advertisement
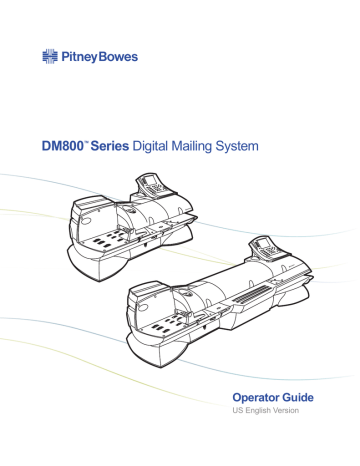
DM800™ Series Digital Mailing System Operating Guide
Printer
Maintenance
Printing a Test
Pattern
The printer components, consisting of the printer nozzle, ink cartridge and printhead, require minimum maintenance to ensure clean, clear meter imprints on your mail.
If the print quality deteriorates and you cannot improve it with the procedures in this chapter, contact the Pitney Bowes Help Desk. Refer to the
Pitney Bowes Contact Information List at the front of this guide for the phone number.
You can print a test pattern to check the quality of the meter imprint without spending any of your postage funds.
To print a test pattern:
1. From the IntelliLink® Control Center, press the Menu key.
2. Select Maintenance.
3. Select Print Test Pattern.
4. The “Print Test Pattern” screen appears and prompts you to “Press
Tape or print an envelope”.
5. Load an envelope on the feed deck and press Start, or press Tape to print on a tape.
6. Once the test pattern prints, the system asks you if the test pattern printed correctly.
If the test pattern looks like the sample shown here, press the Yes,
Lines are unbroken screen key. Go to step 10.
If the test pattern has missing or incomplete lines as shown here, press the No, clean the print nozzle screen key. Go to step 7.
SV61162 Rev. C
7. The “Cleaning Print Nozzle” screen displays until the cleaning operation completes.
9-9
9 • Maintaining and Updating
Printing a Test
Pattern
continued
8. Once the cleaning operation completes, the “Print Test Pattern” screen appears again.
9. Repeat steps 5 and 6 again. If the print pattern still has broken or missing lines, you may need to replace the ink cartridge (see Replacing the
Ink Cartridge) or printhead (see Changing the Printhead).
If the test pattern is ok, go to step 10.
10. Press the left arrow key to return to the postage screen.
Cleaning the
Printer Nozzle
You can clean the printer nozzle at any time by following these steps:
1. From the IntelliLink® Control Center, press the Menu key.
2. Select Maintenance.
3. Select Clean Printer Nozzle. The “Cleaning Print Nozzle” screen displays until the cleaning operation completes.
4. Once the cleaning operation completes, the “Print Test Pattern” screen appears.
5. Print a test pattern as described above in Printing a Test Pattern to verify that you can print a clean and clear meter stamp.
6. Repeat this operation at least one more time.
9-10 SV61162 Rev. C
DM800™ Series Digital Mailing System Operating Guide
Replacing the
Ink Cartridge
“Low Ink - Order Ink” appears on the IntelliLink® Control Center main screen when there is only enough ink for approximately 10 days of mailing.
You can choose to ignore this warning - refer to the Configuring Low Ink
Warning section in Chapter 5 in this guide.
Your actual ink usage will vary depending on whether you routinely print advertisements or inscriptions and how may pieces of mail you print per day.
“Low Ink” displays approximately two days before the ink runs out. You can print about another 300 meter stamps or leave the mailing system running for six days without printing. If you do not have a replacement cartridge, order one now. Refer to Supplies and Options, Chapter 11 in this guide.
“Out of Ink” displays when there is no more ink left in the cartridge and your mailing system stops printing. In order to resume printing you must change the ink cartridge.
WARNING!
You must use only ink cartridges supplied by Pitney
Bowes. The use of any other ink cartridges will void your warranty and maintenance agreement.
WARNING!
The ink in the cartridge may be harmful if swallowed. Keep new and used cartridges out of reach of children. Discard empty cartridges immediately
WARNING!
Do not remove the ink cartridge if the printhead is not installed. If the ink cartridge and printhead are removed at the same time, ink from the print supply line will flow down the tube and squirt from the needle in the ink cartridge holder out into the printer and system interior.
WARNING!
Make sure there is enough room to fully lift the main cover without bumping the IntelliLink®
Control Center.
SV61162 Rev. C 9-11
9 • Maintaining and Updating
Replacing the
Ink Cartridge
continued
To replace the ink cartridge:
1. Lift up the main cover and locate the ink cartridge lid.
2. Push the tab on the front of the cartridge lid.
Lift the lid up and push toward the back of the machine.
Ink cartridge lid
3. Remove the ink cartridge by lifting it straight up.
9-12
Ink cartridge
SV61162 Rev. C
DM800™ Series Digital Mailing System Operating Guide
Replacing the
Ink Cartridge
continued
4. Insert the ink cartridge with the grooved side facing you.
5. Close the ink cartridge lid and push down until it locks into place.
6. Close the main cover.
7. Print a test pattern to verify that you have installed the ink cartridge correctly (see Printing
a Test Pattern in this chapter).
Changing the
Printhead
If you have cleaned the printer nozzle and changed the print cartridge and the meter stamp is still not satisfactory, replace the printhead.
CAUTION: Do NOT attempt to clean the printhead.
Instructions for replacing the printhead are included with each replacement and are repeated here for your convenience.
1. Press the Menu key.
2. Select Maintenance.
3. Select Replace Printhead. The “Printhead Warning - Continue?” screen appears. Read this screen carefully since once you agree to continue, you cannot cancel the process.
4. Once you verify that you have a replacement printhead, select Yes,
continue from the screen. The “Replace Printhead” screen appears.
5. Open the main cover and locate the printhead tab.
Printhead tab
SV61162 Rev. C 9-13
9 • Maintaining and Updating
6. Push the printhead tab to the left as shown here.
7. While continuing to press the printhead tab to the left, pull the assembly forward as shown here. This exposes the printhead cover.
Printhead cover
8. Grasp the printhead cover and pull up as shown here.
9-14 SV61162 Rev. C
Changing the
Printhead
continued
DM800™ Series Digital Mailing System Operating Guide
9. Locate the stand-off on top of the printhead shown here.
10. Grasp the printhead stand-off and lift the printhead up and out.
11. Discard the old printhead.
Printhead stand-off
SV61162 Rev. C
12. Locate the new printhead.
Remove the orange packing tab from the new printhead as shown here.
13. Install the new printhead in the printhead slot.
9-15
9 • Maintaining and Updating
14. Close the printhead cover and push the printhead tab back into place.
15. Close the main cover; the “Initializing Printhead” screen appears.
16. Once the initializing is complete, the “Print Test Pattern” screen appears and prompts you to “Press Tape or print an envelope”.
You must perform the print test at this time. Follow the prompts, or refer to Printing a Test Pattern in this chapter for more information.
17. Proceed to Changing the Wiper Blade Assembly.
Changing the
Wiper Blade
Assembly
When you change the printhead, you must also replace the wiper blade assembly.
Instructions for replacing the wiper blade assembly are included with each replacement and are repeated here for your convenience.
1. From the IntelliLink® Control Center, press the Menu key.
2. Select Maintenance.
3. Select Replace Wiper Blade Assembly.
The “Preparing Wiper Blade” screen appears. During this time, the system moves the printhead assembly back so that you can access the wiper blade assembly.
4. The “Replace Wiper Blade Assembly” screen appears instructing you to remove the wiper blade assembly from the package.
5. Lift the main cover and locate the wiper blade assembly.
6. Push the wiper blade tab toward the back of the machine. This causes the wiper blade to slide to the left.
7. Lift the wiper blade up and out of the assembly and discard.
8. Place the new wiper blade in the assembly with the two white prongs facing to the right. Slide it to the right until it snaps into place.
Wiper blade tab Wiper blade assembly
9. Close the main cover; the
“Initializing Wiper Blade” screen appears.
10. Once the initializing is complete, the “Print Test Pattern” screen appears and prompts you to “Press Tape or print an envelope”.
You must perform the print test at this time. Follow the prompts, or refer to Printing a Test Pattern in this chapter for more information.
9-16 SV61162 Rev. C
Performing
Updates or
Adding
Features
DM800™ Series Digital Mailing System Operating Guide
This section describes how to:
• Turn on new features.
• Perform software updates and download new postal rates.
• Add new advertisements and inscriptions.
Turn on New Features
If you purchase a particular feature before your system is delivered, your
Pitney Bowes representative will enter the feature code when installing your system. If you purchase the feature after your system is installed, you will be given the feature code when you purchase the feature.
1. Press the Menu key on the IntelliLink® Control Center and select Turn
Features On.
2. The system prompts you to enter the numeric code of the feature you want to enable.
3. Type in the code and press the Enter key. The system notifies you that the feature is now turned on.
Perform Software Updates
1. Press the Menu key.
2. Select Set Up and then press the down arrow key.
3. Select Updates and Add-Ons.
4. Select Check for Updates. The system connects to Pitney Bowes and requests a list of updates.
5. If no updates are available, click OK to exit this screen.
6. If updates are available, select the appropriate update and follow the prompts displayed on the screen.
Add new Advertisements or Inscriptions
1. Press the Menu key.
2. Select Set Up and then press the down arrow key.
3. Select Updates and Add-Ons.
4. Select either Advertisements or Inscriptions depending on which one is appropriate.
5. If your system provides more than one way of adding or updating features, your system may prompt you to “Select Method of Update”. If you see this prompt go to step 6, otherwise follow the prompts.
SV61162 Rev. C 9-17
9 • Maintaining and Updating
Performing
Updates or
Adding Features
continued
6. Select the method of update from the options displayed on the screen.
The options are:
Art Card
Feature Code
Phone Download a. Art Card:
If you select Art Card, the system prompts you to “Place Art Card in slot at side of control panel”. Insert the art card containing the update or add-on and the system begins the download. As soon as it completes you are prompted to restart your system so that the updates can take effect.
b. Feature Code:
If you select Feature Code, you are prompted to enter the numeric value of the feature you want to enable. Type in the code for the feature and press the Enter key. The system then notifies you that the feature is now turned on.
To get a list of all the current features enabled on your system, select the Feature Code, then press the right arrow key and a list of the features appears.
c. Phone Download:
If you select Phone Download, your system dials Pitney Bowes and performs the update or add-on as soon as it establishes a connection. As soon as it completes the add-on, it prompts you to restart your system so that the updates can take effect.
9-18 SV61162 Rev. C
SV61162 Rev. C
10 Troubleshooting
Contents
How to Troubleshoot Your Mailing
System ........................................................10-2
Envelope Sealing Problems .......................10-2
Envelope Feeding Problems ......................10-4
Tape Feeding Problems .............................10-8
Printing Problems .......................................10-9
Postage Refill Problems ............................10-10
Display Problems ...................................... 10-11
Weighing Problems ...................................10-12
10-1
10 • Troubleshooting
How to
Troubleshoot
Your Mailing
System
This chapter contains a list of problems you may encounter while using your DM Series™ System.
Review the problems and if you are unable to find a solution, call the Help
Desk or you can schedule a request for service at our web site. Refer to the Pitney Bowes Contact Information List at the front of this guide for the phone number of the Help Desk and the web site addresses.
Envelope Sealing Problems
Envelope(s) not sealing, or not sealing properly
Possible Causes
No E-Z Seal® Sealing Solution in the bottle, or bottle is placed incorrectly.
Moistener brush is dirty or worn.
Solution
Remove the E-Z Seal® solution bottle and refill or reposition the bottle.
Refer to E-Z Seal® Maintenance section in Chapter 9 of this guide.
Replace or clean the moistener brush.
Refer to the Cleaning or Replacing the
Moistener Brush section in Chapter 9 of this guide.
Envelopes are not positioned on the feed deck correctly, or side guide is out too far.
Place the envelopes with the flaps down and against the rear wall.
Make sure the envelopes are pushed far enough so that they cover the feed sensor on the rear wall.
Adjust the side guide so it is close to, but not touching, the bottom edge of the envelope stack.
Be sure and leave a slight clearance between the side guide and envelopes
(about 1/16 inch clearance).
Feed sensor
Side guide
10-2 SV61162 Rev. C
DM800™ Series Digital Mailing System Operating Guide
Envelope Sealing Problems
Envelope(s) not sealing, or not sealing properly
Possible Causes
Envelope flap dimensions are not within the acceptable range.
Solution
Use envelopes with flap depths between
1" and 3 7/8" (25.4 mm and 98.4 mm).
Flap depth
SV61162 Rev. C 10-3
10 • Troubleshooting
Envelope Feeding Problems
More than one envelope is feeding
Possible Causes
Too many envelopes are on the feed deck; envelopes are not stacked properly on the feed deck.
Solution
Remove some of the envelopes and test with a smaller stack.
Slant the envelopes slightly to the left
(shingled).
Envelopes shingled to the left
Feeder adjustment setting is incorrect.
OR
Envelopes are too thick or thin for the feeder adjustment setting.
Adjust the thickness adjustment knob to correspond to the envelope thickness.
For thicker pieces of mail (3/8” to 5/8”), or mail containing several inserts, use the thick mail setting. For mail containing only single inserts, or for postcards, use the normal mail setting.
Thick mail setting
Trying to feed presealed envelopes with the seal mode set to sealer on.
Normal mail setting
Press the Seal key from the control center and select Sealer off.
10-4 SV61162 Rev. C
DM800™ Series Digital Mailing System Operating Guide
Envelope Feeding Problems
Envelope(s) getting jammed
Possible Causes
You are using envelopes that have dimensions that are outside the acceptable range.
Solution
Refer to the Mailing Materials section in Appen-
dix C, in this guide for the acceptable envelope dimensions.
To clear a jam in the Feed deck:
1. Lift the feeder cover.
2. Pull up on the top release jam lever.
3. Lift up the lower release lever.
4. Remove the envelope.
Top release jam lever
Lower release lever
5. Depending on how badly the envelope is damaged, you may need to replace it.
6. Make sure the feed deck is clear and the jam release levers are down.
7. To continue processing mail, close the cover and select Start to continue from the display.
SV61162 Rev. C 10-5
10 • Troubleshooting
Envelope Feeding Problems
Envelope(s) getting jammed
continued
Possible Causes
You are using envelopes that have dimensions that are outside the acceptable range.
Solution
To clear a jam in the WOW™ deck:
1. Lift the WOW™ cover.
2. Pull the WOW™ transport jam release lever to the left.
3. Remove the envelope.
WOW™ transport jam release lever
5. Depending on how badly the envelope is damaged, you may need to replace it.
6. Make sure the WOW™ deck is clear and the jam release lever is down.
7. To continue processing mail, close the cover and select Start to continue from the display.
10-6 SV61162 Rev. C
DM800™ Series Digital Mailing System Operating Guide
Envelope Feeding Problems
Envelope(s) getting jammed
continued
Possible Causes
You are using envelopes that have dimensions that are outside the acceptable range.
Solution
To clear a jam in the Transport deck:
1. Pull out on the transport release knob.
2. Remove the envelope.
3. If the jam occurred before the system applied postage to the envelope, the system will now print the postage on a tape.
Apply the postage tape to the envelope.
4. Push the transport deck back up until it snaps into position.
5. Make sure the transport deck is level with the feed deck.
6. Run a test pattern to make sure the printhead isn’t damaged. Refer to the
Printing a Test Pattern section in
Chapter 9 in this guide.
Transport deck
Transport release knob
SV61162 Rev. C 10-7
10 • Troubleshooting
Tape Feeding Problems
Tape jamming in the feeder
Possible Causes
Adhesive is left on the leading edge of the new tape roll, or the leading edge of the tape is rolled or folded under the tape roller.
Solution
1. Lift the feed cover.
2. Select Unload Tape from the screen.
3. The system backs the tape out of the tape slot.
If the system fails to back the tape out of the slot, gently pull the tape out of the slot.
4. Cut off the portion of the tape that is rolled over or crimped. Make sure the leading edge of the tape is completely covered with the protective backing and that you have a clean, straight cut.
5. Put the tape back in so that it feeds from the bottom of the roll to the right.
The protective backing on the tape should be facing down.
Pull about 10 inches of tape from the end of the roll up toward the cover and then loop it down into the slot. Feed the tape back into the tape slot (feed tape from the bottom of the roll).
6. From the “Out of Tape” screen, select
Press Tape to feed tape to feed the tape through the machine. The machine automatically cuts off the excess tape.
7. Close the feed cover.
8. If this problem continues, call the Help desk. Refer to the Pitney Bowes Con-
tact Information List in this guide.
10-8 SV61162 Rev. C
DM800™ Series Digital Mailing System Operating Guide
Printing Problems
No postage is printing
Possible Causes
The Postage Mode is set to Seal
Only.
Postal Inspection is required. Your mailing system performs an automatic postal inspection every time you do a refill. If you have not done a refill in the last 120 days, you will not be able to print postage.
Solution
From the IntelliLink® Control Center, press the Mode key and select the appropriate postage mode option displayed on the screen.
Refer to the Selecting the Postage Mode section in Chapter 4 in this guide.
Add postage. If you do not need to add postage at this time, simply log onto the
Pitney Bowes Data Center and check for updates. The system will automatically perform a meter inspection.
Your postal rate or special service requires a ZIP Code or Zone.
Meter imprint is out of alignment
Envelope is skewing on the feed deck.
Enter the ZIP Code or Zone. Refer to the
Entering ZIP Codes and Zones section in
Chapter 4 in this guide.
Adjust the thickness adjustment knob to correspond to the envelope thickness.
For thicker pieces of mail (3/8” to 5/8”), or mail containing several inserts, use the thick mail setting. For mail containing only single inserts, or for postcards, use the normal mail setting.
Thick mail setting
Normal mail setting
Position the side guide close to but not touching the envelope.
SV61162 Rev. C 10-9
10 • Troubleshooting
Printing Problems
Meter imprint is streaked or incomplete; poor print quality:
Possible Causes
The printer nozzle requires maintenance.
You need to change the printhead and wiper blade assembly.
Solution
Clean the printer nozzle and run a test print as described in the Cleaning the Printer Nozzle section in Chapter 9 in this guide.
If you have already cleaned the printer nozzle and this fails to correct the problem, you need to change the printhead and wiper blade assembly.
Refer to the Changing the Printhead and Chang-
ing the Wiper Blade Assembly sections in Chapter
9 in this guide.
If this fails to correct the problem, call the Help desk. Refer to the Pitney Bowes Contact Informa-
tion List in this guide.
Postage Refill Problems
Refill operation fails when
IntelliLink®
Control Center is on or off the mailing system
Phone line is not connected to an analog line or is loose.
Reconnect the phone line to the back of the
IntelliLink® Control Center.
Phone cord is damaged. Check phone cord for damage (cuts, crimps) and replace if necessary.
Problem with the phone line.
Test the main phone outlet and repair if necessary.
You are using the wrong
Postage By Phone®
Meter Payment System telephone number.
Refill amount exceeds the funds in your account.
Internal problem with the IntelliLink® Control
Center.
Contact the Help Desk for correct number. Refer to the Pitney Bowes Contact Information List in this guide for the phone number of the Help Desk.
The Help Desk may also provide you with a local number to use for Postage By Phone® System.
To change the Postage By Phone® System number, refer to Phone/Network Set Up: PB Phone # section in Chapter 5 of this guide.
Check your account balance. Refer to the
Checking Your Postage By Phone® Account Bal-
ance section in Chapter 6 of this guide.
Call the Help Desk. Refer to the Pitney Bowes
Contact Information List in this guide for the phone number of the Help Desk.
10-10 SV61162 Rev. C
DM800™ Series Digital Mailing System Operating Guide
Display Problems
Display is blank after moving the
IntelliLink®
Control Center
Unable to access display, or keyboard does not respond
Possible Causes
There is no power to the
IntelliLink® Control Center.
Solution
1. Make sure the AC adapter is plugged into the back of the IntelliLink® Control Center.
2. Test the outlet to make sure it has power.
3. If the problem persists, call the Help Desk.
Refer to the Pitney Bowes Contact Informa- tion List in this guide for the phone number of the Help Desk.
This may be a system error. Call the Help Desk. Refer to the Pitney Bowes
Contact Information List in this guide for the phone number of the Help Desk.
Difficult to read the display
You need to adjust the display contrast.
Adjust the display contrast; refer to the Set Dis-
play Contrast and Speaker Volume section in
Chapter 5 in this guide.
If the problem persists, call the Help Desk. Refer to the Pitney Bowes Contact Information List in this guide for the phone number of the Help
Desk.
SV61162 Rev. C 10-11
10 • Troubleshooting
Weighing Problems
Scale does not return to zero or postage weights are erractic
Possible Causes
For MP Series External Weighing
Platform scales:
The scale top cover may not be seated properly on the scale.
Solution
1. Remove the top cover and make sure that the 4 plastic grommets in the scale are seated correctly. The 4 plastic posts of the top cover fit into these grommets.
2. If a grommet, or any part of a grommet, is pushed below the surface of the metal on the scale, reseat it until it appears as shown here:
10-12
Grommet pushed below surface
Properly seated grommet
3. Check to make sure the bubble is centered in the circle as shown. If not, and you have a flatblade screwdriver, center the bubble by adjusting the legs.
Otherwise go to step 4.
Center the bubble
SV61162 Rev. C
DM800™ Series Digital Mailing System Operating Guide
Weighing Problems
Scale does not return to zero or postage weights are erractic
continued
Possible Causes
For MP Series External Weighing
Platform scales:
The scale top cover may not be seated properly on the scale.
Solution
4. If you do not have a screwdriver, lift the corner and adjust the leg(s) until the bubble is centered in the circle.
SV61162 Rev. C
Mail may be touching another surface or object.
5. Replace the top cover and test the scale.
To test the scale:
1. Place a piece of mail of known weight and correct postage on the scale.
2. Press the Mode key.
3. Select Attached Scale; “Attached
Scale Mode” appears on the control center screen.
4. Press the Class key and enter a class.
5. Press the Enter key.
6. Check to see that the correct postage amount appears on the screen.
Make sure you center the mail on the scale and check to be sure it is not touching any other surface or object.
10-13
11 Supplies and Options
Contents
Ordering Supplies ........................................ 11-2
Consumables You Can Order ...................... 11-2
Moistener Kits .............................................. 11-2
Printhead Kit and Wiper Blade
Replacements ............................................ 11-2
Accessories You Can Order ........................ 11-3
USPS Supplies ............................................ 11-4
SV61162 Rev. C 11-1
11 • Supplies and Options
Ordering
Supplies
You can order supplies through the Pitney Bowes Supply Line™, or you can order from the Pitney Bowes web site. The web site features a wide assortment of genuine Pitney Bowes supplies at attractive prices. You can take advantage of special quantity pricing and online discounts. Refer to the Pitney Bowes Contact Information List at the front of this guide for the
Pitney Bowes Supply Line™ phone number and/or web site information.
Ordering a Pitney Bowes Supply Catalog
You can order a Pitney Bowes Supply Line™ Catalog. Refer to the Pitney
Bowes Contact Information List at the front of this guide for the phone number.
Consumables
You Can Order
Ink Cartridges*
Red Ink Cartridges (1) Pack 766-8
* Shelf life/installed life is 1 year or up to 42,100 impressions without an envelope add (up to 21,000 with an envelope add).
WARNING! You must use only ink cartridges supplied by Pitney
Bowes. The use of any other ink cartridges will void your warranty and maintenance agreement.
Self-Adhesive Tape
5” - Box of 3 rolls
E-Z Seal® Sealing Solution
Pint Bottles - four (16 oz) bottles per box
627-8
601-0
Moistener Kits
946-2
Printhead Kit and
Wiper Blade
Replacements
Printhead & Wiper Blade Replacement Kit
(1 printhead, 2 wiper blades)
Wiper Blade Replacement, 1 per box
771-1
771-2
11-2 SV61162 Rev. C
DM800™ Series Digital Mailing System Operating Guide
Accessories
You Can Order
Advertisements and Inscriptions
Advertisements and inscriptions contain messages you can include in the meter stamp. A number of standard advertisements and inscriptions are included with your mailing system.
You can order additional customized advertisements and inscriptions by calling the Pitney Bowes Supply Line™ or visiting the Pitney Bowes web site. Refer to the Pitney Bowes Contact Information List at the front of this guide for the Pitney Bowes Supply Line™ phone number and the Pitney
Bowes web site addresses.
Advertisements included with your DM800™ Series
Digital Mailing System
Address Service Requested
Return Service Requested
Seasons Greetings
United States Flag
Recycle
Happy Thanksgiving
Please Open Immediately
Urgent
URGENT
Inscriptions included with your DM800™ Series
Digital Mailing System
Presorted First Class
Presorted Standard
Non Profit Organization
Standard
Par Avion
Air Mail
Printed Matter
First Class
Priority Mail
Presorted
SV61162 Rev. C 11-3
11 • Supplies and Options
Ordering Permits for Your Mailing System
This feature may be offered as a standard or optional feature and is not available on all Pitney Bowes solutions. Please contact your local account representative to determine if this option is accessible on your system.
You can print a permit on a piece of mail instead of a meter stamp. You purchase permits from the US Post Office. Your permit contains a number that entitles you to special rates and discounts. Sample permits are shown here.
Date
MMM DD YYYY
Piece count
ZIP Code
To order a permit, you need to do the following:
1. Go to the US Post Office and obtain in a permit license. The Post Office provides you with the permit number(s).
2. Contact the Pitney Bowes Supply Line™ and provide them with the permit number(s). You request Pitney Bowes to create customized artwork for the permit(s). Refer to the Pitney Bowes Contact Information
List at the front of this guide for the Pitney Bowes Supply Line™ phone number.
3. Pitney Bowes sends you the permit(s) on an art card that plugs into the side of the IntelliLink® Control Center. Refer to the Performing Up-
dates or Adding Features section in Chapter 9 in this guide.
USPS Supplies
You can order free mailing supplies from the USPS for use with the
DM800™ Series Digital Mailing System by visiting the USPS Shipping
Supplies Online web site.
11-4 SV61162 Rev. C
A Glossary
SV61162 Rev. C A-1
A • Glossary
Accounting
AccuTrac™ Mail Accounting Software A Pitney Bowes mail accounting system software application that allows you to record postage transactions to track costs so you can charge these costs to accounts or customers.
Advertisement
A feature of the mailing system that allows you to charge postage to individual accounts.
Advertisements contain messages and graphics you can print next to the meter stamp.
Alpha Keyboard The part of the keyboard used to enter accounts and other set up information.
Alphanumeric Text
Arrow Keys
Art Card Slot
Text consisting of alphabetic and numerical symbols that can include punctuation marks and other conventional symbols.
The keys you can use to move to new menus, scroll through menus, and select options.
This slot is on the right side of the IntelliLink® Control
Center on the mailing machine and accepts the plug-in art card . The art card contains ads, inscriptions, and permits.
Barcode
Budget Manager
Business Manager
Calibrate
Carrier
Certified Mail
A series of vertical bars and spaces that represent a correct
ZIP code for the delivery address on a piece of mail.
This is an optional enhanced accounting package you can acquire for your DM Series™ Digital Mailing System. It allows you to create and more accounts with higher levels of detail.
Business Manager is an enterprise accounting system that allows you to capture and manage postal transactions from the several different Pitney Bowes meters, mailing machines, and mailing systems. You can manage all systems from a single host PC that is running the Business
Manager application.
The action performed which sets the scale at zero in order to assure accuracy.
The service that delivers your mail such as the USPS or
Federal Express.
Certified Mail is a service offered by the United States
Postal Service® for a fee in addition to postage. Sending
Certified Mail provides a delivery record that the Postal
Service maintains for a period of two years. For additional
Certified Mail options, see Return Receipts or Restricted
Delivery in this glossary.
A-2 SV61162 Rev. C
Certified Mail Rates
Class Key
Clear Key
Communications Port
Control Center
Data Exchange
Delivery Confirmation
Differential Weighing
Error Message
External Device Port
E-Z Seal® Sealing Solution
SV61162 Rev. C
DM800™ Series Digital Mailing System Operating Guide
Please refer to the USPS web site at www.usps.com for rates.
Enables you to select the correct class for your mailing (e.g.
First Class, Priority, Express Flat Rate).
Press to clear an entry or if no data has been entered press to take you to the previous screen.
Place to connect an optional Pitney Bowes scale, printer, or a PC.
The IntelliLink® Control Center is the module mounted on top of the mailing machine that contains the graphic display, function keys, alpha, and numeric keys and the Postal
Security Device (PSD).
Importing account information to a program on your PC.
Delivery Confirmation is a service offered by the United
States Postal Service® that allows you to verify the date and time of delivery of your mail or, if the delivery was unsuccessful, the date and time of the delivery attempt. The service is currently available for Priority Mail and Package
Services, which includes Parcel Select, Parcel Post, Bound
Printed Matter, Special Standard Mail and Library Mail.
You may combine Delivery Confirmation with other services such as COD, insured mail, registered mail, parcel airlift
(PAL) or special handling.
There is no charge for Delivery Confirmation when you ship by Priority Mail and provide an electronic file to the
Postal Service. There is a per piece charge when you ship
Package Services using the electronic option. To get the latest fees, go to www.usps.com
and search for "Delivery
Confirmation".
The weighing mode that allows you to put all of the mail on the scale, then remove each piece one at time. As you remove each piece, the system calculates the weight and prints postage (either on envelopes or tapes). This saves time by eliminating the need to place each piece individually on the scale.
An indication that notifies the operator of a disabling event
(i.e, out of ink).
A plug on the machine that allows you to connect an optional external device, such as a scale or a PC.
The envelope moistening solution you can order from the
Pitney Bowes Supply Line™.
A-3
A • Glossary
Feed Deck
FIM (Facing Identification Mark)
Funds
Funds Key
High Value Warning
Indicia
Ink Cartridge
Inscription
Inspection
Insufficient Funds
IntelliLink® Control Center
Jam Release Lever
Lock Code
Low Funds Warning
Menu Key
Meter
The area of the mailing machine where you feed the envelopes.
A series of five or six vertical bars used by automated postal equipment to identify, orient, and separate reply mail.
The amount of money in your Postage meter (Postal
Security Device - PSD).
Press to get information about funds used in a job, add funds to your meter, enter new refill amounts or get
Postage By Phone® Meter Payment System balance.
A warning that you have entered a postage value above the value that you have entered into the system as your maximum allowable amount. This feature prevents you from accidentally printing more postage than you need.
See Meter Imprint.
Cartridge containing the ink used to produce the meter stamp.
An optional message, such as “First Class” or “Non-Profit,” that prints vertically to the immediate left of the postage imprint.
A meter check required by the USPS.
A warning message that alerts you when you attempt to use more postage than is currently in your Postage Meter
(Postal Security Device - PSD).
See Control Center.
Relieves the tension along the feeder path.
A code that locks the mailing system with a four digit password preventing unauthorized use of your meter.
You may set your machine to warn you when your funds go below a specified amount.
Press to view the main settings and options available.
See Postal Security Device.
A-4 SV61162 Rev. C
DM800™ Series Digital Mailing System Operating Guide
Meter Imprint (or Meter Stamp)
Mixed Mail
Mode Key
Modem
Numeric Keys
Password
Permit
Postage by Phone® System
Postage Meter
Postal Security Device (PSD)
Postage Tape
Presets
Printer Nozzle
Prompt
Quick Refill
Postage stamp printed directly on a piece of mail or tape using a meter device in place of traditional glue or adhesive affixed stamps. This type of postage requires a special form of indicia called an “information based indicia” (IBI). The
US Postal Service’s IBI Program (IBIP) is the program that makes printing of postage by a meter device possible.
Mail consisting of varying lengths and widths.
Press to choose from a variety of mail processing modes.
That part of the mailing system that dials the Pitney Bowes
Postage By Phone® Meter Payment System center and transfers information over the phone.
The part of the IntelliLink® Control Center that you use to enter amounts and numbers.
See Supervisor Password.
A permit is a special postal mark used instead of the usual meter stamp imprint. You open a permit account at the Post
Office. These permits provide you with special processing or discount rates.
The Pitney Bowes system that allows you to purchase postage over the phone line.
See Postal Security Device.
The PSD contains the funds and performs all of the calculations necessary to print meter stamps that comply with the latest USPS standards. The PSD is contained in the DM Series™ Digital Mailing System IntelliLink® Control
Center.
Tape on which reports or meter stamps are printed when a piece of mail is too large or small, or too fragile to run through the mailing system.
A combination of mailing system settings you create and name so that you can call them up as a named preset thereby eliminating the need to enter each setting whenever you use this combination of settings.
The mechanism in the print engine that sprays the ink onto the envelope or tape.
A displayed message requesting you to respond to a choice, condition, or action.
This refill repeats the same amounts of the previous refill.
SV61162 Rev. C A-5
A • Glossary
Rate update
Reports Key
Return Receipts
Restricted Delivery
Screen Keys
Seal Key
Shingle
Side Guide
Signature Confirmation
Sleep Timer
Stacker
Supervisor Password
Tape Exit
A-6
Changing of the postal rates by the USPS.
This key allows you to view a or select a report to print.
A return receipt for Certified Mail serves as a legal document proving the date and time when the recipient took possession of the piece of mail. You fill out a return receipt postcard and the Postal Service sends the green return receipt postcard back to you, the sender.
Restricted Delivery for Certified Mail requires your USPS carrier to deliver only to the person you specified. This person must sign for the mail.
The five keys directly to the left of the display screen that allow you to select options from the menus displayed on the screen.
Press if you want to seal your envelopes without applying postage.
A way to arrange pieces of mail in stepped positions for feeding, so that the mail is accepted one at a time.
The moveable guide at the front of the feed deck used to stabilize the envelope position when feeding it.
A signature proof of delivery service which provides mailers with the signature and text name of the recipient, along with the date, time, and ZIP Code that is provided with Delivery
Confirmation. Actual signatures can be easily obtained from the USPS via fax or mail. This service meets the needs of mailers who require a signature for high-value shipments, legal requirements, or who are specifically concerned with avoiding fraud. For security purposes, digital signatures are not publicly displayed on the web site.
Signature Confirmation may be combined with special services. To get the latest fees, go to www.usps.com
and search for "Signature Confirmation".
The mode that the mailing system automatically enters after a certain period of inactivity.
The holder at the end of the feeder path where mail is deposited. Two types of stackers are available: tabletop drop-stacker and power-stacker.
Code that restricts access to certain mailing system operations.
Location where the tape comes out of the right side of the mailing system.
SV61162 Rev. C
DM800™ Series Digital Mailing System Operating Guide
Test Pattern
Thickness Adjustment Knob
Tyvek®
USPS
WEIGH-ON-THE-WAY™ (WOW™)
Wiper Blade
ZIP Code
ZIP+4 Code
The pattern printed during a test to show the clarity of the meter imprint.
Adjusts the tension to accommodate the thickness of the pieces of mail you are feeding.
A plastic material used for envelopes.
The Unites States Postal Service.
A mail weighing mode that weighs mixed mail as it passes along the feed deck and applies the appropriate postage.
Part of the printing assembly that wipes excess ink off the printhead.
A ZIP Code is a numeric code used by the USPS to identify general and specific geographic areas in the United States.
A 9-digit numeric code incorporating the original 5-digit ZIP
Code, a hyphen, and 4 additional digits. The first 5 digits identify the delivery office. The 4-digit add-on identifies specific delivery segments.
SV61162 Rev. C A-7
SV61162 Rev. C
Appendix B - Operator
Training Checklist
The following checklist includes the topics your
Pitney Bowes representative will discuss with you to ensure that you fully understand how to operate your DM Series™ mailing system.
The checklist is divided into the following sections:
Learning About Your System ........................ B-2
Basic Operations .......................................... B-3
Advanced Operations* ................................. B-4
If You Need to Change Your
System Set up .............................................. B-5
What You Need to Do to
Maintain Your System ................................... B-7
If You Have Problems with Your System ...... B-8
*The Advanced Operations section contains topics for all possible options you can purchase with your system. Your representative will cover only those options that apply to your specific system configuration.
For additional training options, contact your local sales professional.
B-1
B • Operator Training Checklist
Learning About Your System
Place a check mark in the Done box when you complete the topic.
Learning About
System controls, connections and their locations.
The IntelliLink® Control
Center and the main display screen.
DM Series™ Digital Mailing
System throughput.
Mailing material you can use with your system.
How to get technical phone support.
How to get information on the web.
Critical safety information.
Refer to Chapter and Section
Chapter 2, The IntelliLink® Control
Center
Appendix C, Specifications
Appendix C, Mailing Material
Pitney Bowes Contact Information
List
Pitney Bowes Contact Information
List
Chapter 1, Safety Requirements
Page Done
Chapter 2, Parts of Mailing System 2-5
2-14
C-2
C-4
1-4
B-2 SV61162 Rev. C
SV61162 Rev. C
DM800™ Series Digital Mailing System Operating Guide
Basic Operations
Place a check mark in the Done box when you complete the topic.
How to do the following:
Move around, select and enter information in the main screen.
Determine the best way to run mail on your system.
Select the way you are going to run mail on your system.
Get your mail ready to run on your system.
Pick a class, carrier and/or special service for your mail.
Refer to Chapter and Section
Chapter 4, Navigating Hints
Chapter 4, Determining the Correct
Postage Mode
Chapter 4, Selecting the Postage
Mode and Running Mail
Chapter 4, Preparing Your Mail
Choose an account if you are using accounting on your system.
Add postage to your mail after you have already printed it.
Change the date on your mail after you have already printed it.
Connect your IntelliLink®
Control Center (which contains your postage meter) to an analog phone line for adding postage and downloading updates.
See how much money you have in your postage meter.
See how much money is in your Pitney Bowes account.
Chapter 4, Selecting the Class,
Carrier, Special Services, or
Options
Chapter 4, Selecting or
Deselecting an Account
Chapter 4, Adding Postage or
Changing the Date
Chapter 4, Adding Postage or
Changing the Date
Chapter 6, Connecting Your Postage Meter to an Analog Phone
Line
Chapter 6, Checking Available
Funds in Your Postage meter
Chapter 6, Checking Your Postage By Phone® Meter Payment
System Account Balance
Chapter 6, Adding Postage Add postage to your postage meter.
Print a report on an envelope or on a tape
Order replacement supplies for your system.
Chapter 8, Printing a Report
Chapter 11, Ordering Supplies
Page Done
4-2
4-4
4-10
4-6
4-19
4-18
4-30
4-31
6-4
6-6
6-6
6-7
8-2
11-2
B-3
B • Operator Training Checklist
Advanced Operations
Place a check mark in the Done box when you complete the topic.
How to do the following:
Change or advance the date to be printed on your envelope or tape (this does not change your system's date).
Add advertisements to your meter stamp.
Add inscriptions to you meter stamp.
Change the location on the envelope where you print the meter stamp.
Define presets so you can recall specific settings on your mail system.
Use confirmation services
(adding barcode labels to your mail)
Track your confirmation services records on the internet.
Select an optional Smart
Class™.
Setting up the optional Smart
Class™ feature.
Clear the number of mail pieces you have processed on your system.
Add a supervisor password to your system to prevent operators from performing certain operations (like adding postage, or clearing the number of mail pieces).
Add a lock code to your system to keep unauthorized operators out.
Add new features or updates to your system using the
IntelliLink® Control Center.
Refer to Chapter and Section
Chapter 4, Meter Stamp Options:
Date
Chapter 4, Meter Stamp Options:
Advertisement
Chapter 4, Meter Stamp Options:
Inscription
Chapter 4, Meter Stamp Options:
Print Position
Chapter 5, Defining Presets
Chapter 4, Using Electronic
Confirmation Services
Chapter 4, Tracking Information on the Internet
Chapter 4, Selecting a Smart
Class™
Chapter 5, Setting up the Optional
Smart Class™ Feature
Chapter 4, Clearing the Batch
Count
Chapter 5, Setting Up a Supervisor
Password
Chapter 9, Performing Updates or
Adding Features
Page Done
4-21
4-22
4-23
4-24
5-21
4-25
4-26
4-20
5-31
4-32
5-6
Chapter 5, Setting Up a Lock Code 5-7
9-17
B-4 SV61162 Rev. C
SV61162 Rev. C
DM800™ Series Digital Mailing System Operating Guide
If You Need To Change Your System Setup
Place a check mark in the Done box when you complete the topic.
How to do the following:
Change the date on your
DM Series™ System.
Set up a new scale or change settings on an existing scale, including:
• adjust for the scales environment.
• set your system to automatically recognize the scale.
• set up to use differential weighing.
• set up to clear or retain the class value when you add a new weight on the scale.
• set up to clear or retain the ZIP or Zone value when you add a new weight on the scale.
• set up to clear or retain the ZIP or Zone value when the class changes.
• set up to prompt the operator for a ZIP Code or Zone.
• set up a group of ZIP
Codes for a bulk mailing center.
• add ZIP Codes to a Zone
0 rate.
Set the value at which you are warned that you are running low on funds in your meter.
Set the value at which you are warned that you are running low on ink for printing your postage.
Refer to Chapter and Section
Chapter 5, Setting the Date and
Time of Day
Chapter 5, Setting Up the Scale and Selecting Rates
Chapter 5, Scales/Rates: Attached
Scale
Chapter 5, Scales/Rates: Autoscale
Chapter 5, Scales/Rates: Diff
Weigh Trip Weight
Chapter 5, Scales/Rates: Class if
New Piece
Chapter 5, Scales/Rates: Destination if New Piece
Chapter 5, Scales/Rates: Destination if New Class
Chapter 5, Scales/Rates: ZIP/Zone
Prompt
Chapter 5, Scales/Rates: BMC
Intra ZIP
Chapter 5, Scales/Rates: Add ZIPs to Zone 0
Chapter 5, Configuring High/Low
Funds Warnings
Chapter 5, Configuring Low Ink
Warning
Page Done
5-5
5-8
5-8
5-9
5-9
5-9
5-10
5-10
5-10
5-11
5-11
5-17
5-17
B-5
B • Operator Training Checklist
If You Need To Change Your System Setup (continued)
Place a check mark in the Done box when you complete the topic.
How to do the following:
Change timeouts on your
DM Series™ Digital Mailing
System, including:
• set how long the main screen can remain inactive before turning off.
• set how long your system can remain inactive before it shuts down power to the printer and the meter.
• set how much time to wait before your system restores the default or normal preset values.
• set up how much time to wait before the feeder stops after the last envelope is fed.
• set up how much time the system will continue to feed mail placed on the feed deck without having to press the Start key.
Set up your system for a barcode scanner.
Refer to Chapter and Section
Chapter 5, Configuring System
Timeouts
Chapter 5, Configuring System
Timeouts: Display Sleep
Chapter 5, Configuring System
Timeouts: Display Sleep
Chapter 5, Configuring System
Timeouts: Normal Preset Timer
Chapter 5, Configuring System
Timeouts: Feeding Timeout
Chapter 5, Configuring System
Timeouts: Waiting for Env
Chapter 5, Configuring the
Optional Barcode Scanner
Page Done
5-18
5-18
5-18
5-19
5-19
5-20
5-26
B-6 SV61162 Rev. C
SV61162 Rev. C
DM800™ Series Digital Mailing System Operating Guide
What You Need to Maintain Your System
Place a check mark in the Done box when you complete the topic.
How to do the following:
Determine what supplies you need to keep on hand.
Clean the outside or your system.
Replace the tape roll.
Refill the E-Z Seal® Sealing
Solution.
Clean the moistener brush that wets the envelope flap.
Replace the moistener wick for the moistener brush.
Check the print quality by doing a print test.
Change the printhead.
Refer to Chapter and Section
Chapter 9, Items to Keep on Hand
Chapter 9, Cleaning the Exterior
Chapter 9, Tape Maintenance
Chapter 9, E-Z Seal ® Sealing
Solution Maintenance
Chapter 9, Moistener Maintenance
Chapter 9, Cleaning or Replacing the Wick
Chapter 9, Printer Maintenance
Page Done
9-2
9-2
9-2
9-5
9-6
9-7
9-9
Chapter 9, Changing the Printhead 9-13
Change the wiper blade on the printhead.
Replace the ink cartridge.
Chapter 9, Changing the Wiper
Blade Assembly
Chapter 9, Replacing the Ink
Cartridge
9-16
9-11
B-7
B • Operator Training Checklist
If You Have Problems with Your System
Place a check mark in the Done box when you complete the topic.
What to do if the following occurs:
Envelopes are not sealing correctly.
Envelopes are not feeding correctly, or are getting jammed.
Tape is jamming.
Refer to Chapter and Section
Chapter 10, Envelope Sealing
Problems
Chapter 10, Envelope Feeding
Problems
Postage is not printing correctly.
Cannot add postage to your meter.
Difficult to read the display
Getting erratic readings from the scale.
Chapter 10, Tape Feeding Problems
Chapter 10, Printing Problems
Chapter 10, Postage Refill
Problems
Chapter 10, Display Problems
Chapter 10, Weighing Problems
Page Done
10-2
10-4
10-8
10-9
10-10
10-11
10-12
B-8 SV61162 Rev. C
C Specifications
SV61162 Rev. C C-1
C • Specifications
Specifications
DM800™ Series Digital Mailing System - Specifications Table
Dimensions and Weight
Overall Dimensions:
Size (in) without Stacker (1)
Size (mm) without Stacker (1)
36L x 18H x 21D
915L x 457H x 533D
Size (in) with Optional WOW™ Module 56L x 18H x 21D
Size (mm) with Optional WOW™ Module 1422L x 457H x 533D
Weight (kgs):
Base System (Feeder and Printer)
Optional WOW™ Module
72 (32.7)
35 (15.9)
Optional Power Stacker DMPS 31 (14)
(1) For standard drop stacker, add 12" (305 mm) to the overall length; for the optional Power Stacker DMPS, add 31" (787 mm).
Electrical
Electrical Requirements
Agency Approvals
Compliance
Operating Conditions
Temperature Range F (C)
100 - 240 VAC,
50/60 Hz,
6.5 amps, max.
UL and CSA
ENERGY STAR®
Rel. Humidity
Min 40 (04)
Max 109 (43)
Min 8%
Max 95%
Capacities and Features
Feeder Type
Feeder Deck Capacity
Side Guide
Sealing Fluid in Storage Tank
Automatic
7 inches (177.8mm) for a stack of mail
Yes
Enough to seal 3000 pieces of mail
C-2 SV61162 Rev. C
DM800™ Series Digital Mailing System Operating Guide
SV61162 Rev. C
Capacities and Features (continued)
Throughput Speed #10, without optional WOW module, envelopes/min (2)
Throughput Speed #10, with optional WOW module, envelopes/min (2)
Throughput Speed Tape/min for longest meter stamp
Up to 190 or 210
Up to 70 or 90
14
(2) The actual throughput of your mailing system will vary depending on the material processed, the skill of the operator, and whether you are running in reduced speed mode. Refer to Chapter 4, Running Mail for information on running in reduced speed mode.
Sealing
Sealing Method
E-Z Seal® Sealing Solution Fluid
Sensing
Ink Capacity
Without Ads or Inscriptions
With Ads or Inscriptions
Sealing with flap closed
Warning message for low fluid level of
E-Z Seal®
Up to 42,100 impressions
Up to 21,000 impressions
Note: both quantities require a minimum of 80 impressions per day.
Internal Modem
33.6Kbytes/second
Telephone Cord for Analog Line
26 AWG or smaller
Optional Integrated Scale
Platform (0 - 10 lbs. capacity)
Accounting Features
Standard Accounting
Optional Budget Manager
100 standard, or optional
Up to 3000 accounts
Up to 50 operators
1-32 custom carriers
1-50 custom class/fees
1-15 custom reports
10,000 to 15,000 transactions
C-3
C • Specifications
Specifications
continued
Advertisements and Inscriptions
Advertisements
Inscriptions
Permit Mail Image
(An option you may be able to purchase, not available on all systems.)
Up to 10 custom advertisements, plus preloaded advertisements
Up to 20 custom inscriptions, plus preloaded inscriptions
Maximum # of images is 3.
Maximum identifying image name length is 15 characters.
Mailing Materials
Envelope Dimensions
(refer to envelope measurement figure on the next page)
Minimum: 3.5 in. x 5 in. (88.9 mm x 127 mm) postcard size.
Maximum: 13 in. x 13 in. (330 mm x 330 mm) in landscape orientation.
C5 envelopes can be processed when in portrait orientation.
Minimum: 1 in. (25.4 mm) Envelope Flap Depth
(refer to envelope measurement figure)
Envelope Thickness
Maximum: 3 7/8 in. (98.4 mm)
Minimum: 0.007 in. (0.2 mm)
Maximum: 5/8 in. (15.9 mm)
Acceptable Envelope Materials Include • Standard envelope paper
Envelope Flap Profiles
Weight of the Piece of Mail
Tape Roll Width
• Self-mailers
• Tri-fold mail
• Pre-sealed envelopes
• Commercial (square and baronial)
• Executive
• Monarch
10 lbs. maximum for each piece
Either 4 in. (102mm) or 5 inches (127 mm)
C-4 SV61162 Rev. C
13 in.
(330 mm)
Envelope Dimensions
DM800™ Series Digital Mailing System Operating Guide
13 in. (330mm)
3 7/8 in. (98.4 mm)
Maximum
3.5 in.
(88.1 mm)
5 in. (127mm)
1 in. (25.4mm)
Minimum
SV61162 Rev. C C-5
Index
SV61162 Rev. C I-1
I • Index
A
Accessories
description 2-4,11-3 ordering 2-4,11-3
Accounting
selecting the accounting type 7-13
Accounts
changing number 7-5 changing password 7-5
checking Postage By Phone balance 6-6
clearing account information 7-10
explaining account structure 7-15,7-16
Accounts key
AccuTrac™ Mail Accounting System 2-3
AC adapter
connector location 2-9,2-10,6-5
Adding fund to your postage meter 6-7
Advance Date
storing in a custom preset 4-21,5-22
Advertisements
included with system 11-3 ordering 2-4,11-3
Alpha keyboard
description 2-15 location 2-15
Analog phone line
Analog phone line connection 2-10,6-4
Arrow keys
description 2-15 location 2-15
Art card
Attached scale - autotape mode
Attached scale mode
B
Barcodes
using for USPS Confirmation Services 4-27
Barcode scanner
Batch count
Budget Manager
C
Class
selecting a Smart Class™ 4-19 selecting class, carrier, special services 4-19
Class key
Cleaning
exterior of mailing system 9-2
Clear key
description 2-15 location 2-15
Communications
Connectors
on IntelliLink Control Center 2-9
Cover
Custom presets key
how to define preset values 5-22,5-24
I-2 SV61162 Rev. C
DM800™ Series Digital Mailing System Operating Guide
D
Date
Daylight saving
Differential weighing
Display
DJPS/DMPS Power Stacker 2-3,2-5,4-10,4-11,4-
E
E-Z Seal 9-5 adding more solution 9-5
E-Z Seal bottle
description 2-11 location 2-11
Enter key
description 2-15 location 2-15
Envelopes
External device ports
F
Feed deck
Funds
setting the high value warning 5-17 setting the low funds warning 5-17
tranferring account funds 7-11
Funds key
checking available funds 6-6 check Postage By Phone 6-6
H
Help
High funds warning
description 5-17 setting up 5-17
I
Ink cartridge
Inscriptions
included with system 11-3 ordering 2-4,11-3
Inspections
notification of 1-4,6-2 required by USPS 6-2
IntelliLink Control Center (ICC)
connected to remote analog line 2-10
J
Jams
clearing envelope jams in the feed module 10-5
clearing jams in the printer module 10-7
clearing jams in the WOW™ module 10-6
Jam release levers
description 2-11,2-12 location 2-11,2-12 location in optional WOW™ module 2-12
K
Key in postage mode
SV61162 Rev. C I-3
I • Index
L
Language
Lock button
Low funds warning
description 5-17 setting up 5-17
M
preparation 3-2 quick setup and start 3-2
selecting the postage mode 4-10,4-14,4-16
Mailing system
Maintenance
cleaning the printer nozzle 9-10
cleaning/replacing the brush 9-6
cleaning/replacing the wick 9-7
replacing the ink cartridge 9-11
replacing the wiper blade assembly 9-16
Main screen
advertisement display 2-16 postage indicia 2-16 status area 2-16
Manual weight entry mode
Menu key
I-4
using to change elements on mail 4-21
Meter
Meter stamp
Modem
advanced connection settings 5-16
selecting dialing sound 5-14,5-15
Mode key
using to select postage mode 4-10
cleaning/replacing the brush 9-6
cleaning/replacing the wick 9-7
Multi-account summary report 8-4
N
Navigating hints
Normal preset key
Numeric keys
O
On/off switch
Ordering
E-Z Seal 11-2 ink cartridges 11-2 tape 11-2
P
Passwords
SV61162 Rev. C
DM800™ Series Digital Mailing System Operating Guide
protecting mail operations 5-6
setting up for each account 7-5
turning on/off for accounting 7-9
Permit
Postage
checking funds in account 6-6 checking funds in postage meter 6-6
entering the dialing prefix 5-13
entering the number to dial 5-13,5-14
Postage funds
Postage modes
attached scale 4-4,4-5 attached scale - autotape 4-5
differential weighing 4-4,4-5,4-11,4-12,4-13
Postage tape
description 2-11,2-12 location 2-11,2-12 location in option WOW™ module 2-12
Postal Security Device 2-2,6-2
Postcards
Power stacker
optional DJPS 2-3,2-5,2-7,4-10,4-11,4-12,4-
Presets custom presets
how to delete 5-24 how to edit 5-24 how to rename 5-24 how to view 5-24
normal preset
Printer
location of USB connector 2-8,5-25
maintenance 9-9 printing a test pattern 9-9
Printhead
description 2-13 location 2-13
Printing postage
Print permit mode
Q
Quick Reference Card
R
Rates
adding ZIPs to zero zone 5-11 setting up discount codes 5-11
Reduced speed mode
Reports
selecting a 8-3 single account 8-3
SV61162 Rev. C I-5
I • Index
Reports key
S
Scales
procedures for setting up 5-8 setting up attached scale 5-8
setting up ZIP code prompt 5-10 setting up Zone prompt 5-10
scanner
configuring the barcode scanner 5-26
Screen keys
Seal key
Seal only mode
Side guide
adjusting for mail 3-3,4-7,10-2 correct setting 10-2
Smart Class™
Specifications
advertisements and inscriptions C-4
Stacker
Start key
description 2-15 location 2-15
Subaccount
Subsubaccount
Supplies
T
Tape
Tape key
description 2-15 location 2-15
Thickness adjustment knob
description 2-11 location 2-6,2-11
Timeouts
feeder 5-19 normal preset 5-19
transaction 5-20 waiting for envelope 5-20
Time and date stamp mode
Transport release knob
location on optional WOW™ module 2-12
Troubleshooting
envelope feeding problems 10-4–10-6
envelope sealing problems 10-2,10-3
U
Updates
USB ports
USPS confirmation services 4-25
editing or deleting records 4-29
using barcodes 4-27 using before printing 4-27
I-6 SV61162 Rev. C
DM800™ Series Digital Mailing System Operating Guide
W
WEIGH-ON-THE-WAY™
Weighing mail
differential weighing 4-11,4-12,4-13
using WEIGH-ON-THE-WAY™ 4-11,4-12 using Weigh First Piece 4-12
Weight
Weigh First Piece
Wiper blade
Z
ZIP Code
setting system to prompt for 5-10
Zone
setting system to prompt for 5-10
SV61162 Rev. C I-7
advertisement
* Your assessment is very important for improving the workof artificial intelligence, which forms the content of this project
Related manuals
advertisement
Table of contents
- 74 Navigating Hints
- 75 Overview of Mailing System Setup
- 76 Setting the Display Language
- 76 Adjusting Display Contrast and Volume Control
- 77 Setting the Date and Time of Day
- 78 Setting Up a Supervisor Password
- 79 Setting Up a Lock Code
- 80 Setting Up the Scale and Selecting Rates
- 84 Setting Up Postage By Phone®
- 89 Configuring High/Low Funds Warnings
- 90 Configuring Low Ink Warnings
- 91 Configuring System Timeouts
- 95 Defining Custom Presets
- 97 Taking the Meter Out of Service
- 161 Performing Updates or Adding Features
- 160 Changing the Wiper Blade Assembly
- 157 Changing the Printhead
- 154 Replacing the Ink Cartridge
- 153 Printer Maintenance
- 150 Moistener Maintenance
- 149 E-Z Seal® Maintenance
- 146 Tape Maintenance
- 146 Cleaning the Exterior
- 146 Items to Keep On Hand
- 180 USPS Supplies
- 179 Accessories You Can Order
- 178 Wiper Blade and Printhead Kits
- 178 Moistener Kits
- 178 Consumables You Can Order
- 178 Ordering Supplies