Blitz TWIN Works 650/500 H, TWIN Works 650/500 V, TWIN Works 650/270 V, TWIN Works 650/300 H, TWIN Works 530/500 H, TWIN Works 530/500 V, TWIN Works 530/270 V, TWIN Works 530/300 H, TWIN Works 780/500 H, TWIN Works 780/500 V Owner's manual
Add to My manuals46 Pages
advertisement
▼
Scroll to page 2
of
46
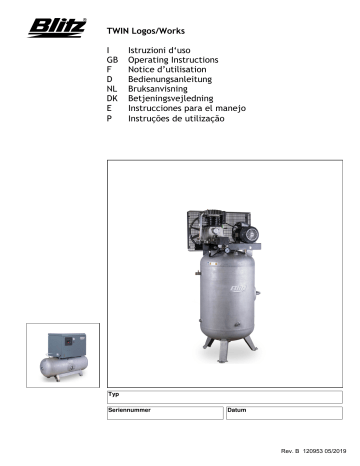
TWIN Logos/Works Istruzioni d‘uso Operating Instructions Notice d’utilisation Bedienungsanleitung Bruksanvisning Betjeningsvejledning Instrucciones para el manejo Instruções de utilização Typ Seriennummer Datum Rev. B 120953 05/2019 2 IT UK READ THE INSTRUCTION HANDBOOK Before positioning, operating or adjusting the compressor, read the instruction handbook carefully. FR DE NL DK ES PT IT UK RISK OF ELECTRIC SHOCK Caution: before doing any work on the compressor it must be disconnected from the power supply. FR DE NL DK ES PT 3 IT UK RISK OF HIGH TEMPERATURES Caution: the compressor contains some parts which might reach high temperatures. FR DE NL DK ES PT IT UK RISK OF ACCIDENTAL START-UP Attention, the compressor could start automatically after a power-cut if not switched off. FR DE NL DK ES PT IT 4 5 IT 6 7 1. 2. 3. 4. 5. 6. 7. 8. 9. 10. bar bar Hp/kW Min-1 dB(A) 8,5 8,5 8 8 0.65/0.5 0.65/0.5 1450 2850 73 75 8,5 8,5 8,5 8,5 8 8 8 8 0.75/0.65 1.5/1.1 2/1.5 2.5/1.8 1700/1450 3400/2850 3450/2850 2800 73 75 79 82 11. 12. 13. 1. 2. 3. 4. 5. 6. bar bar Hp/kW Min-1 dB(A) 10,5 10,5 10 10 1.5/1.1 2/1.5 1450 1700-1450 75 75 10,5 10,5 10,5 10 10 10 2.5/1.8 3/2.2 1.5/1.1 1450 2850 1450 75.5 80 75 SERBATOIO / TANK / RESERVOIR / KESSEL / TANK / BEHOLDER / DEPÓSITO / DEPÓSITO / SÄILIÖ / TANK MANOMETRO / PRESSURE GAUCE / MANOMETRE / MANOMETER / MANOMETER /TRYKMÅLER / MANÓMETRO / MANÓMETRO / MANOMETRI / MANOMETER PRESSOSTATO / PRESSURE SWITCH / PRESSOSTAT / DRUCKWÄCHTER / DRUKREGELAAR / PRESSOSTAT / PRESOSTATO / BARÓSTATO / PAINEMITTARI / TYCKMÄTARE MANICO / HANDLE / POIGNEE / SCHLAUCH / HANDVAT / HANK / MANIJA / ASA / KAHVA / HANDTAG CARENATURA DI PROTEZIONE / GUARD / CARENAGE DE PROTECTION / SCHUTZVERKLEIDUNG / BESCHERMINGSSTROOMLIJNKAP / STRØMLINIEBEKLÆDNING / CARENADURA DE PROTECCIÓN / COBERTURA DE PROTECÇÃO / SUOJUS / SKYDDSBEKLÄDNAD GRUPPO COMPRESSORE / COMPRESSOR UNIT / GROUPE COMPRESSEUR / KOMPRESSORAGGREGAT / COMPRESSOR GROEP / KOMPRESSORENHED / GRUPO COMPRESOR / GRUPO COMPRESSOR / KOMPRESSORIYKSIKKÖ / KOMPRESSORGRUPP FILTRI ARIA / AIR FILTER / FILTRE A AIR / LUFTFILTER / LUCHTFILTER / LUFTFILTER / FILTRO DE AIRE / FILTRO AR / ILMASUODATIN / LUFTFILTER ASTA LIVELLO OLIO / OIL LEVEL STICK / TIGE DE NIVEAU D’HUILE / ÖLSTAB / STOK OLIENIVEAU / OLIEMÅLEPIND / VARILLA NIVEL DE ACEITE / VARETA NÍVEL ÓLEO / ÖLJYTASOTANKO / OLJEMÄTSTICKA USCITA ARIA COMPRESSA RIDOTTA / REDUCED COMPRESSED AIR OUTLET / SORTIE RÉDUITE AIR COMPRIMÉ / REDUZIERTE DRUCKLUFTAUSGANG / UITGANG SAMENGEPERSTE LUCHT VERMINDERD / UDGANG FOR REDUCERET TRYKLUFT / SALIDA DEL AIRE COMPRIMIDO REDUCIDA / SAÍDA AR COMPRIMIDO REDUZIDA / PAINEILMAN VÄHENNETTY ULOSMENO / REDUCERAD TRYCKLUFTSUTGÅNG RIDUTTORE DI PRESSIONE / PRESSURE REDUCER / REDUCTEUR DE PRESSION / DRUCKMINDERER / DRUKREDUCTIEMACHINE /TRYKBEGRÆNSER / REDUCTOR DE PRESIÓN / REDUTOR DE PRESSÃO / PAINEENVÄHENTÄJÄ / TYCKREDUCERARE USCITA ARIA COMPRESSA DIRETTA / DIRECT COMPRESSED AIR OUTLET / SORTIE DIRECTE AIR COMPRIMÉ / DIREKTER DRUCKLUFTAUSGANG/ UITGANG SAMENGEPERSTE LUCHT DIRECT / UDGANG FOR DIREKTE LUFTTRYK / SALIDA DEL AIRE COMPRIMIDO DIRECTA / SAÍDA AR COMPRIMIDO DIRECTA / PAINEILMAN SUORA ULOSMENO / DIREKT TRYCKLUFTSUTGÅNG RUOTA / WHEEL / ROUE / RAD / WIEL / HJUL / RUEDA / RODA / PYÖRÄ / HJUL VALVOLA DI NON RITORNO / CHECK VALVE / VANNE DE NON-RETOUR / RÜCKSCHLAGVENTIL / KLEP VOOR NIET TERUGKEER / KONTRAVENTIL/ VÁLVULA DE ANTIRRETROCESO / VÁLVULA DE NÃO RETORNO / TAKAISKUVENTTIILI / VENTIL UTAN ÅTERGÅNG. SCARICO CONDENSA / CONDENSATE DRAIN / EVACUATION CONDENSATION / AUSLASS KONDENSWASSER / AFVOER CONDENSWATER / TØMNING AF KONDENSVAND / DESAGÜE DEL CONDENSADO / PURGA DA CONDENSAÇÃO / KONDENSSIVEDEN TYHJENNYS / KONDENSVATTNETS AVLOPP. CARENATURA DI PROTEZIONE / GUARD / CARENAGE DE PROTECTION / SCHUTZVERKLEIDUNG / BESCHERMINGSSTROOMLIJNKAP / STRØMLINIEBEKLÆDNING / CARENADURA DE PROTECCIÓN / COBERTURA DE PROTECÇÃO / SUOJUS / SKYDDSBEKLÄDNAD TAPPO SFIATO OLIO / BREATHER PLUG / BOUCHON DE PURGE / ENTLUFTUN GSSTOPFEN / VENTILPROP / TAPON DE PURGA / TAMPAO DE PURGA / ILMATULPPAAN / LUFTHAL MANICO / HANDLE / POIGNEE / SCHLAUCH / HANDVAT / HANK / MANIJA / ASA / KAHVA / HANDTAG PRESSOSTATO / PRESSURE SWITCH / PRESSOSTAT / DRUCKWÄCHTER / DRUKREGELAAR / PRESSOSTAT / PRESOSTATO / BARÓSTATO / PAINEMITTARI / TYCKMÄTARE RUOTA / WHEEL / ROUE / RAD / WIEL / HJUL / RUEDA / RODA / PYÖRÄ / HJUL SERBATOIO / TANK / RESERVOIR / KESSEL / TANK / BEHOLDER / DEPÓSITO / DEPÓSITO / SÄILIÖ / TANK IT 8 1. 2. 3. 4. 5. 6. 7. 8. 9. 10. 11. 12. (1) bar bar Hp/kW Min-1 10,5 10,5 10,5 10,5 10,5 10,5 10,5 10,5 10,5 10 10 10 10 10 10 10 10 10 10,5 10,5 10,5 10,5 10 10 10 10 2-1.5 2-1.5 3-2.25 3-2.25 4-3 4-3 4-3 5.5-4.1 5.5-4.1 7.5-5.5 77 78 80 80 85 81 82 83 84 83 10-7.5 15 – 11 20 - 15 88 90 90 dB(A) 1. 2. 3. 4. (1) USCITA ARIA COMPRESSA DIRETTA / DIRECT COMPRESSED AIR OUTLET / SORTIE DIRECTE AIR COMPRIMÉ / DIREKTER DRUCKLUFTAUSGANG / UITGANG SAMENGEPERSTE LUCHT DIRECT / UDGANG FOR DIREKTE LUFTTRYK / SALIDA DEL AIRE COMPRIMIDO DIRECTA / SAÍDA AR COMPRIMIDO DIRECTA / PAINEILMAN SUORA ULOSMENO / DIREKT TRYCKLUFTSUTGÅNG SERBATOIO / TANK / RESERVOIR / KESSEL / TANK / BEHOLDER / DEPÓSITO / DEPÓSITO / SÄILIÖ / TANK RIDUTTORE DI PRESSIONE / PRESSURE REDUCER / REDUCTEUR DE PRESSION / DRUCKMINDERER / DRUKREDUCTIEMACHINE / TRYKBEGRÆNSER / REDUCTOR DE PRESIÓN / REDUTOR DE PRESSÃO / PAINEENVÄHENTÄJÄ / TYCKREDUCERARE PARACINGHIA / BELT-GUARD / PROTECTION COURROIE / RIEMENSCHUTZ / KETTINGBESCHERMER / BESKYTTELSESSKÆRM FOR REM / CUBRECORREA / PROTECÇÃO DA CORREIA / HIHNASUOJUS / REMSKYDD GRUPPO COMPRESSORE / COMPRESSOR UNIT / GROUPE COMPRESSEUR / KOMPRESSORAGGREGAT / COMPRESSOR GROEP / KOMPRESSORENHED / GRUPO COMPRESOR / GRUPO COMPRESSOR / KOMPRESSORIYKSIKKÖ / KOMPRESSORGRUPP MOTORE ELETTRICO / ELECTRIC MOTOR / MOTEUR ÉLECTRIQUE / ELEKTROMOTOR / ELEKTRISCHE MOTOR / ELEKTRISK MOTOR / MOTOR ELÉCTRICO / MOTOR ELÉCTRICO / SÄHKÖMOOTTORI / ELMOTOR PRESSOSTATO / PRESSURE SWITCH / PRESSOSTAT / DRUCKWÄCHTER / DRUKREGELAAR / PRESSOSTAT / PRESOSTATO / BARÓSTATO / PAINEMITTARI / TYCKMÄTARE MANOMETRO / PRESSURE GAUCE / MANOMETRE / MANOMETER / MANOMETER / TRYKMÅLER / MANÓMETRO / MANÓMETRO / MANOMETRI / MANOMETER RUOTA PIVOTTANTE / PIVOT WHEEL / ROUE PIVOTANTE / SCHWENKRAD / DRAAIEND WIEL / HJULTAP / RUEDA PIVOTANTE / RODA GIRATÓRIA / KÄÄNTÖPYÖRÄ / ROTERANDE HJUL SCARICO CONDENSA / CONDENSATE DRAIN / EVACUATION CONDENSATION / AUSLASS KONDENSWASSER / AFVOER CONDENSWATER / TØMNING AF KONDENSVAND / DESAGÜE DEL CONDENSADO / PURGA DA CONDENSAÇÃO / KONDENSSIVEDEN TYHJENNYS / KONDENSVATTNETS AVLOPP RUOTA / WHEEL / ROUE / RAD / WIEL / HJUL / RUEDA / RODA / PYÖRÄ / HJUL VALVOLA DI RITEGNO / CHECK VALVE / VANNE DE RETENNE / RÜCKSCHLAGVENTIL / TEGENHOUDKLEP / KONTRAVENTIL / VÁLVULA DE RETENCIÓN / VÁLVULA DE RETENÇÃO / TAKAISKUVENTTIILI / STOPPVENTIL MOTORE ELETTRICO / ELECTRIC MOTOR / MOTEUR ÉLECTRIQUE / ELEKTROMOTOR / ELEKTRISCHE MOTOR / ELEKTRISK MOTOR / MOTOR ELÉCTRICO / MOTOR ELÉCTRICO / SÄHKÖMOOTTORI / ELMOTOR PARACINGHIA / BELT-GUARD / PROTECTION COURROIE / RIEMENSCHUTZ / KETTINGBESCHERMER / BESKYTTELSESSKÆRM FOR REM / CUBRECORREA / PROTECÇÃO DA CORREIA / HIHNASUOJUS / REMSKYDD GRUPPO COMPRESSORE / COMPRESSOR UNIT / GROUPE COMPRESSEUR / KOMPRESSORAGGREGAT / COMPRESSOR GROEP / KOMPRESSORENHED / GRUPO COMPRESOR / GRUPO COMPRESSOR / KOMPRESSORIYKSIKKÖ / KOMPRESSORGRUPP CENTRALIANA AVVIAMENTO YD / STARTING CONTROL UNIT YD / BOÎTIER DE DÉMARRAGE Y? / STERNDREIECKANLASSER / CENTRALE OPSTARTEN UD / ELEKTRONISK BETJENINGSPANEL FOR START YD / CENTRAL DE PUESTA EN MARCHA YD / CAIXA DE ARRANQUE YD / KÄYNNISTYS VAIHDELAATIKKO YD / STARTCENTRAL YD Livello sonoro misurato in campo libero a 1 m di distanza ±3dB(A) alla massima pressione di utilizzo. Acoustic pressure measured free-field at a distance of 1m: ±3dB(A) at maximum operating pressure. Niveau sonore mesuré en champs libre à 1 m de distance ± 3dB(A) à la pression d’utilisation maximum. Gemessene Schallpegel in einem Abstand von 1 m ±3dB(A) bei max Geluidsniveau gemeten in vrij veld op 1 m afstand ±3dB (A) bij de maximum gebruiksdruk Gemessene Schallpegel in einem Abstand von 1 m ±3dB(A) bei max. Nivel sonoro medido en campo libre a 1 m de distancia ±3dB (A) a la máxima presión de trabajo. Nível sonoro medido em campo livre a 1 m de distância ±3dB(A) à pressão máxima de utilização. IT IT 10 Kw 0,75 - 1 1,5 2 2,5 - 3 0,65–0,7 1,1 1,5 1,8 – 2,2 220/230 V [mm2] 1,5 2,5 2,5 4 110/120 V [mm2] 2,5 4 4–6 / Tab. 2 SEZIONE VALIDA PER LA LUNGHEZZA MASSIMA 20 mt trifase CV Kw 2-3-4 5,5 7,5 10 15 20 1,5-2,2-3 4 5,5 7,5 11 15 230 V [mm2] 2,5 4 6 10 16 25 380/400V 1.5 2.5 2.5 4 10 16 Kw 1,5-2,2.3 5,5-7,5-10 4-5,5-7,5 15 - 20 11 - 15 Alimen. Volt/ph 220/230/3 380/400/3 220/230/3 380/400/3 220/230/3 380/400/3 IT 13 IMPORTANT INFORMATION Read and understand all of the operating instructions, safety precautions and warnings in the Instruction Manual before operating or maintaining this compressor. Most accidents that result from compressor operation and maintenance are caused by the failure to observe basic safety rules or precautions. An accident can often be avoided by recognizing a potentially hazardous situation before it occurs, and by observing appropriate safety procedures. Basic safety precautions are outlined in the “SAFETY” section of this Instruction Manual nad in the sections which contain the operation and maintenance instructions. Hazards that must be avoided to prevent bodily injury or machine damage are identified by WARNINGS on the compressor and in this Instruction Manual. Never use this compressor in a manner that has not been specifically recommended by manufacturer, unless you first confirm that the planned use will be safe for you and others. MEANINGS OF SIGNAL WORDS WARNING: indicates a potentially hazardous situations which, if ignored, could result in serious personal injury. CAUTION: indicates a hazardous situations which, if ignored, couls result moderate personal injury, or could cause machine damage. NOTE: emphasizes essential information IMPORTANT SAFETY INSTRUCTIONS FOR USE OF THE COMPRESSOR. WARNING: DEATH OR SERIOUS BODILY INJURY COULD RESULT FROM IMPROPER OR UNSAFE USE OF COMPRESSOR. TO AVOID THESE RISKS, FOLLOW THESE BASIC SAFETY INSTRUCTIONS. READ ALL INSTRUCTIONS 1. NEVER TOUCH MOVING PARTS Never place your hands, fingers or other body parts near the compressor’s moving parts. 2. NEVER OPERATE WITHOUT ALL GUARDS IN PLACE Never operate this compressor without all guards or safety features in place and in proper working order. If maintenance or servicing requires the removal of a guard or safety features, be sure to replace the guards or safety feature before resuming operation of the compressor. 3. ALWAYS WEAR EYE PROTECTION Always wear safety goggles or equivalent eye protection. Compressed air must never be aimed at anyone or any part of the body. 4. PROTECT YOURSELF AGAINST ELECTRIC SHOCK Prevent body contact with grounded surfaces such as pipes, radiators, ranges and refrigeration enclosures. Never operate the compressor in damp or wet locations. 5. DISCONNECT THE COMPRESSOR Always disconnect the compressor from the power source and remove the compressed air from the air tank before servicing, inspecting, maintaining, cleaning, replacing or checking any parts. 6. AVOID UNINTENTIONAL STARTING Do not carry the compressor while it is connected to its power source or when the air tank is filled with compressed air. Be sure the knob of the pressure switch in the “OFF” position before connecting the compressor to its power source. 7. STORE COMPRESSOR PROPERLY When not in use, the compressor should be stored in dry place. Keep out of reach of children. Lock-out the storage area. 8. KEEP WORK AREA CLEAN Cluttered areas invite injurues. Clear all work areas of unnecessary tools, debris, furniture etc… 9. KEEP CHILDREN AWAY Do not let visitors contact compressor extension cord. Alla visitors should be kept safely away from work area. 10. DRESS PROPERLY Do not wear loose clothing or jewerly. They can be caught in moving parts. Wear protective hair covering to contain long hair. 11. DON’T ABUSE CORD Never yank it to disconnect from receptable. Keep cord from heat, oil and sharp edges. 12. MAINTAIN COMPRESSOR WITH CARE GB Follow instructions for lubricating. Inspect cords periodically and if damaged, have repaired by authorized service facility. Inspect extension cords periodically and replace if damaged. 13. OUTDOOR USE EXTENSION CORDS When compressor in used outdoors, use only extension cords intended for use outdoors and so marked. 14. STAY ALERT Watch what you are doing. Use common sense. Do not operate compressor when you are tired. Compressor should never be used by you if you are under the influence of alcohol, drugs or medication that makes you drowsy. 15. CHECK DAMAGED PARTS AND AIR LEAK Before further use of the compressor, a guard or other part is damaged should be carefully checked to determine that it will operate properly and perform its intended function. Check for alignment of moving parts, binding of moving parts, breakage of parts, mounting, air leak, and any other conditions that may affect its operation. A guard or other part that is damaged should be properly repaired or replaced by an authorized service center unless otherwise indicated elsewhere in this Instruction Manual. Have defective pressure switches replaced by authorized service center. Do not use compressor if switch does not turn it on and off. 16. HANDLE COMPRESSOR CORRECTLY Operate the compressor according to the instructions provided herein. Never allow the compressor to be operated by children, individuals unfamiliar with its operation or unauthorized personnel. 17. KEEP ALL SCREWS, BOLTS AND COVERS TIGHTLY IN PLACE Keep all screws, bolts, and plates tightly mounted. Check their condtions periodically. 18. KEEP MOTOR AIR VENT CLEAN The motor air vent must be kept clean so that air can freely flow at all times. Check for dust build-up frequently. 19. OPERATE COMPRESSOR AT THE RATED VOLTAGE Operate the compressor at voltages specified on their nameplates. If using the compressor at a higher voltage than the rated voltage, it will result in abnormally fast motor revolution and mey damage the unit and burn out the motor. 20. NEVER USE A COMPRESSOR WHICH IS DEFECTIVE OR OPERATING ABNORMALLY If the compressor appears to be operating unusually, making strange noises, or otherwise appears defective, stop using it immediately and arrange for repairs by a authorized service center. 21. DO NOT WIPE PLASTIC PARTS WITH SOLVENT Solvents such as gasoline, thinner, benzine, carbon tetrachloride, and alcohol may damage and crack plastic parts. Do not wipe them with such solvents. Wipe plastic parts with a soft cloth lightly dampened with soapy water and dry thoroughly. 22. USE ONLY GENUINE REPLACEMENT PARTS Replacement parts not original may void your warranty and can lead to malfunction and resulting injuries. Genuine parts are available from your dealer. 23. DO NOT MODIFY THE COMPRESSOR Do not modify the compressor. Always contact the authorized service center any repairs. Unauthorized modification may not only impair the compressor performance but may also result in accident or injury to repair personnel who do not have the required knowledge and technical expertise to perform the repair operations correctly. 24. TURN OFF THE PRESSURE SWITCH WHEN THE COMPRESSOR IS NOT USED When the compressor is not used, turn the knob of the pressure switch OFF, disconnect it from the power source and open the drain cock to discharge the compressed air from the air tank. 25. NEVER TOUCH HOT SURFACE To reduce the risk of burns, do not touch tubes, heads, cylinder and motors. 26. DO NOT DIRECT AIR STREAM AT BODY Risk of injury, do not direct air stream at persons or animals. 27. DRAIN TANK Drain tank daily or after 4 hours of use. Open drain fitting and tilt compressor to empty accumulated water. 28. DO NOT STOP COMPRESSOR BY PULLING OUT THE PLUG Use the “AUTO/OFF” knob of pressure switch. 29. USE ONLY RECOMMENDED AIR HANDLING PARTS ACCEPTABLE FOR PRESSURE NOT LESS THAN 125 PSI (8.6 BAR) GB 14 Risk of bursting. Use only recommended air handling parts acceptable for pressures not less than 125 psi (8.6 bar). REPLACEMENT PARTS When servicing use only identical replacement parts. Repairs should be conducted only by authorized service center. GROUNDING INSTRUCTIONS This compressor should be grounded while in use to protect the operator from electric shock. The compressor is equipped with a threeconductor cord and three-prong grounding type plug to fit the proper grounding type receptacle. The green (or green and yellow) conductor in the cord is the grounding wire. Never connect the green (or green and yellow) wire to a live terminal. If your units is for use on less than 150 volts, it has a plug that looks like that shown in sketch (A) in figure on the right. An adapter, see sketches (B) and (C), is available for connecting sketch (A) type plugs to twoprong receptacles. The green-colored rigid ear, lug, or the like extending from the adapter must be connected to a permanent ground, such as a properly grounded outlet box. NOTE: the grounding adaptor, sketch (C), is prohibited in Canada by Canadian Electrical Code Part.1. Therefore, the instructions for its use are not applicable in Canada. EXTENSION CORD Use only three-extension cords that have three-prong grounding type plugs and three-pole receptables that accept the compressor’s plug. Replace or repair damaged cord. Make sure your extension cord is in good condition. When using an extension cord, be sure to use one heavy enough to carry the current your product will draw. An undersized cord will cause a drop in line voltage resulting in loss of power and overheating. Table shows the correct size to use depending on cord lenght and name plate ampere rating. If in doubt, use the next heavier gage. The smaller the gage number, the heavier the cord. Tab.1 SECTION VALID FOR A MAX LENGHT OF 20 mt singlephase HP Kw 0,75 - 1 1,5 2 2,5 - 3 0,65–0,7 1,1 1,5 1,8 – 2,2 220/230 V [mm2] 1,5 2,5 2,5 4 110/120 V [mm2] 2,5 4 4–6 / The diameter of the extension cable of the 3-phase compressors must be in proportion to its length: see table (tab 2) Tab. 2 SECTION VALID FOR A MAX LENGHT OF 20 mt threephase HP Kw 2-3-4 5,5 7,5 10 15 20 1,5-2,2-3 4 5,5 7,5 11 15 230 V [mm2] 2,5 4 6 10 16 25 380/400V 1.5 2.5 2.5 4 10 16 WARNING Avoid electrical shock hazard. Never use this compressor with a damaged or frayed electrical cord or extension cord. Inspect all electrical cords regularly. Never use in near water or in any environment where electric shock is possible SAVE THESE INSTRUCTION AND MAKE THEM AVAILABLE TO OTHER USERS OF THIS TOOL! OPERATION AND MAINTENANCE NOTE: The information contained in this Instruction Manual is designed to assist you in the safe operation and maintenance of the compressor. Some illustrations in this Instruction Manual may show details or attachments that differ from those on your own compressor. INSTALLATION Remove the compressor from its packing (fig.1), makes sure it is in perfect condition, checking if it was damaged during transport, and carry out the following operations. Fit the wheels and rubber tab on the tanks on which they are not already fitted, observing the instructions in fig.2. In case of infiatable wheels, the maximum inflation pressure must be of 1,6 bar (24 psi). Position the compressor on a flat surface or with a maximum permissible inclination of 10° (fig. 3), in a well aired place, protected against atmospheric agents and not in a place subject to explosion hazard. If the surface is inclined and smooth, check if the compressor moves while in operation – if it does, secure the wheels with two wedges. If the surface is a bracket or a shelf top, make sure it cannot fall, securing it in a suitable way. To ensure good ventilation and efficient cooling, the compressor’s belt guard must be at least 100 cm from any wall (fig. 4). Compressors fitted on the tank, with fixed feet, should not be rigidly secured to the ground. In this case, we advise you to fit 4 anti-vibration supports. USE INSTRUCTIONS – Take care to transport the compressor correctly, do not overturn it or lift it with hooks or ropes (fig. 5 - 6) – Replace the plastic plug on the guard cover (fig. 7 - 8) with the oil level stick (fig. 9) or with the relevant breather plug (fig. 10), supplied with the instructions booklet. Check oil level, consulting the reference marks on the stick (fig. 9) or the oil level inspection window (fig. 11). ELECTRICAL CONNECTION Single-phase compressors are supplied with an electrical cable and a two-pole + earth plug. The compressor must be connected to a grounded power socket (fig.12). Three-phase compressors (L1+L2+L3+PE) must be installed by a specialised technician. Three-phase compressors are supplied without a plug. Connect a plug, with screw-on grommet and securing collar (fig.13), to the cable, consulting the table below. Hp 2-3-4 Kw 1,5-2,2.3 5,5-7,5-10 4-5,5-7,5 15 - 20 11 - 15 Power supply volt/ph 220/230/3 380/400/3 220/230/3 380/400/3 220/230/3 380/400/3 Plug model 16 A 3 pole+ground 16 A 3 pole+ground 32 A 3 pole+ground 32 A 3 pole+ground 63 A 3 pole+ground 32 A 3 pole+ground NOTE: Compressors installed on the 500 lt tank, with capacity of HP7.5/ 55 kW and HP10/7.5 kW can be supplied a star/triangle starting control unit. Installation instructions: – Secure the control unit box on a wall or on a fixed support, and provide it with a power cable with plug, of a diameter in proportion to its length. – Any damage caused by incorrect connections of the power line to the mains, automatically excludes warranty of electrical parts. To avoid connection errors, we advise you to contact a specialised technician. IMPORTANT: Never use the ground socket instead of the neutral wire. The ground connection must be made to meet safety standards(EN 60204). The plug of the power cable must not be used as a switch, but must be fitted in a power socket controlled by a suitable differential switch (thermalbreaker). STARTING Check that the mains power matches that indicated on the electrical data-plate (fig.14) – the permissible tolerance range is +/-5%. When first starting compressors operating on 3-phase voltage, check the rotation direction of the cooling fan by comparing it with the direction of the arrow on the belt guard or on the protective housing. Turn or press into position “0” (according to the type of pressure switch fitted on the appliance) the knob located on the upper section GB 15 (fig. 15). Fit the plug in the power socket (fig. 12 - 13) and start the compressor, turning the pressure switch knob into position “I”. The compressor is fully automatic, and is controlled by the pressure switch which stops it when tank pressure reaches maximum value and restarts it when it falls to minimum value. The pressure difference between maximum and minimum values is usually about 2 bar (29 psi). E.g.: the compressor stops when it reaches 8 bar (116 psi – maximum operating pressure) and restarts automatically when the pressure inside the tank drops to 6 bar (87 psi). After connecting the compressor to the power line, load it to maximum pressure and check exactly how the machine is operating. COMPRESSORS WITH D STARTING CONTROL UNIT (fig. 16) Fit the plug in the power socket (fig. 13) and turn the pressure switch to position “I” (ON) (fig. 17). Turn the master power switch “A” on the control unit to position I – power On is signalled by white indicatorlight “E” going on. Turn switch “B” to position 1 to start the compressor. If the solenoid-valve indicator-light “D” and the motor (C) indicator-light (C) go on in that order, this means the machine is operating perfectly (fig. 18). TANDEM COMPRESSORS WITH TIMED CONTROL UNIT (fi g. 17) Fit the plug in the power socket (fi g. 13) and turn the pressure switch to position “I” (ON). Turn the master power switch “A” on the control unit to position I – power On is signalled by white indicator-light “E” going on. Turn switch “B” to start the compressor. Pos. 1 pumping element n. 1 only is operating Pos. 2 pumping element n. 2 only is operating Pos. 3 both pumping elements are operating simultaneously, at staggered starting times. The compressor is fully automatic, and is controlled by the pressure switch which stops it when tank pressure reaches maximum value and restarts it when it falls to minimum value. IMPORTANT The electro-compressors must be connected to a power socket protected by a suitable differential switch (thermal-breaker). The motor of coaxial compressors is equipped with an automatic thermal breaker located inside the winding – this stops the compressor when motor temperature reaches excessively high values. If the breaker is tripped, the compressors restarts automatically after 10 to 15 minutes. The motors of compressor models coaxial double cylinders are supplied with a manually resetting automatic amperometric thermal-breaker, located outside the terminal board cover. When the breaker is tripped, wait for a few minutes and then reset the breaker manually (fig. 20). The motors of the belt drive series compressors are supplied with a manually resetting amperometric thermal-breaker, located on the terminal board cover. When the breaker is tripped, wait for a few minutes and then reset the breaker manually (fig. 20). The safety davice is automatic in three-phase and silent compressors. When the thermal-breaker is tripped, the pressure switch is released to “0” (OFF) position. Wait for a few minutes and return the pressure switch to “I” (ON) position. For compressors supplied with a control unit, the thermalbreaker is installed inside the control unit. When the thermal-breaker is tripped, observe the following procedure (fig. 22): • Turn the switches on the control unit cover to position “0”, open the cover and press push-button 1 of the thermal-breaker. Close the cover of the control unit and restart the compressor, observing the operations described in the paragraph “Starting compressors with control unit”. The same instructions apply to compressors powered at 60 Hz. ADJUSTING OPERATING PRESSURE (fig. 23) You do not have to use the maximum operating pressure at all times. On the contrary, the pneumatic tool being used often requires less pressure. On compressors supplied with a pressure reducer, operating pressure must be correctly adjusted. Release the pressure reducer knob by pulling it up, adjust pressure to the required value by turning the knob clockwise to increase pressure and anti-clockwise to reduce it. When you have obtained optimum pressure, lock the knob by pressing it downward (fig. 23). For pres- sure reducers equipped without a pressure gauge, the set pressure can be seen on the graduated scale located on the reducer body. On pressure reducers equipped with a pressure gauge, pressure can be seen on the gauge itself. WARNING: Some pressure regulators do not have "push to lock", therefore simply turn the knob to adjust the pressure. MAINTENANCE Before attempting any maintenance jobs on the compressor, make sure of the following: – Master power switch in position “0”. – Pressure switch and the control unit switches all off, in position “0”. – No pressure in the air tank. Every 50 hours of duty: we advise you to dismantle the suction filter and clean the filtering element by blowing compressed air on it (fig. 24). You are recommended to replace the filter element at least once if the compressor operates in a clean environment, but more frequently if in a dusty environment. The compressor generates condensate water which accumulates in the tank. The condensate in the tank must be drained at least once a week, by opening the drain tap (fig. 26) under the tank. Take care if there is compressed air inside the cylinder, and water could flow out with considerable force. Recommended pressure: 1 – 2 bar max. Condensate of compressors that are oil lubricated must not be drained into the sewer or dispersed in the environment as it contains oil. OIL CHANGES – TOPPING UP WITH OIL The compressor is filled with synthetic oil. We recommend a full change of oil in the pumping element within the first 100 hours of duty. Unscrew the oil drain plug on the housing cover, allow all the oil to flow out, and re-screw the plug (fig. 27 - 28). Pour oil into the upper hole of the housing cover (fig. 29 - 30) until it reaches the level indicated on the stick (fig. 9) or indicator (fig. 11) Pour oil into the upper hole of the head (fig. 30) in belt assisted units designed for topping up in that area. Once a week: check oil level of the pumping element (fig. 11) and see if it needs topping up. For operation at ambient temperature in the range -5°C to +40°C, use synthetic oil. The advantage of this oil is that is does not lose its characteristics either in winter or summer. Do not drain used oil into the sewer or dispose of it in the environment. OBSERVE THIS TABLE FOR OIL CHANGES TYPE OF OIL HOURS OF DUTY Synthetic Oil...................................500 Mineral Oil…………………………….100 WHAT TO DO IF SMALL MALFUNCTIONS OCCUR Loss of air in valve under pressure switch This trouble depends on poor tightness of the check valve – take the following action (fig. 31): – Discharge all pressure from the tank - Unscrew the hexagon-head of the valve (A) - Carefully clean both the rubber disk (B) and its seat. - Refit all parts accurately. Air losses These can be caused by poor tightness of a union – check all unions, wetting them with soapy water. Compressor turns but does not load Coaxial compressors: (fig. 32) - this may be due to failure of the valves (C1 – C2) or of a seal (B1 – B2): replace the damaged part. Pulley drive compressors: (fig. 33) - this may be due to failure of the valves F1 and F2 or of a seal (D1 – D2): replace the damaged part. Compressor no starting If the compressor has trouble starting, check the following : - Does mains power match that of the data-plate? (fig. 14) - Are power cable extensions of adequate diameter or length? - Is the work environment too cold? (under 0°C) GB - For belt drive series the thermal-breaker tripped (fig. 20). - Is there oil in the housing to ensure lubrication? (fig. 11) - Is power supplied to the electrical line? (sockets well connected, thermal- breaker, fuses in good condition). Compressor not stopping - If the compressor does not stop when maximum pressure is reached, the tank safety valve comes into operation. To repair the valve, contact your nearest service centre. IMPORTANT - Do not on any account unscrew any connection while the tank is pressurised – always check if the tank is pressure free. - Do not drill holes, weld or purposely deform the compressed air tank. - Do not do any jobs on the compressor unless you have disconnected the power plug. - Temperature in operating ambient: 0°C +35°C. - Do not aim jets of water or inflammable liquids on the compressor. - Do not place inflammable objects near the compressor. - During down-times, turn the pressure switch to position “0” (OFF). - Never aim the air jet at people or animals (fig. 34) - Do not transport the compressor while the tank is pressurised. - Be careful with regard to some parts of the compressor such as the head and delivery tubes, as they can reach high temperatures. Do not touch these parts to avoid burns.(fig. 18 - 19) - Transport the compressor, lifting or pulling it with the appropriate grips or handles (fig. 4 - 6) - Keep children and animals well away from the machine operating area. - If using the compressor for painting: a) Do not work in closed environments or near to naked flames b) Make sure there is adequate exchange of air at the place of work c) Protect your nose and mouth with an appropriate mask. (fig. 35) - If the electrical cable or plug are damaged, do not use the compressor and contact an authorised service centre to replace the faulty element with an original spare part. - If the compressor is located on a shelf or on a top above floor height, t must be secured to prevent it falling while in operation. - Do not put objects or your hands inside the protective grilles to avoid njury to yourself or damaging the compressor. (fig. 36) - Do not use the compressor as a blunt object toward things or animals, o avoid serious damage. - When you have finished using the compressor, always remove the lug from the power socket. N.B. Two-stage compressors can be supplied on request for use up to 4 bar. In this case: Maximum operating pressure 14.75 bar Minimum operating pressure 14 bar NOTE: For the European market, the compressor tanks are manufactured to meet Directive CE87/404 For the European market, the compressors are manufactured to meet Directive 2006/42 EC. The level of acoustic pressure can increase from 1 to 10 dB(A) according to the place in which the compressor is installed. HINTS FOR EFFICIENT OPERATION - For efficient operation of the machine at full continuing load and at maximum operating pressure, make sure the temperature of the work environment indoors does not exceed +25°C. - We advise you to use the compressor at 70% maximum duty per hour at full load as this ensures efficient operation of the product long-term. STORING THE PACKED AND UNPACKED COMPRESSOR For the whole time that the compressor is not used before unpacking it, store it in a dry place at a temperature between +5°C and + 45°C and sheltered away from weather. For the whole time that the compressor is not used after unpacking it, while waiting to start it up or due to production stoppages, place sheets over it to protect it from dust, which may settle on the components. The oil is to be replaced and the operational efficiency of the compressor is to be checked if it is not used for long periods. 16 PNEUMATIC CONNECTIONS Make sure you always use pneumatic tubes for compressed air with maximum pressure characteristics that are adequate for the compressor. Do not attempt to repair tubes if faulty. WE RESERVE THE RIGHT TO MAKE ANY MODIFICATIONS WITHOUT PRIOR NOTICE WHENEVER NECESSARY. 17 FR FR 18 Tab. 1 SECTION VALABLE POUR UNE LONGUEUR MAXIMUM DE 20 mt monophasé CH Kw 0,75 - 1 1,5 2 2,5 - 3 0,65–0,7 1,1 1,5 1,8 – 2,2 220/230 V [mm2] 1,5 2,5 2,5 4 110/120 V [mm2] 2,5 4 4–6 / Kw 2-3-4 5,5 7,5 10 15 20 1,5-2,2-3 4 5,5 7,5 11 15 220/230 V [mm2] 2,5 4 6 10 16 25 380/400V 1.5 2.5 2.5 4 10 16 19 Kw 1,5-2,2.3 5,5-7,5-10 4-5,5-7,5 15 - 20 11 - 15 FR FR 20 21 DE DE 22 Kw 0,75 - 1 1,5 2 2,5 - 3 0,65–0,7 1,1 1,5 1,8 – 2,2 220/230 V [mm2] 1,5 2,5 2,5 4 110/120 V [mm2] 2,5 4 4–6 / Kw 2-3-4 5,5 7,5 10 15 20 1,5-2,2-3 4 5,5 7,5 11 15 220/230 V [mm2] 2,5 4 6 10 16 25 380/400V 1.5 2.5 2.5 4 10 16 23 Kw 1,5-2,2.3 5,5-7,5-10 4-5,5-7,5 15 - 20 11 - 15 DE DE 24 25 DE NL 26 NL 27 WAARSCHUWINGEN PK Kw 0,75 - 1 1,5 2 2,5 - 3 0,65–0,7 1,1 1,5 1,8 – 2,2 220/230 V [mm2] 1,5 2,5 2,5 4 110/120 V [mm2] 2,5 4 4–6 / Kw 2-3-4 5,5 7,5 10 15 20 1,5-2,2-3 4 5,5 7,5 11 15 220/230 V [mm2] 2,5 4 6 10 16 25 380/400V 1.5 2.5 2.5 4 10 16 NL 28 Kw 1,5-2,2.3 5,5-7,510 4-5,5-7,5 15 - 20 11 - 15 Modell Stecker 16 A 3 polen + aardig 16 A 3 polen + aardig 32 A 3 polen + aardig 380/400/3 220/230/3 380/400/3 32 A 3 polen + aardig 63 A 3 polen + aardig 32 A 3 polen + aardig 29 NL NL 30 31 DK DK 32 Kw 0,75 - 1 1,5 2 2,5 - 3 0,65–0,7 1,1 1,5 1,8 – 2,2 220/230 V [mm2] 1,5 2,5 2,5 4 110/120 V [mm2] 2,5 4 4–6 / Kw 2-3-4 1,5-2,2-3 220/230 V [mm2] 2,5 380/400V 1.5 5,5 7,5 10 15 20 4 5,5 7,5 11 15 4 6 10 16 25 2.5 2.5 4 10 16 Kw 1,5-2,2.3 5,5-7,5-10 4-5,5-7,5 15 - 20 11 - 15 Strømfor. volt/ph 220/230/3 380/400/3 220/230/3 380/400/3 220/230/3 380/400/3 DK 33 ARBEJDSTIMER Syntetisk Olie..................................................500 DK 34 35 ES ES 36 ADVERTENCIAS CV Kw 0,75 - 1 1,5 2 2,5 - 3 0,65–0,7 1,1 1,5 1,8 – 2,2 220/230 V [mm2] 1,5 2,5 2,5 4 110/120 V [mm2] 2,5 4 4–6 / Kw 2-3-4 5,5 7,5 10 15 20 1,5-2,2-3 4 5,5 7,5 11 15 220/230 V [mm2] 2,5 4 6 10 16 25 380/400V 1.5 2.5 2.5 4 10 16 37 Kw 1,5-2,2.3 5,5-7,5-10 4-5,5-7,5 15 - 20 11 - 15 Aliment. volt/ph 220/230/3 380/400/3 220/230/3 380/400/3 220/230/3 380/400/3 ES ES 38 39 PT PT 40 AVISOS Kw 0,75 - 1 1,5 0,65–0,7 1,1 220/230 V [mm2] 1,5 2,5 110/120 V [mm2] 2,5 4 2 2,5 - 3 1,5 1,8 – 2,2 2,5 4 4–6 / CV Kw 2-3-4 5,5 7,5 10 15 20 1,5-2,2-3 4 5,5 7,5 11 15 220/230 V [mm2] 2,5 4 6 10 16 25 380/400V 1.5 2.5 2.5 4 10 16 41 Cv 2-3-4 Kw 1,5-2,2.3 5,5-7,510 4-5,5-7,5 15 - 20 11 - 15 220/230/3 380/400/3 220/230/3 380/400/3 220/230/3 380/400/3 PT PT 42 43 A P T TM 1-2-3-4-5-6 C M AU AM GB A P T TM 1-2-3-4-5-6 C M AU AM FR A P T TM 1-2-3-4-5-6 C M AU AM DE A P T TM 1-2-3-4-5-6 C M AU AM NL A P T TM 1-2-3-4-5-6 C M AU AM DK A P T TM 1-2-3-4-5-6 C M AU AM ES A P T TM 1-2-3-4-5-6 C M AU AM PT A P T TM 1-2-3-4-5-6 C M AU AM VDZ, VDZH, VDZS, VDZHS, VDZD, VDZHD, VGZ, VGZH, VZ, VZH DZ, DZH, DZS, DZHS, GZ, GZH, DZHP, GZHP, HV, NV DZNT, DZNDT, GZNT, GKTE, GKTZ, GKTZH Airmobil, Airstation, Hobby, Maximat, Maximat Pro, Kitty II Whisper, Medicus, VX DKD, DET, DEDT, GET, BKE, BKZ, BKES, BKZS, GKE, GKZ Logos, Logos H, Logos H Box, Works, Works H, Works H Box FORMULA: 28M, 36M, 57M, 38H, 52H, 65H, 38V, 52V, 65V TOURING: GT30H, GT42H, GT50H, GT32V, GT42V, GT50V POWERSTATION SLZ ........................................................ Baujahr : 20 ............. . EC Declaration of Conformity according to EC directive 2006/42/EC on machinery (Annex II A) Name and address of the manufacturer BlitzRotary GmbH Hüfinger Str.55 78199 Bräunlingen, Germany This declaration relates exclusively to the machinery in the state in which it was placed on the market, and excludes components which are added and/or operations carried out subsequently by the final user. The declaration is no more valid, if the product is modified without agreement. Herewith we declare, that the machinery described below product denomination Piston Compressor model / type VARIS VERSA TWIN VDZ, VDZH, VDZS, VDZHS, VDZD, VDZHD, VGZ, VGZH, VZ, VZH DZ, DZH, DZS, DZHS, GZ, GZH, DZHP, GZHP, HV, NV, DZNT, DZNDT, GZNT, GKTE, GKTZ, GKTZH Airmobil, Airstation, Hobby, Maximat, Maximat Pro, Kitty II, Whisper, Medicus, VX, DKD, DET, DEDT, GET, BKE, BKZ, BKES, BKZS, GKE, GKZ, Logos, Logos H, Logos H Box, Works, Works H, Works H Box FORMULA: 28M, 36M, 57M, 38H, 52H, 65H, 38V, 52V, 65V TOURING: GT30H, GT42H, GT50H, GT32V, GT42V, GT50V POWERSTATION SLZ machinery- / serial number ........................................................ Year of manufacture 20 ............. complies with all key provisions of Machinery Directive 2006/42/EC. Furthermore, the machine complies with the provisions of the Electromagnetic Compatibility Directive 2014/30/EU and the Low Voltage Directive 2014/35/EU (safety standards have been met pursuant to Annex I, No. 1.5.1 of the Machinery Directive 2006/42/EC). Furthermore, the machine complies with the provisions of the Simple Vessels Directive 2014/29/EU Harmonised Standards used EN 1012-1:2011-02 EN 60204-1: 2014-10 EN ISO 12100:2011-03 EN ISO 12100:2011-03 EN ISO 12100:2011-03 Compressors and vacuum pumps - Safety requirements - Part 1 Safety of machinery - Electrical equipment of machines - Part 1 Safety of machinery - Basic concepts - Part 1 Safety of machinery - Basic concepts - Part 2 Safety of machinery - Risk assessment - Part 1 Other technical standards and specifications used: The person authorised to compile the relevant technical documentation: BlitzRotary GmbH; Hüfinger Str. 55, 78199 Bräunlingen 7348850000 – 10/2014
advertisement
Related manuals
advertisement
Languages
Only pages of the document in English were displayed