- Home
- Domestic appliances
- Climate control
- Split-system air conditioners
- Honeywell
- AUTOMATIC CONTROL SI Edition
- User manual
Year-Round System Control Processes. Honeywell AUTOMATIC CONTROL SI Edition
Add to My manuals512 Pages
Honeywell AUTOMATIC CONTROL SI Edition is the latest and greatest in automatic control for commercial buildings. It is packed with features that will help you to optimize your building's performance and save energy. With this device, you can:
advertisement
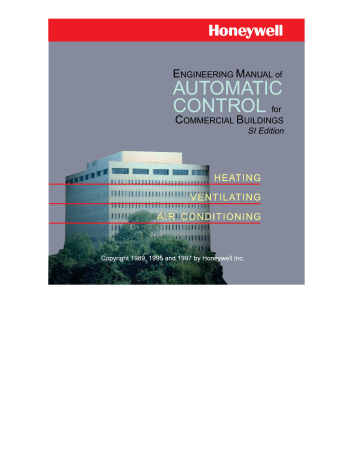
AIR HANDLING SYSTEM CONTROL APPLICATIONS
HEATING SYSTEM CONTROL PROCESS
SPACE CONTROL OF HEATING, ECONOMIZER (FREE COOLING), AND HUMIDIFICATION
Functional Description
SPACE
4
3
45
52
RA
CONTROL
PROGRAM
8
7
6
88
52
28
NC
5
SA
13
12
25
15
9
23.5
22
10
COOL
HEAT
Item
No.
1,2
OA
83
17
ECONOMIZER DECISION.
REFER TO PREVIOUS
ECONOMIZER OPTIONS
18
N.O.
N.C.
1
CONTROL
PROGRAM
20
13
ON
NORMAL
2
SUPPLY AIR
TEMPERATURE
SETPOINT
41
00
14
CONTROL
PROGRAM
13
19
22
SUPPLY AIR
TEMPERATURE
SETPOINT
13
OA MINIMUM SETPOINT
(NOTE: THE TEST AND BALANCE INITIAL
VALUE FOR PROPER VENTILATION IS 22)
27
SPACE
HEATING
DEMAND
100
0
11
SPACE
COOLING
DEMAND
100
0
16
M15175
3-5
6,7
8
9-11
12
Function
Control system energizes when fan is turned on (See FAN SYSTEM START-STOP
CONTROL).
Space humidity PI loop controls humidifier valve if space humidity falls to setpoint.
SA humidity high limit PI loop throttles humidifier valve if duct humidity rises above setpoint.
Control program coordinates space and humidifier leaving air humidity control and fan interlock.
Space temperature heating PI loop inputs to
SA temperature heating reset schedule.
SA temperature PI loop inputs to heating and mixed air control programs.
13
14
15,16
17
18
19
20
Hot water valve modulates to maintain SA temperature setpoint.
Control program coordinates space and SA heating control and fan interlock.
Space temperature cooling PI loop inputs to SA temperature cooling reset schedule.
Mixing dampers modulate to maintain SA temperature setpoint.
Economizer decision program determines when
OA is suitable to assist with cooling demand.
Mixing dampers minimum ventilation value.
Control program coordinates space and supply cooling control, ventilation control, and fan interlock.
246 ENGINEERING MANUAL OF AUTOMATIC CONTROL
AIR HANDLING SYSTEM CONTROL APPLICATIONS
FEATURES
1. The outdoor air quantity is modulated from a minimum to take advantage of free cooling based on space temperature demand.
2. The SA temperature will not fall below a set minimum.
3. Air is supplied at the temperature necessary to make up the sensible heat loss of the space.
4. Space relative humidity is maintained at a minimum value by a space humidity controller controlling the humidifier.
5. Separate setpoints for heating and cooling.
2. SA condition at design load is 32
°
C DB and 7.0 grams of moisture per kilogram of dry air.
3. Light load outdoor air condition is 13
°
C DB and 11.5
°
C
WB.
4. SA condition at light load is 24
°
C DB and 7.0 grams of moisture per kilogram of dry air.
5. Minimum outdoor air is 25 percent.
6. RA condition is 23.5
°
C DB and 35% RH.
Design Load
CONDITIONS FOR SUCCESSFUL OPERATION
See FAN SYSTEM START-STOP CONTROL.
1. An appropriate schedule of settings.
2. The low temperature limit controller located to respond to the lowest temperature in the duct.
OA
-18
°
C DB,
50% RH
1
MA 13
°
C DB,
7.5
°
C WB
RA 23.5
°
C DB,
35% RH
MIX
2 HEAT
HUMIDIFY
DESIGN LOAD
3
4
SA 32
°
C DB,
7.0g H
2
O/kg DRY AIR
32
°
C DB,
16
°
C WB
C3256
LIMITATIONS
This application used in applications that do not require mechanical cooling.
SPECIFICATIONS
Anytime the supply fan runs, control system shall be enabled.
Anytime the space relative humidity drops below the setpoint, the space humidity PI loop shall modulate the humidifier, subject to an SA humidity high limit override set at 88%.
As the space heating load varies from 0 to 100%, the SA heating PID loop setpoint shall be reset from 13
°
C to 41
°
C.
The hot water valve shall be modulated as required to maintain the SA temperature setpoint.
Anytime the fan runs, the mixing dampers shall position to a minimum ventilation setting.
As the space cooling load varies from 0 to 100%, the SA cooling
PI loop setpoint shall be reset from 27
°
C to 13
°
C. The outdoor and return (and relief if applicable) air dampers shall be modulated as required to maintain the SA temperature setpoint.
Cooling damper control shall be returned to minimum position anytime the economizer mode is disabled.
Separate space heating and cooling setpoints shall be provided.
PSYCHROMETRIC ASPECTS
In the following charts it is assumed that:
1. Design outdoor air condition is –18
°
C DB and 50 percent relative humidity.
The following results are obtained:
Item
No.
Explanation
1
2
3
4
Design outdoor air condition is –18
°
C DB and
50 percent relative humidity.
Mixed air condition is 12.5
°
C DB and
7.5
°
C WB.
Heated air condition is 32
°
C DB and 16
°
C WB.
SA condition is 32
°
C DB and 7.0 grams of moisture per kilogram of dry air.
Light Sensible Load
MA 15 ° C DB, 11.5
° C WB
6
SA 24 ° C DB, 15.5
° C WB
7.5g H
2
O/kg DRY AIR
RA 22 ° C DB, 13 ° C WB
OA
13
°
C DB,
11.5
° C WB
5
LIGHT SENSIBLE LOAD C3257
The following results are obtained:
Item
No.
Explanation
5
6
Mixed air condition is 15
°
C DB and 11.5
°
C WB.
SA condition is 24
°
C DB, and 7.5 grams of moisture per kilogram of dry air.
ENGINEERING MANUAL OF AUTOMATIC CONTROL
247
AIR HANDLING SYSTEM CONTROL APPLICATIONS
YEAR-ROUND SYSTEM CONTROL PROCESSES
HEATING, COOLING, AND ECONOMIZER
Functional Description
EA
100
5
OA
NC
NC
NO
3 ON
2
NORMAL
RA
SPACE TEMPERATURE
CHILLED WATER COOLING
SETPOINT = FREE COOLING
SETPOINT PLUS
10 1.1
(0.8 MINIMUM)
FREE COOLING
SETPOINT
HEATING SETPOINT = FREE
COOLING SETPOINT MINUS
12 1.1
(0.8 MINIMUM)
8
24.5
SETPOINT
24.5
11
9
23.5
SETPOINT
22
13
SUPPLY
FAN
1
SA
ON
15
15
14
SUPPLY AIR
TEMPERATURE
SETPOINT
SPACE
HEATING
DEMAND
41 100
13 0
18
21
100
PERCENT
OPEN
4
20
18
19 16
36 0
17
SUPPLY AIR
TEMPERATURE
SETPOINT
FREE
COOLING
DEMAND
24 0
14 100
22
ECONOMIZER DECISION.
REFER TO PREVIOUS
ECONOMIZER OPTIONS
7
6
22
CONTROL
PROGRAM
OA MINIMUM SETPOINT
(NOTE: THE TEST AND BALANCE
INITIAL VALUE FOR PROPER
VENTILATION IS 22)
18
SUPPLY AIR
TEMPERATURE
SETPOINT
CHW
COOLING
DEMAND
24 0
13 100
0
100
96
M15176
Item
No.
1-3
4-6
7
Function
Control system energizes when fan is turned on (See FAN SYSTEM START-STOP
CONTROL).
Mixing dampers modulate to maintain minimum ventilation value and free cooling
SA temperature setpoint.
Economizer enables free cooling when OA is appropriate.
8
9-13
14
Space temperature dictates heat and cool demands.
Free cooling setpoint and heat/cool deadband values determine the SA temperature setpoint for hot and chilled water control setpoints. Software has a minimum 0.8
kelvins heating and cooling deadband.
Heat demand varies SA temperature setpoint.
248 ENGINEERING MANUAL OF AUTOMATIC CONTROL
AIR HANDLING SYSTEM CONTROL APPLICATIONS
15,16
17
18
19
20
21
22
FEATURES
Hot water valve modulates to maintain SA temperature setpoint.
Free cooling demand varies SA temperature setpoint.
Chilled water cooling demand varies SA temperature setpoint.
Chilled water valve modulates to maintain SA temperature cooling setpoint.
MA temperature sensor for operator information.
OA temperature sensor for operator information.
Control program coordinates space and supply cooling, heating, and ventilation control, and fan interlock.
1. Use of space control resetting SA temperature control adds stability. The MA sensor is required to prevent freeze-up if the free cooling setpoint is lowered in freezing weather.
2. SA temperature is maintained only as high or low as required to meet space requirements.
3. Free cooling cycle selection determined by the economizer control program to minimize load on mechanical cooling system.
4. Optimum comfort temperature provided during free cooling cycle with energy conserving deadbands for heating and cooling.
The space temperature shall have a free cooling PI loop setpoint selected to provide optimum occupant comfort temperature. The space temperature shall have a chilled water cooling PI loop setpoint adjustable to no lower than 0.8 kelvins (minimum) above the free cooling setpoint. The space temperature shall have a heating PI loop setpoint adjustable to no higher than 0.8 kelvins
(minimum) below the free cooling setpoint.
As the space heating load varies from 100 to 0%, an SA heating PI control loop setpoint shall vary from 41
°
C to 13
°
C.
The hot water valve shall modulate to maintain the heating SA temperature setpoint, except that anytime the space temperature is greater than one degree above the free cooling space temperature setpoint, the hot water valve control PI setpoint shall be 11
°
C.
As the space free cooling load varies from 0 to 100%, an SA free cooling PI control loop setpoint shall vary from 24
°
C to
14
°
C. The mixing dampers shall modulate to maintain the free cooling SA temperature setpoint.
As the space chilled water cooling load varies from 0 to 100%, an SA chilled water cooling PI control loop setpoint shall vary from 24
°
C to 13
°
C. The chilled water valve shall modulate to maintain this cooling SA temperature setpoint.
PSYCHROMETRIC ASPECTS
In the following chart it is assumed that:
1. OA condition is 18
°
C and 53% RH.
2. System is in the economizer mode.
CONDITIONS FOR SUCCESSFUL OPERATION
1. Sensor locations must be selected to measure representative air conditions.
2. SA temperature control loops should provide PI control to assure stability with minimum offset.
NOTE: In cold climates this unit would most often have the heating coil ahead of the cooling coil and the low temperature switch after the heating coil. Control would not change. In the configuration shown, it would be possible to add a dehumidification cycle with reheat (software) at a later time.
SPECIFICATIONS
See FAN SYSTEM START-STOP CONTROL.
Anytime the supply fan runs, control system shall be enabled, and mixing dampers shall position to minimum ventilation position during scheduled occupancy periods.
Anytime the economizer decision program determines that
OA is suitable to assist in cooling, the temperature controls shall be enabled to override the dampers minimum ventilation position for free cooling as required.
COOLING COIL
DISCHARGE 15
°
C
2
COIL
COOLING
LOAD
3
1
100% OA
18
°
C DB, 53% RH
SPACE
24.5
°
C DB, 38% RH
M15177
The following results are obtained:
Item
No.
Explanation
1
2
3
100% economizer air is entering the cooling coil.
The chilled water coil cools the entering air to its 15
°
C setpoint (removing little moisture because the water flow is low and the OA moisture content is not high).
Space temperature is 24.5
°
C and 38% RH.
ENGINEERING MANUAL OF AUTOMATIC CONTROL
249
AIR HANDLING SYSTEM CONTROL APPLICATIONS
MULTIZONE UNIT
Functional Description
THE ZONE WITH THE GREATEST HEATING DEMAND
RESETS THE HOT DECK TEMPERATURE FROM
MAINTAIN ITS SPACE TEMPERATURE
THE ZONE WITH THE GREATEST COOLING DEMAND
RESETS THE COLD DECK TEMPERATURE FROM
MAINTAIN ITS SPACE TEMPERATURE
6
46
5
23.5
7
23.5
62
23.5
23.5
HALL
LOBBY
EAST
OFFICE
23.5
24.5
100
PERCENT
OPEN TO
COLD
DECK
SETPOINT
SPACE
TEMPERATURE
WEST
OFFICE
25
11
PERCENT
OPEN
22
OA
78
3
RA
00
10
2
NORMAL
ON
1
ECONOMIZER DECISION.
REFER TO PREVIOUS
ECONOMIZER OPTIONS
OA MINIMUM SETPOINT
(NOTE: THE TEST AND
BALANCE INITIAL
VALUE FOR PROPER
VENTILATION IS 22)
22
4
14
25 15
00
CONTROL
PROGRAM
16
12
Item
No.
1,2
3,4
5-8
9
Function
Control system energizes when fan is turned on (See FAN SYSTEM START-STOP
CONTROL).
Mixing dampers position to minimum position during occupied fan operation and modulate for cooling.
Zone mixing dampers modulate to maintain space temperature setpoint.
Zone with greatest cooling demand determines cold deck temperature setpoint, and zone with greatest heating demand determines hot deck temperature setpoint.
10,11
12,13
14
15
16
14
13
8
SA
M15178
Hot deck valve modulated to maintain hot deck temperature setpoint.
Cold deck valve modulated to maintain cold deck temperature setpoint.
Economizer enables free cooling when OA is suitable.
Fan leaving air temperature for operator information.
Control program coordinates cooling, heating, ventilation, and fan interlock control.
250 ENGINEERING MANUAL OF AUTOMATIC CONTROL
AIR HANDLING SYSTEM CONTROL APPLICATIONS
FEATURES
1. This application uses zone control of heating and cooling.
2. Deck temperatures dictated by zones with greatest heating and cooling demand and with a deadband.
CONDITIONS FOR SUCCESSFUL OPERATION
All zones should be connected to load analyzer program to satisfy total load requirements. However, in larger systems it may be good practice to connect only selected diverse zone loads. Zones that may be allowed to go out of control (storage rooms, etc.) should not be connected to the load analyzer program.
In the winter, zone space temperature is maintained by mixing air from the cold deck with hot deck air (the temperature of which is dictated by the zone with the greatest demand for heating). The zone with the greatest demand for heating gets
100% hot deck air. The zone with the greatest demand for cooling (assuming a zone space temperature rises two degrees above setpoint and demands cooling) gets 100% cold deck air and dictates the cold deck temperature maintained via the economizer cycle.
In the following chart it is assumed that:
1. Desired space condition is 24
°
C DB.
2. Outdoor air condition is 24
°
C DB and 80% RH.
3. The mixed air is 25 percent outdoor air during the cooling cycle.
4. Coil leaving air temperature is 13
°
C (at least one zone demands full cooling).
SPECIFICATIONS
See FAN SYSTEM START-STOP CONTROL.
Anytime the supply fan runs, control system shall be enabled, and mixing dampers shall position to minimum ventilation position during scheduled occupancy periods.
Each zone space temperature PID loop shall modulate its zone mixing dampers to maintain its space temperature setpoint.
The zone with the greatest temperature deviation below setpoint shall reset the hot deck temperature setpoint from 13
°
C to 36
°
C as required to maintain the zone space temperature 2 degrees below setpoint.
The zone with the greatest temperature deviation above setpoint shall reset the cold deck temperature setpoint from
25.5
°
C to 13
°
C as required to maintain the zone space temperature 1 degree above setpoint.
The hot deck PID loop shall modulate the hot deck hot water valve to maintain the hot deck temperature setpoint.
The cold deck PID loop shall modulate the OA/RA mixing dampers in sequence with the cold deck chilled water valve to maintain the cold deck temperature setpoint.
Anytime the economizer decision program determines that
OA is unsuitable to assist in cooling, the OA/RA mixing dampers shall be returned to their minimum ventilation position.
PSYCHROMETRIC ASPECTS
In the summer, zone space temperature is maintained by mixing air from the hot deck with cold deck air (the temperature of which is dictated by the zone with the greatest demand for cooling). The zone with the greatest demand for cooling gets
100% cold deck air.
4
COLD
DECK
13 ° C DB
1 OA 24
°
C DB, 80% RH
5
3
6
2
7
MA AND HOT DECK
RA 24 ° C DB, 60% RH
The following results are obtained:
Item
No.
1
2
3
4
5
6
7
Explanation
M15179
OA temperature at example time.
Mixed air is 25% OA and 75% RA. This is also the hot deck air, assuming no zone temperature has dropped two degrees and demanded heating.
This line represents the cooling process of the cold deck air. The zone demanding the most cooling dictates how far the process goes from
Point 2 to Point 4.
13
°
C DB is the minimum cold deck setpoint set up in the program, set by a zone requiring full cooling.
Discharge air to a zone requiring half cold deck air and half mixed air.
The space cooling process line.
Return air is 24
°
C DB and 60% RH (humidity rises because humidity is high outdoors and only partial supply airflow is dehumidified).
ENGINEERING MANUAL OF AUTOMATIC CONTROL
251
AIR HANDLING SYSTEM CONTROL APPLICATIONS
4-6
7
8
9
10,27
11-16
HEATING, COOLING, HUMIDIFICATION, AND DEHUMIDIFICATION CONTROL
WITHOUT DEAD-BANDS
Functional Description
9
EA
83
5
OA
7
N.C.
N.C.
N.O.
3
ON
2
NORMAL
83
9
PERCENT
OPEN
4
16
RA
0
10
18
15
100
13
27
11
20 52
52
24
SA
21 50
SPACE
11 23.5
88
1
ON
0
26
SUPPLY
FAN
13.5
25
16
12 23.5
13 35
REHEAT
SUPPLY AIR
TEMPERATURE
SETPOINT
COOLING
DEMAND
41
14
0
13 40
OA
CW
24
13
17
45
100
28
ECONOMIZER DECISION.
REFER TO PREVIOUS
ECONOMIZER OPTIONS
8
6
OA MINIMUM SETPOINT
(NOTE: THE TEST AND
BALANCE INITIAL
VALUE FOR PROPER
VENTILATION IS 22)
22
CONTROL
PROGRAM
COOL COIL
LEAVING AIR
TEMPERATURE
SETPOINT
13
19
HUMIDI-
FICATION
DEMAND
0
21 45
HUMIDIFIER
VALVE POSITION
0
23
100
55
100
22
50
M15180
Item
No.
1-3 17,18
Function
Control system energizes when fan is turned on (See FAN SYSTEM START-STOP
CONTROL).
Manual positioning value determines minimum ventilation mixing damper position.
Operator information, outdoor air temperature.
Economizer enables free cooling when OA is suitable.
Operator information, MA temperature.
Heating coil valve modulates to keep reheat coil entering air from getting too low.
Space temperature PI loop resets setpoint of reheat coil SA PI loop to maintain constant space temperature.
19
20-26
27
Chilled water valve modulates in sequence with mixing dampers as required to maintain
SA PI setpoint.
Chilled water coil leaving air temperature lowered if required for dehumidification.
Space humidity PI control loop modulates humidifier valve to maintain space relative humidity, subject to an SA high limit humidity PI loop.
Control program coordinates ventilation, heating, cooling, humidification, dehumidification, and fan interlocks.
252 ENGINEERING MANUAL OF AUTOMATIC CONTROL
AIR HANDLING SYSTEM CONTROL APPLICATIONS
FEATURES
1. The system admits outdoor air for cooling based upon the economizer decision.
2. Space relative humidity is maintained by controlling both humidification and dehumidification.
3. Reheat prevents subcooling on dehumidification cycle.
4. Constant temperature and humidity control. (Do not use this where deadband temperature or humidity control is acceptable.)
PSYCHROMETRIC ASPECTS
For cooling conditions it is assumed that:
1. Design outdoor air condition is 35
°
C DB and 26
°
C WB.
2. RA condition is 24.5
°
C DB and 18
°
C WB.
3. System operates on 25 percent minimum outdoor air.
4. Space temperature setpoint is set at 23.5.
5. Space humidity control is set at 50 percent.
6. Coil leaving air temperature is at 13
°
C.
CONDITIONS FOR SUCCESSFUL OPERATION
1. Heating is available during dehumidification cycle.
OA 35 ° C DB,
26
°
C WB
3
13
°
C DB
SPACE
23.5
°
C DB
2
1
MA
4
RA 24.5
° C DB,
17
°
C WB
1 KELVIN
SPECIFICATIONS
See FAN SYSTEM START-STOP CONTROL.
1. Anytime the supply fan runs, control system shall be enabled, and mixing dampers shall position to minimum ventilation position during scheduled occupancy periods.
2. Anytime the economizer decision program determines that OA is suitable to assist in cooling, the OA/RA mixing dampers shall be under control of the SA PI loop.
3. The space humidity PI loop shall modulate the humidifier, subject to a humidifier leaving air high limit humidity PI loop setpoint, to maintain the space humidity PI loop setpoint. Humidifying control shall be disabled anytime the chilled water valve is modulating or the fan is off.
4. The space humidity PI loop shall override the temperature controls to modulate the chilled water valve open for dehumidification if required to maintain the space humidity PI loop setpoint. The dehumidifying control loop shall be disabled anytime there is no hot water flow or temperature.
5. As the SA PI cooling demand varies from 100 to 45%, the cooling SA PI loop setpoint shall vary from 13
°
C to 24
°
C.
6. As the SA PI cooling demand varies from 40 to 0%, the reheat coil hot water valve SA PI loop setpoint (chilled water and economizer) shall vary from 11
°
C to 41
°
C.
7. The heating coil hot water valve shall modulate to prevent the cooling coil leaving air temperature from dropping below 11
°
C.
The following results are obtained:
Item
No.
1
2
3
4
Explanation
COOLING C3263
Mixed air temperature at cooling design condition.
Air entering the coil is cooled along a line of constant moisture content until saturation is approached. Near saturation the moisture content is reduced as the air is cooled. This process involves both latent and sensible cooling.
Cooling coil leaving air temperature will be as low as required to satisfy either the space temperature controller or the space humidity controller whichever is calling for the greatest cooling. If dehumidification cools discharge temperature below setpoint, the heating coil provides reheat.
The space temperature is 23.5
°
C DB and the
RA temperature is 24.5
°
C DB. The 1 kelvin
DB rise is an example of sensible cooling load which may occur in ceiling, space, and RA ducts. The rise will be a function of system, building, and lighting arrangement.
ENGINEERING MANUAL OF AUTOMATIC CONTROL
253
AIR HANDLING SYSTEM CONTROL APPLICATIONS
For heating conditions it is assumed that:
1. Design outdoor air condition is –18
°
C DB and 30 percent relative humidity.
2. RA condition is 24.5
°
C DB and 13.5
°
C WB.
3. System operates on 25 percent minimum outdoor air.
4. Space temperature is set at 23.5
°
C.
5. Space humidification control is set at 50 percent.
The following results are obtained:
Item
No.
1
Explanation
2
3
4
Heating coil leaving air temperature will be as high as required to satisfy the space temperature controller.
Humidification will be provided to satisfy space humidification requirements.
The space heating and humidifying load varies with people and weather.
The 1 kelvin DB RA rise is discussed in the cooling example.
OA
-18
°
C DB
30% RH
4
1 KELVIN
SPACE
23.5
°
C DB
MA
RA 24
°
C DB, 17
°
C WB
3
2 HUMIDIFIER
DISCHARGE
1 HEATING COIL
DISCHARGE
HEATING C3264
254 ENGINEERING MANUAL OF AUTOMATIC CONTROL
AIR HANDLING SYSTEM CONTROL APPLICATIONS
VAV AHU, WATER-SIDE ECONOMIZER, OA AIRFLOW CONTROL
Functional Description
WARM-UP MODE INVOLVED AT OPTIMUM
START TIME IF PERIMETER SPACE
TEMPERATURE IS LESS THAN 21
WARM-UP ENDS WHEN RETURN
AIR REACHES 23.5
.
.
24
0.45
83
8
RA
14
21
ON
WARM-UP
MODE
OFF
PERIMETER
ZONE
23.5
12
SPACE
25
13
20
22
32 13
11
SUPPLY AIR
TEMPERATURE SETPOINT
17
NORMAL
2
ON
1
NORMAL
OA
CFM
9
2306
16.5
19
2300
10
16
00
18
76
4
63
PERCENT
LOAD 15
13.5
3
PROPELLER
EXHAUST
FAN
ON
SA TO VAV
BOXES
7
6
0.45
5
0.45
MAXIMUM
SETPOINT
CONTROL
PROGRAM
22
23
ANYTIME ALL VAV BOX DAMPERS ARE LESS THAN 90% OPEN, DECREMENT THE AHU
ANYTIME ANY VAV BOX DAMPER IS FULL OPEN, INCREMENT THE AHU DUCT STATIC
M15181
Item
No.
1-3
4-6
7-10
11-14
Function
Control system energizes when supply fan is turned on (See FAN SYSTEM START-STOP
CONTROL).
Supply fan loads to maintain duct static pressure.
During occupied periods, exhaust fan runs and
OA airflow is controlled.
When perimeter temperature is low at startup,
SA temperature setpoint is warm until RA temperature rises.
15-16
17-18
19-20
21
22
ENGINEERING MANUAL OF AUTOMATIC CONTROL
255
Heating valve maintains SA temperature setpoint during warmup.
Cooling valve maintains SA temperature setpoint during occupied periods.
OA and MA temperatures are operator information.
SA temperature setpoint switches from cooling to heating value during warm-up modes.
Control program coordinates temperature control, ventilation, and fan interlock.
AIR HANDLING SYSTEM CONTROL APPLICATIONS
23
24
Control program optimizes duct pressure setpoint.
OA shaft static pressure point shared from OA fan control system for this graphic (not a physical point as shown) and provided here for operator information.
NOTE: This system is often found on each floor of a building, and often includes an outdoor air fan (preferably with filtration to protect the AHU OA air flow elements) and shaft, and a water-side economizer. The waterside economizer provides chilled water year round (in cold weather the cooling tower provides chilled water via heat exchangers without the need for the chillers).
Dual equal sized chillers and boilers (non-redundant) are assumed.
FEATURES
1. Supplies constant temperature variable volume (energy conserving) air to VAV boxes.
2. Provides constant airflow of OA with varying supply airflow.
3. Provides 100% RA during warm-up periods
(preoccupancy purge may be required for IAQ).
4. Perimeter boxes provide space heat when required during occupied periods.
5. AHU provides heating during warm-up periods, and when
OA temperature effects cause low SA temperatures. If boxes have electric heat and the AHU hot water is from lower cost gas/oil-sourced heat, box heaters may be disabled during warm-up periods.
6. Duct static pressure setpoint is lowered anytime all VAV box dampers are less than 90% open (If this strategy is used, the duct static pressure pickup need not be at the end of the longest run, but may be at any location where the air is not too turbulent. The maximum setpoint is higher than if the pickup had been at the end of the run because of the pickup location).
7. Reduced fan airflow is provided during warmup, night purge, and cool-down periods to reduce fan energy, which varies with the cube of the fan airflow.
8. Reduced fan airflow and staged AHU startup during cooldown periods requires only one chiller and keeps the chiller pull-down ahead of the AHU cooling demands such that AHUs get cold (not cool) water for effective cooling and dehumidification, and allows the chiller to operate at an efficient loading (less than 100%).
CONDITIONS FOR SUCCESSFUL OPERATION
1. Airflow element and transducer must be kept clean and calibrated.
2. OA fan must provide adequate OA shaft pressure.
Alternatively, if there is no OA fan, the OA airflow setpoint may be maintained by modulating the RA damper which would have to be added.
3. A controller network and adequate software and programming provided to support communication between the box controllers and the fan controller to allow static pressure reset and to position the box dampers properly during night purge, warmup, and cool-down periods.
4. If any VAV box whose damper position is a program input can never satisfy its space cooling demand for any reason
(and its damper is always open), the duct static pressure reset program will not lower the duct static pressure setpoint.
The duct static pressure reset program works best when there are no more than thirty monitored VAV boxes per fan system (with great quantities of boxes, it is likely that at least one box damper will always be full open).
For example, if an interior zone is always under a full cooling load, static pressure reset will not occur unless that zone (and similar zones) is oversized. The oversized zone would then throttle back when the building is at full load when the duct static pressure is at design.
5. All AHUs must be near the same normal occupancy schedule or the cool-down start-up specification edited.
6. Boiler, chiller, pumping system, and OA fan controls carefully networked into the AHU control schemes to assure smooth and efficient building operations.
7. All specified values and setpoints are tuned to specific project requirements.
SPECIFICATIONS
NOTE: A set of 16 similar sized AHUs are assumed.
See FAN SYSTEM START-STOP CONTROL.
Anytime any AHU starts in the optimum start cool-down mode, three to four AHUs shall start and the remaining AHUs shall stage on at five minute intervals (unless they similarly start under their optimum start programs). Any time any AHU operates in the night purge, warmup, or cool-down modes of operation, all associated perimeter VAV boxes shall operate at
60% of their maximum airflow setpoint, and all associated interior VAV boxes shall operate at 25% of their maximum airflow setpoint, unless the OA temperature is less than –9.5
°
C in which case the perimeter VAV boxes shall operate at their maximum airflow setpoint.
256 ENGINEERING MANUAL OF AUTOMATIC CONTROL
AIR HANDLING SYSTEM CONTROL APPLICATIONS
During unoccupied periods, anytime the top floor west zone perimeter space temperature is greater than 25
°
C and the OA temperature is less than 22
°
C and the OA dew point is less than
16
°
C, the night purge program shall start. When the night purge program starts, AHUs 9 through 16 (provided their west zone space temperatures are greater than 23.5
°
C) shall start, and the
OA and exhaust fans shall start. When an AHU runs in the night purge mode, its OA damper shall position full open. When the OA fan runs in the night purge mode, its duct static pressure setpoint shall be reset to a value 50% above the normal maximum setpoint. AHU fans running in the night purge mode shall stop when their noted space temperature drops to 23.5
°
C.
Anytime the night purge program runs for one minute and any of AHUs 9 through 16 are off, AHU’s 8 through 1 shall start respectively on a one-for-one basis (provided their west zone space temperatures are greater than 23.5
°
C). Anytime all fans shut down in the night purge mode, the night purge program mode shall end.
Anytime the supply fan runs, the return fan shall start and the control system shall be enabled. Also, anytime the supply fan runs during scheduled occupancy periods the exhaust fan shall start.
At the scheduled occupancy time, each AHU OA damper control loop shall be enabled under EPID control with a start value of 50 and a ramp duration of 400 seconds. Each AHU
OA damper shall modulate to maintain its OA airflow setpoint.
The supply fan loading shall be under EPID control with a start value of 20% and ramp duration of 150 seconds. The supply fan shall load to maintain the duct static pressure setpoint.
The SA temperature shall be under EPID control with a start value of 50% (at which point the hot and chilled water valves are both closed) and a ramp duration of 120 seconds. The hot and chilled water valves shall be modulated in sequence to maintain the SA temperature setpoint.
Anytime the optimum start perimeter zone space temperature sensor is less than 21
°
C at start-up time, the SA temperature setpoint shall be 32
°
C until the RA temperature rises to
23
°
C, at which time the SA temperature setpoint shall be lowered to 13
°
C. The EPID shall be invoked at the switching of the setpoint to 13
°
C with a start value of 50 and a ramp duration of 180 seconds.
EXPLANATION:
With VAV fan systems, operation during unoccupied periods should be based on minimum energy cost (not minimum ontime). Ideally, for a dual chiller building, the VAV box airflow would be regulated to run one chiller at its most efficient operating point. At this point the AHU fan would draw a small portion of its full-load amperage, good dehumidification would occur, and pumping energy may be reduced. In the night purge mode of operation, the objective is to supply a maximum amount of OA to the AHUs, and to direct it to the warm areas of the building. Reducing the AHU airflow and increasing the OA airflow should result in the supply airflow being a significant proportion OA. If IAQ requirements dictate a prepurge cycle, this operational mode should suffice then also, but would be staged by time rather than temperature.
PSYCHROMETRIC ASPECTS
In the following chart it is assumed that:
1. Outdoor air condition is 35
°
C DB and 26
°
C WB.
2. RA condition is 25.5
°
C DB and 14.5
°
C WB.
3. Coil leaving air temperature 10
°
C.
4. 80% RA.
OA 35 ° C DB,
26
°
C WB
SPACE LOAD
3
COIL DISCHARGE
10
°
C DB, 8
°
C WB
2 COOL
1
15.8
°
C DB
4
RA 26
°
C DB,
14
°
C WB
C3266
The following results are obtained:
Item
No.
Explanation
1
2
3
4
RA mixes with 20 percent (minimum position) outdoor air to obtain mixed air condition.
Air entering the coil is cooled along a line of constant moisture content until saturation is approached. Near saturation the moisture content is reduced as the air is cooled. This process involves both latent and sensible cooling.
Mixed air is cooled and dehumidified by cooling coil to obtain cooling coil leaving air condition.
Reheat coils and/or space internal load heats air to 25.5
°
C DB and 14.5
°
C WB.
ENGINEERING MANUAL OF AUTOMATIC CONTROL
257
AIR HANDLING SYSTEM CONTROL APPLICATIONS
VAV AHU WITH RETURN FAN AND FLOW TRACKING CONTROL
Functional Description
EA
83
20
22
17
24.5
30
RA
4
ON 58
9
PERCENT
LOAD
4.530
10
EXHAUST
FAN
ON
5
EXHAUST
FAN "ON"
DIFFERENTIAL m
3
/s
1.274
13
ZERO
CALIBRATION
360
14
SPACE
PRESSURIZATION
DIFFERENTIAL m
3
/s
0.613
12
CONTROL
PROGRAM
31
18
14.5
83
21
NORMAL
2
ON
1
NORMAL
3
6.423
11 m 3 /s
SA
OA
16
9
00
6
63
PERCENT
LOAD
0.060
23
24
0.060
25
26
76
13
27
7
8
0.45
0.45
Item
No.
1-5
6-8
9-14
15
17
ECONOMIZER DECISION.
REFER TO PREVIOUS
ECONOMIZER OPTIONS
CONTROL
PROGRAM
32
ON
WARM-UP
MODE
OFF
29
32 13
28
19
SA
TEMPERATURE
SETPOINT
OA
TEMPERATURE
13 4
16.5
-21
22
15
OA MINIMUM SETPOINT
(NOTE: THE TEST AND BALANCE INITIAL
VALUE FOR PROPER VENTILATION IS 22)
M15182
Function
Control system energizes when supply fan is turned on (See FAN SYSTEM START-STOP
CONTROL).
Supply fan loads to maintain duct static pressure at the end of the longest run.
Return fan loads to track supply airflow minus exhaust airflow minus air for pressurization.
Manual positioning value determines minimum summer ventilation mixing damper position. This position is fixed for the OA and
16
17
18 relief air dampers; but is a minimum position for the return air damper, the value of which will be overriden to maintain a constant mixing box negative static pressure and thus a constant
OA airflow.
OA determines SA temperature setpoint.
Economizer enables free cooling when OA is suitable.
Mixed air temperature is for operator information.
258 ENGINEERING MANUAL OF AUTOMATIC CONTROL
advertisement
Key Features
- Control all aspects of your building's HVAC system from a single location
- Monitor and adjust temperature, humidity, and ventilation levels
- Create custom control programs to meet your specific needs
- Integrate with other building systems, such as lighting and security
- Access your system remotely via the internet
Related manuals
Frequently Answers and Questions
What are the benefits of using Honeywell AUTOMATIC CONTROL SI Edition?
How easy is it to use Honeywell AUTOMATIC CONTROL SI Edition?
How much does Honeywell AUTOMATIC CONTROL SI Edition cost?
advertisement
Table of contents
- 99 Series 40 Control Circuits
- 101 Series 80 Control Circuits
- 102 Series 60 Two-Position Control Circuits
- 105 Series 60 Floating Control Circuits
- 106 Series 90 Control Circuits
- 113 Motor Control Circuits
- 128 Introduction
- 128 Definitions
- 130 Typical System
- 130 Components
- 137 Electronic Controller Fundamentals
- 138 Typical System Application
- 139 Microprocessor-Based/DDC Fundamentals
- 141 Introduction
- 141 Definitions
- 142 Background
- 142 Advantages
- 143 Controller Configuration
- 144 Types of Controllers
- 145 Controller Software
- 150 Controller Programming
- 153 Typical Applications
- 159 Introduction
- 159 Definitions
- 161 Abbreviations
- 162 Indoor Air Quality Concerns
- 172 Indoor Air Quality Control Applications
- 178 Bibliography
- 180 Introduction
- 180 Definitions
- 181 Objectives
- 181 Design Considerations
- 183 Design Priniples
- 186 Control Applications
- 189 Acceptance Testing
- 189 Leakage Rated Dampers
- 190 Bibliography
- 191 Building Management System Fundamentals
- 192 Introduction
- 192 Definitions
- 193 Background
- 194 System Configurations
- 197 System Functions
- 204 Integration of Other Systems
- 209 Air Handling System Control Applications
- 211 Introduction
- 211 Abbreviations
- 212 Requirements for Effective Control
- 214 Applications-General
- 215 Valve and Damper Selection
- 216 Symbols
- 217 Ventilation Control Processes
- 219 Fixed Quantity of Outdoor Air Control
- 231 Heating Control Processes
- 236 Preheat Control Processes
- 243 Humidification Control Process
- 244 Cooling Control Processes
- 251 Dehumidification Control Processes
- 254 Heating System Control Process
- 256 Year-Round System Control Processes
- 269 ASHRAE Psychrometric Charts
- 271 Building Airflow System Control Applications
- 273 Introduction
- 273 Definitions
- 274 Airflow Control Fundamentals
- 288 Airflow Control Applications
- 298 References
- 299 Chiller, Boiler, and Distribution System Control Applications
- 303 Introduction
- 303 Abbreviations
- 303 Definitions
- 304 Symbols
- 305 Chiller System Control
- 335 Boiler System Control
- 343 Hot and Chilled Water Distribution Systems Control
- 382 High Temperature Water Heating System Control
- 388 District Heating Applications
- 403 Individual Room Control Applications
- 405 Introduction
- 416 Unitary Equipment Control
- 432 Hot Water Plant Considerations
- 437 Introduction
- 437 Definitions
- 441 Valve Selection
- 446 Valve Sizing
- 456 Introduction
- 456 Definitions
- 457 Damper Selection
- 466 Damper Sizing
- 471 Damper Pressure Drop
- 472 Damper Applications
- 475 Introduction
- 475 Conversion Formulas and Tables
- 482 Electrical Data
- 485 Properties of Saturated Steam Data
- 486 Airflow Data
- 488 Moisture Content of Air Data
- 494 Application
- 494 Equipment
- 494 Controllers
- 494 Actuators
- 495 Operation
- 495 General
- 495 Bridge Circuit Theory
- 495 Basic Bridge Circuit
- 495 Bridge Circuit in Balanced Condition
- 495 Bridge Circuit on Increase in Controlled Variable
- 496 Bridge Circuit on Decrease in Controlled Variable
- 496 Bridge Circuit with Limit Controls
- 497 Bridge Circuit with Low-Limit Control
- 497 Bridge Circuit with High-Limit Control
- 498 Control Combinations
- 498 Low-Limit Control
- 498 High-Limit Control
- 499 Two-Position Limit Control
- 499 Manual and Automatic Switching
- 499 Closing the Actuator with a Manual Switch
- 499 One Thermostat to Another
- 499 Reversing for Heating and Cooling Control
- 500 One Actuator to Another
- 500 Unison Control
- 500 Manual Minimum Positioning of Outdoor Air Damper
- 501 Step Controllers
- 501 Application
- 501 Equipment
- 501 Starters
- 501 Contactors and Relays
- 502 Operation
- 502 Momentary Start-Stop Circuit
- 502 Hand-Off-Auto Start-Stop Circuit
- 503 Momentary Fast-Slow-Off Start-Stop Circuit
- 504 Control Combinations