shaft rotation when a Forward Run command is given by exchanging the order of the output phasing.
The factory default setting of parameter b1-04 is “1: Disabled”. When b1-04= “1: Disabled”, reverse operation is prohibited and no exchanging of output phasing occurs.
"
b1-07 Local/Remote Run Selection
Setting
0
1
Description
Cycle Extern Run
Accept Extrn Run (factory default)
When the Drive is switched between the Local (Hand) mode (the digital operator) to the Remote (Auto) mode by the Hand/
Off/Auto selector switch, there is the possibility that a Run command is already present (i.e. a contact closure between terminals TB1-3 and TB1-4. Parameter b1-07 determines whether the Drive will:
Ignore the external Run command until it is removed and re-instated (b1-07= “0: Cycle Extern Run”)
OR
Accept the already present Run command and immediately begin acceleration to the commanded speed
(b1-07= “1: Accept Extrn Run”).
IMPORTANT
When switching from local mode to Auto mode when b1-07= “1:Accept Extrn Run” the Drive may start unexpectedly if the Run command is already applied. Be sure all personnel are clear of rotating machinery and electrical connections prior to switching between local mode and Auto mode.
"
b1-08 Run Command Selection During Programming
Setting
0
1
Disabled
Enabled (factory default)
Description
As a convenience to the user, the Drive will respond to a Run input even when the digital operator is being used to adjust parameters. If it is necessary that external Run commands not be recognized while the Drive is being programmed, set b1-08= “0: Disabled”.
Programming 5 - 15
"
b1-11 Drive Delay Time Setting
Setting Range: 0 to 600 Seconds
Factory Default: 0 Seconds
If a time is set into parameter b1-11, the Drive will delay executing any run command until the b1-11 time has expired.
During Drive delay time execution, the digital operator will display:
DDLY
Waiting to RUN
Both the ALARM and Run indicators will blink while the Drive waits to execute the Run command.
!
b2 DC Braking
The DC Braking Group contains parameters associated with the DC injection braking feature. Parameters involving the starting frequency, current level, braking time, and motor pre heat current level are located here.
"
b2-01 DC Injection Braking Start Frequency
Setting Range: 0.0 to 10.0 Hz
Factory Default: 0.5 Hz
Parameter b2-01 sets the output frequency where the Drive begins DC Injection during Ramp to stop. in order to lock the rotor of the motor and established the end point of the ramp. If b2-01 < E1-09 (Minimum Frequency), then DC Injection begins at E1-09.
Parameter b2-01 also determines the output frequency that the Drive must be at or below before a Zero Speed condition is considered true. This affects any digital output configured as a Zero Speed signal (H2-0x= “1: Zero Speed”).
Output Frequency
| b2-04
| b2-01 t ime
DC injection
Fig 5.6 DC Injection Braking During Stopping
"
b2-02 DC Injection Braking Current
Setting Range: 0 to 100%
Factory Default: 50%
The level of DC Injection Braking Current affects the strength of the magnetic field attempting to lock the motor shaft.
Increasing the level of current will increase the amount of heat generated by the motor windings and should only be increased to the level necessary to hold the motor shaft. DC Injection current is set in percentage of Drive rated output current. Drive rated output current is stated on the Drive nameplate.
Programming 5 - 16
"
b2-03 DC Injection Braking Time at Start b2-04 DC Injection Braking Time at Stop
Setting Range: 0.00 to 10.00 Seconds
Factory Default: b2-03 = 5.00 Seconds b2-04 = 0.00 Seconds b2-03 is one of the special parameter settings required by the Bypass logic circuit. See Table 5.1.
The Drive can be programmed to automatically DC Inject for a predetermined amount of time prior to accelerating to speed
(b2-03) and/or at the end of a Ramp to stop (b2-04). Parameter b2-03 can be used to stop a rotating motor prior to attempting acceleration (i.e. a wind milling fan). If DC Injection braking at start or Speed Search is not enabled, attempting to Drive a spinning motor may cause nuisance tripping.
Parameter b2-04 can be used to resist any residual motion of the load after the deceleration has finished.
DC injection
Output Frequency b2-03 b2-04
Fig 5.7 DC Injection Braking During Starting and Stopping
Parameter b2-04 also serves the function of affecting the length of time DC Injection to stop (b1-03= “2: DC Injection to
Stop”) will occur.
"
b2-09 Motor Pre-Heat Current
Setting Range: 0 to 100%
Factory Default: 0%
A DC current can be circulated within the motor windings while the motor is stopped. The current will produce heat within the motor and prevent condensation. Parameter b2-09 determines the percentage of Drive rated output current that will be used for the motor pre-heat function. This function can be useful in applications where the motor sits for extended periods of time in humid conditions. Motor pre-heating can only be initiated by closing a digital input programmed as a Motor Pre-heat Input
(H1-0x= 60). Check with the motor manufacturer to determine the maximum acceptable current level the motor can withstand when stopped. Be sure not to exceed the motor manufacturers recommended level.
Programming 5 - 17
!
b3 Speed Search
The Speed Search function allows the Drive to determine the speed of a motor shaft that is being driven by rotational inertia.
Speed Search will allow the Drive to determine the speed of the already rotating motor and begin to ramp the motor to a set speed without first having to bring it to a complete stop. When a momentary loss of supply power is experienced, the Drive output is turned off. This results in a coasting motor. When power returns, the Drive can determine the speed of the coasting motor and start without requiring it to be brought to minimum speed. Speed Search can be programmed to always be active by setting b3-01 or it can be commanded by remote contact closure by setting a digital input.
There are two forms of Speed Search in the Drive, the speed estimation method and the current detection method.
IMPORTANT
When setting the Drive for remote Speed Search input, via a contact closure, the method of Speed Search is determined by the setting of b3-01. If b3-01= ”0: SpdsrchF Disable” then the remote input will initiate speed estimation method, and if b3-01= ”2: SpdsrchI Disable”, then the remote input will start the current detection method.
Parameters L2-03 and L2-04 also affect the current detection method of Speed Search operation.
"
b3-01 Speed Search Selection
Setting
0
1
2
3
Description
SpdsrchF Disable
SpdsrchF Enable
SpdsrchI Disable (factory default)
SpdsrchI Enable
Speed Estimation: Method (b3-01= 0 or 1)
The speed estimation method will calculate the speed using measurements of residual motor fields. The speed estimation version is bi-directional and will determine both the motor speed and direction. To enable speed estimation Speed Search at start, set b3-01= “1: SpdsrchF Enable”.
IMPORTANT
If the speed estimation method of Speed Search is to be used, then Auto-tuning must be performed prior to using Speed Search. If the length of cable between the Drive and motor is ever changed after Auto-tuning then Auto-tuning should be performed again.
IMPORTANT
The speed estimation mode cannot be used when there are multiple motors operated by one Drive or the motor is two or more frames smaller than the standard size motor per the Drive capacity.
Programming 5 - 18
AC power supply
Output frequency
ON OFF
Start using speed detected
Set frequency reference
Output current
10 ms
Minimum baseblock time (L2-03) x 0.75 *1
Minimum baseblock time (L2-03) x 0.75*1
*2
*1 Baseblock time may be reduced by the output frequency
immediately before the baseblock.
minimum Speed Search Wait Time (b3-05).
Fig 5.8 Speed Search (Estimated Speed Method) after momentary power loss where the power loss time is less than the minimum baseblock time
AC power supply
Output frequency
ON OFF
Start using speed detected
Set frequency reference
Output current
10 ms
Minimum baseblock time
(L2-03)
Speed Search Wait Time
(b3-05)
Note: If the frequency immediately before the baseblock is low or the power supply break time is long, operation may be the same as the search in case 1.
Fig 5.9 Speed Search (Estimated Speed Method) after momentary power loss where the power loss time exceeds the minimum baseblock time
Current Detection Method (b3-01=2 or 3):
The current detection method starts searching from a predetermined frequency while monitoring the Drive output current to determine when the rotor speed and the Drive output speed (frequency) match.
The current detection version is not bi-directional. To enable current detection Speed Search at start set b3-01= “3: SpdscrhI enable” and program any digital input equal to Speed Search 1 (H1-0x= 61) or Speed Search 2 (H1-0x= 62). Speed Search 1 will start searching from the max. frequency (E1-04) and ramp down to meet the rotor speed. Speed Search 2 will start searching from the set frequency and ramp down to meet the rotor speed.
IMPORTANT
If a UV1 fault occurs when current detection Speed Search is attempted, increase the setting of L2-04.
IMPORTANT
If an OC fault occurs when Speed Search is attempted after power loss recovery, increase the setting of L2-03.
Programming 5 - 19
Run command
OFF ON
Maximum output frequency or set frequency
Output frequency
Deceleration time set in b3-03
Set frequency reference b3-02
Speed search current level
Output current
Minimum baseblock time
*
(L2-03)
Fig 5.10 Speed Search (Current Detection Method) at Startup
AC power supply
Output frequency
ON OFF
Output frequency before power loss
Deceleration time set in b3-03
Set frequency reference b3-02 speed search operating current
Output current
*1 Baseblock time may be reduced by the output frequency
immediately before baseblock.
*2 After AC power supply recovery, motor waits for the minimum
Minimum baseblock time (L2-03)
*1
*2
Fig 5.11 Speed Search (Current Detection Method) after momentary power loss where the power loss time is less than the minimum baseblock time
AC power supply
ON OFF Output frequency before power loss
Set frequency reference
Output frequency b3-02
Speed search operating time
Output current
Speed search wait time (b3-05)
Minimum baseblock time
(L2-03)
Fig 5.12 Speed Search (Current Detection Method) after momentary power loss where the power loss time exceeds the minimum baseblock time
Setting of b3-01
2
3
0
1
Automatic Speed Search for all RUN commands and momentary power loss
No
Yes - Speed Estimation
No
Yes - Current Detection
Speed Search Method
Used for Multi-function inputs
Speed Estimation
Current Detection
Programming 5 - 20
"
b3-02 Speed Search Deactivation Current
Setting Range: 0 to 200% of Drive rated output current
Factory Default: 120% of Drive rated output current
When using the current detection method of Speed Search, parameter b3-02 sets the current level that will determine when the search is complete and the rotor and output speeds match. When the output frequency is higher than the actual rotor speed the slip causes the current to be high. As the output frequency is lowered, the closer it comes to the rotor speed, the lower the current draw will be. When the output current drops below the level as set in b3-02 (100% = Drive Rated Current) the output frequency stops decreasing and normal operation resumes.
"
b3-03 Speed Search Deceleration Time
Setting Range: 0.1 to 10.0 Seconds
Factory Default: 2.0 Seconds
Parameter b3-03 sets the deceleration ramp used by the current detection method of Speed Search when searching for the motor’s rotor speed. Even if Speed Search 2 is selected, for Speed Search at start, the time entered into b3-03 will be the time to decelerate from maximum frequency (E1-04) to minimum frequency (E1-09).
"
b3-05 Speed Search Delay Time
Setting Range: 0.0 to 20.0 Seconds
Factory Default: 0.2 Seconds
In cases where an output contactor is used between the Drive and the motor, extra waiting time is provided after power returns and before Speed Search is performed. This extra time allows for the contactor to operate. When Speed Search at start is used, b3-05 will serve as the lower limit of the Minimum Baseblock Time (L2-03).
"
b3-14 Bi-Directional Speed Search Selection
Setting
0
1
Description
Disabled
Enabled (factory default)
The b3-14 parameter can be used to turn off the bi-directional capabilities of the Speed Estimation form of Speed Search. By turning off the bi-directional capability, the speed search will only try to match the speed in the last known direction.
Programming 5 - 21
!
b5 PI Function
The capability to accept an analog signal as feedback for a PI (Proportional + Integral) control function is built into the Drive.
D1-04
D1-02
D1-01
Option Card b1-01
4
3
Frequency Reference using multi-step command
Frequency reference
(U1-01)
Reg. 0Fh, bit 1
1
1 b5-20 b5-18
Scaling
PI Differential
1
Fdbk. H3-09=16
0
0
0 b5-01=0
PI control is OFF under the following conditions:
- b5-01=0
- During JOG command input
ON
ON
Enable / Disable reverse operation when PI output is negative
+
Upper limit
Fmax x109%
+
0 b5-11
1
Lower limit 0
Upper limit
Fmax x109%
1
0
2
Sleep function selection b5-21
+
b5-16
Delay
Timer b5-15
Sleep Level
Sleep Function
RUN on/off
Serial Com
1 0
PI Differential
Fdbk. H3-09=16
1
Terminal A1
MEMOBUS Reg. 06H
PI target value
Constant b5-19
Terminal A1
Terminal A2
2
PI SFS cancel
H1-xx=34
1
0
PI SFS b5-17
Scaling o1-03
PI Set Point
(U1-38)
Scaling b5-20 b5-01=3 b5-01=1
PI Input
(U1-36)
OFF
Lower limit
Fmax x109%
SFS
2
Output frequency
Sleep function selection b5-21
0
+
b5-22
PI Snooze Level b5-23
Delay
Timer
PI
Snooze
PI Snooze Function
0
1
PI Differential
Fdbk. H3-09=16
0
1
H3-09=B
PI Feedback 2
(U1-46)
+
-
1
0 b5-28
0
1
PI Differential
Fdbk. H3-09=16
PI SFS cancel
H1-xx=34
1
PI SFS b5-17
1 0
H3-09=16
+
PI Input
0
+
-
PI Feedback
(U1-24) b5-20
Scaling
H1-xx=35
0
Z -1
1
I-time b5-03
0
P
1/t
Proportional gain b5-02
1
Integral Hold
H1-xx=31
Sleep function selection b5-21
2
+
+
I - limit b5-04
Z -1
0
1
+ +
Integral Reset
H1-xx=30
PI Snooze Function b5-29
0
+
1
0 or 1
+
-
PI
Wake Up
P
PI Differential
Fdbk. H3-09=16 b5-24
PI Wake Up Level
PI offset
(b5-07)
PI Limit b5-06
PI delay time b5-08
1/t
0
Z -1
1
PI Output
Characteristic b5-09
1
PI Differential
Fdbk. H3-09=16
+
+
0 b5-07
PI offset
PI Output
Gain b5-10
1 0 b5-30
PI output monitor
(U1-37)
Fig 5.13 PI Block Diagram
Bypass units are shipped with the parameters in Table 5.1 and Table 5.2 pre-established.
To add PI control to a Bypass unit; observe the control options that are included in the unit by review of the model number on the nameplate (inside of door and external lower right side) as well as the option codes and model number description in
Chapter 1. Then revise the parameter settings indicated in Table 5.3 and 5.4 for a line of data, in Table 5.4, with the same
(or similar) combination of options. This will add the logic required for PI control to that required for Bypass control.
Table 5.3 includes parameters that are the same regardless of control options specified while Table 5.4 provides detail on the option dependent parameters.
Programming 5 - 22
PARAMETER
NUMBER b1-01 b5-01
H1-03
H1-04
H3-02
H3-08
H3-09
H3-13 o1-03 o1-06 o1-08
SETTING
Table 5.3 PI Control Parameter Settings in Bypass Units
Bypass & PI
Control
Bypass
Default
UNITS DESCRIPTION
SEE TABLE
5.4
1
19
SEE TABLE
5.2
0
SEE TABLE
5.2
4 SEE TABLE
5.4
100
SEE TABLE
5.4
SEE TABLE
5.2
SEE TABLE
5.2
KEYPAD DISPLAY
For Bypass Setting
N/A Frequency Reference Selection – Selects the speed command input source
N/A PI Mode Selection – Enables PI mode
Reference Source / Terminals
PI Mode Setting / PI Mode
Terminal S5 Sel / PI Disable N/A Terminal S5 Function Selection – Set for PI
Disable, turn off PI controller
N/A Terminal S6 Function Selection – Set for various operating modes
% Terminal A1 Gain Setting
Terminal S6 Sel / Com/Inv Sel 2, for example
Terminal / (0-1000)
B
1
1
1
24
SEE TABLE
5.2
SEE TABLE
5.2
0
0
3
N/A Terminal A2 Signal Level – Signal selection,
0 to 10 VDC (Drive control board switch
S1-2 off) or 4 to 20 mA (Drive control board switch S1-2 on)
N/A Terminal A2 Function Selection – Selects how this input will be used by the Drive
Term A2 Signal / 0-10 VDC
Terminal A2 Sel / PI Feedback
TA1/A2 Select / Main Fref TA2 N/A Master Frequency Reference Terminal
Selection – Determines which terminal (A1 or A2) will be the main speed reference source.
% Digital Operator Display Selection – Set for percent
Display Scaling / (0-39999)
N/A User Monitor Selection Mode – Enables a custom display for PI Control monitoring
N/A Third Line User Monitor Selection – Display
PI Feedback
Monitor Mode Sel / 1: 3 Non
Selectable
3rd Monitor Sel / 24: PI Feedback
"
Digital Operator and Control Panel Display for PI Control
In Table 5.3, the o1-0X parameter listed setup the Drive display to indicate 3 variables for PI control as in Figure 5.14 when the HAND/OFF/AUTO switch is in AUTO.
FWD REV SEQ
AUTO
REF ALARM
- - - - - - - - - - - - - - - - - - - - - - - - - - - - -
RUN
Monitor
MENU
ESC
DATA
ENTER
STOP
RESET
Fig 5.14 Drive Display for PI Control, AUTO Mode
PI SETPOINT
OUTPUT
PI FEEDBACK
Programming 5 - 23
When the HAND/OFF/AUTO switch is transfered to the HAND position, the display will automatically change to indicate the speed command, as in Figure 5.15.
FWD REV SEQ
AUTO
REF ALARM
- - - - - - - - - - - - - - - - - - - - - - - - - - - - -
RUN
Monitor
MENU
ESC
DATA
ENTER
STOP
RESET
SPEED COMMAND
OUTPUT
FEEDBACK
Fig 5.15 Drive Display for PI Control, HAND Mode
Options
None
None
S
S
S
G, H, Q or V 2
G, H, Q or V 0
G, H, Q or V 0
L 0
V and S
L and S
0
1*
1
1
1
1
Table 5.4 Option Dependent Drive PI Control Parameters in Bypass Units
Parameters Effected by Options Specified b1-01 H1-04 H3-08
Drive PCB
Switch S1
1 2
Resulting Hand
Speed Command
Source
Keypad
U1-01
Speed
Pot.
Auto: PI
Feedback
Terminal A2
4-20 mA
0-10
VDC
TB1
3&4
Auto:
Run/Stop
Serial
#
Auto: PI Setpoint
Keypad
U1-01
Serial
#
Speed
Pot.
0 4* 2* Off On* X X X X
4
4
4
6D
@
6E
@
6C
@
6C
@
6C
@
6C
@
6C
@
2
2
0
0
0
0
2
0
0
0
Off* Off
Off Off
Off On
Off Off
Off Off
Off Off
Off On
On On
Off Off
On Off
X
X
X
X
X
X
X
X
X
X
X
X
X
X
X
X
X
X
X
X
X
X
X
X
X
X
X
X
X
X
X
X
X
X
X
X
X
X
X
X
Definitions:
L = LonWorks Option Card
S = Speed Potentiometer
V = Native Protocol (Modbus)
G = DeviceNet Option Card
H = Profibus Option Card
Q = Ethernet Option Card
Parameter Reference: b1-01: Speed Command Input Source
0: Operator
1: Terminals
H1-04: Terminal S6 Function Selection
6C: Com/Inv Sel 2
6D: Auto Mode Selection
6E: Hand Mode Selection
4: Multi-Step Ref 2
Note:
* = The factory default
# = The H/O/A switch must be in the AUTO position
to allow serial com. to control the Drive.
@ = Jumpers required from S5 to S6
H3-08: Terminal A2 Signal Level
0: 0 - 10 VDC
2: 4 - 20 mA
Hand mode run/stop for Drive and Bypass is always via the front control panel HAND/OFF/AUTO switch.
Programming 5 - 24
"
Discussion of Table 5.4 Options Dependent, PI Control Bypass Parameter Settings:
Typical Drive Parameter Settings for PI Control with Various Combinations of Bypass and Control Options
Notes:
For project specific PI control tuning see the PI Control (b5-XX) parameters in this chapter. Tables 5.3 and 5.4 provide the basic configuration for PI Control from a Drive in an E7 Bypass unit. The b5-XX parameters are defaulted to a good starting point for most HVAC applications. Final adjustment to some of the b5-XX parameters for the project at hand may be required.
Hand mode run/stop for Drive and Bypass is always via the front control panel HAND/OFF/AUTO switch.
Options - None;
Bypass with PI Control and no options:
Hand mode speed command from Keypad/Operator.
Auto mode PI Setpoint from Keypad/Operator.
Auto mode PI Feedback input signal, 4-20 mA applied to Drive terminal A2.
Auto mode run/stop contact closure for Drive and Bypass applied to terminals TB1-3 and TB1-4.
Significant
Parameter Setting b1-01 = 0: Operator b5-01 = 1: Enable
H1-03 = 19: PI Disable
H3-08 = 2: 4-20 mA (default)
H3-09 = B: PI Feedback
H3-13 = 1: Main Fref TA2
Result
Speed command (Hand) and PI setpoint (Auto) sourced = Keypad/Operator (U1-01)
Enable PI mode of operation
A terminal S5 input contact closure disables PI mode. This input contact is closed when H/O/A = Hand.
Terminal A2 is programmed for 4-20 mA (Note – Control PCB DIP switch S1-2 must also be ON)
Terminal A2 function is set to provide PI feedback for closed loop control
Terminal A2 (the feedback terminal) serves as the main input
Options - None;
Bypass with PI Control and no options:
Hand mode speed command from Keypad/Operator.
Auto mode PI Setpoint from Keypad/Operator.
Auto mode PI Feedback input signal, 0-10 VDC applied to Drive terminal A2.
Auto mode run/stop contact closure for Drive and Bypass applied to terminals TB1-3 and TB1-4.
Significant
Parameter Setting b1-01 = 0: Operator b5-01 = 1: Enable
H1-03 = 19: PI Disable
H3-08 = 0: 0-10 VDC
H3-09 = B: PI Feedback
H3-13 = 1: Main Fref TA2
Result
Speed command (Hand) and PI setpoint (Auto) source = Keypad/Operator (U1-01)
Enable PI mode of operation
A terminal S5 input contact closure disables PI mode. This input contact is closed when H/O/A = Hand.
Terminal A2 is programmed for 0-10 VDC (Note – Control PCB DIP switch S1-2 must also be OFF)
Terminal A2 function is set to provide PI feedback for closed loop control
Terminal A2 (the feedback terminal) serves as the main input
Programming 5 - 25
Options - S
"Speed Pot."; Bypass with PI Control and speed potentiometer for speed control and setpoint:
Hand mode speed command from speed potentiometer.
Auto mode PI Setpoint from speed potentiometer.
Auto mode PI Feedback input signal, 0-10 VDC applied to Drive terminal A2.
Auto mode run/stop contact closure for Drive and Bypass applied to terminals TB1-3 and TB1-4.
Significant
Parameter Setting b1-01 = 1: Terminals (default) b5-01 = 1: Enable
H1-03 = 19: PI Disable
H3-08 = 0: 0-10 VDC
H3-09 = B: PI Feedback
H3-13 = 1: Main Fref TA2
Result
Speed command (Hand) and PI setpoint (Auto) source = Terminals
Enable PI mode of operation
A terminal S5 input contact closure disables PI mode. This input contact is closed when H/O/A = Hand.
Terminal A2 is programmed for 0-10 VDC (Note – Control PCB DIP switch S1-2 must also be OFF)
Terminal A2 function is set to provide PI feedback for closed loop control
Terminal A2 (the feedback terminal) serves as the main input
Options - S
"Speed Pot."; Bypass with PI Control and speed potentiometer for speed control:
Hand mode speed command from speed potentiometer.
Auto mode PI Setpoint from Keypad/Operator.
Auto mode PI Feedback input signal, 0-10 VDC applied to Drive terminal A2.
Auto mode run/stop contact closure for Drive and Bypass applied to terminals TB1-3 and TB1-4.
Significant
Parameter Setting b1-01 = 1: Terminals (default) b5-01 = 1: Enable
H1-03 = 19: PI Disable
H1-04 = 6D: Auto Mode Sel
S6 must be jumpered to S5
H3-08 = 0: 0-10 VDC
H3-09 = B: PI Feedback
H3-13 = 1: Main Fref TA2
Result
Speed command (Hand) and PI setpoint (Auto) source = Terminals
Enable PI mode of operation
A terminal S5 input contact closure disables PI mode. This input contact is closed when H/O/A = Hand.
A terminal S6 input contact opening (H/O/A = Auto) puts the Drive in “Hand” mode to source the PI Setpoint from the Keypad/Operator (overrides b1-01). A terminal S6 input contact closure (H/O/A = Hand) puts the Drive in “Auto” mode to allow b1-01 to determine the speed command source. This input is jumpered to S5, therefore the contact is closed when H/O/A = Hand.
Terminal A2 is programmed for 0-10 VDC (Note – Control PCB DIP switch S1-2 must also be OFF)
Terminal A2 function is set to provide PI feedback for closed loop control
Terminal A2 (the feedback terminal) serves as the main input
Programming 5 - 26
Options - G, H, L, Q, or V
"Serial Communications"; Bypass with PI Control and serial communication for Setpoint input:
Hand mode speed command from Keypad/Operator.
Auto mode PI Setpoint input signal from serial communication.
Auto mode run/stop contact closure for Drive and Bypass applied to terminals TB1-3 and TB1-4.
Significant
Parameter Setting b1-01 = 2: Serial Com b5-01 = 1: Enable
H1-03 = 19: PI Disable
H1-04 = 6E: Hand Mode Sel
S6 must be jumpered to S5
H3-08 = 0: 0-10 VDC
H3-09 = B: PI Feedback
H3-13 = 1: Main Fref TA2
Result
Speed command (Hand) and PI setpoint (Auto) source = Serial Communication
Enable PI mode of operation
A terminal S5 input contact closure disables PI mode. This input contact is closed when H/O/A = Hand.
A terminal S6 input contact opening (H/O/A = Auto) puts the Drive in “Auto” mode to allow b1-01 to determine the PI Setpoint source. A terminal S6 input contact closure (H/O/A = Hand) puts the Drive in “Hand” mode to source the speed command from the Keypad/Operator (overrides b1-01). This input is jumpered to
S5, therefore the contact is closed when H/O/A = Hand.
Terminal A2 is programmed for 0-10 VDC (Note – Control PCB DIP switch S1-2 must also be OFF)
Terminal A2 function is set to provide PI feedback for closed loop control
Terminal A2 (the feedback terminal) serves as the main input
Options - G, H, L, Q, or V
"Serial Communications"; Bypass with PI Control and serial communication for run/stop control and Setpoint input:
Hand mode speed command from Keypad/Operator.
Auto mode PI Setpoint input signal from serial communication.
Auto mode run/stop command for Drive from serial communication.
Auto mode run/stop contact closure for Bypass applied to terminals TB1-3 and TB1-4.
Significant
Parameter Setting b1-01 = 0: Operator b5-01 = 1: Enable
H1-03 = 19: PI Disable
Result
Speed command source = Keypad/Operator (U1-01)
Enable PI mode of operation
A terminal S5 input contact closure disables PI mode. This input contact is closed when H/O/A = Hand.
H1-04 = 6C: Com/Inv Sel 2 S6 must be jumpered to S5
A terminal S6 input contact opening (H/O/A = Auto) selects serial com for both the run/stop command and speed command. A terminal S6 input contact closure
(H/O/A = Hand) allows b1-01 to select Keypad/Operator as the speed command source. This input is jumpered to S5, therefore the contact is closed when
H/O/A = Hand.
H3-08 = 2: 4-20 mA (default)
H3-09 = B: PI Feedback
Terminal A2 is programmed for 4-20 mA (Note – Control PCB DIP switch S1-2 must also be ON)
Terminal A2 function is set to provide PI feedback for closed loop control
H3-13 = 1: Main Fref TA2 Terminal A2 (the feedback terminal) serves as the main input
Programming 5 - 27
Options - G, H, L, Q, or V
and S "Serial Communications" and "Speed Pot."; Bypass with PI Control and serial communication for run/stop control and Setpoint input, with hand mode speed potentiometer:
Hand mode speed command from speed potentiometer.
Auto mode PI Setpoint input signal from serial communication.
Auto mode run/stop command for Drive from serial communication.
Auto mode run/stop contact closure for Bypass applied to terminals TB1-3 and TB1-4.
Significant
Parameter Setting b1-01 = 1: Terminals (default) b5-01 = 1: Enable
H1-03 = 19: PI Disable
Result
Speed command (Hand) and PI setpoint (Auto) source = Terminals
Enable PI mode of operation
A terminal S5 input contact closure disables PI mode. This input contact is closed when H/O/A = Hand.
H1-04 = 6C: Com/Inv Sel 2 S6 must be jumpered to S5
A terminal S6 input contact opening (H/O/A = Auto) selects serial com for both the run/stop command and speed command. A terminal S6 input contact closure
(H/O/A = Hand) allows b1-01 to select Keypad/Operator as the speed command source. This input is jumpered to S5, therefore the contact is closed when
H/O/A = Hand.
H3-08 = 0: 0-10 VDC
H3-09 = B: PI Feedback
Terminal A2 is programmed for 0-10 VDC (Note – Control PCB DIP switch S1-2 must also be OFF)
Terminal A2 function is set to provide PI feedback for closed loop control
H3-13 = 1: Main Fref TA2 Terminal A2 (the feedback terminal) serves as the main input
Programming 5 - 28
The analog feedback to the Drive for the PI control is via the A2 terminal. The Drive must be programmed
(H3-09= “B: PI Feedback”) to use terminal A2 as feedback for the PI functionality of the Drive.
The PI setpoint can be configured to come from one of many different inputs or parameters. The table below describes the options for originating the PI setpoint.
06H
D1-01
Table 5.5 PI Setpoint Options
The PI Setpoint will be read from:
Parameter b5-19
Modbus Register
Terminal A1
Serial Com.
Option PCB
If these conditions are true
Status of b5-18
Status of
Modbus
Register
0Fh bit 1
Status of b1-01
= 1
= 0
= 0
= 0
= 0
= 0
N/A
ON
OFF
OFF
OFF
OFF
N/A
N/A
= 0
= 1
= 2
= 3
In some situations there are two feedback inputs. The Drive can be programmed to maintain a set differential between two analog signals. If input A2 is configured as a “PI Differential Mode” (H3-09= “16: PI Differential”), then the Drive will maintain a set difference between the measurements read on inputs A1 and A2. This differential setpoint is programmed by parameter (b5-07).
"
b5-01 PI Mode
Setting
0
1
3
Description
Disabled (factory default)
Enabled
Fref+PI
The Drive can be used as a stand-alone PI controller. If PI functionality is selected by parameter b5-01, the Drive will adjust its output to cause the feedback from a transmitter to match the PI setpoint (b5-19). The setting of b5-01 will determine whether
PI functionality is disabled (b5-01= “0: Disabled”), enabled (b5-01= “1: Enabled”), or enable with the output of the
PI function used to trim a Speed Command (b5-01= “3: Fref+PI”).
"
b5-02 Proportional Gain Setting
Setting Range: 0.00 to 25.00
Factory Default: 2.00
The proportional gain will apply a straight multiplier to the calculated difference (error) between the PI Setpoint and the measured transmitter feedback at terminal A2. A large value will tend to reduce the error but may cause instability
(oscillations) if too high. A small value may allow to much offset between the setpoint and feedback (See Figure 5.14 on following page).
"
b5-03 Integral Time Setting
Setting Range: 0.0 to 360.0 Seconds
Factory Default: 5.0 Seconds
Programming 5 - 29
The Integral factor of PI functionality is a time-based gain that can be used to eliminate the error (difference between the setpoint and feedback at steady state). The smaller the Integral Time set into b5-03, the more aggressive the Integral factor will be. To turn off the Integral Time, set b5-03= 0.00.
Setpoint
Offset
Setpoint
Zero offset with
Integral Action
Feedback Feedback
No Integral
TIME
With Integral
Fig 5.16 PID Feedback Response Characteristics
TIME
"
b5-04 Integral Limit Setting
Setting Range: 0.0 to 100.0%
Factory Default: 100.0%
On some applications, especially those with rapidly varying loads, the output of the PI function may have large oscillations. To suppress these oscillations, a limit can be applied to the integral factor by programming b5-04.
"
b5-06 PI Output Limit
Setting Range: 0.0 to 100.0%
Factory Default: 100.0%
Places a cap on the output of the PI function. Limiting the PI function may help to prevent large overshoots in the Drive’s response to error (the difference between the setpoint and the feedback).
"
b5-07 PI Offset Adjustment
Setting Range: -100.0% to +100.0%
Factory Default: 0.0%
The PI Offset Adjustment parameter has two different uses. Parameter b5-07 serves different functions depending on whether it is used on a standard PI loop or a Differential PI loop.
Parameter b5-07 causes an offset to be applied to the output of the PI function in a non-differential PI loop. Every time the PI output is updated, the offset (b5-07) is summed with the PI output. This can be used to artificially kick-start a slow starting PI loop.
If the Drive is configured for Differential PI Regulation (H3-09= “16: PI Differential”), then this parameter is the target setpoint for the differential to be maintained between the signal measured on analog input A1 and the signal measured on analog input A2.
Programming 5 - 30
"
b5-08 PI Primary Delay Time Constant
Setting Range: 0.00 to 10.00 Seconds
Factory Default: 0.00 Seconds
Acts as a time based filter that lowers the responsiveness of the PI function, but also makes the function more stable when the setpoint varies rapidly or when the feedback is noisy.
"
b5-09 PI Output Level Selection
Setting
0
1
Description
Normal Output (direct acting) (factory default)
Reverse Output (reverse acting)
Normally, the output of the PI function causes an increase in motor speed whenever the measured feedback is below the setpoint. This is referred to as direct acting response. However, if b5-09= “1: Reverse Output”, the output of the PI function causes the motor to slow down when the feedback is below the setpoint. This is referred to as reverse acting response.
"
b5-10 PI Output Gain Setting
Setting Range: 0.0 to 25.0
Factory Default: 1.0
Applies a multiplier to the output of the PI function. Using the gain can be helpful when the PI function is used to trim the
Speed Command. Increasing b5-10 causes the PI function to have a greater regulating affect on the speed command.
"
b5-11 PI Reverse Selection
Setting
0
1
Description
0 Limit (factory default)
Reverse
Parameter b5-11 determines whether reverse operation is allowed while using PI control (b5-01
≠
0). The factory default setting will not allow the Drive to run in reverse. This parameter does not need to be changed from factory default for a majority of
HVAC applications. (Refer also to b5-09).
"
b5-12 PI Feedback Reference Missing Detection Selection
Setting
0
1
2
Description
Disabled (factory default)
Alarm
Fault
Loss of feedback can cause problems to a PI application. The Drive can be programmed to turn on a digital output whenever a loss of feedback occurs. Feedback Loss Detection is turned on by b5-12. When b5-12= “1: Alarm”, the Drive acknowledges the loss of feedback without stopping or turning on the fault output (MA-MB). If b5-12= “2: Fault”, the Drive coasts to a stop and turns on the fault output if the feedback is determined to be lost.
Programming 5 - 31
"
b5-13 PI Feedback Loss Detection Level
Setting Range: 0 to 100%
Factory Default: 0%
"
b5-14 PI Feedback Loss Detection Time
Setting Range: 0.0 to 25.0 Seconds
Factory Default: 1.0 Seconds
The Drive interprets feedback loss whenever the feedback signal drops below the value of b5-13 and stays below that level for at least the time set into b5-14. See Figure 5.15 below for timing details.
Measured
Feedback b5-13
T T
TIME
T = b5-14
ON (CLOSED) t OFF (OPEN)
Fig 5.17 Loss of PI Feedback Feature
"
b5-15 Sleep Function Start Level
Setting Range: 0.0 to 200.0 Hz
Factory Default: 0.0 Hz
"
b5-16 Sleep Delay Time
Setting Range: 0.0 to 25.5 Seconds
Factory Default: 0.0 Seconds
The Sleep Function can be programmed to prevent running the Drive when the PI loop output or the speed command is so low that no usable work is being done and/or equipment damage may result. The Sleep Function can be Enabled by entering a value in parameter b5-15. If the Drive’s output drops below the level set by the Sleep Function Start Level (b5-15) and remains there at least as long as the delay time determined by the Sleep Delay Time (b5-16), then the Drive’s internal Run command drops out and the Drive output ceases. Though the Drive’s output has ceased, all other Drive functions continue. Once the Drive’s theoretical output returns to a level above the Sleep Function Start Level (b5-15) and remains above that level for at least the
Sleep Delay Time (b5-16), the internal Run command returns and the Drive output begins again. The b5-16 Delay Time prevents oscillation about the sleep level. Note: The sleep function can be used even if the P1 function is disabled
(b5-01 = “0: Disabled”).
t
Upper Limit d2-01
Sleep Level b5-15
Fig 5.18 Sleep Function Response
Programming 5 - 32
"
b5-17 PI Accel/Decel Time
Setting Range: 0.0 to 25.5 Seconds
Factory Default: 0.0 Seconds
This is a soft start function that is applied to the PI setpoint analog input. Instead of having nearly instantaneous changes in signal levels, there is a programmed ramp applied to level changes. When changing setpoints the error can be limited by gradually ramping the setpoint through the use of parameter b5-17.
"
b5-18 PI Setpoint Selection
Setting
0
1
Description
Disabled (factory default)
Enabled
In order to use parameter b5-19 as the PI Setpoint, set parameter b5-18= “1: Enabled”. If b5-18= “0: Disabled” the PI Setpoint will either be:
• Modbus Register 06H (If Register 0FH bit 1 is high)
• The active speed command (i.e. Determined by the setting of b1-01). See Table 1 “Setpoint Options”
"
b5-19 PI Setpoint Value
Setting Range: 0.00 to 100.00%
Factory Default: 0.00%
Parameter b5-19 is for a PI Setpoint value. When b5-18= “1: Enabled”, the value of b5-19 will take precedent over any other PI setpoint unless the Drive is set up for Differential Feedback, in which case, b5-18 and b5-19 have no affect on the PI function.
"
b5-20 PI Setpoint Display Scaling
Setting
0
1
3
3
Hz (factory default)
%
RPM (Synchronous)
Engineering Units
Description
The PI Setpoint Display Scaling value (b5-20) is a scaling factor that is applied to the monitor display for both the PI Setpoint
(U1-38) and the PI Feedback (U1-24).
Table 5.6 PI Setpoint Display Scaling Options
If b5-20 is:
0
1
2 through 39
(enter the # of motor poles)
40 through 39999
U1-24 and U1-38
Display Increments.
0.01 Hz
0.00%
0 RPM
Engineering Units
Programming 5 - 33
If the monitors seem more natural in terms of percentage, set b5-20= 1. If the monitors are easier to work with when displaying the equivalent synchronous RPM, set b5-20= [the number of motor poles].
If another engineered unit, such a fpm or cfm, is desired, set b5-20= xxxxx where
X X X X X
Digit 5 Digit 4 Digit 3 Digit 2 Digit 1
Digits 1 through 4 set the desired number to be displayed at 100% speed.
Digit 5 determines the number of decimal places
If Digit 5 = 0 number format is XXXX
If Digit 5 = 1 number format is XXX.X
If Digit 5 = 2 number format is XX.XX
If Digit 5 = 3 number format is X.XXX
For example:
If b5-20= 10425 then at 100% output the digital operator would display 42.5 for monitor U1-38 or U1-24.
"
b5-21 Sleep Source
Setting
0
1
2
Description
SFS Input (Output of PI block)
PI Setpoint (factory default)
Snooze
Parameter b5-21 selects the sleep function characteristic action:
When b5-21= “0: SFS Input” the sleep function start level (b5-15) is compared to the Drive’s output (Speed Command after PI block). This is the setting that should be used for open loop or closed loop control.
It is also possible to have the sleep function start level (b5-15) compared to the Drive input or setpoint. For this special application set b5-21= “1: PI Setpoint”.
When b5-21= “2: Snooze” a variation of the sleep function called “Snooze” is enabled, see parameter b5-22 to b5-27.
IMPORTANT
The sleep function can be used even if the PI function is disabled (b5-01= ”0: Disabled”).
Programming 5 - 34
"
b5-22 PI Snooze Level
Setting Range: 0 to 100%
Factory Default: 0%
"
b5-23 PI Snooze Delay Time
Setting Range: 0 to 3600 Seconds
Factory Default: 0 Seconds
"
b5-24 PI Snooze Deactivation Level
Setting Range: 0 to 100%
Factory Default: 0%
The Snooze Function is a variation on the Sleep Function. The Snooze function must be selected by setting parameter b5-21= “2: Snooze”. Once the Snooze Function is selected, the Drive monitors the output frequency. If the output frequency drops below the PI Snooze Level (b5-22), and stays below that level for at least the PI Snooze Delay Time (b5-23), the Drive output shuts off. This is different from the Sleep Function because it is the feedback that must drop below the PI Snooze
Deactivation Level (b5-24) before normal Drive output will begin again. See Figure 5.19 on the following page.
"
b5-25 PI Setpoint Boost Setting
Setting Range: 0 to 100%
Factory Default: 0%
Just before the Snooze Function is activated, the PI Setpoint can be temporarily increased to create an overshoot of the intended PI Setpoint. The temporary boost is determined by the PI Setpoint Boost Setting (b5-25). Once the temporary boost level is reached (or the PI Maximum Boost Time (b5-26) is exceeded), the Drive output shuts off (snoozes) and the intended PI
Setpoint returns. From this point on, the Snooze Function operates normally and the Drive output returns when the feedback level drops below b5-24. See Figure 5.19 on the following page.
Programming 5 - 35
"
b5-26 PI Maximum Boost Time
Setting Range: 0 to 3600 Seconds
Factory Default: 0 Seconds
Associated with the Snooze Function. In cases where the temporary PI Setpoint (intended PI setpoint + PI Setpoint Boost) cannot be reached within the PI Maximum Boost Time (b5-26), the Setpoint Boost is interrupted and the Drive output is turned off.
b5-26
PI Output
PI Output
PI Setpoint
PI Setpoint
PI Feedback
PI Feedback b5-23 b5-22 b5-24 t
t
t b5-23
Snooze
Function
OFF
ON
OFF
TIME
Either PI
Feedback boosted setpoint value reaches the new or the maximum boost boosted setpoint time b5-26 is reached. value or the maximum boost time is reached .
Fig 5.19 Snooze Function Operation
"
b5-27 PI Snooze Feedback Level
Setting Range: 0 to 100%
Factory Default: 60%
This is a second method of initiating the Snooze Function. If the PI feedback level exceeds the PI Snooze Feedback Level
(b5-27), then the Drive output shuts off. Once the PI feedback drops below the PI Snooze Deactivation Level (b5-24) then normal Drive and PI operation return.
"
b5-28 PI Feedback Square Root Function Activation
Setting
0
1
Description
Disabled (factory default)
Enabled
If b5-28= “1: Enabled”, the square root of the PI feedback is compared to the PI Setpoint in order to determine appropriate
Drive output to properly regulate the system. This is helpful in cases where the measured feedback is pressure but the PI loop needs to regulate flow.
Programming 5 - 36
"
b5-29 PI Square Root Gain
Setting Range: 0.00 to 2.00
Factory Default: 1.00
A multiplier applied to the square root of the feedback.
"
b5-30 PI Output Square Root Monitor Selection
Setting
0
1
Description
Disabled (factory default)
Enabled
If the PI Function is regulating the flow of a closed loop system by using a pressure feedback, it may be convenient to view the square root of the PI output using monitor U1-37.
!
b8 Energy Savings
The energy savings function improves overall system operating efficiency by operating the motor at its highest efficiency. This
is accomplished by continuously monitoring the motor load and adjusting the motor terminal voltage so that the motor always operates near its rated slip frequency. A motor is most efficient when operating near rated slip conditions.
"
b8-01 Energy Savings Selection
Setting
0
1
Description
Disabled (factory default)
Enabled
When the Energy Savings function is enabled (b8-01= “1: Enabled”), the Drive reduces the output voltage to the motor below
the voltage value specified by the programmed V/f pattern whenever the motor load is light. Since torque is reduced during this voltage reduction, the voltage has to return to normal levels when the load returns. The energy savings is realized through improved motor efficiency. The reduced output voltage causes increased rotor slipping even with a light load. A motor is most efficient when operating fully loaded (i.e. operating at rated slip).
"
b8-04 Energy Saving Coefficient Value
Setting Range: 0.0 to 655.0
Factory Default: Model Dependent
Parameter b8-04 is used in maximizing motor efficiency. The factory setting will be Drive capacity dependent but can be adjusted in small amounts while viewing the kW monitor (U1-08) and running the Drive to minimize the output kW. A larger value typically results in less voltage to the motor and less energy consumption. Too large a value will cause the motor to stall.
Programming 5 - 37
!
C1 Accel/Decel
"
C1-01 Acceleration Time 1
C1-02 Deceleration Time 1
C1-03 Acceleration Time 2
C1-04 Deceleration Time 2
Setting Range: 0.0 to 6000.0 Seconds
Factory Default: 30.0 Seconds
C1-01 (Acceleration Time 1) sets the time to accelerate from zero to maximum speed (E1-04). C1-02 (Deceleration Time 1) sets the time to decelerate from maximum speed to zero. C1-01 and C1-02 are the factory default active accel/decel “pair”. Another accel/decel pair (C1-03 and C1-04) exists that can be activated by a multi-function digital input (H1-0x= 7), or specified by a switch over frequency as programmed in parameter C1-11.
Note: In fan applications employing duct high pressure safety limit switches, it may be necessary to further adjust the deceleration time to avoid high pressure limit trips due to damper closure as the system is shut down (an alternate solution in this situation is to set parameter b1-03 to “Coast to Stop”).
"
C1-09 Fast Stop Time
Setting Range: 0.0 to 6000.0 Seconds
Factory Default: 10.0 Seconds
A special deceleration parameter is available for use with emergency or fault operations. Parameter C1-09 will set a special deceleration that can be operated by closing a digital input configured as H1-0x= 15 or H1-0x= 17. A digital input configured as H1-0x= 15 will look for a switch closure before initiating the Fast Stop operation. A digital input configured as
H1-0x= 17 will look for the switch opening before initiating the Fast Stop operation.
Unlike a standard deceleration time, once the Fast Stop operation is initiated even momentarily, the Drive cannot be re-operated until the deceleration is complete, the Fast Stop input is cleared, and the Run command is cycled.
Programming 5 - 38
!
d1 Preset References
"
d1-01 Frequency Reference 1 d1-02 Frequency Reference 2 d1-03 Frequency Reference 3 d1-04 Frequency Reference 4
Setting Range: 0.00 to E1-04 Value
Factory Default: d1-01 = 10.00 Hz d1-02 = 6.00 Hz d1-03 = 0.00 Hz d1-04 = 40.00 Hz d1-01, d1-02 and d1-04 are special parameter settings required by the Bypass logic circuit. See Table 5.1.
d1-04 d1-03
Output
Speed d1-02 d1-01 d1-17 t
Closed
Open
RUN
Multi-step
Reference 1 Input
Multi-step
Reference 2 Input
Jog Input
Fig 5.20 Preset Reference Timing Diagram example
"
d1-17 Jog Frequency Reference
Setting Range: 0.00 to E1-04 Value
Factory Default: 6.00 Hz
Closed
Open
Closed
Open
Closed
Open
The Drive can be programmed to utilize digital inputs to change between four presets speeds and a jog speed. It is a two-step process to set the Drive up for preset speeds. First, d1-01 through d1-04 and d1-17 must be programmed with the desired preset speeds and the desired jog speed, respectively. Next, up to three of the Drive’s digital inputs (Terminals S3 through S7) need to be programmed (via parameters H1-01 to H1-05) and wired (to normally open contacts) as Multi-step Speed Reference 1, Multi-step
Speed Reference 2, and Jog Frequency.
Table 5.7 Preset Speed Truth Table
Preset Speed
Terminal
programmed as Multi-step
Reference 1
OFF
Terminal programmed as Multi-step
Reference 2
OFF 1
2
3
ON
OFF
OFF
ON
4 ON ON
5 -
*
The Jog Frequency input is given priority over the multi-step speeds.
Terminal programmed as Jog
Reference
OFF
OFF
OFF
OFF
ON*
Details
Frequency Reference 1 (d1-01) or analog input A1
Frequency Reference 2 (d1-02) or analog input A2
Frequency Reference 3 (d1-03)
Frequency Reference 4 (d1-04)
Jog Frequency (d1-17)
Programming 5 - 39
As shown in Table 5.6, it is possible to use analog inputs in place of Frequency Reference 1 and Frequency
Reference 2.
#
If b1-01= “1: Terminals” then the analog input A1 will be used instead of Frequency Reference 1 for the first preset speed.
If b1-01= “0: Operator”, then Frequency Reference 1 will be used.
#
If H3-09= “2: Aux Reference” then the analog input A2 will be used instead of Frequency Reference 2 for the second preset speed. If H3-09
≠
2 then Frequency Reference 2 will be used.
IMPORTANT
The programming of d1-01 through d1-04 and d1-17 will be affected by the setting of o1-03. The programming of these parameters will be in the units specified by Display Scaling parameter (o1-03).
Programming 5 - 40
!
d2 Reference (Speed Command) Limits
"
d2-01 Frequency Reference Upper Limit
Setting Range: 0.0 to 110.0%
Factory Default: 100.0%
"
d2-02 Frequency Reference Lower Limit
Setting Range: 0.0 to 110.0%
Factory Default: 0.0%
The use of parameters d2-01 and d2-02 places limitations on the speed command that the Drive will accept. The parameters are set in units of percentage of the maximum frequency (E1-04) and provide limits on any remote speed command input. By entering upper or lower frequency limits, the Drive programmer can prevent operation of the Drive above or below levels that may cause resonance, equipment damage or discomfort (see also parameter d3-0X). For example, limits may be needed to prevent low speed operation of: cooling tower fans with gear boxes, pumps with pressure dependent seals or AHUs with minimum delivery requirements.
Internal Speed Command d2-01 d2-01
Operating
Range
Frequency Reference Upper Limit
Frequency Reference Lower Limit
Set Speed Command
Note: See also the “Sleep” function in Figure 5.19 for alternate “lower limit” implementation.
Fig 5.21 Frequency Reference Upper and Lower Limit Effects on the Speed Command
Programming 5 - 41
!
d3 Jump Frequencies
"
d3-01 Jump Frequency 1 d3-02 Jump Frequency 2 d3-03 Jump Frequency 3
Setting Range: 0.0 to 200.0 Hz
Factory Default: 0.0 Hz
"
d3-04 Jump Frequency Width
Setting Range: 0.0 to 20.0 Hz
Factory Default: 1.0 Hz
In order to avoid continuous operation at a speed that causes resonance in driven machinery, the Drive can be programmed with jump frequencies that will not allow continued operation within specific frequency ranges. If a speed is commanded that falls within a dead band, or Jump Frequency, the Drive will clamp the frequency reference just below the dead band and only accelerate past it when the commanded speed rises above the upper end of the dead band, for increasing references. Similarly, the Drive will clamp the frequency reference just above the dead band and only decelerate past it when the command speed falls below the lower end of the dead band, for decreasing references.
d3-03 d3-03 d3-02 d3-04 d3-01 d3-04
User Frequency
Reference
Fig 5.22 Jump Frequency Characteristics d3-04
Setting the center point of the dead band with the d3-01 through d3-03 parameters and setting the width of the dead band with parameter d3-04 determines the dead band characteristics. The programmer can set up to three Jump Frequencies. If multiple
Jump Frequencies are programmed the following rule applies: d3-01
< = d3-02
<
= d3-03
Programming 5 - 42
!
d4 Sequence
"
d4-01 MOP Reference Memory
Setting
0
1
Description
Disabled (factory default)
Enabled
The Drive offers the capacity to change the speed command much the way a Motor Operated Potentiometer (MOP) would.
Using programmed digital inputs configured as MOP Increase (H1-0x= 10) and MOP Decrease (H1-0x= 11), the Drive will increase the speed command whenever the MOP Increase input is closed and decrease the speed command whenever the MOP
Decrease is closed. The speed command will remain constant whenever both inputs are open or closed.
Parameter d4-01 determines whether the last speed command, before the Run command was removed, is remembered even if the power is cycled to the Drive. If d4-01= “0: Disabled”, then when a new Run command is issued the Drive’s speed command will be 0 rpm. If d4-01= “1: Enabled”, then the speed command will be the last commanded speed before the Run command was removed.
Programming 5 - 43
!
E1 V/f Pattern
"
E1-01 Input Voltage Setting
Setting Range: 155.0V to 255.0V (208V/240V Models)
310.0V to 510.0V (480V Models)
Factory Defaults: 208.0V (208V Models)
240.0V (240V Models)
480.0V (480V Models)
Set the Input Voltage parameter (E1-01) to the nominal voltage of the connected AC power supply. This parameter adjusts the levels of some protective features of the Drive (i.e. Overvoltage, Stall Prevention, etc.). E1-01 also serves as the Maximum/
Base Voltage used by the Preset V/Hz curves (E1-03= 0 to D).
"
E1-03 V/f Pattern Selection
A
B
8
9
5
6
7
Setting
0
1
2
3
4
C
D
F
FF
Description
50 Hz
60 Hz Saturation
50 Hz Saturation
72 Hz
50 Hz VT1
50 Hz VT2
60 Hz VT1
60 Hz VT2
50 Hz HST1
50 Hz HST2
60 Hz HST1
60 Hz HST2
90 Hz
120 Hz
Custom V/f (factory default, with parameter values per setting 1)
Custom w/o limit
The Drive operates utilizing a set V/f pattern to determine the appropriate output voltage level for each commanded speed.
There are 14 different preset V/f patterns to select from with varying voltage profiles, saturation levels (frequency at which maximum voltage is reached), and maximum frequencies.
There are also settings for Custom V/f patterns that will allow the programmer to manually set (“Customize”) the V/f pattern using parameters E1-04 through E1-13.
Using parameter E1-03, the programmer can select one of the preset V/f patterns or chose between a custom V/F pattern with an upper voltage limit (E1-03= “F: Custom V/F”) and a custom V/f pattern without a voltage limit (E1-03= “FF: Custom w/o limit”).
Programming 5 - 44
Specifications E1-03
50Hz
60Hz Saturation
50Hz Saturation
72Hz
0
1
F
2
3
Table 5.8 Preset V/f Patterns
V/f Pattern *1 Specifications E1-03
230
(V)
17
10
0 1.3 2.5
0
50
(Hz)
230
(V)
17
10
0 1.5 3.0
2
1
F
50 60
(Hz)
230
(V)
3
50Hz
High
Starting
Torque 1
60Hz
High
Starting
Torque 2
High
Starting
Torque 1
High
Starting
Torque 2
8
9
A
B
90Hz C
50Hz
60Hz
Variable
Torque 1
Variable
Torque 2
Variable
Torque 1
Variable
Torque 2
4
5
6
7
17
10
0 1.5 3.0
60 72
(Hz)
230
(V)
5
57
40
10
9
0 1.3
25
4
50
(Hz)
230
(V)
7
57
40
10
9
0 1.5
30
6
60
(Hz)
120Hz D
V/f Pattern *1
230
(V)
9
28
22
15
13
0 1.3 2.5
8
50
(Hz)
230
(V)
B
28
22
17
13
0 1.5 3.0
A
230
(V)
C
60
(Hz)
17
10
0 1.5 3.0
230
(V)
D
17
10
0 1.5 3.0
60 90
(Hz)
60 120
(Hz)
If one of the custom V/f patterns is selected, then parameters E1-04 through E1-13 will determine the V/F pattern.
IMPORTANT
When a factory Initialization is performed, the setting of E1-03 is unaffected but the settings of E1-04 through
E1-13 are returned to their factory default settings.
"
E1-04 Maximum Output Frequency
Setting Range: 0.0 to 120.0 Hz
Factory Default: 60.0 Hz
Programming 5 - 45
"
E1-05 Maximum Output Voltage
Setting Range: 0.0 to 255.0V (208V/240V Models)
0.0 to 510.0V (480V Models)
Factory Defaults: 208.0V (208V Models)
240.0V (240V Models)
480.0V (480V Models)
"
E1-06 Base Frequency
Setting Range: 0.0 to 200.0 Hz (settings above 120.0 Hz are currently not supported)
Factory Default: 60.0 Hz
"
E1-07 Mid Output Frequency A
Setting Range: 0.0 to 200.0 Hz (settings above 120.0 Hz are currently not supported)
Factory Default: 3.0 Hz
"
E1-08 Mid Output Voltage A
Setting Range: 0.0 to 255.0V (208V/240V Models)
0.0 to 510.0V (480V Models)
Factory Defaults: 18.0V (208V Models)
18.0V (240V Models)
18.0V (480V Models)
"
E1-09 Minimum Output Frequency
Setting Range: 0.0 to 200.0 Hz (settings above 120.0 Hz are currently not supported)
Factory Default: 1.5 Hz
"
E1-10 Mid Output Voltage
Setting Range: 0.0 to 255.0V (208V/240V Models)
0.0 to 510.0V (480V Models)
Factory Defaults: 10.8V (208V Models)
10.8V (240V Models)
10.8V (480V Models)
"
E1-11 Mid Output Frequency B
Setting Range: 0.0 to 200.0 Hz (settings above 120.0 Hz are currently not supported)
Factory Default: 0.0 Hz
"
E1-12 Mid Output Voltage B
E1-13 Base Voltage
Setting Range: 0.0 to 255.0V (208V/240V Models)
0.0 to 510.0V (480V Models)
Factory Defaults: 0.0V (208V Models)
0.0V (240V Models)
0.0V (480V Models)
Programming 5 - 46
To set up a custom V/f pattern, program the points shown in the diagram below using parameters E1-04 through E1-13. Be sure that the following condition is true:
E1-09
≤
E1-07
≤
E1-06
≤
E1-11
≤
E1-04
Max Voltage E1-05
Mid Voltage B E1-12
Base Voltage E1-13
Mid Voltage A E1-08
Min Voltage E1-10
Min
Freq
Mid
E1-11
Base
Freq
Mid
Freq B
A
E1-04
Max
Freq
Frequency
Fig 5.23 Custom V/f Pattern Programming Curve
Increasing the voltage in the V/f pattern increases the available motor torque. However, when setting a custom V/f pattern, increase the voltage gradually while monitoring the motor current, to prevent:
• Drive faults as a result of motor over-excitation
• Motor overheating or excessive vibration
Table 5.8 is for 240V class units only. For 480V class units, multiply the voltage values by 2.
Table 5.9 V/f Pattern Default Settings for Drive Capacity 0.5 to 2 HP for 240V Class
Parameter
No.
Name Unit
E1-03 V/f Pattern Selection —
E1-04
E1-05
E1-06
E1-07
E1-08
E1-09
E1-10
E1-11
Max Output Frequency
Max Output Voltage
Base Frequency
Mid Output Frequency A
Mid Output Voltage A
Min Output Frequency
Mid Output Voltage
Mid Output Frequency B
E1-12
E1-13
Mid Output Voltage B
Base Voltage
For 480V class units, the value is twice that of 240V class units.
V
V
V
Hz
V
Hz
Hz
V
Hz
V
0
50.0
240.0
50.0
2.5
17.2
1.3
10.3
0
0
0
1
60.0
240.0
60.0
3.0
17.2
1.5
10.3
0
0
0
2
60.0
240.0
50.0
3.0
17.2
1.5
10.3
0
0
0
Factory Setting
3 4
72.0
50.0
240.0
240.0
60.0
3.0
50.0
25.0
17.2
1.5
10.3
0
0
0
40.2
1.3
9.2
0
0
0
5 6 7
50.0
60.0
60.0
240.0
240.0
240.0
50.0
25.0
60.0
30.0
60.0
30.0
57.5
1.3
10.3
0
0
0
40.2
1.5
9.2
0
0
0
57.5
1.5
10.3
0
0
0
Programming 5 - 47
Table 5.9 V/f Pattern Default Settings for Drive Capacity 0.5 to 2 HP for 240V Class (Continued)
Parameter
No.
E1-03
Name
V/f Pattern Selection
Unit
— 8 9 A
Factory Setting
B C D E
E1-04 Max. Output Frequency Hz
E1-05
E1-06
E1-07
E1-08
E1-09
E1-10
E1-11
Max. Output Voltage
Base Frequency
Mid. Output Frequency A
Mid. Output Voltage A
Min. Output Frequency
Mid. Output Voltage
Mid Output Frequency B
E1-12
E1-13
Mid Output Voltage B
Base Voltage
For 480V class units, the value is twice that of 240V class units.
V
V
V
Hz
V
Hz
V
Hz
V
50.0
240.0
50.0
2.5
21.8
1.3
12.6
0
0
0
50.0
240.0
50.0
2.5
27.6
1.3
14.9
0
0
0
60.0
240.0
60.0
3.0
21.8
1.5
12.6
0
0
0
60.0
90.0
120.0
240.0
240.0
240.0
60.0
3.0
60.0
3.0
60.0
3.0
27.6
1.5
17.2
0
0
0
17.2
1.5
10.3
0
0
0
0
0
17.2
1.5
10.3
0
F
180.0
60.0
240.0
240.0
60.0
3.0
60.0
3.0
17.2
1.5
10.3
0
0
0
0
0
17.2
1.5
10.3
0
Table 5.10 V/f Pattern Default Settings for Drive Capacity 3 to 75 HP for 240V Class
Parameter
No.
Name Unit
E1-03 V/f Pattern Selection —
E1-04
E1-05
E1-06
E1-07
E1-08
E1-09
E1-10
Max. Output Frequency
Max. Output Voltage
Base Frequency
Mid. Output Frequency A
Mid. Output Voltage A
Min. Output Frequency
Mid. Output Voltage
E1-11
E1-12
Mid Output Frequency B
Mid Output Voltage B
Hz
V
E1-13 Base Voltage V
For 480V class units, the value is twice that of 240V class units.
V
V
Hz
V
Hz
V
Hz
0
50.0
240.0
50.0
2.5
16.1
1.3
8.0
0
0
0
1
60.0
240.0
60.0
3.0
16.1
1.5
8.0
0
0
0
2
60.0
240.0
50.0
3.0
16.1
1.5
8.0
0
0
0
Factory Setting
3
0
0
0
4 5
72.0
50.0
50.0
240.0
240.0
240.0
60.0
50.0
50.0
3.0
16.1
1.5
8.0
25.0
40.2
1.3
6.9
25.0
57.5
1.3
8.0
0
0
0
0
0
0
6 7
0
0
0
60.0
60.0
240.0
240.0
60.0
60.0
30.0
40.2
1.5
6.9
30.0
57.5
1.5
8.0
0
0
0
Programming 5 - 48
Table 5.10 V/f Pattern Default Settings for Drive Capacity 3 to 40 HP for 240V (Continued)
Parameter
No.
Name Unit
E1-03 V/f Pattern Selection —
E1-04 Max. Output Frequency Hz
E1-05
E1-06
E1-07
E1-08
E1-09
E1-10
E1-11
E1-12
Max. Output Voltage
Base Frequency
Mid. Output Frequency A
Mid. Output Voltage A
Min. Output Frequency
Mid. Output Voltage
Mid Output Frequency B
Mid Output Voltage B
E1-13 Base Voltage
For 480V class units, the value is twice that of 240V class units.
Hz
V
Hz
V
V
V
Hz
V
V
8
50.0
9
50.0
1.3
10.3
0
0
0
240.0
240.0
50.0
50.0
2.5
20.7
2.5
26.4
1.3
12.6
0
0
0
A
Factory Setting
B C D E F
60.0
60.0
90.0
120.0
180.0
60.0
1.5
10.3
0
0
0
240.0
240.0
240.0
240.0
240.0
240.0
60.0
60.0
60.0
60.0
60.0
60.0
3.0
20.7
3.0
26.4
3.0
16.1
3.0
16.1
3.0
16.1
3.0
16.1
1.5
14.9
0
0
0
1.5
8.0
0
0
0
1.5
8.0
0
0
0
1.5
8.0
0
0
0
0
0
1.5
8.0
0
Table 5.11 V/f Pattern Default Settings for Drive Capacity 50 to 150 HP for 230V
Parameter
No.
Name
E1-03 V/f Pattern Selection
E1-04
E1-05
E1-06
E1-07
E1-08
E1-09
E1-10
Max. Output
Frequency
Max. Output Voltage
Max. Voltage
Frequency
Mid. Output
Frequency A
Mid. Output
Voltage A
Min. Output
Frequency
Mid. Output
Voltage
E1-11
E1-12
Mid Output Frequency B
Mid Output Voltage B
E1-13 Base Voltage
For 480V class units, the value is twice that of 240V class units.
Unit
–
Hz
V
Hz
V
V
Hz
V
Hz
V
V
0
50.0
240.0
50.0
2.5 3.0
13.8
1.3 1.5
6.9
0
0
0
1
60.0
240.0
60.0
13.8
6.9
0
0
0
2
60.0
240.0
50.0
3.0
13.8
1.5
6.9
0
0
0
Factory Setting
3
72.0
240.0
60.0
3.0
13.8
1.5
6.9
0
0
0
4
50.0
240.0
50.0
25.0
40.2
1.3
5.7
0
0
0
5
50.0
240.0
50.0
57.5
6
60.0
240.0
60.0
40.2
1.3 1.5
6.9
0
0
0
5.7
0
0
0
7
60.0
240.0
60.0
30.0
57.5
1.5
6.9
0
0
0
Programming 5 - 49
Table 5.11 V/f Pattern Default Settings for Drive Capacity 100 to 150 HP for 230V (Continued)
Parameter
No.
Name Unit
E1-03 V/f Pattern Selection – 8
E1-04
E1-05
E1-06
E1-07
E1-08
E1-09
E1-10
E1-11
Max. Output
Frequency
Max. Output Voltage
Base
Frequency
Mid. Output
Frequency A
Mid. Output
Voltage A
Min. Output
Frequency
Mid. Output
Voltage
Mid Output Frequency B
Hz
V
Hz
V
V
Hz
V
Hz
50.0
240.0
50.0
2.5
17.2
1.3
8.0
0
E1-12
Mid Output Voltage
B
V 0
E1-13 Base Voltage V
For 480V class units, the value is twice that of 240V class units.
0
9
50.0
240.0
50.0
2.5
23.0
1.3
10.3
0
0
0
A
60.0
240.0
60.0
3.0
17.2
1.5
8.0
0
0
0
Factory Setting
B
60.0
240.0
60.0
3.0
23.0
1.5
12.6
0
0
0
C
90.0
240.0
60.0
3.0
13.8
1.5
6.9
0
0
0
D
120.0
240.0
60.0
3.0
13.8
1.5
6.9
0
0
0
E
180.0
240.0
60.0
3.0
13.8
1.5
6.9
0
0
0
0
0
0
1.5
6.9
F
60.0
240.0
60.0
3.0
13.8
!
E2 Motor Setup
"
E2-01 Motor Rated Current
Setting Range: Model Dependent (see appendix B)
Factory Default: Model Dependent
The Motor Rated Current parameter (E2-01) is necessary information for the Drive motor protection function. The motor overload protection parameter L1-01 is enabled by default. In addition, motor rated current is used by the torque compensation function to insure optimum torque production. Set E2-01 to the full load amps (FLA) value stamped on the motor’s nameplate. During Auto-tuning, it is required for the operator to enter the motor rated current in parameter T1-04 on the
Auto-Tuning menu. If the Auto-tuning operation completes successfully, the value entered into T1-04 will be also written into
E2-01.
For applications employing a Drive that is oversized for the motor, E2-01 may be set as low as 10% of the Drive output current rating. The ampere value in E2-01 however, must always be greater than the “No Load Current” value in parameter E2-03 or an OPE02 error will be displayed.
Programming 5 - 50
"
E2-03 No Load Current
Setting Range: Model Dependent (see appendix B)
Factory Default: Model Dependent
Set E2-03 to the motor no-load current at rated voltage and rated frequency. Consult the motor manufacturer for the proper value if the no load current is not stated on the motor nameplate.
!
F6 Com OPT Setup
(Applies only to the LonWorks
®
option)
"
F6-01 Operation Selection After Communication Error
Setting
0
1
2
3
Description
Ramp to Stop
Coast to Stop
Fast-Stop
Alarm Only (factory default)
If a serial communication option board is attached to the Drive at the 2CN connector, the Drive will automatically monitor the card for any type of communication errors. F6-01 is applicable no matter whether a run command or speed command is coming via the option board, digital operator, or terminal input. The setting of F6-01 determines whether the communication error is seen as a fault or an alarm. If F6-01= “3: Alarm Only”, then the fault output is not energized upon a communication error. All other settings of F6-01 cause the fault output to energize. The setting of F6-01 does not apply to any of the embedded communication protocols used at the RS-485/422 terminals on the removable terminal board. (See parameters H5-0X)
"
F6-02 Option PCB External Fault Detection Selection
Setting
0
1
Description
Always Detected (factory default)
Detected only during operation
"
F6-03 Option PCB External Fault Stopping Method
Setting
0
1
2
3
Description
Ramp to Stop
Coast to Stop (factory default)
Fast-Stop
Alarm Only
If an external fault is received from the LonWorks
® or other communication option card, the settings of F6-02 and F6-03 will determine the Drive operation in reaction to the fault signal. Parameter F6-02 will determine if the external fault is always recognized (F6-02= “0: Always Detected”) or only recognized when the Run command is active (F6-02= “1: Detected only during operation”).
Once the fault is recognized, parameter F6-03 will determine the operation of the Drive. If parameter F6-03 is set to anything other then “3”, the Drive will fault and a stopping sequence is begun. If F6-03= “3: Alarm Only”, then the external fault is treated like an alarm. Operation will continue and an EF0 fault will flash on the digital operator.
Programming 5 - 51
"
F6-05 Current Scaling via Communication Option PCB
Setting
0
1
Description
A Display (factory default)
100%/8192 (Drive Rated Current)
A communication option card can read the Drive’s DPRAM to access the current monitor. The format of the current reading in the DPRAM will be determined by parameter F6-05.
F6-05= “0: A Display” $ Current is a decimal number corresponding to actual Amperes
F6-05= “1: 100%/8192 (Drive Rated Current)” $ Current reading is a number where
8192 = 100% of Drive rated output current
!
H1 Digital Inputs
"
H1-01 Terminal S3 Function Selection
H1-02 Terminal S4 Function Selection
H1-03 Terminal S5 Function Selection
H1-04 Terminal S6 Function Selection
H1-05 Terminal S7 Function Selection
Setting Range: 0 to 6E
Factory Default: H1-01= “70: Bypass Drv Envl” This is one of the special parameter settings required by the Bypass logic circuit. See Table 5.1.
H1-02= This is one of the special parameter settings required by the Bypass logic circuit. See Table 5.2
H1-03= This is one of the special parameter settings required by the Bypass logic circuit. See Table 5.2.
H1-04= “4: Multi-Step Ref 2” (2 Wire)
“3: Multi-Step Ref 1” (3 Wire)
H1-05= “6: Jog Freq Ref ” (2 Wire)
“4: Multi-Step Ref 2” (3 Wire)
Programming 5 - 52
The Drive has five multi-function contact digital inputs. By programming parameters H1-01 through H1-05, the user can assign specific functions to each input. Below is a table with a complete list of all of the digital input functions. The programming manual has a more detailed description of each of the functions.
13
14
15
17
F
10
11
12
18
19
1B
Parameter setting
0
1
4
6
2
3
9
A
C
7
8
Function
3-Wire Control
Local/Remote Selection
Option/Inv Selection 1
Multi-step Reference 1
Multi-step Reference 2
Jog Frequency Reference 1
Multi-Accel/Decel 1
External Baseblock N.O.
External Baseblock N.C.
Accel/Decel Ramp Hold
Terminal A2 Enable
Terminal Not Used
MOP Increase
MOP Decrease
Forward Jog
Reverse Jog
Fault Reset
Fast Stop N.O.
Fast Stop N.C.
Timer Function
PI Disable
Program Lockout
Table 5.12 Digital Input Functions
69
6A
6B
6C
62
64
67
68
6D
6E
70
Parameter setting
1C
1D
1E
20-2F
30
31
34
35
36
60
61
Function
Trim Control Increase
Trim Control Decrease
Reference Sample Hold
External Fault
Integral Reset
Integral Hold
PI Soft Start Cancel
PI Input Characteristic
Option/Inv Selection 2
Motor Pre-heat
Speed Search 1
Speed Search 2
Speed Search 3
Communications Test Mode
High Slip Braking
Jog Frequency Reference 2
Drive Enable (Cycle Run)
Com/Inv Selection
Com/Inv SEL 2
Auto Mode @ Close
Hand Mode @ Close
Drive Enable (Accept Run)
Following are descriptions of only those parameters that are required for Bypass operations and PI control.
"
Function: Multi-step Ref 1
Setting: 3
"
Function: Multi-step Ref 2
Setting: 4
The Drive can be programmed to step through four preset speeds and a jog. It is also possible to mix in the analog inputs as speed references that can be chosen in place of the first and second preset frequency references. The selection of which preset speed will be the active speed command is determined by the status of the digital inputs set for Multi-step Ref 1 (H1-0x= 3) and
Multi-step Ref 2 (H1-0x= 4). Changing the active speed command via the Multi-step References can be done while the Drive is running.
Programming 5 - 53
The following table details which reference is active based on the status of the Multi-step Ref 1 and Multi-step Ref 2 inputs:
Table 5.13 Digital Input Functions
Preset Speed
1
2
3
4
5
Terminal
Programmed as Multi-step
Reference 1
OFF
ON
OFF
ON
-
Terminal
Programmed as Multi-step
Reference 2
OFF
OFF
ON
ON
-
*
The Jog Frequency input is given priority over the multi-step speeds.
Terminal
Programmed as
Jog Reference
OFF
OFF
OFF
OFF
ON*
Details
Frequency Reference 1 (d1-01) or analog input A1
Frequency Reference 2 (d1-02) or analog input A2
Frequency Reference 3 (d1-03)
Frequency Reference 4 (d1-04)
Jog Frequency (d1-17)
The determination of whether the Preset Speed 1 will be the Frequency Reference 1 (d1-01 or the analog input A1) is determined by the status of b1-01. If b1-01= “1: Terminals”, the value of the input to A1 will determine the commanded speed when Preset Speed 1 is selected. If b1-01
≠
1, the setting of d1-01 will determine the commanded speed when Preset Speed 1 is selected.
The determination of Preset Speed 2 is made much the same way as Preset Speed 1 except that the setting of parameter H3-09 decides whether the analog input A2 or d1-02 is Preset Speed 2. If H3-09= “2: Aux Reference”, the value of the input to A2 will determine the commanded speed when Preset Speed 2 is selected. If H3-09
≠
2, the setting of d1-02 will determine the commanded speed when Preset Speed 2 is selected.
"
Function: Fault Reset
Setting: 14
Whenever the Drive detects a fault condition, the fault output contact will close and the Drive’s output will shut OFF causing the motor to coast (specific stopping methods can be selected for some faults such as L1-04 for motor overheat). Once the Run command is removed, the fault can be reset by either the RESET key on the digital operator or by closing a digital input configured as a Fault Reset (H1-0x= 14).
"
Function: PI Disable
Setting: 19
When the PI Function has been enabled by b5-01 (PI Mode Selection), it can be indefinitely disabled by closing a digital input configured as a PI Disable input (H1-0x= 19). When disabled, the Drive operates as a standard Drive that does not have PI enabled.
"
Function: Com/Inv Sel 2
Setting: 6C
The Com/Inv Selection function allows the user to switch the origin of the Run and speed command between the Drive’s terminals and the RS-485/422 port (and the embedded communication protocols) on the removable terminal board. When a digital input is programmed for the Com/Inv Selection function (H1-0x= 6B) that input will function as follows:
Programming 5 - 54
Option/Inv Function Input Status
OPEN
CLOSED
Table 5.14
Run and Speed Command Source
From the control circuit and analog input terminals
From Serial Com port (R+,R-,S+, and S-) (embedded protocols)
To switch the command source between the serial communication port and the control circuit terminals be sure to program the following parameters:
• Set b1-01 (Frequency Reference Selection) to 1 (Terminals).
• Set b1-02 (Run Command Selection) to 1 (Terminals).
• Set H1-0x (Input Terminal Function Selection) to 6B or 6C.
The Com/Inv Sel 2 function will operate the same way except the logic is reversed. When a digital input is programmed for the
Com/Inv Selection function (H1-0x= 6C) that input will function as follows:
Option/Inv Function Input Status
OPEN
CLOSED
Table 5.15
Run and Speed Command Source
From Serial Com port (R+, R-, S+, and S-) (embedded protocols)
From the control circuit and analog input terminals
IMPORTANT
Switching the Reference and Run sources can only be done while the Drive is stopped.
"
Function: Auto Mode Sel
Setting: 6D
"
Function: Hand Mode Sel
Setting: 6E
This effects the speed command (reference) input only. The Auto Mode Selection (H1-0x= 6D) and the Hand Mode Selection
(H1-0x= 6E) allows use of a digital input to toggle between the Auto and Hand operational modes for speed control. The Auto
Mode Selection and Hand Mode Selection cannot both be programmed simultaneously. If both 6D and 6E are programmed together, an OPE03 fault will occur.
The 6D setting for digital input defines the speed command (or setpoint) source as the keypad/operator for an open contact and allows b1-01 to determine the speed command source for a closed contact. Setting 6D has no effect on the run command.
Input Contact Status
OPEN
CLOSED
Speed Command or PI Setpoint Source
Keypad/operator (override b1-01)
Determined by b1-01
Programming 5 - 55
The 6E setting for digital input defines the speed command (or setpoint) source as the keypad/operator for an closed contact and allows b1-01 to determine the speed command source for a open contact.
Input Contact Status
OPEN
CLOSED
Speed Command or PI Setpoint Source
Determined by b1-01
Keypad/operator (overrides b1-01)
Programming 5 - 56
!
H2 Digital Outputs
"
H2-01 Terminal M1-M2 Function Selection
H2-02 Terminal M3-M4 Function Selection
Setting Range: 0 to 3B
Factory Default: H2-01= “0: During Run 1”
H2-02= “3B: Run Src Com/Opt”
H2-02 is one of the special parameter settings required by the Bypass logic circuit. See Table 5.1.
The Drive has two multi-function outputs. By programming parameters H2-01 and H2-02, the user can assign specific functions to each output. Below is a table with a complete list of all of the digital output functions. Refer to the Programming
Manual for a more detailed description of each of the functions.
Parameter setting
0
1
2
3
9
A
B
7
8
C
E
4
5
6
Table 5.16 Digital Output Functions
Function
During Run1
Zero Speed
F
REF
/F
OUT
Agree 1
F
REF
/Set Agree 1
Frequency Detect 1
Frequency Detect 2
Drive Ready
DC Bus Undervoltage
Baseblock 1
Option Reference
Remote Operation
Torque Detect 1 N.O.
Loss of Reference
Fault
Parameter
Setting
F
10
11
12
1F
20
38
39
3A
3B
17
1A
1E
Function
Terminal Not Used
Minor Fault
Reset Cmd Active
Timer Output
Torque Detect 1 N.C.
Reverse Direction
Restart Enabled
Overload (OL1)
OH Pre-alarm
Drive Enable
Drive Waiting
Frequency Reduced, OH
Run from Serial Com
Programming 5 - 57
!
H3 Analog Inputs
"
H3-02 Terminal A1 Gain Setting
Setting Range: 0.0 to 1000.0%
Factory Default: 100.0%
H3-02 is one of the special parameter settings required by the Bypass logic circuit, depending on the options provided. See
Table 5.2.
The addition of another input signal on terminal A1 to the Drive and Bypass unit, after shipment to the job site, would be the only reason for changing this parameter.
For example, in variable air volume AHUs with a “volume matching” control strategy, P1 differential control is employed with feedback signals connected to both terminals A1 and A2.
"
H3-03 Terminal A1 Bias Setting
Setting Range: -100.0% to +100.0%
Factory Default: 0.0%
In order to have the Drive properly interpret an analog input, it may be necessary to apply a gain and/or a bias to the signal.
The analog inputs have a resolution of 10 bits (1024 steps). Using the factory default settings for the analog input’s gain and bias, the 0-10Vdc or 4-20mA signal at the analog input will yield a 0-100% speed command span.
Gain = 100%
Bias = 0%
0V
4mA
10V
20mA
Fig 5.24 Output Frequency as Commanded Via Analog Input
If a different span of analog input signal is desirable, it will be necessary to adjust the gain, the bias, or both to allow the analog input level to generate the desired frequency command. Adjustment of the gain setting will change the speed command that is equivalent to the maximum analog input (10Vdc or 20mA). If, for instance, the gain is increased to 200%, then 10Vdc or
20mA will be equivalent to a 200% speed command and 5 VAC or 12mA will be equivalent to a 100% Speed Command.
Since the Drive output is limited by the maximum frequency parameter (E1-04), 0-5Vdc or 4-12mA will now be equivalent to
0-100% speed command span.
Programming 5 - 58
Gain =200%
100%
Bias = 0%
0V
4mA
5V
12mA
10V
20mA
Fig 5.25 Output Frequency as Commanded via Analog Input with Increased Gain Setting
Adjustment of the bias setting will likewise adjust the speed command that is equivalent to the minimum analog input level
(0Vdc or 4mA). If, for instance, the bias is set to –25%, then 0Vdc or 4mA will be equivalent to a –25% speed command.
Since the minimum speed command is 0% an analog input of 2.5 to10Vdc or 8 to 20mA will now be equivalent to 0-100% speed command span.
Gain = 100%
0V
4mA
Bias = -25%
2.5V
8mA
10V
20mA
Fig 5.26 Output Frequency with Reduced Bias Setting
As a further example, for an inverse-acting speed command, set the bias= 100% and the gain= 0%. The minimum analog input level (0Vdc or 4mA) will produce a 100% speed command and the maximum analog input level (10Vdc or 20mA) will produce a 0% speed command.
0V
4mA
10V
20mA
Analog Input Signal
Analog Input Level
Fig 5.27 Output Frequency with Inverted Gain and Bias Settings
Programming 5 - 59
"
H3-08 Terminal A2 Signal Level
Setting
0
2
0 - 10VDC
4 - 20mA (Default)
Description
H3-08 is one of the special parameter settings required by the Bypass logic circuit. See Table 5.2.
The H3-08 parameter (Terminal A2 Signal Level) allows the programmer to specify the signal that will be applied to the A2 analog input. The A2 analog input can accept either a 0–10 Vdc or 4-20 mA signal as a reference. The Drive also has a DIP switch (S1) on the removable terminal board that must be set for the proper reference signal into the A2 analog input. The
S1-2 dipswitch setting determines the internal resistance of the A2 input while parameter H3-08 determines how the Drive interprets the measured signal.
O
S1
1
1
2
Terminating resistance
DIP Switch S1-1 located on terminal board.
Fig 5.28 DIP Switch S1
Name
S1-1
S1-2
Table 5.17 DIP Switch S1
Function
RS-485 and RS-422 terminating resistance
Input method for analog input A2
Setting
OFF: No terminating resistance (Factory default)
ON: Terminating resistance of 110
Ω
OFF: 0 to 10 V (internal resistance: 20 k
Ω
)
ON: 4 to 20 mA (internal resistance: 250
Ω
) (Factory default)
Programming 5 - 60
"
H3-09 Terminal A2 Function Selection
H3-09 is one of the special parameter settings required by the Bypass logic circuit. See Table 5.2.
Setting
0
2
B
D
E
16
1F
Frequency Bias
Aux Reference
PI Feedback
Frequency Bias 2
Motor Temperature
PI Differential
Not Used
Description
The A2 analog input can be programmed to perform many different functions. The setting of parameter H3-09 determines which of the following functions the A2 analog input will perform.
Function: Aux Reference
Setting: 2
In order for the A2 analog input to be used as the master Speed Command, parameter H3-09 must be set for Aux Reference
(H3-09= “2: Aux Reference”). Once A2 is configured as an auxiliary reference, it can be selected as the master Speed
Command by setting H3-13= “1: Main Fref TA2”. If H3-09= 2, terminal A2 analog input will become the speed command when a digital input programmed for Multi-Step Ref 1 (H1-0x= 3) is selected by a contact closure.
Function: PI Feedback
Setting: B
Configuring the A2 analog input as PI Feedback (H3-09= “B: PI Feedback”) is a requirement of setting the Drive up for PI operation. The A2 analog input is the only source for feedback for PI operation though the setpoint can come from a number of different sources (refer to the section covering the PI parameters for more information regarding specifying the setpoint source. PI parameters are listed in section b5).
Parameters H3-10 (Terminal A2 Gain) and H3-11 (Terminal A2 Bias) can be used to configure the A2 analog input to match the signal from the Feedback Transmitter.
The U1-24 monitor (PI Feedback) can be used to check the PI Feedback level with the digital operator.
Function: PI Differential
Setting: 16
Normal PI operation will adjust the Drive output in order to match the measured feedback value to a desired setpoint. When PI is operated in the differential mode, however, the Drive output is adjusted in order to maintain a desired differential between two feedback signals.
When the A2 analog input is configured as a PI Differential (H3-09= “16: PI Differential”), the A1 analog input becomes the other PI Differential input. The desired differential is set by parameter b5-07 (PI Differential Setpoint) and can be set so that
A2 is held less than A1 (b5-07 <0) or A2 is held greater than A1 (b5-07>0).
When PI Differential operation is chosen, the A1 feedback level can be monitored by U1-24 (PI Feedback) and the A2 feedback level can be monitored by U1-53 (PI Feedback2).
Programming 5 - 61
"
H3-10 Terminal A2 Gain Setting
Setting Range: 0.0 to 1000.0%
Factory Default: 100.0%
"
H3-11 Terminal A2 Bias Setting
Setting Range: -100.0% to +100.0%
Factory Default: 0.0%
Parameters H3-10 and H3-11 perform the same function for the A2 analog input that parameters H3-02 and H3-03 perform for the A1 analog input. Please refer to the parameter description for H3-02 and H3-03 for information about H3-10 and
H3-11.
These parameters could be used for final calibration of a factory or field installed pressure to electric transducer input connected to terminal A2 and AC. This field calibration may be needed if there is a job site variation from the typical 3 to 15
PSIG pneumatic signal input range.
"
H3-12 Analog Input Filter Time Constant
Setting Range: 0.0 to 2.00 Seconds
Factory Default: 0.30 Seconds
An analog input filter can be used to prevent erratic Drive control when a “noisy” analog reference is used. Parameter H3-12 sets the time constant for a first order filter that will be applied to both the A1 and A2 analog inputs. The Drive operation becomes more stable the longer the time programmed, but it becomes less responsive to rapidly changing analog signals.
Analog
Input
Filter
Noisy input signal
Fig 5.29 Analog Input Filter Time Constant Effect on “Noisy” Signal
Programming 5 - 62
"
H3-13 Master Frequency Reference Terminal Selection
Setting
0
1
Description
Main Fref= A1 (factory default)
Main Fref= A2
H3-13 is one of the special parameter settings required by the Bypass logic circuit. See Table 5.2.
Parameter H3-13 allows the programmer to select which analog input will serve as the Speed Command input when “Terminals” are selected as the Auto Mode Speed source (b1-01= “1: Terminals”), or Terminal is selected as the reference source for the Hand mode (b1-12= “1: Terminals”). For the A2 analog input to be an effective selection for the H3-13 parameter, parameter H3-09 must be configured as Aux Reference (H3-09= “2: Aux Reference”).
If H3-09
≠
2, then the A1 analog input will be used regardless of the setting of parameter b1-12.
Programming 5 - 63
!
L2 Momentary Power Loss Ride-thru Function
When momentary power loss recovery is enabled (L2-01
≠0), a speed search is executed to catch the potentially spinning motor shaft. This speed search will occur regardless of the setting of b3-01 “Speed Search Selection”.
"
L2-01 Momentary Power Loss Detection Selection
Setting
0
1
2
Description
Disabled
PwrL Ride Thru t
CPU Power Active (factory default)
"
L2-02 Momentary Power Loss Ride-Thru Time
Setting Range: 0.0 to 25.5 Seconds
Factory Default: Model Dependent
The Drive allows different responses to momentary power losses. The setting of L2-01 determines whether the Drive attempts to restart after a short loss of incoming AC power and for what length of time this capability remains active.
If L2-01= “0: Disabled”, the Drive detects a UV1 fault 15ms after power loss and automatic restarting is disabled. The Drive cannot restart until the external run command is removed and the UV1 fault is reset.
If L2-01= “1: PwrL Ride Thru t”, the Drive restarts without the UV1 fault if power is returned within the time specified in
L2-02, the Momentary Power Loss Ride-thru Time. During the power loss but before the fault trip, the digital operator will display a UV alarm. If L2-02 is set for a time longer than the control power supply can be sustained, a UV1 fault will not occur and the Drive restarts upon the return of AC power. The time that the control power supply can be maintained varies with
Drive size. The larger the Drive, the greater the potential ride-thru time.
If L2-01= “2: CPU Power Active”, the Drive ignores L2-02 and attempts a restart as long as the control power supply is still able to maintain a minimal voltage level. In effect, setting L2-01= “2: CPU Power Active” (factory default) is programming the Drive for maximum Power Loss Ride-thru. An equivalent setting is L2-01= “1: PwrL Ride Thru t”, with L2-02 set to a time longer than the control power supply can be maintained after power is lost.
Note:
The run command must be held during power loss for any power loss ride-thru capability to be possible. It is for this reason that 3-wire control is not recommended for use with the Momentary Power Loss function.
Programming 5 - 64
!
L3 Stall Prevention
"
L3-01 Stall Prevention Selection During Accel
Setting
0
1
2
Description
Disabled
General Purpose (factory default)
Intelligent
"
L3-02 Stall Prevention Level During Accel
Setting Range: 0 to 200% of Drive rated output current
Factory Default: 120% of Drive rated output current
The stall prevention during acceleration function adjusts the acceleration time in order to prevent OC fault trips during acceleration. If L3-01= “0: Disabled”, stall prevention is disabled. If the load is large enough and the acceleration time short enough the Drive may fault and stop.
If L3-01= “1: General Purpose”, then the standard stall prevention function is enabled. When the output current exceeds the level set by the L3-02 parameter, the Drive will discontinue accelerating and maintain speed. If, during acceleration, the output current comes within 15% of the level set by parameter L3-02, the acceleration time is lengthened. Once the output current level has dropped below the L3-02 level, acceleration will begin again with the acceleration rate reaching the programmed rate once again 15% below the L3-02 level.
-15%
Stall level during acceleration
Output Current
Time
Output frequency
Output frequency is controlled to prevent the motor stalling.
Time
Fig 5.30 Detailed Time Chart for Stall Prevention During Acceleration
If L3-01= “2: Intelligent”, the intelligent stall prevention is enabled. The active acceleration time is ignored and the Drive will attempt to accelerate as quickly as possible without exceeding the L3-02 output current level.
IMPORTANT
Stall Prevention during Acceleration is not effective when the output frequency is less than 6Hz.
Programming 5 - 65
The following figure demonstrates acceleration when L3-01= “1: General Purpose”.
Output
Frequency a - Set accel time b - Accel time is extended
t
L3-02
Output
Current
Fig 5.31 Time Chart for Stall Prevention During Acceleration
The L3-02 parameter is set as a percentage of the Drive rated output current. If the motor capacity is small compared to the
Drive’s capacity, or if the motor stalls during acceleration, lower the set value of L3-02.
"
L3-04 Stall Prevention Selection During Decel
Setting
0
1
2
3
Description
Disabled
General Purpose (factory default)
Intelligent
Stall prev w/R
The stall prevention during deceleration function adjusts the deceleration time in order to prevent OV fault trips during deceleration. If L3-04= “0: Disabled”, stall prevention is disabled and if the load is large and the deceleration time short enough the Drive may fault and stop.
If L3-04= “1: General Purpose”, then the standard stall prevention function is enabled. If, during deceleration, the DC Bus voltage exceeds the stall prevention level (see table below), the Drive will discontinue decelerating and maintain speed. Once the DC Bus voltage has dropped below the stall prevention level, the deceleration will continue down to the Speed Command level. See figure below.
480 VAC
Table 5.18 Stall Prevention During Decel
Drive Voltage
240 VAC
E1-01
≥
400 VAC
E1-01
<
400 VAC
Stall Prevention Level during Deceleration
(V)
380
760
660
If L3-01= “2: Intelligent”, the intelligent stall prevention is enabled. The active deceleration time is ignored and the Drive will attempt to decelerate as quickly as possible without causing the DC Bus voltage to exceed the stall prevention level.
The following figure demonstrates acceleration when L3-04= “1 General Purpose”.
Programming 5 - 66
a - Set decel time b - Decel time is extended
Output
Frequency
DC Bus
Voltage
t
a b
380/660/760 Vdc
t
TIME
Fig 5.32 Time Chart for Stall Prevention During Deceleration
"
L3-05 Stall Prevention Selection During Running
Setting
0
1
2
Description
Disabled
Decel Time 1 (factory default)
Decel Time 2
"
L3-06 Stall Prevention Level During Running
Setting Range: 30 to 200% of Drive rated output current
Factory Default: 120% of Drive rated output current
The Stall Prevention During Running function will attempt to avoid a Drive OC fault occurrence while the Drive is operating at a constant speed. If L3-05= “0: Disabled”, the Drive may fault if the load increases sufficiently to cause the output current to reach the OC fault level (180% of Drive rated output current).
If L3-05= “1: General Purpose”, the Drive is outputting a constant speed, and the Drive’s output current level exceeds the level set by parameter L3-06 for more than 100 ms the Drive will begin to decelerate at the rate specified by parameter C1-02. The
Drive will continue to decelerate until the output current level drops below the L3-06 level (less a 2% hysteresis). Once the output current drops below the L3-06 – 2% level the Drive will begin to accelerate at the currently active acceleration rate
(either C1-01 or C1-03).
If L3-05= “2: Decel Time 2”, the Drive will function as described above except C1-04 will be used instead of C1-02 as the deceleration rate used when the output current exceeds L3-06 for more than 100 ms.
The following figure demonstrates acceleration when L3-05
≠
0.
Output
Frequency a
- Decel time
C1-02 or C1-04.
C1-02 or C1-04 b
– Active accel time b - Active Accel time
t
a a b b
Output
Current
L3-06
t
TIME
Fig 5.33 Time Chart for Stall Prevention Level During Running
The L3-06 parameter is set as a percentage of the Drive rated output current. If the Drive still faults when L3-05
≠
0, then either lower the L3-06 or adjust the C1-02 or C1-04 settings for a quicker deceleration.
Programming 5 - 67
!
L4 Speed Command Loss Detection
"
L4-05 Frequency Reference Loss Detection Selection
Setting
0
1
Description
Disabled (factory default)
Enabled @ % of PrevRef
"
L4-06 Frequency Reference at Loss of Frequency Reference
Setting Range: 0.0 to 100.0% of previous speed command
Factory Default: 80.0% of previous speed command
The Drive can be configured to compensate for the loss of its external speed command. An external speed command is considered lost if it drops 90% of its value in 400mS or less.
100%
Frequency
Reference
T
10%
t
T = 400mS
Output
Frequency
Fig 5.34 Loss of Frequency Reference Timing Diagram
TIME
L4-06
t
To enable Frequency loss detection, set L4-05= “1: Enabled @ % of PrevRef”. If Frequency Reference Loss Detection is enabled and the reference is lost, the Drive continues to operate at the speed commanded by parameter L4-06. When the speed command returns, the Drive again follows the speed command.
Setting H2-01/H2-02= “C: Loss of Ref”, configures a digital output as a Frequency Reference Loss indication only when
L4-05= “1: Enabled @ % of PrevRef”.
Programming 5 - 68
!
L5 Fault Restart
"
L5-01 Number of Auto Restart Attempts
Setting Range: 0 to 10
Factory Default: 10
"
L5-02 Auto Restart Operation Selection
Setting
0
1
Description
No Flt Relay (factory default)
Flt Relay Active
"
L5-03 Maximum Restart Time After Fault
Setting Range: 0.5 to 600.0 Seconds
Factory Default: 600.0 Seconds
All major faults will cause the Drive to stop. For some faults it is possible to configure the Drive to attempt a restart automatically. After the fault occurs, the Drive baseblocks for L2-03 seconds. After the baseblock is removed the Drive checks if a fault condition still exists. If no fault condition exists the Drive will attempt to restart the motor. If the restart is successful, the Drive performs a Speed Search (Regardless of the status of b3-01 “Speed Search Selection”) from the set speed command and the Auto Restart Attempts count is increased by one. Even if the restart fails the restart count is increased by one as long as the Drive attempted to rotate the motor. The restart count will not be incremented if the restart is not attempted due to a continuing fault condition (i.e. an OV fault). The Drive waits L5-03 seconds before attempting another restart.
Run t
OV
OC
OC
Fault
Attempts trying each
L5-03 seconds successful try but failed successful t
L2-03 L2-03 L2-03 t
1
2
3
Count
Voltage remains high for a long time, then reset (1) and run
Drive trips on OC, resets (2) and tries again but motor still shorted, trips again.
OC condition gone, resets (3) and runs.
Fig 5.35 Automatic Restart Timing Diagram
The auto restart count is reset back to 0 if any of the following occur:
• No further faults for ten minutes after the last retry.
• The Drives power is turned off (the Drive must be without power long enough to let control power dissipate).
• The SHIFT/RESET key is pushed after the last reset attempt.
Programming 5 - 69
The setting of parameter L5-02 determines whether the fault output (MA-MB) will be closed during an auto restart attempt.
The setting of L5-02 can be important when interfacing the Drive with other equipment.
The following faults will allow the Auto Restart function to initiate:
• OC (Overcurrent)
• LF (Output Open Phase)
• PF (Input Phase Loss)
• PUF (DC Bus Fuse)
• OL1 (Motor Overload)
• OL3 (Overtorque)
• OL2 (Drive Overload)
• OV (DC Bus Overvoltage)
• GF (Ground Fault)
• UV1 (DC Bus Undervoltage)
• OH1 (Overheat)
In order for auto restart after a UV1 fault, Momentary Power Loss Ride-thru must be enabled (L2-01= “1: PwrL Ride Thru t”, or “2: CPU Power Active”). Setting H2-01 or H2-02 equal to “1E” configures a digital output as “Restart Enabled” to signal if an impending auto restart is possible.
Programming 5 - 70
!
L6 Torque Detection
"
L6-01 Torque Detection Selection 1
Setting
0
1
4
5
2
3
6
7
8
Description
Disabled (factory default)
OL@SpdAgree - Alm
OL At Run -Alm
OL@SpdAgree - Flt
OL At Run - Flt
UL@SpdAgree - Alm
UL at Run - Alm
UL@SpdAgree - Flt
UL At Run - Flt
"
L6-02 Torque Detection Level 1
Setting Range: 0 to 300% of Drive rated output current
Factory Default: 15% of Drive rated output current
"
L6-03 Torque Detection Time 1
Setting Range: 0.0 to 10.0 Seconds
Factory Default: 10.0 Seconds
The Drive can be programmed to indicate when either an overtorque or an undertorque conditions exist. A digital output must be programmed for “Torque Detection”, (H2-01/H2-02= “B: Trq Det 1 N.O.” or “17: Trq Det 1 N.C.). A warning of an overtorque condition can indicate a jam and an undertorque condition can indicate a broken belt, no water in a pump, or other loss of load.
To configure Torque Detection requires the following decisions:
1.
Do you wish to check for an overtorque condition or an undertorque condition?
2.
Do you wish to check for the torque condition whenever the Drive is running or only at speed agree? Nuisance detection during acceleration, when variable torques are normally required, can be avoided.
3.
Do you want the Drive to fault if the torque condition is detected or only alarm and continue operation?
The following table can help choose the proper setting for Torque Detection Selection 1 to get the wanted results.
Table 5.19 L6-01 Setting Choices
L6-01
Setting
Overtorque Undertorque
6
7
4
5*
8
2
3
0
1 X
X
X
X
X
X
X
X
*Suggested settings for Loss of Load indication
Fault Alarm
Torque Detection Disabled
X
X
X
X
X
X
Always
Detected
X
X
X
X
Only Detected @
Spd Agree
X
X
X
X
Programming 5 - 71
After selecting the proper detection scheme the Torque Detection Level (L6-02) must be specified. If the current level read by the output current transformers rises above (overtorque) or drops below (undertorque) this level, and remains there for at least the Torque Detection Time (L6-03), then the Torque Detection Function will change the state of any digital output configured for Torque Detection (H2-01/H2-02= “B: Trq Det 1 N.O.”, or “17: Trq Det 1 N.C.”).
*
*
Torque detection level -10%
L6-03 t
L6-03
CLOSED
TIME
Closed
Open
* When the output current drops below the Torque Detection Level by
approximately 10% of the Drive’s rated output current the digital output is reset.
Fig 5.36 Over Torque Detection
*
Torque detection level 10%
*
L6-02 t
L6-03
L6-03
Closed
TIME
* When the output current rises above the Torque Detection Level by
approximately 10% of the Drive’s rated output current the digital output is reset.
Fig 5.37 Under Torque Detection
Programming 5 - 72
!
L8 Hardware Protection
"
L8-01 Internal Dynamic Braking Resistor Protection Selection
Setting
0
1
Description
Not Provided (factory default)
Provided
This parameter is not applicable for Drive operation.
"
L8-02 Overheat Pre-Alarm Level
Setting Range: 50 to 130 o
C
Factory Default: 95 o
C
"
L8-03 Overheat Pre-Alarm Operation Selection
Setting
0
1
2
3
4
Description
Ramp to Stop (Decel Time C1-02)
Coast to Stop
Fast-Stop (Decel Time C1-09)
Alarm Only
OH Alarm and Reduce (factory default)
The Drive is capable of warning the operator of an impending heatsink over-temperature fault via an OH pre-alarm. The level at which the pre-alarm will activate is determined by the setting of parameter L8-02. Measurement of the heatsink temperature is done with several strategically mounted thermistors. If any of the heatsink thermistors measure a temperature in excess of the setting of
L8-02, the Drive will fault (OH2) and either: ramp to stop using the C1-02 deceleration rate (L8-03= “0: Ramp to Stop”), coast to stop (L8-03= “1: Coast to Stop”), ramp to stop using the C1-09 fast stop deceleration rate (L8-03= “2: Fast-Stop”), alarm (OH) and continue running (L8-03 = “3: Alarm Only”), alarm (OH) and continue running but at a reduced speed (L8-03= “4: Alarm &
Reduce”). If L8-03= 4: Alarm and Reduce, the Drive will continue to run but will reduce the speed to the level determined by parameter L8-19. Refer to the description for parameter L8-19.
If a digital output is configured for OH Prealarm (H2-01= “20: OH PreAlarm”), it will close whenever the heatsink temperature is greater than the L8-02 level no matter what the setting is of L8-03.
"
L8-10 Heatsink Cooling Fan Operation Selection
Setting
0
1
Description
Fan On-Run Mode (factory default)
Fan Always On
Programming 5 - 73
"
L8-11 Heatsink Cooling Fan Operation Delay Time
Setting Range: 0 to 300 Seconds
Factory Default: 300 Seconds
Parameters L8-10 and L8-11 allow the Drive programmer to customize the heatsink cooling fan operation. Parameter L8-10 determines whether the cooling fans are always ON whenever the Drive is powered (L8-10= “1: Fan Always On”) or if the cooling fans are only ON when the Drive is in a Run condition (L8-10= “0: Fan On-Run Mode”).
Parameter L8-11 is a delayed OFF for the cooling fan if L8-10= “0: Fan On-Run Mode”. When the cooling fans are set to turn
OFF when the Run command is removed, parameter L8-11 will cause the fans to continue cooling the Drive for the amount of time programmed into L8-11 after the Run command is actually removed. The Drive can be programmed to allow the cooling fan to run for up to 5 minutes (factory default) after the run command is removed.
Both parameters are intended to extend fan life while still providing sufficient cooling for proper Drive operation.
Run
Command
ON (CLOSED) t
Heatsink Fan
RUN
L8-11
TIME
ON (CLOSED) t
Fig 5.38 Heatsink Cooling Fan Operation Timing Diagram
"
L8-19 Overheat Frequency Reference Reduction Level
Setting Range: 0.0 to 100.0% of maximum frequency
Factory Default: 20.0% of maximum frequency
When the heatsink temperature reaches the OH Pre-alarm level (L8-02) and the Overheat Pre-Alarm Operation Selection parameter is set for Alarm and Reduce (L8-03= “4: OH Alarm & Reduce”), the L8-19 parameter sets the amount of speed decrease that will be applied to the Speed Command in order to lower the heatsink temperature. The decrease in speed will lower the current being switched and conducted by the heat producing output transistors of the Drive.
Parameter L8-19 is set in percentage of maximum frequency (E1-04).
Programming 5 - 74
!
o1 Monitor Configuration
"
o1-01 User Monitor Selection
Setting Range: 6 to 53
Factory Default: 6
34
36
37
38
20
24
28
39
40
51
52
53
Setting
6
7
8
10
11
12
13
14
15
16
18
Description
Output Voltage (factory default)
DC Bus Voltage
Output Power
Input Terminal Status
Output Terminal Status
Drive Operation Status
Cumulative Operation Time
Software Number
Terminal A1 Input Voltage
Terminal A2 Input Voltage
Motor Secondary Current (I q
)
Output Frequency After Soft Start
PI Feedback Value
CPU Number
First Parameter Causing an OPE
PI Input
PI Output
PI Setpoint
Memobus Communication Error Code
Heatsink Cooling Fan Operation Time
Auto Mode Frequency Reference Value
Hand Mode Frequency Reference Value
PI Feedback 2 Value
Programming 5 - 75
"
o1-02 Power-On Monitor
Setting
1
2
3
4
Description
Frequency Reference (factory default)
Output Frequency
Output Current
User Monitor (set by o1-01)
When the Drive is powered up, three monitors are displayed on the digital operator. The first and largest monitor is the
“Power-On” monitor. The factory default “Power-On monitor” is Speed Command (U1-01). Below the Speed Command monitor are the next two sequential monitors, Output Frequency (U1-02) and Output Current (U1-03). Pressing the
INCREASE key once scrolls the monitors to show the User Monitor as selected by o1-01. The factory default for o1-01 is the
Output Voltage monitor (U1-06).
The active monitor displayed when the Drive is powered on can be changed to either be U1-01 (Speed Command), U1-02
(Output Frequency), U1-03 (Output Current), or the User Monitor. Whichever monitor is selected as the Power-On top monitor, the two monitors displayed below it are the next two sequential monitors. See example below.
Active Monitor
Active Monitor Title
Output Frequency
Output Current
Next two sequential monitors
For example, if the Drive needs to display the Elapsed Timer as the Power-On monitor, then o1-01 must be set to “13” and o1-02 must be set to “4”. The next time Drive power is cycled, the digital operator displays U1-13 (Elapsed Time), U1-14
(Flash ID), and U1-15 (Term AI Level).
Active Monitor
-DRIVE- Rdy
Elapsed Time
U1-13= 2
H
- - - - - - - - - - - - - - - - - - - - - - - - - - - - -
U1-14= 03010
U1-16= 51.2%
Flash ID
Term AI Level
Active Monitor Title
Next two sequential monitors
Programming 5 - 76
"
o1-03 Digital Operator Display Scaling
Setting
0
1
2 - 39
40 - 39999
Description
Hz (factory default)
%
RPM (Enter the # of Motor Poles)
User Display
Parameter o1-03 allows the programmer to change the units in which the speed monitors and some speed parameters are displayed. The o1-03 parameter will change the units of the following:
• U1-01 (Frequency Reference Monitor)
• U1-02 (Output Frequency Monitor)
• U1-20 (Output Frequency after Soft Start)
• d1-01 through d1-17 (Preset Frequency References and Jog Reference)
The table below details how the setting of o1-03 will affect the way the listed monitors and parameters will be displayed.
Table 5.20 Display Scaling
If o1-03 is:
0
1
The frequency format is
0.01 Hz
0.00%
2 through 39
(enter the # of motor poles)
0 RPM
40 through 39999 Engineering Units
The factory default setting (o1-03= “0”) sets the Drive up to display the affected monitors and parameters in terms of hertz
(Hz).
If the speeds seem more natural in terms of percentage of maximum, set o1-03= “1”. If the speeds are easier to work with when displaying the equivalent synchronous motor RPM, set o1-03= [the number of motor poles]. If another engineered unit, such as fpm or gpm, is desired, set o1-03= xxxx where:
X X X X X
Digit 5 Digit 4 Digit 3 Digit 2 Digit 1
Digits 1 through 4 set the desired number to be displayed at 100% speed.
Digit 5 determines the number of decimal places in the displayed number.
If Digit 5 = 0 number format is XXXX
If Digit 5 = 1 number format is XXX.X
If Digit 5 = 2 number format is XX.XX
If Digit 5 = 3 number format is X.XXX
For example:
If o1-03= 10425, then at full speed the digital operator will display “42.5”. Configuring parameter o1-03 for displaying in terms of an engineering unit is only appropriate if the actual display units have a linear relationship with the actual output speed.
Programming 5 - 77
"
o1-05 LCD Contrast Adjustment
Setting Range: 0 to 5
Factory Default: 3
The contrast setting of the LCD display of the digital operator can be adjusted by the setting of parameter o1-05. The higher the number programmed into o1-05, the darker the background will become. Set o1-05 to the value that makes the LCD the easiest to view at the normal viewing distance and angle.
"
o1-06 User Monitor Selection Mode
Setting
0
1
Description
3 Mon Sequential (factory default)
3 Mon Selectable
"
o1-07 Second Line User Monitor
Setting Range: 1 to 53
Factory Default: 2
"
o1-08 Third Line User Monitor
Setting Range: 1 to 53
Factory Default: 3
Normally the monitors shown directly below the active monitor are the next two sequential monitors. If o1-06 (User Monitor
Selection Mode) is set to “1: 3 Mon Selectable”, those two monitors are locked as specified by parameters o1-07 and o1-08 and will not change as the top parameter is scrolled with the INCREASE and DECREASE keys.
Active Monitor
-DRIVE- Rdy
PI Feedback
U1-24= 64.55%
- - - - - - - - - - - - - - - - - - - - - - - - - - - - -
U1-37= 0.00%
U1-38= 2.50%
PI Output
PI Setpoint
Active Monitor Title
For Example:
The Display above showing PI Feedback, PI Output and PI Setpoint would be useful when setting up a PI Control Loop.
Programming 5 - 78
!
o2 Key Selections
"
o2-03 User Parameter Default Value
Setting
0
1
2
No Change
Set Defaults
Clear All
Description
The Drive gives the option of configuring any and all of the programming parameters and then saving the parameters as “User
Initialization Values”. After configuring the Drive, set parameter o2-03= “1: Set Defaults”, to save the parameters to a User
Initialization memory location. Once this has been done, the “Initialize Parameters” parameter (A1-03) will offer the choice of
“1110:User Initialize”. Choosing A1-03= “1110: User Initialized”, will reset all modified parameters back to what they were the last time they were saved using o2-03.
The choice of setting A1-03= “1110: User Initialized”, is unavailable until first setting the User Initialization parameters using o2-03. Once a User Initialization is set (saved), it can be cleared by setting o2-03= “2: Clear All”. After clearing the User
Initialization parameters, the choice of “1110: User Initialize” is no longer a available in A1-03.
"
o2-05 Frequency Reference Setting Method Selection
Setting
0
1
Description
Disabled
Enabled (factory default)
The factory default setting of the Frequency Reference Setting Method parameter (o2-05= “1: Enabled”) dictates that when setting a Speed Command via the digital operator (“Hand” mode), it is not necessary to press the DATA/ENTER key before the Drive will begin to accelerate or decelerate to the new set speed. This is referred to as MOP (Motor Operated
Potentiometer) type functionality. When o2-05= “1: Enabled”, the speed command is stored to memory 5 seconds after the
INCREASE or DECREASE keys are released.
When o2-05= “0: Disabled”, the digital operator INCREASE and DECREASE keys will change the speed command but the
Drive will not accelerate or decelerate to the new speed command until the DATA/ENTER key is pressed. In order to change the Speed Command in the HAND mode, U1-01 must be the top monitor and then the ENTER key must be pressed in order to access the Speed Command function. This in not to be confused with pressing the ENTER key in order to achieve a change in speed using the INCREASE and DECREASE keys, which is the subject of parameter o2-05.
Programming 5 - 79
"
o2-06 Operation Selection when Digital Operator is Disconnected
Setting
0
1
Description
Disabled
Enabled (factory default)
Leaving o2-06 enabled will cause the Drive to fault, when the digital operator is removed, even if it’s not outputting to the motor. The reset key on the digital operator will need to be pressed after reconnecting the digital operator to reset the fault and continue normal operation.
If o2-06 = “0: Disabled” then the Drive will not fault if the digital operator is disconnected, but the Drive will discontinue motor operation. If full Drive operation is required while the digital operator is removed set o2-06 = “0: Disabled” and o2-15 = “0: Disabled” (Hand Key Function). If both o2-06 and o2-15 are disabled then the digital operator can be disconnected without disturbing Drive operation.
"
o2-07 Cumulative Operating Time Setting
Setting Range: 0 to 65535 Hours
Factory Default: 0 Hours
"
o2-08 Cumulative Operation Time Selection
Setting
0
1
Description
Power-On Time
Running Time (factory default)
The Drive features an Elapsed Timer monitor that records in units of hours. The Elapsed Timer monitor is U1-13. Parameter o2-08 programs this function to either accumulate elapsed hours based on time the Drive is powered (o2-08= “0: Power-On
Time”) or time the Drive is running (o2-08= “1: Running Time”). The Drive is considered “running” anytime there is an active run command or when the Drive is outputting voltage (i.e. including during deceleration).
-DRIVE- Rdy
Elapsed Time
U1-13= 0H
- - - - - - - - - - - - - - - - - - - - - - - - - - - - -
U1-14= 03010
U1-15= 34.1%
Parameter o2-07 allows manual adjustment of the Elapsed Timer, primarily to accommodate maintenance or control board replacement in the event of damage. To reset the Elapsed Timer back to zero, set o2-07= 0.
Programming 5 - 80
"
o2-10 Cumulative Cooling Fan Operation Time Setting
Setting Range: 0 to 65535 Hours
Factory Default: 0 Hours
The elapsed time of heatsink cooling fan operation is tracked by the U1-40 monitor. Much like the o2-07 parameter can be used to adjust or reset the Drive operation elapsed timer, parameter o2-10 can be used to adjust the time displayed by the
U1-40 monitor in the event of fan replacement.
-DRIVE- Rdy
FAN Elapsed Time
U1-40= 152H
- - - - - - - - - - - - - - - - - - - - - - - - - - - - -
U1-51= 52.33%
U1-52= 57.60%
"
o2-12 Fault Trace / Fault History Clear Function
Setting
0
1
Description
Disabled (No Effect) (factory default)
Enabled
The operator can clear the Fault Trace (U2) and Fault History logs by setting o2-12= “1: Enabled”. Clearing the Fault Trace and Fault History logs erases all the information.
"
o2-14 kWh User Monitor Initialization
Setting
0
1
Description
Disabled (No Change) (factory default)
Clear All
The kWh monitors (U1-29 and U1-30) track the power usage of the Drive and are not reset by powering down the Drive. To reset the monitors back to zero, set o2-14= “1: Clear all”.
Programming 5 - 81
!
o3 Digital Operator Copy Function
"
o3-01 Copy Function Selection
The membrane over the Drive keypad also makes the keypad non-removable on Bypass units. In order to use the keypad copy function on a Bypass unit - order a separate keypad, part number CDR001115 and obtain locally a standard CAT 5
Ethernet cable.
Note: The copy function is disabled when serial communication is active.
Setting
0
1
2
3
Description
COPY SELECT (factory default)
INV
→
OP READ
OP
→
INV WRITE
OP
↔
INV VERIFY
"
o3-02 Read Allowed Selection
Setting
0
1
Description
Disabled
Enabled (factory default)
The digital operator has parameter COPY capabilities via built in non-volatile memory. The digital operator can READ all of the parameters in the Drive and store them for later WRITE back to the Drive or into a Drive with the same product code and software number. In order to read the parameter values and store them in the digital operator, select o3-02= “1: Enabled”. If you attempt to READ the data, which overwrites any previously stored data, without first setting o3-02= “1: Enabled”, you will get the following error:
-ADV-
PRE
READ IMPOSSIBLE
After setting o3-02= “1: Enabled”, it is possible to store parameter values in the digital operator by setting o3-01=1
(INV
→
OP READ).
A successful READ of the parameter values will display:
-ADV-
READ
READ COMPLETE
Programming 5 - 82
An error may occur while saving the parameter values to the digital operator’s memory. If an error is displayed, press any key to cancel the error display and return to parameter o3-01. To COPY parameter values into a Drive, set o3-01= “2: OP->INV
WRITE”. During the writing of the parameter values into the Drive the digital operator will display:
-ADV-
COPY
OP
→
INV COPYING
A successful COPY of the parameter values will display:
-ADV-
COPY
COPY COMPLETE
An error may occur while writing the parameter values to the Drive. If an error is displayed, press any key to cancel the error display and return to parameter o3-01.
It is possible to compare the parameter values stored in the digital operator with the parameter values currently in the Drive by using the VERIFY function. This VERIFY function should not be confused with the “-VERIFY-“ that is displayed on the digital operator when viewing the “Modified Constants” menu. To VERIFY the parameter values in the Drive as compared with those stored in the digital operator, set o3-01= “3: OP<-->INV VERIFY”. During the comparing of the parameter values into the Drive the digital operator will display:
-ADV-
VERIFY
DATA VERIFYING
A successful VERIFY of the parameter values will display:
-ADV-
VERIFY
VERIFY COMPLETE
Programming 5 - 83
If all the parameter values stored in the digital operator do not match those programmed in the Drive, the digital operator displays the following:
-ADV-
VYE
VERIFY ERROR
The digital operator will not display which parameters did not match, only that the verification found discrepancies in some parameter values.
NOTE:
In order to properly use the COPY or VERIFY functions, the following Drive specifications must be identical between the Drive that the parameters were read from and the Drive that the parameters are to be written to:
• Model Number (e.g. CIMR-P7U2015)
• Software Number (e.g. 1010 also known as FLASH ID)
Yaskawa offers DriveWizard™ software that can also READ, COPY, and VERIFY Drive parameter values. DriveWizard™ lists all discrepancies between the Drive and a pre-saved parameter file when verifying is performed.
To use
DriveWizard first select o2-15= “0: Disabled” and select o2-06= “0: Disabled” then remove the digital operator/keypad and attach the DriveWizard cable in its place.
Programming 5 - 84
!
T1 Auto-Tuning
Auto-Tuning can only be accomplished through the DriveWizard software. Available by download from www.drives.com.
"
T1-02 Motor Rated Power
Setting Range: 0.00 to 650.00 kW
Factory Default: Model Dependent
"
T1-04 Motor Rated Current
Setting Range: Model Dependent
Factory Default: Model Dependent
Auto tuning is recommended to achieve optimum performance. In addition, the Drive requires Line-To-Line Resistance auto-tuning before it can properly perform the Estimated Speed Search method. This method of speed search allows for bi-directional speed search. The T1 parameters are found under the Auto-Tuning menu.
"
Auto-Tuning Using DriveWizard
DriveWizard is a PC software program designed to provide the tools necessary to handle Drive installation as well as parameter record keeping and maintenance. As such it provides an Auto-Tuning method for Drives in Bypass units. The
Auto-Tuning function “tunes” the Drive setup to the characteristics of the specific motor to which it is applied. Auto-Tuning is essential if bi-directional Speed Search is required and enabled for the application.
DriveWizard can be obtained either through CD or www.Drives.com. Follow the installation procedures provided with the software.
With the DriveWizard software loaded onto a PC, connect a standard CAT 5 Ethernet cable from the PC’s RS-232 port (with a
DB-9 to CAT 5 adaptor) to the digital operator/keypad port on the Drive. Before disconnecting the digital operator/keypad from the Drive, set parameter o2-06 (“Oper Detection”) to “0:disabled”. This will allow the Drive to continue running with the digital operator/keypad removed.
Start DriveWizard and setup the PC communications by setting the appropriate communications port and Baud rate. Typical settings are Com Port 1 and 9600 Baud.
Once the communications port is set, connect to the Drive by clicking on the pull-down menu “Inverter” and selecting
“Connect.” [This can also be done by typing Ctrl+C on your keyboard, or by clicking on the yellow icon resembling two puzzle pieces.] This will upload all of the current parameters in the Drive to the computer as a working parameter file.
At this point the parameters can be saved as a backup file if desired. [DriveWizard is a third method of saving the complete parameter list and user settings. In addition to the “User Parameters” (o2-03) and “Keypad Copy” (o3-01) functions discussed in this chapter, DriveWizard can be employed to maintain a downloadable list of the Drive parameter set up on a PC, for backup or transfer to other drives.]
Auto-Tuning is performed by selecting the Auto-Tuning function from the “Inverter” pull-down menu. DriveWizard will ask you to verify that the motor is in a safe operating condition, and then ask you to enter two parameters. DriveWizard will ask you to fill in parameters T1-02 “Mtr Rated Power” and T1-04 “Rated Current”. After this data has been entered, click on the
“Load” button to enter these values into the Drive memory. The “Start” button will become available, click on “Start” to begin the auto-tuning process. While Auto-Tuning is running the Drive output current and frequency will be displayed, the flashing green light indicates DriveWizard is communicating with the Drive. When complete, DriveWizard will have auto-tuned the
Drive, adjusted several motor related parameters and the Drive will be ready for optimum performance for bi-directional Speed
Search and other functions.
Programming 5 - 85
Notes:
Programming 5 - 86
Chapter 6
Diagnostics & Troubleshooting
This chapter describes diagnostics and troubleshooting for the Drive.
Bypass Diagnostics ........................................................................ 2
Troubleshooting the Bypass Printed Circuit Boards .................. 2
Drive Diagnostics ........................................................................... 3
Fault Detection .......................................................................... 4
Alarm Detection ....................................................................... 10
Operator Programming Errors (OPE) ...................................... 13
Auto-Tuning Faults .................................................................. 14
Digital Operator COPY Function Faults ................................... 15
Drive Troubleshooting .................................................................. 16
If Parameter Cannot Be Set .................................................... 16
If the Motor Does Not Operate ................................................ 17
The Direction of the Motor Rotation is Reversed ..................... 18
If the Motor Does Not Put Out Torque or
If Acceleration is Slow ............................................................. 18
If the Motor Operates at a Higher Speed
Than the Speed Command ...................................................... 18
If the Motor Overheats ............................................................. 19
If Peripheral Devices Like PLCs or Others are Influenced by
Starting or Running Drive ......................................................... 19
If the Ground Fault Interrupter Operates When the Drive is Run ....................................................................... 20
If There is Mechanical Vibration .............................................. 20
If the Motor Rotates Even When Drive Output is Stopped ....... 21
If Zero Volts is Detected When a Motor is Started, or Stalls .... 21
If Output Frequency Does Not Rise to Frequency Reference . 21
Drive Main Circuit Test Procedure ................................................ 22
Drive Date Stamp Information ...................................................... 26
Diagnostic & Troubleshooting 6 - 1
advertisement
Related manuals
advertisement
Table of contents
- 14 Bypass Model Number and Enclosure Style
- 16 Enclosure Data
- 19 Confirmations upon Delivery
- 21 Bypass Product Options
- 23 Bypass Component Descriptions
- 29 Exterior and Mounting Dimensions
- 36 Checking and Controlling Installation Site
- 40 Termination Configuration - Power Wiring
- 47 Control Wiring
- 58 Wiring Diagram
- 60 Logic Diagram
- 66 Digital Operator and Control Panel Display
- 72 Drive Main Menus
- 80 Example of Changing a Parameter
- 84 Start Up Introduction
- 85 Bypass Start Up Preparation
- 86 Bypass Unit Start Up Procedure
- 90 Bypass Operation Description
- 96 Bypass Basic Programming Parameters
- 182 Bypass Diagnostics
- 183 Drive Diagnostics
- 196 Drive Troubleshooting
- 202 Drive Main Circuit Test Procedure
- 206 Drive Date Stamp Information
- 208 Maintenance
- 215 Removing and Replacing Drive in a Bypass Unit
- 220 Parameter List
- 244 Monitor List
- 246 Fault Trace List
- 247 Fault History List
- 250 Drive Capacity
- 256 Standard Drive and Bypass Specifications
- 260 Using Modbus Communication
- 265 Modbus Function Code Details
- 267 Modbus Data Tables
- 272 Modbus Self-Diagnosis
- 274 General Peripheral Devices
- 276 Primary Parts - 208/230/240VAC
- 277 Primary Parts - 480VAC
- 278 Bypass Replacement Parts