Leadscrew error compensation. Fagor CNC 8055 para otras aplicaciones, CNC 8055 for lathes, CNC 8055 para fresadoras, CNC 8055 for milling machines, CNC 8055 para tornos, CNC 8055 for other applications
Add to My manuals706 Pages
advertisement
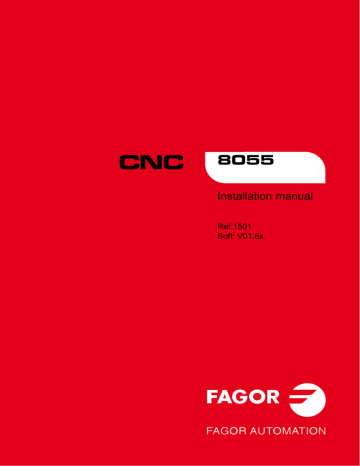
7.
Installation manual
7.5.7
Leadscrew error compensation
The CNC provides a table for each one of the axes requiring leadscrew compensation. It is possible to define different compensation values for each moving direction. This type of compensation is activated by setting a.m.p. LSCRWCOM (P15)=ON for the desired axis.
The CNC enables one leadscrew error compensation table for each axis. The number of elements of the table is determined by the a.m.p. NPOINTS (P16), being possible to define up to 1000 points per axis.
CNC 8055
CNC 8055i
S
OFT
: V01.6
X
Each parameter of the table represents a point of the profile to compensate. The following information is defined at each point:
• The position occupied by the point in the profile (position to compensate). It is defined by its coordinate referred to machine zero. Possible values ±99999.9999 mm or ±3937.00787 inches.
• The amount of error of the axis in this point in the positive direction. Possible values ±99999.9999
mm or ±3937.00787 inches.
• The amount of error of the axis in this point in the negative direction. Possible values
±99999.9999 mm or ±3937.00787 inches.
For each axis position, define the amount of error to be compensated in both directions. If the amount of error in the negative direction is zero in all points, it assumes that the amount of error defined for the positive direction is valid for both directions.
Leadscrew error compensation on rotary axes
On rotary axes, although the display is limited between 0 and 360º, the internal count is accumulative. When using leadscrew error compensation, set positions 0° and 360°, first and last point of the table, with the same amount of error. This way, the CNC will apply the same compensation in all the revolutions.
Otherwise, the compensation will be limited to the indicated field.
Considerations and limitations
When defining the profile points in the table, the following requirements must be met:
• The axis points must be in sequential order starting from the most negative (least positive) point to be compensated.
• For those points outside the compensation zone, the CNC will apply the compensation value corresponding to the table point closest to them.
• The amount of error of the machine reference point may have any value.
• The error difference between two consecutive points must not be greater than the distance between them (maximum slope= 100%).
Setting example
The X axis leadscrew must be compensated in the positive direction for between X-20 and X160 according to the leadscrew error graph below:
·322·
Installation manual
Set a.m.p. LSCRWCOM (P15) = ON and NPOINTS (P16) = 7
Considering that the Machine Reference Point (physical location of the marker pulse) is located 30 mm from HOME (machine reference zero), at X30. The leadscrew error compensation parameters must be set as follows:
Point
P001
P002
P003
P004
P005
P006
P007
Position
X
X
X
X
X
X
X
-20.000
0.000
30.000
60.000
90.000
130.000
160.000
Positive error
EX
EX
EX
EX
EX
EX
EX
0.001
-0.001
0.000
0.002
0.001
-0.002
-0.003
Negative error
EX
EX
EX
EX
EX
EX
EX
0
0
0
0
0
0
0
7.
CNC 8055
CNC 8055i
S
OFT
: V01.6
X
·323·
advertisement
Related manuals
advertisement
Table of contents
- 9 About the product
- 11 Declaration of conformity
- 13 Version history
- 15 Safety conditions
- 19 Warranty terms
- 21 Material returning terms
- 23 Additional remarks
- 25 Fagor documentation
- 27 CNC structure
- 29 Central unit
- 33 –CPU– Module
- 43 –Vpp Axes– module
- 50 –Vpp SB Axes– module
- 57 –I/O– module (inputs - outputs)
- 62 Monitors
- 63 11" LCD Monitor
- 65 11" LCD monitor + M, T, MC or TC keyboard
- 67 Operator panel
- 68 MC, TC, MCO/TCO and alphanumeric operator panels
- 69 Alphanumeric keyboard (optional)
- 73 CNC structure
- 77 Connectors
- 102 Operator panel
- 104 Alphanumeric keyboard (optional)
- 108 Heat dissipation by natural convection
- 109 Heat dissipation by forced convection with inside fan
- 110 Heat dissipation by air flow to the outside using a fan
- 113 Installation of the modules
- 114 Power supply
- 120 Digital inputs and digital outputs (single module)
- 122 Digital inputs and digital outputs (double module)
- 124 Electrical characteristics of the inputs and outputs
- 126 Numbering of the digital inputs and outputs
- 131 Digital inputs and outputs
- 132 Analog inputs and outputs
- 133 Setup
- 137 Connection of the emergency input and output
- 145 Parameter matching between the CNC and the Sercos drive
- 146 subroutine
- 148 General machine parameters
- 206 Axis parameters
- 239 Spindle parameters
- 240 Machine parameters for the main and 2nd spindles
- 259 Machine parameters for auxiliary spindle
- 261 Drive parameters
- 264 Friction compensation
- 265 Serial line parameters
- 268 Ethernet parameters
- 272 PLC Parameters
- 280 Tables
- 280 Miscellaneous (M) function table
- 282 Leadscrew error compensation table
- 284 Cross compensation parameter table
- 285 Axes and coordinate systems
- 288 Rotary axes
- 290 Gantry axes
- 291 Slaved axes and synchronized axes
- 292 Incline axis
- 294 Tandem axes
- 300 Relationship between the axes and the JOG keys
- 301 Path-jog mode
- 303 Movement with an electronic handwheel
- 304 Standard handwheel
- 305 Path handwheel
- 306 Feed handwheel mode
- 307 "Additive handwheel" mode
- 309 feedback system
- 310 Counting speed limitation
- 311 Resolution
- 315 Axis adjustment
- 316 Drive adjustment
- 317 Gain setting
- 318 Proportional gain setting
- 319 Feed-forward gain setting
- 320 Derivative (AC-forward) gain setting
- 321 Leadscrew backlash compensation
- 322 Leadscrew error compensation
- 324 Circle geometry test
- 326 Reference systems
- 327 Home search
- 331 Setting on systems without distance-coded feedback
- 333 Setting on systems with distance-coded feedback
- 334 Axis travel limits (software limits)
- 335 Unidirectional approach
- 336 Auxiliary M, S, T function transfer
- 338 Transferring M, S, T using the AUXEND signal
- 340 Main and second spindle
- 342 Spindle types
- 343 Spindle speed (S) control
- 345 Spindle gear change
- 347 Spindle in closed loop
- 353 Auxiliary spindle controlled by PLC
- 354 Treatment of emergency signals
- 357 Digital servo (CAN or Sercos)
- 358 Communications channel
- 361 Drive’s absolute feedback
- 362 Axes (2) controlled by a single drive
- 365 "C" axis and spindle with a single feedback
- 368 Additive coupling between axes
- 370 Fagor handwheels: HBA, HBE and LGB
- 374 Machine safety related functions
- 374 Maximum machining spindle speed
- 375 Cycle start disabled when hardware errors occur
- 376 Configuring a CNC as two and a half axes
- 377 Machine parameter setting
- 378 PLC program
- 380 Tool magazine
- 380 Tool change via PLC
- 381 Tool magazine management
- 382 Gear ratio management on axes and spindle
- 383 Axis example: Encoder at the motor
- 384 Axis example: external feedback device without a gear box
- 388 Axis example: external feedback device with gear box
- 391 Spindle example: Encoder at the motor
- 393 Spindle example: external encoder without gear box
- 396 Spindle example: external encoder with gear box
- 399 Feedback combination for SERCOS axes with external feedback to the CNC
- 400 Open communication
- 402 Reception setting
- 402 Incompatibility with WINDNC via RS
- 403 Trace of characters sent and received
- 404 Examples of open communication
- 408 Auto-adjustment of axis machine parameter DERGAIN
- 412 PLC resources
- 413 PLC program execution
- 416 Loop time
- 417 Modular structure of the program
- 417 First cycle module (CY1)
- 417 Main module (PRG)
- 418 Periodic execution module (PE t)
- 419 Priority of execution of the PLC modules
- 421 Inputs
- 422 Outputs
- 423 Marks
- 425 Registers
- 426 Timers
- 429 Monostable mode. TG1 input
- 431 Delayed activation mode. TG2 input
- 433 Delayed deactivation mode. TG3 input
- 435 Signal limiting mode. TG4 Input
- 437 Counters
- 440 Operating mode of a counter
- 442 Module structure
- 443 Directing instructions
- 446 Consulting instructions
- 448 Operators and symbols
- 449 Action instruction
- 450 Binary assignment instructions
- 451 Conditional binary action instructions
- 452 Sequence breaking action instructions
- 453 Arithmetic action instructions
- 455 Logic action instructions
- 457 Specific action instructions
- 460 Auxiliary M, S, T functions
- 463 Auxiliary M, S, T function transfer
- 464 Transferring M, S, T using the AUXEND signal
- 466 Displaying messages, errors and screens
- 468 Access to the PLC from the CNC
- 469 Access to the PLC from a PC, via DNC
- 472 General logic inputs
- 481 Axis logic inputs
- 486 Spindle logic inputs
- 491 Logic inputs of the auxiliary spindle
- 492 Key inhibiting logic inputs
- 493 Logic inputs of the PLC channel
- 495 General logic outputs
- 503 Logic outputs of the axes
- 505 Spindle logic outputs
- 507 Logic outputs of the auxiliary spindle
- 508 Logic outputs of key status
- 511 Variables associated with tools
- 515 Variables associated with zero offsets
- 516 Variables associated with function G
- 518 Variables associated with machine parameters
- 519 Variables associated with work zones
- 521 Variables associated with feedrates
- 524 Variables associated with coordinates
- 526 Variables associated with electronic handwheels
- 528 Variables associated with feedback
- 529 Variables associated with the main spindle
- 532 Variables associated with the second spindle
- 535 Variables associated with the live tool
- 536 Variables associated with local and global parameters
- 537 Sercos variables
- 538 Software & hardware configuration variables
- 541 Variables associated with telediagnosis
- 543 Operating-mode related variables
- 547 Other variables
- 558 PLC execution channel
- 559 Considerations
- 561 Blocks which can be executed from the PLC
- 565 Control of the PLC program from the CNC
- 567 Action CNCEX
- 568 Synchronize a PLC axis with a CNC axis
- 570 Configuration file
- 572 Configuration language
- 573 Key words
- 577 Arithmetic operations
- 579 Conditional instructions
- 580 Example of a configuration file
- 582 Error log file (P999500)
- 585 Axis control
- 586 Tool control
- 587 Spindle control
- 589 Screens, subroutines and cycles
- 590 Associated keys
- 592 OEM text in several languages
- 595 Associated programs
- 596 Associated subroutines
- 597 Configuration file
- 601 Error log file (P999500)
- 602 Cycle data entry
- 604 Example. Consult inputs and outputs
- 605 Example. Machining canned cycle
- 608 Definition of symbols (mnemonics)
- 610 First cycle module
- 611 Main module
- 619 Technical characteristics of the 8055iCNC
- 623 Central unit of the 8055 CNC
- 627 11" LCD Monitor
- 629 Probe connection at the 8055i
- 631 Probe connection at the 8055 CNC
- 633 Summary of internal CNC variables
- 641 Summary of PLC commands
- 645 Summary of PLC inputs and outputs
- 651 2-digit BCD code output conversion table
- 653 Key code
- 663 Logic outputs of key status
- 673 Key inhibiting codes
- 683 Machine parameter setting chart
- 695 M functions setting chart
- 697 Leadscrew error compensation table
- 699 Cross compensation table
- 701 Maintenance