Chapter 2 – Network Design. ABB POWER LEADER PMCS Network Architecture
Add to My manuals80 Pages
advertisement
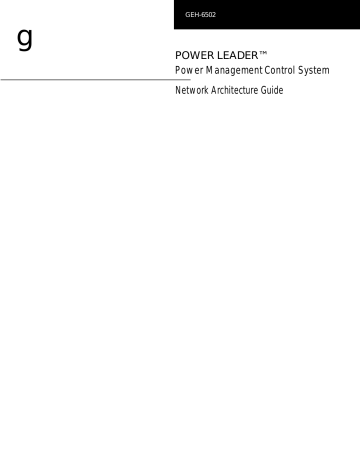
Power Management Control System
Chapter 2 – Network Design
Chapter 2 – Network Design
This section describes how to design a Power
Management Control System network on paper so that actual construction and configuration of the network will proceed smoothly.
You need two things for this exercise: a complete list of the IEDs to be networked and a diagram or map of where the IEDs will be located, preferably with realistic distances noted so that wiring runs may be kept within the appropriate limits.
Using the list of IEDs to be networked, refer to Table 1 and note which communications protocols are required
(commnet or Modbus). For Modbus IEDs, note the communications speed at which each IED operates. For
IEDs supporting both protocols, you will need to decide which protocol will be used. Generally, it is preferable to use Modbus rather than commnet unless the Modbus network is at or near capacity for physical IEDs.
When the list of IEDs and the floor plan are in hand, proceed to Section 2–1 for network design rules.
9
Power Management Control System
Chapter 2 – Network Design
2–1 Modbus Rules
The most basic network configuration for PMCS assumes that the software is running on a host PC supporting one or more RS-485 networks on the Modbus protocol. (See
Figure 1 for an example of this configuration.)
Table 2 explains the configuration rules for PMCS networks based on the Modbus platform. Commnet IEDs may be integrated through the Modbus Concentrator (see
Table 4 for commnet wiring rules).
Host PC is based on:
Modbus
Follow these rules for the host…
1. The host PC can support up to 256 independent
Modbus networks. The actual number is determined by the communication cards installed in the host PC
(see below).
2. The Modbus networks are connected to the host PC via an eight-port RS-485 communications card.
An option for more limited systems is an RS-
232/RS-485 converter, which permits a single RS-
485 network.
3. The host PC must be located at one end of the
Modbus network(s).
And these rules for the attached Modbus network(s)…
1. Each Modbus network supports up to 31 physical Modbus IEDs and up to 247 Modbus addresses. This is possible because commnet IEDs attached to Modbus Concentrators occupy
Modbus addresses but do not create an electrical drain on the RS-
485 network and thus are not counted as physical Modbus IEDs.
2. Each Modbus network must be properly terminated at each end of the network. See Section 2–4.
3. Maximum cable length of each Modbus network is 4000 feet. (See notes on using repeaters to increase this range, Section 2–4. Also, see the note regarding substation installation in Chapter 3.)
4. All Modbus IEDs attached to a single RS-485 network must communicate at the same baud rate. (See Table 1 for Modbus
IEDs’ communication speeds.)
5. RS-485 cable shields must be properly grounded. For maximum protection against surge and EMI damage, each IED on the network should have an isolated ground connection. See Section
2–4, Modbus rule 4, for an example of proper RS-485 wiring and grounding. Also, see the note regarding substation installation in
Chapter 3.
Table 2. Host PC configuration rules.
3
The following RS-485 interface card is recommended for providing the RS-485 connection at the host PC. If any other serial card is used, PMCS requires that the communications driver be compatible with the MS Windows serial communications protocol. Please refer to Section 3–1 for information on the special termination requirements of the RS-485 card.
Manufacturer
Connect Tech, Inc.
Description
Quantity/8 ports
Part, Order Number
Intellicon-Flex8 RS-485 card 1 I4808064XXNC
Intellicon/DFLEX SLIM
8 Port, DB9 I/O Box
4
1
SIMMS
IOB08DB9
4
The following RS-232/RS-485 converter is recommended for providing a single RS-485 connection at the host PC.
Manufacturer Description Part, Order Number
Multilin RS-485/RS-232 Converter F485120
When using the above RS-232/RS-485 converter, remember that the converter has DIP switches inside that determine its baud rate. Switch group 3 should be set according to the baud rate at which the converter is to be used. Refer to the converter’s documentation for further information.
10
Power Management Control System
Chapter 2 – Network Design
2–2 Ethernet Configuration Rules
It is also possible to run the PMCS on a host PC operating on an Ethernet network. If PMCS is running on an
Ethernet-based PC, an Ethernet Gateway is required to communicate with the attached Modbus network(s). (See
Figure 2 for an example of this configuration.)
Recently, IEDs with built-in Ethernet support have begun to become available; PMCS is also capable of supporting these devices. Examples of such devices are the EPM 7700 meter and EPM 9450Q / 9650Q meters. These devices reside on the Ethernet network at the same level as the
Ethernet Gateway.
Table 3 explains the configuration rules for PMCS networks based on the Ethernet platform. Commnet IEDs may be integrated through the Modbus Concentrator.
(See Table 4 for commnet wiring rules.)
EPM 7700 devices require a separate network configuration beyond connecting the devices to the
Ethernet LAN. Please refer to the following PMCS technical documentation for complete network configuration rules and guidelines:
GEH-6514, PMCS Read-This-Book-First. Refer to the section titled “Configuring the EPM 7700 Device Network.”
DEH-40035, GE 7700 Gateway User’s Guide. Refer to the section titled “EPM 7700 Network Configuration.”
EPM9450Q and EPM9650Q devices require separate network configuration beyond connecting the devices to the Ethernet LAN. Refer to the instruction manuals of these devices and to the sections titled “Internal Network
Option.” Also refer to DEH-6510, DDE Server User’s Guide.
Refer to the sections describing the use and configuration of the Modbus TCP Server.
11
Power Management Control System
Chapter 2 – Network Design
Host PC is based on: Follow these rules for the host…
And these rules for the Modbus networks attached to the
Ethernet Gateways…
Ethernet 1. Ethernet Gateway(s) must be used to communicate with non-Ethernet IEDs.
Ethernet-capable IEDs may be installed directly on the Ethernet network at the same level as the Ethernet Gateway(s).
2. The host PC supports up to 64 Ethernet
Gateways.
3. Each Ethernet Gateway supports up to four independent Modbus networks.
The EPM 9450Q /9650Q devices will support one Modbus network.
4. The actual number of IEDs supported by the host varies from system to system, depending on the variety of IEDs used and the number of PMCS data tags required by the IEDs. See GEH-6509,
PMCS DDE Interface Guide,
for details.
5. Ethernet networks should conform to the design guidelines described in
Section 2-3.
1. Each Modbus network supports up to 31 physical
Modbus IEDs and up to 247 Modbus addresses. This is possible because commnet IEDs attached to
Modbus Concentrators occupy Modbus addresses but are not seen as physical Modbus IEDs.
2. Each Modbus network must be properly terminated at each end of the network. See Section 2–4.
3. The Ethernet Gateway must be located at one end of the Modbus network(s).
4. Maximum cable length of each Modbus network is
4000 feet. (See notes on using repeaters to increase this range, Section 2–4. Also, see the note regarding substation installation in Chapter 3.)
5. All Modbus IEDs attached to a single RS-485 network must communicate at the same baud rate.
(See Table 1 for Modbus IEDs’ communication speeds.)
6. RS-485 cable shields must be properly grounded. For maximum protection against surge and EMI damage, each IED on the network should have an isolated ground connection. See Section 2–4,
Modbus rule 4, for an example of proper RS-485 wiring and grounding. Also, see the note regarding substation installation in Chapter 3.
Table 3. Ethernet configuration rules2–3 Ethernet
Network Considerations
This section describes some of the specifications which must be considered when designing an Ethernet network to be used with PMCS.
Note: These specifications are guidelines only and should not be used for actual network design. Consult with a qualified LAN engineer for design requirements that meet your specific installation. The complete specifications are listed in IEEE 802.3 Ethernet. In addition, the National
Electrical Code (NEC) and all applicable local codes must be followed for installing wiring.
Ethernet supports four physical media: 10Base-2
(thinnet), 10Base-5 (thicknet), 10Base-T (twisted pair), and 10Base-FL (fiber). 10Base-T is most common.
12
Power Management Control System
Chapter 2 – Network Design
NOTE for EPM 7700 and 9450Q and 9650Q: The EPM
7700 with Xpress card directly uses either of two types of
Ethernet physical media that must be specified when ordering the meter, 10Base-T, or 10Base-FL. EPM 9450Q and EPM 9650Q must be ordered with 10 Base-T Ethernet
Option. The meters operate in a 10 Mbps system.
A 10Base-T LAN can have a maximum of 1024 devices connected.
Use of repeaters, routers, bridges, gateways, etc.
Repeaters may be used to connect LAN segments and do not determine the boundaries of the LAN. They are used to extend the LAN beyond a single segment. Routers, bridges and gateways may be used to connect the LAN to other LANs or to a WAN.
10Base-T is specified when twisted pair is used and 10Base-
FL is specified where fiber optic cable is used. While media converters are available to allow the use of both twisted pair and fiber optic cable in the same LAN, and can be used to extend the length of the LAN, they are beyond the scope of this discussion.
CAUTION:
The recommended installation practice is to implement optical fiber for connections between buildings to provide electrical isolation. This eliminates harmful ground loops caused by differences in the ground potential between structures.
CAUTION: data communication lines. Data line surge protection is not required for fiber optic connections.
Data line surge protection is recommended for network components such as hubs, computers, or modems connected to IEDs with copper wire, especially installations where the data communication cable is exposed (i.e., not encased in conduit) or runs parallel to power conductors. PMCS IEDs are routinely installed in areas exposed to heavy electromagnetic fields
(EMF), which can induce damaging surges in
10Base-FL specifications and rules
Maximum/Minimum length of segments
For a 10Base-FL LAN, the maximum length of a segment is
2000 meters (6500 ft). The minimum length of any cable is 2.5 Meters or about 8 ft. This minimum length is of particular concern when a device is located in close proximity to the hub.
Maximum number of segments
A 10Base-FL LAN can consist of up to 5 segments using 4 repeaters. However, only three of these segments can have devices connected.
Maximum number of devices
A 10Base-FL LAN can have a maximum of 1024 devices connected.
Use of repeaters, routers, bridges, gateways, etc.
Repeaters may be used to connect segments and do not determine the boundaries of the LAN. They are used to extend the LAN beyond a single segment. Routers, bridges and gateways may be used to connect the LAN to other
LANs or to a WAN.
10Base-T specifications and rules
10Base-T Ethernet uses CAT 3, 4 or 5 twisted pair cable, depending on the installation.
Maximum/Minimum length of segments
For a 10Base-T LAN, the maximum length of a segment is
100 meters (328 ft). The minimum length of any cable is
2.5 Meters or about 8 ft. This minimum length is of particular concern when a device is located in close proximity to the hub.
Maximum number of segments
A 10Base-T LAN can consist of up to 5 segments using 4 repeaters. However, only three of these segments can have devices connected.
Maximum number of devices
13
Power Management Control System
Chapter 2 – Network Design
2–4 Commnet Configuration Rules
POWER LEADER commnet IEDs may be integrated into a
PMCS network through a special Modbus IED called the
Modbus Concentrator. The rules outlined in Table 4 apply to using commnet IEDs with PMCS, regardless of whether the host PC is operating on an Ethernet or Modbus network. (See Figures 3 and 4 for examples of commnet
IEDs operating on PMCS.)
Rules regarding:
Modbus
Concentrator limitations
Commnet IED configuration rules:
1. Each Modbus Concentrator supports up to eight commnet segments.
2. Each commnet segment supports up to four commnet IEDs.
3. Only one waveform-capturing meter (POWER LEADER Meter) is allowed per commnet segment.
4. POWER LEADER Repeaters and Junction/Outlet Boxes do not count toward the four-IED-per-segment limit.
5. No connections between commnet segments are permitted. Each segment must be wired independently (having no contact with other commnet segments) and connected to the Concentrator at one point only (no loops permitted).
Reference
Figure:
No figure provided
Commnet wiring limitations
1. Maximum cable length of a commnet segment is 1000 feet. Maximum range between commnet IEDs on a segment is 1000 feet (except for repeaters; see below).
2. In no case may a commnet IED be wired more than 1000 feet from the Modbus
Concentrator or a POWER LEADER Repeater.
3. POWER LEADER Repeaters may be used to extend the range of commnet segments. A repeater regenerates the commnet signal to its original strength, allowing it to travel up to another 1000 feet.
4. Long-distance segments may be created by placing multiple repeaters adjacent to one another in a commnet segment. A repeater communicating directly with another repeater may span up to 6000 feet.
5. Maximum allowable cable length of a single commnet segment is 12,000 feet, which may be constructed with any allowable combination of repeaters and IEDs.
6. For ease and economy of wiring, the POWER LEADER Junction/Outlet box may be used to create nodes of commnet IEDs with a common wiring point to be connected to the Modbus concentrator. The POWER LEADER Junction/Outlet
Box allows the interconnection of as many as four shielded, twisted-pair cables to create this common wiring point. For instance, rather than a daisy-chain of wiring in a lineup from one meter or trip unit to the next, up to four IEDs may be wired to the POWER LEADER Junction/Outlet Box, which is then connected to the Modbus Concentrator.
No figure provided
Table 4. Commnet IED configuration rules.
14
Power Management Control System
Chapter 2 – Network Design
2–5 Modbus Wiring Rules – Diagrams
The Modbus network protocol has wiring rules and limits on the number of IEDs that may be attached.
This section describes in greater detail the rules you must follow when designing a Modbus network.
1. Each RS-485 network may support up to 31 Modbus
IEDs. Figure 7 illustrates this rule. (See the
exception below Figure 6.)
Host
WARNING:
Network wiring and grounding rules described herein apply primarily to commercial/industrial installations. Substation installations will exist in the presence of dangerously elevated ground potential relative to points outside of the station grid as well as large electromagnetic induction fields. Additionally, large ground faults can elevate substation ground potentials. Follow local utility bestpractices/safety procedures to prevent
risk of
shock/electrocution to personnel and damage to equipment that could result in a loss of protection and communications.
NOTE:
It is important to take future expandability into consideration when designing a network configuration. This is particularly so when the network is near its maximum number of IEDs or maximum cable length. Adding IEDs to a network after it has been installed may require rewiring the network.
31 RS-485 IEDs maximum;
PMCS Host PC, Ethernet Gateway or MSP always located at one end of Modbus network.
Figure 7. Network illustrating Modbus Rules 1 and 2.
Exception to Rule 1: Some types of IEDs must be wired on dedicated private serial network segments, one IED per serial Modbus line.
2. The host (or Ethernet Gateway) must always be located at one end of any Modbus segment. It may not be located in the center of a Modbus network.
Figure 7 shows the correct placement of the host
(PC or Ethernet Gateway).
3. All Modbus IEDs on a single RS-485 network must communicate at the same baud rate. If IEDs with different communication speeds are connected to the same RS-485 network, the whole segment will
communicate at the speed of the slowest IED. Figure
8 illustrates this rule. (Communication speeds for
supported IEDs are listed in Table 1.)
CAUTION:
Wire-run distances mentioned in the configuration rules assume application above grade or in conduit. For below-grade applications, refer to Section 3–1, Wiring
Requirements.
Regardless of which platform is supporting the RS-485 networks (Ethernet Gateway, RS-485 card, or RS-232/RS-
485 converter), the following rules apply to each individual RS-485 network.
Figure 8. Network illustrating Modbus Rule 3.
4. Each RS-485 network must be properly terminated at both ends of the cable run after the final IED.
(See Section 3–1 for details on termination.) Figure
15
Power Management Control System
Chapter 2 – Network Design
5. Each RS-485 network must have its shield properly
grounded. Figure 9 illustrates proper RS-485 wiring
and grounding.
RS-485 Host
(RS-485 card*, RS232/RS-485 converter,
Multiple Serial Port or Ethernet Gateway RS-485 port)
Network Connections: + Shield
CAUTION:
Improper grounding may create a ground-loop condition and cause communications failures. Make sure you follow the wiring diagram carefully.
To ensure proper grounding, follow this procedure.
Begin by grounding the RS-485 cable shield at the host. Follow the cable to the first IED on the network. Do NOT connect the cable ground to the
IED. Pick up the RS-485 output cable from the IED and attach its ground to the IED’s shield connection or grounding screw. For IEDs with no grounding connectors, connect to earth ground.
Follow the cable to the next IED, and repeat the above procedure. Do not connect the RS-485 shield from the previous IED, but DO connect the RS-485
OUT shield on its way to the next IED.
RS-485
Two wire, twisted, shielded pair cable
RS-485 IED #1
Shield
+
-
RS-485 IED #2
Shield connected at host
120-ohm terminating resistor
* Connect Tech RS-485 cards require a 600-ohm resistor in place of the 120-ohm terminating resistor.
Shield not connected at first IED
RS-485 IN
Shield connected at first IED
RS-485 OUT
Shield not connected at IED
RS-485 IN
EXCEPTION:
The Multilin 565 Feeder
Management Relay does not have isolated communications ports. Do NOT connect the shield at this IED. Instead connect the shield of the incoming RS-485 cable to the shield of the outgoing RS-485 cable, skipping the Multilin 565.
Rules of thumb
: RS-485 cable ground should always be connected at the previous IED, never upon arrival at an IED. All RS-485 IEDs must have either two communications cables attached or one communications cable and a terminating resistor.
Shield
+
-
Shield connected at IED
RS-485 OUT
RS-485 IED #31
Shield not connected at IED
RS-485 IN
Shield
+
-
120-ohm terminating resistor
Figure 9. Network illustrating Modbus Rules 4 and 5.
6. A single RS-485 network may have up to 215 commnet IEDs attached to it via POWER LEADER
Modbus Concentrators. Figure 10 illustrates this
rule.
16
Host
MC
RS-485 IEDs
(31 Max)
Modbus
Concentrator
Commnet IEDs
(up to 32 per Modbus Concentrator,
215 total per RS-485 network)
Power Management Control System
Chapter 2 – Network Design
9. There may be no more than two RS-485 repeaters
between any two RS-485 IEDs. Figure 13 illustrates
this rule.
Rptr Rptr
Correct - Maximum two repeaters between RS-485 IEDs
Rptr Rptr Rptr
Incorrect - more than 2 repeaters between RS-485 IEDs
Figure 13. Network illustrating Modbus Rule 9.
Figure 10. Network illustrating Modbus Rule 6.
7. A single RS-485 network may have no more than
4000 feet of cable (total cable length, not distance
between IEDs). Figure 11 illustrates this rule.
Host
100 ft 200 ft
Total Cable Length < 4000 feet
RS-485 IEDs
(31 Max)
300 ft
1500 ft
300 ft
1500 ft
Figure 11. Network illustrating Modbus Rule 7.
8. RS-485 repeaters may be used to extend the range beyond 4000 feet. A single RS-485 repeater may be used to provide a 4000-foot extension, and each additional repeater in a sequence extends the range
by another 4000 feet. Figure 12 illustrates this rule.
NOTE ON DUAL-PORT RS-485 IEDS:
Several of the Multilin power management IEDs offer two RS-485 ports on the same IED. Do not connect both RS-485 ports to a PMCS network.
The same data are available from both RS-485 ports and will cause conflicts if the PMCS attempts to access both ports simultaneously.
However, the Modbus Monitor’s wiring scheme is slightly different from the Multilin scheme. The dual-port version of the POWER LEADER
Modbus Monitor MUST be connected to two separate RS-485 networks. See Rule 10 for details.
10. Modbus Monitors (dual-port version) may not be wired in any configuration other than the four
shown in Figure 14. Although the Monitor’s RS-485
ports have separate addresses, you may NOT wire the same Modbus network to both ports. A two-port
Modbus Monitor must be wired to two separate
Modbus networks.
NOTE
: For more information on wiring the
POWER LEADER Modbus Monitor, refer to
DEH-027, Modbus Monitor User’s Guide.
Host
100 ft
With 2 Repeaters,
500 ft
Total Cable Length < 8000 feet
700 ft
RS-485
Repeaters
R
4000 ft
R
200 ft
2500 ft
Figure 12. Network illustrating Modbus Rule 8.
17
Power Management Control System
Chapter 2 – Network Design
Example A
Modbus
Segment A
Monitor
#1
Example B
Modbus
Segment A
Modbus
Segment B
Monitor
#1 makes this concern irrelevant for examples A, B, and D, since in Example A you could have either a single- or a dual-port Monitor, while in
Examples B and D you may only use a dual-port monitor(s).
Example C
Modbus
Segment A
Monitor
#1
Example D
Modbus
Segment A
Modbus
Segment B
Monitor
#1
Monitor
#2
Monitor
#2
Figure 14. Valid Modbus Monitor network architectures.
CAUTION:
Any other wiring of the Modbus
Monitor may result in incorrect operation and errors.
CAUTION DUAL PORT MONITOR USERS: Do not connect the Monitor’s two RS-485 ports to the same
Modbus segment.
This will cause communication errors and possibly damage the Monitor.
Example A shows a single Modbus Monitor wired to one
Modbus segment. Example B shows the same monitor in a dual-port version, wired to two different Modbus segments.
Examples C and D illustrate fully loaded Modbus segments. No more than two Monitors are permitted on any Modbus segment.
Example C illustrates a pair of Monitors connected to a single Modbus segment. In this example, the Monitors may be either single port or dual-port versions, provided both are the same version (see note below). Example D shows the same pair of Monitors wired to a second Modbus segment.
CAUTION:
With regard to Example C (two
Monitors on a single RS-485 segment), it is not permissible to mix different models of Monitors on a segment. Monitors #1 and #2 must be of the same model, either both single-port or both dualport.
The nature of the other network architectures
18
2–6 Commnet Wiring Rules – Diagrams
POWER LEADER commnet IEDs may be integrated into
PMCS through the use of the POWER LEADER Modbus
Concentrator, which collects data from commnet IEDs and communicates that data across the RS-485 network.
Each Modbus Concentrator supports up to eight commnet segments. Each commnet segment may accommodate up to four commnet IEDs. The following are the basic rules to ensure proper network operation for POWER LEADER commnet IEDs. Note that these rules apply only to individual commnet segments of a POWER LEADER
Modbus Concentrator, not to the RS-485 network.
1. Each Modbus Concentrator supports up to eight commnet segments. Each commnet segment may support up to four commnet IEDs, only one of which may be a waveform-capturing meter. POWER
LEADER Repeaters and Junction/Outlet Boxes are
not counted as commnet IEDs. Figure 15 illustrates
this rule.
Power Management Control System
Chapter 2 – Network Design degrades and the danger of errors rises to an unacceptable level. The Repeater regenerates a signal to its original strength, allowing it to travel up to another 1000 feet. Thus, each Repeater can add up to 1000 feet of range to the commnet segment.
For example, a segment containing a single
Repeater may have no more than 2000 feet of total cable length. No more than 1000 feet of cable are permitted between the Modbus Concentrator and the first Repeater or between the Repeater and the
last IED on the segment. Figure 17 illustrates this
rule.
CAUTION:
In no case may there be more than
1000 feet of cable between any two commnet
IEDs other than Repeaters. At ranges over 1000 feet, commnet signals become degraded and communication errors may result.
Modbus
Concentrator
4 commnet IEDs/segment max
Modbus
Concentrator
400 ft
600 ft
R
200 ft
600 ft
Max length of a commnet segment with one Repeater < 2000 feet
200 ft
Figure 17. Network illustrating commnet Rule 3.
4. Long-distance cable runs may be built by placing two
Repeaters adjacent to one another in the segment. A pair of adjacent Repeaters has a range of up to 6000
feet of cable. Figure 18 illustrates this rule.
Figure 15. Network illustrating commnet Rule 1.
2. A commnet segment may have no more than 1000 feet of cable between the Modbus Concentrator and the final IED on a segment. (Repeaters may be used
to extend this range; see Rule 3.) Figure 16
illustrates this rule.
Modbus
Concentrator
300 ft
200 ft
200 ft
200 ft
Max length of a commnet segment < 1000 feet
Figure 16. Network illustrating commnet Rule 2.
3. The maximum communication range of commnet
IEDs (including the Modbus Concentrator’s commnet ports) is 1000 feet, after which its signal
1000 ft
Modbus
Concentrator
400 ft
600 ft
R
6000 ft
R
600 ft
200 ft
Max length of a commnet segment with two Repeaters < 8000 feet
200 ft
R R
R
6000 ft
4000 ft
1000 ft
Ma x len gth of a com m ne t segm ent with th ree R e pea ter s < 12 000 fe et
(note: only o ne othe r IE D m ay be use d o n a co m m n et segm ent w ith th ree rep eaters)
Figure 18. Network illustrating commnet Rule 4.
5. The maximum allowable cable length of a single commnet segment is 12,000 feet. This may be
19
Power Management Control System
Chapter 2 – Network Design achieved with any allowable combination of
Repeaters and IEDs.
6. For ease of wiring, the POWER LEADER
Junction/Outlet Box may be used to create nodes of commnet IEDs with a common wiring point to be connected to the Modbus concentrator. The
POWER LEADER Junction/Outlet Box allows the interconnection of as many as four shielded, twistedpair cables to create this common wiring point. This can be of great help in economizing on wiring and offering greater flexibility in network design. For instance, rather than a daisy-chain of the wiring in a lineup from one meter or trip unit to the next, up to four IEDs may be wired to the POWER LEADER
Junction Box, which is then connected to the
Modbus Concentrator.
Examples of the use of a POWER LEADER Junction
Box with the Modbus Concentrator are provided in
Figure 19 and Figure 20. Junction Boxes are not
counted as IEDs for purposes of the four IED per
commnet segment limit. Figure 19 is an example of
a Junction Box used to create a node connecting four commnet IEDs to a Modbus Concentrator.
Figure 20 is an example of a Junction Box with
Repeaters, observing the four IED per segment limit
(the two Repeaters and the Junction Box do not count as IEDs).
commnet
IED
CAUTION:
The four-IED-per-segment limit must be observed at all times. Although the POWER
LEADER Junction Box has terminals to accept up to 12 commnet lines, do NOT connect more than four commnet IEDs to a single Junction
Box or Modbus Concentrator commnet segment.
to
Modbus
Concentrator
Junction
Box commnet
IED commnet
IED commnet
IED
Figure 19. Network illustrating commnet Rule 6.
to
Modbus
Concentrator commnet
IED
Junction
Box
Long-range commnet segment
POWER
LEADER
Repeater
POW ER
LEADER
Repeater commnet
IED commnet
IED commnet
IED
Figure 20. Network illustrating commnet Rule 6.
20
Power Management Control System
Chapter 2 – Network Design
2–7 Performance Recommendations
Although a PMCS network will function as long as all the rules in the previous section are followed, you can enhance performance by considering the following recommendations for Modbus, commnet.
The Ideal Network
Theoretically, a single Modbus IED or 40 commnet IEDs distributed across five Modbus Concentrators (one IED per commnet segment) yields maximum performance.
Naturally, in the real world few networks will fall into this precise configuration. To extract maximum performance from the PMCS, follow the performance recommendations below.
Modbus performance recommendations
1.
Use multiple RS-485 networks if possible, depending on the RS-485 connection at the host. If using an eight-port RS-485 card or an Ethernet Gateway (four ports) for connection to the network, you can improve performance by using the full number of ports available, rather than burdening a single RS-485 port.
Distributing the IEDs across all available RS-485 ports permits the communications load to be distributed rather than asking a single network to carry the full load.
2.
Divide the IED loads evenly when distributing IEDs across multiple RS-485 networks.
3.
Pay careful attention to Modbus Rule 2, regarding the communication speeds of IEDs on a given network.
Although a network will function with mixed IEDs, its communication speed will be dragged down to the lowest common denominator. Thus, a single 2400baud IED forces the entire network to communicate at
2400 baud, regardless of the presence of any 19.2kbaud IEDs.
Commnet performance recommendations
1.
Modbus is preferred over commnet where either protocol is available. This is the case for the POWER
LEADER Electronic Power Meter and the POWER
LEADER MDP Overcurrent Relay. Each of these IEDs offers a Modbus communications option.
2.
Minimize the number of commnet IEDs per segment.
The Modbus Concentrator is a polling IED, meaning that it queries each commnet segment continuously and in order asking for information. It then stores the information until it is asked by the PMCS to transmit its data to the host. If the number of commnet IEDs is unevenly distributed, the Concentrator takes longer than necessary to poll each segment.
3.
Keep data-intensity in mind when connecting more than eight commnet IEDs to a single Modbus
Concentrator. If it is necessary to connect more than eight commnet IEDs to a single Modbus Concentrator, one or more segments will be supporting multiple
IEDs. Keep the following list in mind when selecting which IEDs to double up on the same commnet segment. The best choices for doubling up are listed first.
1. Spectra MicroVersaTrip trip unit
2. Enhanced MicroVersaTrip-C and -D trip units
3. POWER LEADER MDP Overcurrent Relay
4. Spectra Electronic Control Module
5. POWER LEADER Electronic Power Meter
6. POWER LEADER Meter
IEDs at the top of the list are less data-intensive and easier for the Concentrator to poll. IEDs at the bottom of the list are very data-intensive and, if possible, should be given their own commnet segment. In other words, if you must put multiple IEDs on a segment, it is preferable to put low-demand IEDs together on a segment and try to keep high-demand IEDs on their own segments. Try to distribute the high-demand
IEDs across the available segments, keeping the number of high-demand IEDs per segment evenly distributed.
2–8 Addressing the IEDs
Each IED attached to a PMCS network must have a unique address. Prior to installing any wiring, you should plan the addresses for the IEDs to avoid any conflicts. Keep in mind these important points when assigning network addresses.
• Keep a table of IED names and addresses to avoid conflicts and to help with host configuration. Table 5 summarizes Modbus addressing considerations, based on the following rules.
- Modbus Concentrator addresses must be in the range of 1 to 32.
- Modbus-native IEDs other than the Concentrator may occupy any address from 1 to 247.
- Commnet IEDs must have Modbus-equivalent addresses in the range of 33 to 247.
- The host PC does not require an address due to the master-slave organization of the PMCS.
21
Power Management Control System
Chapter 2 – Network Design
Modbus
Address
NOTE:
Per the EIA485 standard, each RS-485 network supports up to 32 “drops” or electrical drains on the network. However, the Ethernet
Gateway or RS-485 interface card counts as one drop. Thus, only 31 other IEDs may be attached to each RS-485 network, even though 32 Modbus addresses are available for use. Also, unlike commnet’s POWER LEADER Repeaters, RS-485 repeaters are counted as IEDs because although they have no Modbus address, they do act as a drop on the network.
Appropriate Usage/Supported IEDs
0 • Broadcast (not available to user)
1 – 32 • Modbus Concentrators must have addresses in this range
• Other Modbus native IEDs may also have addresses in this range
33 – 247 • Modbus native IEDs may have addresses in this range
• Commnet IEDs must have addresses in this range
Table 5. Modbus address range appropriate usage.
• Commnet IEDs are preprogrammed with a factory-set address. You must change this address immediately upon installation of the IED. Refer to the IED’s user manual for instructions on assigning an address.
• Because the commnet network accepts a different range of addresses than the Modbus network, commnet addresses must be mapped to corresponding Modbus addresses. The formula for this mapping is: desired Modbus address + 267 = commnet address to set at IED
. For example, to set a commnet
IED to Modbus address 33, the commnet address set at the IED must be 300. Table 6 illustrates address mapping.
For Modbus Address:
33
34
35
...
246
247
Set commnet IED Address to:
300
301
302
...
513
514
Table 6. Modbus-to-commnet address mapping.
- You may want to block commnet address assignments by lineup and/or Modbus Concentrator segment. For example, start with 40 for the first lineup attached to one Modbus Concentrator, 50 for the second lineup attached, and so on. Addresses must be in the range
33 to 247. The example presented in Figure 18 demonstrates this.
- Increment the individual IEDs in each lineup by one.
For example, if the first IED in a lineup is Modbus address 101, the second IED should be 102, the third
IED should be 103, etc.
• Addresses may be entered or changed at any time that control power is present.
Figure 21 illustrates a sample network with IED addresses;
Table 7 provides details of the IEDs shown in Figure 21.
22
Power Management Control System
Chapter 2 – Network Design
Figure 21. Sample network with IED addresses.
23
Power Management Control System
Chapter 2 – Network Design
Equipment
Lineup 1
POWER/VAC Medium-Voltage
Switchgear
Lineup 2
8000-Line Motor Control Center
Lineup 3
AKD-8 Low-Voltage Switchgear
Attached
IEDs
Modbus Concentrator 1
Segment 1
POWER LEADER Electronic Power Meter
MDP Overcurrent Relay with commnet
MDP Overcurrent Relay with commnet
MDP Overcurrent Relay with commnet
Segment 2
POWER LEADER Electronic Power Meter
POWER LEADER Electronic Power Meter
Segment 3
POWER LEADER Electronic Power Meter
POWER LEADER Electronic Power Meter
Segment 4
MDP Overcurrent Relay with commnet
MDP Overcurrent Relay with commnet
EPM 7700 Electronic Power Meter
Multilin 269 Plus Motor Relay
Modbus Concentrator 2
Segment 1
- Spectra Electronic Control Module
Segment 2 -
Spectra Electronic Control Module
Segment 3 -
Spectra Electronic Control Module
Segment 4 -
Spectra Electronic Control Module
EPM 7700 Electronic Power Meter using IP address =
3.46.9.102
Modbus Concentrator 3
Segment 1
- POWER LEADER Meter
Segment 2
- Enhanced MicroVersaTrip trip unit
Segment 3
- POWER LEADER Meter
Segment 4 -
Enhanced MicroVersaTrip trip unit
Lineup 4
Medium-Voltage Motor Control Center
Lineup 5
Substation
GE Fanuc Programmable Logic Controller 90/30
Multilin 565 Feeder Management Relay
EPM 5300P
EPM 5200P
EPM 9650Q
EPM 7300
EPM 7330
EPM 7330
Table 7. IED-addressing scheme for Figure 21.
Commnet
Address
—
302
303
304
305
307
308
312
313
317
318
—
—
—
332
337
352
357 n/a
—
—
—
—
—
—
—
422
427
432
437
442
447
452
—
—
Modbus
Address
001
035
036
037
038
040
041
045
046
050
051
052
060
002
065
070
085
090 n/a
200
205
210
215
220
225
003
155
160
165
170
175
180
185
004
005
24
Power Management Control System
Chapter 2 – Network Design
2–9 Multiple RS-485 Networks – Addressing
PMCS supports up to 256 independent Modbus networks.
Regardless of how many RS-485 networks are connected, the addressing concepts regarding multiple RS-485 networks remain the same. Each RS-485 network is addressed independently of the others. Thus, Network 1 may have an IED with Modbus address 20, and Network 2 may have an IED with Modbus address 20 without conflict.
The PMCS will be aware that they are different IEDs, much as the postal system delivering mail realizes that 17
Mulberry Lane in Town A is a different address than 17
Mulberry Lane in Town B.
2–10 System Expansion
Whenever new IEDs are added to the network, be sure to observe these points:
• Follow the proper installation procedures.
• Ensure that the system configuration rules have been followed.
• All new IEDs are shipped with the same default address. To avoid conflicts, change the address of each new IED immediately upon installation to an unoccupied address in the PMCS networks.
2–11 Case Studies
Five case studies are provided as examples of how to design a network based on PMCS. In each case, a fictitious company called GHO Corp. is installing a power management system based on PMCS.
In Case One, GHO Corp. has only a few Modbus RTUbased IEDs that it would like to network to the PMCS software for remote control and viewing of power consumption and alarms.
In Case Two, GHO Corp. wishes to expand the Modbus network it developed in Case One by adding some commnet IEDs to the network.
In Case Three, GHO Corp. already has an existing network based on Ethernet and would now like to integrate a power management system with this network.
GHO Corp. still has only a few Modbus RTU-based IEDs that it would like to network to the PMCS for remote control and viewing of power consumption and alarms.
Now, however, it wants the host to be based on Ethernet rather than Modbus, which requires the use of an
Ethernet Gateway.
In Case Four, GHO Corp. wishes to install a PMCS power management system using both Modbus- and commnetbased IEDs, with the host based on Ethernet.
Case Five demonstrates the use of dual-port RS-485 IEDs in a Modbus network, showing the differences between the
Multilin dual-port IEDs and the POWER LEADER
Modbus Monitor, which also provides two RS-485 ports.
Case Study One
GHO Corp. has assigned its plant engineer, Bill, the task of designing and installing a simple power management system. GHO Corp. wishes to use PMCS to monitor and control several Modbus power management IEDs.
Bill’s first task is an easy one. He must choose a platform on which the PMCS host will reside. Using the flowchart in
Section 1-1, he makes his decision. There is no existing
Ethernet network in his facility, nor are there any plans for one. Bill chooses Modbus as his basic platform for the
PMCS.
Next, Bill makes a list of the IEDs that GHO Corp. wants to include on their PMCS network:
• One PLC 90/30 Programmable Logic Controller for process control
• Three EPM 3720 Meters for monitoring power
• One Multilin 269+ Motor Relay for motor protection
• One Multilin 565 Feeder Management Relay for feeder protection
He checks the list of communications protocols in Table 1 and notes that all of the IEDs communicate on Modbus; because no commnet IEDs are being used, no Modbus
Concentrators are needed. The Modbus IEDs communicate at different baud rates, though, and Bill makes a note that they should be placed on separate RS-
485 networks for improved performance.
Bill now turns to his floor layout to see just where the wiring could be run and how many feet of cable will be needed. He maps where his IEDs must be located and where the host PC will sit. He measures the cable runs required to connect the IEDs to the host PC, keeping in mind that the wiring rules require him to daisy-chain the
IEDs on each RS-485 network one after another. His floor
25
Power Management Control System
Chapter 2 – Network Design
Bill's Office
300'
Terminating
Resistors
Lathe Area
EPM 3720
Electronic Power Meter
350'
RS485 networks terminated at host PC
Bill's Office
Network 4 - 19.2 kbaud
100'
Lathe Area
EPM 3720
Electronic Power Meter
350'
Milling Area
Multilin 565
Feeder Management Relay
Main power feed
350'
Milling Area
EPM 3720
Electronic Power Meter
Network 3 - 19.2 kbaud
Multilin 565
Feeder Management Relay at main power feed
600'
EPM 3720
Electronic Power Meter
Machining Area
550'
Multilin 269+
Motor Relay
Assembly Line Area
200'
Machining Area
EPM 3720
Electronic Power Meter
PLC 90/30
Programmable Logic Controller
550'
GHO Corp Machine Shop network wiring diagram
Figure 22. Floor layout for Case One.
600'
Multilin 269+
Motor Relay
Terminating
Resistors
Assembly Line Area
EPM 3720
Electronic Power Meter
PLC 90/30
Programmable Logic Controller
GHO Corp Machine Shop network wiring diagram
550'
Figure 23. Redesigned layout for Case One.
Bill’s calculates his total cable length at 2300 feet, well short of the 4000-foot limit.
Next, Bill checks Table 2 for the Modbus wiring rules.
Proper termination is required at each end of the network, and is provided at the RS-485 card by attaching jumpers to the correct pins (see RS-485 card user manual). The appropriate terminating resistors must be used at the opposite end of each RS-485 network, per Section 2–4, rule
3.
His cable length is well under the 4000-foot limit, so no repeaters will be needed.
Because he has only six IEDs to connect, only one RS-485 network is required, and thus an RS-232/RS-485 converter would do the job. However, he considers the performance recommendations given in Section 2-6 and, remembering his earlier note about the different baud rates of his
Modbus IEDs, he decides to distribute the IEDs across four ports of an RS-485 network card, so that he can place IEDs with matching baud rates on the same RS-485 network.
The system redesigned for optimum performance is shown
Confident that his new design will provide maximum performance, and with his wiring requirements and limits met, Bill moves on to select Modbus addresses for the IEDs.
He checks Section 2-7 and sees that he can assign his IEDs any Modbus address between 1 and 247. He selects addresses and records them for future reference. The
address chart is shown in Table 8.
IED Type
PLC 90/30
EPM 3720
EPM 3720
EPM 3720
Multilin 269+
Multilin 565
Physical Location
Assembly line
Milling
Lathe area
Machining
Assembly line
Power intake area
Modbus Address
01
02
03
04
05
06
Table 8. IED Addresses for Case One.
Chapter 3 provides Bill with physical wiring requirements and rules. He finds that he’ll have to use Belden 3074F cable, readily available. He also locates the correct terminating resistors at both ends of each RS-485 network.
He installs the IEDs according to the instructions in the user manual for each IED. He then makes connections to the RS-485 communications cable in daisy-chain fashion, one IED to the next, terminated at each end of each RS-
485 network, double-checking his wiring against the example provided in Section 2–4.
He must also bear in mind proper shield-grounding considerations – each RS-485 IED grounded at only one
26
Power Management Control System
Chapter 2 – Network Design point and no two IEDs’ grounds connected (Rule 4,
Section 2-4).
Bill assigns a Modbus address to each IED. He then sets communication speeds and functional and protective parameters according to the instructions in each user manual.
Bill installs the PMCS software at the host PC and configures IED addresses at the host to match the addresses assigned to each on the network.
When all connections have been made and the IEDs and software are appropriately configured, Bill applies power to the system and runs tests to assure that everything is functioning properly.
If any difficulties are encountered, Bill refers to the trouble-shooting guide in Chapter 4.
Case Two
Case Two begins where Case One left off. The Modbus network is in place and GHO Corp. has been so pleased with their new PMCS system that they now wish to tie in a second building (Facility Two) and add several additional power management IEDs. However, the IEDs they wish to add are all commnet IEDs.
The host platform is based on Modbus, with a multi-port
RS-485 interface card providing the connection to the networks. Knowing the host platform and its currently attached IEDs, Bill makes a list of the IEDs that GHO
Corp. want to add to their PMCS network. His list of additional IEDs is:
• Six Enhanced MicroVersaTrip trip units for equipment protection
• Three POWER LEADER Meters for waveform capture
• One POWER LEADER EPM
• One POWER LEADER MDP Overcurrent Relay
• One Spectra Electronic Control Module
Commnet IEDs require Modbus Concentrators to be recognized by the PMCS. Bill has nine commnet IEDs to connect, so he will need only one Modbus Concentrator
(each Concentrator supports up to 32 commnet IEDs).
However, with some of the commnet IEDs located in
Facility Two, well beyond the 1000-foot segment limit, Bill realizes that he must either locate the Modbus
Concentrator in Facility 1 and run several very long commnet segments using POWER LEADER Repeaters to span the long runs or place a Modbus Concentrator in
Facility Two and extend his RS-485 network over to Facility
Two with RS-485 repeaters. Bill decides that it will be easier and more cost effective to run a single long RS-485 segment with a pair of RS-485 repeaters than to extend six commnet segments. An added benefit: each repeater uses optical isolation between its incoming and outgoing lines, eliminating harmful ground loops that can result when the ground potential between two structures is different.
For even greater electrical isolation Bill could have used an optical fiber link between the two remote locations.
Bill turns to his floor layout, to see just where the wiring could be run and how much distance it must cover. He knows where his host PC is located and realizes that he will have to interrupt the Modbus network at one or more locations to insert Modbus Concentrators to support his commnet IEDs. He maps where his IEDs must be located and, based on this information, where the Concentrators will be mounted. Next he plans the commnet segments and measures the cable runs required for each segment to connect the IEDs to the Modbus Concentrator, keeping in mind that the commnet rules require him to daisy-chain the IEDs one after another (unless he uses a
Junction/Outlet box). His floor layout is shown in Figure
24.
27
Power Management Control System
Chapter 2 – Network Design
RS485 networks terminated at host PC
Bill's Office
Network 4 - 19.2 kbaud
300'
100'
Network 3 - 19.2 kbaud
Multilin 565
Feeder Management Relay at main power feed
Facility Two
EPM 3720
600'
Multilin 269
Assembly Line Area
PLC 90/30
Programmable Logic Controller
550'
RS485 repeater
Terminating
Resistor
Commnet Segment 1
PLEPM EMVT
Segment 2
EMVT EMVT
EPM 3720
600'
Long-range RS485 cable run
3500 feet
RS485 repeater
GHO Corp Machine Shop network wiring diagram
Lathe Area
EPM 3720
Machining Area
Terminating
Resistor
Figure 24. Floor layout for Case Two.
350'
Milling Area
Modbus
Concentrator
Segment 3
Segment 5
EMVT EMVT POWER
LEADER
Meter
Segment 4
MDP POW ER LEADER
Meter
POWER
LEADER
Meter
EMVT ECM
IED Type
PLC 90/30
EPM 3720
EPM 3720
EPM 3720
Multilin 269+
Multilin 565
Modbus
Concentrator
Enhanced
MicroVersaTrip
Enhanced
MicroVersaTrip
Enhanced
MicroVersaTrip
Enhanced
MicroVersaTrip
Enhanced
MicroVersaTrip
Enhanced
MicroVersaTrip
POWER
LEADER Meter
POWER
LEADER Meter
POWER
LEADER Meter
POWER
LEADER EPM
MDP
Overcurrent
Relay
Spectra ECM
Physical Location
Assembly line
Milling
Lathe area
Machining
Assembly line
Power Intake area
Facility 2, north wall
Facility 2, Segment 1
Facility 2, Segment 2
Facility 2, Segment 2
Facility 2, Segment 3
Facility 2, Segment 5
Facility 2, Segment 5
Facility 2, Segment 3
Facility 2, Segment 4
Facility 2, Segment 5
Facility 2, Segment 1
Facility 2, Segment 4
Facility 2, Segment 3
Table 9. IED Addresses for Case Two.
Modbus Address
01
02
03
04
05
06
10
33
34
35
36
37
38
39
40
41
42
43
44
He must also bear in mind proper shield grounding considerations – each RS-485 IED grounded at only one point and no two IED’s grounds connected (Rule 4,
Section 2-4).
Bill checks Table 4 for the commnet wiring rules and finds that he must keep his POWER LEADER Meters on separate commnet networks, limit his commnet IEDs to four per segment, and keep each segment under 1000 feet
(unless he uses repeaters). The commnet segments he has planned satisfy all these rules.
Because his cabling limits are met, Bill selects Modbusequivalent addresses for the IEDs and adds them to his address chart for future reference. His updated address
Bill next checks Chapter 3 for physical wiring requirements and rules. He knows he needs Belden 3074F cable for the new RS-485 wiring to extend RS-485 Network
3 to the RS-485 repeater for the jump to Facility Two and to make the connection to the Modbus Concentrator from the RS-485 repeater in Facility Two. He moves the terminating resistor from the end of RS-485 Network 3 out to the new end at the Modbus Concentrator in Facility
Two.
28
Power Management Control System
Chapter 2 – Network Design
Commnet wiring requires Belden 8719 cable. Bill installs the IEDs according to the instructions in each user manual. He wires each commnet segment in daisy-chain fashion, one IED to the next, being sure to ground the shield at the Modbus Concentrator only.
Bill then sets local addresses on the IEDs in accordance with the addressing rules in Section 2–6. He sets communication speeds and parameters according to the instructions in each user manual.
Bill installs the PMCS software at the host PC and configures the IED addresses.
When all connections have been made and the IEDs and software are appropriately configured, Bill applies power to the system and runs tests to assure that everything is functioning properly.
If any difficulties are encountered, Bill refers to the trouble-shooting guide in Chapter 4.
have different communication speeds. For performance reasons, Bill decides to break the IEDs off to independent networks rather than connect all of them to the same RS-
485 network. The Ethernet Gateway offers four RS-485 ports, so using more than one port poses no additional cost burdens or configuration concerns.
Bill turns to his floor layout, to see just where the wiring could be run and how much distance it must cover. He maps where his IEDs must be located and where the
Ethernet Gateway will sit. He then measures the cable runs required to connect the IEDs to the Ethernet Gateway, keeping in mind that the RS-485 rules require him to daisy-chain the IEDs one after another. His floor layout is
Ethernet
RS485 networks terminated at Ethernet Gateway
Network 4 - 19.2 kbaud
Bill's Office
Ethernet
Gateway
150'
Lathe Area
Network 1 -
9600 baud
150'
Multilin SR745
Transform er
Managem ent Relay
Network 3 - 19.2 kbaud
Multilin 565
Feeder Management Relay
600'
350'
Milling Area
Multilin SR469
Motor Management Relay
Machining Area
Case Three
In Case Three, GHO Corp. has an existing Ethernet network installed and would now like to add power management capabilities with PMCS. Once again, plant engineer Bill has been given the task of designing and installing this system.
As before, Bill’s first task is to choose a platform on which the PMCS host will reside. Using the flowchart in Section
1-1, he decides that the PMCS will reside on Ethernet, requiring one or more Ethernet Gateways to communicate with the RS-485 networks.
Next, Bill makes a list of the IEDs that GHO Corp. needs to support on their PMCS network. The IED list is the same as in Case One:
• One PLC 90/30 Programmable Logic Controller for process control
• One EPM 3720 Meter for monitoring power
• One Multilin SR745 Transformer Management Relay
• One Multilin SR469 Motor Management Relay
• One Multilin 269+ Motor Relay for motor protection
• One Multilin 565 Feeder Management Relay for feeder protection
The list of communication protocols in Table 1 shows that all the IEDs communicate on Modbus; because no commnet IEDs are being used, no Modbus Concentrators are needed. However, because the PMCS will be operating on Ethernet, he will need to use an Ethernet Gateway to relay communications between the host and the Modbus networks. Table 1 also indicates that the Modbus IEDs
EPM 3720
Electronic Power Meter
600'
Multilin 269+
Motor Relay
Terminating
Resistors
Assembly Line Area
PLC 90/30
Programmable Logic Controller
GHO Corp Machine Shop network wiring diagram
550'
Figure 25. Floor layout for Case Three.
Next, Bill checks Table 2 for the Modbus wiring rules and
Table 3 for the Ethernet wiring rules.
He notes that he must properly terminate the RS-485 network at each end and that he must keep his total RS-
485 cable length under 4000 feet, unless he invests in RS-
485 repeaters or puts the IEDs on separate RS-485 networks, which may run in different directions and effectively increase his range.
His cabling limits are satisfied, so Bill selects Modbus addresses for the IEDs, and records them for future
reference. His address chart is shown in Table 10.
29
Power Management Control System
Chapter 2 – Network Design
IED Type
Multilin 565
Multilin 269+
PLC 90/30
EPM 3720
Multilin SR745
Multilin SR469
Physical Location
Power Intake Area
Assembly Line
Assembly Line
Machining
Lathe Area
Milling
RS-485 Port,
Modbus Address
1, 01
2, 01
3, 01
3, 02
4, 01
4, 02
Table 10. IED Addresses for Case Three.
Bill next checks Chapter 3 for physical wiring requirements and rules. He finds that he’ll have to use
Belden 3074F cable for the RS-485 wiring. He also locates the correct terminating resistors at each end of the RS-485 network.
He installs the IEDs according to the instructions in each user manual. He makes communication connections to the RS-485 communication cable in daisy-chain fashion, one IED to the next, with terminating resistors at the final
IED and the host (Ethernet Gateway). While wiring, he follows the RS-485 cable shield wiring rules explained in
Section 2–4 (rule 4).
Bill then assigns local Modbus addresses to the IEDs and sets communication speeds and parameters according to the instructions in each user manual.
He installs the PMCS software at the host PC and configures the IED addresses to match the addresses set at the IEDs.
When all connections have been made and the IEDs and software are appropriately configured, Bill applies power to the system and runs tests to assure that everything is functioning properly.
If any difficulties are encountered, he refers to the troubleshooting guide in Chapter 4.
Case Four
In Case Four, GHO Corp. wishes to create a power management system that will interconnect with their existing corporate Ethernet. They would like the capabilities of both Modbus and commnet IEDs and plan to integrate three separate facilities using repeaters. GHO
Corp. plant engineer Bill has been given the task of designing and installing this system.
As in the previous cases, Bill’s first task is to choose a platform on which the PMCS host will reside. GHO Corp.
requires Ethernet integration, so the flowchart in Section
1-1 determines that the PMCS will reside on Ethernet, requiring an Ethernet Gateway.
Next, Bill makes a list of the IEDs that GHO Corp. wishes to support on their PMCS network. His IED list is:
• One PLC 90/30 Programmable Logic Controller for process control
• Two EPM 3720 Meters and one EPM 7700 for monitoring power
• One Multilin 269+ Motor Relay for motor protection
• One Multilin 565 Feeder Management Relay for feeder protection
• Six Enhanced MicroVersaTrip trip units
• Three POWER LEADER Meters (with waveform capture)
• One POWER LEADER EPM
• One POWER LEADER MDP Overcurrent Relay
• One Spectra Electronic Control Module
Bill knows that he will need an Ethernet Gateway to connect his Modbus network(s) to Ethernet and both RS-
485 and POWER LEADER Repeaters to reach the remote locations in Facility Two and Facility Three. He checks his
IED list against the list of communication protocols in
Table 1 and notes that some of the IEDs communicate on
Modbus and some on commnet, so he will also need at least one Modbus Concentrator to support communications with the commnet IEDs. The Modbus
IEDs do not all communicate at the same speed, so more than one RS-485 network is required.
Next, Bill checks Tables 2 through 4 for the Modbus,
Ethernet and commnet wiring rules.
The EPM 7700, being a native Ethernet device, can be connected directly to the Ethernet hub Bill intends to install near his office. He’ll connect the hub to the corporate LAN, to his PC, to the 7700, and finally to the
Ethernet Gateway. Bill, realizing the LAN is shared by the entire building, installs an Ethernet data line surge
30
Power Management Control System
Chapter 2 – Network Design protector at the hub on the incoming line from the EPM
7700 IED to shield the rest of the network from potentially damaging transients.
Because he has only six Modbus IEDs (five IEDs and the
Modbus Concentrator) and 12 commnet IEDs to connect, he requires only one RS-485 network (each RS-485 network accommodates up to 31 Modbus IEDs and up to
215 commnet IEDs). However, because his Modbus IEDs communicate at several different baud rates, Bill decides to assign them to different RS-485 networks to achieve greater system performance.
He also notes that each RS-485 network must be properly terminated at each end. He must keep the RS-485 cable length of each RS-485 network under 4000 feet, unless he uses RS-485 repeaters, as on Network 3, to span the 3,500 feet to Facility 2.
The commnet rules are also easy to comply with. Each of the commnet segments must be kept under 1000 feet, unless repeaters are used to extend the range of the segments, as is required to reach the commnet IEDs in
Facility 3. Each commnet segment is limited to four commnet IEDs, and no segment may have more than one waveform capture meter (POWER LEADER Meter). Bill makes sure that his POWER LEADER Meters are limited to one per segment.
Bill now turns to his floor layout, to see just where the wiring could be run and how much distance it must cover.
He maps where his IEDs must be located and where the host PC will sit. He then measures the cable runs required to connect the IEDs to the host PC, keeping in mind that the RS-485 rules require him to daisy-chain the Modbus
IEDs one after another from the Ethernet Gateway and the commnet IEDs (four per segment) from the Modbus
Concentrator. His floor layout is shown in Figure 26.
The RS-485 cabling is less than 4000 feet for each of the
RS-485 networks, except for Network 3, where RS-485 repeaters are used to bridge the 3,500 feet to Facility Two.
Each of the commnet segments requires less than 1000 feet of cable, except for segment three, where POWER
LEADER Repeaters are used to span the 5000 feet to
Facility Three. The wiring rules are satisfied.
Bill selects Modbus addresses for the Modbus IEDs and
Modbus equivalent addresses for the commnet IEDs, using the worksheets in the back of the Modbus Concentrator User
Guide
(GEH-6491), and records them for future reference.
Bill’s address chart, found in Table 11, follows the floor
layout.
Ethernet connection to corporate LAN
Bill's Office
Ethernet
Ethernet
Hub
100'
Ethernet connection to EPM 7700 is surge-protected
Ethernet
Ethernet
Gateway
RS-485 networks terminated at Ethernet Gateway
Lathe Area
650'
EPM 7700
Milling Area
Network 1 -
9600 baud
Network 3 - 19.2 kbaud
600'
EPM 3720
Multilin 565
Feeder Management Relay at main power feed
Network 2 -
2400 baud
Machining Area
600'
Multilin 269
Assembly
Line
Area
EPM 3720
PLC 90/30
Programmable Logic Controller
550'
Long-range
RS485 cable run
3500 feet
Facility Two
RS485 repeater
Terminating
Resistor
Terminating
Resistor
Facility Three
POW ER
LEADER
Meter
EMVT
RS485 repeater
ECM
POWER
LEADER
Repeater
Long-range commnet cable run
5000 feet
Commnet Segment 1
PLEPM EMVT
Segment 2
EMVT EMVT
Modbus
Concentrator
Segment 5
EMVT EMVT
Segment 4
POWER
LEADER
Meter
MDP
Segment 3
POWER LEADER Repeater
POWER LEADER
Meter
Figure 26. Floor layout for Case Four.
31
Power Management Control System
Chapter 2 – Network Design
IED Type Physical Location
Multilin 565
Multilin 269+
EPM 7700
PLC 90/30
Modbus Concentrator
EPM 3720
EPM 3720
Enhanced MicroVersaTrip trip unit
Enhanced MicroVersaTrip trip unit
Enhanced MicroVersaTrip trip unit
Enhanced MicroVersaTrip trip unit
Enhanced MicroVersaTrip trip unit
Enhanced MicroVersaTrip trip unit
POWER LEADER Meter
POWER LEADER Meter
POWER LEADER Meter
Power intake area
Assembly line
Lathe area
Assembly line
Facility 2, north wall
Machining
Milling
Facility 2, Segment 1
Facility 2, Segment 2
Facility 3, Segment 2
Facility 2, Segment 3
Facility 2, Segment 5
Facility 2, Segment 5
Facility 3, Segment 3
Facility 2, Segment 5
Facility 2, Segment 4
POWER LEADER EPM Facility 2, Segment 1
POWER LEADER MDP Overcurrent Relay Facility 2, Segment 4
Spectra ECM Facility 3, Segment 3
RS-485 Port, Modbus
(or equivalent) Address
Port 1, IED 01
Port 2, IED 01
N/A - native Ethernet IED
Port 3, IED 02
Port 3, IED 03
Port 4, IED 01
Port 4, IED 02
Port 3, IED 33
Port 3, IED 40
Port 3, IED 41
Port 3, IED 50
Port 3, IED 70
Port 3, IED 71
Port 3, IED 51
Port 3, IED 72
Port 3, IED 60
Port 3, IED 34
Port 3, IED 61
Port 3, IED 52
Table 11. IED Addresses for Case Four.
Chapter 3 provides physical wiring requirements and rules. For commnet wiring, he’ll use Belden M8719 cable.
For RS-485 wiring, he’ll use Belden 3074F cable and the correct terminating resistors for both ends of the RS-485 networks.
Bill installs the IEDs at the equipment according to the instructions in each user manual and runs the RS-485 cable for each RS-485 network from the Ethernet Gateway to each Modbus IED in daisy-chain fashion, one IED to the next, and terminated at each end.
Bill runs the commnet cable from the Modbus
Concentrator for each commnet segment, grounded only at the Modbus Concentrator.
He assigns local Modbus addresses to the Modbus IEDs and sets communication speeds and parameters according to the instructions in each user manual.
Next, Bill sets the local address at each commnet IED according to what he wants the Modbus-equivalent address of each IED to be. He configures the Modbus
Concentrator, either manually or with the autoconfigure option, following the instructions in the Concentrator
User Manual. During configuration, the Concentrator probes each of its commnet segments for IEDs, records their commnet addresses, and assigns a Modbus-equivalent address so that communication from the PMCS will be directed to the correct IED.
Bill configures the Ethernet Gateway, assigning a unique
IP network address after he checks with the LAN administrator to determine which IP addresses are available. He then sets the serial port communication parameters for each Gateway port after referring to document GEH-6505, Ethernet Gateway User’s Guide, for information on configuring the Gateway serial ports.
Bill assigns a unique IP address to the EPM 7700 meter’s
Xpress Card based on information in the EPM 7700 user documentation and the addresses he received from the
LAN administrator.
He installs the PMCS software at the host PC and configures the IED addresses in the DDE server. Next, Bill modifies the 7700 network configuration file for the EPM
32
Power Management Control System
Chapter 2 – Network Design
7700, according to the GE 7700 Gateway User’s Guide (DEH-
40035).
When all connections have been made and the IEDs and software are appropriately configured, Bill applies power to the system and runs tests to assure that everything is functioning properly. If any difficulties are encountered, he refers to the trouble-shooting guide in Chapter 4.
Case Five
In this case study, the circumstances are similar to those in
Case One, with the addition of several RS-485 dual-port
IEDs. The PMCS host resides on Modbus, connected to several RS-485 Modbus segments.
The IED list is:
• One EPM 7300 Electronic Power Meter
• One Multilin SR745 Transformer Management Relay
• One Multilin SR760 Feeder Management Relay
• One Multilin 269+ Motor Relay
• One Multilin 565 Feeder Management Relay
• Two dual-port RS-485 Modbus Monitors to serve as remote-viewing stations for the IEDs on segments 3 and 4
• One Modbus Concentrator to support the commnet
IEDs below
• One POWER LEADER Electronic Power Meter
• One Spectra Electronic Control Module
• One Enhanced MicroVersaTrip-C trip unit
He checks the list of communication protocols in Table 1 and notes that most of his IEDs communicate on Modbus, but because he wants to use several commnet IEDs in the
Machining area, he’ll need a Modbus Concentrator. As well, the Modbus IEDs communicate at different baud rates, and Bill makes a note that they should be placed on separate RS-485 networks for improved performance. He decides to use four RS-485 networks supported by the recommended communications card at the host PC.
Bill now turns to his floor layout to see just where the wiring could be run and how many feet of cable will be needed. He maps where his IEDs must be located and where the host PC will sit. Next he measures the cable runs required to connect the IEDs to the host PC, keeping in mind that the wiring rules require him to daisy-chain the
IEDs on each RS-485 network one after another.
Bill calculates the cable length of each RS-485 network and finds that none are over the 4000-foot limit, so he won’t need to use any RS-485 repeaters. The commnet segments are also within the wiring limits, so no POWER LEADER
Repeaters are required.
The factory floor is very large though, and Bill wants to be able to view IED data at several locations to save walking all the way back to his office every time he wants to check an
IED. To serve this purpose, he’s purchased a pair of dualport Modbus Monitors, which he will install in the Milling and the Machining areas, respectively. He checks the
Modbus Monitor wiring rules and sees that he’ll be able to connect RS-485 Network 3 to the RS-485 Port A of each
Monitor and RS-485 Network 4 to the RS-485 Port B of each Monitor. This will allow him to view data from the
IEDs in these areas at either station as well as back in his office at the host PC.
Proper termination is required at each end of the network and is provided at the RS-485 card by placing jumpers between the correct pins (see RS-485 card user manual).
The appropriate terminating resistors must be used at the opposite end of each RS-485 network, per Section 2–4, rule
4.
The network architecture diagram Bill creates is shown in
RS-485 networks terminated at host PC
Bill's Office
100'
Network 4 - 19.2 kbaud
550'
Lathe Area
SR750
Feeder Management Relay
350'
Milling Area
Network 3 - 19.2 kbaud
Multilin 565
400'
Feeder Management Relay at main power feed
600'
Assembly Line Area
Multilin 269+
Motor Relay
Terminating
Resistors
SR469
Motor
Management
Relay
300'
Multilin 239
Motor Protection
Relay
RS-485
Port A
RS-485
Port B
Modbus Monitor #1
550'
750'
Machining
Area
300'
Modbus
300'
Concentrator
RS-485
Port A
RS-485
Port B
Modbus Monitor #2
EPM 3720
Electronic
Power Meter
400'
Spectra ECM
EMVT-C
Trip Unit
250'
250'
50'
POW ER LEADER EPM
GHO Corp Machine Shop network wiring diagram
Figure 27. Floor layout for Case Five.
Confident that his new design will provide maximum performance and with his wiring requirements and limits
33
Power Management Control System
Chapter 2 – Network Design met, Bill selects Modbus addresses for the IEDs. He checks
Section 2-7 and sees that he can assign the Modbus IEDs on each network any Modbus address between 1 and 247
(except for the Modbus Concentrator, which must have an address between 1 and 32). The commnet IEDs must have
Modbus-equivalent addresses between 33 and 247. He selects addresses and records them for future reference.
The address chart is shown in Table 12.
RS-485
Network #
1
3
3
3
4
4
4
4
4
4
4
4
2
3
IED Type Physical
Location
Multilin 565
Multilin 269+
SR469 Motor
Management
Relay
Modbus Monitor
#1, RS-485 Port A
Multilin 239
Motor Protection
Relay
Modbus Monitor
#2, RS-485 Port A
Power intake area
Assembly line
Assembly line
Lathe area
Machining area
Machining
Multilin SR750
Feeder
Management
Relay
EPM 3720
Milling area
Modbus Monitor
#1, RS-485 Port B
Milling area
Lathe area
Modbus Monitor
#2, RS-485 Port B
Modbus
Concentrator
Machining area
Machining area
EMVT-C trip unit Machining area
Spectra ECM
POWER
LEADER EPM
Machining area
Machining area
Table 12. IED Addresses for Case Five.
Modbus
Address
01
01
01
02
03
04
01
02
03
04
05
33
34
35 to the next, terminated at both ends of each RS-485 network, double-checking his wiring against the example provided in Section 2–4. Since several of his Multilin IEDs have two ports, he is careful to connect only one RS-485 port per IED. The Modbus Monitors are also RS-485 dualport, but Bill carefully follows the wiring instructions to correctly connect them to the RS-485 networks. The A port of each Monitor is connected to one RS-485 network and the B port of each is connected to another network.
He must also bear in mind proper shield-grounding considerations: each RS-485 IED grounded at only one point and no two IEDs’ grounds connected (Rule 4,
Section 2-4). The Multilin 565 special grounding considerations are also taken into account (see Chapters 2 and 3).
Bill assigns a Modbus address to each IED. He then sets communication speeds and functional and protective parameters according to the instructions in each user manual.
Bill installs the PMCS software at the host PC and configures IED addresses at the host to match the addresses assigned to each IED on the network.
Configuration files for the Modbus Monitors are downloaded to the units or created using the Monitor’s
“Create from PMCS” feature (see DEH-027 for details).
When all connections have been made and the IEDs and software are appropriately configured, Bill applies power to the system and runs tests to assure that everything is functioning properly.
If any difficulties are encountered, Bill refers to the trouble-shooting guide in Chapter 4.
Chapter 3 provides Bill with physical wiring requirements and rules. He’ll use Belden 3074F cable, readily available.
He also locates the correct terminating resistors at both ends of each RS-485 network.
He installs the IEDs according to the instructions in each
IED’s user manual. He then makes connections to the RS-
485 communications cable in daisy-chain fashion, one IED
34
Power Management Control System
Chapter 2 – Network Design
(This page left blank intentionally.)
35
advertisement
Related manuals
advertisement
Table of contents
- 11 Welcome to PMCS!
- 11 What is Power Management?
- 11 Benefits of Power Management
- 11 What is PMCS?
- 12 How Does PMCS Work?
- 12 Using This Guide
- 13 Chapter 1 – Introduction
- 13 1–1 Typical Systems
- 14 1–2 Master-Slave Organization
- 15 1–3 Required Hardware
- 15 Host Computer
- 15 RS-485 Interface Card or RS-232/RS-485 Converter
- 15 Ethernet Network Card
- 15 1–4 Compatibility & Interconnection with Existing Ethernet Networks
- 15 1–5 Operation During Power Outage
- 16 1–6 Time & Date Stamping
- 16 1–7 Remote System Operation
- 17 1–8 Supported IEDs
- 19 Chapter 2 – Network Design
- 20 2–1 Modbus Rules
- 21 2–2 Ethernet Configuration Rules
- 22 T
- 22 Table 3. Ethernet configuration rules2–3 Ethernet Network Considerations
- 23 10Base-T specifications and rules
- 23 10Base-FL specifications and rules
- 24 2–4 Commnet Configuration Rules
- 25 2–5 Modbus Wiring Rules – Diagrams
- 29 2–6 Commnet Wiring Rules – Diagrams
- 31 2–7 Performance Recommendations
- 31 The Ideal Network
- 31 Modbus performance recommendations
- 31 Commnet performance recommendations
- 31 2–8 Addressing the IEDs
- 35 2–9 Multiple RS-485 Networks – Addressing
- 35 2–10 System Expansion
- 35 2–11 Case Studies
- 35 Case Study One
- 37 Case Two
- 39 Case Three
- 40 Case Four
- 43 Case Five
- 47 Chapter 3. Network Wiring and Construction
- 48 3–1 Wiring Requirements
- 49 Type of Wire
- 49 Termination
- 49 Shield Grounding
- 49 3–2 Modbus – Commnet Integration
- 49 Wiring Concerns
- 51 3–3 Modbus – Ethernet Integration
- 51 3–4 Local Configuration of IEDs
- 51 3–5 Applying Power to the System
- 51 3–6 Software Loading and Startup
- 52 Chapter 4 –Trouble-Shooting
- 52 4–1 Communication Network Trouble-Shooting
- 53 4–2 Host Trouble-Shooting
- 53 4–3 IED Trouble-Shooting
- 53 4–4 Equipment Trouble-Shooting
- 53 4–5 Product Service Procedure
- 54 4–6 Trouble-Shooting Guide
- 59 Overview
- 59 239 Motor Protection Relay
- 59 269+ Motor Management Relay
- 60 565 Feeder Management Relay
- 60 735 Feeder Relay
- 61 MX200 (Microprocessor Controller)
- 61 Generator PLC (Series 90-70)
- 61 Electronic Power Meter EPM 7330