Section 5 GAP 26 (Pitot/AOA Probe) Installation. Garmin G3X Touch for Experimental Aircraft, GDU 465, GDU 455, G3X, GDU 460, GDU 450
Add to My manuals943 Pages
advertisement
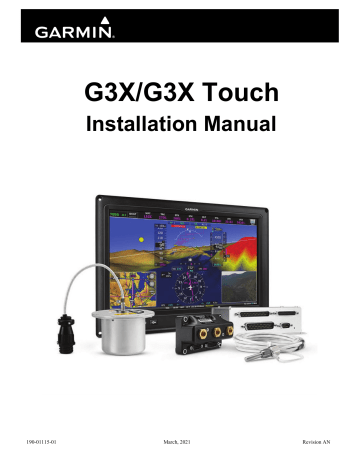
NOTE
GDU 37X and GDU 4XX displays may not be combined in the same system.
A G3X system can have up to two G5 standby flight displays. For G5 installation information, refer to the
G5 installation manual (190-02072-01).
GDU displays communicate with other LRUs via the CAN bus (with optional RS-232 backup paths supported for some LRUs) and with other devices via RS-232.
A G3X Touch system installed with no ADAHRS units can display MFD data, including engine information, on up to four GDU 4XX displays. This system configuration can also support Garmin autopilot functionality when paired with one or more G5 flight displays.
A single GDU display, installed without any other G3X system components, may be configured as a standalone MFD. A standalone GDU 37X MFD does not support flight or engine instruments, or advanced interface capabilities, and is intended for applications where only basic mapping and navigation features are required.
2.1.1.2 ADAHRS
The GSU 25 is the ADAHRS (air data, attitude, and heading reference system) unit for the G3X system.
An ADAHRS senses the aircraft’s attitude, measures all air data parameters, and calculates aircraft heading.
Up to three ADAHRS units are supported. In a system with multiple GDU displays and multiple ADAHRS units, each display can present data from a separate ADAHRS, and any GDU display may also be switched to display data from any ADAHRS. Data from multiple ADAHRS units is also automatically crosscompared, and disagreements are noted on the PFD display.
Each GSU 25 ADAHRS is connected to pneumatic pressure inputs for pitot, static, and angle of attack
(AOA). Connection of the AOA input is only required for GSU 25 #1, and is optional for GSU 25 #2 and
#3. For aircraft capable of indicated airspeeds greater than 300 knots, the GSU 25D is used.
The GSU 25 communicates with other LRUs via the CAN bus, and can optionally be connected to the
PFD1 GDU via RS-232 for redundancy. For GSU 25 installation information, refer to
.
The older GSU 73 ADAHRS is also supported. The GSU 73 does not provide AOA data, but a system that includes a GSU 73 may also include additional GSU 25 units. For GSU 73 installation information, refer to
.
In a system installed with one or more dedicated ADAHRS units and one or more G5 standby flight displays, attitude and air data from the G5 will also be displayed on the GDU displays, in the event that valid data is not available from any dedicated ADAHRS unit.
In a G3X Touch system installed with no dedicated ADAHRS units, attitude and air data from the G5 will be used throughout the system, including for autopilot functionality, but will not be visible on the GDU
4XX displays.
190-01115-01
Rev. AN
G3X/G3X Touch Installation Manual - Installation Preparation
Page 2-4
2.1.1.3 Magnetometer
The G3X system requires a minimum of one magnetometer (magnetic field sensor) to provide the
ADAHRS unit(s) and/or G5 standby display(s) with magnetic field information. In an installation with multiple ADAHRS units, magnetometer data is shared via the CAN bus. When multiple ADAHRS units are installed, additional magnetometers may be installed for redundancy, although this is not commonly done. In a G3X Touch system with a G5 but no ADAHRS units, only a single magnetometer is supported.
Several different magnetometers are supported:
The GMU 11 magnetometer connects to the G3X system via the CAN bus. Refer to
GMU 11 installation information. The GSU 73 does not support the GMU 11.
The GMU 22 magnetometer connects to the ADAHRS LRU via RS-232 and RS-485 interfaces. Refer to
for GMU 22 installation information. The GMU 44 is also supported and is functionally identical to the GMU 22.
Refer to
Appendix B for magnetometer placement information.
2.1.1.4 Outside Air Temperature
The outside air temperature (OAT) probe used in the G3X system is the GTP 59. A minimum of one OAT probe is required, and is connected to the #1 ADAHRS. In an installation with multiple ADAHRS units, air temperature data is shared via the CAN bus. Additional OAT probes may be connected to the other
ADAHRS LRUs for redundancy, although this is not commonly done. Refer to Section 21
for GTP 59 installation information.
In a G3X Touch system with one or more G5 displays but no ADAHRS units, a GTP 59 can optionally be connected via the GAD 13 temperature probe adapter. If the system is later expanded with the addition of one or more ADAHRS units, the GAD 13 may be retained, or the GAD 13 may be removed and the
GTP 59 connected to the #1 GSU 25 ADAHRS unit. Refer to the G5 installation manual (190-02072-01) for GAD 13 information.
2.1.1.5 Pitot/Static
The ADAHRS units (and optional G5 displays) in the G3X system must be connected to the aircraft’s pitot/static system. The airframe manufacturer’s guidance should be followed to ensure proper location of the pitot tube and static port.
The GAP 26 pitot/AOA probe is a combination pitot tube and angle of attack (AOA) probe. It is available in several configurations, including heated and unheated versions. Refer to
installation information.
G3X ADAHRS units and G5 displays may also be used with any other pitot tube, if AOA is not required.
Refer to
Section 37 for information on conducting periodic tests of the static system.
2.1.1.6 Angle of Attack
The G3X system is capable of sensing and displaying the aircraft’s current angle of attack (AOA) when installed with a GSU 25 ADAHRS and a GAP 26 pitot/AOA probe. The GDU displays present on-screen
AOA information, and also generate AOA audio alerts.
The optional GI 260 AOA indicator can also be added to provide a separate heads-up indication of AOA.
Refer to
Section 11 for GI 260 installation information.
190-01115-01
Rev. AN
G3X/G3X Touch Installation Manual - Installation Preparation
Page 2-5
2.1.1.7 Engine Information
The G3X system includes highly flexible capabilities for monitoring numerous engine sensors and parameters, and can support most piston and turbine engines, including twin-engine installations. Airframe sensors such as voltage, fuel quantity, and discrete (switch/contact) inputs are also supported. Refer to
for engine application and sensor installation information, and
,
for engine/airframe sensor wiring information.
The engine information system (EIS) unit for the G3X system is the GEA 24. The GEA 24 provides the ability to monitor numerous analog, digital, and discrete signals from a variety of engine and airframe sensors. Multiple GEA 24 units may be installed in order to monitor large piston engines, or for twinengine applications. The GEA 24 also supports a digital interface to a number of FADEC (Full Authority
Digital Engine Control) engines. The GEA 24 communicates with other LRUs via the CAN bus, and can optionally be connected to the MFD GDU via RS-232 for redundancy. For GEA 24 installation
information, refer to Section 10
. For information on EIS sensor configuration and calibration, refer to
.
The GSU 73 also supports EIS inputs. Alternatively, a system that includes a GSU 73 may instead use a
GEA 24 for EIS, if the GEA 24 is wired as EIS LRU #2.
The GEA 24 and GSU 73 can drive external annunciator lamps for Master Caution and Master Warning, to provide additional notification of abnormal engine indications. Refer to
for information on connecting annunciator lamps to GEA 24 or GSU 73 discrete output pins.
2.1.1.8 GPS
Each GDU display includes an internal VFR GPS receiver, and a connection for an external antenna. GPS position data is shared between GDU displays via the CAN bus. For a list of GPS antennas supported by the GDU display, refer to
The GPS 20A is a TSO-compliant WAAS GPS position source that is compatible with the G3X system.
The GPS 20A provides GPS data to the G3X system via the CAN bus, and can send ADS-B position data to a transponder via RS-232. For GPS 20A installation information and a list of supported GPS antennas, refer to
.
GPS data is used for ADAHRS performance monitoring, so at least one source of GPS data is required.
This requirement can be met by installing a GPS 20A, or by connecting a GPS antenna to at least one GDU
GPS receiver. In a system with multiple GDU displays, additional GPS antennas may be connected to the other displays for redundancy, if desired.
The G3X system is capable of displaying basic position data from an external IFR GPS navigator, but this data is not used for ADAHRS monitoring and thus does not satisfy the above requirement.
For general GPS antenna installation information, refer to
2.1.1.9 ARINC 429
ARINC 429 is an industry-standard data bus format that is primarily used with IFR GPS or GPS/NAV receivers (see below). The GAD 29 is the primary ARINC 429 data adapter for the G3X system; the
GSU 73 also supports ARINC 429 input/output. ARINC 429 data is relayed to and from the rest of the
G3X system via the CAN bus. For GAD 29 installation information, refer to
190-01115-01
Rev. AN
G3X/G3X Touch Installation Manual - Installation Preparation
Page 2-6
2.1.1.10 Navigation
Basic VFR GPS navigation with the G3X system is performed by the GDU displays, using their internal navigation databases in conjunction with GPS data from GDU GPS receivers or the GPS 20A. Flight plan entry and modification is also performed via the GDU displays. For VFR operations, no other source of navigation data is required.
The G3X system also supports up to two external navigation sources. Supported external navigation sources include IFR GPS, VHF NAV, and GPS/NAV receivers.
Lateral and vertical deviation (CDI/VDI) and status data from external navigators is displayed on the GDU displays, as well as external GPS navigator flight plan information. On-screen controls allow switching the current source of navigation data between multiple external sources, as well as to the G3X system’s internal flight plan for VFR navigation.
The Garmin GNC 355, GNS 4XX/5XX, GNX 375, GPS 175, and GTN 6XX/7XX IFR GPS navigators are supported by the G3X system, including WAAS approach capability. This integration requires the use of a
GAD 29 ARINC 429 interface module. GPS navigation data is provided to the G3X system via one
RS-232 input and one ARINC 429 input for each GNC 355, GNS 4XX/5XX, GNX 375, GPS 175, and
GTN 6XX/7XX IFR GPS navigator unit. The G3X system sends flight data and selected course information back to the external GPS navigator via an ARINC 429 output.
The G3X system uses an additional ARINC 429 input to receive VOR, localizer, and glideslope deviation information from a Garmin GTN 650/750 or GNS 430/480/530 IFR GPS/NAV receiver.
VOR, localizer, and glideslope information from a Garmin GNC 255 or SL30 VHF NAV receiver is also supported. These radios connect to the G3X system via an RS-232 connection to a GDU display.
When two external navigation sources are connected to the G3X system, the determination of which source is #1 and which is #2 is determined by the ordering of the RS-232 connections to the GDU displays.
The #1 navigation source should be connected to a lower-numbered RS-232 port on the PFD1 GDU, and the #2 navigation source should be connected either to a higher-numbered RS-232 port on the PFD1 GDU, or to any RS-232 port on the MFD1 GDU. For additional information, refer to
The G3X Touch system can send basic flight plan data to a GNC 355, GNS 4XX/5XX, GNX 375,
GPS 175, or GTN 6XX/7XX IFR GPS navigator, allowing VFR flight plans to be created on the G3X system and uploaded to the IFR navigator. The GDU 4XX display in a G3X Touch system can also act as a relay between the GNC 355, GNS 4XX/5XX, GNX 375, GPS 175, and GTN 6XX/7XX IFR GPS
navigator and a tablet computer, via Bluetooth (see Section 2.1.1.23
). Flight plan transfer capability requires a second RS-232 connection between the PFD1 GDU and the #1 GNC 355, GNS 4XX/5XX,
GNX 375, GPS 175, or GTN 6XX/7XX IFR GPS navigator, using the “Connext” RS-232 format. The
Connext interface and Bluetooth are not supported by the legacy G3X system and GDU 37X display.
If a G5 standby display instrument is installed, data from the external navigation source selected on the
G3X PFD is also displayed on the G5. This requires an ARINC 429 connection between the navigator,
GAD 29, and G5.
For detailed information on connecting external navigators to a G3X system, refer to
190-01115-01
Rev. AN
G3X/G3X Touch Installation Manual - Installation Preparation
Page 2-7
2.1.1.11 COM Radios
The G3X Touch system is capable of displaying and controlling up to two VHF COM radios. Supported
COM radios include:
• GNC 255 (software version 2.10 or later)
• GNC 355
• GTN 635/650/750 (software version 6.11 or later)
• GTR 20
• GTR 200/200B
• GTR 225 (software version 2.10 or later)
• SL30
• SL40
Supported Garmin panel-mount COM radios can be controlled either via the GDU displays or via their own front-panel controls.
The GTR 20 is a remote-mounted COM radio that is entirely controlled via the G3X Touch display, with
no front-panel interface. For GTR 20 installation information, refer to Section 22
and
.
The interface between the G3X Touch system and the COM radio portion of a GTN, GNC 255, or SL30 uses the same RS-232 connection described above for navigation data. Interface to an SL40 COM radio requires a dedicated RS-232 connection to a GDU display. The GTR 20 and GTR 200 connect to the G3X
Touch system via the CAN bus.
For information on connecting and configuring COM radios with the G3X Touch system, refer to
.
The legacy G3X system and GDU 37X displays do not support on-screen display or control of COM radios, and are not compatible with the GTR 20. However, GDU 37X displays do have the ability to send a
COM frequency via RS-232 to the standby position of connected radio.
2.1.1.12 NAV Radios
NAV Tuning
The G3X Touch system is capable of displaying and controlling up to two VHF NAV radios. Supported
NAV radios include:
• GNC 255 (software version 2.20 or later)
• GTN 650/750 (software version 6.70 or later)
• SL30
Supported Garmin panel-mount NAV radios can be controlled either via the GDU displays or via their own front-panel controls.
The interface between the G3X Touch system and the NAV radio portion of a GTN, GNC 255, or SL30 uses the same RS-232 connection described above for navigation data.
For information on connecting and configuring NAV radios with the G3X Touch system, refer to
The legacy G3X system and GDU 37X displays do not support on-screen display or control of NAV radios. However, GDU 37X displays do have the ability to send a NAV frequency via RS-232 to the standby position of a connected radio.
190-01115-01
Rev. AN
G3X/G3X Touch Installation Manual - Installation Preparation
Page 2-8
2.1.1.13 ADS-B
When equipped with a Mode S transponder with extended squitter capability, and a GPS position source that meets TSO performance requirements, the G3X system provides full ADS-B Out capability. Refer to
for additional information.
The G3X system also supports full ADS-B In capabilities, including FIS-B weather and dual-frequency traffic data reception. In a legacy G3X system with GDU 37X displays, ADS-B In is provided by the
GDL 39R receiver. A G3X Touch system with GDU 4XX displays supports ADS-B In via the
GTX 45R/345/345R transponders, the GDL 39R, or the GDL 52R.
.
For information on interfacing a GDL 39R or GDL 52R ADS-B receiver, see the appropriate installation guide (190-11110-00 or 190-02087-10).
2.1.1.14 Transponder
The G3X system can interface to any Garmin transponder with a digital interface (all models except the
GTX 320). The transponder code, operating mode, and flight ID can all be displayed and controlled via the
GDU displays.
A panel-mount transponder such as the GNX 375, GTX 327, 328, 330, 335 and 345 can be controlled either from the GDU displays or via the transponder’s front-panel interface. Remote-mount transponders such as the GTX 23ES, 32, 33, 35R/45R and GTX 335R/345R lack front-panel controls, and are controlled only via the GDU displays.
The transponder connects via RS-232 to the #1 ADAHRS unit, which relays transponder data to the rest of the G3X system via the CAN bus. The ADAHRS provides pressure altitude data to the transponder, so a separate altitude encoder is not required. A G3X Touch system installed with no ADAHRS units does not support transponder integration.
In a G3X system with a transponder and a GTN, the transponder is typically controlled by the G3X system, not the GTN. Note that the GTX 23ES and GTX 35R/45R can only be controlled by the G3X system, not by the GTN.
The GTX 23ES, 33ES, 35R, 45R, 330ES, 335/335R and GTX 345/345R are Mode S transponders with extended squitter capability. When provided with a GPS position source that meets the TSO performance requirements specified in 14 CFR 91.227, these transponders are an acceptable method of complying with the requirements for ADS-B Out. Compliant GPS position sources include the GPS 20A, GTN, GNS
WAAS units, or the internal WAAS GPS contained in certain models of the GTX 335/345. The GDU GPS receiver does not meet the TSO GPS requirements, thus it is not sufficient to provide position data to a transponder for ADS-B Out compliance.
Certain transponders support ADS-B or TIS-A traffic data, and/or FIS-B weather data. See below for
information on traffic ( Section 2.1.1.17
For information on connecting and configuring a transponder with the G3X system, refer to
. Refer to Section 37 for information on performing periodic tests of the
transponder.
For information on installing remote transponders, refer to 190-00906-01 for the GTX 23ES, or
190-01499-10 for the GTX 35R/45R. For all other transponders, refer to the appropriate installation manual.
190-01115-01
Rev. AN
G3X/G3X Touch Installation Manual - Installation Preparation
Page 2-9
2.1.1.15 Autopilot
The G3X system features an advanced digital flight director and autopilot, based around the GSA 28 smart autopilot servo. Servo installation kits are available for numerous popular aircraft, and universal installation brackets are available for other aircraft. Up to five GSA 28 servos are supported (pitch, roll, yaw damper, pitch trim, and roll trim). GSA 28 servos can optionally control aircraft electric trim motors; this keeps the aircraft in trim when the autopilot is engaged, and also provides trim motor speed control and stuck-switch protection when hand-flying. The GSA 28 can also be used as the trim actuator in the pitch and roll axes. The GSA 28 servos also support enhanced stability and protection features (ESP)
which increase safety when hand-flying. For GSA 28 installation information, refer to Section 18
and
. For G3X autopilot and ESP setup and adjustment information, refer to Section 34
or
and flight director operation.
The GMC mode control panels are a family of optional accessories that provide a convenient set of dedicated controls for the G3X autopilot and flight director. A G3X autopilot installation with a GMC mode control panel also has increased redundancy, allowing control of basic autopilot modes via the GMC even when power is removed from all GDU displays.
The GMC 307 supports all the features of the GMC 305, and adds dedicated control knobs for heading and altitude. Autopilot operation in a reversionary condition without operational GDU displays is provided by an RS-232 connection from the GMC 305/307 to the GSA 28 roll servo. For GMC 305/307 installation
information, refer to sections Section 12
The GMC 507 is physically similar to the GMC 307, but it connects to the G3X system via the shared
CAN bus. The GMC 507 adds an additional flight director mode button. For GMC 507 installation information, refer to section
.
In a G3X Touch system with GDU 4XX displays and one or more ADAHRS units, all autopilot and flight director functions can be controlled either from the GDU display or the optional GMC control panel. Refer to the G3X Touch Pilot’s Guide (190-01754-00) for more information.
In a G3X Touch system with no ADAHRS units, one or more G5 displays and a GMC control panel are required for autopilot and flight director operation using the G5. Refer to the G5 Pilot's Guide
(190-02072-00) for more information.
In a legacy G3X system with GDU 37X displays, a GMC control panel is required to enable certain advanced flight director modes; refer to the G3X Pilot’s Guide (190-01115-00) for more information.
Certain third-party autopilots that are designed to be integrated with the G3X system may also be used in conjunction with the G3X flight director and GMC control panel. Consult the third-party autopilot manufacturer for further information.
Third-party digital autopilots that are not integrated with the G3X system are typically connected either via a GDU display RS-232 output that provides NMEA 0183 format data, or via various connections to a
GTN/GNS navigator. Consult the autopilot manufacturer for further information.
The GAD 29B can provide analog heading and course error outputs to non-Garmin analog autopilots.
190-01115-01
Rev. AN
G3X/G3X Touch Installation Manual - Installation Preparation
Page 2-10
2.1.1.16 Weather Data
The G3X system supports a variety of airborne weather data sources:
FIS-B weather data can be provided to GDU displays from a GDL 39R remote-mounted ADS-B receiver.
The GDL 39R can be connected to a single GDU display via RS-232. In a G3X Touch system, the
GDL 39R may also be connected to additional GDU 4XX displays wirelessly using Bluetooth.
A G3X Touch system with GDU 4XX displays can receive FIS-B weather data from GTX 45R, and
GTX 345/345R transponders, via an RS-232 connection from the GTX to each GDU display. These transponders can also simultaneously provide FIS-B weather data to a GTN or GNS WAAS navigator. The legacy G3X system with GDU 37X displays does not support FIS-B weather data from GTX transponders.
The GDU 3X5 and GDU 4X5 displays contain a built-in XM satellite weather receiver. These displays require a separate antenna connection and active XM subscription in order to receive satellite weather data.
For XM antenna installation information, refer to
A G3X Touch system with GDU 4XX displays is also compatible with the GDL 51R SXM receiver and the GDL 52R dual ADS-B/SXM receiver. The GDL 51R/52R connect to each GDU 4XX display via an
RS-232 connection, or wirelessly via Bluetooth.
A WX-500 or similar lightning detector can be used with the G3X Touch system via an RS-232 connection to a GDU 4XX display. The G3X system displays lightning strike or cell data and provides heading data output to the lightning detector.
For any of the above data sources, weather data is displayed only on the GDU displays that are connected to the weather source (either via a RS-232 connection, wirelessly via Bluetooth, or from an internal XM receiver). Weather data is not shared between GDU displays via the CAN bus.
On a GDU display that has access to multiple sources of weather data simultaneously, the pilot may switch between available weather sources at any time.
When connected to a FIS-B weather receiver, the GDU 4XX can receive METARs, TAFs, Winds aloft,
NEXRAD, TFRs, AIRMETs, SIGMETs, PIREPs, and NOTAMs over either an RS-232 or Bluetooth connection. The GDU 4XX can additionally receive, process, and display the FIS-B features, Cloud Tops
Forecast, Icing Forecast, Lightning, and Turbulence Forecast over Bluetooth. An RS-232 connection to a
FIS-B weather receiver will not provide these features. For installations that use RS-232 connections,
Garmin recommends leaving that connection in place and adding a Bluetooth connection.
190-01115-01
Rev. AN
G3X/G3X Touch Installation Manual - Installation Preparation
Page 2-11
2.1.1.17 Traffic
The G3X system supports a variety of airborne traffic data sources:
ADS-B traffic data can be provided by a GDL 39R receiver, via the same connection method used for
FIS-B weather data.
A G3X Touch system with GDU 4XX displays can receive traffic data from a GDL 52R dual ADS-B/
SXM receiver, via the same connection method used for FIS-B weather data.
A G3X Touch system with GDU 4XX displays can receive ADS-B traffic data from GTX 45R and
GTX 345/345R transponders, via the same RS-232 connection used for FIS-B weather data. These transponders can also simultaneously provide ADS-B traffic data to a GTN or GNS WAAS navigator. The legacy G3X system with GDU 37X displays does not support ADS-B traffic data from GTX transponders.
The GTS 8XX active traffic system is compatible with the G3X system. The GTS interface to the G3X system requires an RS-232 connection to a GDU display. TCAS-capable GTS 8XX units also require a separate data connection to the GTX transponder.
TIS-A traffic data can be provided by GTX 23ES, 33, 330, and GTX 335/335R transponders. Traffic data is provided to the G3X system via the CAN bus from the #1 ADAHRS unit, to which the transponder is connected.
Traffic data from various third-party devices that emulate the Garmin TIS-A format is supported, via an
RS-232 connection from the traffic device to a GDU display.
For any of the above data sources, traffic data is shared between GDU displays via the CAN bus. If multiple sources of traffic data are available, the best source is selected automatically. Refer to the Pilot’s
Guide for further information on traffic data source selection.
In an installation that includes a GTN/GNS navigator and transponder with ADS-B or TIS-A traffic capability, traffic data is provided to the GTN/GNS via an ARINC 429 or HSDB (High Speed Data Bus) connection. For further information, refer to
Section 27 and the transponder installation manual.
2.1.1.18 Electrical System
The G3X system supports a variety of connections to the aircraft’s electrical system:
Most important LRUs support dual power inputs, allowing them to be powered from separate dual electrical busses. Alternatively, one of the power inputs may be connected to a backup battery to ensure adequate electrical power supply in the event of alternator failure, or during engine start. Backup batteries designed for the G3X system are available from third-party suppliers, or a backup battery can be integrated into the aircraft’s electrical system design in order to power additional devices.
In a G3X Touch system with GDU 4XX displays, the GAD 27 electrical control system provides lowvoltage protection during engine start, as well as control of the flaps, trim, external lighting, and cockpit lights. The GAD 27 is not compatible with legacy G3X systems that use GDU 37X displays. For further
GAD 27 installation information, refer to
If the aircraft is equipped with a cockpit light dimming system, the GDU displays and various other
Garmin panel-mount avionics support connection to the dimming bus to control display brightness.
The G3X system is compatible with Vertical Power products, via an RS-232 connection to a GDU display.
For further information on interfacing Vertical Power products to the G3X system, consult the manufacturer.
190-01115-01
Rev. AN
G3X/G3X Touch Installation Manual - Installation Preparation
Page 2-12
2.1.1.19 Audio
The G3X system interacts with the aircraft’s audio system in the following ways:
• Audio alerts are generated by the GDU displays for various events, including audio notification of abnormal conditions. Typically, alert audio from the PFD1 GDU is wired to the aircraft’s audio panel or intercom.
• Stereo audio for XM music is provided by the GDU 3X5 and GDU 4X5 displays, and can be connected to any stereo audio panel or intercom.
• A G3X Touch system with GDU 4XX displays may be connected via the CAN bus to the
GMA 245/245R audio panels, allowing full control of audio panel functionality from the GDU display. The GMA 245 is a panel-mounted digital audio panel with intercom and Bluetooth input; the GMA 245R has the same capabilities but is remote-mounted with no front-panel controls. For further information, refer to
, the GMA 245/245R Pilot’s Guide (190-01879-10), and Installation Manual (190-01879-11).
• The GTR 20 and GTR 200 COM radios contain a built-in two-place intercom with alert audio and stereo music inputs. For simple two-place VFR aircraft, the GTR 20 or GTR 200 can provide all audio functionality, with no separate audio panel required. For installations with more complex audio switching requirements, including multiple COM radios, NAV radios, or 4+ seat aircraft, a separate audio panel is recommended.
2.1.1.20 Video
In a G3X Touch system with GDU 4XX displays, each display has a rear connector which supports composite (NTSC/PAL/SECAM) video. Video input to a GDU 4XX display can be used with various cameras or entertainment systems, with the video image displayed on a dedicated MFD page, or in an inset window on the GDU 46X PFD. Wireless remote control of Garmin Virb action cameras is also supported, allowing recording to be started or stopped from the GDU 4XX display.
2.1.1.21 Carbon Monoxide Detector
A CO Guardian or other compatible carbon monoxide detector can be connected to a GDU display via
RS-232, and its data relayed to other displays via the CAN bus. Alerts will appear on the PFD display for excessive carbon monoxide levels, and the current CO level can be displayed in a data field. CO detectors with pulse oximeter functions are also supported. For installation information, consult the CO detector manufacturer.
2.1.1.22 Emergency Locator Transmitter (ELT)
The G3X system can provide NMEA 0183 formatted GPS position data to an ELT, via an RS-232 output from a GDU display. In an installation with a GTN/GNS navigator, an RS-232 output from the IFR GPS using the “Aviation” data format may be preferred. For further ELT interface guidance, consult the ELT manufacturer.
190-01115-01
Rev. AN
G3X/G3X Touch Installation Manual - Installation Preparation
Page 2-13
2.1.1.23 Bluetooth
The GDU 4XX displays in a G3X Touch system include Bluetooth transceivers. This allows a wireless connection to a tablet computer, using Garmin Pilot or another application that supports the Garmin
Connext protocol. The tablet computer can receive GPS position and attitude data from the G3X Touch system, and can exchange flight plan information with the GDU 4XX or with a connected GTN navigator.
In an installation with multiple GDU 4XX displays, the Bluetooth connection to the tablet computer should be made to the PFD1 GDU only. Refer to the G3X Touch Pilot’s Guide (190-01754-00) for Bluetooth connection information.
A tablet computer can also establish a separate Bluetooth connection to a GDL 39R/51R/52R ADS-B receiver, or to a GTX 45R/345/345R transponder. This allows the display of ADS-B traffic and weather data on the tablet computer, using Garmin Pilot or another application that supports the Garmin Connext protocol.
In a G3X Touch system with a GDL 39R ADS-B receiver, the primary connection between the GDL and a single GDU 4XX display is via RS-232. However, Bluetooth may also be used to connect additional
GDU 4XX displays to the GDL 39R, in order to view FIS-B weather data on multiple displays.
2.1.1.24 Standby Instruments
Although there is no regulatory requirement to equip the aircraft with backup flight instruments, Garmin strongly recommends the installation of backup instruments for aircraft that will be flown in other than
Day VFR conditions. In case of an electrical system failure, or in the unlikely event of an issue with the
G3X system, backup instruments should at minimum provide a secondary reference for aircraft attitude, airspeed, and altitude.
The G5 standby flight display is designed as a complementary backup instrument for the G3X system. It features dissimilar hardware and software design to eliminate common-mode failures, supports an optional built-in backup battery, and synchronizes data such as baro setting and selected heading with the G3X system. In conjunction with a GMC mode control panel, the G5 is also capable of driving the GSA 28 autopilot servos even if power is removed from all GDU displays. A G3X Touch system with no
ADAHRS units can also operate the GSA 28 autopilot servos if a G5 and a GMC mode control panel are present. For further information, refer to the G5 installation/operation manual (190-02072-00).
2.2 Electrical Considerations
This section presents information required for planning the electrical layout of the G3X installation.
CAUTION
To avoid damage to the LRUs, take precautions to prevent Electro-Static
Discharge (ESD) when handling connectors and associated wiring. ESD damage can be prevented by touching an object that is of the same electrical potential as the LRU before handling the LRU itself.
2.2.1 Power Specifications
All G3X LRUs are capable of operating at either 14 or 28 VDC (except the GAD 27 which is 14 VDC only, and the GAP 26, see
in Section 5). Table 2-1 and Table 2-2 list supply voltage and current draw
info for the G3X LRUs, use this information when determining power supply requirements. All installed electrical appliances must be considered when determining total power requirements.
190-01115-01
Rev. AN
G3X/G3X Touch Installation Manual - Installation Preparation
Page 2-14
2.2.1.1 GAP 26 Power Requirements
The 010-01074-00 version of the GAP 26 does not require power as it does not have a heater. The initial current vs temperature requirements for the 010-01074-10 and 010-01074-20 are listed in Table 2-1. See
for acceptable wiring configurations.
CAUTION
Do not connect the heated/regulated version of the GAP 26 (010-01074-20) to 28 VDC.
The heated/non-regulated version of the GAP 26 (010-01074-10) may be connected to
either 14V or 28V. See Section 5
for wiring information.
Table 2-1 GAP 26 Initial Current Draw vs Probe Temperature (-10, -20 units only)
Probe Temperature -40°C (-40°F) 0°C (32°F) 50°C (122°F) 100°C (212°F) 175°C (347°F)
Amps 12 Amp 9.25 Amp 7.3 Amp 5.85 Amp 4.36 Amp
Table 2-1 refers to probe temperature at initial turn-on. For example, upon turn-on at -40°C, the standard
(-10) or regulated (-20) heated probes will initially draw 12 amps, but will draw less current as they warm up.
The -10 non-regulated probe draws current proportional to the probe temperature as shown in Table 2-1.
The -20 heated regulated probe uses similar power to the -10 probe when airborne, but will limit the current to regulate the probe temperature to ~75°C (167°F) when the probe temperature reaches this value.
2.2.1.2 Other LRU Power Requirements
Table 2-2 G3X LRU Power Requirements
LRU
GAD 27
GAD 29
GDL 39/39R
Supply Voltage
14 Vdc
28 Vdc
14 Vdc
28 Vdc
14 Vdc
28 Vdc
0.2 Amp
0.1 Amp
0.25 Amp
0.125 Amp
Current Draw
0.2 Amp (varies with connected devices)
Not supported, do not use in 28V installations
GDL 51R
GDL 52R
14 Vdc
28 Vdc
14 Vdc
28 Vdc
0.16 Amp
0.09 Amp
0.29 Amp
0.15 Amp
*Garmin recommends using Mod 1 level GSU 73 in aircraft that use a +28 V supply voltage and intend to monitor current on high voltage devices such as the aircraft alternator.
**The specified current draw is measured with the display backlight set to 100%
190-01115-01
Rev. AN
G3X/G3X Touch Installation Manual - Installation Preparation
Page 2-15
Table 2-2 G3X LRU Power Requirements
LRU
GDU 37X**
Supply Voltage
14 Vdc
28 Vdc
14 Vdc
1.10 Amp
0.540 Amp
1.25 Amp
Current Draw
GDU 45X**
GDU 46X**
28 Vdc
14 Vdc
28 Vdc
14 Vdc
0.7 Amp
2.0 Amp
1.0 Amp
1.25 Amp
GDU 470**
GEA 24
28 Vdc
14 Vdc
28 Vdc
14 Vdc
0.7 Amp
0.43 Amp max (typical external sensor loading)
0.21 Amp max (typical external sensor loading)
0.4 Amp
GI 260
GMC 305
28 Vdc
14 Vdc
28 Vdc
14 Vdc
0.2 Amp
0.050 A (50 mA)
0.028 A (28 mA)
0.120 A (120 mA)
GMC 307
GMC 507
28 Vdc
14 Vdc
28 Vdc
14/28 Vdc
0.067 A (67 mA)
0.20 A (200 mA)
0.11 A (110 mA)
0.1 A (100 mA) GMU 11
GMU 22
12 Vdc
(from GSU 25/GSU 73) Included in GSU 25/GSU 73 Current Draw
14 Vdc 0.2 Amp
GPS 20A
28 Vdc
14 Vdc
0.1 Amp
0.36 Amp (typical)
1.80 Amp (max)
2.80 Amp (max with 1 Amp trim motor at full load)
GSA 28
28 Vdc
14 Vdc
0.20 Amp (typical)
0.90 Amp (max)
1.40 Amp (max with 1 Amp trim motor at full load)
0.2 Amp (includes GMU 22 load)
GSU 25
28 Vdc 0.11 Amp (includes GMU 22 load)
*Garmin recommends using Mod 1 level GSU 73 in aircraft that use a +28 V supply voltage and intend to monitor current on high voltage devices such as the aircraft alternator.
**The specified current draw is measured with the display backlight set to 100%
190-01115-01
Rev. AN
G3X/G3X Touch Installation Manual - Installation Preparation
Page 2-16
Table 2-2 G3X LRU Power Requirements
LRU Supply Voltage
14 Vdc
14 Vdc
1.75 Amp (max)
Current Draw
GSU 73*
28 Vdc 0.80 Amp (max)
0.6 Amp, Typical when receiving
3.0 Amp, Typical when transmitting
7.50Amp, Maximum, 90% modulated into 3:1
VSWR and 11V power input voltage
GTR 20
GTR 200**
28 Vdc
0.30 Amp, Typical when receiving
1.40 Amp, Typical when transmitting
3.75 Amp, Maximum, 90% modulated into 3:1
VSWR and 22 V power input voltage
*Garmin recommends using Mod 1 level GSU 73 in aircraft that use a +28 V supply voltage and intend to monitor current on high voltage devices such as the aircraft alternator.
**The specified current draw is measured with the display backlight set to 100%
190-01115-01
Rev. AN
G3X/G3X Touch Installation Manual - Installation Preparation
Page 2-17
2.3 Wiring/Cabling Considerations
configuration modules) installation information. Section 27 through Section 33 contain interconnect
LRUs/sensors be installed prior to constructing the wiring harnesses and cables.
Use MIL-W-22759/16 (or other approved wire) AWG #22 or larger wire for all connections unless otherwise specified. The supplied standard pin contacts are compatible with up to AWG #22 wire. In cases where some installations have more than one LRU sharing a common circuit breaker, sizing and wire gauge is based on aircraft circuit breaker layout, length of wiring, current draw on units, and internal unit protection characteristics. Do not attempt to combine more than one unit on the same circuit breaker.
Use MIL-C-27500 (or other approved cable) for all shielded cable connections unless otherwise specified.
HSDB (Ethernet) connections may use either aviation grade Category 5 Ethernet cable, or MIL-C-27500 shielded twisted-pair cable.
RG-400 or RG-142 coaxial cable with 50 Ω nominal impedance and meeting applicable aviation regulations should be used for the installation.
2.3.1 Wiring Harness Installation
Use cable meeting the applicable aviation regulation for the interconnect wiring. Any cable meeting specifications is acceptable for the installation. When routing cables, observe the following precautions:
• All cable routing should be kept as short and as direct as possible.
• Check that there is ample space for the cabling and mating connectors.
• Avoid sharp bends in cabling.
• Avoid routing near aircraft control cables.
• Avoid routing cables near heat sources, RF sources, EMI interference sources, power sources (e.g.,
400 Hz generators, trim motors, etc.) or near power for fluorescent lighting.
• Route the GPS antenna cable as far as possible away from all COM transceivers and antenna cables.
• Analog Input wires routed too close to spark plugs, plug wires, or magnetos may result in erratic readings.
The installer shall supply and fabricate all of the cables. Required connectors, pins, etc. are provided with
LRU Installation Kits. Electrical connections for the GMU 22 are made through a round 9-pin connector, and are made through D subminiature connectors for all other LRUs.
defines the electrical characteristics of all input and output signals. Required connectors and associated hardware are supplied with the connector kit.
Contacts for the connectors must be crimped onto the individual wires of the aircraft wiring harness.
Table 1-8 lists contact part numbers (for reference) and recommended crimp tools.
CAUTION
Check wiring connections for errors before connecting any wiring harnesses.
Incorrect wiring could cause internal component damage.
190-01115-01
Rev. AN
G3X/G3X Touch Installation Manual - Installation Preparation
Page 2-18
2.3.1.1 Backshell Assemblies
Connector kits include backshell assemblies. The backshell assembly houses the configuration module and a thermocouple reference junction. Garmin’s backshell connectors give the installer the ability to quickly and easily terminate shield grounds at the backshell housing. The instructions needed to install the
Jackscrew Backshell, Configuration Module, Shield Block Ground, and Thermocouple are located in
.
NOTE
The GDU 37X rear connector (J3701) is electrically isolated. For installations using shielded cables, a ground pin must be tied to the connector shell (
).
2.3.1.2 Configuration Module
The G3X system is designed to store configuration and calibration data in multiple locations to retain the
installed in the connector backshell of the PFD1 display to store important configuration data. Only the
PFD1 display uses a configuration module; in systems using a GSU 73, an additional configuration module
is installed in the GSU 73 connector backshell. See Section 25
for installation instructions.
Figure 2-3 Original Green Configuration Module P/N 011-00979-20
190-01115-01
Rev. AN
G3X/G3X Touch Installation Manual - Installation Preparation
Page 2-19
Figure 2-4 shows the Apple® iOS compatible configuration module that installs on the GDU 4XX (PFD 1)
connector backshell. This configuration module is required for using Connext capability with Apple products. Contact Garmin Aviation Product Support if the GDU 4XX unit was sold with an original green configuration module. See
for installation instructions.
NOTE
Please refer to the G3X Touch Pilot’s Guide (190-01754-00) for guidance in using
Connext Bluetooth connections to Garmin Pilot device(s).
To test for the installation of the Apple iOS compatible configuration module, enter config mode, select the
System Information page, highlight PFD1, press Menu, and run the Apple compatibility test.
Figure 2-4 Apple iOS Compatible Black Configuration Module P/N 010-12253-00
2.3.1.3 CAN Bus
The primary digital interface used to exchange data between LRUs in the G3X system is the Controller
Area Network, also known as the CAN bus. CAN was developed by Bosch GmbH in the 1980s, and its specifications are currently governed by ISO 11898-2. CAN is widely used in aviation, automotive, and industrial applications due to its simplicity and reliability.
2.3.1.3.1 CAN Bus Architecture
The electrical architecture of the CAN bus takes the form of a linear “backbone” consisting of a single
CAN bus from end to end should be 20 meters (66 feet) or less. At each of the two extreme ends of the
CAN bus, a 120 Ω resistor is installed to “terminate” the bus. In the G3X system, termination resistors are provided either within the LRUs themselves, or via termination adapters that plug into an LRUs CAN
connection (see Section 2.3.1.3.3
).
CAN BUS BACKBONE: CONSISTS OF TWISTED, SHIELDED PAIR
WIRING CONNECTED TO CAN HI AND CAN LO OF EACH LRU, AND
PROPERLY TERMINATED LRUs ON BOTH ENDS OF BUS.
LRU LRU
190-01115-01
Rev. AN
TERMINATION CONNECTIONS
Figure 2-5 CAN Bus Backbone
G3X/G3X Touch Installation Manual - Installation Preparation
Page 2-20
Multiple LRUs may be connected in a daisy-chain manner along the backbone of the CAN bus
DAISY-CHAINED LRUs
LRU LRU
LRU LRU
LRU
TERMINATED BACKBONE LRUs
Figure 2-6 Daisy-chained LRUs on Backbone
Daisy-chained LRUs (LRUs not at the extreme ends of the CAN bus) connect to the CAN backbone
kept as short as possible, and should not exceed 0.3 meters (1 foot). The best way to connect devices between the ends of the CAN bus while maintaining short stub node lengths is to splice the connections as close to the device as practical (
). Unshielded wire sections should be kept as short as practical.
Multiple devices must not connect to the CAN bus backbone at the same point. Rather than splicing two or more stub node connections together, the CAN bus should instead be daisy chained from one device to the
LRU
Max. node length
0.3 meter (1 ft)
LRU
LRU LRU
LRU
Figure 2-7 Node Connections
190-01115-01
Rev. AN
G3X/G3X Touch Installation Manual - Installation Preparation
Page 2-21
The layout of the CAN bus must be a single linear backbone with exactly two distinct end points
LRU LRU
LRU LRU
LRU
LINEAR CAN BACKBONE, DAISY-CHAINED CONNECTIONS WITH SHORT STUB
NODE LENGTHS. MULTIPLE LRUs ARE NOT CONNECTED TO BACKBONE AT
THE SAME LOCATION.
Figure 2-8 Correct CAN Wiring Example
LRU LRU LRU LRU LRU
LRU
HUB
DEVICE
LRU LRU LRU LRU LRU
AVOID “T” OR “Y” SHAPE AVOID STAR SHAPE DO NOT USE THIRD-PARTY
HUB DEVICES
Figure 2-9 Incorrect CAN Wiring Examples
190-01115-01
Rev. AN
G3X/G3X Touch Installation Manual - Installation Preparation
Page 2-22
2.3.1.3.2 CAN Bus Wiring
Wiring used for the CAN bus should be shielded twisted-pair cable, MIL-C-27500 or equivalent. 22 AWG or larger wire is recommended for physical robustness and ease of installation. The shields for each CAN bus wire segment should be interconnected, forming a continuously connected shield from one end of the
CAN bus to the other (Figure 2-10 and
). At minimum, the CAN bus shield should always be grounded to the device connector backshells at the two extreme ends of the bus, but it is acceptable to also ground the shield at any or all other devices on the CAN bus.
Figure 2-10 CAN Bus Shield Grounding
For proper CAN bus operation, it is important for all devices on the CAN bus to share a common power ground reference. Connect all LRU power ground pins to a single common ground point - do not use local ground points or use the aircraft structure as a ground return path.
190-01115-01
Rev. AN
G3X/G3X Touch Installation Manual - Installation Preparation
Page 2-23
2.3.1.3.3 CAN Bus Termination
At each of the two extreme ends of the CAN bus backbone, a 120 Ω resistor is installed to terminate the bus. In the G3X system, separate resistors are not required. Instead, termination resistors are provided either within the LRUs themselves, or via termination adapters that plug into an LRU’s CAN connection.
• The GAD 29, GEA 24, GMA 245, GMU 11, GPS 20A, GSU 25, and G5 installation kits provide a
9-pin termination adapter that provides termination when attached to the device’s main connector.
The termination adapter contains a 120 Ω resistor that is connected between pins 1 and 2 ( Figure
).
• The GDU 37X, GDU 4XX, GAD 27, and GSU 73 contain a 120 Ω resistor inside the unit that provides termination when the CAN LO pin is connected externally to the CAN TERM pin
• The GMC 507, GSA 28, and GTR 20/200 contain a 120 Ω resistor inside the unit that provides termination when the two CAN TERM pins are connected together (
).
• The GI 260 does not have provisions for CAN termination, and cannot be installed at the end of the CAN bus. The total amount of extra wire length added to the CAN HI and CAN LO wires on the GI 260 pigtail harness should not exceed 0.4 meters (15 inches).
GARMIN CAN TERMINATOR
Figure 2-11 CAN Bus Termination (011-02887-00) for GAD 29, GEA 24, GMA 245, GMU 11,
GPS 20A, GSU 25, and G5
1
2
3
Figure 2-12 CAN Bus Termination for GAD 27, GDU 37X/4XX, and GSU 73
190-01115-01
Rev. AN
Figure 2-13 CAN Bus Termination for GSA 28
G3X/G3X Touch Installation Manual - Installation Preparation
Page 2-24
Figure 2-14 CAN Bus Termination for GTR 20/200
CAN bus should not be terminated (Figure 2-16).
LRU LRU
LRU LRU
LRU
CORRECT - CAN BUS TERMINATED AT EACH END OF BACKBONE
Figure 2-15 Correct CAN Bus Termination Example
LRU
TERM
LRU
LRU
LRU
INCORRECT - ONE OF THE TERMINATIONS IS NOT AT END OF BACKBONE
LRU
LRU LRU
LRU LRU
LRU
190-01115-01
Rev. AN
INCORRECT - ONLY ONE END OF BACKBONE IS TERMINATED
Figure 2-16 Incorrect CAN Bus Termination Examples
G3X/G3X Touch Installation Manual - Installation Preparation
Page 2-25
2.3.1.3.4 CAN Bus LRU Removal Guidelines
The following should be considered when removing an LRU from the ends of G3X CAN network:
• GEA 24, GSU 25, GAD 29, GPS 20A, G5, or other devices that uses the 9-pin CAN termination adapter: The CAN bus will remain terminated as long as the CAN termination adapter is left connected.
• GDU 37X, GDU 4XX, GAD 27, GMC 507, or GSU 73: The CAN bus will be unusable until the
LRU is reconnected, or the bus is properly terminated at both ends of the CAN backbone.
• GSA 28: A removal adapter (part number 011-03158-00) is provided with each GSA 28 connector kit. This adapter can be used when a GSA 28 is removed from the aircraft. The removal adapter keeps the node on the CAN bus in the same state as when the servo was installed (either terminated or un-terminated). The removal adapter also allows trim signals to pass through when no servo is installed.
2.3.1.3.5 CAN Bus Installation Guidelines
For maximum reliability of the CAN bus, the following guidelines should be followed:
• The CAN bus backbone must be a single linear path with exactly two distinct ends. CAN bus connections should be “daisy chained” from device to device. Avoid “star” and “Y” topologies, and do not use a hub device (see
).
• The overall length of the bus should not exceed 20 meters (66 feet).
• Keep all stub node connections as short as practical. The maximum length of any stub node connection is 0.3 meters (1 foot).
• Avoid connecting more than one device to the CAN bus backbone at the same point. Instead, daisy chain the CAN bus backbone from one device to the next.
• Observe proper wiring, shielding, and grounding requirements described in section
.
• Terminate the CAN bus at the two extreme ends of the bus, as described in
.
• When adding a new device to the CAN bus, evaluate proposed modifications to the CAN bus wiring connections to ensure compliance with all above requirements.
2.3.1.3.6 CAN Bus Troubleshooting
CAN is very simple, and a properly installed CAN bus is normally very reliable. If problems are occurring, there is a good reason and the following steps can help to identify the issue.
1. Review the status LED of devices on the CAN bus such as the GSU25, GEA24, and GSA 28 servos (see
). The status indications are listed in Table 2-3.
No Light
Steady Green
Flashing Green
Red
LED Indication
Alternating Red/Green
Table 2-3 Status LED Indications
Description
No Power
On, but not communicating via CAN Bus
On and communicating via CAN Bus
Hardware Fault
CAN bus network error two similar devices are configured with the same unit ID
190-01115-01
Rev. AN
G3X/G3X Touch Installation Manual - Installation Preparation
Page 2-26
2. Make sure that the CAN bus is daisy-chained between CAN device around the system, and that
CAN devices are not connected via a single point like a star or routed through a hub device. This can cause unwanted signal reflections and “orphan” some devices on the bus and prevent their communication.
3. Make sure the CAN bus is terminated in only two locations, and only at the extreme ends of the
CAN bus.
4. With power removed, remove a connector from one of the devices that is not located at either of the extreme ends of the CAN bus. a) Using an ohm meter, verify that the resistance between the CAN HI and CAN LO pins on the con nector is 60 ohms. This will verify that the CAN backbone is properly terminated at each end (two
120 ohm terminating resistors in parallel). b) A resistance of 120 ohms indicates that one of the two required CAN terminations is missing.
c) A resistance of 40 ohms or less indicates that too many terminations are installed.
5. Verify that the CAN HI and CAN LO signals are not swapped, shorted together, or open-circuited at any LRU connector.
6. Verify that the CAN HI and CAN LO signals are not shorted to ground (this can happen when shielded wire is installed incorrectly).
7. Highlight each device on the configuration mode system information page (
verify that the value displayed for Network Error Rate is a steady 0% (Figure 2-17).
Figure 2-17 Network Error Rate (configuration mode)
8. Power up only the PFD1 display and one other CAN device at a time, and verify the connection quality for each device. Sometimes a device will communicate with PFD1 only when it is the only powered device on the CAN bus, if one or more of the above issues is present. Evaluating each
CAN device in turn can help narrow down a problem.
9. It is very important for each device on the CAN bus to share a common power/signal ground.
Ground potential differences between devices on the CAN bus can cause communication errors.
Ground devices to a common ground bus, not to the airframe or to multiple grounding buses.
190-01115-01
Rev. AN
G3X/G3X Touch Installation Manual - Installation Preparation
Page 2-27
2.4 Mechanical Considerations
This section presents all information required for planning the physical layout of the G3X installation.
2.4.1 Physical Specifications
Use Table 2-4 to determine panel requirements. All width, height, and depth measurements are taken with unit rack (if applicable) and connectors. LRU dimensions are listed in each LRU section. Panel cutout templates are available for the GDU 37X, GDU 45X, GDU 46X, GDU 470, GMC 305, and GMC 307 in the respective LRU sections of this document. Cutout templates for the GDU 37X/4XX displays and the
GMC 507 are also available in digital form (.DXF files) from the G3X manuals download page on www.garmin.com
.
Table 2-4 G3X LRU Physical Specifications
LRU Width Height Depth Unit Weight
Weight of Unit and Connector(s)
GAD 27
(Flaps/
Lights/Trim
Controller)
3.78 inches
[96.01 mm]
1.954 inches
[49.63 mm] no connector
3.569 inches
[90.65 mm] with connector
5.204 inches
[132.18 mm] no connector
6.533 inches
[165.93 mm] with connector
0.64 lbs
(0.29 kg)
0.97 lbs
(0.44 kg)
GAD 29
(ARINC
429
Adapter)
6.10 inches
[154.9 mm]
1.48 inches
[37.6 mm]
3.23 inches [82.0 mm] no connector
5.10 inches [129.4 mm] w/connector
5.54 inches 140.7 mm] w/connector and CAN terminator
GAD 29 0.38 lbs
(0.172 kg)
GAD 29
0.63 lbs
(0.285 kg)
GAP 26
-00, -10
(Air Data
Probe)
0.82 inches
[20.9 mm]
16.0 inches
[406.4 mm]
6.12 inches [157.7 mm]
-00 probe:
0.33 lbs
(0.15 kg)
-10 probe:
0.39 lbs
(0.18 kg)
NA
*weight includes nut plate
190-01115-01
Rev. AN
G3X/G3X Touch Installation Manual - Installation Preparation
Page 2-28
LRU
GAP 26
-20
(Air Data
Probe and
Heater
Control
Box)
GDL 39R
GDL 51R
GDL 52R
GDU 370
(Display)
GDU 375
(Display)
GDU 450
(Display)
GDU 455
(Display)
GDU 460
(Display)
Table 2-4 G3X LRU Physical Specifications
Width
Probe
.82 inches
[20.9 mm]
Control Box
2.25 inches
[57.0 mm]
(includes wiring grommet and screw heads, but not harness)
5.00 inches
(127.0 mm)
Height
Probe
16.0 inches
[406.4 mm]
Control Box:
1.11 inches
[28.2 mm]
1.63 inches
(41.35 mm)
Depth
6.12 inches
[157.7 mm]
Control Box:
4.55 inches
[115.6 mm]
6.17 inches
(156.7 mm)
Unit Weight
-20 probe:
0.39 lbs
(0.18 kg)
-20 control box
0.36 lbs
(0.16 kg)
6.10 inches
(154.9 mm)
1.60 inches
(40.6 mm)
6.04 inches
(153.4 mm)
6.04 inches
(153.4 mm)
7.83 inches
(198.8 mm)
7.83 inches
(198.8 mm)
5.00 inches
(127.0 mm)
3.41 inches
(86.6 mm)
17.7 oz
(502 g)
0.78 lbs
(0.35 kg)
0.83 lbs
(0.38 kg)
1.6 lbs
(0.71 kg)
8.00 inches
(203.0 mm)
5.93 inches
(150.5 mm)
8.00 inches
(203.0 mm)
5.93 inches
(150.5 mm)
10.85 inches
(275.5 mm)
7.82 inches
(198.6 mm)
GDU 465
(Display)
10.85 inches
(275.5 mm)
*weight includes nut plate
7.82 inches
(198.6 mm)
Depth behind panel including recommended backshell 3.68 inches
(93.4 mm)
Depth behind panel including recommended backshell 3.68 inches
(93.4 mm)
3.57 inches
(90.7 mm)
2.71 lbs
(1.23 kg)
2.84 lbs
(1.29 kg)
4.60 lbs
(2.09 kg)
3.57 inches
(90.7 mm)
4.73 lbs
(2.15 kg)
Weight of Unit and Connector(s)
NA
19.5 oz
(552 g)
0.904 lbs
(0.41 kg)
0.954 lbs
(0.43 kg)
1.8 lbs*, (0.803 kg)
1.9 lbs*, (0.862 kg)
2.98 lbs*, (1.35 kg)
3.11 lbs*, (1.41 kg)
4.81 lbs*, (2.18 kg)
4.94 lbs*, (2.24 kg)
190-01115-01
Rev. AN
G3X/G3X Touch Installation Manual - Installation Preparation
Page 2-29
LRU
GDU 470
(Display)
Width
Table 2-4 G3X LRU Physical Specifications
Height
6.01 inches
(152.6 mm)
7.82 inches
(198.6 mm)
Depth
Depth behind panel including recommended backshell 3.68 inches
(93.4 mm)
3.0 inches (76.2 mm)
5.0 inches (127.0 mm) w/connectors
Unit Weight
2.66 lbs
(1.21 kg)
0.71 lbs
(0.322 kg)
GEA 24
(EIS)
6.5 inches
(165.1 mm)
1.9 inches
(48.3 mm)
GI 260
(AOA
Indicator)
Including
Socket
Mount
GMC 305
(Mode
Controller)
GMC 307
(Mode
Controller)
GMC 507
(Mode
Controller)
GMU 11
(Magnetom eter)
GMU 22
(Magnetom eter)
1.36 inches
(34.6 mm)
6.25 inches
(158.8 mm)
6.25 inches
(158.8 mm)
6.25 inches
(158.8 mm)
2.74 inches
(6.96 mm)
N/A
3.19 inches
(81.0 mm)
1.85 inches
(47.0 mm)
2.10 inches
(53.3 mm)
2.10 inches
(53.3 mm)
0.93 inches
(2.36 mm)
2.10 inches
(53.3 mm)
GPS 20A
5.06 inches
(128.5 mm)
1.76 inches
(44.7 mm)
GSA 28
(Servo
Actuator)
2.5 inches
(63.5 mm)
4.0 inches
(101.6 mm)
GSU 25
(ADAHRS)
4.0 inches
(101.6 mm)
*weight includes nut plate
2.12 inches
(53.8 mm)
2.61 inches
(66.2 mm) w/conn
3.37 inches (85.6 mm)
Diameter
3.49 inches (88.65 mm)
0.35 lbs
(0.158 kg)
0.56 lbs
(0.254 kg)
2.8 inches (71.1 mm)
1.40 lbs
(0.635 kg)
2.5 inches (63.5 mm)
0.48 lbs
(0.217 kg)
Weight of Unit and Connector(s)
2.93 lbs (1.33 kg)
1.6 lbs, (0.725 kg)
NA
0.60 lbs, (0.272 kg)
0.72 lbs, (0.327 kg)
0.78 lbs, (0.354 kg)
0.302 lbs
(0.1368 kg)
0.50 lbs, (0.226 kg)
0.67 lbs
(0.304 kg)
for connector/ accy weights
0.68 lbs, (0.310 kg)
190-01115-01
Rev. AN
G3X/G3X Touch Installation Manual - Installation Preparation
Page 2-30
LRU
GSU 73
(ADAHRS/
EIS)
GTP 59
GTR 20
GTX
23ES
GTX 35R
GTX 45R
-
Width
6.15 inches
(156.2 mm)
1.28 inches
(32.4 mm)
Modular
Rack
1.72 inches
(44 mm)
Remote
Rack
1.78 inches
(45 mm)
6.3 inches
(160 mm)
6.3 inches
(160 mm)
Table 2-4 G3X LRU Physical Specifications
5.50 inches
(139.7 mm)
3.96 inches
(100.6 mm)
-
Height
Modular
Rack
6.30 inches
(160 mm)
Remote
Rack
6.92 inches
(176 mm)
1.7 inches
(43 mm)
1.7 inches
(43 mm)
Depth
5.50 inches (139.8 mm)
7.33 inches (186.2 mm) w/connectors
-
8.80 inches (223.5 mm)
10.22 inches (259.5 mm) w/connectors
11.05 inches (281 mm)
Including Connectors
(measured from front face of unit to rear of connector backshells)
Unit Weight
3.1 lbs
(1.406 kg)
0.3 lbs
(0.136 kg)
1.23 lbs
(0.560 kg)
3.1 lbs
(1.41 kg)
9.9 inches (252 mm)
(unit, mount, and connector backshells)
9.9 inches (252 mm)
(unit, mount, and connector backshells)
-
Weight of Unit and Connector(s)
3.5 lbs, (1.587 kg)
1.34 lbs, (0.608 kg)
Modular Rack, Unit
, and Connectors
3.9 lbs (1.77 kg)
1.7 lbs (0.77 kg)
2.0 lbs (0.91 kg)
Remote Rack, Unit
, and Connectors
4.4 lbs (2.00 kg)
Unit, Standard
Mouting Tray,
Backplate, and
Connectors
2.5 lbs (1.13 kg)
Unit, Standard
Mouting Tray,
Backplate, and
Connectors
2.9 lbs (1.32 kg)
*weight includes nut plate
190-01115-01
Rev. AN
G3X/G3X Touch Installation Manual - Installation Preparation
Page 2-31
2.4.2 Cooling Requirements
While no forced cooling air is required for the G3X system, it is highly recommended that the air behind the panel be kept moving (by ventilation or a fan). Units tightly packed in the avionics stack heat each other through radiation, convection, and sometimes by direct conduction. Even a single unit operates at a much higher temperature in still air than in moving air. Fans or some other means of moving the air around electronic equipment are usually a worthwhile investment.
No cooling air is required for most G3X LRUs, with the following exceptions:
• No cooling air is required for the GSU 73, however the GSU 73 should be mounted in a location that provides adequate airflow to comply with the maximum outer case temperature listed in
.
• No cooling air is required for the GTR 20/200, however, as with all electronic equipment, lower operating temperatures extends equipment life. Reducing the operating temperature by 15° to
20°C (27° to 36°F) reduces the mean time between failures (MTBF).
NOTE
Avoid installing the G3X LRUs near heat sources. If this is not possible, ensure that additional cooling is provided. Allow adequate space for installation of cables and connectors. The installer will supply and fabricate all of the cables. All wiring should be in accordance with FAA AC 43.13
1B and AC 43.13
2B.
2.4.3 Compass Safe Distance
After reconfiguring the avionics in the cockpit panel, if the unit is mounted less than 12 inches from the compass, recalibrate the compass and make the necessary changes for noting correction data.
2.5 LRU/Sensor Installation Information
Each LRU/sensor has unique considerations that the installer should be familiar with before beginning the physical installation. Become familiar with all installation information by studying sections 3-18 of this document before actually beginning the installation of the LRUs/sensors.
2.5.1 External Navigator Connection/Configuration
External Navigators are connected LRUs that can be used for GPS navigation, as well as providing a backup source of position data in the event that all other sources of GPS data are unavailable. For installations without a GPS 20A, failure of a single GDU or GPS antenna (in a multi-display/multi-antenna installation) would cause the system to use GPS information from the remaining functional GDU. If no
GPS data is available from any operating GDU, the remaining GDUs will use GPS position data from an external GPS navigator (GNS 4XX/5XX, GNS 480, or GTN 6XX/7XX series unit, see
or
) if installed/configured (accuracy will be degraded when using an external GPS navigator).
The G3X automatically assigns the hierarchy of any connected external navigation devices. The first device found (by software) with GPS capability becomes the #1 external navigator. If two equal devices are found (as in dual GTN/GNS installations), the RS-232 serial port number of the GDU 4XX/37X determines the hierarchy. GTN #1 should always be connected to a lower numbered port on the PFD.
GTN #2 can be connected to a higher numbered port on the PFD or to any port in the MFD. In the case of an SL 30 or GNC 255 being added to a system with a GTN, the SL 30 or GNC 255 gets assigned as the #2 external navigator. The hierarchy applies to the entire navigation radio even if only the GPS source is in use. So, in a system with a GTN 625 and a GNC 255, GPS1 and NAV2 (respectively) would be available as external navigation sources.
190-01115-01
Rev. AN
G3X/G3X Touch Installation Manual - Installation Preparation
Page 2-32
3 GAD 27 (FLAPS/LIGHTS/TRIM CONTROLLER) INSTALLATION
This section contains general information as well as installation information for the GAD 27. Use this section to mount the GAD 27 unit.
Figure 3-1 GAD 27 Unit View
3.1 Equipment Description
The GAD 27 is a small, compact, all solid state (no relays) integrated controller that provides a solution to many of the typical airframe interfacing needs of G3X-equipped aircraft. Configuration of the GAD 27 is conveniently handled through the PFD without requiring the use of a laptop or other external device. The following is a summary of the functionality provided by the GAD 27.
CAUTION
The GAD 27 is not intended for 28V installations.
Flap Controller
The Flap Controller interfaces directly to the flap motor and uses flap position measured by the GEA 24 from an external position sensor to support up to 8 pre-programmed flap settings. The GAD 27 can automatically move the flaps between pre-programmed positions in response to a momentary press of the flap control switch by the pilot. Each momentary press of the flap switch causes the flaps to move by one step in the specified direction, stopping at the next pre-programmed position.
For example, Up, Middle, and Down pre-programmed flap positions can be defined. By "bumping" the momentary flap switch downward, the GAD 27 will automatically move the flaps from the Up position to the Middle position in the downwind. Similarly, after turning final, the pilot can bump the switch downward again and the GAD 27 will automatically extend the flaps to the full down position. Since the
GAD 27 receives airspeed from the G3X Touch system, it can also prevent flap extension when the
190-01115-01
Rev. AN
G3X/G3X Touch Installation Manual - GAD 27 Installation
Page 3-1
airspeed is above user-defined limits.
Optional flap limit switches can also be used with the GAD 27, which will cause the flap motor to stop upon reaching the extreme ends of its travel.
If the flap switch is held longer than 1 second, the flaps will run in the specified direction until the flap switch is released or the flap limit switch is triggered. This method of manually moving the flaps is not affected by user-defined airspeed limits. This behavior can also be used in conjunction with a nonmomentary switch in order to fully retract the flaps with a single pilot action. Note that if any of the preprogrammed flap positions are negative (i.e. "reflexed") the flaps will still stop at the pre-programmed
"zero" position during manual flap retraction.
Aircraft Trim
Aircraft Trim provides trim mixing of pilot and copilot trim switches to provide a combined single interface to the trim motors or autopilot servos. Switches used on pilot/copilot control sticks do not supply trim motor power or control relays (just provide ground to discrete inputs) which improves switch reliability. No external relays are needed, the stick switches can be wired directly to the GAD 27.
Discrete Inputs
Provides 9 additional user configurable discrete inputs (in addition to the 4 provided by the GEA 24).
Lighting Bus Outputs
One to three external panel mounted potentiometers (dimmer controls) can be mapped to any of the six lighting bus outputs with configurable lighting curves to meet all the typical lighting bus needs of the aircraft.
There are two types of lighting bus outputs:
• A voltage output which can be used as a reference voltage. This input cannot source current to drive lights.
• A PWM designed to dim LED or incandescent bulbs.
Light Control with Flashing
Controls up to two external lights using simple low power switches to ground discrete inputs. An alternating flash (wig-wag) function can either be switch activated or automatically turned on/off based on a user-selected airspeed.
Voltage Stabilizer
Provides a 12V power bus output to keep essential avionics online during engine start when battery voltage drops.
3.1.1 Status LED
The GAD 27 has an LED on its outer case that indicates its current status. See Section 36.1.1
for details.
190-01115-01
Rev. AN
G3X/G3X Touch Installation Manual - GAD 27 Installation
Page 3-2
3.2 Equipment Available
3.2.1 Required Equipment
Model
GAD 27
Table 3-1 GAD 27 Part Numbers
Assembly Part
Number
010-01525-00
Unit Only Part
Number
011-03876-00
3.2.2 Additional Equipment Required
Table 3-2 Contents of GAD 27 Connector Kit (011-03877-00)
Item
Backshell w/Hdw, Jackscrew, 15/26 Pin
Backshell w/Hdw, Jackscrew, 50/78 Pin
Terminal Block Label Flags
Ring Terminal, Insulated, 14-16 AWG, #6
D-Sub Connector Receptacle, Crimp Socket, 15 pin
D-Sub Connector Receptacle, Crimp Socket, 50 pin
Military Crimp Socket Contact, Size 20, 20-24 AWG
Garmin P/N
011-01855-01
011-01855-04
161-04025-00
235-00094-00
330-00625-50
330-00625-50
336-00022-02
Quantity
1
1
1
12
1
1
70
3.3 General Specifications
See
for power/current specifications, and Section 2.4.1
for dimension/weight specifications.
3.4 Mounting Requirements
The GAD 27 is remotely mounted and is secured to the airframe using four screws supplied by the installer. Refer to
for outline and installation drawings.
3.5 Unit Installation
Fabrication of a wiring harness is required. Sound mechanical and electrical methods and practices are recommended for installation of the GAD 27. Refer to
for wiring considerations, and to
for pinouts.
1. Mount the unit to a suitable mounting location using (4) #10-32 pan or hex head screws.
2. Assemble the connector backshells and wiring harness.
3. Connect backshell connectors.
4. Screw down ring terminals to terminal block. The screws in the terminal block should be removed, the ring terminal inserted, and then the screw replaced.
190-01115-01
Rev. AN
G3X/G3X Touch Installation Manual - GAD 27 Installation
Page 3-3
3.6 Outline and Installation Drawings
.390 9.91
3.000 76.20
.277 7.04
1.831 46.51
CENTER OF GRAVITY
6.533 165.93
4.650 118.11
NOTES:
1.
DIMENSIONS: INCHES [MM].
2.
DIMENSIONS ARE SHOWN FOR REFERENCE ONLY.
3.780 96.01
.100 2.54
.984 24.99
CENTER OF GRAVITY
3.215 81.66
CENTER OF GRAVITY
4.687 119.05
5.204 132.18
3.569 90.65
1.723 43.77
.040 1.02
TYPICAL THICKNESS
BENEATH FASTENER HEAD
190-01115-01
Rev. AN
Figure 3-2 GAD 27 Outline Drawing
G3X/G3X Touch Installation Manual - GAD 27 Installation
Page 3-4
GAD 27
CONNECTOR KIT
011-03877-00
P271
GAD 27
CONNECTOR KIT
011-03877-00
GAD 27
011-03876-00
TB273
J272
J271
P272
011-01855-01
330-00625-15
011-01855-04
330-00625-50
190-01115-01
Rev. AN
Figure 3-3 GAD 27 Installation Drawing
G3X/G3X Touch Installation Manual - GAD 27 Installation
Page 3-5
4 GAD 29/29B (ARINC 429 ADAPTER) INSTALLATION
This section contains general information as well as installation information for the GAD 29. Use this section to mount the GAD 29 unit.
NOTE
A GAD 29 cannot be installed in a system that also includes a GSU 73. For ARINC
429 I/O, use the appropriate pins on the GSU 73 instead.
NOTE
All information for the GAD 29 is applicable to the GAD 29B unless explicitly noted.
Figure 4-1 GAD 29 Unit View
4.1 Equipment Description
The GAD 29 allows the G3X system to interface to IFR navigators such as the GNC, GNS, GNX, GPS and
GTN series. The GAD 29 has a 25 pin D-sub connector and a 9 pin D-sub connector. These connectors will provide the following functionality:
• 2 Low Speed ARINC 429 Transmitters
• 4 Low Speed ARINC 429 Receivers
• 1 CAN Network Port
• *Analog Outputs
• *Excitation Pass Through
*GAD29B only
190-01115-01
Rev. AN
G3X/G3X Touch Installation Manual - GAD 29 Installation
Page 4-1
4.1.1 Status LED
The GAD 29 has an LED on its outer case that indicates its current status. See Section 36.1.1
for details.
4.2 Equipment Available
4.2.1 Required Equipment
Model
GAD 29
Table 4-1 GAD 29 Part Numbers
Assembly Part
Number
010-01172-00
Unit Only Part
Number
011-03236-00
4.2.2 Additional Equipment Required
Table 4-2 Contents of GAD 29 Connector Kit (011-03271-00)
Item
Backshell w/Hdw, Jackscrew, 9 Pin
Backshell w/Hdw, Jackscrew, 25 Pin
Conn, Plug,D-Sub, Crimp Pin, Commercial, 25 CKT
Conn, Rcpt, D-Sub, Crimp Socket, Commercial, 09 CKT
Contact, Socket, Military Crimp, Size 20
Contact ,Pin, Military Crimp, Size 20
Garmin P/N
011-01855-00
011-01855-02
330-00624-25
330-00625-09
336-00022-02
336-00024-00
Quantity
1
1
1
1
11
27
4.3 General Specifications
See
for power/current specifications, and Section 2.4.1
for dimension/weight specifications.
4.4 Mounting Requirements
The GAD 29 will mount remotely. The GAD 29 will be secured to the airframe using four screws supplied by the installer. Refer to
for outline and installation drawings.
4.5 Unit Installation
Fabrication of a wiring harness is required. Sound mechanical and electrical methods and practices are recommended for installation of the GAD 29. Refer to
for wiring considerations, and to
for pinouts.
1. Mount the unit to a suitable mounting location using (4) #10-32 pan or hex head screws.
2. Assemble the connector backshells and wiring harness.
3. Connect CAN terminator to unit if required (
4. Connect backshell connectors.
190-01115-01
Rev. AN
G3X/G3X Touch Installation Manual - GAD 29 Installation
Page 4-2
4.6 Outline and Installation Drawings
190-01115-01
Rev. AN
Figure 4-2 GAD 29 Outline Drawing
G3X/G3X Touch Installation Manual - GAD 29 Installation
Page 4-3
190-01115-01
Rev. AN
Figure 4-3 GAD 29 Installation Drawing (no CAN terminator)
G3X/G3X Touch Installation Manual - GAD 29 Installation
Page 4-4
190-01115-01
Rev. AN
Figure 4-4 GAD 29 Installation Drawing (with CAN terminator)
G3X/G3X Touch Installation Manual - GAD 29 Installation
Page 4-5
5 GAP 26 (PITOT/AOA PROBE) INSTALLATION
This section contains information for the GAP 26 Pitot/AOA (Angle of Attack) probe. Use this section to install the GAP 26.
5.1 Equipment Description
The GAP 26 Pitot/AOA (Angle of Attack) probe is an air data probe intended for use in non FAA certified aircraft, including light sport and home-built aircraft. This air data probe is intended to be used as part of the G3X system.
The function of the GAP 26 is to provide pitot and AOA pressures to the GSU 25 for the purpose of displaying airspeed and AOA to the pilot as part of the G3X system. The GAP 26 does not provide a static pressure source to the GSU 25. There are three different versions of the GAP 26, the -00 (unheated), the
-10 (heated, for ice protection), and the -20 (heated, with ice protection and regulated temperature limit).
All versions of the GAP 26 have identical aerodynamic performance including identical internal water separation/baffling chambers, drain holes, pressure port locations and pneumatic tubing. The -20 version of the GAP 26 includes a heater control box, that is mounted separately from the probe
.
5.1.1 Moisture Protections
Both pitot and AOA pressure chambers have internal baffling and dedicated drain holes to provide moisture protection.
5.1.2 Ice Protection
The heated version of the GAP 26 (010-01074-10) has dual internal electro-thermal heating elements to provide ice protection to the areas of the probe where surface impingement of icing elements is expected to occur. In addition to the same level of ice protection (as the -10 probe), the heated/regulated version of the
GAP 26 (010-01074-20) limits the maximum tip temperature to make the probe safer if powered on the ground and to provide a discrete output that indicates when the heater is powered and providing sufficient heat.
NOTE
The pneumatic tubing for pitot pressure is the longer of the two tubes extending out of the
190-01115-01
Rev. AN
Figure 5-1 GAP 26 Unit View (-10 version shown)
G3X/G3X Touch Installation Manual - GAP 26 Installation
Page 5-1
5.2 Equipment Available
Model
Table 5-1 GAP 26 Part Numbers
Assembly Part
Number
010-01074-00
Unit Only Part
Number
011-02964-00 GAP 26 Probe Only
GAP 26 Probe Only,
Heated
GAP 26 Probe Only,
Heated, Regulated
010-01074-10
010-01074-20
011-02964-10
011-02964-20
Heater Control Box
Part Number
N/A
N/A
011-02965-00
5.3 Required Equipment
• GAP 26 Pitot/AOA Probe (010-01074-00, 010-01074-10, or 010-01074-20)
• Electrical and pneumatic connectors per installer preference. For heated probe installations where the installer desires to shorten the provided aluminum tubing, a minimum of 8 inches of aluminum tubing should remain between the probe and any transition to non-metallic tubing to protect the non-metallic tubing from excessive heat.
• Mount: Standard AN5812 pitot tube mount.
• #6-32 screws (4 pcs), required length (.218” min - .312” max), recommend screws with nylon patch on threads for thread locking for mounting probe.
• #4 or #6 (4 pcs) pan or hex head screws for mounting heater control box.
5.4 General Specifications
See
for power/current specifications, and Section 2.4.1
for dimension/weight specifications.
5.5 Unit Installation
Fabrication of a wiring harness is required. Sound mechanical and electrical methods and practices are recommended for installation of the GAP 26. Refer to
for wiring considerations (-10 and -20
units only).
5.5.1 Mounting Location
• The GAP 26 is an under-wing mounted pitot/AOA probe, it is not intended for fuselage mount applications. For proper functionality, the GAP 26 should be mounted in a location where airflow over the probe is relatively undisturbed (typically mid-wing span).
• The tip of the GAP 26 should be located at least 4” from, but not more than 10” below the bottom surface of the wing. The probe tip may protrude up to 2” max in front of the leading edge of the wing.
• Viewed from the side, the GAP 26 probe bayonet centerline should be mounted within ±5° from parallel to the wing chord line.
• Viewed from the top, the GAP 26 bayonet centerline should be mounted within ±5° from parallel with the aircraft centerline.
• Consider using the aircraft designer/manufacturer’s recommended mounting location (if specified). Optimal AOA functionality results when the tip of the GAP 26 probe is located no
further back than 25% of the wing chord length from the leading edge. (See Figure 5-2
)
• The 3/16” diameter aluminum pneumatic tubing is intended to be hand bendable to suit various mounting configurations. Minimum allowable bend radius is 1.5”. It is recommended to bend any given section only once to prevent work hardening and cracking of the aluminum tubing.
• Garmin recommends that the GAP 26 not be used on aircraft where the ship static pressure port is located under the wing (due to the likelihood that the AOA measurement will be significantly
190-01115-01
Rev. AN
G3X/G3X Touch Installation Manual - GAP 26 Installation
Page 5-2
impacted). If the static port is located under the wing, it is recommended that the port be moved to an alternate location as part of the GAP 26 installation. If port relocation is required, obtain guidance from the aircraft designer regarding acceptable alternate static port locations.
• Route all GAP 26 power and ground wires away from any audio wires.
• To avoid magnetic interference, do not use the airframe to ground the GAP 26 or any other highcurrent device. See
for further magnetometer installation considerations.
CHORD LENGTH
25%
OF CHORD LENGTH
CHORD LINE
2" MAX ALLOWABLE TIP LOCATION
AHEAD OF WING LEADING EDGE
5° MAX
ANGLE BETWEEN CHORD
LINE AND PROBE CENTERLINE
WING LEADING EDGE
4" MIN CENTERLINE
DISTANCE
10" MAX CENTERLINE
DISTANCE
PROBE CENTERLINE
GARMIN RECOMMENDED
FARTHEST AFT PROBE TIP LOCATION
GARMIN RECOMMENDED
FARTHEST FORWARD PROBE TIP LOCATION
Figure 5-2 GAP 26, Mounting Location Guidance
5.5.2 Heater Wiring Configuration
The GAP 26 uses two internal heaters that may be powered by 14 or 28 volt systems. Each of the heaters
heaters can be connected to a power source as shown in Figure 5-4 and Figure 5-5
.
190-01115-01
Rev. AN
“Banded” Wire
Figure 5-3 GAP 26 Banded Wire
G3X/G3X Touch Installation Manual - GAP 26 Installation
Page 5-3
CAUTION
Do not use the heated/regulated version of the GAP 26 (010-01074-20) in 28V installations. The heated/non-regulated version of the GAP 26 (010-01074-10)
may be used in either 14V or 28V installations when connected as per Figure 5-4
or
.
CAUTION
Do not connect the heaters in parallel to 28V. See
aircraft. The heaters will be damaged if connected incorrectly to 28V.
Figure 5-4 GAP 26, 14V Installation Configuration (010-01074-10 only)
Figure 5-5 GAP 26, 28V Installation Configuration (010-01074-10 only)
190-01115-01
Rev. AN
G3X/G3X Touch Installation Manual - GAP 26 Installation
Page 5-4
5.5.3 Control Box Installation (-20 version only)
Mount the control box (
) to a suitable mounting location within two feet of the GAP 26 using (4)
#4 or #6 pan or hex head screws (choose screw length that is appropriate to mounting location).
Connect the white connector from the probe to the white connector from the control box (this allows the control box to sense probe temperature). Connect the red connectors from the probe to the red connectors from the control box, (
Figure 5-7 ) this provides power and ground to the heaters. The red wires with red
connectors from the control box connect to the plain wires with red connectors from the heater and the black wires with red connectors from the control box connect to the banded wires with red connectors from
discrete input (
).
Figure 5-6 011-02964-20 Probe Wiring
-
+
190-01115-01
Rev. AN
Figure 5-7 011-02964-20 Probe to Control Box Connectors
G3X/G3X Touch Installation Manual - GAP 26 Installation
Page 5-5
5.5.4 Discrete Output Specification (-20 version only)
The discrete output (bare blue wire) from the control box (011-02965-00) can be connected to any available discrete input. The discrete output is floating (open-circuit) when the probe is powered off, or when powered on and below 25° C. When the probe is above 25° C and powered on, the discrete output will be shorted to ground. See
GAP 26 Alert Configuration (-20 version only)
(for GDU 37X versions) or
configuration.
5.5.5 System Leak Considerations
The AOA pitot system leak test is not a regulatory requirement. If the system experiences inconsistent performance or an inability to calibrate the AOA System, leak testing may be performed to provide assurance that any leakage is within an acceptable range.
If a pitot/static tester is used to perform this test, the recommended airspeed input applied to the probe pressure ports is 150 knots. The leak rate should be less than 5 knots/min with the probe removed from the aircraft. If the leak rate is less than 5 knots/min with the probe removed, attach the probe and perform the test with the GAP 26 in line (ensuring drain holes are fully sealed).
The guidance for pitot system tests listed in AC 43.13-1B, Section 4 are not directly applicable to this
AOA pitot system. However, using it as a reference, it specifies that the system shall be tested per the manufacturer’s instructions but further states that if the manufacturer does not provide instructions, the default test is to apply 150 knots pressure to the system and measure the pressure loss over one minute.
This loss is not to exceed 10 knots/min. While some GAP 26 probes will pass a test of this type, some may not. Garmin has determined that a leak rate of 250 knots/min or less is allowable and still ensures proper functionality.
NOTE
Both pressure chambers on the GAP 26 probe have drain holes that when open during normal operation would constitute a “designed-in” leak that is several times higher than
250 knots/min but does not add significant error.
CAUTION
When the GSU 25 is used in conjunction with the GAP 26 pitot/AOA probe to perform Part 43 Appendix E altimeter tests, the probe adapter from the pitot-static tester must completely cover the pitot and AOA ports and drain holes on the GAP
26 to avoid over-pressuring (and causing damage to) the internal AOA sensor of the GSU 25. If the GAP 26 is installed but AOA is unused (i.e., the AOA port of the
GAP 26 is not connected to the AOA port of the GSU 25) then the GAP 26 AOA port must be connected to the same pressure port as the pitot port during pitotstatic testing.
*Note: If the AOA is unused and connected to the static port (as described in the preceding Caution statement) it can remain connected to the static port for the pitot-static test.
After the leak test is completed, ensure that all pressure ports and drain holes on the GAP 26 are open and clear of debris.
190-01115-01
Rev. AN
G3X/G3X Touch Installation Manual - GAP 26 Installation
Page 5-6
5.6 Outline and Installation Drawings
190-01115-01
Rev. AN
Figure 5-8 GAP 26 Outline Drawing
G3X/G3X Touch Installation Manual - GAP 26 Installation
Page 5-7
.250
0
.389
1.639
1.500
1.776
2X 1.250
190-01115-01
Rev. AN
Figure 5-9 GAP 26 Heater Control Box (used with -20 unit only)
G3X/G3X Touch Installation Manual - GAP 26 Installation
Page 5-8
6 GDU 37X (DISPLAY UNIT) INSTALLATION
This section contains general information as well as installation information for the GDU 37X. Use this section to mount the GDU 37X unit(s).
Figure 6-1 GDU 37X Unit View
6.1 Equipment Description
NOTE
There is no TSO/ETSO applicable to the GDU 37X.
NOTE
GPS data is used for ADAHRS sensor drift correction, so at least one source of GPS data is required. This requirement can be met by installing a GPS 20A, or by connecting a GPS antenna to at least one GDU GPS receiver. In a system with multiple GDU displays, additional GPS antennas may be connected to the other displays for redundancy, if desired.
The GDU 37X provides a central display and user interface for the G3X system. The display is mounted flush to the aircraft instrument panel using four #6 captured screws with a 3/32” hex head. The GDU 37X is available in two models, GDU 370 and GDU 375. The GDU 370 is a Garmin Display Unit with a VFR
WAAS-GPS receiver. The GDU 375 provides these same features plus an SiriusXM ® receiver.
190-01115-01
Rev. AN
G3X/G3X Touch Installation Manual - GDU 37X Installation
Page 6-1
6.1.1 Navigation Functions
• Display of position and ground speed
• Display of stored navigation and map databases
• Area navigation functions using the determined position/velocity and stored navigation data
• Advisory approach navigation functions and associated databases
• Display of flight plan and navigation from an external GPS navigator
• Display of navigation data from an external VOR/ILS NAV radio
6.1.2 Interface Summary
NOTE
A G3X system installation can use either GDU 37X or GDU 4XX displays, but a G3X system installation cannot use GDU 37X and GDU 4XX displays.
The GDU 37X uses CAN and RS-232 interfaces to communicate with Garmin LRUs and other devices.
Refer to
, and
for interconnect and configuration information.
6.2 General Specifications
See
for power/current specifications, and Section 2.4.1
for dimension/weight specifications.
6.3 Installation Information
6.3.1 Required Equipment
Each of the following accessories is provided with the GDU 37X unit (010-00667-15). The connector kit is required to install the unit (
Figure 6-2 ). The GDU 37X Nut Plate ( Figure 6-2
) is included in the installation kit for use when it is not possible to tap the instrument panel for 6-32 screw threads.
installed.
Table 6-1 Contents of GDU 37X Connector Kit (011-01921-00)*
Item
Sub-Assy, bkshl w/Hdw, Jackscrew
Conn, Rcpt, D-Sub, Crimp Socket
Contact, Sckt, D-Sub, Crimp, Size 20
Garmin P/N
011-01855-04
330-00625-50
336-00094-00
Quantity
1
1
20
190-01115-01
Rev. AN
G3X/G3X Touch Installation Manual - GDU 37X Installation
Page 6-2
6.3.1.1 GDU 37X PFD Configuration Module
The GDU 37X PFD 1 display uses a configuration module designated as the master system configuration module. The master system configuration module stores configuration data identical to the PFD configuration data stored in the PFD memory. The PFD cross-checks the configuration module data against internal PFD memory and self-configures to match the master system configuration module. The
PFD also maintains control of other LRUs’ configuration and calibration settings except for GSU 73
AHRS calibration settings which are stored in the GSU 73 configuration module. This allows critical data to be retained with the airframe even if the PFD 1 display is replaced.
6.3.2 Additional Equipment Required
A 3/32” hex drive tool is required to secure the GDU 37X to the panel as described in
Installation.
190-01115-01
Rev. AN
Figure 6-2 GDU 37X Mounting Accessories
G3X/G3X Touch Installation Manual - GDU 37X Installation
Page 6-3
6.4 Unit Installation
Fabrication of a wiring harness is required. Sound mechanical and electrical methods and practices are
recommended for installation of the GDU 37X. Refer to Section 2.3
for wiring considerations, and to
for pinouts.
Connector kits include backshell assemblies. Garmin’s backshell connectors give the installer the ability to quickly and easily terminate shield grounds at the backshell housing. The instructions needed to assemble the backshell connector w/Shield Block grounding system are located in
NOTE
The GDU 37X rear connector (J3701) is electrically isolated. For installations using
shielded cables, a ground pin must be tied to the connector shell (Figure 6-3).
Figure 6-3 Grounded Connector Shell
6.5 Antennas
Refer to
Section 23 for antenna information.
NOTE
GDU 37X units cannot be used with GA 35, GA 36, or GA 37 antennas.
6.6 Mounting Requirements
Refer to
for outline and installation drawings.
6.6.1 Unit Installation
The GDU 37X is installed by holding the unit flush with the instrument panel and fastening the four captured 3/32” hex socket head screws to the panel as shown in
6.6.2 Panel Cutout Template
can be used as a template when marking the panel for cutout. Dimensions on the figure are to verify accuracy of printout only, see
for complete cutout dimensions. A .dxf version of the drawing is also available for download at https://support.garmin.com/support/manuals .
190-01115-01
Rev. AN
G3X/G3X Touch Installation Manual - GDU 37X Installation
Page 6-4
GDU 37X PANEL CUTOUT TEMPLATE
IMPORTANT!
Ensure the Page Scaling setting is set to NONE when printing this page. Verify dimensions of printed template are accurate before cutting panel.
Cut out panel to inside line
7.33 in
[186.2 mm]
190-01115-01
Rev. AN
5.57 in
[141.4 mm]
For corner holes, center punch and drill
(#36) / tap (6/32) to create threaded holes
OR drill out with 25 drill bit and use Garmin nut-plate P/N 115-01054-00
Figure 6-4 GDU 37X Panel Cutout Template
G3X/G3X Touch Installation Manual - GDU 37X Installation
Page 6-5
6.7
Outline and Installation Drawings
190-01115-01
Rev. AN
Figure 6-5 GDU 37X Outline Drawing
G3X/G3X Touch Installation Manual - GDU 37X Installation
Page 6-6
DIMENSIONS SHOWN FOR REFERENCE ONL
190-01115-01
Rev. AN
Figure 6-6 GDU 37X Assembly/Panel Cutout Drawing
G3X/G3X Touch Installation Manual - GDU 37X Installation
Page 6-7
7 GDU 45X (DISPLAY UNIT) INSTALLATION
This section contains general information as well as installation information for the GDU 45X. Use this section to mount the GDU 45X unit(s). If upgrading from a GDU 37X to a GDU 45X display, refer to
upgrade instructions in Section 37.2.1.5
for information pertaining to preserving/transferring stored system
calibration information.
7.1 Equipment Description
Figure 7-1 GDU 45X Unit View
NOTE
There is no TSO/ETSO applicable to the GDU 45X.
NOTE
GPS data is used for ADAHRS sensor drift correction, so at least one source of GPS data is required. This requirement can be met by installing a GPS 20A, or by connecting a GPS antenna to at least one GDU GPS receiver. In a system with multiple GDU displays, additional GPS antennas may be connected to the other displays for redundancy, if desired.
NOTE
Make sure that no dust or grit accumulates at the bottom of the display glass. The
GDU 45X display uses invisible infrared beams for touch detection, this makes it very important to keep the screen clean, especially along the edges.
NOTE
See
for information on replacing a GDU 37X display with a GDU 4XX display.
The GDU 45X is not suitable for installation in a type-certificated aircraft.
The GDU 45X is mounted flush to the aircraft instrument panel using four #6 screws. The GDU 45X is
190-01115-01
Rev. AN
G3X/G3X Touch Installation Manual - GDU 45X Installation
Page 7-1
available in two models, GDU 450 and GDU 455. The GDU 450 is a Garmin Display Unit with a GPS receiver and video input. The GDU 455 provides these same features plus a SiriusXM ® receiver.
7.1.1 Navigation Functions
• Display of position and ground speed
• Display of stored navigation and map databases
• Area navigation functions using the determined position/velocity and stored navigation data
• Advisory approach navigation functions and associated databases
• Display of flight plan and navigation from an external GPS navigator
• Display of navigation data from an external VOR/ILS NAV radio
7.1.2 Interface Summary
NOTE
A G3X system installation can use either GDU 37X or GDU 4XX displays, but a G3X system installation cannot use GDU 37X and GDU 4XX displays.
NOTE
Please refer to the G3X Touch Pilot’s Guide (190-01754-00) for guidance in using
Connext Bluetooth connections to Garmin Pilot device(s).
The GDU 45X uses CAN and RS-232 interfaces to communicate with Garmin LRUs and other devices.
Refer to sections
,
, and
Section 35 for interconnect and
configuration information.
The GDU 45X supports video input via a wired connection (see
The GDU 45X includes a wireless Bluetooth transceiver than can communicate with tablet computers and other Garmin devices that support the Connext interface protocol. Refer to the G3X Touch Pilot’s Guide
(190-01754-00) for guidance in using Connext Bluetooth connections.
7.2 General Specifications
See
for power/current specifications, and Section 2.4.1
for dimension/weight specifications.
7.3 Installation Information
7.3.1 Required Equipment
installed. The GDU 45X Nut Plate (
Figure 7-4 ) is included in the installation kit for use when it is not
possible to tap the instrument panel for 6-32 screw threads. The installation kits are not included with the
GDU 45X.
Table 7-1 Contents of GDU 45X Installation Kit (010-12150-01)*
Item
GDU 45X Connector Kit*
Nut Plate Kit
Machine Screw for Panel Mounting, 0.550”, Black
*Contents of the connector kit are listed in
Garmin P/N
011-01921-10
115-01725-00
211-00169-01
Quantity
1
1
4
190-01115-01
Rev. AN
G3X/G3X Touch Installation Manual - GDU 45X Installation
Page 7-2
Table 7-2 Contents of GDU 45X Connector Kit (011-01921-10)
Item
Sub-Assy, bkshl w/Hdw, Jackscrew
Conn, Rcpt, D-Sub, Crimp Socket
Contact, Sckt, D-Sub, Crimp, Size 20
Garmin P/N
011-01855-04
330-00625-50
336-00022-02
Quantity
1
1
30
7.3.1.1 GDU 45X PFD Configuration Module
The GDU 45X PFD 1 display uses a configuration module designated as the master system configuration module. The master system configuration module stores configuration data identical to the PFD configuration data stored in the PFD memory. The PFD cross-checks the configuration module data against internal PFD memory and self-configures to match the master system configuration module. The
PFD also maintains control of other LRUs’ configuration and calibration settings except for GSU 73
AHRS calibration settings which are stored in the GSU 73 configuration module (the GSU 25 does not have a configuration module). This allows critical data to be retained with the airframe even if the PFD 1 display is replaced.
7.3.2 Additional Equipment Required
A 3/32” hex drive tool is required to secure the GDU 45X to the panel as described in
Installation and shown in Figure 7-3
.
7.4 Unit Installation
Fabrication of a wiring harness is required. Sound mechanical and electrical methods and practices are
recommended for installation of the GDU 45X. Refer to Section 2.3
for wiring considerations, and to
for pinouts.
Connector kits include backshell assemblies. Garmin’s backshell connectors give the installer the ability to quickly and easily terminate shield grounds at the backshell housing. The instructions needed to assemble the backshell connector w/Shield Block grounding system are located in
Replacement cursor knobs (part number K00-00578-00) for the GDU 45X are available from a Garmin dealer.
190-01115-01
Rev. AN
G3X/G3X Touch Installation Manual - GDU 45X Installation
Page 7-3
7.5 Antennas
Refer to
Section 23 for antenna information.
NOTE
GDU 45X units cannot be used with GA 35, GA 36, or GA 37 antennas.
7.6 Mounting Requirements
Refer to
for outline and installation drawings.
7.6.1 Unit Installation
The GDU 45X is installed by holding the unit flush with the instrument panel and fastening the four 3/32”
hex socket head screws to the panel as shown in Figure 7-3
.
7.6.2 Panel Cutout Template
The GDU 45X Nut Plate (115-01725-00) can be used as a template when marking the panel for cutout
) (dimensions on the figure are to verify accuracy of printout only). See
cutout dimensions. A .dxf version of the drawing is also available for download at https://support.garmin.com/support/manuals .
190-01115-01
Rev. AN
G3X/G3X Touch Installation Manual - GDU 45X Installation
Page 7-4
7.7
Outline and Installation Drawings
190-01115-01
Rev. AN
Figure 7-2 GDU 45X Outline Drawing
G3X/G3X Touch Installation Manual - GDU 45X Installation
Page 7-5
190-01115-01
Rev. AN
Figure 7-3 GDU 45X Assembly Drawing
G3X/G3X Touch Installation Manual - GDU 45X Installation
Page 7-6
C L
C L
0.0
0
95.7
2X3.77
94.8
3.73
190-01115-01
Rev. AN
Figure 7-4 GDU 45X Panel Cutout Drawing (not to scale)
G3X/G3X Touch Installation Manual - GDU 45X Installation
Page 7-7
95.7
2X3.77
94.8
3.73
GDU 45X Panel Cutout Drawing
IMPORTANT!
Ensure the Page Scaling setting is set to NONE when printing this page. Verify dimensions of printed template are accurate before cutting panel.
For corner holes, center punch and drill
(#36) / tap (6/32) to create threaded holes
OR drill out with #25 drill bit and use Garmin nut-plate P/N 115-01725-00.
The outline in this drawing is identical to the outline of the actual bezel.
Cut out panel to inside line
190-01115-01
Revision AN
Figure 7-6 GDU 45X Panel Cutout Drawing
G3X/G3X Touch Installation Manual - GDU 45X Installation
Page 7-8
8 GDU 46X (DISPLAY UNIT) INSTALLATION
This section contains general information as well as installation information for the GDU 46X. Use this section to mount the GDU 46X unit(s). If upgrading from a GDU 37X to a GDU 46X display, refer to
upgrade instructions in Section 37.2.1.5
for information pertaining to preserving/transferring stored system
calibration information.
8.1 Equipment Description
Figure 8-1 GDU 46X Unit View
NOTE
There is no TSO/ETSO applicable to the GDU 46X.
NOTE
GPS data is used for ADAHRS sensor drift correction, so at least one source of GPS data is required. This requirement can be met by installing a GPS 20A, or by connecting a GPS antenna to at least one GDU GPS receiver. In a system with multiple GDU displays, additional GPS antennas may be connected to the other displays for redundancy, if desired.
NOTE
Make sure that no dust or grit accumulates at the bottom of the display glass. The GDU
46X display uses invisible infrared beams for touch detection, this makes it very important to keep the screen clean, especially along the edges.
NOTE
See
for information on replacing a GDU 37X display with a GDU 4XX display.
The GDU 46X is not suitable for installation in a type-certificated aircraft.
190-01115-01
Rev. AN
G3X/G3X Touch Installation Manual - GDU 46X Installation
Page 8-1
The GDU 46X is mounted flush to the aircraft instrument panel using four #6 screws. The GDU 46X is available in two models, GDU 460 and GDU 465. The GDU 460 is a Garmin Display Unit with a GPS receiver and video input. The GDU 465 provides these same features plus a SiriusXM ® receiver.
8.1.1 Navigation Functions
• Display of position and ground speed
• Display of stored navigation and map databases
• Area navigation functions using the determined position/velocity and stored navigation data
• Advisory approach navigation functions and associated databases
• Display of flight plan and navigation from an external GPS navigator
• Display of navigation data from an external VOR/ILS NAV radio
8.1.2 Interface Summary
NOTE
A G3X system installation can use either GDU 37X or GDU 4XX displays, but a G3X system installation cannot use GDU 37X and GDU 4XX displays.
NOTE
Please refer to the G3X Touch Pilot’s Guide (190-01754-00) for guidance in using
Connext Bluetooth connections to Garmin Pilot device(s).
The GDU 46X uses CAN and RS-232 interfaces to communicate with Garmin LRUs and other devices.
Refer to sections
,
, and
Section 35 for interconnect and
configuration information.
The GDU 46X supports video input via a wired connection (see
The GDU 46X includes a wireless Bluetooth transceiver than can communicate with tablet computers and other Garmin devices that support the Connext interface protocol. Refer to the G3X Touch Pilot’s Guide
(190-01754-00) for guidance in using Connext Bluetooth connections.
8.2 General Specifications
See
for power/current specifications, and Section 2.4.1
for dimension/weight specifications.
8.3 Installation Information
8.3.1 Required Equipment
installed. The GDU 46X Nut Plate (
) is included in the installation kit for use when it is not possible to tap the instrument panel for 6-32 screw threads. The installation kits are not included with the
GDU 46X.
Table 8-1 Contents of GDU 46X Installation Kit (010-12150-00)
Item
GDU 46X Connector Kit*
Nut Plate Kit
Machine Screw for Panel Mounting, 0.550”, Black
*Contents of the connector kit are listed in
Garmin P/N
011-01921-10
115-01725-01
211-00169-01
Quantity
1
1
4
190-01115-01
Rev. AN
G3X/G3X Touch Installation Manual - GDU 46X Installation
Page 8-2
Table 8-2 Contents of GDU 46X Connector Kit (011-01921-10)*
Item
Sub-Assy, bkshl w/Hdw, Jackscrew
Conn, Rcpt, D-Sub, Crimp Socket
Contact, Sckt, D-Sub, Crimp, Size 20
Garmin P/N
011-01855-04
330-00625-50
336-00022-02
Quantity
1
1
30
8.3.1.1 GDU 46X PFD Configuration Module
The GDU 46X PFD 1 display uses a configuration module designated as the master system configuration module. The master system configuration module stores configuration data identical to the PFD configuration data stored in the PFD memory. The PFD cross-checks the configuration module data against internal PFD memory and self-configures to match the master system configuration module. The
PFD also maintains control of other LRUs’ configuration and calibration settings except for GSU 73
AHRS calibration settings which are stored in the GSU 73 configuration module (the GSU 25 does not have a configuration module). This allows critical data to be retained with the airframe even if the PFD 1 display is replaced.
8.3.2 Additional Equipment Required
A 3/32” hex drive tool is required to secure the GDU 46X to the panel as described in
Installation and shown in Figure 8-3
.
8.4 Unit Installation
Fabrication of a wiring harness is required. Sound mechanical and electrical methods and practices are
recommended for installation of the GDU 46X. Refer to Section 2.3
for wiring considerations, and to
for pinouts.
Connector kits include backshell assemblies. Garmin’s backshell connectors give the installer the ability to quickly and easily terminate shield grounds at the backshell housing. The instructions needed to assemble the backshell connector w/Shield Block grounding system are located in
Replacement cursor knobs (part number K00-00578-00) for the GDU 46X are available from a Garmin dealer.
8.5 Antennas
Refer to
Section 23 for antenna information.
NOTE
GDU 46X units cannot be used with GA 35, GA 36, or GA 37 antennas.
8.6 Mounting Requirements
Refer to
for outline and installation drawings.
8.6.1 Unit Installation
The GDU 46X is installed by holding the unit flush with the instrument panel and fastening the four 3/32”
hex socket head screws to the panel as shown in Figure 8-3
.
8.6.2 Panel Cutout Template
The GDU 46X Nut Plate (115-01725-01) can be used as a template when marking the panel for cutout
) (dimensions on the figure are to verify accuracy of printout only). See Figure 8-4 for complete
cutout dimensions. A.dxf version of the drawing is also available for download at https://support.garmin.com/support/manuals .
190-01115-01
Rev. AN
G3X/G3X Touch Installation Manual - GDU 46X Installation
Page 8-3
8.7
Outline and Installation Drawings
7.237.23 183.57183.57
.30.30 7.527.52
3.573.57 90.7590.75
10.2510.25 260.47260.47
.30.30 7.517.51
.41.41 10.3010.30
7.827.82 198.60198.60
4.054.05 102.86102.86
3.563.56 90.4690
2.772.77 70.4670
.87.87 22.1022.10
2.132.13 54.1054.10
1.571.57 39.9039.90
.58.58 14.6914.69
4.324.32 109.63109.63
6.966.96 176.73176.73
1.531.53 38.7438.74
190-01115-01
Rev. AN
2.592.59 65.9065.90
Figure 8-2 GDU 46X Outline Drawing
G3X/G3X Touch Installation Manual - GDU 46X Installation
Page 8-4
190-01115-01
Rev. AN
Figure 8-3 GDU 46X Assembly Drawing
G3X/G3X Touch Installation Manual - GDU 46X Installation
Page 8-5
131.00
5.16
131.00
131.90 (2X)
5.19
.00
5.16
5.16
131.00
131.90 (2X)
5.19
190-01115-01
Rev. AN
Figure 8-4 GDU 46X Panel Cutout Drawing (not to scale)
G3X/G3X Touch Installation Manual - GDU 46X Installation
Page 8-6
GDU 46X Panel Cutout Drawing
IMPORTANT
!
Ensure the Page Scaling setting is set to NONE when printing this page. Verify dimensions of printed template are accurate before cutting panel.
For corner holes, center punch and drill
(#36) / tap (6/32) to create threaded holes
OR drill out with #25 drill bit and use Garmin nut-plate P/N 115-01725-01.
The outline in this drawing is identical to the outline of the actual bezel.
7.35 mm (4X)
Cut out panel to inside line
R7.35 mm (4X)
7.35 mm (4X)
190-01115-01
Revision AN
Figure 8-6 GDU 46X Panel Cutout Drawing
G3X Installation Manual - GDU 46X Installation
Page 8-8
9 GDU 470 (DISPLAY UNIT) INSTALLATION
This section contains general information as well as installation information for the GDU 470. Use this section to mount the GDU 470 unit(s). If upgrading from a GDU 37X to a GDU 470 display, refer to
upgrade instructions in Section 37.2.1.5
for information pertaining to preserving/transferring stored system
calibration information.
9.1 Equipment Description
Figure 9-1 GDU 470 Unit View
NOTE
There is no TSO/ETSO applicable to the GDU 470.
NOTE
GPS data is used for ADAHRS sensor drift correction, so at least one source of GPS data is required. This requirement can be met by installing a GPS 20A, or by connecting a GPS antenna to at least one GDU GPS receiver. In a system with multiple GDU displays, additional GPS antennas may be connected to the other displays for redundancy, if desired.
190-01115-01
Rev. AN
G3X/G3X Touch Installation Manual - GDU 470 Installation
Page 9-1
NOTE
Make sure that no dust or grit accumulates at the bottom of the display glass The
GDU 470 display uses invisible infrared beams for touch detection, this makes it very important to keep the screen clean, especially along the edges.
NOTE
See
for information on replacing a GDU 37X display with a GDU 4XX display.
The GDU 470 is not suitable for installation in a type-certificated aircraft.
The GDU 470 is mounted flush to the aircraft instrument panel using four #6 screws. The GDU 470 is a
Garmin Display Unit with a GPS receiver and video input.
9.1.1 Navigation Functions
• Display of position and ground speed
• Display of stored navigation and map databases
• Area navigation functions using the determined position/velocity and stored navigation data
• Advisory approach navigation functions and associated databases
• Display of flight plan and navigation from an external GPS navigator
• Display of navigation data from an external VOR/ILS NAV radio
9.1.2 Interface Summary
NOTE
A G3X system installation can use either GDU 37X or GDU 4XX displays, but a G3X system installation cannot use GDU 37X and GDU 4XX displays.
NOTE
Please refer to the G3X Touch Pilot’s Guide (190-01754-00) for guidance in using
Connext Bluetooth connections to Garmin Pilot device(s).
The GDU 470 uses CAN and RS-232 interfaces to communicate with Garmin LRUs and other devices.
Refer to sections
,
, and
Section 35 for interconnect and
configuration information.
The GDU 470 supports video input via a wired connection (see
).
The GDU 470 includes a wireless Bluetooth transceiver than can communicate with tablet computers and other Garmin devices that support the Connext interface protocol. Refer to the G3X Touch Pilot’s Guide
(190-01754-00) for guidance in using Connext Bluetooth connections.
9.2 General Specifications
See
for power/current specifications, and Section 2.4.1
for dimension/weight specifications.
190-01115-01
Rev. AN
G3X/G3X Touch Installation Manual - GDU 470 Installation
Page 9-2
9.3 Installation Information
9.3.1 Required Equipment
installed. The installation kits are not included with the GDU 470.
The GDU 470 Nut Plate (
Figure 9-4 ) is included in the installation kit for use when it is not possible to tap
the instrument panel for 6-32 screw threads. A separate drilling guide is included to aid the installation of a
GDU 470 in a panel that formerly contained a GDU 37X display.
Table 9-1 Contents of GDU 470 Installation Kit (010-12150-02)*
Item
GDU 4XX Connector Kit*
Nut Plate Kit
GDU 47X Drill Guide
Machine Screw for Panel Mounting, 0.550”, Black
*Contents of the connector kit are listed in Table 9-2
Garmin P/N
011-01921-10
115-01725-03
115-01725-04
211-00169-01
Quantity
1
1
1
4
Table 9-2 Contents of GDU 4XX Connector Kit (011-01921-10)
Item
Sub-Assy, bkshl w/Hdw, Jackscrew
Conn, Rcpt, D-Sub, Crimp Socket
Contact, Sckt, D-Sub, Crimp, Size 20
Garmin P/N
011-01855-04
330-00625-50
336-00022-02
Quantity
1
1
30
9.3.1.1 GDU 470 PFD Configuration Module
The GDU 470 PFD 1 display uses a configuration module designated as the master system configuration module. The master system configuration module stores configuration data identical to the PFD configuration data stored in the PFD memory. The PFD cross-checks the configuration module data against internal PFD memory and self-configures to match the master system configuration module. The
PFD also maintains control of other LRUs’ configuration and calibration settings except for GSU 73
AHRS calibration settings which are stored in the GSU 73 configuration module (the GSU 25 does not have a configuration module). This allows critical data to be retained with the airframe even if the PFD 1 display is replaced.
9.3.2 Additional Equipment Required
A 3/32” hex drive tool is required to secure the GDU 470 to the panel as described in
Unit
Installation and shown in Figure 9-3
.
190-01115-01
Rev. AN
G3X/G3X Touch Installation Manual - GDU 470 Installation
Page 9-3
9.4 Unit Installation
Fabrication of a wiring harness is required. Sound mechanical and electrical methods and practices are recommended for installation of the GDU 470. Refer to
for wiring considerations, and to
for pinouts.
Connector kits include backshell assemblies. Garmin’s backshell connectors give the installer the ability to quickly and easily terminate shield grounds at the backshell housing. The instructions needed to assemble the backshell connector w/Shield Block grounding system are located in
Replacement cursor knobs (part number K00-00578-00) for the GDU 470 are available from a Garmin dealer.
9.5 Antennas
Refer to
Section 23 for antenna information.
NOTE
GDU 470 units cannot be used with GA 35, GA 36, or GA 37 antennas.
9.6 Mounting Requirements
Refer to
Figure 9-3 for outline and installation drawings.
9.6.1 Unit Installation
The GDU 470 is installed by holding the unit flush with the instrument panel and fastening the four 3/32”
hex socket head screws to the panel as shown in Figure 9-3
.
9.6.2 Panel Cutout Template
The GDU 470 Nut Plate (115-01725-03) can be used as a template when marking the panel for cutout
) (dimensions on the figure are to verify accuracy of printout only). See
cutout dimensions. A .dxf version of the drawing is also available for download at https://support.garmin.com/support/manuals .
9.6.3 Panel Drilling Guide
The GDU 470 Drill Guide (115-01725-04) can be used as a template when marking the panel for cutout
( Figure 9-6,
dimensions on the figure are to verify accuracy of printout only). See Figure 9-4
for complete dimensions. The drill guide is especially useful when updating from the GDU 37X to the GDU 470, as the rivet holes on the GDU 470 drill guide and nut plate match the GDU 37X nut plate rivet holes. The drill guide is attached to the panel using the existing GDU 37X nutplate holes, and is used to make the panel modifications and drill the new mounting holes. The corners of the existing GDU 37X panel cutout must be slightly enlarged using the drilling guide as a template. The nut plate is then used to mount the GDU
470 to the updated panel opening.
190-01115-01
Rev. AN
G3X/G3X Touch Installation Manual - GDU 470 Installation
Page 9-4
9.7
Outline and Installation Drawings
190-01115-01
Rev. AN
Figure 9-2 GDU 470 Outline Drawing
G3X/G3X Touch Installation Manual - GDU 470 Installation
Page 9-5
190-01115-01
Rev. AN
Figure 9-3 GDU 470 Assembly Drawing
G3X/G3X Touch Installation Manual - GDU 470 Installation
Page 9-6
advertisement
Related manuals
advertisement
Table of contents
- 24 Section 1 Inventory of Materials
- 24 1.1 Unpacking Unit
- 24 1.2 Required Garmin Equipment
- 24 1.3 Optional Garmin Equipment
- 24 1.4 Optional Garmin LRUs
- 24 1.5 Required non-Garmin Equipment
- 24 1.6 Optional Garmin Equipment (non-LRU)
- 24 1.7 Optional non-Garmin Equipment
- 24 1.8 Optional 3rd Party Sensors/LRUs
- 24 1.9 Garmin Software and Documents
- 25 Section 2 Installation Preparation
- 25 2.1 System Overview
- 25 2.2 Electrical Considerations
- 25 2.3 Wiring/Cabling Considerations
- 25 2.4 Mechanical Considerations
- 25 2.5 LRU/Sensor Installation Information
- 26 Section 3 GAD 27 (Flaps/Lights/Trim Controller) Installation
- 26 3.1 Equipment Description
- 26 3.2 Equipment Available
- 26 3.3 General Specifications
- 26 3.4 Mounting Requirements
- 26 3.5 Unit Installation
- 26 3.6 Outline and Installation Drawings
- 27 Section 4 GAD 29/29B (ARINC 429 Adapter) Installation
- 27 4.1 Equipment Description
- 27 4.2 Equipment Available
- 27 4.3 General Specifications
- 27 4.4 Mounting Requirements
- 27 4.5 Unit Installation
- 27 4.6 Outline and Installation Drawings
- 28 Section 5 GAP 26 (Pitot/AOA Probe) Installation
- 28 5.1 Equipment Description
- 28 5.2 Equipment Available
- 28 5.3 Required Equipment
- 28 5.4 General Specifications
- 28 5.5 Unit Installation
- 28 5.6 Outline and Installation Drawings
- 103 Section 6 GDU 37X (Display Unit) Installation
- 103 6.1 Equipment Description
- 103 6.2 General Specifications
- 103 6.3 Installation Information
- 103 6.4 Unit Installation
- 103 6.5 Antennas
- 103 6.6 Mounting Requirements
- 103 6.7 Outline and Installation Drawings
- 104 Section 7 GDU 45X (Display Unit) Installation
- 104 7.1 Equipment Description
- 104 7.2 General Specifications
- 104 7.3 Installation Information
- 104 7.4 Unit Installation
- 104 7.5 Antennas
- 104 7.6 Mounting Requirements
- 104 7.7 Outline and Installation Drawings
- 105 Section 8 GDU 46X (Display Unit) Installation
- 105 8.1 Equipment Description
- 105 8.2 General Specifications
- 105 8.3 Installation Information
- 105 8.4 Unit Installation
- 105 8.5 Antennas
- 105 8.6 Mounting Requirements
- 105 8.7 Outline and Installation Drawings
- 106 Section 9 GDU 470 (Display Unit) Installation
- 106 9.1 Equipment Description
- 106 9.2 General Specifications
- 106 9.3 Installation Information
- 106 9.4 Unit Installation
- 106 9.5 Antennas
- 106 9.6 Mounting Requirements
- 106 9.7 Outline and Installation Drawings
- 107 Section 10 GEA 24 (EIS Interface) Installation
- 107 10.1 Equipment Description
- 107 10.2 Equipment Available
- 107 10.3 General Specifications
- 107 10.4 Unit Installation
- 107 10.5 Mounting Requirements
- 107 10.6 Outline and Installation Drawings
- 112 Section 11 GI 260 (AOA Indicator) Installation
- 112 11.1 Equipment Description
- 112 11.2 Equipment Available
- 112 11.3 General Specifications
- 112 11.4 Unit Installation
- 112 11.5 Unit Calibration
- 112 11.6 Unit Operation
- 112 11.7 Outline and Installation Drawings
- 113 Section 12 GMC 305 (AFCS Mode Controller) Installation
- 113 12.1 Equipment Description
- 113 12.2 Equipment Available
- 113 12.3 General Specifications
- 113 12.4 Mounting and Wiring Requirements
- 113 12.5 Outline and Installation Drawings
- 114 Section 13 GMC 307 (AFCS Mode Controller) Installation
- 114 13.1 Equipment Description
- 114 13.2 Equipment Available
- 114 13.3 General Specifications
- 114 13.4 Mounting and Wiring Requirements
- 114 13.5 Outline and Installation Drawings
- 115 Section 14 GMC 507 (AFCS Mode Controller) Installation
- 115 14.1 Equipment Description
- 115 14.2 General Specifications
- 115 14.3 Mounting and Wiring Requirements
- 115 14.4 Outline and Installation Drawings
- 116 Section 15 GMU 11 (Magnetometer) Installation
- 116 15.1 Equipment Description
- 116 15.2 General Specifications
- 116 15.3 Equipment Available
- 116 15.4 Unit Installation
- 116 15.5 Outline and Installation Drawings
- 117 Section 16 GMU 22 (Magnetometer) Installation
- 117 16.1 Equipment Description
- 117 16.2 General Specifications
- 117 16.3 Equipment Available
- 117 16.4 Unit Installation
- 117 16.5 Outline and Installation Drawings
- 157 Section 17 GPS 20A (WAAS GPS Position Source) Installation
- 157 17.1 Equipment Description
- 157 17.2 Statement of Compliance (per AC 90-114A CHG1)
- 157 17.3 Equipment Available
- 157 17.4 General Specifications
- 157 17.5 Mounting Requirements
- 157 17.6 Unit Installation
- 157 17.7 Antennas
- 157 17.8 Antenna Cable Requirements
- 157 17.9 Outline and Installation Drawings
- 158 Section 18 GSA 28 (Autopilot Servo) Installation
- 158 18.1 Equipment Description
- 158 18.2 Equipment Available
- 158 18.3 General Specifications
- 158 18.4 Required Equipment
- 158 18.5 Unit Installation
- 158 18.6 Unit Wiring
- 158 18.7 Outline and Installation Drawings
- 159 Installation
- 159 19.1 Equipment Description
- 159 19.2 General Specifications
- 159 19.3 Required Equipment
- 159 19.4 Unit Installation
- 159 19.5 Outline and Installation Drawings
- 160 Section 20 GSU 73 (Sensor Unit) Installation
- 160 20.1 Equipment Description
- 160 20.2 General Specifications
- 160 20.3 Required Equipment
- 160 20.4 Unit Installation
- 160 20.5 Outline and Installation Drawings
- 161 Section 21 GTP 59 (Temperature Probe) Installation
- 161 21.1 Equipment Description
- 161 21.2 General Specifications
- 161 21.3 Unit Installation
- 161 21.4 GTP 59 Icing
- 161 21.5 Outline and Installation Drawings
- 162 Section 22 GTR 20 (VHF Communications Radio) Installation
- 162 22.1 Equipment Description
- 162 22.2 Equipment Available
- 331 22.3 General Specifications
- 331 22.4 Installation Considerations
- 331 22.5 Antenna Considerations
- 331 22.6 Mounting Considerations
- 331 22.7 Mounting, Wiring, and Power Checks
- 331 22.8 Outline and Installation Drawings
- 332 Section 23 GPS/XM Antenna Installation
- 332 23.1 Non-Garmin Materials Required
- 332 23.2 Non-Garmin Antennas
- 332 23.3 Garmin Antennas
- 332 23.4 Antenna Mounting Considerations
- 332 23.5 Teardrop Footprint Antenna Installation (GA 35, GA 55, and GA 56)
- 332 23.6 ARINC 743 Footprint Antenna Installation (GA 36, GA 37, GA 55A, GA 57X)
- 332 23.7 Non-Structural Mount Installation
- 332 23.8 Outline and Installation Drawings
- 333 Section 24 Engine/Airframe Sensor Installation
- 333 24.1 Engine/Airframe Sensor Options
- 333 24.2 Engine Sensor Applications
- 333 24.3 Engine Sensor Installation
- 334 Section 25 Connector Installation Instructions
- 334 25.1 Cable Connector Installation
- 334 25.2 Jackscrew Backshell Assembly
- 334 25.3 Jackscrew Connector Installation
- 334 25.4 Thermocouple Installation into a Backshell
- 334 25.5 Configuration Module Installation into a Backshell
- 334 25.6 P-Lead Resistor Installation (Braid Shield)
- 335 Section 26 LRU Pinouts
- 335 26.1 GAD 27 (Flaps/Lights/Trim Controller)
- 335 26.2 GAD 29/29B (ARINC 429 Adapter)
- 335 26.3 GDU 37X (Display Unit)
- 335 26.4 GDU 4XX (Display Unit)
- 335 26.5 GEA 24 (EIS Interface)
- 335 26.6 GI 260 (AOA Indicator)
- 335 26.7 GMC 305 (AFCS Mode Controller)
- 335 26.8 GMC 307 (AFCS Mode Controller)
- 335 26.9 GMC 507 (AFCS Mode Controller)
- 335 26.10 GMU 11 (Magnetometer)
- 335 26.11 GMU 22 (Magnetometer)
- 335 26.12 GPS 20A (WAAS GPS Position Source)
- 335 26.13 GSA 28 (Autopilot Servo)
- 335 26.14 GSU 25 (AHRS/Air Data Sensor Unit)
- 335 26.15 GSU 73 (Sensor Unit)
- 514 26.16 GTP 59 (Temperature Probe)
- 514 26.17 GTR 20 (VHF Communications Radio)
- 514 26.18 GTX 23 (Mode S Transponder)
- 515 Section 27 G3X w/GSU 25 and/or GAD 29 Interconnect Drawings
- 515 27.1 Core Interconnect Drawings w/GSU 25 and/or GAD
- 515 27.2 External Interconnect Drawings w/GSU
- 516 Section 28 G3X w/GSU 73 Interconnect Drawings
- 516 28.1 Core Interconnect Drawings
- 516 28.2 External Interconnect Drawings w/GSU
- 517 Section 29 G3X w/GTR 20 Interconnect Drawings
- 517 29.1 Notes for Section 29 Drawings
- 517 29.2 Single GTR 20 Interconnect Drawings
- 517 29.3 Dual GTR 20 Interconnect Drawings
- 518 Section 30 Sensor Wiring Examples
- 518 30.1 Notes for Section 30 Drawings
- 518 30.2 Sensor Wiring Examples w/GEA
- 518 30.3 Sensor Wiring Examples w/GSU
- 519 Section 31 Lycoming/Continental Sensor Wiring Examples
- 519 31.1 Notes for Section 31 Drawings
- 519 31.2 GEA 24 - Lycoming/Continental Sensor Drawings
- 519 31.3 GSU 73 - Lycoming/Continental Sensor Drawings
- 520 Section 32 Rotax Sensor Wiring Examples
- 520 32.1 Notes for Section 32 Drawings
- 520 32.2 GEA 24 - Rotax Sensor Drawings
- 520 32.3 GSU 73 - Rotax Sensor Drawings
- 521 Section 33 Jabiru Sensor Wiring Examples
- 521 33.1 Notes for Section 33 Drawings
- 521 33.2 GEA 24 - Jabiru Sensor Drawings
- 521 33.3 GSU 73 - Jabiru Sensor Drawings
- 522 Section 34 GDU 37X Configuration and Post Installation Checkout
- 522 34.1 Recommended Test Equipment
- 522 34.2 Configuration Mode
- 522 34.3 Software Loading Procedure
- 522 34.4 Configuration Pages
- 522 34.5 Garmin Database Updates
- 522 34.6 SiriusXM® Activation Instructions (GDU 375 only)
- 522 34.7 External Interface Configuration (Garmin units only)
- 885 34.8 GDU Splash Screen
- 885 34.9 Checklist Editor
- 886 Section 35 GDU 4XX Configuration and Post Installation Checkout
- 886 35.1 Recommended Test Equipment
- 886 35.2 Configuration Mode
- 886 35.3 Software Loading Procedure
- 886 35.4 Configuration Pages
- 886 35.5 Garmin Database Updates
- 886 35.6 SiriusXM® Activation Instructions (GDU 455/465 only)
- 886 35.7 External Interface Configuration (Garmin units only)
- 886 35.8 Sharing G3X Touch Flight Plans (Crossfill) with External IFR Navigators
- 886 35.9 Checklist Editor
- 887 Section 36 Troubleshooting
- 887 36.1 General Troubleshooting
- 887 36.2 CAN Network Troubleshooting
- 887 36.3 GDU 37X/4XX
- 887 36.4 Air Data Troubleshooting
- 887 36.5 Engine Indication Troubleshooting
- 887 36.6 ADAHRS Troubleshooting
- 887 36.7 Post Installation Calibration Procedures
- 887 36.8 GSU 73 Data Logging
- 887 36.9 Sending Troubleshooting Data to Garmin
- 888 Section 37 Maintenance
- 888 37.1 Inspections/Continued Airworthiness/Maintenance
- 888 37.2 Return to Service Information