advertisement
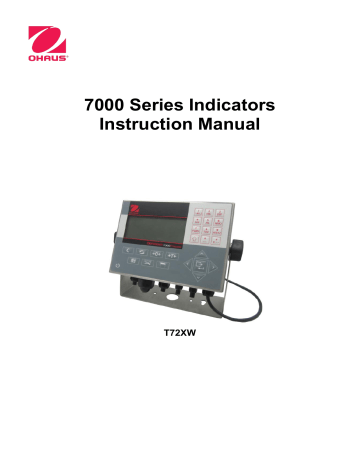
EN 6 7000 SERIES INDICATORS
1.11.4 SD Memory Option
An optional SD Memory card provides a medium on which to store files such as Alibi memory, IDs in the counting application and target weights in the checkweighing application.
Note: The SD card is required for alibi memory.
The SD memory can also be used to extract and save the configuration and calibration settings of the terminal.
These can then be restored to the terminal or loaded to a different terminal. This feature can be used to clone the setup of one terminal then transfer it to other units, which minimizes the chance of error in setting up a new configuration.
1.12 Installation
Opening the Enclosure
The front panel of the harsh enclosure T72XW terminal is locked in place by six spring clips attached to the body of the enclosure. To access the termin al’s PCB to install options, connect internal wiring and set switches, separate the front panel from the enclosure as follows:
1. Insert the tip of a flat-blade screwdriver into one of the two slots located on the bottom of the front panel assembly
(see Figure 1-2). While squeezing the front panel and enclosure together, gently push the screwdriver in toward
the enclosure. A “pop” sound is made when the cover clip is released.
Figure 1-2: Opening the Harsh Enclosure
2.
Repeat Step 1 for the other slot.
3.
After releasing the two clips securing the bottom of the front panel, move the panel to each side to disengage
top edge of the bottom enclosure.
4.
to unsnap the top two clips, then lift the cover to clear the two top clips. The cover will swing down, hinged by two wire cables at the bottom.
2
1
Figure 1-3: Removing the Cover
7000 SERIES INDICATORS
Installing Cables and Connectors
EN 7
Information for installing cables and connectors for the T72XW terminal is provided in this section, including:
Ferrite Core
Main Board Wiring Connections
Wiring Connections for Options
Ferrite Core
In order to meet certain electrical noise emission limits and to protect the T72XW from external influences, it is necessary to install a ferrite core on the load cell cable connected to the terminal. The ferrite core is included with the basic terminal.
To install the ferrite, simply route the cable through the center of the core and then take one wrap around the outside of the core and route the cable through the center again. Either the complete cable or the individual wires
Figure 1-4: Installing the Ferrite Core
Main Board Wiring Connections
Once the T72XW terminal harsh enclosure is open, connections can be made to the terminal strips on the main
Load cell connector
Option 1 connector
Option 2 connector
AC power connecto
DIP switches
Figure 1-5: T72XW Main Board Connections, AC Model
Analog Load Cell Connections
WARNING!
TO AVOID DAMAGE TO THE PCB OR LOAD CELL, REMOVE POWER FROM THE
T72XW TERMINAL AND WAIT AT LEAST 30 SECONDS BEFORE CONNECTING OR
DISCONNECTING ANY HARNESS.
EN 8 7000 SERIES INDICATORS
Load cell connections are made to the load cell connector located on the main board as shown in Figure
1-.
The AC version of the T72XW terminal is designed to power up to ten 350-ohm load cells (or a minimum resistance of approximately 35 ohms). The battery version of the T72XW terminal is designed to power up to four 350-ohm load cells (or a minimum resistance of approximately 87 ohms). To confirm that the load cell load for this installation is within limits, the total scale resistance (TSR) must be calculated. To calculate TSR:
TSR =
Load Cell Input Resistance (Ohms)
Number of Load Cells
Ensure that the TSR of the load cell network to be connected to the T72XW has a resistance greater than the minimums listed above before connecting the load cells. If the resistance is below the minimum, the T72XW will not operate properly.
lengths based on TSR and cable gauge.
Table 1-4: Recommended Maximum Cable Lengths
TSR (Ohms)
350
87 (4-350
cells)
43 (8-350
cells)
35 (10-350
cells)
24 Gauge
(meters/feet)
243/800
60/200
30/100
24/80
20 Gauge
(meters/feet)
610/2000
182/600
91/300
60/200
16 Gauge
(meters/feet)
1219/4000
304/1000
152/500
120/400
The T72XW terminal is designed to support both 2mV/V and 3mV/V load cells from the same circuitry. A load cell output rating selection jumper is not required.
cells, jumpers must be placed between the +Excitation and +Sense terminals and between the
Excitation and
Sense terminals.
Figure 1-2: Load Cell Termination
Note: For the standard four-wire cable: If an increase in load results in a decrease in weight display, reverse the signal wires (+SIG and
SIG)
7000 SERIES INDICATORS
COM1 Serial Port Connections
carries which signal on the COM1 port. Make the connections as necessary.
EN 9
Terminal
TxD
RxD
Gnd
Signal
Transmit RS-232
Receive RS-232
Logic Ground
Figure 1-3: COM1 Port Signals
necessary.
NOTES:
1. USE ONLY SHIELDED CABLE.
2. MAXIMUM CABLE LENGTH: 50 FEET (15 METERS).
3. WIRE SIZE: 18 AWG (.823 mm
2
24 AWG (0.205 mm
) MAXIMUM
2
) MINIMUM.
Figure 1-4: Sample COM1 Connections
PCB Switch Settings
PCB switch settings are described in this section, including settings for main PCB switches and the discrete I/O switch
.
Main PCB Switches
Figure 1-5: Location of Switch Block 1 on the Main PCB
EN 10 7000 SERIES INDICATORS
Table 1-5: Switch 1 Functions
Switch
SW1-1
SW1-2
Functions
Metrology Security Switch (legal for trade)
When in the ON position, this switch prohibits changes to metrological parameters in setup. This must be ON for
“approved” applications
Master Reset
Set in the ON position and power cycle to perform a master reset of all data in the terminal
Set in the OFF position during normal operation.
Notes
This is true even if the Scale
Approval parameter is selected as “None” in setup.
When a Master Reset is performed, set SW1-4 to ON to reset metrologically significant data, such as scale calibration,
GEO code, etc.
SW1-3
SW1-4
Flash Software
Set in the ON position for software download
Set in the OFF position during normal operation
Reset Calibration
Set in the ON position to reset calibration during a master reset
Set in the OFF position to retain current calibration values during a master reset
Not used
Works with switch SW1-2
SW1-5
SW1-6 Not used
When both SW1-2 and SW1-4 are positioned ON and AC power is applied to the terminal, a Master Reset function will be initiated. This procedure will erase all programming in the terminal and return all settings back to factory default values. This process is described in the T72XW Technical Manual, Chapter 4, Service and Maintenance.
SD Card Installation
The SD memory card can be used for additional storage in the Checkweighing and Counting applications, and
on the edge of the T72XW main board.
Figure 1-6: Sliding an SD Card into the SD Socket (left); SD Card Installed (right)
Capacity Label Instructions
The regulations in some locations require that the scale capacity and increment be shown on the front of the terminal, near the display. To satisfy this requirement, a blue capacity label is included with the terminal that must be completed and adhered to the front overlay.
If only one range is used, the unused portion of the label may be cut off with scissors. Written information must be legible and a minimum of 2mm or 0.08 in. in height. A permanent marker should be used for this information.
Figure 1-7: Preparing the Capacity Label
7000 SERIES INDICATORS EN 11
another location acceptable to the local regulations.
Capacity Label in
Place
Figure 1-8: Capacity Label Installed
Closing the Enclosure
After all work has been completed inside the terminal, the enclosure must be snapped shut properly to maintain its environmental integrity.
To properly close the terminal, follow these steps:
1.
Position the front cover over the rear housing then gently press it down into place.
2.
Press down firmly in each of the four corners of the front cover in sequence until each corner clip snaps audibly snaps into place.
3.
It is very important that each of the 4 corner clips have snapped into place. When pressing down on the cover during installation, listen for the “click” sound of each clip engaging.
Securing the Enclosure
When the T72XW terminal is used in a metrologically “approved” application, it must be protected from tampering by use of a seal. A wire security seal is included with the terminal.
For sealing details of the T72XW terminal, refer to Figure 1-9 and follow these steps:
1.
Ensure that the appropriate approval region has been selected in setup under Scale > Type > Approval, and
that the Metrology security switch SW1-1 is in its ON position (refer to Figure 1-5 and
2.
3.
4.
With the front panel installed on the enclosure and snapped into place, thread the free end of the wire seal through either the left or right hole in the T72XW front panel, and through the hole in the retaining clip.
5.
remaining slack in the wire, and snap the seal shut.
Sealing wire threaded through hole and clip
Sealing wire threaded through plastic seal
Figure 1-9: Seal Threaded and Ready to be Closed
advertisement
Related manuals
advertisement
Table of contents
- 7 INTRODUCTION
- 11 COM2 Serial Port
- 11 Discrete I/O
- 11 Ethernet
- 12 SD Memory Option
- 18 NSTALLATION
- 18 Display Layout
- 18 Front Panel Keys
- 19 OPERATION: TERMINAL
- 19 Display Elements
- 20 Keypad Operation
- 22 Language Selection – F Codes
- 22 Menu Navigation
- 24 Alibi Memory
- 25 Adjust Contrast
- 25 Transaction Counter
- 25 Totals Memory
- 26 Expand x
- 26 Information Recall
- 27 Setup Access
- 30 Unit Switching
- 31 Expand By
- 31 Print
- 31 Information Recall
- 31 ID Entry
- 32 Time and Date
- 32 Totalization
- 32 Alibi Memory
- 33 Animal Weighing
- 33 Checkweighing
- 33 Counting
- 34 CONFIGURATION: TERMINAL
- 34 Navigation
- 35 Setup Page
- 37 Scale
- 45 Application
- 49 Terminal
- 54 Communication
- 60 Maintenance
- 65 APPLICATIONS: CONFIGURATION AND OPERATION
- 65 Overview
- 65 Operational Features
- 66 Configuration
- 67 Operating Sequence
- 68 Serial Input Commands
- 69 Print Formats
- 70 Overview
- 70 Operational Features
- 71 Configuration
- 74 Operating Sequence
- 78 Print Formats
- 79 Overview
- 79 Operational Features
- 80 Configuration
- 82 Operating Sequences
- 85 Print Formats
- 87 SERVICE AND MAINTENANCE
- 87 Blank Display
- 88 Power Test
- 88 Problem Diagnosis
- 88 Error Codes and Error Messages
- 89 Internal Diagnostics
- 92 Backup to SD Memory Card
- 93 Restore from SD Memory Card
- 95 COMPLIANCE
- 97 APPENDIX A DEFAULT TEMPLATES
- 99 APPENDIX B ALIBI MEMORY
- 102 APPENDIX C COMMUNICATIONS
- 128 APPENDIX D GEO CODES