advertisement
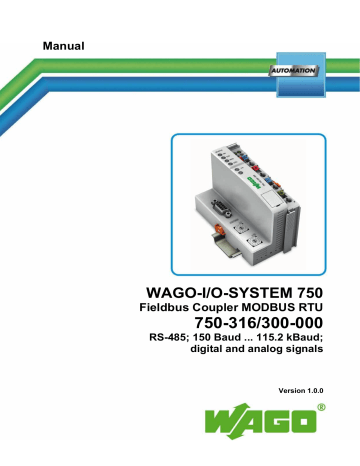
WAGO-I/O-SYSTEM 750
750-316/300-000 Fieldbus Coupler MODBUS RTU
3.5.3 Field Supply
System Description 23
3.5.3.1 Connection
Sensors and actuators can be directly connected to the relevant channel of the I/O module in 1, 2, 3 or 4 conductor connection technology. The I/O module supplies power to the sensors and actuators. The input and output drivers of some I/O modules require the field side supply voltage.
The fieldbus coupler/controller provides field side power (DC 24 V). In this case it is a passive power supply without protection equipment.
Power supply modules with or without fuse holder and diagnostic capability are available for the power supply of other field potentials (DC 24 V, AC/DC 0 …
230 V, AC 120 V, AC 230 V). The power supply modules can also be used to set up various potential groups. The connections are connected in pairs to a power contact.
Figure 7: Field Supply for Standard Couplers/Controllers and Extended ECO Couplers
Table 5: Legend for Figure “Field Supply for Standard Couplers/Controllers and Extended ECO
Couplers”
Field supply
1 24 V (-15 % / +20 %)
2 0 V
3 Optional ground potential
Power jumper contacts
4 Potential distribution to adjacent I/O modules
Manual
Version 1.0.0
24 System Description WAGO-I/O-SYSTEM 750
750-316/300-000 Fieldbus Coupler MODBUS RTU
The field-side power supply is automatically derived from the power jumper contacts when snapping an I/O module.
The current load of the power contacts must not exceed 10 A on a continual basis.
By inserting an additional power supply module, the field supply via the power contacts is disrupted. From there a new power supply occurs which may also contain a new voltage potential.
Re-establish the ground connection when the connection to the power jumper contacts is disrupted!
Some I/O modules have no or very few power contacts (depending on the I/O function). Due to this, the passing through of the relevant potential is disrupted. If you require a field supply via power jumper contacts for subsequent I/O modules, then you have to use a power supply module.
Note the data sheets of the I/O modules.
Use a spacer module when setting up a node with different potentials!
In the case of a node setup with different potentials, e.g. the alteration from
DC 24 V to AC 230 V, you should use a spacer module. The optical separation of the potentials acts as a warning to heed caution in the case of wiring and maintenance works. Thus, you can prevent the results of wiring errors.
Manual
Version 1.0.0
advertisement
Related manuals
advertisement
Table of contents
- 6 Notes about this Documentation
- 6 Validity of this Documentation
- 6 Copyright
- 7 Symbols
- 9 Number Notation
- 9 Font Conventions
- 10 Important Notes
- 10 Legal Bases
- 10 Subject to Changes
- 10 Personnel Qualifications
- 10 Provisions
- 11 Technical Condition of Specified Devices
- 12 Safety Advice (Precautions)
- 14 System Description
- 15 Manufacturing Number
- 16 Component Update
- 16 Storage, Assembly and Transport
- 17 Assembly Guidelines/Standards
- 18 Power Supply
- 18 Isolation
- 19 System Supply
- 19 Connection
- 20 Dimensioning
- 23 Field Supply
- 23 Connection
- 25 Fusing
- 28 Supplementary Power Supply Regulations
- 29 Supply Example
- 31 Power Supply Unit
- 32 Grounding
- 32 Grounding the DIN Rail
- 32 Framework Assembly
- 32 Insulated Assembly
- 33 Grounding Function
- 34 Shielding
- 34 General
- 34 Bus Cables
- 35 Signal Lines
- 35 WAGO Shield Connecting System
- 36 Device Description
- 39 Connectors
- 39 Device Supply
- 40 Fieldbus Connection
- 41 Display Elements
- 42 Operating Elements
- 42 Service Interface
- 43 Mode Selector Switch
- 49 Manual Configuration
- 52 Technical Data
- 52 Device Data
- 52 System Data
- 52 Connection Type
- 53 Climatic Environmental Conditions
- 53 Mechanical Strength acc. to IEC
- 54 Approvals
- 56 Standards and Guidelines
- 57 Mounting
- 57 Installation Position
- 57 Overall Configuration
- 59 Mounting onto Carrier Rail
- 59 Carrier Rail Properties
- 60 WAGO DIN Rail
- 60 Spacing
- 61 Mounting Sequence
- 62 Inserting and Removing Devices
- 63 Inserting the Fieldbus Coupler/Controller
- 63 Removing the Fieldbus Coupler/Controller
- 64 Inserting the I/O Module
- 65 Removing the I/O Module
- 66 Connect Devices
- 66 Data Contacts/Internal Bus
- 67 Power Contacts/Field Supply
- 69 Function Description
- 69 Startup of the Fieldbus Coupler
- 71 Process Data Architecture
- 71 Basic Setup
- 72 Example of an Input Process Image
- 73 Example of an Output Process Image
- 74 Process Data MODBUS RTU
- 75 Data Exchange
- 75 Memory Space
- 76 Addressing
- 76 Adressing the I/O Modules
- 79 Commissioning
- 80 Diagnostics
- 80 LED Signaling
- 81 Evaluating Fieldbus Status
- 82 Evaluating Node Status – I/O LED (Blink Code Table)
- 163 Figure 1: Fieldbus Node (Example)
- 164 Figure 2: Labeling on the Side of a Component (Example)
- 164 Figure 3: Example of a Manufacturing Number
- 167 Figure 4: Isolation for Fieldbus Couplers/Controllers (Example)
- 168 System Supply Module (right)
- 169 Couplers
- 174 Figure 8: Supply Module with Fuse Carrier (Example 750-610)