Hydac PB HAT 1400 SAE J1939 E Operating/Maintenance Manual
Add to My manuals19 Pages
Hydac PB HAT 1400 SAE J1939 E is a single turn angle sensor capable of measuring the current turning angle with 1 kHz sample rate, 0.1% accuracy and 14-bit resolution.
It can convert the angle value to a linear process value, and send the current process value cyclically or on request. The device can be configured via CAN 2.0 B interface according to SAE-J1939 standards. Each HAT has a unique name and address, configurable by the user. The configuration process includes setting the baud rate, transmission rate, process value visualization, operation mode, and more.
Some possible use cases for the Hydac PB HAT 1400 SAE J1939 E include:
advertisement
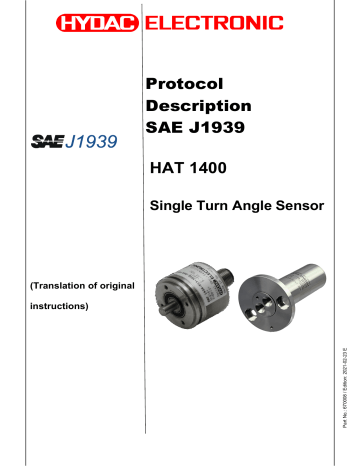
(Translation of original instructions)
Protocol
Description
SAE J1939
HAT 1400
Single Turn Angle Sensor
E
2
Content
Protocol description SAE J1939 HAT 1400
1 Introduction _______________________________________________________ 4
1.1
1.2
Functions .............................................................................................................. 4
Interfaces .............................................................................................................. 4
2 Address Claiming ___________________________________________________ 4
2.1
General overview ................................................................................................. 4
2.2
Name ..................................................................................................................... 4
2.2.1
Addressing ability _____________________________________________________________ 4
2.2.2
Function specific sections ______________________________________________________ 4
2.2.3
Manufacturer specific sections __________________________________________________ 5
2.3
Address ................................................................................................................. 5
2.4
Start-up process ................................................................................................... 5
3 Configuration ______________________________________________________ 6
3.1
Short description of the configuration message ............................................... 6
3.2
Complete list of settings (Object List "OL") ...................................................... 7
3.2.1
Profile _______________________________________________________________________ 7
3.2.2
General information ____________________________________________________________ 7
3.2.3
Name sections ________________________________________________________________ 8
3.2.4
Process value transmission _____________________________________________________ 8
3.2.5
Process value visualisation _____________________________________________________ 8
3.2.6
Operation Data ________________________________________________________________ 9
3.3
Process value transmission ................................................................................ 9
3.3.1
Angle value ___________________________________________________________________ 9
3.4
Process value visualisation ................................................................................ 9
3.5
Sending process values .................................................................................... 10
3.5.1
Sending process values (cyclically) _____________________________________________ 10
3.5.2
Send process values (on request) _______________________________________________ 11
4 Carry out configuration _____________________________________________ 12
4.1
The design of the configuration message is PGN 61184 (0x00EF00) . .......... 12
4.1.1
Structure of the SAE J1939 29-BIT CAN-ID ________________________________________ 12
4.1.2
Description PGN 61184 "Proprietary A" __________________________________________ 12
4.1.3
Description of the specific data block of PGN 61184 ________________________________ 13
4.1.4
Description "Acknowledge Code" of the configuration message _____________________ 13
4.2
ACK - Acknowledgement message .................................................................. 13
4.3
Commands.......................................................................................................... 14
4.3.1
Start editing mode ____________________________________________________________ 14
4.3.2
Saving the settings ___________________________________________________________ 14
4.3.3
Reset to factory default settings ________________________________________________ 15
4.3.4
Restart ______________________________________________________________________ 15
4.4
Example configuration process ........................................................................ 15
4.4.1
Example: Read out profile number ______________________________________________ 15
4.4.2
Example: Edit Baud rate _______________________________________________________ 16
4.4.3
Example: Reading the serial number _____________________________________________ 17
4.4.4
Example: Setting of transmission rate ___________________________________________ 17
4.4.5
Example: Read out operation mode ______________________________________________ 17
5 Miscellaneous _____________________________________________________ 18
5.1
Read out software identification ....................................................................... 18
Edition: 2021-02-23 HYDAC ELECTRONIC GMBH Part No.: 670008
Protocol description SAE J1939 HAT 1400
Preface
3
This manual provides you, as user of our product, with key information on the operation and maintenance of the equipment.
It will acquaint you with the product and assist you in obtaining maximum benefit in the applications for which it is designed.
Keep the manual in the vicinity of the instrument for immediate reference.
Please note: the specifications given in this documentation regarding the instrument technology were correct at the time of publishing.
Modifications to technical specifications, illustrations and dimensions are therefore possible.
If you discover errors while reading the documentation or have additional suggestions or tips, please contact us at:
HYDAC ELECTRONIC GMBH
Technical Documentation
Hauptstrasse 27
66128 Saarbruecken
-Germany-
Phone: +49(0)6897 / 509-01
Fax: +49(0)6897
Email: [email protected]
We look forward to receiving your input.
“Putting experience into practice”
E
Edition: 2021-02-23 HYDAC ELECTRONIC GMBH Part no.: 670008
E
4
1 Introduction
Protocol description SAE J1939 HAT 1400
1.1 Functions
HAT 1400 is a single turn angle sensor for the determination of the absolute angle within a range of 0 to 360°.
Measuring the current turning angle using:
-
1kHz sample rate
-
Accuracy 0.1 % typ.
- bit
Conversion of the angle value into a user-scaleable linear process value.
Sending the current process value:
-
Cyclically, within the range from 1 millisecond to 1 minute
1.2 Interfaces
HAT has a CAN 2.0 B interface and can be operated according to the process defined in the standards SAE-J1939. The interface functions are divided into 3 parts:
Address Claiming
Configuration
Sending process values
2 Address Claiming
2.1 General overview
Each HAT has a name and an address. Both can be configured by the user. The name of the HAT is a 64 bit value and is clearly recognisable worldwide, the address is a 8 bit value which must be clearly recognisable at the bus. This means, it is not allowed to have two devices with the same address connected to the same bus.
During Address Claiming the HAT communicates its address and name to the other bus participants. This is a reaction to eventual address conflicts.
2.2 Name
The name consists of the following parts:
1 Bit Arbitrary Address Capable
2.2.2 Function specific sections
The function specific sections are configurable.
3 Bit Industrial Group (i.e. Global, Marine, Agriculture, ...)
7 Bit Vehicle System (depends on Industrial Group: Tractor, trailer, …)
4 Bit Vehicle System Instance (sequence number for systems of the same kind)
8 Bit Function (depending on Industrial Group: i.e. System Display, Levelling System, …)
5 Bit Function Instance (sequence number for functions of the same kind)
3 Bit ECU-Instance (sequence number for controllers having the same function)
Edition: 2021-02-23 HYDAC ELECTRONIC GMBH Part no.: 670008
Protocol description SAE J1939 HAT 1400
2.2.3 Manufacturer specific sections
11 Bit Manufacturer Code
21 Bit Idendity
The function-related parts are configurable, the manufacturer-related parts are firmly defined. This ensures a worldwide clear address identification.
5
2.3 Address
The address can be set between 1 and 253. The address 254 is reserved for the status "no address assigned", the value 255 is used as broadcast address.
In each message the HAT sends, the address is assigned to the lowest 8 bits of the message ID. The pre-defined address is 1 see chapter 3.2 „Complete list of settings (Object
List
"OL")
“ OL-Index 1.
2.4 Start-up process
After each start-up, the HAT sends an "Address Claimed" message (i.e.: 0x18EEFF01
[<name>]).. Thus, it communicates its address and its name to the other participants. This message can also be requested by other participants using a "request" message.
If an other participant sends an "Address Claimed" message using the same address, the reaction of the HAT depends on the name of the other participant. If the HAT has a name with a higher priority, it again sends an "Address Claimed" message. If the HAT sends a higher address, it sends a "Cannot Claim" message and will then no more be available. In order to carry out a device reset, HAT must be briefly disconnected from the supply voltage.
After sending an "Address Claimed" message, it takes 250 ms until the HAT takes up its regular operation mode. This is one of the requirements of SAE-J1939 to give other devices having the same address enough time to respond.
E
HAT is a "Service Configurable Device". This means, the address is adjustable, but the HAT cannot be assigned a new address in normal bus mode. Going through a configuration process, HAT must be assigned a clearly defined address for its later bus, before it is getting connected to the bus for normal operation. The configuration process is described in the next chapter.
If 3 devices having the same address are connected to the bus, two of them will always send a "Cannot Claim" message which is sent out at the same time in the worst case. This can lead to a bus error. For this reason, the user must make sure that the address at the bus is clearly defined.
Edition: 2021-02-23 HYDAC ELECTRONIC GMBH Part no.: 670008
6 Protocol description SAE J1939 HAT 1400
3 Configuration
The HAT has different settings which can be read and written by a master using SAE-J1939 messages. This is carried out by means of a so-called proprietary parameter group A with the PGN 61184 (0x00EF00). The data then contain information on which settings must be read or written and information on the values themselves as well.
All settings are managed in an object list OL (similar to CANopen). All configuration objects in this list have a clear index, by means of which they can be addressed individually. Some of the objecs represent device settings which can also be changed by the operator. In the table described in the following, all the objects or settings with their corresponding index are listed. The object access can only be defined as "read only" (ro) or "read and write" (rw).
Objects representing the device settings are generally changeable (rw).
The device configuration process will be defined in detail in chap 4 "Carry out configuration"
E
3.1 Short description of the configuration message
The configuration message serves to read or write entries in the object list. Here, the data range of the configuration message (PGN 61184) is subdivided as follows:
Index r/w dc ack Value
(Byte 1) (Byte 2) (Byte 3) (Byte 4) (Byte 5) (Byte 6) (Byte 7) (Byte 8)
Name Byte Content
Index 1 Index of the object in the object list "OL" r/w 2 Read or write access, 0=read, 1=write dc ack
3
4
"Don’t care", always 0
Acknowledge code, see table 4.1.4 description of "Acknowledge
Code"
Value 5-8 Used data, "Little Endian" format
The user data range "Value" of the configuration message will be defined using the data type of the OL (object list). The data type defines the number of used data bytes. The number is represented in "Little-Endian" which means the least significant data byte (LSB) will be located at the lowest address (byte 5).
In a uint16 value, for example, only the first two bytes (byte 5 and byte 6) of the value range of the configuration message are used and interpreted as unsigned 16 bit integer value.
Edition: 2021-02-23 HYDAC ELECTRONIC GMBH Part no.: 670008
Protocol description SAE J1939 HAT 1400
Datatype uint8
Bit
8
7
Value
(Byte 5) (Byte 6) (Byte 7) (Byte 8)
LSB x x x uint16 16 LSB MSB x x uint32 32 bool8 8 LSB x x x string[4] 32 [0] [1] [2] [3]
LSB: Least Significant Bit/Byte
Significant x Byte is not used.
3.2 Complete list of settings (Object List "OL")
E
In the following table, all the settings with their corresponding index and their supported access type (read only "ro", or read & write "r/w") are listed.
The default values for Index 1, 2, 6, 11 – 16, 21 – 26, 33 – 34 depend on the part number and are listed as an example below.
3.2.1 Profile
Default value
Scope of application
Index Data type r/w Settings
0 uint16 ro
Profile number
(defines the layout of the setting table)
3 -
Index Data type r/w Settings
1
2 uint8 uint8 rw Source Address rw
Baudrate index, see table
4.4.2a Baudrate index
3 string[0..3] ro Device Id character 0..3
4 string[4..7] ro Device Id character 4..7
5
6
7 string[4] uint32 uint32 ro ro ro
Versions and release number as characters
Part number,
32 Bit number
Serial number, 32 Bit number
Default value
1
3 (250 kBit)
"HAT1"
"000\0"
-
-
-
Scope of application
[1, 253]
[0, 8] \ {5}
-
-
-
-
-
Edition: 2021-02-23 HYDAC ELECTRONIC GMBH Part no.: 670008
8 Protocol description SAE J1939 HAT 1400
E
Index
11
12
13
14
15
16
Data type r/w
Settings uint8 rw 3 Bit Industrial Group uint8 rw 7 Bit Vehicle System uint8 rw
4 Bit Vehicle System
Instance uint8 rw 8 Bit Function uint8 rw 5 Bit Function Instance uint8 rw 3 Bit Control Unit Instance
3.2.4 Process value transmission
Index
21
22
23
24
25
26
Data type r/w
Settings uint16 rw
Transmission Rate [ms],
16Bit uint8 rw Message length [Bytes], 4..8 uint8 rw Priority, (0..7) uint8 rw PDU format (1 Byte) uint8 rw PDU Specific (1 Byte) uint8 rw
Offset of the measured variable in the message
[bytes]
3.2.5 Process value visualisation
Index
31
32
33
34
35
36
Data type r/w
Settings uint8 ro Unit (6: °) uint8 ro Data length in bytes uint32 int32 int32 int32 rw rw ro ro
Resolution per digit with 3 decimal places100 ppm is equal to 0.100°
Offset of the process value with 3 decimal places.
100000 is equal to 100.000°
Lower measuring range with
3 decimal places 0 is equal with 0.000 °
Upper measuring range with
3 decimal places 360000 is equal to 360.000°
Default value
0 (Global)
0x7F
0
0xFF
0
0
Default value
100
8
6
0xFF
0x00
0
Default value
6 (°)
4
100
0
0
360000
Scope of application
[0, 7]
[0, 127]
[0, 15]
[0, 255]
[0, 31]
[0, 7]
Scope of application
[0, 0xFFFF]
[4, 8]
[0, 7]
[0, 0xFF]
[0, 0xFF]
[0, 4]
Scope of application
[6, 6]
-
[1, 0xFFFFFFFF]
[-1000000000,
1000000000]
-
-
Edition: 2021-02-23 HYDAC ELECTRONIC GMBH Part no.: 670008
Protocol description SAE J1939 HAT 1400
Examle Etry Index 33, resolution per digit:
The device accepts values of 1 up to the maximum value of the data type uint32
(0xFFFFFFFF).
Useful settings would be:
1000 = 1° per Digit (Process value range 0 to 360)
100 = 0.1° per Digit (Process value range 0 to 3600) or
10 = 0.01° per Digit (Process value range 0 to 36000)
9
Index
51
52
Data type r/w
Settings uint32 ro Process value uint8 + uint16 ro
Operation mode / status code
Default value
-
-
Scope of application
-
-
3.3 Process value transmission
The following tables describe how the process values (measured values) are transmitted as groups within a PGN. The specific PGN for the group is defined via the OL (Object List), see for example chapter 3.2.4 Process value transmission, OL Index 23 and 24.
The used data format is "Little-Endian", which means the least significant data byte will be located at the lowest data block byte address.
E
Transmission rate
Data length of the message
Priority
On request or cyclic; chap.: 3.2.4 OL Index 21
4 .. 8
0 .. 7
Extended Data Page, Data Page 0, 0
PDU Format, Specific, Priority see OL (chap.:3.2.4) OL Index 24, 25, 23
Start pos.
OL Index 26, see chap. 3.2.4
Length
4 Byte
Description
Angle value
3.4 Process value visualisation
The process or measured value sent via SAE J1939, is always positive
(0..0xFFFFFFFD). If the factory-set upper or lower measuring range is negative, an offset must be set in order to enable sending of the measured value.
Edition: 2021-02-23 HYDAC ELECTRONIC GMBH Part no.: 670008
E
10 Protocol description SAE J1939 HAT 1400
Example angle 0 .. The current process value must be sent in steps of 0.1°. This means, a value of 1000 corresponds with 100° This leads to the following settings
Process value visualisation Value
Unit
Data length in bytes
Resolution per LSB
Offset of the process value
Lower measurement range
[°]
4
100 (0.1 °), see chap.3.2.5 OL Index
33
0 ( 0.000 °)
0 ( 0.000 °)
Upper measurement range 360000 ( 360.000 °)
3.5 Sending process values
3.5.1 Sending process values (cyclically)
The device sends its process values (measured values) cyclically with the PGN which is set in the OL (Object List). a. Structure of the Process value PGN
Transmission rate
Data length of the message
Extended Data Page (EDP)
Data Page (DP)
PDU format
Chapter 3.2 OL Index 21
If the " Transmission Rate" in the Object List has a value greater than 0, the corresponding PGN will be sent cyclically.
The transmission rate is indicated in [ms].
8
0
0
Chapter 3.2 OL Index 24
PDU specific
Priority
Offset
Chapter 3.2 OL Index 25
Chapter 3.2 OL Index 23
Chapter 3.2 OL Index 26
The values 0xFFFF and 0xFFFE are reserved for SAE J1939. This means, the measured value at the lower measuring range limit must be greater than or equal to 0 and the value at the upper measuring range limit must be lower than or equal to 4294967293. If the value 0xFFFE is sent, this means "Error" according to SAE J1939 and the device mode and the device status will be set accordingly.
Edition: 2021-02-23 HYDAC ELECTRONIC GMBH Part no.: 670008
Protocol description SAE J1939 HAT 1400
3.5.2 Send process values (on request)
11
The device sends its process values (measured values) on request via a request message
(PGN 59904 (0x00EA00)) by means of the PGN which has been set in the user setup
(Object List).
(see chap.: 3.2 OL Index 23-25) a. Structure Request message
Transmission rate
Data length of the message
Extended Data Page (EDP)
Data Page (DP)
PDU format
On request should be set to 3 during request (PGN: 59904), the answer generally has a DLC of 8 bytes.
0
0
234 (0xEA)
PDU specific
Priority
Device address (see chap.:3.2.2) or "Global
Address" = 255 (0xFF)
6
If "Transmission Rate" (OL Index 21) is 0, the corresponding PGN is sent exclusively on request.
In the SAE J1939-21 it is recommended not to exceed more than
2-3 master requests per second.
E b. Example: Process value "3.3.1 Angle value" on request
Master: Request PGN 59904 on HAT with device address 1 (0x00EA01)
DLC:3 (s. OL Index 1, 24, 25)
PGN
LSB
PGN
LSB +1
PGN
MSB
(Byte 1) (Byte 2) (Byte 3) (Byte 4) (Byte 5) (Byte 6) (Byte 7) (Byte 8)
HAT: Response PGN 65280 (0x00FF00) DLC:8
( 141.6° angle degree (0x588 = 1416d) [visualisation at a resolution of 0.1° (OL Index
33)])
Structure of the response see chapter 3.5.1.1 "Structure of process value PGN"
Angle
LSB
Angle
LSB+1
Angle
LSB+2
Angle
MSB
(Byte 1) (Byte 2) (Byte 3) (Byte 4) (Byte 5) (Byte 6) (Byte 7) (Byte 8)
0x88 0x05 0x00 0x00 x x x x
Edition: 2021-02-23 HYDAC ELECTRONIC GMBH Part no.: 670008
E
12 Protocol description SAE J1939 HAT 1400
4 Carry out configuration
To read or write the settings, the master sends a message with the PGN 61184 (0x00EF00) to the HAT's address. HAT responds by the same PGN (parameter group number) and sends an acknowledge code.
In case of reading requests the requested data are written into the value range of the response.
Procedure for the permanent change of settings must be strictly adhered to:
„Start editing mode“, see commands chap. 4.3.1
Reading and writing of the desired Object List Entries
"Saving the settings", see commands chap. 4.3.2
"Restart", see commands chap. 4.3.4
Please note:
The reading of entries from the Object List (OL) can be carried out directly.
4.1 The design of the configuration message is PGN 61184 (0x00EF00) .
HAT uses the PGN 61184 „Proprietary A“ for the configuration of the device settings. This special PGN is intended for the customised communication according to SAE J1939-21.
The PGN is part of the specific parameter groups which means the "PDU Specific" part of the PGN contains the address of the target device, in our case the device address of the
HAT.
4.1.1 Structure of the SAE J1939 29-BIT CAN-ID
Bitposition
29 Bit ‐ ID
28
Priority
26 25 24 23
EDP DP
16 15
Parameter Group Number (PGN)
PDU Format
< 0xF0
>=0xF0
PDU Specific
Destination Adress
Group Extension
8 7
Source Address
4.1.2 Description PGN 61184 "Proprietary A"
Transmission rate
Data length of the message
Extended Data Page (EDP)
Data Page (DP)
PDU format
PDU specific
Priority
On request
8
0
0
239 (0xEF)
HAT device address see chap.: 3.2.2 OL Index 1
6
0
Edition: 2021-02-23 HYDAC ELECTRONIC GMBH Part no.: 670008
Protocol description SAE J1939 HAT 1400
4.1.3 Description of the specific data block of PGN 61184
Index
(Byte 1) r/w
(Byte 2) dc
(Byte 3) ack
(Byte 4) (Byte 5) (Byte 6)
Value
(Byte 7)
Name Byte Content
Index r/w dc ack
Value
0
1
Index of the object in the object list "OL"
Read or write access, 0=read, 1=write
(Byte 8)
2
3
"Don’t care", always 0
Acknowledge code, see table 4.1.4 description of "Acknowledge
Code"
4-7 Used data, "Little Endian" format
13
E
5
6
3
4
0
1
2
4.1.4 Description "Acknowledge Code" of the configuration message
Byte 4 "ack" of the configuration message (PGN 61184) will be defined by the query processing depending on the HAT. If requested by the master, this byte is always 0.
Byte 4 Description of "Acknowledge Code"
OK; always set to 0 in the case of requests
Parameters read only
Value too high
Value too low
Index does not exist
Error while saving parameters
Error while restoring parameters
4.2 ACK - Acknowledgement message
If the Master calls a PGN which is not supported by the HAT, it will send an
"Acknowledgement message" with the PGN 59392 (0x00E800).
Byte Content
0
1
Control Byte with the value 1
(Negative Acknowledgement NACK)
Group Function Value (optional, always 0)
2, 3
4
5..7
Reserved, always 0xFF
Adress of the NACK trigger
The requested PGN
Edition: 2021-02-23 HYDAC ELECTRONIC GMBH Part no.: 670008
14 Protocol description SAE J1939 HAT 1400
4.3 Commands
Commands are a special function with the configuration They are handled via the PGN
61184 as well. In contrast to the general entries in the Object List (OL), writing on a control command index triggers a function in the device.
E
4.3.1 Start editing mode
Before the settings are written, the master must set the HAT to an editing mode. This is carried out by writing the string "edit" into the Index 101. In the editing mode, HAT reacts exclusively to configuration commands. In the editing mode no measured values can be sent. The editing mode therefore always has to be finished by a restart.
Prior to restarting, the changes must be explicitly saved (Index 102). If restart is carried out without saving, all changes will be lost!
Master
Index
(Byte 1)
101
HAT
Index
(Byte 1) r/w
(Byte 2)
1 r/w
(Byte 2) dc
(Byte 3)
0 dc
(Byte 3) ack
(Byte 4)
0 ack
(Byte 4)
Value ( "edit“)
(Byte 5) (Byte 6) (Byte 7) (Byte 8)
0x65 "e" 0x64 "d" 0x69 "i" 0x74 "t"
(Byte 5) (Byte 6)
Value
(Byte 7) (Byte 8)
4.3.2 Saving the settings
The changed settings will not automatically become persistent, which means, they will not be stored permanently. For this purpose, an extra storage process needs to be carried out explicitly. This is carried out by writing the string "save" into the Index 102.
Master
Index r/w dc ack Value ( „save“)
(Byte 1)
102
(Byte 2)
1
(Byte 3)
0
(Byte 4)
0
(Byte 5) (Byte 6) (Byte 7) (Byte 8)
0x73 "s" 0x61 "a" 0x76 "v" 0x65 "e"
HAT
Index
(Byte 1) r/w
(Byte 2) dc
(Byte 3) ack
(Byte 4) (Byte 5) (Byte 6)
Value
(Byte 7) (Byte 8)
Edition: 2021-02-23 HYDAC ELECTRONIC GMBH Part no.: 670008
Protocol description SAE J1939 HAT 1400
4.3.3 Reset to factory default settings
15
The settings can be reset to factory default settings at any time. For this purpose, the string
"load" must be written into Index 103.
Master
Index r/w dc ack Value ( „load“)
(Byte 1) (Byte 2) (Byte 3) (Byte 4) (Byte 5) (Byte 6) (Byte 7) (Byte 8)
103 1 0 0 0x6C 0x6F "o" 0x61 "a" 0x64 "d"
HAT
Index r/w dc ack Value
(Byte 1) (Byte 2) (Byte 3) (Byte 4) (Byte 5) (Byte 6) (Byte 7) (Byte 8)
E
4.3.4 Restart
A restart is carried out by briefly disconnecting HAT from the power supply. A restart can also be carried out by writing the string "boot" into the index 104.
Master
Index r/w dc ack Value ( "boot")
(Byte 1)
104
(Byte 2)
1
(Byte 3)
0
(Byte 4)
0
(Byte 5) (Byte 6) (Byte 7) (Byte 8)
0x62 "b" 0x6F "o" 0x6F "o" 0x74 "t"
4.4 Example configuration process
Configuration message: For all subsequent examples the previously described PGN is
61184 (0x00EF00), in case of a successful request, the HAT responds by using the same
PGN.
4.4.1 Example: Read out profile number
All the settings of one device are combined in one profile. By reading of Index 0 of the
Object List (OL) the 2 bytes long profile number is sent, HAT has profile number 3.
Master
Index r/w dc ack Value
(Byte 1) (Byte 2) (Byte 3) (Byte 4) (Byte 5) (Byte 6) (Byte 7) (Byte 8)
HAT
Index r/w dc ack Value ( 4
)
(Byte 1) (Byte 2) (Byte 3) (Byte 4) (Byte 5) (Byte 6) (Byte 7) (Byte 8)
0 0 0 0 3 0 0 0
Edition: 2021-02-23 HYDAC ELECTRONIC GMBH Part no.: 670008
E
16
4.4.2 Example: Edit Baud rate
Protocol description SAE J1939 HAT 1400
The Baud rate is set via a Baud rate index. The parameter is located on the OL Index 2 of the OL. In the example the Baud rate 500 kBit/s is set (Baud rate index 2). A new Baud rate will not be saved before the Baud rate index has been changed, saved and the device has been restarted.
Master
Index r/w dc ack Value ( 2 = 500 kBit/s)
(Byte 1) (Byte 2) (Byte 3) (Byte 4) (Byte 5) (Byte 6) (Byte 7) (Byte 8)
2 1 0 0 2 0 0 0
HAT
Index
(Byte 1) r/w
(Byte 2) dc
(Byte 3) ack
(Byte 4) (Byte 5)
Value (
(Byte 6)
4)
(Byte 7) (Byte 8)
6
7
8
3
4
5 a. Baud rate index
HAT supports Baud rates of 10 kBit up to 1 MBit, according to the following table (OL Index
2 "Baud rate index"):
Index Baud rate
0 1000 kBit
1
2
800 kBit
500 kBit
250 kBit
125 kBit reserved / not used
50 kBit
20 kBit
10 kBit
Edition: 2021-02-23 HYDAC ELECTRONIC GMBH Part no.: 670008
Protocol description SAE J1939 HAT 1400
4.4.3 Example: Reading the serial number
By writing onto the OL Index 7 the serial number can be read out.
Master
Index r/w dc ack Value
(Byte 1) (Byte 2) (Byte 3) (Byte 4) (Byte 5) (Byte 6) (Byte 7) (Byte 8)
17
HAT (PGN 61184)
Index r/w dc ack Value ( 0x12345678 [305.419.896d])
(Byte 1) (Byte 2) (Byte 3) (Byte 4) (Byte 5) (Byte 6) (Byte 7) (Byte 8)
7 0 0 0 0x78 0x56 0x34 0x12
4.4.4 Example: Setting of transmission rate
By writing onto the OL Index 21 the transmission rate for the statistical inclination can be set to 150 ms (0x96 hex).
Master
Index r/w dc ack Value ( 0x96 [150d])
(Byte 1) (Byte 2) (Byte 3) (Byte 4) (Byte 5) (Byte 6) (Byte 7) (Byte 8)
21 1 0 0 0x96 0 0 0
HAT (PGN 61184)
Index r/w dc ack Value
E
(Byte 1) (Byte 2) (Byte 3) (Byte 4) (Byte 5) (Byte 6) (Byte 7) (Byte 8)
21 1 0 0 0 0 0 0
4.4.5 Example: Read out operation mode
The device mode and the device status display the status of the device.
By reading the OL Index 53, the operation mode can be read out.
The OL-Index 53 provides the operation mode (1 Byte) and the status code (2 Bytes).
Master
Index r/w dc ack Value
(Byte 1) (Byte 2) (Byte 3) (Byte 4) (Byte 5) (Byte 6) (Byte 7) (Byte 8)
53 0 0 0 0 0 0 0
HAT (PGN 61184) Device is in the "operational" mode.
Index r/w dc ack
Value ( 0x96 [150d])
Operation Device status
(Byte 1) (Byte 2) (Byte 3) (Byte 4) mode (Byte 5) (Byte 6) (Byte 7)
(Byte 8)
53 0 0 0 0 0 0 0
Edition: 2021-02-23 HYDAC ELECTRONIC GMBH Part no.: 670008
E
18 Protocol description SAE J1939 HAT 1400 a. Operation mode (see OL Index 53)
In case of multiple errors, the status will result from an or-operation of the error values.
Mode
0
2
2
2
2
3
Error
No Error
Error while loading UserSetup
Error while storing UserSetup
Faulty configuration of the Process value visualisation.
Faulty configuration of the Process value transmission data.
Measured signal error
Status
-
Bit 1
Bit 3
Bit 4
Bit 5
Bit 2
5 Miscellaneous
5.1 Read out software identification
The Software Identification (Version number) can be requested by means of a J1939 request message located on PGN 65242 (0x00FEDA).
The device responds by sending the software identification PGN 65242 (0x00FEDA).
Example depending on software version:
Byte 1 Byte 2 Byte 3 Byte 4 Byte 5 Byte 6 Byte 7 Byte 8
1 "V" "0" "5" "." "0" "2" "*"
Edition: 2021-02-23 HYDAC ELECTRONIC GMBH Part no.: 670008
Protocol description SAE J1939 HAT 1400
HYDAC ELECTRONIC GMBH
Hauptstr. 27
D-66128 Saarbruecken
Germany
Web: www.hydac.com
E-mail: [email protected]
19
Fax.: +49 (0)6897 509-1726
HYDAC Service
If you have any questions concerning repair work, please do not hesitate to contact HYDAC
SYSTEMS & SERVICES:
HYDAC SYSTEMS & SERVICES GMBH
Hauptstr. 27
D-66128 Saarbruecken
Germany
Phone: +49 (0)6897 509-1936
Fax: +49 (0)6897 509-1933
Note
The information in this manual relates to the operating conditions and applications described. For applications or operating conditions not described please contact the relevant technical department.
If you have any questions or suggestions or encounter any problems of a technical nature, please contact your HYDAC representative.
Subject to technical modifications.
E
Edition: 2021-02-23 HYDAC ELECTRONIC GMBH Part no.: 670008
advertisement
Related manuals
advertisement
Table of contents
- 4 Introduction
- 4 Functions
- 4 Interfaces
- 4 Address Claiming
- 4 General overview
- 5 Address
- 5 Start-up process
- 6 Configuration
- 6 Short description of the configuration message
- 7 Complete list of settings (Object List "OL")
- 9 Process value transmission
- 9 Process value visualisation
- 10 Sending process values
- 12 Carry out configuration
- 12 The design of the configuration message is PGN 61184 (0x00EF00)
- 13 ACK - Acknowledgement message
- 14 Commands
- 15 Example configuration process
- 18 Miscellaneous
- 18 Read out software identification