- Home
- Home security & automation
- Security access control systems
- Mitsubishi
- MOTION CONTROLLERS Q172DCPU
- Instruction manual
advertisement
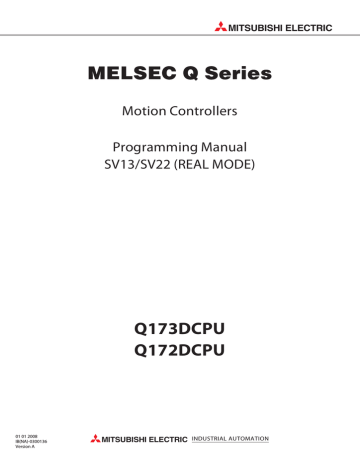
6 POSITIONING CONTROL
6.21.3 Simultaneous start
[Control details]
Simultaneous start JOG operation for specified multiple axes.
(1) JOG operation continues at the JOG speed setting register value for each axis while the JOG operation simultaneous start command (M2048) turns on, and a deceleration stop is made by the M2048 OFF.
Control of acceleration/deceleration is based on the data set in the JOG operation data.
V Acceleration based on
JOG operation data JOG operation speed
Deceleration stop based on JOG operation data t
JOG operation based on D710 to D713 data
D710 to D713
ON
M2048 OFF
(2) JOG operation axis is set in the JOG operation simultaneous start axis setting register (D710 to D713). b15 b14 b13 b12 b11 b10 b9 b8 b7 b6 b5 b4 b3 b2 b1 b0
D710 Axis 16 Axis 15 Axis 14 Axis 13 Axis 12 Axis 11 Axis 10 Axis 9 Axis 8 Axis 7 Axis 6 Axis 5 Axis 4 Axis 3 Axis 2 Axis 1
D711 Axis 32 Axis 31 Axis 30 Axis 29 Axis 28 Axis 27 Axis 26 Axis 25 Axis 24 Axis 23 Axis 22 Axis 21 Axis 20 Axis 19 Axis 18 Axis 17
Forward rotation
JOG
D712
D713
Axis 16 Axis 15 Axis 14 Axis 13 Axis 12 Axis 11 Axis 10 Axis 9 Axis 8 Axis 7 Axis 6 Axis 5 Axis 4 Axis 3 Axis 2 Axis 1
Axis 32 Axis 31 Axis 30 Axis 29 Axis 28 Axis 27 Axis 26 Axis 25 Axis 24 Axis 23 Axis 22 Axis 21 Axis 20 Axis 19 Axis 18 Axis 17
Reverse rotation
JOG
(Note-1) Set the JOG operation simultaneous
start axis with 1/0.
1: Simultaneous start is executed
0: Simultaneous start is not executed
(Note-2) The range of axis No.1 to 8 is valid in
the Q172DCPU.
6 - 181
6 POSITIONING CONTROL
(3) The setting range for JOG speed setting registers are shown below.
No.
(Note)
JOG operation JOG speed setting register
Forward JOG Reverse JOG Most significant Least significant
Setting range mm inch degree PLS
Setting range
Units
Setting range
Units
Setting range
Units
Setting range
Units
1 M3202 M3203 D641 D640
2 M3222 M3223 D643 D642
3 M3242 M3243 D645 D644
4 M3262 M3263 D647 D646
5 M3282 M3283 D649 D648
6 M3302 M3303 D651 D650
7 M3322 M3323 D653 D652
8 M3342 M3343 D655 D654
9 M3362 M3363 D657 D656
10 M3382 M3383 D659 D658
11 M3402 M3403 D661
12 M3422 M3423 D663
D660
D662
13 M3442 M3443 D665
14 M3462 M3463 D667
15 M3482 M3483 D669
16 M3502 M3503 D671
17 M3522 M3523 D673
D664
D666
D668
D670 1 to
D672 600000000
18 M3542 M3543 D675
19 M3562 M3563 D677
20 M3582 M3583 D679
21 M3602 M3603 D681
22 M3622 M3623 D683
23 M3642 M3643 D685
24 M3662 M3663 D687
25 M3682 M3683 D689
26 M3702 M3703 D691
27 M3722 M3723 D693
28 M3742 M3743 D695
29 M3762 M3763 D697
30 M3782 M3783 D699
31 M3802 M3803 D701
32 M3822 M3823 D703
D674
D676
D678
D680
D682
D684
D686
D688
D690
D692
D694
D696
D698
D700
D702
10 mm
-2
/min
1 to
600000000
10 -3 inch
/min
10 -3
1 to
2147483647 degree
/min
1 to
2147483647
(Note-1)
PLS/s
(Note-1): When the "speed control 10 multiplier setting for degree axis" is set to "valid" in the fixed parameter, the unit is " 10 -2 [degree/min] ".
(Note-2): The range of axis No.1 to 8 is valid in the Q172DCPU.
6 - 182
6 POSITIONING CONTROL
[Program]
Program for simultaneous start of JOG operations are shown as the following conditions.
(1) System configuration
JOG operation for Axis 1 and Axis 2.
Motion CPU control module
Q61P Q03UD
CPU
Q172D
CPU
QX41 QY41 Q172D
LX
JOG operation command (PX000)
AMP
Axis
1 M
AMP
Axis
2 M
AMP
Axis
3 M
AMP
Axis
4 M
(2) JOG operation conditions
(a) JOG operation conditions are shown below.
Item
Axis No.
JOG operation speed
JOG operation conditions
Axis 1
150000
Axis 2
150000
(b) JOG operation command ...... During PX000 ON
(3) Motion SFC program
Motion SFC program for which executes the simultaneous start of JOG operation is shown below.
Simultaneous start
Simultaneous start
[F10]
SET M2042
JOG operation is executed with the speed of
150000[mm/min] as the following, when the
2 axes simultaneous start switch (PX000) turns on.
Turn on all axes servo ON command.
[G10]
M2415*M2435 Wait until Axis 1 servo ready and Axis 2 servo ready turn on.
P0
[G20]
PX000
[F20] D710=H0002
D712=H0001
D640L=K150000
D642L=K150000
SET M2048
JOG operation is executed at the
JOG operation simultaneous start command ON
[F30]
RST M2048
P0
(Note): Example of the above Motion SFC program is started using the automatic start or PLC program.
6 - 183
6 POSITIONING CONTROL
6.22 Manual Pulse Generator Operation
Positioning control based on the number of pulses inputted from the manual pulse generator is executed.
Simultaneous operation for 1 to 3 axes is possible with one manual pulse generator, the number of connectable modules are shown below.
Number of connectable to the manual pulse generator
3
POINT
• When two or more Q173DPXs are installed, connect the manual pulse generator to first (It counts from 0 slot of the main base) Q173DPX.
(When the manual pulse generator is used, only first Q173DPX is valid.)
[Control details]
(1) Positioning of the axis set in the manual pulse generator axis setting register based on the pulse input from the manual pulse generator.
Manual pulse generator operation is only valid while the manual pulse generator enable flag turn ON.
Manual pulse generator connecting position
Manual pulse generator axis No. setting register
Manual pulse generator enable flag
(2) The travel value and output speed for positioning control based on the pulse input from manual pulse generator are shown below.
(a) Travel value
The travel value based on the pulse input from a manual pulse generator is calculated using the following formula.
[Travel value] = [Travel value per pulse] [Number of input pulses] [Manual pulse generator 1- pulse input magnification setting]
The travel value per pulse for manual pulse generator operation is shown below.
If units is [mm], the command travel value for input of one pulse is:
(0.1[µm]) (1[PLS]) (Manual pulse generator 1- pulse input magnification setting)
6 - 184
6 POSITIONING CONTROL
(b) Output speed
The output speed is the positioning speed corresponding to the number of pulses input from a manual pulse generator in unit time.
[Output speed] = [Number of input pulses per 1[ms]] [Manual pulse generator 1- pulse input magnification setting]
(3) Setting of the axis operated by the manual pulse generator
The axis operated by the manual pulse generator is set in the manual pulse generator axis setting register (D714 to D719).
The bit corresponding to the axis controlled (1 to 32) is set.
(4) Manual pulse generator 1- pulse input magnification setting
Make magnification setting for 1- pulse input from the manual pulse generator for each axis.
1- pulse input magnification setting register Applicable axis No. (Note-1) Setting
(Note-1): The range of axis No.1 to 8 is valid in the Q172DCPU.
(Note): The manual pulse generator does not have the speed limit value, so they set the magnification setting within the related speed of servomotor.
6 - 185
6 POSITIONING CONTROL
(5) The setting manual pulse generator 1- pulse input magnification checks the "1- pulse input magnification setting registers of the manual pulse generator" of the applicable axis at leading edge of manual pulse generator enable flag.
If the value is outside of range, the manual pulse generator axis setting error register (SD513 to SD515) and manual pulse generator axis setting error flag
(SM513) are set and a value of "1" is used for the magnification.
(6) Manual pulse generator smoothing magnification setting
A magnification to smooth leading edge/trailing edge of manual pulse generator operation is set.
Manual pulse generator smoothing magnification setting register
Manual pulse generator 1 (P1): D752
Manual pulse generator 2 (P2): D753
Manual pulse generator 3 (P3): D754
Setting range
0 to 59
(a) Operation
Manual pulse generator input
OFF
ON
Manual pulse generator 1 enable flag (M2051)
V
V1 t t t t
Output speed (V1) = [Number of input pulses/ms] [Manual pulse generator 1- pulse input magnification setting]
Travel value (L) = [Travel value per pulse] [Number of input pulses]
[Manual pulse generator 1-pulse input magnification setting]
(b) When the smoothing magnification is set, the smoothing time constant is as following formula.
Smoothing time constant (t) = (Smoothing magnification + 1) 56.8 [ms]
REMARK
The smoothing time constant is within the range of 56.8 to 3408 [ms].
6 - 186
6 POSITIONING CONTROL
(7) Errors details at the data setting for manual pulse generator operation are shown below.
Error details
Axis set to manual pulse generator operation is specified.
Axis setting is 4 axes or more
All of bit is "0" for the effective axis No. of manual pulse generator axis No. setting register.
Error processing
• Duplicated specified axis is ignored.
• First setting manual pulse generator operation is executed.
• Manual pulse generator operation is executed according to valid for 3 axes from the lowest manual pulse generator axis setting register.
• Manual pulse generator operation is not executed.
[Cautions]
(1) The start accept flag turns on for axis during manual pulse generator operation.
Positioning control or home position return cannot be started using the Motion
CPU or MT Developer.
Turn off the manual pulse generator enable flag after the manual pulse generator operation end.
(2) The torque limit value is fixed at 300[%] during manual pulse generator operation.
(3) If the manual pulse generator enable flag turns on for the starting axis by positioning control or JOG operation, an error [214] is set to the applicable axis and manual pulse generator input is not enabled. After the axis has been stopped, the leading edge of manual pulse generator enable flag becomes valid, the start accept flag turns on by the manual pulse generator input enabled status, and input from the manual pulse generator is input.
V Positioning control
Manual pulse generator operation t
ON
Manual pulse generator 1 enable flag (M2051)
OFF
Disable
Manual pulse generator enable status
Start accept flag
OFF
ON
Enable
Input from manual pulse generator is ignored.
(4) If the manual pulse generator enable flag of another manual pulse generator No. turns on for axis during manual pulse generator operation, an error [214] is set to the applicable axis and the input of that manual pulse generator is not enabled.
Turn the manual pulse generator enable flag on again after stopping the manual pulse generator operation which had become input enable previously.
6 - 187
6 POSITIONING CONTROL
(5) If the manual pulse generator enable flag turns on again for axis during smoothing deceleration after manual pulse generator enable flag turns off, an error [214] is set and manual pulse generator input is not enabled. Turn the manual pulse generator enable flag on after smoothing deceleration stop (after the start accept flag OFF).
(6) If another axis is set and the same manual pulse generator enable flag turns on again during smoothing deceleration after manual pulse generator enable flag turns off, the manual pulse generator input is not enabled.
At this time, the manual pulse generator axis setting error bit of the manual pulse generator axis setting error storage register (SD513 to SD515) turns on, and the manual pulse generator axis setting error flag (SM513) turns on.
Include the start accept flag OFF for specified axis in interlocks as the conditions which turn on the manual pulse generator enable flag.
[Procedure for manual pulse generator operation]
Procedure for manual pulse generator operation is shown below.
Start
Set the manual pulse generator
1- pulse input magnification
Set the manual pulse generator operation axis
Using the Motion SFC program
Turn the manual pulse generator enable flag ON
Execute the positioning by manual pulse generator
Turn the manual pulse generator enable flag OFF
. . . . . . . Using the Motion SFC program
End
6 - 188
6 POSITIONING CONTROL
[Program]
Program executes manual pulse generator operation is shown as the following conditions.
(1) System configuration
Manual pulse generator operation of Axis 1 and Axis 2.
Motion CPU control module
Q61P Q03UD
CPU
Q172D
CPU
QX41 QY41 Q172D
PX
Manual pulse generator P1
Manual pulse generator P2
Manual pulse generator enable flag
(M2051 : P1, M2052 : P2)
AMP
Axis
1
M
AMP
Axis
2
M
AMP
Axis
3
M
AMP
Axis
4 M
(2) Manual pulse generator operation conditions
(a) Manual pulse generator operation axis................Axis 1, Axis 2
(b) Manual pulse generator 1- pulse input magnification............ 100
(c) Manual pulse generator operation enable ...........M2051 (Axis 1)/
M2052 (Axis 2) ON
(d) Manual pulse generator operation end ................M2051 (Axis 1)/
M2052 (Axis 2) OFF
(3) Motion SFC program
Motion SFC program for manual pulse generator operation is shown below.
Manual pulse generator
Manual pulse generator
[F10]
SET M2042
[G10]
PX000*M2415*M2435
[F20]
D720=100
D721=100
D714L=H00000001
D716L=H00000002
SET M2051
SET M2052
Wait until PX000, Axis 1 servo ready and
Axis 2 servo ready turn on.
Manual pulse generator 1- pulse input magnification for Axis 1, Axis 2.
Control Axis 1 by P1.
Control Axis 2 by P2.
Manual pulse generator enable flag ON for Axis 1, Axis 2.
[G20]
!PX000
Wait until PX000 turn off after manual pulse generator operation end.
[F30]
RST M2051
RST M2052
Manual pulse generator enable flag OFF for Axis 1, Axis 2.
(Note): Turn the manual pulse generator enable
flag off for P1, P2, so that the operation
may not continued for safety.
END
(Note): Example of the above Motion SFC program is started using the automatic start or PLC program.
6 - 189
6 POSITIONING CONTROL
MEMO
6 - 190
6 POSITIONING CONTROL
6.23 Home Position Return
(1) Use the home position return at the power supply ON and other times where confirmation of axis is at the machine home position is required.
(2) The following six methods for home position return are shown below.
• Proximity dog type
• Count type
• Data set type
• Dog cradle type
• Stopper type
• Limit switch combined type
(3) The home position return data must be set for each axis to execute the home position return.
(4) Select the optimal home position return method for the system configuration and applications with reference to the following.
Home position return methods
Proximity dog type 1
Contents
• Home position is zero point of servomotor.
• When the proximity dog is ON, it cannot be started.
Proximity dog type
Count type
(Note)
Proximity dog type 2
Count type 1
• Home position is zero point of servomotor.
• When the proximity dog is ON, it can be started.
• This method is valid when the stroke range is short and "proximity dog type 1" cannot be used.
• Home position is zero point of servomotor. • It is used in the system which can surely pass a zero point from the home position return start to point of travel distance set as "travel value after proximity dog ON".
• Zero point is not used in the home position
Applications
• It is used in the system which can surely pass a zero point from the home position return start to proximity dog ON OFF.
• This method is used when the proximity dog is
Count type 2
Data set type
Count type 3
Data set type 1
Data set type 2 narrow.
• Home position is zero point of servomotor. • This method is valid when the stroke range is short and "count type 1" cannot be used.
• Home position is command position of
Motion CPU.
• Home position is real position of servomotor.
• External input signals such as dog signal are not set in the absolute position system.
• This method is valid for the data set independent of a deviation counter value.
• External input signals such as dog signal are not set in the absolute position system.
Dog cradle type
• Home position is zero point of servomotor immediately after the proximity dog signal
• It is easy to set the position of proximity dog, because the proximity dog is set near the
Stopper type
Stopper type 1
Stopper type 2
Limit switch combined type
• Home position is position which stopped the machine by the stopper.
• Proximity dog is used.
• Home position is position which stopped the machine by the stopper.
• Proximity dog is not used.
• Home position is zero point of servomotor.
• Proximity dog is not used.
• External limit switch is surely used.
• This method is valid to improve home position accuracy in order to make the home position for the position which stopped the machine by the stopper.
• It is used in the system that the proximity dog signal cannot be used and only external limit switch can be used.
(Note): If the proximity dog signal of servo amplifier is used, the count type home position return cannot be execute.
6 - 191
advertisement
* Your assessment is very important for improving the workof artificial intelligence, which forms the content of this project
Related manuals
advertisement
Table of contents
- 2 SAFETY PRECAUTIONS
- 12 REVISIONS
- 13 CONTENTS
- 16 About Manuals
- 18 1. OVERVIEW
- 18 1.1 Overview
- 20 1.2 Features
- 20 1.2.1 Performance Specifications
- 22 2. POSITIONING CONTROL BY THE MOTION CPU
- 22 2.1 Positioning Control by the Motion CPU
- 36 3. POSITIONING DEDICATED SIGNALS
- 38 3.1 Internal Relays
- 45 3.1.1 Axis statuses
- 55 3.1.2 Axis command signals
- 62 3.1.3 Common devices
- 75 3.2 Data Registers
- 79 3.2.1 Axis monitor devices
- 85 3.2.2 Control change registers
- 86 3.2.3 Common devices
- 89 3.3 Motion Registers (#)
- 91 3.4 Special Relays (SM)
- 94 3.5 Special Registers (SD)
- 100 4. PARAMETERS FOR POSITIONING CONTROL
- 100 4.1 System Settings
- 101 4.2 Fixed Parameters
- 102 4.2.1 Number of pulses/travel value per rotation
- 104 4.2.2 Backlash compensation amount
- 104 4.2.3 Upper/lower stroke limit value
- 106 4.2.4 Command in-position range
- 107 4.2.5 Speed control 10 multiplier setting for degree axis
- 110 4.3 Parameter Block
- 112 4.3.1 Relationships between the speed limit value, acceleration time, deceleration time and rapid stop deceleration time
- 112 4.3.2 S-curve ratio
- 113 4.3.3 Allowable error range for circular interpolation
- 114 5. SERVO PROGRAMS FOR POSITIONING CONTROL
- 114 5.1 Servo Program Composition Area
- 114 5.1.1 Servo program composition
- 115 5.1.2 Servo program area
- 116 5.2 Servo Instructions
- 129 5.3 Positioning Data
- 135 5.4 Setting Method for Positioning Data
- 135 5.4.1 Setting method by specifying numerical values
- 136 5.4.2 Indirect setting method by devices
- 140 6. POSITIONING CONTROL
- 140 6.1 Basics of Positioning Control
- 140 6.1.1 Positioning speed
- 141 6.1.2 Positioning speed at the interpolation control
- 146 6.1.3 Control units for 1 axis positioning control
- 146 6.1.4 Control units for interpolation control
- 148 6.1.5 Control in the control unit "degree"
- 150 6.1.6 Stop processing and restarting after stop
- 156 6.1.7 Acceleration/deceleration processing
- 158 6.2 1 Axis Linear Positioning Control
- 161 6.3 2 Axes Linear Interpolation Control
- 166 6.4 3 Axes Linear Interpolation Control
- 172 6.5 4 Axes Linear Interpolation Control
- 177 6.6 Auxiliary Point-Specified Circular Interpolation Control
- 182 6.7 Radius-Specified Circular Interpolation Control
- 188 6.8 Central Point-Specified Circular Interpolation Control
- 194 6.9 Helical Interpolation Control
- 195 6.9.1 Circular interpolation specified method by helical interpolation
- 216 6.10 1 Axis Fixed-Pitch Feed Control
- 220 6.11 Fixed-Pitch Feed Control Using 2 Axes Linear Interpolation
- 224 6.12 Fixed-Pitch Feed Control Using 3 Axes Linear Interpolation
- 228 6.13 Speed Control ( I )
- 232 6.14 Speed Control ( II )
- 235 6.15 Speed/Position Switching Control
- 235 6.15.1 Speed/position switching control start
- 242 6.15.2 Re-starting after stop during control
- 247 6.16 Speed-Switching Control
- 247 6.16.1 Speed-switching control start, speed-switching points and end specification
- 253 6.16.2 Specification of speed-switching points using repetition instructions
- 259 6.17 Constant-Speed Control
- 263 6.17.1 Specification of pass points by repetition instructions
- 268 6.17.2 Speed-switching by instruction execution
- 273 6.17.3 1 axis constant-speed control
- 277 6.17.4 2 to 4 axes constant-speed control
- 284 6.17.5 Constant speed control for helical interpolation
- 287 6.17.6 Pass point skip function
- 289 6.17.7 FIN signal wait function
- 299 6.18 Position Follow-Up Control
- 306 6.19 Speed control with fixed position stop
- 311 6.20 Simultaneous Start
- 314 6.21 JOG Operation
- 314 6.21.1 JOG operation data
- 315 6.21.2 Individual start
- 320 6.21.3 Simultaneous start
- 323 6.22 Manual Pulse Generator Operation
- 330 6.23 Home Position Return
- 331 6.23.1 Home position return data
- 339 6.23.2 Home position return by the proximity dog type 1
- 342 6.23.3 Home position return by the proximity dog type 2
- 344 6.23.4 Home position return by the count type 1
- 346 6.23.5 Home position return by the count type 2
- 347 6.23.6 Home position return by the count type 3
- 349 6.23.7 Home position return by the data set type 1
- 350 6.23.8 Home position return by the data set type 2
- 351 6.23.9 Home position return by the dog cradle type
- 356 6.23.10 Home position return by the stopper type 1
- 358 6.23.11 Home position return by the stopper type 2
- 360 6.23.12 Home position return by the limit switch combined type
- 362 6.23.13 Home position return retry function
- 366 6.23.14 Home position shift function
- 370 6.23.15 Condition selection of home position set
- 371 6.23.16 Servo program for home position return
- 373 6.24 High-Speed Oscillation
- 376 7. AUXILIARY AND APPLIED FUNCTIONS
- 376 7.1 M-code Output Function
- 379 7.2 Backlash Compensation Function
- 381 7.3 Torque Limit Function
- 383 7.4 Skip Function in which Disregards Stop Command
- 385 7.5 Cancel of the Servo Program
- 386 7.5.1 Cancel/start
- 388 APPENDICES
- 388 APPENDIX 1 Error Codes Stored Using The Motion CPU
- 390 APPENDIX 1.1 Servo program setting errors (Stored in SD517)
- 395 APPENDIX 1.2 Minor errors
- 405 APPENDIX 1.3 Major errors
- 409 APPENDIX 1.4 Servo errors
- 428 APPENDIX 2 Example Programs
- 428 APPENDIX 2.1 Reading M-code
- 429 APPENDIX 2.2 Reading error code
- 431 APPENDIX 3 Setting Range for Indirect Setting Devices
- 433 APPENDIX 4 Processing Times of the Motion CPU
- 434 APPENDIX 5 Device List
- 445 WARRANTY