- Home
- Home security & automation
- Security access control systems
- Mitsubishi
- MOTION CONTROLLERS Q172DCPU
- Instruction manual
advertisement
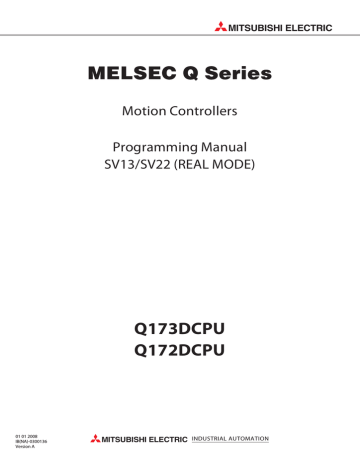
APPENDICES
APPENDIX 1.3 Major errors
These errors occur by control command from the external input signal or Motion SFC program, and the error codes 1000 to 1999 are used.
Major errors include the positioning control start errors, positioning control errors, absolute position system errors and system errors.
(1) Positioning control start errors (1000 to 1099)
These errors are detected at the positioning control start.
The error codes, causes, processing and corrective actions are shown in Table
1.8.
Table 1.8 Positioning control start error (1000 to 1099) list
Control mode
Error code
Error cause
Error processing
Corrective action
1000
• The external STOP signal of the applicable axis turned on.
• Turn the STOP signal off.
1001
1002
1004
1005
1003
• The external signal FLS
(upper limit LS) turned off at the forward direction
(address increase direction) start.
• The external signal RLS
(lower limit LS) turned off at the reverse direction
(address decrease direction) start.
• The external DOG (proximity dog) signal turned on at the home position return start of the proximity dog type.
• Move in the reverse direction by the JOG operation, etc. and set within the external limit range.
• Move in the forward direction by the JOG operation, etc. and set within the external limit range.
• Perform the home position return after move to the proximity dog
ON by the JOG operation, etc.
Positioning control at the home position return of does not the proximity dog type.
• Wait until the servo READY state (M2415+20n: ON). start.
• The applicable axis is not servo READY state.
(M2415+20n: OFF).
(1) The power supply of the servo amplifier is OFF.
(2) During initial processing after turning on the servo amplifier.
(3) The servo amplifier is not mounted.
(4) A servo error is occurred.
(5) Cable fault.
(6) Servo OFF command
(M3215+20n) is ON.
• The servo error detection signal of the applicable axis
(M2408+20n) turned on.
• Eliminate the servo error, reset the servo error detection signal
(M2408+20n) by the servo error reset command (M3208+20n), then start operation.
APP - 18
APPENDICES
Error code
(2) Positioning control errors (1100 to 1199)
These errors are detected at the positioning control.
The error codes, causes, processing and corrective actions are shown in Table
1.9.
Table 1.9 Positioning control error (1100 to 1199) list
Control mode
Error cause
Error processing
Corrective action
1101
1102
1104
1105
1151
1103
• The external signal FLS
(upper limit LS) turned off during the forward direction
(address increase direction).
• The external signal RLS
(lower limit LS) turned off during the reverse direction
(address decrease direction).
• The external stop signal
(stop signal) turned on during home position return.
• The servo error detection signal turned on during positioning control.
• Travel in the reverse direction by the JOG operation, etc. and set within the external limit
Deceleration stop by
"Stop processing on STOP input" of the parameter block.
range.
• Travel in the forward direction by the JOG operation, etc. and set within the external limit range.
• Execute the home position return so that the external stop signal (stop signal) may not turn
Immediate stop without decelerating. on.
• Start after disposal at the servo error.
• The power supply of the servo amplifier turned off during positioning control.
(Servo not mounted status detection, cable fault, etc.)
• Home position return did not complete normally without
Turn the servo
READY
(M2415+
20n) off. stop within the in-position range of home position at
• Turn on the power supply of the servo amplifier.
• Check the connecting cable to the servo amplifier.
• Make the gain adjustment. the home position return.
• A synchronous encoder set in the system setting differs from a synchronous encoder actually connected.
Input from synchronous encoder does not accept.
• Set a synchronous encoder actually connected in the system setting.
• Q172DEX or encoder hardware error.
• Disconnected encoder cable.
Immediate input stop
• Check (replace) the Q172DEX or encoder.
• Check the encoder cable.
APP - 19
APPENDICES
Error code
(3) Absolute position system errors (1200 to 1299)
These errors are detected at the absolute position system.
The error codes, causes, processing and corrective actions are shown in Table
1.10.
Table 1.10 Absolute position system error (1200 to 1299) list
Control mode
Error cause
Error processing
Corrective action
1201
1202
1203
1204
• A sum check error occurred with the backup data in the controller at the turning on servo amplifier power supply.
Home
• Home position return was not performed. position return
• CPU module battery error.
• Home position return started request ON but did not complete normally.
• Check the battery and execute a home position return.
• A communication error between the servo amplifier
Home position and encoder occurred at the return turning on servo amplifier request ON,
• Check the motor and encoder cables and execute a home position return again. power supply. servo error
[2016] set.
(Fully closed loop control servo amplifier use: Servo error [2070] is set.)
• Check the motor and encoder cables.
• The amount of change in encoder current value is excessive during operation.
A continual check is performed (both of servo
ON and OFF states) after the servo amplifier power has been turned ON.
• The following expression holds: "Encoder current value [PLS] feedback current value [PLS]
(encoder effective bit number)" during operation.
A continual check is performed (both of servo
ON and OFF states) after the servo amplifier power has been turned on.
Home position return request ON
APP - 20
APPENDICES
Error code
(4) System errors (1300 to 1399)
These errors are detected at the power-on.
The error codes, causes, processing and corrective actions are shown in Table
1.11.
Table 1.11 System error (1300 to 1399) list
Control mode
Error cause
Error processing
Corrective action
1310
• Initial communication with the Multiple CPU system did not complete normally.
• Motion CPU fault.
Positioning control
• Replace the Motion CPU. does not start.
APP - 21
advertisement
* Your assessment is very important for improving the workof artificial intelligence, which forms the content of this project
Related manuals
advertisement
Table of contents
- 2 SAFETY PRECAUTIONS
- 12 REVISIONS
- 13 CONTENTS
- 16 About Manuals
- 18 1. OVERVIEW
- 18 1.1 Overview
- 20 1.2 Features
- 20 1.2.1 Performance Specifications
- 22 2. POSITIONING CONTROL BY THE MOTION CPU
- 22 2.1 Positioning Control by the Motion CPU
- 36 3. POSITIONING DEDICATED SIGNALS
- 38 3.1 Internal Relays
- 45 3.1.1 Axis statuses
- 55 3.1.2 Axis command signals
- 62 3.1.3 Common devices
- 75 3.2 Data Registers
- 79 3.2.1 Axis monitor devices
- 85 3.2.2 Control change registers
- 86 3.2.3 Common devices
- 89 3.3 Motion Registers (#)
- 91 3.4 Special Relays (SM)
- 94 3.5 Special Registers (SD)
- 100 4. PARAMETERS FOR POSITIONING CONTROL
- 100 4.1 System Settings
- 101 4.2 Fixed Parameters
- 102 4.2.1 Number of pulses/travel value per rotation
- 104 4.2.2 Backlash compensation amount
- 104 4.2.3 Upper/lower stroke limit value
- 106 4.2.4 Command in-position range
- 107 4.2.5 Speed control 10 multiplier setting for degree axis
- 110 4.3 Parameter Block
- 112 4.3.1 Relationships between the speed limit value, acceleration time, deceleration time and rapid stop deceleration time
- 112 4.3.2 S-curve ratio
- 113 4.3.3 Allowable error range for circular interpolation
- 114 5. SERVO PROGRAMS FOR POSITIONING CONTROL
- 114 5.1 Servo Program Composition Area
- 114 5.1.1 Servo program composition
- 115 5.1.2 Servo program area
- 116 5.2 Servo Instructions
- 129 5.3 Positioning Data
- 135 5.4 Setting Method for Positioning Data
- 135 5.4.1 Setting method by specifying numerical values
- 136 5.4.2 Indirect setting method by devices
- 140 6. POSITIONING CONTROL
- 140 6.1 Basics of Positioning Control
- 140 6.1.1 Positioning speed
- 141 6.1.2 Positioning speed at the interpolation control
- 146 6.1.3 Control units for 1 axis positioning control
- 146 6.1.4 Control units for interpolation control
- 148 6.1.5 Control in the control unit "degree"
- 150 6.1.6 Stop processing and restarting after stop
- 156 6.1.7 Acceleration/deceleration processing
- 158 6.2 1 Axis Linear Positioning Control
- 161 6.3 2 Axes Linear Interpolation Control
- 166 6.4 3 Axes Linear Interpolation Control
- 172 6.5 4 Axes Linear Interpolation Control
- 177 6.6 Auxiliary Point-Specified Circular Interpolation Control
- 182 6.7 Radius-Specified Circular Interpolation Control
- 188 6.8 Central Point-Specified Circular Interpolation Control
- 194 6.9 Helical Interpolation Control
- 195 6.9.1 Circular interpolation specified method by helical interpolation
- 216 6.10 1 Axis Fixed-Pitch Feed Control
- 220 6.11 Fixed-Pitch Feed Control Using 2 Axes Linear Interpolation
- 224 6.12 Fixed-Pitch Feed Control Using 3 Axes Linear Interpolation
- 228 6.13 Speed Control ( I )
- 232 6.14 Speed Control ( II )
- 235 6.15 Speed/Position Switching Control
- 235 6.15.1 Speed/position switching control start
- 242 6.15.2 Re-starting after stop during control
- 247 6.16 Speed-Switching Control
- 247 6.16.1 Speed-switching control start, speed-switching points and end specification
- 253 6.16.2 Specification of speed-switching points using repetition instructions
- 259 6.17 Constant-Speed Control
- 263 6.17.1 Specification of pass points by repetition instructions
- 268 6.17.2 Speed-switching by instruction execution
- 273 6.17.3 1 axis constant-speed control
- 277 6.17.4 2 to 4 axes constant-speed control
- 284 6.17.5 Constant speed control for helical interpolation
- 287 6.17.6 Pass point skip function
- 289 6.17.7 FIN signal wait function
- 299 6.18 Position Follow-Up Control
- 306 6.19 Speed control with fixed position stop
- 311 6.20 Simultaneous Start
- 314 6.21 JOG Operation
- 314 6.21.1 JOG operation data
- 315 6.21.2 Individual start
- 320 6.21.3 Simultaneous start
- 323 6.22 Manual Pulse Generator Operation
- 330 6.23 Home Position Return
- 331 6.23.1 Home position return data
- 339 6.23.2 Home position return by the proximity dog type 1
- 342 6.23.3 Home position return by the proximity dog type 2
- 344 6.23.4 Home position return by the count type 1
- 346 6.23.5 Home position return by the count type 2
- 347 6.23.6 Home position return by the count type 3
- 349 6.23.7 Home position return by the data set type 1
- 350 6.23.8 Home position return by the data set type 2
- 351 6.23.9 Home position return by the dog cradle type
- 356 6.23.10 Home position return by the stopper type 1
- 358 6.23.11 Home position return by the stopper type 2
- 360 6.23.12 Home position return by the limit switch combined type
- 362 6.23.13 Home position return retry function
- 366 6.23.14 Home position shift function
- 370 6.23.15 Condition selection of home position set
- 371 6.23.16 Servo program for home position return
- 373 6.24 High-Speed Oscillation
- 376 7. AUXILIARY AND APPLIED FUNCTIONS
- 376 7.1 M-code Output Function
- 379 7.2 Backlash Compensation Function
- 381 7.3 Torque Limit Function
- 383 7.4 Skip Function in which Disregards Stop Command
- 385 7.5 Cancel of the Servo Program
- 386 7.5.1 Cancel/start
- 388 APPENDICES
- 388 APPENDIX 1 Error Codes Stored Using The Motion CPU
- 390 APPENDIX 1.1 Servo program setting errors (Stored in SD517)
- 395 APPENDIX 1.2 Minor errors
- 405 APPENDIX 1.3 Major errors
- 409 APPENDIX 1.4 Servo errors
- 428 APPENDIX 2 Example Programs
- 428 APPENDIX 2.1 Reading M-code
- 429 APPENDIX 2.2 Reading error code
- 431 APPENDIX 3 Setting Range for Indirect Setting Devices
- 433 APPENDIX 4 Processing Times of the Motion CPU
- 434 APPENDIX 5 Device List
- 445 WARRANTY