Tool calibration with a probe (level 2). Fagor CNC 8055 for lathes, CNC 8055, CNC 8055 for other applications
Add to My manuals210 Pages
Fagor CNC 8055 is a versatile and powerful CNC system designed to provide users with advanced control over their machine tools. With its intuitive interface and comprehensive range of features, the Fagor CNC 8055 is ideal for a wide variety of applications, from simple 2-axis milling to complex 5-axis contouring.
Some of the key capabilities of the Fagor CNC 8055 include:
- Advanced contouring capabilities with support for up to 5 axes of simultaneous motion
- Powerful macro programming language for creating custom cycles and routines
- Intuitive graphical user interface for easy programming and operation
- Remote monitoring and diagnostics for increased uptime and productivity
- Comprehensive range of I/O options for flexible connectivity
With its advanced features and capabilities, the Fagor CNC 8055 is the perfect choice for users who demand the best in CNC control.
advertisement
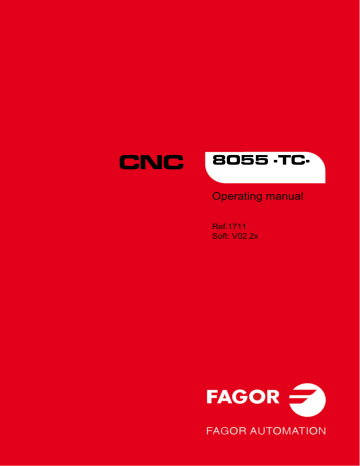
2.
Operating manual
2.7.3
Tool calibration with a probe (level 2)
This calibration level requires the purchase of the right software options purchased and the use of a table-top probe.
Once the cycle has concluded, it updates the tool offset table with the length value X Z of the tool offset that is currently selected. The I and K values are updated to 0.
Defining the cycle data
The following data must be defined.
• Tool number (T) and tool offset (D) to be calibrated.
• Safety distance (Ds) for probe approach.
• Probing feedrate (F).
Probe position.
In this zone, one must indicate whether the cycle assumes the probe position defined in the machine parameters or the position defined in this zone. To select one of them, use the cursor to select the
"Machine parameters / Programmable parameters" field and press the two-color key.
TOOL WEAR MEASUREMENT
In this cycle, besides calibrating a tool, it is also possible to measure tool wear.
Using the tool wear measuring operation, the user can define the maximum tool wear value. After several tool wear measuring probing operations, the wear will increase and when it exceeds the set maximum value, the tool will be rejected.
To perform this cycle it is necessary to have a table-top probe, installed in a fixed position on the machine and with its faces parallel to axes X, Y, Z.
When accessing this calibration level, the CNC shows the following information:
CNC 8055
CNC 8055i
·TC· O PTION
S OFT : V02.2
X
A.
Indicating the selected work mode.
B.
Graphic assistance for tool calibration.
C.
Current machine status.
D.
Tool number and associated offset.
E.
Calibration data.
F.
Type of operation and wear values.
G.
Probe position.
This level may be saved as part of a part-program using the [P.PROG] key or executed using the
[START] key.
·58·
Operating manual
Defining the cycle data
The following data must be defined. Not all the data will always be available; the cycle will show the necessary data according to the chosen operation.
• Safety distance (Ds) for probe approach.
• Probing feedrate (F).
• Icon to set the Y axis direction.
• Type of operation:
The cycle allows doing a measurement or a calibration. To select the desired operation, place the cursor in the "Measurement / Calibration" field and press the two-color key. To take a measurement, define the following data.
Imax
Kmax
Maximum tool length wear measurement along the X axis.
Maximum tool length wear measurement along the Z axis.
Jmax Maximum tool length wear measurement along the Y axis.
Stop / Chg Cycle behavior when exceeding the maximum wear permitted. Use the two-color key to select one of them.
The "Stop" option interrupts the execution for the user to select another tool. With the "Chg" option, the cycle replaces the tool with another one of the same family.
Measuring is only available when purchasing the software option: "Tool life monitoring".
• Probe position.
In this zone, one must indicate whether the cycle assumes the probe position defined in the machine parameters or the position defined in this zone. To select one of them, use the cursor to select the "Machine parameters / Programmable parameters" field and press the two-color key.
Machine parameters: The cycle assumes the probe position defined in the machine parameters.
Programmed parameters: The cycle assumes the probe position defined in the cycle (Xmax,
Xmin, Ymax, Ymin, Zmax, Zmin).
Actions after completing the tool wear measuring cycle
To activate the rejected tool, either because it has been replaced with another one or because it will be used to keep working, the following options will be offered:
1.
Go into the tool table in ISO mode and delete the actual (real) life of that tool.
2.
Go into the tool table in ISO mode and write the desired value for the actual (real) life of that tool.
In this case, activating the tool requires the real life to be smaller than the nominal (rated) life value. Otherwise, the tool will appear as expired (worn out) (status = E).
2.
CNC 8055
CNC 8055i
·TC· O PTION
S OFT : V02.2
X
·59·
advertisement
Key Features
- Advanced contouring capabilities with support for up to 5 axes of simultaneous motion
- Powerful macro programming language for creating custom cycles and routines
- Intuitive graphical user interface for easy programming and operation
- Remote monitoring and diagnostics for increased uptime and productivity
- Comprehensive range of I/O options for flexible connectivity
Related manuals
Frequently Answers and Questions
What is the maximum number of axes that the Fagor CNC 8055 can control?
Does the Fagor CNC 8055 support macro programming?
Is the Fagor CNC 8055 easy to use?
Can the Fagor CNC 8055 be monitored and diagnosed remotely?
What types of I/O options are available for the Fagor CNC 8055?
advertisement
Table of contents
- 7 About the product
- 9 Declaration of conformity and Warranty conditions
- 11 Version history
- 15 Safety conditions
- 19 Returning conditions
- 21 Additional notes
- 23 Fagor documentation
- 25 Keyboard
- 27 General concepts
- 29 P999997 text program management
- 30 Power-up
- 31 Working in T mode with the TC keyboard
- 31 Video off
- 31 Managing the CYCLE START key
- 34 Introduction
- 34 Standard screen of the TC mode
- 36 Description of the special screen of the TC mode
- 38 Selecting a program for simulation or execution
- 39 Axis control
- 39 Work units
- 39 Coordinate preset
- 39 Managing the axis feedrate (F)
- 40 Machine reference (home) search
- 41 Zero offset table
- 42 Jog movement
- 42 Moving an axis to a particular position (coordinate)
- 42 Incremental movement
- 43 Continuous jog
- 44 Path-jog
- 46 Movement with an electronic handwheel
- 47 Feed handwheel
- 48 Path-handwheel
- 49 Tool control
- 50 Tool change
- 51 Variable tool change point
- 52 Tool calibration
- 53 Define the tool in the tool table (level 1)
- 56 Manual tool calibration with/without a probe (level 1)
- 58 Tool calibration with a probe (level 2)
- 60 Probe calibration (level 3)
- 61 Manual tool calibration without stopping the spindle
- 62 Live tool
- 64 Spindle control
- 65 Spindle in rpm
- 67 Spindle in constant surface speed mode
- 69 Spindle orientation
- 71 Controlling the external devices
- 72 ISO management
- 77 Operation editing mode
- 78 Definition of spindle conditions
- 79 Definition of machining conditions
- 81 Cycle level
- 82 Simulating and executing the operation
- 83 Background cycle editing
- 84 Positioning cycle
- 85 Definition of data
- 86 Turning cycle
- 89 Data definition (levels 1 and 2)
- 91 Data definition (levels 3, 4 and 5)
- 93 Basic operation (levels 1 and 2)
- 95 Facing cycle
- 98 Data definition (levels 1 and 2)
- 99 Data definition (levels 3, 4 and 5)
- 101 Basic operation (levels 1 and 2)
- 103 Taper turning cycle
- 104 Definition of data
- 107 Basic operation
- 109 Rounding cycle
- 110 Geometry definition
- 113 Basic operation
- 115 Threading cycle
- 118 Geometry definition
- 124 Standard threads
- 132 Basic operation. Longitudinal threading
- 133 Basic operation. Taper threading
- 134 Basic operation. Face threading
- 135 Basic operation. Thread repair
- 136 Grooving cycle
- 138 Calibration of the grooving tool
- 139 Geometry definition
- 143 Basic operation. Grooving
- 145 Basic operation. Cut off
- 146 Drilling and tapping cycles
- 148 Geometry definition
- 150 Drilling cycle. Basic operation
- 151 Tapping cycle. Basic operation
- 152 Multiple drilling cycle. Basic operation
- 153 Multiple threading cycle. Basic operation
- 154 Multiple slot milling cycle. Basic operation
- 155 Profiling cycle
- 156 Level 1. Profile definition
- 158 Levels 2, 3 and 4. Profile definition
- 159 Level 2. Optimizing of the machining of a profile
- 160 Definition of geometry levels 1 and 2. ZX profile
- 163 Definition of geometry at levels 3 and 4. XC, ZC profiles
- 164 Basic operation at levels 1 and 2. ZX profile
- 165 Basic operation at levels 3 and 4. XC, ZC profiles
- 166 Example. Level
- 167 Examples. Level
- 177 Profiling cycles with Y axis
- 177 Graphics: XY and ZY plane selection
- 178 Tool calibration
- 182 Editing blocks in ISO mode
- 183 Programming assistance
- 183 Zero offsets and presets
- 183 Work zones
- 183 Insert labels and repetitions from label to label
- 184 Mirror image
- 184 Scaling factor
- 186 List of saved programs
- 187 See the contents of a program
- 187 Seeing one of the operations in detail
- 188 Edit a new part-program
- 189 Saving an ISO block or a cycle
- 190 Delete a new part program
- 191 Copying a part-program into another one
- 192 Modify a part-program
- 192 Delete an operation
- 192 Add or insert a new operation
- 193 Move an operation to another position
- 194 Modify an existing operation
- 195 Managing programs using the explorer
- 198 Simulating or executing an operation or cycle
- 199 Simulating or executing a part-program
- 199 Simulating or executing a portion of a part-program
- 200 Simulating or executing an operation that has been saved
- 201 Execution mode
- 202 Tool inspection
- 203 Graphic representation