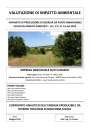
advertisement
▼
Scroll to page 2
of
145
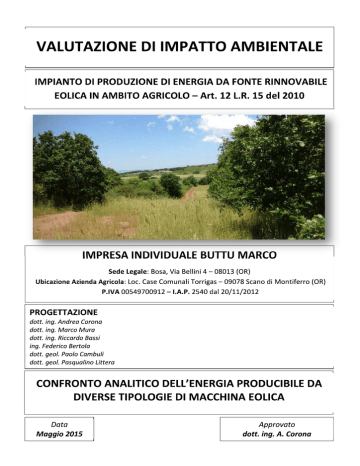
NESA: matricola 1004686 sensore NESA di velocità del vento alla quota di 20 m: matricola 1004630 - slope 0.30156 - offset 0.2831 sensore NESA di direzione del vento alla quota di 20 m. sensore NESA di velocità del vento alla quota di 30 m: matricola 1004629 - slope 0.30283 - offset 0.2678 sensore NESA di velocità del vento alla quota di 42 m: matricola 1004628 - slope 0.30306 - offset 0.2942 sensore NESA di direzione del vento alla quota di 42 m. pag. 1 Società Elettrica Italiana pag. 2 Società Elettrica Italiana Società Elettrica Italiana V 29,8m [m/s] [kW] 1 0 0 2 0 0 3 0 0 4 4 7 5 15 19 6 30 34 7 54 56 8 74 78 9 105 109 10 128 138 11 148 162 12 167 184 13 184 196 14 199 205 15 205 205 16 205 202 17 200 200 18 194 196 19 183 196 20 182 196 21 181 196 22 181 196 23 181 196 24 181 196 25 181 196 Producibilità e Ricavi su Base Annua Parametri di Calcolo* Rotore 29,8m Rotore 31m Produzione di energia con 12 m/s di ventosità media al mozzo Ricavato per cessione a tariffa unica omnicomprensiva [kWh/anno] 1.056.300 283.100 1.112.200 298.100 Produzione di energia con 11 m/s di ventosità media al mozzo Stima ricavato per cessione a tariffa unica omnicomprensiva [kWh/anno] 1.002.600 283.100 1.112.200 283.200 Produzione di energia con 10 m/s di ventosità media al mozzo Stima ricavato per cessione a tariffa unica omnicomprensiva [kWh/anno] 925.200 248.000 976.900 261.800 Produzione di energia con 9 m/s di ventosità media al mozzo Stima ricavato per cessione a tariffa unica omnicomprensiva [kWh/anno] 823.800 220.800 872.500 233.800 Produzione di energia con 8 m/s di ventosità media al mozzo Stima ricavato per cessione a tariffa unica omnicomprensiva [kWh/anno] 700.200 187.700 745.100 199.700 Produzione di energia con 7 m/s di ventosità media al mozzo Stima ricavato per cessione a tariffa unica omnicomprensiva [kWh/anno] 558.900 149.800 598.700 160.400 Produzione di energia con 6 m/s di ventosità media al mozzo Stima ricavato per cessione a tariffa unica omnicomprensiva [kWh/anno] 408.000 109.300 440.700 118.100 Produzione di energia con 5 m/s di ventosità media al mozzo Stima ricavato per cessione a tariffa unica omnicomprensiva [kWh/anno] 259.700 69.600 284.600 76.300 Produzione di energia con 4 m/s di ventosità media al mozzo Stima ricavato per cessione a tariffa unica omnicomprensiva [kWh/anno] 132.200 35.400 149.500 40.100 pag. 3 31m [kW] Operating Instructions ENERCON E-40 Version 1.2.1 June 1998 ENERCON ENERCON E-40 GmbH Operating Instructions Dreekamp 5 Tel.: 04941 / 927 - 0 26605 Aurich Fax: 04941 / 927 -199 Page 2 of 96 Imprint: Operation manual: Prepared by: Date: Version: ENERCON E-40 Dipl.-Ing. W. Winkler March 1998 1.1.5 The wind energy converter ENERCON E-40 is produced and delivered by ENERCON GmbH Dreekamp 5 D-26605 Aurich Tel.: +49 / 4941 / 927 - 0 Imprint ENERCON ENERCON E-40 GmbH Operating Instructions Dreekamp 5 Tel.: 04941 / 927 - 0 26605 Aurich Fax: 04941 / 927 -199 Page 3 of 96 Liability ENERCON asks you to read the contents of these Operating Instructions - in particular chapter 2 "Safety Instructions" carefully and completely and to follow these instructions. Make yourself familiar with the contents because we do not accept any liability for damage caused by failure to comply with the instructions. ENERCON reserves the right to change these Operating Instructions or to replace them by another manual at any time. ATTENTION: The first commissioning of the E-40 is carried out only by ENERCON personnel. Upon commissioning, the owner or his representative are introduced to the operation of the turbine and the safety rules (e.g. climbing up to the nacelle) in theory and in practice by ENERCON personnel. Before the official handing over of the wind energy converter, the owner is strictly forbidden to carry out any switching operations or to enter the WEC and the tower base. NOTE: The contents of these Operating Instructions refer to the standard version of the E40. Since, however, the basic principles of functioning and operation of the turbine are the same for all versions, this manual does not include any details on optional features. In case you should find any information in these Operating Instructions which could be misleading, please let us know. We will try to clarify the problem at once and correct any mistakes in order to avoid operating mistakes. Please contact our "Technical Writing" (Export) department. Liability ENERCON E-40 Operation instructions Page 4 of 96 Table of Contents Imprint: .................................................................................................................................................... 2 Liability.................................................................................................................................................... 3 Table of Contents................................................................................................................................... 4 1 Short description of the E-40 ............................................................................................................. 8 1.1 The ENERCON concept ............................................................................................................... 9 1.2 Generator ...................................................................................................................................... 9 1.3 Rotor............................................................................................................................................ 10 1.4 Yaw control................................................................................................................................. 10 1.5 E-40 Safety System .................................................................................................................... 11 1.5.1 The Brake System................................................................................................................. 11 1.5.2 Lightning Protection System.................................................................................................. 11 1.5.3 Sensor System ...................................................................................................................... 12 1.5.4 Control System...................................................................................................................... 12 1.5.5 Grid Management ................................................................................................................. 13 2 Safety Instructions............................................................................................................................ 15 2.1 The E-40’s Safety System.......................................................................................................... 15 2.2 Protective measures for works on and inside the E-40 ......................................................... 15 2.2.1 General regulations and rules of conduct ............................................................................. 15 2.2.2 Schematic diagrams of the WEC’s safety provisions ........................................................... 16 2.2.2.1 Safety provisons of the nacelle, side view...................................................................... 16 2.2.2.2 Safety provisions of tower and tower base..................................................................... 17 2.2.2.3 Safety provisions of the nacelle, rear view ..................................................................... 18 2.2.3 First aid.................................................................................................................................. 18 2.2.4 Work involving a risk of fire ................................................................................................... 19 2.2.5 Turbine shut-down in case of formation of ice ...................................................................... 19 2.2.6 Safety instructions for persons working in the transformer- or substation and in the tower base................................................................................................................................................ 19 2.2.7 Climbing and descending the tower ladder ........................................................................... 20 2.2.8 Staying on the tower platform and in the nacelle .................................................................. 22 2.2.9 Rotor lock .............................................................................................................................. 22 2.3 Inspection of safety provisions ................................................................................................ 23 2.3.1 Owner’s obligation to inform ENERCON............................................................................... 23 3 Operation ........................................................................................................................................... 24 3.1 Control and Monitoring System ............................................................................................... 24 3.2 Display of E-40 status messages ............................................................................................. 25 3.3 Responding of safety-relevant sensors................................................................................... 25 3.4 Starting........................................................................................................................................ 26 Table of contents ENERCON E-40 Operating Instructions Page 5 of 96 3.5 Normal operation ....................................................................................................................... 26 3.6 Idling............................................................................................................................................ 27 3.7 Stopping...................................................................................................................................... 27 3.7.1 Manual stopping .................................................................................................................... 27 3.7.2 Manual stopping in emergency stituations ............................................................................ 28 3.8 Lack of wind ............................................................................................................................... 29 3.9 Storm ........................................................................................................................................... 29 3.10 Rotor speed monitoring (rotor overspeed) ........................................................................... 29 3.11 Yaw control............................................................................................................................... 30 3.12 Untwisting of cables ................................................................................................................ 31 3.13 Emergency pitch control units of the E-40 ............................................................................ 32 3.14 Rotor brake ............................................................................................................................... 32 3.15 Rotor lock ................................................................................................................................. 32 3.16 Shear pin monitoring ............................................................................................................... 33 3.17 Vibrations and Tower Oscillations ......................................................................................... 33 3.18 Air gap monitoring ................................................................................................................... 34 3.19 Temperature monitoring.......................................................................................................... 34 3.20 Pitch control error.................................................................................................................... 34 3.21 Protective circuit-breaker tripped........................................................................................... 35 3.22 Grid error................................................................................................................................... 35 3.23 Converter fault.......................................................................................................................... 36 3.24 Maintenance ............................................................................................................................. 36 4 Towers and ground stations of the E-40 ........................................................................................ 37 4.1 Steel tower .................................................................................................................................. 37 4.2 Reinforced concrete tower........................................................................................................ 38 4.3 Stations for different tower versions ....................................................................................... 38 4.3.1 Combined transformer / substation....................................................................................... 39 4.3.2 Transformer station ............................................................................................................... 40 4.3.3 Three-room substation .......................................................................................................... 41 5 Control and Power Cabinets............................................................................................................ 42 5.1 Power cabinet ............................................................................................................................. 42 5.2 Control cabinet / display ........................................................................................................... 42 5.3 LC display and menu functions................................................................................................ 44 5.3.1 General instructions .............................................................................................................. 44 5.3.2 Menu "start delay" ................................................................................................................. 46 5.3.3 Menu "mains parameters"..................................................................................................... 46 5.3.4 Menu "mains data" ................................................................................................................ 47 5.3.5 Menu "blade defroster" (optional).......................................................................................... 47 5.3.6 Menu "power optimization" (optional) .................................................................................... 48 Table of contents ENERCON E-40 Operating Instructions Page 6 of 96 5.3.7 Menu 1 / 2 "shadow stop" (optional)...................................................................................... 49 5.3.7.1 Menu and menu settings ................................................................................................ 49 5.3.7.2 Functions in shadow stop menu 1.................................................................................. 50 5.3.7.3 Functions in shadow stop menu 2.................................................................................. 51 5.3.8 Menu "time / date" ................................................................................................................. 52 5.3.9 Menu "set kilowatt hours" ...................................................................................................... 52 5.3.10 Menu "set operating hours" ................................................................................................. 52 5.3.11 Menu "adjust contrast" ........................................................................................................ 52 5.3.12 Menu "language" ................................................................................................................. 53 5.3.13 Menu "pitch data" ................................................................................................................ 53 5.3.14 Menu "version numbers" ..................................................................................................... 53 5.3.15 Menu "hardware options" .................................................................................................... 53 5.3.16 Menu "program info" ........................................................................................................... 53 5.4 Control cabinet operator panel................................................................................................. 54 6 The nacelle (the machine house) .................................................................................................... 58 6.1 Arrangement of components in and on the E-40 nacelle....................................................... 58 6.2 Description of important components in the rotor head ....................................................... 59 6.2.1 Slip ring casing ...................................................................................................................... 59 6.2.2 Pitch control unit.................................................................................................................... 59 6.2.2.1 Pitch control cabinet ....................................................................................................... 60 6.2.2.2 Battery cabinet................................................................................................................ 60 6.2.2.3 Relay cabinet.................................................................................................................. 60 6.2.2.4 Pitch control motor ......................................................................................................... 60 6.2.2.5 Angle encoder ................................................................................................................ 61 6.3 Operator panel of the E-40 nacelle sub-distribution .............................................................. 61 6.3.1 Description of the nacelle sub-distribution control elements ................................................. 62 7 Remote Monitoring ........................................................................................................................... 66 7.1 System components .................................................................................................................. 67 7.1.1 Optional equipment ............................................................................................................... 67 7.2 Additional monitoring systems ................................................................................................ 68 7.3 Scope of monitoring .................................................................................................................. 68 7.3.1 Wind energy converter .......................................................................................................... 68 7.3.2 Wind farm.............................................................................................................................. 71 7.3.3 Substation (optional) ............................................................................................................. 72 7.3.4 Meteorological stations (optional).......................................................................................... 72 7.4 System messages ...................................................................................................................... 73 7.4.1 Status messages................................................................................................................... 73 7.4.2 Malfunctions (faults) .............................................................................................................. 73 7.4.3 Fault messages..................................................................................................................... 74 7.5 Transfer ....................................................................................................................................... 75 7.5.1 Fault message to central monitoring system (office computer) ............................................ 75 7.5.2 Fault message to fax............................................................................................................. 75 7.5.3 Fault message to SMS or pager (city call) ............................................................................ 75 Table of contents ENERCON E-40 Operating Instructions Page 7 of 96 7.6 Control ........................................................................................................................................ 75 7.7 Other functions .......................................................................................................................... 75 7.7.1 Transfer protocol ................................................................................................................... 75 7.7.2 Requesting of missing data................................................................................................... 76 8 Optional Equipment .......................................................................................................................... 77 8.1 Obstruction lighting / Hazard beacon ...................................................................................... 77 8.1.1 Obstruction lighting with standby power supply and monitoring............................................ 77 8.1.2 Obstruction lighting without standby power supply, but including monitoring........................ 77 8.1.3 Obstruction lighting without standby power supply and without monitoring .......................... 78 8.1.4 Flashing hazard beacon with standby power supply and monitoring .................................... 78 8.2 Rotor blade heating ................................................................................................................... 78 8.2.1 Description of rotor blade heating ......................................................................................... 78 8.2.2 Operation............................................................................................................................... 79 8.2.3 Advantages of the use of a rotor blade heating .................................................................... 79 8.3 Shadow stop............................................................................................................................... 81 9 Starting and Stopping of the E-40 (brief instruction) .................................................................... 82 9.1 Startup of the E-40 ..................................................................................................................... 82 9.2 Stopping the E-40....................................................................................................................... 82 10 What to do if the E-40 refuses to function?.................................................................................. 83 10.1 Identifying the fault with the help of the display................................................................... 83 10.2 Tips for a restart ....................................................................................................................... 83 10.2.1 Turbine aligns itself to the wind, but fails to start ................................................................ 84 10.2.2 Turbine does not align itself to the wind properly ................................................................ 84 10.2.3 Turbine does not start although there is no apparent fault.................................................. 84 11 Annex ............................................................................................................................................... 85 11.1 Technical data of the E-40....................................................................................................... 85 11.1.1 General................................................................................................................................ 85 11.1.2 Tower specifications............................................................................................................ 86 11.1.3 Sound power level of the E-40 / 500 kW............................................................................. 87 11.2 Glossary of Technical Terms .................................................................................................. 89 11.3 Status Messages (Revision No. 28)........................................................................................ 92 Table of contents ENERCON E-40 Operation instructions SHORT DESCRIPTION OF THE E-40 The E-40 is a wind energy converter with three-bladed rotor, active pitch control and variable speed operation with a rated power of 500 kW. With its rotor diameter of 40 m and tower heights between 44 and 65 m it efficiently makes use of the prevailing wind conditions at its respective sites of operation for the generation of electrical energy. 40 m direction of rotation wind direction 65 m 1 Page 8 of 96 Figure 1: General view of the E-40, 63 m tower, 65 m hub height (sketch) Short description of the E-40 ENERCON E-40 Operating Instructions Page 9 of 96 The main focus for development and design of all ENERCON wind energy converters has been the idea of minimizing the loads. Based on that, all components have been developed and designed accordingly. The result is a turbine that convinces inter alia with its low load spectrum and its long lifetime. Power control with variable speed allows for an operation of the E-40 with optimum efficiency but without higher operating loads even in the partial load range and moreover prevents the occurance of undesirable power spikes. Therefore a good energy yield and a high quality of the power that is fed to the grid are guaranteed. 1.1 The ENERCON concept An essential feature of the ENERCON concept is the gearless drive. The key components of the E-40 are the ring generator, rotor and grid management system. The rotating part of the ENERCON ring generator and the rotor of the E-40 form a single unit. The generator is flanged directly to the rotating part of the rotor hub so that this part rotates with the same low number of revolutions. The absence of a gear box and other fast rotating components reduces energy losses between rotor and generator, sound emissions, mechanical wear and tear, oil losses and mechanical friction losses. The power generated by the E-40 generator is fed to the connected utility grid via the ENERCON grid management system while the E-40 can adapt itself to the prevailing grid parameters like grid voltage and frequency in order to guarantee the desired power quality for supporting the grid in case this is necessary. 1.2 Generator The E-40 ring generator is directly driven by the turbine rotor (rotor blades). The generator rotor is directly connected to the rotor hub and therefore does not need a bearing of its own. The E-40 generator delivers its rated power of 500 kW for the standard operation mode already at a rotor speed of 38 rpm. The multipole ENERCON generator whose operation is based on a synchronous generator has been especially designed for this purpose. By further development of a classical synchronous generator model a very high efficiency could be achieved. The E-40 generator reaches an efficiency of about 94 % over its whole range of operation. Compared to similar solutions in hydroturbine construction, the E-40 generator stands out due its low weight. Short description of the E-40 ENERCON E-40 Operating Instructions Page 10 of 96 Due to the low speed and large diameter of the generator the temperature level during operation is comparatively low and does not fluctuate much. Low temperature fluctuations during operation, low temperatures even at rated power and the avoidance of alternating loads reduce mechanical stresses and the associated ageing of the generator material. In addition, the variable speed reduces speed spikes. 1.3 Rotor The rotor blades made of fibreglass-reinforced epoxy resin are determining for the yield of the wind energy converter as well as for its sound emission. Shape and profile of the E-40 rotor blades are designed according to the following requirements high efficiency, long lifetime, low sound emission, low loads low material consumption. The E-40 rotor blades are especially designed for the operation with variable pitch and variable speed. Their special profile makes them less susceptible to turbulences and dirt at the leading edge. The outer surface of the rotor blades is protected against environmental influences by a coating on polyurethane basis. This material is abrasionproof, tenacious and resistant against chemical influence and solar radiation. The three rotor blades are adjusted via independent microprocessor-controlled pitch control systems. The pitch of the blades is continuously monitored by redundant pitch sensors and then synchronized. This allows for a quick and precise adjustment of the blade angle according to the prevailing wind conditions. 1.4 Yaw control Directly on the tower a flange plate is mounted. On this tower flange plate the king pin with a geared ring with external toothing is arranged. Two servomotors (yaw drives) engage into the geared ring in order to position the nacelle according to the wind direction. The king pin and the main carrier together form the bearing for the yaw control of the nacelle. The weight of the nacelle is passed on into the tower via two sliding blocks which are fastened to the bottom of the main carrier and supported by the tower flange plate. Short-time fluctuations of the wind direction lead to dynamic yaw moments which affect the automatic nacelle alignment. The sliding blocks (yaw pads) of the nacelle generate a moment of friction towards the tower axis which is capable of transmitting the dynamic yaw moments into the tower. Sliding blocks and tower flange plate therefore form a so-called friction bearing. Consequently, there is no load acting on the yaw control and its gears while the yaw control is at a standstill. Short description of the E-40 ENERCON E-40 Operating Instructions 1.5 Page 11 of 96 E-40 Safety System The safety system guarantees a safe operation of the turbine according to the requirements of international standards and of independent institutes such as Germanischer Lloyd or TÜV. 1.5.1 The Brake System ENERCON wind energy converters feature aerodynamic brakes only. This way of braking reduces the driving forces and moments on the turbine when braking the rotor and in return "softly" reduces the speed of the turbine. Even when not in operation, the rotor is not locked. The turbine is allowed to idle, but only at a very low speed since the rotor blades are adjusted in feathered position. Rotor and drive train remain practically free of load. A complete locking of the rotor is only actuated when using the emergency-stop switch or in case of maintenance work. Then an additional rotor brake (hydaulic disc brake) is used, which is applied only after the rotor has already been braked to some degree by the blade pitch control. The three mutually independent blade pitch drives are used for operational braking to bring the blades into feathered position ("pitch the blades out of the wind") in only a few seconds. The aerodynamic forces at the blades are lost and the rotor speed is rapidly decreased. It is important to note that in order to reduce the rotor speed to a safe level, it would be sufficient to pitch just one of the three blades out of the wind. In an emergency (e.g. in case of a failure of the utility grid), each rotor blade will be moved safely into feathered position by its own battery-buffered pitch drive. The availability of the batteries is ensured by regular battery checks and by automatic charging. The actuation of the blade pitch units via their emergency units occurs synchronously by electromechanic linking. The combination of a redundant power supply for the case of emergency (grid or battery) with three totally autonomous pitch drives offers a safety concept which perfectly meets with the requirements for two completely independent ("fail-safe") braking systems. 1.5.2 Lightning Protection System The E-40 is equipped with the ENERCON lightning protection system that deflects possible lightning strokes without causing any damage to the turbine. A lightning stroke is deflected from the rotor blade tip (or from the nacelle top, respectively) down to the earth surrounding the foundation. The rotor blade tip is made out of aluminium. Along the leading and trailing edge of the rotor blade an aluminium profile is embedded directly under the surface. These profiles connect the aluminium tip with an aluminium ring placed around the blade root near the blade flange. This ring has a sufficient distance to the conducting components of the root section so that hub and rotor bearings are protected against any consequential damage. Short description of the E-40 ENERCON E-40 Operating Instructions Page 12 of 96 Via a spark gap the lightning stroke current is transmitted from the aluminium ring to the air terminal rod and on to the rotor head. The air terminal rods, one for each of the three blades, are arranged on the rotor casing. From there, the lightning stroke currents are transmitted to the nacelle via another ring and another spark gap. Thanks to this arrangement, a lightning stroke is deflected to the supporting structure of the WEC regardless of its momentary rotor position or rotor blade angle. On the rear part of the nacelle casing another air terminal rod is mounted. Via the air terminal rods, stator jib carrier, main pin, main carrier and a sliding contact the lightning stroke current is transmitted into the tower. Via tower and the foundation the current is deflected into the ground. In case of a lightning stroke or any other unusual voltage surge (overvoltage) the complete electrical and electronic systems are protected by permanently installed energy-absorbing components. All the conductive main components of the WEC are connected permanently and solidly to the equipotential bonding strip with the shortest possible lines and sufficient cross-sections.The main terminals of the WEC are equipped with low-resistance earthed surge voltage protectors. Any interference current arriving on the lines from outside is conducted into the equipotential bonding system. The capacity of the capacitors in connection with the surge voltage protectors is sufficient to absorb the energy produced by lightning strikes. The turbine electronics are galvanically decoupled and are arranged in metal cabinets. P.c. boards with their own power supplies are provided with highly damped filters. The microprocessor and the complete control system are galvanically decoupled by means of optocoupling devices, isolation amplifiers or relays. The remote monitoring system is protected by a special protection module for data inferfaces. 1.5.3 Sensor System An extensive monitoring system ensures a safe operation of the turbine. All safetyrelevant functions are monitored electronically and in addition with mechanical sensors with higher order access. In case one of the sensors detects a severe fault, the turbine is shut down immediately. 1.5.4 Control System The E-40 control system consists of a microprocessor system developed by ENERCON that constantly monitors the sensors of the various components as well as the data of wind direction and wind speed and in return adapts the operation of the E-40 accordingly. The individual functions of the control system are in described in detail in chapter 3 (Operation). If the measured wind speed during a 3-minute interval is sufficient for operation (start-up wind speed 2.0 m/s), the automatic start-up procedure will be initiated: First approx. 10 kW are taken from the grid for a short time. Due to the type of construction and way of functioning of the generator, there are no high starting currents. As soon as the lower limit of operational rotor speed is reached, the power output to the grid will be released. During operation in the partial load range (below rated power), speed and power output are constantly adapted to the changing wind conditions. In the upper partial load range the rotor blade angle is adjusted slightly in order to prevent a breakdown of the lift-producing airflow (stall effect). Short description of the E-40 ENERCON E-40 Operating Instructions Page 13 of 96 Above the rated wind speed the power output is constantly kept at rated power by adjusting the blade angles accordingly. The necessary adjustments are determined by evaluating the measured rotational speed and acceleration data. If wind speeds of 25 m/s on an average during one minute or 30 m/s on an average during 15 seconds are exceeded, the turbine is stopped. It is only started up again if the wind speed keeps below 25 m/s continuously for at least 15 minutes. Even when the turbine is stopped, the rotor is allowed to idle at low speed. For sites with extrem strong wind speeds, it is possible to extend the operation beyond the 25 m/s range (see chapter 3.9 for details). The yaw control of the E-40 nacelle is operating at all wind speeds above 1.8 m/s (which is below the start-up wind speed). The wind vane at hub height continuously detects the wind direction. If the 1-min-average deviation of the nacelle direction compared to the measured wind direction is greater than 8°, the nacelle will be repositioned by means of the yaw motors. The yaw motion will be monitored by counting the rotations of the yaw motor and by checking the yaw time for plausibility. In case the machine is parked manually or via the control system, the blades are pitched down so that the effective surface of attack for the wind is reduced and the E-40 slowly turns to a stand-still. 1.5.5 Grid Management The grid management system converts the current generated by the E-40 generator into AC current by means of rectifiers and inverters according to the requirements and standards given by the utilities and feeds it into the grid via a transformer. The grid management unit is elastically coupled with the E-40 generator via a D.C. link. Figuratively speaking, the rotor of the wind energy converter is connected to the electric grid via a soft rubber band. This "elastic" coupling allows the electronics to balance low frequency power fluctuation so that the power output of the E40 can be controlled very precisely between 5 kW and 500 kW and no relevant 1 flicker coefficients are occuring. This combination of technologies allows a gridparallel operation without complicated grid connection conditions. Various certificates issued by independent institutes are confirming this. Depending on the phase angle of the voltage in the grid and the power output by the generator, a reference value is generated for the current to be fed to the grid. According to this reference value, the rectified current supplied by the generator is converted into alternating current and fed into the grid. This reference value is compared to the actual current (actual value) every 100 s and corrected if necessary. The shape of the current supplied is sinusoidal and largely without disturbing harmonics. A filter reduces the harmonics even further, which means that the system easily complies with the admissible limit values. The permissible operating range for grid-parallel operation is limited by the minimum and maximum grid voltage given by the respective utility. These two values (under- and overvoltage) can be preset separately as limit values for the E-40. In addition to that, minimum and maximum values for the frequency can be preset. 1 Flicker are low-frequency voltage fluctuations. In front of the tower of a wind energy converter a lee is formed as the rotor blades pass the tower, which with most WECs leads to an irregular power output and therefore voltage fluctuations. In the vicinity of a WEC, flicker can be noticed by a slight unsteadiness in the lighting. Short description of the E-40 ENERCON E-40 Operating Instructions Page 14 of 96 The E-40 immediately disconnects itself from the grid if these preset limit values are not being kept. As there are no compensating capacitors, voltage and frequency will collapse and the E-40 inverter discouples itself from the grid within a very short time. Therefore even short-term current spikes are not occuring. In addition to that, the E-40 can operate in the so-called "grid voltage-dependent power feeding" mode (optional). In this option, the grid voltage is constantly measurend and monitored. In case the voltage increases, e.g. due to lack of load during the night, the power output of the E-40 will be decreased immediately. Short description of the E-40 ENERCON E-40 Operation instructions 2 SAFETY INSTRUCTIONS 2.1 The E-40’s Safety System Page 15 of 96 The term "Safety System" describes the part of the control system that is intended to prevent malfunctions or to reduce consequential damage resulting from malfunctions to a minimum. The extensive safety system of the E-40 is described mainly in the chapters 3, 5 and 6. The other chapters of these operating instructions, however, also contain information about the control system where appropriate. 2.2 Protective measures for works on and inside the E-40 WARNING: Only persons without restrictions on physical health and fitness, e.g. caused by the use of medicines, are allowed to climb the tower and ascend to the nacelle. Persons suffering from vertigo should not climb the tower or ascend to the nacelle, either. NOTE: Accidents or other incidents that are not part of the normal operating routine of the WEC must be documented by appropriate reports. 2.2.1 General regulations and rules of conduct Until the day of commissioning, the wind energy converter remains ENERCON’s property. Until this date, the owner is strictly forbidden to enter the WEC without being accompanied by ENERCON staff. Especially during the erection of the turbine by the ENERCON erection team there is a particularly high risk of accidents. The erection team has undergone special training and is provided with all the necessary safety and rescue equipment, such as helmets and emergency abseiling equipments for the evacuation of persons from great heights. During the erection the instructions of the head of the erection team must be followed strictly. The owner should also make sure that there are no unauthorized persons inside the blocked off danger area. During commissioning, the owner or his representative will be informed by ENERCON in theory and practice about the turbine’s safety system and labour safety precautions. The owner is provided with all the necessary operating instructions and undertakes to familiarize himself with the documents. He also undertakes to instruct all persons he allows to ascend the turbine according to these documents. He must make sure that unauthorized persons do not have access to the control cabinet, the power cabinets or the tower ladder. Access doors etc. must be locked. Safety Instructions ENERCON E-40 Operating Instructions Page 16 of 96 Work on the safety equipment and the electrical system of the wind energy converter may only be carried out by especially trained service personnel. Failure to comply with this rule will lead to ENERCON’s rejection of any liability for the area affected even within the warranty period. In any case the owner is obliged to inform ENERCON Service about any alterations or repairs to safety equipment, electrical system and controls. 2.2.2 Schematic diagrams of the WEC’s safety provisions 2.2.2.1 Safety provisons of the nacelle, side view safety attachement point and steps for roof access nacelle lighting control cabinet nacelle with emergency stop button front light nacelle first aid kit winch rotor lock handle yellow hand railing access and winch hatch spinner access ladder to nacelle tower top safety attachement point safety railing upper tower door platform cable conduit Figure 2: sketch of the E-40 nacelle with steel tower Safety Instructions ENERCON E-40 Operating Instructions Page 17 of 96 2.2.2.2 Safety provisions of tower and tower base cable attachment 2 inverter cabinets hatchway to upper floor external lighting with motion detector, tower entrance upper floor lower tower internal lighting savety ladder control cabinet display louvre control panel with quick stop and main switch panic lock and door latch optional light switch fire extinguisher (optional) bord telephone access hatch to cellar access stairs Figure 3: Example sketch of an E-40 steel tower (42 m) Safety Instructions ENERCON E-40 Operating Instructions Page 18 of 96 2.2.2.3 Safety provisions of the nacelle, rear view generator touch guard generator touch guard maintenance control panel rotor lock crank handle generator touch guard generator touch guard first aid kit fire extinguisher bord telephone steps for roof access and safety points motive-power socket outlet switches for nacelle and spinner lighting, socket outlet Figure 4: sketch of the E-40 nacelle 2.2.3 First aid First aid can only be rendered quickly if the access to the turbine is kept free and if it is ensured that the turbine can be reached by car. Normally, no one should enter the WEC alone. If this cannot be avoided, we recommend to carry a mobile phone or to arrange a safety call with another person before entering the WEC. This other person should be instructed to call help if the person on the WEC does not call back within a certain pre-arranged time. The telephone in the WEC is only for internal communication between tower base and nacelle and cannot be used for emergency calls. In order to tend minor injuries, a first-aid kit is provided in the nacelle, attached to the main carrier. Any material used should be replaced as soon as possible. The manufacturers of the body harnesses also provide abseiling equipments. With this rescue equipment other persons can be evacuated, but it can also be used to let oneself down. The abseiling equipment is not included in the scope of delivery. Safety Instructions ENERCON E-40 Operating Instructions 2.2.4 Page 19 of 96 Work involving a risk of fire When carrying out any work involving a risk of fire, always take care that there are no persons above your own working position in the tower or in the nacelle. ATTENTION: For ENERCON wind energy converters only hardly inflammable material is used and there are no major fire loads in the form of combustible liquids. In case of a fire, it is theoretically possible to try to extinguish the fire with water, powder, foam and CO2. However, since none of these methods can be recommended without restrictions (keeping a minimum distance), we advise against any attempt to extinguish a fire yourself. In case of a fire, call the fire department immediately and inform ENERCON. CAUTION: In case of a fire in the nacelle or in the upper part of the tower there is a risk of burning parts falling down. Therefore, if the turbine is still working, it must be stopped immediately and a wide area around the turbine is to be blocked off. 2.2.5 Turbine shut-down in case of formation of ice With temperatures around the freezing point, ice may form on the rotor blades. Should the rotor blades be covered by a coat of ice or should icicles be formed, the owner is obliged to shut down the turbine if pieces of ice falling down from the rotor blades would present a hazard for the area around the turbine. ENERCON does not accept any liability for any type of damage or accidents caused by the formation of ice. 2.2.6 Safety instructions for persons working in the transformer- or substation and in the tower base Persons working in and on the turbine must wear helmets, especially on the climbing ladder and if there are persons working further up. WARNING: Control, power and rectifier cabinets carry hazardous electric voltages. These voltages may still be present in the components even when the main switch has been turned off. In accordance with the regulations, these live parts are protected by a touch guard (Macrolon screen) against inadvertent contact: In order to facilitate maintenance, this touch guard has not been installed permanently and can be removed. Warning: with the touch guard removed, there is a potential danger to life. The cabinet doors therefore should only be opened by specially trained persons. Control and power cabinets should always be kept locked in order to prevent unauthorized persons from opening the cabinets when the tower base is open. Safety Instructions ENERCON E-40 Operating Instructions Page 20 of 96 ATTENTION: Note that actuating the quick stop button on the control cabinet merely leads to a quick shut-down and braking of the rotor, whereas all the other systems continue to be supplied with voltage. These systems (except for the lighting in tower and nacelle and the separate socket outlets), however, can be de-energized by the main switch. Actuating the main switch alone also causes an emergency braking of the turbine. Although the turbine has been designed for emergency brakings, this method of stopping it should only be used in an emergency, since the loads acting on the turbine then are comparatively high. Since a safe manual operation of the wind energy converter requires a lot of experience, the owner should on no account carry out any adjustments on the pitch control drive and the yaw control on his own. ENERCON strictly refuses to accept liability for damages caused by improper operation of the pitch control drive, the yaw control, the hydraulic rotor brake and the rotor lock by the owner or persons authorized by him. 2.2.7 Climbing and descending the tower ladder CAUTION: For climbing the tower and descending it is absolutely necessary to use a safety gear consisting of body harness, energy absorbers (2 anchorage lines with snap hooks) and a fall arrester (also called runner), which corresponds to the following standards: 1 Body harness EN 361 DIN 7478 Form A (until 6/95) Energy absorber (anchorage lines / hooks) EN 355 DIN 32766 (until 6/95 Fall arrester (runner) EN 353-1 DIN 32770 (until 6/95) Climbing ladder EN 353-1 DIN 32770 (until 6/95 EN 354 DIN 7471 (until 6/95) EN 397 DIN 4840 (until 6/95) 2 Fasteners (lines, snap hooks) Helmet 2 Before climbing the tower, make yourself familiar with the instructions for use of your personal protective equipment. These instructions include details on how to connect the individual items with each other. Failure to comply with these instructions may endanger your life. In particular the instructions for servicing and ageing of the material should be observed. Furthermore, according to ZH 1/55 (German safety regulations), each person requiring a safety harness has to carry out a visual check of the equipment before using it. The fall arrester for the climbing ladder should be tested near the bottom for correct functioning. In order to test the proper fit of the harness, a hanging test should be carried out, also near the bottom. 1 Standards (EN and DIN) can be obtained for example from the Beuth-Verlag, Berlin (Germany) 2 Helmet and fasteners are not included in the scope of delivery. Safety Instructions ENERCON E-40 Operating Instructions Page 21 of 96 It is a general rule that the ladder should be ascended alone, i.e. the next person should only commence his ascent when the person before him has vacated the ladder at the top. A simultaneous ascent of several persons is only allowed if the persons following behind the first one wear helmets. The same applies to descending the ladder. Lighting should be provided for the complete climbing way inside the tower or, in case of an external ladder, by the outside spotlight on the nacelle which can be switched on in the ground station. CAUTION: Ascending the turbine in stormy conditions or during thunderstorms is forbidden. The same applies if the ladder steps are covered with ice. In case of a tower with external ladder, the rotor must always be stopped while someone is climbing up. On towers with internal ladder the rotor may continue to run, as long as no one steps out onto the upper tower platform. If someone intends to stand on the upper tower platform or climb further up to the nacelle, the rotor must be stopped and the machine has to switch to manual operation. For manual operation, only parts of the machine are operating, e.g. the yaw drive is stopped. Therefore, switching the machine to manual operation mode, is only allowed for low wind speeds. After ending the stay in the nacelle, the wind energy converter has to be put back into automatic operation mode. ENERCON refuses to accept any liability for damages caused by improper use of the manual operation mode. During ascent or descent both hands should be kept free and only used to hold onto the ladder. It is permitted to carry small articles in a robust, close-fitting shoulder bag. Large or heavy items must be hauled up by winch, securely fastened with ropes and hooks (see table on previous page). Wind energy converters with concrete tower are first entered via the foundation caisson by means of the removable tower base ladder. The safety climbing ladder starts on top of the foundation caisson and is secured by a ladder guard against unauthorized use. Check that the tower base ladder is placed against the caisson at an angle of approx. 70° and stands firmly. The upper end of the ladder must project at least 1 m above the upper edge of the caisson. It is the owner’s responsibility to ensure that there is a sufficiently high embankment of earth around the caisson. If the surface on the caisson is slippery, you should secure yourself to the safety ladder with an energy absorber (fasten the snap hook of the energy absorber to the guide rail), or, if a holding ring is provided at hip level, fasten the rope to this ring. If lighting is required for the ascent, the external tower lighting must be switched on at the control panel of the control cabinet in the ground station before starting to climb up. Look out for grease, oil etc. on the ladder rungs, the platform, and the nacelle floor and clean it up immediately, if necessary (danger of slipping). During the time spent on the turbine it should also be ensured that no unauthorized persons can gain access to the control cabinet, the power cabinets or the safety climbing ladder. The tower base door must always be kept locked. ENERCON steel towers are provided with special safety lock systems. The panic locks and turning knobs provided ensure that persons inside the nacelle cannot be locked in by mistake. The doors can always be opened from the inside without a key. Safety Instructions ENERCON E-40 Operating Instructions 2.2.8 Page 22 of 96 Staying on the tower platform and in the nacelle Before leaving the safety climbing ladder at the upper end and releasing the body harness from the runner, secure yourself with an energy absorber. Anchorage point when leaving the steel tower is an eye welded onto the internal tower wall next to the end of the ladder. Upon stepping out onto the tower platform, secure yourself with the energy absorber to the holding ring mounted around the tower at shoulder level. When climbing up a concrete tower with external ladder, secure yourself directly to the holding ring as soon as you reach the tower platform, before releasing the harness from the runner. When changing the anchorage point always use the second safety hook of the energy absorber to ensure that you are always secured by at least one hook. When entering or leaving the nacelle the platform hatch (in turbines with concrete towers) must be closed. Anchorage points for climbing into the nacelle are the foldaway ladder and the yellow handrail screwed to the main carrier on the left. While access hatch or winch hatch are open, all persons inside the nacelle must stay fastened. Other anchorage points are, for example, eyebolts and handles firmly attached to the main carrier or its steel components. WARNING: Handles fixed to GRP material are not suitable as anchorage points! When the nacelle hatches are closed, persons inside the nacelle may take off their body harness. WARNING: It is not allowed to remove any safety provisions. If it is necessary to remove the protective screens in front of the rotating parts, a sufficient distance to the rotor must be kept. As a general rule, all hatch covers must be closed again after passing through. Dangerous voltage may still be present in the battery cabinets on the generator rotor even when the power has been disconnected. Only specially trained service personnel is allowed to open theses battery cabinets or the rectifiers. Furthermore it is not allowed to step onto the GRP casing of the nacelle through the roof hatch. The winch may only be used for transporting material, not for persons. The manufacturers of the body harnesses also provide abseiling equipments (equipment for rescuing persons from great heights). With this rescue equipment other persons can be evacuated, but it can also be used to let oneself down. A suitable anchorage point for the abseiling equipment in the nacelle is the winch hook. The abseiling equipment is not included in the scope of delivery. 2.2.9 Rotor lock The two locking bolts engage in the rotor of the generator every 30°. If the rotor is not stopped correctly in one of these 30° positions and someone tries to lock the rotor in spite of that, serious damage to the installation may result. Therefore only trained personnel is allowed to lock the rotor by means of the crank handle in the main carrier. Furthermore, the owner and other third parties are not allowed to enter the room around the rotor hub through the generator. Safety Instructions ENERCON E-40 Operating Instructions 2.3 Page 23 of 96 Inspection of safety provisions The inspections of the safety provisions (e.g. sensors within an emergency shutdown control, emergency button, emergency lighting, ...) prescribed according to the accident prevention regulations (in Germany UVV) are mostly included in the preventive maintenance schedule carried out by ENERCON. The following inspections required according to the accident prevention regulations are not part of the ENERCON maintenance: Inspection object Reference Inspection intervals Documentation Tower base ladder1 UVV 74 § 16 (1) as required not necessary Fire extinguisher2 UVV 1 §39 (3), §43(8) at least every 6 months e.g. sticker Winch² UVV 8 §23 (1) (2) at least yearly entry in checking book Safety harness² ZH1/55, item 6.1 at least yearly e.g. sticker These four inspections are the sole responsibility of the owner. (The winch checking book is kept in the compartment above the winch). 2.3.1 Owner’s obligation to inform ENERCON If any defects in the safety provisions are detected (for example broken screw for fastening the safety climbing ladder, bent guide rail for the runner), the service department must be informed immediately. At this point we refer to the accident and incident reports mentioned under 2.2. If serious defects in safety devices are detected it is necessary additionally to post a warning against climbing the tower, e.g. by attaching a note to the door of the control cabinet. In this way you can warn the service personnel carrying out routine maintenance. ATTENTION: All work on safety systems and on the electrical system may only be carried out by service personnel specially trained by ENERCON. Failure to observe this rule will result in ENERCON’s rejection of any claims of liability even within the warranty period. As a general rule, the owner is obliged to inform the service department prior to any alterations or repairs to safety systems, electrical systems and controls. 1 only in WECs with concrete tower 2 this inspection must be carried out by an expert, acc. to the German regulations UVV or ZH1 Safety Instructions ENERCON E-40 Operating Instructions 3 OPERATION 3.1 Control and Monitoring System Blade A Blade B Blade A pitch measurement activation of pitch control motor battery charging and monitoring regulation of battery heating generator air gap monitoring (2x) rotational speed measurement monitoring of other parameters pitch measurement activation of pitch control motor battery charging and monitoring regulation of battery heating generator air gap monitoring (2x) front bearing temperature (main pin) generator temperature (rotor) monitoring of other parameters pitch measurement activation of pitch control motor battery charging and monitoring regulation of battery heating generator air gap monitoring (2x) rear bearing temperature (main pin) monitoring of other parameters Page 24 of 96 nacelle sub-distribution OWG starting / stopping the WEC operation for maintenance I slip ring casing OWG (optical waveguide) distribution rotor tower cable I OWG OWG (optical waveguide) distribution Generator excitation Customer interface (optional) fault current detection overcurrent limiting output of operating data as analog values measuring of analog inputs, output of status messages in the form of switch contacts. Grid management 1 Converter control board 1 Control of inverter, synchronization with the grid current, monitoring of grid parameters, monitoring of current in the DC link and in the inverters, control of mains contactor Control and monitoring of the step-up converter monitoring of the mains contactor, fan regulation, temperature measurement, sensor monitoring Grid management 1 Converter control board 1 Control of inverter, synchronization with the grid current, monitoring of grid parameters, monitoring of current in the DC link and in the inverters, control of mains contactor Control and monitoring of the step-up converter monitoring of the mains contactor, fan regulation, temperature measurement, sensor monitoring I / O board Supply of voltage to all sensors in the control cabinet and in the nacelle. Measurement and evaluation of analog and digital measuring data, such as wind direction, wind speed and rotational speed, stator temperature, etc. Control of relays e.g. for yaw control, main security circuit etc. MPU - Control and Monitoring Display Display of operating data, indication and location of faults via LEDs, output of status messages in numeric code and in plain text, changing of operating data, internal clock Organization of the data transmission between the processors, monitoring of the data bus, calculation of the power output reference value on the basis of the power curve, regulation of the excitation current, eveluation and processing of fault signals, starting and stopping of the WEC, measurement and monitoring of the power fed into the grid, communication with windfarm computer for data transmission Data repeater (short-distance modem) communication with windfarm computer for data transmission PC long-distance data transmission Figure 5: Survey of the control and monitoring system of the E-40 Operation ENERCON E-40 Operating Instructions Page 25 of 96 The control and monitoring system of the E-40 is a multi-processor system in which each processor controls a certain area (Figure 5). Communication between the processors is via data bus 0systems, mainly via optical waveguides. The MPU (Main Processing Unit) organizes the data exchange between the processors, evaluates fault signals and is responsible for the starting and stopping routines. It also takes care of the communication with the remote monitoring system. The E-40 is capable of monitoring a multitude of operating conditions and to check the current status of each condition. The operating data are measured by a large number of sensors, e.g. temperature sensors, microswitches, phase-angle sensors, speed sensors etc., and scanned by the control and monitoring system. Some of these sensors, e.g. those sensing the wind direction, are continuously supplying data which have an effect on the turbine operation. Other sensors check whether the operating status of the turbine is correct. Some safety-relevant conditions, such as rotor speed and generator temperature, are checked several times by independent sensors. 3.2 Display of E-40 status messages As soon as a sensor responds, the corresponding status message can be read on the LC display of the E-40 control cabinet. The main status informs about the current operating condition, and a sub-status supplies further details. Example: The LC display indicates status 10:2 The main status is described by the number in front of the colon, the substatus by the number following it. Main status 10 means "Emergency stop actuated". Sub-status 2 means "Nacelle" (here the sub-status indicates the location where the emergency stop was actuated). The status is also described in plain text. Via the remote monitoring system (see chapter 7) the status messages allow a remote diagnosis of the operating behaviour of a turbine or a whole windfarm, respectively. A status list with the E-40 status messages is enclosed in the annex to these instructions. Faults occurring in the turbine are indicated by a flashing status indicator in the display. Minor faults can be acknowledged by pressing the "acknowledge" key when the cause has been found. The turbine will then re-start automatically. Some faults can only be remedied and acknowledged by service personnel. In that case the status message in the LC display flashes. For better identification, these faults are marked with an asterisk. The following paragraphs will explain how the turbine reacts on the responding of the individual sensors. 3.3 Responding of safety-relevant sensors When a safety-relevant sensor has responded, the control system first initiates an automatic stopping procedure. The method of stopping and whether a re-start is made or not, depends on the type of fault. Operation ENERCON E-40 Operating Instructions 3.4 Page 26 of 96 Starting After switching on the main switch on the E-40 control cabinet, the LC display will soon indicate "Turbine operational" (status 0:2), providing the control system has not detected a fault. There is no specific text assigned to status 0. Only the substatus 2 (turbine ready) is indicated. The rotor blades are pitched from the feathered position (approx. 90°) to 60° position and are allowed to "idle" (see below). The turbine then turns at a rotational speed of 6 rpm max. Operation starts automatically if during three successive minutes the average wind speed is higher than the necessary start-up wind speed. By pressing the quick-start button the three-minute wind measuring can be suppressed and the start is initiated after a few seconds. The starting procedure can only be initiated when the turbine is in automatic mode, i.e. when the red lamp above the "automatic / manual" switch does not light. As soon as the starting procedure begins, the LC display shows status 0:1 (Turbine starting). Status im LC-Display: 0:1 0:2 Turbine starting Turbine operational Provided there is enough wind, the blades are pitched forward until the minimum speed for supplying power is reached. While the blades are adjusted further towards 0°, the rotor speed and thus the power output of the turbine will increase gradually. The LC display now indicates status 0:0 (Turbine in operation). 3.5 Normal operation Once the starting routine is completed, the wind energy converter is operating in normal operating mode. With increasing wind speed, the rotor speed and the power output will also increase. The pitch control units constantly adjust the blades according to the wind conditions so that an optimum operation is guaranteed. The control and monitoring system continuously determines the wind conditions, optimizes rotor speed, generator excitations and generator power, adapts the position of the nacelle to the direction of the wind and monitors all of the sensors. The standby power supplies for the pitch control drives are tested regularly to ensure their readiness for use at any time. If the wind speed is sufficient, the E-40 will reach its rated power output during the start and then continue to operate in automatic control mode. In the automatic control mode, the power output and rotor speed are kept constant at their rated values by adjusting the blade angles. For this, the appropriate blade angle changes are determined by evaluating the rotor speed measurements and are transmitted to the pitch control drives. Status in the LC display: 0:0 Turbine in operation Normally, the standard operating mode of the E-40 is the sound-optimized mode. With older turbines it is possible to change the operating mode to power-optimized via the menu of the control system. With newer versions, sound- and poweroptimized operating modes are identical. For more details, please read chapter 5.3.6. Operation ENERCON E-40 Operating Instructions 3.6 Page 27 of 96 Idling When the turbine has been shut down (e.g. due to lack of wind or faults), the rotor blades normally are in a position of 60° to the operating position. The rotor then rotates at a speed of 6 rpm maximum. As soon as this speed is exceeded, the rotor blades are pitched further towards feathered position. This operating mode is called "idling". Idling reduces loads and allows to restart the machine within a very short time. The reason for the shut-down or the idling mode is indicated by the status message (e.g. lack of wind). After switching on the E-40 at the main switch of the machine, it takes one minute until idling starts. Under the following circumstances the E-40 will not run in idling mode after it has been shut down: if stopped manually, if the operating mode is set to "manual" and the blade angles are set to 88°, in case of shadow stop in case of faults on the pitch control drives (status messages 40 - 50) and other faults (see Figure 6) such as "grid failure" (status message 76) "air gap sensor", "shear pin monitoring" and "bearing temperature" (status messages 72 - 76) as well as "data bus error" (status message 200). 3.7 Stopping The E-40 can be stopped by manual actuation of the start/stop switch, of the emergency stop button or the emergency shut-down switch. In case of faults or unsuitable wind conditions, the control and monitoring system will stop the turbine. When the turbine has been stopped, the rotor is allowed to idle in order to keep the rotor and drive train practically free of load. When responding, some sensors will cause a quick shut-down of the turbine via the emergency pitch control units. Other sensors transmit error signals to the control system. Some of these signals allow a re-start after a few minutes. The various methods of stopping are shown in Figure 6 (next page). 3.7.1 Manual stopping If the E-40 is operating, it can be stopped via the start / stop switch in the control cabinet. The control system pitches the rotor blades out of the wind and the turbine slows down until standstill. The rotor brake is not applied. The yaw control remains active to allow the E-40 to align itself properly to the wind. Before switching off the turbine with the main switch, it is absolutely necessary to stop it manually with the start / stop switch in order to pitch the rotor blades into feathered position. This is normally done by the emergency pitch control units of the rotor blades. For a reset of the turbine, press the "acknowledge" key. If this does not produce the desired result, actuate the main switch. Main status message: 1:1 turbine stopped : control cabinet Operation ENERCON E-40 Operating Instructions Page 28 of 96 shut-down normal operation failure e.g. quick-stop Emergency-stop Rotor lock Rotor brake e.g. Vibrations grid failure e.g. Overspeed Pitch control error switch to emergency power supply for pitch motors switch to emergency power supply for pitch motors switch to emergency power supply for pitch motors rapid pitching of blades to feathered position rapid pitching of blades to feathered position rapid pitching of blades to feathered position e.g. load shedding Data bus error rapid pitching of blades to feathered position e.g. Air gap monitoring Bearing temperature battery error pitching of blades to feathered position e.g. oscillation generator overtemperature overtemperature converter grid error pitching of blades to 60° (idling) e.g. Shadow stop Turbine stopped (manually) pitching of blades to feathered position e.g. Storm Lack of wind pitching of blades to 60° (idling) Application of mechanical rotor brake Figure 6: Methods of stopping the E-40 3.7.2 Manual stopping in emergency stituations If persons or parts of the turbine are in acute danger, the turbine can be stopped by pressing the emergency stop button or the quick stop button. On the control cabinet there is an quick stop button which initiates an immediate emergency braking of the rotor by means of a quick blade adjustment via the emergency pitch control units. All turbine components continue to be supplied with power. On the nacelle sub-distribution and, optionally, in the power cabinet (in versions with 42 m steel tower, upon opening the door of the power cabinet at a height of 1 m on the right) there are emergency stop buttons which in the same way as the emergency stop button ensure a quick stopping of the turbine and additionally switch off the power supply of yaw control, pitch control, excitation, winch and converter. The buttons are of the latching type; they have to be pulled back into their original position when the turbine is to be re-started and the emergency situation no longer exists. By setting the main switch on the control cabinet to the OFF position, all turbine components, except for tower and control cabinet lighting and the separate light switches and socket outlets, are de-energized. Furthermore a quick blade adjustment via the rotor blade standby power supplies is initiated. Operation ENERCON E-40 Operating Instructions Page 29 of 96 The main switch should only be actuated when the rotor has already stopped. Its principal task is to deenergize the wind energy converter for maintenance work. Main status: 3.8 10 : Emergency stop actuated Lack of wind If after the start of the turbine a mean wind speed is measured which is lower than the required start-up wind speed, status 2 will be indicated after at least one minute. Main status: 2: Lack of wind If the turbine is already in operation and the rotor speed gets too low due to insufficient wind, the rotor blades are slowly adjusted towards 60° until the rotor is idling. In that case, too, the status "Lack of wind" will be indicated. The E-40 only reassumes operation automatically when the start-up wind speed has been reached. If due to low temperatures (<3°C) there is the possibility that the anemometer may be iced, the turbine will carry out starting attempts every hour in order to test if the wind speed is now sufficient for operation. If the turbine starts and supplies power, it will change over to normal operation. However, there is no correct recording of wind speeds since the iced sensor can not transmit the wind speed properly. 3.9 Storm If the wind speed is higher than 25 m/s, the wind turbine will not start. As soon as the maximum rotor speed or the maximum blade angles are exceeded, normal operation of the turbine is stopped; the turbine changes over to the idling mode. The components of the E-40, such as rotor blades, nacelle, tower and foundation, are designed so as to withstand - depending on the actual design of tower, foundation etc. - gusts of up to 70 m/s. Main status: 3: Storm The turbine will restart automatically if the wind speed has dropped below the cut-out wind speed for a certain period of time (10 min.). This does not apply for turbines with a strong-wind power curve, also called storm-regulation. In that case the E-40 can be operated at wind speeds of up to 36 m/s. At wind speeds higher than 25 m/s, the pitch of the rotor blades is continually adjusted in order to keep the load in the admissible range. The rotor speed decreases for higher wind speeds. Up to a wind speed of 27.5 m/s the power output is kept at its rated level. At higher wind speeds up to 36 m/s the power output drops linearly to 0 kW. If the wind speed drops below 36 m/s, the turbine immediately generates power again, since it will continue to idle even at higher wind speeds and the converter remains connected to the grid. 3.10 Rotor speed monitoring (rotor overspeed) The rotor speed is permanently monitored by the control and monitoring system and adjusted if necessary. In order to protect the E-40 against damage, the rotor speed is measured and checked for plausibility by a redundant system. Operation ENERCON E-40 Operating Instructions Page 30 of 96 If due to strong gusts the rotor speed measured should exceed the rated speed by more than 15 %, an emergency shut-down will be carried out by means of the emergency pitch control units of the rotor blades. The LC display indicates main status 40 "rotor overspeed" with the corresponding sub-status stating which speed sensor was the first to record the excess speed. After 3 minutes the turbine will carry out a new starting attempt automatically. If this fault signal has been indicated more than 5 times within the last 24 hours, a new starting attempt is not made. The status signal is flashing and first must be acknowledged. In addition to the electronic monitoring, each of the three pitch control cabinets is equipped with three electromechanical switches which in case of excess rotor speed will shut down the turbine. These mechanical overspeed switches respond when the rated rotor speed is exceeded by more than 25 %. In that case, a quick blade adjustment is initiated via the emergency pitch control units of the rotor blades. An automatic re-start of the turbine is then no longer possible. The mechanical overspeed switches have to be reset manually by service personnel and the fault must be acknowledged. Main status: 3.11 40 : 41 : 48 : Rotor overspeed Rotor overspeed switch Speed sensor error Yaw control The E-40 is provided with a combined wind sensor mounted on a supporting tube with integrated lighting protection system on the upper side of the nacelle. The combined wind sensor consists of a wind vane for the continuous measuring of the wind direction and an anemometer which measures the wind speed. The yaw control system of the E-40 works at all wind speeds above 1.8 m/s. Thus it is ensured that it is operating whenever a starting attempt is made (start-up wind speed: 2 m/s). Even if the turbine has already been shut down, e.g. due to high wind speed, it is still aligned in the direction of the wind. A re-alignment takes place when the average deviation of the nacelle direction compared to the wind direction measured is greater than the specified minimum angle (8° on a 1-minute average). The yaw motion is monitored by counting the rotations of the yaw motor and by checking the yaw time for plausibility. During the re-positioning operation the rotational speed of the yaw drives is monitored by a sensor of the control and monitoring system. If the control system recognizes any irregularities in the yaw operation or the untwisting of cables (see chapter 3.12), a stopping process is initiated. The nacelle of the E-40 is supported by two friction pads. Due to the yaw operations carried out, these pads wear out in the course of time (approx. 10 years). They are monitored by a sensor which responds when the pads are worn out to such an extent that they must be replaced. In that case the turbine is stopped slowly and yaw control is blocked by the control system. Main status: 20 : 22 : 23 : Wind measurement fault Yaw control fault Yaw pads worn Operation ENERCON E-40 Operating Instructions Page 31 of 96 yaw control low wind (v < 3,5 m/s) cable untwist right deviation of nacelle position to wind direction more than 8° left (1-min average) 2 - 3 left turns of nacelle more than 3 left turns of nacelle deviation of nacelle position to wind direction more than 8° right (1-min average) yaw operation right yaw operation left cable untwist right 2 - 3 left turns of nacelle more than 3 left turns of nacelle low wind (v < 3,5 m/s) cable untwist left cable untwist left Figure 7: Schematic representation of the yaw control 3.12 Untwisting of cables The power and control cables of the E-40 are suspended in the tower in such a way that they are relieved of strain. In concrete towers they are hanging on steel cables and in steel towers they are guided over a pulley before being fastened to the tower wall with plastic clamps. In both cases the cables have enough freedom of motion to allow the nacelle to rotate several times about its own axis. If the nacelle rotates several times in the same direction, the cables gradually become twisted. The control system of the E-40 ensures that the cables are untwisted automatically. The cable twist sensors are installed in the cable twist switch which is mounted near the access hatch of the nacelle. The sensors for detecting the cable twisting are connected to the yaw gear rim. Additionally a left and a right limit switch are installed which shut down the turbine if the yaw control does not respond to the switches for uncoiling the cables. This prevents any further twisting of the tower cables. The turbine is stopped and cannot be restarted automatically. If the cables have been twisted by 2 or 3 turns, the control system takes advantage of the next period of low wind to uncoil the cables. Should this not be possible because of the wind conditions and the cables become twisted by more than three turns, the turbine is stopped and the cables are uncoiled irrespective of the current wind speed. This process takes about 25 minutes. After having uncoiled the cables, the turbine automatically starts again, provided there is sufficient wind. During the uncoiling process the display indicates main status 21 (cable twisting). The sub-status shows in which direction the cables are twisted and whether they are uncoiled at low wind speed or not. Main status: 21 : 22 : Cable twisted Yaw control fault Operation ENERCON E-40 Operating Instructions 3.13 Page 32 of 96 Emergency pitch control units of the E-40 If due to a malfunction an emergency shut-down has to be initiated (e.g. in case of a grid failure), the rotor is stopped via the emergency pitch control units of the rotor blades. Each rotor blade is provided with its own set of standby batteries which allows to bring the rotor blades safely into feathered position even in case of a complete failure of the mains supply. The discharge degree of the batteries and their availability are constantly monitored by the control system by means of regular battery checks and by automatic charging. Main status: 3.14 44 : 45 : Emergency stop battery error Battery charging fault Rotor brake If the emergency stop button in the nacelle sub-distribution or in the ground station (tower base) is pressed, an emergency stop of the E-40 is initiated. In addition to the quick blade adjustment, which starts immediately, the rotor brake is also activated in order to support the braking process. The rotor brake can also be actuated manually on the control panel of the nacelle sub-distribution. Main status: 11 : Rotor brake activated manual The rotor brake is only necessary for servicing and not required for a safe operation of the turbine since the rotor can also be stopped safely without the brake. A failure of the rotor brake during an emergency stopping process would not impair the safety functions of the turbine. 3.15 Rotor lock CAUTION: Only trained service personnel is allowed to apply the rotor lock and to go through the generator. The WEC owner is strictly forbidden to apply the rotor lock himself, because improper handling can cause damage. The rotor lock allows to mechanically lock the rotor head of the E-40 in order to carry out maintenance work. For this purpose the rotor is locked in the desired position by inserting bolts every 30°. Additionally, the rotor brake is activated automatically as soon as the rotor lock is applied. In order to avoid damage to the wind energy converter, the rotor lock may only be applied when the rotor is at a standstill and the wind speed is below 15 m/s. Never try to apply the rotor lock while the rotor is turning. This would result in an emergency stop with quick blade adjustment via the standby power supply units of the rotor blades. If the rotor lock has been applied, this is indicated by a red LED in the sectional drawing of the nacelle on the display of the control cabinet. Main status: 12 : Rotor lock Operation ENERCON E-40 Operating Instructions 3.16 Page 33 of 96 Shear pin monitoring As an additional safety feature the stator (stator ring) is fastened to the main pin with so-called shear pins. These shear pins will respond (break off) when a certain threshold (the multiple rated-load torque) is exceeded. The stator then rotates freely together with the rotor. The power and supply lines are separated by the plug-type connectors, and the stator is allowed to idle freely on the main pin. The shear pin monitoring ensures that the emergency shut-down of the turbine by means of the standby power supply units is activated as soon as this predetermined breaking point responds. This safety feature prevents that in case of a malfunction of the converters high rotational speeds may cause damage to the wind turbine. An automatic restart of the turbine is not possible. Main status: 3.17 73 : Shear pin monitoring Vibrations and Tower Oscillations The vibration sensor of the E-40 is installed in the main carrier of the turbine. It consists of a limit switch with spring steel bar at the end of which a ball is fastened with a chain. The ball rests on top of a tube end. In case of strong vibrations or shocks the vibration sensor ball will fall from its tube support and actuate the limit switch which then will release an immediate stop of the rotor via the standby power supply units of the rotor blades. Such vibrations could be caused for instance by an unbalanced state of the rotor. If the sensor responds, this is indicated by a red diode lighting up in the sectional drawing of the nacelle on the display of the control cabinet and the LC display indicates status 30 "Vibration sensor". Before a restart can be made by resetting the vibration sensor in the nacelle and then acknowledging the fault, it is necessary to find the reason first why the vibration sensor has responded. The vibration sensor primarily reacts on vibrations or heavy shock and not so much on tower oscillations. Main status: 30 : Vibration sensor The tower oscillations of the E-40 are sensed by two acceleration sensors (one in the direction of the nacelle, the other at right angles to the nacelle) by means of which the control system can measure the amplitude of the excursion from the neutral position of the tower at any time. The criterion for shutting down the turbine in case of tower oscillations is not the acceleration measured, but the actual oscillation amplitude of the tower. Depending on the tower version (height of tower, material) there are different limit values for the maximum admissible oscillation amplitude. If the tower oscillations exceeded the admissible limit value, the turbine will shut down. After a short time it will restart automatically. If within 24 hours inadmissible oscillations occur repeatedly, the turbine is stopped and no auto restart is made. The LC display then indicates the flashing status message 31 "Tower oscillations" with the respective sub-status indicating the direction (lengthwise or crosswise). Main status: 31 : Tower oscillations Operation ENERCON E-40 Operating Instructions Page 34 of 96 The availability of the acceleration sensors is constantly monitored by the control and monitoring system. Should one of the sensors be defective, the turbine is stopped immediately and no restart is made. The sub-status on the LC display indicates which sensor is defective. 3.18 Air gap monitoring The air gap of the E-40 ring generator between rotor and stator is only a few millimeters and must not fall below a certain minimum value. This minimum spacing is monitored by 6 microswitches. If the air gap should become smaller than the minimum value, the control system will initiate a turbine stop. An automatic restart is not possible. Main status: 3.19 72 : Air gap monitoring Temperature monitoring Some turbine components must be protected against high operating temperatures. Temperatures are measured by sensors installed at the appropriate places. In order to ensure a high level of safety, some of these measuring points, such as the generator, are additionally equipped with thermostats, which react as soon as a certain limit value is exceeded. The main components whose temperatures are monitored are: the ring generator (rotor and stator), the main bearings of the rotor at the hub, the emergency pitch control units (batteries) of the rotor blades, and the heat sinks in the power cabinets (rectifier and inverter). If a sensor reports an inadmissible temperature value to the control and monitoring system, a turbine stop will be initiated. The turbine will restart automatically as soon as the relevant temperature falls below a certain limit. If, however, a temperature sensor should prove to be defective, the service personnel first has to eliminate the cause before the turbine can be restarted. Main status: 44 : 67 : 68 : 70 : 76 : 80 : 95 : 3.20 Emergency stop battery error Heat sink temperature Transformer overtemperature (optional) Generator overtemperature Bearing temperature Excitation error Error temp. measurement Pitch control error The active pitch control of the E-40 serves for restricting the power generated from the wind at high wind speeds and also for braking the rotor. In the partial-load range the pitch control allows to adjust the blade angle according to the wind speed and thus make optimum use of the energy contained in the wind. When the E-40 has reached its rated power (500 kW), the rotor blades are gradually pitched out of the wind with increasing wind speed. In this way the rotor speed is controlled and the power output is restricted. Operation ENERCON E-40 Operating Instructions Page 35 of 96 ENERCON wind energy converters are braked only aerodynamically by adjusting the rotor blades. This way of braking reduces the aerodynamic lifting force and the loads acting on the blades, so that the rotor is slowed down within a very short time. The three completely independent electrical pitch control devices act are capable of pitching the blades out of the wind and bringing them into feathered position within a few seconds. When the wind energy converter is shut down, the rotor is not locked. It is allowed to idle, so that rotor and drive train remain practically free of load. The blade angles are constantly monitored by means of an angle encoder. If there are differences between the angles of the three blades or sudden changes of the measured angles, for example in case of a fault in the angle encoder, the turbine must be stopped. As a rule the blades are adjusted within a range of 88° (turbine at standstill) to 0° (turbine in operation). If due to a fault in the system a blade angle should be outside this range, limit switches in connection with the emergency pitch control ensure that the blades are always pitched back to a safe parking position, which cannot be influenced by the automatic pitch control. The rotor blade control decides on its own whether an emergency shut-down is carried out or not. In each case the LC display shows the status message "Pitch control error" together with the relevant sub-status, giving information about the cause of the fault. Main status: 3.21 42 : Pitch control error Protective circuit-breaker tripped If a protective circuit-breaker is activated due to overcurrent, this is signalled to the control and monitoring system by an auxiliary contact on the circuit-breaker, and the necessary action is initiated. In order to ensure optimum protection of the installation components concerned, the pre-set limit values on the protective circuit-breaker must not be changed. When a circuit-breaker has been released, it may only be reset after the service personnel has eliminated the cause of the fault. Main status: 3.22 90 : Protective circuit-breaker tripped Grid error Grid voltage and frequency are constantly monitored by the grid control boards of the control and monitoring system and compared with the limit values specified by the utility. If the system detects any deviations, the WEC is at once isolated from the public grid. If the grid is stabilized again and no other faults have occurred for several minutes, the WEC is automatically restarted. If a certain number of grid faults within 24 hours is exceeded, the turbine will not restart automatically any longer. In that case it is necessary to find the cause of the frequent irregularities of the grid. Main status: 60 : Grid error Operation ENERCON E-40 Operating Instructions 3.23 Page 36 of 96 Converter fault The power generated by the E-40 generator with variable frequency is converted into direct voltage by the rectifiers. In the inverters this direct voltage is converted into power with grid-synchronous voltage and frequency. To ensure optimum operation, it is necessary to acquire and evaluate a large number of data and to compare them with the specified limit values. If a fault occurs, the turbine is stopped. Whether a re-start is possible or not depends on the type of fault. Main status: 3.24 62 : 64 : 65 : 67 : 69 : Grid feeding error Overcurrent in converter Overvoltage in converter Heat sink temperature Acoustic sensor Maintenance For maintenance and repair work the E-40 can be changed over to maintenance mode. Actuating the "maintenance" switch on the control cabinet does not actually influence the functioning of the E-40, but upon setting the switch to "ON" (red signal lamp lights up), the status message 8 : 0 (Maintenance) is transmitted to the remote monitoring system. In this way it is ensured that status messages generated during maintenance and not during normal operation are not transferred to the central monitoring system. The maintenance switch is always the first switch to be set to the ON position before the beginning of any maintenance and repair work and should only be switched off when the turbine has reassumed operation and the service personnel is leaving the installation. Main status in the LC display: 8: Maintenance In addition to actuating the maintenance switch, the manual / automatic switch can be set to "manual". This interrupts the automatic yaw and pitch control. Both functions can be operated manually, which is necessary for a number of maintenance activities. Operation ENERCON E-40 Operation instructions 4 Page 37 of 96 TOWERS AND GROUND STATIONS OF THE E-40 The E-40 is supplied with either steel or reinforced concrete towers of the following versions (see also section 11.1.2 "Tower specifications"): steel tower with a length of 42 m (hub height 44 m) steel tower with a length of 44 m (hub height 46 m) steel tower with a length of 53 m (hub height 55 m) steel tower with a length of 63 m (hub height 65 m) reinforced concrete tower with a length of 42 m (hub height 44 m) reinforced concrete tower with a length of 48 m (hub height 50 m) In the past, other tower versions were also used. To find out your tower version, please check your contract documents. 4.1 Steel tower Apart from different tower lengths, there are also differences with regard to the arrangement of the electrical installations, e.g. the transformer, the medium-voltage switchgear, the low-voltage connection and the power and control cabinets. The transformer, the medium-voltage switchgear and the low-voltage distribution are normally located in a ground station next to the tower. For some towers (44 m, 55 m steel tower) it is also possible to locate this equipment in the cellar of the tower below the actual tower base. The power and control cabinets are installed in the tower base. Depending on the size of the tower, either all the cabinets are installed at the lowest level, or only the control cabinet is at the lowest level, whereas the power cabinets are arranged on the first platform. If the wind energy converter is equipped with a remote monitoring system, the computer for this system is located in a separate cabinet in the tower. The tower can be entered by a door provided with a safety lock. The safety ladder for climbing up to the nacelle is inside the tower. Also inside the tower are the control and power cables via which the nacelle is electrically connected to the ground station. The cables are guided through the basement to the transformer and switchgear station. The basement can be accessed via a hatch in the floor. For climbing and for maintenance work, lighting is provided inside the tower over its whole length. The standing platforms mounted on the inside of the tower allow the persons climbing up to rest at certain intervals. The standing platforms are also used by the maintenance personnel for checking and servicing the tower flange connections. In steel towers, control and power cables are guided over a pulley below the nacelle in order to ensure sufficient freedom of motion for twisting due to nacelle movements. Below the pulley the cables are fastened to the inside of the tower wall with plastic clamps. Towers and ground stations of the E-40 ENERCON E-40 Operating Instructions 4.2 Page 38 of 96 Reinforced concrete tower The E-40 with reinforced concrete tower has the electrical components (contol cabinet, power cabinet, transformer, switchgear, etc.) installed in a separate three-room substation. This station consists of a low-voltage room, a transformer room and a medium-voltage room. The low-voltage room houses the control cabinet, the power cabinets and the utility's meter board for imported and exported electricity. If the WEC is equipped with a remote monitoring system, the computer for this system is located in a separate cabinet. In the transformer room the voltage generated by the turbine is converted into the voltage required for the medium-voltage grid. The medium-voltage room houses the switchgear which connects the medium-voltage transformer to the public grid. The ascent to the nacelle is made via the safety climbing ladder mounted to the outside of the tower. Standing and holding rings attached to the joints of the tower segments enable the maintenance personnel to carry out servicing and visual inspection of the bolted joints. On the inside of the tower the power and control cables of the E-40 are suspended on steel cables in such a way that they are relieved of strain with sufficient freedom of motion to allow for cable twisting. Through the foundation the cables are guided to the substation. 4.3 Stations for different tower versions CAUTION: The WEC owner is strictly forbidden to carry out any switching operations on the medium-voltage switchgear. Only authorized personnel of the local utility and ENERCON personnel are allowed to carry out switching operations on the mediumvoltage switchgear. Access to the medium-voltage room is only allowed to authorized persons. In the following the three mostly used types of stations are described. Deviating versions are possible due to differing requirements at the respective locations. If your tower and the ground station belonging to it deviate from the versions described here, they are a special version tailored to your requirements. The specification can be found in your contract documents or maintenance documents and need not be discussed here because it does not affect the actual functioning of the turbine. The functions of the substation are explained by the following drawings. The safety instructions apply to all versions in the same way and must be observed by you, even if your tower / your ground station should deviates from the standard versions described here. Towers and ground stations of the E-40 ENERCON E-40 Operating Instructions Combined transformer / substation The combined transformer / substation with a floor space of 3.1 m x 2.7 m is the standard version for stand-alone WECs and is used for turbines with steel towers. In wind farms, one WEC usually is provided with a combined transformer / substation with a floor space of 4.2 m x 2.65 m whereas the other turbines are only equipped with a transformer station. The combined station unites the two functions of transformer and substation. cable cubicle LV distribution air-insulated transducer panel cable cubicle cables from wind energy converter transformer cubicle 3100 630kVA low voltage door opening medium voltage meter boards 3 * HD125 medium-voltage switchgear 4.3.1 Page 39 of 96 door 2700 Figure 8: Combined transformer / substation Towers and ground stations of the E-40 ENERCON E-40 Operating Instructions Transformer station If a stand-alone turbine with steel tower requires low-voltage metering, a transformer station with a floor space of 2.83 m x 1.73 m is used. The GKP-S1 used to be installed as a transformer station also for wind farms. For this purpose nowadays mostly the compact station MKP, which is slightly smaller, is used. door cable cubicle cable cubicle transformer cubicle door LV distribution and meter boards low voltage 630kVA transformer 2830 medium voltage switchgear medium voltage 4.3.2 Page 40 of 96 door 1730 Figure 9: Transformer station GKP-S1 Towers and ground stations of the E-40 ENERCON E-40 Operating Instructions Three-room substation WECs with concrete towers are usually provided with a three-room substation with a floor space of 4.7m x 2.2 m. Control and power cabinets are also included in the station. This station is the standard version with concrete towers and can be equipped with low-voltage metering if required. 2200 meter boards remote control (SCADA) door 4700 ENERCON power cabinet ENERCON power cabinet ENERCON control cabinet low voltage room door low voltage 630 kVA transformer transformer cubicle air-insulated transducer cubicle cable cubicle medium voltage cable cubicle transformer room medium voltage room 4.3.3 Page 41 of 96 door Figure 10: Three-room substation Towers and ground stations of the E-40 ENERCON E-40 Operation instructions 5 Page 42 of 96 CONTROL AND POWER CABINETS CAUTION: Control and power cabinets must always be kept locked. They carry hazardous electric voltages and must not be opened! In power cabinets, these voltages may still be present in the components even when the main switch has been turned off. 5.1 Power cabinet In the power cabinet of the E-40 the electric energy generated with variable voltage and frequency is converted into electric energy with voltage and frequency as specified by the utility and in accordance with the requirements of the grid. During this process, the current is first converted into direct current by the rectifiers and then into three-phase alternating current by the inverters. By means of a filter the alternating current thus generated is smoothed according to the utility's specifications. The power fed into the grid is monitored and controlled electronically by microprocessors. There is a continuous exchange of data between the power cabinet and the control cabinet, in which reference and actual data are compared and the power output can be controlled according to the requirements. 5.2 Control cabinet / display The control cabinet houses the microprocessor-controlled electronics for monitoring and controlling the E-40. A display on the control cabinet supplies information about all the current operating conditions of the WEC. b c d e f m/s wind speed rpm rotational speed kW power kWh electrical energy h operating hours generator temperature generator error G1 G2 a G3 g rotor lock overspeed (rotor) shear pin emergency stop vibration sensor G4 cable overtwist limit switch G5 yaw pads F1 F2 F3 ENERCON Dreekamp 5 26605 Aurich F4 F5 emergency stop activated rotor brake active yaw control error pitch contol error power output error excitation error grid error blade pitching in blade pitching out yaw control right yaw control left grid connected h Figure 11: The display on the E--40 control cabinet Control and power cabinets ENERCON E-40 Operating Instructions Page 43 of 96 Below the display the operator panel of the E-40 is arranged. By means of the operator panel (see section 5.4) it is possible to make adjustments on the WEC via the control cabinet. The following text describes the display (Figure 11) in detail. a) LC display On the LC display the current operating conditions of the WEC are indicated. The display is activated by pressing one of the function keys (G1-G5 or F1-F5) and switches off automatically after a few minutes. Via the function keys a number of turbine parameters can be read and modified. Certain parameters can only be changed when entering a service code. A detailed description of the adjustments that can be made is given under section 5.3. b) Wind speed Indication of the current wind speed as measured by the anemometer on top of the nacelle. The wind speed is measured in meters per second (m/s). c) Rotational speed Indicates the current rotor speed in revolutions per minute (rpm). d) Power Indicates the power currently fed into the grid in kilowatt (kW). e) Electric energy Indicates the energy generated up to the present time in kilowatt hours (kWh). In case of a loss of voltage (turbine shut-down) the meter reading is stored permanently (for several years). f) Operating hours Indicates the operating hours (h) the turbine has accumulated up to the present time. Only the hours in which the power was more than 0 kW are counted. These data, too, are stored in case of a loss of voltage. g) Sectional drawing of nacelle Red LEDs visually indicate the most important faults and operating conditions. h) LED panel In this panel important faults are indicated visually by red LEDs. The green LEDs signal the control and operating conditions of the turbine in normal operation. Control and power cabinets ENERCON E-40 Operating Instructions 5.3 LC display and menu functions 5.3.1 General instructions Page 44 of 96 The LC display is activated by pressing one of the function keys G1-G5 or F1-F5 and switches off automatically after a few minutes. The main menu has the following structure: Date : 23.02.98 E-40 Time : 10:35:11 ENERCON Dreekamp 5 26605 Aurich Germany Monday Current status: Nr.: 1: 1 Turbine stopped control cabinet since: 23.02.98 10:31:36 menue Via the function keys the individual menus are activated and turbine parameters can be read and / or changed. Some menus can only be read (e.g. mains values). Other menus allow changes of the pre-set values (e.g. clock). In some cases (e.g. mains parameter) a special code known only to service personnel must be entered. The menues for the setting of kilowatt hours and operating hours are only visible, when entering the service code. This is a mere precaution to prevent any misuse of the installation. The menues for the blade heating system and the shadow stop are only visible if the corresponding optional equipment is installed. CAUTION: In order to avoid operating mistakes, switching operations on the LC display of the control cabinet should only be carried out by trained personnel. Menus are selected by pressing one of the function keys G1 to G5. By pressing the END key the main menu is reached. The following diagram shows which settings can be made in which menu and / or which data can be read. A detailed description of the menus is included in the following paragraphs. Menu items and setting possibilities may deviate from the diagram shown here due to the ongoing development of installation engineering or due to different optional features. Control and power cabinets ENERCON E-40 Operating Instructions main MENU mains start delay menu: start delay mains parameters menu: mains data mains values menu: mains data Page 45 of 96 end adjust menus operat. adjustments The submenus of the menu "operat. adjustments" differ according to optional features and the date of production blade heating system menu: blade defroster power optimization menu: power optimization shadow stop menu 1: shadow stop menu 2: shadow stop clock menu: time / date display set kWh menu: set kilowatt hours Menues available only when entering service code. set operat. hours menu: set operating hours adjust contrast menu: adjust contrast language menu: language end end service menus Menus in which turbine parameters can be requested; Settings can be changed after entering a service code Menus in which turbine parameters can be requested and / or changed pitch data menu: pitch data version numbers menu: version numbers hardware options menu: hardware options display info / tests menu: program info end end Figure 12: Schematic representation of menu structure (see also text) Control and power cabinets ENERCON E-40 Operating Instructions 5.3.2 Page 46 of 96 Menu "start delay" mains start delay. It shows the The menu "start delay" is accessed via menu time for a start delay after a grid error or grid failure. The standard value is 0. Usually, there is no need to change this value. The value can be changed only if the service code has been entered. CAUTION: An incorrect value for start delay may reduce the energy yield of the turbine. 5.3.3 Menu "mains parameters" The menu "mains parameters" is accessed via menu ters. The menu has the following structure: M a i n s p a r a m e t e r s ============================== Nom. voltage : 230V Min. voltage : > 207V < (-10.0%) Max. voltage : 255V (+11.1%) Power limitation voltage : 250V (+ 8.6%) Nom. frequency: 50.00Hz Min. frequency: 49.60Hz Max. frequency: 50.40Hz Access locked ! mains mains parame- cursor up cursor down current value enter new value end By pressing the keys select up / select down individual parameters can be selected. When a parameter has been selected, it can be changed within certain limits, provided the service code has been entered. For changing, the keys parameter up / parameter down and standard parameters are used. By means of the key present parameter you can change back to the original value. By pressing accept parameter the new value is confirmed and stored. CAUTION: Incorrect grid parameters can endanger the safe operation of the turbine on the utility grid or reduce the yield of the turbine. Control and power cabinets ENERCON E-40 Operating Instructions 5.3.4 Page 47 of 96 Menu "mains data" mains mains values. The menu The menu "mains data" is accessed via menu "mains data" includes the actual values of the voltages for all three phases and the actual frequency value. Values are given separately for each converter and also as the average of both converters. The limit voltage value is also indicated. Ajustments cannot be made. 5.3.5 Menu "blade defroster" (optional) adjust menus operational The menu "blade defroster" is accessed via menu adjustments blade heating system. If a rotor blade heating is not installed, this menu is not available. A detailed description of the rotor blade heating is given in section 8.2. The menu "blade defroster" has the following structure: end B l a d e d e f r o s t e r ============================ automatic : ein Heater : inactiv automat. off start manuell Heatingdur.: 1:00:00 New time 1:01:00 +/- : +hour +minute enter heating duration +second By setting the key automatic on / off to on, the rotor blade heating is set to automatic mode. It can also be operated manually. In automatic mode the rotor blade heating switches itself on as soon as a temperature 2 °C is measured and at the same time one of the following criteria is fulfilled: the turbine does not start repeatedly although the wind speed is above the start-up wind speed tower oscillations are more than normal. Control and power cabinets ENERCON E-40 Operating Instructions Page 48 of 96 If the rotor blade heating is not in automatic mode, it can be started manually by pressing the key start manual. By pressing the same key again (now "stop manual"), the rotor blade heating is switched off again. This of course can also be done while the blade heating is in automatic mode. After pressing the key adjust heating duration the duration of heating in automatic mode can be selected or changed. For normal conditions it makes sense to select a value of one hour. It is not guaranteed for shorter durations, that the rotor blades get defrosted if the temperature outside is much less than 0 °C. Changing the heating duration is done by pressing +/- hour, +/- minute, +/- second. Pressing the key +/- causes a switch from + to -. The time selected is stored as the new heating duration by pressing enter heating duration. 5.3.6 Menu "power optimization" (optional) In older versions of the E-40 it is possible to choose between sound-optimized and power-optimized (or yield-optimized) mode. With the newer versions, the sound emission in power-optimized mode has been reduced to such an extent that the distinction is no longer necessary. Since the new versions are always operated in power-optimized mode, the menu "power optimization" does not exist in these turbines. adjust menus operaThe menu "power optimization" is accessed via menu power optimization. The menu "power optimization" has the tional adjustments following structure: end P o w e r o p t i m z a t i o n ================================ Power optimization start/ stop time from: 7:00:00 o’clock to : 22:00:00 o’clock old time Power-optimization : on Power-optimization : activ enter time on/off +/- +hour +minute +second "Power optimization on / off" indicates whether this mode has been chosen at all. "Power optimization active / inactive" indicates whether it is active at the moment. Control and power cabinets ENERCON E-40 Operating Instructions Page 49 of 96 The standard operating mode of the older E-40s is the sound-optimized mode. Via the control system menu the operating mode can be changed to "poweroptimized". The power optimization can also be activated via a time switch. In this way it is possible to operate the E-40 in power-optimized mode during the day, and in sound-optimized mode at night, when certain low sound emission values must be observed. The power optimization is activated via On/Off. It is necessary to define the period during which the turbine is to be operated in power-optimized mode. Press the start / stop time key to determine whether you intend to change the beginning or the end of that period. The times are changed by pressing the +/- hour, +/- minute, +/second keys. Pressing the key +/- causes a switch from + to -. The time selected is stored as by pressing enter time. Before confirming the new time it is possible to reestablish the old value by pressing the key old time. Via on / off the power optimization can be deactivated at any time. The times entered remain stored. 5.3.7 Menu 1 / 2 "shadow stop" (optional) If required, ENERCON wind energy turbines can be equipped with a shadow shutdown feature. The shadow shutdown feature is described in more detail in section 8.3. 5.3.7.1 Menu and menu settings adjust menus operational You can access the “Shadow stop” menu via menu shadow stop. Operation of the shadow stop feature is divided beadjustments tween two menus. Read off the settings and/or values of the current and the stop light intensity in shadow stop menu 1. Furthermore you can see from the display what the current status of the shadow stop function is, i.e. whether it is on or off, active or inactive. Access menu 2 from menu 1. Use menu 2 to input the stop times. Control and power cabinets ENERCON E-40 Operating Instructions Page 50 of 96 5.3.7.2 Functions in shadow stop menu 1 The following variables are shown in shadow stop menu 1: S h a d o w s t o p ==================== end Act. light intensity : 50% intens. up Stop Intensity : 51% Shadow stop : on Shadow stop : inactiv intens. down on/off menue2 Looking at the light intensities, a low percentage value means a low light intensity and a high percentage value indicates strong light intensity. "Shadow stop on/off" indicates whether the function is active. Use the on/off button to switch the function on or off "Shadow stop active/inactive" shows whether the turbine is currently switched off because of shadow conditions. If the actual light intensity is equal to or higher than the stop light intensity, the wind turbine automatically stops during the time entered in menu 2, as long as the shadow stop function is set to "on". If the turbine is stopped because of shadow formation, the status “active” is displayed in shadow stop menu 1. Conversely, if the turbine is not stopped because of shadow formation, the LC display shows “inactive”. While the turbine is stopped, the main menu of the LC display gives the following status message: Status: 4 : Shadow stop You can use the Intens. up and Intens. down keys to alter the value of the stop light intensity. The shadows cast by the rotor blades become weaker with increasing distance and at some point they become completely insignificant, so shadow formation at greater distances is only irritating if the light intensity is high. On average, 60 % can be assumed to be a reasonable value for the stop light intensity. However, this value must be set in accordance with the local circumstances. Control and power cabinets ENERCON E-40 Operating Instructions Page 51 of 96 Even after the turbine has been stopped, the light conditions are still constantly measured. The turbine starts again automatically if the stop light intensity is undercut for a duration of 10 minutes or if the shadow has moved far enough to ensure that shadow formation is no longer a problem. 5.3.7.3 Functions in shadow stop menu 2 Use menu 2 to edit the times during which shadow stop is activated when the sun shines. S h a d o w s t o p ==================== from to 13.02 --.---.---.---.---.---.---.---.---.---.---.-- 7.03 --.---.---.---.---.---.---.---.---.---.---.-- value No: clear all from 12:21:15 --:--:---:--:---:--:---:--:---:--:---:--:---:--:---:--:---:--:---:--:---:--:-- to >12:52:39< --:--:---:--:---:--:---:--:---:--:---:--:---:--:---:--:---:--:---:--:---:--:-- up down enter value 1 menue1 +/- +hour +minute +second A maximum number of 64 values can be entered here. A value consists of a start and an end date as well as a start and stop time. You can enter values in any order. Overlapping values are permitted, but they should be avoided for the sake of clarity. You can alter, add to or delete previously entered values at any time. Use the Clear all key to delete all entered values. You have to confirm the delete process by double-clicking the key. Once the values have been deleted in this way they are lost. When the shadow stop feature is programmed for the first time, all the values it may already contain should be deleted to ensure that the turbine is not switched off at the wrong times. Use the up and down keys to scroll through the values. The current value is marked by two arrows. The current number of the value is shown in the bottom lefthand corner of the LC display. Press the Edit key if you want to enter or alter a value. This activates the start date. Now the menu for entering the date appears next to the F1 - F4 keys. Use the corresponding keys (+day, +month) to enter the day and month of the start date you require. Press the +/- key to switch between +day/+month and -day/-month. Press Control and power cabinets ENERCON E-40 Operating Instructions Page 52 of 96 delete to delete the current value and to leave the input mode. Press the enter value key to adopt the start date and to activate the input mode for the end date. The input procedure here is the same as for the start date. Once the end date has been adopted, the menu bar automatically changes. Now you can enter the start and stop times. Proceed in the same way as for entering the date. When the values have been entered, press the up or down keys to save the new values and leave the input mode. All values must be in local time (winter time). The control system for the turbine automatically takes account of leap years, so it th is important when entering periods of time in February to enter the 29 if this is the th start or end date. If a period of time is only entered e.g. up to 28 February, the th shadow stop function will not operate in a leap year on 29 , if the next period starts st on 1 March. You can use the remote monitoring system at any time to check the times for the shadow stop function at a later date. 5.3.8 Menu "time / date" adjust menus You can access the “time / date” menu via menu pressing the time / date key you can switch between time and date. clock. By The new time is changed by pressing the key +/-hour, +/-minute, +/-second. Use the +/- key to switch between + and -. Press the enter new time key to adopt the newly set time. The procedure for setting the date is the same as for setting the time. 5.3.9 Menu "set kilowatt hours" Access to the menu "set kilowatt hours" is only possible if you have entered the adjust menus display set kWh. This menu service code. Then press menu is needed to re-enter the old kwh value if it has been necessary to replace the display. The actual value of the kilowatt hours is constantly being displayed by the kwh indicator (part of the display). 5.3.10 Menu "set operating hours" Access to the menu "set operating hours" is only possible if you have entered the adjust menus display set operating hours. service code. Then press menu This menu is needed to re-enter the old value if it has been necessary to replace the display. The actual value of the operating hours is constantly being displayed by the kwh indicator (part of the display). 5.3.11 Menu "adjust contrast" adjust menus display The menu "adjust contrast" is accessed via menu adjust contrast. In the "contrast control" menu the current contrast of the display is shown in %. Use the keys F1 - F5 (dark, darker, standard, lighter, light) to change the contrast. Press the enter new value key to adopt the newly set contrast. Control and power cabinets ENERCON E-40 Operating Instructions 5.3.12 Page 53 of 96 Menu "language" adjust menus display lanThe "language" menu is accessed via menu guage. Use the keys Deutsch and English to switch between German and English user guidance for all menus. Press the adopt language key to adopt the new language. 5.3.13 Menu "pitch data" The menu "pitch data" is accessed via menu service menus pitch data. It is only required for servicing purposes. Under "pitch data" the following variables are displayed for all three rotor blades: alpha-act. alpha-ref. motor speed. motor corr. control status: test value 1 / 2 / 3 [set blade angle in °] [reference value for the blade angle in °] [motor speed in internal measuring units] [correction value for motor speed] [internal status code] [Service values] Use the key save value to stop the display of current values and to indicate the last value permanently. By pressing the same key again (then shown as release value the current values are indicated again. By means of the keys "test values 1 / 2 / 3" the service personnel is able to enter certain values for testing (e.g. counting) to the pitch control which can also read on the display of the control cabinet. The key "value pos/neg" is used to determine the sign of these values. 5.3.14 Menu "version numbers" service menus version The menu "version numbers" is accessed via menu numbers. This menu shows the control system version numbers for MPU, I/O board, excitation controller, pitch control, display, synchronization and customer interface (optional). Synchronization only exists in older turbines. It may happen that not all values are properly set. 5.3.15 Menu "hardware options" service menus hardware The menu "hardware options" is accessed via menu options. This menu shows certain features of the sensor system with which the E-40 is equipped. 5.3.16 Menu "program info" The menu "program info" is accessed via menu service menus display info / tests. This menu supplies information about the version number of the display and some related information. The LED red key is used to check the functioning of all red LEDs on the display, the LED green key is for checking the green LEDs. Press the scroll LED key repeatedly to check if each LED responds one after the other. Press the scroll LCD key to check if the LC displays for wind speed, power output etc. indicate all the values correctly. After leaving the menu the LC displays will go back to their original values. Control and power cabinets ENERCON E-40 Operating Instructions 5.4 Page 54 of 96 Control cabinet operator panel CAUTION: In order to avoid operating mistakes, switching operations on the operator panel of the control cabinet should only be carried out by specially trained personnel. side view of emergency stop butten emergency stop not actuated a b c quick start error reset quick stop e Start Stop d blade out n o maintenance on manual on g f off main switch h on maintenance j tower ext. lighting emergency stop actuated blade in i left stop right manual automatic k yaw control m l Figure 13: Control cabinet operator panel It is emphasized here that a change-over to manual mode (by setting the "manual / automatic switch" to "manual") while the turbine is running, may only be carried out by skilled personnel for the purpose of testing and servicing, to ensure a safe operation of the turbine. In manual mode the control system of the turbine is working only to a limited extent and it is therefore not allowed to change over to "manual" when the rotor blades are not in feathered position, i.e. pitched out of the wind. Control and power cabinets ENERCON E-40 Operating Instructions Page 55 of 96 Generally speaking, the manual operation of the rotor blades requires profound knowledge of the E-40. The control elements "d", "h" and "i" therefore may only be operated by skilled personnel. a) Quick start By pressing the quick start button the usual starting routine can be shortened (see chapter 9.1). The wind measurement normally carried out before the turbine starts is suppressed and the turbine starts already after a few seconds. Since there is no wind measurement, it is absolutely necessary to align the nacelle in the direction of the wind (manually or automatically). A quick start is only possible if the following conditions are fulfilled: the main switch of the turbine has been set to "on" the start / stop switch is in position "start" the turbine is in automatic mode no fault has been signalled After a quick start the display and the whole installation should be observed until the turbine is operating in automatic control mode. b) Error reset Faults are signalled on the LC display with the status code and in plan text. It is important also to pay attention to faults that are of secondary importance. When the cause of the fault signal has been found, the turbine can be re-started by pressing the "error reset" key. The turbine will re-start automatically. However, if the malfunction was not eliminated, the same fault signal is likely to appear again. Some faults can only be reseted when the cause of the fault has been eliminated and a service code is entered. In that case the status message in the LC display will flash. For better identification, these fault messages are marked with an asterisk, too. The fault has to be inspected by a serviceman who knows the service code and also has the necessary means to eliminate the cause of the fault. c) Quick stop By pressing the quick stop button a quick shut-down and braking of the rotor is initiated while all the other systems continue to be supplied with power. The purpose of the quick stop button is to protect persons and turbine components in emergency situations. The button is of the latching type; it has to be pulled back into its original position when the emergency situation no longer exists and the turbine is to be re-started. The quick stop button on the control cabinet must not be mixed up with the emergency stop button (shut-down of all the systems). On the control panel of the nacelle sub-distribution emergency stop button is installed which in the same way as the quick stop button ensures a quick shut-down of the turbine and additionally switches off the power supply of yaw control, pitch control, excitation, winch and converter. Control and power cabinets ENERCON E-40 Operating Instructions Page 56 of 96 d) Blade in, blade out These keys allow a manual operation of the E-40 rotor blades. By pressing the plus-key (blade in) the blade is pitched forward and by pressing the minuskey (blade out) the blade is pitched back. For safety reasons it is not possible at high wind speeds to pitch the blades forward to such an extent that the rotor would exceed the allowed rated speed. In such a case the turbine will withdraw the blades automatically. e) Start / Stop The start / stop switch is used to either start the turbine when it is stopped or to stop the rotating turbine. With the switch in the "start" position, the starting can only begin if the following conditions are fulfilled: the main switch of the turbine has been set to "on" the turbine is in automatic mode the turbine is ready for operation and no fault has been signalled during three successive minutes a wind speed sufficient for start-up was measured. In the "stop" position the control system will cause the blades to move towards feathered position via the pitch control drives. The rotor speed will decrease until the turbine has come to a standstill. f) Maintenance Before carrying out any repair and maintenance work or switching operations, the maintenance switch must be set to "on". This is indicated by the red signal lamp "n". The maintenance switch should only be switched off again when the turbine has reassumed operation and the service personnel is leaving the installation. Actuating the "maintenance" switch on the control cabinet does not actually influence the functioning of the E-40, but it ensures that status messages generated during maintenance and repair work are not passed on to the data transmission computer and evaluated. The remote monitoring system connected merely receives a message that maintenance work is being carried out. g) Main switch Via the main switch the entire installation is supplied with voltage. Only the tower and control cabinet lighting as well as the obstruction lighting (optional) are provided with a separate power supply. The main switch is mainly used to deenergize the electrical systems to be able to carry out maintenance work. If the main switch is actuated while the turbine is running, an emergency braking with quick blade adjustment via the emergency pitch control units (batteries) of the rotor blades will be initiated. This applies also if the turbine is in idling mode. To avoid this, the main switch should only be actuated if the rotor has been stopped previously by actuating the start / stop switch (rotor speed: 0 rpm) and the rotor blades are in feathered position. For a turbine reset first the "error reset" key must be used and then the main switch. Control and power cabinets ENERCON E-40 Operating Instructions Page 57 of 96 h) Manual / automatic If this switch is set to "manual" (red signal lamp "o" lights up), the automatic yaw control and pitch control will be largely inoperative. Yaw control and pitch control can then be operated manually. At high wind speeds, however, the control system ensures that the blades cannot be pitched forward to such an extent that the rotor would exceed the allowed rated speed. The manual operation mode is mainly used for maintenance work. This switch operates in a two-way circuit with an identical switch located on the nacelle sub-distribution. i) Yaw control In manual operation the yaw control switch is used to turn the nacelle clockwise or anti-clockwise. The nacelle remains in the position set until it is aligned to the wind either by hand or by changing over to "automatic" mode. An exact alignment to the direction of the wind in order to avoid any diagonal direction of flow is possible only in the automatic mode (normal operation). j) External tower lighting This switch is used to turn the spotlight at the bottom of the nacelle on and off. The switch operates in a two-way circuit with an identical switch in the nacelle. Internal tower lighting (optional) Is used to switch on and off the tower lighting inside E-40 steel towers. k) Hooter nacelle When the hooter key is pressed, an acoustic signal is sounded in the nacelle signalling that someone wants to make a phone call to the person in the nacelle. For talking, only the receivers in the nacelle and ground station, respectively, have to be picked up. l) Hooter ground station If someone signals from the nacelle that he wants to make a phone call, an acoustic signal is sounded. m) Bord telephone Allows telephone conversations between persons in the nacelle and in the gound station. For talking, only the receivers in the nacelle and ground station, respectively, have to be picked up. n) Maintenance "on" Signal lamp lights up when maintenance switch is set to "on". o) Manual "on" This signal lamp lights up when the turbine is in manual operating mode. Control and power cabinets ENERCON E-40 Operation instructions 6 Page 58 of 96 THE NACELLE (THE MACHINE HOUSE) With the ring generator and rotor the nacelle houses two key components of the turbine. Also arranged in the nacelle are the pitch control units, the standby power supplies, the slip ring casing, the nacelle sub-distribution, the winch etc. 6.1 Arrangement of components in and on the E-40 nacelle pitch control cabinet battery cabinet relay cabinet wind sensor anemometer vane rotor blade generator stator blade adapter control cabinet nacelle stator jib carrier generator rotor pitch motor main bearing winch slip ring casing yellow hand railing hub main pin main carrier yaw motor tower Figure 14: Sketch of the nacelle (cross-section) The king pin onto which the main carrier of the nacelle is privoted connects the nacelle to the tower. The king pin is provided with a geared ring with external toothing. Two yaw drives with their driving pinions mesh with the geared ring and thus allow the nacelle to rotate. The nacelle itself rests on two friction pads, which by the moment of friction generated against the tower axis, are capable of transmitting the dynamic yaw moments into the tower without putting any strain on the yaw drives. The nacelle is entered from the upper tower platform through a hinged hatch with fan-type sliding grid in the rear part of the nacelle (see also figure 2 in chapter 2). The hinged hatch, which is secured with a bracket, first has to be released. Then you can enter the nacelle via a three-piece folding ladder attached to the hatch. For safety reasons it is necessary to close the fan-type sliding grid after having entered the nacelle. By opening a second sliding grid arranged behind the first one on the The nacelle (the machine house) ENERCON E-40 Operating Instructions Page 59 of 96 bottom of the nacelle and the hatch beneath it, an opening is made through which material can be hauled up with the winch. Persons standing on the tower platform, on the folding ladder or in the nacelle with the sliding grids open, always must be secured at least by a fall breaker. The nacelle roof is provided with a hinged hatch above the main carrier which allows the maintenance personnel to have access to the wind sensor and (if the turbine features obstructions lighting) to the lamps. The safety equipment provided in the nacelle includes in particular a first-aid kit, a carbon-dioxide fire extinguisher, an emergency stop button, which initiates an immediate shut-down of the turbine, and a bord telephone for the communication between nacelle and ground station / tower base (see figure 2 and figure 4 in chapter 2). 6.2 Description of important components in the rotor head The rotor head includes all the components that belong to the rotating part of the generator and are supported by the main pin. 6.2.1 Slip ring casing The slip ring casing is attached to the front end of the main pin. Via the slip ring casing the control and power lines of the rotor head are connected with the stationary part of the machine. The slip ring casing also houses a speed sensor which supplies pulses for mesuring the current rotor speed to the pitch control unit. 6.2.2 Pitch control unit The pitch control unit adjusts the angles of the rotor blades. Each pitch control motor is controlled via relays and is provided with its own control system and a separate standby power supply. Each of these three components is encapsulated in a small metal cabinet. To each rotor blade therefore three small metal cabinetes are assigned: 1 battery cabinet, 1 pitch control cabinet and 1 relay cabinet. These cabinets are mounted on the rotating part of the generator near the blade connections. Also installed on the rotating part of the generator is the rotor subdistribution which distributes the voltage supplied via the slip ring casing. Information from or to the control cabinet in the tower base is transferred to the slip ring casing via the rotor sub-distribution by means of optocouplers. The pitch systems communicates via optical waveguides. Apart from the above-mentioned elements, the entire pitch control system consists of the following components: pitch control motor with flanged gearcabinet, blade flange bearing (connection hub - blade adaptor) and angle encoder with limit switches. The nacelle (the machine house) ENERCON E-40 Operating Instructions Page 60 of 96 6.2.2.1 Pitch control cabinet The control system in the pitch control cabinet processes the sensor information from the rotating part relevant for the pitch control controls the pitch of the blades and drives the servomotor for the pitch control. The pitch system also checks the discharge degrees of the batteries of the respective standby power supply and carries out the charging. The battery heating is supplied with power also via the pitch control cabinet. Battery voltage and battery temperature are checked and the charging current is adjusted accordingly. Moreover, each pitch control cabinet contains a mechanical overspeed switch (centrifugal switch) which, when activated, changes the pitch control motor over to the standby power supply of the blade so that the blade can be pitched out of the wind. As soon as the emergency pitch control (standby power supply) is activated, the pitch control cabinetes are separated from the pitch system. Supplied with power by the battery cabinetes, the rotor blades are brought into feathered position as quickly as possible. When the rotor blades reach the limit angle, the power supply will be changed back to mains / automatic control mode. The data supplied by the speed sensor in the slip ring casing are evaluated and used as a basis for calculating the rotor speed and rotor acceleration. Based on these control data, on the absolute blade angle and on the blade angles of the other two rotor blades, the new blade angle to be adjusted is determined. Should a fault occur, this will be reported immediately to the central processor (MPU) in the ground station control cabinet and the necessary measures will be initiated. Via angle encoders the blade angles adjusted of the three rotor blades are constantly monitored and can be compared by the pitch control systems. Additionally, the pitch control system monitors all the sensors of the rotor head, such as the temperature of the generator rotor. 6.2.2.2 Battery cabinet The battery cabinet houses a charge-monitored set of batteries. In an emergency, e.g. power failure or other malfunctions, the rotor blades can be pitched out of the wind by means of these batteries. 6.2.2.3 Relay cabinet The relay cabinet establishes the electrical connection between pitch control and servomotor or battery, respectively. The relay cabinet contains contactors for changing over the servomotors from battery to normal operation and vice versa. In order to ensure a synchronous operation of the three pitch control units, the change-over between pitch control unit and standby power supply always is carried out simultaneously for all three blades. 6.2.2.4 Pitch control motor The rotor blades of the E-40 are rigidly connected to the blade adaptors. These in turn are pivoted by a four-point contact bearing on the blade hub. On the E-40, the The nacelle (the machine house) ENERCON E-40 Operating Instructions Page 61 of 96 individual rotor blades are adjusted (pitched) simultaneously but independently of each other by means of DC motors with integrated brakes. The electric pitch control motor is mounted to the side of the blade adaptor and turns the rotor blade via a gearing that meshes with the external gear of the blade flange bearing. The pitch motors are controlled via the relay cabinet. 6.2.2.5 Angle encoder The blade angles are checked by means of angle encoders. The angle encoder allows to check the blade angle with an accuracy of 0.09° and then to synchronize the other rotor blades accordingly. Should the angles of the different rotor blades deviate by more than 0.2° from each other, this will result in a complete turbine shutdown. The angle encoder is installed in the compact limit switch in the centre of the blade adaptor near the transition to the hub. The compact limit switch contains several switches which are needed to prevent any adjustment of the rotor blade beyond its working range and to stop or start the emergency braking process. 6.3 Operator panel of the E-40 nacelle sub-distribution The nacelle sub-distribution is mounted to the main carrier of the nacelle. All the control lines leading through the tower as well as the control and supply lines of the rotor head, which are guided across the slip ring casing, end in the nacelle subdistribution. The control elements are arranged on the cover of the sub-distribution. The nacelle (the machine house) ENERCON E-40 Operating Instructions Page 62 of 96 side view of emergency stop butten emergency stop not actuated a c b blade B Blade out of limit position blade in quick start d e blade out j rotor brake release off g gency s er p to blade C em blade A emergency stop actuated f k left on rotor brake stop right manual automatic yaw control h i Figure 15: Operation panel on the nacelle sub-distribution 6.3.1 Description of the nacelle sub-distribution control elements CAUTION: In order to avoid operating mistakes, switching operations on the operator panel of the nacelle sub-distribution should only be carried out by specially trained personnel. The nacelle (the machine house) ENERCON E-40 Operating Instructions Page 63 of 96 It is emphasized here that in order to ensure a safe operation of the turbine at all times, a change-over to manual mode while the turbine is running should only be carried out by skilled personnel for the purpose of testing and servicing. In manual mode (red signal lamp is on) the control system of the turbine is working only to a limited extent and it is therefore not allowed to change over to "manual" when the rotor blades are not in feathered position, i.e. pitched out of the wind. Generally speaking, the manual operation of the rotor blades requires a profound knowledge of the E-40. The relevant control elements (a, b, d) therefore should only be operated by skilled personnel. WARNING: Persons staying inside the rotor head without the rotor lock being applied risk their lives. It is therefore forbidden to enter the rotor head through the generator without first having applied the rotor lock. a) Blade A, blade B, blade C By means of these keys the service personnel can adjust the rotor blades individually for testing and servicing purposes. To be able to use this function the rotor lock must be applied completely. Then it is possible to adjust a single blade by pressing one of the keys "blade A", "blade B" or "blade C" together with the key "blade in" or "blade out". b) Blade out of limit position If a rotor blade has been pitched beyond its normal feathered position, one of the fault messages "Limit switch ..." (42) will appear on the LC display or the remote monitoring system. In order to move the blade out of this position, the keys "blade out of limit switch" and "blade in" have to be pressed simultaneously in "manual" mode. Then all three blades will move forward, including the one in the limit switch position. Then all three blades should be moved towards their new feathered position by pressing the minus key. c) Emergency stop Upon pressing the Emergency stop button, an emergency braking of the rotor with quick blade adjustment via the emergency pitch system of the rotor blades is initiated. The rotor brake is also activated. Additionally this button, in contrast to the quick stop button on the control cabinet, switches off the power supply of yaw control, pitch control, excitation, winch and converter. The button is of the latching type; it has to be pulled back into its original position when the emergency situation no longer exists and the turbine is to be restarted. d) Blade in, blade out These keys allow a manual operation of the E-40 rotor blades. By pressing the plus-key (blade in) the blade is pitched forward and by pressing the minuskey (blade out) the blade is pitched back. For safety reasons it is not possible to pitch the blades forward to such an extent that the rotor would exceed the allowed rated speed. In such a case the turbine will withdraw the blades automatically. The nacelle (the machine house) ENERCON E-40 Operating Instructions Page 64 of 96 e) Quick start By pressing the quick start button the usual starting routine can be shortened. Without the quick start key the wind speed is measured for three successive minutes before the starting process begins. By pressing the quick start key, this wind measurement is suppressed and the turbine starts already after a few seconds. A quick start can only be initiated from the nacelle if the start / stop switch on the control cabinet of the ground station is in position "start" and the turbine is operating in automatic mode. If the start / stop switch on the control cabinet is set to "start" and the quickstart key is actuated in the nacelle, the turbine will start and remain in operation until the quick start key is pressed again. If the start / stop key on the control cabinet is set to "stop", which should normally be the case while somebody is inside the nacelle, it is still possible to start the turbine via the "quick start" key in the nacelle, providing, however, that the "maintenance" switch on the control cabinet has been set to "on". If there are no fault messages, the turbine will start. It will stop again as soon as one of the following events occur: 1. The quick start key is pressed again. 2. The start / stop switch on the control cabinet is set to "start" and then to "stop" again. 3. The maintenance switch is set to "off". 4. Automatically after 10 minutes at the latest. The turbine remains in operation if within 10 minutes after the quick start the start / stop switch on the control cabinet is set to "start". f) Hooter When the hooter key is pressed, an acoustic signal is sounded in the ground station signalling that someone wants to make a phone call to the person in the ground station. For talking, only the receivers in the nacelle and ground station, respectively, have to be picked up. g) Release brake, rotor brake For carrying out maintenance work on the generator, the rotor hub, the slip ring casing or other components of the rotor head it is necessary to apply the rotor lock. In case of a failure of the power supply the rotor brake is released. Therefore it is not allowed to enter the rotor without first applying the additional rotor lock. Since the locking bolts of the rotor lock can only be inserted in the corresponding holes of the generator rotor disc, the rotor first has to be braked hydraulically by means of brake pliers and a braking disk. The brake is activated as soon as the emergency stop / quick stop button is pressed. The red signal lamp "j" indicates that the brake has been activated. The brake can also be activated manually by setting the rotor brake switch to "on" and deactivated by setting the switch to "of" (signal lamp "j" goes out). The nacelle (the machine house) ENERCON E-40 Operating Instructions Page 65 of 96 By means of the key "rotor brake release" the rotor brake is released briefly. This key is only effective if the rotor lock is set or partly set. This makes it possible to carry out small corrections of the rotor position so that the bolts can snap into place. h) Manual / automatic If this switch is set to "manual" (red signal lamp "k" lights up), the automatic yaw control and pitch control will be largely inoperative. Yaw control and pitch control can then be operated manually. At high wind speeds, however, the control system ensures that the blades cannot be pitched forward to such an extent that the rotor would exceed the allowed rated speed. This manual operation mode can be used for carrying out maintenance work. This switch operates in a two-way circuit with an identical switch located on the control cabinet. i) Yaw control In manual operation the yaw control switch is used to turn the nacelle clockwise (right) or anti-clockwise (left). The nacelle remains in the position set until it is aligned to the wind either by hand or by changing over to "automatic" mode. An exact alignment to the direction of the wind is possible only in the automatic control mode. The nacelle (the machine house) ENERCON E-40 Operation instructions 7 Page 66 of 96 REMOTE MONITORING Individual ENERCON wind energy converters or windfarms (see figure 16) are equipped with a remote monitoring and control system. With individual wind energy converters this system is installed near the control cabinet or in the substation, in windfarms it is normally installed in the substation. The hardware required for the remote monitoring is a standard PC configuration. ENERCON Service provides a central remote monitoring system which polls the individual wind energy converters and windfarms to obtain current operating data, allows to change turbine parameters by remote control and receives fault signals and warnings. Please not, that the operation single wind turbines as well as wind farms are able to operate without the wind farm monitoring system. The remote monitoring system is not part of the control system of the wind energy converters. sub station control system E-40 E-40 E-40 ... RS 232 Repeater surge voltage protector 4-conductor data cable datapuffer data repeator for distances > 1 km UPS optional surge voltage protector modem surge voltage protector Figure 16: Remote monitoring system for windfarms On windfarms, the turbine data are transmitted to a PC (windfarm computer) by means of a short-distance modem. The windfarm program collects the data of the individual wind energy converters. Windfarms are equipped with communication lines which connect each wind energy converter with the remote monitoring system. The PC is provided with a modem for the telephone network to be able to communicate with other computers. From the remote monitoring system at the wind energy converter or on the windfarm, current operating data are transmitted to the central monitoring system Remote monitoring ENERCON E-40 Operating Instructions Page 67 of 96 via telephone or mobile phone networks by means of a modem. Additionally, (central) remote monitoring and control systems can be installed at the owner’s home office. In the following, the term "wind farm" will be used both for wind energy converter and for wind farm. A full description of the remote monitoring system is given in the wind energy converter monitoring program description. 7.1 System components The standard equipment delivered by ENERCON with each wind energy converter is the remote monitoring system installed in the turbine plus a city call receiver 1 (pager) for the owner. Currently , the remote monitoring system consists of the following components: computer: state-of-the-art standard PC, currently 586 or faster; hard drive approx. 500 MB; 4 MB RAM; monitor, black and white; four-conductor telecommunication cable between each wind energy converter and the remote monitoring computer (to be provided by owner); 28,800 bps Hayes-compatible modem; interface: ENERCON ENERCON remote monitoring software for windfarm including 1 license. The equipment actually delivered depends on the current state of the art and may exceed this standard considerably. The connection between windfarm and the remote monitoring centre is established via telephone (modem). The telephone connection must be provided by the owner. Mobile phones (GSM or C-network) may also be used. 7.1.1 Optional equipment Optionally, the remote monitoring computer can be equipped with an uninterruptible power supply (UPS). Another option is an additional central monitoring system for the owner which allows the owner to scan all the data of his wind energy converters. If this option is chosen, the system currently would comprise the following components: computer: state-of-the-art standard PC, currently Pentium 120 or faster; hard drive approx. 1 GB; 8 MB RAM, graphics card, CD-ROM (8-fold speed); operating system Windows 95; 15" color monitor (low radiation); 28,800 Hayes-compatible modem; keyboard, mouse, mousepad; ENERCON remote monitoring software for central monitoring system (including three licenses). It is also possible to use the owner's own computer with licenses if all the hardware pre-requisites are met. 1 The exact configuration of the remote monitoring computer is constantly changing according to the latest state of the art in PCs. Remote monitoring ENERCON E-40 Operating Instructions Page 68 of 96 Upon delivery, the system will be completely installed. The equipment actually delivered depends on the current state of the art and may exceed this standard considerably. 7.2 Additional monitoring systems In addition to the individual wind energy converters, a meteorological station (wind measuring mast), the substation or additional power or voltage controls can be connected to the remote monitoring system. 7.3 Scope of monitoring The remote monitoring system allows the display and statistical evaluation of many data accumulated during the operation of the turbines, such as wind speed, rotational speed, power and energy generated. These data can be evaluated statistically for various periods of time. The data are normally stored in a binary format. However, it is also possible to convert them into dBase IV format and thus evaluate them according to individual criteria e.g. by means of a spreadsheet program. By evaluating the online data, permanent monitoring of the WECs and in particular a comparison between different WECs within a windfarm are possible. 7.3.1 Wind energy converter The following table shows the standard calculation and output of data. The output intervals are permanent (online), minutely, quarter-hourly, daily, monthly and yearly. Parameter Unit Value calculated Wind speed m/s average, peak Rotational speed rpm average, peak1 Power kW average, peak1 Phase angle 1 pre-set value Operating hours h accumulated Energy generated kWh accumulated Nacelle direction degree average, main direction Main status, sub-status - availability A graphical representation of the data is also possible.The following pictures will show, by way of example, the different methods of representation in which the data can be displayed on the remote monitoring computer in the windfarm, on the owner's computer and on the central monitoring system at ENERCON. The screen forms are standardized and are the same for the turbine types E-30, E-32/33, E-40 and E-66. The following exemplary graphs refer to the turbine type E-40. 1 Peak values are values actually measured, not based on calculations Remote monitoring ENERCON E-40 Operating Instructions Page 69 of 96 Figure 17: Online comparison of wind, rotational speed and power of a turbine Figure 18: Graphical evaluation of the quarter-hourly data of a day Remote monitoring ENERCON E-40 Operating Instructions Page 70 of 96 Figure 19: Graphical evaluation of the data of one month Figure 20: : Distribution of the wind directions of one day Remote monitoring ENERCON E-40 Operating Instructions 7.3.2 Page 71 of 96 Wind farm For wind farms, it is possible to compare the individual turbines of a windfarm with each other or to select certain individual turbines. The following graphs will show, by way of example, the different methods of representation in which the data can be shown. Figure 21: Comparison of operating hours and energy yield in tabular form Figure 22: Online power comparison Remote monitoring ENERCON E-40 Operating Instructions Page 72 of 96 Figure 23: Turbine comparison of daily yield 7.3.3 Substation (optional) Provided the substation is monitored under an power / voltage control system (see 7.2), the following data can be displayed or calculated: 7.3.4 Parameter Unit Value calculated main status, sub-status - availability energy generated kWh accumulated active power kW average, peak reactive power (not yet available) kVA average, peak voltage L1 kV average, peak voltage L2 kV average, peak voltage L3 kV average, peak Meteorological stations (optional) Where an additional meteorological station (wind measuring mast) has been installed and is monitored (see 7.2), the parameters listed in the following table can be recorded. The calculation intervals are permanent (online), minutely, 10minutely, daily, weekly, monthly and yearly. Remote monitoring ENERCON E-40 Operating Instructions 7.4 Page 73 of 96 Parameter Unit Value calculated wind m/s average, peak wind direction ° average, main temperature °C average, peak atmospheric pressure hPa average, peak air humidity % average, peak Main status, sub-status - availability System messages System messages are divided into several areas depending on the type of event. 7.4.1 Status messages Depending on the operating condition (e.g. "in operation" or "fault X"), each WEC is assigned a two-digit status message (see also chapter 3). For a detailed description, there is a main status (e.g. "emergency stop actuated") and a sub-status ("nacelle"). The operating condition is indicated by an unequivocal combination of numbers (in our example 10 : 2). A complete and updated list of status messages can be obtained from ENERCON and is also included in the annex to these operating instructions. 7.4.2 Malfunctions (faults) In case of a malfunction in the turbine, the remote monitoring system automatically informs the owner and the Service, provided this option has been activated in the system. If a malfunction occurs in a turbine of a windfarm, a message is immediately transferred to the Service Head Office via modem. The windfarm computer must be connected to the telephone network. For a successful transfer of the message, the corresponding telephone number must be known to the program and the software of the central program must have been started. In case of a failure of transfer, the program tries again to send a fault message every quarter hour until the transfer is successful (for a maximum of six hours). Fault messages will be sent for the following malfunctions: 1. Turbine shut-down (due to a fault which can only be remedied by Service or by the owner); 2. Status changes repeated three times within a critical time during a malfunction not leading automatically to a full shut-down of the turbine; 3. Transmission error between turbine and windfarm computer; 4. Turbine does not respond; 5. Simulation of a fault message on the windfarm computer; 6. No power despite wind > 4 m/s. Remote monitoring ENERCON E-40 Operating Instructions Page 74 of 96 Faults 2 - 6 are warnings for which the routine program is interrupted automatically. The messages listed under items 2, 3 and 4 are not safety-relevant and therefore do not activate the pager or the fax. 7.4.3 Fault messages In case of a fault message, the following data are transferred to the central monitoring system and stored (see Figure 24). windfarm identification turbine no. time of the fault message type of malfunction (fault) status message (main status, sub-status) last quarter-hourly data (average wind speed, energy generated, average / maximum power, average / maximum rotational speed) the last 15 minutely data (time, main status / sub-status, average / current wind speed, energy generated, average / maximum power, average / maximum rotational speed). Figure 24: Fault messages In case of a fault, the minutely average data of the last 15 minutes are displayed automatically. Otherwise, the older data are overwritten by new data (ring-type memory). Remote monitoring ENERCON E-40 Operating Instructions 7.5 Page 75 of 96 Transfer The data and status messages supplied by the wind energy converter can be transferred by fax, telephone (modem), SMS and various pager systems. As soon as a turbine shuts down because of a malfunction, several fault messages can be sent to up to four receivers. 7.5.1 Fault message to central monitoring system (office computer) In case of a fault message, the data listed above (see 7.4) are transferred via the windfarm monitoring system to the central monitoring system at the Service station. If the owner is also connected to the monitoring system, he will also receive the message. 7.5.2 Fault message to fax All fault messages that are send to a PC can also be sent to a fax. 7.5.3 Fault message to SMS or pager (city call) The program provides the possibility to connect to the City Call of German Telekom. The City Call number is then dialled by the central computer or the windfarm computer directly after having received the fault message. The City Call can either be activated without sending any further data or it may include transmission of a numerical fault code. 7.6 Control The following parameters can be controlled by the central computer of the monitoring system: Start or stop of the windfarm (maximum) power output of the individual or the turbine windfarm (in case there is a power / voltage control system for the substation) power gradient (change of power output as a function of time) for starting and stopping routines of the windfarm or the individual turbine). 7.7 Other functions If an automatic data request could not be completed successfully (e.g. due to a bad telephone line), the missing data of the respective day can be requested manually and then included in the data processing subsequently. A transfer protocol (protocol of modem connections) can also be provided. 7.7.1 Transfer protocol At each attempt to establish a connection, the transfer protocol registers the windfarm number, date, time, type of connection and the data transfer. With automatic data requests, only failed attempts are registered and colour-marked in the protocol. The transfer protocol always lists the last 120 messages. Remote monitoring ENERCON E-40 Operating Instructions 7.7.2 Page 76 of 96 Requesting of missing data The central monitoring program can request missing data automatically. The program tries to retrieve the missing data up to three times per windfarm. Irrespective of this, the 'missing' entry in the transfer protocol is deleted. If the automatic data request fails or if there has not been an automatic data request for a prolonged time, the missing data can also be requested manually. Remote monitoring ENERCON E-40 Operation instructions 8 OPTIONAL EQUIPMENT 8.1 Obstruction lighting / Hazard beacon Page 77 of 96 Depending on the authorities' requirements and on the geographical situation of the turbine (e.g. vicinity to an airport / airfield) it may be necessary to install an obstruction lighting or hazard beacon on the turbine. At present, ENERCON wind energy converters can be equipped with four different types of obstruction lighting. Please check your contract documents to find out if your turbine is equipped with obstruction lighting and with which type, if this the case. 8.1.1 Obstruction lighting with standby power supply and monitoring The obstruction lighting with standby power supply consists of double lights with a lamp wattage of 2 x 100 W and a mean intensity of light of at least 10 cd in the horizontal radiation range. The standby power supply consists of lead storage batteries providing a stored energy time of at least 10 hours in case of a failure of the utility's network. The lights are installed on top of the nacelle at a distance of 1.5 m from each other and in such a way that they are clearly visible from all directions. Thanks to the distance between the lamps they cannot be covered and blocked from view by a rotor blade when the rotor is at a standstill (lack of wind). The lamps are switched on by a photo-electric lighting controller. The obstruction lighting can be supplied with electrical energy alternatively by two phases of the three-phase current, which means that if one phase should fail, the other phase automatically takes over the power supply. The lighting system is also provided with a fault indicator output which will send a signal to the control system in case of a fault. The following malfunctions are indicated: failure of one / both supply voltages (phases), failure of one / both lights, failure of the photo-electric lighting controller, fault in the battery charging device, failure of the batteries and fault in the air-conditioning. The electronics for the obstruction lighting are installed in a fully air-conditioned cabinet in the nacelle. On the outside an on-off switch and a fault signal and operation signal lamp are mounted. Inside the cabinet a switch is provided by means of which the lighting can be changed from automatic mode to manual mode for maintenance purposes. An operating hour meter installed in the cabinet registers the operating hours of the obstruction lighting. 8.1.2 Obstruction lighting without standby power supply, but including monitoring All functions are identical with section 8.1.1, but without standby power and airconditioning. Optional Equipment ENERCON E-40 Operating Instructions 8.1.3 Page 78 of 96 Obstruction lighting without standby power supply and without monitoring This lighting system also consists of double lights with a lamp wattage of 2 x 100 W and a mean light intensity of at least 10 cd in the horizontal radiation range. This lighting model has no monitoring feature for a possible failure of the lights or phases. The lights remain switched on 24 hours a day. A switch is provided for switching the lights off for maintenance purposes. 8.1.4 Flashing hazard beacon with standby power supply and monitoring If due to its height or geographical situation the wind energy converter should constitute a particular hazard to aircraft in flight, ENERCON can provide the turbine with special hazard beacon. This system consists of two red medium-intensity lights that are flashing synchronously and are mounted in a staggered arrangement on top of the nacelle. The light intensity per flashing light is 2,000 cd in horizontal radiation direction at a power consumption of 250 W. The flashing rate is 30 flashes per minute. The service life of an electronic-flash lamp is two years. In case of a network failure the flashing obstruction lighting will be supplied by an adequately dimensioned standby power supply. The standby power supply is connected to the network by a static bypass switch. Failures of the standby power supply, flashing light or control system are signalled to the remote monitoring system via potential-free contacts. The hazard beacon are switched on and off by a photo-electric lighting controller in accordance with ambient light conditions. 8.2 Rotor blade heating At some locations and with certain weather conditions, ice may form on the rotor blades of wind energy converters. The formation of ice on the rotor blades impairs the aerodynamic characteristics and therefore also reduces the energy output. In case of a heavy formation of ice there is also the risk that pieces of ice are thrown off the rotor blades and constitute a hazard for the area around the turbine. Irregular formation of ice on the three rotor blades results in an unbalance of the rotor which may cause tower oscillations. The rotor blades of the E-40 are designed so that ice formation does not constitute a hazard with regard to inadmissible loads. Ice is mainly formed when temperatures are around freezing point and the atmospheric humidity is high. Ice formation usually occurs on the leading edges of the rotor blades. The operation of the rotor blades is described in more detail in section 5.3.4. 8.2.1 Description of rotor blade heating The rotor blade heating warms the blade up from the inside. The temperature on the outside rises to values above freezing point and the ice will begin to thaw. Optional Equipment ENERCON E-40 Operating Instructions Page 79 of 96 ENERCON rotor blades have internal compartments divided by spars. These spars allow to direct a flow of air along the edges of the rotor blade. The heating of the rotor blades is performed by a heater fan installed near the blade flange.The air heated by the heater fan is conveyed through a short pipe towards the leading edge of the rotor blade, from there it will flow to the blade tip and then back towards the blade flange along the trailing edge. Then the air is heated up again and conveyed back into the rotor blade (recirculating air system). In each rotor blade one heater fan is installed. Figure 25 shows how the rotor blade heating is installed. 8.2.2 Operation The rotor blade heating is activated when outside temperatures equal to or less than 2°C are measured and when at the same time there are indications of a formation of ice on the rotor blades, a fact that can only be established indirectly. Ice formation on the rotor blades will impair the aerodynamic characteristics of the rotor blades. If the turbine fails to start repeatedly in spite of the wind speed being clearly above the start-up wind speed, this indicates that ice may have formed on the blades. Moreover, ice on the rotor blades often causes an unbalance of the rotor which in turn leads to tower oscillations. Of course, the rotor blade heating can also be operated manually. If the control system of an ENERCON wind energy converter equipped with a rotor blade heating detects formation of ice on the rotor blades, the turbine will stop automatically and activate the heating in order to defrost the blades. After defrosting, the turbine will re-start automatically. The rotor blade heating is dimensioned so as to be able to thaw the ice on the blades with a comparatively low heating capacity. The heating is not able to prevent the formation of ice from the start, because this would require a permanent operation of the heating. 8.2.3 Advantages of the use of a rotor blade heating Since the control system detects a formation of ice at an early stage, the rotor blade heating can prevent that the turbine runs with iced rotor blades for a prolonged period of time or that it has to be shut down. The energy yield, which is produced is increased. The risk of pieces of ice being thrown off the blades is considerably reduced, especially since defrosting takes place while the turbine is at a standstill. For reasons of liability, however, ENERCON cannot guarantee that the use of the rotor blade heating will altogether eliminate the risk of larger pieces of ice slipping down from the turbine. The control of the rotor blade heating is still being refined. Experience gained with the heating up to now seem to indicate that the rotor blade heating can considerably reduce periods of standstill and loss of yield due to the formation of ice on the rotor blades. Optional Equipment ENERCON E-40 Operating Instructions Page 80 of 96 tip rotation direction spar trailing edge piping leading edge heating device fan flow of air air tube blade adapter blade flange Figure 25: Sketch of rotor blade heating Optional Equipment ENERCON E-40 Operating Instructions 8.3 Page 81 of 96 Shadow stop Whenever this is required, all ENERCON wind energy turbines can be fitted with the control system for the shadow stop feature. This can be necessary when the turbines are located in the direct vicinity of buildings. The basis for the shadow stop function is provided by calculated times in which shadow formation can occur as a result of the angle of the sun and the geographical position of the turbine, and which can consequently lead to irritation for people living or working near the turbine. These times are entered in the control system. If the shadow of the rotor reaches a certain building and/or point on the ground, the turbine can be stopped until the shadow has moved away from the building or the point. Parallel to the pre-set times, a light sensor determines the light intensity and recognises whether a shadow is cast. Only if the brightness during these times exceeds the pre-set value is the shadow shutdown function activated. You can operate the shadow stop function using the LC display (see section 5.3.7). Optional Equipment ENERCON E-40 Operation instructions 9 Page 82 of 96 STARTING AND STOPPING OF THE E-40 (BRIEF INSTRUCTION) Before starting to operate the E-40, it is absolutely necessary that you read the chapters 2, 3, 5 and 6. 9.1 Startup of the E-40 If the main switch on the control cabinet is not already in the "ON" position, set it to "ON". The "manual / automatic" switch must be set to automatic. Main switch ON Then set the "start / stop" switch to "start“ . Start Stop The starting routine begins automatically after several minutes of wind measurement or: When you have set the "start / stop" switch to "start", press the "quick start" button. Quick start This suppresses the wind measurement and the starting process begins already after a few seconds. 9.2 Stopping the E-40 In order to stop the E-40, set the "start / stop" switch to the "stop" position. The turbine stops. Do not actuate the main switch for this purpose. Start Stop Starting and Stopping of the E-40 (brief instruction) ENERCON E-40 Operation instructions 10 Page 83 of 96 WHAT TO DO IF THE E-40 REFUSES TO FUNCTION? The control and management system of the E-40 allows to operate the turbine with a high degree of availability and security. The precise fault diagnosis of the control system allows the owner to delimit the fault by means of the display on the control cabinet and to give detailed information to the Service department about the fault symptoms, when necessary. If the wind energy converter is connected to the remote monitoring system, the Service department is normally able to make a remote diagnosis. It may even be possible for the owner to put the turbine back into operation by following instructions given by the Service department over the phone. Should it not be possible to restart the turbine via the operator panel, the owner can carry out a visual inspection of the turbine and thus give valuable information to the Service staff regarding the possible cause of the fault. WARNING: On no account should the owner try to put the turbine into operation by carrying out measurements in the control cabinets or exchanging electronic or mechanical components without having consulting the Service department. These tasks may only be carried out by specially trained Service personnel. Always be aware that components, plates, terminals etc. may carry dangerous voltages. 10.1 Identifying the fault with the help of the display The LC display is activated by pressing one of the function keys (G1-G5 or F1-F5) and switches itself off automatically after a few minutes. On the activated LC display a fault is indicated stating main status and substatus and a short description of the fault. If the status message on the LC display is flashing and marked with asterics, this means that there will be no automatic restart and the Service has to fix the fault. A continuous fault indication means that the E40 will automatically attempt to restart after a short time. Important fault messages are additionally indicated by red LEDs in the sectional view of the nacelle and in the LED overview of the display. Attached to these operating instructions you will find a status list of the E-40 to facilitate the identification of the status messages. 10.2 Tips for a restart With some faults a restart of the turbine is not possible before the fault in question has been eliminated. This chapter contains helpful information in case a restart should not be possible. Please read also chapter 9.1 (Starting the E-40). What to do if the E-40 refuses to function? ENERCON E-40 Operating Instructions 10.2.1 Page 84 of 96 Turbine aligns itself to the wind, but fails to start The first thing to do is to check on the LC display which status message is given. If the status display is not flashing and the cause of the fault is no longer there, the E-40 should resume operations after a few minutes, providing the wind speed is sufficient (more than 2 m/s), but does not exceed 30 m/s. If the turbine still fails to start, the complete control system can be reset by pressing the "quit error" key. If the turbine still does not resume operations after approx. 3 minutes or after pressing the "quick start" key, the turbine should be stopped by actuating the start / stop switch and setting the main switch to OFF. After 2 or 3 unsuccessful attempts to reset and restart the turbine via acknowledgement key and main switch, the service department should be informed. If a fault has occurred that could be acknowledged by a turbine reset, there may still be a malfunction in the turbine which must be eliminated. Therefore, if the same fault signal appears again repeatedly, you should contact the Service department. Some faults can only be reseted when the cause of the fault has been eliminated and a service code is entered. In that case the LC display will flash. For better identification, these fault messages are marked with an asterisk. The fault has to be inspected by a serviceman who knows the service code and also has the necessary means to eliminate the cause of the fault. 10.2.2 Turbine does not align itself to the wind properly It is important to check first whether the "manual / automatic" switch on the control cabinet is in the automatic mode (red signal lamp does not light), because otherwise an automatic yaw control is not possible. If the automatic yaw control is activated, the cause of the fault may be a faulty wind indicator. The cause of the fault should be identified and eliminated by Service personnel. 10.2.3 Turbine does not start although there is no apparent fault If there is sufficient wind, the control system should be reset for at least 5 seconds by switching off the main switch. Before actuating the main switch the turbine must be stopped by setting the start / stop switch to "stop". After 5 seconds, switch on the main switch. If the turbine does not start automatically in four minutes at the latest, reset the control system once more and attempt to start it with the "quick start" button, after first checking the nacelle position and aligning it with the wind, if necesary. If there is still no response, the Service department must be informed. What to do if the E-40 refuses to function? ENERCON E-40 Operation instructions 11 ANNEX 11.1 Technical data of the E-40 11.1.1 General Rated power: Power (10 m/s): Start-up wind speed: Tower height Overall height: Overall weight: Generator: Rotor speed: Power control: Yaw control: Type of rotor: Braking systems: Direction of rotation: Blade weight Blade length Number of blades Blade material Blade profile: Rotor weight (with hub): Rotor diameter: Swept area: Nacelle weight (without rotor) Page 85 of 96 500 kW 323 kW 2.0 m/s 42 - 63 m 64 - 85 m approx. 116.5 t (for concrete tower, 42 m) ENERCON ring generator, synchronous with variable frequency, type of protection IP 23 variable, 18 - 36 rpm pitch active through adjustment gears, damped through friction bearings upwind rotor three independent pitch-control systems clockwise approx. 1 t 18.9 m 3 fiberglass-reinforced epoxy ENERCON 13.6 t 40.3 m ² 1.275 m 12.9 t Annex ENERCON E-40 Operating Instructions 11.1.2 Page 86 of 96 Tower specifications Versions Designation Length of tower Steel towers E-40/S/42/2 E-40/S/44/2/01 E-40/S/44/2/02 E-40/S/49/3 42.0 m 44.2 m 44.2 m 49.0 m 44 m 46 m 46 m 50 m , bottom flange 2.606 mm 2.948 mm 2.710 mm 2.738 mm , top 1.200 mm 1.200 mm 1.200 mm 1.200 mm Weight 35.9 t 35 t 32 t 43.8 t Segments: 2 2 2 3 Height [m] 21/ 21 22.5/ 21.7 22.5 /21.7 21/ 21/ 7 Weight [t] 11.7/ 24.2 12/ 23 12 /20 11.7/ 20.3/ 11.8 No. of platforms 4 3 3 5 extr. gust (5 sec) 70 m/s 70 m/s 56 m/s 54.8 m/s Wind class (GL) / Wind zone (DiBT) I/ IV I/ IV II / III II / III Hub height Corrosion protection zinc spraying (zinc epoxy coating), with threefold top coat on the outside and twofold top coat inside Ascent safety climbing ladder installed inside the tower Versions Designation Steel towers E-40/S/53/2 E-40/S/53/3 E-40/S/56/3 E-40/S/63/3 53.4 m 53.4 m 56.0 m 63 m 55 m 55 m 58 m 65 m , bottom flange 2.948 mm 2.948 mm 2.948 mm 3.228 mm , top 1.200 mm 1.200 mm 1.200 mm 1.200 mm Weight 44 t 36 t 53.4 t 61.5 t Segments: 2 3 3 3 Height [m] 28.4/ 25.0 18.0/ 18.0 / 17.4 21.0/ 21.0/ 14.0 21.0/ 21.0/ 21.0 Weight [t] 17/ 27 7.6/ 10.8/ 17.6 11.7/ 20.3/ 21.4 11.7/ 20.3/ 29.5 No. of platforms 3 4 4 4 extr. gust (5 sec) 56 m/s 50 m/s 55.6 m/s 56.3 m/s Wind class (GL) / Wind zone (DiBT II / III II / III II / III Length of tower Hub height Corrosion protection Ascent zinc spraying (zinc epoxy coating), with threefold top coat on the outside and twofold top coat inside safety climbing ladder installed inside the tower Annex ENERCON E-40 Operating Instructions Versions Reinforced concrete towers Designation E-40/B/42/2 E-40/B/48/3 E-40/B/53/03 E-40/B/63/3 Length of tower 41.5 m 47.8 m 53.3 63.6 m Hub height 43.1 m 49.3 m 54.9 65.2 m , bottom 1.780 mm 1.940 mm 2.140 mm 2.140 mm , top 984 mm 1.020 mm 1.128 mm 1.020 mm Weight 90 t 106 t k.A. k.A. Segments: 2 3 4 4 Height [m] 20,0/ 22,1 Weight [t] 52 /38 32/ 37 /37 k.A. k.A. III III III II Wind zone (DiBT) 20,1/ 16,1/ 12,0 14,1/ 16,1/ 12,1 /10,1 20,1/ 20,1/ 12,1/ 10,1 Corrosion protection for all steel parts Ascent safety climbing ladder installed outside the tower No. of platforms 11.1.3 Page 87 of 96 external Sound power level of the E-40 / 500 kW tower height hub height sound power level and tonality according to KÖTTER 42 m 44 m 44 m 46 m 48 m 50 m 99,1 dB(A) 53 m 55 m 63 m 65 m 98,9 dB(A) 0 dB guraranteed sound power level and tonality 98,3 dB(A) < 1 dB 98.4 dB(A) 1 dB 0 dB 98,5 dB(A) < 1 dB 99,2 dB(A) 0 dB 99,0 dB(A) < 1 dB 99,5 dB(A) 0 dB 99,0 dB(A) < 1 dB 1. These data is based on the measurements of the E-40 sound power level carried out by Kötter Beratende Ingenieure, Rheine according to their latest measurement report 23554-2.001 dated Jan. 15, 1998, valid for a reference wind speed of 8 m/s in 10 m height with a measurements accuracy of > 2 dB(A). 2. The measurements of the sound power level have been carried out i.a. according to the IEA guidelines („Recommended Practices for Wind Turbine Testing and Evaluation - 4. Acoustics: Measurement of Noise Emission from Wind Turbines, 3. Edition 1994“). 3. For a windspeed > 12 m/s in hub height (rated power) ENERCON guarantees a sound power level of 101 dB(A) and a tonality of < 1 dB. 4. Zero tonality corresponds to Ltn = Lpt - Lpn < - 2 dB according to IEC standard 88/48/CDV (page 21/22). 5. Based on modifications in the operational mode and in view of the abovementioned measurement accuracy ENERCON is guaranteeing lower values of the sound power level than those certified by Kötter. 6. The mechanical concept of the ENERCON turbines (no fast rotating parts therefore no mechanical wear) guarantees that no increase of machinery noise will occur during the entire lifetime of the turbines. 7. Please ask ENERCON for the most resent sound data. Annex 25.00 30.00 35.00 40.00 45.00 50.00 55.00 60.00 0 100 200 300 distance [m] 400 500 600 700 Hub height 44 m; Apparant sound power level 98.9 dB(A) Hub height 50 m; Apparant sound power level 99.1 dB(A) Hub height 55 m; Apparant sound power level 99.2 dB(A) Hub height 65 m; Apparant sound power level 99.5 dB(A) The calculation is based on the German norms, especially the VDI 2714. For the calculation it has been assumed, that the terrain is flat. The measurements of the apparent sound power level have been carried out by KÖTTER Beratende Ingenieure GmbH according to the relevant IEA (1994) and IEC guidelines (IEC 88/48/CDV, part 10, draft). The calculation does not substitute a detailed calculation of the sound pressure level at the site. This calculation is not part of any warranty from ENERCON. 800 ENERCON E-40 Operating Instructions Page 88 of 96 Figure 26: Diagram of sound power levels Annex Sound pressure level [dB(A)] ENERCON E-40 Operating Instructions 11.2 Page 89 of 96 Glossary of Technical Terms Abseiling Equipment = Descent device, Equipment for rescuing persons from great heights Acceleration sensor Sensors which are used for measuring the oscillation amplitudes Anemometer "anemo" = prefix from Greek anemos = wind; instrument for measuring the speed of the wind Angle encoder Measure, check and control the angles of the rotor blades Automatic / normal operation Turbine operation completely controlled by the control system Battery cabinet Part of the pitch control unit. Contains a set of standby batteries which in an emergency allows to bring the rotor blades into feathered position Blade flange bearing Bearing, revolving connection between blade adaptor and hub Bord telephone Telephone for communication between persons in nacelle and tower base (ground station) Cd Candela = unit of luminous intensity Converter Converts the current with variable voltage and frequency supplied by the generator into three-phase or alternating current according to the requirements of the utility. Consists of the rectifier and inverter, which are connected with the d.c. link. d.c. link The energy supplied by the generator and converted into direct current by the rectifiers is transferred to the rectifiers via the d.c. link. Epoxy resin Structural plastic formed by polyaddition which is used for the ENERCON rotor blades Excitation current (excitation) Generates a magnetic field in the generator rotor which induces current in the generator stator when the rotor is rotating Feathered position Position of the rotor blades toward the wind in which the blades present a minimum surface of attack to the wind and minimum lift. Flicker Low-frequency voltage fluctuations causing unsteadiness of lighting in the vicinity of wind turbines. They are caused by the fluctuating tower passing loads (lee in front of the tower). With the E-40, this is not a major problem. Generator rotor Rotating part of the generator Generator stator Stationary part of the generator Grid management unit By means of rectifiers and inverters the grid management unit converts the current generated by the generator into a gridcompatible, three-phase current and feeds it into the utility's medium voltage grid via a transformer (see also converter) Glass-fibre reinforced plastic, fibre-reinforced composite material used in the construction of wind energy converters. Consisting of resin and glass-fibre fabrics and ropes, this is a strong, easy to process and light-weight material. Glass-fibre reinforced plastics are suitable for individual and series production of rotor blades, nacelles, casings or attachments. GFRP can be machined and is largely chemically stable. GRP Hazard beacon Signal lights marking the wind turbine for aircraft in flight Annex ENERCON E-40 Operating Instructions Page 90 of 96 Heat sink Together with the fans, heat sinks serve for dissipating the heat from the power cabinets Hub Casting, pivoted on the main pin. The rotor blades are attached to it via the blade adaptors. Hygroscopic Tending to absorb moisture from the air Inverter Converts direct current into alternating current Jumper Plug-in contacts on p.c.boards King pin Structural component flanged to the tower serving as connection to the nacelle. Also it serves together with the main carrier as bearing for the yaw drive. LED Light emitting diode Load spectrum Total sum of the loads acting on the turbine Macrolon screen Special screen used as a protection against unintentional touching of live parts Main carrier Welded structural component to which most of the nacelle components are attached. Also it serves together with the king pin as bearing for the yaw drive. Main pin Component attached to the main carrier around which hub and generator rotor rotate (running on tapered roller bearings) Manual operation Mode of operation of the E-40 in which maintenance work is carried out. The control system functions are restricted. Owners should not try to operate the turbine in this mode. Mechanical overspeed switch Safety sensor initiating an emergency shut-down of the turbine when activated Nacelle Main carrier with casing housing equipment and machinery Nacelle casing Four-part GRP casing of the nacelle consisting of top, two bottom parts and the roof hatch Nacelle sub-distribution Electrical distribution in the nacelle. On the lid of the subdistribution the nacelle control panel is arranged. Obstruction lighting Signal lights marking the wind turbine for aircraft in flight Opto coupler Component converting the energy from light pulses into electric energy, serves for coupling optical with electrical lines (can be used in both directions) Panic lock Special form of door bolt with a turning mechanism which allows to open a locked door from the inside without the use of a key Partial load Operation below rated power Phase Conducting line Pitch Blade angle adjustment Pitch control cabinet Contains the control system for the pitch control unit Pitch control unit The pitch control unit adjusts the angles of the rotor blades. It consists of pitch control cabinet, relay cabinet, battery cabinet, pitch control motor, gearbox, blade flange bearing Polyamide base Plastic base marked by special production and processing characteristics Polyester imide Bivalent strengthened polyester Annex ENERCON E-40 Operating Instructions Page 91 of 96 Rated power Maximum power for which the turbine is designed Rated wind speed Wind speed at which the rated power is just reached. Rectifier Converts alternating current into direct current Relay cabinet Part of the pitch control unit. Contains contactors for changing over the pitch control motors from normal to battery operation and back Ring generator Because of its type of construction (large diameter, little depth) the E-40 generator is called ring generator. Rotor (rotor head) Rotating part of the turbine (generator rotor, hub, rotor blades) Rotor casing Revolving three-part GRP casing of the rotor head Rotor sub-distribution Distributes the electric power and information supplied by the slipring casing to the rotor Slip-ring casing Establishes the electrical connection between nacelle and rotor Spark gap Air gap between two lightning conductor elements through which the lightning current is conducted Spar Longitudinal reinforcements in the rotor blades Speed sensor Sensor measuring the rotational speed of the rotor Spinner Revolving GRP casing of the hub area on the rotor head Stall effect Breakdown of the lift-producing airflow over the rotor blade Start-up wind speed Minimum wind speed at which the start-up procedure of the E-40 is initiated (approx. 2 m/s); if the wind speed rises further (approx. 2.5 m/s), the turbine starts to supply power Stator Stationary part of the generator in which currents are induced and thus electrical energy is generated Stator casing Stationary, multipart GRP casing of the stator Stator jib carrier Supporting device to which the stator is fastened Upwind rotor The rotor is in front of the tower, facing the wind Variable speed operation The rotational speed of the rotor is adjusted according to the wind speed. With increasing wind speed the rotor rotates faster (until the rated wind speed is reached). This ensures optimum enregy yield. Vibration sensor Monitor the tower vibrations and initiates an emergency shutdown of the turbine when activated Yaw drive Drive which turns nacelle and rotor into the direction of the wind Annex ENERCON E-40 Operating Instructions 11.3 Page 92 of 96 Status Messages (Revision No. 28) bold characters = main status normal = sub-status # = status message from remote monitoring system * = status message which can only be reset after having entered the service code 0 Turbine ready 0 Turbine in operation 1 Turbine starting 2 Turbine operational 1 Turbine stopped 1 Control cabinet 2 Customer interface 3 Remote control PC 4 Nacelle 2 Lack of wind 3 Storm 1 Peak wind speed 2 Average wind speed 3 Maximum blade angle 4 Average blade angle 4 Shadow stop 5 Blade defroster 1 Automatic 2 Manual 3 Remote control PC 6 Battery heat up time 7 Unauthorized access 0 Turbine stopped 8 Maintenance 9 Generator heating 10 Emergency stop actuated 1 Control panel 2 Nacelle 3 Converter 1 4 Converter 2 11 Rotor brake activated manual 12 Rotor lock 1 Activated (switch) 2 Completely set (Sensor) 3 Sensor fault 15 Emergency-stop test 16 Overspeed-switch test 0 Test running 1 Blade A 2 Blade B 3 Blade C 4 Blade A+B 5 Blade A+C 6 Blade B+C 7 Blade A+B+C 20 Wind measurement fault 1 Wind vane fault 2 No signal from wind vane 3 10V perm. sign. f. wind vane 4 Wind vane locked 11 Anemometer fault 12 No signal from anemometer 13 15V perm. sign. f. anemometer 21 Cable twisted 1 Left (2-3 turns) 2 Right (2-3 turns) 3 Left (> 3 turns) 4 Right (> 3 turns) 22 Yaw control fault 1 Limit switch left 2 Limit switch right 3 Untwist time too long 4 Yaw sensor fault 5 Cable twist switch 23 Yaw pads worn 30 Vibration sensor 31 Tower oscillation 1 Transverse oscillation 2 Longitudinal oscillation 3 Transvers sensor fault 4 Longitudinal sensor fault 11 Transverse oscillation (max.) 12 Longitudinal oscillation (max.) 40 Rotor overspeed 1 Measured ,blade A 2 Measured, blade B 3 Measured, blade C 4 Measured, I/O board 41 Rotor overspeed switch 1 Blade A 2 Blade B 3 Blade C 4 Blade A+B 5 Blade A+C 6 Blade B+C 7 Blade A+B+C 42 Pitch control error 1 Speed after stop too high 2 Blade angle > 50° 4 Limit switch -2° blade A 5 Limit switch -2° blade B 6 Limit switch -2° blade C 7 Limit switch 87° blade A 8 Limit switch 87° blade B 9 Limit switch 87° blade C 10 Limit switch 91° blade A 11 Limit switch 91° blade B 12 Limit switch 91° blade C 13 State error blade A 14 State error blade B 15 State error blade C 16 Angle error blade A 17 Angle error blade B 18 Angle error blade C 19 Angle skip blade A 20 Angle skip blade B Annex ENERCON E-40 Operating Instructions 21 Angle skip blade C 22 Motor current too high blade A 23 Motor current too high blade B 24 Motor current too high blade C 25 Motor current too high bl. A+B 26 Motor current too high bl. A+C 27 Motor current too high bl. B+C 28 0°-calibration sensor blade A 29 0°-calibration sensor blade B 30 0°-calibration sensor blade C 43 Main security circuit error 1 Open when starting 2 Cut off during operation 44 Emergency stop battery error *1 Undervoltage battery A *2 Undervoltage battery B *3 Undervoltage battery C 4 Overvoltage battery A 5 Overvoltage battery B 6 Overvoltage battery C *7 Battery test blade A *8 Battery test blade B *9 Battery test blade C 10 Temp. too low 11 Temp. too high 13 Temp. too low battery A 14 Temp. too low battery B 15 Temp. too low battery C 16 Temp. too high battery A 17 Temp. too high battery B 18 Temp. too high battery C 45 Battery charging error 1 No charging current battery A 2 No charging current battery B 3 No charging current battery C 4 Charg. current too high battery A 5 Charg. current too high battery B 6 Charg. current too high battery C 46 Battery test fault 1 Blade A 2 Blade B 3 Blade C 48 Speed sensor error 1 Speed sensor (short-term) 2 Speed sensor (long-term) 3 Measuring I/O-board 4 Measuring Pitch control 5 Diff. I/O-board / pitch control 7 Measuring Blade A 8 Measuring Blade B 9 Measuring Blade C 10 Acceleration measuring 50 Monitoring switch *1 blade A *2 blade B *3 blade C *4 Nacelle 55 Bladeheating fault 1 Difference too large 2 Not switchable 3 Power contactor 60 Grid error 1 Undervoltage L1 2 Undervoltage L2 3 Undervoltage L3 Page 93 of 96 4 Overvoltage L1 5 Overvoltage L2 6 Overvoltage L3 7 Underfrequency 8 Overfrequency 9 Phase sequence error 10 Overvoltage L1+L2+L3 Conv. 1 11 Undervoltage L1 conv. 1 12 Undervoltage L2 conv. 1 13 Undervoltage L3 conv. 1 14 Overvoltage L1 conv. 1 15 Overvoltage L2 conv. 1 16 Overvoltage L3 conv. 1 17 Underfrequency conv. 1 18 Overfrequency conv. 1 19 Phase sequence error conv. 1 20 Overvoltage L1+L2+L3 conv.2 21 Undervoltage L1 conv. 2 22 Undervoltage L2 conv. 2 23 Undervoltage L3 conv. 2 24 Overvoltage L1 conv. 2 25 Overvoltage L2 conv. 2 26 Overvoltage L3 conv. 2 27 Underfrequency conv. 2 28 Overfrequency conv. 2 29 Phase sequence error conv. 2 30 Overvolt. L1+L2+L3 conv.1+2 31 Undervoltage L1 conv. 1+2 32 Undervoltage L2 conv. 1+2 33 Undervoltage L3 conv. 1+2 34 Overvoltage L1 conv. 1+2 35 Overvoltage L2 conv. 1+2 36 Overvoltage L3 conv. 1+2 37 Underfrequency conv. 1+2 38 Overfrequency conv. 1+2 39 Phase sequence error conv. 1+2 51 Monitoring electric supply comp. 52 Start delay #61 Grid failure data repeater 62 Grid feeding error 1 Too low power converter1 2 Too low power converter 2 3 Too much power converter1 4 Too much power converter2 5 Total power too low 6 Total power too high 7 Dif. P-set / p-aktual 11 Power switch conv. 1 off 12 Power switch conv. 2 off 13 Power switch conv. 1+2 off 20 Leakage current 21 Isometer conv.1 22 Isometer conv.2 23 Isometer conv.1+2 24 Isometer 25 Accidental earth contact 31 Dif. power mes. MPU/conv.1 32 Dif. power mes. MPU/conv.2 33 Dif. power mes. MPU/conv.1+2 41 Fault isometer conv.1 42 Fault isometer conv.2 43 Fault isometer conv.1+2 45 Fault earth contact monitoring Annex ENERCON E-40 Operating Instructions 63 Synchronizer error 1 Rectifier not resetable 2 Rectifier after reset off 3 Grid error 64 Overcurrent in converter 1 I DC-link star 2 I DC-link delta 3 I DC-link star+delta 10 I rectifier converter 1 11 L1 converter 1 12 L2 converter 1 13 L3 converter 1 14 Step-up converter 1 20 I rectifier converter 2 21 L1 converter 2 22 L2 converter 2 23 L3 converter 2 24 Step-up converter 2 30 I rectifier converter 1+2 34 Step-up converter 1+2 65 Overvoltage in converter 1 U DC-link converter 1 2 U DC-link converter 2 3 U DC-link converter 1+2 67 Heat sink temperature 1 Overtemperature conv. 1 2 Overtemperature conv. 2 3 Difference too large 11 Overtemp. HS1 conv. 1 12 Overtemp. HS2 conv. 1 13 Overtemp. HS3 conv. 1 14 Thermoswitch HS1 conv. 1 15 Thermoswitch HS2 conv. 1 16 Thermoswitch HS3 conv. 1 21 Overtemp. HS1 conv. 2 22 Overtemp. HS2 conv. 2 23 Overtemp. HS3 conv. 2 24 Thermoswitch HS1 conv. 2 25 Thermoswitch HS2 conv. 2 26 Thermoswitch HS3 conv. 2 68 Transformer overtemperature *69 Acoustic sensor 1 Converter 1 2 Converter 2 3 Converter 1+2 70 Generator overtemperature 1 Stator 2 Rotor *72 Air gap monitoring 1 Sensor 1 blade A 2 Sensor 2 blade A 3 Sensor 1 blade B 4 Sensor 2 blade B 5 Sensor 1 blade C 6 Sensor 2 blade C 10 Serveral sensors 11 Several sensors blade A 12 Several sensors blade B 13 Several sensors blade C *73 Shear pin monitoring *76 Bearing temperature 1 Overtemp. front bearing 2 Overtemp. rear bearing Page 94 of 96 80 Excitation error 1 Leakage current 2 Overcurrent 3 Frequency error 4 Undervoltage L1 5 Undervoltage L2 6 Undervoltage L3 7 Overvoltage L1 8 Overvoltage L2 9 Overvoltage L3 10 Overtemperature heat sink 11 Fault temp. measurement 12 Phase sequence error 20 Charging error converter 1 21 Overvoltage DC-link 22 Excitation current too low 23 Excitation current too high 24 Overcurrent (software) 25 Overcurrent (hardware) 90 Prot. circuit-breaker tripped 1 Yaw drive 1 2 Yaw drive 2 3 Rotor brake 4 Excitation 5 Power switch converter 1 6 Power switch converter 2 7 Power switch converter 1+2 91 Semiconductor fuse fault 1 Converter 1 2 Converter 2 3 Converter 1 or 2 95 Error temp. measurement 1 Stator temperature 2 Rotor temperature 3 Outside temperature 4 Bearing temperature front 5 Bearing temperature rear 6 Battery temperature A 7 Battery temperature B 8 Battery temperature C 9 Tower temperature 10 Control cabinet temperature 11 Conv.1 cabinet temperature 12 Conv.2 cabinet temperature 13 Conv.1 heat sink 1 temperature 14 Conv.1 heat sink 2 temperature 15 Conv.1 heat sink 3 temperature 16 Conv.2 heat sink 1 temperature 17 Conv.2 heat sink 2 temperature 18 Conv.2 heat sink 3 temperature 19 Excitation unit 20 Blade temperature A 21 Blade temperature B 22 Blade temperature C 150 Initialize EEPROM !! 1 MPU 2 I/O-board 3 Display 4 Synchronizer Annex ENERCON E-40 Operating Instructions 152 EPROM incompatible !! 1 Excitation 2 I/O-board 3 Display 4 Synchronizer 5 Blade A 6 Blade B 7 Blade C 8 Converter control 1 9 Converter control 2 10 Grid feeding control 1 11 Grid feeding control 2 12 Customer interface 160 Supply MPU 4 +15V processor 5 -15V processor 161 Supply excitation 2 +12V processor 3 -12V processor 4 +15V processor 5 -15V processor 162 Supply I/O-board 4 +15V processor 5 -15V processor 22 +12V sensoric 24 + 15V sensoric 25 -15V sensoric 30 +5V ref. sensoric 31 +10V ref.sensoric 163 Supply display 6 -24V processor 164 Supply synchronizer 2 +12V processor 3 -12V processor 10 +5V ref. processor 165 Supply blade A 2 +12V processor 3 -12V processor 10 +5V ref. processor 23 -12V sensoric 24 +15V sensoric 31 +10V ref. sensoric 166 Supply blade B 2 +12V processor 3 -12V processor 10 +5V ref. processor 23 -12V sensoric 24 +15V sensoric 31 +10V ref. sensoric 167 Supply blade C 2 +12V processor 3 -12V processor 10 +5V ref. processor 23 -12V sensoric 24 +15V sensoric 31 +10V ref. sensoric 168 Supply converter control 1 2 +12V processor 3 -12V processor 23 -12V sensoric 24 +15V sensoric 30 +5V ref. sensoric 31 +10V ref. sensoric Page 95 of 96 169 Supply converter control 2 2 +12V processor 3 -12V processor 23 -12V sensoric 24 +15V sensoric 30 +5V ref. sensoric 31 +10V ref. sensoric 170 Supply grid feeding control 1 2 +12V processor 3 -12V processor 171 Supply grid feeding control 2 2 +12V processor 3 -12V processor 172 Supply customer interface 4 +15V processor 5 -15V processor 190 Hazard light fault 200 Data bus error 1 Excitation 2 I/O-board 3 Display 4 Synchronizer 5 Blade A 6 Blade B 7 Blade C 8 Converter 1 9 Converter 2 10 Customer interface 201 Data ring error 1 Pitch control blade A 2 Pitch control blade B 3 Pitch control blade C 202 Converter bus error 1 Converter 1 2 Converter 2 203 MPU bus error 1 MPU (receiver) 2 MPU (transmitter) 205 No data from MPU 1 Excitation 2 I/O-board 3 Display 4 Synchronizer 5 Blade A 6 Blade B 7 Blade C 8 Converter 1 9 Converter 2 10 Customer interface 220 Processor reset 1 Excitation 2 I/O-board 3 Display 4 Synchronizer 5 Blade A 6 Blade B 7 Blade C 8 Converter 1 9 Converter 2 10 Customer interface Annex ENERCON E-40 Operating Instructions Page 96 of 96 221 Watch dog reset 1 Excitation 2 I/O-board 3 Display 4 Synchronizer 5 Blade A 6 Blade B 7 Blade C 8 Converter 1 9 Converter 2 10 Customer interface 222 Turbine reset 1 Grid failure 2 Quit Button 3 Remote Control PC 225 Wrong state 1 Excitation 2 I/O-board 3 Display 4 Synchronizer 5 Blade A 6 Blade B 7 Blade C 8 Converter 1 9 Converter 2 10 Customer interface #240 Remote control PC 1 Switched on 2 Switched off 3 Grid failure 4 No response from turbine 5 Transmission error 6 Initialization error 7 General error 241 Remote control Number of authorisize person means explaining status Annex U.O. Via Don Spagnoli, 3 29010 SARMATO (PC) TEL. +39/0523/886202 FAX +39/0523/886172 Sito WEB: www.elettromultiservice.com E-Mail: [email protected] COD.FISC./P.IVA 03439930961 NS. RIF. L13118-1A RELAZIONE TECNICA Verifica e depotenziamento di una generatrice eolica di costruzione ENERCON Caratteristiche del progetto originale aerogeneratore: Enercon tipo EB 400 potenza: 500 kVA tensione: 460 V corrente: 627,5 A frequenza: 50 Hz In data 24 Aprile 2013 oggetto per la verifica delle condizioni elettriche e meccaniche e per effettuare tutte le attività necessarie per garantire che la potenza massima erogabile sia al massimo di 200 kW continuativi. OPERAZIONI PRELIMINARI Scarico a tutti i lati S ed elettriche. na per poter accedere alle parti meccaniche VERIFICHE MECCANICHE Struttura portante: integra, senza anomalie sulle saldature Pacco magnetico statorico: integro e correttamente bloccato sulla struttura Raggiera della ruota polare: integra e senza anomalie sulle saldature Masse magnetiche polari: bloccate Cuscinetti portanti principali: non è stato possibile smontarli, per evitare danneggiamenti, ma è stata effettuata una completa analisi chimica tribologica del grasso lubrificante prelevato per cementazione delle superfici di rotolamento Ingranaggi per la rotazione delle pale: efficienti e ben ingrassati. VERIFICHE ELETTRICHE Nr. 3 motoriduttori auto frenanti in c.c. Weier MOT.GN 112S 1,5 kW 1500 rpm misura della resistenza di isolamento con megger a 250 V d.c. valori misurati: 1000 M Bobine freno per detti valori misurati: 1000 M Sede Legale: Piazza Meda, 5 20121 MILANO Unità Operativa: Via Don Spagnoli, 3 29010 Sarmato (PC) Cap. Soc. 90.000,00 int. vers. Società unipersonale, soggetta alla direzione e coordinamento Leroy Somer S.p.A. C.F./P.IVA e nr. iscr.ne Registro Imprese di Milano: 03439930961 Iscrizione R.E.A.: 1674521 Avvolgimento principale statorico (collegati due gruppi parallelo stella) - misura della resistenza di isolamento a 500 Vd.c. 0,60 M - misura della resistenza ohmica con doppio ponte valore di fase rilevato a 20 °C 28,41 m Ruota polare - misura della resistenza di isolamento a 250 Vd.c. 11,5 M pedenza dei poli in c.a. 220 V 50 Hz: esito favorevole (in allegato tabella misure) Verifica delle cassette di derivazione bordo macchina e dei cablaggi: regolari V MANUTENZIONE E MODIFICA amere alimentazione ad uno dei due rami in parallelo, in modo che sul rotore passo circolare una corrente ridotta del 50%. Parimenti è stato eliminato dal circuito statorico uno dei due avvolgimenti collegati in parallelo. Riducendo la corrente di eccitazione del 50% non si ottiene una riduzione della potenza proporzionale, bensì ancora inferiore, perché il circuito di eccitazione deve essere in grado di sovra eccitare la macchina per permetterle in qualsiasi condizione di esercizio della rete di mantenere il cosfi (fattore di sfasamento) entro i limiti imposti dalla normativa. Considerando una capacità di regolazione tra cosfi 0,8 e cosfi 1 la potenza effettivamente disponibile ai morsetti risulta quindi: kVA 500 : 2 = kVA 250 x 0,8 = 200 kW Il risultato di tali operazioni è la riduzione della p nelle condizioni ottimali di funzionamento, potrà raggiungere al massimo la potenza di 200 kW. NUOVA TARGA identificativa riportante i nuovi dati di esercizio. Allegati: analisi tribologia del grasso bollettini di collaudo nuova targhetta. RACCOMANDAZIONI PER LA MESSA IN SERVIZIO ingrassatori a gas PERMA tipo Futura Plus con altri originali. Occorrerà inoltre effettuare una nuova misura della resistenza di isolamento statorico ed continua con intensità massima 300 A. E.M.S. Elettro Multi Service s.r.l. Ing. M. Boledi Sarmato, 20 maggio 2013 Sede Legale: Piazza Meda, 5 20121 MILANO Unità Operativa: Via Don Spagnoli, 3 29010 Sarmato (PC) Cap. Soc. 90.000,00 int. vers. Società unipersonale, soggetta alla direzione e coordinamento Leroy Somer S.p.A. C.F./P.IVA e nr. iscr.ne Registro Imprese di Milano: 03439930961 Iscrizione R.E.A.: 1674521 Allegato fotografico Img.01 foto scarico turbina eolica in officina Img.02 alternatore smontato Img.03 dettaglio alternatore smontato Sede Legale: Piazza Meda, 5 20121 MILANO Unità Operativa: Via Don Spagnoli, 3 29010 Sarmato (PC) Cap. Soc. 90.000,00 int. vers. Società unipersonale, soggetta alla direzione e coordinamento Leroy Somer S.p.A. C.F./P.IVA e nr. iscr.ne Registro Imprese di Milano: 03439930961 Iscrizione R.E.A.: 1674521 Img.04 dettaglio pacca statorio e rotorico Img.05 dettaglio poli Img.06 foto dettagli Sede Legale: Piazza Meda, 5 20121 MILANO Unità Operativa: Via Don Spagnoli, 3 29010 Sarmato (PC) Cap. Soc. 90.000,00 int. vers. Società unipersonale, soggetta alla direzione e coordinamento Leroy Somer S.p.A. C.F./P.IVA e nr. iscr.ne Registro Imprese di Milano: 03439930961 Iscrizione R.E.A.: 1674521 Img.07 lato collegamento poli Img.08 dettaglio ralla principale e sistema pich controll Img.09 motori pich controll Img.10 dettaglio revisione motore pich controll Sede Legale: Piazza Meda, 5 20121 MILANO Unità Operativa: Via Don Spagnoli, 3 29010 Sarmato (PC) Cap. Soc. 90.000,00 int. vers. Società unipersonale, soggetta alla direzione e coordinamento Leroy Somer S.p.A. C.F./P.IVA e nr. iscr.ne Registro Imprese di Milano: 03439930961 Iscrizione R.E.A.: 1674521
advertisement
Related manuals
Download
PDF
advertisement
Table of contents
- 30 Imprint
- 31 Liability
- 32 Table of Contents
- 36 1 Short description of the E
- 37 1.1 The ENERCON concept
- 37 1.2 Generator
- 38 1.3 Rotor
- 38 1.4 Yaw control
- 39 1.5 E-40 Safety System
- 39 1.5.1 The Brake System
- 39 1.5.2 Lightning Protection System
- 40 1.5.3 Sensor System
- 40 1.5.4 Control System
- 41 1.5.5 Grid Management
- 43 2 Safety Instructions
- 43 2.1 The E-40’s Safety System
- 43 2.2 Protective measures for works on and inside the E
- 43 2.2.1 General regulations and rules of conduct
- 44 2.2.2 Schematic diagrams of the WEC’s safety provisions
- 44 2.2.2.1 Safety provisons of the nacelle, side view
- 45 2.2.2.2 Safety provisions of tower and tower base
- 46 2.2.2.3 Safety provisions of the nacelle, rear view
- 46 2.2.3 First aid
- 47 2.2.4 Work involving a risk of fire
- 47 2.2.5 Turbine shut-down in case of formation of ice
- 48 2.2.7 Climbing and descending the tower ladder
- 50 2.2.8 Staying on the tower platform and in the nacelle
- 50 2.2.9 Rotor lock
- 51 2.3 Inspection of safety provisions
- 51 2.3.1 Owner’s obligation to inform ENERCON
- 52 3 Operation
- 52 3.1 Control and Monitoring System
- 53 3.2 Display of E-40 status messages
- 53 3.3 Responding of safety-relevant sensors
- 54 3.4 Starting
- 54 3.5 Normal operation
- 55 3.6 Idling
- 55 3.7 Stopping
- 55 3.7.1 Manual stopping
- 56 3.7.2 Manual stopping in emergency stituations
- 57 3.8 Lack of wind
- 57 3.9 Storm
- 57 3.10 Rotor speed monitoring (rotor overspeed)
- 58 3.11 Yaw control
- 59 3.12 Untwisting of cables
- 60 3.13 Emergency pitch control units of the E
- 60 3.14 Rotor brake
- 60 3.15 Rotor lock
- 61 3.16 Shear pin monitoring
- 61 3.17 Vibrations and Tower Oscillations
- 62 3.18 Air gap monitoring
- 62 3.19 Temperature monitoring
- 62 3.20 Pitch control error
- 63 3.21 Protective circuit-breaker tripped
- 63 3.22 Grid error
- 64 3.23 Converter fault
- 64 3.24 Maintenance
- 65 4 Towers and ground stations of the E
- 65 4.1 Steel tower
- 66 4.2 Reinforced concrete tower
- 66 4.3 Stations for different tower versions
- 67 4.3.1 Combined transformer / substation
- 68 4.3.2 Transformer station
- 69 4.3.3 Three-room substation
- 70 5 Control and Power Cabinets
- 70 5.1 Power cabinet
- 70 5.2 Control cabinet / display
- 72 5.3 LC display and menu functions
- 72 5.3.1 General instructions
- 74 5.3.2 Menu "start delay
- 74 5.3.3 Menu "mains parameters
- 75 5.3.4 Menu "mains data
- 75 5.3.5 Menu "blade defroster" (optional)
- 76 5.3.6 Menu "power optimization" (optional)
- 77 5.3.7 Menu 1 / 2 "shadow stop" (optional)
- 77 5.3.7.1 Menu and menu settings
- 78 5.3.7.2 Functions in shadow stop menu
- 79 5.3.7.3 Functions in shadow stop menu
- 80 5.3.8 Menu "time / date
- 80 5.3.9 Menu "set kilowatt hours
- 80 5.3.10 Menu "set operating hours
- 80 5.3.11 Menu "adjust contrast
- 81 5.3.12 Menu "language
- 81 5.3.13 Menu "pitch data
- 81 5.3.14 Menu "version numbers
- 81 5.3.15 Menu "hardware options
- 81 5.3.16 Menu "program info
- 82 5.4 Control cabinet operator panel
- 86 6 The nacelle (the machine house)
- 86 6.1 Arrangement of components in and on the E-40 nacelle
- 87 6.2 Description of important components in the rotor head
- 87 6.2.1 Slip ring casing
- 87 6.2.2 Pitch control unit
- 88 6.2.2.1 Pitch control cabinet
- 88 6.2.2.2 Battery cabinet
- 88 6.2.2.3 Relay cabinet
- 88 6.2.2.4 Pitch control motor
- 89 6.2.2.5 Angle encoder
- 89 6.3 Operator panel of the E-40 nacelle sub-distribution
- 90 6.3.1 Description of the nacelle sub-distribution control elements
- 94 7 Remote Monitoring
- 95 7.1 System components
- 95 7.1.1 Optional equipment
- 96 7.2 Additional monitoring systems
- 96 7.3 Scope of monitoring
- 96 7.3.1 Wind energy converter
- 99 7.3.2 Wind farm
- 100 7.3.3 Substation (optional)
- 100 7.3.4 Meteorological stations (optional)
- 101 7.4 System messages
- 101 7.4.1 Status messages
- 101 7.4.2 Malfunctions (faults)
- 102 7.4.3 Fault messages
- 103 7.5 Transfer
- 103 7.5.1 Fault message to central monitoring system (office computer)
- 103 7.5.2 Fault message to fax
- 103 7.5.3 Fault message to SMS or pager (city call)
- 103 7.6 Control
- 103 7.7 Other functions
- 103 7.7.1 Transfer protocol
- 104 7.7.2 Requesting of missing data
- 105 8 Optional Equipment
- 105 8.1 Obstruction lighting / Hazard beacon
- 105 8.1.1 Obstruction lighting with standby power supply and monitoring
- 105 8.1.2 Obstruction lighting without standby power supply, but including monitoring
- 106 8.1.3 Obstruction lighting without standby power supply and without monitoring
- 106 8.1.4 Flashing hazard beacon with standby power supply and monitoring
- 106 8.2 Rotor blade heating
- 106 8.2.1 Description of rotor blade heating
- 107 8.2.2 Operation
- 107 8.2.3 Advantages of the use of a rotor blade heating
- 109 8.3 Shadow stop
- 110 9 Starting and Stopping of the E-40 (brief instruction)
- 110 9.1 Startup of the E
- 110 9.2 Stopping the E
- 111 10 What to do if the E-40 refuses to function?
- 111 10.1 Identifying the fault with the help of the display
- 111 10.2 Tips for a restart
- 112 10.2.1 Turbine aligns itself to the wind, but fails to start
- 112 10.2.2 Turbine does not align itself to the wind properly
- 112 10.2.3 Turbine does not start although there is no apparent fault
- 113 11 Annex
- 113 11.1 Technical data of the E
- 113 11.1.1 General
- 114 11.1.2 Tower specifications
- 115 11.1.3 Sound power level of the E-40 / 500 kW
- 117 11.2 Glossary of Technical Terms
- 120 11.3 Status Messages (Revision No. 28)