- Home
- Home security & automation
- Security access control systems
- Mitsubishi
- MOTION CONTROLLERS Q172DCPU
- Instruction manual
advertisement
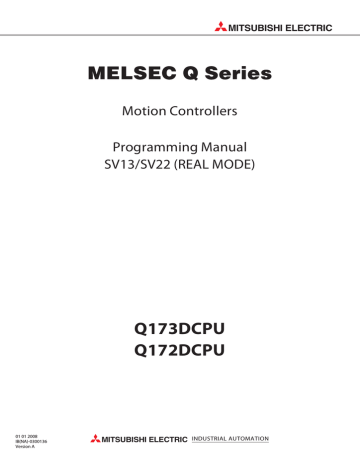
3 POSITIONING DEDICATED SIGNALS
3.2 Data Registers to to
D800
D0
Device No. to
D640 to
D704 to
D758
(1) Data register list
SV13 SV22
Application Device No.
D0
Application
Axis monitor device
(20 points 32 axes) to
Axis monitor device
(20 points 32 axes)
Real mode……each axis
Virtual mode….output module
D640
Control change register
(2 points 32 axes)
Control change register
(2 points 32 axes) to
D704
Common device (Command signal)
(54 points)
Common device (Command signal)
(54 points) to
D758
Unusable
(42 points)
Unusable
(42 points) to
D800 to
Virtual servomotor axis monitor device (Note)
(10 points 32 axes)
(Mechanical system setting axis only)
D1120
Synchronous encoder axis monitor device (Note) (10 points 12 axes) to
D1240
CAM axis monitor device (Note)
(10 points 32 axes)
User device
(7392 points) to
D1560 to
User device
(6632 points)
D8191 D8191
Usable in the user device.
(Note): When it is used in the SV22 real mode only, it can be used as an user device.
POINT
• Total number of user device points
7392 points (SV13) / 6632 points
(Note)
(SV22)
(Note): Up to 7272 points can be used when not using it in the virtual mode.
3 - 40
3 POSITIONING DEDICATED SIGNALS
Axis
No.
Device No.
(2) Axis monitor device list
Signal name
1 D0 to D19
2 D20 to D39
3 D40 to D59
Signal name Refresh cycle Fetch cycle
4 D60 to D79 0
5 D80 to D99 1
6 D100 to D119 2
7 D120 to D139 3
Feed current value
Real current value Operation cycle
8 D140 to D159 4
9 D160 to D179 5
Deviation counter value
10 D180 to D199 6 Minor error code
11 D200 to D219 7 Major error code
Immediate
12 D220 to D239 8 Servo error code Main
13 D240 to D259
14 D260 to D279
Home position return
9 re-travel value
Operation cycle
15 D280 to D299 10 Travel value after
16 D300 to D319 11 proximity dog ON
17 D320 to D339 12 Execute program No.
18 D340 to D359 13 M-code
At start
Operation cycle
19 D360 to D379 14 Torque limit value
20 D380 to D399
21 D400 to D419
Data set pointer for
15 constant-speed control
At start/during start
22 D420 to D439 16
23 D440 to D459 17
Unusable (Note-1)
24 D460 to D479 18
25 D480 to D499 19
Real current value at stop input
Operation cycle
26 D500 to D519
27 D520 to D539
28 D540 to D559
29 D560 to D579
30 D580 to D599
31 D600 to D619
32 D620 to D639
Unit
Command unit
PLS
Signal direction
Monitor device
PLS
Command unit
%
Command unit
Monitor device
(Note-1): It can be used as the travel value change register. The travel value change register can be set to the device optionally in the servo program. Refer to Section 6.15 for details.
POINT
(1) The range of axis No.1 to 8 is valid in the Q172DCPU.
(2) The device area more than 9 axes as an user device in the Q172DCPU.
However, when the project of Q172DCPU is replaced with Q173DCPU, this area cannot be used.
3 - 41
3 POSITIONING DEDICATED SIGNALS
Axis
No.
Device No.
(3) Control change register list
Signal name
0
JOG speed setting
1
Signal name
Refresh cycle Fetch cycle
At start
POINT
(1) The range of axis No.1 to 8 is valid in the Q172DCPU.
(2) The device area more than 9 axes as an user device in the Q172DCPU.
However, when the project of Q172DCPU is replaced with Q173DCPU, this area cannot be used.
Unit
Command unit
Signal direction
Command device
3 - 42
3 POSITIONING DEDICATED SIGNALS
Device
No.
Signal name
D704 PLC ready flag request
D705
D706
Speed switching point specified flag request
All axes servo ON command request
D707
D708
Real mode/virtual mode switching request (SV22)
JOG operation simultaneous start command request
D709 Unusable
D710
D711
D712
D713
D714
D715
D716
D717
D718
D719
JOG operation simultaneous start axis setting register
Manual pulse generator axis
1 No. setting register
Manual pulse generator axis
2 No. setting register
Manual pulse generator axis
3 No. setting register
15 input magnification setting register
(Note-1), (Note-2)
(4) Common device list
Refresh cycle Fetch cycle
Main cycle
Signal direction
Command device
Device
No.
Signal name
D752
D753
Manual pulse generator 1 smoothing magnification setting register
Manual pulse generator 2 smoothing magnification setting register
D754
Manual pulse generator 3 smoothing magnification setting register
D755
Manual pulse generator 1 enable flag request
D756
Manual pulse generator 2 enable flag request
Refresh cycle Fetch cycle
At the manual pulse generator enable flag
Main cycle
Signal direction
Command device
At start
At the manual pulse generator enable flag
D758
D759
D760
D761
D762
D763
D764
D765
D766
D767
D768
D769
D770
D771
D772
D773
D774
D775
D776
D777
Command device
D778
D779
Unusable
(42 points)
D780
D781
D782
D783
D784
D785
D786
D787
D788
D789
D790
D791
D792
D793
D794
D795
D796
D797
D798
D799
(Note-1): The range of axis No.1 to 8 is valid in the Q172DCPU.
(Note-2): Device area of 9 axes or more is unusable in the Q172DCPU.
3 - 43
3 POSITIONING DEDICATED SIGNALS
3.2.1 Axis monitor devices
The monitoring data area is used by the Motion CPU to store data such as the feed current value during positioning control, the real current value and the deviation counter value.
It can be used to check the positioning control state using the Motion SFC program.
The user cannot write data to the monitoring data area (except the travel value change register).
Refer to "APPENDIX 4 Processing Times of the Motion CPU" for the delay time between a positioning device (input, internal relay and special relay) turning on/off and storage of data in the monitor data area.
(1) Feed current value storage register (D0+20n, D1+20n)
…..……...…….. Monitor device
(a) This register stores the target address output to the servo amplifier on the basis of the positioning address/travel value specified with the servo program.
1) A part for the amount of the travel value from "0" after starting is stored in the fixed-pitch feed control.
2) The current value from address at the time of starting is stored in the speed/position switching control.
However, the address at the time of starting varies depending on the
ON/OFF state of the feed current value update command (M3212+20n) at the start.
• M3212+20n: OFF ..... Resets the feed current value to "0" at the start.
• M3212+20n: ON ..... Not reset the feed current value at the start.
3) "0" is stored during speed control.
(b) The stroke range check is performed on this feed current value data.
(2) Real current value storage register (D2+20n, D3+20n)
....…….. Monitor device
(a) This register stores the real current value which took the droop pulses of the servo amplifier into consideration to the feed current value.
(b) The "feed current value" is equal to the "real current value" in the stopped state.
(3) Deviation counter value storage register (D4+20n, D5+20n)
....…….. Monitor device
This register stores the droop pulses read from the servo amplifier.
3 - 44
3 POSITIONING DEDICATED SIGNALS
(4) Minor error code storage register (D6+20n) ............. Monitor device
(a) This register stores the corresponding error code (Refer to APPENDIX 1.2) at the minor error occurrence. If another minor error occurs after error code storing, the previous error code is overwritten by the new error code.
(b) Minor error codes can be cleared by an error reset command (M3207+20n).
(5) Major error code storage register (D7+20n) ............. Monitor device
(a) This register stores the corresponding error code (Refer to APPENDIX 1.3) at the major error occurrence. If another major error occurs after error code storing, the previous error code is overwritten by the new error code.
(b) Major error codes can be cleared by an error reset command (M3207+20n).
(6) Servo error code storage register (D8+20n) ......... Monitor device
(a) This register stores the corresponding error code (Refer to APPENDIX 1.4) at the servo error occurrence. If another servo error occurs after error code storing, the previous error code is overwritten by the new error code.
(b) Servo error codes can be cleared by an error reset command (M3208+20n).
(7) Home position return re-travel value storage register (D9+20n)
....…….. Monitor device
If the position stopped in the position specified with the travel value after proximity dog ON (Refer to Section 6.23.1) using MT Developer is not zero point, it made to travel to zero point by re-travel in the Motion CPU. The travel value (signed) of making it travel to zero point by re-travel at this time is stored.
(Data does not change with the last value in the data setting type.)
The following value is stored according to the number of feedback pulses of the motor connected.
Number of feedback pulses
Less than 131072[PLS]
131072[PLS] or more, 262144[PLS] or less
More than 262144[PLS]
Storage data
Feedback pulses
1/10 of feedback pulses
1/10000 of feedback pulses
(8) Travel value after proximity dog ON storage register
(D10+20n, D11+20n) ………………………………… Monitor device
(a) This register stores the travel value (unsigned) from the proximity dog ON to home position return completion after the home position return start.
(b) The travel value (signed) of the position control is stored at the time of speed/position switching control.
3 - 45
3 POSITIONING DEDICATED SIGNALS
(9) Execute program No. storage register (D12+20n)
....…….. Monitor device
(a) This register stores the starting program No. at the servo program starting.
(b) The following value is stored in the JOG operation and manual pulse generator operation.
1) JOG operation...................................... FFFF
2) Manual pulse generator operation ...... FFFE
3) Power supply on................................... FF00
(c) When the following control is being executed using MT Developer in the test mode, FFFD is stored in this register.
• Home position return
(10) M-code storage register (D13+20n) ..........……….. Monitor device
(a) This register stores the M-code (Note) set to the executed servo program at the positioning start.
If M-code is not set in the servo program, the value "0" is stored.
(b) It does not change except positioning start using the servo program.
(c) The value "0" is stored at leading edge of PLC ready flag (M2000).
REMARK
(Note): Refer to the following sections for M-codes and reading M-codes.
• M-code ......................... Section 7.1
• Reading M-code ........... APPENDIX 2.1
(11) Torque limit value storage register (D14+20n) ...... Monitor device
This register stores the torque limit value imposed on the servo amplifier.
The default value "300[%]" is stored at the power supply of servo amplifier ON.
3 - 46
3 POSITIONING DEDICATED SIGNALS
(12) Data set pointer for constant-speed control (D15+20n)
....…….. Monitor device
This pointer is used in the constant-speed control when specifying positioning data indirectly and substituting positioning data during operation.
It stores a "point" that indicates which of the values stored in indirect devices has been input to the Motion CPU when positioning is being repeated by using a repetition instructions (FOR-TIMES, FOR-ON or FOR-OFF).
Use this pointer in conjunction with the updated data set pointer (controlled by the user in the Motion SFC program) - which indicates the extent to which the positioning data has been updated using the Motion SFC program - to confirm which positioning data is to be updated.
Data set pointer for constant-speed control and updated data set pointer are described here using the example servo program below.
Pass point
<K 0>
9
*
CPSTART2
Axis
Axis
Speed
FOR-TIMES
1
2
3
4
5
6
7
8
*
9
ABS-2
Axis
Axis
ABS-2
Axis
Axis
ABS-2
Axis
Axis
ABS-2
Axis
Axis
ABS-2
Axis
Axis
ABS-2
Axis
Axis
ABS-2
Axis
Axis
ABS-2
Axis
Axis
NEXT
CPEND
1
2
1,
2,
1,
2,
1,
2,
1,
2,
1,
2,
1,
2,
1,
2,
1,
2,
D3200
D3000
D3002
. . . 0
. . . 1
D3004
D3006
. . . 2
D3008
D3010
. . . 3
D3012
D3014
. . . 4
D3016
D3018
. . . 5
D3020
D3022
. . . 6
D3024
D3026
. . . 7
D3028
D3030
Point
Repetition instructions
FOR-TIMES
FOR-ON
FOR-OFF
NEXT
0, 1, 2, etc., starting from the first instructions defined by the above repetition instructions :
The input situation of positioning data to the Motion CPU is shown the next page by executing the 2-axes constant-speed control using above the servo program and updating the positioning data in indirect devices D3000 to D3006.
3 - 47
3 POSITIONING DEDICATED SIGNALS
[Input situation of positioning data in the Motion CPU]
Update of data using the Motion SFC program
Updated data
(A)
(B)
Updating
Indirect device D
0
2
(1)
(2)
(A)
(B)
0
Point
Input
First positioning
Positioning data input to the Motion CPU at each point
Positioning point
Data set pointer for constant-speed control
Point 0 6
(13)
5
(11)
4
(9)
3
(7)
2
(5)
1
(3)
0
(1)
Indicates the last positioning data input to the Motion CPU.
(C)
(D)
4
6
8
10
(3)
(4)
(5)
(6)
(C)
(D)
1
2
1
(14)
7
(15)
(12)
6
(13)
(10)
5
(11)
(8)
4
(9)
(6)
3
(7)
(4)
2
(5)
(2)
1
(3)
Each time the positioning at a point is completed, the value increases by one.
12 (7) (6) (4)
3
(16) (14) (12) (10) (8)
14
16
18
20
22
(8)
(9)
(10)
(11)
(12)
4
5
2 0
(A)
7 6
(15) (13)
5
(11)
4
(9)
3
(7)
(B) (16) (14) (12) (10) (8)
2
(5)
(6)
24
26
28
(13)
(14)
(15)
30 (16)
6
7
3 1
(C)
(D)
0
(A)
7 6 5
(15) (13) (11)
4
(9)
3
(7)
(B) (16) (14) (12) (10) (8)
4 2
(5)
(6)
1
(C)
(D)
0
(A)
7 6 5
(15) (13) (11)
4
(9)
(B) (16) (14) (12) (10)
Update data set pointer
Indicates the last positioning data updated by the Motion
SFC program last time.
The user controls this pointer in the
Motion SFC program.
1 5 3
(7)
(8)
2
(5)
(6)
(C)
(D)
0 7 6 5
(A) (15) (13) (11)
(B) (16) (14) (12)
6 4
(9)
3
(7)
(10) (8)
2
(5)
(6)
1
(C)
(D)
0
(A)
7 6
(15) (13)
(B) (16) (14)
7 5
(11)
4
(9)
3
(7)
(12) (10) (8)
2
(5)
(6)
1
(C)
(D)
0
(A)
7
(15)
(B) (16)
Second positioning
Point 0 6 5 4 3
(13) (11) (9)
(14) (12) (10)
(7)
(8)
2
(5)
(6)
1
(C)
(D)
0
(A)
(B)
The internal processing shown above is described in the next page.
3 - 48
3 POSITIONING DEDICATED SIGNALS
[Internal processing]
(a) The positioning data ((1) to (14)) of points 0 to 6 is input to the Motion CPU by the starting. The last point "6" of the input data to be input is stored in the data set pointer for constant-speed control at this time.
The "6" stored in the data set pointer for constant-speed control indicates that updating of the positioning data stored in points 0 to 6 is possible.
(b) The positioning data ((A) to (D)) of points 0 to 1 is updated using the Motion
SFC program.
The last point "1" of the positioning data to be rewritten is stored in the updated data set pointer (which must be controlled by the user in the
Motion SFC program). Updating of positioning data of points 2 to 6 (data (5) to (14)) remains possible.
(c) On completion of the positioning for point 0, the value in the data set pointer for constant-speed control is automatically incremented by one to "7".
The positioning data ((1) to (2)) of point 0 is discarded and the positioning data ((15) to (16)) for point 7 is input to the Motion CPU at this time.
(d) Hereafter, whenever positioning of each point is completed, the positioning data shifts one place.
The positioning data that can be updated is the data after that indicated by the updated data set pointer: this is the data which has not yet been input to the Motion CPU.
Even if the values of the indirect devices D8 and D10 are updated by the
Motion SFC program after the positioning completion of the point 3, the positioning data of point 2 that is input to the Motion CPU will not be updated and the second positioning will be executed using the unupdated data. The data set pointer for constant-speed control has not yet been input to the Motion CPU, and indicates the positioning data which a user can update using the Motion SFC program.
POINT
Number of points that can be defined by a repeat instruction
• Create the servo program at least eight points.
• If there are less than eight points and they include pass points of few travel value, the positioning at each point may be completed, and the data input to the Motion
CPU, before the data has been updated using the Motion SFC program.
• Create a sufficient number of points to ensure that data will not be input before the
Motion CPU has updated the values in the indirect devices.
(13) Real current value at STOP input storage register
(D18+20n, D19+20n) .............……………………... Monitor device
This register stores the real current value at the STOP signal (STOP) input of the Q172DLX.
3 - 49
3 POSITIONING DEDICATED SIGNALS
3.2.2 Control change registers
This area stores the JOG operation speed data.
Table 3.1 Data storage area for control change list
Name Axis 1 Axis 2 Axis 3 Axis 4 Axis 5 Axis 6 Axis 7 Axis 8
D641, D640 D643, D642 D645, D644 D647, D646 D649, D648 D651, D650 D653, D652 D655, D654
Axis 9 Axis 10 Axis 11 Axis 12 Axis 13 Axis 14 Axis 15 Axis 16
JOG speed setting register
D657, D656 D659, D658 D661, D660 D663, D662 D665, D664 D667, D666 D669, D668 D671, D670
Axis 17 Axis 18 Axis 19 Axis 20 Axis 21 Axis 22 Axis 23 Axis 24
D673, D672 D675, D674 D677, D676 D679, D678 D681, D680 D683, D682 D685, D684 D687, D686
Axis 25 Axis 26 Axis 27 Axis 28 Axis 29 Axis 30 Axis 31 Axis 32
D689, D688 D691, D690 D693, D692 D695, D694 D697, D696 D699, D698 D701, D700 D703, D702
(Note): The range of axis No.1 to 8 is valid in the Q172DCPU.
(1) JOG speed setting registers (D640+2n, D641+2n)
....…….. Command device
(a) This register stores the JOG speed at the JOG operation.
Unit
Item
(b) Setting range of the JOG speed is shown below.
JOG speed
Setting range
1 to
600000000
Unit
10 -2
[mm/min]
Setting range
1 to
600000000
Unit
10 -3
[inch/min]
Setting range Unit (Note-1)
1 to
2147483647
Setting Unit
10 -3
[degree/min]
1 to
2147483647
[PLS/s]
(Note-1) : When the " speed control 10 multiplier setting for degree axis" is set to "valid" in the fixed parameter, the unit is
" 10 -2 [degree/min] ".
(c) The JOG speed is the value stored in the JOG speed setting registers at leading edge of JOG start signal.
Even if data is changed during JOG operation, JOG speed cannot be changed.
(d) Refer to Section 6.21 for details of JOG operation.
3 - 50
3 POSITIONING DEDICATED SIGNALS
3.2.3 Common devices
(1) Common bit device SET/RST request register (D704 to D708,
D755 to D757) ..…........….................................... Command device
Because cannot be turn on/off in every bit from the PLC CPU, the bit device is assigned to D register, and each bit device turns on with the lowest rank bit 0 to
1 and each bit device becomes off with 1 to 0.
The details of request register are shown below.
(Refer to Section "3.1.3 Common devices" for the bit device M2000 to M2053.)
Details of the request register
No. Function
1 PLC ready flag
2 Speed switching point specified flag
3 All axes servo ON command
4 Real mode/virtual mode switching request (SV22)
5 JOG operation simultaneous start command
6 Manual pulse generator 1 enable flag
7 Manual pulse generator 2 enable flag
8 Manual pulse generator 3 enable flag
Bit device
M2000
M2040
M2042
M2043
M2048
M2051
M2052
M2053
Request register
D704
D705
D706
D707
D708
D755
D756
D757
(2) JOG operation simultaneous start axis setting registers (D710 to
D713) ....….……………..….……………………… Command device
(a) These registers set the axis No. and direction which start simultaneously the
JOG operation. b15 b14 b13 b12 b11 b10 b9 b8 b7 b6 b5 b4 b3 b2 b1 b0
D710 Axis 16 Axis 15 Axis 14 Axis 13 Axis 12 Axis 11 Axis 10 Axis 9 Axis 8 Axis 7 Axis 6 Axis 5 Axis 4 Axis 3 Axis 2 Axis 1 Forward rotation
JOG
D711 Axis 32 Axis 31 Axis 30 Axis 29 Axis 28 Axis 27 Axis 26 Axis 25 Axis 24 Axis 23 Axis 22 Axis 21 Axis 20 Axis 19 Axis 18 Axis 17
D712 Axis 16 Axis 15 Axis 14 Axis 13 Axis 12 Axis 11 Axis 10 Axis 9 Axis 8 Axis 7 Axis 6 Axis 5 Axis 4 Axis 3 Axis 2 Axis 1
D713 Axis 32 Axis 31 Axis 30 Axis 29 Axis 28 Axis 27 Axis 26 Axis 25 Axis 24 Axis 23 Axis 22 Axis 21 Axis 20 Axis 19 Axis 18 Axis 17
Reverse rotation
JOG
(Note-1) : Make JOG operation simultaneous start axis setting with 1/0.
1 : Simultaneous start execution
0 : Simultaneous start not execution
(Note-2) : The range of axis No.1 to 8 is valid in the Q172DCPU.
(b) Refer to Section 6.21.3 for details of the JOG operation simultaneous start.
(3) Manual pulse generator axis No. setting registers (D714 to D719)
....…….. Command device
(a) These registers stores the axis No. controlled with the manual pulse generator.
3 - 51
3 POSITIONING DEDICATED SIGNALS b15 b14 b13 b12 b11 b10 b9 b8 b7 b6 b5 b4 b3 b2 b1 b0
D714 Axis 16 Axis 15 Axis 14 Axis 13 Axis 12 Axis 11 Axis 10 Axis 9 Axis 8 Axis 7 Axis 6 Axis 5 Axis 4 Axis 3 Axis 2 Axis 1
P1
D715 Axis 32 Axis 31 Axis 30 Axis 29 Axis 28 Axis 27 Axis 26 Axis 25 Axis 24 Axis 23 Axis 22 Axis 21 Axis 20 Axis 19 Axis 18 Axis 17
P2
D716 Axis 16 Axis 15 Axis 14 Axis 13 Axis 12 Axis 11 Axis 10 Axis 9 Axis 8 Axis 7 Axis 6 Axis 5 Axis 4 Axis 3 Axis 2 Axis 1
D717 Axis 32 Axis 31 Axis 30 Axis 29 Axis 28 Axis 27 Axis 26 Axis 25 Axis 24 Axis 23 Axis 22 Axis 21 Axis 20 Axis 19 Axis 18 Axis 17
P3
D718 Axis 16 Axis 15 Axis 14 Axis 13 Axis 12 Axis 11 Axis 10 Axis 9 Axis 8 Axis 7 Axis 6 Axis 5 Axis 4 Axis 3 Axis 2 Axis 1
D719 Axis 32 Axis 31 Axis 30 Axis 29 Axis 28 Axis 27 Axis 26 Axis 25 Axis 24 Axis 23 Axis 22 Axis 21 Axis 20 Axis 19 Axis 18 Axis 17
(Note-1) : Make the axis No. controlled with the manual pulse generator
setting with 1/0.
1 : Specified axis
0 : Unspecified axis
(Note-2) : The range of axis No.1 to 8 is valid in the Q172DCPU.
(b) Refer to Section 6.22 for details of the manual pulse generator operation.
(4) Manual pulse generator 1-pulse input magnification setting registers (D720 to D751) ..................................... Command device
(a) These register set the magnification (1 to 10000) per pulse of number of the input pulses from manual pulse generator at the pulse generator operation.
1-pulse input magnification setting register
D720
D721
D722
D723
D724
D725
D726
D727
D728
D729
D730
D731
D732
D733
D734
Axis No.
Axis 1
Axis 2
Axis 3
Axis 4
Axis 5
Axis 6
Axis 7
Axis 8
Axis 9
Axis 10
Axis 11
Axis 12
Axis 13
Axis 14
Axis 15
Setting range
1-pulse input magnification setting register
D736
D737
D738
D739
D740
D741
1 to 10000
D742
D743
D744
D745
D746
D747
D748
D749
D750
Axis No.
Axis 17
Axis 18
Axis 19
Axis 20
Axis 21
Axis 22
Axis 23
Axis 24
Axis 25
Axis 26
Axis 27
Axis 28
Axis 29
Axis 30
Axis 31
Setting range
1 to 10000
(Note-1): The range of axis No.1 to 8 is valid in the Q172DCPU.
(b) Refer to Section 6.22 for details of the manual pulse generator operation.
3 - 52
3 POSITIONING DEDICATED SIGNALS
(5) Manual pulse generator smoothing magnification setting registers
(D752 to D754) .................................................... Command device
(a) These registers set the smoothing time constants of manual pulse generators.
Manual pulse generator smoothing magnification setting register
Manual pulse generator 1 (P1): D752
Manual pulse generator 2 (P1): D753
Manual pulse generator 3 (P1): D754
Setting range
0 to 59
(b) When the smoothing magnification is set, the smoothing time constant is as indicated by the following expression.
Smoothing time constant (t) = (smoothing magnification + 1) 56.8 [ms]
(c) Operation
Manual pulse generator input
Manual pulse generator enable flag (M2051)
OFF
V
ON
V
1 t t t t
Output speed (V
1
) [PLS/s] = (Number of input pulses/s) (Manual pulse
generator 1-pulse input magnification setting)
Travel value (L) =
(Travel value per pulse)
×
Number of input pulses
(Manual pulse generator 1-pulse input magnification setting)
REMARK
(1) The travel value per pulse of the manual pulse generator is shown below.
• Setting unit mm :0.1[µm] inch :0.00001[inch] degree :0.00001[degree]
PLS :1[PLS]
(2) The smoothing time constant is 56.8[ms] to 3408[ms].
3 - 53
advertisement
* Your assessment is very important for improving the workof artificial intelligence, which forms the content of this project
Related manuals
advertisement
Table of contents
- 2 SAFETY PRECAUTIONS
- 12 REVISIONS
- 13 CONTENTS
- 16 About Manuals
- 18 1. OVERVIEW
- 18 1.1 Overview
- 20 1.2 Features
- 20 1.2.1 Performance Specifications
- 22 2. POSITIONING CONTROL BY THE MOTION CPU
- 22 2.1 Positioning Control by the Motion CPU
- 36 3. POSITIONING DEDICATED SIGNALS
- 38 3.1 Internal Relays
- 45 3.1.1 Axis statuses
- 55 3.1.2 Axis command signals
- 62 3.1.3 Common devices
- 75 3.2 Data Registers
- 79 3.2.1 Axis monitor devices
- 85 3.2.2 Control change registers
- 86 3.2.3 Common devices
- 89 3.3 Motion Registers (#)
- 91 3.4 Special Relays (SM)
- 94 3.5 Special Registers (SD)
- 100 4. PARAMETERS FOR POSITIONING CONTROL
- 100 4.1 System Settings
- 101 4.2 Fixed Parameters
- 102 4.2.1 Number of pulses/travel value per rotation
- 104 4.2.2 Backlash compensation amount
- 104 4.2.3 Upper/lower stroke limit value
- 106 4.2.4 Command in-position range
- 107 4.2.5 Speed control 10 multiplier setting for degree axis
- 110 4.3 Parameter Block
- 112 4.3.1 Relationships between the speed limit value, acceleration time, deceleration time and rapid stop deceleration time
- 112 4.3.2 S-curve ratio
- 113 4.3.3 Allowable error range for circular interpolation
- 114 5. SERVO PROGRAMS FOR POSITIONING CONTROL
- 114 5.1 Servo Program Composition Area
- 114 5.1.1 Servo program composition
- 115 5.1.2 Servo program area
- 116 5.2 Servo Instructions
- 129 5.3 Positioning Data
- 135 5.4 Setting Method for Positioning Data
- 135 5.4.1 Setting method by specifying numerical values
- 136 5.4.2 Indirect setting method by devices
- 140 6. POSITIONING CONTROL
- 140 6.1 Basics of Positioning Control
- 140 6.1.1 Positioning speed
- 141 6.1.2 Positioning speed at the interpolation control
- 146 6.1.3 Control units for 1 axis positioning control
- 146 6.1.4 Control units for interpolation control
- 148 6.1.5 Control in the control unit "degree"
- 150 6.1.6 Stop processing and restarting after stop
- 156 6.1.7 Acceleration/deceleration processing
- 158 6.2 1 Axis Linear Positioning Control
- 161 6.3 2 Axes Linear Interpolation Control
- 166 6.4 3 Axes Linear Interpolation Control
- 172 6.5 4 Axes Linear Interpolation Control
- 177 6.6 Auxiliary Point-Specified Circular Interpolation Control
- 182 6.7 Radius-Specified Circular Interpolation Control
- 188 6.8 Central Point-Specified Circular Interpolation Control
- 194 6.9 Helical Interpolation Control
- 195 6.9.1 Circular interpolation specified method by helical interpolation
- 216 6.10 1 Axis Fixed-Pitch Feed Control
- 220 6.11 Fixed-Pitch Feed Control Using 2 Axes Linear Interpolation
- 224 6.12 Fixed-Pitch Feed Control Using 3 Axes Linear Interpolation
- 228 6.13 Speed Control ( I )
- 232 6.14 Speed Control ( II )
- 235 6.15 Speed/Position Switching Control
- 235 6.15.1 Speed/position switching control start
- 242 6.15.2 Re-starting after stop during control
- 247 6.16 Speed-Switching Control
- 247 6.16.1 Speed-switching control start, speed-switching points and end specification
- 253 6.16.2 Specification of speed-switching points using repetition instructions
- 259 6.17 Constant-Speed Control
- 263 6.17.1 Specification of pass points by repetition instructions
- 268 6.17.2 Speed-switching by instruction execution
- 273 6.17.3 1 axis constant-speed control
- 277 6.17.4 2 to 4 axes constant-speed control
- 284 6.17.5 Constant speed control for helical interpolation
- 287 6.17.6 Pass point skip function
- 289 6.17.7 FIN signal wait function
- 299 6.18 Position Follow-Up Control
- 306 6.19 Speed control with fixed position stop
- 311 6.20 Simultaneous Start
- 314 6.21 JOG Operation
- 314 6.21.1 JOG operation data
- 315 6.21.2 Individual start
- 320 6.21.3 Simultaneous start
- 323 6.22 Manual Pulse Generator Operation
- 330 6.23 Home Position Return
- 331 6.23.1 Home position return data
- 339 6.23.2 Home position return by the proximity dog type 1
- 342 6.23.3 Home position return by the proximity dog type 2
- 344 6.23.4 Home position return by the count type 1
- 346 6.23.5 Home position return by the count type 2
- 347 6.23.6 Home position return by the count type 3
- 349 6.23.7 Home position return by the data set type 1
- 350 6.23.8 Home position return by the data set type 2
- 351 6.23.9 Home position return by the dog cradle type
- 356 6.23.10 Home position return by the stopper type 1
- 358 6.23.11 Home position return by the stopper type 2
- 360 6.23.12 Home position return by the limit switch combined type
- 362 6.23.13 Home position return retry function
- 366 6.23.14 Home position shift function
- 370 6.23.15 Condition selection of home position set
- 371 6.23.16 Servo program for home position return
- 373 6.24 High-Speed Oscillation
- 376 7. AUXILIARY AND APPLIED FUNCTIONS
- 376 7.1 M-code Output Function
- 379 7.2 Backlash Compensation Function
- 381 7.3 Torque Limit Function
- 383 7.4 Skip Function in which Disregards Stop Command
- 385 7.5 Cancel of the Servo Program
- 386 7.5.1 Cancel/start
- 388 APPENDICES
- 388 APPENDIX 1 Error Codes Stored Using The Motion CPU
- 390 APPENDIX 1.1 Servo program setting errors (Stored in SD517)
- 395 APPENDIX 1.2 Minor errors
- 405 APPENDIX 1.3 Major errors
- 409 APPENDIX 1.4 Servo errors
- 428 APPENDIX 2 Example Programs
- 428 APPENDIX 2.1 Reading M-code
- 429 APPENDIX 2.2 Reading error code
- 431 APPENDIX 3 Setting Range for Indirect Setting Devices
- 433 APPENDIX 4 Processing Times of the Motion CPU
- 434 APPENDIX 5 Device List
- 445 WARRANTY