AS NEEDED MAINTENANCE. Stratasys FORTUS 900MC
Add to My manuals72 Pages
Stratasys FORTUS 900MC is an innovative, high-performance 3D printer designed to meet the demands of various industries. It offers exceptional precision, reliability, and versatility, making it an ideal choice for producing prototypes, concept models, and functional parts. With its advanced FDM technology and compatibility with engineering-grade materials, the FORTUS 900MC empowers users to create durable, accurate, and complex 3D printed objects.
advertisement
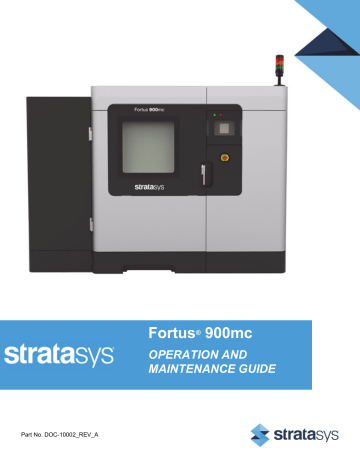
AS NEEDED MAINTENANCE
CLEANING THE LIQUEFIER TIPS
The system automatically cleans the tips before and during each part build - using the tip cleaning assembly.
However, occasionally, material may build up on the tips that cannot be removed during the auto-cleaning process. Remove excess material manually using a brass, wooden-handled brush (included in the Startup Kit).
CLEANING THE CABINET
Use a soft cloth moistened with mild soap and water to wipe down the outside of the cabinet. Do not use abrasive or high alkaline cleaners on the system. Vacuum all air vents of dirt and debris that would block airflow through the system.
CLEANING PLASTIC COMPONENTS
Clean the oven door and all plastic components on the outside of the system using mild soap and water.
Commercially available products made for cleaning plastic are also acceptable. Do not use abrasive or high alkaline cleaners on the system. Avoid streaks by rinsing with clear water and then drying with a soft cloth.
In addition to the above noted user maintenance tasks, Stratasys recommends all 900mc systems go through a
1 year PM which addresses lubing and the replacement of wear components and filters, which if not replaced, may contribute to diminished component life. In addition, Stratasys recommends a 6 month PM on systems with serial numbers lower than L0140 AND serial numbers listed L0148 through L0151. The 6 month PM primarily involves lubing of all the moving XYZ axis components.
Please contact Stratasys Customer Support if you are interested in receiving a quote for these services or would like additional information. Failure to adhere to this schedule could lead to reduced life of XYZ components such as lead screws and bearings.
CLEANING THE OVEN DOOR, CAMERA/LAMP, AND TOUCHSCREEN DISPLAY
Commercial glass cleaner can be used on the outer surfaces of the oven door and touchscreen bezel because these items have an anti-scratch coating applied.
Note: Never apply a glass cleaning product to the high temperature glass inside the oven because discoloration may occur at elevated temperatures.
Use only a 50-50 mix of isopropyl alcohol and water to clean the high temperature glass windows of the oven door and camera/lamp assemblies.
Use the following guidelines for cleaning the polycarbonate oven door window insert:
• Do not use abrasives or high alkaline products.
• Do not apply cleaners in direct sunlight or at elevated temperatures.
• Do not use scrapers, squeegees, razor blades or other sharp instruments.
• Do not clean with gasoline, acetone or carbon tetrachloride.
• If scratching should occur, minor abrasions can be removed or minimized using a mild automotive polish.
• The glass on the oven door should only be cleaned with isopropyl alcohol. This prevents the glass from producing a film at high temperatures.
51
SUPPLEMENTAL INFORMATION
ELECTRICAL PANEL COMPONENTS (GEN 2 ONLY,
SERIAL NUMBER > 1030)
The electrical panel is located in the back of the system and accessed from behind two hinged access panels.
These can be either opened or removed by a service representative when they are servicing the system.
Virtually all system communication, interface and control takes place or originates from within electrical panel of the Fortus 900mc system. The electrical panel is not intended for customer/user access because potentially deadly electrical power sources are present. Safe electrical practices must be followed when performing service within this enclosure.
Electrical panel components include the following:
• Motor Amplifiers
• 120V DC Power Supply (3X)
• Computer
• AC Filters
• 24V DC Power Supply
• AC Distribution Bus
• UPS
• Oven Thermal Breaker
• Heater Solid State Relay
Amp, Programmed X
Amp, Programmed Y Amp, Programmed Z
Power Supply
(24V, 250W)
Filter, Motor EMI
CCA, MAC
Board
CCA, Auxiliary
120VDC P.S.
Din Rail Assy.
SOK SATA
Computer Assy.
Filter, AC Line
Line Reactor
UPS
CCA Differential
Line Filter
SSR, Oven
Heaters
Block,
Heater
Terminal
Power
Supply
LED
52
Breaker, Thermal
Oven
Din Rail Detailed View (Gen II only, Serial Number > 1030)
Y MOTOR
Z MOTOR
T3
SAFETY RELAY
SAFETY
CONTACTOR
SAFETY
CONTACTOR
MOTOR
CONTROL
OVEN
BLOWER
EX FAN
FANS EB
HEATER
MAC MN
T2
MAIN
MAC LINE
T1
OVEN
LIGHTS
53
AUXILIARY PANEL (GEN 2 ONLY, SERIAL NUMBER >
1030)
The auxiliary panel is located on the right side of the system and accessed from the access panels. With the
MAC board interface and control, the auxiliary panel provides two primary functions; vacuum generation and air drying. These functions are performed using an external compressed air source (non-lubricated) at 90-120 psi).
Because of the large build area offered by the Fortus 900mc, two separate vacuum zones on the vacuum platen are provided. The zones are identified as the “inner” and “outer” and permit use of either large or small build sheets. Dried air is supplied to the filament feed path of the system making sure that material delivered to the head does not become contaminated by moisture that could cause part quality issues.
Auxiliary Panel Components:
• Relief Valve
• Solenoid Air Valve
• Input Regulator and Filter
• Coalescing Water and Oil Filter
• Input Manifold and Dual Pressure Sensor
• Vacuum Generators
• Air Dryer
• Dry Air Filter
• Output Manifold and Gauges
Dry Air Filter
Solenoid Air Valve
(on reverse side of panel)
Vacuum Generators
Coalescing Water and Oil Filter
Pressure Regulator and Filter
Output
Manifold,
Gauges and
Airflow
Orifice
Air Dryer
54
Input Manifold and
Dual Pressure Sensor
advertisement
Key Features
- Advanced FDM Technology for High Precision and Detail
- Wide Range of Engineering-Grade Materials for Diverse Applications
- Large Build Volume for Large-Scale Projects
- Heated Build Chamber for Dimensional Stability
- Intuitive Control Panel for Ease of Use
- Connectivity Options for Remote Monitoring and Control
- Integrated Camera for Remote Build Monitoring
Related manuals
Frequently Answers and Questions
What is the maximum build volume of the FORTUS 900MC?
What materials are compatible with the FORTUS 900MC?
Does the FORTUS 900MC have a heated build chamber?
advertisement
Table of contents
- 7 ABOUT THIS GUIDE
- 7 FORTUS 900MC PRINTER
- 7 PRINTER COMPONENTS
- 7 Access Doors and Panels
- 8 Front of System
- 9 Top of System
- 11 Oven Components
- 14 Canister Bays
- 15 Rear of System
- 17 Model Tag
- 17 Printer Highlights
- 18 Available Materials
- 18 Minimum Clearances
- 19 AC POWER DISCONNECTION
- 19 Lockout Tagout
- 21 OPERATING ENVIRONMENT
- 22 TOOLS
- 22 Start-Up Kit Contents
- 23 SAFETY INFORMATION
- 23 HAZARD TYPES
- 23 SAFETY SYMBOLS
- 25 SAFETY PRECAUTIONS
- 25 Gantry
- 25 Z Stage
- 25 GUARD DOOR INTERLOCKS
- 26 STABILITY WEDGE BLOCKS
- 27 GENERAL SAFETY PRACTICES
- 28 BASIC USER OPERATIONS
- 29 POWERING ON THE SYSTEM
- 31 Queue Window
- 32 Tip Offset Menu
- 32 Part Placement Menu
- 33 System Default Values
- 34 Building Screen
- 35 LOADING/UNLOADING MATERIAL
- 35 Loading Material to the Liquefier Tips
- 36 Unloading Material from the Liquefier Tips
- 37 CHANGING TIPS OR MATERIAL TYPE
- 39 AUTOMATIC CALIBRATIONS
- 39 Start Auto Z Zero Calibration
- 39 Start Auto Tip Calibration
- 40 Adjust XYZ Calibration Offsets
- 42 AutoHome XYZ
- 43 BASIC JOB BUILD TASKS
- 43 Before a Build
- 44 Select a Job to Build
- 45 Build Job Warnings
- 47 Working with the Job Queues
- 47 Pausing or Stopping a Job
- 49 After a Job Build
- 51 USER MAINTENANCE
- 52 DAILY MAINTENANCE
- 52 Clean the Platen
- 53 Empty the Purge Bucket
- 54 WEEKLY MAINTENANCE
- 54 Vacuum the Build Envelope
- 54 Clean/Inspect Tip Wipe Assembly
- 56 QUARTERLY MAINTENANCE
- 56 Clean the Tip Sensor Plunger
- 57 AS NEEDED MAINTENANCE
- 57 Cleaning The Liquefier Tips
- 57 Cleaning the Cabinet
- 57 Cleaning Plastic Components
- 57 Cleaning the Oven Door, Camera/Lamp, and Touchscreen Display
- 61 CONNECTION TO ELECTRICAL SUPPLY
- 63 ELECTRICAL DIAGRAMS
- 63 Ladder Diagram (Gen 2 only, Serial Number > 1030)
- 67 E-Stop Circuit (Gen 2 only, Serial Number > 1030)
- 68 Safety Interlock Circuit (Gen 2 only, Serial Number > 1030)
- 69 Safety Interlock Summary (Gen 2 only, Serial Number > 1030)
- 70 900mc Electrical (Gen 2 only, Serial Number > 1030)