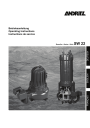
advertisement
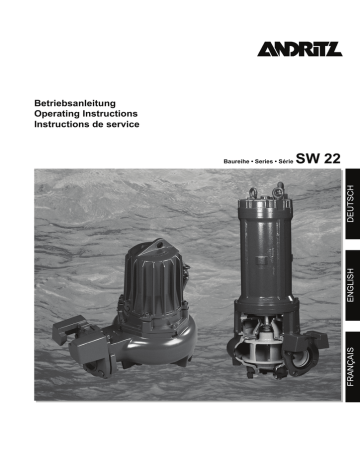
Series SW 22
3.4.3.3 Leak monitoring
Except for the AM1 motor, all motors are fitted with a moisture feeler. This sensor is installed in the oil chamber resp. in the connection space. In combination with the DG 110 control unit supplied as an accessory, it ensures secure and reliable monitoring of the mechanical seal for leaks. Depending on the type of the control unit, either the motor is automatically switched off or appropriate signals are issued if any water enters the oil chamber or the connecting space.
Leak monitoring oil chamber:
The electrical resistance of the oil in the chamber is measured by two sensors S1/S2. The sensors must be connected to a tripping unit in the control panel (electrode relays). In case of water entering the chamber through the shaft seals, the resistance will change. For explosion-proof models an intrinsicallysafe relay has to be chosen.
Leak monitoring connection space:
Two sensors S3/S4 are used for monitoring leaks into the connection chamber. The sensors must also be connected in the control panel to a tripping unit with galvanically separated safety circuit (electrode relays). For explosion-proof models an intrinsically-safe relay has to be choosen.
Control unit DG 110
L01 (L)
A1/A2 polarity = as required
The DG 110 is used for monitoring the conductivity of the pumps’ oil filling. This conductivity is an indicator for the amount of water that has penetrated inside. It is measured by an electrode that reaches into the oil chamber resp. into the connection space. The DG 110 is fitted with a sensitive measuring and switching amplifier with a relay output. The measuring voltage applied for the measurements is 2.5V. The theoretically possible measuring current is 0.1mA. The threshold value of the relay is 100kOhm. The relay picks up when the measured value drops below this threshold. This state is indicated by a red lightemitting diode on the control unit. The input circuit is fitted with a filter against noise pulses. An isolating transformer isolates the measuring circuit from the mains voltage.
3.5
Dimensions, weights, centers of gravity, capacity
On request.
Weight: refer to the documentation related to the contract.
3.6
Installation requirements
1-
2+
L0 (N)
Sensor in the pump
A1
A2
11
12
14
• Protect the unit against atmospheric influences.
• Ensure sufficient ventilation, heating and cooling and heed any sound proofing regulations that might be applicable.
• Check that the unit and its components can be safely transported to or removed from the installation location without accidents. Make sure that the existing doors or openings are large enough.
• Make sure that the required lifting gear and the tools required for attaching the gear are available.
3.6.1
Space requirements for operation and maintenance
• Ensure that sufficient space, at least from 2 sides, is left for subsequent maintenance requirements. This space should have, for reason of good accessibility, min. 0.8 m width.
• The set should be easily accessible from all sides.
3.6.2
Subsoil, foundation
• The subsoil or concrete foundation must be sufficiently strong to ensure that the pump can be safely installed as required for proper functioning.
3.6.3
Supply connections
Check that all supplies like power, water and drainage necessary for installation and later operation are available in the form required.
4. Mounting/installation
Sensor in the pump
Sketch of the DG 110 control unit
Auxiliary voltage A1 - A2 220-240 V +/- 10%, 50/60 Hz
Special voltage 24 V u. 110/115 V 50/60 Hz
24 V = galvanically separated, unpoled
Current consumption 1.5 VA
Measuring voltage 1 - 2 2.5 V
Measuring current max. 0.1 mA
Switching threshold 100 kOhm +/- 5%
Operating mode
Output static current principle
1 change-over contact
For proper functioning, the pump must be installed in a careful and proper manner. Installation faults can cause injuries and damage and can also result in premature wear of the pump.
Check the oil level before installing the pump (refer to section 6.2.1).
4.1
Preliminary checks
• The building must have been prepared according to the dimensions given on the foundation and layout plans.
• Pay attention to the maximum depth of immersion of the pump (see pump label).
20
advertisement
Related manuals
advertisement
Table of contents
- 3 1. Sicherheitshinweise
- 3 2. Transport und Zwischenlagerung
- 3 2.1 Transportieren
- 3 2.2 Auspacken
- 3 2.3 Zwischenlagern
- 3 2.4 Konservieren
- 3 3. Beschreibung
- 4 3.1 Benennung
- 4 3.2 Konstruktiver Aufbau
- 4 3.3 Bauformen
- 4 3.4 Motor
- 7 3.5 Abmessungen, Gewichte, Schwerpunkte, Fassungsvermögen
- 7 3.6 Angaben zum Einsatzort
- 7 4. Aufstellung/Einbau
- 7 4.1 Überprüfung vor Aufstellungsbeginn
- 8 4.2 Stationäre Nassaufstellung (N)
- 8 4.3 Mobile Nassaufstellung (M)
- 8 4.4 Trockenaufstellung (TV, TH)
- 8 4.5 Vergießen und sonstige Abschlussarbeiten (N, TV, TH)
- 8 4.6 Rohrleitungen
- 8 5. Inbetriebnahme/Außerbetriebnahme
- 8 5.1 Fertigmachen zum Betrieb
- 9 5.2 Niveausteuerung
- 9 5.3 Inbetriebnahme
- 9 5.4 Außerbetriebnahme
- 10 6. Wartung/Instandhaltung
- 10 6.1 Sicherheitshinweise
- 10 6.2 Wartung und Inspektion
- 11 6.3 Demontage- und Montagehinweise
- 12 7. Störungen: Ursachen und Beseitigung
- 13 8. Anhang
- 13 8.1 Teileverzeichnis
- 26 8.2 Schnittbilder
- 15 1. Safety instructions
- 15 2. Handling and intermediate storage
- 15 2.1 Handling
- 15 2.2 Unpacking
- 15 2.3 Intermediate storage
- 15 2.4 Preservation
- 15 3. Description
- 16 3.1 Designation
- 16 3.2 Construction
- 16 3.3 Mounting arrangements
- 16 3.4 Motor
- 19 3.5 Dimensions, weights, centers of gravity, capacity
- 19 3.6 Installation requirements
- 19 4. Mounting/installation
- 19 4.1 Preliminary checks
- 20 4.2 Stationary wet-pit installation (N)
- 20 4.3 Mobile wet-pit installation (M)
- 20 4.4 Dry-pit installation (TV, TH)
- 20 4.5 Grouting of the pump and other final checks (N, TV, TH)
- 20 4.6 Piping
- 20 5. Commissioning/decommissioning
- 20 5.1 Preparing the pump for operation
- 21 5.2 Level control
- 21 5.3 Commissioning
- 21 5.4 Decommissioning
- 22 6. Maintenance/servicing
- 22 6.1 General notes
- 22 6.2 Maintenance and inspections
- 23 6.3 Disassembly and assembly instructions
- 24 7. Problems: causes and remedies
- 25 8. Appendix
- 25 8.1 Parts list
- 26 8.2 Sectional drawings