- Home
- Domestic appliances
- Climate control
- Temperature & humidity sensors
- YASKAWA
- P7B Drive Bypass
- Manual
advertisement
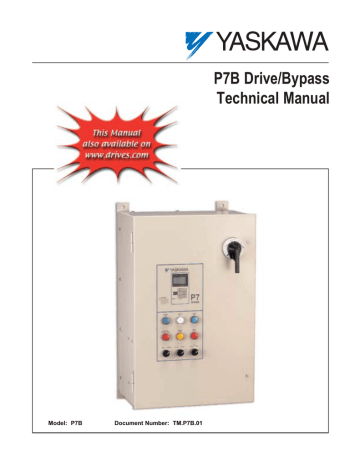
Termination Configuration - Power Wiring
The Circuit Breaker/MCP is located in the upper right hand side of the Bypass unit. The Bypass three phase input power connection is made to the input terminals of the MCP. See Figure 2.1 and 2.2 for representative examples.
Input Power
Motor
Connections Ground Lug
Input Power
Ground Lug
Fig 2.1 Typical Input Power Connection,
Wall Mount Unit
Fig. 2.2 Typical Input and Output Power
Connections, Floor Mount Unit
The OverLoad Relay (OLR) is mounted to the contactor assembly or back panel (depending on rating), just above the bypass contactor. The Bypass three phase output power connection to the motor is made to the output terminals of the OverLoad
Relay. See Figure 2.3 for representative examples.
Motor Connections
Motor Connections
Overload Relay
Fig 2.3 Typical Output Power Connection, Wall Mount Units
Electrical Installation 2 - 2
!
Field Wiring, Pressure Wire Connector, Wire Type, Range and Tightnening
Torque Specifications
D002
D003
D004
D007
D010
D016
D024
D030
D074
D088
D114
D143
D169
D211
D273
D343
D396
BYPASS MODEL NO.
BASE NUMBER
208V
_ _ _ _ -XXXX
240V
*
480V
A002 B001
A003
A004
D046
D059
A006
A009
A015
A022
A028
A042
A054
A068
A080
A104
A130
A154
A192
A248
A312
A360
B034
B040
B052
B065
B077
B096
B002
B003
B004
B007
B011
B014
B021
B027
B124
B156
B180
B240
B302
B361
B414
B477
B515
B590
MFG.
PART
NUMBER
FAL36003
FAL36007
FAL36015
FAL36030
FAL36050
FAL36100
KAL36150
KAL36250
LAL36400
MAL36600
MAL36800
CUSTOMER A.C. LINE WIRING
CURRENT
RATING
(AMPS)
3
7
CIRCUIT BREAKER
WIRE SIZE
RANGE
(AWG)
14 - 4
14 - 4
15
30
50
100
150
250
400
600
800
14 - 4
12 - 4
12 - 1/0
12 - 1/0
4 - 350 kcmil
4 - 350 kcmil
1 x (1-600 kcmil)
2 x (1-250 kcmil)
(1-3) x (3/0-500 kcmil)
(1-3) x (3/0-500 kcmil)
TIGHTENING
TORQUE
(LB.-IN.)
35
35
35
35
80
80
250
250
375
2 x 375
(1-3) x 300
(1-3) x 300
BYPASS MODEL NO.
BASE NUMBER
208V 240V
*
480V
D002 A002 B001
STANDARD BYPASS OVERLOAD RELAY
MFG.
PART
NUMBER
LR2 D13
WIRE SIZE
RANGE
(AWG)
18 - 10
TIGHTENING
TORQUE
(LB.-IN.)
15
CUSTOMER A.C. MOTOR WIRING
OR, WITH OPTION A OVERLOAD RELAYS
MFG.
PART
NUMBER
LR2 D13
WIRE SIZE
RANGE
(AWG)
18 - 10
TIGHTENING
TORQUE
(LB.-IN.)
15
D003
D004
D007
D010
D016
D024
D030
A003
A004
A006
A009
A015
A022
A028
B002
B003
B004
B007
B011
B014
B021
B027
B034
B040
LR2 D15
LR2 D15
LR2 D15
LR2 D25
LR2 D35
18 - 10
18 - 10
18 - 10
14 - 6
10 - 1/0
15
15
15
15
75
LR2 D15
LR2 D15
LR2 D15
LR2 D15
18 - 10
18 - 10
18 - 10
18 - 10
D046
D059
D074
D088
D114
D143
D169
D211
D273
D343
D396
A042
A054
A068
A080
A104
A130
A154
A192
A248
A312
A360
B052
B065
B077
B096
B124
B156
B180
B240
B302
B361
LR2 D35
LR2 D35
LR2 D35
LR2 D35
LR2 D35
LR2 D3563
LR9 F5567
LR9 F5569
LR9 F5569
LR9 F5569
LR9 F5571
LR9 F5571
LR9 F7575
LR9 F7575
LR9 F7579
LR9 F7579
LR9 F7579
10 - 1/0
10 - 1/0
10 - 1/0
10 - 1/0
10 - 1/0
10 - 1/0
6 - 3/0
6 - 3/0
6 - 3/0
6 - 3/0
6 - 300 kcmil
6 - 300 kcmil
2 x (6-300 kcmil)
2 x (6-300 kcmil)
2 x (6-300 kcmil)
2 x (6-300 kcmil)
2 x (6-300 kcmil)
200
200
200
200
275
275
2 x 500
2 x 500
2 x 500
2 x 500
2 x 500
75
75
75
75
75
100
LR2 D15
LR2 D25
LR2 D25
LR2 D35
LR2 D35
LR2 D35
LR2 D35
LR2 D35
LR9 F5567
LR9 F5569
LR9 F5569
LR9 F5569
LR9 F5571
LR9 F5571
18 - 10
14 - 6
14 - 6
10 - 1/0
10 - 1/0
10 - 1/0
10 - 1/0
10 - 1/0
6 - 3/0
6 - 3/0
6 - 3/0
6 - 3/0
6 - 300 kcmil
6 - 300 kcmil
B414
B477
B515
B590
LR9 F7581
LR9 F7581
LR9 F7581
3 x (6-300 kcmil)
3 x (6-300 kcmil)
3 x (6-300 kcmil)
3 x 500
3 x 500
3 x 500
LR9 F7575
LR9 F7575
2 x (6-300 kcmil)
2 x (6-300 kcmil)
*
The fourth underscore position in these model numbers codes for the enclosure type: V = NEMA1, B = NEMA12 FVFF.
15
15
15
15
75
75
200
200
200
200
275
275
15
15
15
75
75
75
2 x 500
2 x 500
FOR 0 TO 100 AMPS, USE 60 -75 C COPPER WIRE, AND ABOVE 100 AMPS, USE 75 C COPPER WIRE.
D074
D088
D114
D143
D169
D211
D273
D343
D396
BYPASS MODEL NO.
BASE NUMBER
208V
_ _ _ _ -XXXX
240V
*
480V
D002 A002 B001
D003
D004
D007
D010
D016
D024
D030
A003
A004
A006
A009
A015
A022
A028
D046
D059
A042
A054
A068
A080
A104
B034
B040
B052
B065
B077
B096
B124
B002
B003
B004
B007
B011
B014
B021
B027
A130
A154
A192
A248
A312
A360
B156
B180
B240
B302
B361
B414
B477
B515
B590
CUSTOMER EARTH GROUND WIRING
WIRE SIZE
RANGE
(AWG)
14 - 10
GROUND LUG
TIGHTENING
TORQUE
(LB.-IN.)
35
4 - 2/0
LC1 D18
6 - 4
LC1 D25
LC1 D32
LC1 D40
LC1 D50
LC1 D65
LC1 D80
LC1 D115
LC1 D150
LC1 F185
LC1 F265
LC1 F330
LC1 F400
LC1 F500
LC1 F630
8
18 - 8
18 - 8
14 - 6
10 - 3
10 - 3
10 - 3
10 - 2
8 - 250 kcmil
8 - 250 kcmil
6 - 3/0
6 - 300 kcmil
6 - 300 kcmil
4 - 500 kcmil
2 x (2-600 kcmil)
3 x (2-600 kcmil)
40
45
120
OR, WITH OPTION D A.C. CONTACTORS
MFG.
PART
NUMBER
LC1 D09
WIRE SIZE
RANGE
(AWG)
18 - 10
TIGHTENING
TORQUE
(LB.-IN.)
7
15
2 x 500
3 x 500
45
100
100
100
200
275
275
500
15
20
45
45
IMPORTANT
Determine the wire size for the main circuit so that line voltage drop is within 2% of the rated voltage. Line voltage drop is calculated as follows:
Line voltage drop(V) =
√
3 x wire resistance (
Ω
/km) x wire length (m) x current (A) x 10
-3
WARNING
Prior to removing any protective cover or wiring any part of the Drive, remove all power sources, including main input power and control circuit power. Wait a minimum of 5 minutes after power removal, before removing any cover. The charge lamp located within the Drive should be off prior to working inside. Even if the charge lamp is off, one must measure the AC input, output, and DC Bus potential to insure safe levels prior to resuming work. Failure to adhere to this warning may result in personal injury or death.
Electrical Installation 2 - 3
!
Cable Length between Drive and Motor
The Bypass unit should be installed as close as possible to the motor to minimize the length of load side power cable needed between the Drive and the motor. If the cable between the Drive and the motor is long, the high-frequency leakage current will increase, causing the Drive output current to increase as well. This may affect peripheral devices. To prevent this, reduce cable length, or if necessary, adjust the carrier frequency (set in C6-02) as shown in Table 2.1.
The line side power cables, load side power cables and the control wiring should all be run in a separate conduit. Careful attention to this recommended design practice will avoid many potential motor and Drive related problems.
Motor Cable Length
Table 2.1 Motor Cable Length vs. Carrier Frequency (C6-02)
164 ft. (50m) maximum 328 ft. (100m) maximum More than 328 ft.(100m)
Carrier Frequency 15kHz maximum 10kHz maximum 5kHz maximum
(See the limitations on carrier frequency, based on Drive capacity and model number in Appendix B).
Electrical Installation 2 - 4
!
Grounding
"
Drive and Motor Ground Wire Landing
The Drive ground lug (terminal ) is connected to the enclosure. The enclosure ground lug must be connected to earth ground. See Figures 2.1 and 2.2.
The Drive has a second ground lug to accept the motor ground lead. See Figure 2.9.
"
Ground Wiring Precautions
Observe the following precautions when connecting the ground wire:
1.
208-240 VAC Drives should have a ground connection with resistance of less than 100
Ω
..
2.
480 VAC Drives should have a ground connection with resistance of less than 10
Ω
..
3.
Do not share the ground wire with other devices, such as large-current electrical equipment.
4.
Always use a ground wire that complies with technical standards on electrical equipment and minimize the length of the ground wire. Leakage current flows through the Drive. Therefore, if the distance between the ground rod and the ground terminal is too long, potential on the ground terminal of the Drive will become unstable.
5.
When using more than one Drive, be careful not to loop the ground wire.
OK NO
Fig 2.4 Ground Wiring Examples
For grounding connection to earth ground see Figures 2.1 and 2.2.
"
Control Circuit Ground Terminals
The removable Drive control terminal card provides two ground terminals (marked TB3 and TB4) to accept the control wire shield connection. The control wire shield should be connected on this end only, the opposite end should be isolated with electrical tape.
IMPORTANT
Grounding of the Bypass enclosure and motor is required for proper system operation.
Electrical Installation 2 - 5
!
Wire Routing
The following Figures indicate suggested wire entry and bending areas for representative wall mount enclosures.
Control circuit wiring
Motor connection
Input power
Control circuit wiring
Motor connection
Input power
Typical Enclosure 2
Fig 2.5 Wall Mount Enclosures
Typical Enclosure 2
Electrical Installation 2 - 6
!
Drive Main Circuit Configurations 208-240 VAC
The main circuit configurations of the Drive are shown in Tables 2.2 and 2.3.
Table 2.2 Drive Main Circuit Configurations
208-240 VAC
CIMR-_ _ _ 20P4 to 2018
(1/2 Hp to 25 Hp)
CIMR-_ _ _ 2022 and 2030
(30 Hp to 40 Hp)
Note
1
{
Notes
1 & 3
{
Power supply
Control circuits
Power supply
Control circuits
CIMR-_ _ _ 2037 to 2110
(50 Hp to 150 Hp)
Notes
1 & 3
{
---
Power supply
Control circuits
Note1. Input fuses or molded case circuit breakers are required for proper branch circuit protection for all Drives. Failure to use recommended fuses/circuit breakers (See Appendix E) may result in damage to the wiring, Drive and/or personal injury.
2. Control power is supplied internally from the main circuit DC power supply for all Drives.
3. Consult your Yaskawa representative before using 12-pulse rectification.
Electrical Installation 2 - 7
!
P7 Drive Main Circuit Configurations 480 VAC
Table 2.3 Drive Main Circuit Configurations
480 VAC
CIMR-_ _ _ 40P4 to 4018
(1/2 Hp to 30 Hp)
CIMR-_ _ _ 4030 to 4055
(40 Hp to 100 Hp)
Note
1
{
Notes
1 & 3
{
Power supply
Control circuits
Power supply
Control circuits
Notes
1 & 3
{
CIMR-_ _ _ 4075 to 4160 and CIMR-_ _ _ 4185 to 4300
(125 Hp to 500 Hp)
3
Power supply
Control circuits
---
Note1. Input fuses or molded case circuit breakers are required for proper branch circuit protection for all Drives. Failure to use recommended fuses/circuit breakers (See Appendix E) may result in damage to the wiring, Drive and/or personal injury.
2. Control power is supplied internally from the main circuit DC power supply for all Drives.
3. Consult your Yaskawa representative before using 12-pulse rectification.
Electrical Installation 2 - 8
advertisement
Related manuals
advertisement
Table of contents
- 14 Bypass Model Number and Enclosure Style
- 16 Enclosure Data
- 19 Confirmations upon Delivery
- 21 Bypass Product Options
- 23 Bypass Component Descriptions
- 29 Exterior and Mounting Dimensions
- 36 Checking and Controlling Installation Site
- 40 Termination Configuration - Power Wiring
- 47 Control Wiring
- 58 Wiring Diagram
- 60 Logic Diagram
- 66 Digital Operator and Control Panel Display
- 72 Drive Main Menus
- 80 Example of Changing a Parameter
- 84 Start Up Introduction
- 85 Bypass Start Up Preparation
- 86 Bypass Unit Start Up Procedure
- 90 Bypass Operation Description
- 96 Bypass Basic Programming Parameters
- 182 Bypass Diagnostics
- 183 Drive Diagnostics
- 196 Drive Troubleshooting
- 202 Drive Main Circuit Test Procedure
- 206 Drive Date Stamp Information
- 208 Maintenance
- 215 Removing and Replacing Drive in a Bypass Unit
- 220 Parameter List
- 244 Monitor List
- 246 Fault Trace List
- 247 Fault History List
- 250 Drive Capacity
- 256 Standard Drive and Bypass Specifications
- 260 Using Modbus Communication
- 265 Modbus Function Code Details
- 267 Modbus Data Tables
- 272 Modbus Self-Diagnosis
- 274 General Peripheral Devices
- 276 Primary Parts - 208/230/240VAC
- 277 Primary Parts - 480VAC
- 278 Bypass Replacement Parts