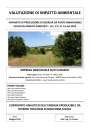
advertisement
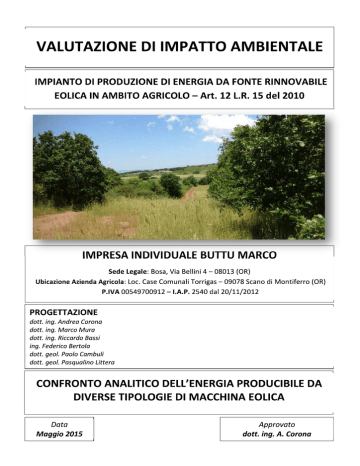
ENERCON E-40 Operating Instructions
Page 30 of 96
If due to strong gusts the rotor speed measured should exceed the rated speed by more than 15 %, an emergency shut-down will be carried out by means of the emergency pitch control units of the rotor blades. The LC display indicates main status 40 "rotor overspeed" with the corresponding sub-status stating which speed sensor was the first to record the excess speed. After 3 minutes the turbine will carry out a new starting attempt automatically.
If this fault signal has been indicated more than 5 times within the last 24 hours, a new starting attempt is not made. The status signal is flashing and first must be acknowledged.
In addition to the electronic monitoring, each of the three pitch control cabinets is equipped with three electromechanical switches which in case of excess rotor speed will shut down the turbine. These mechanical overspeed switches respond when the rated rotor speed is exceeded by more than 25 %. In that case, a quick blade adjustment is initiated via the emergency pitch control units of the rotor blades.
An automatic re-start of the turbine is then no longer possible. The mechanical overspeed switches have to be reset manually by service personnel and the fault must be acknowledged.
Main status: 40 :
41 :
48 :
Rotor overspeed
Rotor overspeed switch
Speed sensor error
3.11 Yaw control
The E-40 is provided with a combined wind sensor mounted on a supporting tube with integrated lighting protection system on the upper side of the nacelle. The combined wind sensor consists of a wind vane for the continuous measuring of the wind direction and an anemometer which measures the wind speed.
The yaw control system of the E-40 works at all wind speeds above 1.8 m/s.
Thus it is ensured that it is operating whenever a starting attempt is made (start-up wind speed: 2 m/s). Even if the turbine has already been shut down, e.g. due to high wind speed, it is still aligned in the direction of the wind. A re-alignment takes place when the average deviation of the nacelle direction compared to the wind direction measured is greater than the specified minimum angle (8° on a 1-minute average).
The yaw motion is monitored by counting the rotations of the yaw motor and by checking the yaw time for plausibility. During the re-positioning operation the rotational speed of the yaw drives is monitored by a sensor of the control and monitoring system. If the control system recognizes any irregularities in the yaw operation or the untwisting of cables (see chapter 3.12), a stopping process is initiated.
The nacelle of the E-40 is supported by two friction pads. Due to the yaw operations carried out, these pads wear out in the course of time (approx. 10 years). They are monitored by a sensor which responds when the pads are worn out to such an extent that they must be replaced. In that case the turbine is stopped slowly and yaw control is blocked by the control system.
Main status: 20 :
22 :
23 :
Wind measurement fault
Yaw control fault
Yaw pads worn
Operation
advertisement
Related manuals
advertisement
Table of contents
- 30 Imprint
- 31 Liability
- 32 Table of Contents
- 36 1 Short description of the E
- 37 1.1 The ENERCON concept
- 37 1.2 Generator
- 38 1.3 Rotor
- 38 1.4 Yaw control
- 39 1.5 E-40 Safety System
- 39 1.5.1 The Brake System
- 39 1.5.2 Lightning Protection System
- 40 1.5.3 Sensor System
- 40 1.5.4 Control System
- 41 1.5.5 Grid Management
- 43 2 Safety Instructions
- 43 2.1 The E-40’s Safety System
- 43 2.2 Protective measures for works on and inside the E
- 43 2.2.1 General regulations and rules of conduct
- 44 2.2.2 Schematic diagrams of the WEC’s safety provisions
- 44 2.2.2.1 Safety provisons of the nacelle, side view
- 45 2.2.2.2 Safety provisions of tower and tower base
- 46 2.2.2.3 Safety provisions of the nacelle, rear view
- 46 2.2.3 First aid
- 47 2.2.4 Work involving a risk of fire
- 47 2.2.5 Turbine shut-down in case of formation of ice
- 48 2.2.7 Climbing and descending the tower ladder
- 50 2.2.8 Staying on the tower platform and in the nacelle
- 50 2.2.9 Rotor lock
- 51 2.3 Inspection of safety provisions
- 51 2.3.1 Owner’s obligation to inform ENERCON
- 52 3 Operation
- 52 3.1 Control and Monitoring System
- 53 3.2 Display of E-40 status messages
- 53 3.3 Responding of safety-relevant sensors
- 54 3.4 Starting
- 54 3.5 Normal operation
- 55 3.6 Idling
- 55 3.7 Stopping
- 55 3.7.1 Manual stopping
- 56 3.7.2 Manual stopping in emergency stituations
- 57 3.8 Lack of wind
- 57 3.9 Storm
- 57 3.10 Rotor speed monitoring (rotor overspeed)
- 58 3.11 Yaw control
- 59 3.12 Untwisting of cables
- 60 3.13 Emergency pitch control units of the E
- 60 3.14 Rotor brake
- 60 3.15 Rotor lock
- 61 3.16 Shear pin monitoring
- 61 3.17 Vibrations and Tower Oscillations
- 62 3.18 Air gap monitoring
- 62 3.19 Temperature monitoring
- 62 3.20 Pitch control error
- 63 3.21 Protective circuit-breaker tripped
- 63 3.22 Grid error
- 64 3.23 Converter fault
- 64 3.24 Maintenance
- 65 4 Towers and ground stations of the E
- 65 4.1 Steel tower
- 66 4.2 Reinforced concrete tower
- 66 4.3 Stations for different tower versions
- 67 4.3.1 Combined transformer / substation
- 68 4.3.2 Transformer station
- 69 4.3.3 Three-room substation
- 70 5 Control and Power Cabinets
- 70 5.1 Power cabinet
- 70 5.2 Control cabinet / display
- 72 5.3 LC display and menu functions
- 72 5.3.1 General instructions
- 74 5.3.2 Menu "start delay
- 74 5.3.3 Menu "mains parameters
- 75 5.3.4 Menu "mains data
- 75 5.3.5 Menu "blade defroster" (optional)
- 76 5.3.6 Menu "power optimization" (optional)
- 77 5.3.7 Menu 1 / 2 "shadow stop" (optional)
- 77 5.3.7.1 Menu and menu settings
- 78 5.3.7.2 Functions in shadow stop menu
- 79 5.3.7.3 Functions in shadow stop menu
- 80 5.3.8 Menu "time / date
- 80 5.3.9 Menu "set kilowatt hours
- 80 5.3.10 Menu "set operating hours
- 80 5.3.11 Menu "adjust contrast
- 81 5.3.12 Menu "language
- 81 5.3.13 Menu "pitch data
- 81 5.3.14 Menu "version numbers
- 81 5.3.15 Menu "hardware options
- 81 5.3.16 Menu "program info
- 82 5.4 Control cabinet operator panel
- 86 6 The nacelle (the machine house)
- 86 6.1 Arrangement of components in and on the E-40 nacelle
- 87 6.2 Description of important components in the rotor head
- 87 6.2.1 Slip ring casing
- 87 6.2.2 Pitch control unit
- 88 6.2.2.1 Pitch control cabinet
- 88 6.2.2.2 Battery cabinet
- 88 6.2.2.3 Relay cabinet
- 88 6.2.2.4 Pitch control motor
- 89 6.2.2.5 Angle encoder
- 89 6.3 Operator panel of the E-40 nacelle sub-distribution
- 90 6.3.1 Description of the nacelle sub-distribution control elements
- 94 7 Remote Monitoring
- 95 7.1 System components
- 95 7.1.1 Optional equipment
- 96 7.2 Additional monitoring systems
- 96 7.3 Scope of monitoring
- 96 7.3.1 Wind energy converter
- 99 7.3.2 Wind farm
- 100 7.3.3 Substation (optional)
- 100 7.3.4 Meteorological stations (optional)
- 101 7.4 System messages
- 101 7.4.1 Status messages
- 101 7.4.2 Malfunctions (faults)
- 102 7.4.3 Fault messages
- 103 7.5 Transfer
- 103 7.5.1 Fault message to central monitoring system (office computer)
- 103 7.5.2 Fault message to fax
- 103 7.5.3 Fault message to SMS or pager (city call)
- 103 7.6 Control
- 103 7.7 Other functions
- 103 7.7.1 Transfer protocol
- 104 7.7.2 Requesting of missing data
- 105 8 Optional Equipment
- 105 8.1 Obstruction lighting / Hazard beacon
- 105 8.1.1 Obstruction lighting with standby power supply and monitoring
- 105 8.1.2 Obstruction lighting without standby power supply, but including monitoring
- 106 8.1.3 Obstruction lighting without standby power supply and without monitoring
- 106 8.1.4 Flashing hazard beacon with standby power supply and monitoring
- 106 8.2 Rotor blade heating
- 106 8.2.1 Description of rotor blade heating
- 107 8.2.2 Operation
- 107 8.2.3 Advantages of the use of a rotor blade heating
- 109 8.3 Shadow stop
- 110 9 Starting and Stopping of the E-40 (brief instruction)
- 110 9.1 Startup of the E
- 110 9.2 Stopping the E
- 111 10 What to do if the E-40 refuses to function?
- 111 10.1 Identifying the fault with the help of the display
- 111 10.2 Tips for a restart
- 112 10.2.1 Turbine aligns itself to the wind, but fails to start
- 112 10.2.2 Turbine does not align itself to the wind properly
- 112 10.2.3 Turbine does not start although there is no apparent fault
- 113 11 Annex
- 113 11.1 Technical data of the E
- 113 11.1.1 General
- 114 11.1.2 Tower specifications
- 115 11.1.3 Sound power level of the E-40 / 500 kW
- 117 11.2 Glossary of Technical Terms
- 120 11.3 Status Messages (Revision No. 28)