- Home
- Domestic appliances
- Climate control
- Temperature & humidity sensors
- YASKAWA
- P7B Drive Bypass
- Manual
advertisement
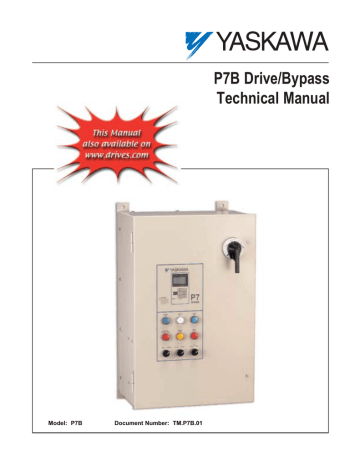
Bypass Product Options
Option A - Two motor “AND” control: Allows the operation of two motors from one Drive or Bypass. Pump #1 “AND” pump #2 are operated at the same speed via the output from one Drive or Bypass. The motors are always operated simultaneously therefore, no transfer switch is involved. With the 2 motor “AND” option, motor OverLoad Relays and fuses are provided for each motor and the Drive’s internal motor overload function is disabled.
The two motors can be of different capacity if this capacity difference was considered in the ordering process. The factory needs to know the FLA value of each motor controlled in order to select the correct motor overload devices and fuses.
(Specifying different capacity motors results in longer, non-standard lead times).
Option D - Two motor “OR” control: A MTR #1/AUTO/MTR #2 selector switch is provided to allow local or remote motor operation selection, between two identical motors, for control by either the Drive or the Bypass (for example, Pump #1 “OR”
AUTO “OR” Pump #2). In the AUTO position, a customer supplied contact closure at TB1 terminals 23 and 24 can switch between the two motors. The two motors must be the same horsepower and current draw.
Option E - RFI/EMI Filter: Filters to further attenuate possible VFD generated noise. Radio frequency interference/electro magnetic interference filters reduce conducted noise on the Drive input power leads and therefore, radiated noise from those leads. This option is installed on the input power side of the Drive, between the input contactor and the Drive.
Option F - Drive Input Fuses: Fuses capable of protecting semiconductor devices, rated at 200 kAIC are connected to the line side of the Drive, between the input contactor and the Drive, to protect the Drive semiconductors when motor or output conductor short circuit faults occur.
Option G - Serial Communication, DeviceNet: An option card that provides DeviceNet protocol for network communication.
Option H - Serial Communication, Profibus: An option card that provides Profibus protocol for network communication.
Option K - 5% Output Reactor: Employed on the output side of the Drive for reduction of peak voltages applied to the driven motor. In long Drive to motor lead length situations, high carrier frequency and reflected waves can cause high voltage spikes at the motor. An output reactor provides motor protection in these long motor lead length situations. This option is installed on the output power side of the Drive, between the output contactor and the Drive.
Option L - Serial Communication, Echelon LonWorks: An isolated RS-422/485 circuit board provides LonTalk protocol for network communication. This option plugs into the CN2 connection on the Drive control circuit board.
Option M - 4 to 20 mA Output: Provides two programmable 0 to 10 VDC analog outputs or two programmable 4 to 20 mA analog outputs.
Option N - Input Capacitive Network Radio Frequency Interference Filter: Electronic equipment can be sensitive to low levels of voltage distortion and electrical noise. This passive wye-delta capacitve filter is intended for installation on the VFD input in order to protect other sensitive electronic loads, it provides attenuation of conducted RFI and EMI.
Option P - Pressure to Electrical Transducer: This transducer is employed when converting a pneumatic signal to an electrical signal for use as the Drive speed command input. The need for this option comes up on retrofit applications when the pneumatic signal that formerly controlled the pneumatic actuator on Inlet Guide Vanes (IGV), for example, is now to be used to control the fan speed via the Drive. This option is wired to Drive terminals +V, A2 and AC, parameters H3-10 and
H3-11 are used for final field calibration of this input if there is jobsite variation from the typical 3 to 15 PSIG pneumatic signal input range.
Physical Installation 1 - 9
Option Q - Serial Communication, Ethernet: An option card that provides Modbus TCP protocol for network communication.
Option R - 3% Input Line Reactor: Employed on the input side of the Drive for Total Harmonic Distortion (THD) suppression. A line reactor also minimizes the potential for Drive input diode damage from line transients and reduces voltage peaks on the DC bus capacitors. This option is installed on the input power side of the Drive, between the input contactor and the
Drive.
Option S - Speed Potentiometer: A door mounted single turn potentiometer for manual control of Drive output and motor speed. This option is wired to Drive terminals +V, A1 and AC and is used as the local speed command input to the Drive instead of the keypad up and down arrows. Parameters for use of this option in conjunction with other input signals are detailed in Table 5.2.
Option V - Embedded Serial Communication, Modbus: A no cost option. The Drive in a Bypass unit is capable of Modbus network communication via the standard RS-422/485 terminals.
Option W - Engraved Plastic Nameplate: An enclosure identification nameplate to carry the controlled equipment “tag number”.
Option X - 3% DC Bus Reactor: Attenuates harmonic distortion by limiting the rate of rise of the input current. The bus reactor is wired to the Drive (+1) and (+2) DC bus terminals to provide the equivalent impedance of a 3% input reactor. This option is only used on the low end of the horsepower range where DC bus reactors are not a standard Drive component (25 HP and below @ 208 VAC, 25 HP and below @ 240 VAC, and 30 HP and below @ 480 VAC.)
Option Z - 5% DC Bus Reactor: Attenuates harmonic distortion by limiting the rate of rise of the input current. The bus reactor is wired to the Drive (+) and (-) DC bus terminals to provide the equivalent impedance of a 5% input reactor. This option is only used on the low end of the horsepower range where DC bus reactors are not a standard Drive component
(25 HP and below @ 208 VAC, 25 HP and below @ 240 VAC, and 30 HP and below @ 480 VAC.)
Physical Installation 1 - 10
advertisement
Related manuals
advertisement
Table of contents
- 14 Bypass Model Number and Enclosure Style
- 16 Enclosure Data
- 19 Confirmations upon Delivery
- 21 Bypass Product Options
- 23 Bypass Component Descriptions
- 29 Exterior and Mounting Dimensions
- 36 Checking and Controlling Installation Site
- 40 Termination Configuration - Power Wiring
- 47 Control Wiring
- 58 Wiring Diagram
- 60 Logic Diagram
- 66 Digital Operator and Control Panel Display
- 72 Drive Main Menus
- 80 Example of Changing a Parameter
- 84 Start Up Introduction
- 85 Bypass Start Up Preparation
- 86 Bypass Unit Start Up Procedure
- 90 Bypass Operation Description
- 96 Bypass Basic Programming Parameters
- 182 Bypass Diagnostics
- 183 Drive Diagnostics
- 196 Drive Troubleshooting
- 202 Drive Main Circuit Test Procedure
- 206 Drive Date Stamp Information
- 208 Maintenance
- 215 Removing and Replacing Drive in a Bypass Unit
- 220 Parameter List
- 244 Monitor List
- 246 Fault Trace List
- 247 Fault History List
- 250 Drive Capacity
- 256 Standard Drive and Bypass Specifications
- 260 Using Modbus Communication
- 265 Modbus Function Code Details
- 267 Modbus Data Tables
- 272 Modbus Self-Diagnosis
- 274 General Peripheral Devices
- 276 Primary Parts - 208/230/240VAC
- 277 Primary Parts - 480VAC
- 278 Bypass Replacement Parts