- Home
- Home security & automation
- Security access control systems
- Mitsubishi
- MOTION CONTROLLERS Q172DCPU
- Instruction manual
advertisement
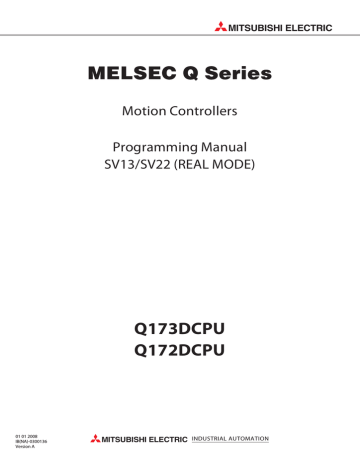
3 POSITIONING DEDICATED SIGNALS
3.1.2 Axis command signals
(1) Stop command (M3200+20n) ............................... Command signal
(a) This command is a signal which stop a starting axis from an external source and becomes effective at leading edge of signal. (An axis for which the stop command is turning on cannot be started.)
ON
Stop command
(M3200+20n)
OFF
V
Stop command for specified axis
Control when stop command turns off
Setting speed
Stop t
Deceleration stop processing
(b) The details of stop processing when the stop command turns on are shown below. (Refer to Section 6.13 or 6.14 for details of the speed control.)
Processing at the turning stop command on
Control details during execution
During control During deceleration stop processing
Positioning control
Speed control ( , )
JOG operation
The axis decelerates to a stop in the deceleration time set in the parameter block or servo program.
The deceleration stop processing is continued.
Speed control with fixed position stop
Manual pulse generator operation
An immediate stop is executed without deceleration processing.
Home position return
(1) The axis decelerates to a stop in the deceleration time set in the parameter block.
(2) A "stop error during home position return" occurs and the error code [202] is stored in the minor error storage register for each axis.
(c) The stop command in a dwell time is invalid. (After a dwell time, the start accept flag (M2001+n) turns OFF, and the positioning complete signal
(M2401+20n) turns ON.)
POINT
If it is made to stop by turning on the stop command (M3200+20n) during a home position return, execute the home position return again.
If the stop command is turned on after the proximity dog ON in the proximity dog type, execute the home position return after move to before the proximity dog ON by the JOG operation or positioning.
3 - 20
3 POSITIONING DEDICATED SIGNALS
(2) Rapid stop command (M3201+20n) ..................... Command signal
(a) This command stops a starting axis rapidly from an external source and becomes effective at leading edge of signal. (An axis for which the rapid stop command is turning on cannot be started.)
ON
Rapid stop command
(M3201+20n)
OFF
V
Rapid stop command for specified axis
Control when rapid stop command turns off
Setting speed
Stop t
Rapid stop processing
(b) The details of stop processing when the rapid stop command turns on are shown below.
Processing at the turning rapid stop command on
Control details during execution
During control During deceleration stop processing
Position control
Speed control ( , )
JOG operation
Speed control with fixed position stop
The axis decelerates to a rapid stop deceleration time set in the parameter block or servo program.
Deceleration processing is stopped and rapid stop processing is executed.
Manual pulse generator operation
An immediate stop is executed without deceleration processing.
(1) The axis decelerates to a stop in the rapid stop deceleration time set in the parameter block.
Home position return
(2) A "stop error during home position return" error occurs and the error code [203] is stored in the minor error storage register for each axis.
(c) The rapid stop command in a dwell time is invalid. (After a dwell time, the start accept flag (M2001+n) turns OFF, and the positioning complete signal
(M2401+20n) turns ON.)
POINT
If it is made to stop rapidly by turning on the rapid stop command (M3201+20n) during a home position return, execute the home position return again.
If the rapid stop command turned on after the proximity dog ON in the proximity dog type, execute the home position return after move to before the proximity dog ON by the JOG operation or positioning.
3 - 21
3 POSITIONING DEDICATED SIGNALS
(3) Forward rotation JOG start command (M3202+20n)/Reverse rotation JOG start command (M3203+20n) ......... Command signal
(a) JOG operation to the address increase direction is executed while forward rotation JOG start command (M3202+20n) is turning on.
When M3202+20n is turned off, a deceleration stop is executed in the deceleration time set in the parameter block.
(b) JOG operation to the address decrease direction is executed while reverse rotation JOG start command (M3203+20n) is turning on.
When M3203+20n is turned off, a deceleration stop is executed in the deceleration time set in the parameter block.
POINT
Take an interlock so that the forward rotation JOG start command (M3202+20n) and reverse rotation JOG start command (M3203+20n) may not turn on simultaneously.
(4) Complete signal OFF command (M3204+20n)
......................... Command signal
(a) This command is used to turn off the positioning start complete signal
(M2400+20n) and positioning complete signal (M2401+20n).
Dwell time Dwell time t
ON
Positioning start complete signal
(M2400+20n)
Positioning complete signal (M2401+20n)
Complete signal OFF command (M3204+20n)
OFF
OFF
OFF
ON
ON
POINT
Do not turn the complete signal OFF command on with a PLS instruction.
If it is turned on with a PLS instruction, it cannot be turned off the positioning start complete signal (M2400+20n) and the positioning complete signal (M2401+20n).
3 - 22
3 POSITIONING DEDICATED SIGNALS
(5) Speed/position switching enable command (M3205+20n)
......... Command signal
(a) This command is used to make the CHANGE signal (speed/position switching signal) effective from an external source.
• ON .......... Control switches from speed control to position control when the CHANGE signal turned on.
• OFF .......... Control does not switch from speed to position control even if the CHANGE signal turns on.
Control does not switch from speed control to position control because M3205+20n turns off
CHANGE CHANGE Control switches from speed control to position control because
M3205+20n turns on t
ON
Speed/position switching enable command (M3205+20n)
OFF
CHANGE signal from external source
OFF
(6) Error reset command (M3207+20n) ..................... Command signal
This command is used to clear the minor/major error code storage register of an axis for which the error detection signal has turn on (M2407+20n: ON), and reset the error detection signal (M2407+20n).
ON
Error detection signal
(M2407+20n)
OFF
ON
Error reset command
(M3207+20n)
Minor error code storage register (D6+20n)
Major error code storage register (D7+20n)
OFF
**
**
00
00
** : Error code
(7) Servo error reset command (M3208+20n) ........... Command signal
This command is used to clear the servo error code storage register of an axis for which the servo error detection signal has turn on (M2408+20n: ON), and reset the servo error detection signal (M2408+20n).
ON
Servo error detection signal
(M2408+20n)
OFF
ON
Servo error reset command
(M3208+20n)
Servo error code storage register
OFF
** 00
** : Error code
3 - 23
3 POSITIONING DEDICATED SIGNALS
REMARK
Refer to APPENDIX 1 for details on the minor error code, major error code and servo error code storage registers.
(8) External stop input disable at start command (M3209+20n)
....................... Command signal
This signal is used to set the external stop signal input valid or invalid.
• ON .......... External stop input is set as invalid, and even axes which stop input is turning on can be started.
• OFF .......... External stop input is set as valid, and axes which stop input is turning on cannot be started.
POINT
When it stops an axis with the external stop input after it starts by turning on the external stop input disable at start command (M3209+20n), switch the external stop input from OFF ON (if the external stop input is turning on at the starting, switch it from ON OFF ON).
(9) Feed current value update request command (M3212+20n)
....................... Command signal
This signal is used to set whether the feed current value will be cleared or not at the starting in speed/position switching control.
• ON .......... The feed current value is updated from the starting.
The feed current value is not cleared at the starting.
• OFF .......... The feed current value is updated from the starting.
The feed current value is cleared at the starting.
POINT
When it starts by turning on the feed current value update request command
(M3212+20n), keep M3212+20n on until completion of the positioning control.
If M3212+20n is turned off on the way, the feed current value may not be reliable.
(10) Servo OFF command (M3215+20n) .................. Command signal
This command is used to execute the servo OFF state (free run state).
• M3215+20n: OFF ..... Servo ON
• M3215+20n: ON ....... Servo OFF (free run state)
This command becomes invalid during positioning, and should therefore be executed after completion of positioning.
CAUTION
Turn the power supply of the servo amplifier side off before touching a servomotor, such as machine adjustment.
3 - 24
3 POSITIONING DEDICATED SIGNALS
(11) Gain changing command (M3216+20n) ............. Command signal
This signal is used to change the gain of servo amplifier in the Motion controller by the gain changing command ON/OFF.
• ON .......... Gain changing command ON
• OFF .......... Gain changing command OFF
Refer to the "MR-J3- B Servo Amplifier Instruction Manual" for details of gain changing function.
Instruction Manual list is shown below.
Servo amplifier type Instruction manual name
MR-J3- B MR-J3- B Servo Amplifier Instruction Manual (SH-030051)
(12) Control loop changing command (M3218+20n)
....................... Command signal
When using the fully closed loop control servo amplifier, this signal is used to change the fully closed loop control/semi closed loop control of servo amplifier in the Motion controller by the control loop changing command
ON/OFF.
• ON .......... During fully closed loop control
• OFF .......... During semi closed loop control
Fully closed loop control change
Semi closed loop control change
ON
Control loop changing command
(M3218+20n)
OFF
ON
Control loop monitor status
(M2272+n)
OFF
Refer to the "Fully closed loop control MR-J3- B-RJ006 Servo Amplifier
Instruction Manual" for details of control loop changing.
Instruction Manual list is shown below.
Servo amplifier type
MR-J3- B-RJ006
Instruction manual name
Fully closed loop control MR-J3- B-RJ006
Servo Amplifier Instruction Manual (SH-030056)
POINTS
(1) When the servo amplifier is not started (LED: "AA", "Ab", "AC", "Ad" or "AE"), if the control loop changing command is turned ON/OFF, the command becomes invalid.
(2) When the followings are operated during the fully closed loop, it returns to the semi closed loop control.
(a) Power supply OFF or reset of the Multiple CPU system
(b) Wire breakage of the SSCNET cable between the servo amplifier and
Motion controller
(c) Control circuit power supply OFF of the servo amplifier
3 - 25
3 POSITIONING DEDICATED SIGNALS
(13) FIN signal (M3219+20n) .................................... Command signal
When a M-code is set in a servo program, transit to the next block does not execute until the FIN signal changes as follows: OFF ON OFF.
Positioning to the next block begins after the FIN signal changes as above.
It is valid, only when the FIN acceleration/deceleration is set and FIN signal wait function is selected.
<K 0>
Point
1
2
3
4
CPSTART2
Axis
Axis
Speed
1
2
FIN acceleration/
deceleration
ABS-2
Axis
Axis
M-code
1,
2,
ABS-2
Axis
Axis
M-code
ABS-2
Axis
Axis
M-code
ABS-2
Axis
Axis
CPEND
1,
2,
1,
2,
1,
2,
Point 1 WAIT 2
M-code 10 11
10000
100
M-code outputting signal
(M2419+20n)
FIN signal
(M3219+20n)
200000
200000
10
300000
250000
11
350000
300000
12
400000
400000
Timing Chart for Operation Description
1. When the positioning of point 1 starts, M-code 10 is output and the M-code outputting signal turns on.
2. FIN signal turns on after performing required processing in the
Motion SFC program. Transition to the next point does not execute until the FIN signal turns on.
3. When the FIN signal turns on, the M-code outputting signal turns off.
4. When the FIN signal turns off after the M-code outputting signal turns off, the positioning to the next point 2 starts.
POINTS
(1) The FIN signal and M-code outputting signal are both signal for the FIN signal wait function.
(2) The FIN signal and M-code outputting signal are valid only when FIN acceleration/deceleration is designated in the servo program.
Otherwise, the FIN signal wait function is disabled, and the M-code outputting signal does not turn on.
3 - 26
advertisement
* Your assessment is very important for improving the workof artificial intelligence, which forms the content of this project
Related manuals
advertisement
Table of contents
- 2 SAFETY PRECAUTIONS
- 12 REVISIONS
- 13 CONTENTS
- 16 About Manuals
- 18 1. OVERVIEW
- 18 1.1 Overview
- 20 1.2 Features
- 20 1.2.1 Performance Specifications
- 22 2. POSITIONING CONTROL BY THE MOTION CPU
- 22 2.1 Positioning Control by the Motion CPU
- 36 3. POSITIONING DEDICATED SIGNALS
- 38 3.1 Internal Relays
- 45 3.1.1 Axis statuses
- 55 3.1.2 Axis command signals
- 62 3.1.3 Common devices
- 75 3.2 Data Registers
- 79 3.2.1 Axis monitor devices
- 85 3.2.2 Control change registers
- 86 3.2.3 Common devices
- 89 3.3 Motion Registers (#)
- 91 3.4 Special Relays (SM)
- 94 3.5 Special Registers (SD)
- 100 4. PARAMETERS FOR POSITIONING CONTROL
- 100 4.1 System Settings
- 101 4.2 Fixed Parameters
- 102 4.2.1 Number of pulses/travel value per rotation
- 104 4.2.2 Backlash compensation amount
- 104 4.2.3 Upper/lower stroke limit value
- 106 4.2.4 Command in-position range
- 107 4.2.5 Speed control 10 multiplier setting for degree axis
- 110 4.3 Parameter Block
- 112 4.3.1 Relationships between the speed limit value, acceleration time, deceleration time and rapid stop deceleration time
- 112 4.3.2 S-curve ratio
- 113 4.3.3 Allowable error range for circular interpolation
- 114 5. SERVO PROGRAMS FOR POSITIONING CONTROL
- 114 5.1 Servo Program Composition Area
- 114 5.1.1 Servo program composition
- 115 5.1.2 Servo program area
- 116 5.2 Servo Instructions
- 129 5.3 Positioning Data
- 135 5.4 Setting Method for Positioning Data
- 135 5.4.1 Setting method by specifying numerical values
- 136 5.4.2 Indirect setting method by devices
- 140 6. POSITIONING CONTROL
- 140 6.1 Basics of Positioning Control
- 140 6.1.1 Positioning speed
- 141 6.1.2 Positioning speed at the interpolation control
- 146 6.1.3 Control units for 1 axis positioning control
- 146 6.1.4 Control units for interpolation control
- 148 6.1.5 Control in the control unit "degree"
- 150 6.1.6 Stop processing and restarting after stop
- 156 6.1.7 Acceleration/deceleration processing
- 158 6.2 1 Axis Linear Positioning Control
- 161 6.3 2 Axes Linear Interpolation Control
- 166 6.4 3 Axes Linear Interpolation Control
- 172 6.5 4 Axes Linear Interpolation Control
- 177 6.6 Auxiliary Point-Specified Circular Interpolation Control
- 182 6.7 Radius-Specified Circular Interpolation Control
- 188 6.8 Central Point-Specified Circular Interpolation Control
- 194 6.9 Helical Interpolation Control
- 195 6.9.1 Circular interpolation specified method by helical interpolation
- 216 6.10 1 Axis Fixed-Pitch Feed Control
- 220 6.11 Fixed-Pitch Feed Control Using 2 Axes Linear Interpolation
- 224 6.12 Fixed-Pitch Feed Control Using 3 Axes Linear Interpolation
- 228 6.13 Speed Control ( I )
- 232 6.14 Speed Control ( II )
- 235 6.15 Speed/Position Switching Control
- 235 6.15.1 Speed/position switching control start
- 242 6.15.2 Re-starting after stop during control
- 247 6.16 Speed-Switching Control
- 247 6.16.1 Speed-switching control start, speed-switching points and end specification
- 253 6.16.2 Specification of speed-switching points using repetition instructions
- 259 6.17 Constant-Speed Control
- 263 6.17.1 Specification of pass points by repetition instructions
- 268 6.17.2 Speed-switching by instruction execution
- 273 6.17.3 1 axis constant-speed control
- 277 6.17.4 2 to 4 axes constant-speed control
- 284 6.17.5 Constant speed control for helical interpolation
- 287 6.17.6 Pass point skip function
- 289 6.17.7 FIN signal wait function
- 299 6.18 Position Follow-Up Control
- 306 6.19 Speed control with fixed position stop
- 311 6.20 Simultaneous Start
- 314 6.21 JOG Operation
- 314 6.21.1 JOG operation data
- 315 6.21.2 Individual start
- 320 6.21.3 Simultaneous start
- 323 6.22 Manual Pulse Generator Operation
- 330 6.23 Home Position Return
- 331 6.23.1 Home position return data
- 339 6.23.2 Home position return by the proximity dog type 1
- 342 6.23.3 Home position return by the proximity dog type 2
- 344 6.23.4 Home position return by the count type 1
- 346 6.23.5 Home position return by the count type 2
- 347 6.23.6 Home position return by the count type 3
- 349 6.23.7 Home position return by the data set type 1
- 350 6.23.8 Home position return by the data set type 2
- 351 6.23.9 Home position return by the dog cradle type
- 356 6.23.10 Home position return by the stopper type 1
- 358 6.23.11 Home position return by the stopper type 2
- 360 6.23.12 Home position return by the limit switch combined type
- 362 6.23.13 Home position return retry function
- 366 6.23.14 Home position shift function
- 370 6.23.15 Condition selection of home position set
- 371 6.23.16 Servo program for home position return
- 373 6.24 High-Speed Oscillation
- 376 7. AUXILIARY AND APPLIED FUNCTIONS
- 376 7.1 M-code Output Function
- 379 7.2 Backlash Compensation Function
- 381 7.3 Torque Limit Function
- 383 7.4 Skip Function in which Disregards Stop Command
- 385 7.5 Cancel of the Servo Program
- 386 7.5.1 Cancel/start
- 388 APPENDICES
- 388 APPENDIX 1 Error Codes Stored Using The Motion CPU
- 390 APPENDIX 1.1 Servo program setting errors (Stored in SD517)
- 395 APPENDIX 1.2 Minor errors
- 405 APPENDIX 1.3 Major errors
- 409 APPENDIX 1.4 Servo errors
- 428 APPENDIX 2 Example Programs
- 428 APPENDIX 2.1 Reading M-code
- 429 APPENDIX 2.2 Reading error code
- 431 APPENDIX 3 Setting Range for Indirect Setting Devices
- 433 APPENDIX 4 Processing Times of the Motion CPU
- 434 APPENDIX 5 Device List
- 445 WARRANTY