- Home
- Domestic appliances
- Climate control
- Split-system air conditioners
- Honeywell
- AUTOMATIC CONTROL SI Edition
- User manual
Airflow Control Applications. Honeywell AUTOMATIC CONTROL SI Edition
Add to My manuals512 Pages
Honeywell AUTOMATIC CONTROL SI Edition is the latest and greatest in automatic control for commercial buildings. It is packed with features that will help you to optimize your building's performance and save energy. With this device, you can:
advertisement
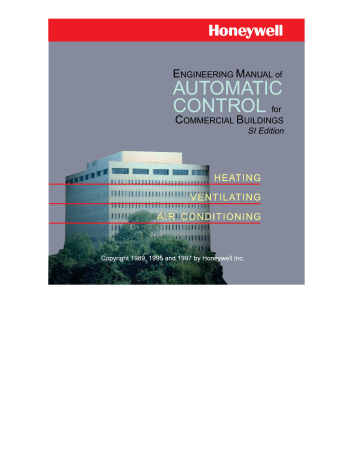
BUILDING AIRFLOW SYSTEM CONTROL APPLICATIONS leveled 10:1 inclined manometer calibrated against a hook gauge can read to approximately
±
1.25 Pa. A standard pitot tube with an inclined manometer can be used with the following degree of accuracy:
20
Table 2. Pitot Tube Accuracy.
Velocity (m/s) Percent Error (
±
)
1.04
15
10
4
3
1.60
2.94
6.6
18.6
It can be seen that the use of the pitot tube in practical applications is limited at velocities lower than 3 to 4 m/s."
An analysis of the accuracy of the pitot tube at 4 m/s follows:
Velocity Pressure:
VP = (4
÷
1.3) 2
= 9.467 Pa
Accuracy:
High
9.467 Pa
+1.250 Pa
10.717 Pa or 4.26 m/s
Low
9.467 Pa
–1.250 Pa
8.217 Pa or 3.73 m/s
Range
4.26 m/s
–3.73 m/s
0.53 m/s or 100.4
÷
2 =
±
0.265 m/s
Percent Error:
(
±
0.265
÷
4) x 100 =
±
6.6%
In practical situations, the velocity of the air stream is not uniform across the cross-section of a duct. Friction slows the air moving close to the walls so the velocity is greater away from the wall.
To determine the average velocity, a series of velocity pressure readings at points of equal area is found. It is recommended to use a formal pattern of sensing points across the duct cross-section.
These readings across the duct cross-section are known as traverse readings. Figure 17 shows recommended pitot tube locations for traversing round and rectangular ducts. In round ducts, velocity pressure readings at the centers of the areas of equal concentric areas are taken. Readings are taken along at least two diameters perpendicular to each other. In rectangular ducts, readings at the centers of equal rectangular areas are taken. The velocities are then mathematically totaled and averaged.
EQUAL
CONCENTRIC
AREAS
CENTERS
OF AREA OF
THE EQUAL
CONCENTRIC
AREAS
0.316 R
0.548 R
0.707 R
0.837 R
0.949 R
ROUND DUCT
CENTERS
OF AREAS
16-64 EQUAL
RECTANGULAR AREAS
RECTANGULAR DUCT
PITOT TUBE STATIONS INDICATED BY
Fig. 17. Pitot Tube Locations for Traversing
Round and Rectangular Ducts.
C2657
The principle behind the manual pitot tube transverse is simple and straightforward. However, care must be taken to obtain accurate readings without inadvertent violation of the formal traverse pattern. With the manual pitot tube traverse, individual velocity readings must be calculated mathematically, totaled, and divided by the number of readings to obtain average velocity.
TOTAL AND STATIC PRESSURE SENSORS
Other arrangements are available to instantaneously average sensed pressures and manifold these values to the exterior of the duct. The Tchebycheff (Tcheb) tube method (Fig. 18) is one such arrangement. This method separately manifolds the total and static pressure sensors. Inside each manifold is a tube with a single slot which receives an average pressure signal from the manifold. The averaged signals from the total and static pressure tubes may be used for indication and control functions. This method assures an accurate reading of flow conditions and a steady signal.
AIRFLOW
C2658
Fig. 18. Tcheb Tube Sensors and Manifold.
278 ENGINEERING MANUAL OF AUTOMATIC CONTROL
BUILDING AIRFLOW SYSTEM CONTROL APPLICATIONS
AIRFLOW MEASURING DEVICES
Various devices for measuring airflow are available. Figure 19 shows a flow measuring station that consists of:
— An air straightener section to eliminate swirl type airflow and help normalize the velocity profile
— Total pressure sensors aligned into the air stream and spaced on an equal area basis
— Static pressure sensors with ports perpendicular to the airflow direction and positioned on an equal area basis
— Separate manifolds for static and total pressure averaging
The flow measuring station in Figure 19 uses a tube as an air straightener (Fig. 20) with total and static pressure sensors at the downstream end. These tubes are arranged on an equal area basis.
AIR
STRAIGHTENER
TOTAL PRESSURE
CONNECTION
Electronic flow stations use the tube type construction with thermal velocity sensors instead of static and total pressure sensors. Other flow sensing arrangements use holes in round tubing (Fig. 21A and 21B) or airfoil designs (Fig. 21C). It is important to consult the manufacturer of each type of flow station for specifications, calibration data, and application information (location limitations within ducts).
AIRFLOW 39.25
˚ 39.25
˚
TOTAL
PRESSURE
TUBE
STATIC
PRESSURE
TUBE
TOTAL
PRESSURE
TUBE
STATIC
PRESSURE
TUBE
(SEE NOTE)
B.
A.
NOTE: STATIC PRESSURE SIGNAL WILL BE LESS THAN ACTUAL
STATIC PRESSURE AND CANNOT BE USED FOR STATIC
PRESSURE CONTROL. AS DEPRESSION VARIES WITH
AIR VELOCITY, VELOCITY PRESSURE (VP=TP - SP) WILL
BE AMPLIFIED.
TOTAL PRESSURE
PORT
AIR PROFILE STATIC PRESSURE
PORTS
FLOW
TOTAL
PRESSURE
STATIC
PRESSURE
AIRFLOW
AIR PROFILE
C.
C2661
Fig. 21. Miscellaneous Flow Sensing Arrangements.
TOTAL
PRESSURE
SENSOR
STATIC
PRESSURE
SENSOR
MANIFOLD
ASSEMBLY
STATIC
PRESSURE
CONNECTION
C2659
Fig. 19. Averaging Flow Measuring Station.
Figure 22 illustrates illustrates an airflow pickup station typically used in the primary air inlet to a VAV air terminal unit. The pickup station consists of two tubes that measure differential pressure. This measurement can be used in an airflow calculation.
VAV BOX
INLET
SLEEVE
AIRFLOW
PICKUP
DAMPER
AXLE
M12214
Fig. 22. Airflow Pickup Station for VAV Box Applications.
C2660
Fig. 20. Air Straighteners/Sensors and Manifolds.
ENGINEERING MANUAL OF AUTOMATIC CONTROL 279
BUILDING AIRFLOW SYSTEM CONTROL APPLICATIONS
AIRFLOW CONTROL APPLICATIONS
CENTRAL FAN SYSTEM CONTROL
Figure 23 shows the net airflow balance for a building space and where the return air, outdoor air, and supply fan inlet meet.
Assume that the return air damper is open, the relief air damper is closed, and the outdoor air damper is open enough to allow minimum design outdoor air to pass. When the outdoor and relief dampers open further and the return damper closes further, outdoor air increases above minimum. These conditions are used for free cooling (economizer cycle control) and when minimum air must be greater than the difference between supply and return fan airflow rates.
EXFILTRATION (EX) OUTDOOR AIR
RELIEF (OR)
RETURN
AIR (RA)
RETURN
FAN
BUILDING
SPACE
EXHAUST
AIR (EA)
EXHAUST
FAN
SUPPLY
FAN
SUPPLY
AIR (SA)
SA = RA +EX +EA
OUTDOOR AIR
INTAKE (OA)
SA = OA + (RA - OR)
FOR MINIMUM OA,
OR = 0 AND SA = OA + RA
C2618
Fig. 23. Central Fan Control with Net Airflow Balance.
branch (Fig. 24C). Each sensed point should have its own setpoint in the control loop. This avoids the assumption that branches and multisensor locations have identical requirements. The sensed point having the lowest duct pressure relative to its own setpoint should control the supply fan.
When a long straight duct (10 diameters) is available, a single point static sensor or pitot tube can be used. When long duct sections are not available, use static or airflow measuring stations which are multipoint and have flow straighteners to provide the most accurate sensing. A reference pressure pickup should be located outside the duct (in or near the controlled space) and adjacent to the duct sensor to measure space static in areas served by the duct. The static pressure sensor should not be located at the control panel in the equipment room if duct static is measured elsewhere. Equipment room static pressure varies as outdoor winds change, outdoor air and relief damper positions change, or exhaust fan operation changes.
SUPPLY
FAN
AIR
TERMINAL UNITS
A.
DUCT STATIC
PRESSURE SENSOR
SUPPLY FAN CONTROL FOR VAV SYSTEMS
General
The supply fan control system provides adequate duct static pressure to all air terminal units. This duct static pressure at the air terminal unit is used to overcome pressure drops between the air terminal unit inlet and the controlled space. Inadequate static limits maximum airflow to less than required, while excessive duct static increases sound levels and wastes energy.
The location of the duct static pressure sensor is critical for proper control of the supply fan.
Ideally, if the supply duct is one simple run with short takeoffs to the air terminal units (Fig. 24A), the duct static pressure sensor is located at the air terminal unit furthest from the supply fan. However, capacity variations of the furthest air terminal unit may adversely influence the duct static pressure sensor.
Under these circumstances, the sensor will transmit more stable and uniform pressures if located upstream of the last three or four air terminal units.
Typically, the supply duct is complex with multiple runs or branches. This duct layout requires a compromise in duct static pressure sensor location that is usually about 75 percent of the distance between the fan and the furthest air terminal unit
(Fig. 24B). In complex duct runs where multiple branches split close to the fan, sensors should be located in each end of the
SUPPLY
FAN
SUPPLY
FAN
AIR TERMINAL
UNITS
DUCT STATIC
PRESSURE SENSOR
B.
DUCT STATIC
PRESSURE SENSOR
AIR TERMINAL
UNITS
DUCT STATIC
PRESSURE SENSOR
C2619
C.
Fig. 24. Locating Duct Static Pressure
Sensor for Supply Fan Control.
280 ENGINEERING MANUAL OF AUTOMATIC CONTROL
BUILDING AIRFLOW SYSTEM CONTROL APPLICATIONS
A wide proportional band setting (10 times the maximum duct static pressure at the fan discharge) on the fan control is a good starting point and ensures stable fan operation. Integral action is necessary to eliminate offset error caused by the wide proportional band. Integral times should be short for quick response. The use of inverse derivative, which essentially slows system response, does not produce the combination of stability and fast response attainable with wide proportional band and integral control modes. (See the Control Fundamentals section for more information on proportional band and integral action.)
Inlet vane dampers, variable pitch blades (vane axial fans), or variable speed drives are used to modulate airflow (both supply and return). Actuators may require positive positioning to deal with nonlinear forces. Variable speed drives, especially variable frequency, provide excellent fan modulation and control as well as maximum efficiency.
A controlling high-limit application is used when the fan system must continue to run if duct blockage occurs, but its operation is limited to a maximum duct static. For example, a fire or smoke damper in the supply duct closes causing the primary duct static pressure sensor to detect no pressure. This would result in maximum output of the supply fan and dangerously high static pressure if the controlling high pressure limit is not present. A controlling high-limit control will modulate the fan to limit its output to the preset maximum duct static (Fig. 26).
DUCT
STATIC
HIGH-LIMIT
SENSOR
SMOKE DAMPERS
DUCT STATIC
PRESSURE SENSORS
Duct Static High-Limit Control
High-limit control of the supply fan duct static should be used to prevent damage to ducts, dampers, and air terminal units (Fig. 25). Damage can occur when fire or smoke dampers in the supply duct close or ducts are blocked, especially during initial system start-up. Fan shut-down and controlling highlimit are two techniques used to limit duct static. Both techniques sense duct static at the supply fan discharge.
SUPPLY
FAN
SMOKE DAMPERS
DUCT STATIC
PRESSURE SENSORS
AIR TERMINAL UNITS
C2621
Fig. 26. Controlling Static High-Limit.
SUPPLY
FAN
DUCT STATIC
HIGH-LIMIT SENSOR
AIR TERMINAL
UNITS
Fig. 25. Duct Static High-Limit Control.
C2620
Fan shut-down simply shuts down the fan system (supply and return fans) when its setpoint is exceeded. High-limit control requires a manual restart of the fans and should be a discrete component separate from the supply fan primary control loop.
The fan shut-down technique is lowest in cost but should not be used with smoke control systems where continued fan operation is required.
RETURN FAN CONTROL FOR VAV SYSTEMS
Return fan operation influences building (space) pressurization and minimum outdoor air. There are four techniques to control the return fan: open loop, direct building static, airflow tracking, and duct static.
Open Loop Control
Open loop control (Fig. 27) modulates the return fan without any feedback. This type of control presumes a fixed relationship between the supply and return fans, controls the return fan in tandem with the supply fan, and changes the output of the return fan without measuring the result. Open loop control requires similar supply and return fan operating characteristics.
Therefore, a careful analysis of the supply and return fan operating curves should be done before selecting this technique.
Also, accurate balancing is essential to ensure proper adjustment at maximum and minimum operating points.
Mechanical linkage adjustments or other means are used to adjust the differential between the two fans for desired flows and to minimize tracking errors at other operating points. With digital control, software can be used to align the fan loading relationships, to vary exhaust effects, and to offset dirty filter effects to minimize flow mismatches.
ENGINEERING MANUAL OF AUTOMATIC CONTROL 281
BUILDING AIRFLOW SYSTEM CONTROL APPLICATIONS
RETURN
FAN
AIR TERMINAL
UNITS
DUCT STATIC
PRESSURE SENSOR
Since building static is controlled directly, the pressure remains constant even when exhaust fan airflow changes. Minimum outdoor airflow varies with changes in exhaust fan airflow and building infiltration/exfiltration. In a control sequence where the outdoor air damper is closed, the building static must be reset to zero and all exhaust fans should be turned off.
SUPPLY
FAN
CONTROLLER
STATIC PRESSURE
REFERENCE C2622
Fig. 27. Open Loop Control.
Open loop control is often acceptable on small systems more tolerant of minimum outdoor air and building pressurization variations. Since open loop control does not sense or control return airflow, changes caused by the return side dampering and exhaust fan exfiltration change the minimum airflow and building pressurization. Systems with low airflow turndowns also are more suitable for open loop control. As a rule, turndowns should not exceed 50 percent.
In a control sequence where the outdoor air damper is closed
(e.g., night cycle or morning warm-up), open loop control should not be used. Excessive negative pressurization will occur in the duct between the return and supply fans.
Airflow Tracking Control
In airflow tracking (Fig. 29) control, the return fan airflow is reset based on the relationship between supply and exhaust fan airflows. That relationship is usually a fixed difference between the supply total airflow and return plus exhaust total airflow, but it can also be a percentage of supply total airflow. When duct layout prevents measuring of total airflow from one flow station, measurements in multiple ducts are totaled. This technique is usually higher cost, especially when multiple flow stations are required. Airflow tracking control and direct building static control are preferable to open loop control. Proportional plus integral control is necessary for accurate operation.
RETURN
FAN
FLOW
MEASURING
STATIONS
CONTROLLER
Direct Building Static Control
In direct building static control, the return fan responds directly to the building space static pressure referenced to the static pressure outside of the building (Fig. 28). The location of the building space static pressure sensor should be away from doors opening to the outside, elevator lobbies, and some confined areas. Usually a hallway on an upper floor is suitable. The outdoor static pressure sensor must avoid wind effects and be at least 5 meters above the building to avoid static pressure effects caused by wind. Due to stack effect, this technique should not be used in tall buildings with open spaces or atriums, unless the building has been partitioned vertically. This technique should use proportional plus integral control with a wide throttling range for stable, accurate, and responsive operation.
RETURN
FAN
SUPPLY
FAN C2624
Fig. 29. Airflow Tracking Control for Return Fan.
Minimum outdoor airflow should be maintained at a constant level, independent of exhaust fan airflow and changes in building infiltration/exfiltration. Building space pressurization varies only when building infiltration/exfiltration changes.
Exhaust fan airflow must reset the return fan airflow for building pressurization to be independent of exhaust fans. In a control sequence where the outdoor air damper is closed, the differential between supply airflow and return airflow must be reset to zero and all exhaust fans should be turned off.
Refer to the Air Handling System Control Applications section for an example of a VAV AHU WITH RETURN FAN
AND FLOW TRACKING CONTROL.
CONTROLLER
BUILDING SPACE
STATIC PRESSURE
OUTDOOR STATIC
PRESSURE
C2623
Fig. 28. Direct Building Static Control.
282 ENGINEERING MANUAL OF AUTOMATIC CONTROL
BUILDING AIRFLOW SYSTEM CONTROL APPLICATIONS
Duct Static Control
Duct static control is similar to supply fan duct static highlimit control, except return duct static pressure is negative. If individual space returns are damper controlled, return fan control must use this technique (Fig. 30). Duct static control is relatively simple, but individual space return controls make the entire system complex.
DUCT STATIC
PRESSURE SENSOR
RETURN
FAN
RELIEF
FAN
STATIC PRESSURE
CONTROLLER
BUILDING SPACE
STATIC PRESSURE
OUTDOOR STATIC
PRESSURE
C2627
Fig. 32. Direct Building Static Control for Relief Fan.
RELIEF
FAN
RA
CONTROLLER
STATIC PRESSURE
REFERENCE
Fig. 30. Duct Static Control.
C2625
Minimum building outdoor air is the difference between supply total airflow and return total plus the exhaust fan total airflow. If controlling the space returns from airflow tracking
(using dampers), the exhaust fan volume must be included in the tracking control system for constant building and space pressurization. If controlling the space returns by space pressurization, building and space pressurization remain constant regardless of exhaust fan operation.
RELIEF FAN CONTROL FOR VAV SYSTEMS
Relief fans are exhaust fans for the central air handling system. They relieve excessive building pressurization and provide return air removal for economizer cycles.
In Figure 31, a relief damper is located after the relief fan and is controlled to open fully whenever the relief fan operates.
Direct building static pressure or airflow tracking controls the relief fan. In direct building static pressure control (Fig. 32), the same guidelines apply as for return fan control. During minimum ventilation cycles and when the outdoor air damper is closed, the relief fan should be turned off and the relief damper closed. In airflow tracking (Fig. 33), flow measuring stations should be located in relief and outdoor air ducts, not in supply and return ducts as with return fans.
RELIEF
FAN
RA
EXHAUST
FAN
RELIEF
DAMPER
SUPPLY
FAN
BUILDING
SPACE
OA
C2626
Fig. 31. Relief Damper Location.
FLOW
MEASURING
STATIONS
AIRFLOW
CONTROLLER
OA
C2628
Fig. 33. Airflow Tracking Control for Relief Fan.
RETURN DAMPER CONTROL FOR VAV SYSTEMS
In systems having a return fan, when the mixed air control cycle is not operating, the outdoor air (or maximum outdoor air) and relief dampers are closed and the return damper remains fully open. When the mixed air control cycle is operating, the return damper modulates closed and outdoor air (or maximum outdoor air) and relief dampers modulate open. The return damper should be sized for twice the pressure drop of the outdoor air (or maximum outdoor air) and relief dampers. This prevents the possibility of drawing outdoor air through the relief damper (Fig. 34).
RA RELIEF
DAMPER
RETURN
FAN
RETURN
AIR
DAMPER
OA
OUTDOOR
AIR
DAMPER
MIXED AIR
TEMPERATURE
CONTROLLER
SUPPLY
FAN
C2629
Fig. 34. Return Air Damper Mixed Air Control Cycle.
ENGINEERING MANUAL OF AUTOMATIC CONTROL 283
BUILDING AIRFLOW SYSTEM CONTROL APPLICATIONS
In systems not having a return air fan, the return damper controls minimum outdoor airflow or building pressurization.
Airflow tracking or direct building static pressure control can be used to control the return damper, depending on which parameter is most important. See Figure 35 for airflow tracking and Figure 36 for direct building static pressure control.
RETURN
AIR
DAMPER
OA
FLOW
MEASURING
STATION
SUPPLY
FAN
AIRFLOW
CONTROLLER
A. FLOW MEASURING STATION IN OUTDOOR AIR DUCT
RELIEF
FAN
RA
FLOW
MEASURING
STATION
AIRFLOW
CONTROLLERS
SELECTOR
SUPPLY
FAN
OA
FLOW
MEASURING
STATION
MIXED AIR
TEMPERATURE
CONTROLLER
C2632
Fig. 37. Mixed Air Control Cycle with Relief
Fan Control Using Airflow Tracking.
OA
FLOW
MEASURING
STATION
AIRFLOW
CONTROLLER
BUILDING
SPACE
STATIC
PRESSURE
OUTDOOR
STATIC
PRESSURE
RA
RELIEF
FAN
B. FLOW MEASURING STATIONS IN SUPPLY AND RETURN DUCTS
C2630
Fig. 35. Return Damper Control Using Airflow Tracking.
STATIC
PRESSURE
CONTROLLERS
SELECTOR
SUPPLY
FAN
OA SUPPLY
FAN
OA
STATIC PRESSURE
CONTROLLER
BUILDING SPACE
STATIC PRESSURE
OUTDOOR STATIC
PRESSURE
C2631
Fig. 36. Return Damper Control Using
Direct Building Static Pressure.
If a mixed air control cycle is required, a relief fan may be required. In airflow tracking (Fig. 37), the mixed air controller opens the outdoor air damper above minimum and the relief fan tracks the outdoor air. In direct building static pressure control (Fig. 38) the mixed air controller opens the outdoor air and relief dampers and closes the return damper, causing the relief fan to eliminate excessive pressure.
MIXED AIR
TEMPERATURE
CONTROLLER C2633
Fig. 38. Mixed Air Control Cycle with Relief Fan
Control Using Direct Building Static Pressure.
284 ENGINEERING MANUAL OF AUTOMATIC CONTROL
BUILDING AIRFLOW SYSTEM CONTROL APPLICATIONS
SEQUENCING FAN CONTROL
VAV systems with multiple fans can use fan sequencing. This allows the fans to operate with greater turndown. For example, if a single fan modulates from 100 percent to 50 percent of wide open capacity (50 percent turndown), then two fans with exactly half the capacity of the larger fan can run with 75 percent turndown. Also, sequencing is more efficient. Most of the year the system is not run at full capacity. Under light load conditions, some fans run while others are at standby. It should be taken into account that fan power varies with the cube of the fan airflow when determining fan staging strategies.
For single supply fan systems, fan output volume is controlled by duct static pressure. However, the decision to turn fans on or off is based on total supply airflow. For centrifugal fans, if
Supply Fan 1 in Figure 39 is operating near its maximum velocity capacity, Supply Fan 2 is energized. This opens Damper
2 and Fan 2 is slowly modulated upward. As the duct static is satisfied, Fan 1 will modulate downward until Fan 1 and Fan 2 are operating together, controlled by duct static pressure. If the outputs of Fans 1 and 2 approach maximum capability, Supply
Fan 3 is energized. When zone load decreases and terminal units decrease airflow, duct static increases, modulating fans downward. When total supply flow decreases enough, Fan 3 is turned off and Fans 1 and 2 increase in output as required to maintain duct static. Similarly, Fan 2 may be turned off. Time delays protect fan motors from short cycling and fan operation may be alternated to spread wear.
RETURN
FAN
Vaneaxial fan sequencing is also decided by total supply flow, but the operating fan(s) is modulated to minimum output when the next fan is turned on. This sequence is used to avoid a stall of the starting fan. When all requested fans are running, they are modulated upward to satisfy duct static setpoint.
OTHER CONTROL MODES
Warm-Up Control
If warm-up control is used, it is not necessary to provide outdoor air. The following control actions should be accomplished when using warm-up control:
— Exhaust and relief fans should be off.
— Building pressurization control (if used) should be reset to zero static differential.
— Airflow tracking control (if used) should be reset to zero differential.
— If a return fan is used, the supply fan maximum airflow is limited to no greater than the return fan capacity.
With digital control VAV systems, this is accomplished by commanding the VAV boxes to some percent of their maximum airflow setpoints during this mode.
— Space thermostats should change the warm-up mode to normal operation to prevent over or under heating.
Smoke Control
If smoke control is used, the return damper closes and the return fan operates as a relief or exhaust fan. Controls must prevent over pressurization of ducts and spaces.
SUPPLY
FAN 1 DAMPER 1
SUPPLY
FAN 2
SUPPLY
FAN 3
DAMPER 2
DAMPER 3
FLOW
MEASURING
STATION
Night Purge Control
Night purge can be used to cool a building in preparation for occupancy and to cleanse the building of odors, smoke, or other contaminants. Outdoor and relief air dampers must be open and the return damper closed. If airflow tracking is used, supply fan must be limited to the return fan volume. Some control systems allow space thermostats to be set at lower setpoints during this cycle to maximize free cooling. If digital control is used, significant energy savings can be accomplished by commanding all VAV box airflow setpoints to approximately
50 percent of their maximum values.
CONTROL
PANEL
Fig. 39. VAV System with Fan Sequencing.
C2634
ZONE AIRFLOW CONTROL
AIRFLOW TRACKING/SPACE STATIC PRESSURE
Zone airflow control provides pressurization control for a portion of a facility. Figure 40 shows a zone airflow control example for a building. Airflow tracking or direct space static pressure control of the return damper on each floor determines the pressurization of each floor.
ENGINEERING MANUAL OF AUTOMATIC CONTROL 285
BUILDING AIRFLOW SYSTEM CONTROL APPLICATIONS
SUPPLY
FAN
OUTDOOR
STATIC
PRESSURE
SENSOR
INDOOR
STATIC
PRESSURE
SENSORS
(2)
RETURN
FAN
CONTROLLERS
(3)
AIRFLOW
SENSOR (2)
RETURN
FAN
CONTROLLER
DUCT
STATIC
REFERENCE
STATIC
C2664
Fig. 40. Control of Return Dampers in
Zone Airflow Control.
Airflow tracking is preferred for zone control on the first floor. Direct space static pressure control is difficult to stabilize because of sudden static pressure changes that occur whenever doors open. Also, the leakage around doors would require pressure control at very low setpoints, which are difficult to measure. On upper floors where building permeability is tight, airflow tracking control is not as viable. Direct space static pressure control is preferred for zone control on these floors.
Relatively small differences in airflow tracking differentials of tightly sealed zones result in large pressure differentials. Also, all exhaust airflows must be included when dealing with airflow tracking, which makes the control more complex.
Both airflow tracking and direct space static pressure control require accurate sensing. In airflow tracking, the airflow sensors are located in supply and return ducts to sense total airflow.
Minimum velocities and location of the airflow sensor relative to any variations from a straight duct are critical considerations.
In direct space static pressure control, the indoor static pressure sensor should be in the largest open area and away from doors that open to stairways and elevators. The outdoor static pressure sensor should be at least 5 meters above the building (depending on surrounding conditions) and be specifically designed to accommodate multidirectional winds.
For zone control using airflow tracking or direct space static pressure, return fan control should hold duct pressure constant at a point about two-thirds of the duct length upstream of the return fan (Fig. 41). This control is the same as that used to control the supply fan, except that the duct pressure is negative relative to the ambient surrounding the duct.
C2665
Fig. 41. Control of Return Fan in Zone Airflow Control.
To ensure minimum outdoor airflow, an airflow sensor enables control and provides information on the quantity of outdoor air. The airflow sensor is located in the duct having minimum outdoor airflow (Fig. 42). The control modulates the outdoor air, return air, and exhaust air dampers to provide outdoor air as needed. Normally, the difference between total supply and return airflows, as determined by zone controls, provides the minimum outdoor air. Since each zone is set to provide proper pressurization and buildings which are sealed tightly require less outdoor air for pressurization, this control scheme ensures minimum outdoor air. If minimum outdoor air is increased, it does not affect building pressurization.
AIRFLOW SENSOR
CONTROLLER
SUPPLY
FAN
RETURN
FAN
C2666
Fig. 42. Minimum Outdoor Air in Zone Airflow Control.
286 ENGINEERING MANUAL OF AUTOMATIC CONTROL
BUILDING AIRFLOW SYSTEM CONTROL APPLICATIONS
Essentially, the increase of outdoor air above that required to maintain building pressurization is done the same way as mixed air control except outdoor air is controlled by flow rather than mixed air temperature (Fig. 42). In colder climates, overrides must be included to avoid freezing coils.
MULTIPLE FAN SYSTEMS
EXHAUST SYSTEM CONTROL
FUME HOODS
Fume hoods are the primary containment devices in most chemical-based research venues. The lab envelope itself becomes the secondary containment barrier. In all cases, the basic use of the fume hood is for the safety of the worker/ researcher. Because no air is recirculated to the lab, the fume hood is also the primary user of energy in most labs. The continuing control challenge is to provide the safest possible environment while minimizing operating costs.
Multiple fan systems are a form of zone airflow control systems. The same concepts for zone pressurization using airflow tracking or direct space static pressure control apply to multiple fan systems. A return fan is modulated instead of the zone return damper to control zone pressurization.
There are three types of general purpose fume hoods (Fig. 43): bypass, auxiliary, and standard. Bypass and auxiliary air hoods approximate a constant exhaust airflow rate as the fume hood sash opens and closes. Operation of the standard hood causes the face velocity to increase or decrease with the up and down movement of the sash as a fixed volume of air is exhausted
(constant volume).
TYPES
Local exhausts are individual exhaust fan systems used in toilets, kitchens, and other spaces for spot removal of air contaminants.
These fans are generally off/on types. They should be controlled or at least monitored from a central location as the exhaust airflow can significantly affect energy efficiency.
The bypass hood limits face velocity to about twice the full sash open face velocity which may be acceptable. However, conditioned air is always exhausted making energy savings improbable.
General exhausts route contaminants into common ducts which connect to a common exhaust fan. If the airflow is manually balanced, the exhaust fan runs at a fixed level. However, if the airflow is controlled at each entry to vary the airflow in response to the local need, duct pressurization control of the exhaust fan is required. It may also be necessary to introduce outdoor air prior to the general exhaust fan in order to maintain a minimum discharge velocity.
STANDARD BYPASS
The auxiliary air hood is a bypass type with a supply air diffuser located in front of and above the sash. If the make-up air through the diffuser is not conditioned as well as room air, some minimal energy savings result by employing this type of equipment. However, the performance of this hood is controversial regarding containment of materials in the hood, operator discomfort, and thermal loading of the laboratory. Its use is usually discouraged.
AUXILIARY AIR
SASH OPEN SASH OPEN SASH OPEN
SASH CLOSED
SASH CLOSED
Fig. 43. General Purpose Fume Hoods.
ENGINEERING MANUAL OF AUTOMATIC CONTROL 287
SASH CLOSED
C1484
advertisement
Key Features
- Control all aspects of your building's HVAC system from a single location
- Monitor and adjust temperature, humidity, and ventilation levels
- Create custom control programs to meet your specific needs
- Integrate with other building systems, such as lighting and security
- Access your system remotely via the internet
Related manuals
Frequently Answers and Questions
What are the benefits of using Honeywell AUTOMATIC CONTROL SI Edition?
How easy is it to use Honeywell AUTOMATIC CONTROL SI Edition?
How much does Honeywell AUTOMATIC CONTROL SI Edition cost?
advertisement
Table of contents
- 99 Series 40 Control Circuits
- 101 Series 80 Control Circuits
- 102 Series 60 Two-Position Control Circuits
- 105 Series 60 Floating Control Circuits
- 106 Series 90 Control Circuits
- 113 Motor Control Circuits
- 128 Introduction
- 128 Definitions
- 130 Typical System
- 130 Components
- 137 Electronic Controller Fundamentals
- 138 Typical System Application
- 139 Microprocessor-Based/DDC Fundamentals
- 141 Introduction
- 141 Definitions
- 142 Background
- 142 Advantages
- 143 Controller Configuration
- 144 Types of Controllers
- 145 Controller Software
- 150 Controller Programming
- 153 Typical Applications
- 159 Introduction
- 159 Definitions
- 161 Abbreviations
- 162 Indoor Air Quality Concerns
- 172 Indoor Air Quality Control Applications
- 178 Bibliography
- 180 Introduction
- 180 Definitions
- 181 Objectives
- 181 Design Considerations
- 183 Design Priniples
- 186 Control Applications
- 189 Acceptance Testing
- 189 Leakage Rated Dampers
- 190 Bibliography
- 191 Building Management System Fundamentals
- 192 Introduction
- 192 Definitions
- 193 Background
- 194 System Configurations
- 197 System Functions
- 204 Integration of Other Systems
- 209 Air Handling System Control Applications
- 211 Introduction
- 211 Abbreviations
- 212 Requirements for Effective Control
- 214 Applications-General
- 215 Valve and Damper Selection
- 216 Symbols
- 217 Ventilation Control Processes
- 219 Fixed Quantity of Outdoor Air Control
- 231 Heating Control Processes
- 236 Preheat Control Processes
- 243 Humidification Control Process
- 244 Cooling Control Processes
- 251 Dehumidification Control Processes
- 254 Heating System Control Process
- 256 Year-Round System Control Processes
- 269 ASHRAE Psychrometric Charts
- 271 Building Airflow System Control Applications
- 273 Introduction
- 273 Definitions
- 274 Airflow Control Fundamentals
- 288 Airflow Control Applications
- 298 References
- 299 Chiller, Boiler, and Distribution System Control Applications
- 303 Introduction
- 303 Abbreviations
- 303 Definitions
- 304 Symbols
- 305 Chiller System Control
- 335 Boiler System Control
- 343 Hot and Chilled Water Distribution Systems Control
- 382 High Temperature Water Heating System Control
- 388 District Heating Applications
- 403 Individual Room Control Applications
- 405 Introduction
- 416 Unitary Equipment Control
- 432 Hot Water Plant Considerations
- 437 Introduction
- 437 Definitions
- 441 Valve Selection
- 446 Valve Sizing
- 456 Introduction
- 456 Definitions
- 457 Damper Selection
- 466 Damper Sizing
- 471 Damper Pressure Drop
- 472 Damper Applications
- 475 Introduction
- 475 Conversion Formulas and Tables
- 482 Electrical Data
- 485 Properties of Saturated Steam Data
- 486 Airflow Data
- 488 Moisture Content of Air Data
- 494 Application
- 494 Equipment
- 494 Controllers
- 494 Actuators
- 495 Operation
- 495 General
- 495 Bridge Circuit Theory
- 495 Basic Bridge Circuit
- 495 Bridge Circuit in Balanced Condition
- 495 Bridge Circuit on Increase in Controlled Variable
- 496 Bridge Circuit on Decrease in Controlled Variable
- 496 Bridge Circuit with Limit Controls
- 497 Bridge Circuit with Low-Limit Control
- 497 Bridge Circuit with High-Limit Control
- 498 Control Combinations
- 498 Low-Limit Control
- 498 High-Limit Control
- 499 Two-Position Limit Control
- 499 Manual and Automatic Switching
- 499 Closing the Actuator with a Manual Switch
- 499 One Thermostat to Another
- 499 Reversing for Heating and Cooling Control
- 500 One Actuator to Another
- 500 Unison Control
- 500 Manual Minimum Positioning of Outdoor Air Damper
- 501 Step Controllers
- 501 Application
- 501 Equipment
- 501 Starters
- 501 Contactors and Relays
- 502 Operation
- 502 Momentary Start-Stop Circuit
- 502 Hand-Off-Auto Start-Stop Circuit
- 503 Momentary Fast-Slow-Off Start-Stop Circuit
- 504 Control Combinations