advertisement
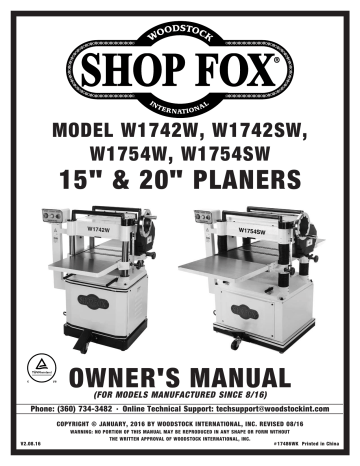
W1742W, W1742SW, W1754W, W1754SW (Mfd. Since 05/16)
Schedule
MAINTENANCE
MAKE. SURE. that. your.
machine. is. unplugged.
during. all. maintenance.
procedures!. If. you. ignore.
this. warning,. serious.
personal.injury.may.occur.
Every.160.Hours.of.Operation:
• Check/tension/replace V-belts ( Page.35
).
• Clean/vacuum dust buildup from inside cabinet and off motor.
• Lubricate table height worm gear
( Page.33
).
• Lubricate table height chain/sprockets
( Page.34
).
• Lubricate drive chain/sprockets ( Page.34
).
Yearly:
• Change gearbox oil ( Page.34
).
For optimum performance from your machine, follow this maintenance schedule and refer to any specific instructions given in this section.
Note:.
This maintenance schedule is based on average daily usage. Adjust the maintenance schedule to match your usage.
Cleaning.&.Protecting
Vacuum excess wood chips and sawdust, and wipe off the remaining dust with a dry cloth.
If any resin has built up, use a resin dissolving cleaner to remove it.
Ongoing:
To maintain a low risk of injury and proper machine operation, if you ever observe any of the following items, shut the machine down immediately, disconnect it from power, and fix the problem before continuing operations.
Protect the unpainted cast iron table by wiping it clean after every use—this ensures moisture from wood dust does not remain on bare metal surfaces. Keep the table rust-free with regular applications of a high-quality metal protectant.
• Tighten loose mounting bolts or fasteners.
• Dull or damaged knives ( Page.28
).
• Worn, frayed, cracked, or damaged wires.
• Resolve any other unsafe condition.
Every 8 Hours of Operation:
• Clean machine and protect unpainted cast- iron.
• Lubricate feed roller bushings ( Page.33
).
Every.40.Hours.of.Operation:
•.
Clean cutterhead and check knife height
( Page.28
).
• Lubricate table columns and leadscrews
( Page.33
).
Lubrication
Failure. to. follow. reasonable. lubrication.
practices. as. instructed. in. this. manual. for.
your.machine.could.lead.to.premature.failure.
of.components.and.void.the.warranty.
This planer features bearings that are lubricated and sealed at the factory. These bearings do not require any service unless they need to be replaced. If a bearing fails, your planer will probably develop a noticeable rumble or vibration, which will increase when under load.
Follow the maintenance schedule on this page and the procedures beginning on Page.33
to properly lubricate the other planer components, which are essential for long life and trouble-free operation of your planer.
-32-
W1742W, W1742SW, W1754W, W1754SW (Mfd. Since 05/16)
Feed.Roller.Bushings
Oil Type ......................................ISO 68 Equivalent
Oil Amount ............................................ 2–3 Drops
Frequency ........................Every 8 Hours of Operation
The infeed and outfeed rollers rotate inside bushing blocks on both ends of the rollers. Add 2–3 drops of ISO
68 machine oil to the center hole of the four feed roller tension adjustment bolts on top of the head casting, as shown in Figure.33
.
Lubricate
Here
Figure.33.
Lubrication of feed roller bushings.
Columns.&.Leadscrews
Oil Type ......................................ISO 68 Equivalent
Oil Amount ............................................ Thin Coat
Grease Type ................................NLGI#2 Equivalent
Frequency ...................... Every 40 Hours of Operation
The table rides on the columns and is moved by the rotation of the leadscrews inside the columns. Loosen the dust sleeve (see Figure.34
) to access the columns and leadscrews. Apply a thin coat of ISO 68 machine oil to the outside surface of the columns and brush on a light application of multi-purpose grease to the leadscrew threads. Move the table up and down to distribute the lubricant.
Table.Height.Worm.Gear
Grease Type ........................... Lithium-Based NLGI#2
Frequency ..................... Every 160 Hours of Operation
Worm Gear
Housing
Column Dust
Sleeve
Figure.34.
Location of column dust sleeve.
Remove the three cap screws that secure the worm gear housing (see Figure.35
), then lift the housing and handwheel assembly off the machine. Clean away any debris from the housing and gears, then brush on a moderate amount of grease onto the gear teeth. Re-install worm gear housing.
Cap Screws
(1 of 3)
Figure.35.
Location of the table height worm gear housing.
-33-
W1742W, W1742SW, W1754W, W1754SW (Mfd. Since 05/16)
Table.Height.Chain.&.Sprockets
Grease Type ........................... Lithium-Based NLGI#2
Frequency ..................... Every 160 Hours of Operation
The table leadscrews are synchronized by the table height chain and sprockets located underneath the planer base
(see Figure.36
). Use shop rags and mineral spirits to clean away debris and grime, then brush on a light coat of multi-purpose grease to the chain and sprockets.
Figure.36.
Table height chain and sprockets as viewed from underneath base.
Drive.Chain.&.Sprockets
Grease Type ........................... Lithium-Based NLGI#2
Frequency ..................... Every 160 Hours of Operation
Drive Chain and Sprockets
The infeed and outfeed rollers receive the transferred power from the cutterhead through the drive chain system on the right side of the machine, as shown in
Figure.37
.
Remove the table height handwheel and the safety covers attached to the inside of the drive chain cover, then remove the cover to access these parts.
Use shop rags and mineral spirits to clean away any debris and grime, then brush on a light coat of multi-purpose grease to the chain and sprockets.
Fill Plug
Figure.37.
Location of drive chains, sprockets, and fill plug.
Gearbox.Oil
Oil Type ......................... ISO 320 or SAE 140 Gear Oil
Oil Amount ................................................ 20 Oz.
Frequency ................ After First 20 Hours, Then Yearly
Note: SAE 85W-140 multi-weight gear oil may also be used as a substitute. DO NOT mix oil types!
Note: We recommend that you replace the gearbox oil after the first 20 hours of operation. This is a normal break-in procedure and will help maximize the service life of the machine by flushing away any particles from the break-in and manufacturing process.
Although it is not necessary to remove the drive chain cover to access the fill and drain plugs, it is more convenient to do so (see Figures.37–38 ). Add oil into the fill-plug hole until it just reaches the fill plug.
Drain Plug
Figure.38.
Location of gearbox drain plug.
-34-
advertisement
Related manuals
advertisement
Table of contents
- 4 INTRODUCTION
- 4 Contact Info
- 4 Machine Differences
- 4 Manual Accuracy
- 5 Machine Specifications
- 7 Identification
- 8 Controls & Components
- 9 Internal Components
- 10 SAFETY
- 10 Standard Machinery Safety Instructions
- 12 Additional Safety for Planers
- 13 ELECTRICAL
- 13 Circuit Requirements
- 14 Grounding Requirements
- 14 Extension Cords
- 15 SETUP
- 15 Unpacking
- 15 Items Needed for Setup
- 16 Inventory
- 17 Cleaning Machine
- 18 Machine Placement
- 19 Lifting & Moving
- 20 Assembly
- 21 Dust Collection
- 22 Checking Gearbox Oil Level
- 23 Test Run
- 24 OPERATIONS
- 24 General
- 25 Workpiece Inspection
- 25 Wood Types
- 26 Planing Tips
- 26 Cutting Problems
- 28 Depth of Cut
- 29 Bed Roller Height
- 30 Setting Feed Rate
- 30 (W1742W & W1754W)
- 30 Adjusting/Replacing Knives
- 32 (W1742SW & W1754SW)
- 33 ACCESSORIES
- 33 Planer Accessories
- 34 MAINTENANCE
- 34 Schedule
- 34 Cleaning & Protecting
- 34 Lubrication
- 37 SERVICE
- 37 General
- 37 Tensioning/Replacing V-Belts
- 38 Tensioning Table Height Chain
- 39 Pressure Bar Heights
- 43 Adjusting Roller Spring Tension
- 44 Positioning Chip Deflector
- 45 Calibrating Table Height Scale
- 45 Anti-Kickback Fingers
- 46 Pulley Alignment
- 47 Troubleshooting
- 49 Electrical Safety Instructions
- 50 W1742W & W1742SW Wiring Diagram
- 51 W1754W & W1754SW Wiring Diagram
- 52 PARTS:.W1742W.&.W1742SW
- 52 Headstock
- 54 Table
- 56 Gearbox
- 57 Feed Gearing
- 58 Cabinet Stand
- 60 PARTS:.W1754W.&.W1754SW
- 60 Headstock
- 62 Table
- 64 Gearbox
- 65 Feed Gearing
- 66 Cabinet Stand
- 68 PARTS:.LABELS.&.COSMETICS
- 71 WARRANTY