advertisement
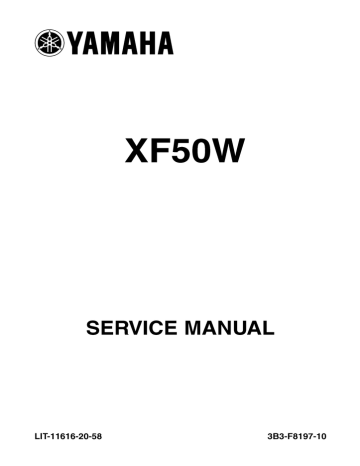
ADJUSTING THE VALVE CLEARANCE
EAS00049
ENGINE
ADJUSTING THE VALVE CLEARANCE
The following procedure applies to all of the valves.
NOTE:
• Valve clearance adjustment should be made on a cold engine, at room temperature.
• When the valve clearance is to be measured or adjusted, the piston must be at top dead center (TDC) on the compression stroke.
1. Remove:
• front cover
• side cover(left and right)
• battery /battery cover
• single seat/trunk
• footrest board
• Refer to”COVER AND PANEL”.
2. Drain:
• coolant
(completely from the radiator)
3. Remove:
• radiator cover ®
• radiator
• fan case ®
Refer to”RADIATOR”in chapter 6.
4. Remove:
• spark plug cap
• spark plug
• ignition coil
• cylinder head cover
5. Remove:
• water pump
Refer to”WATER PUMP”in chapter 6.
6. Measure:
• valve clearance
Out of specification -» Adjust.
Valve clearance (cold)
Intake valve
0.10 ~ 0.16mm(0.0039 ~ 0.0063in)
Exhaust valve
0.18 ~ 0.24mm(0.0071 ~ 0.0094in)
3-10
ADJUSTING THE VALVE CLEARANCE
CHK
ADJ
< &
• • • • • • • • • • • • • • • • • • • • • • • a. Turn the crankshaft counterclockwise. b. When the piston is at TDC on the compression stroke, align the punch mark a in the camshaft sprocket with the stationary b on the plate. c. Align the TDC mark c on the AC magneto rotor with the stationary pointer d on the crankcase cover. d. Measure the valve clearance with a thickness gauge ® .
Out of specification -» Adjust.
• • • • • • • • • • • • • • • • • • • • • • •
3-11
7. Adjust: valve clearance
• • • • • • • • • • • • • • • • • • • • • • • a. Remove the timing chain tensioner and camshaft sprocket. b. Remove the head nuts, bolts and plate. c. Remove the rocker arm shaft, rocker arm and collar. d. Remove the valve p a d 2 with a magnetic b a r 1 .
NOTE:
8 Cover the timing chain opening with a rag to prevent the valve pad from falling into the crankcase.
8 Make a note of the position of each valve pad so that they can be installed in the correct place. e. Select the proper valve pad from the following table.
Valve pad thickness range Available valve pads
Nos.
120 ~ 240
1.20 (0.0472in)
~ 2.40 mm
(0.0945 in)
25 thicknesses in
0.05 mm (0.002 in) increments f. Round off the original valve pad number according to the following table.
ADJUSTING THE VALVE CLEARANCE
CHK
ADJ
< &
Last digit
0 or 2
5
8
Rounded value
0
5
10
EXAMPLE:
Original valve pad number =148(thickness
=1.48mm(0.0583in))
Rounded value =150 g. Locate the rounded number of the original valve pad and the measured valve clearance in the valve pad selection table. The point where the column and row intersect is the new valve pad number.
NOTE:
The new valve pad number is only an approximation. The valve clearance must be measured again and the above steps should be repeated if the measurement is still incorrect. h. Install the new valve pad .
NOTE:
• Lubricate the valve pad with molybdenum disulfide oil.
• Install the valve pad in the correct place. i. Install the rocker arm, collar and rocker arm shaft. j. Install the plate and cylinder head nuts
X | 10Nm(1.0m
* kg, 7.2ft
* lb) k. Install the cylinder head bolts .
X | 10Nm(1.0m
* kg, 7.2ft
* lb) l. Install the camshaft sprocket.
X | 30Nm(3.0m
* kg, 21.7ft
* lb) m. Install the timing chain tensioner and gasket.
X | 9Nm(0.9m
* kg, 6.5ft
* lb)
3-12
ADJUSTING THE VALVE CLEARANCE
CHK
ADJ
< & n. Install the timing chain tensioner spring and cap bolt .
X I 8Nm(0.8m
* kg, 5.8ft
* lb) o. Measure the valve clearance again. p. If the valve clearance is still out of specification, repeat all of the valve clearance adjustment steps until the specified clearance is obtained.
• • • • • • • • • • • • • • • • • • • • • • •
3-13
ADJUSTING THE VALVE CLEARANCE
INTAKE
ORIGINAL VALVE PAD NUMBER •
0.00~0.04
120 125 130 135 140 145 150 155 160 165 170 175 180 185 190 195 200 205 210 215 220 225 230 235 240
120 125 130 135 140 145 150 155 160 165 170 175 180 185 190 195 200 205 210 215 220 225 230
120 125 130 135 140 145 150 155 160 165 170 175 180 185 190 195 200 205 210 215 220 225 230 235 0.05~0.09
0.10~0.16
0.17~0.21 125 130 135 140 145 150 155 160 165 170 175 180 185 190 195 200 205 210 215 220 225 230 235 240
0.22~0.26 130 135 140 145 150 155 160 165 170 175 180 185 190 195 200 205 210 215 220 225 230 235 240
0.27~0.31 135 140 145 150 155 160 165 170 175 180 185 190 195 200 205 210 215 220 225 230 235 240
0.32~0.36 140 145 150 155 160 165 170 175 180 185 190 195 200 205 210 215 220 225 230 235 240
0.37~0.41 145 150 155 160 165 170 175 180 185 190 195 200 205 210 215 220 225 230 235 240
0.42~0.46 150 155 160 165 170 175 180 185 190 195 200 205 210 215 220 225 230 235 240
0.47~0.51 155 160 165 170 175 180 185 190 195 200 205 210 215 220 225 230 235 240
0.52~0.56 160 165 170 175 180 185 190 195 200 205 210 215 220 225 230 235 240
0.57~0.61 165 170 175 180 185 190 195 200 205 210 215 220 225 230 235 240
0.62~0.66 170 175 180 185 190 195 200 205 210 215 220 225 230 235 240
0.67~0.71 175 180 185 190 195 200 205 210 215 220 225 230 235 240
0.72~0.76 180 185 190 195 200 205 210 215 220 225 230 235 240
0.77~0.81 185 190 195 200 205 210 215 220 225 230 235 240
0.82~0.86 190 195 200 205 210 215 220 225 230 235 240
0.87~0.91 195 200 205 210 215 220 225 230 235 240
0.92~0.96 200 205 210 215 220 225 230 235 240
0.97~1.01 205 210 215 220 225 230 235 240
1.02~1.06 210 215 220 225 230 235 240
1.07~1.11 215 220 225 230 235 240
1.12~1.16 220 225 230 235 240
1.17~1.21 225 230 235 240
1.22~1.26 230 235 240
1.27~1.31 235 240
1.32~1.36 240
VALVE CLEARANCE(cold):
0.10~0.16mm(0.0039~0.0063in)
Example:175 pad is installed
Measured clearance is 0.24mm(0.0094in)
Replace pad 175 with pad 185
Pad number: (example)
Pad No.175=1.75mm(0.0689in)
Pad No.185=1.85mm(0.0728in)
EXHAUST
ORIGINAL VALVE PAD NUMBER X
0.00~0.02
0.03~0.07
0.08~0.12
120 125 130 135 140 145 150 155 160 165 170 175 180 185 190 195 200 205 210 215 220 225 230 235 240
120 125 130 135 140 145 150 155 160 165 170 175 180 185 190 195 200 205 210 215 220
120 125 130 135 140 145 150 155 160 165 170 175 180 185 190 195 200 205 210 215 220 225
120 125 130 135 140 145 150 155 160 165 170 175 180 185 190 195 200 205 210 215 220 225 230
120 125 130 135 140 145 150 155 160 165 170 175 180 185 190 195 200 205 210 215 220 225 230 235 0.13~0.17
0.18~0.24
0.25~0.29 125 130 135 140 145 150 155 160 165 170 175 180 185 190 195 200 205 210 215 220 225 230 235 240
0.30~0.34 130 135 140 145 150 155 160 165 170 175 180 185 190 195 200 205 210 215 220 225 230 235 240
0.35~0.39 135 140 145 150 155 160 165 170 175 180 185 190 195 200 205 210 215 220 225 230 235 240
0.40~0.44 140 145 150 155 160 165 170 175 180 185 190 195 200 205 210 215 220 225 230 235 240
0.45~0.49 145 150 155 160 165 170 175 180 185 190 195 200 205 210 215 220 225 230 235 240
0.50~0.54 150 155 160 165 170 175 180 185 190 195 200 205 210 215 220 225 230 235 240
0.55~0.59 155 160 165 170 175 180 185 190 195 200 205 210 215 220 225 230 235 240
0.60~0.64 160 165 170 175 180 185 190 195 200 205 210 215 220 225 230 235 240
0.65~0.69 165 170 175 180 185 190 195 200 205 210 215 220 225 230 235 240
0.70~0.74 170 175 180 185 190 195 200 205 210 215 220 225 230 235 240
0.75~0.79 175 180 185 190 195 200 205 210 215 220 225 230 235 240
0.80~0.84 180 185 190 195 200 205 210 215 220 225 230 235 240
0.85~0.89 185 190 195 200 205 210 215 220 225 230 235 240
0.90~0.94 190 195 200 205 210 215 220 225 230 235 240
0.95~0.99 195 200 205 210 215 220 225 230 235 240
1.00~1.04 200 205 210 215 220 225 230 235 240
1.05~1.09 205 210 215 220 225 230 235 240
1.10~1.14 210 215 220 225 230 235 240
1.15~1.19 215 220 225 230 235 240
1.20~1.24 220 225 230 235 240
1.25~1.29 225 230 235 240
1.30~1.34 230 235 240
1.35~1.39 235 240
1.40~1.44 240
VALVE CLEARANCE(cold):
3-14
ADJUSTING THE VALVE CLEARANCE
CHK
ADJ
< &
8. Install:
8all removed parts
NOTE:
For installation, reverse the removal procedure.
9. Fill:
8cooling system
(with the specified amount of the recommended coolant)
Refer to”CHANGING THE COOLANT”.
3-15
CHECKING THE ENGINE IDLING SPEED
CHK
ADJ
< &
EAS00054
CHECKING THE ENGINE IDLING SPEED
NOTE:
Prior to adjusting the engine idling speed, the air filter element should be clean, and the engine should have adequate compression.
1. Start the engine and let it warm up for several minutes.
2. Remove:
8 panel
Refer to”FOOTREST BOARD AND IN-
NER FENDER”.
3. Connect:
8 digital circuit tester
(onto the spark plug lead of cylinder)
Digital circuit tester
90890-06760
4. Check:
• engine idling speed
Out of specification -» Replace the throttle body assembly.
A Engine idling speed
2000~2200r/min
5. Install:
8 panel
Refer to”FOOTREST BOARD AND IN-
NER FENDER”.
3-16
ADJUSTING THE THROTTLE CABLE FREE PLAY
EAS00056
ADJUSTING THE THROTTLE CABLE FREE
PLAY
NOTE:
Prior to adjusting the throttle cable free play, the engine idling speed should be adjusted properly.
1. Check:
• throttle cable free play a
Out of specification ^Adjust.
Throttle cable free play (at the flange of the throttle grip)
1.5~3.5mm (0.06~0.14in)
2. Adjust:
8throttle cable free play
• • • • • • • • • • • • • • • • • • • • • • •
Handlebar side a. Loosen the locknut 1 . b. Turn the adjusting nut 2 in direction a or b until the specified throttle cable free play is obtained.
Direction a Throttle cable free play is increased.
Direction b Throttle cable free play is decreased. c. Tighten the locknut. w
After adjusting the throttle cable free play, start the engine and turn the handlebars to the right and to the left to ensure that this does not cause the engine idling speed to change.
• • • • • • • • • • • • • • • • • • • • • • •
3-17
CHECKING THE SPARK PLUG
EAS00060
CHECKING THE SPARK PLUG
1 . Remove:
8 panel
Refer to”FOOTREST BOARD AND IN-
NER FENDER”.
2. Disconnect:
8 spark plug cap w
Remove the spark plug cap, the engine is extremely hot.
3. Remove:
8 spark plug c C
Before removing the spark plug, blow away any dirt accumulated in the spark plug well with compressed air to prevent it from falling into the cylinder.
4. Check:
8 spark plug type
Incorrect -* Change.
Spark plug type (manufacturer)
CR7E(NGK)
3-18
5. Check:
8 electrode ©
Damage/wear -* Replace the spark plug.
8 insulator ©
Abnormal color -* Replace the spark plug.
Normal color is medium-to-light tan.
6. Clean:
8 spark plug
(with a spark plug cleaner or wire brush)
7. Measure:
8 spark plug gap a
(with a wire Thickness gauge)
Out of specification -* Regap.
Spark plug gap
0.7 ~0.8mm(0.028 ~0.031in)
CHECKING THE SPARK PLUG
CHK
ADJ
< &
8. Install:
• spark plug
X I 13Nm(1.3m
* kg, 9.4ft
* lb)
NOTE:
Before installing the spark plug, clean the spark plug and gasket surface.
9. Connect:
• spark plug cap
10. Install:
• panel
Refer to”FOOTREST BOARD AND IN-
NER FENDER”.
3-19
CHECKING THE IGNITION TIMING
CHK
ADJ
< &
EAS00062
CHECKING THE IGNITION TIMING wiring connections of the entire ignition system.
Make sure all connections are tight and free of corrosion.
1. Remove:
8front cover
8side cover(left and right)
8battery /battery cover
8single seat/trunk
Refer to”COVER AND PANEL”.
2. Drain:
8coolant
(completely from the radiator)
3. Remove:
8radiator cover
8radiator
8fan case
Refer to”RADIATOR”in chapter 6.
4. Attach:
8timing light 1
8digital circuit tester2
(onto the spark plug lead of cylinder)
Timing light
90890-03141
YU-03141
Digital circuit tester
90890-06760
3-20
CHECKING THE IGNITION TIMING
CHK
ADJ
< &
5. Check:
8ignition timing
• • • • • • • • • • • • • • • • • • • • • • • a. Start the engine, warm it up for several minutes, and then let it run at the specified engine idling speed.
A Engine idling speed
2000 ~ 2200r/min b. Check that the mark a on the AC magneto rotor is within the firing range b on the right crankcase cover.
Incorrect firing range -» Check the ignition system.
• • • • • • • • • • • • • • • • • • • • • • •
NOTE:
The ignition timing is not adjustable.
6. Remove:
• timing light
• digital circuit tester
7. Install:
• fan case
• radiator
• radiator cover
Refer to”RADIATOR”in chapter 6.
8. Fill:
• cooling system
(with the specified amount of the recommended coolant)
Refer to”CHANGING THE COOLANT”.
9. Install:
• single seat/trunk
• battery /battery cover
• side cover(left and right)
• front cover
Refer to”COVER AND PANEL”.
3-21
MEASURING THE COMPRESSION PRESSURE
CHK
ADJ
< &
EAS00067
MEASURING THE COMPRESSION PRES-
SURE
NOTE:
Insufficient compression pressure will result in a loss of performance.
1. Measure:
8 valve clearance
Out of specification -» Adjust
Refer to “ADJUSTING THE VALVE
CLEARANCE”.
2. Start the engine, warm it up for several minutes, and then turn it off.
3. Remove:
8 panel
Refer to”FOOTREST BOARD AND IN-
NER FENDER”.
4. Disconnect:
8 spark plug cap w
Remove the spark plug cap, the engine is extremely hot.
5. Remove:
8spark plug c C
Before removing the spark plug, use compressed air to blow away any dirt accumulated in the spark plug well to prevent it from falling into the cylinder.
6. Install:
8compression gauge 1
3-22
^
Compression gauge
90890-03081
YU-33223
7. Measure:
8 compression pressure
Out of specification -» Refer to steps (c) and (d).
Compression pressure (at sea level)
Minimum
1262kPa(12.62kg/cm
2
, 179.7psi)
Standard
1450kPa(14.5kg/cm
2
, 206.5psi)
Maximum
1624kPa(16.24kg/cm
2
, 231.3psi)
MEASURING THE COMPRESSION PRESSURE
• • • • • • • • • • • • • • • • • • • • • • • a. Set the main switch to “ON”. b. With the throttle wide open, crank the engine until the reading on the compression gauge stabilizes.
FflWUzWIgM
To prevent sparking, ground the spark plug lead before cranking the engine. c. If the compression pressure is above the maximum specification, check the cylinder head, valve surfaces, and piston crown for carbon deposits.
Carbon deposits -» Eliminate. d. If the compression pressure is below the minimum specification, pour a teaspoonful engine of oil into the spark plug bore and measure again.
Refer to the following table.
Compression pressure
(with oil applied into the cylinder)
Reading Diagnosis
Higher than without oil Piston ring(s) wear or damage -» Repair.
Same as without oil Piston ring(s), valves, cylinder head gasket or piston possibly defective -» Repair.
• • • • • • • • • • • • • • • • • • • • • • •
8. Remove:
• compression gauge
9. Install:
• spark plug
X I 13Nm(1.3m
* kg9.4ft
* lb)
10. Connect:
• spark plug cap
11. Install:
• panel
Refer to”FOOTREST BOARD AND IN-
NER FENDER”.
3-23
CHECKING THE ENGINE OIL LEVEL
EAS00069
CHECKING THE ENGINE OIL LEVEL
1. Stand the scooter on a level surface.
NOTE:
8 Place the scooter on a suitable stand.
8 Make sure the scooter is upright.
- T - V ~//
/
^(S) \ ^ ^ \
<\l.
}yyf(M' ^
2. Start the engine, warm it up for several minutes, and then turn it off.
3. Check:
8 engine oil level
The engine oil level should be between the minimum level mark a and maximum level mark b .
Below the minimum level mark -» Add the recommended engine oil to the proper level.
i b
!
a
*0
Recommended engine oil type
YAMALUBE 4, SAE10W30 or
SAE20W40
Recommended engine oil grade
API service SG type or higher
JASO standard MA c C
Do not allow foreign materials to enter the crankcase.
NOTE:
Before checking the engine oil level, wait a few minutes until the oil has settled.
4. Start the engine, warm it up for several minutes, and then turn it off.
5. Check the engine oil level again.
NOTE:
Before checking the engine oil level, wait a few minutes until the oil has settled.
3-24
CHANGING THE ENGINE OIL
CHK
ADJ
< &
EAS00076
CHANGING THE ENGINE OIL
1. Start the engine, warm it up for several minutes, and then turn it off.
2. Place a container under the engine oil drain bolt.
3. Remove:
8engine oil filler cap 1
8engine oil drain bolt 2
(along with the gasket)
4. Drain:
8engine oil
(completely from the crankcase)
5. If the oil filter element is also to be replaced or cleaned, perform the following procedure.
• • • • • • • • • • • • • • • • • • • • • • • a. Remove the oil strainer cover 1,spring3 and oil filter element 4 . b. Replace the O-ring New 2 c. Install the new or clean oil filter element and the oil strainer cover.
Oil strainer cover
32Nm(3.2m
• kg, 23.1ft
• lb)
• • • • • • • • • • • • • • • • • • • • • • •
6. Install:
• engine oil drain bolt
(along with the gasket)
3-25
X | 23Nm(2.3m
* kg, 16.6ft
* lb)
7. Fill:
• crankcase
(with the specified amount of the recommended engine oil)
«0
Quantity
Total amount
0.8~0.9L(0.74~0.83 Imp qt, 0.87~0.98
US qt)
Periodic oil change
0.73~0.83L(0.67~0.76 Imp qt,
0.80~0.90 US qt)
CHANGING THE ENGINE OIL
8. Install:
8engine oil filler cap
9. Start the engine, warm it up for several minutes, and then turn it off.
10.Check:
8engine
(for engine oil leaks)
11.Check:
8engine oil level
Refer to “CHECKING THE ENGINE OIL
LEVEL”.
12.Check: engine oil pressure
• • • • • • • • • • • • • • • • • • • • • • • a. Slightly loosen the oil gallery bolt <RN.1>. b. Start the engine and keep it idling until engine oil starts to seep from the oil gallery bolt. If no engine oil comes out after one minute, turn the engine off so that it will not seize. c. Check the engine oil passages, the oil filter cartridge and the oil pump for damage or leakage. Refer to “OIL PUMP” in chapter 5. d. Start the engine after solving the problem(s) and check the engine oil pressure again. e. Tighten the oil gallery bolt to specification.
V
%
Oil gallery bolt
7Nm (0.7m
• kg, 5.1ft
• lb)
• • • • • • • • • • • • • • • • • • • • • • •
3-26
CHANGING THE TRANSMISSION OIL
CHK
ADJ
< &
CHANGING THE TRANSMISSION OIL
1. Stand the scooter on a level surface.
NOTE:
• Stand the scooter on a suitable stand.
• Make sure that the scooter upright.
2. Start the engine, warm it up for several minutes, and then turn it off.
3. Place a container under the transmission oil drain bolt.
4 Remove:
• transmission oil fill bolt
(along with the gasket)
• transmission oil drain bolt ©
5. Drain:
• transmission oil
(completely from the transmission case)
6. Install:
• transmission oil drain bolt
X I 13Nm(1.3m
* kg, 9.4ft
* lb)
7. Fill:
• transmission case
(with the specified amount of the recommended transmission oil)
K} Recommended oil
SAE10W30 hypoid gear oil
Total amount
0.11~0.13L(0.10~0.12 Imp qt,
0.12~0.14 US qt)
Periodic oil change
0.09~0.11L(0.08~0.10 Imp qt,
0.10~0.12 US qt)
8. Install:
• transmission oil fill bolt ©
(along with the gasket)
X I 23Nm(2.3m
* kg, 16.6ft
* lb)
3-27
9. Start the engine for several minutes to warm it up and check for the oil leakage.
10.Check:
• transmission case
(for transmission oil leaks)
MEASURING THE ENGINE OIL PRESSURE
EAS00077
MEASURING THE ENGINE OIL PRESSURE
1. Check:
8 engine oil level
Below the minimum level mark -» Add the recommended engine oil to the proper level.
Refer to”CHECKING THE ENGINE OIL
LEVEL”.
2. Start the engine, warm it up for several minutes, and then turn it off.
C
When the engine is cold, the engine oil will have a higher viscosity, causing the engine oil pressure to increase. Therefore, be sure to measure the engine oil pressure after warming up the engine.
3. Remove:
8 panel
Refer to”FOOTREST BOARD AND IN-
NER FENDER”.
4. Lossen:
8oil gallery bolt 1 w
The engine, muffler and engine oil are extremely hot.
5. Check:
8engine oil pressure
• • • • • • • • • • • • • • • • • • • • • • • a. Start the engine and keep it idling until engine oil starts to seep from the oil gallery bolt. If no engine oil comes out after one minute, turn the engine off so that it will not seize. b. Check the engine oil passages, the oil filter and oil pump for damage or leakage.Refer to”OIL PUMP” in chapter 5. c. Start the engine after solving the problem(s) and check the engine oil pressure again.
3-28
• • • • • • • • • • • • • • • • • • • • • • •
MEASURING THE ENGINE OIL PRESSURE
CHK
ADJ
< &
6. Install:
8oil gallery bolt
X I 7Nm(0.7m
* kg, 5.1ft
* lb)
7. Install:
• panel
Refer to”FOOTREST BOARD AND IN-
NER FENDER”.
3-29
REPLACING THE AIR FILTER ELEMENT
EAS00086
REPLACING THE AIR FILTER ELEMENT
1. Remove:
8front cover
8side cover(left)
Refer to”SIDE COVERS AND TAIL/
BRAKE LIGHT”.
2. Remove:
8air filter case c o v e r 1
8air filter element
3-30
3. Check:
8 air filter element ©
Damage/dirty^ Replace.
NOTE:
8 Replace the air filter element every
4000km(2000mi) .
8 The air filter needs more frequent service if you are riding in unusually wet or dusty areas.
4. Install:
8 air filter element
8 air filter case cover
X I 10Nm(1.0m
* kg, 7.2ft
* lb)
C
Never operate the engine without the air filter element installed. Unfiltered air will cause rapid wear of engine parts and may damage the engine. Operating the engine without the air filter element will also affect the throttle body tuning, leading to poor engine performance and possible overheating.
NOTE:
When installing the air filter element into the air filter case cover, make sure their sealing surfaces are aligned to prevent any air leaks.
REPLACING THE AIR FILTER ELEMENT
CHK
ADJ
< &
5. Install:
8side cover(left)
8front cover
Refer to”SIDE COVERS AND TAIL/
BRAKE LIGHT”.
3-31
CHECKING THE THROTTLE BODY JOINT AND
INTAKE MANIFOLD/CHECKING THE FUEL HOSE
EAS00094
CHECKING THE THROTTLE BODY JOINT
AND INTAKE MANIFOLD
1. Remove:
8front cover
8side cover(left and right)
8single seat/trunk
Refer to”COVER AND PANEL”.
2. Check:
• throttle body joint (T)
• intake manifold (2)
Cracks/damage -» Replace.
Refer to “FUEL INJECTION SYSTEM” in chapter 7.
3. Install:
• single seat/trunk
• side cover(left and right)
• front cover
Refer to”COVER AND PANEL”.
EAS00096
CHECKING THE FUEL HOSE
The following procedure applies to all of the fuel hose.
1. Remove:
• front cover
• side cover(left and right)
• single seat/trunk
• footrest board
Refer to”COVER AND PANEL”.
3-32
2. Check:
• fuel hose (T)
Cracks/damage -» Replace.
Loose connection -» Connect properly.
3. Install:
• footrest board
• single seat/trunk
• side cover(left and right)
• front cover
Refer to”COVER AND PANEL”.
CHECKING THE BREATHER HOSES
CHK
ADJ
< &
EAS00098
CHECKING THE BREATHER HOSES
1. Remove:
8front cover
8side cover(left and right)
8single seat/trunk
Refer to”COVER AND PANEL”. fer
\ \
X
\ ^ V v^ tx tU
1>f a i i l ^
Si M ^
> i
2. Check:
8 breather hose (T)
8 transmission case breather hose (2)
Cracks/damage -» Replace.
Loose connection -» Connect properly.
C
Make sure the breather hoses are routed correctly.
3. Install:
8single seat/trunk
8side cover(left and right)
8front cover
Refer to”COVER AND PANEL”.
3-33
CHECKING THE EXHAUST SYSTEM
EAS00099
CHECKING THE EXHAUST SYSTEM
The following procedure applies to all of the muffler assembly and gasket.
1. Remove:
8muffler assembly
Refer to”ENGINE REMOVAL”in chapter
5.
2. Check:
• muffler assembly (T)
Crack/damage -» Replace.
• gasket (2)
Exhaust gas leak -» Replace.
3. Check:
• tightening torque
Exhaust pipe nut (3)
13Nm(1.3m
• kg, 9.4ft
• lb)
Muffler and rear arm bolt (4)
31Nm(3.1m
• kg, 22.4ft
• lb)
4. Install:
8muffler assembly
Refer to”ENGINE REMOVAL”in chapter
5.
3-34
CHECKING THE COOLANT LEVEL
EAS00103
CHECKING THE COOLANT LEVEL
1. Stand the scooter on a level surface.
NOTE:
8 Place the scooter on a suitable stand.
8 Make sure the scooter is upright.
2. Check:
8 coolant level
The coolant level should be between the maximum level mark a and minimum level mark b .
Below the minimum level mark -» Add the recommended coolant to the proper level.
C
8 Adding water instead of coolant lowers the antifreeze content of the coolant. If water is used instead of coolant check, and if necessary, correct the antifreeze concentration of the coolant.
8 Use only distilled water. However, if distilled water is not available, soft water may be used.
3. Start the engine, warm it up for several minutes, and then turn it off.
4. Check:
8 coolant level
NOTE:
Before checking the coolant level, wait a few minutes until it settles.
3-35
CHECKING THE COOLING SYSTEM
EAS00104
CHECKING THE COOLING SYSTEM
1. Remove:
8front cover
8side cover(left and right)
8battery /battery cover
8single seat/trunk
8footrest board
Refer to”COVER AND PANEL”.
8radiator cover
Refer to”RADIATOR”in chapter 6.
J l " iy,
\ / -/C-^y ^
<^Cl&
^^\^y^fe^^\^p—\
N^gf
/ ^ I \ X M T ^
^ ^ v
Vg
°V
X3
'•'•':\ 1 '
^7
/
*
s
o )
^~ ^ ^^sr^/^js,
2. Check:
• radiator ©
• radiator inlet hose (2)
• radiator outlet hose (3)
Cracks/damage -» Replace.
Refer to “COOLING SYSTEM” in chapter 6.
3. Install:
• radiator cover
Refer to”RADIATOR”in chapter 6.
• footrest board
• single seat/trunk
• battery /battery cover
• side cover(left and right)
• front cover
Refer to”COVER AND PANEL”.
3-36
CHANGING THE COOLANT
EAS00105
CHANGING THE COOLANT
1. Remove:
8front cover
8side cover(right)
8coolant reservoir cap cover
Refer to”COVER AND PANEL”.
8radiator cover
Refer to”RADIATOR”in chapter 6.
2. Disconnect:
8coolant reservoir hose 1
3. Drain:
8coolant
(from the coolant reservoir)
8coolant
(from the radiator under drain bolt)
4. Remove:
8radiator cap
8coolant reservoir cap w
A hot radiator is under pressure. Therefore, do not remove the radiator cap when the engine is hot. Scalding hot fluid and steam may be blown out, which could cause serious injury. When the engine has cooled, open the radiator cap as follows:
Place a thick rag or a towel over the radiator cap and slowly turn the radiator cap counterclockwise toward the detent to allow any residual pressure to escape. When the hissing sound has stopped, press down on the radiator cap and turn it counterclockwise to remove.
5. Connect:
8coolant reservoir hose
6. Install:
8radiator under drain bolt
X I 1Nm(0.1m
* kg, 0.7ft
* l b )
3-37
CHANGING THE COOLANT
7. Fill:
8cooling system
(with the specified amount of the recommended coolant)
«0 Recommended antifreeze
High-quality ethylene glycol antifreeze containing corrosion inhibitors for aluminum engines
Mixing ratio
4:6(antifreeze:water)
Quantity
Total amount
0.50L(0.46 Imp qt, 0.53 US qt)
Coolant reservoir capacity
0.26L(0.23 Imp qt, 0.28 US qt)
Up to the maximum level mark
3-38
NOTE:
The specified amount of coolant is a standard amount. Fill the cooling system with coolant until coolant comes out of the air bleed bolt hole.
Handling notes for coolant
Coolant is potentially harmful and should be handled with special care. w
If coolant splashes in your eyes, thoroughly wash them with water and consult a doctor.
If coolant splashes on your clothes, quickly wash it away with water and then with soap and water.
If coolant is swallowed, induce vomiting and get immediate medical attention. c C
Adding water instead of coolant lowers the antifreeze content of the coolant. If water is used instead of coolant check, and if necessary, correct the antifreeze concentration of the coolant.
Use only distilled water. However, if distilled water is not available, soft water may be used.
If coolant comes into contact with painted surfaces, immediately wash them with water.
Do not mix different types of antifreeze.
8. Install:
8radiator cap
CHANGING THE COOLANT
CHK
ADJ
< &
9. Fill:
8coolant reservoir
(with the recommended coolant to the maximum level mark 1 )
10.Install:
8coolant reservoir cap
11.Start the engine, warm it up for several minutes, and then stop it.
12.Check:
8coolant level
Refer to “CHECKING THE COOLANT
LEVEL”.
NOTE:
Before checking the coolant level, wait a few minutes until the coolant has settled.
13.Install:
8radiator cover
Refer to”RADIATOR”in chapter 6.
8coolant reservoir cap cover
8side cover(right)
8front cover
Refer to”COVER AND PANEL”.
3-39
advertisement
Related manuals
advertisement
Table of contents
- 8 Scooter Identification
- 8 Vehicle Identification Number
- 8 Model Label
- 9 Features
- 9 Outline Of The FI System
- 10 FI System
- 11 Important Information
- 11 Preparation For Removal And Disassembly
- 11 Replacement Parts
- 11 Gaskets, Oil Seals And O-rings
- 12 Lock Washers/Plates And Cotter Pins
- 12 Bearings And Oil Seals
- 12 Circlips
- 13 Equipment Preparation
- 14 Checking The Connections
- 15 Special Tools
- 20 General Specifications
- 21 Engine Specifications
- 31 Chassis Specifications
- 34 Electrical Specifications
- 37 Conversion Table
- 37 General Tightening Torque Specifications
- 38 Tightening Torques
- 38 Engine
- 40 Chassis
- 42 Lubrication Points And Lubricant Types
- 42 Engine
- 44 Chassis
- 45 Cooling System Diagrams
- 48 Cable Routing
- 56 Introduction
- 57 Periodic Maintenance And Minor Repair
- 57 Periodic Maintenance Chart For The Emission Control System
- 58 General Maintenance And Lubrication Chart
- 60 Cover And Panel
- 60 Side Covers And Tail/brake Light
- 62 Single Seat And Trunk
- 63 Leg Shield 1,2
- 64 Footrest Board And Inner Fender
- 65 Engine
- 65 Adjusting The Valve Clearance
- 71 Checking The Engine Idling Speed
- 72 Adjusting The Throttle Cable Free Play
- 73 Checking The Spark Plug
- 75 Checking The Ignition Timing
- 77 Measuring The Compression Pressure
- 79 Checking The Engine Oil Level
- 80 Changing The Engine Oil
- 82 Changing The Transmission Oil
- 83 Measuring The Engine Oil Pressure
- 85 Replacing The Air Filter Element
- 87 Checking The Throttle Body Joint And Intake Manifold
- 87 Checking The Fuel Hose
- 88 Checking The Breather Hoses
- 89 Checking The Exhaust System
- 90 Checking The Coolant Level
- 91 Checking The Cooling System
- 92 Changing The Coolant
- 95 Chassis
- 95 Adjusting The Front Brake
- 95 Adjusting The Rear Brake
- 96 Checking The Front And Rear Brake Shoes
- 97 Checking And Adjusting The Steering Head
- 99 Checking The Front Fork
- 100 Checking The Tires
- 103 Checking The Wheels
- 103 Checking And Lubricating The Cables
- 104 Lubricating The Levers And Pedals
- 104 Lubricating The Centerstand
- 105 Electrical System
- 105 Checking And Charging The Battery
- 111 Checking The Fuse
- 113 Replacing The Headlight Bulb
- 114 Adjusting The Headlight Beam
- 117 Front Wheel And Brake
- 118 Front Wheel
- 119 Front Brake Shoe Plate
- 120 Removing The Front Wheel
- 120 Disassembling The Brake Shoe Plate
- 121 Checking The Front Wheel
- 122 Checking The Speedometer Gear Unit
- 123 Checking The Brake
- 124 Assembling The Brake Shoe Plate
- 125 Assembling The Front Wheel
- 126 Installing The Front Wheel
- 127 Adjusting The Front Wheel Static Balance
- 129 Rear Wheel And Brake
- 130 Removing The Rear Wheel
- 130 Checking The Rear Wheel
- 131 Checking The Rear Wheel Drive Hub
- 131 Checking The Brake
- 132 Assembling The Brake Shoe Plate
- 134 Installing The Rear Wheel
- 134 Adjusting The Rear Wheel Static Balance
- 135 Front Fork
- 137 Removing The Front Fork Legs
- 137 Disassembling The Front Fork Legs
- 139 Checking The Front Fork Legs
- 140 Assembling The Front Fork Legs
- 142 Installing The Front Fork Legs
- 143 Handlebar
- 145 Removing The Handlebar
- 145 Checking The Handlebar
- 146 Installing The Handlebar
- 148 Steering Head
- 148 Handlebar Bracket And Headlight Stay Bracket
- 149 Lower Bracket
- 150 Removing The Lower Bracket
- 151 Checking The Steering Head
- 152 Installing The Steering Head
- 153 Rear Shock Absorber Assembly
- 154 Removing The Rear Shock Absorber Assembly
- 154 Checking The Rear Shock Absorber Assembly
- 155 Installing The Rear Shock Absorber Assembly
- 158 Engine Removal
- 158 Leads, Hoses And Muffler
- 160 Engine
- 161 Installing The Engine
- 162 Cylinder Head
- 164 Removing The Cylinder Head
- 166 Checking The Cylinder Head
- 167 Installing The Cylinder Head
- 170 The Rocker Arms And Camshaft
- 171 Removing The Rocker Arms And Camshaft
- 172 Checking The Camshaft
- 173 Checking The Rocker Arms And Rocker Arm Shafts
- 174 Checking The Timing Chain, Camshaft Sprocket, And Timing Chain Guides
- 175 Checking The Timing Chain Tensioner
- 176 Installing The Camshaft And Rocker Arms
- 177 Valves And Valve Springs
- 179 Removing The Valves
- 181 Checking The Valves And Valve Guides
- 183 Checking The Valve Seats
- 185 Checking The Valve Springs
- 186 Installing The Valves
- 188 Cylinder And Piston
- 189 Removing The Cylinder And Piston
- 190 Checking The Cylinder And Piston
- 192 Checking The Piston Rings
- 193 Checking The Piston Pin
- 194 Checking The Timing Chain Guide
- 194 Installing The Piston And Cylinder
- 196 Belt Drive
- 196 V-belt Case Cover
- 197 Kickstarter
- 198 Installing The Kickstarter
- 199 V-belt And Primary/Secondary Sheave
- 200 Secondary Sheave
- 201 Removing The Primary Sheave
- 201 Removing The Secondary Sheave And V-belt
- 202 Disassembling The Secondary Sheave
- 202 Checking The Clutch Shoes
- 203 Checking The V-belt
- 203 Checking The Primary Sheave
- 204 Checking The Primary Sheave Weights
- 204 Checking The Slider
- 204 Checking The Secondary Sheave
- 205 Assembling The Primary Sheave
- 206 Assembling The Secondary Sheave
- 207 Installing The Secondary Sheave, V-belt And Primary Sheave
- 210 Starter Clutch And AC Magneto
- 210 Stator Coil Assembly
- 212 Starter Clutch
- 213 Removing The AC Magneto
- 214 Removing The Starter Clutch
- 215 Checking The Starter Clutch
- 216 Installing The Starter Clutch
- 216 Installing The AC Magneto
- 218 Oil Pump
- 219 Checking The Oil Pump
- 220 Assembling The Oil Pump
- 220 Installing The Oil Pump
- 221 Transmission
- 222 Checking The Transmission
- 223 Crankshaft
- 223 Crankshaft Assembly
- 225 Disassembling The Crankcase
- 226 Removing The Crankshaft Assembly
- 226 Checking The Crankshaft And Connecting Rod
- 227 Checking The Crankcase
- 228 Checking The Timing Chain And Timing Chain Guide(intake Side)
- 228 Checking The Bearings And Oil Seals
- 228 Checking The Circlips And Washers
- 229 Installing The Crankshaft
- 229 Assembling The Crankcase
- 232 Radiator
- 233 Checking The Radiator
- 234 Installing The Radiator
- 235 Thermostat
- 236 Checking The Thermostat
- 237 Installing The Thermostat
- 238 Water Pump
- 240 Disassembling The Water Pump
- 240 Checking The Water Pump
- 241 Assembling The Water Pump
- 242 Installing The Water Pump
- 244 Fuel Injection System
- 245 Wiring Diagram
- 247 ECU's Self-Diagnostic Function
- 248 Checking For A Defective Engine Trouble Warning Light Bulb
- 248 Self-Diagnostic Fanction Table
- 250 Troubleshooting Chart
- 251 Diagnostic Mode
- 255 Troubleshooting Details
- 269 Throttle Body And Fuel Injector
- 269 Throttle Body
- 270 Fuel Injector And Fuel Hose
- 271 Fuel Tank
- 272 Removing The Fuel Hose
- 272 Removing The Fuel Pump
- 273 Checking The Throttle Body
- 274 Installing The Fuel Pump
- 274 Installing The Fuel Hose
- 275 Checking The Fuel Pump And Pressure Regulator Operation
- 275 Checking The Throttle Position Sensor
- 277 Checking The ISC (Idle Speed Control) Valve
- 278 Air Induction System
- 278 Air Injection
- 278 Air Cut-Off Valve
- 279 Air Induction System Diagrams
- 280 Air Cut-Off Valve And Air Filter Case
- 281 Checking The Air Induction System
- 283 Electrical Components
- 284 Wiring Diagram
- 286 Checking Switch Continuity
- 287 Checking The Switches
- 288 Checking The Bulbs And Bulb Sockets
- 288 Types Of Bulbs
- 289 Checking The Condition Of The Bulbs
- 290 Checking The Condition Of The Bulb Sockets
- 291 Ignition System
- 291 Circuit Diagram
- 292 Troubleshooting
- 296 Electric Starting System
- 296 Circuit Diagram
- 297 Starting Circuit Cut-off System Operation
- 298 Troubleshooting
- 302 Starter Motor
- 303 Checking The Starter Motor
- 305 Assembling The Starter Motor
- 306 Charging System
- 306 Circuit Diagram
- 307 Troubleshooting
- 309 Lighting System
- 309 Circuit Diagram
- 310 Troubleshooting
- 312 Checking The Lighting System
- 316 Signaling System
- 316 Circuit Diagram
- 317 Troubleshooting
- 318 Checking The Signaling System
- 324 Cooling System
- 324 Circuit Diagram
- 325 Troubleshooting
- 327 Checking The Cooling System
- 331 Starting Failure/Hard Starting
- 331 Engine
- 331 Fuel System
- 331 Electrical Systems
- 332 Incorrect Engine Idling Speed
- 332 Engine
- 332 Fuel System
- 332 Electrical Systems
- 333 Poor Medium-And-High-Speed Performance/Faulty Clutch
- 333 Engine
- 333 Fuel System
- 333 Faulty Clutch
- 333 Engine Operates But Scooter Will Not Move
- 333 Clutch Slips
- 333 Poor Starting Performance
- 334 Poor Speed Performance
- 334 Overheating
- 334 Engine
- 334 Cooling System
- 334 Fuel System
- 334 Chassis
- 334 Electrical Systems
- 334 Overcooling
- 334 Cooling System
- 335 Poor Braking Performance
- 335 Faulty Front Fork Legs
- 335 Leaking Oil
- 335 Malfunction
- 335 Unstable Handling
- 336 Faulty Lighting Or Signaling System
- 336 Headlight Does Not Come On
- 336 Headlight Bulb Burnt Out
- 336 Tail/brake Light Does Not Come On
- 336 Tail/brake Light Bulb Burnt Out
- 336 Turn Signal Does Not Come On
- 336 Turn Signal Blinks Slowly
- 336 Turn Signal Remains Lit
- 336 Turn Signal Blinks Quickly
- 336 Horn Does Not Sound