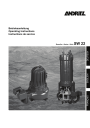
advertisement
▼
Scroll to page 2
of
41
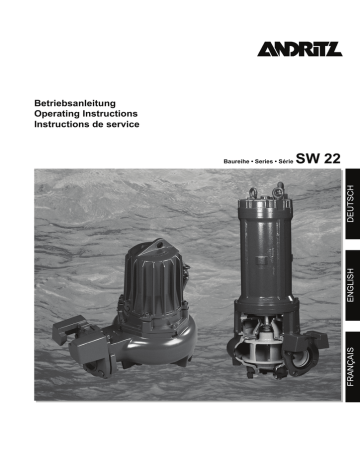
Betriebsanleitung Operating Instructions Instructions de service ENGLISH SW 22 Seite 3 3.4 Motor .................................................................................................................................................................................... 5 2.2 Konservieren 2.1 4 3.1 N M TH TV Motor Laufradformen 3.2.3 3.4 5 3.4.2 AM1 DOL AM2 DOL AM3A B Y 1 2 Y 1 2 DOL Y 1 2 AM3B DOL Y 1 2 AM3C DOL Y 1 2 AM3C DOL Δ 3 4 AM3C S/D Y/Δ 5 6 AM3D S/D Y/Δ 5 6 AM3E S/D Y/Δ 7 8 AM3F S/D Y/Δ 7 8 Motor Ölkammer Motor-/Steuerkabel Motorkabel Motorkabel Motor Motor Ölkammer Ölkammer Motor-/Steuerkabel Motor-/Steuerkabel Motor Ölkammer Ölkammer Motor-/Steuerkabel Motor-/Steuerkabel 6 3.4.3 Motorkabel Motor 3.4.3.1 3.4.3.2 Motorkabel Motor Ölkammer Motor-/Steuerkabel Motorkabel Motor Ölkammer Motor-/Steuerkabel 7 11 12 3.6.2 14 1- 2+ A1 A2 3.6.3 L0 (N) 8 4.6.3 4.3 5.1 5.1.1 9 4.2 5.1.2.1 5.2 Pumpentyp µF VAC SW 65-160 und 80-160 2-polig bis 0,8 kW (P2) 25 450 30 450 SW 65-160 und 80-160 4-polig bis 0,9 kW (P2) 40 450 40 450 5.1.2.2 Funktionskontrolle 5.4 5.4.1 6.1 6.2.1.1 0,01 AM1 2-polig 1,8 kW bis 3,4 kW 1,1 AM1 4-polig 1,1 AM2 2-polig 0,5 AM2 4-polig 0,9 kW bis 1,3 kW 0,5 AM2 4-polig 1,9 kW bis 2,4 kW 0,6 AM3A 0,6 AM3B 0,6 AM3C 1,9 AM3D 3,7 AM3E 10 12 6.2.1.2 Motortyp EX 0,4 6.2.6 11 6.2.7 Lauf- Pumpenrad typ Motor Hydraulik B C D F SW 65-160.F - 1 2 - - F SW 80-160.F - 1 3 - - F SW 80-170.F - 4 5 - - F SW 80-230.F AM3B 6 7 - - F SW 80-230.F AM3C 8 9 10 11 F SW 80-230.F AM3D 12 13 14 15 F SW 100-230.F AM3C 8 9 10 11 F SW 100-230.F AM3D 12 13 14 15 F SW 100-280.F AM3C 16 17 18 19 F SW 100-280.F AM3D 20 21 22 23 K SW 65-160.K - 24 25 - - K SW 80-160.K - 24 26 - - K SW 80-210.K Hydr. A+B 27 28 - - K SW 80-210.K Hydr. C+D 29 30 - - K SW 80-250.K AM3A 31 32 K SW 80-250.K AM3B 33 34 - - K SW 80-250.K AM3C 35 36 37 38 K SW 80-250.K AM3D 39 40 41 42 K SW 100-250.K AM3A 31 32 - - K SW 100-250.K AM3B 33 34 - - K SW 100-250.K AM3C 35 36 37 38 K SW 100-250.K AM3D 39 40 41 42 K SW 100-310.K AM3C 43 44 45 46 K SW 100-310.K AM3D 47 48 49 50 K SW 150-370.K AM3D 51 52 53 54 K SW 150-370.K AM3E 55 55 56 56 Z SW 150-350.Z AM3E 55 55 56 56 Z SW 200-400.Z AM3F 57 57 58 58 Z SW 250-380.Z AM3E 59 59 60 60 Z SW 250-380.Z AM3F 57 57 58 58 12 Pumpe verstopft 13 8. Anhang 8.1 VDMA-Nr. VDMA-Nr. 101 812 Motorgehäusedeckel 135 814 151 819 162 Saugdeckel 822.01 163 822.02 230.xx Laufrad 824.xx 320.01 Kugellager 826.xx 320.02 Kugellager 834.xx 360 835.xx Motoren-Klemmbrett 411.xx 836.xx 412.xx O-Ring 839.05 433 839.06 433.01 839.09 433.02 839.10 Spaltring 900.xx 903.xx 502 550.xx 552 561 Halbrundkerbnagel 914.xx 576 Griff 920.xx Hutmutter 690.01 690.02 904 922 Sechskantmutter 930.xx 702 932.xx 704 940 732.01 950 732.02 970 811 14 990.xx Motoröl Index Page 1. Safety instructions ................................................................................................................16 2. Handling and intermediate storage .....................................................................................16 2.1 Handling ............................................................................................................................................................................. 16 2.2 Unpacking .......................................................................................................................................................................... 16 2.3 Intermediate storage .......................................................................................................................................................... 16 2.4 Preservation ....................................................................................................................................................................... 16 3. Description.............................................................................................................................16 3.1 Designation ........................................................................................................................................................................ 17 3.2 Construction ....................................................................................................................................................................... 17 3.3 Mounting arrangements ..................................................................................................................................................... 17 3.4 Motor .................................................................................................................................................................................. 17 3.5 Dimensions, weights, centers of gravity, capacity.............................................................................................................. 20 3.6 Installation requirements .................................................................................................................................................... 20 4. Mounting/installation ............................................................................................................20 4.1 Preliminary checks ............................................................................................................................................................. 20 4.2 Stationary wet-pit installation (N) ....................................................................................................................................... 21 4.3 Mobile wet-pit installation (M)............................................................................................................................................. 21 4.4 Dry-pit installation (TV, TH)................................................................................................................................................ 21 4.6 Piping ................................................................................................................................................................................. 21 5. Commissioning/decommissioning ......................................................................................21 5.1 Preparing the pump for operation ...................................................................................................................................... 21 5.2 Level control....................................................................................................................................................................... 22 5.3 Commissioning................................................................................................................................................................... 22 5.4 Decommissioning............................................................................................................................................................... 22 6. Maintenance/servicing ..........................................................................................................23 6.1 General notes..................................................................................................................................................................... 23 6.2 Maintenance and inspections............................................................................................................................................. 23 6.3 Disassembly and assembly instructions ............................................................................................................................ 24 7. Problems: causes and remedies..........................................................................................25 8. Appendix ................................................................................................................................26 8.1 Parts list ............................................................................................................................................................................. 26 8.2 Sectional drawings ............................................................................................................................................................. 27 15 ENGLISH 4.5 Grouting of the pump and other final checks (N, TV, TH) .................................................................................................. 21 These instructions must be read in conjunction with the separate User’s Safety Instructions, the Motor Operating Instructions as well as the Operating Instructions supplied for other components. Examples of correct handling of the unit: 1. Safety instructions • These operating instructions contain basic instructions, which have to be adhered to during installation, operation and maintenance. These operating instructions must be read by the mechanic and the operator before installation and operation of the pump and have to be kept available at the operating place of the machine/unit at all times. Persons who are not familiar with the operating instructions shall not use this product. • The working area has to be closed off expediently and must adhere to local workplace regulations. • Make sure that the emergency exit from the workplace is not barricaded. • To prevent suffocation and poisoning caused by venomous gases, make sure that enough oxygen exists at the workplace. • If you have to work with welding tools or electric tools, make sure that there is no explosion hazard. • Always use personal safety equipment such as safety boots, rubber gloves, safety glasses and helmet. • Immediately after repair or maintenance work, all safety and protection equipment must be reinstalled and placed in function again. • The operator is responsible to third parties for the work area of the pump. • Rules for accident prevention as well as engineering rules must be observed. • Never put a hand or finger into suction inlet or discharge of the pump while the impeller is rotating. • Persons are not permitted to stay in the pumping medium during operation of the pump. • For operation of the pumps in explosive environments only models with explosion-proof motors (Ex model) must be used. • In accordance with product liability law, we point out that we shall not be liable for damages caused by the pump due to non-observance of the instructions and guidelines set forth in the operating instructions. Same terms are valid for accessories. Proper handling Improper handling 2.2 Unpacking Check that the delivery is complete and undamaged. If any defects are found, have them confirmed on the original bill of lading by the carrier and report these defects to us immediately. The cable end is fitted with a moisture-proof seal. Do not remove this seal until the cable is to be connected to the power supply. 2.3 Intermediate storage • Store the pump in an upright position. • Seal all suction and pressure ports with a sealing cap, a dummy flange or a dummy plug. • Storage location: must be free of dust, dry and protected against heat and frost. • Long-time storage of more than 3 months: preservation required! • Long-time storage of more than 2 years: renew the lubricants before setting the pump into operation. 2. Handling and intermediate storage 2.4 2.1 If requested, we will preserve your pumps before delivery or at site. Please contact our service department. 16 Handling • Heed the weight and the center of gravity. • Attach the lifting gear to the lifting eyes or lifting ear of the motor. Do not lift the unit by the electric cable. Preservation 3. Description The channel impeller pumps of the SW series are single-stage submersible sewage pumps with a pressure-water-tight motor and a closed-coupled design. They can be supplied for different types of installation and with various impeller types. For dry well installation of the pump in a separate sump all models are available with a motor jacket cooling. The pumps are not suitable for pumping liquids containing heavy abrasive solids, like sand or stones. Before pumping of chemically aggressive liquids, the resistance of the materials must be checked. For details on the supplied execution, please refer to the documentation related to the contract. 3.1 Designation Example: • Function of a mechanical seal: Two slide faces rub against each other and are lubricated by a liquid film at the same time. Mechanical seals are wearing parts for which no guarantee can be given. 3.3 Nominal width discharge branch [mm] Mounting arrangements N M TH TV Impeller nominal diameter [mm] Impeller form Hydraulic basic number Installation Motor type Rated output P2 [kW] No. of poles Kind of current Explosion-proof Motor cooling shroud Example The individual mounting arrangements are described in section 3.3. 3.2 Construction Also refer to the sectional drawings (section 8.2). 3.2.1 Pump casing 3.4 Motor Pressure-water-tight squirrel cage motor. Temperature class F, protection class IP 68. Explosion-proof motors are also available. (For details, please refer to the documentation related to the contract.) 3.2.2 Impeller types Vortex impeller (.F) For high gas content liquids, as well as stringy or matting materials, sludge and abrasive suspensions. Single-channel impeller (.K) For media that contain coarser solid particles or stringy or matting materials. Large impeller free passage for smooth transport. Two-channel impeller (.Z) For contaminated media that contain solid particles but no strand-forming admixtures with long fibers or gas and air bubbles. 3.2.3 Shaft and bearings Greased maintenance-free roller bearings. 3.2.4 • Maximum coolant temperature 35°C, short term up to 60°C. • Motors for operation mode S1 are designed with a maximum number of 15 switches per hour. • As a general rule: Starting method up to 3 kW DOL, for more then 3 kW star-delta. For accurate details please refer to the nameplate or to the documentation related to the contract. • For operation, the motor must be fully submersed. • If the motor is operated in a surfaced or not fully submersed state: operation in this state requires forced circulation cooling or a special motor dimensioning. • Noise level during operation, 1.60 m from the ground ≤ 70 d(B)A. • When operating the pumps with a frequency converter the converter must be equipped with an outlet filter to protect the pump motor from damaging voltage spikes. Such voltage spikes may destroy parts of the pump motor. 3.4.1 Electrical connecting plan Depending on the type and the size, the motor can be fitted with different connection cables. For details on the motor type, please refer to the documentation related to the contract. Shaft seal Shaft sealing by to mechanical seals acting irrespective of direction of rotation. Motors AM1 / 2 poles up to 1.2 kW with mechanical seal and radial sealing ring. For details on the supplied shaft seal, please refer to the documentation related to the contract. 17 ENGLISH The pump casing has a radial discharge branch and a axial suction branch. 3.4.2 Connecting plans • Connecting plan - No. 3 • Execution A: Standard • Execution B: Explosion proof Motor type Starting Connection AM1 DOL AM2 DOL AM3A Execution A B Y 1 2 Y 1 2 DOL Y 1 2 AM3B DOL Y 1 2 AM3C DOL Y 1 2 AM3C DOL Δ 3 4 AM3C S/D Y/Δ 5 6 AM3D S/D Y/Δ 5 6 AM3E S/D Y/Δ 7 8 AM3F S/D Y/Δ 7 8 Main supply Motor protection Motor protection Motor cable Motor Oil chamber Motor-/Control cable Table 1: Allocation of connecting plans T1, T3 : Temperature sensor (controller) S1, S2 : Leak monitoring oil chamber • Connecting plan - No. 1 • Connecting plan - No. 4 Main supply Motor protection Main supply Motor protection Motor protection Motor protection Motor cable Motor cable Motor Motor Oil chamber Oil chamber Motor-/Control cable T1, T3 : Temperature sensor (controller) S1, S2 : Leak monitoring oil chamber (acc. execution) Motor-/Control cable T1, T2 : Temperature sensor (limiter) S1, S2 : Leak monitoring oil chamber • Connecting plan - No. 2 • Connecting plan - No. 5 Main supply Motor cable Motor protection Motor protection Motor Motor cable Motor Oil chamber Oil chamber Motor-/Control cable Motor-/Control cable T1, T2 : Temperature sensor (limiter) S1, S2 : Leak monitoring oil chamber (acc. execution) 18 T1, T3 : Temperature sensor (controller) S1, S2 : Leak monitoring oil chamber • Connecting plan - No. 6 3.4.3 Monitoring devices To avoid damage, the pump unit is fitted with various monitoring devices. For the connection of the monitoring devices, refer to section 3.4.2. Motor cable Motor 3.4.3.1 Protective motor switch Depending on the current consumption of the motor during operation, the protective motor switch must be set to 90 - 100% of the nominal motor current (refer to the nameplate). Oil chamber Connection space 3.4.3.2 Temperature feeler All motors are fitted with a temperature sensor. This sensor prevents the motor coils from overheating. Standard execution: Motor-/Control cable T1, T2 : Temperature sensor (limiter) S1, S2 : Leak monitoring oil chamber S3, S4 : Leak monitoring connection space (acc. execution) • Connecting plan - No. 7 Motor cable Motor Standard models have the sensors connected to the motor power supply cable, the wire ends marked T1 and T3. They must be connected to the safety circuit of the control box in order to provide an automatic re-start of the motor, when the motor cooled down. The switch-off temperature of the sensors for standard models is from 130°C to 150°C. Standard models of 1Ph-motors have the sensors internally connected, so that no external connection to the control box is necessary. When the motor cools, it is switched on again automatically. Oil chamber Connection space Motor-/Control cable T1, T3 : Temperature sensor (controller) S1, S2 : Leak monitoring oil chamber S3, S4 : Leak monitoring connection space (acc. execution) • Connecting plan - No. 8 Motor cable Motor Explosion proof models (1 Ph and 3 Ph) have a set of temperature sensors with a higher switch-off temperature of approx. 140°C, connected to the motor cable, the wires are marked T1 and T2. They must be connected to the safety circuit of the control box in order to provide a manual re-start, when the motor cools. Fitted are looking ex sensors instead of standard sensors, i. e. in case of series connection to the relay the sensors can be positioned back for the duration of the cooling by simply detaching the pump from power supply. Explosion proof execution, AM3C, AM3D: Explosion proof models have a set of temperature sensors built-in, instead of standard sensor with a higher switch-off temperature of approx. 140°C, connected to the motor cable, the wire ends marked T1 and T2. They must be connected to a special relay in the starter box in order to provide manual pump restart. Explosion proof execution, AM3E, AM3F: Oil chamber Connection space Motor-/Control cable T1, T3 : Temperature sensor (controller) T1, T2 :Temperature sensor (limiter) S1, S2 : Leak monitoring oil chamber S3, S4 : Leak monitoring connection space (acc. execution) Explosion proof models have a set of temperature sensors built-in additionally to the standard sensor as described above, with a higher switch-off temperature of approx. 140°C, connected to the motor cable, the wire ends marked T1 and T2. Ex-sensors must be connected to a special relay in the starter box in order to provide manual pump re-start. The manual re-start must be assured by a special combination of relays in the control panel. PTC resistor protection: For operation in conjunction with a frequency converter, the explosion-proof submersible motors must be protected by a thermal motor circuit breaker comprised of PTC resistors according to DIN 44081 / 44082 and an approved triggering device (heed the documentation related to the contract and the separate connecting plan!). 19 ENGLISH Explosion proof execution, AM1, AM2, AM3A and AM3B: 3.4.3.3 Leak monitoring Except for the AM1 motor, all motors are fitted with a moisture feeler. This sensor is installed in the oil chamber resp. in the connection space. In combination with the DG 110 control unit supplied as an accessory, it ensures secure and reliable monitoring of the mechanical seal for leaks. Depending on the type of the control unit, either the motor is automatically switched off or appropriate signals are issued if any water enters the oil chamber or the connecting space. Leak monitoring oil chamber: The electrical resistance of the oil in the chamber is measured by two sensors S1/S2. The sensors must be connected to a tripping unit in the control panel (electrode relays). In case of water entering the chamber through the shaft seals, the resistance will change. For explosion-proof models an intrinsicallysafe relay has to be chosen. The DG 110 is used for monitoring the conductivity of the pumps’ oil filling. This conductivity is an indicator for the amount of water that has penetrated inside. It is measured by an electrode that reaches into the oil chamber resp. into the connection space. The DG 110 is fitted with a sensitive measuring and switching amplifier with a relay output. The measuring voltage applied for the measurements is 2.5V. The theoretically possible measuring current is 0.1mA. The threshold value of the relay is 100kOhm. The relay picks up when the measured value drops below this threshold. This state is indicated by a red lightemitting diode on the control unit. The input circuit is fitted with a filter against noise pulses. An isolating transformer isolates the measuring circuit from the mains voltage. 3.5 On request. Weight: refer to the documentation related to the contract. 3.6 Leak monitoring connection space: Two sensors S3/S4 are used for monitoring leaks into the connection chamber. The sensors must also be connected in the control panel to a tripping unit with galvanically separated safety circuit (electrode relays). For explosion-proof models an intrinsically-safe relay has to be choosen. Control unit DG 110 L01 (L) A1/A2 polarity = as required A1 11 12 2+ 14 A2 Sensor in the pump Space requirements for operation and maintenance • Ensure that sufficient space, at least from 2 sides, is left for subsequent maintenance requirements. This space should have, for reason of good accessibility, min. 0.8 m width. • The set should be easily accessible from all sides. 3.6.2 Subsoil, foundation • The subsoil or concrete foundation must be sufficiently strong to ensure that the pump can be safely installed as required for proper functioning. 3.6.3 L0 (N) Installation requirements • Protect the unit against atmospheric influences. • Ensure sufficient ventilation, heating and cooling and heed any sound proofing regulations that might be applicable. • Check that the unit and its components can be safely transported to or removed from the installation location without accidents. Make sure that the existing doors or openings are large enough. • Make sure that the required lifting gear and the tools required for attaching the gear are available. 3.6.1 1- Dimensions, weights, centers of gravity, capacity Supply connections Check that all supplies like power, water and drainage necessary for installation and later operation are available in the form required. 4. Mounting/installation Sensor in the pump Sketch of the DG 110 control unit Auxiliary voltage A1 - A2 220-240 V +/- 10%, 50/60 Hz Special voltage 24 V u. 110/115 V 50/60 Hz 24 V = galvanically separated, unpoled Current consumption 1.5 VA Measuring voltage 1 - 2 2.5 V Measuring current max. 0.1 mA Switching threshold 100 kOhm +/- 5% Operating mode static current principle Output 1 change-over contact 20 For proper functioning, the pump must be installed in a careful and proper manner. Installation faults can cause injuries and damage and can also result in premature wear of the pump. Check the oil level before installing the pump (refer to section 6.2.1). 4.1 Preliminary checks • The building must have been prepared according to the dimensions given on the foundation and layout plans. • Pay attention to the maximum depth of immersion of the pump (see pump label). • If the pump is installed in a sump, the sump opening must be covered with a tread-safe cover after installation. • The operator has to prevent damage through the flooding of rooms caused by defects of the pump through the use of appropriate measures (e.g. installation of alarm units, backup pump or alike). Stationary wet-pit installation (N) • Install the foot bend, the guide rail and the ceiling bracket (refer to the dimension sheet). • Then attach the pump so that it hangs in the guide rail and lower it using the chain. The pump automatically engages in the foot bend installed on the floor. 4.3 Dry-pit installation (TV, TH) • Install the pump (refer to the dimension sheet). • Connect the suction line and the discharge line to the pump. Make sure that the lines are not subjected to stress. • If necessary, mount a venting pipe on the pump casing. 4.5 Piping The following not binding specifications are recommendations for the correct dimensioning and laying of pipework (the planner is responsible for the correct dimensioning of the pipework!). 4.6.1 • • • • • • • • Lay the pipe in a continuously ascending manner. Maximum flow rate: 3 m/s (heed the head loss). There must be no bottlenecks in the discharge pipe. Lay the pipework system in such a manner that no inerts will deposit in any other pump. Dimension the flange and the pipe according to the maximum possible pressure. Prevent air pockets. If necessary, vent high points. Prevent changing flow rates by using a uniform pipe diameter. Install non-return valves and shut-off valves. 4.6.2 5. Commissioning/decommissioning 5.1 5.1.1 Preparing the pump for operation Checks Before switching on the pump, ensure that the following actions have been carried out: • Check the oil level (refer to section 6.2.1). • Check that the fastening screws of the pump, the foot bend, etc. are firmly tightened. 5.1.2 Electrical connections The electrical connections may only be established by a qualified electrician. The connections must be established according to the VDE and EVU regulations and according to the relevant regulations for motors with an explosion-proof design. Grouting of the pump and other final checks (N, TV, TH) • After the pump or the foot bend has been aligned and fastened: grout in/underpour and, if necessary, also underpack the fastening device with flash-set, non-shrinking cement. • Let the cement set for at least 48 hours. • Retighten the foundation bolts. 4.6 • Heed the relevant regulations. • Heed the permissible nominal pressure of the individual components. Mobile wet-pit installation (M) • Attach a rigid or a flexible pipe to the discharge branch of the pump. • Lower the pump using the chain and place it in a vertical position onto a firm subsoil, with the motor facing upwards. • Tighten the chain vertically and secure it to prevent the pump from tipping over. 4.4 Pressure tests • Before operation, an expert check must secure that the required electrical protection measures exist. The connection to ground, earthing, isolating transformer, fault current breaker or fault voltags circuit must correspond to the guidelines set forth by the responsible power plant. • Connect the motor according to the electrical connecting plans (refer to section 3.4.2). • Make sure that the electrical pin-and-socket connections are installed flood- and moisture-safe. Before starting operation check the cable and the plug against damages. • The end of the pump power supply cable must not be submerged in order to prevent water from penetrating through the cable into the motor. • Ensure that motor starter/control box are not installed in explosive environments. • Do not operate the motor without a protective motor switch and a temperature and a leak monitoring device (if such a device exists). • Make sure that the available mains voltage and frequency match the data given on the nameplate. • The connection and control cables of the motor and the level controller must be routed in such a manner that they cannot get caught by the suction force of the pump. Suction line (mounting arrangement TV, TH) • Maximum flow rate: 2 m/s (at maximum capacity). • Do not install bends on different levels following one after the other. • Lay the pipe in a continuously descending manner (at least 1 %) towards the pump). • Provide a separate suction pipe for each pump. • Make sure that no air pockets can develop in the pipe. 21 ENGLISH 4.2 4.6.3 5.1.2.1 Connection of 1 Ph-Motors 5.2 Pumps with 230V/1Ph-motors must be connected to a seperate control box with motor starter and operating capacitor. Original/ Matching control units can be supplied as accessory. If any other then an original control unit is used, make sure that the thermal relay in the motor starter is set according to the nominal current consumption of the pump motor. For capacitor sizes, see table below: Pump type Operating capacitor µF VAC SW 65-160 and 80-160 2 poles up to 0.8 kW (P2) 25 450 SW 65-160 and 80-160 2 poles over 1 kW (P2) 30 450 SW 65-160 and 80-160 4 poles up to 0.9 kW (P2) 40 450 SW 80-170 and 80-210 up to 1.1 kW (P2) 40 450 Table 2: Data for capacitor 5.1.2.2 Connection of 3 Ph-Motors Pumps with 3Ph-motors are supplied with or must be connected to a separate control box. Original/Matching control units can be supplied as accessory. If any other than an original control unit is used, make sure that the thermal relay in the motor starter is set according to the nominal current consumption of the pump motor. 5.1.3 5.1.3.1 Check of the direction of rotation 1 Ph-pumps 1 Ph-pumps do not require any check, as they always run with the correct direction of rotation. 5.1.3.2 3 Ph-pumps • When connecting to a right handed rotating field all pumps run with the correct direction of rotation (U, V, W -> L1, L2, L3). The direction of rotation of the mains can be controlled by a rotating field measuring instrument. • If no rotating field measuring instrument is available, the pump can be briefly switched off and immediately switched on again in both horizontal/vertical position. Observe direction of rotation of the impeller throught the suction branch/delivery branch. The direction of rotation is correct, when the impeller is rotating anti-clockwise in the suction branch and clockwise in the discharge branch. Before checking the direction of rotation, make sure that no foreign particles are in the pump casing. Never reach into the pump or hold any objects into the pump. Keep a sufficient safety distance to the pump. • If the direction of rotation is not correct, have the direction of rotation of the motor corrected by an electrician. Do not run pump counter to its given operation direction. Level control For stations with automatic pump operation, a level controller must be installed. When the pump is switched off, the motor still must be fully submersed. The water level may only be lowered down to the pump casing if the pump is designed for S3 (intermittent) operation or if it is fitted accordingly (e.g. with a forced circulation cooling system). 5.3 5.3.1 Commissioning Initial commissioning/recommissioning • Mounting arrangement N: Only start up the pump when it is fully submersed. The gate valve must be throttled. Slowly open the gate valve until the discharge line is completely filled. • Mounting arrangement M: Only start up the pump when it is fully submersed. • Mounting arrangement TV, TH: Fill and vent the suction pipe and the pump. Only start up the pump when it is filled with liquid. The gate valve must be throttled. Slowly open the gate valve until the discharge line is completely filled. 5.3.2 Function check • Check that the values displayed at the pressure gauge, at the vacuum gauge, at the ammeter and, if installed, at the flow meter match the values given in the documentation related to the contract. • Check the operating data at all operating states possible in the system (parallel operation of pumps, other delivery purposes, etc.). • Write down the determined values as standard values for subsequent monitoring. 5.3.3 5.4 5.4.1 Operation with closed gate valve Do not operate the pump when the gate valves on the suction and the discharge sides are closed or, if a non-return valve is installed on the suction side, when the gate valve on the discharge side is closed. In this mode, the medium to be delivered heats up very quickly in the pump, causing a high pressure in the pump due to the generation of steam. If the casing’s bursting pressure is exceeded, the casing parts can burst apart as in an explosion, causing severe injuries and damage. Decommissioning Switching off the pump • Close the shut-off device in the discharge line. • A non-return valve above which a corresponding pressure is built by the liquid column makes the actuation of a discharge side valve unnecessary. • Switch off the pump. 5.4.2 Draining the pump • With danger of frost: drain the pump and the pipes and protect them from freezing up while they are decommissioned. • After contaminated media have been delivered: drain the pump and, if necessary, flush it. This measure is also required to protect the pump against corrosion while it is standing still. 22 6.1 6.2.1.2 General notes • Always disconnect the electrical connections before carrying out any work on the machine. Secure the pump unit so that it cannot be switched on inadvertently. • Before maintenance or repair make sure that all rotating parts stand still! • Before carrying out maintenance and service, the pump must be thoroughly flushed with clean water. Rinse the pump parts in clean water after dismanteling. • In case of a defect of the pump, a repair shall be carried out only by the manufacturer or through an authorized workshop. Conversions or alternations of the machine/unit are permitted only after arrangement with the manufacturer. Only original spare parts shall be used. • In accordance with the product liability law we point out that we shall not be liable for damages caused by our product due to unauthorized repair by persons other than the manufacturer or an authorized workshop or due to the use of spare parts other than original parts. The same product liability limitations are valid for accessories. 6.2 • Have the oil changed after 3.000 operating hours, however latest after one year of operation. • When the pump is new or after replacement of the shaft seals, check the oil level after one week of operation. • The oil becomes greyish white like milk if it contains water. This may be the result of defective shaft seal. Hot oil or liquid to be delivered that has penetrated into the intermediate casing can cause an excess pressure in the intermediate casing. Therefore, use a cover (e.g. a piece of cloth) when opening the oil drain outlet/oil filler cap to protect against liquid that spurts out. • • • • • • • • Maintenance and inspections Oil change Turn the pump to horizontal position. Place an oil pan below the drain outlet. Open the oil drain outlet. Completely drain the old oil and dispose it in the stipulated manner. Rinse the oil chamber using some fresh oil while turning the rotor on the impeller. Fill in oil until the oil chamber is completely filled. Check oil level in upright position of the pump. Oil chamber must be filled up to the bottom line of the inspection hole. Insert the adjusting screw. Pumps running under normal operation conditions should be inspected at least once a year. If the pumped liquid is very muddy or sandy or if the pump is operating continu-ously, the pump should be inspected every 1.000 operating hours. 6.2.2 6.2.1 Check all components for possible wear. Replace defective parts. 6.2.1.1 Lubricants: filling quantity and lubrication intervals • Oil quality: The oil chamber is filled with medical white oil by factor standard: Brand name Ondina 917, Co. Shell. Equivalent oils may be used alternatively. • Filling quantity: Fill the oil chamber with appropiate oil up to the bottom line of the inspection hole. Keep pump in upwright position. Following table is indicating values for the oriantation: Oil quantity in liter with execution Motor type AM1 2 poles 0.8 kW up to 1.2 kW Nominal current (A): Check with ampmeter. 6.2.3 6.2.4 Quality and filling quantity Standard EX 0.01 0.4 Nominal current Pump casing and impeller Checking the bearing clearance Apply radial and axial pressure to the impeller. If the impeller can be moved in radial or axial direction, the ball bearings must be replaced. 6.2.5 Cable entry Make sure that the cable entry is watertight and that the cables are not bent sharply and/or pinched. 6.2.6 Leak monitoring AM1 2 poles 1.8 kW up to 3.4 kW 1.1 AM1 4 poles 1.1 AM2 2 poles 0.5 AM2 4 poles 0,9 kW up to 1.3 kW 0.5 AM2 4 poles 1.9 kW up to 2.4 kW 0.6 AM3A 0.6 AM3B 0.6 • Change the oil if the indicator signals that water has penetrated into the intermediate casing (refer to section 6.2.1). • If, after a short time, the indicator again signals that water has penetrated, drain the oil into a glass vessel and check whether the oil contains water. If it does, replace the mechanical seal. Mechanical seals are wearing parts for which no guarantee can be given. • When the mechanical seal has been replaced, check it for leaks after one or two weeks. AM3C 1.9 6.2.7 AM3D 3.7 AM3E 10 12 For a regular and workmanlike accomplishment of all neccesary service and control works we recomend to conclude a maintenance contract. Kindly contact our service department. 16 Maintenance contract Table 3: Oriantation values for filling quantity • Recommended commercially available oils: Shell, Ondina 917 Shell, Tellus C22 23 ENGLISH 6. Maintenance/servicing 6.3 Disassembly and assembly instructions Only qualified personnel may disassemble and assemble the pump as shown in the sectional drawing (refer to section 8.2). The order of the steps to be carried out for the disassembly is indicated in the sectional drawing. Only specially trained personnel may disassemble explosion-proof motors 6.3.1 • • • • Assignment of the sectional drawings: Execution A: Standard Execution B: Explosion proof Execution C: Standard, with cooling jacket Execution D: Explosion proof, with cooling jacket Imp- Pump eller type Motor Hydraulic Execution A B C D F SW 65-160.F - 1 2 - - F SW 80-160.F - 1 3 - - F SW 80-170.F - 4 5 - - F SW 80-230.F AM3B 6 7 - - F SW 80-230.F AM3C 8 9 10 11 F SW 80-230.F AM3D 12 13 14 15 F SW 100-230.F AM3C 8 9 10 11 F SW 100-230.F AM3D 12 13 14 15 F SW 100-280.F AM3C 16 17 18 19 F SW 100-280.F AM3D 20 21 22 23 K SW 65-160.K - 24 25 - - K SW 80-160.K - 24 26 - - K SW 80-210.K Hydr. A+B 27 28 - - K SW 80-210.K Hydr. C+D 29 30 - - K SW 80-250.K AM3A 31 32 K SW 80-250.K AM3B 33 34 - - K SW 80-250.K AM3C 35 36 37 38 K SW 80-250.K AM3D 39 40 41 42 K SW 100-250.K AM3A 31 32 - - K SW 100-250.K AM3B 33 34 - - K SW 100-250.K AM3C 35 36 37 38 K SW 100-250.K AM3D 39 40 41 42 K SW 100-310.K AM3C 43 44 45 46 K SW 100-310.K AM3D 47 48 49 50 K SW 150-370.K AM3D 51 52 53 54 K SW 150-370.K AM3E 55 55 56 56 Z SW 150-350.Z AM3E 55 55 56 56 Z SW 200-400.Z AM3F 57 57 58 58 Z SW 250-380.Z AM3E 59 59 60 60 Z SW 250-380.Z AM3F 57 57 58 58 Table 4: Assignment of the sectional drawings 24 7. Problems: causes and remedies 1) Output low or no output at all 2) Excessive output 3) Motor overload 4) Temperature monitoring device switches off 5) Leak monitoring device indicates that water has penetrated into the intermediate casing 1) 2) 3) 4) 5) Cause of the malfunction Remedy The water level is lowered excessively (suction head is too high, inlet level is too low) • Check the supply and the dimensioning of the system • Check the level controller The pump has not been fully vented • Vent the pump The temperature of the medium is too high • Lower the temperature (please contact the manufacturer) The gas content of the medium is too high • Check the gas content of the medium (please contact the manufacturer) The counterpressure is too high • Open the shut-off devices further • Check the dimensioning of the system (pressure losses too high?) • Adjust the head of the pump (only after the manufacturer has been consulted) The counterpressure is too low • Check the dimensioning of the system • Throttle the discharge side shut-off valve further Wrong direction of rotation • Correct the direction of rotation The pump is clogged • Remove the deposits The interior parts are worn • Replace the worn parts The speed is too low • Check the electrical installation The speed is too high • Check the electrical installation The pump runs on two phases • Check the electrical installation There are deposits on the motor • Clean the motor on the outside The switching frequency is too high • Check the level controller Water has penetrated into the intermediate casing • Change the oil. If leaks occur again: check and, if necessary, replace the mechanical seal Table 5: Problems 25 ENGLISH The inlet/suction line has not been fully • Vent the inlet/suction line vented (mounting arrangements TH, TV only) • Check the inlet/suction line and the fittings for leaks 8. Appendix 8.1 Parts list VDMA No. Designation VDMA No. 101 Pump casing 812 Motor casing cover 135 Wear plate 814 Stator with winding 151 Cooling jacket 819 Motor shaft with rotor 162 Suction cover 822.01 Lower bearing cover 163 Pressure cover 822.02 Upper bearing cover 230.xx Impeller 824.xx Connection cable 320.01 Lower ball bearing 826.xx Cable leading-in socket 320.02 Upper ball bearing 834.xx Cable inlet 360 Bearing cover 835.xx Motor terminal board 411.xx Sealing ring 836.xx Terminal strip 412.xx O-Ring 839.05 Protective conductor clamp 433 Mechanical seal 839.06 Connection 433.01 Mechanical seal 839.09 Cable socket, insulated 433.02 Mechanical seal 839.10 Cable socket, insulated 502 Wear ring 900.xx Ring nut/ Special screws 550.xx Supporting ring 903.xx Locking screw 552 Clamping disc 904 Threaded pin 561 Grooved drive stud 914.xx Threaded pin 576 Handle 920.xx Dome nut 690.01 Leak monitoring 922 Hexagonal nut 690.02 Leak monitoring 930.xx Tooth washer 702 Threaded tube (discharge) 932.xx Circlip 704 Threaded tube (suction) 940 Key 732.01 Holder for leak monitoring 950 Ball bearing disc 732.02 Holder for leak monitoring 970 Pump label 811 26 Designation Motor casing 990.xx Motor oil 8.2 Schnittbild | Sectional drawing | Vue en coupe 01 8.2.2 Schnittbild | Sectional drawing | Vue en coupe 02 8.2.1 Schnittbilder | Sectional drawings | Vues en coupe Schnittbild | Sectional drawing | Vue en coupe 03 8.2.4 Schnittbild | Sectional drawing | Vue en coupe 04 ENGLISH 8.2.3 SW 80-170.F 27 8.2 8.2.5 Schnittbilder | Sectional | drawings | Vues en coupe Schnittbild | Sectional drawing | Vue en coupe 05 8.2.7 Schnittbild | Sectional drawing | Vue en coupe 07 28 8.2.6 Schnittbild | Sectional drawing | Vue en coupe 06 8.2.8 Schnittbild | Sectional drawing | Vue en coupe 08 SW 80-230.F ... AM3C SW 100-230.F ... AM3C 8.2 Schnittbilder | Sectional | drawings | Vues en coupe Schnittbild | Sectional drawing | Vue en coupe 09 8.2.10 Schnittbild | Sectional drawing | Vue en coupe 10 8.2.9 SW 80-230.F ... AM3C ... EX SW 100-230.F ... AM3C ... EX Schnittbild | Sectional drawing | Vue en coupe 11 8.2.12 Schnittbild | Sectional drawing | Vue en coupe 12 ENGLISH 8.2.11 SW 80-230.F ... AM3C ... MK SW 100-230.F ... AM3C ... MK SW 80-230.F ... AM3C ... EX ... MK SW 100-230.F ... AM3C ... EX ... MK 29 8.2 Schnittbilder | Sectional | drawings | Vues en coupe 8.2.13 Schnittbild | Sectional drawing | Vue en coupe 13 8.2.15 Schnittbild | Sectional drawing | Vue en coupe 15 30 8.2.14 Schnittbild | Sectional drawing | Vue en coupe 14 8.2.16 Schnittbild | Sectional drawing | Vue en coupe 16 SW 100-280.F ... AM3C 8.2 Schnittbilder | Sectional | drawings | Vues en coupe Schnittbild | Sectional drawing | Vue en coupe 17 8.2.18 Schnittbild | Sectional drawing | Vue en coupe 18 8.2.17 SW 100-280.F ... AM3C ... EX Schnittbild | Sectional drawing | Vue en coupe 19 8.2.20 Schnittbild | Sectional drawing | Vue en coupe 20 ENGLISH 8.2.19 SW 100-280.F ... AM3C ... MK SW 100-280.F ... AM3C ... EX ... MK 31 8.2 Schnittbilder | Sectional | drawings | Vues en coupe 8.2.21 Schnittbild | Sectional drawing | Vue en coupe 21 8.2.23 Schnittbild | Sectional drawing | Vue en coupe 23 32 8.2.22 Schnittbild | Sectional drawing | Vue en coupe 22 8.2.24 Schnittbild | Sectional drawing | Vue en coupe 24 SW 65-160.K SW 80-160.K 8.2 Schnittbilder | Sectional | drawings | Vues en coupe Schnittbild | Sectional drawing | Vue en coupe 25 8.2.26 Schnittbild | Sectional drawing | Vue en coupe 26 8.2.25 Schnittbild | Sectional drawing | Vue en coupe 27 8.2.28 Schnittbild | Sectional drawing | Vue en coupe 28 ENGLISH 8.2.27 SW 80-210.K ... (A,B) SW 80-210.K ... (A,B) ... EX 33 8.2 Schnittbilder | Sectional | drawings | Vues en coupe 8.2.29 Schnittbild | Sectional drawing | Vue en coupe 29 8.2.31 Schnittbild | Sectional drawing | Vue en coupe 31 SW 80-250.K ... AM3A SW 100-250.K ... AM3A 34 8.2.30 Schnittbild | Sectional drawing | Vue en coupe 30 8.2.32 Schnittbild | Sectional drawing | Vue en coupe 32 SW 80-250.K ... AM3A ... EX SW 100-250.K ... AM3A ... EX 8.2 Schnittbilder | Sectional | drawings | Vues en coupe Schnittbild | Sectional drawing | Vue en coupe 33 8.2.34 Schnittbild | Sectional drawing | Vue en coupe 34 8.2.33 Schnittbild | Sectional drawing | Vue en coupe 35 8.2.36 Schnittbild | Sectional drawing | Vue en coupe 36 ENGLISH 8.2.35 SW 80-250.K ... AM3C SW 100-250.K ... AM3C SW 80-250.K ... AM3C ... EX SW 100-250.K ... AM3C ... EX 35 8.2 Schnittbilder | Sectional | drawings | Vues en coupe 8.2.37 Schnittbild | Sectional drawing | Vue en coupe 37 SW 80-250.K ... AM3C ... MK SW 100-250.K ... AM3C ... MK 8.2.39 Schnittbild | Sectional drawing | Vue en coupe 39 36 8.2.38 Schnittbild | Sectional drawing | Vue en coupe 38 SW 80-250.K ... AM3C ... EX ... MK SW 100-250.K ... AM3C ... EX ... MK 8.2.40 Schnittbild | Sectional drawing | Vue en coupe 40 8.2 Schnittbilder | Sectional | drawings | Vues en coupe Schnittbild | Sectional drawing | Vue en coupe 41 8.2.42 Schnittbild | Sectional drawing | Vue en coupe 42 8.2.41 8.2.44 Schnittbild | Sectional drawing | Vue en coupe 44 ENGLISH Schnittbild | Sectional drawing | Vue en coupe 43 8.2.43 SW 100-310.K ... AM3C SW 100-310.K ... AM3C ... EX 37 8.2 Schnittbilder | Sectional | drawings | Vues en coupe 8.2.45 Schnittbild | Sectional drawing | Vue en coupe 45 8.2.46 Schnittbild | Sectional drawing | Vue en coupe 46 SW 100-310.K ... AM3C ... MK 8.2.47 Schnittbild | Sectional drawing | Vue en coupe 47 38 SW 100-310.K ... AM3C ... EX ... MK 8.2.48 Schnittbild | Sectional drawing | Vue en coupe 48 8.2 Schnittbilder | Sectional | drawings | Vues en coupe Schnittbild | Sectional drawing | Vue en coupe 49 8.2.50 Schnittbild | Sectional drawing | Vue en coupe 50 8.2.49 Schnittbild | Sectional drawing | Vue en coupe 51 8.2.52 Schnittbild | Sectional drawing | Vue en coupe 52 ENGLISH 8.2.51 39 Baureihe | Series | Série SW 22 8.2 Schnittbilder | Sectional | drawings | Vues en coupe 8.2.53 Schnittbild | Sectional drawing | Vue en coupe 53 8.2.55 Schnittbild | Sectional drawing | Vue en coupe 55 40 8.2.54 Schnittbild | Sectional drawing | Vue en coupe 54 8.2.56 Schnittbild | Sectional drawing | Vue en coupe 56 8.2 Schnittbilder | Sectional | drawings | Vues en coupe Schnittbild | Sectional drawing | Vue en coupe 57 8.2.58 Schnittbild | Sectional drawing | Vue en coupe 58 8.2.57 Schnittbild | Sectional drawing | Vue en coupe 59 8.2.60 Schnittbild | Sectional drawing | Vue en coupe 60 ENGLISH 8.2.59 41 Technische Änderungen vorbehalten We reserve the right to make technical changes Tous droits réservés pour actualisation technique ANDRITZ Ritz GmbH | Güglingstraße 50 | 73529 Schwäbisch Gmünd | Germany Phone +49 (0) 7171 609-0 | Fax +49 (0) 7171 609-287 | [email protected] | www.ritz.de 4009113/08.11
advertisement
Related manuals
advertisement
Table of contents
- 3 1. Sicherheitshinweise
- 3 2. Transport und Zwischenlagerung
- 3 2.1 Transportieren
- 3 2.2 Auspacken
- 3 2.3 Zwischenlagern
- 3 2.4 Konservieren
- 3 3. Beschreibung
- 4 3.1 Benennung
- 4 3.2 Konstruktiver Aufbau
- 4 3.3 Bauformen
- 4 3.4 Motor
- 7 3.5 Abmessungen, Gewichte, Schwerpunkte, Fassungsvermögen
- 7 3.6 Angaben zum Einsatzort
- 7 4. Aufstellung/Einbau
- 7 4.1 Überprüfung vor Aufstellungsbeginn
- 8 4.2 Stationäre Nassaufstellung (N)
- 8 4.3 Mobile Nassaufstellung (M)
- 8 4.4 Trockenaufstellung (TV, TH)
- 8 4.5 Vergießen und sonstige Abschlussarbeiten (N, TV, TH)
- 8 4.6 Rohrleitungen
- 8 5. Inbetriebnahme/Außerbetriebnahme
- 8 5.1 Fertigmachen zum Betrieb
- 9 5.2 Niveausteuerung
- 9 5.3 Inbetriebnahme
- 9 5.4 Außerbetriebnahme
- 10 6. Wartung/Instandhaltung
- 10 6.1 Sicherheitshinweise
- 10 6.2 Wartung und Inspektion
- 11 6.3 Demontage- und Montagehinweise
- 12 7. Störungen: Ursachen und Beseitigung
- 13 8. Anhang
- 13 8.1 Teileverzeichnis
- 26 8.2 Schnittbilder
- 15 1. Safety instructions
- 15 2. Handling and intermediate storage
- 15 2.1 Handling
- 15 2.2 Unpacking
- 15 2.3 Intermediate storage
- 15 2.4 Preservation
- 15 3. Description
- 16 3.1 Designation
- 16 3.2 Construction
- 16 3.3 Mounting arrangements
- 16 3.4 Motor
- 19 3.5 Dimensions, weights, centers of gravity, capacity
- 19 3.6 Installation requirements
- 19 4. Mounting/installation
- 19 4.1 Preliminary checks
- 20 4.2 Stationary wet-pit installation (N)
- 20 4.3 Mobile wet-pit installation (M)
- 20 4.4 Dry-pit installation (TV, TH)
- 20 4.5 Grouting of the pump and other final checks (N, TV, TH)
- 20 4.6 Piping
- 20 5. Commissioning/decommissioning
- 20 5.1 Preparing the pump for operation
- 21 5.2 Level control
- 21 5.3 Commissioning
- 21 5.4 Decommissioning
- 22 6. Maintenance/servicing
- 22 6.1 General notes
- 22 6.2 Maintenance and inspections
- 23 6.3 Disassembly and assembly instructions
- 24 7. Problems: causes and remedies
- 25 8. Appendix
- 25 8.1 Parts list
- 26 8.2 Sectional drawings