advertisement
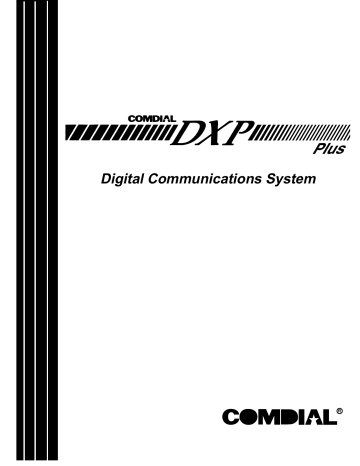
R
Installing The DXPT1 Digital Carrier Transmission Option
In The DXP Plus Digital Communications System
1.0 Introducing The DXPT1 Option
The digital carrier transmission option (DXPT1) gives the DXP Plus digital communications system the capability to handle up to 24 channels of voice and/or data transmissions over a single four-wire cable using multiplexing techniques in superframe (SF) or extended superframe (ESF) format. The DXPT1 board includes a customer service unit (CSU) to eliminate the need for a CSU external to the DXP Plus.
Since the DXP Plus supports a maximum of 240 lines, and each DXPT1 board handles up to 24 channels, you can install up to 10 DXPT1 boards in the DXP Plus system. You can install these 10 boards in any available universal board slot in the main or expansion cabinets. Of course, any other line boards that you install, such as loop start,
DID or multipurpose, reduce the number of lines available for T1 service and thus reduces the number of DXPT1 boards that you can install.
Whenever you install one or more DXPT1 boards, and the DXP Plus is receiving its timing signals from an external source, you must install one synchronization card (DXOPT–SYN) on the services board. When you connect the system to central office (CO) lines, you must include a synchronization card, and the DXP Plus must be controlled by CO signalling. In installations where the DXP Plus supplies the clock signal for the distant system, there is no requirement for DXOPT–SYN cards.
If you plan to use tone dial configured DID or E&M lines with the T1 digital carrier transmission option, you will need to install one or more DTMF receiver cards to the DXP Plus. Typically, you will need one DTMF receiver for every six lines. This ratio indicates that you need to add one DTMF receiver card for each DXPT1 board that is configured for 24 DID or E&M lines. In high traffic situations, you may need additional DTMF receiver cards.
For information on DTMF receiver card installation, see IMI89–186, Installing A DTMF Receiver In The DXP
Plus Digital Communications System.
NOTE: The DTMF receiver cards that you add for this purpose are in addition to any you may add to the system to support industry-standard telephone station boards
If you are unfamiliar with the terms and component names associated with the T1 digital carrier transmission option, refer to glossary of terms presented in Section 8 located at the end of this publication.
CAUTION
For operation with the DXP Plus, the T1 board must be Revision B or higher. If the T1 board that you are installing is a lower revision, contact Comdial Technical Services (1–800–366–8224) for advice before you proceed with the installation..
This manual has been developed by Comdial Corporation (the “Company”) and is intended for the use of its customers and service personnel. The information in this manual is subject to change without notice. While every effort has been made to eliminate errors, the Company disclaims liability for any difficulties arising from the interpretation of the information contained herein.
The information contained herein does not purport to cover all details or variations in equipment or to provide for every possible contingency to be met in connection with installation, operation, or maintenance. Should further information be desired, or should particular problems arise which are not covered sufficiently for the purchaser’s purposes, contact Comdial, Inside Sales Department,
Charlottesville, Virginia 22906.
Printed in U.S.A.
IMI89-193.01
7/95
IMI89–193 Installing The DXPT1 Line Board
1.1
Understanding The DXPT1 Board
Through time division multiplexing, the DXPT1 board greatly increases the efficiency and economy of the DXP
Plus system by providing up to 24 channels on two twisted metallic pairs. This multiplexing technique allows two-way voice or data communications at 1.544 Mbps (million bits per second) with either a central office (CO), public branch exchange (PBX), or another digital communications system (DXP Plus). The DXPT1 board includes a built-in customer service unit (CSU) but there is no restriction on adding an external CSU.
When you connect two DXP Plus systems together using E&M protocol through the T1 lines, designate one DXP
Plus as the master and the other one as the slave. In this application, only the slave DXP Plus system requires a
DXOPT–SYN card.
When the T1 option is installed, the DXP Plus supports the following signaling protocols per channel.
•
Loop Start (subscriber end only)
•
Ground Start (subscriber end only)
•
E&M two- or four-wire tie lines
•
DID (direct inward dial)
Loop Start and Ground Start will support synchronized ring, hook flash, and pause. Dialing can be DTMF (tone) or dial pulse. For E&M and DID tone operation, check the number of DTMF receiver cards needed in the system
E&M and DID will support wink start, delay dial, and immediate dial (dial pulse only). Dialing can be tone or dial pulse.
1.2
Understanding The DXOPT-SYN Synchronization Card
The DXOPT–SYN card uses a reference timing frequency of 8 KHz that it derives from the 1.544 MHz frequency supplied to the DXPT1 board by the central office (CO) or other external source. By referencing this 8 KHz with
8 KHz timing derived internally, the master 16.384 MHz voltage-controlled oscillator (VCO) can be synchronized. The T1 transmit clock (1.544 MHz) is derived from the 16.384 MHz frequency on the DXPT1 board. If the 1.544 MHz received frequency is incorrect (not within a 200 Hz tolerance), the system may loose synchronization with the CO or other external source. The DXOPT–SYN card reports this condition by turning on the appropriate alarms on the DXPT1 board and DXOPT–SYN card. A loss of clock synchronization causes frame slips that result in data communications errors.
The DXOPT–SYN card allows two timing references ( primary and secondary) to be selected. You can select either automatic or manual (for maintenance mode). In the automatic mode, a loss of primary timing causes the system to switch to the secondary timing reference. If both the primary and secondary timing references are lost, the VCO oscillator on the DXOPT–SYN card is defaulted to the fixed 16.384 MHz oscillator on the services board. This results in the loss of T1 clock synchronization.
2 – Installing The DXPT1 Line Board
Installing The DXPT1 Line Board IMI89–193
2.0 Installing Circuit Boards In The Equipment Cabinet
CAUTION
Circuit boards are susceptible to damage caused by electrostatic discharge, and you must keep this fact in
mind as you handle the circuit boards. Refer to the Comdial publication IMI01-005, Handling Of
Electrostatically Sensitive Components, for general information. Specific handling precautions are also included in this installation instruction.
2.1
Creating A Static Safe Work Area
When servicing the common equipment cabinet at the installation location, it is a good practice to place a conductive mat in front of the cabinet area and ground the mat to a good earth ground. (The third wire ground of the AC power line is also an acceptable grounding point.) The grounded conductive mat provides a safe static electric discharge path.
When removing the common equipment cabinet from the installation location for servicing, it is a good practice to prepare a static-safe work area on which to place the cabinet.
You should supply yourself with a static discharge wrist strap, and wear it every time you handle electronic circuit boards either at the cabinet mounting location or at your work area.
Backboard
Common
Equipment
Cabinet
Static Discharge
Wrist Stap
Conductive
Mat 1 Meg Ohm
Resister
PLUS034
ESD Protective
Mat
ESD Protective
Worksurface
Static
Wrist
Strap
Static 2
Common Point Ground
Typical Earth
Ground
ESD Protective
Mat
Earth
Ground
Creating A Static Safe Work Area
Providing Static Protection At The Cabinet
Mounting Location
Installing The DXPT1 Line Board – 3
IMI89–193 Installing The DXPT1 Line Board
3.0 Configuring The DXPT1 Board
Before you install the DXPT1 board, determine if you must meet special system requirements such as fractional service (8 or 16 channel operation). If you do have special system requirements, use the dual in-line pin (DIP) switches provided on the board to re-configure the DXPT1 board.
The DXPT1 board contains 28 DIP switches (three 8-position modules and one 4-position module). Rectangular cutouts in the front-edge panel provide access to these switches.
The eight DIP switches nearest the bottom of the panel are accompanied by eight green LED indicators.
NOTE: These eight switches and their associated indicators are for factory diagnostic purposes only.
The remaining 20 DIP switches labeled SW1, SW2. and LIU are for configuring the DXPT1 board to meet specific operating requirements. See Figure 2. The default setting for all of these switches is 0 (on the left as you face the front edge of the board). This is the standard superframe (SF) configuration for most customer applications. However, special customer needs may require that you reset one or more of these switches using the procedure given below.
1. Obtain a static discharge wrist strap (supplied with the main DXP cabinet) and attach it to one of your wrists.
Make sure to adjust the strap for a snug fit against your skin; do not apply the strap over any of your clothing.
2. Connect one end of the wrist strap-cord to the wrist strap and the other end to earth ground.
NOTE: With the DXP cabinet in the installed position, the ground lug on the right side of the cabinet is normally a good grounding point since this lug should have a heavy ground wire connected between it and a good earth ground.
3. Remove the DXPT1 board from its static protection bag and set it on a static-safe work area.
4. Using a ball-point pen or similar object, move the DIP switches from left (0 position) to right (1 position) as needed. All DIP switches are facing left for typical applications. See Tables 1, 2, and 3 for descriptions of the
DIP switches.
4 – Installing The DXPT1 Line Board
Installing The DXPT1 Line Board IMI89–193
Reset Pushbutton
(Behind Hole)
(Default)
1
2
3
4
0
LIU
1
(See Table 3)
Diagnostic
Switches and LEDs
For Factory
Use Only
(Default)
1
4
5
2
3
6
7
8
0
SW1
1
(See Table 1)
(Default)
1
2
3
4
5
6
7
8
0
SW2
1
(See Table 2)
T1002A
Locating The DIP Switches
Installing The DXPT1 Line Board – 5
IMI89–193 Installing The DXPT1 Line Board
3.1
Understanding The T1 Options (SW1–1 Through SW1–8)
The following T1 operating modes are described to help you understand the many options that you can select with
DIP switches SW1–1 through SW1–8 on the DXPT1 board.
3.1.1 T1 General Operation
T1 is the digital two-way transmission of telecommunications over a single high-speed circuit. Up to 24 separate voice or data transmissions form digital pulses that are transferred at the rate of 1.544 million bits per second
(Mb/s) over the T1 trunk. At the receiving end, the digital pulses are decoded into 24 separate circuits.
Pulse characteristics such as repetition rate, pulse width, pulse amplitude, and average ones density ((ratio of one
(1) bits to zero (0) bits)) are as specified by digital signal level 1 (DS-1) described in American National
Standards Institute Specification, ANSI T1.403-1989.
3.1.2 Framing Modes
Digital data is handled most efficiently when it is organized into frames. A frame of digital information consists of 193 bits (24 channels x one eight-bit word + one framing or control bit). The framing bit is used for frame identification when multiple frames are used.
The frame repetition rate is eight thousand frames per second (8 Kf/s).
This option uses either of two framing formats—superframe (SF) and extended superframe (ESF).
The superframe format contains 12 frames. In the 6th and 12th frames, the voice information in the eighth (least significant) bit positions is overwritten with signaling information. This signaling method is called robbed-bit signaling. The robbed bits in the 6th and 12th frames are designated signaling bit A and B respectively.
The extended superframe format extends the framing boundaries to include 24 frames . The ESF format provides improved maintenance capability over the SF format. In this format, 24 framing bits (or 8 Kb/s) are available to provide the following:
• framing synchronization (2 Kb/s)
• facility data link (FDL) (4 Kb/s)
•
CRC-6 error check (2 Kb/s)
The robbed bits from the 6th, 12th, 18th, and 24th frames are used for signaling. Therefore, two additional signaling paths are available—signaling bits C and D (future).
3.1.3 Signaling Type
Channel associated signaling (CAS) is a signaling method employing robbed bits. The signals using the robbed bits are related to the same channel as the one carrying the information. CAS is currently the only signaling-type option available for this equipment.
3.1.4 Yellow Alarm
A yellow alarm is a signal transmitted by a digital communications system when that system has lost synchronization to the incoming signal. Communications can be restored if a a yellow alarm lasts less than four seconds. After four seconds, a red alarm (out-of-service) is issued and all calls are set to on-hook. When the system is using the superframe format, the transmitted yellow alarm signal contains binary zeros (0s) in the second bit positions of all 24 channels. This is the default setting for DIP switch SW1–4.
The 12th frame method (used in Japan) forces the framing bit for the 12th channel to a binary one (1). This is detected by the receiving system as a yellow alarm.
In the extended superframe format, the system that has lost synchronization to the incoming signal will transmit a
16-bit pattern consisting of eight one (1) bits followed by eight zero (0) bits over the facility data link (FDL) to represent a yellow alarm.
6 – Installing The DXPT1 Line Board
Installing The DXPT1 Line Board IMI89–193
3.1.5 Zero Suppression
There are two ways to avoid system timing problems when eight or more successive zero (0) bits are transmitted.
One method is B7 suppression and the other is bipolar 8-zero substitution (B8ZS). For pulse modulated voice
(PCM), eight consecutive zero (0) bits should never occur.
B7 suppression is a technique that forces a one (1) bit in the 7th bit position when all of the bits in a binary word are zero (0). The resulting distortion in a voice circuit is negligible. However, this technique could induce errors if it was used in digital data transmissions.
Digital information transmitted over T1 trunks is bipolar; that is, the binary ones (1s) pulses (marks) alternate between a positive and a negative voltage level. The bipolar 8-zero substitution (B8ZS) method substitutes four bits in bit positions four, five, seven, and eight when eight zero (0) bits occur in a binary word. The substituted bits are inserted in a unique pattern that causes a bipolar error. The B8ZS binary words containing the deliberate bipolar errors are detected at the receiving terminal where the errant bipolar pulses are removed and substituted with all zero (0) bits. Because the received binary words are returned to their original bit patterns (all binary zero bits), a clear channel is provided for error-free digital data transmission. Both ends of the communications link must be configured to use B8ZS. (B8ZS is a feature designed for future requirements.)
3.1.6 Fractional T1
Fractional T1 is when you use only a portion of a T1 trunk, as needed. On the DXP Plus you must set DIP switches SW1–7 and SW1–8 for 24 channel operation. This setting allows the system to pass error information end-to-end when operating fractional T1 with the ESF format.
Setting The SW1 DIP Switches
Switch
Number
1 (top)
2
3
4
5,6
7,8
Switch
Position
0 (default)
1
0 (default)
1
0 (default)
1
0 (default)
1
0, 0 (default)
0,1
1,0
1,1
Function
FRAME MODE superframe mode (SF) extended superframe mode (ESF)
SIGNALING TYPE channel associated signaling (CAS) reserved
RESERVED FOR FUTURE USE reserved reserved
YELLOW ALARM TYPE bit 2 of all channels method
12 frame method (Japanese)
ZERO SUPPRESSION
B7 suppression
B8ZS suppression (digital data) no suppression no suppression
CHANNEL CAPACITY
24 channel capacity 0,0 default)
NOTE: SW1–1 through SW1–8 switches are read only when you apply power to the board or do a manual reset.
With power on, manually reset the board by inserting a slender object, such as a straightened-out paper clip, into the small hole located between the Yellow and Syn LEDs on the front-edge panel. You can also reset the board remotely from a video display terminal or personal computer. A reset causes a T1 service disruption.
Installing The DXPT1 Line Board – 7
IMI89–193 Installing The DXPT1 Line Board
3.2
Understanding The T1 Options
(SW2–1 Through SW2–8 And LIU–1 Through LIU–4)
The following T1 operating modes are described to help you understand the many options that you can select with
DIP switches SW2–1 through SW2–8 and LIU–1 through LIU–4 on the DXPT1 board. DIP switches designated
LIU are associated with the DXPT1 board’s line interface unit.
3.2.1 Loopback
Loopback is the maintenance routine used to verify the receive function (local or remote) and to isolate system problems. When using the superframe format, the customer interface (CI) loopback option from the network, if provided, can be activated from the network via in-band signaling (per ANSI T1.403, 1989, SECTION 8.3.1.1).
Framed code words activate and deactivate loopback routines when the option is enabled with DIP switch
SW2–1. The default setting is off, but many central offices will support SF loopback. See your central office representative to ensure that you are complying with their requirements.
You access remote and payload loopback operation via the facility data link when using the extended superframe format.
You can manually make three different types of loopback requests depending on the option you select using DIP switches SW2–7 and SW2–8. These are: local, remote, and payload loopback. When using payload loopback
(ESF format only), all channel bits maintain bit-sequence integrity but the framing bit is re-established.
3.2.2 Customer Service Unit (CSU) Identification Bit
You can set the message-oriented (C/R) bit transmitted over the ESF data link by DIP switch SW2-2 to be a zero
(0) bit or a one (1) bit. The C/R bit is used to identify the T1 signal origin as being either from customer premise equipment (CPE) or carrier equipment such as a CSU.
Set C/R to be a zero (0) bit for customer premise equipment (CPE) or when using an external CSU (default).
Set C/R to be a one (1) bit if the network requires the T1 internal CSU to be classified as carrier equipment.
3.2.3 Cyclic Redundancy Check (CRC-6)
This is a method for checking the accuracy of data transmissions when using the ESF format. This method uses a polynomial algorithm based on the content of a superframe of data. When CRC-6 checking is enabled via DIP switch SW2–4, an alarm will be activated whenever a CRC code (checksum) is received over the ESF data link that does not match the locally calculated code (checksum).
3.2.4 Yellow Alarm During ANSI Messages On The Facility Data Link
When using the ESF format, the facility data link is available for reporting transmission performance information once a second. Normally, these transmissions are inhibited by yellow alarms. However, you can set DIP switch
SW2-5 to allow these transmissions during yellow alarms.
3.2.5 Green B8ZS/COFA LED Definition
The green LED on the DXPT1 board’s edge-panel labeled “B8ZS/COFA” indicates either that B8ZS code words are being received or that a change of frame alignment (COFA) occurred during the last synchronization by the external T1 source or carrier equipment. You can determine which condition you want reported by how you set
DIP switch SW2–6. The default setting is for “COFA” reporting.
3.2.6 Receive Sensitivity
The equalizer gain logic (EGL) determines how sensitive the receive circuits are to the incoming signals. You set the level for -26 dB or -36 dB by using DIP switch LIU-1. (Normally, the -26 dB level setting is the better choice.)
8 – Installing The DXPT1 Line Board
Installing The DXPT1 Line Board IMI89–193
3.2.7 Transmit Level Attenuation
You can manually set the transmit level for a particular value (0, -7.5, -15, or -22.5 dB) or select the automatic feature that sets the transmit level automatically depending on the receive signal. A weak receive signal causes a strong transmit signal and vice versa. Use DIP switch LIU–2 to select either the manual or the automatic setting.
If you select the manual setting, set the desired value with DIP switches LIU–3 and LIU–4. Normally, 0 dB is used when connecting to a network interface box.
Setting The SW2 DIP Switches
Switch
Number
Switch
Position
Function
2
3
4
5
6
7,8
1 (top) 0 (default)
1
0 (default)
1
0 (default)
1
0 (default)
1
0 (default)
1
0 (default)
1
0,0 (default)
0,1
1,0
1,1 superframe NETWORK IN-BAND loopback disabled enabled
CSU ID (C/R) BIT (ESF MODE)
C/R bit = 0 designates customer premise equipment (CPE)
C/R bit = 1 designates carrier equipment
RESERVED FOR FUTURE USE reserved reserved
CRC (CYCLIC REDUNDANCY CHECK) FOR ESF MODE disabled enabled
FDL YELLOW ALARM DURING ANSI MESSAGES disabled enabled
B8ZS/COFA LED DEFINITION
COFA (change of frame alignment)
B8ZS detect
MANUAL loopback REQUEST no loopback local loopback request remote loopback request payload loopback request (ESF only)
NOTE: When changing DIP switch SW2–2 or SW2–5, you must reset the board before the switch is read. With power on, manually reset the board by inserting a slender object, such as a straightened-out paper clip, into the small hole located between the Yellow and Syn LEDs on the front-edge panel. You can also reset the board remotely from a video display terminal or personal computer. A reset causes a T1 service disruption.
Setting The LIU DIP Switches
Switch
Number
1 (top)
2
3,4
Switch
Position
0 (default)
1
0 (default)
1
0,0 (default)
0,1
1,0
1,1
Function
RECEIVE SIGNAL SENSITIVITY
-26 dB
-36 dB
TRANSMIT LEVEL MODE
Automatic (level set by receive signal)
Manual (level set by switches 3 and 4 below)
TRANSMIT LEVEL ATTENUATION
(LIU-2 must be “1")
0 dB
-7.5 dB
-15 dB
-22.5 dB
Installing The DXPT1 Line Board – 9
IMI89–193 Installing The DXPT1 Line Board
4.0 Installing The DXPT1 Board
1. Normally you should disconnect the AC power cord from the AC outlet and disconnect the optional battery back-up assembly from the main cabinet power supply; however, when necessary, you can install a DID line board in an operating system. If you must do this, connect one end of a standard telephone handset coil cord to the precharge port on the power supply. During step 6, you will connect the other end of this coil cord to the precharge jack on the line board.
2. Install your static discharge wrist strap on your bare wrist; adjust it for a snug fit. Be sure that the strap is touching bare skin and is not isolated by clothing. Connect the wrist strap cord between the wrist strap and an
AC or earth ground
3. Loosen the retaining hardware and lift the front panel away from the common equipment cabinet.
NOTE: With the common equipment in the installed position, the ground lug on the side of the cabinet is an appropriate grounding point since it should have a heavy ground wire connected between it and a good earth ground.
4. Each DXPT1 line board is supplied in a static protection bag for safe keeping. When you are ready to install the board, remove it from its static protection bag.
5. Locate the proper board slot.
•
On DXP Plus systems the DXPT1 line boards connect to any universal slot.
NOTE: On DXP Plus systems, do not install a DXPT1 line board at the right-most board slot in the second (or lower) expansion cabinet. The system reserves this slot for internal use.
6. If you are installing the DXPT1 line board in an operating system, connect the free end of the precharge cord that you installed in step 1 to the precharge jack on the line board.
7. Orient the DXPT1 line board with its top and bottom guides in main cabinet board cage, and press the board firmly until its board edge connection properly mates with the connector on cabinet’s backplane. If you connected a handset cord between the pre-charge port on DXP Plus power supply and the jack on DXPT1 line board (as directed in step 6), disconnect it after installing board.
CAUTION
When pressing circuit boards into place, press them only at the extractor lever locations.
If you apply pressure at other locations you may damage the board assembly.
8. Repeat steps 3 and 4 until all DXPT1 line boards are installed.
9. Make a final inspection to ensure that all boards are, oriented correctly and mated properly.
10. Install and tighten the supplied screws to secure the circuit boards to the board cage. Do not neglect this step!
It is important because it helps in providing a protective ground condition for the board thus ensuring RFI
(radio frequency interference) and lightning protection.
10 – Installing The DXPT1 Line Board
Installing The DXPT1 Line Board
Pre-charge jack
PLUS011A
IMI89–193
Universal board slots
1 - 11
Pre-charge cable for installation during power up
Pre-charge jack
Pre-charge jack
Universal board slots
1 - 9
Connect board to any universal board slot
Pre-charge jack
Universal board slots
1 - 10
DO NOT install boards in last slot on right in lower expansion cabinet.
Installing The DXPT1 Board
Static discharge wrist strap
Installing The DXPT1 Line Board – 11
IMI89–193 Installing The DXPT1 Line Board
4.1
Connecting The T1 Trunk
Terminate the end of the T1 trunk with a miniature 8-pin modular plug, and plug it into the main jack on the front edge of the DXPT1 board.
The DXPT1 board contains a built-in CSU that protects the DXP Plus from voltage surges, provides transmission drive up to 6,000 feet, and performs diagnostic tests for the network. Therefore, a customer-supplied CSU is not necessary unless your customer requires this addition.
If a direct connection to a repeater is within a few hundred feet, the transmit signal from the DXPT1 board may overdrive the repeater. Repeaters normally operate best with -7.5 to -23 dB input signals. Arrange LIU switches 2,
3, and 4 to set the transmit signal level (0 dB is default).
IMPORTANT CAUTION
To help ensure that external over-voltage surges do not damage the system, Comdial engineers suggest that you install a properly-grounded gas discharge tube or a similar primary protection device on the T1 trunk where it enters the building. If the site includes a network interface box, verify that there is standard lightning protection installed externally to the box on its network side. Primary protection where the cable enters the building is necessary to prevent a fire hazard inside the building.
12 – Installing The DXPT1 Line Board
Installing The DXPT1 Line Board IMI89–193
Front View of Main Connector
On DXPT1 Board
6
7
4
5
8
2
3
1 R1
T1
R
T
C1
Receive
C1
Transmit
NOTE: No connections are allowed to pins 7 or 8. (Issue 2 boards
ONLY.)
T1003A
Connecting The TI Trunk To The DXPT1 Circuit Board
Installing The DXPT1 Line Board – 13
IMI89–193 Installing The DXPT1 Line Board
4.2
Detailing The T1 Cable Requirements
Normally, the DXPT1 board connection to a central office is via a network interface box (smart jack). The box is usually small with an 8-pin modular telephone jack for connecting to the customer premise T1 equipment
(DXPT1). For short lengths of approximately 200 feet or less, use a standard telephone cable with an 8-pin modular plug for connection to the DXPT1. Make straight-through connections for pins 1, 2, 4, and 5 when using these plugs on both ends of the cable. (Do not connect Pins 7 and 8.)
When spanning distances greater than 200 feet, use a low-capacitance cable (data-grade cable) having two twisted, solid-conductor wire pairs with shielding. The type of cable with metal shielding covering each twisted pair provides the best immunity from electrical interference. Only connect the shielding to earth ground at one end of the cable—do not ground the shielding at the other end of the cable.
When connecting the local DXP Plus directly to another DXP Plus system, be sure to connect the transmit pair
(pins 4 and 5) of the local system to the receive pair (pins 1 and 2) of the distant system. Likewise, connect the receive pair (pins 1 and 2) of the local system to the transmit pair (pins 4 and 5) of the distant system.
14 – Installing The DXPT1 Line Board
Installing The DXPT1 Line Board IMI89–193
4.3
Understanding The DXP Plus Logical Numbering
Because there are no dedicated station or line ports in the DXP Plus, the system uses an automatic configuration method to logically number its stations and lines. Automatic configuration occurs after you perform a master clear on the system.
How automatic configuration works
With automatic configuration, the system does a search for all installed station and line boards in the main and expansion cabinets, and assigns a logical number for each provided station and line encountered during the search.
The search begins in the main cabinet at the left-most universal slot and proceeds left to right. The search then moves to the upper expansion cabinet where it searches left-most slot to right-most slot. The search finally moves to the lower expansion cabinet where it again searches left-most slot to right-most slot. When automatic configuration is finished, the system has logically numbered all station and line ports in ascending order from the left-most slot to right-most slot throughout the entire system.
How logical number and physical location relate to one another
The logical number of a station or line corresponds to its relationship to other stations or lines in the system but is not dependent upon the board’s placement in the cabinet. The physical location of a station or line corresponds to the order of the system’s board slots. The main cabinet contains slots 1–9, the upper expansion cabinet contains slots 10–20, and the lower expansion cabinet contains slots 21–30. Therefore, even if the first encountered station board is located in slot five of the main cabinet, the system still assigns logical number one to the first station provided by that board. During installation, you can skip slots. For example, you can install eight-line, loop start, line boards in only slots one and 30 if you wish. In this case, slot one yields logical line numbers 1–8 and slot 30 yields logical line numbers 9–17.
Where you can place circuit boards
Each installed board requires timing circuits equal to its capacity. For example, a 16–station board requires 16 timing circuits, an eight–line loop start line board requires eight circuits, and a fully configured T1 trunk board requires 24 timing circuits. In the DXP Plus, each universal slot provides 32 timing circuits. Because of this timing circuit provision of each slot, you can place any station or line board at any slot location with no restrictions.
Adding boards without renumbering
If you install or relocate a station or line board, this board does not operate until you take appropriate programming action. If you use an available open slot for adding or relocating a board, that board’s stations or lines assume logical numbers in sequence after the system’s last assigned logical station or line number. For example, if the system’s last logical station number is 24, the logical numbers of the newly installed board’s stations begin at logical number 25.
After you remove a board and delete it through programming, that board’s logical numbers are available for reassignment. This means that you can remove a board, add or move another board, take the appropriate programming action, and have the stations or lines of the added or relocated board assume the logical numbers made available by the removed board. For example, if the system’s last logical number is 64 and you remove the board providing stations with logical numbers 1–16 and delete it through programming, the stations on an added board assume logical numbers beginning with 1 instead of 65. However, if you remove and program delete an eight-station board and add a 16-station board, the first eight stations stations on the added board assume logical numbers 1–8 and the last eight stations assume logical numbers 65–72.
Remember, should you master clear the system, the automatic configuration feature logically numbers all station and line ports in ascending order from the left-most slot to right-most slot throughout the entire system. This action renumbers those station and lines provided by boards that you have added or relocated since you last performed the system master clear.
Installing The DXPT1 Line Board – 15
IMI89–193 Installing The DXPT1 Line Board
5.0 Installing The Syncronization Card
On The Services Board
Whenever you install one or more DXPT1 boards, and the DXP Plus is receiving its timing signals from an external source, you must install one synchronization card (DXOPT–SYN) on the services board using the following procedure.
NOTE: Whenever you install one or more DXPT1 boards, and the DXP Plus is receiving its timing signals from an external source, you must install one synchronization card (DXOPT–SYN) on the services board. When you connect the system to central office (CO) lines, you must include a synchronization card, and the DXP
Plus must be controlled by CO signalling. In installations where the DXP Plus supplies the clock signal for the distant system, there is no requirement for DXOPT–SYN cards and you do not need to perform this procedure.
1. Switch off the DXP Plus power supply, disconnect the AC power cord from the AC outlet and disconnect the optional battery back-up assembly from the main cabinet power supply
2. Install your static discharge wrist strap on your bare wrist; adjust it for a snug fit. Be sure that the strap is touching bare skin and is not isolated by clothing. Connect the wrist strap cord between the wrist strap and an
AC or earth ground
3. Loosen the retaining hardware and lift the front panel away from the common equipment cabinet.
NOTE: With the common equipment in the installed position, the ground lug on the side of the cabinet is an appropriate grounding point since it should have a heavy ground wire connected between it and a good earth ground.
CAUTION
Do not remove or install the services board while the DXP Plus is powered-on or severe system problems may occur.
4. Locate the services board, loosen the retaining screws, remove it from the main cabinet, place it in a static protection bag, and transport it to the static-safe work area.
5. At the static-safe work area, with your wrist strap in place, remove the services board and the DXOPT–SYN card (if used) from their static protection bags.
6. Refer to the illustration, and install the DXOPT–SYN card at the top position on the services board with the supplied hardware. (Actually, you can use any of the three positions; however, other non-related option cards require installation in the lower positions so it is best to leave these positions open for those other uses.).
7. Use the method detailed in Section 5.1 to set the strapping switches on the services board. If you wish, refer to step 8 for details, and transport the board assembly to the cabinet installation site before you set the strapping switches.
8. Place the services board with the newly installed DXOPT–SYN card into a static protection bag and transport the assembly back to the main cabinet.
16 – Installing The DXPT1 Line Board
Installing The DXPT1 Line Board IMI89–193
Installing The Synchronization Card On The Services Board
Installing The DXPT1 Line Board – 17
IMI89–193 Installing The DXPT1 Line Board
5.1
Configuring The Services and Interface Boards
The DXP Plus extracts clocking information from the central office (CO) that supplies the T1 lines, and routes this information to the DXOPT–SYN sync card. The sync card uses this clocking information to derive the synchronizing signal for the DXPT1 board’s transmit clock signal. Therefore, the DXPT1 board’s transmit clock is slaved to the CO supplying the T1 lines. If there is only one CO supplier, that source is the primary clock source; however, if there are two different suppliers of T1 lines, use the more reliable T1 supplier as the primary source and the other T1 supplier as the secondary source.
You must designate one DXPT1 board as the primary board. Choose this board from among those boards that interface the T1 lines supplied by the primary CO supplier. Designate the primary board by placing straps on the
DXSRV–PLS services board and by setting DIP switches on the expansion cabinet interface boards.
If you system has only one CO supplier, you do not need to designate a secondary board; however, if the system has a second CO supplier of T1 lines, you must designate one DXPT1 board as the secondary board. Choose this board from among those boards that interface the T1 lines supplied by the second CO supplier. Designate the secondary board by placing straps on the services board or by setting DIP switches on the expansion cabinet interface boards.
If you designate primary and secondary boards to the system even though there is only one CO clock source, the
DXOPT–SYN card functions as though it is receiving two clock signals and lights both PRI and SEC LEDs on the front edge of the card.
18 – Installing The DXPT1 Line Board
Installing The DXPT1 Line Board
5.1.1 Summerizing the Strapping
DXPT1 Cabinet Location
Services Board Strap
PRIMARY or SECONDARY*
Expansion Cabinet Interface Board
Switch Setting SWA or SWB**
Main –UNV1
Main–UNV2
Main–UNV3
Main–UNV4
Main–UNV5
Main–UNV6
Main–UNV7
Main–UNV8
Main–UNV9
Upper Expansion–UNV1
Upper Expansion–UNV2
Upper Expansion–UNV3
Upper Expansion–UNV4
Upper Expansion–UNV5
Upper Expansion–UNV6
Upper Expansion–UNV7
Upper Expansion–UNV8
Upper Expansion–UNV9
Upper Expansion–UNV10
Upper Expansion–UNV11
Lower Expansion–UNV1
Lower Expansion UNV2
Lower Expansion UNV3
Lower Expansion UNV4
Lower Expansion UNV5
Lower Expansion UNV6
Lower Expansion UNV7
Lower Expansion UNV8
A
B
C
D
E
F
G
H
I
J or K
J or K
J or K
J or K
J or K
J or K
J or K
J or K
J or K
J or K
J or K
L or M
L or M
L or M
L or M
L or M
L or M
L or M
L or M
3
4
5
1
2
6
7
8
9
10
11
1
2
3
4
5
6
7
8
Lower Expansion UNV9
Lower Expansion UNV10
L or M
L or M
9
10
* Strap PRIMARY block for primary DXPT1 and/or strap SECONDARY block for secondary DXPT1.
** Switches A and B do not designate primary or secondary—they designate the first and second DXPT1 boards installed in an expansion cabinet.
IMI89–193
Installing The DXPT1 Line Board – 19
IMI89–193 Installing The DXPT1 Line Board
5.1.2 Setting The Strapping
Configure the services and interface boards by performing the steps in the following process.
1. Install your static discharge wrist strap on your bare wrist; adjust it for a snug fit. Be sure that the strap is touching bare skin and is not isolated by clothing. Connect the wrist strap cord between the wrist strap and an
AC or earth ground
NOTE: With the common equipment in the installed position, the ground lug on the side of the cabinet is an appropriate grounding point since it should have a heavy ground wire connected between it and a good earth ground.
2. Remove the services board assembly from the static protection bag.
3. Identify the main cabinet board slots where you will install the DXPT1 boards, and the primary and secondary
(if available) CO line supplier. With this knowledge, designate one DXPT1 board as primary and another
DXPT1 board as secondary by placing straps on the services board.
(a) If you install one DXPT1 board in the main cabinet, you must strap one pin-pair (A–I) on the services board’s PRIMARY strap block. This strap designates the main cabinet slot where you installed the
DXPT1 board.
Example: If you install a DXPT1 board in universal slot two in the main cabinet, you must strap pin-pair
B on the PRIMARY strap block .
(b) If you install two or more DXPT1 boards in the main cabinet, you must designate one board as the primary board and another as the secondary board. After you have made these designations, you must strap one pin-pair (A–I) on the services board’s PRIMARY strap block and one pin-pair (A–I) on its
SECONDARY strap block to designate the main cabinet slots where you have installed the primary and secondary boards.This action designates the primary clock source for the DXOPT–SYN card.
Example: If you install two DXPT1 boards in universal slots two and three in the main cabinet and you designate these boards primary and secondary respectively, you must strap pin-pair B on the PRIMARY strap block and strap pin-pair C on the SECONDARY strap block.
20 – Installing The DXPT1 Line Board
Installing The DXPT1 Line Board IMI89–193
4. Identify the expansion cabinet slots where you will install the DXPT1 boards and the primary and secondary
(if available) CO line supplier. With this knowledge, designate one DXPT1 board as primary and another
DXPT1 board as secondary by placing straps on the services board and setting DIP switches on the expansion cabinet interface board.
(a) If you install one DXPT1 board in an expansion cabinet, you must strap one pin-pair (J–M) on the services board’s PRIMARY strap block. This strap designates the expansion cabinet where you have installed the board. You must also close a DIP switch in switch bank A on the expansion cabinet’s interface board to designate the expansion cabinet slot where you installed the DXPT1 board.
Example: If you install the DXPT1 board in universal slot 2 of the upper expansion cabinet, strap pin-pair
J on the PRIMARY strap block, and close SWA–2 on the upper expansion cabinet’s interface board.
(b) If you install two or more DXPT1 boards in an expansion cabinet, you must designate one board as the primary board and another as the secondary board. After you have made these designations, you must strap one pin-pair (J–M) on the services board’s PRIMARY strap block and one pin-pair (J–M) on its
SECONDARY strap block to designate the expansion cabinet where you have installed the primary and secondary boards. You must also close a DIP switch on switch bank A and another on switch bank B on the expansion cabinet’s interface board to designate the expansion cabinet slots where you installed the primary and secondary DXPT1 boards. Do this same procedure if you use both expansion cabinets.
Example: If you install two DXPT1 boards in universal slots two and three in the upper expansion cabinet and you designate these boards primary and secondary respectively, you must strap pin-pair J on the
PRIMARY strap block and strap pin-pair K on the SECONDARY strap block. You also must close
SWA–2 and SWB–3 on the upper expansion cabinet’s interface board.
5. If the system requires DXPT1 boards in both main and expansion cabinets, identify the cabinet slots where you will install the DXPT1 boards and the primary and secondary (if available) CO line supplier. With this knowledge, designate any one DXPT1 board as primary and any other DXPT1 board as secondary by placing straps on the services board and setting DIP switches on the expansion cabinet interface board.
You must either strap one pin-pair (A–M) on the services board’s PRIMARY strap block or strap one pin-pair
(A–M) on its SECONDARY strap block. The DXPT1 board designation of primary or secondary and the cabinet you use for its installation determines which services board pin-pair you use. You must also close a
DIP switch (SWA or SWB, 1–11) on the appropriate expansion cabinet’s interface board to designate the expansion cabinet slot where you installed the opposite DXPT1 board.
Example: If you designate the DXPT1 board that you install in universal slot 2 of the main cabinet as the primary board, strap pin-pair B on the services board PRIMARY strap block. If you designate the DXPT1 board that you install in universal slot 2 in the upper expansion slot as the secondary board, strap pin-pair J on the services board SECONDARY strap block, and close SWA–2 on the upper expansion cabinet’s interface board.
Installing The DXPT1 Line Board – 21
IMI89–193
Services Board
Installing The DXPT1 Line Board
PLUS009
Strapping
Pairs
Upper
Cabinet
Lower
Cabinet
F
G
I
H
J
A
B
C
D
E
K
L
M
J6
J7
Primary Clock
Strapping Block
Secondary Clock
Strapping Block
Locating The Services Board Strapping Blocks
22 – Installing The DXPT1 Line Board
Installing The DXPT1 Line Board IMI89–193
SWA
SWB
Closed
Switch A
Expansion
Cabinet
Slot Locations
1
2
3
4
5
6
7
8
9
10
11
12
Open
Closed
Switch B
Expansion
Cabinet
Slot Locations
1
2
3
4
5
6
7
8
9
10
11
12
Open
Note: SWA-12 and SWB-12 are not used on Interface 2 (upper cabinet). SWA-11/12 and SWB-11/12 are not used on Interface 3 (lower cabinet).
PLUS010
SWA and SWB switches not in use must be in "off"
(open) position!
Expansion Cabinet
Interface Board
Locating The Interface Board DIP Switches
Installing The DXPT1 Line Board – 23
IMI89–193 Installing The DXPT1 Line Board
5.2
Installing The Services Board Assembly
1. With your static discharge wrist strap still properly installed, install the services board in the main cabinet.
2. If the installation includes a DXOPT–SYN card, make sure the lower (larger) slide switch on the front edge of the card is in the up AUTO position. Leave the upper (smaller) switch in either position as it has no effect when the automatic mode is selected.
3. Orient the services board assembly with its top and bottom guides in main cabinet board cage, and press the board firmly until its board edge connection properly mates with the connector on cabinet’s backplane.
CAUTION
When pressing circuit boards into place, press them only at the extractor lever locations. If you apply pressure at other locations you may damage the board assembly.
4. Make a final inspection to ensure that the board assembly is oriented correctly and mated properly.
5. Install and tighten the supplied screws to secure the board assembly to the board cage.
6. If applicable, plug the power cable from the optional external battery assembly into the DXP power supply.
7. Connect the AC power cord to the AC wall outlet and turn the power switch on. If no alarms are on (red
LEDs), and at least one of the green PRI or SEC LEDs is lit, replace the cabinet’s front panel; otherwise, troubleshoot the installation for errors.
24 – Installing The DXPT1 Line Board
Installing The DXPT1 Line Board IMI89–193
PRI
LED
SEC
LED
AUTO
MANUAL
SWITCH
(Set to AUTO
Position)
STATUS
ON = OK
OPBD2
MAIN
CABINET
BATTERY
OUT
OPBD3
OPBD1
PRI
SEC
UNLOCKED
PRI
SEC
DXOPT
SYN
AUTO
MAN
MANUAL
PAGE
BGM
MOH
RELAY 1
RELAY 2
RELAY 3
RELAY 4
COMDIAL
PLUS006
Services Board
Static Discharge
Wrist Strap
Installing The Services Board Assembly
Installing The DXPT1 Line Board – 25
IMI89–193 Installing The DXPT1 Line Board
6.0 Understanding The T1 Alarms And Indicators
Most of the T1 alarms and indicators (LEDs) are located on the front-edge panel of the DXPT1 board, while several are located on the front edge of the DXOPT-SYN card. The following sections discuss the alarms and indicators.
NOTE: Red /Yellow LEDs, when lit, indicate errors or non-standard configuration for normal operation.
Red Alarm (red LED) When this LED indicator is lit, the system cannot establish communications with the network.
Yellow Alarm (yellow LED) The yellow alarm is lit whenever the far end has lost synchronization to its incoming signal. In the superframe format, a transmitted yellow alarm has a zero
(0) bit in the second bit position of every eighth-bit. In the extended superframe format, a transmitted yellow alarm consists of repeating 16-bit patterns containing eight binary one (1) bits followed by eight binary zero (0) bits on the facility data link.
Sync Alarm (red LED) This LED (labeled SYNC LOSS), when lit, indicates that the frame bit in the received data cannot be found.
Signal Alarm (red LED)
Blue Alarm (red LED)
Bipolar Alarm (red LED)
The signal alarm (labeled SIG LOSS) turns on to indicate that the DXP has lost its incoming signal.
When this alarm indicator is lit, the alarm indication signal (AIS) consisting of all one (1) bits is being received to indicate that the far end has lost its received signal. The purpose of this signal is to maintain the system clocks during a link failure.
The system converts the digital bitstream in T1 communications to a bipolar format through a process called alternate mark inversion (AMI). The voltage polarity of the ones pulses (marks) alternates between Plus and minus with a zero
(space) represented by no pulse. A bipolar violation occurs whenever two successive pulses are of the same polarity. This alarm LED indicates a bipolar violation (BPV) has occurred. It is important to note that BPV errors are not passed through regeneration points.
26 – Installing The DXPT1 Line Board
Installing The DXPT1 Line Board IMI89–193
Cyclic Redundancy
Check (red LED)
Slip (red LED)
Unlock (red LED)
When using the ESF format, the cyclic redundancy check (CRC) indicator lights whenever there is a discrepancy in the check sum received for an incoming frame from the originating system and the locally calculated check sum. This discrepancy indicates a data error in the received frame. The CRC is enabled by
DIP switch SW2-4.
This indicator is turned on whenever a frame slip is detected. This is caused by the transmit clock not being synchronized with the receive clock.
The transmit frequency (1.544 Mhz) is not locked with the receive clock when this indicator is lit.
B8ZS)/COFA (green LED) This is a dual-purpose indicator. Depending on how you set DIP switch SW2-6, this indicator reports either a change of frame alignment (COFA) at re-synchronization time (default setting) or bipolar 8-zero substitution (B8ZS) code words detected in the received data.
RLB, LLB, and
PAYL (red LEDs)
Whenever a loopback routine is active, either the remote loopback (RLB), local loopback (LLB), or payback loopback (PAYL) mode (selected by DIP switches
SW2-7 and SW2-8) is indicated by the appropriate LED being lit.
PRI and SEC (green LEDs) The PRI and SEC LEDs on the DXOPT-SYN card light to indicate where the receive clock reference is originating from—the primary or secondary DXPT1 board location. When two or more DXPT1 boards are installed, you make the primary and secondary assignments via jumpers on the the DXAUX board. If only one DXPT1 board is installed, you can set the jumpers so that both LEDs will light.
UNLOCKED (red LED) When lit, the Unlocked LED indicates either the DXOPT-SYN card is defective or the receive frequency is out of tolerance (1.544 Mhz
±
200 Hz).
MANUAL (red LED) This LED, when lit, indicates that the manual mode has been selected via the
AUTO/MANUAL mode switch on the DXOPT-SYN card. When you select the manual mode (normally for maintenance/troubleshooting ), you can select either the primary or secondary timing reference by setting the PRI/SEC switch on the
DXOPT-SYN card. For normal operation, select the automatic mode. Do not manually force the clock reference to primary or secondary if the appropriate green LED is not lit. This will cause the VCO oscillator to default to its minimum or maximum tolerance, and the T1 board(s) may not frequency-lock.
Installing The DXPT1 Line Board – 27
IMI89–193 Installing The DXPT1 Line Board
6.1
Viewing The DXPT1 Board Alarms And Indicators
l
¤ l l l l l l l
¡
LED*
l
¡
¡
¡
¡
¡
¡
¡
¡ l l l
LABEL ERROR OR STATUS CONDITION WHEN LED IS LIT
(Status)
Red
Yellow
Sync
SIG
Blue
Loss of sync with the incoming signal
Loss of incoming signal
Alarm indication signal (AIS) being received (indicates loss of signal at far end)
Bipolar
CRC
Bipolar violation detected
Cyclic redundancy check error in incoming frame if SW2-4
SLIP
Unlock is enabled (ESF only)
Frame slip detected
Transmit frequency (1.544 MHz) not locked with receive clock
B8ZS/COFA B8ZS/COFA (B8ZS zero suppress mode/change of frame alignment) per SW2-6
RLB
LLB
PAYL
Rapid flash = defective board
Steady on = board in wrong slot or board constraints violated
Off with repeated five second blink on = normal operation
(T1 trunk idle)
On with repeated five second blink off = normal operation
(T1 trunk busy)
Communications with network cannot be established
(out-of-service)
Disruption in remote T1 service
Remote loopback active
Local loopback active
Payload loopback active
Diagnostics codes (for factory test only)
Diagnostics codes (for factory test only)
Diagnostics codes (for factory test only)
Diagnostics codes (for factory test only)
Diagnostics codes (for factory test only)
Diagnostics codes (for factory test only)
Diagnostics codes (for factory test only)
Diagnostics codes (for factory test only)
6.2
Viewing DXOPT-SYN Synchronization Card Alarms And Indicators
LED*
¡
¡ l l
LABEL ERROR OR STATUS CONDITION WHEN LED IS LIT
PRI
SEC
Timing reference is present from the DXPT1 primary board
Timing reference is present from the DXPT1 secondary board
UNLOCKED Trouble (defective DXOPT-SYN card or receive frequency out of tolerance (1.544 MHz
±
200 Hz))
MANUAL The manual mode is active for selecting the DXPT1 reference
NOTE: Red /Yellow LEDs, when lit, indicate errors or non-standard configuration for normal operation. Green
LEDs indicate a normal condition.
*LED color legend l = Red ¤ = Yellow ¡ = Green
28 – Installing The DXPT1 Line Board
Installing The DXPT1 Line Board
Primary
Secondary
Unlocked
Status
Manual
DXOPT-SYN
Card
Services Board
Status
Red
Yellow
Sync
Signal
Blue
Bipolar
CRC
Slip
Unlock
B8ZS/COFA
Remote Loopback
Local Loopback
Payload Loopback
IMI89–193
DXPT1 Board
PLUS007
Diagnostic Switches and LEDs for Factory
Use Only
Viewing DXPT1 And DXOPT–SYN Alarms And Indicators
Installing The DXPT1 Line Board – 29
IMI89–193 Installing The DXPT1 Line Board
7.0 Understanding Installer/User
Information Regarding FCC Rules and Regulations
This electronic key system complies with Federal Communications Commission (FCC) Rules, Part 68. The FCC registration label on the DXP Plus contains the FCC registration number, the ringer equivalence number, the model number, and the serial number or production date of the system.
7.1
Notification To Telephone Company
Unless a telephone operating company provides and installs the system, the telephone operating company which provides the lines must be notified before a connection is made to them. The lines (telephone numbers) involved, the FCC registration number, and the ringer equivalence number must be provided to the telephone company.
The FCC registration number and the ringer equivalence number of this equipment are provided on the label attached to the common equipment. The user/installer is required to notify the telephone company when final disconnection of this equipment from the telephone company line occurs.
7.2
Compatibility With Telephone Network
When necessary, the telephone operating company provides information on the maximum number of telephones or ringers that can be connected to one line, as well as any other applicable technical information. The telephone operating company can temporarily discontinue service and make changes which could affect the operation of this equipment. They must, however, provide adequate notice, in writing, of any future equipment changes that would make the system incompatible.
7.3
Installation Requirements
Connection of the electronic key system to the telephone lines must be through a universal service order code
(USOC) outlet jack supplied by the telephone operating company. If the installation site does not have the proper outlet, ask the telephone company business office to install one. The correct outlet jack for this system is either a type RJ21X or type RJ14C.
7.4
Party Lines And Coin Lines
Local telephone company regulations may not permit connections to party lines and coin lines by anyone except the telephone operating company.
7.5
Troubleshooting
If a service problem occurs, first try to determine if the trouble is in the on-site system or in the telephone company equipment. Disconnect all equipment not owned by the telephone company.
If this corrects the problem, the faulty equipment must not be reconnected to the telephone line until the problem has been corrected. Any trouble that causes improper operation of the telephone network may require the telephone company to discontinue service to the trouble site after they notify the user of the reason.
7.6
Repair Authorization
FCC regulations do not permit repair of customer owned equipment by anyone except the manufacturer, their authorized agent, or others who might be authorized by the FCC. However, routine repairs can be made according to the maintenance instructions in this publication, provided that all FCC restrictions are obeyed.
30 – Installing The DXPT1 Line Board
Installing The DXPT1 Line Board IMI89–193
7.7
Radio Frequency Interference
The electronic key system contains incidental radio frequency generating circuitry and, if not installed and used properly, may cause interference to radio and television reception. This equipment has been tested and found to comply with the limits for a Class A computing device pursuant to Subpart J of Part 15 of FCC Rules. These limits are designed to provide reasonable protection against such interference when operated in a commercial environment. Operation of this equipment in a residential area may cause interference to radio and television reception; in which case the user is encouraged to take whatever measures may be required to correct the interference. If this equipment does cause interference to radio or television reception, which can be determined by turning the equipment off and on, the user is encouraged to try to correct the interference by one or more of the following measures: Reorient the television or radio’s receiving antenna, and/or relocate the DXP, the individual telephone stations, and the radio or TV with respect to each other. If necessary, the user should consult the manufacturer or an experienced radio/television technician for additional suggestions. The user may find the following booklet prepared by the Federal Communications Commission helpful: “How to Identify and Resolve
Radio-TV Interference Problems.” This booklet is available from the Government Printing Office, Washington
D.C. 20402. Stock No. 004-000-00345-4.
This equipment has been tested and found to comply with the limits of a Class A digital device, pursuant to Part
15 of the FCC Rules. These limits are designed to provide reasonable protection against harmful interference when the equipment is operated in a commercial environment. This equipment generates, uses, and can radiate radio frequency energy and, if not installed and used in accordance with the instruction manual, may cause harmful interference to radio communications. Operation of this equipment in a residential area is likely to cause harmful interference in which case the user will be required to correct the interference at his own expense.
This digital apparatus does not exceed the (Class A) limits for radio noise emissions from digital apparatus set out in the Radio Interference Regulations of the Canadian Department of Communications.
Le pre’sent appareil nume’rique n’emet pes de bruits radioe’lectriques de’passant les limites applicables aux appareils nume’riques (de la class A) prescrites dans le Re’glement sur le brouillage radioe’lectrique e’dicte’ par le ministe’re des Communications du Canada.
CAUTION
Changes or modifications to this unit not expressly approved by the party responsible for compliance could void the user’s authority to operate the equipment.
Installing The DXPT1 Line Board – 31
IMI89–193 Installing The DXPT1 Line Board
7.0
Knowing The Specifications
DXP Capacity
Modes
Framing
Channels Allocated
Industry Standards
Maximum Output
10 T1 boards
Superframe, extended superframe
D4
8, 16, or 24
ANSI T1.403-1989
AT&T PUB 62411
2.4V to 3.6V base to peak, short circuit protection to 120 mA, rms
1.544 Mbps Line Rate
Line Code
Type
Zero Suppression
Receive Sensitivity
Impedance
DXP Loss Insertion
Transmit
Receive
T1 Connector
T1 Cable
Bipolar AMI
B7 or B8ZS selectable
-26 dB or -36 dB selectable
100 Ohms
-6 dB (selectable to 0 and -3 dB per channel)
0 dB
RJ48C, miniature 8-position, shielded
(per ANSI T1-403, 1989)
Up to 6,000 feet between DXPs, 22 AWG, twisted-pair, no external components
Built-in; CPE or CARRIER selectable (ESF) CSU Function
Transmit Attenuation
Manual
Automatic
Input Jitter Tolerance
Surge Protection
Elastic Store
Compliance
0, -7.5, -15, or -22.5 dB selectable
Default
138 UI @ 1 Hz; 0.4 UI @ 10 KHz—100 KHz
(0 dB line); corner frequency = 6 Hz (attenuates
20 dB per decade above corner)
1 AMP fuse and transient protection for metallic
>6 volts P-P; Longitudinal (tip—ring and chassis ground) protection 1500 volts minimum.
Two frames, no frame loss when slipping
FCC Part 68/Doc
FCC Part 15
UL-1489/CSA (safety):
Yellow Alarm Type
Superframe Mode
Extended Superframe Mode
Bit 2 zero in all channels or Japanese 12th frame method, selectable
Alternating bytes = all zeros and all ones;
(prohibiting ANSI FDL messaging during yellow alarms is selectable)
Signaling
Signaling Protocols
Dialing
Protocol Type (DID, E&M)
DID Type Restriction
Loop Start (subscriber end)
Ground Start (subscriber end)
E & M
Direct Inward Dial (DID)
DTMF or Dial Pulse
Wink, Delay-Dial, and Immediate Start
(dial pulse only for immediate start)
Limited to four of five types when mixing tone/dial pulse/wink/delay dial/immediate start)
Clocking
Synchronization
Min. RX Freq. Capture
TX Master Mode Freq.
Slave mode from DXOPT-SYN card on
Auxiliary board
1.544 MHz
±
200 Hz, T1 board;
16.384 MHz
±
2048 Hz, Sync card
1.544 MHz
±
75 Hz
Loopback Modes
Superframe Mode
Extended Superframe Mode
LED Alarms/Errors
Local or remote loopback, manual
Network loopback inband command; set 00001 5sec, reset 001 5 sec.
Local, remote, payload loopback (manual)
FDL ANSI network remote loopback
FDL ANSI network payload loopback
Status
Red Alarm
Yellow Alarm
Blue Alarm
Loss of receive synchronization
Loss of signal
Bipolar error(s)
CRC errors (ESF)
Slip errors
Phase Lock error
Facilities Interface Code (FIC) 04DU9–1SN
32 – Installing The DXPT1 Line Board
Installing The DXPT1 Line Board IMI89–193
8.0 Defining The T1 Terms
Bipolar
A bipolar signal is composed of alternating pulses that both represent a digital logic 1. The positive pulse is a (+) and the negative pulse is a (-). Zero volts represents a space, or digital logic 0.
Bipolar Violation (or error)
A bipolar error is a digital logic 1 (or mark) that has the same polarity as its predecessor.
NOTE: Every time the system regenerates the signal stream, it corrects any bipolar errors; therefore, it prevents end-to-end error checking from using bipolar errors.
B8ZS (Binary Eight Zero Substitution)
This is a technique to send an all-zero channel without violating the ones-density requirement (a single one in each channel and no more than 15 zeros in a row). Voice transmission will not allow an all zero channel. The system accomplishes B8ZS suppression by inserting a special bipolar error that is interpreted, not as an error, but an all zero channel. The B8ZS feature replaces the all-zero channel two different ways. The feature replaces the all-zero channel with the sequence 000 + - 0 - + if the preceding pulse was a +, and the feature replaces the all-zero channel with the sequence 000 - + 0 + - if the preceding pulse was -. The + represents a positive pulse, the - represents a negative pulse, and 0 represents no pulse. Set the B8ZS feature with switches SW1–5 and
SW1–6.
CAS (Channel Associated Signalling)
The Channel Associated Signalling is the only inbound signalling method currently supported by the DXPT1 board.
COFA (Change of Frame Alignment)
When switch SW2-6 is off, the green LED on the DXPT1 indicates whether the network source or the network span caused the last frame synchronization. (This indication disregards the first re-sync at cold start or a system reset —cold start and reset causes the network source to re-sync.) A COFA occurs if the network source does a re-sync. The COFA is a diagnostic tool that identifies the source of the loss of frame synchronization.
CPE/Carrier Equipment
The DXPT1 is normally classified as Customer Premise Equipment (CPE). If you use SW2–2 to configure the
DXPT1 board to use the internal CSU while in the ESF mode, the network may require that the system be classified as Carrier Equipment (CE). The information packet that the DXPT1 board sends to the network contains a facility data link (FDL) maintenance message that has a bit in it that provides this identification.
CRC (Cyclic Redundancy Check)
A method of checking errors from the transmission source to the destination. For T1 operation, CRC caculates a checksum depending on the data in a frame. The system uses CRC in ESF mode exclusively. (You must enable
CRC with DIP switch SW2-4).
Delay Dial E&M, DID Protocol Type
Once seized by a calling system, the system being called makes A=1 and B=1 until it is ready to receive digits.
When it is ready to receive digits, it makes A=0 and B=0. The system uses a delay dial protocol when wink protocol timing is not compatible to the network.
Dial Pulse – T1
Dial pulse is a method of sending address digits (numbers) using A and B bits logic bits instead of sending DTMF tones. Some carriers may not support dial-pulse signalling. While the method is slower when compared with tones, it requires no DTMF receivers.
Installing The DXPT1 Line Board – 33
IMI89–193 Installing The DXPT1 Line Board
Direct Inward Dial (DID) T1 Trunk
DID is a protocol for inbound calls where the network sends the extension number during the beginning of the call. The system supports the 0 through 7 inbound digits. The network does not translate the digits to a valid extension—the system’s DID translation tables perform this action.
DS-0 (Digital Signal-Level Zero)
Digital Signal-Level Zero is a single 64Kbit channel inside a T1 span.
E & M T1 Trunk
E&M is a signalling protocol that supports both inbound and outbound digits. Inbound digits from the network are already translated to a 3–digit or 4–digit valid extension. E & M is symmetrical from both ends and ignores the subscriber/office classification of other trunks. Use this signalling protocol for interconnecting two DXP Plus systems.
Extended Superframe Mode (ESF)
Extended Superframe Mode consists of 24 frames. The frame bit uses only 6 frames leaving 18 bits for other purposes. These spare 18 bits provide 6 bits for CRC information and 12 bits for a facility data link. The facility data link is for maintenance information (as defined by the ANSI T1.403 specification). Like the superframe mode, the 64–Kbit user channels have 24 frames available for use.
Ground Start T1 Trunks
Ground start is a call signalling protocol that monitors only outbound digits and supports disconnect supervision.
Ground start protocol supports only the subscriber end of the communications link
FDL (Facility Data Link)
The Facility Data Link is a 4–Kbit communication link from the network to the DXPT1 board only when the board is operating in the ESF mode. The system sends preemptive messages (for example, yellow alarm and loopback), if needed, and sends error packets to the network once a second. The packets contain alarm history in accordance with the ANSI T1.403 specification.
Fractional T1
Fractional T1 is a T1 span where the user uses less than 24 channels. The DXPT1 board allocates eight or 16 channels to a fractional T1 but does not reallocate unused channels in the eight, 16, or 24 mode to other resources.
A fractional T1 in ESF mode will nullify the CRC and other error checking capability since the network shares channels.
Immediate Start Protocol State
Once a calling system seizes a called system, the calling system sends address digits to the called system without requiring an acknowledgement. Inbound immediate start protocol does not support tone dial. Dial-pulse is adequate however. Immediate start protocol is applicable to DID and E&M tie lines.
Inband Signalling
A signalling method where the system sends overhead signalling along with channel traffic.
ISDN (Integrated Services Digital Network) Primary Rate (also called PRI)
Currently not offered by the DXPT1 board.
Loopback Local
An operation method that loops the DXPT1 board’s transmit output and receive input paths. The loopback terminates all traffic and halts call processing. While in this idle condition, the system continues to transmit the T1 transmit stream to the network but it will not answer incoming calls. If the remote T1 equipment is the clock source (primary or secondary) for the DXOPT-SYN card, the remote equipment terminates the reference signal because the network receive circuit is open in local loopback. You initiate local loopback by setting the appropriate SW1 switches. The main purpose of local loopback is to verify the DXPT1 board’s ability to synchronize properly. Loopback local operation is applicable to superframe adn extended superframe modes.
34 – Installing The DXPT1 Line Board
Installing The DXPT1 Line Board IMI89–193
Loopback Payload
The loopback payload feature is an ESF-only method of loopback which loops the network receive input path to the remote T1 equipment’s transmit output path. This loopback method does not loop the first bit of each frame to allow the DXPT1 board’s facility data link to continue to transmit maintenance information. You can use switches
SW2–7 and SW2–8 to manually initiate the payload loopback or you can allow the network to send an FDL message to initiate or restore the payload loopback. The DXPT1 board goes out-of-service during the loopback time.
Loopback Remote
The loopback remote feature loops the network receive input path to the remote T1 equipment’s transmit output path. The remote loopback feature terminates all traffic and halt any call processing. You can use the SW2 switches to manually initiate remote loopback or you can allow the network to remotely initiate the condition. In superframe mode with SW2–1 set to on, the network can send a special in-band pattern
(00010001000100010001.... min 5 seconds) to cause the DXPT1 board to automatically enter the remote loopback mode. The network can disable the loopback by sending a different in-band pattern
(001001001001001001001.... min 5 seconds). In ESF mode, the DXPT1 board’s facility data link, or maintenance channel, can enable and disable remote loopback automatically or you can set SW2–7 on and SW2–8 off to manually enable remote loopback or set both switches off to manually disable the feature. Loopback remote operation is applicable to superframd and extended superframe modes.
LIU Line Interface Unit
The line interface unit is the interface between the T1 copper wires and the DXPT1 board’s framing circuitry.
The LIU is responsible for separating the 1.544MHZ receive clock from the incoming stream and converting bipolar Alternate Mark Inversion (AMI) to 5–volt digital logic. The LIU also supports the automatic line build-out that regulates the transmit level according to the receive strength (LIU-2 switch).
Loop Start T1 Trunk
Loop Start T1 Trunk is a network protocol that monitors outbound digits to the DXPT1 board. This protocol does not support disconnect supervision. Loop start protocol supports the subscriber end of the communications path but does not support the office (network) end.
Primary Clock Reference
The straps on the DXAUX board designate the primary clock reference. Primary clock reference is the first choice reference clock used to synchronize the DXP Plus to the incoming span. If the system looses synchronization, it uses its secondary clock reference. If the secondary clock reference is not available, the DXOPT-SYN card’s variable clock oscillator (VCO) switches to the fixed oscillator on the DXSRV (services) board. When it does this, slips occur.
Repeater
A repeater is a amplifying device that central office technicians place at approximately one mile intervals along a
T1 circuit to boost the T1 signal. The T1 specifications allow a maximum of 50 repeaters along a communications path.
Slip
This term describes the condition that exists when the transmit 1.544 MHz clock is different from the receive
1.544 MHz clock. When the system collects or looses a frame of information due to the span frequencies being different, the system generates a slip error. Slip does not affect voice transmissions and may not affect modem traffic; however slip does effect digital data traffic. The DXPT1 board does not currently support digital data traffic. Also, at times a central office takes a T1 span out of service if too many slips occur—one or two a day is permissible (the carrier supplier will furnish you with an an exact number if you request that information from them).
Installing The DXPT1 Line Board – 35
IMI89–193 Installing The DXPT1 Line Board
Smart-Jack (Network Interface Box)
A smart jack is a demarcation box provided by the central office. A smart jack provides isolation and increased signal drive (up to one mile) and can respond to loopback commands for diagnostic purposes. The central office usually provides an 8–pin modular jack for T1 equipment connection. Pin 1 of the modular jack goes to pin 1 of the DXPT1 modular jack, and so on. Only pins 1 and 2 (DXPT1 receive), 4 and 5 (DXPT1 transmit) require connecting.
Superframe Mode (SF)
The standard T1 mode consists of 12 frames per superframe cycle. The first frame bit remains constant and rotates through a 12-bit pattern. By identifying the frame pattern, the system can select the sixth and twelfth frame for the AB bit signalling inband method. T1 parameters allow for 24 64–Kbit user channels.
Suppression
Suppression is a means to prevent more than 15 zeros in a row and not less than 1 pulse (mark) per channel. The
DXPT1 board supports two suppression methods. These are the B7 method and the B8ZS method (selected by
SW1–5 and SW1–6). The B7 method inserts a logic 1 in the seventh bit position of a channel if all bits are zeros.
The B8ZS method inserts a bipolar violation that will be identified and stripped at the receiving end (selected by switches SW1–5, and SW1–6). Voice coding should not allow an all zero channel.
Unlock Alarm
On a normally operating DXPT1 board, the unlock alarm LED is always off. If this LED is on, it indicates that the phase lock loop creating the transmit 1.544 MHz frequency is defective. For this indicator to be meaningful, the DXOPT-SYN card must be synchronized (no red LEDs on). If the DXOPT-SYN card is not synchronized, you must correct that situation.
Wink E&M, DID Protocol State
This effect is a quick response by a called system (A=1, B=1) to a calling system that seized the line. The response indicates that the called system is ready to receive address digits.
Yellow Alarm
The yellow alarm indicates that the network has lost its incoming frame synchronization. The DXPT1 board signalling is inactive for approximately three to four seconds during this alarm time, and the system halts all call processing. If the system clears the received yellow alarm within the time limit, the DXPT1 board’s inactive state terminates and call processing continues.
The system sends a yellow alarm to the network if it loses incoming frame synchronization or if the DXPT1 loses communications to the CPU board. Received and transmitted yellow alarms can not exist at the same time. If such a situation occurs, the system inhibits the transmitted alarm.
ZBTSI (Zero Byte Time Slot Interchange)
Zero Byte Time Slot Interchange is a complex technique to insure that the T1 transmission meets the pulse density requirement. This ZBTSI technique is unpopular in the telephone industy, and the DXPT1 board does not support the feature.
Accredited by the Dutch Council for Certification for certification and registration activities.
Comdial’s Quality Management System Is
Certified To The ISO 9001 Standard.
R
Charlottesville, Virginia 22901-2829
World Wide Web: http://www.comdial.com/
Installing The Serial Data Modem
In The DXP Plus Digital Communications System
1.1
Understanding The Modem
The serial data modem allows remote servicing and programming of the DXP Plus digital communications system. The DXMDM is a general-purpose, Hayes*-compatible, serial data modem that receives its operating power and configuration programming from the DXP Plus. The modem’s operating parameters appear in the following chart.
* Hayes is a registered trademark of Hayes Microcomputer Products
BPS Out
2400
BPS In
2400
Data Bits
8
Stop Bits
1
Parity
None
Flow Control
None
R
Power
Cord
PWR
Status
SER
IAL
Line
Serial Port
Cord
Detailing The Serial Data Modem
PLUS013
This manual has been developed by Comdial Corporation (the “Company”) and is intended for the use of its customers and service personnel. The information in this manual is subject to change without notice. While every effort has been made to eliminate errors, the Company disclaims liability for any difficulties arising from the interpretation of the information contained herein.
The information contained herein does not purport to cover all details or variations in equipment or to provide for every possible contingency to be met in connection with installation, operation, or maintenance. Should further information be desired, or should particular problems arise which are not covered sufficiently for the purchaser’s purposes, contact Comdial, Inside Sales Department,
Charlottesville, Virginia 22906.
Printed in U.S.A.
IMI89-185.01
7/95
IMI89–185 Installing The Serial Data Modem
1.2
Installing The DXMDM Modem
The following procedure explains how to install the serial data modem. Figure 1 illustrates the relative position of the modem and the location of its connections. The modem fits on the left side of the equipment shelf.
1. Locate DIP switch SW7 on the services board, and set it to its OFF position.
2. Insert the modem as illustrated in Figure 1.
3. Attach the modem to the equipment shelf with a single screw through the mounting-screw hole on the modem’s front plate.
4. Connect the PWR cable from the modem to the jack labeled Modem Power on the CPU board. The modem’s
STAT light should come on.
NOTE: The serial data modem comes from the factory with the PWR and serial port cables already installed.
They are purposefully difficult to remove; however, you can disconnect the cables for replacement if necessary. To do so, reach into the opening and press the tab down to release the connector while you pull the cable out from the jack.
5. Connect the serial port cable from the modem to the jack labeled Modem Com (serial data port) on the CPU board. This is the default port for the modem. When you use this connection, you will not need to take any programming action. Alternately, you can connect the modem to one of the serial data ports provided by the communications card installed on the auxiliary board (if one is installed on your system). If you use a a serial data port other than the default port, you must assign it for modem operation using the database programming procedure.
6. Connect a telephone line into the modem’s line jack.
7. Set DIP switch SW7 to its ON position to ensure continuous modem operation. This step is necessary because the serial data modem depends upon the DXP Plus for both its power and configuration. With switch SW7 set
ON, the system automatically matches the baud rate and serial data parameters of the modem regardless of which port you choose for modem connection.
CAUTION
If you disconnect the modem PWR cord from the DXP Plus, you must reset the modem after you reconnect the PWR cord. Set switch SW7 to OFF, wait five seconds, and then return it to ON to reset the modem.
(You can also reset the modem from the programming station. To do so, enter the system-manager
programming mode and then dial 18#).
2 – Installing The Serial Data Modem
Installing The Serial Data Modem
Power
Cord
PWR
Status
SER
IAL
Line
Serial Port
Cord
Telephne Line Cord
IMI89–185
PLUS014
Figure 1. Installing The Modem In The Main Cabinet
Telephone Line Jack
Serial Port Cord
Equipment Shelf
Power Cord
Modem
Power Jack
Default
Modem
Communications
Jack
DIP
Switches
CPU Board
PLUS015
Figure 2. Viewing Modem Position And Connection Locations
Installing The Serial Data Modem – 3
Installing A Dual Tone Multiple Frequency (DTMF)
Receiver Card In The DXP Plus Digital Communications
System
1.0 Introducing The DTMF Receiver Card
The DXP Plus digital communications system supports the use of on-premise industry-standard telephones.
To support the DTMF dialing of industry standard telephones, the DXP Plus services board provides on-board
DTMF receiver circuitry. This circuitry supports dialing of one industry-standard telephone at a time. This provision is adequate, if your site requires only a few industry-standard telephones; however. if you intend to support a population of industry-standard telephones that will generate a large volume of outgoing call traffic, you must install one or more DTMF receiver cards to provide additional DTMF receivers for the telephones. Each
DXOPT–TON card allows four industry-standard telephones to dial simultaneously. The number of cards that you need to install in the system depends upon how active the industry-standard telephones will be at the site. See
Section 1.1 for details.
If you do need to add receiver cards, you have three choices as to where to install them.
1. The best and recommended choice is to add one receiver card to top position on the main cabinet’s services board.
NOTE: You can add two additional receiver cards to the lower two positions on the services board; however, you must take specific programming action to enable their use (the name of this program option is: Services
DTMF Highway). If you add these two cards and take this program option, you can only add one card to the lower expansion cabinet’s interface board (discussed in step 2 below).
2. The second best choice is to add up to three receiver cards to each expansion cabinet’s interface board if one or both is available. Remember, add only one card to the lower expansion cabinet’s interface board if you have added or will add two additional receiver cards to the lower two positions on the services board and take programming action to enable their use
3. The third choice is to add an auxiliary board to the system and install up to four DTMF receiver cards on it.
This is the least desirable choice because it requires you to occupy a board slot that you could otherwise use for line or station boards.
R
This manual has been developed by Comdial Corporation (the “Company”) and is intended for the use of its customers and service personnel. The information in this manual is subject to change without notice. While every effort has been made to eliminate errors, the Company disclaims liability for any difficulties arising from the interpretation of the information contained herein.
The information contained herein does not purport to cover all details or variations in equipment or to provide for every possible contingency to be met in connection with installation, operation, or maintenance. Should further information be desired, or should particular problems arise which are not covered sufficiently for the purchaser’s purposes, contact Comdial, Inside Sales Department,
Charlottesville, Virginia 22906.
Printed in U.S.A.
IMI89-186.01
7/95
IMI89–186 Installing The DTMF Receiver Card
1.2
Determining The Board Configuration That You Will Need
Use the following specifications to determine the maximum number of station boards and DTMF receiver cards that you may need.
•
Each eight-station board supports up to eight telephones. (It will actually support 16 telephones—two telephones at each port sharing a common intercom number.)
•
Up to two industry-standard telephones can be bridged at one station port as long as you do not exceed a combined ringer equivalence number, or REN, of 2.0. (Remember, with two telephones at the same port, they share a common intercom number.)
•
Each 16-station board supports up to 16 telephones. (It will actually support 32 telephones—two telephones at each port sharing a common intercom number)
•
Up to two industry-standard telephones can be bridged at one station port as long as you do not exceed a combined ringer equivalence number, or REN, of 2.0. (Remember, with two telephones at the same port, they share a common intercom number.)
•
Each receiver card allows four industry-standard telephones to dial simultaneously. (The number of cards that you need to install in the system will depend upon how active the industry-standard telephones will be at the site.)
•
You can install one receiver card in the top position on the services board. The services board always provides on-board DTMF receiver circuitry capable of supporting simultaneous dialing of one industry-standard telephone. With the addition of a receiver card, the services board supports simultaneous dialing of five industry-standard telephones. You can add two additional receiver cards to the lower two positions on the services board; however, you must take specific programming action to enable their use
(this program feature name is: Services DTMF Highway). With these additional two cards, the services board supports simultaneous dialing of 13 industry-standard telephones.
•
You can install three receiver cards on the upper and lower expansion cabinet interface boards. With three receiver cards installed, each interface board supports simultaneous dialing of 12 industry-standard telephones.
CAUTION
If you add two additional receiver cards to the lower two positions on the services board, you can add only one receiver card to the lower expansion cabinet’s interface board..
•
You can install four receiver cards on an auxiliary board. With four receiver cards installed, an auxiliary board supports simultaneous dialing of 16 industry-standard telephones (Remember, while you can install up to five auxiliary boards in the system, each auxiliary board that you use occupies a slot where you could install a station or line board.)
Based upon the above specifications, a fully-equipped DXP Plus system with a minimum of one line board and
no auxiliary boards will provide the following industry-standard telephone support:
• main cabinet (reserving one slot for a line board) supports 128 telephones (eight 16-station boards times 16 station ports per board—256 telephones with two telephones per station port sharing the same extension number),
• upper expansion cabinet supports 176 telephones (eleven 16-station boards times 16 station ports per board—352 telephones with two telephones per station port sharing the same extension number),
• lower expansion cabinet supports 160 telephones (ten 16-station boards times 16 station ports per board—320 telephones with two telephones per station port sharing the same extension number).
These individual totals add together to provide a system support total of 464 telephones (The total is 928 telephones with two telephones per station port sharing the same intercom number.)
2 – Installing The DTMF Receiver Card
Installing The DTMF Receiver Card IMI89–186
You can configure the system so that a maximum of 29 of these telephones can dial simultaneously.
• services board circuitry that supports one telephone plus one receiver card that supports four telephones provides support for six simultaneously dialing telephones
• upper expansion cabinet interface board with three receiver cards supports 12 simultaneously dialing telephones
• lower expansion cabinet interface board with three receiver cards supports 12 simultaneously dialing telephones
If you add the maximum of five auxiliary boards and install four receiver cards on each board, you can increase
the simultaneous dialing capacity to 109 telephones but you reduce the maximum telephone capacity to 384.
(The total is 788 telephones with two telephones per station port sharing the same extension number.)
1.2.1 Calculating Your Receiver Card Needs
You can use the following formula to determine how many receiver cards that you must install in your system.
(Simultaneous Dialing Telephones) - (1 Telephone Supported By Services Board)
( 4 Telephones Per Card)
= Receiver Cards
As an example, the system maximum is as follows: (110 - 1)
÷
4 = 27 cards
If you are not sure how many telephones will dial at the same time in your system, you can use the following typical system averages and formula to arrive at a usable estimate.
A typical telephone system, experiences the following call traffic percentages. Your system may be similar.
•
Light Call Traffic = up to 15 percent of the telephones dial simultaneously
•
Moderate Call Traffic = up to 20 percent of the telephones dial simultaneously
•
Heavy Call Traffic = up to 30 percent of the telephones dial simultaneously
(Percent Of Simultaneous Dialing) x (Installed Telephones) = (Simultaneous Dialing Telephones)
For example, the formula for the system’s maximum values is as follows: .286 x 384 = 110 telephones
1.3
Complying With Underwriters Laboratories Regulations
Per The Underwriters Laboratories regulation 1459, 2nd edition, be aware of the following precautions when installing telephone equipment that is to be directly connected to the telephone company network:
•
Never install telephone wiring during a lightning storm.
•
Never install telephone jacks in wet locations unless the jack is specifically designed for wet locations.
•
Never touch uninsulated telephone wires or terminals unless the telephone line has been disconnected at the network interface.
•
Use caution when installing or modifying telephone lines.
Installing The DTMF Receiver Card – 3
IMI89–186 Installing The DTMF Receiver Card
2.0 Installing Circuit Boards
CAUTION
Circuit boards are susceptible to damage caused by electrostatic discharge, and you must keep this fact in mind as you handle the circuit boards.
Refer to the Comdial publication IMI01-005, Handling Of
Electrostatically Sensitive Components, for general information. Specific handling precautions are also included in this installation instruction.
2.1
Creating A Static Safe Work Area
When servicing the common equipment cabinet at the installation location, it is a good practice to place a conductive mat in front of the cabinet area and ground the mat to a good earth ground. (The third wire ground of the AC power line is also an acceptable grounding point.) The grounded conductive mat provides a safe static electric discharge path.
When removing the common equipment cabinet from the installation location for servicing, it is a good practice to prepare a static-safe work area on which to place the cabinet.
You should supply yourself with a static discharge wrist strap, and wear it every time you handle electronic circuit boards either at the cabinet mounting location or at your work area.
4 – Installing The DTMF Receiver Card
Installing The DTMF Receiver Card IMI89–186
PLUS035
Expansion
Cabinet
Common
Equipment
Cabinet
Static Discharge
Wrist Stap
Expansion
Cabinet
Conductive
Mat
1 Meg Ohm
Resister
Earth
Ground
Providing Static Protection At The Cabinet Mounting Location
Static
Wrist
Strap
Common Point Ground
ESD Protective
Mat
ESD Protective
Worksurface
Typical Earth
Ground
Static 2
ESD Protective
Mat
Creating A Static Safe Work Area
Installing The DTMF Receiver Card – 5
IMI89–186 Installing The DTMF Receiver Card
3.0 Installing The Receiver Card
You can install one receiver card in the top position on the services board. You can add two additional receiver cards to the lower two positions on the services board; however, you must take specific programming action to enable their use (this program feature name is: Services DTMF Highway). You can install three receiver cards on the upper and lower expansion cabinet interface boards.
CAUTION
If you add two additional receiver cards to the lower two positions on the services board, you can add only one receiver cards to the lower expansion cabinet interface board.
1. Be sure you are standing on the conductive mat that you have placed in front of the cabinet area and grounded to a good earth ground. (The third wire ground of the AC power line is an acceptable grounding point if the
AC wall jack is properly grounded.) The grounded conductive mat provides a safe static electric discharge path.
2. Install your static discharge wrist strap on your bare wrist; adjust it for a snug fit. Be sure that the strap is not isolated by clothing. Connect the wrist strap cord between the wrist strap and an AC or earth ground.
NOTE: With the common equipment in the installed position, the ground lug on the side of the cabinet is an appropriate grounding point since it should have a heavy ground wire connected between it and a good earth ground.
3. Turn off the power to the system and disconnect the optional battery back up equipment.
4. Loosen the retaining hardware, and lift the front panel away from the common equipment cabinet.
5. Loosen the retaining hardware and remove the services board from the cabinet, place it in a static protection bag, and transport the board to the static-safe work area. Do the same for the interface board if you plan to add a receiver card to it. Further, if the common equipment cabinet contains an auxiliary board and you plan to add the receiver card to it, follow the same procedure.
6. At the static safe work area, with your wrist strap in place, remove the circuit boards and receiver cards from their static protection bags.
7. Referring to the illustrations on the next page, orient the host circuit board and the receiver card, and attach them with the supplied hardware.
8. Place the host circuit board and the newly installed receiver card into a static protection bag and transport them back to the common equipment cabinet.
9. With your static strap on your wrist, remove the board assembly from the static protection bag and install the board in its designated board slot.
CAUTION
When pressing circuit boards into place, press them only at the extractor lever locations.
If you apply pressure at other locations you may damage the board assembly.
9. Make a final inspection to ensure that the board assembly is oriented correctly and mated properly.
10. Install and tighten the supplied screws to secure the circuit board assembly to the board cage.
10. Plug the AC line cord into the AC outlet, reconnect any battery back up equipment, and turn on the switch on the power supply.
11. Replace the front panel on the common equipment cabinet.
6 – Installing The DTMF Receiver Card
Installing The DTMF Receiver Card
Upper Expansion Cabinet
Interface Board
Receiver Card
(3 Places)
Services Board
IMI89–186
Receiver Card
(1 Place)
Lower Expansion Cabinet
Interface Board
Receiver Card
(1 Place)
DXOPT-TON
(2 Places If
Programmed
-See Text)
Auxiliary Board
Receiver Card
(4 Places)
Receiver Card
(2 Places -
See Text Details)
PLUS060
Connecting The Receiver Card To Its Host Circuit Board
Installing The DTMF Receiver Card – 7
Installing The Ring Generator Assembly
In The DXP Plus Digital Communications System
1.0 Introducing The Ring Generator Assembly Installation
The DXP Plus digital communications system supports the use of on-premise industry-standard telephones. To do this, it requires a ring generator assembly to supply ringing voltage to the industry-standard telephones to signal incoming calls.
Regardless of the number of installed industry-standard telephones, you will need to install one ring generator for the main cabinet and one ring generator for each expansion cabinet if the site includes expansion cabinets.
1.1
Complying With Underwriters Laboratories Regulations
Per The Underwriters Laboratories regulation 1459, 2nd edition, be aware of the following precautions when installing telephone equipment that is to be directly connected to the telephone company network:
•
Never install telephone wiring during a lightning storm.
•
Never install telephone jacks in wet locations unless the jack is specifically designed for wet locations.
•
Never touch uninsulated telephone wires or terminals unless the telephone line has been disconnected at the network interface.
•
Use caution when installing or modifying telephone lines.
R
This manual has been developed by Comdial Corporation (the “Company”) and is intended for the use of its customers and service personnel. The information in this manual is subject to change without notice. While every effort has been made to eliminate errors, the Company disclaims liability for any difficulties arising from the interpretation of the information contained herein.
The information contained herein does not purport to cover all details or variations in equipment or to provide for every possible contingency to be met in connection with installation, operation, or maintenance. Should further information be desired, or should particular problems arise which are not covered sufficiently for the purchaser’s purposes, contact Comdial, Inside Sales Department,
Charlottesville, Virginia 22906.
Printed in U.S.A.
IMI89-187.01
7/95
IMI89–187 Installing The Ring Generator Assembly
2.0 Creating A Static Safe Work Area
When servicing the common equipment cabinet at the installation location, it is a good practice to place a conductive mat in front of the cabinet area and ground the mat to a good earth ground. (The third wire ground of the AC power line is also an acceptable grounding point.) The grounded conductive mat provides a safe static electric discharge path.
When removing the common equipment cabinet from the installation location for servicing, it is a good practice to prepare a static-safe work area on which to place the cabinet.
You should supply yourself with a static discharge wrist strap, and wear it every time you handle electronic circuit boards either at the cabinet mounting location or at your work area.
2 – Installing The Ring Generator Assembly
Installing The Ring Generator Assembly IMI89–187
PLUS035
Expansion
Cabinet
Common
Equipment
Cabinet
Static Discharge
Wrist Stap
Expansion
Cabinet
Conductive
Mat
1 Meg Ohm
Resister
Earth
Ground
Providing Static Protection At The Cabinet Mounting Location
Static
Wrist
Strap
Common Point Ground
ESD Protective
Mat
ESD Protective
Worksurface
Typical Earth
Ground
Static 2
ESD Protective
Mat
Creating A Static Safe Work Area
Installing The Ring Generator Assembly – 3
IMI89–187 Installing The Ring Generator Assembly
3.0 Installing The Ring Generator Assembly
You can install the ring generator assembly in the main and expansion cabinets per the following steps.
1. Turn off the power to the system, unplug the AC line cord from the AC outlet, and disconnect the optional battery back up equipment.
2. Install your static discharge wrist strap on your bare wrist; adjust it for a snug fit. Be sure that the strap is touching bare skin and is not isolated by clothing. Connect the wrist strap cord between the wrist strap and an
AC or earth ground
NOTE: With the common equipment in the installed position, the ground lug on the side of the cabinet is an appropriate grounding point since it should have a heavy ground wire connected between it and a good earth ground.
3 Loosen the retaining hardware and lift the front panel away from the common equipment cabinet.
4. Loosen the retaining screws and remove the power supply assembly from the common equipment cabinet.
5. Connect the ring generator assembly to the side panel of the power supply chassis, and secure it with the supplied hardware.
6. Slide the attached assemblies into the opening at the top right side of the common equipment main cabinet until the assembly’s front panel contacts the side of the cabinet.
7. Locate the power cable routed from the backplane, and connect it to the power supply.
8. Locate the ring generator cable routed from the backplane, and connect it to the ring generator.
9. Fasten the assembly to the common equipment cabinet with the hardware you removed in step 2.
10. Plug the AC line cord into the AC outlet, reconnect any battery back up equipment and turn on the switch on the power supply.
11. Replace the front panel on the common equipment cabinet.
4 – Installing The Ring Generator Assembly
Installing The Ring Generator Assembly
Ring Generator Assembly
IMI89–187
Power Supply Assembly
PLUS064
PLUS030
Attaching The Ring Generator To The Power Supply
Ring Generator
Assembly
Power Supply
Assembly
Ring
Generator
Cable
Power
Cable
Installing The Ring Generator And Power Supply
Installing The Ring Generator Assembly – 5
Installing The Conference Board
In The DXP Plus Digital Communications System
1.0 Introducing The Conferencing Board
The software timing for the DXP Plus systems, dedicates 32 time slots for conferencing operations. Different types of conferencing actions require different quantities of time slots as detailed in the following list:
•
SOHVA = 3 time slots,
•
Executive Override = 6 time slots,
•
Four-Way Conference = 8 time slots,
•
Six-Way Conference = 12 time slots,
•
Service Observing = 3 time slots,
•
Three-Way Conference = 6 time slots,
•
Five-Way Conference = 10 time slots,
•
Seven-Way Conference = 14 time slots.
The maximum conference combinations that the system allows at any one time are as follows:
• three five-way or one five-way
Plus 2 SOHVA,
• five three-way or four three-way
Plus one SOHVA,
• two six-way,
• one four-way Plus two three-way,
•
• four four-way, two seven-way
The optional conference board adds the capability for five additional three-way conferences. These are three-way conferences consisting of three stations or two stations and one line. These additional three-way conferences do not provide additional SOHVA or service observe capability.
When you install the conference board, the system uses its capacity of three-way conferences before using the main system resources for additional conferencing.
1.2
Complying With Underwriters Laboratories Regulations
Per The Underwriters Laboratories regulation 1459, 2nd edition, be aware of the following precautions when installing telephone equipment that is to be directly connected to the telephone company network:
•
Never install telephone wiring during a lightning storm.
•
Never install telephone jacks in wet locations unless the jack is specifically designed for wet locations.
•
Never touch uninsulated telephone wires or terminals unless the telephone line has been disconnected at the network interface.
•
Use caution when installing or modifying telephone lines.
R
This manual has been developed by Comdial Corporation (the “Company”) and is intended for the use of its customers and service personnel. The information in this manual is subject to change without notice.
While every effort has been made to eliminate errors, the Company disclaims liability for any difficulties arising from the interpretation of the information contained herein.
The information contained herein does not purport to cover all details or variations in equipment nor to provide for every possible contingency to be met in connection with installation, operation, or maintenance.
Should further information be desired, or should particular problems arise which are not covered sufficiently for the purchaser’s purposes, contact Comdial, Inside Sales Department, Charlottesville, Virginia
22906.
Printed in U.S.A.
IMI89-188.01
7/95
IMI89–188 Installing The Conference Board
2.0 Installing Circuit Boards
CAUTION
Circuit boards are susceptible to damage caused by electrostatic discharge, and you must keep this fact in mind as you handle the circuit boards.
Refer to the Comdial publication IMI01-005, Handling Of
Electrostatically Sensitive Components, for general information. Specific handling precautions are also included in this installation instruction.
2.1
Creating A Static Safe Work Area
When servicing the common equipment cabinet at the installation location, it is a good practice to place a conductive mat in front of the cabinet area and ground the mat to a good earth ground. (The third wire ground of the AC power line is also an acceptable grounding point.) The grounded conductive mat provides a safe static electric discharge path.
When removing the common equipment cabinet from the installation location for servicing, it is a good practice to prepare a static-safe work area on which to place the cabinet.
You should supply yourself with a static discharge wrist strap, and wear it every time you handle electronic circuit boards either at the cabinet mounting location or at your work area.
2 – Installing The Conference Board
Installing The Conference Board IMI89–188
PLUS035
Expansion
Cabinet
Common
Equipment
Cabinet
Static Discharge
Wrist Stap
Expansion
Cabinet
Conductive
Mat
1 Meg Ohm
Resister
Earth
Ground
Providing Static Protection At The Cabinet Mounting Location
Static
Wrist
Strap
Common Point Ground
ESD Protective
Mat
ESD Protective
Worksurface
Typical Earth
Ground
Static 2
ESD Protective
Mat
Creating A Static Safe Work Area
Installing The Conference Board – 3
IMI89–188 Installing The Conference Board
2.2
Installing Conference Boards In The Equipment Cabinet
Install one or more conference boards (as needed) in any unused universal board slots.
1. Normally you should disconnect the AC power cord from the AC outlet and disconnect the optional battery back-up assembly from the main cabinet power supply; however, when necessary, you can install a DXCNF board in an operating system. If you must do this, connect one end of a standard telephone handset coil cord to the precharge port on the power supply. During step 6, you will connect the other end of this coil cord to the precharge jack on the station board.
2. Install your static discharge wrist strap on your bare wrist; adjust it for a snug fit. Be sure that the strap is touching bare skin and is not isolated by clothing. Connect the wrist strap cord between the wrist strap and an
AC or earth ground
NOTE: With the common equipment in the installed position, the ground lug on the side of the cabinet is an appropriate grounding point since it should have a heavy ground wire connected between it and a good earth ground.
3. Loosen the retaining hardware, and lift the front panel away from the common equipment.
4. Each conference board is supplied in a static protection bag for safe keeping. When you are ready to install the circuit board, remove it from its static protection bag.
5. Locate an unused board slot for conference board installation.
NOTE: On DXP Plus systems, do not install a conference board at the right-most board slot in the second (or lower) expansion cabinet. The system reserves this slot for internal use.
6. If you are installing the conference board in an operating system, connect the free end of the precharge cord that you installed in step 1 to the precharge jack on the station board.
7. Orient the conference board with its top and bottom guides in the cabinet’s board cage. and press the board firmly until its board edge connection properly mates with the connector on cabinet’s backplane.
CAUTION
When pressing circuit boards into place, press them only at the extractor lever locations.
If you apply pressure at other locations you may damage the board assembly.
8. Repeat steps 4–7 until all circuit boards are installed.
9. Make a final inspection to ensure that the conference board is oriented correctly and mated properly.
10. Install and tighten the supplied screws to secure the conference board to the board cage.
11. Plug the AC line cord into the AC outlet, reconnect any battery back up equipment, and turn on the switch on the power supply.
12. Replace the front panel on the common equipment cabinet.
4 – Installing The Conference Board
Installing The Conference Board
PLUS023
Power Supply
Pre-charge Port
IMI89–188
Pre-charge
Cable For
Conference
Board
Installation
During
Power Up
Conference
Board
Pre-charge
Port
Conference
Board
Static Discharge Wrist Strap
Viewing A Typical Conference Board Installation
Installing The Conference Board – 5
Installing The DXOPT–COM Communications Card
In The DXP Plus Digital Communications System
1.0 Understanding The Communications Card
The communications card provides serial data ports for interfacing such items as open architecture interface applications, PC attendant positions, and the SMDA data printer.
NOTE: The serial data ports located on the CPU board are dedicated to PC-based programming and the remote maintenance modem.
You can install communications cards on the services board, the expansion cabinet interface boards, and the main cabinet’s auxiliary board. Each of these boards will accept two communications cards in its lower two slots.
The DXP Plus supports a maximum of 18 serial data ports. Two of these ports are the dedicated ports provided by the CPU board while communications cards provide the remaining 16 undedicated ports. The system designates serial data ports 3–18 to specific locations as detailed in the following chart.
Serial Data Port Designation*
Serial data ports 3–10
DXOPT–COM Location
Lower two slots on the services board
Serial data ports 11–18
Lower two slots on one of the three following locations:
— the upper expansion cabinet interface board
— the lower expansion cabinet interface board
— the auxiliary board installed in the main cabinet.
You must take programming action to match the data port number with the installation location that you choose for the communications card.
* The full compliment of 16 undedicated serial data ports requires four installed communications cards.
R
1.1
Communications Card Connections
The interface connector between the external device and the communications card is a standard modular jack, and each serial data communications port supports various baud rates, data bits, stop bits, parity, and flow control.
You can program these various options using data base programming.
This manual has been developed by Comdial Corporation (the “Company”) and is intended for the use of its customers and service personnel. The information in this manual is subject to change without notice. While every effort has been made to eliminate errors, the Company disclaims liability for any difficulties arising from the interpretation of the information contained herein.
The information contained herein does not purport to cover all details or variations in equipment or to provide for every possible contingency to be met in connection with installation, operation, or maintenance. Should further information be desired, or should particular problems arise which are not covered sufficiently for the purchaser’s purposes, contact Comdial, Inside Sales Department,
Charlottesville, Virginia 22906.
Printed in U.S.A.
IMI89-190.01
7/95
IMI89–190
2.0 Installing Circuit Boards
Installing The Communications Card
CAUTION
Circuit boards are susceptible to damage caused by electrostatic discharge, and you must keep this fact in mind as you handle the circuit boards.
Refer to the Comdial publication IMI01-005, Handling Of
Electrostatically Sensitive Components, for general information. Specific handling precautions are also included in this installation instruction.
2.1
Creating A Static Safe Work Area
When servicing the common equipment cabinet at the installation location, it is a good practice to place a conductive mat in front of the cabinet area and ground the mat to a good earth ground. (The third wire ground of the AC power line is also an acceptable grounding point.) The grounded conductive mat provides a safe static electric discharge path.
When removing the common equipment cabinet from the installation location for servicing, it is a good practice to prepare a static-safe work area on which to place the cabinet.
You should supply yourself with a static discharge wrist strap, and wear it every time you handle electronic circuit boards either at the cabinet mounting location or at your work area.
2 – Installing The Communications Card
Installing The Communications Card IMI89–190
PLUS035
Expansion
Cabinet
Common
Equipment
Cabinet
Static Discharge
Wrist Stap
Expansion
Cabinet
Conductive
Mat
1 Meg Ohm
Resister
Earth
Ground
Providing Static Protection At The Cabinet Mounting Location
Static
Wrist
Strap
Common Point Ground
ESD Protective
Mat
ESD Protective
Worksurface
Typical Earth
Ground
Static 2
ESD Protective
Mat
Creating A Static Safe Work Area
Installing The Communications Card – 3
IMI89–190 Installing The Communications Card
3.0 Installing The DXOPT-COM Card
You can install up to four communications cards to attain a maximum of 16 serial data ports. You can install these cards in the lower two slots of the services board, the expansion cabinet interface boards, and the main cabinet’s auxiliary board.
•
The best, and recommended, choice is to add communications cards to the services board.
•
The second best choice is to add communications cards to either or both expansion cabinet’s interface boards if one or both are available.
•
The third choice is to add an auxiliary board to the system and install communications cards on it. This is the least desirable choice because it requires you to occupy a board slot that you could otherwise use for line or station boards.
1. Be sure you are standing on the conductive mat that you have placed in front of the cabinet area and grounded to a good earth ground. (The third wire ground of the AC power line is an acceptable grounding point if the
AC wall jack is properly grounded.) The grounded conductive mat provides a safe static electric discharge path.
2. Install your static discharge wrist strap on your bare wrist; adjust it for a snug fit. Be sure that the strap is touching bare skin and is not isolated by clothing. Connect the wrist strap cord between the wrist strap and an
AC or earth ground
NOTE: With the common equipment in the installed position, the ground lug on the side of the cabinet is an appropriate grounding point since it should have a heavy ground wire connected between it and a good earth ground.
3. Disconnect the AC power cord from the AC outlet and disconnect the optional battery back-up assembly from the cabinet power supplies.
4. Loosen the retaining hardware and remove the host circuit board, or boards, from the equipment cabinet, place it in a static protection bag, and transport the board to the static-safe work area.
5. At the static safe work area, with your wrist strap in place, remove the host circuit boards and the communications cards from their respective static protection bags.
6. Referring to the illustrations on the next page, orient the host circuit board and the communications card, and attach them with the supplied hardware.
7. Place the host circuit board and its newly installed communications card into a static protection bag and transport this assembly back to the common equipment cabinet.
8. With your static strap on your wrist, remove the board assembly from the static protection bag and install the board in its designated board slot.
CAUTION
When pressing circuit boards into place, press them only at the extractor lever locations.
If you apply pressure at other locations you may damage the board assembly.
9. Make a final inspection to ensure that the board assembly is oriented correctly and mated properly.
10. Install and tighten the supplied screws to secure the circuit board assembly to the board cage.
11. Plug the AC line cord into the AC outlet, reconnect any battery back up equipment and switch on the power supply.
12. Replace the front panel on the common equipment cabinet.
4 – Installing The Communications Card
Installing The Communications Card
PLUS017
Supplied Mounting
Hardware (8 Places)
PLUS016
Supplied
Hardware (8 Places)
IMI89–190
Services Board
Communications
Card
Interface Board
For Upper
Expansion
Cabinet
Communications
Card
PLUS019
Supplied
Hardware (8 Places)
Interface Board
For Lower
Expansion
Cabinet Communications
Card
Installing The Communications Card
Installing The Communications Card – 5
IMI89–190 Installing The Communications Card
4.0 Identifying The Communications Card’s Serial
Data Port Connections
Each communications card provides four serial data ports. Each serial data port is a standard 6-conductor modular jack that serves as the interface connection between an external data device and the DXP Plus system.
The system designates serial data ports 3–18 to specific locations and, you must take programming action to match the data port number with the installation location that you choose for the communications card.
Serial Data Port Designation
Serial data ports 3–10
Serial data ports 11–18
DXOPT–COM Location
Lower two slots on the services board
Lower two slots on : upper expansion cabinet interface board
–or– lower expansion cabinet interface board
–or– the auxiliary board installed in the main cabinet.
6 – Installing The Communications Card
Installing The Communications Card IMI89–190
PLUS020
Serial
Ports
3 - 6
Serial
Ports
7 - 10
Services Board
Serial
Ports
11 - 14
Serial
Ports
15 - 18
Interface Board
For Lower
Expansion Cabinet
Auxiliary
Board (Main
Cabinet Location
ONLY)
Interface Board
For Upper
Expansion Cabinet
Identifying The Serial Data Port Locations
Installing The Communications Card – 7
IMI89–190 Installing The Communications Card
5.0 Connecting Data Devices
5.1
Selecting The Baud Rate
Each serial data communications port supports various baud rates, data bits, stop bits, parity, and flow control.
You can program these various options using the data base programming; however, the maximum baud rate that you can assign to a serial data port varies depending upon whether you locate the communications card. Also, if a device is transmitting/receiving data from the DXP Plus at a high rate, engineering sources recommend that you use a communications protocol (such as RTS/CTS or XON/XOFF) to prevent buffer overrun and data loss.
Maximum
Baud Rate
19,200 Baud
Serial Data Port
Serial data ports 3–10
Serial data ports 11–18
DXOPT–COM Location
Lower two slots on the services board
Lower two slots on: the upper expansion cabinet interface board,
–or– the lower expansion cabinet interface board,
–or– the auxiliary board installed in the main cabinet.
9600 Baud
The maximum distance from a serial data port that you can confidently locate a data device is dependent upon the baud rate at which you operate the serial data port.
•
When operating the port at 9600 baud, your data cable run must be no longer than 500 feet.
•
When operating the port at 19,200 baud, your data cable run must be no longer than 50 feet.
8 – Installing The Communications Card
Installing The Communications Card IMI89–190
4.1
Making the Data Connections
Each serial data port is a standard 6–conductor modular jack that serves as the interface between an external data device and the DXP Plus system.
When preparing a data cable for connection to a data device, refer to the manufacturer’s manual for the equipment being interfaced, and make the wiring connections detailed in the following list:
•
Wire the common equipment RD (data from device to common equipment) connection to the device TD
(transmit data) connection.
•
Wire the common equipment TD (data to device from common equipment) connection to the device RD
(receive data) connection.
•
Wire the common equipment SG (signal ground) connection to the device SG (signal ground) connection.
•
If required for proper operation, wire the common equipment CTS (clear-to-send status from device to common equipment) connection to the device RTS (request-to-send) connection.
NOTE: The common equipment requires a positive voltage, with respect to signal ground, in order to send data.
If the cable has spare wires, be sure to ground them so that they will not act as antennas and induce interference into the system. Further, if there is a source of RF power nearby (such as a radio transmitter), use shielded cable and ground the shield at both ends.
CAUTION
As an added precaution against induced interference, route the data cable as far away from any fluorescent lighting as you can reach, and make every effort to route the data cable perpendicular to other wiring.
PLUS50
3
4
5
6
1
2
Pin 1 = (RTS) Request To Send
Pin 2 = (CTS) Clear To Send
Pin 3 = (RD) Receive Data
Pin 4 = (TD) Transmit Data
Pin 5 = (SG) Signal Ground
Pin 6 = (GND) Chasis Ground
Identifying The Serial Data Connections
Installing The Communications Card – 9
IMI89–190 Installing The Communications Card
R
Charlottesville, Virginia 22901-2829
World Wide Web: http://www.comdial.com/
Accredited by the Dutch Council for Certification for certification and registration activities.
Comdial’s Quality Management System Is
Certified To The ISO 9001 Standard.
Installing The External Battery Assembly
On The DXP Plus Digital Communications System
1.0 Introducing The External Battery Assembly
The external battery assembly is for use with the DXP Plus digital communications system. Unpack and carefully inspect all equipment for shipping damage. Notify the shipper immediately of any damages found. Verify that the packages contain all parts and accessories needed for proper installation and operation. The assembly includes the following items:
•
Batteries: Five 6-volt, 50 ampere-hour, (Comdial product code BT000-141), charger unit and interface cables.
•
Metal enclosure with wire harness, includes combination circuit breaker, on/off switch
Should the AC power to the system be interrupted, one external battery assembly provides the following minimum power capability:
•
1.0 hour of operation for a fully loaded system.
Ke
T =
1 + [(0.084) (N)]
Calculate the minimum battery backup time provided by an external battery assembly to a fully configured DXP
Plus system using the following formula:
T =
(.85)(50)
1 + [(0.084) (472)]
=
41.0
40.65
= 1.0 Hour
T = Back-up time in hours
K = 0.82 (Constant) e = 50 (ampere-hour capacity of battery assembly)
N = Total number of stations
Example:
Assume that you have installed a DXP Plus with three cabinets supporting 472 telephones and containing one line board along with a battery assembly to provide back-up power.
R
During AC operation, the battery assembly accepts re-charging current to maintain the voltage potential of its batteries at an operational level.
NOTE: The external battery assembly requires approximately 10 hours to completely re-charge to full potential after it has been completely discharged and, in some cases, when initially installed.
This manual has been developed by Comdial Corporation (the “Company”) and is intended for the use of its customers and service personnel. The information in this manual is subject to change without notice.
While every effort has been made to eliminate errors, the Company disclaims liability for any difficulties arising from the interpretation of the information contained herein.
The information contained herein does not purport to cover all details or variations in equipment nor to provide for every possible contingency to be met in connection with installation, operation, or maintenance.
Should further information be desired, or should particular problems arise which are not covered sufficiently for the purchaser’s purposes, contact Comdial, Customer Service Department, Charlottesville, Virginia
22906.
Printed in U.S.A.
IMI89–189.02
9/96
IMI89–189 Installing The External Battery Assembly
2.0 Understanding System Grounding Requirements
Transient voltage spikes, if induced onto CO or CENTREX lines, can travel through the cable and into the common equipment. The telephone company offers basic protection against this condition but it is usually designed to protect the central office circuits. While it will also provide some protection to the common equipment, you should not rely upon it for total protection. To help ensure that external over-voltage surges do not damage the system, you should install and properly ground primary protection devices, such as gas discharge tubes or similar primary protection devices, on all lines. While the line boards have internal secondary surge protection on all line ports, in order for this protection to be effective, you MUST connect the common equipment cabinet to a reliable, effective earth ground.
Proper grounding is necessary for trouble-free operation and personnel safety. The DXP Plus has the following three types of grounds:
•
Service Ground —a neutral power line wire that is connected to the ground bus in the premises’ AC power panel,
•
System Ground—a non-current carrying power line wire that is connected to the ground bus in the premises’
AC power panel,
•
Frame Ground—a low impedence conductor that places the common equipment cabinet at reference ground potential. The frame ground provides the greatest safety by limiting electrical potential between non-current carrying parts of the system. The common equipment cabinet provides a ground stud on its cabinet for access to its frame ground.
The entire system is effectively earth-grounded when you permanently connect the common equipment cabinet, all expansion cabinets, and the battery back-up assembly to earth or to some conducting body which serves in place of earth. The ground path must be of sufficient current-carrying capacity to prevent a build up of voltages which may result in circuit noise, hazard to personnel, or equipment damage.
An acceptable earth ground is one such as the service ground for the AC power or a public metallic cold water pipe at a point immediately at its entrance to the premises and ahead of any meters, pumps, or insulating sections that have been added for vibration reduction. Avoid using the premises’ structural steel frame as it may not be at earth ground potential. Use #10–12 or larger insulated solid copper grounding wire to connect the frame ground of the battery assembly cabinet (available through the ground stud on the cabinet’s side) to the frame ground of the main common equipment cabinet. Use #6 or larger insulated solid copper grounding wire to make the ground connection from the main cabinet’s frame ground to earth ground. Keep this ground wire separate from the three-wire AC line cord, do not splice it, and keep it as short as possible.
The impedence of the wiring between the common equipment cabinet frame ground and the earth ground must not exceed 0.25 ohms and the impedence between the earth ground and the power company’s reference standard ground must not exceed 5 ohms. Use an acceptable low impedence measuring device to measure the impedence of these paths. The #6 or larger wire size will minimize the wiring impedence; however, if the impedence between earth ground and the power company’s standard reference ground exceeds 5 ohms, contact the local power company. The ground path must always be of sufficient current-carrying capacity to prevent a build up of voltages that may result in circuit noise, hazard to personnel, or equipment damage.
Be sure that all of the ground connections are visible for inspection and maintenance. Tag all of the ground connections with a sign that reads: Do Not Remove or Disconnect.
2 – Installing The Battery Back Up Assembly
Installing The External Battery Assembly
PLUS073
IMI89–189
No. 10 or 12 Solid Copper
Wire Between Cabinets
Grounding Terminal
Two Grounding Terminals
Grounding Terminal
Grounding Terminal
No. 6 Solid Copper
Wire To Earth Ground
From Main Cabinet
Typical Earth Ground
Grounding The System
Installing The Battery Back Up Assembly – 3
IMI89–189 Installing The External Battery Assembly
3.0 Mounting The Charger Chassis
You must mount the charger chassis to the battery cabinet; however, the particular position that you chose for this mounting depends upon the method that you plan to mount the cabinet at the DXP Plus site.
•
If you plan to mount the battery cabinet on a backboard at the side of the common equipment cabinets, you must attach the charger, with its cables pointing toward you, to the left end of the battery cabinet as you face the cabinet’s battery opening.
•
If you plan to mount the battery cabinet below the main common equipment cabinet on the same backboard
(single common equipment cabinet installations), you must attach the charger, with its cables pointing toward you, to the right end of the battery cabinet as you face the cabinet’s battery opening.
•
If you plan to mount the battery cabinet on the back side of a standard 23–inch double equipment rack with the common equipment cabinets mounted to the front side of the rack, you must attach the charger, with its cables pointing away from you, to the to the left end of the battery cabinet as you face the cabinet’s battery opening.
To mount the charger chassis,
1. Choose the method of battery cabinet mounting, and orient the charger so that it is facing properly for the mounting scheme.
2. Remove the front panel from the empty battery cabinet, and save the retaining hardware.
3. Remove the wiring access plate from the end of the battery cabinet.
4. Route the black battery connection wires through the wiring access hole.
5. Attach the charger chassis to the battery cabinet with the three supplied screws.
bb480k
Wiring Access Plate
Charger Chasis
Battery Cabinet
Mounting The Charger For Separate Backboard Installations
4 – Installing The Battery Back Up Assembly
Screws (3 Places)
Installing The External Battery Assembly
Battery Cabinet
Wiring Access Plate
Charger Chasis bb480L
Screws (3 Places)
Mounting The Charger For Below Main Cabinet Installations bb480j
Wiring Access Plate
Charger Chasis
IMI89–189
Screws (3 Places)
Battery Cabinet
Mounting the Charger For Double Rack Installations
Installing The Battery Back Up Assembly – 5
IMI89–189 Installing The External Battery Assembly
CAUTION
The complete external battery assembly is heavy. The charger chassis, empty battery cabinet, and wiring weigh approximately 25 pounds and all the batteries together weigh approximately 130 pounds for a combined assembly hanging weight of approximately 155 pounds.
You can mount the battery cabinet at several different locations.
•
You can mount the battery cabinet on a separate backboard located to the right of the common equipment cabinet location. Locate the battery cabinet as detailed in the illustration on the facing page.
•
At sites that employ only a main equipment cabinet, you can mount the battery cabinet directly below the main common equipment cabinet on the same backboard.
•
You can mount the battery cabinet in the middle of a standard 23–inch equipment rack if you wish. This can be a companion rack set next to the one where you have mounted the DXP Plus cabinets. Alternately, you can use a self-supporting, two-sided rack with the DXP Plus cabinets mounted on one side and the battery cabinet mounted on the other side directly behind and slightly above the main common equipment.
Remember from the Section 2.0 discussion, you must attach the charger chassis to the battery cabinet in a orientation that supports the cabinet mounting.
NOTE: The following instructions describe how to mount the battery cabinet using a backboard.
1. Add a second backboard to the right of the backboard that supports the DXP Plus common equipment cabinet.
Be sure that this backboard bridges the studs that support the underlying wall material. Securely attach the backboard to the mounting surface. (Suitable backboards are available commercially or you can construct one out of 3/4-inch plywood.) You must drive the hardware that secures the backboard to the mounting surface into the underlying wall studs instead of just into the wall material alone.
2. Refer to the illustration for the locating dimensions required for the mounting screws, and mark their locations on the backboard. You must attach the battery cabinet vertically to the backboard.
3. Drill holes in the backboard of a proper size to accommodate the hardware being used.
4. Insert the two top screws into the backboard and tighten them to within approximately 1/8–inch of the surface.
5. Hang the cabinet on the top screws using the top mounting holes in the rear mounting flange of the cabinet.
Note that these holes are elongated with an enlargement at one end. This feature allows the cabinet to slide down on the screws to secure the mounting when the cabinet is hung on them.
6. Use the openings for the middle and lower set of mounting screws as a guide, and mark the location for the remaining screws.
7. Lift the cabinet from the top screws and set it aside while preparing the holes for the remaining screws.
8. Rehang the cabinet as discussed in step 6.
9. Insert the lower screws into the backboard and tighten them to within approximately 1/8-inch of the surface.
6 – Installing The Battery Back Up Assembly
Installing The External Battery Assembly IMI89–189
BB480a
Mounting The External Battery Assembly
Installing The Battery Back Up Assembly – 7
IMI89–189 Installing The External Battery Assembly
5.0 Assembling and Wiring The Batteries In The Cabinet
5.1
Installing The Batteries
Install the batteries in the cabinet with their terminals facing the cabinet opening. The batteries set in place, and you do not need to anchor them to the cabinet.
Installing The Batteries
8 – Installing The Battery Back Up Assembly
PLUS003
Installing The External Battery Assembly IMI89–189
5.2
Strapping The Batteries
You must strap the batteries together using the supplied strapping bars and hardware. Use three strapping bars at each strapping location, and install the hardware as shown in the illustration.
BB480c
Strapping The Batteries
# 10-32 Machine Screw
#10 Flat Washer
Battery Straps
Battery Terminal
#10 Flat Washer
#10 Lockwasher
#10 Hex Nut bb480h
Attaching The Strapping Hardware
Installing The Battery Back Up Assembly – 9
IMI89–189 Installing The External Battery Assembly
5.3
Wiring The Batteries
The charger has a pair of negative wires and a pair of positive wires (designated by red sleeving near one end of the wires). This two-wire arrangement divides the current carrying load between the two wires of each pair. The cabinet’s assembly package includes two individual black wires that you use to wire the circuit breaker to the batteries. Again, two wires divide the current carrying load between both wires.
The negative wires from the charger are terminated with smaller size terminals than the those that terminate the charger’s positive wires. Connect the smaller (negative) terminals to the circuit breaker and the larger (positive) terminals to the positive battery post. The individual wires that you use to connect the circuit breaker to the battery post are also terminated with a large terminal on one end and a small terminal on the other. Connect the smaller terminals to the circuit breaker and the larger terminals to the negative battery post.
Wire the batteries as shown in the schematic. Use the supplied hardware to connect the wires to the batteries per method shown in the detailed drawing.
Once you have wired the batteries, attach the front cover to the cabinet with the supplied hardware.
+
-
Two Black Wires With Red Sleeving
(Positive Lead)
Circuit Breaker
Two Black Wires
(Negative Lead)
-
Two Black Wires
(Negative Lead)
Strap (Four Places)
+
-
+
-
+
-
+
-
+
Charger Batteries
Connecting The Wire Harness
10 – Installing The Battery Back Up Assembly
PLUS005
Installing The External Battery Assembly IMI89–189
#10-32 Machine Screw
Wire Terminal
Battery Terminal
Wire Terminal
#10 Flat Washer
#10 Lockwasher
#10 Hex Nut bb480i
Attaching The Wiring Hardware
BB480e
Installing The Front Cover
Installing The Battery Back Up Assembly – 11
IMI89–189 Installing The External Battery Assembly
6.0 Connecting The Battery Assembly To The System
1. Connect the AC power and turn on the power supply switch in both DXP Plus main and expansion cabinets.
2. Connect a battery back-up cable between the battery assembly and the power supplies in the DXP Plus main and expansion cabinets.
3. The battery assembly includes a charger that maintains the batteries at full charge. Once you have installed the battery assembly, connect its AC power cord to the same AC outlet surge protector that powers the
DXP Plus main common equipment cabinet.
PLUS004
Circuit Breaker
Power Line
Surge Protector
Dedicated
AC Outlet
Connecting The Battery Back Up Assembly To The System
12 – Installing The Battery Back Up Assembly
Installing The External Battery Assembly IMI89–189
7.0 Verifying The Battery Voltage
Every three months, use an accurate voltmeter to measure the no-load voltage of the external battery assembly.
The measured voltage range should be within 27–34.5 volts when the batteries are at full charge.
If the no-load voltage is lower than 27 volts, measure the charging voltage supplied by the common equipment cabinet. The measured charging voltage must be 35 volts maximum.
If the charging voltage is low or if the voltage of a freshly-charged battery assembly is no greater than 30 volts, contact your technical service representative.
{
Green Status Lights
On = Batteries fully charges (>32 V)
On = Batteries under charged (>30 V)
On = Batteries low (>27 V)
On = AC power on
PLUS002
Fuse 5 AMP slow blow type
Measured Voltage
(charger on and batteries fully charged)
{
= +34.5 GND
= +34.5 GND
= -34.5 Volts
= -34.5 Volts
Verifying The Battery Voltages
Installing The Battery Back Up Assembly – 13
IMI89–189 Installing The External Battery Assembly
8.0 Special Cautionary Battery Information
•
Do not dispose of batteries in a fire as the cells may explode. Check with the local codes for possible disposal instructions.
•
Do not open or mutilate the batteries. Released electrolyte is corrosive and may cause damage to the eyes or skin. It may be toxic if swallowed.
•
Exercise care in handling batteries in order not to short the battery with conducting materials such as rings, bracelets, and keys. The battery may over-heat and cause burns.
•
Charge the batteries provided with or identified for use with the DXP Plus digital communications system only in accordance with the instructions and limitations specified in this publication.
•
Observe proper polarity orientation when installing the batteries.
•
Do not mix old and new batteries in the external battery assembly.
•
Do not mix batteries of different sizes or from different manufacturers in this product.
NOTICE
This symbol, when encountered on the equipment cabinet or on other installed hardware, means: CAUTION—refer to the instruction manual.
Accredited by the Dutch Council for Certification for certification and registration activities.
Comdial’s Quality Management System Is
Certified To The ISO 9001 Standard.
R
Charlottesville, Virginia 22901-2829
World Wide Web: http://www.comdial.com/
Installing The Switchable Power Supply In The
DXP Plus Common Equipment Cabinet
1.0 Introducing The Switchable Power Supply
This publication discusses the installation of the switchable IEC 950 approved 120/230 volt power supply assembly for the DXP Plus main and expansion common equipment cabinets. The voltage ranges of this power supply assembly is as follows:
•
90–129 VAC at 50/60 Hz
•
200–254 VAC at 50 Hz
The power supply assembly is packed separately from the common equipment cabinet; therefore, you should unpack and carefully inspect it for shipping damage and notify the shipper of any damages you find. Also, verify that the package contains all parts and accessories needed for proper installation and operation.
Refer to IMI66–105, Installation Instructions DXP Plus Main Cabinet Assembly for complete installation instructions of the main DXP plus cabinet and to IMI66–106, Installation Instructions DXP Plus Expansion
Cabinet Assembly for complete installation instructions of the DXP plus expansion cabinet.
The power supply assembly is protected with a 6.3A, 250V slow-blow fuse. A replacement fuse must have the same rating.
NOTE: Both the switchable power supply assembly employ electronic switching circuitry in their design. During operation, power supplies of this type generate an audible sound from their switching regulators. This sound is normal and is not an indication that the power supply is operating improperly.
R
This manual has been developed by Comdial Corporation (the “Company”) and is intended for the use of its customers and service personnel. The information in this manual is subject to change without notice.
While every effort has been made to eliminate errors, the Company disclaims liability for any difficulties arising from the interpretation of the information contained herein.
The information contained herein does not purport to cover all details or variations in equipment nor to provide for every possible contingency to be met in connection with installation, operation, or maintenance.
Should further information be desired, or should particular problems arise which are not covered sufficiently for the purchaser’s purposes, contact Comdial, Inside Sales Department, Charlottesville, Virginia
22906.
Printed in U.S.A.
IMI89-196.01
7/95
IMI89–196 Installing The Switchable Power Supply
2.0 Understanding System Grounding Requirements
Transient voltage spikes, if induced onto CO or CENTREX lines, can travel through the cable and into the common equipment. The telephone company offers basic protection against this condition but it is usually designed to protect the central office circuits. While it will also provide some protection to the common equipment, you should not rely upon it for total protection. To help ensure that external over-voltage surges do not damage the system, you should install and properly ground primary protection devices, such as gas discharge tubes or similar devices, on all lines. While the line boards have internal secondary surge protection on all line ports, in order for this protection to be effective, you MUST connect the common equipment cabinet to a reliable, effective earth ground.
Proper DXP grounding is necessary for trouble-free operation and personnel safety. The DXP Plus has the following three types of grounds:
•
Service Ground—a neutral power line wire that is connected to the ground bus in the premises’ AC power panel,
•
System Ground—a non-current carrying power line wire that is connected to the ground bus in the premises’
AC power panel,
•
Frame Ground—a low impedance conductor that places the common equipment cabinet at reference ground potential. The frame ground provides the greatest safety by limiting electrical potential between non-current carrying parts of the system. The common equipment cabinet provides a ground stud on its cabinet for access to its frame ground.
Effective grounding requires that you connect the frame ground to a good earth ground. A good earth ground is one such as the ground bus in the premises’ AC power panel or a public metallic cold water pipe at a point immediately at its entrance to the premises and ahead of any meters, pumps, or insulating sections that have been added for vibration reduction. Avoid using the premises’ structural steel frame as it may not be at earth ground potential. Use #10–12 or larger insulated solid copper grounding wire to connect the frame ground of the expansion cabinet (available through the ground stud on the expansion cabinet’s side) to the frame ground of the main common equipment cabinet. Use #6 or larger insulated solid copper grounding wire to make the ground connection from the main cabinet’s frame ground to earth ground. Keep this ground wire separate from the three-wire AC line cord, do not splice it, and keep it as short as possible.
The impedance of the wiring between the DXP Plus and the earth ground must not exceed 0.25 ohms and the impedance between the earth ground and the power company’s reference standard ground must not exceed 5 ohms. Use an acceptable low impedance measuring device to measure the impedance of these paths. The #6 or larger wire size will minimize the wiring impedance; however, if the impedance between earth ground and the power company’s standard reference ground exceeds 5 ohms, contact the local power company. The ground path must always be of sufficient current-carrying capacity to prevent a build up of voltages that may result in circuit noise, hazard to personnel, or equipment damage.
Be sure that all of the ground connections are visible for inspection and maintenance. Tag all of the ground connections with a sign that reads: Do Not Remove Or Disconnect.
2 – Installing The Switchable Power Supply
Installing The Switchable Power Supply
PLUS073
Grounding Terminal
No. 10 or 12 Solid Copper
Wire Between Cabinets
IMI89–196
Two Grounding Terminals
Grounding Terminal
Grounding Terminal
Typical Earth Ground
No. 6 Solid Copper
Wire To Earth Ground
From Main Cabinet
Grounding The System
Installing The Switchable Power Supply – 3
IMI89–196 Installing The Switchable Power Supply
3.0 Matching The Source Voltage
The factory ships the switchable power supply set for 230 VAC operation. If you plan to operate the power supply from a 120 VAC source, you must set the voltage selection switch for that input. The switch is located at the upper right edge of the power supply assembly. Slide the switch actuator to the setting that matches the AC source voltage available at the installation site.
CAUTION
Be sure that you set the power supply for the proper source voltage. An improper setting can result in equipment damage.
Voltage Selector Switch
(Slide Actuator To Setting That
Matches The AC Source Volage)
PLUS076
Matching The Source Voltage
4 – Installing The Switchable Power Supply
Installing The Switchable Power Supply IMI89–196
4.0 Installing The AC Power Plug
The line cord is terminated with a typical continental European plug matching the CEE 7/7 standard. If this plug does not meet the site needs, you can install a plug of the proper type for your installation.
To install a line cord plug,
• familiarize yourself with the requirements for the plug that you plan to install on the unterminated line cord (the illustration shows a typical continental European plug matching the CEE 7 standard),
• strip off the insulation from the line cord wires according to the requirements for your plug,
• open the plug and slide its outer shell onto the line cord,
• connect the ground, neutral, and line wires according to the requirements for your plug,
• if your plug includes a clamp, tighten it on the line cord,
• reassemble the plug,
Test the installation for open and short circuits using an ohm meter.
L1
L2
Neutral (Blue)
Ground (Green/Yellow)
Line (Brown)
L3
L1, L2, and L3= strip length requirements
PLUS069
Neutral (Blue) Line (Brown)
Ground (Green/Yellow)
Clamp
Inside Of Plug
Standard Wire Color
Power
Source
Wire Color
Europe USA
Line Brown Black
Installing A Typical Continental European AC Power Plug
Installing The Switchable Power Supply – 5
IMI89–196 Installing The Switchable Power Supply
5.0 Installing The Power Supply
NOTE: The common equipment cabinet employs an electronic switching power supply. During operation, power supplies of this type generate an audible sound from their switching regulators. This sound is normal and is not an indication that the power supply is operating improperly.
Install the power supply assembly in the common equipment cabinet per the following discussion and illustration.
1. Be sure to ground the common equipment cabinet per the instructions in the previous paragraph before installing the power supply assembly.
2. Remove the power supply assembly from the carton. Be sure to save the small bag containing the mounting hardware.
3. Slide the power supply into the opening at the top right side of the common equipment main cabinet until the assembly’s front panel contacts the side of the cabinet.
4. Locate the power cable routed from the backplane and connect it to the power supply’s mating connector.
5. Remove the four #6 thread-forming screws from the hardware bag and secure the power supply assembly to the equipment cabinet.
CAUTION
The power supply is fan cooled. If air flow to the fan is blocked or the fan is out of service for any reason, the power supply can overheat. If the power supply overheats, the Thermal Overload indicator lights, and the 36 VDC output voltage shuts off.
Typical Common Equipment Cabinet
Power
Supply
Assembly
PLUS075
Installing The Power Supply
6 – Installing The Switchable Power Supply
Machine Screw
(4 Places)
Installing The Switchable Power Supply IMI89–196
6.0 Making The AC Power Connection
•
For the main cabinet’s AC power connection, employ a dedicated 15 AMP circuit, with a third-wire ground and supplied to a standard electrical outlet. Remember, this electrical outlet must be located within four feet of the common equipment cabinet. Remember also, you may need to supply two 15 AMP dedicated electrical outlets, each protected by its own circuit breaker, if you plan to later install expansion cabinets.
NOTE: If you install the optional battery back-up assembly, you can use this same outlet to supply AC power to that assembly’s battery charger.
•
To provide protection against surges and spikes that may appear on the AC line, install a plug-in power line surge protector between the AC power cord of the installed equipment and the AC outlet..
CAUTION
DO NOT attach or secure the line cord to the surface of the mounting location in any manner.
PLUS038
Two 15 AMP
Circuit Breakers
Ganged Together
Power
Cable
Two Dedicated
117 VAC 15 Amp
NEMA 5-15R
Electrical Outlets
With Third Wire
Ground
(Each Is Protected
By Its Own Circuit
Breaker.)
Plug-In
Power Line
Surge Protectors
Typical Earth
Ground
Making The AC Connection
Installing The Switchable Power Supply – 7
IMI89–196 Installing The Switchable Power Supply
7.0 Measuring The Power Supply Voltages
If you need to measure power supply voltages, you can do so at the DC voltage connector. Measure the power under the following conditions:
•
AC line cord connected to the AC outlet,
•
DC power cable disconnected from power supply’s DC voltage connector,
•
AC power switch turned on.
Measurement details are shown in the illustration.
CAUTION
For new installations, once you have measured the power supply voltages, turn off the AC power switch and disconnect the AC line cord from the outlet. Leave the AC power disconnected until you have installed the circuit boards in the equipment cabinet.
8.0 Identifying The Fuse
The power supply fuse is a slow-blow type rated at 6.3 AMPS and 250 VOLTS. A replacement fuse must have the same rating.
8 – Installing The Switchable Power Supply
Installing The Switchable Power Supply IMI89–196
PLUS070
On = -36 VDC
On = +5 VDC
On = -5 VDC
On = Thermal Overload
On = Battery Backup Connected
On/Off Switch
Source Voltage Switch
Fuse
6.3A, 250V
Slow Blow
Type
Reset Switch
(Press If Thermal Overload
Indicator Turns On)
Pins 1 & 2 = -36 V Ground
Pins 3 & 4 = -36 VDC
Pin 5 = +5 VDC
Pin 6 = -5 VDC
Pin 7 = Digital & Analog Ground
Pin 8 =Thermal Overload Signal
Power Supply Measurements
Measure Between Terminals
+ Voltmeter
Lead
- Voltmeter
Lead
Measured Values
Pin 1
Pin 5
Pin 3
Pin 7
- 36 VDC +1.0V / -0V
+ 5 VDC +/-3 V
Pin 6 Pin 7
Pin 8 Pin 7
- 5 VDC +/-3 V
0 volts = normal operation
+ 5 V nominal = thermal overload
(press reset switch)
Measuring The Power Supply Voltages
Installing The Switchable Power Supply – 9
Installing The Switchable External Battery Assembly On
The DXP Plus Digital Communications System
1.0 Introducing The External Battery Assembly
The external battery assembly is for use with the DXP Plus digital communications system. Unpack and carefully inspect all equipment for shipping damage. Notify the shipper immediately of any damages found. Verify that the packages contain all parts and accessories needed for proper installation and operation. The assembly includes the following items:
•
Batteries: Five 6-volt, 50 ampere-hour, (Comdial product code BT000-141), charger unit and interface cables.
•
Metal enclosure with wire harness, includes combination circuit breaker, on/off switch
Should the AC power to the system be interrupted, one BB480 external battery assembly provides the following minimum power capability:
•
1.0 hour of operation for a fully loaded system.
Ke
T =
1 + [(0.084) (N)]
Calculate the minimum battery backup time provided by a battery assembly to a fully configured DXP Plus system using the following formula:
T =
(.82)(50)
1 + [(0.084) (472)]
=
41.0
40.65
= 1.0 Hour
T = Back-up time in hours
K = 0.82 (Constant) e = 50 (ampere-hour capacity of battery assembly)
N = Total number of stations
Example:
Assume that you have installed a DXP Plus with three cabinets supporting 472 telephones and containing one line board along with a battery assembly to provide back-up power.
R
During AC operation, the battery assembly accepts re-charging current to maintain the voltage potential of its batteries at an operational level.
NOTE: The BB480 external battery assembly requires approximately 10 hours to completely re-charge to full potential after it has been completely discharged and, in some cases, when initially installed.
This manual has been developed by Comdial Corporation (the “Company”) and is intended for the use of its customers and service personnel. The information in this manual is subject to change without notice.
While every effort has been made to eliminate errors, the Company disclaims liability for any difficulties arising from the interpretation of the information contained herein.
The information contained herein does not purport to cover all details or variations in equipment nor to provide for every possible contingency to be met in connection with installation, operation, or maintenance.
Should further information be desired, or should particular problems arise which are not covered sufficiently for the purchaser’s purposes, contact Comdial, Customer Service Department, Charlottesville, Virginia
22906.
Printed in U.S.A.
IMI89–197.02
11/95
IMI89–197 Installing The Switchable Battery Back Up Assembly
2.0 Understanding System Grounding Requirements
Transient voltage spikes, if induced onto CO or CENTREX lines, can travel through the cable and into the common equipment. The telephone company offers basic protection against this condition but it is usually designed to protect the central office circuits. While it will also provide some protection to the common equipment, you should not rely upon it for total protection. To help ensure that external over-voltage surges do not damage the system, you should install and properly ground primary protection devices, such as gas discharge tubes or similar primary protection devices, on all lines. While the line boards have internal secondary surge protection on all line ports, in order for this protection to be effective, you MUST connect the common equipment cabinet to a reliable, effective earth ground.
Proper grounding is necessary for trouble-free operation and personnel safety. The DXP Plus has the following three types of grounds:
•
Service Ground —a neutral power line wire that is connected to the ground bus in the premises’ AC power panel,
•
System Ground—a non-current carrying power line wire that is connected to the ground bus in the premises’
AC power panel,
•
Frame Ground—a low impedence conductor that places the common equipment cabinet at reference ground potential. The frame ground provides the greatest safety by limiting electrical potential between non-current carrying parts of the system. The common equipment cabinet provides a ground stud on its cabinet for access to its frame ground.
The entire system is effectively earth-grounded when you permanently connect the common equipment cabinet, all expansion cabinets, and the battery back-up assembly to earth or to some conducting body which serves in place of earth. The ground path must be of sufficient current-carrying capacity to prevent a build up of voltages which may result in circuit noise, hazard to personnel, or equipment damage.
An acceptable earth ground is one such as the service ground for the AC power or a public metallic cold water pipe at a point immediately at its entrance to the premises and ahead of any meters, pumps, or insulating sections that have been added for vibration reduction. Avoid using the premises’ structural steel frame as it may not be at earth ground potential. Use #10–12 or larger insulated solid copper grounding wire to connect the frame ground of the battery assembly cabinet (available through the ground stud on the cabinet’s side) to the frame ground of the main common equipment cabinet. Use #6 or larger insulated solid copper grounding wire to make the ground connection from the main cabinet’s frame ground to earth ground. Keep this ground wire separate from the three-wire AC line cord, do not splice it, and keep it as short as possible.
The impedence of the wiring between the common equipment cabinet frame ground and the earth ground must not exceed 0.25 ohms and the impedence between the earth ground and the power company’s reference standard ground must not exceed 5 ohms. Use an acceptable low impedence measuring device to measure the impedence of these paths. The #6 or larger wire size will minimize the wiring impedence; however, if the impedence between earth ground and the power company’s standard reference ground exceeds 5 ohms, contact the local power company. The ground path must always be of sufficient current-carrying capacity to prevent a build up of voltages that may result in circuit noise, hazard to personnel, or equipment damage.
Be sure that all of the ground connections are visible for inspection and maintenance. Tag all of the ground connections with a sign that reads: Do Not Remove or Disconnect.
2 – Installing The Battery Back Up Assembly
Installing The Switchable Battery Back Up Assembly
PLUS073
Grounding Terminal
No. 10 or 12 Solid Copper
Wire Between Cabinets
IMI89–197
Two Grounding Terminals
Grounding Terminal
Grounding Terminal
No. 6 Solid Copper
Wire To Earth Ground
From Main Cabinet
Typical Earth Ground
Grounding The System
Installing The Battery Back Up Assembly – 3
IMI89–197 Installing The Switchable Battery Back Up Assembly
3.0 Matching The Source Voltage
The factory ships the switchable battery back up charger assembly set for 230 VAC operation. If you plan to operate the charger from a 120 VAC source, you must set the voltage selection switch for that input. The switch is located at the lower left edge of the charger chassis. Slide the switch actuator to the setting that matches the AC source voltage available at the installation site.
PLUS074
Matching The Source Voltage
Voltage Select Switch
4 – Installing The Battery Back Up Assembly
Installing The Switchable Battery Back Up Assembly IMI89–197
4.0 Installing The AC Power Plug
The charger assembly’s line cord is terminated with a typical continental European plug matching the CEE 7/7 standard. If this plug does not meet the site needs, you can install a plug of the proper type for your installation.
To install a line cord plug,
• familiarize yourself with the requirements for the plug that you plan to install on the unterminated line cord (the illustration shows a typical continental European plug matching the CEE 7 standard),
• strip off the insulation from the line cord wires according to the requirements for your plug,
• open the plug and slide its outer shell onto the line cord,
• connect the ground, neutral, and line wires according to the requirements for your plug,
• if your plug includes a clamp, tighten it on the line cord,
• reassemble the plug,
Test the installation for open and short circuits using an ohm meter.
L1
L2
Neutral (Blue)
Ground (Green/Yellow)
Line (Brown)
L3
L1, L2, and L3= strip length requirements
PLUS069
Neutral (Blue) Line (Brown)
Ground (Green/Yellow)
Clamp
Inside Of Plug
Line
Power
Source
Ground
Standard Wire Color
Wire Color
Europe USA
Brown Black
Green/Yellow Yellow
Installing A Typical Continental European AC Power Plug
Installing The Battery Back Up Assembly – 5
IMI89–197 Installing The Switchable Battery Back Up Assembly
2.0 Mounting The Charger Chassis
You must mount the charger chassis to the battery cabinet; however, the particular position that you chose for this mounting depends upon the method that you plan to mount the cabinet at the DXP Plus site.
•
If you plan to mount the battery cabinet on a backboard at the side of the common equipment cabinets, you must attach the charger, with its cables pointing toward you, to the left end of the battery cabinet as you face the cabinet’s battery opening.
•
If you plan to mount the battery cabinet below the main common equipment cabinet on the same backboard
(single common equipment cabinet installations), you must attach the charger, with its cables pointing toward you, to the right end of the battery cabinet as you face the cabinet’s battery opening.
•
If you plan to mount the battery cabinet on the back side of a standard 23–inch double equipment rack with the common equipment cabinets mounted to the front side of the rack, you must attach the charger, with its cables pointing away from you, to the to the left end of the battery cabinet as you face the cabinet’s battery opening.
To mount the charger chassis,
1. Choose the method of battery cabinet mounting, and orient the charger so that it is facing properly for the mounting scheme.
2. Remove the front panel from the empty battery cabinet, and save the retaining hardware.
3. Remove the wiring access plate from the end of the battery cabinet.
4. Route the black battery connection wires through the wiring access hole.
5. Attach the charger chassis to the battery cabinet with the three supplied screws.
bb480k
Wiring Access Plate
Charger Chasis
Battery Cabinet
Mounting The Charger For Separate Backboard Installations
6 – Installing The Battery Back Up Assembly
Screws (3 Places)
Installing The Switchable Battery Back Up Assembly
Battery Cabinet
Wiring Access Plate
Charger Chasis bb480L
Screws (3 Places)
Mounting The Charger For Below Main Cabinet Installations bb480j
Wiring Access Plate
Charger Chasis
IMI89–197
Screws (3 Places)
Battery Cabinet
Mounting the Charger For Double Rack Installations
Installing The Battery Back Up Assembly – 7
IMI89–197 Installing The Switchable Battery Back Up Assembly
CAUTION
The complete battery back up assembly is heavy. The charger chassis, empty battery cabinet, and wiring weigh approximately 25 pounds and all the batteries together weigh approximately 130 pounds for a combined assembly hanging weight of approximately 155 pounds.
You can mount the battery cabinet at several different locations.
•
You can mount the battery cabinet on a separate backboard located to the right of the common equipment cabinet location. Locate the battery cabinet as detailed in the illustration on the facing page.
•
At sites that employ only a main equipment cabinet, you can mount the battery cabinet directly below the main common equipment cabinet on the same backboard.
•
You can mount the battery cabinet in the middle of a standard 23–inch equipment rack if you wish. This can be a companion rack set next to the one where you have mounted the DXP Plus cabinets. Alternately, you can use a self-supporting, two-sided rack with the DXP Plus cabinets mounted on one side and the battery cabinet mounted on the other side directly behind and slightly above the main common equipment.
Remember from the Section 2.0 discussion, you must attach the charger chassis to the battery cabinet in a orientation that supports the cabinet mounting.
NOTE: The following instructions describe how to mount the battery cabinet using a backboard.
1. Add a second backboard to the right of the backboard that supports the DXP Plus common equipment cabinet.
Be sure that this backboard bridges the studs that support the underlying wall material. Securely attach the backboard to the mounting surface. (Suitable backboards are available commercially or you can construct one out of 3/4-inch plywood.) You must drive the hardware that secures the backboard to the mounting surface into the underlying wall studs instead of just into the wall material alone.
2. Refer to the illustration for the locating dimensions required for the mounting screws, and mark their locations on the backboard. You must attach the cabinet vertically to the backboard.
3. Drill holes in the backboard of a proper size to accommodate the hardware being used.
4. Insert the two top screws into the backboard and tighten them to within approximately 1/8–inch of the surface.
5. Hang the cabinet on the top screws using the top mounting holes in the rear mounting flange of the cabinet.
Note that these holes are elongated with an enlargement at one end. This feature allows the cabinet to slide down on the screws to secure the mounting when the cabinet is hung on them.
6. Use the openings for the middle and lower set of mounting screws as a guide, and mark the location for the remaining screws.
7. Lift the cabinet from the top screws and set it aside while preparing the holes for the remaining screws.
8. Rehang the cabinet as discussed in step 6.
9. Insert the lower screws into the backboard and tighten them to within approximately 1/8-inch of the surface.
8 – Installing The Battery Back Up Assembly
Installing The Switchable Battery Back Up Assembly IMI89–197
BB480a
Mounting The Battery Cabinet
Installing The Battery Back Up Assembly – 9
IMI89–197 Installing The Switchable Battery Back Up Assembly
3.0 Assembling and Wiring The Batteries In The Cabinet
3.1
Installing The Batteries
Install the batteries in the cabinet with their terminals facing the cabinet opening. The batteries set in place, and you do not need to anchor them to the cabinet.
Installing The Batteries
10 – Installing The Battery Back Up Assembly
PLUS003
Installing The Switchable Battery Back Up Assembly IMI89–197
3.2
Strapping The Batteries
You must strap the batteries together using the supplied strapping bars and hardware. Use three strapping bars at each strapping location, and install the hardware as shown in the illustration.
BB480c
Strapping The Batteries
# 10-32 Machine Screw
#10 Flat Washer
Battery Straps
Battery Terminal
#10 Flat Washer
#10 Lockwasher
#10 Hex Nut bb480h
Attaching The Strapping Hardware
Installing The Battery Back Up Assembly – 11
IMI89–197 Installing The Switchable Battery Back Up Assembly
3.3
Wiring The Batteries
The charger has a pair of negative wires and a pair of positive wires(designated by red sleeving near one end of the wires). This two-wire arrangement divides the current carrying load between the two wires of each pair. The cabinet’s assembly package includes two individual black wires that you use to wire the circuit breaker to the batteries. Again, two wires divide the current carrying load between both wires.
The negative wires from the charger are terminated with smaller size terminals than the those that terminate the charger’s positive wires. Connect the smaller (negative) terminals to the circuit breaker and the larger (positive) terminals to the positive battery post. The individual wires that you use to connect the circuit breaker to the battery post are also terminated with a large terminal on one end and a small terminal on the other. Connect the smaller terminals to the circuit breaker and the larger terminals to the negative battery post.
Wire the batteries as shown in the schematic. Use the supplied hardware to connect the wires to the batteries per method shown in the detailed drawing.
Once you have wired the batteries, attach the front cover to the cabinet with the supplied hardware.
+
-
Two Black Wires With Red Sleeving
(Positive Lead)
Circuit Breaker
Two Black Wires
(Negative Lead)
-
Two Black Wires
(Negative Lead)
Strap (Four Places)
+
-
+
-
+
-
+
-
+
Charger Batteries
Connecting The Wire Harness
12 – Installing The Battery Back Up Assembly
PLUS005
Installing The Switchable Battery Back Up Assembly IMI89–197
#10-32 Machine Screw
Wire Terminal
Battery Terminal
Wire Terminal
#10 Flat Washer
#10 Lockwasher
#10 Hex Nut bb480i
Attaching The Wiring Hardware
BB480e
Installing The Front Cover
Installing The Battery Back Up Assembly – 13
IMI89–197 Installing The Switchable Battery Back Up Assembly
4.0 Connecting The Battery Back-Up Assembly To The System
1. Connect the AC power and turn on the power supply switch in both DXP Plus main and expansion cabinets.
CAUTION
Always connect the AC power, and turn on the power supplies before you connect the battery back-up cables. Using a different connection sequence could cause equipment damage.
2. Connect a battery back-up cable between the charger cabinet and the power supplies in the DXP Plus main and expansion cabinets.
3. The battery back-up assembly includes a charger that maintains the batteries at full charge. Once you have installed the cabinet assembly, connect its AC power cord to the same AC outlet surge protector that
powers the DXP Plus main common equipment cabinet.
PLUS004
Circuit Breaker
Power Line
Surge Protector
Dedicated
AC Outlet
Connecting The Battery Assembly To The System
14 – Installing The Battery Back Up Assembly
Installing The Switchable Battery Back Up Assembly IMI89–197
5.0 Verifying The Battery Voltage
Every three months, use an accurate voltmeter to measure the no-load voltage of the battery back-up assembly.
The measured voltage range should be within 27–34.5 volts when the batteries are at full charge.
If the no-load voltage is lower than 27 volts, measure the charging voltage supplied by the common equipment cabinet. The measured charging voltage must be 35 volts maximum.
If the charging voltage is low or if the voltage of freshly-charged batteries is no greater than 30 volts, contact your technical service representative.
{
Green Status Lights
On = Batteries fully charges (>32 V)
On = Batteries under charged (>30 V)
On = Batteries low (>27 V)
On = AC power on
PLUS002
Fuse 5 AMP slow blow type
Measured Voltage
(charger on and batteries fully charged)
{
= +34.5 GND
= +34.5 GND
= -34.5 Volts
= -34.5 Volts
Verifying The Battery Voltages
Installing The Battery Back Up Assembly – 15
IMI89–197 Installing The Switchable Battery Back Up Assembly
6.0 Special Cautionary Battery Information
•
Do not dispose of batteries in a fire as the cells may explode. Check with the local codes for possible disposal instructions.
•
Do not open or mutilate the batteries. Released electrolyte is corrosive and may cause damage to the eyes or skin. It may be toxic if swallowed.
•
Exercise care in handling batteries in order not to short the battery with conducting materials such as rings, bracelets, and keys. The battery may over-heat and cause burns.
•
Charge the batteries provided with or identified for use with the DXP Plus digital communications system only in accordance with the instructions and limitations specified in this publication.
•
Observe proper polarity orientation when installing the batteries.
•
Do not mix old and new batteries in the assembly.
•
Do not mix batteries of different sizes or from different manufacturers in this product.
NOTICE
This symbol, when encountered on the equipment cabinet or on other installed hardware, means: CAUTION—refer to the instruction manual.
Accredited by the Dutch Council for Certification for certification and registration activities.
Comdial’s Quality Management System Is
Certified To The ISO 9001 Standard.
R
Charlottesville, Virginia 22901-2829
World Wide Web: http://www.comdial.com/
Troubleshooting The DXPT1 Digital Carrier Transmission Option
On The DXP Plus Digital Communications System
What This Document Contains
3.2
3.3
3.4
4.
4.1
2.3
2.4
3.
3.1
1.
1.1
1.2
1.3
2.
2.1
2.2
4.6
4.7
4.8
5.
5.1
5.2
4.2
4.3
4.4
4.5
6.
A.
Defining The T1 Terms 2
Introducing The DXPT1 6
Describing The Channel Service Unit (CSU) 6
Considering Pre-Installation Details 7
Troubleshooting The Physical Layer 8
Selecting Functions With DIP Switches SW1-1 Through SW1-8 8
Selecting Functions With DIP Switches SW2-1 Through SW2-8 8
Selecting Functions With DIP Switches LIU-1 Through LIU-4 9
Setting Up The DXOPT-SYN (Sync) Card 9
Troubleshooting The Protocol Layer 10
Defining The Signalling Bits For The E & M Protocol 10
Defining The Signalling Bits For The Direct Inward Dial (DID) Protocol 11
Defining The Signalling Bits For The Ground Start Protocol 11
Defining The Signalling Bits For The Loop Start Protocol 12
Using The Diagnostic Function 13
Understanding The Diagnostic Switches And Indicators 13
Requesting Cold Start Information 14
Requesting Information On Received Signal Strength 15
Requesting Information On Switch Settings 16
Requesting AB Signalling 17
Requesting Information On Trunk Assignments 18
Requesting Information About Channel State 19
Using The Hexadecimal Codes For Remote Diagnostics 20
Selecting The T1 PAD Settings 21
Setting T1 Transmit Level 21
Setting T1 Receive Level 21
Solving T1 Problems 21
APPENDIX A (Superframe and Extended Superframe Formats) 22
Referring To Other Documents
Installing The DXPT1 Digital Carrier Transmission Option, IMI89–193
Carrier-To-Customer Installation DS1 Metallic Interface, ANSI T1.403–1989
Private Branch Exchange (PBX) Switching Equipment for Voiceband Applications, 4.10 “Digital
Signaling and Supervision”, EIA/TIA–464A
This manual has been developed by Comdial Corporation (the “Company”) and is intended for the use of its customers and service personnel. The information in this manual is subject to change without notice. While every effort has been made to eliminate errors, the Company disclaims liability for any difficulties arising from the interpretation of the information contained herein.
The information contained herein does not purport to cover all details or variations in equipment or to provide for every possible contingency to be met in connection with installation, operation, or maintenance. Should further information be desired, or should particular problems arise which are not covered sufficiently for the purchaser’s purposes, contact Comdial, Inside Sales Department,
Charlottesville, Virginia 22906.
Printed in U.S.A.
IMI89–207.01
7/95
R
IMI89–207 Troubleshooting The DXPT1 Installation
1 Defining The T1 Terms
Bipolar
A bipolar signal is composed of alternating pulses that both represent a digital logic 1. The positive pulse is a (+) and the negative pulse is a (-). Zero volts represents a space, or digital logic 0.
Bipolar Violation (or error)
A bipolar error is a digital logic 1 (or mark) that has the same polarity as its predecessor.
NOTE: Every time the system regenerates the signal stream, it corrects any bipolar errors; therefore, it prevents end-to-end error checking from using bipolar errors.
B8ZS (Binary Eight Zero Substitution)
This is a technique to send an all-zero channel without violating the ones-density requirement (a single one in each channel and no more than 15 zeros in a row). Voice transmission will not allow an all zero channel. The system accomplishes B8ZS suppression by inserting a special bipolar error that is interpreted, not as an error, but an all zero channel. The B8ZS feature replaces the all-zero channel two different ways. The feature replaces the all-zero channel with the sequence 000 + - 0 - + if the preceding pulse was a +, and the feature replaces the all-zero channel with the sequence 000 - + 0 + - if the preceding pulse was -. The + represents a positive pulse, the - represents a negative pulse, and 0 represents no pulse. Set the B8ZS feature with switches SW1–5 and SW1–6.
CAS (Channel Associated Signalling)
The Channel Associated Signalling is the only inbound signalling method currently supported by the
DXPT1 board.
COFA (Change of Frame Alignment)
When switch SW2-6 is off, the green LED on the DXPT1 indicates whether the network source or the network span caused the last frame synchronization. (This indication disregards the first re-sync at cold start or a system reset —cold start and reset causes the network source to re-sync.) A COFA occurs if the network source does a re-sync. The COFA is a diagnostic tool that identifies the source of the loss of frame synchronization.
CPE/Carrier Equipment
The DXPT1 is normally classified as Customer Premise Equipment (CPE). If you use SW2–2 to configure the DXPT1 board to use the internal CSU while in the ESF mode, the network may require that the system be classified as Carrier Equipment (CE). The information packet that the DXPT1 board sends to the network contains a facility data link (FDL) maintenance message that has a bit in it that provides this identification.
CRC (Cyclic Redundancy Check)
A method of checking errors from the transmission source to the destination. For T1 operation, CRC caculates a checksum depending on the data in a frame. The system uses CRC in ESF mode exclusively.
(You must enable CRC with DIP switch SW2-4).
Delay Dial E&M, DID Protocol Type
Once seized by a calling system, the system being called makes A=1 and B=1 until it is ready to receive digits. When it is ready to receive digits, it makes A=0 and B=0. The system uses a delay dial protocol when wink protocol timing is not compatible to the network.
Dial Pulse – T1
Dial pulse is a method of sending address digits (numbers) using A and B bits logic bits instead of sending DTMF tones. Some carriers may not support dial-pulse signalling. While the method is slower when compared with tones, it requires no DTMF receivers.
2 – Troubleshooting The DXPT1 Installation
Troubleshooting The DXPT1 Installation IMI89–207
Direct Inward Dial (DID) T1 Trunk
DID is a protocol for inbound calls where the network sends the extension number during the beginning of the call. The system supports the 0 through 7 inbound digits. The network does not translate the digits to a valid extension—the system’s DID translation tables perform this action.
DS-0 (Digital Signal-Level Zero)
Digital Signal-Level Zero is a single 64Kbit channel inside a T1 span.
E & M T1 Trunk
E&M is a signalling protocol that supports both inbound and outbound digits. Inbound digits from the network are already translated to a 3–digit or 4–digit valid extension. E & M is symmetrical from both ends and ignores the subscriber/office classification of other trunks. Use this signalling protocol for interconnecting two DXP Plus systems.
Extended Superframe Mode (ESF)
Extended Superframe Mode consists of 24 frames. The frame bit uses only 6 frames leaving 18 bits for other purposes. These spare 18 bits provide 6 bits for CRC information and 12 bits for a facility data link.
The facility data link is for maintenance information (as defined by the ANSI T1.403 specification). Like the superframe mode, the 64–Kbit user channels have 24 frames available for use.
Ground Start T1 Trunks
Ground start is a call signalling protocol that monitors only outbound digits and supports disconnect supervision. Ground start protocol supports only the subscriber end of the communications link
FDL (Facility Data Link)
The Facility Data Link is a 4–Kbit communication link from the network to the DXPT1 board only when the board is operating in the ESF mode. The system sends preemptive messages (for example, yellow alarm and loopback), if needed, and sends error packets to the network once a second. The packets contain alarm history in accordance with the ANSI T1.403 specification.
Fractional T1
Fractional T1 is a T1 span where the user uses less than 24 channels. The DXPT1 board allocates eight or
16 channels to a fractional T1 but does not reallocate unused channels in the eight, 16, or 24 mode to other resources. A fractional T1 in ESF mode will nullify the CRC and other error checking capability since the network shares channels.
Immediate Start Protocol State
Once a calling system seizes a called system, the calling system sends address digits to the called system without requiring an acknowledgement. Inbound immediate start protocol does not support tone dial.
Dial-pulse is adequate however. Immediate start protocol is applicable to DID and E&M tie lines.
Inband Signalling
A signalling method where the system sends overhead signalling along with channel traffic.
ISDN (Integrated Services Digital Network) Primary Rate (also called PRI)
Currently not offered by the DXPT1 board.
Loopback Local
An operation method that loops the DXPT1 board’s transmit output and receive input paths. The loopback terminates all traffic and halts call processing. While in this idle condition, the system continues to transmit the T1 transmit stream to the network but it will not answer incoming calls. If the remote T1 equipment is the clock source (primary or secondary) for the DXOPT-SYN card, the remote equipment terminates the reference signal because the network receive circuit is open in local loopback. You initiate local loopback by setting the appropriate SW1 switches. The main purpose of local loopback is to verify the DXPT1 board’s ability to synchronize properly. Loopback local operation is applicable to superframe adn extended superframe modes.
Throubleshooting The DXPT1 Installation – 3
IMI89–207 Troubleshooting The DXPT1 Installation
Loopback Payload
The loopback payload feature is an ESF-only method of loopback which loops the network receive input path to the remote T1 equipment’s transmit output path. This loopback method does not loop the first bit of each frame to allow the DXPT1 board’s facility data link to continue to transmit maintenance information. You can use switches SW2–7 and SW2–8 to manually initiate the payload loopback or you can allow the network to send an FDL message to initiate or restore the payload loopback. The DXPT1 board goes out-of-service during the loopback time.
Loopback Remote
The loopback remote feature loops the network receive input path to the remote T1 equipment’s transmit output path. The remote loopback feature terminates all traffic and halt any call processing. You can use the SW2 switches to manually initiate remote loopback or you can allow the network to remotely initiate the condition. In superframe mode with SW2–1 set to on, the network can send a special in-band pattern
(00010001000100010001.... min 5 seconds) to cause the DXPT1 board to automatically enter the remote loopback mode. The network can disable the loopback by sending a different in-band pattern
(001001001001001001001.... min 5 seconds). In ESF mode, the DXPT1 board’s facility data link, or maintenance channel, can enable and disable remote loopback automatically or you can set SW2–7 on and SW2–8 off to manually enable remote loopback or set both switches off to manually disable the feature. Loopback remote operation is applicable to superframd and extended superframe modes.
LIU Line Interface Unit
The line interface unit is the interface between the T1 copper wires and the DXPT1 board’s framing circuitry. The LIU is responsible for separating the 1.544MHZ receive clock from the incoming stream and converting bipolar Alternate Mark Inversion (AMI) to 5–volt digital logic. The LIU also supports the automatic line build-out that regulates the transmit level according to the receive strength (LIU-2 switch).
Loop Start T1 Trunk
Loop Start T1 Trunk is a network protocol that monitors outbound digits to the DXPT1 board. This protocol does not support disconnect supervision. Loop start protocol supports the subscriber end of the communications path but does not support the office (network) end.
Primary Clock Reference
The straps on the DXAUX board designate the primary clock reference. Primary clock reference is the first choice reference clock used to synchronize the DXP Plus to the incoming span. If the system looses synchronization, it uses its secondary clock reference. If the secondary clock reference is not available, the DXOPT-SYN card’s variable clock oscillator (VCO) switches to the fixed oscillator on the DXSRV
(services) board. When it does this, slips occur.
Repeater
A repeater is a amplifying device that central office technicians place at approximately one mile intervals along a T1 circuit to boost the T1 signal. The T1 specifications allow a maximum of 50 repeaters along a communications path.
Slip
This term describes the condition that exists when the transmit 1.544 MHz clock is different from the receive 1.544 MHz clock. When the system collects or looses a frame of information due to the span frequencies being different, the system generates a slip error. Slip does not affect voice transmissions and may not affect modem traffic; however slip does effect digital data traffic. The DXPT1 board does not currently support digital data traffic. Also, at times a central office takes a T1 span out of service if too many slips occur—one or two a day is permissible (the carrier supplier will furnish you with an an exact number if you request that information from them).
4 – Troubleshooting The DXPT1 Installation
Troubleshooting The DXPT1 Installation IMI89–207
Smart-Jack (Network Interface Box)
A smart jack is a demarcation box provided by the central office. A smart jack provides isolation and increased signal drive (up to one mile) and can respond to loopback commands for diagnostic purposes.
The central office usually provides an 8–pin modular jack for T1 equipment connection. Pin 1 of the modular jack goes to pin 1 of the DXPT1 modular jack, and so on. Only pins 1 and 2 (DXPT1 receive), 4 and 5 (DXPT1 transmit) require connecting.
Superframe Mode (SF)
The standard T1 mode consists of 12 frames per superframe cycle. The first frame bit remains constant and rotates through a 12-bit pattern. By identifying the frame pattern, the system can select the sixth and twelfth frame for the AB bit signalling inband method. T1 parameters allow for 24 64–Kbit user channels.
Suppression
Suppression is a means to prevent more than 15 zeros in a row and not less than 1 pulse (mark) per channel. The DXPT1 board supports two suppression methods. These are the B7 method and the B8ZS method (selected by SW1–5 and SW1–6). The B7 method inserts a logic 1 in the seventh bit position of a channel if all bits are zeros. The B8ZS method inserts a bipolar violation that will be identified and stripped at the receiving end (selected by switches SW1–5, and SW1–6). Voice coding should not allow an all zero channel.
Unlock Alarm
On a normally operating DXPT1 board, the unlock alarm LED is always off. If this LED is on, it indicates that the phase lock loop creating the transmit 1.544 MHz frequency is defective. For this indicator to be meaningful, the DXOPT-SYN card must be synchronized (no red LEDs on). If the
DXOPT-SYN card is not synchronized, you must correct that situation.
Wink E&M, DID Protocol State
This effect is a quick response by a called system (A=1, B=1) to a calling system that seized the line. The response indicates that the called system is ready to receive address digits.
Yellow Alarm
The yellow alarm indicates that the network has lost its incoming frame synchronization. The DXPT1 board signalling is inactive for approximately three to four seconds during this alarm time, and the system halts all call processing. If the system clears the received yellow alarm within the time limit, the DXPT1 board’s inactive state terminates and call processing continues.
The system sends a yellow alarm to the network if it loses incoming frame synchronization or if the
DXPT1 loses communications to the CPU board. Received and transmitted yellow alarms can not exist at the same time. If such a situation occurs, the system inhibits the transmitted alarm.
ZBTSI (Zero Byte Time Slot Interchange)
Zero Byte Time Slot Interchange is a complex technique to insure that the T1 transmission meets the pulse density requirement. This ZBTSI technique is unpopular in the telephone industy, and the DXPT1 board does not support the feature.
Throubleshooting The DXPT1 Installation – 5
IMI89–207 Troubleshooting The DXPT1 Installation
1.1
Introducing The DXPT1
The DXPT1 is a digital interface board supporting up to 24 simultaneous calls on two pairs of wire. The advantages of T1 over single-channel systems are largely:
•
Cost savings (much lower price per channel)
Greater reliability
•
•
Uses less copper wires
Improved voice reproduction
More features available
T1 is over 20 years old but the services have been upgraded during this time (for example, extended superframe).
T1 uses time division multiplexing techniques which multiplexes 24 channels in a stream. Each channel is 8 bits wide. The total is 24 channels x 8 bits = 192 bits for user information. An additional bit is added at the beginning of the stream to identify the particular frame. A frame every 125 msec or 8000/second.
12 frames make up a superframe for standard T1. ESF mode requires 24 frames per superframe. The frame bit in superframe mode is used 100% of the time. The sequence for the frame bits is:
100011011100. The first bit of each frame (frame bit) repeats over and over
| |
A B Of the 12 frames, the 6th and 12th contain the “A” and “B” signalling bits respectively.
The signalling is inband (mixed with the channel). For the two binary bits (A and B), only four combinations are possible (00, 01, 10, 11). These bits are assigned according to the signalling protocol (for example, E&M, DID, Loop Start, and Ground Start). See section 3, “Troubleshooting The Protocol
Layer.”
The span speed is 1.544 MHz (193 x 8000/sec).
For extended superframe (ESF), the frame-related bits in the 24 frames are:
ESF Framing Format mcm0mcm0mcm1mcm0mcm1mcm1...6 frame bits (0 or 1) on frames 4, 8, 12, 16, 20, 24 (2 Kbps)
12 maintenance bits (m) (4 Kbps)
6 CRC error checking bits (c), if enabled (2 Kbps)
Therefore, all of the 24 non-user bits (frame, maintenance, and error checking) use a bandwidth of 8 Kbps out of the total bandwidth of 1.544 Mbps.
The A and B signalling bits are inserted over the least significant bits (LSB) of each channel in the 6th and 12th frame respectively. This does not change the speech encoding enough to be detected by the user.
The A and B signalling bits are repeated in the 18th and 24th frames.
1.2
Describing The Channel Service Unit (CSU)
The DXPT1 board has a CSU built into the board. This allows direct connection to the network (DS1 level). If a CSU was not built-in, the connection would be DSX-1 and would only transmit 655 feet to the nearest 66-type connector block. The CSU increases signal drive to 1 mile, provides electrical isolation
(1500 volts), and provides automatic line build out (ALBO). The output is set depending on the received signal level strength. When a strong signal is received, the transmit level is -15 dB. When a weak signal is received, the transmit level is 0 dB. This ability to adjust output levels prevents over driving a line repeater in the network, if directly connected. If a customer still wants to add an external CSU, he/she may do so. Normally, the DXPT1 is connected to a central office “smart” jack. The customer’s savings from using the built-in CSU can easily amount to approximately one thousand dollars, at today’s prices.
NOTE: If an external CSU is added by the installer for the purposes described above, and the mode is
Extended Superframe, check the SW2-2 switch for the correct ID, if in conflict.
6 – Troubleshooting The DXPT1 Installation
Troubleshooting The DXPT1 Installation
1.3
Considering Pre-Installation Details
IMI89–207
CAUTION
For operation with the DXP Plus, the T1 board must be Revision B or higher. If the T1 board that you are installing is a lower revision, contact Comdial Technical Services (1–800–366–8224) for advice before you proceed with the installation..
If you are the installer, you must consider the following things to ensure a proper installation.
A. Determine the T1 trunk configuration and communicate this to the central office and/or the network for coordination and assignment of service.
B. Determine whether the dial type is tone or pulse.
C. If DID or E&M protocols are going to be used, determine the number of DTMF receivers needed.
D. If the above protocols are used, coordinate the blocks of numbers assigned with the data base.
E. For DID and E & M protocols, determine the type. Wink start, delay dial, or immediate start are available. Wink start is very popular. If you choose immediate start inbound, select dial pulse over tone dial to ensure that the DXP has enough time to react.
F. AT&T will not supply dial tone unless the customer ordered this feature. However, if you enable the automatic route selection (ARS) feature, it will supply dial tone.
G. Configure an interface cable (8-conductor cable terminated with modular jacks) to connect to the
DXPT1. See section 4 in Installing The DXPT1 Digital Carrier Transmission Option, IMI89–193 for more instructions. Pins 7 and 8 must be open at the DXP Plus end for DXPT1 Issue 2 while Issue 3 boards and above will not require pins 7 and 8 to be open. A smart-jack often connects pins 7 and 8 to chassis ground. If the chassis ground is connected at the smart-jack, the DXP Plus receive will most likely show loss of signal. (Pins 1 and 2 are shorted to 7 and 8 to allow for an inverted cable to be used.)
H. Order spare boards, if needed.
I.
Make sure you have a synchronization card to install on the auxiliary board.
J.
Determine the optimum DXPT1 board configuration. If a T1 board occupies a universal slot, more stations are possible than by using analog trunk boards.
K. If fractional T1 is being considered, decide whether 8-, 16-, or 24-channel mode is most beneficial.
L. Verify that primary lightning protection (such as gas discharge tubes) is provided where the T1 copper wires enter the building. This should be the case when a smart jack is installed by the central office. Primary protection is a must since the DXPT1 contains only secondary protection.
M. For a DXP-to-DXP application, where no outside network exists, only one synchronization card is required. The designated “master” DXP Plus does not require a synchronization card.
Throubleshooting The DXPT1 Installation – 7
IMI89–207 Troubleshooting The DXPT1 Installation
2 Troubleshooting The Physical Layer
SW1, SW2, and the LIU switches must be set up according to the customer’s requirements. See Installing
The DXPT1 Digital Carrier Transmission Option, IMI89–193 for directions.
2.1
Selecting Functions With DIP Switches SW1-1 Through SW1-8
NOTE: SW1 switch contents will be updated only during a reset operation.
The mode, superframe or extended superframe, is critical. If set wrong, the board will not find frame sync causing the red Sync LED to light.
Yellow alarm mode (SW1-4) is always off, unless the customer is in Japan.
Suppression is defaulted to B7. If digital data is ever presented to the DXPT1 board from a drop and insert multiplexer (mux), or any other means, B8ZS will be required even though the channel is disabled in the DXP Plus. The digital data could be all zeros violating the ones density requirement of 1 in 8 bits in a channel. The network or mux must also have B8ZS enabled. If B8ZS is being sent in any channel the green LED above SW1 will flicker if SW2-6 is enabled. Do not set SW1-5 and SW1-6 to the “no suppression” setting unless approved by Comdial Engineering. The “no suppression” setting is for possible future needs.
SW1-7 and 8 are critical to the channel capacity required.
2.2
Selecting Functions With DIP Switches SW2-1 Through SW2-8
SW2-1 is valid only in the superframe mode. This switch must be “on” if the network is capable of initiating an inband loopback. The switch will not cause a remote loopback but it will look for the command from the network. Leaving the switch “on” does not hurt anything whether the network can perform the loopback operation or not. A reset is not required when changing the switch.
SW2-2 is programmed at reset in the ESF mode only, and it will always be “off” (default) unless the network requires the facility data link messages to be a different ID. The default is customer premise equipment. If the network requests that the messages have a carrier-type header ID, turn the switch “on” and reset the board. This will probably never need to be “on”.
SW2-4 is for reporting CRC errors in the ESF mode, if the network has the ability to support the CRC feature. The default position is “off” to prevent false errors when the error checking is not supported by the network.
SW2-5 is to allow or prevent the sending of facility data link message packets in ESF mode during a preemptive yellow alarm and loopback messages. The ANSI specification allows FDL packets to be stopped during a yellow alarm and loopback, but some customers/networks want the packets to continue.
Switch changes require a reset to be programmed.
SW2-6 defines the meaning of the green LED labeled “B8ZS/COFA.” A reset is not required when changing this switch. When the switch is “off” (default), the LED indicates COFA detected. When the switch is “on,” the LED indicates B8ZS detected. B8ZS detection is handy to verify if the network is sending B8ZS. If so, and the B8ZS suppression is not set (SW1-5, 6), the B8ZS will be seen as bipolar alarms, and recorded as such, even though they are not,
SW2-7, 8 are manual loopback requests for diagnostic reasons. Local loopback verifies the ability of the
DXPT1 to sync on itself to insure frame syncing problems are not caused by the DXPT1 board. These switches are rarely used to enable remote loopback and payload loopback.
NOTE: A local loopback will disable the synchronization card reference causing an automatic switch to the next reference. If only one reference is configured, the system defaults to the DXP Plus fixed oscillator on the services board.
8 – Troubleshooting The DXPT1 Installation
Troubleshooting The DXPT1 Installation IMI89–207
2.3
Selecting Functions With DIP Switches LIU-1 Through LIU-4
There are four LIU switches. The first switch will change the receive sensitivity from -26 dB to -36 dB.
Changing to -36 dB for extra long loops (1 mile) is not recommended unless the DXPT1 will not maintain frame sync. In the -36 dB setting, noise could be a problem because of increased sensitivity.
The LIU-2 switch sets the transmit signal level. The transmit signal level has nothing to do with the audio voice levels. The default is manual “on” and the transmit level is determined by LIU-3 and 4 settings.
LIU-3 and LIU-4 are defaulted “off” which corresponds to 0 dB (strong signal).
For applications where the DXPT1 is directly connected to a nearby repeater, the automatic mode is preferred (LIU-2="off") to keep from over driving the repeater. Repeaters are very sensitive on their inputs. In auto mode, the transmit is determined by the receive level according to the following chart:
LIU-3 and 4 are ignored in auto mode.
IF LEVEL RECEIVED IS
0 to -7.5 dB
-7.5 to -15 dB
-15 to -22.5 dB
-22.5 to -26 dB
LEVEL TRANSMITTED IS
-15 dB
-7.5 dB
-7.5 dB
0 dB
If in auto mode and LIU switch 3 or 4 is changed, a re-sync is required to reset the new setting.
Unplugging the T1 span in and out is an easy way to cause a re-sync.
2.4
Setting Up The DXOPT-SYN Synchronization Card
Program the synchronization card by strapping the two strap blocks on the auxiliary board. A reference clock from each T1 board is presented. You can strap the board so that one T1 clock source is the primary clock reference, and another T1 source is the secondary clock reference. The secondary clock reference is then used in case the primary span fails. If only one T1 board is installed, we recommend that you strap the auxiliary board so that the one T1 source is serving as both the primary and secondary reference.
Otherwise, don’t strap the secondary strapping block. See section 4, Installing The DXPT1 Digital Carrier
Transmission Option, IMI89–193. The green LEDs on the sync card verifies the presence of a reference source. If the green LEDs are off, check the straps, and make sure that the DXPT1 board is not in the local loopback mode.
If one or more of the green LEDs are lit, the sync card’s red LED (Unlocked) should be off. Do not place the sync card’s switch in the manual mode during normal operation. The manual mode switch is for maintenance when you want to force the use of the primary or secondary reference. The automatic mode allows automatic selection of the secondary reference in the event that the primary reference is lost. If the sync card does not synchronize, and the green LEDs are lit, the synchronization card is probably bad. The only other possibility is that the sync card detection circuit on the services board is not working, which is unlikely. If the DXPT1 board is in an expansion cabinet, be sure the interface boards are multilayer (that is, not transparent). Earlier interface boards, of the non-multilayer type, are subject to electrical noise.
Throubleshooting The DXPT1 Installation – 9
IMI89–207 Troubleshooting The DXPT1 Installation
3 Troubleshooting The Protocol Layer
Four protocols are supported:
•
E & M
•
DID
•
Ground Start
•
Loop Start
Ground and loop start are subscriber-end only (DXP Plus end) not office-end (network end).
Before starting protocol layer troubleshooting, make sure you have completed all physical layer troubleshooting to ensure that no alarms are occurring and that the DXPT1 board has no red LEDs lit except for the large status LED.
Troubleshooting the protocol layer consists of checking the A and B transmit and receive signalling bits.
Depending on the protocol that is active and on which function is occurring, A and B signalling bits can be a digital one (“1") or a zero (”0"). In some cases, the level (“0" or ”1") doesn’t matter and could be either one (X). These levels are designated by a “0,” “1,” or “X” in the following tables.
When the function involves a user dialing a number with a rotary dial, the signalling bit designated by
“DP” in the following tables, represents the dial pulse (make= 1 ; break = 0). For a ground start protocol, the signalling bit representing a dial pulse will be a digital one (“1") when a tone dial is used in place of a rotary dial.
NOTE: In the table below, an X is a don’t care. Signalling can be a 1 or 0. DP is a dial pulse (make = 1, break = 0).
3.1
Defining The Signalling Bits For The E & M Protocol
FUNCTION
^
OUTGOING CALL
Idle
DXP off-hook
Wink
Wink
Dial pulsing
Wait for ANS
Far end ANSW
INCOMING CALL
Idle
CO goes off-hook
DXP sends wink
DXP after wink
Far end DP
Far end wait FR ANS
DXP answers call
1
0
0
0
0
0
1
A
1
1
0
1
DP
1
1
TRANSMIT
B
1
1
0
1
DP
1
1
1
0
0
0
0
0
1
A
0
0
1
1
0
0
0
1
1
0
1
DP
1
1
RECEIVE
X
X
X
X
X
X
X
B
X
X
X
X
X
X
X
EIA/TIA 464-A
STANDARD
^
Wink on
Wink off
Make=1, Brk=0
10 – Troubleshooting The DXPT1 Installation
Troubleshooting The DXPT1 Installation
3.2
Defining The Signalling Bits For The Direct Inward Dial (DID) Protocol
FUNCTION
INCOMING CALL
Idle
CO goes off-hook
DXP sends wink
DXP after wink
Far end DP
Far end wait FR ANS
DXP answers call
TRANSMIT
A B
0
0
0
0
1
0
1
0
0
0
0
1
0
1
RECEIVE
A B
0
0
1
1
DP
1
1
X
X
X
X
X
X
X
EIA/TIA 464-A
STANDARD
Make=1, Break=0
IMI89–207
3.3
Defining The Signalling Bits For The Ground Start Protocol
FUNCTION
OUTGOING CALL
Idle
PBX grounds ring
PBX grounds tip
PBX removes ring ground
PBX loop closed
Dial pulsing
Dialing CMPL
INCOMING CALL
Idle
CO grounds tip
Ringing interval
PBX presents call
PBX answers call
Normal talking STAT
DISCONNECT PBX
Talking state
PBX opens loop
CO removes tip ground
CO ABANDONS INCOM...
Talking State
CO removes tip ground
PBX opens loop
PBX ABANDONS BEFORE
CO HAS RETURNED TIP
GROUND
PBX waiting tip ground
PBX removes ring ground
TRANSMIT
A B
0
0
0
0
1
1
1
0
0
0
0
0
0
1
DP
1
1
0
0
1
1
1
1
1
1
1
1
1
1
1
1
1
1
1
1
1
0
0
0
0
0
1
0
0
1
0
0
0
0
0
0
0
0
0
0
0
0
0
1
1
0
RECEIVE
A B
0
1
X
1
X
X
X
X
1
X
1
1
X
X
X
X
X
X
X
1
1
X
X
EIA/TIA 464-A
STANDARD
“1" vs DP for DTMF
Idle state
CO hangs up
Idle state
Throubleshooting The DXPT1 Installation – 11
IMI89–207 Troubleshooting The DXPT1 Installation
3.4
Defining The Signalling Bits For The Loop Start Protocol
FUNCTION
OUTGOING CALL
Idle
PBX loop closed
PBX pulsing
Dialing CMPL
INCOMING CALL
Idle
CO sends ring
Interval between ring
PBX presents call
PBX answers call
Normal talking STAT
DISCONNECT PBX
PBX opens loop
Idle
CO ABANDONS INCOM...
CO applies ring
Interval between ring
CO abandons
PBX stop presenting
TRANSMIT
A B
0
0
0
0
0
0
0
0
1
0
0
1
0
1
DP
1
1
1
1
1
1
1
1
1
1
1
1
1
1
1
1
1
0
0
0
0
0
0
0
0
0
0
0
0
0
0
0
0
RECEIVE
A B
1
1
1
0
X
X
X
1
1
1
1
1
1
1
0
1
EIA/TIA 464-A
STANDARD
Waiting for dial tone
“1" vs DP for DTMF
12 – Troubleshooting The DXPT1 Installation
Troubleshooting The DXPT1 Installation IMI89–207
4 Using The Diagnostic Function
The diagnostic function on the DXPT1 board provides a method for obtaining information about the T1 operation. You can do this either on-site or from a remote location by sending and receiving coded messages. Remote operation is described in section 4.8.
4.1
Understanding The Diagnostic Switches And Indicators
The diagnostic portion of the DXPT1 board contains eight DIP switches, eight green LEDs, and a “clear” pushbutton for clearing functions. Set the DIP switches to request certain T1 system information. When testing from a remote location, using a computer and modem, you can similate the switch settings by sending a coded message.
The system responds to your request for information by lighting certain LEDs to provide you with the requested information. If you are testing from a remote location, the system responds by sending a coded message that similates the lighted LEDs.
Use the clear pushbutton to stop any counting function
(denoted by the LEDs sequencing) and reset the counter.
The diagnostic port is a monitor mode only access. You cannot cause harm to the equipment by moving the switches or pushing the clear pushbutton. Leaving any of the switches on will not cause any operational problems.
Since the operation is cryptic, the customer normally doesn’t use the diagnostic monitor. Functions of the port are to simplify problem solving in the field
Clear
Switch 1
Off
Switch 8
On
LED 1
LED 8
T1005
4.1.1 Determining Channel Number
The letters ABCDE in switch positions 4 through 8 are
DXPT1 Diagnostic Switches And Indicators used to designate a channel number in many of the tables used on the following pages. See the table below for the relationship between the letters ABCDE and channel numbers 1 through 24. (Example, a
DIP switch setting of 10100101 requests trunk assignments on channel 6).
CHANNEL A
7
8
5
6
3
4
1
2
OFF
OFF
OFF
OFF
OFF
OFF
OFF
OFF
B
OFF
OFF
OFF
OFF
OFF
OFF
OFF
OFF
C
OFF
OFF
OFF
OFF
ON
ON
ON
ON
D
OFF
OFF
ON
ON
OFF
OFF
ON
ON
E CHANNEL A
OFF
ON
OFF
ON
OFF
ON
OFF
ON
9
10
11
12
13
14
15
16
OFF
OFF
OFF
OFF
OFF
OFF
OFF
OFF
B
ON
ON
ON
ON
ON
ON
ON
ON
C
OFF
OFF
OFF
OFF
ON
ON
ON
ON
D
OFF
OFF
ON
ON
OFF
OFF
ON
ON
E CHANNEL A
OFF
ON
OFF
ON
OFF
ON
OFF
ON
17
18
19
20
21
22
23
24
ON
ON
ON
ON
ON
ON
ON
ON
B
OFF
OFF
OFF
OFF
OFF
OFF
OFF
OFF
C
OFF
OFF
OFF
OFF
ON
ON
ON
ON
D
OFF
OFF
ON
ON
OFF
OFF
ON
ON
E
OFF
ON
OFF
ON
OFF
ON
OFF
ON
Throubleshooting The DXPT1 Installation – 13
IMI89–207 Troubleshooting The DXPT1 Installation
4.2
Requesting Cold Start Information
When the DXP-T1 system is turned on, internal self-tests are run to determine the condition of the system. When you use this request, you are asking the system to provide you with the results of these tests. Upon making the cold start information request, the system verifies the following.
• operating mode is superframe (SF) or extended superframe (ESF),
•
FDL daughterboard (used for ESF) is installed on the T1 board and okay or not installed (or defective),
• channel capacity currently selected is 8, 16, or 24 channels,
• static RAM is okay or has read/write errors,
• internal CPU RAM is okay or has read/write errors.
4.2.1
Setting The DIP Switches For Cold Start Information
Set the DIP switches as shown in the following table. Switch 1 is the top switch. When the switch is moved to the right, it is turned on. The hex code shown is used for remote operation only.
SWITCH SETTINGS TYPE OF REQUEST
1 2 3 4 5 6 7 8 Provide results of all self-tests run during system start-up (cold start).
ON ON ON OFF OFF OFF OFF ON
HEX
CODE
E1
^
4.2.2
Reading The Cold Start Information From The LEDs
The Table below shows the cold start information that is revealed by the LEDs. LED 1 is at the top.
LEDs
1
OFF
2
OFF
ON
3
OFF
4
OFF
ON
5
OFF
OFF
ON
6
OFF
ON
OFF
7
OFF
ON
8
LED DEFINITIONS
^
Not used
SF mode
ESF mode
Always off
Either in SF mode or FDL board missing or bad
FDL board recognized (ESF only)
Selected channel capacity is 24
Selected channel capacity is 8
Selected channel capacity is 16
Static RAM has read/write errors
Static RAM is okay
Internal CPU RAM has read/write errors
Internal CPU RAM is okay
OFF
ON
Example: If you see the following LED light pattern, you can determine the cold start results from the above
LED definitions. (For remote testing, the lFDL board recognized system would send hex code 53.) m = LED off and | = LED on m
| = ESF mode m
| = FDL board recognized m = 24-channel m capacity
| = static RAM fully operational
| = internal CPU RAM fully operational
14 – Troubleshooting The DXPT1 Installation
Troubleshooting The DXPT1 Installation IMI89–207
4.3
Requesting Information On Received Signal Strength
When you use this request, you are asking the system to provide the signal strength of its received signals.
Upon making the received signal strength request, the system supplies you with the following information:
• the range in dB of the received signals.
4.3.1
Setting The DIP Switches For Received Signal Strength Information
Set the DIP switches as shown in the following table. Switch 1 is the top switch. When the switch is moved to the right, it is turned on. The hex code shown is used for remote operation only.
SWITCH SETTINGS TYPE OF REQUEST
1 2 3 4 5 6 7 8 Provide the dB range of the received signal strength.
ON ON ON ON ON ON ON ON
HEX
CODE
FF
^
4.3.2
Reading The Received Signal Strength Information From The LEDs
The Table below shows the received signal strength information that is revealed by the LEDs. LED 1 is at the top.
1 2 3
LEDs 1 through 4 not used (off)
4
LEDs
5
OFF
OFF
OFF
6
OFF
OFF
ON
7
OFF
ON
ON
ON ON ON
LED DEFINITIONS
8
ON
ON
ON
ON
-7.5 to -15 dB (medium signal)
-15 to -22.5 dB (weak signal)
-22 dB and below (spec is to -26 dB)
(very weak)
0 to - 7.5 dB (strong signal)
HEX
CODE
^
01
03
07
0F
NOTE: If signal is very weak from a long span of a mile or more, and frame synchronization is not being maintained, turn DIP switch LIU-1 on.
Throubleshooting The DXPT1 Installation – 15
IMI89–207 Troubleshooting The DXPT1 Installation
4.4
Requesting Information On Switch Settings
You can determine how particular DIP switches on the DXPT1 board are set by using one of the following requests. Depending on which request you make, the system supplies you with the following information:
•
DIP switch settings for SW1,
•
DIP switch settings for SW2,
•
DIP switch settings for LIU.
4.4.1
Requesting Information On DIP Switch Settings
Set the diagnostic DIP switches as shown in the following table. Switch 1 is the top switch. When the switch is moved to the right, it is turned on. The hex code shown is used for remote operation only.
SWITCH SETTINGS TYPE OF REQUEST
1 2 3 4 5
OFF
OFF
OFF
OFF
OFF
OFF
OFF
OFF
OFF
OFF OFFO
OFF
OFF
OFF
OFF OFF
OFF
OFF
OFF
ON
6
OFF
OFF
ON
OFF
7
OFF
ON
ON
OFF
8
ON
ON
ON
ON
Provide the DIP switch settings for SW1
Provide the DIP switch settings for SW1
Provide the DIP switch settings for LIU
Provide the DIP switch settings for the diagnostic switches (the diagnostic LEDs simply “mirror” the switch settings; that is,
LEDs 5 and 8 should be lit).
HEX
CODE
01
03
07
09
4.4.2
Reading The DIP Switch Settings Information From The LEDs
The diagnostic LEDs “mirror” the switch settings for the DIP switches requested. For example, if LED 1 is on, then switch 1 is on for the requested DIP switches. If LED 1 is off, then switch 1 is off, and so forth.
When requesting information on the LIU DIP switch settings, the system replies via LEDs 1 through 4.
LEDs 5 through 8 are not used in this application.
16 – Troubleshooting The DXPT1 Installation
Troubleshooting The DXPT1 Installation IMI89–207
4.5
Requesting AB Signalling
When you use this request, you are asking the system to reveal the A and B bits. Upon making the AB signalling request, the system supplies you with the following information:
•
A bit transmitted to the CO,
•
B bit transmitted to the CO,
•
A bit received from the CO,
•
B bit received from the CO.
4.5.1
Setting The DIP Switches To Request AB Signalling
Set the DIP switches as shown in the following table. Switch 1 is the top switch. When the switch is moved to the right, it is turned on. Use switches 4 through 8 (designated in the table by A through E) to select the channel you want to test (1 through 24). See the table in section 4.1.1 for the relationship between the 24 different letter groups and channel numbers. For remote operation, determine the corresponding hex code from Table 1.
SWITCH SETTINGS
1 2 3 4
OFF OFF ON A
5
B
6
C
TYPE OF REQUEST
7 8
D E
Provide AB signalling on the channel designated by ABCDE. See section 4.1.1.
HEX
CODE see
Table
1
4.5.2
Reading The AB Signalling Information From The LEDs
The Table below shows samples of the AB signalling information that is revealed by the LEDs. LEDs 5 through 8 are off. LED 1 is at the top.
1
ON
OFF
OFF
OFF
2 3 4
LEDs
5
OFF
ON
OFF
OFF
OFF
OFF
ON
OFF
OFF
OFF
OFF
ON
6 7 8 LED DEFINITIONS
LEDs 5-8 are off Transmitting A bit to central office
Transmitting B bit to central office
Receiving A bit from central office
Receiving B bit from central office
HEX
CODE
80
40
20
10
Throubleshooting The DXPT1 Installation – 17
IMI89–207 Troubleshooting The DXPT1 Installation
4.6
Requesting Information On Trunk Assignments
Make this request to receive information on the trunk assignments that have been made. Upon making this request, the system provides you with the following information:
• trunk type (ground start, DID, E&M, or loop start),
• dial type (rotary or tone),
• signalling protocol (immediate, wink, delay).
4.6.1
Setting The DIP Switches For Requesting Trunk Assignment Information
Set the DIP switches as shown in the following table to request trunk assignment information. Use switches 4 through 8 (designated in the table by A through E) to select the channel you want to test
(1 through 24). See the table in section 4.1.1 for the relationship between the 24 different letter groups and channel numbers. For remote operation, determine the corresponding hex code from Table 1. Switch
1 is the top switch.
1 2
SWITCH SETTINGS
3
ON OFF ON
4
A
5
B
6
C
TYPE OF REQUEST
7
D
8 Provide information about trunk
E assignments on the channel specified by the letters ABCDE (see the table in section
4.1.1).
HEX
CODE see
Table
1
4.6.2
Reading The Trunk Assignment Information From The LEDs
The Table below shows the trunk assignment information that is revealed by the LEDs. LED 1 is at the top.
1
ON
ON
OFF
OFF
OFF
2
OFF
ON
ON
OFF
3
OFF
OFF
OFF
ON
4
LEDs
OFF
OFF
OFF
OFF
5
ON
OFF OFF OFF OFF
6
OFF
OFF
7 8
LED DEFINITIONS
OFF
OFF
ON
ON
OFF
OFF
ON
OFF
ON
OFF
Ground start
DID
E&M
Loop start
Tone dial
Not used
Wink start
Delay start
Immediate start
Not used
No trunk assignments made
18 – Troubleshooting The DXPT1 Installation
Troubleshooting The DXPT1 Installation IMI89–207
4.7
Requesting Information About Channel State
Use this request to determine the state of the channel specified in the request command. Upon making this request, the system provides you with the following information:
• channel state (idle or busy).
4.7.1
Setting The DIP Switches For Requesting Channel State Information
Set the DIP switches as shown in the following table to request the state of the channel specified in the request command. Use switches 4 through 8 (designated in the table by A through E) to select the desired channel.(1 through 24). See the table in section 4.1.1 for the relationship between the 24 different letter groups and channel numbers. For remote operation, determine the corresponding hex code from Table 1.
Switch 1 is the top switch.
1 2
SWITCH SETTINGS
3
ON ON OFF
4
A
5
B
6
C
TYPE OF REQUEST
7
D
8 Provide information about the state of the
E channel specified by the letters ABCDE (see the table in section 4.1.1).
HEX
CODE see
Table
1
4.7.2
Reading The Channel State Information From The LEDs
The Table below shows the channel state information that is revealed by the LEDs. LED 1 is at the top.
1 2 3
LEDs
4 5 6 7 8
LED DEFINITIONS
OFF OFF OFF OFF OFF OFF ON ON The selected channel is in the idle state.
HEX
CODE
03
Throubleshooting The DXPT1 Installation – 19
IMI89–207 Troubleshooting The DXPT1 Installation
4.8
Using The Hexadecimal Codes For Remote Diagnostics
You can similate the diagnostic DIP switch settings, that are usually made on-site, by sending the following code sequence via modem to the remote DXPT1 board: tkmsg<space>(valid port number)<space>7B,(hex code)
The hexadecimal value that you use for the field code corresponds to a bit pattern that you are using to similate DIP switch settings. For example, to similate a switch setting of 11100001 (switches 1, 2, 3, and
8 on) use hex code E1 in the field position. (Switch 1 is the top switch as you look at the front edge of the
DXPT1 board. The switches are “on” when you move them to the right.).
After you have interrogated the DXPT1 board by transmitting a valid diagnostic code to it, the DXPT1 responds with a hex code that similarily represents a bit pattern that you can find in Table 1. This bit pattern represents the diagnostic LEDs located adjacent to the DIP switches on the DXPT1 board. For example, let’s assume you received the hex code 53 in response to a request for cold start information.
Since 53 (hex) represents a bit pattern of 01010011, it follows that LEDs 2, 4, 7, and 8 are lit. (LED 1 is the top LED in the group of eight on the DXPT1 board.) See the example in section 4.2.2.
Table 1. Hexadecimal Codes Related To Bit Patterns
Hex
Code
Bit Pattern
1 2 3 4 5 6 7 8
01 1 0 0 0 0 0
0 1 1 0 0 0 0 1
0 1 1 0 0 0 1 0
0 1 1 0 0 0 1 1
0 1 1 0 0 1 0 0
0 1 1 0 0 1 0 1
0 1 1 0 0 1 1 0
0 1 1 0 0 1 1 1
0 1 1 0 1 0 0 0
0 1 1 0 1 0 0 1
0 1 1 0 1 0 1 0
0 1 1 0 1 0 1 1
0 1 1 0 1 1 0 0
0 1 1 0 1 1 0 1
0 1 1 0 1 1 1 0
0 1 1 0 1 1 1 1
0 1 1 1 0 0 0 0
0 1 1 1 0 0 0 1
0 1 1 1 0 0 1 0
0 1 1 1 0 0 1 1
0 1 1 1 0 1 0 0
0 1 1 1 0 1 0 1
0 1 1 1 0 1 1 0
0 1 1 1 0 1 1 1
0 1 1 1 1 0 0 0
0 1 1 1 1 0 0 1
0 1 1 1 1 0 1 0
0 1 1 1 1 0 1 1
0 1 1 1 1 1 0 0
0 1 1 1 1 1 0 1
0 1 1 1 1 1 1 0
0 1 1 1 1 1 1 1
0 1 0 0 0 0 0 0
0 1 0 0 0 0 0 1
0 1 0 0 0 0 1 0
0 1 0 0 0 0 1 1
0 1 0 0 0 1 0 0
0 1 0 0 0 1 0 1
0 1 0 0 0 1 1 0
0 1 0 0 0 1 1 1
0 1 0 0 1 0 0 0
0 1 0 0 1 0 0 1
0 1 0 0 1 0 1 0
0 1 0 0 1 0 1 1
0 1 0 0 1 1 0 0
0 1 0 0 1 1 0 1
0 1 0 0 1 1 1 0
0 1 0 0 1 1 1 1
0 1 0 1 0 0 0 0
0 1 0 1 0 0 0 1
0 1 0 1 0 0 1 0
0 1 0 1 0 0 1 1
0 1 0 1 0 1 0 0
0 1 0 1 0 1 0 1
0 1 0 1 0 1 1 0
0 1 0 1 0 1 1 1
0 1 0 1 1 0 0 0
0 1 0 1 1 0 0 1
0 1 0 1 1 0 1 0
0 1 0 1 1 0 1 1
0 1 0 1 1 1 0 0
0 1 0 1 1 1 0 1
0 1 0 1 1 1 1 0
0 1 0 1 1 1 1 1
38
39
3A
3B
3C
3D
3E
3F
30
31
32
33
34
35
36
37
28
29
2A
2B
2C
2D
2E
2F
20
21
22
23
24
25
26
27
18
19
1A
1B
1C
1D
1E
1F
10
11
12
13
14
15
16
17
08
09
0A
0B
0C
0D
0E
0F
00
01
02
03
04
05
06
07
Bit Pattern
1 2 3 4 5 6 7 8
0 0 1 0 0 0 0 0
0 0 1 0 0 0 0 1
0 0 1 0 0 0 1 0
0 0 1 0 0 0 1 1
0 0 1 0 0 1 0 0
0 0 1 0 0 1 0 1
0 0 1 0 0 1 1 0
0 0 1 0 0 1 1 1
0 0 1 0 1 0 0 0
0 0 1 0 1 0 0 1
0 0 1 0 1 0 1 0
0 0 1 0 1 0 1 1
0 0 1 0 1 1 0 0
0 0 1 0 1 1 0 1
0 0 1 0 1 1 1 0
0 0 1 0 1 1 1 1
0 0 1 1 0 0 0 0
0 0 1 1 0 0 0 1
0 0 1 1 0 0 1 0
0 0 1 1 0 0 1 1
0 0 1 1 0 1 0 0
0 0 1 1 0 1 0 1
0 0 1 1 0 1 1 0
0 0 1 1 0 1 1 1
0 0 1 1 1 0 0 0
0 0 1 1 1 0 0 1
0 0 1 1 1 0 1 0
0 0 1 1 1 0 1 1
0 0 1 1 1 1 0 0
0 0 1 1 1 1 0 1
0 0 1 1 1 1 1 0
0 0 1 1 1 1 1 1
0 0 0 0 0 0 0 0
0 0 0 0 0 0 0 1
0 0 0 0 0 0 1 0
0 0 0 0 0 0 1 1
0 0 0 0 0 1 0 0
0 0 0 0 0 1 0 1
0 0 0 0 0 1 1 0
0 0 0 0 0 1 1 1
0 0 0 0 1 0 0 0
0 0 0 0 1 0 0 1
0 0 0 0 1 0 1 0
0 0 0 0 1 0 1 1
0 0 0 0 1 1 0 0
0 0 0 0 1 1 0 1
0 0 0 0 1 1 1 0
0 0 0 0 1 1 1 1
0 0 0 1 0 0 0 0
0 0 0 1 0 0 0 1
0 0 0 1 0 0 1 0
0 0 0 1 0 0 1 1
0 0 0 1 0 1 0 0
0 0 0 1 0 1 0 1
0 0 0 1 0 1 1 0
0 0 0 1 0 1 1 1
0 0 0 1 1 0 0 0
0 0 0 1 1 0 0 1
0 0 0 1 1 0 1 0
0 0 0 1 1 0 1 1
0 0 0 1 1 1 0 0
0 0 0 1 1 1 0 1
0 0 0 1 1 1 1 0
0 0 0 1 1 1 1 1
Hex
Code
B8
B9
BA
BB
BC
BD
BE
BF
B0
B1
B2
B3
B4
B5
B6
B7
A8
A9
AA
AB
AC
AD
AE
AF
A0
A1
A2
A3
A4
A5
A6
A7
98
99
9A
9B
9C
9D
9E
9F
90
91
92
93
94
95
96
97
88
89
8A
8B
8C
8D
8E
8F
80
81
82
83
84
85
86
87
Hex
Code
Bit Pattern
1 2 3 4 5 6 7 8
1 0 1 0 0 0 0 0
1 0 1 0 0 0 0 1
1 0 1 0 0 0 1 0
1 0 1 0 0 0 1 1
1 0 1 0 0 1 0 0
1 0 1 0 0 1 0 1
1 0 1 0 0 1 1 0
1 0 1 0 0 1 1 1
1 0 1 0 1 0 0 0
1 0 1 0 1 0 0 1
1 0 1 0 1 0 1 0
1 0 1 0 1 0 1 1
1 0 1 0 1 1 0 0
1 0 1 0 1 1 0 1
1 0 1 0 1 1 1 0
1 0 1 0 1 1 1 1
1 0 1 1 0 0 0 0
1 0 1 1 0 0 0 1
1 0 1 1 0 0 1 0
1 0 1 1 0 0 1 1
1 0 1 1 0 1 0 0
1 0 1 1 0 1 0 1
1 0 1 1 0 1 1 0
1 0 1 1 0 1 1 1
1 0 1 1 1 0 0 0
1 0 1 1 1 0 0 1
1 0 1 1 1 0 1 0
1 0 1 1 1 0 1 1
1 0 1 1 1 1 0 0
1 0 1 1 1 1 0 1
1 0 1 1 1 1 1 0
1 0 1 1 1 1 1 1
1 0 0 0 0 0 0 0
1 0 0 0 0 0 0 1
1 0 0 0 0 0 1 0
1 0 0 0 0 0 1 1
1 0 0 0 0 1 0 0
1 0 0 0 0 1 0 1
1 0 0 0 0 1 1 0
1 0 0 0 0 1 1 1
1 0 0 0 1 0 0 0
1 0 0 0 1 0 0 1
1 0 0 0 1 0 1 0
1 0 0 0 1 0 1 1
1 0 0 0 1 1 0 0
1 0 0 0 1 1 0 1
1 0 0 0 1 1 1 0
1 0 0 0 1 1 1 1
1 0 0 1 0 0 0 0
1 0 0 1 0 0 0 1
1 0 0 1 0 0 1 0
1 0 0 1 0 0 1 1
1 0 0 1 0 1 0 0
1 0 0 1 0 1 0 1
1 0 0 1 0 1 1 0
1 0 0 1 0 1 1 1
1 0 0 1 1 0 0 0
1 0 0 1 1 0 0 1
1 0 0 1 1 0 1 0
1 0 0 1 1 0 1 1
1 0 0 1 1 1 0 0
1 0 0 1 1 1 0 1
1 0 0 1 1 1 1 0
1 0 0 1 1 1 1 1
78
79
7A
7B
7C
7D
7E
7F
70
71
72
73
74
75
76
77
68
69
6A
6B
6C
6D
6E
6F
60
61
62
63
64
65
66
67
58
59
5A
5B
5C
5D
5E
5F
50
51
52
53
54
55
56
57
48
49
4A
4B
4C
4D
4E
4F
40
41
42
43
44
45
46
47
Bit Pattern
1 2 3 4 5 6 7 8
1 1 1 0 0 0 0 0
1 1 1 0 0 0 0 1
1 1 1 0 0 0 1 0
1 1 1 0 0 0 1 1
1 1 1 0 0 1 0 0
1 1 1 0 0 1 0 1
1 1 1 0 0 1 1 0
1 1 1 0 0 1 1 1
1 1 1 0 1 0 0 0
1 1 1 0 1 0 0 1
1 1 1 0 1 0 1 0
1 1 1 0 1 0 1 1
1 1 1 0 1 1 0 0
1 1 1 0 1 1 0 1
1 1 1 0 1 1 1 0
1 1 1 0 1 1 1 1
1 1 1 1 0 0 0 0
1 1 1 1 0 0 0 1
1 1 1 1 0 0 1 0
1 1 1 1 0 0 1 1
1 1 1 1 0 1 0 0
1 1 1 1 0 1 0 1
1 1 1 1 0 1 1 0
1 1 1 1 0 1 1 1
1 1 1 1 1 0 0 0
1 1 1 1 1 0 0 1
1 1 1 1 1 0 1 0
1 1 1 1 1 0 1 1
1 1 1 1 1 1 0 0
1 1 1 1 1 1 0 1
1 1 1 1 1 1 1 0
1 1 1 1 1 1 1 1
1 1 0 0 0 0 0 0
1 1 0 0 0 0 0 1
1 1 0 0 0 0 1 0
1 1 0 0 0 0 1 1
1 1 0 0 0 1 0 0
1 1 0 0 0 1 0 1
1 1 0 0 0 1 1 0
1 1 0 0 0 1 1 1
1 1 0 0 1 0 0 0
1 1 0 0 1 0 0 1
1 1 0 0 1 0 1 0
1 1 0 0 1 0 1 1
1 1 0 0 1 1 0 0
1 1 0 0 1 1 0 1
1 1 0 0 1 1 1 0
1 1 0 0 1 1 1 1
1 1 0 1 0 0 0 0
1 1 0 1 0 0 0 1
1 1 0 1 0 0 1 0
1 1 0 1 0 0 1 1
1 1 0 1 0 1 0 0
1 1 0 1 0 1 0 1
1 1 0 1 0 1 1 0
1 1 0 1 0 1 1 1
1 1 0 1 1 0 0 0
1 1 0 1 1 0 0 1
1 1 0 1 1 0 1 0
1 1 0 1 1 0 1 1
1 1 0 1 1 1 0 0
1 1 0 1 1 1 0 1
1 1 0 1 1 1 1 0
1 1 0 1 1 1 1 1
Hex
Code
F8
F9
FA
FB
FC
FD
FE
FF
F0
F1
F2
F3
F4
F5
F6
F7
E8
E9
EA
EB
EC
ED
EE
EF
E0
E1
E2
E3
E4
E5
E6
E7
D8
D9
DA
DB
DC
DD
DE
DF
D0
D1
D2
D3
D4
D5
D6
D7
C8
C9
CA
CB
CC
CD
CE
CF
C0
C1
C2
C3
C4
C5
C6
C7
20 – Troubleshooting The DXPT1 Installation
Troubleshooting The DXPT1 Installation IMI89–207
5 Selecting The T1 PAD Settings
The system pad settings that you select through the DXP Plus system programming are very important for the correct audio level to be transmitted and received and for echo suppression.
5.1
Setting T1 Transmit Level
For the older software, set to normal (uses low, very-low, normal, high, very-high settings). For software using Gain1, Gain2, Nominal, Loss1, Loss2, Loss3, Loss4, and Loss5, use Nominal setting.
5.2
Setting T1 Receive Level
For the older software, set to Very-Low. For the Loss/Gain software, set to Loss4. If echo problems occur, try Loss5.
6 Solving T1 Problems
See the following table for T1 problems you could encounter and their possible causes.
PROBLEM
Signalling bits are not being received properly
(no seize) or the network is not “seeing” the seize.
POSSIBLE CAUSE
Associated multiplexer (mux) equipment may be defective if installed between the DXP and the central office (CO).
When the T1 option is installed in a DXP system, the DXP shows massive seizes on the inbound channels.
Incorrect trunk assignments. For example, ground start idle bits will cause seizes on DID and E&M trunk assignments.
The DXPT1 is seizing outward A=1 and B=1 and channel is in the idle state.
Channel not assigned and not disabled. All
LEDs will be off upon making a request for trunk assignment information (see section
4.6.2).
The SIG red LED on the DXPT1 board is lit indicating no receive signal.
- If new install, cabling may be reversed.
- Wiring to DXPT1 board may be defective
- DXPT1 board may be defective. Verify by installing local loopback.
Bipolar alarms are indicated when T1 option is first installed.
- Only one receive wire connected. Check cable.
- Noise sources or lightning.
The SLIP red LED on the DXPT1 board is lit indicating frame slips are occurring.
DXOPT-SYN card may not be locked. There should not be any red LEDs on this card lit.
Verify presence of primary or secondary sources by the green LEDs lit on this card.
Echos are heard.
- Two- to four-wire hybrid conversions have been made. Cut in echo suppressors to eliminate echos on calls over 600 miles and inform the network.
- Pad setting may be incorrect causing acoustical feedback (see section 5, PAD
Settings). 0 dB (or -3 dB) is recommended for transmitted data and -9 dB at an industry standard telephone (IST).
Throubleshooting The DXPT1 Installation – 21
IMI89–207
A.
Appendix A
Troubleshooting The DXPT1 Installation
Appendix A consists of two tables showing superframe and extended superframe format. The information for these tables is from the American National Standards Institute (ANSI) specification
T1.403-1989.
Table 2. Superframe Format
Frame
Number
10
11
12
7
8
9
5
6
3
4
1
2
Bit
Number
0
193
386
579
772
965
1158
1351
1544
1737
1930
2123
F Bits
Term
Frame
(F
1
)
1
—
0
—
1
—
0
—
1
—
0
—
Signal
Frame
(F
2
)
—
1
—
1
—
—
0
—
0
1
—
0
NOTES:
(1) Frame 1 transmitted first.
(2) Frames 6 and 12 are denoted signalling frames.
(3) Option T- Traffic (bit 8 not used for robbed-bit signalling).
Bit Use In Each
Time Slot
Traffic SignalT T
1-8
1-8
1-8
1-8
1-8
1-7
1-8
1-8
1-8
1-8
1-8
1-7
—
—
—
—
—
8
—
—
—
—
—
8 signalling Bit
Use Options signalling
—
—
—
—
—
—
—
—
—
—
—
—
Channel
—
A
—
—
—
—
—
—
—
—
—
B
22 – Troubleshooting The DXPT1 Installation
Troubleshooting The DXPT1 Installation
Table 3. Extended Superframe Format
F Bits
Frame
Number
19
20
21
22
23
24
14
15
16
17
18
7
8
9
5
6
3
4
1
2
10
11
12
13
Bit
Number
0
193
386
579
772
965
1158
1351
1544
1737
1930
2123
2316
2509
2702
2895
3088
3281
3474
3667
3860
4053
4246
4439
FPS
—
1
—
—
—
1
—
—
0
—
—
—
—
—
0
—
—
—
—
0
—
—
1
—
DL
NOTES:
(1) Frame 1 transmitted first.
(2) Frames 6, 12, 18, and 24 are denoted signalling frames.
(3) FPS = Framing Pattern Sequence (...001011...)
(4) DL = 4KBits/s Data Link (Message Bits m)
(5) CRC - CRC6 Cyclic Redundancy Check (Bits C1-C6)
(6) Option T = Traffic (Bit 8 not used for Robbed-Bit signalling)
(7) Option 2 = 2-State signalling (Channel A)
(8) Option 4 = 4-State signalling (Channels A and B)
(9) Option 16 = 16-State signalling (Channels A, B, C, and D) m
— m
— m
—
— m
— m
— m
— m
— m m
— m
—
— m
— m
—
C
1
—
—
—
C
2
—
—
—
C
3
—
—
—
C
4
—
—
—
C
5
—
—
—
C
—
—
6
Bit Use In Each
Time Slot
1-8
1-8
1-8
1-8
1-8
1-7
1-8
1-8
1-8
1-8
1-8
1-7
1-8
1-8
1-8
1-8
1-8
1-7
1-8
1-8
1-8
1-8
1-8
1-7
—
—
—
—
—
8
—
—
—
—
—
8
—
—
—
—
—
8
—
—
—
—
—
8 signalling Bit
Use Options
CRC Traffic Signal T 2 4 16
— — — —
— — — —
— — — —
— — — —
— — — —
— A A A
— — — —
— — — —
— — — —
— — — —
— — — —
— A B B
— — — —
— — — —
— — — —
— — — —
— — — —
— A A C
— — — —
— — — —
— — — —
— — — —
— — — —
— A B D
IMI89–207
Throubleshooting The DXPT1 Installation – 23
Understanding The System Diagnostics for the
DXP Plus Digital Communications System
1.0 Introducing System Diagnostics
The digital communications system provides you with the option of doing several different types of diagnostic checks on the system. This publication details the types of diagnostics and their functions.
NOTE: You should perform all diagnostic tests on an idle system and under the direction of a Comdial technician.
A busy system could produce invalid test results. Because there are numerous items that could contribute to a failure of any of these tests, Comdial assistance is required in interpreting the results of the diagnostic tests.
R
Diagnostics
1. Initialize Diagnostic Data
2. ROM Checksum Verification
3. Scratch RAM Test
4. Non-Volatile RAM Test
5. Time Switch Memory Test
6. Main Cabinet DTMF Receiver Test
7. Expansion II Cabinet DTMF Receiver Test
8. Expansion III Cabinet DTMF Receiver Test
9. AUX. Board DTMF Receiver Test
10. Speaker Coefficients
11. CPU Board Dip Switches
▲
PUSH
CONT BRIGHT
Viewing The Diagnostics Screen
POWER ON
OFF
This manual has been developed by Comdial Corporation (the “Company”) and is intended for the use of its customers and service personnel. The information in this manual is subject to change without notice. While every effort has been made to eliminate errors, the Company disclaims liability for any difficulties arising from the interpretation of the information contained herein.
The information contained herein does not purport to cover all details or variations in equipment or to provide for every possible contingency to be met in connection with installation, operation, or maintenance. Should further information be desired, or should particular problems arise which are not covered sufficiently for the purchaser’s purposes, contact Comdial, Inside Sales Department,
Charlottesville, Virginia 22906.
Printed in U.S.A.
IMI89–239.01
5/96
IMI89–239 Understanding The System Diagnostics
2.0 Defining System Diagnostics
2.1
Initialize Diagnostic Data
This option clears all previous diagnostic test results from memory.
2.2
ROM Checksum Verification
The ROM checksum test calculates and displays a checksum to test the integrity of the system software builds
(located in the flash ROM).
If the system passes the test, it displays Passed on the screen. If the system fails the test, it displays Failed along with the expected and actual checksum value.
2.3
Scratch RAM Test
This test checks the integrity of the scratch RAM area by writing and reading words in memory. The test works by writing a known pattern, “55AA” into memory and then reading the area of memory back. The system then writes and reads a second known pattern, “AA55.” This algorithm checks every byte in the the scratch RAM area.
If an error occurs, the system displays a message stating that the test failed. Scratch RAM is considered the working area of memory for the DXP’s microprocessor. This area of memory is “volatile,” which means that any data in this area is lost when the system loses power.
2.4
NonVolatile RAM test
This test checks the integrity of the NOV-RAM area of memory. The NOV-RAM area of memory is write protected and backed up by super capacitors on the DXP’s memory board. The programmed database and SMDRs are stored in this area of memory. This test uses the same write/read algorithm that the scratch RAM test employs.
2.5
Time Switch Memory Test
This test checks all 560 timeslots with a write/read algorithm pattern similar to that of the scratch/NOV-RAM test. All voice, data, and tones that pass into and out of the DXP pass through the timeswitch.
2– Understanding The System Diagnostics
Understanding The System Diagnostics IMI89–239
2.6
DTMF Receiver Tests
(Main Cabinet, Expansion II Cabinet, and Expansion III Cabinet)
This diagnostic test checks the functionality of the DTMF receivers located in the cabinet under test. The test performs its check by connecting DTMF tones 0-9, ✳, and # through the timeswitch and confirming that the correct tone was recognized by the receiver.
The system displays the number of each tested DTMF receiver in the cabinet along with a message that tells whether the receiver passed or failed the test. While the actual displayed numbers for the DTMF receivers vary depending upon how many receiver cards that you have installed in the system, the displayed numbers for each cabinet reflect DTMF receiver locations in that cabinet. These locations begin with the receiver card located in the upper slot on the leftmost host board, proceed to the lower card slot on that host board, and then progress to the upper card slot on the next host board to the right of the first.
You can install receiver cards in any of the locations shown in the following chart.
Receiver Card Location
Main Cabinet Auxiliary Board
Services Board (see note)
Upper Expansion Cabinet Interface Board
Upper Expansion Cabinet Auxiliary Board 1
Upper Expansion Cabinet Auxiliary Board 2
Lower Expansion Cabinet Interface Board (see note)
Lower Expansion Cabinet Auxiliary Board 1
Lower Expansion Cabinet Auxiliary Board 2
CPU Board (no receiver card required)
NOTE: If you place two receiver cards in the lower two positions of the Services board, you must take specific programming action (Services DTMF Highway) to enable their use. If you do this, you can add only one reveiver card to the Lower Expansion Cabinet Interface board.
2.7
Speaker Coefficients
Certain models of Comdial digital telephones have performance characteristics that can be modified by using this section of diagnostics. Do not attempt to modify any of the values found in this section unless you have been directed to do so by a Comdial technician; doing so could severely impact the performance of the associated telephone. Once modified, these values remain in the telephone’s permanent memory and are not affected by a master clear.
Understanding The System Diagnostics –3
IMI89–239 Understanding The System Diagnostics
2.8
CPU Board and DIP Switches
This test displays the current settings of the eight DIP switches on the CPU board. This screen updates simultaneously as the switches are changed. This diagnostic is useful for determining the status of the switches from a remote location.
The following paragraphs discuss the currently used switches:
Switch 1—Fixes serial port baud rates to known values
Port 1
Port 2
Baud In
9600
300
Baud Out
9600
300
8
7
Data Bits
1
2
Stop Bits Parity
None
None
Switches 2 through 6 —Comdial Engineers reserve these switches for future design needs.
Flow Ctrl..
None
None
Switch 7—Initializes DXP Modem—sets auto answer, for example. Switch 7 should always be on to ensure that the system will re-initialize the modem after a loss of power or reset. The standard Hayes*-compatible initialize string that the system sends is: AT SO=1 M0 Q1 E0 . Programmers can alter this string if needed through system programming.
*Hayes is a registered trademark of Hayes Microcomputer Products.
Switch 8—Used for software upgrades. At initial power-up after a software up-grade, this switch causes the system to automatically detect the up-graded software and perform a master clear function. If someone up-grades the software to a different revision and this switch is not ON at the power-up, the system will not run.
Accredited by the Dutch Council for Certification for certification and registration activities.
Comdial’s Quality Management System Is
Certified To The ISO 9001 Standard.
R
Charlottesville, Virginia 22901-2829
World Wide Web: http://www.comdial.com/
advertisement
Related manuals
advertisement
Table of contents
- 3 General Description Software Release
- 4 1. Introducing The DXP Plus
- 6 2. Understanding The Telephone Features
- 15 3. Reviewing The Hardware
- 31 4. Connecting The System
- 39 5. Knowing The General Specifications
- 47 6. Understanding The System Features
- 501 Cabinet Installation
- 120 Main Common Equipment Cabinet
- 143 Expansion Common Equipment Cabinet
- 158 Station Board Installation
- 158 Analog Station Board
- 173 Digital Station Board
- 184 Industry-Standard Telephone Station Board
- 197 Line Board Installation
- 197 Loop Start Line Board
- 207 Direct Inward Dialing (DID) Line Board
- 220 Multipurpose Line Board
- 231 DXPT1 Digital Carrier Transmission Option
- 120 Miscellaneous Hardware Installation
- 267 Serial Data Modem
- 270 Dual Tone Multiple Frequency (DTMF) Receiver Card
- 277 Ring Generator Assembly
- 282 Conference Board
- 287 DXOPT–COM Communications Card
- 297 External Battery Assembly
- 311 Switchable Power Supply
- 320 Switchable External Battery Assembly
- 231 Troubleshooting
- 336 Troubleshooting The DXPT1 Digital Carrier Transmission Option
- 359 Understanding The System Diagnostics
- 363 Peripherals
- 363 Quick Q - ACD Technical Manual
- 424 Quick Q - ACD System Manager’s Guide
- 501 Total Control - PC Attendant Installation
- 519 Total Control - PC Attendant’s Console User’s Guide
- 595 Tracker Paging System - Installation And Programming
- 604 Caller ID Feature - Installation And Programming
- 612 Digital Voice Announce Equipment - Installation And Programming
- 624 ExecuMail Equipment - Installation And Programming
- 641 Comdial Enterprise Interface - Installation And Use
- 656 Analog Terminal Interface - Installation and Programming
- 671 Off-Premise Extension Interface - Installtion and Programming
- 687 ISDN–PRI Interface - Installation and Programming
- 728 VMMI
- 730 Introducing VMMI
- 733 Connecting a PC to the Communications System
- 736 Installing the VMMI Program and Help Software
- 737 Making the Programming Connection
- 738 Using VMMI Software to Archive and Restore the Database
- 739 Using VMMI Software to Build a New Database
- 740 Up-Grading the System Software on the DXP Plus
- 741 Activating System Software on the FX Series
- 744 Up-Grading The System Software on the DXP
- 753 Programming Instructions (2a software)
- 755 Table Of Contents
- 759 1. Understanding General Programming Information
- 771 2. Reviewing General Programming Considerations
- 772 3. Understanding Keyboard And Terminal Definitions
- 774 4. Reviewing The Command Prompts And Error Reporting
- 775 5. Performing The Terminal Emulation Programming
- 777 6. Programming Sysfem Features
- 822 7. Programming Station Features
- 899 8. Programming Line Features
- 930 9. Programming Intercom Numbers
- 935 10. Programming Call Costing and Station Message- Detail Accounting and Reports (SMDABMDR Programmingj
- 949 11. Programming Toll Restriction
- 958 12. Enabling Automatic Route Selection
- 970 13. Selecting System Printouts (Printer Interface)
- 971 14. Programming For Peripheral Devices
- 999 15. Configuring The System’s Board Layout
- 1002 Index
- 1009 Programming Records (11a software)
- 1013 1 Introduction
- 1014 2 System Records
- 1029 3 Station Records
- 1058 4 Line Records
- 1070 5 Intercom Numbers
- 1075 6 SMDA/SMDR Records
- 1079 7 Toll/ARS Records
- 1093 8 Printout Records
- 1095 9 Peripherals
- 1103 10 Board Configuration
- 1108 Technical Advisory Bulletins
- 1108 11a Software Enhancements
- 1123 11b Software Enhancements
- 1131 DXP Plus General Description (12a software)
- 1150 DXP-DXP plus-FX -- Gen Description (15a software)
- 1151 Table of Contents
- 1153 Introducing The Software Release 1
- 1153 Introducing The Software Features 1
- 1153 Feature Set 15A Features 1
- 1153 Stand Alone Features 1
- 1154 Detailing Hardware And Software Considerations For The DXP System 2
- 1154 Detailing The Hardware Considerations 2
- 1154 Detailing The Software Considerations 2
- 1155 Explaining The Software Release Features 3
- 1155 Call Forward To Hunt Groups 3
- 1155 Centrex Message Waiting with Caller ID (DXP, DXP Plus only) 3
- 1156 Message Waiting Indications 4
- 1156 Programming For Centrex Message Waiting 4
- 1157 Board Programming 5
- 1158 Programming For Caller ID 6
- 1158 Call ID 6
- 1158 Absorb Ring Time 6
- 1158 Delete Viewed RNA Records 6
- 1158 Caller ID RNA 6
- 1158 CID Button 6
- 1158 Save Button 6
- 1159 Dial By Name Support For Non-Display Telephones 7
- 1159 Programming The Dial By Name Feature For Non-Display Telephones 7
- 1160 Daylight Saving Time 8
- 1160 Programming The Daylight Saving Time Feature 8
- 1160 E911 Caller ID Support For System Stations 8
- 1160 Programming For E911 Caller ID Support 8
- 1160 E911 Line Marking 8
- 1160 Emergency Number Alarm Level 8
- 1160 Emergency Call Feature Code 8
- 1160 E-911 Feature Code Parameters 8
- 1161 Ground Start Line Board (Impact FX Only) 9
- 1161 Idle System Restore 9
- 1161 IST Board For Avalon Pull-Cord Support (Impact FX only) 9
- 1162 SCbus Interface Support (Impact FX only) 10
- 1163 Programming For SCbus Interface Support 11
- 1163 Board Configuration 11
- 1163 PCTB Board Programming 11
- 1163 SCbus Ports 11
- 1163 Phone Types 11
- 1163 OAI Links 11
- 1163 Port Time Slots 11
- 1164 Ring Monitoring 12
- 1164 Programming For Ring Monitoring 12
- 1164 Operating A Ring Monitoring Arrangement 12
- 1165 Detailing Certain Ring Monitoring Operational Rules 13
- 1165 Station Headset Mode 13
- 1165 Programming The Headset Mode 13
- 1166 QSIG Networking Support (Stand Alone Feature) 14
- 1166 Programming For QSIG Networking Support 14
- 1166 Enabling QSIG 14
- 1166 Connected Line ID Restriction 14
- 1166 Calling Line ID Restriction 14
- 1166 Display Presentation 14
- 1166 Node Configuration 14
- 1166 Network Extension Provisioning 14
- 1167 System Networking Feature Enhancements (Stand Alone Feature) 15
- 1167 Basic Impact Attendant Support 15
- 1167 Dial Zero Extension 15
- 1167 Directed Call Pickup 15
- 1167 DSS/BLF Support (Network Station Monitor) 15
- 1168 Programming For Network DSS/BLF Support 16
- 1168 Ten Node Networking 16
- 1168 Transfer To Voice Mail 16
- 1168 Programming For The Transfer To Voice Mail Networking Feature 16
- 1169 VVP Serial Integration 17
- 1170 Programming The Features 19
- 1170 Upgrading The DXP Software 19
- 1171 Converting The DXP Database 20
- 1171 Translating An Earlier DXP Database To A Common Code Base Database 20
- 1172 Master Clearing The DXP System 21
- 1173 Upgrading The DXP Plus Software 22
- 1174 Upgrading the Impact FX Software 23
- 1174 Using The System Software Key 23
- 1175 Enabling The Impact FX System Software 24