Section 16 GMU 22 (Magnetometer) Installation. Garmin G3X Touch for Experimental Aircraft, GDU 465, GDU 455, G3X, GDU 460, GDU 450
Add to My manuals943 Pages
advertisement
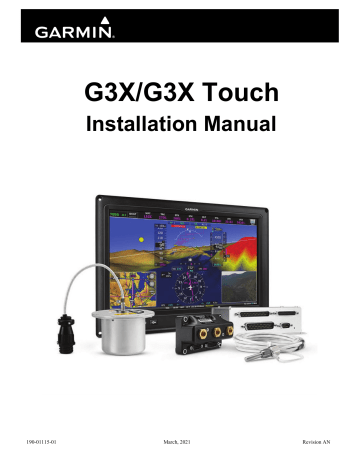
12.5 Outline and Installation Drawings
190-01115-01
Rev. AN
Figure 12-2 GMC 305 Outline Drawing
G3X/G3X Touch Installation Manual - GMC 305 Installation
Page 12-4
190-01115-01
Rev. AN
Figure 12-3 GMC 305 Installation Drawing
G3X/G3X Touch Installation Manual - GMC 305 Installation
Page 12-5
2.69068.33
6X 2.860
3.125
79.38
72.64
00.00
3.12579.38
6X 2.86072.64
2.69068.33
190-01115-01
Rev. AN
Figure 12-4 GMC 305 Cutout Drawing (Not to Scale)
G3X/G3X Touch Installation Manual - GMC 305 Installation
Page 12-6
GMC 305 PANEL CUTOUT
IMPORTANT!
Ensure the Page Scaling setting is set to NONE when printing this page. Verify dimensions of printed template are accurate before cutting panel.
CUT OUT PANEL
TO INSIDE LINE
NOTES:
1.
2.
DIMENSIONS: INCHES[mm]. METRIC VALUES ARE FOR REFERENCE ONLY.
DIMENSIONS ARE NOMINAL AND TOLERANCES ARE NOT IMPLIED UNLESS
SPECIFICALLY STATED.
Figure 12-5 GMC 305 Panel Cutout Template
190-01115-01
Rev. AN
G3X/G3X Touch Installation Manual - GMC 305 Installation
Page 12-7
13 GMC 307 (AFCS MODE CONTROLLER) INSTALLATION
NOTE
References to the GMC Mode Controller throughout this manual apply equally to the
GMC 305, GMC 307, and GMC 507 except where specifically noted.
This section contains general information as well as installation information for the GMC 307. Use this section to mount the GMC 307 unit.
Figure 13-1 GMC 307 Unit View (-00 version shown, -20 version has no YD button)
13.1 Equipment Description
The GMC 307 is a Garmin Automatic Flight Control System (AFCS) Mode Controller that can be used in a G3X installation. The GMC 307 provides a user interface for the autopilot function of the G3X system.
The GMC 307 mounts flush to the aircraft instrument panel using two pawl latches.
13.2 Equipment Available
13.2.1 Required Equipment
Table 13-1 GMC 307 Part Numbers
Model
GMC 307 w/Yaw Damper
GMC 307 no Yaw Damper
Assembly Part
Number
010-01595-00
010-01595-20
Unit Only Part
Number
011-03993-00
011-03993-20
190-01115-01
Rev. AN
G3X/G3X Touch Installation Manual - GMC 307 Installation
Page 13-1
13.2.2 Additional Equipment Required
required to install the unit.
Table 13-2 Contents of GMC 307 Installation Kit (010-12421-00)
Item
Connector Kit, 15 Pin, Hi Density Male w/Jackscrews
Garmin P/N
011-01824-00
Quantity
1
Table 13-3 Contents of Connector Kit (011-01824-00)
Item
Backshell w/Hdw, Jackscrew, 9/15 Pin
Connector, Male, High Density D-Sub,15 CKT
Contact, Pin, Military Crimp, Size 22D
Garmin P/N
011-01855-00
330-00366-15
336-00021-00
Quantity
1
1
12
13.3 General Specifications
See
for power/current specifications, and Section 2.4.1
for dimension/weight specifications.
13.4 Mounting and Wiring Requirements
13.4.1 Panel Cutout Template
can be used as a template when marking the panel for cutout. Dimensions on the figure are to verify accuracy of printout only, see
for complete cutout dimensions. A .dxf version of the drawing is also available for download at https://support.garmin.com/support/manuals .
190-01115-01
Rev. AN
G3X/G3X Touch Installation Manual - GMC 307 Installation
Page 13-2
13.4.2 Unit Installation
Fabrication of a wiring harness is required. Sound mechanical and electrical methods and practices are recommended for installation of the GMC 307. Refer to
for wiring considerations, and to
for pinouts.
2. Hold the unit flush with the instrument panel.
3. Using a 3/32" hex drive tool turn each of the two pawl latches clockwise until tightened to
20 +/-2 in-lbs. When tightened, the pawl latches are in the horizontal position.
CAUTION
To remove the GMC from the instrument panel, turn each of the two pawl latches counterclockwise. After initially breaking the pawl latch loose, continue to loosen while not exceeding 15 in-lbs of torque.
Figure 13-2. Pawl Latch
13.4.3 Wiring
The 15 pin connector, pins, and backshell supplied in the GMC 307 installation kit are used to add wiring for the GMC 307.
It is recommended that a 2 Amp fuse or circuit breaker be used to supply power to the GMC 307
). Backup power is optional.
The GMC 307 is connected via RS-232 to any GDU 37X/4XX display ( Figure 27-1.7
RS-232 channel must be configured for “Garmin Instrument Data”.
If the installation includes a Garmin integrated autopilot using GSA 28 servos, the GMC 307 installation also includes an RS-232 connection to the GSA 28 roll servo (
must be connected to any one of the available RS-232 channels on one of the GDU 37X/4XX units. The
GMC 307 RS-232 channel 2 must be connected to the GSA 28 roll servo RS-232 channel 1 if this roll servo is installed.
For installations using a non-Garmin autopilot with a GMC 307 controller, refer to Figure 27-2.25
.
190-01115-01
Rev. AN
G3X/G3X Touch Installation Manual - GMC 307 Installation
Page 13-3
13.5 Outline and Installation Drawings
190-01115-01
Rev. AN
Figure 13-3 GMC 307 Outline Drawing
G3X/G3X Touch Installation Manual - GMC 307 Installation
Page 13-4
190-01115-01
Rev. AN
Figure 13-4 GMC 307 Installation Drawing
G3X/G3X Touch Installation Manual - GMC 307 Installation
Page 13-5
190-01115-01
Rev. AN
Figure 13-5 GMC 307 Cutout Drawing (Not to Scale)
G3X/G3X Touch Installation Manual - GMC 307 Installation
Page 13-6
GMC 307 PANEL CUTOUT
IMPORTANT!
ENSURE THE PAGE SCALING SETTING IS SET TO NONE
WHEN PRINTING THIS PAGE. VERIFY DIMENSIONS OF
PRINTED TEMPLATE ARE ACCURATE BEFORE CUTTING
PANEL.
1.98
50.3
6.015 152.78
CUT OUT PANEL
TO INSIDE LINE
BEZEL OUTLINE
(REF.)
NOTES:
1. DIMENSIONS: INCHES [mm]. METRIC VALUES ARE FOR REFERENCE ONLY.
2. TOLERANCES: INCH mm
.XX ±.02 .X ±0.5
.XXX ±.010 .XX ±0.25
Figure 13-6 GMC 307 Panel Cutout Template
190-01115-01
Rev. AN
G3X/G3X Touch Installation Manual - GMC 307 Installation
Page 13-7
14 GMC 507 (AFCS MODE CONTROLLER) INSTALLATION
NOTE
References to the GMC Mode Controller throughout this manual apply equally to the
GMC 305, GMC 307, and GMC 507 except where specifically noted.
This section contains general information as well as installation information for the optional GMC 507.
Use this section to mount the GMC 507 unit.
Figure 14-1 GMC 507 Unit View (-00 version)
14.1 Equipment Description
The GMC 507 is a Garmin Automatic Flight Control System (AFCS) Mode Controller that can be used in a G3X installation. The GMC 507 provides a user interface for the autopilot function of the G3X system.
The GMC 507 mounts flush to the aircraft instrument panel using two pawl latches or may be mounted in the radio stack using the optional mounting rack listed in Table 14-3 .
14.1.1 Equipment Available
The GMC 507 is available by the part numbers listed in Table 14-1.
GMC 507
LRU
Table 14-1 Available LRU Part Numbers
Assembly Part Number
010-01946-00
Unit Only Part Number
011-04548-00
14.1.2 Additional Equipment Required
The following accessories are not provided with the GMC 507 unit. The Connector Kit (Table 14-2) is required to install the unit.
Table 14-2 Contents of Connector Kit (011-01824-01)
Item
Backshell w/Hdw, Jackscrew, 9/15 Pin
Connector, Male, High Density D-Sub,15 CKT
Contact, Pin, Military Crimp, Size 22D
Garmin P/N
011-01855-00
330-00366-15
336-00021-00
Quantity
1
1
15
190-01115-01
Rev. AN
G3X/G3X Touch Installation Manual - GMC 507 Installation
Page 14-1
14.1.3 Optional Equipment
Table 14-3 GMC 507 Installation Rack Kit (010-12700-10)
GMC 507 Installation Rack
Item Garmin P/N
115-02774-00
Quantity
1
14.2 General Specifications
See
for power/current specifications, and Section 2.4.1
for dimension/weight specifications.
14.3 Mounting and Wiring Requirements
14.3.1 Panel Cutout Template
Figure 14-6 can be used as a template when marking the panel for cutout. Dimensions on the figure are to verify accuracy of printout only, see
for complete cutout dimensions. A .dxf version of the drawing is also available for download at https://support.garmin.com/support/manuals .
CAUTION
Exercise caution when installing the rack in the instrument panel. Deformation of the rack will make it difficult to install and remove the GMC 507.
NOTE
If the front edges of the installation rack are behind the front surface of the aircraft panel, the GMC 507 pawl latches may not fully engage.
NOTE
The GMC 507 install rack may be used as a template for drilling the mounting holes.
14.3.2 Unit Installation
Fabrication of a wiring harness is required. Sound mechanical and electrical methods and practices are recommended for installation of the GMC 507. Refer to
for wiring considerations, and to
for pinouts.
14.3.2.1 Panel Cutout Installation
1. Per Figure 14-2, ensure the pawl latch fasteners are fully retracted and in the vertical position.
2. Insert the unit into the instrument panel cutout so that the backside of the bezel rests against the instrument panel. Orient the install rack as shown in
.
3. Using a 3/32" hex drive tool turn each of the two pawl latches clockwise until tightened to
20 +/-2 in-lbs. When tightened, the pawl latches are in the horizontal position (see Figure 14-2 ).
190-01115-01
Rev. AN
G3X/G3X Touch Installation Manual - GMC 507 Installation
Page 14-2
14.3.2.2 Radio Stack Installation
The GMC 507 Install Rack (115-02774-00) is to be used when installing the GMC 507 unit into a radio
Rack.
1. Ensure the left and right front edges of the install rack are flush with the front surface of the instrument panel.
2. Secure the install rack to a rigid, primary aircraft structure using (qty. 4) #6 100° flat head machine
may be secured using self-locking hex nuts on the outside.
3. With the pawl latch fasteners retracted, insert the GMC 507 into the Install Rack until the bezel contacts the front edges of the Install Rack.
4. Using a 3/32" hex drive tool turn each of the two pawl latches clockwise until tightened to
20 +/-2 in-lbs. When tightened, the pawl latches are in the horizontal position (see Figure 14-2).
CAUTION
To remove the GMC from the instrument panel, turn each of the two pawl latches counterclockwise. After initially breaking the pawl latch loose, continue to loosen while not exceeding 15 in-lbs of torque.
Figure 14-2. Pawl Latch
14.3.3 Wiring
The 15 pin connector, pins, and backshell supplied in the GMC 507 installation kit are used to add wiring for the GMC 507.
See
for example interconnect drawing.
190-01115-01
Rev. AN
G3X/G3X Touch Installation Manual - GMC 507 Installation
Page 14-3
14.4 Outline and Installation Drawings
190-01115-01
Rev. AN
Figure 14-3 GMC 507 Outline Drawing (no installation rack)
G3X/G3X Touch Installation Manual - GMC 507 Installation
Page 14-4
190-01115-01
Rev. AN
Figure 14-4 GMC 507 Installation Drawing (no installation rack)
G3X/G3X Touch Installation Manual - GMC 507 Installation
Page 14-5
Figure 14-5 GMC 507 Cutout Drawing, No Installation Rack (Not to Scale)
190-01115-01
Rev. AN
G3X/G3X Touch Installation Manual - GMC 507 Installation
Page 14-6
GMC 507 PANEL CUTOUT
IMPORTANT!
ENSURE THE PAGE SCALING SETTING IS SET TO NONE
WHEN PRINTING THIS PAGE. VERIFY DIMENSIONS OF
PRINTED TEMPLATE ARE ACCURATE BEFORE CUTTING
PANEL.
1.930 49.0
CUT OUT PANEL
TO INSIDE LINE
6.020
152.9
BEZEL OUTLINE
(REF.)
NOTES:
1. DIMENSIONS: INCHES [mm]. METRIC VALUES ARE FOR REFERENCE ONLY.
2. TOLERANCES: INCH mm
.XX ±.02 .X ±0.5
.XXX ±.010 .XX ±0.25
Figure 14-6 GMC 507 Panel Cutout Template (no installation rack)
190-01115-01
Rev. AN
G3X/G3X Touch Installation Manual - GMC 507 Installation
Page 14-7
190-01115-01
Rev. AN
Figure 14-7 GMC 507 Outline Drawing with Installation Rack
G3X/G3X Touch Installation Manual - GMC 507 Installation
Page 14-8
190-01115-01
Rev. AN
Figure 14-8 GMC 507 Installation Drawing with Installation Rack
G3X/G3X Touch Installation Manual - GMC 507 Installation
Page 14-9
Figure 14-9 GMC 507 Panel Cutout Template for Installation with Installation Rack
190-01115-01
Rev. AN
G3X/G3X Touch Installation Manual - GMC 507 Installation
Page 14-10
15 GMU 11 (MAGNETOMETER) INSTALLATION
This section contains general information as well as installation information for the GMU 11. Use this section to mount the GMU 11 unit.
Figure 15-1 GMU 11 Unit View
15.1 Equipment Description
The GMU 11 magnetometer is a remote mounted device that provides magnetometer data to a Garmin
GSU 25 ADAHRS. The Garmin ADAHRS and magnetometer replace traditional rotating mass instruments.
An Attitude and Heading Reference System combines the functions of a Vertical Gyro and a Directional
Gyro to provide measurement of Roll, Pitch, and Heading angles. The Garmin ADAHRS and magnetometer replace traditional rotating mass instruments.
Using long-life solid-state sensing technology, the GMU 11 Magnetometer uses magnetic field measurements to create an electronically stabilized AHRS.
The GMU 11 magnetometer provides magnetic information to support the function of the ADAHRS
(GSU 25). The supply voltage for the GMU 11 Magnetometer comes from aircraft power (9-32 V
100mA.)
NOTE
The GSU 73 is not compatible with the GMU 11 magnetometer. Installations that include a
GSU 73 must also include a GMU 22 connected to the GSU 73.
15.2 General Specifications
See
for power/current specifications, and Section 2.4.1
for dimension/weight specifications.
190-01115-01
Rev. AN
G3X/G3X Touch Installation Manual - GMU 11 Installation
Page 15-1
15.3 Equipment Available
Model
GMU 11
Table 15-1 GMU 11 Part Numbers
Assembly Part
Number
010-01788-00
Unit Only Part
Number
011-04349-00
GMU 11, Installation Kit
Item
Table 15-2 GMU 11 Accessories
Garmin P/N
011-04349-90
Installation Rack
No
Quantity
1
Table 15-3 Contents of GMU 11 Installation Kit (011-04349-90)
Item
Connector Kit, 9 Pin, w/CAN Term
Nut, Hex, Nyl Locking, 316SS/P, 6-32
Screw, 6-32x.500, PHP, SS/P
Washer, Flat, SAE, SS, #6
Garmin P/N
011-03002-00
210-10008-08
211-60207-12
212-00024-06
Quantity
1
4
4
4
15.4 Unit Installation
The following guidelines describe proper mechanical installation of the Garmin GMU 11 Magnetometer.
The guidelines include requirements for proper location selection in the aircraft, requirements for supporting structure and mechanical alignment and restriction on nearby equipment.
Fabrication of a wiring harness is required. Sound mechanical and electrical methods and practices are required for installation of the GMU 11. Refer to
for wiring considerations and to Section 26.8
for pinouts.
The GMU 11 is an extremely sensitive three-axis magnetic sensor. It is more sensitive to nearby magnetic disturbances than a flux gate magnetometer. For this reason, when choosing a mounting location for the
GMU 11, observe the following distances from objects or devices that can disturb the magnetic field.
Table 15-4 specifies recommended distances from magnetic disturbances for GMU 11 location.
NOTE
If the requirements listed in
Table 15-4 cannot be met, a magnetometer interference test
must be performed to ensure proper operation of the G3X system. Refer to the AHRS/
Magnetometer Installation Considerations document (190-01051-00) available from the
Garmin website ( www.garmin.com
) .
190-01115-01
Rev. AN
G3X/G3X Touch Installation Manual - GMU 11 Installation
Page 15-2
Table 15-4 Recommended Distance from Magnetic Disturbances
Disturbance Source*
Minimum Distance from GMU 11
10 feet (3.0 meters) Electric motors and relays, including servo motors
Ferromagnetic structure greater than 1 kg total (iron, steel, or cobalt materials, especially landing gear structure)
Ferromagnetic materials less than 1 kg total, such as control cables
Any electrical device drawing more than 100 mA current
Electrical conductors passing more than 100 mA current [(should be twisted shielded pair if within 10 feet (3.0 meters)]
Electrical devices drawing less than 100 mA current
Magnetic measuring device other than another GMU 11 (e.g. installed flux gates, even if not powered)
Electrical conductors passing less than 100 mA current [(should be twisted shielded pair if within 10 feet (3.0 meters)]
*Disturbance sources listed in table do not apply to a second installed GMU 11
8.2 feet (2.5 meters)
3 feet (1.0 meter)
3 feet (1.0 meter)
3 feet (1.0 meter)
2 feet (0.6 meter)
2 feet (0.6 meter)
1.3 feet (0.4 meter)
Ensure that any electrical conductor that comes within 10 feet (3.0 meters) of the GMU 11 is installed as a twisted shielded pair, not a single-wire conductor. (If possible, the shield should be grounded at both ends.)
Use nonmagnetic materials to mount the GMU 11, and replace any magnetic fasteners within 0.5 meter with nonmagnetic equivalents (e.g. replace zinc-plated steel screws used to mount wing covers or wing tips with nonmagnetic stainless steel screws).
In general, wing mounting of the GMU 11 magnetometer is preferred (unless as noted in
Fuselage mounting is less desirable because of numerous potential disturbances that interfere with accurate operation. For installations with dual GMU 11 magnetometers, co-locating the two magnetometers close to each other in the tail or in one wing is recommended as this reduces the likelihood of heading splits or miscompares when operating on the ground in the vicinity of local magnetic anomalies.
Mechanical mounting fixtures for the GMU 11 must be rigidly connected to the aircraft structure. Use of typical aircraft-grade non-magnetic materials and methods for rigid mounting of components is acceptable, so long as adequate measures are taken to ensure a stiffened mounting structure.
Level the GMU 11 to within 3.0° of the in-flight level cruise attitude.
, align the GMU 11’s forward direction to within 0.5° of the any of the 4 cardinal directions with relation between its connector and the nose of the aircraft. Make sure that the bottom of the unit is facing downwards (towards earth) per
.
190-01115-01
Rev. AN
G3X/G3X Touch Installation Manual - GMU 11 Installation
Page 15-3
15.4.1 Consideration for Wing Grounded Lighting Fixtures
The following installation practices are recommended if the GMU 11 is mounted in the wing.
The wing tip lights should not have a power ground referenced to the chassis of the light assembly that would then be referenced back to the airframe ground via the light assembly mounting.
A dedicated power ground should be used and returned as a twisted pair with the power source back into the fuselage for a wing mounted GMU 11.
These installation practices will prevent magnetically interfering currents from flowing in the wing skin that encloses the GMU 11. Electrically isolating the light assembly should not be used as an alternative to the preceding consideration, unless the isolated light assembly has been analyzed for adequate protection against direct attachment of lightning.
Refer to
for outline and installation drawings.
15.4.2 Mounting Instructions
After evaluation of the mounting location has been completed and ensuring that requirements are met, install the unit assemblies.
Mount the GMU 11 in its mounting location, taking care to tighten the mounting screws firmly. Use of non-magnetic tools (e.g. beryllium copper or titanium) is recommended when installing or servicing the
GMU 11. Do not use a screwdriver that contains a magnet when installing or servicing the GMU 11.
Refer to
for outline and installation drawings.
190-01115-01
Rev. AN
G3X/G3X Touch Installation Manual - GMU 11 Installation
Page 15-4
15.5 Outline and Installation Drawings
2.74
2.28
1.37
0.93
0.38
190-01115-01
Rev. AN
Figure 15-2 GMU 11 Outline Drawing
G3X/G3X Touch Installation Manual - GMU 11 Installation
Page 15-5
190-01115-01
Rev. AN
Figure 15-3 GMU 11 Installation Drawing
G3X/G3X Touch Installation Manual - GMU 11 Installation
Page 15-6
190-01115-01
Rev. AN
Figure 15-4 GMU 11 Orientation Drawing
G3X/G3X Touch Installation Manual - GMU 11 Installation
Page 15-7
16 GMU 22 (MAGNETOMETER) INSTALLATION
NOTE
All GMU 22 information in this Installation Manual also applies to the GMU 44, which had previously been the G3X magnetometer but has been replaced by the GMU 22.
This section contains general information as well as installation information for the GMU 22. Use this section to mount the GMU 22 unit. Installers may also benefit from studying
guidance for installing the GMU 22 into specific experimental airframes.
Figure 16-1 GMU 22 Unit View
16.1 Equipment Description
The GMU 22 magnetometer is a remote mounted device that provides magnetometer data to Garmin
ADAHRS devices (GSU 25/73). The Garmin ADAHRS and magnetometer replace traditional rotating mass instruments.
An Attitude and Heading Reference System combines the functions of a Vertical Gyro and a Directional
Gyro to provide measurement of Roll, Pitch, and Heading angles. The Garmin ADAHRS and magnetometer replace traditional rotating mass instruments.
Using long-life solid-state sensing technology, the GMU 22 Magnetometer uses magnetic field measurements to create an electronically stabilized AHRS.
The GMU 22 magnetometer provides magnetic information to support the function of the ADAHRS
(GSU 25/73). The ADAHRS (GSU 25/73) provides operating voltage to the GMU 22 Magnetometer.
16.1.1 Interface Summary
The following is an interface summary for the GMU 22:
• GMU 22 to ADAHRS (GSU 25/73) Interface: Power, RS-232, RS-485 (19,200 baud)
16.2 General Specifications
See
for power/current specifications, and Section 2.4.1
for dimension/weight specifications.
190-01115-01
Rev. AN
G3X/G3X Touch Installation Manual - GMU 22 Installation
Page 16-1
16.3 Equipment Available
Model
GMU 22
Table 16-1 GMU 22 Part Numbers
Assembly Part
Number
010-01196-00
Unit Only Part
Number
011-03269-00
Installation Rack
No
Table 16-2 GMU 22 Accessories
GMU 22, Connector Kit
GMU 22 Universal Mount*
Item Garmin P/N
011-00871-10
011-01779-01
Quantity
1
1 (optional)
Installation Rack, GMU 22 115-00481-10 1
*Refer to AHRS Magnetometer Installation Considerations (190-01051-00) from www.garmin.com
Table 16-3 Contents of GMU 22 Connector Kit (011-00871-10)
Item
Modified Install Rack
Screw, 6-32x .250, Pan Head Phillips, Brass, w/Nylon
Circular Connector, Female, 9 Ckt
Circular non-Magnetic Backshell
Socket Contact Mil Crp, Size 20
Garmin P/N
115-00481-10
211-60037-08
330-00360-00
330-90005-01
336-00022-00
Quantity
1
3
1
1
10
16.4 Unit Installation
The following guidelines describe proper mechanical installation of the Garmin GMU 22 Magnetometer.
The guidelines include requirements for proper location selection in the aircraft, requirements for supporting structure and mechanical alignment and restriction on nearby equipment.
Fabrication of a wiring harness is required. Sound mechanical and electrical methods and practices are required for installation of the GMU 22. Refer to
for wiring considerations and to Section 26.8
for pinouts.
The GMU 22 is an extremely sensitive three-axis magnetic sensor. It is more sensitive to nearby magnetic disturbances than a flux gate magnetometer. For this reason, when choosing a mounting location for the
GMU 22, observe the following distances from objects or devices that can disturb the magnetic field.
Table 16-4 specifies recommended distances from magnetic disturbances for GMU 22 location.
NOTE
If the requirements listed in
Table 16-4 cannot be met, a magnetometer interference test
must be performed to ensure proper operation of the G3X system. Refer to the AHRS/
Magnetometer Installation Considerations document (190-01051-00) available from the
Garmin website ( www.garmin.com
) .
190-01115-01
Rev. AN
G3X/G3X Touch Installation Manual - GMU 22 Installation
Page 16-2
Table 16-4 Recommended Distance from Magnetic Disturbances
Disturbance Source*
Minimum Distance from GMU 22
10 feet (3.0 meters) Electric motors and relays, including servo motors
Ferromagnetic structure greater than 1 kg total (iron, steel, or cobalt materials, especially landing gear structure)
Ferromagnetic materials less than 1 kg total, such as control cables
Any electrical device drawing more than 100 mA current
Electrical conductors passing more than 100 mA current [(should be twisted shielded pair if within 10 feet (3.0 meters)]
Electrical devices drawing less than 100 mA current
Magnetic measuring device other than another GMU 22 (e.g. installed flux gates, even if unpowered)
Electrical conductors passing less than 100 mA current [(should be twisted shielded pair if within 10 feet (3.0 meters)]
*Disturbance sources listed in table do not apply to a second installed GMU 22
8.2 feet (2.5 meters)
3 feet (1.0 meter)
3 feet (1.0 meter)
3 feet (1.0 meter)
2 feet (0.6 meter)
2 feet (0.6 meter)
1.3 feet (0.4 meter)
Ensure that any electrical conductor that comes within 10 feet (3.0 meters) of the GMU 22 is installed as a twisted shielded pair, not a single-wire conductor. (If possible, the shield should be grounded at both ends.)
Use nonmagnetic materials to mount the GMU 22, and replace any magnetic fasteners within 0.5 meter with nonmagnetic equivalents (e.g. replace zinc-plated steel screws used to mount wing covers or wing tips with nonmagnetic stainless steel screws).
In general, wing mounting of the GMU 22 magnetometer is preferred (unless as noted in
Fuselage mounting is less desirable because of numerous potential disturbances that interfere with accurate operation. For installations with dual GMU 22 magnetometers, co-locating the two magnetometers close to each other in the tail or in one wing is recommended as this reduces the likelihood of heading splits or miscompares when operating on the ground in the vicinity of local magnetic anomalies.
Mechanical mounting fixtures for the GMU 22 must be rigidly connected to the aircraft structure. Use of typical aircraft-grade materials and methods for rigid mounting of components is acceptable, so long as adequate measures are taken to ensure a stiffened mounting structure.
Level the GMU 22 mounting rack to within 3.0° of the in-flight level cruise attitude.
Align the GMU 22 mounting rack’s forward direction to within 0.5° of the longitudinal axis of the aircraft.
In a system with more than one ADAHRS (GSU 25/73), ADAHRS 1 must be connected to a GMU22, but installing additional GMU 22 units for other GSU 25 ADAHRS units is optional. An ADAHRS without a
GMU 22 connected will use magnetometer data supplied by other ADAHRS as long as they are both communicating via CAN.
190-01115-01
Rev. AN
G3X/G3X Touch Installation Manual - GMU 22 Installation
Page 16-3
16.4.1 Consideration for Wing Grounded Lighting Fixtures
The following installation practices are recommended if the required GMU 22 mounting bracket is located in the wing.
The wing tip lights should not have a power ground referenced to the chassis of the light assembly that would then be referenced back to the airframe ground via the light assembly mounting.
A dedicated power ground should be used and returned as a twisted pair with the power source back into the fuselage for a wing mounted GMU 22.
These installation practices will prevent magnetically interfering currents from flowing in the wing skin that encloses the GMU 22. Electrically isolating the light assembly should not be used as an alternative to item 1 above, unless the isolated light assembly has been analyzed for adequate protection against direct attachment of lightning.
Refer to
for outline and installation drawings.
16.4.2 ADAHRS (GSU 25/73) to GMU 22 Interconnect Harness Fabrication Instructions
included in the GMU 22 Connector Installation Kit. Other parts are provided by the installer. Reference
numbers refer to item bubble numbers shown in Figure 16-7 .
Table 16-5 Parts Needed for GMU 22 Installation
Figure D-2.4 Ref
1
2
3, 4, 9
Description
Shield Termination
(method optional)
Shield Extension Wire
GMU 22 Connector Kit*
Qty. Included
5
6
3-Conductor Cable
2-Conductor Cable
*Included in G3X w/GSU 73 Installation Kit (K10-00017-00)
0
0
0
0
1
GPN or MIL Spec
Parts used depend on method chosen
M22759/16-22
011-00871-00
M27500-22TE3T14
M27500-22TE2T14
for the GMU 22 has female polarity.
Table 16-6 GMU 22 Connector Kit (011-00871-00)** Contents, Reference
Item
Screw,6-32x.250,PHP,BR,w/Nyl
Conn,Circular,Female,9 Ckt
Backshell,Circular,Kit,SS
Garmin P/N
211-60037-08
330-00360-00
330-90005-01
Cont,Sckt,Mil Crp,Size 20 336-00022-00
**Included in G3X w/GSU 73 Installation Kit (K10-00017-00)
Quantity
3
1
1
10
Ref
9
4
4
3
190-01115-01
Rev. AN
G3X/G3X Touch Installation Manual - GMU 22 Installation
Page 16-4
16.4.3 Mounting Instructions
After evaluation of the mounting location has been completed and ensuring that requirements are met, assemble the GMU 22 mounting plate kits according to the dimensions given in
unit assemblies.
Mount the GMU 22 to its mounting plate, taking care to tighten the mounting screws firmly. Use of nonmagnetic tools (e.g. beryllium copper or titanium) is recommended when installing or servicing the
GMU 22. Do not use a screwdriver that contains a magnet when installing or servicing the GMU 22.
The metal components in the GMU 22 connector may slightly affect the magnetic field sensed by the
GMU 22. Place the connector at least 2 inches from the body of the GMU 22 to minimize this effect. After attaching the GMU 22's connector to its mate in the aircraft wiring, secure the connector in place using good installation practices. This will ensure that any remaining magnetic effect can be compensated for
using the Magnetometer Calibration ( Section 34.4.4.3
for GDU 37X systems and
for
GDU 4XX systems).
See Figure 16-2 for minimum recommended clearance for bend radius of the GMU 22 cable.
NOTE
If the GMU 22 is ever removed, the anti-rotation properties of the mounting screws must be restored. This may be done by replacing the screws with new Garmin part number
211 60037 08. If original screws must be re-used, coat screw threads with Loctite 242
(blue) thread-locking compound, Garmin part number 291 00023 02, or equivalent.
Important: Mounting screws must be brass.
MINIMUM RECOMMENDED CLEARANCE
FOR MINIMUM BEND RADIUS OF THE
GMU 22 CABLE IS 1.57[40] FROM THE
GMU 22 SURFACE
1.57 40
190-01115-01
Rev. AN
Figure 16-2 GMU 22 Minimum Recommended Clearance
G3X/G3X Touch Installation Manual - GMU 22 Installation
Page 16-5
16.5 Outline and Installation Drawings
0
1.54
.061
65.33
63.79
2.511
2.572
31.90
1.256
190-01115-01
Rev. AN
Figure 16-3 GMU 22 Mounting Rack (115-00481-00)
G3X/G3X Touch Installation Manual - GMU 22 Installation
Page 16-6
190-01115-01
Rev. AN
Figure 16-4 GMU 22 Mounting Rack (115-00481-10)
G3X/G3X Touch Installation Manual - GMU 22 Installation
Page 16-7
190-01115-01
Rev. AN
Figure 16-5 GMU 22 Top Mounted Installation
G3X/G3X Touch Installation Manual - GMU 22 Installation
Page 16-8
190-01115-01
Rev. AN
Figure 16-6 GMU 22 Bottom Mounted Installation
G3X/G3X Touch Installation Manual - GMU 22 Installation
Page 16-9
NOTE:
1. BUBBLE NUMBERS IN THIS DRAWING REFER TO
REFERENCE NUMBERS LISTED IN TABLES 13-5 AND 13-6.
190-01115-01
Rev. AN
Figure 16-7 GMU 22 Wiring Details
G3X/G3X Touch Installation Manual - GMU 22 Installation
Page 16-10
17 GPS 20A (WAAS GPS POSITION SOURCE) INSTALLATION
This section contains general information as well as installation information for the GPS 20A. Use this section to mount the GPS 20A unit.
NOTE
The GPS 20A can only be used with GA 35, GA 36, or GA 37 antennas.
,
GPS STATUS LED
UNIT STATUS LED
J201
Figure 17-1 GPS 20A Unit View
17.1 Equipment Description
The GPS 20A provides an ADS-B Out position source. The WAAS/SBAS position information is compatible with a wide range of 1090 ES transponders to meet the position requirements of
14 CFR 91.227. The GPS 20A also provides position data to all G3X and G3X Touch displays.
NOTE
If a GPS 20A (and connected GA 35, GA 36, or GA 37 antenna) is used for GPS position, additional GPS antennas (connected to GDU 37X/4XX units) may be used for redundancy, but are not required.
NOTE
The GPS 20A is not an FAA-approved product and thus is not eligible for installation in certified aircraft.
190-01115-01
Rev. AN
G3X/G3X Touch Installation Manual - GPS 20A Installation
Page 17-1
17.1.1 Status LED
The GPS 20A has two LEDs on its outer case that indicate its current unit and GPS status (
The unit status LED is in the middle of the outer case between the coax and 9 pin connectors. See
for details.
GPS status indications.
Table 17-1 GPS Status LED Indications
Red
LED Indication
No Light
Slow Flashing Green
Fast Flashing Green
Steady Green
Alternating Red/Green
Description
GPS hardware failure
GPS acquiring, low signal to noise ratio or antenna not connected
GPS acquiring, good signal to noise ratio
GPS fix acquired
GPS WAAS fix acquired
CAN bus network error, two similar devices are configured with same unit ID
17.2 Statement of Compliance (per AC 90-114A CHG1)
The Garmin GPS 20A, while not TSO approved, meets the ADS-B Out position source performance requirements for FAR 91.227 compliance when used in combination with a Mode S ADS-B Out transponder meeting the requirements of TSO-C166b and installed in accordance with the instructions in this document. Example transponders which may be used in combination with the GPS 20A for FAR
91.227 compliance are the Garmin GTX 330ES, GTX 23ES, GTX 35R, GTX 45R, GTX 345/345R, and
GTX 335/335R.
17.3 Equipment Available
17.3.1 Required Equipment
Model
GPS 20A
Table 17-2 GPS 20A Part Numbers
Assembly Part
Number
010-01546-00
Unit Only Part
Number
011-03913-00
190-01115-01
Rev. AN
G3X/G3X Touch Installation Manual - GPS 20A Installation
Page 17-2
advertisement
Related manuals
advertisement
Table of contents
- 24 Section 1 Inventory of Materials
- 24 1.1 Unpacking Unit
- 24 1.2 Required Garmin Equipment
- 24 1.3 Optional Garmin Equipment
- 24 1.4 Optional Garmin LRUs
- 24 1.5 Required non-Garmin Equipment
- 24 1.6 Optional Garmin Equipment (non-LRU)
- 24 1.7 Optional non-Garmin Equipment
- 24 1.8 Optional 3rd Party Sensors/LRUs
- 24 1.9 Garmin Software and Documents
- 25 Section 2 Installation Preparation
- 25 2.1 System Overview
- 25 2.2 Electrical Considerations
- 25 2.3 Wiring/Cabling Considerations
- 25 2.4 Mechanical Considerations
- 25 2.5 LRU/Sensor Installation Information
- 26 Section 3 GAD 27 (Flaps/Lights/Trim Controller) Installation
- 26 3.1 Equipment Description
- 26 3.2 Equipment Available
- 26 3.3 General Specifications
- 26 3.4 Mounting Requirements
- 26 3.5 Unit Installation
- 26 3.6 Outline and Installation Drawings
- 27 Section 4 GAD 29/29B (ARINC 429 Adapter) Installation
- 27 4.1 Equipment Description
- 27 4.2 Equipment Available
- 27 4.3 General Specifications
- 27 4.4 Mounting Requirements
- 27 4.5 Unit Installation
- 27 4.6 Outline and Installation Drawings
- 28 Section 5 GAP 26 (Pitot/AOA Probe) Installation
- 28 5.1 Equipment Description
- 28 5.2 Equipment Available
- 28 5.3 Required Equipment
- 28 5.4 General Specifications
- 28 5.5 Unit Installation
- 28 5.6 Outline and Installation Drawings
- 103 Section 6 GDU 37X (Display Unit) Installation
- 103 6.1 Equipment Description
- 103 6.2 General Specifications
- 103 6.3 Installation Information
- 103 6.4 Unit Installation
- 103 6.5 Antennas
- 103 6.6 Mounting Requirements
- 103 6.7 Outline and Installation Drawings
- 104 Section 7 GDU 45X (Display Unit) Installation
- 104 7.1 Equipment Description
- 104 7.2 General Specifications
- 104 7.3 Installation Information
- 104 7.4 Unit Installation
- 104 7.5 Antennas
- 104 7.6 Mounting Requirements
- 104 7.7 Outline and Installation Drawings
- 105 Section 8 GDU 46X (Display Unit) Installation
- 105 8.1 Equipment Description
- 105 8.2 General Specifications
- 105 8.3 Installation Information
- 105 8.4 Unit Installation
- 105 8.5 Antennas
- 105 8.6 Mounting Requirements
- 105 8.7 Outline and Installation Drawings
- 106 Section 9 GDU 470 (Display Unit) Installation
- 106 9.1 Equipment Description
- 106 9.2 General Specifications
- 106 9.3 Installation Information
- 106 9.4 Unit Installation
- 106 9.5 Antennas
- 106 9.6 Mounting Requirements
- 106 9.7 Outline and Installation Drawings
- 107 Section 10 GEA 24 (EIS Interface) Installation
- 107 10.1 Equipment Description
- 107 10.2 Equipment Available
- 107 10.3 General Specifications
- 107 10.4 Unit Installation
- 107 10.5 Mounting Requirements
- 107 10.6 Outline and Installation Drawings
- 112 Section 11 GI 260 (AOA Indicator) Installation
- 112 11.1 Equipment Description
- 112 11.2 Equipment Available
- 112 11.3 General Specifications
- 112 11.4 Unit Installation
- 112 11.5 Unit Calibration
- 112 11.6 Unit Operation
- 112 11.7 Outline and Installation Drawings
- 113 Section 12 GMC 305 (AFCS Mode Controller) Installation
- 113 12.1 Equipment Description
- 113 12.2 Equipment Available
- 113 12.3 General Specifications
- 113 12.4 Mounting and Wiring Requirements
- 113 12.5 Outline and Installation Drawings
- 114 Section 13 GMC 307 (AFCS Mode Controller) Installation
- 114 13.1 Equipment Description
- 114 13.2 Equipment Available
- 114 13.3 General Specifications
- 114 13.4 Mounting and Wiring Requirements
- 114 13.5 Outline and Installation Drawings
- 115 Section 14 GMC 507 (AFCS Mode Controller) Installation
- 115 14.1 Equipment Description
- 115 14.2 General Specifications
- 115 14.3 Mounting and Wiring Requirements
- 115 14.4 Outline and Installation Drawings
- 116 Section 15 GMU 11 (Magnetometer) Installation
- 116 15.1 Equipment Description
- 116 15.2 General Specifications
- 116 15.3 Equipment Available
- 116 15.4 Unit Installation
- 116 15.5 Outline and Installation Drawings
- 117 Section 16 GMU 22 (Magnetometer) Installation
- 117 16.1 Equipment Description
- 117 16.2 General Specifications
- 117 16.3 Equipment Available
- 117 16.4 Unit Installation
- 117 16.5 Outline and Installation Drawings
- 157 Section 17 GPS 20A (WAAS GPS Position Source) Installation
- 157 17.1 Equipment Description
- 157 17.2 Statement of Compliance (per AC 90-114A CHG1)
- 157 17.3 Equipment Available
- 157 17.4 General Specifications
- 157 17.5 Mounting Requirements
- 157 17.6 Unit Installation
- 157 17.7 Antennas
- 157 17.8 Antenna Cable Requirements
- 157 17.9 Outline and Installation Drawings
- 158 Section 18 GSA 28 (Autopilot Servo) Installation
- 158 18.1 Equipment Description
- 158 18.2 Equipment Available
- 158 18.3 General Specifications
- 158 18.4 Required Equipment
- 158 18.5 Unit Installation
- 158 18.6 Unit Wiring
- 158 18.7 Outline and Installation Drawings
- 159 Installation
- 159 19.1 Equipment Description
- 159 19.2 General Specifications
- 159 19.3 Required Equipment
- 159 19.4 Unit Installation
- 159 19.5 Outline and Installation Drawings
- 160 Section 20 GSU 73 (Sensor Unit) Installation
- 160 20.1 Equipment Description
- 160 20.2 General Specifications
- 160 20.3 Required Equipment
- 160 20.4 Unit Installation
- 160 20.5 Outline and Installation Drawings
- 161 Section 21 GTP 59 (Temperature Probe) Installation
- 161 21.1 Equipment Description
- 161 21.2 General Specifications
- 161 21.3 Unit Installation
- 161 21.4 GTP 59 Icing
- 161 21.5 Outline and Installation Drawings
- 162 Section 22 GTR 20 (VHF Communications Radio) Installation
- 162 22.1 Equipment Description
- 162 22.2 Equipment Available
- 331 22.3 General Specifications
- 331 22.4 Installation Considerations
- 331 22.5 Antenna Considerations
- 331 22.6 Mounting Considerations
- 331 22.7 Mounting, Wiring, and Power Checks
- 331 22.8 Outline and Installation Drawings
- 332 Section 23 GPS/XM Antenna Installation
- 332 23.1 Non-Garmin Materials Required
- 332 23.2 Non-Garmin Antennas
- 332 23.3 Garmin Antennas
- 332 23.4 Antenna Mounting Considerations
- 332 23.5 Teardrop Footprint Antenna Installation (GA 35, GA 55, and GA 56)
- 332 23.6 ARINC 743 Footprint Antenna Installation (GA 36, GA 37, GA 55A, GA 57X)
- 332 23.7 Non-Structural Mount Installation
- 332 23.8 Outline and Installation Drawings
- 333 Section 24 Engine/Airframe Sensor Installation
- 333 24.1 Engine/Airframe Sensor Options
- 333 24.2 Engine Sensor Applications
- 333 24.3 Engine Sensor Installation
- 334 Section 25 Connector Installation Instructions
- 334 25.1 Cable Connector Installation
- 334 25.2 Jackscrew Backshell Assembly
- 334 25.3 Jackscrew Connector Installation
- 334 25.4 Thermocouple Installation into a Backshell
- 334 25.5 Configuration Module Installation into a Backshell
- 334 25.6 P-Lead Resistor Installation (Braid Shield)
- 335 Section 26 LRU Pinouts
- 335 26.1 GAD 27 (Flaps/Lights/Trim Controller)
- 335 26.2 GAD 29/29B (ARINC 429 Adapter)
- 335 26.3 GDU 37X (Display Unit)
- 335 26.4 GDU 4XX (Display Unit)
- 335 26.5 GEA 24 (EIS Interface)
- 335 26.6 GI 260 (AOA Indicator)
- 335 26.7 GMC 305 (AFCS Mode Controller)
- 335 26.8 GMC 307 (AFCS Mode Controller)
- 335 26.9 GMC 507 (AFCS Mode Controller)
- 335 26.10 GMU 11 (Magnetometer)
- 335 26.11 GMU 22 (Magnetometer)
- 335 26.12 GPS 20A (WAAS GPS Position Source)
- 335 26.13 GSA 28 (Autopilot Servo)
- 335 26.14 GSU 25 (AHRS/Air Data Sensor Unit)
- 335 26.15 GSU 73 (Sensor Unit)
- 514 26.16 GTP 59 (Temperature Probe)
- 514 26.17 GTR 20 (VHF Communications Radio)
- 514 26.18 GTX 23 (Mode S Transponder)
- 515 Section 27 G3X w/GSU 25 and/or GAD 29 Interconnect Drawings
- 515 27.1 Core Interconnect Drawings w/GSU 25 and/or GAD
- 515 27.2 External Interconnect Drawings w/GSU
- 516 Section 28 G3X w/GSU 73 Interconnect Drawings
- 516 28.1 Core Interconnect Drawings
- 516 28.2 External Interconnect Drawings w/GSU
- 517 Section 29 G3X w/GTR 20 Interconnect Drawings
- 517 29.1 Notes for Section 29 Drawings
- 517 29.2 Single GTR 20 Interconnect Drawings
- 517 29.3 Dual GTR 20 Interconnect Drawings
- 518 Section 30 Sensor Wiring Examples
- 518 30.1 Notes for Section 30 Drawings
- 518 30.2 Sensor Wiring Examples w/GEA
- 518 30.3 Sensor Wiring Examples w/GSU
- 519 Section 31 Lycoming/Continental Sensor Wiring Examples
- 519 31.1 Notes for Section 31 Drawings
- 519 31.2 GEA 24 - Lycoming/Continental Sensor Drawings
- 519 31.3 GSU 73 - Lycoming/Continental Sensor Drawings
- 520 Section 32 Rotax Sensor Wiring Examples
- 520 32.1 Notes for Section 32 Drawings
- 520 32.2 GEA 24 - Rotax Sensor Drawings
- 520 32.3 GSU 73 - Rotax Sensor Drawings
- 521 Section 33 Jabiru Sensor Wiring Examples
- 521 33.1 Notes for Section 33 Drawings
- 521 33.2 GEA 24 - Jabiru Sensor Drawings
- 521 33.3 GSU 73 - Jabiru Sensor Drawings
- 522 Section 34 GDU 37X Configuration and Post Installation Checkout
- 522 34.1 Recommended Test Equipment
- 522 34.2 Configuration Mode
- 522 34.3 Software Loading Procedure
- 522 34.4 Configuration Pages
- 522 34.5 Garmin Database Updates
- 522 34.6 SiriusXM® Activation Instructions (GDU 375 only)
- 522 34.7 External Interface Configuration (Garmin units only)
- 885 34.8 GDU Splash Screen
- 885 34.9 Checklist Editor
- 886 Section 35 GDU 4XX Configuration and Post Installation Checkout
- 886 35.1 Recommended Test Equipment
- 886 35.2 Configuration Mode
- 886 35.3 Software Loading Procedure
- 886 35.4 Configuration Pages
- 886 35.5 Garmin Database Updates
- 886 35.6 SiriusXM® Activation Instructions (GDU 455/465 only)
- 886 35.7 External Interface Configuration (Garmin units only)
- 886 35.8 Sharing G3X Touch Flight Plans (Crossfill) with External IFR Navigators
- 886 35.9 Checklist Editor
- 887 Section 36 Troubleshooting
- 887 36.1 General Troubleshooting
- 887 36.2 CAN Network Troubleshooting
- 887 36.3 GDU 37X/4XX
- 887 36.4 Air Data Troubleshooting
- 887 36.5 Engine Indication Troubleshooting
- 887 36.6 ADAHRS Troubleshooting
- 887 36.7 Post Installation Calibration Procedures
- 887 36.8 GSU 73 Data Logging
- 887 36.9 Sending Troubleshooting Data to Garmin
- 888 Section 37 Maintenance
- 888 37.1 Inspections/Continued Airworthiness/Maintenance
- 888 37.2 Return to Service Information