- Home
- Home security & automation
- Security access control systems
- Mitsubishi
- MOTION CONTROLLERS Q172DCPU
- Instruction manual
advertisement
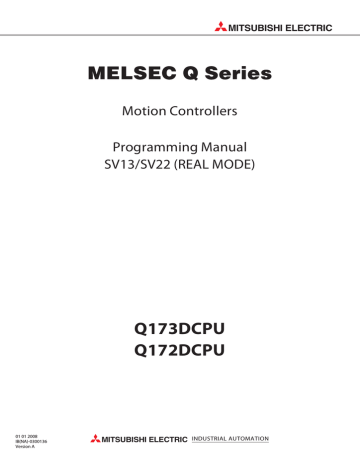
3 POSITIONING DEDICATED SIGNALS
3.1 Internal Relays
(1) Internal relay list
Device No.
SV13 SV22
Purpose Device No. Purpose to
M2000 to
M2320 to
M2400 to
M3040 to
M3072 to
M3136 to
M3200 to
M3840 to
M8191
(2000 points)
Common device
(320 points)
Unusable
(80 points)
Axis status
(20 points 32 axes)
Unusable
(32 points)
Common device (Command signal)
(64 points)
Unusable
(64 points)
Axis command signal
(20 points 32 axes)
User device
(4352 points) to
M2000 to
M2320 to
M2400 to
(2000 points)
Common device
(320 points)
Unusable
(80 points)
Axis status
(20 points 32 axes)
Real mode……Each axis
Virtual mode….Output module
Unusable
(32 points)
M3040 to
M3072 to
M3136 to
M3200 to
M3840 to
M4000 to
M4640 to
M4688 to
Common device (Command signal)
(64 points)
Unusable
(64 points)
Axis command signal
(20 points 32 axes)
Real mode……Each axis
Virtual mode….Output module
Unusable
(160 points)
Virtual servomotor axis status
(20 points 32 axes)
Synchronous encoder axis status
(4 points 12 axes)
Unusable (Note-1)
(112 points)
(Note-1)
M4800 to
M5440 to
Virtual servomotor axis command signal (Note-1)
(20 points 32 axes)
Synchronous encoder axis command signal
(4 points 12 axes)
M5488 to
M8191
User device
(2704 points)
It can be used as an user device.
(Note-1): It can be used as an user device in the SV22 real mode only.
POINT
• Total number of user device points
6352 points (SV13) / 4074 points
(Note)
(SV22)
(Note): Up to 6096 points can be used when not using it in the virtual mode.
3 - 3
3 POSITIONING DEDICATED SIGNALS
Axis No.
25
26
27
28
29
30
31
32
19
20
21
22
15
16
17
18
11
12
13
14
7
8
9
10
23
24
1
2
3
4
5
6
(2) Axis status list
Device No.
M2880 to M2899
M2900 to M2919
M2920 to M2939
M2940 to M2959
M2960 to M2979
M2980 to M2999
M3000 to M3019
M3020 to M3039
19 M-code outputting signal
Signal name
M2400 to M2419
M2420 to M2439
M2440 to M2459
M2460 to M2479
M2480 to M2499
M2500 to M2519
M2520 to M2539
M2540 to M2559
M2560 to M2579
M2580 to M2599
M2600 to M2619
M2620 to M2639
M2640 to M2659
M2660 to M2679
M2680 to M2699
M2700 to M2719
M2720 to M2739
M2740 to M2759
M2760 to M2779
M2780 to M2799
M2800 to M2819
M2820 to M2839
M2840 to M2859
M2860 to M2879
18
Signal name
0 Positioning start complete
1 Positioning complete
2 In-position
3 Command in-position
4 Speed controlling
5 Speed/position switching latch
6 Zero pass
7 Error detection
8 Servo error detection
9 Home position return request
10 Home position return complete
11 FLS
12
13
External signals
RLS
STOP
14 DOG/CHANGE
15 Servo ready
16 Torque limiting
17 Unusable
Virtual mode continuation operation disable warning signal (SV22)
(Note-1)
Refresh cycle
Operation cycle
Immediate
Operation cycle
Main cycle
Operation cycle
Main cycle
Operation cycle
At virtual mode transition
Operation cycle
Fetch cycle Signal direction
Status signal
Status signal
(Note-1): It is unusable in the SV13/SV22 real mode.
POINT
(1) The range of axis No.1 to 8 is valid in the Q172DCPU.
(2) The device area more than 9 axes as an user device in the Q172DCPU.
However, when the project of Q172DCPU is replaced with Q173DCPU, this area cannot be used.
3 - 4
3 POSITIONING DEDICATED SIGNALS
Axis No. Device No.
(3) Axis command signal list
1 M3200 to M3219
2 M3220 to M3239
3 M3240 to M3259
Signal name
4 M3260 to M3279
5 M3280 to M3299
6 M3300 to M3319
7 M3320 to M3339
0 Stop command
1 Rapid stop command
2 Forward rotation JOG start command
3 Reverse rotation JOG start command
8 M3340 to M3359
9 M3360 to M3379
10 M3380 to M3399
4 Complete signal OFF command
Speed/position switching enable
5 command
Signal name
Refresh cycle
11 M3400 to M3419
12 M3420 to M3439
13 M3440 to M3459
6 Unusable
7 Error reset command
8 Servo error reset command
14 M3460 to M3479
15 M3480 to M3499
16 M3500 to M3519 10
17 M3520 to M3539 11
18
19
M3540 to M3559
M3560 to M3579
External stop input disable at start
9 command
Unusable
Feed current value update request
12 command
20 M3580 to M3599
21 M3600 to M3619
Address clutch reference setting
13 command (SV22 only)
(Note-1)
22
23
M3620 to M3639
M3640 to M3659
Cam reference position setting
14 command (SV22 only)
(Note-1)
24 M3660 to M3679 15 Servo OFF command
25 M3680 to M3699 16 Gain changing command
26 M3700 to M3719 17 Unusable
27 M3720 to M3739 18 Control loop changing command
28 M3740 to M3759
29 M3760 to M3779
30 M3780 to M3799
31 M3800 to M3819
32 M3820 to M3839
Fetch cycle
Operation cycle
Main cycle
Operation cycle
Main cycle
At start
At start
At virtual mode transition
Operation cycle
Operation cycle
(Note-2)
Operation cycle
Signal direction
Command signal
Command signal
Command signal
Command signal
(Note-1): It is unusable in the SV13/SV22 real mode.
(Note-2): Operation cycle 7.1[ms] or more: Every 3.5[ms]
POINT
(1) The range of axis No.1 to 8 is valid in the Q172DCPU.
(2) The device area more than 9 axes as an user device in the Q172DCPU.
However, when the project of Q172DCPU is replaced with Q173DCPU, this area cannot be used.
3 - 5
3 POSITIONING DEDICATED SIGNALS
Device
No.
Signal name
M2000 PLC ready flag
M2001 Axis 1
M2002 Axis 2
M2003 Axis 3
M2004 Axis 4
M2005 Axis 5
M2006 Axis 6
M2007 Axis 7
M2008 Axis 8
M2009 Axis 9
M2010 Axis 10
M2011 Axis 11
M2012 Axis 12
M2013 Axis 13
M2014 Axis 14
M2015 Axis 15
M2016 Axis 16
M2017 Axis 17
Start accept flag
M2018 Axis 18
M2019 Axis 19
M2020 Axis 20
M2021 Axis 21
M2022 Axis 22
M2023 Axis 23
M2024 Axis 24
M2025 Axis 25
M2026 Axis 26
M2027 Axis 27
M2028 Axis 28
M2029 Axis 29
M2030 Axis 30
M2031 Axis 31
M2032 Axis 32
M2033 Unusable
M2034 (2 points)
M2035
Motion error history clear request flag
M2036
M2037
Unusable
(2 points)
M2038 Motion SFC debugging flag
M2039 Motion error detection flag
M2040
Speed switching point specified flag
M2041 System setting error flag
M2042 All axes servo ON command
M2043
Real mode/virtual mode switching request (SV22)
M2044
Real mode/virtual mode switching status (SV22)
M2045
Real mode/virtual mode switching error detection signal (SV22)
M2046 Out-of-sync warning (SV22)
M2047 Motion slot fault detection flag
(4) Common device list
Refresh cycle
Operation cycle
Fetch cycle
Main cycle
Signal direction
Command signal
(Note-4)
M3072
Status signal
(Note-1),
(Note-2)
Remark Device
No.
M2053
Signal name
Manual pulse generator 3 enable flag
Refresh cycle
M2054 Operation cycle over flag Operation cycle
M2055
M2056
M2057
M2058
M2059
M2060
Unusable
(6 points)
— —
M2085 Axis
—
M2086 Axis
Main cycle
Command signal
M3080
— —
M2089 Axis
—
M2090 Axis
At debugging mode transition
Status signal
Immediate M2093
Operation cycle
At start
Operation cycle
At virtual mode transition
Command signal
Status signal
Command signal
M3073
M2094
M2095
M2096
M2097
M2098
M3074 M2099
M2100
M3075
Unusable
(8 points)
At virtual mode transition
Operation cycle
Status signal
Speed changing accepting flag
Synchronous encoder current value changing flag
(Note-3)
(12 axes)
Operation cycle
Operation cycle
M2048
JOG operation simultaneous start command
M2049 All axes servo ON accept flag
M2050 Unusable
M2051
Manual pulse generator 1 enable flag
M2052
Manual pulse generator 2 enable flag
Main cycle
Command signal
M3076
Status
Operation cycle signal
Main cycle
M2113
Command signal
—
Unusable
M2115
M3077 (6 points)
M2116
M3078
M2117
M2118
Fetch cycle
Main cycle
Signal direction
Remark
(Note-4)
Command signal
Status signal
M3079
Status signal
(Note-1),
(Note-2)
Status signal
(Note-1),
(Note-2)
3 - 6
3 POSITIONING DEDICATED SIGNALS
M2178
M2179
M2180
M2181
M2182
M2183
M2184
M2185
M2186
M2187
M2161
M2162
M2163
M2164
M2165
M2166
M2167
M2168
M2169
M2170
M2171
M2172
M2173
Unusable
(28 points)
M2174
(Note-5)
M2175
M2176
M2177
Device
Signal name
No.
M2119
M2120
M2121
M2122
M2123
Unusable
(9 points)
M2124
M2125
M2126
M2127
M2128 Axis 1
M2129 Axis 2
M2130 Axis 3
M2131 Axis 4
M2132 Axis 5
M2133 Axis 6
M2134 Axis 7
M2135 Axis 8
M2136 Axis 9
M2137 Axis 10
M2138 Axis 11
M2139 Axis 12
M2140 Axis 13
M2141 Axis 14
M2142 Axis 15
M2143 Axis 16 Automatic
M2144 Axis 17 decelerating flag
M2145 Axis 18
M2146 Axis 19
M2147 Axis 20
M2148 Axis 21
M2149 Axis 22
M2150 Axis 23
M2151 Axis 24
M2152 Axis 25
M2153 Axis 26
M2154 Axis 27
M2155 Axis 28
M2156 Axis 29
M2157 Axis 30
M2158 Axis 31
M2159 Axis 32
M2160
Common device list (Continued)
Refresh cycle Fetch cycle
Signal direction
Remark Device
(Note-4)
No.
M2188
M2189
M2190
M2191
— —
Operation cycle
Status signal
(Note-1),
(Note-2)
Signal name
M2209
M2210
M2211
M2212
M2213
M2214
M2215
M2216
M2217
M2218
M2219
M2220
M2221
M2222
M2223
M2224
M2225
M2226
M2227
M2228
M2229
M2193
M2194
M2195
M2196
M2197
M2198
M2199
M2200
M2201
M2202
M2203
M2204
M2205
M2206
M2207
M2208
Unusable
(36 points)
(Note-5)
M2230
M2231
M2232
M2233
Unusable
(16 points)
M2234
M2235
M2236
M2237
M2238
M2239
— —
M2242 Axis
—
M2243 Axis
M2253 Axis 14
M2254 Axis 15
Refresh cycle
Speed change "0" accepting flag
Operation cycle
3 - 7
Fetch cycle
Signal direction
Remark
(Note-4)
Status signal
(Note-1),
(Note-2)
3 POSITIONING DEDICATED SIGNALS
Device
No.
M2257 Axis 18
M2258 Axis 19
M2259 Axis 20
M2260 Axis 21
M2261 Axis 22
Signal name
M2262 Axis 23
M2263 Axis 24
M2264 Axis 25
Speed change "0" accepting flag
M2265 Axis 26
M2266 Axis 27
M2267 Axis 28
M2268 Axis 29
M2269 Axis 30
M2270 Axis 31
M2271 Axis 32
M2272 Axis 1
M2273 Axis 2
M2274 Axis 3
M2275 Axis 4
M2276 Axis 5
M2277 Axis 6
M2278 Axis 7
M2279 Axis 8
Control loop
M2280 Axis 9
M2281 Axis 10 monitor status
M2282 Axis 11
M2283 Axis 12
M2284 Axis 13
M2285 Axis 14
M2286 Axis 15
M2287 Axis 16
M2288 Axis 17
Common device list (Continued)
Refresh cycle
Operation cycle
Fetch cycle
Signal direction
Remark
(Note-4)
Device
No.
Signal name
24
Control loop monitor status
Refresh cycle
Operation cycle
Fetch cycle
Signal direction
Remark
(Note-4)
Status signal
(Note-1),
(Note-2)
Status signal
(Note-1),
(Note-2)
M2304
M2305
M2306
M2307
M2308
M2309
M2310
M2311
M2312
M2313
Unusable
(16 points)
M2314
M2315
M2316
M2317
M2318
M2319
(Note-1): The range of axis No.1 to 8 is valid in the Q172DCPU.
(Note-2): Device area of 9 axes or more is unusable in the Q172DCPU.
(Note-3): This signal is unusable in the SV13/SV22 real mode.
(Note-4): It can also be ordered the device of a remark column.
(Note-5): These devices can be used as the clutch statuses.
The clutch status can also be set as the optional device at the clutch parameter.
Refer to Chapter 7 of the "Q173DCPU/Q172DCPU Motion controller (SV22)
Programming Manual (VIRTUAL MODE)" for details.
3 - 8
3 POSITIONING DEDICATED SIGNALS
(5) Common device list (Command signal)
Device No.
M3072
M3073
M3074
M3075
M3076
Signal name
PLC ready flag
Speed switching point specified flag
All axes servo ON command
Real mode/virtual mode switching request (SV22)
JOG operation simultaneous start command
Manual pulse generator 1 enable flag
Manual pulse generator 2 enable flag
Refresh cycle Fetch cycle
Main cycle
At start
Operation cycle
At virtual mode transition
Signal direction
Command signal
Remark
(Note-1), (Note-2)
M2000
M2040
M2042
M2043
M2048
M3077
M3078
Main cycle
M2051
M2052
M3079
M3080
Manual pulse generator 3 enable flag
Motion error history clear request flag
M2053
M2035
M3081 to
Unusable
(Note-3)
(55 points)
— — — —
M3135
(Note-1): The state of a device is not in agreement when the device of a remark column is turned ON/OFF directly. In addition, when the request from a data register and the request from the above device are performed simultaneously, the request from the above device becomes effective.
(Note-2): It can also be ordered the device of a remark column.
(Note-3): Do not use it as an user device. It can be used as a device that performs automatic refresh because of area for the reserve of command signal.
POINT
The device of a remark column turns ON by OFF to ON of the above device, and turns OFF by ON to OFF of the above device.
The command signal cannot be turned ON/OFF by the PLC CPU in the automatic refresh because the statuses and commands are mixed together in M2000 to
M2053. Use the above devices in the case.
And, it can also be turned ON/OFF by the data register. (Refer to Section 3.2.3)
3 - 9
3 POSITIONING DEDICATED SIGNALS
3.1.1 Axis statuses
(1) Positioning start complete signal (M2400+20n) .......... Status signal
(a) This signal turns on with the start completion for the positioning control of the axis specified with the servo program. It does not turn on at the starting using JOG operation or manual pulse generator operation.
It can be used to read a M-code at the positioning start.
(Refer to Section 7.1.)
(b) This signal turns off at leading edge of complete signal OFF command
(M3204+20n) or positioning completion.
At leading edge of complete signal OFF command (M3204+20n)
V
Dwell time t
Servo program start
Start accept flag
(M2001 to M2032)
Positioning start complete signal
(M2400+20n)
Complete signal OFF command
(M3204+20n)
At positioning completion
V
OFF
OFF
OFF
ON
ON
ON
Dwell time
Positioning completion t
Servo program start
Start accept flag
(M2001 to M2032)
Positioning start complete signal
(M2400+20n)
OFF
OFF
ON
ON
3 - 10
3 POSITIONING DEDICATED SIGNALS
(2) Positioning complete signal (M2401+20n) ..................Status signal
(a) This signal turns on with the completion of the command output to positioning address for the axis specified with the servo program.
It does not turn on at the start or stop on the way using home position return, JOG operation, manual pulse generator operation or speed control.
It does not turn on at the stop on the way during positioning.
It can be used to read a M-code at the positioning completion.
(Refer to Section 7.1.)
(b) This signal turns off at leading edge of complete signal OFF command
(M3204+20n) or positioning start.
At leading edge of complete signal OFF command (M3204+20n)
V
Dwell time t
Servo program start
Start accept flag
(M2001 to M2032)
Positioning complete signal
(M2401+20n)
OFF
OFF
Complete signal OFF command (M3204+20n)
OFF
At next positioning start
V
ON
Dwell time
ON
OFF
ON
ON
Positioning completion
Positioning start t
Servo program start
Start accept flag
(M2001 to M2032)
Positioning complete signal
(M2401+20n)
OFF
OFF
ON
ON
OFF
ON
CAUTION
The deviation counter value is not considered, so that the positioning complete signal (M2401+20n) turns on with the completion of the command output to positioning address. Use the positioning complete signal (M2401+20n) together with the in-position signal (M2402+20n) to confirm the positioning completion of servo axis in the final instruction under program.
3 - 11
3 POSITIONING DEDICATED SIGNALS
(3) In-position signal (M2402+20n) ...................................Status signal
(a) This signal turns on when the number of droop pulses in the deviation counter becomes below the "in-position range" set in the servo parameters.
It turns off at the start.
Number of droop pulses In-position range t
In-position
(M2402+20n)
ON
OFF
(b) An in-position check is performed in the following cases.
• When the servo power supply is turned on.
• After the automatic deceleration is started during positioning control.
• After the deceleration is started with the JOG start signal OFF.
• During the manual pulse generator operation.
• After the proximity dog ON during a home position return.
• After the deceleration is started with the stop command.
• When the speed change to a speed "0" is executed.
(4) Command in-position signal (M2403+20n) .................Status signal
(a) This signal turns on when the absolute value of difference between the command position and feed current value becomes below the "command in-position range" set in the fixed parameters.
This signal turns off in the following cases.
• Positioning control start
• Home position return
• Speed control
• JOG operation
• Manual pulse generator operation
(b) Command in-position check is continually executed during position control.
This check is not executed during speed control or speed control in the speed/position switching control.
(b)
Command in-position
(M2403+20n)
ON
V
Position control start
OFF
Command in-position setting
Speed/position control start
Execution of command in-position check
Switch from speed to position
Command in-position setting t
Execution of command in-position check
3 - 12
3 POSITIONING DEDICATED SIGNALS
(5) Speed controlling signal (M2404+20n) ........................Status signal
(a) This signal turns on during speed control, and it is used as judgement of during the speed control or position control.
It is turning on while the switching from speed control to position control by the external CHANGE signal at the speed/position switching control.
(b) This signal turns off at the power supply on and during position control.
At speed/position switching control
CHANGE
At speed control
Speed control start
At position control
Positioning start
Speed/position control start t
ON
Speed controlling signal
(M2404+20n)
OFF
Speed control
Position control
(6) Speed/position switching latch signal (M2405+20n)
.........................Status signal
(a) This signal turns on when the control is switched from speed control to position control.
It can be used as an interlock signal to enable or disable changing of the travel value in position control.
(b) The signal turns off at the following start.
• Position control
• Speed/position control
• Speed control
• JOG operation
• Manual pulse generator operation
CHANGE
Start
Speed/position control start t
Speed/position switching latch signal(M2405+20n)
ON
OFF
ON
CHANGE signal from external source
OFF
3 - 13
3 POSITIONING DEDICATED SIGNALS
(7) Zero pass signal (M2406+20n) ....................................Status signal
This signal turns on when the zero point is passed after the power supply on of the servo amplifier.
Once the zero point has been passed, it remains on state until the Multiple CPU system has been reset.
However, in the home position return method of proximity dog, count, dog cradle or limit switch combined type, this signal turns off once at the home position return start and turns on again at the next zero point passage.
(8) Error detection signal (M2407+20n) ............................Status signal
(a) This signal turns on with detection of a minor error or major error, and it is used as judgement of the error available/not available.
The applicable error code (Note-1) is stored in the minor error code storage register with detection of a minor error. (Refer to Section 3.2.1)
The applicable error code (Note-1) is stored in the major error code storage register with detection of a major error. (Refer to Section 3.2.1)
(b) This signal turns off when the error reset command (M3207+20n) turns on.
Error detection
ON
Error detection signal
(M2407+20n)
OFF
Error reset command
(M3207+20n)
OFF
REMARK
ON
(Note-1): Refer to APPENDIX 1 for the error codes with detection of major/minor errors.
(9) Servo error detection signal (M2408+20n) ..................Status signal
(a) This signal turns on when an error occurs at the servo amplifier side (except for errors cause of alarms and emergency stops) (Note-1) , and it is used as judgement of the servo error available/not available.
When an error is detected at the servo amplifier side, the applicable error code (Note-1) is stored in the servo error code storage register. (Refer to
Section 3.2.1)
(b) This signal turns off when the servo error reset command (M3208+20n) turns on or the servo power supply turns on again.
Servo error detection
ON
Servo error detection signal
(M2408+20n)
OFF
Servo error reset command
(M3208+20n)
OFF
ON
3 - 14
3 POSITIONING DEDICATED SIGNALS
REMARK
(Note-1): Refer to APPENDIX 1.4 for the error codes on errors detected at the servo amplifier side.
(10) Home position return request signal (M2409+20n)
.........................Status signal
This signal turns on when it is necessary to confirm the home position address.
(a) When not using an absolute position system
1) This signal turns on in the following cases:
• Multiple CPU system power supply on or reset
• Servo amplifier power supply on
• Home position return start
(Unless a home position return is completed normally, the home position return request signal does not turn off.)
2) This signal turns off by the completion of home position return.
(b) When using an absolute position system
1) This signal turns on in the following cases:
• When not executing a home position return once after system start.
• Home position return start
(Unless a home position return is completed normally, the home position return request signal does not turn off.)
• Erase of an absolute data in Motion CPU according to causes, such as battery error
• Servo error [2025] (absolute position erase) occurrence
• Servo error [2143] (absolute position counter warning) occurrence
• Major error [1202], [1203], or [1204] occurrence
• When the " rotation direction selection " of servo parameter is changed.
2) This signal turns off by the completion of the home position return.
CAUTION
When using the absolute position system function, on starting up, and when the Motion controller or absolute value motor has been replaced, always perform a home position return.
In the case of the absolute position system, use the PLC program to check the home position return request before performing the positioning operation.
Failure to observe this could lead to an accident such as a collision.
3 - 15
3 POSITIONING DEDICATED SIGNALS
(11) Home position return complete signal (M2410+20n)
.......................Status signal
(a) This signal turns on when the home position return operation using the servo program has been completed normally.
(b) This signal turns off at the positioning start, JOG operation start and manual pulse generator operation start.
(c) If the home position return of proximity dog, dog cradle or stopper type using the servo program is executed during this signal on, the "continuous home position return start error (minor error: 115)" occurs and it cannot be start the home position return.
(12) FLS signal (M2411+20n) (Note-1) ...................................Status signal
(a) This signal is controlled by the ON/OFF state for the upper stroke limit switch input (FLS) of the Q172DLX/servo amplifier.
• Upper stroke limit switch input OFF ...... FLS signal: ON
• Upper stroke limit switch input ON ........ FLS signal: OFF
(b) The state for the upper stroke limit switch input (FLS) when the FLS signal is ON/OFF is shown below.
1) Q172DLX use
(Note-2)
FLS signal : ON
Q172DLX
FLS
FLS
FLS signal : OFF
Q172DLX
FLS
FLS
COM
2) Servo amplifier input use
(Note-3)
FLS signal : ON
MR-J3- B
FLS
DI1
COM
FLS signal : OFF
MR-J3- B
FLS
DI1
DICOM DICOM
(Note-1): Refer to the "Q173DCPU/Q172DCPU Motion controller Programming Manual
(COMMON)" for an external signal.
(Note-2): Refer to the "Q173DCPU/Q172DCPU User’s Manual" for a pin configuration.
(Note-3): Refer to the "MR-J3- B Servo Amplifier Instruction Manual" for a pin configuration.
3 - 16
3 POSITIONING DEDICATED SIGNALS
(13) RLS signal (M2412+20n) (Note-1) .................................. Status signal
(a) This signal is controlled by the ON/OFF state for the lower stroke limit switch input (FLS) of the Q172DLX/servo amplifier.
• Lower stroke limit switch input OFF ...... RLS signal: ON
• Lower stroke limit switch input ON ........ RLS signal: OFF
(b) The state of the lower stroke limit switch input (RLS) when the RLS signal is ON/OFF is shown below.
1) Q172DLX use
(Note-2)
RLS signal : ON
Q172DLX
RLS
RLS
RLS signal : OFF
Q172DLX
RLS
RLS
COM COM
2) Servo amplifier input use (Note-3)
RLS signal : ON
MR-J3- B
RLS
DI2
RLS signal : OFF
MR-J3- B
RLS
DI2
DICOM DICOM
(Note-1): Refer to the "Q173DCPU/Q172DCPU Motion controller Programming Manual
(COMMON)" for an external signal.
(Note-2): Refer to the "Q173DCPU/Q172DCPU User’s Manual" for a pin configuration.
(Note-3): Refer to the "MR-J3- B Servo Amplifier Instruction Manual" for a pin configuration.
(14) STOP signal (M2413+20n) ........................................Status signal
(a) This signal is controlled by the ON/OFF state for the stop signal input
(STOP) of the Q172DLX.
• Stop signal input of the Q172DLX OFF ..... STOP signal: OFF
• Stop signal input of the Q172DLX ON ....... STOP signal: ON
(b) The state of the stop signal input (STOP) of the Q172DLX when the STOP signal input is ON/OFF is shown below.
STOP signal : ON
Q172DLX
STOP
STOP
STOP signal : OFF
Q172DLX
STOP
STOP
COM COM
3 - 17
3 POSITIONING DEDICATED SIGNALS
(15) DOG/CHANGE signal (M2414+20n) (Note-1) ..................Status signal
(a) This signal turns on/off by the proximity dog input (DOG) of the
Q172DLX/servo amplifier at the home position return.
This signal turns on/off by the speed/position switching input (CHANGE) of the Q172DLX at the speed/position switching control.
(There is no CHANGE signal in the servo amplifier.)
(b) When using the Q172DLX, "Normally open contact input" and "Normally closed contact input" of the system setting can be selected.
The state of the speed/position switching input (CHANGE) when the
CHANGE signal is ON/OFF is shown below.
1) Q172DLX use
(Note-2)
DOG/CHANGE signal : ON
Q172DLX
DOG/CHANGE
DOG/CHANGE
DOG/CHANGE signal : OFF
Q172DLX
DOG/CHANGE
DOG/CHANGE
COM COM
2) Servo amplifier input use
(Note-3)
DOG/CHANGE signal : ON
MR-J3- B
DOG/CHANGE
DI3
DOG/CHANGE signal : OFF
MR-J3- B
DOG/CHANGE
DI3
DICOM DICOM
(Note-1): Refer to the "Q173DCPU/Q172DCPU Motion controller Programming Manual
(COMMON)" for an external signal.
(Note-2): Refer to the "Q173DCPU/Q172DCPU User’s Manual" for a pin configuration.
(Note-3): Refer to the "MR-J3- B Servo Amplifier Instruction Manual" for a pin configuration.
(16) Servo ready signal (M2415+20n) ..............................Status signal
(a) This signal turns on when the servo amplifiers connected to each axis are in the READY state.
(b) This signal turns off in the following cases.
• M2042 is off
• Servo amplifier is not mounted
• Servo parameter is not set
• It is received the forced stop input from an external source
• Servo OFF by the servo OFF command (M3215+20n) ON
• Servo error occurs
Refer to "APPENDIX 1.4 Servo errors" for details.
3 - 18
3 POSITIONING DEDICATED SIGNALS
Q61P Q03UD
CPU
Q172D
CPU
Q38DB
Communication is normal
Servo ready signal : ON
AMP
M
AMP
M
POINT
When the part of multiple servo amplifiers connected to the SSCNET becomes a servo error, only an applicable axis becomes the servo OFF state.
(17) Torque limiting signal (M2416+20n) ..........................Status signal
This signal turns on while torque limit is executed.
The signal toward the torque limiting axis turns on
(18) M-code outputting signal (M2419+20n) .....................Status signal
(a) This signal turns during M-code is outputting.
(b) This signal turns off when the stop command, cancel signal, skip signal or
FIN signal are inputted.
M-code M1 M2 M3
ON
M-code outputting signal
(M2419+20n)
FIN signal
(M3219+20n)
OFF
OFF
ON
POINTS
(1) The FIN signal and M-code outputting signal are both for the FIN signal wait function.
(2) The FIN signal and M-code outputting signal are effective only when FIN acceleration/deceleration is designated in the servo program.
Otherwise, the FIN signal wait function is disabled, and the M-code outputting signal does not turn on.
3 - 19
3 POSITIONING DEDICATED SIGNALS
3.1.2 Axis command signals
(1) Stop command (M3200+20n) ............................... Command signal
(a) This command is a signal which stop a starting axis from an external source and becomes effective at leading edge of signal. (An axis for which the stop command is turning on cannot be started.)
ON
Stop command
(M3200+20n)
OFF
V
Stop command for specified axis
Control when stop command turns off
Setting speed
Stop t
Deceleration stop processing
(b) The details of stop processing when the stop command turns on are shown below. (Refer to Section 6.13 or 6.14 for details of the speed control.)
Processing at the turning stop command on
Control details during execution
During control During deceleration stop processing
Positioning control
Speed control ( , )
JOG operation
The axis decelerates to a stop in the deceleration time set in the parameter block or servo program.
The deceleration stop processing is continued.
Speed control with fixed position stop
Manual pulse generator operation
An immediate stop is executed without deceleration processing.
Home position return
(1) The axis decelerates to a stop in the deceleration time set in the parameter block.
(2) A "stop error during home position return" occurs and the error code [202] is stored in the minor error storage register for each axis.
(c) The stop command in a dwell time is invalid. (After a dwell time, the start accept flag (M2001+n) turns OFF, and the positioning complete signal
(M2401+20n) turns ON.)
POINT
If it is made to stop by turning on the stop command (M3200+20n) during a home position return, execute the home position return again.
If the stop command is turned on after the proximity dog ON in the proximity dog type, execute the home position return after move to before the proximity dog ON by the JOG operation or positioning.
3 - 20
3 POSITIONING DEDICATED SIGNALS
(2) Rapid stop command (M3201+20n) ..................... Command signal
(a) This command stops a starting axis rapidly from an external source and becomes effective at leading edge of signal. (An axis for which the rapid stop command is turning on cannot be started.)
ON
Rapid stop command
(M3201+20n)
OFF
V
Rapid stop command for specified axis
Control when rapid stop command turns off
Setting speed
Stop t
Rapid stop processing
(b) The details of stop processing when the rapid stop command turns on are shown below.
Processing at the turning rapid stop command on
Control details during execution
During control During deceleration stop processing
Position control
Speed control ( , )
JOG operation
Speed control with fixed position stop
The axis decelerates to a rapid stop deceleration time set in the parameter block or servo program.
Deceleration processing is stopped and rapid stop processing is executed.
Manual pulse generator operation
An immediate stop is executed without deceleration processing.
(1) The axis decelerates to a stop in the rapid stop deceleration time set in the parameter block.
Home position return
(2) A "stop error during home position return" error occurs and the error code [203] is stored in the minor error storage register for each axis.
(c) The rapid stop command in a dwell time is invalid. (After a dwell time, the start accept flag (M2001+n) turns OFF, and the positioning complete signal
(M2401+20n) turns ON.)
POINT
If it is made to stop rapidly by turning on the rapid stop command (M3201+20n) during a home position return, execute the home position return again.
If the rapid stop command turned on after the proximity dog ON in the proximity dog type, execute the home position return after move to before the proximity dog ON by the JOG operation or positioning.
3 - 21
3 POSITIONING DEDICATED SIGNALS
(3) Forward rotation JOG start command (M3202+20n)/Reverse rotation JOG start command (M3203+20n) ......... Command signal
(a) JOG operation to the address increase direction is executed while forward rotation JOG start command (M3202+20n) is turning on.
When M3202+20n is turned off, a deceleration stop is executed in the deceleration time set in the parameter block.
(b) JOG operation to the address decrease direction is executed while reverse rotation JOG start command (M3203+20n) is turning on.
When M3203+20n is turned off, a deceleration stop is executed in the deceleration time set in the parameter block.
POINT
Take an interlock so that the forward rotation JOG start command (M3202+20n) and reverse rotation JOG start command (M3203+20n) may not turn on simultaneously.
(4) Complete signal OFF command (M3204+20n)
......................... Command signal
(a) This command is used to turn off the positioning start complete signal
(M2400+20n) and positioning complete signal (M2401+20n).
Dwell time Dwell time t
ON
Positioning start complete signal
(M2400+20n)
Positioning complete signal (M2401+20n)
Complete signal OFF command (M3204+20n)
OFF
OFF
OFF
ON
ON
POINT
Do not turn the complete signal OFF command on with a PLS instruction.
If it is turned on with a PLS instruction, it cannot be turned off the positioning start complete signal (M2400+20n) and the positioning complete signal (M2401+20n).
3 - 22
3 POSITIONING DEDICATED SIGNALS
(5) Speed/position switching enable command (M3205+20n)
......... Command signal
(a) This command is used to make the CHANGE signal (speed/position switching signal) effective from an external source.
• ON .......... Control switches from speed control to position control when the CHANGE signal turned on.
• OFF .......... Control does not switch from speed to position control even if the CHANGE signal turns on.
Control does not switch from speed control to position control because M3205+20n turns off
CHANGE CHANGE Control switches from speed control to position control because
M3205+20n turns on t
ON
Speed/position switching enable command (M3205+20n)
OFF
CHANGE signal from external source
OFF
(6) Error reset command (M3207+20n) ..................... Command signal
This command is used to clear the minor/major error code storage register of an axis for which the error detection signal has turn on (M2407+20n: ON), and reset the error detection signal (M2407+20n).
ON
Error detection signal
(M2407+20n)
OFF
ON
Error reset command
(M3207+20n)
Minor error code storage register (D6+20n)
Major error code storage register (D7+20n)
OFF
**
**
00
00
** : Error code
(7) Servo error reset command (M3208+20n) ........... Command signal
This command is used to clear the servo error code storage register of an axis for which the servo error detection signal has turn on (M2408+20n: ON), and reset the servo error detection signal (M2408+20n).
ON
Servo error detection signal
(M2408+20n)
OFF
ON
Servo error reset command
(M3208+20n)
Servo error code storage register
OFF
** 00
** : Error code
3 - 23
3 POSITIONING DEDICATED SIGNALS
REMARK
Refer to APPENDIX 1 for details on the minor error code, major error code and servo error code storage registers.
(8) External stop input disable at start command (M3209+20n)
....................... Command signal
This signal is used to set the external stop signal input valid or invalid.
• ON .......... External stop input is set as invalid, and even axes which stop input is turning on can be started.
• OFF .......... External stop input is set as valid, and axes which stop input is turning on cannot be started.
POINT
When it stops an axis with the external stop input after it starts by turning on the external stop input disable at start command (M3209+20n), switch the external stop input from OFF ON (if the external stop input is turning on at the starting, switch it from ON OFF ON).
(9) Feed current value update request command (M3212+20n)
....................... Command signal
This signal is used to set whether the feed current value will be cleared or not at the starting in speed/position switching control.
• ON .......... The feed current value is updated from the starting.
The feed current value is not cleared at the starting.
• OFF .......... The feed current value is updated from the starting.
The feed current value is cleared at the starting.
POINT
When it starts by turning on the feed current value update request command
(M3212+20n), keep M3212+20n on until completion of the positioning control.
If M3212+20n is turned off on the way, the feed current value may not be reliable.
(10) Servo OFF command (M3215+20n) .................. Command signal
This command is used to execute the servo OFF state (free run state).
• M3215+20n: OFF ..... Servo ON
• M3215+20n: ON ....... Servo OFF (free run state)
This command becomes invalid during positioning, and should therefore be executed after completion of positioning.
CAUTION
Turn the power supply of the servo amplifier side off before touching a servomotor, such as machine adjustment.
3 - 24
3 POSITIONING DEDICATED SIGNALS
(11) Gain changing command (M3216+20n) ............. Command signal
This signal is used to change the gain of servo amplifier in the Motion controller by the gain changing command ON/OFF.
• ON .......... Gain changing command ON
• OFF .......... Gain changing command OFF
Refer to the "MR-J3- B Servo Amplifier Instruction Manual" for details of gain changing function.
Instruction Manual list is shown below.
Servo amplifier type Instruction manual name
MR-J3- B MR-J3- B Servo Amplifier Instruction Manual (SH-030051)
(12) Control loop changing command (M3218+20n)
....................... Command signal
When using the fully closed loop control servo amplifier, this signal is used to change the fully closed loop control/semi closed loop control of servo amplifier in the Motion controller by the control loop changing command
ON/OFF.
• ON .......... During fully closed loop control
• OFF .......... During semi closed loop control
Fully closed loop control change
Semi closed loop control change
ON
Control loop changing command
(M3218+20n)
OFF
ON
Control loop monitor status
(M2272+n)
OFF
Refer to the "Fully closed loop control MR-J3- B-RJ006 Servo Amplifier
Instruction Manual" for details of control loop changing.
Instruction Manual list is shown below.
Servo amplifier type
MR-J3- B-RJ006
Instruction manual name
Fully closed loop control MR-J3- B-RJ006
Servo Amplifier Instruction Manual (SH-030056)
POINTS
(1) When the servo amplifier is not started (LED: "AA", "Ab", "AC", "Ad" or "AE"), if the control loop changing command is turned ON/OFF, the command becomes invalid.
(2) When the followings are operated during the fully closed loop, it returns to the semi closed loop control.
(a) Power supply OFF or reset of the Multiple CPU system
(b) Wire breakage of the SSCNET cable between the servo amplifier and
Motion controller
(c) Control circuit power supply OFF of the servo amplifier
3 - 25
3 POSITIONING DEDICATED SIGNALS
(13) FIN signal (M3219+20n) .................................... Command signal
When a M-code is set in a servo program, transit to the next block does not execute until the FIN signal changes as follows: OFF ON OFF.
Positioning to the next block begins after the FIN signal changes as above.
It is valid, only when the FIN acceleration/deceleration is set and FIN signal wait function is selected.
<K 0>
Point
1
2
3
4
CPSTART2
Axis
Axis
Speed
1
2
FIN acceleration/
deceleration
ABS-2
Axis
Axis
M-code
1,
2,
ABS-2
Axis
Axis
M-code
ABS-2
Axis
Axis
M-code
ABS-2
Axis
Axis
CPEND
1,
2,
1,
2,
1,
2,
Point 1 WAIT 2
M-code 10 11
10000
100
M-code outputting signal
(M2419+20n)
FIN signal
(M3219+20n)
200000
200000
10
300000
250000
11
350000
300000
12
400000
400000
Timing Chart for Operation Description
1. When the positioning of point 1 starts, M-code 10 is output and the M-code outputting signal turns on.
2. FIN signal turns on after performing required processing in the
Motion SFC program. Transition to the next point does not execute until the FIN signal turns on.
3. When the FIN signal turns on, the M-code outputting signal turns off.
4. When the FIN signal turns off after the M-code outputting signal turns off, the positioning to the next point 2 starts.
POINTS
(1) The FIN signal and M-code outputting signal are both signal for the FIN signal wait function.
(2) The FIN signal and M-code outputting signal are valid only when FIN acceleration/deceleration is designated in the servo program.
Otherwise, the FIN signal wait function is disabled, and the M-code outputting signal does not turn on.
3 - 26
3 POSITIONING DEDICATED SIGNALS
3.1.3 Common devices
POINTS
(1) Internal relays for positioning control are not latched even within the latch range.
In this manual, in order to indicate that internal relays for positioning control are not latched, the expression used in this text is "M2000 to M2319".
(2) The range devices allocated as internal relays for positioning control cannot be used by the user even if their applications have not been set.
(1) PLC ready flag (M2000) ..............………………… Command signal
(a) This signal informs the Motion CPU that the PLC CPU is normal.
1) The positioning control, home position return, JOG operation or manual pulse generator operation using the servo program which performs the
Motion SFC program when the M2000 is ON.
2) The above 1) control is not performed even if the M2000 is turned on during the test mode [TEST mode ON flag (SM501): ON] using
MT Developer.
(b) The setting data such as the fixed parameters, servo parameters and limit switch output data can be changed using MT Developer when the M2000 is
OFF only.
The above data using MT Developer cannot be written when the M2000 is
ON.
(c) The following processings are performed when the M2000 turns OFF to ON.
1) Processing details
• Clear the M-code storage area of all axes.
• Turn the PCPU READY complete flag (SM500) on. (Motion SFC program can be executed.)
• Start to execute the Motion SFC program of the automatic starting from the first.
2) If there is a starting axis, an error occurs, and the processing in above
(c) 1) is not executed.
3 - 27
3 POSITIONING DEDICATED SIGNALS
3) The processing in above (c) 1) is not executed during the test mode.
It is executed when the test mode is cancelled and M2000 is ON.
V
Deceleration stop
Positioning start t
PLC ready flag
(M2000)
OFF
PCPU READY complete flag
(SM500)
OFF
ON
ON
Clear a M-code
PCPU READY complete flag
(SM500) does not turn on because during deceleration.
(d) The following processings are performed when the M2000 turns ON to
OFF.
1) Processing details
• Turn the PCPU READY complete flag (SM500) off.
• Deceleration stop of the starting axis.
• Stop to execute the Motion SFC program.
• Turn all points of the real output PY off.
(e) Operation setting at STOP RUN
The condition which the PLC ready flag (M2000) turns on is set in the system setting. Select the following either.
1) M2000 is turned on by switching from STOP to RUN. (Default)
The condition which M2000 turns OFF to ON.
• Move the RUN/STOP switch from STOP to RUN.
• Turn the power supply on where the RUN/STOP switch is moved to
RUN.
The condition which M2000 turns ON to OFF.
• Move the RUN/STOP switch from RUN to STOP.
2) M2000 is turned on by switching from STOP to RUN and setting 1 in the set register.
(M2000 is turned on by set "1" to the switch RUN setting register.)
The condition which M2000 is turned ON to OFF.
• Set "1" to the setting register D704 of the PLC ready flag where the
RUN/STOP switch is moved to RUN. (The Motion CPU detects the change of the lowest rank bit 0 1 in D704.)
3 - 28
3 POSITIONING DEDICATED SIGNALS
The condition which M2000 is turned ON to OFF.
• Set "0" to the setting register D704 of the PLC ready flag where the
RUN/STOP switch is moved to RUN. (The Motion CPU detects the change of the lowest rank bit 1 0 in D704.)
• Move the RUN/STOP switch from RUN to STOP.
(2) Start accept flag (M2001 to M2032) ............................ Status signal
(a) This flag turns on when the servo program is started. The start accept flag corresponding to an axis specified with the servo program turns on.
Servo program start
Start accept flag
(M2001+n)
Positioning complete
(M2401+20n)
Positioning start complete (M2400+20n)
OFF
V
(b) The ON/OFF processing of the start accept flag is shown below.
1) When the servo program is started using the Motion SFC program or
Motion dedicated PLC instruction (D(P).SVST), the start accept flag corresponding to an axis specified with the servo program turns on and it turns off at the positioning completion. This flag also turns off when it is made to stopping on the way.
(When it is made to stop on the way by the speed change to speed "0", this flag remains on.)
Normal positioning completion Positioning stop during control
V
Dwell time
Positioning completion t
Servo program start
Positioning start t
Positioning stop completion
ON ON
OFF Start accept flag
(M2001+n)
OFF
ON
Positioning complete
(M2401+20n)
Positioning start complete (M2400+20n)
OFF
OFF
ON
2) This flag turns on at the positioning control by turning on the JOG start command (M3202+20n or M3203+20n), and turns off at the positioning stop by turning off the JOG start command.
3) This flag turns on during the manual pulse generator enable (M2051 to
M2053: ON), and turns off at the manual pulse generator disable
(M2051 to M2053: OFF).
4) This flag turns on during a current value change by the CHGA instruction of servo program or Motion dedicated PLC instruction
(D(P).CHGA), and turns off at the completion of the current value change.
CHGA instruction
Start accept flag
(M2001 to M2032)
OFF
ON
Current value changing processing
Turns off at the completion of current value change.
3 - 29
3 POSITIONING DEDICATED SIGNALS
The start accept flag list is shown below.
Axis No. Device No. Axis No.
Device No. Axis No.
Device No. Axis No. Device No.
1 M2001 9 M2009 17 M2017 25 M2025
2 M2002 10 M2010 18 M2018 26 M2026
3 M2003 11 M2011 19 M2019 27 M2027
4 M2004 12 M2012 20 M2020 28 M2028
5 M2005 13 M2013 21 M2021 29 M2029
6 M2006 14 M2014 22 M2022 30 M2030
7 M2007 15 M2015 23 M2023 31 M2031
8 M2008 16 M2016 24 M2024 32 M2032
(Note): The range of axis No.1 to 8 is valid in the Q172DCPU.
CAUTION
Do not turn the start accept flags ON/OFF in the user side.
• If the start accept flag is turned off using the Motion SFC program or MT Developer while this flag is on, no error will occur but the positioning operation will not be reliable. Depending on the type of machine, it might operate in an unanticipated operation.
• If the start accept flag is turned on using the Motion SFC program or MT Developer while this flag is off, no error will occur but the "start accept on error" will occur at the next starting and cannot be started.
(3) Motion error history clear request flag (M2035)
.……. Command signal
This flag is used to clear the backed-up Motion error history (#8640 to #8735).
The Motion error history is cleared at leading edge of M2035.
After detection of leading edge of M2035, the Motion error history is cleared, and then the M2035 is automatically turned OFF.
(4) Motion SFC debugging flag (M2038) ......….............… Status signal
This flag turns on when it switches to the debug mode of the Motion SFC program using MT Developer.
It turns off with release of the debug mode.
(5) Motion error detection flag (M2039) .....…..…......…… Status signal
This flag turns on with error occurrence of the Motion CPU.
Turn off this flag by the user side, after checking the error contents and removing the error cause.
The self-diagnosis error information except stop error is cleared at the turning
M2039 ON to OFF.
3 - 30
3 POSITIONING DEDICATED SIGNALS
V
(6) Speed switching point specified flag (M2040) ...... Command signal
This flag is used when the speed change is specified at the pass point of the constant speed control.
(a) By turning M2040 on before the starting of the constant speed control
(before the servo program is started), control with the change speed can be executed from the first of pass point.
• OFF .......... Speed is changed to the specified speed from the pass point of the constant speed control.
• ON .......... Speed has been changed to the specified speed at the pass point of the constant speed control.
M2040 OFF
V
M2040 ON
Pass points of the constant speed control
(When the speed change
is specified with P3.)
Speed switching point specified flag (M2040)
OFF
Servo program start
P1
ON
P2
Start accept flag
(M2001+n)
OFF
P3 P4 t t
Pass points of the constant speed control
(When the speed change
is specified with P3.)
Speed switching point specified flag (M2040)
OFF
ON
P1
Servo program start
ON
Start accept flag
(M2001+n)
OFF
P2 P3 P4
(7) System setting error flag (M2041)................................. Status signal
This flag set the "system setting data" set by MT Developer and performs an adjustment check with a real mounting state (main base unit/extension base units) at the power supply on or reset.
• ON .......... Error
• OFF .......... Normal
(a) When an error occurs, the 7-segment LED at the front side of Motion CPU shows the system setting error.
The error contents can be confirmed using the Motion CPU error batch monitor of MT Developer.
(b) When M2041 is on, positioning cannot be started. Remove an error factor, and turn the power supply on again or reset the Multiple CPU system.
REMARK
Even if the module which is not set as the system setting of MT Developer is installed in the slot, it is not set as the object of an adjustment check. And, the module which is not set as the system setting cannot be used in the Motion CPU.
3 - 31
3 POSITIONING DEDICATED SIGNALS
(8) All axes servo ON command (M2042) .................. Command signal
This command is used to enable servo operation.
(a) Servo operation enabled … M2042 turns on while the servo OFF command
(M3215+20n) is off and there is no servo error.
(b) Servo operation disable ...... • M2042 is off
• The servo OFF command (M3215+20n) is on
• Servo error state
ON
All axes servo ON command
(M2042)
OFF
ON
All axes servo ON accept flag
(M2049)
OFF
ON
(Note)
Each axis servo ready state OFF
(Note): Refer to "3.1.1 Axis statuses "Servo ready signal"" for details.
POINT
When M2042 turns on, it is not turned off even if the CPU is set in the STOP state.
(9) Motion slot fault detection flag (M2047) ....................... Status signal
This flag is used as judgement which modules installed in the motion slot of the main base unit is "normal" or "abnormal".
• ON .......... Installing module is abnormal
• OFF .......... Installing module is normal
The module information at the power supply on and after the power supply injection are always checked, and errors are detected.
(a) Perform the disposal (stop the starting axis, servo OFF, etc.) of error detection using the Motion SFC program.
(10) JOG operation simultaneous start command (M2048)
.……. Command signal
(a) When M2048 turns on, JOG operation simultaneous start based on the
JOG operation execution axis set in the JOG operation simultaneous start axis setting register (D710 to D713).
(b) When M2048 turns off, the axis during operation decelerates to a stop.
3 - 32
3 POSITIONING DEDICATED SIGNALS
(11) All axes servo ON accept flag (M2049) .................... Status signal
This flag turns on when the Motion CPU accepts the all axes servo ON command (M2042).
Since the servo ready state of each axis is not checked, confirm it in the servo ready signal (M2415+20n).
ON
All axes servo ON command
(M2042)
OFF
ON
All axes servo ON accept flag
(M2049)
OFF
ON
Each axis servo ready state
(Note)
OFF
(Note): Refer to "3.1.1 Axis statuses "Servo ready signal"" for details.
(12) Manual pulse generator enable flag (M2051 to M2053)
.......... Command signal
This flag set the enabled or disabled state for positioning with the pulse input from the manual pulse generators connected to P1 to P3 (Note) of the Q173DPX.
• ON .......... Positioning control is executed by the input from the manual pulse generators.
• OFF .......... Positioning control cannot be executed by the manual pulse generators because of the input from the manual pulse generators is ignored.
Default value is invalid (OFF).
REMARK
(Note): Refer to the "Q173DCPU/Q172DCPU User's Manual" for P1 to P3 connector of the Q173DPX.
(13) Operation cycle over flag (M2054) ............................ Status signal
This flag turns on when the time concerning motion operation exceeds the operation cycle of the Motion CPU setting (SD523). Perform the following operation, in making it turn off.
• Turn the power supply of the Multiple CPU system on to off
• Reset the Multiple CPU system
• Reset using the user program
[Error measures]
1) Change the operation cycle into a large value in the system setting.
2) The number of instruction completions of an event task or NMI task in the Motion SFC program.
3 - 33
3 POSITIONING DEDICATED SIGNALS
(14) Speed change accepting flag (M2061 to M2092)
................... Status signal
This flag turns on during speed change by the control change (CHGV) instruction (or Motion dedicated PLC instruction (D(P).CHGV)) of the Motion
SFC program.
CHGV instruction
ON
Speed change accepting flag
OFF
0 to 4ms
Speed change
Setting speed
Speed after speed change
Speed change completion t
The speed change accepting flag list is shown below.
Axis No. Device No. Axis No.
Device No. Axis No.
Device No. Axis No. Device No.
1 M2061 9 M2069 17 M2077 25 M2085
2 M2062 10 M2070 18 M2078 26 M2086
3 M2063 11 M2071 19 M2079 27 M2087
4 M2064 12 M2072 20 M2080 28 M2088
5 M2065 13 M2073 21 M2081 29 M2089
6 M2066 14 M2074 22 M2082 30 M2090
7 M2067 15 M2075 23 M2083 31 M2091
8 M2068 16 M2076 24 M2084 32 M2092
(Note): The range of axis No.1 to 8 is valid in the Q172DCPU.
REMARK
In the SV22 virtual mode, the flag is that of the virtual servomotor axis.
3 - 34
3 POSITIONING DEDICATED SIGNALS
(15) Automatic decelerating flag (M2128 to M2159) ......... Status signal
This signal turns on while automatic deceleration processing is performed during the positioning control or position follow-up control.
(a) This flag turns on while automatic deceleration to the command address at the position follow-up control, but it turns off if the command address is changed.
(b) This signal turns on while automatic deceleration processing is performed during execution of positioning to final point while in constant speed control.
V
P1
P2
Automatic decelerating flag
ON
OFF
P3 t
V
Automatic decelerating flag
ON
OFF
P1
The automatic decelerating flag is turns on after the execution of positioning to final point (P3) even if automatic deceleration processing start while executing the positioning to P2.
P2 t
P3
POINT
Set a travel value in which automatic deceleration processing can be started at the final positioning point, therefore the automatic decelerating flag turns on at the start point of automatic deceleration processing after this final point.
(c) The signal turns off when all normal start complete commands became achieve.
3 - 35
3 POSITIONING DEDICATED SIGNALS
(d) In any of the following cases, this flag does not turn off.
• When deceleration due to JOG signal off
• During manual pulse generator operation
• During deceleration due to stop command or stop cause occurrence
• When travel value is 0
V t
Automatic decelerating flag
ON
OFF
The automatic decelerating flag list is shown below.
Axis No. Device No. Axis No.
Device No. Axis No.
Device No. Axis No. Device No.
1 M2128 9 M2136 17 M2144 25 M2152
2 M2129 10 M2137 18 M2145 26 M2153
3 M2130 11 M2138 19 M2146 27 M2154
4 M2131 12 M2139 20 M2147 28 M2155
5 M2132 13 M2140 21 M2148 29 M2156
6 M2133 14 M2141 22 M2149 30 M2157
7 M2134 15 M2142 23 M2150 31 M2158
8 M2135 16 M2143 24 M2151 32 M2159
(Note): The range of axis No.1 to 8 is valid in the Q172DCPU.
REMARK
In the SV22 virtual mode, the flag is that of the virtual servomotor axis.
3 - 36
3 POSITIONING DEDICATED SIGNALS
(16) Speed change "0" accepting flag (M2240 to M2271)
....………. Status signal
This flag turns on while a speed change request to speed "0" or negative speed change is being accepted.
It turns on when the speed change request to speed "0" or negative speed change is accepted during a start. After that, this signal turns off when a speed change is accepted or on completion of a stop due to a stop cause.
Deceleration stop at the speed change
"0" accept.
Speed change "0"
V
V
1
Thereafter, by changing speed to except "0", it starts continuously.
Speed change V
2
V
2 t
Start accept flag
Speed change "0" accepting flag
Positioning complete signal
OFF
ON
The speed change "0" accepting flag list is shown below.
Axis No. Device No. Axis No.
Device No. Axis No.
Device No. Axis No. Device No.
1 M2240 9 M2248 17 M2256 25 M2264
2 M2241 10 M2249 18 M2257 26 M2265
3 M2242 11 M2250 19 M2258 27 M2266
4 M2243 12 M2251 20 M2259 28 M2267
5 M2244 13 M2252 21 M2260 29 M2268
6 M2245 14 M2253 22 M2261 30 M2269
7 M2246 15 M2254 23 M2262 31 M2270
8 M2247 16 M2255 24 M2263 32 M2271
(Note): The range of axis No.1 to 8 is valid in the Q172DCPU.
REMARK
(1) Even if it has stopped, when the start accept flag (M2001 to M2032) is ON state, the state where the request of speed change "0" is accepted is indicated.
Confirm by this speed change "0" accepting flag.
(2) During interpolation, the flags corresponding to the interpolation axes are set.
(3) In any of the following cases, the speed change "0" request is invalid.
• After deceleration by the JOG signal off
• During manual pulse generator operation
• After positioning automatic deceleration start
• After deceleration due to stop cause
(4) During the SV22 virtual mode, the flag is that of the virtual servomotor axis.
3 - 37
3 POSITIONING DEDICATED SIGNALS
(a) The flag turns off if a speed change request occurs during deceleration to a stop due to speed change "0".
V
V
1
Speed change "0"
Speed change V
2
V
2 t
Start accept flag
Speed change "0" accepting flag
OFF
ON
(b) The flag turns off if a stop cause occurs after speed change "0" accept.
V
Speed change "0"
Stop cause t
Start accept flag
Speed change "0" accepting flag
OFF
ON
(c) The speed change "0" accepting flag does not turn on if a speed change "0" occurs after an automatic deceleration start.
Automatic deceleration start
V
Speed change "0" t
Start accept flag
Speed change "0" accepting flag
(OFF)
3 - 38
3 POSITIONING DEDICATED SIGNALS
(d) Even if it is speed change "0" after the automatic deceleration start to the
"command address", speed change "0" accepting flag turns on.
V
Command address P1
V
1
Automatic deceleration start
Speed change "0"
Command address P2
P1
Speed change V
2
V
2
P2 t
Start accept flag
Speed change "0" accepting flag
OFF
ON
REMARK
It does not start, even if the "command address" is changed during speed change
"0" accepting.
(17) Control loop monitor status (M2272 to M2303)
............................... Command signal
When using the fully closed loop control servo amplifier, this signal is used to check the fully closed loop control/semi closed loop control of servo amplifier.
• ON .......... During fully closed loop control
• OFF .......... During semi closed loop control
It can be changed the fully closed loop control/semi closed loop control of servo amplifier in the Motion controller by the control loop changing command ON/OFF.
Fully closed loop control change
Semi closed loop control change
ON
Control loop changing command
(M3218+20n)
OFF
ON
Control loop monitor status
(M2272+n)
OFF
The Control loop monitor status list is shown below.
Axis No. Device No. Axis No.
Device No. Axis No.
Device No. Axis No. Device No.
1 M2272 9 M2280 17 M2288 25 M2296
2 M2273 10 M2281 18 M2289 26 M2297
3 M2274 11 M2282 19 M2290 27 M2298
4 M2275 12 M2283 20 M2291 28 M2299
5 M2276 13 M2284 21 M2292 29 M2300
6 M2277 14 M2285 22 M2293 30 M2301
7 M2278 15 M2286 23 M2294 31 M2302
8 M2279 16 M2287 24 M2295 32 M2303
(Note): The range of axis No.1 to 8 is valid in the Q172DCPU.
3 - 39
advertisement
* Your assessment is very important for improving the workof artificial intelligence, which forms the content of this project
Related manuals
advertisement
Table of contents
- 2 SAFETY PRECAUTIONS
- 12 REVISIONS
- 13 CONTENTS
- 16 About Manuals
- 18 1. OVERVIEW
- 18 1.1 Overview
- 20 1.2 Features
- 20 1.2.1 Performance Specifications
- 22 2. POSITIONING CONTROL BY THE MOTION CPU
- 22 2.1 Positioning Control by the Motion CPU
- 36 3. POSITIONING DEDICATED SIGNALS
- 38 3.1 Internal Relays
- 45 3.1.1 Axis statuses
- 55 3.1.2 Axis command signals
- 62 3.1.3 Common devices
- 75 3.2 Data Registers
- 79 3.2.1 Axis monitor devices
- 85 3.2.2 Control change registers
- 86 3.2.3 Common devices
- 89 3.3 Motion Registers (#)
- 91 3.4 Special Relays (SM)
- 94 3.5 Special Registers (SD)
- 100 4. PARAMETERS FOR POSITIONING CONTROL
- 100 4.1 System Settings
- 101 4.2 Fixed Parameters
- 102 4.2.1 Number of pulses/travel value per rotation
- 104 4.2.2 Backlash compensation amount
- 104 4.2.3 Upper/lower stroke limit value
- 106 4.2.4 Command in-position range
- 107 4.2.5 Speed control 10 multiplier setting for degree axis
- 110 4.3 Parameter Block
- 112 4.3.1 Relationships between the speed limit value, acceleration time, deceleration time and rapid stop deceleration time
- 112 4.3.2 S-curve ratio
- 113 4.3.3 Allowable error range for circular interpolation
- 114 5. SERVO PROGRAMS FOR POSITIONING CONTROL
- 114 5.1 Servo Program Composition Area
- 114 5.1.1 Servo program composition
- 115 5.1.2 Servo program area
- 116 5.2 Servo Instructions
- 129 5.3 Positioning Data
- 135 5.4 Setting Method for Positioning Data
- 135 5.4.1 Setting method by specifying numerical values
- 136 5.4.2 Indirect setting method by devices
- 140 6. POSITIONING CONTROL
- 140 6.1 Basics of Positioning Control
- 140 6.1.1 Positioning speed
- 141 6.1.2 Positioning speed at the interpolation control
- 146 6.1.3 Control units for 1 axis positioning control
- 146 6.1.4 Control units for interpolation control
- 148 6.1.5 Control in the control unit "degree"
- 150 6.1.6 Stop processing and restarting after stop
- 156 6.1.7 Acceleration/deceleration processing
- 158 6.2 1 Axis Linear Positioning Control
- 161 6.3 2 Axes Linear Interpolation Control
- 166 6.4 3 Axes Linear Interpolation Control
- 172 6.5 4 Axes Linear Interpolation Control
- 177 6.6 Auxiliary Point-Specified Circular Interpolation Control
- 182 6.7 Radius-Specified Circular Interpolation Control
- 188 6.8 Central Point-Specified Circular Interpolation Control
- 194 6.9 Helical Interpolation Control
- 195 6.9.1 Circular interpolation specified method by helical interpolation
- 216 6.10 1 Axis Fixed-Pitch Feed Control
- 220 6.11 Fixed-Pitch Feed Control Using 2 Axes Linear Interpolation
- 224 6.12 Fixed-Pitch Feed Control Using 3 Axes Linear Interpolation
- 228 6.13 Speed Control ( I )
- 232 6.14 Speed Control ( II )
- 235 6.15 Speed/Position Switching Control
- 235 6.15.1 Speed/position switching control start
- 242 6.15.2 Re-starting after stop during control
- 247 6.16 Speed-Switching Control
- 247 6.16.1 Speed-switching control start, speed-switching points and end specification
- 253 6.16.2 Specification of speed-switching points using repetition instructions
- 259 6.17 Constant-Speed Control
- 263 6.17.1 Specification of pass points by repetition instructions
- 268 6.17.2 Speed-switching by instruction execution
- 273 6.17.3 1 axis constant-speed control
- 277 6.17.4 2 to 4 axes constant-speed control
- 284 6.17.5 Constant speed control for helical interpolation
- 287 6.17.6 Pass point skip function
- 289 6.17.7 FIN signal wait function
- 299 6.18 Position Follow-Up Control
- 306 6.19 Speed control with fixed position stop
- 311 6.20 Simultaneous Start
- 314 6.21 JOG Operation
- 314 6.21.1 JOG operation data
- 315 6.21.2 Individual start
- 320 6.21.3 Simultaneous start
- 323 6.22 Manual Pulse Generator Operation
- 330 6.23 Home Position Return
- 331 6.23.1 Home position return data
- 339 6.23.2 Home position return by the proximity dog type 1
- 342 6.23.3 Home position return by the proximity dog type 2
- 344 6.23.4 Home position return by the count type 1
- 346 6.23.5 Home position return by the count type 2
- 347 6.23.6 Home position return by the count type 3
- 349 6.23.7 Home position return by the data set type 1
- 350 6.23.8 Home position return by the data set type 2
- 351 6.23.9 Home position return by the dog cradle type
- 356 6.23.10 Home position return by the stopper type 1
- 358 6.23.11 Home position return by the stopper type 2
- 360 6.23.12 Home position return by the limit switch combined type
- 362 6.23.13 Home position return retry function
- 366 6.23.14 Home position shift function
- 370 6.23.15 Condition selection of home position set
- 371 6.23.16 Servo program for home position return
- 373 6.24 High-Speed Oscillation
- 376 7. AUXILIARY AND APPLIED FUNCTIONS
- 376 7.1 M-code Output Function
- 379 7.2 Backlash Compensation Function
- 381 7.3 Torque Limit Function
- 383 7.4 Skip Function in which Disregards Stop Command
- 385 7.5 Cancel of the Servo Program
- 386 7.5.1 Cancel/start
- 388 APPENDICES
- 388 APPENDIX 1 Error Codes Stored Using The Motion CPU
- 390 APPENDIX 1.1 Servo program setting errors (Stored in SD517)
- 395 APPENDIX 1.2 Minor errors
- 405 APPENDIX 1.3 Major errors
- 409 APPENDIX 1.4 Servo errors
- 428 APPENDIX 2 Example Programs
- 428 APPENDIX 2.1 Reading M-code
- 429 APPENDIX 2.2 Reading error code
- 431 APPENDIX 3 Setting Range for Indirect Setting Devices
- 433 APPENDIX 4 Processing Times of the Motion CPU
- 434 APPENDIX 5 Device List
- 445 WARRANTY