Section 22 GTR 20 (VHF Communications Radio) Installation. Garmin G3X Touch for Experimental Aircraft, GDU 465, GDU 455, G3X, GDU 460, GDU 450
Add to My manuals943 Pages
advertisement
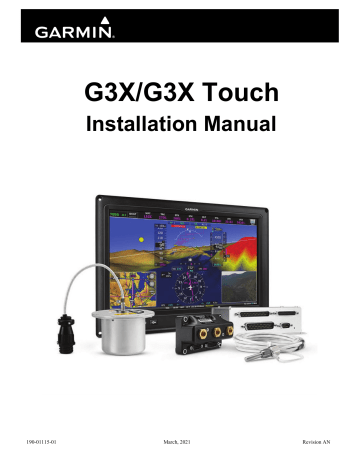
modes even if all GDU displays in the aircraft are unavailable.
GSA 28 autopilot servos can be used to control the trim system in an aircraft. When the autopilot is disengaged, the servos can adjust the trim speed based on the current aircraft airspeed. This allows the trim to run slower at high airspeeds and faster at low airspeeds. When the autopilot is engaged in the air, the servos can adjust the trim control to minimize the force on the primary controls. This helps ensure the aircraft will be properly trimmed when the autopilot is later disengaged. This feature works the same whether using a 3rd party trim motor or a GSA 28 as the trim actuator. When using a GSA 28 as the trim actuator, the following must be considered:
• The GSA 28 cannot hold a fixed position when disengaged, as the shaft will turn freely. It can only be used in installations where the trim actuator does not need to hold a fixed position when powered off. An acceptable application is the GSA 28 driving a manual pitch trim system via capstan and bridle cables.
• When used as the trim servo, the GSA 28 communicates via the CAN bus (same as the other servos communicate), no RS-232 or other data connection is required. The GSA 28 needs to be ID
strapped appropriately for the pitch trim location (see Section 26.13.5
).
• The GSA 28 should be connected to the CWS/DISCONNECT input. For manual electric trim, trim inputs from the stick or relay should be wired directly to the GSA 28 being used as the trim actuator, as well as the main autopilot servo for that axis.
During the flight test phase, the trim system is configured and set up after the primary autopilot performance has been properly configured. This is done so the pilot can focus on properly adjusting the performance of the primary autopilot system without having the auto-trim functionality interfere.
NOTE
Ensure basic autopilot functionality is properly adjusted before enabling trim control for any servo.
18.1.1 Status LED
The GSA 28 has an LED on its outer case that indicates its current status. See Section 36.1.1
18.2 Equipment Available
Table 18-1 GSA 28 Part Numbers
Model
GSA 28 Servo Actuator, Unit Only
Assembly Part Number
010-01068-00
Unit Only Part Number
011-02927-00
18.3 General Specifications
Table 18-2 General Specifications
Characteristic
Height
Width
Depth
Weight
*Harness connector not included
**Accessories not included
Specification
4.0 inches (10.16 cm)
2.5 inches (6.35 cm)
2.8* inches (7.11 cm)
1.40** lbs, (0.635 kg)
190-01115-01
Rev. AN
G3X/G3X Touch Installation Manual - GSA 28 Installation
Page 18-2
18.3.1 Power Specifications
The GSA 28 trim outputs are capable of sourcing a maximum of 1A of current to drive a DC trim motor at
12V, or a maximum of 500 mA of current to drive a DC trim motor at 24V.
To use the GSA 28 to drive DC trim motors requiring higher current, a third-party interface may be used
(see
CAUTION
The DC trim motor connected to the GSA 28 should be rated for the full power supply voltage being used to power the GSA 28. If the GSA 28 is connected by a 24-28V power input, the trim motor must also be rated for 28V.
NOTE
The GSA 28 does not provide a voltage step-up service. To drive a 24V trim motor, the
GSA 28 must be to be supplied with 24V or higher.
Table 18-3 GSA 28 Power Specifications
Supply Voltage
14 Vdc without Auto-trim
28 Vdc without Auto-trim
14 Vdc with Auto-trim
Current Draw
0.36 Amp (typical), 1.80 Amp (max)
0.20 Amp (typical), 1.00 Amp (max)
0.36 Amp (typical), 2.80 Amp (max)
18.3.2 Torque Specifications
Table 18-4 GSA 28 Torque Specifications
Characteristic
Maximum Rated Torque
Specification
60 in-lbs
190-01115-01
Rev. AN
G3X/G3X Touch Installation Manual - GSA 28 Installation
Page 18-3
18.4 Required Equipment
Table 18-5 lists the kits available for the GSA 28.
Table 18-5 GSA 28 Available Equipment w/Weights
Item
GSA 28 Connector Kit
GSA 28 Connector Kit, 90°
GSA 28 Stop Bracket Kit
GSA 28 Mounting Kit, Generic, Push-Pull
GSA 28 Mounting Kit, Generic, W/Bracket
GSA 28 Mounting Kit, Generic, Capstan
GSA 28 Mounting Kit, RV-6 Roll
GSA 28 Mounting Kit, RV-4/8 Pitch
GSA 28 Mounting Kit, RV-7/8/10 Roll
GSA 28 Mounting Kit, RV-9 Roll
GSA 28 Mounting Kit, RV-6/7/9 Pitch
GSA 28 Mounting Kit, RV-10 Pitch
GSA 28 Mounting Kit, RV-10 Yaw
GSA 28 Removal Adapter
Garmin P/N
011-02950-00
011-02950-01
011-02951-00
011-02952-00
011-02952-01
011-02952-02
011-02952-10
011-02952-11
011-02952-12
011-02952-13
011-02952-14
011-02952-15
011-02952-16
011-03158-00
Weight
0.12 lb (0.054 kg)
0.13 lb (0.059 kg)
0.03 lb (0.014 kg)
0.26 lb (0.118 kg)
0.50 lb (0.227 kg)
0.14 lb (0.064 kg)
0.55 lb (0.250 kg)
0.51 lb (0.231 kg)
0.42 lb (0.191 kg)
0.42 lb (0.191 kg)
0.37 lb (0.168 kg)
0.48 lb (0.218 kg)
0.60 lb (0.272 kg)
0.03 lb (0.014 kg)
Table 18-6 Contents of Connector Kit (011-02950-00)
Item
Sub-Assy, Bkshl w/Hdw, Jackscrew, 15/26 Pin
GSA 28 Removal Adapter
Connector, Rcpt, D-SUB, Crimp Socket,Commercial,15 Ckt
Cont,Sckt,Mil Crp,Size 20,20-24 AWG,RoHS
Garmin P/N
011-01855-01
011-03158-00
330-00625-15
336-00022-02
Quantity
1
1
1
16
Table 18-7 Contents of Connector Kit, 90 ° (011-02950-01)
Item
Sub-Assy, Bkshl w/Hdw, Jackscrew, 90°,15/26 Pin
GSA 28 Removal Adapter
Connector, Rcpt, D-SUB, Crimp Socket,Commercial,15 Ckt
Cont,Sckt,Mil Crp,Size 20,20-24 AWG,RoHS
Garmin P/N
011-01959-01
011-03158-00
330-00625-15
336-00022-02
Quantity
1
1
1
16
18.4.1 Additional Equipment Required
• Cables: The installer will fabricate and supply all system cables.
• Mounting hardware is included in the available mounting kits.
190-01115-01
Rev. AN
G3X/G3X Touch Installation Manual - GSA 28 Installation
Page 18-4
18.5 Unit Installation
Fabrication of a wiring harness is required. Sound mechanical and electrical methods and practices should
be used for installation of the GSA 28. Refer to Section 2.3
for wiring considerations, and to Section 26.12
for pinouts.
Connector kits include backshell assemblies. Garmin’s backshell connectors give the installer the ability to quickly and easily terminate shield grounds at the backshell housing. The instructions needed to install the
Jackscrew Backshell are located in
18.5.1 Pinouts
See
for pinout information.
18.5.2 Mounting Requirements
WARNING
It is vital to ensure the autopilot servo and aircraft control linkage is free to move throughout its entire range of travel without binding or interference. Failure to ensure adequate clearance between the moving parts of the control system linkage and nearby structure could result in serious injury or death. If any control system binding or interference is detected during installation or preflight inspection, it must be corrected before flight.
CAUTION
Do not mount the GSA 28 on the ‘hot’ side (engine side) of the firewall, or in any location where it would be exposed to radiated heat from the engine.
18.5.2.1 Optional Attachments
The GSA 28 is supplied from the factory with a standard crank arm attachment (
,
). Also available are a long crank arm supplied in the
011-02952-10 RV-6 roll kit and a capstan attachment available in the 011-02952-02 Capstan Kit. If one of these optional attachments will be used, it is up to the installer to remove the standard crank arm and replace it with the optional attachment. When removing the standard arm, keep the castle nut, lock washer, and flat washer as these items will need to be re-used with the optional attachment. Discard cotter pin that was removed from the GSA 28 and replace with pin provided with optional attachment. Refer to
for more details and instructions for tightening the castle nut.
WARNING
Cotter pins supplied with GSA 28 are only intended for one time use. If removed from GSA
28 discard and use new cotter pin.
WARNING
Do not use crank arm attachments to actuate cable driven controls. A Capstan attachment should be used for this purpose.
190-01115-01
Rev. AN
G3X/G3X Touch Installation Manual - GSA 28 Installation
Page 18-5
CRANK ARM
Figure 18-2 Crank Arm Assembly
18.5.2.2 Stop Bracket Kit
Every GSA 28 is supplied with a 011-02951-00 stop bracket kit. The intention of this stop bracket is to create redundant stops for the servo control arm that prevents the servo’s arm from going over-center relative to the push rod connected to the servo’s arm. It is highly recommended this part gets installed with every push-pull application. The stops created by installing this bracket are redundant in the sense that the aircraft’s built-in stops should always be used as the primary means of limiting travel of the servo’s control arm. This stop bracket limits the motion of the standard control arm to 100° total travel. This bracket should be positioned such that the stop bracket flanges are as close as practical to being equal distance from the servo’s control arm while at the center of travel. Also, to prevent an over-center condition, the servo’s push rod should be as close as practical to perpendicular with the servo’s control arm while positioned at the center of travel. The position of this bracket can be adjusted in increments of 15°. If necessary, further adjustments can be made by changing the length of the push rod connected to the servo.
See
for more details.
After installation of the servo is complete, verify that the stop bracket does NOT impede the full movement of the associated control.
WARNING
An over-center position of the servo control arm relative to the attached push rod can cause the flight controls to jam. This could result in serious injury or death. Please be sure this is well understood prior to flying with the GSA 28 servo.
190-01115-01
Rev. AN
G3X/G3X Touch Installation Manual - GSA 28 Installation
Page 18-6
The 011-02951-00 stop bracket kit is supplied with four #4-40 screws used to attach the bracket to the front face of the servo. The screws provided are 0.25” long. This length of screw is appropriate if there is no bracket or spacers in-between the stop bracket and servo. If a mounting bracket or spacers of thickness
.040” or greater will be place in-between the stop bracket and servo, longer screws should be used to mount the stop bracket. It is recommended the thread engagement into the GSA 28, as measured from the front face of the servo shall be 0.112” – 0.25”. If screws other than what is provided will be used, be sure to use thread locking compound or a proper thread locking patch combined with the lock washers provided.
Also be sure to follow the recommended tightening torque specified in
CAUTION
If screws are being used to mount the stop bracket to the front face of the GSA 28 are different than the screws provided with the stop bracket kit, care must be taken to ensure these screws are not long enough to contact moving parts inside the GSA 28. Maximum screw insertion, as measured from the front of the
GSA 28, must be less than 0.25” to avoid contact with parts inside the GSA 28.
CAUTION
To avoid the possibility of contaminating the internal rotating mechanisms of the GSA 28, do not apply thread locking compound directly to the stop bracket attachment holes in the front face of the servo. Instead, apply a small amount of thread locking compound to the threads of the stop bracket screws before the screws are inserted. Thread locking compound is not required upon initial installation of the included stop bracket screws, which are supplied with thread locking compound already applied.
18.5.2.3 Trim Motor Interface to a 3rd Party Motor
The GSA 28 provides an optional interface between the pilot's electric trim switch and a 14 Vdc trim motor. This interface shall be used only when interfacing to a 3rd party trim motor. This interface is not to be used when a GSA 28 is being used as the trim actuator.When the GSA 28 servo is engaged (i.e. autopilot on) in the air, it automatically drives the connected trim motor as required to relieve control forces for the associated pitch, roll, or yaw axis. When the GSA 28 servo is not engaged (i.e. autopilot off), it provides manual electric trim (MET) functionality by running the trim motor in response to pilot input.
The GSA 28 can be configured to automatically reduce the speed of the trim motor at higher airspeeds, in order to provide finer control of trim tab position. In the event that power to the GSA 28 is removed, a failsafe system connects the trim input switch directly to the trim motor. In this condition, the trim switch powers the trim motor directly and the motor runs at its full speed when the switch is pressed. The same condition also occurs if a trim switch and motor are connected to the GSA 28, but the trim control function is disabled.
CAUTION
The GSA 28 can supply a maximum of 1 Amp of current to the trim motor. Do not connect a trim motor that requires higher current.
NOTE
The GSA 28 supports a single trim switch input only. For use with multiple trim switches
(e.g. pilot and co-pilot), a GAD 27 or other third-party device capable of mixing multiple
trim switches into one is required. See Figure 27-1.10
for additional details.
190-01115-01
Rev. AN
G3X/G3X Touch Installation Manual - GSA 28 Installation
Page 18-7
18.5.2.4 CWS/DISCONNECT
The CWS/DISCONNECT button is used to disengage the autopilot system. It can also optionally be used for autopilot engagement and control wheel steering (see section 9.14.1). The CWS/DISCONNECT input to all servos should be tied together and connected to a normally open momentary push button that
connects to ground when pressed (see Figure 27-1.7
).
NOTE
The CWS/DISCONNECT button must be mounted where it is easily accessible to the pilot during all phases of flight. The pilot must have ability to quickly disconnect the autopilot under all circumstances.
18.5.2.5 GSA 28 Removal Adapter
The GSA 28 connector kit is shipped with a GSA 28 removal adapter (011-03158-00). This part is not intended to be installed with the GSA 28, but is used to replace the GSA 28 when the harness connector is un-plugged. The removal adapter contains an internal 120 Ω resistor between pins 2 and 3 for CAN termination. It also contains shorts between pins 11 & 13 and 12 & 14 to pass through power for trim motors. The intention of this component is to allow operation of the CAN bus and trim motors when the servos are not plugged into the harness. It is recommended that a removal adapter is kept with each servo installation, in case the GSA 28 needs to be removed without losing functionality of the CAN bus and trim motors.
190-01115-01
Rev. AN
Figure 18-3 Wiring Diagram For GSA 28 Removal Adapter
G3X/G3X Touch Installation Manual - GSA 28 Installation
Page 18-8
18.5.2.6 GSA 28 Mounting Kits
Garmin currently provides the mounting kits listed in Table 18-8 for the GSA 28 Servo:
Table 18-8 Mounting Kits
Garmin P/N Description
011-02952-00 Sub-Assy, GSA 28 Mounting Kit, Generic, Push-Pull
011-02952-01 Sub-Assy, GSA 28 Mounting Kit, Generic, W/Bracket
011-02952-02 Sub-Assy, GSA 28 Mounting Kit, Generic, Capstan
Mounting
Bracket
Included
No
Yes
No
011-02952-10 Sub-Assy, GSA 28 Mounting Kit, RV-6 Roll
011-02952-11 Sub-Assy, GSA 28 Mounting Kit, RV-4/8 Pitch
011-02952-12 Sub-Assy, GSA 28 Mounting Kit, RV-7/8/10 Roll
011-02952-13 Sub-Assy, GSA 28 Mounting Kit, RV-9 Roll
011-02952-14 Sub-Assy, GSA 28 Mounting Kit, RV-6/7/9 Pitch
011-02952-15 Sub-Assy, GSA 28 Mounting Kit, RV-10 Pitch
011-02952-16 Sub-Assy, GSA 28 Mounting Kit, RV-10 Yaw
Yes
Yes
Yes
Yes
Yes
Yes
Yes
Install Manual
Figures
,
,
,
,
,
,
,
,
airframe specific kits (GPN 011-02952-10 through -16) are for use with the specified experimental aircraft.
The contents of each kit as well as specific instructions for their use are detailed in the figures listed in
190-01115-01
Rev. AN
G3X/G3X Touch Installation Manual - GSA 28 Installation
Page 18-9
18.5.2.7 Generic Push/Pull Kits
The 011-02952-00 and -01 kits are generic kits for push/pull applications. This kit is supplied with a 3/8”
the GSA 28 and the flight control system. It is the installer’s responsibility to cut this rod to the correct length and tap the ends for the male rod end bearings. It is recommended these push rods are tapped to a depth of at least 0.61” to accommodate the entire thread of the rod end bearing (minus the jam nut). The length of the push rod is adjustable by changing the thread engagement between the male rod end bearings and push rod. The acceptable range of thread engagement is 0.492” +/-0.117”. It is highly recommended the AN315-3R jam nuts are used and properly tightened. A push rod without a tightened jam nut will create backlash that can diminish autopilot performance.
WARNING
Thread engagement between the male rod end bearings supplied with GSA 28 mounting kits and push rod must not be less than 0.375”. This minimum engagement length is recommended to prevent push rod from coming apart.
.141
1.25
.75
USABLE
THREAD
.492±.117
THREAD
ENGAMENT
10-32 UNF-3A AN315-3R
JAM NUT
Figure 18-4 General Dimensions For Servo Push Rod And Rod End Bearings
190-01115-01
Rev. AN
G3X/G3X Touch Installation Manual - GSA 28 Installation
Page 18-10
18.5.2.8 Capstan Kit
The capstan kit is part number 011-02952-02. This kit contains a capstan, a cable guard, and fasteners used to attach these items.
The capstan is designed to accept a MS20663C2 double shank ball with a 1/16” diameter cable. This kit does not currently include a bridle cable or cable clamps necessary to link the capstan to the flight control
a 1/16” cable with a MS20663C2 ball and double shank fitting swaged onto the cable where it engages with the capstan drive wheel. The MS20664C2 ball and shank fittings on the ends keep the cable from fraying.
Several companies sell custom made cable assemblies suitable for this application, a few of these are:
McFarlane Aviation
Phone: 866-920-2741 www.mcfarlane-aviation.com
Aircraft Spruce
Customer Service: 1-800-861-3192 www.aircraftspruce.com/catalog/appages/cableassy.php
NOTE
When determining the length of the bridle cable to be ordered, be sure to allow for enough cable to make the required number of wraps around the capstan (see
).
Figure 18-5 Bridle Cable
190-01115-01
Rev. AN
G3X/G3X Touch Installation Manual - GSA 28 Installation
Page 18-11
side-loading the servo center shaft.
BOTH CABLES EXITING CAPSTAN IN SAME DIRECTION
CABLE EXITING IN OPPOSITE DIRECTION
SHOULD BE IN CENTER OF CABLE WRAP WHEN
IN EITHER
ROTATE A MAXIMUM OF 150 EITHER DIRECTION FROM
BALL
BALL
Figure 18-6 Cable in Capstan
WARNING
The ball must be located in the center of travel on the capstan when the flight control is in the neutral position. When the flight control is moved to the limits of its travel, the ball must not have any possibility of exiting the capstan groove.
The bridle cable must wrap around the capstan either 1 or 1.5 full turns, as shown in Figure
18-6, and must be routed in a way that avoids the possibility of binding.
If the installation would require more than +/- 150° of capstan rotation or more than +/- 2.6 inches of cable travel, the GSA 28 servo and capstan cannot be used.
Failure to closely follow the capstan installation guidance in this section could cause the aircraft flight controls to jam, resulting in serious injury or death
The 011-02952-02 capstan kit is provided with four #4-40 screws and lock washers for attaching the cable guard. The screws provided are 0.25” long. This length of screw is appropriate if there is no bracket or spacers in-between the cable guard and servo. If a mounting bracket or spacers of thickness .056” or greater will be place in-between the stop bracket and servo, longer screws should be used to attach the cable guard. It is recommended the thread engagement into the GSA 28, as measured from the front face of the servo shall be 0.112” – 0.25”. If screws other than what is provided will be used, be sure to use thread locking compound or a proper thread locking patch combined with the lock washers provided. Also be sure
to follow the recommended tightening torque specified in Figure 18-8.4
.
CAUTION
If screws are being used to mount the cable guard to the front face of the GSA 28 are different than the screws provided with the stop bracket kit, care must be taken to ensure these screws are not long enough to contact moving parts inside the GSA 28. Maximum screw insertion, as measured from the front of the GSA 28, must be less than 0.25” to avoid contact with parts inside the GSA 28.
190-01115-01
Rev. AN
G3X/G3X Touch Installation Manual - GSA 28 Installation
Page 18-12
18.5.2.9 Aircraft Specific Mounting Kits
GSA 28 mounting kits are available for several experimental airframes. These mounting kits are listed in
. All of these kits contain sheet metal mounting brackets that have been designed for the specific application and some contain push rods that have been designed for the specific application. The push rods are supplied cut to the appropriate length and tapped for the male rod end bearings provided. Overall push rod length as well as rod end bearing thread engagement length is provided on the drawings for each kit.
The lengths specified are considered nominal. This length should be adjusted to fit the specific application.
Ideal push rod length results in the push rod being perpendicular to the servo arm when it is at the center of travel.
It is recommended the stop bracket is installed with all push/pull applications. The drawings for each of these mounting kits shows the recommended orientation of this bracket. It is acceptable to deviate from these drawings if a better orientation has been determined by the installer. The best orientation results in the stop bracket flanges being equal distance from the servo arm when at the center of travel. See
on stop bracket kit for more details on mounting the stop bracket.
190-01115-01
Rev. AN
G3X/G3X Touch Installation Manual - GSA 28 Installation
Page 18-13
18.5.2.10 GSA 28 Installation Into a Non-Garmin Bracket
For installers who intend to fabricate their own brackets or use an existing bracket designed for a non-
Garmin servo, consider the following:
The geometry of the GSA 28 varies from other popular servo models.
While the GSA 28 has the same 2.5” x 4.0” footprint, the same mounting hole locations, and uses the same mounting bolts as several other popular brands of autopilot servo, it does not fit into all mounting brackets designed for other servos. Some of the key differences to consider are:
• The GSA 28 servo has a larger bushing protrusion on the front plane of the servo.
• The harness connector is larger and in a different location relative to the output shaft.
• The GSA 28 does not contain tapped holes for mounting, instead it uses through holes and a thinner mounting flange.
Brackets fabricated for other manufacturer’s servos may or may not have enough clearance for the large bushing protrusion. Modification to the bracket may be necessary to avoid interference with bushing protrusion. See
for details.
CAUTION
Damage may occur to the GSA 28 if the mounting bracket overlaps the bushing protrusion when tightening down the mounting bolts. The damage can occur when the bushing is displaced into the unit. To prevent damage, ensure there is clearance for the bushing protrusion and be sure the GSA 28 mounting plate is flush with the bracket when the mounting bolts are being tightened.
For RV-7/8/9/10 roll installations, the rear support bracket used with other popular servos is not compatible with the GSA 28. This is because of the difference in thickness of the GSA 28 mounting flange relative the other servos.
for GSA 28 outline dimensions. See Figure 18-8.5
for recommended bracket cutout
dimensions.
NOTE
Garmin cannot validate the structural integrity of non-Garmin brackets.
Mounting brackets provided in the Garmin GSA 28 mounting kits have been designed to withstand (and have been tested to) repetitive stress cycles endured during loads generated by the GSA 28 and aircraft vibrations. If using a non-Garmin mounting bracket, it is the installer’s responsibility to ensure the bracket is structurally adequate for the application. It is important to consider the detrimental effects of bracket displacement and potential for fatigue failures due to reaction forces created by the GSA 28 loading and aircraft vibration.
WARNING
If using a non-Garmin mounting bracket, it is the installer’s responsibility to ensure the bracket is structurally adequate for the application.
190-01115-01
Rev. AN
G3X/G3X Touch Installation Manual - GSA 28 Installation
Page 18-14
Figure 18-7 Non-Garmin GSA 28 Bracket
190-01115-01
Rev. AN
G3X/G3X Touch Installation Manual - GSA 28 Installation
Page 18-15
18.5.3 Unit Mounting
For final installation and assembly, refer to the outline and installation drawings Figure 18-8.1
through
WARNING
Unless otherwise specified, tighten all threaded fasteners in accordance with FAA advisory circular AC 43-13-1B section 7.40, including adjustment for friction drag torque.
18.6 Unit Wiring
Refer to the
interconnect drawing for connecting GSA 28 wiring.
18.7 Outline and Installation Drawings
Refer to the following figures for GSA 28 installation guidance.
190-01115-01
Rev. AN
G3X/G3X Touch Installation Manual - GSA 28 Installation
Page 18-16
190-01115-01
Rev. AN
Figure 18-8.1 GSA 28 Outline/Installation Drawing 011-02927-00
G3X/G3X Touch Installation Manual - GSA 28 Installation
Page 18-17
190-01115-01
Rev. AN
Figure 18-8.2 GSA 28 Accessory Installation Drawing
G3X/G3X Touch Installation Manual - GSA 28 Installation
Page 18-18
190-01115-01
Rev. AN
Figure 18-8.3 GSA 28 Crank Arm Attachments Drawing
G3X/G3X Touch Installation Manual - GSA 28 Installation
Page 18-19
Figure 18-8.4 GSA 28 with Capstan Kit and Cable Instructions (011-02952-02)
190-01115-01
Rev. AN
G3X/G3X Touch Installation Manual - GSA 28 Installation
Page 18-20
190-01115-01
Rev. AN
Figure 18-8.5 GSA 28 Recommended Bracket Cutout Dimensions
G3X/G3X Touch Installation Manual - GSA 28 Installation
Page 18-21
190-01115-01
Rev. AN
Figure 18-8.6 GSA 28 Recommended Mounting Hardware
G3X/G3X Touch Installation Manual - GSA 28 Installation
Page 18-22
Figure 18-8.7 GSA 28 Generic, Push-Pull Mounting Kit (No Bracket) 011-02952-00
190-01115-01
Rev. AN
G3X/G3X Touch Installation Manual - GSA 28 Installation
Page 18-23
Figure 18-8.8 GSA 28 Generic, Push-Pull Mounting Kit w/Bracket 011-02952-01
190-01115-01
Rev. AN
G3X/G3X Touch Installation Manual - GSA 28 Installation
Page 18-24
Figure 18-9.1 GSA 28 RV-6 Roll Mounting Kit 011-02952-10 (page 1 of 3)
190-01115-01
Rev. AN
G3X/G3X Touch Installation Manual - GSA 28 Installation
Page 18-25
Figure 18-9.1 GSA 28 RV-6 Roll Mounting Kit 011-02952-10 (page 2 of 3)
190-01115-01
Rev. AN
G3X/G3X Touch Installation Manual - GSA 28 Installation
Page 18-26
Figure 18-9.1 GSA 28 RV-6 Roll Mounting Kit 011-02952-10 (page 3 of 3)
190-01115-01
Rev. AN
G3X/G3X Touch Installation Manual - GSA 28 Installation
Page 18-27
Figure 18-10.1 GSA 28 RV-4/8 Pitch Mounting Kit 011-02952-11 (page 1 of 4)
190-01115-01
Rev. AN
G3X/G3X Touch Installation Manual - GSA 28 Installation
Page 18-28
Figure 18-10.1 GSA 28 RV-4/8 Pitch Mounting Kit 011-02952-11 (page 2 of 4)
190-01115-01
Rev. AN
G3X/G3X Touch Installation Manual - GSA 28 Installation
Page 18-29
D
AR
RW
FO
Figure 18-10.1 GSA 28 RV-4/8 Pitch Mounting Kit 011-02952-11 (page 3 of 4)
190-01115-01
Rev. AN
G3X/G3X Touch Installation Manual - GSA 28 Installation
Page 18-30
Figure 18-10.1 GSA 28 RV-4/8 Pitch Mounting Kit 011-02952-11 (page 4 of 4)
190-01115-01
Rev. AN
G3X/G3X Touch Installation Manual - GSA 28 Installation
Page 18-31
Figure 18-11.1 GSA 28 RV-7/8/10 Roll Mounting Kit 011-02952-12 (page 1 of 2)
190-01115-01
Rev. AN
G3X/G3X Touch Installation Manual - GSA 28 Installation
Page 18-32
INBOARD
Figure 18-11.1 GSA 28 RV-7/8/10 Roll Mounting Kit 011-02952-12 (page 2 of 2)
190-01115-01
Rev. AN
G3X/G3X Touch Installation Manual - GSA 28 Installation
Page 18-33
Figure 18-12.1 GSA 28 RV-9 Roll Mounting Kit 011-02952-13 (page 1 of 2)
190-01115-01
Rev. AN
G3X/G3X Touch Installation Manual - GSA 28 Installation
Page 18-34
INBOARD
Figure 18-12.1 GSA 28 RV-9 Roll Mounting Kit 011-02952-13 (page 2 of 2)
190-01115-01
Rev. AN
G3X/G3X Touch Installation Manual - GSA 28 Installation
Page 18-35
RD
A
RW
FO
Figure 18-13.1 GSA 28 RV-6/7/9 Mounting Kit 011-02952-14 (page 1 of 2)
190-01115-01
Rev. AN
G3X/G3X Touch Installation Manual - GSA 28 Installation
Page 18-36
Figure 18-13.1 GSA 28 RV-6/7/9 Pitch Mounting Kit 011-02952-14 (page 2 of 2)
190-01115-01
Rev. AN
G3X/G3X Touch Installation Manual - GSA 28 Installation
Page 18-37
Figure 18-14.1 GSA 28 RV-10 Pitch Mounting Kit 011-02952-15 (page 1 of 2)
190-01115-01
Rev. AN
G3X/G3X Touch Installation Manual - GSA 28 Installation
Page 18-38
Figure 18-14.1 GSA 28 RV-10 Pitch Mounting Kit 011-02952-15 (page 2 of 2)
190-01115-01
Rev. AN
G3X/G3X Touch Installation Manual - GSA 28 Installation
Page 18-39
Figure 18-15.1 GSA 28 RV-10 Yaw Mounting Kit 011-02952-16 (page 1 of 3)
190-01115-01
Rev. AN
G3X/G3X Touch Installation Manual - GSA 28 Installation
Page 18-40
Figure 18-15.1 GSA 28 RV-10 Yaw Mounting Kit 011-02952-16 (page 2 of 3)
190-01115-01
Rev. AN
G3X/G3X Touch Installation Manual - GSA 28 Installation
Page 18-41
Figure 18-15.1 GSA 28 RV-10 Yaw Mounting Kit 011-02952-16 (page 3 of 3)
190-01115-01
Rev. AN
G3X/G3X Touch Installation Manual - GSA 28 Installation
Page 18-42
19 GSU 25/25B/25C/25D (AHRS/AIR DATA SENSOR UNIT)
INSTALLATION
NOTE
References to the GSU 25 throughout this manual apply equally to the GSU 25B,
GSU 25C, and GSU 25D except where specifically noted.
The GSU 25 can be installed as part of the G3X system. This section contains general information as well as installation information for the GSU 25. Use this section to mount the GSU 25 unit.
NOTE
The GSU 25 was a prior version of the GSU 25C, all form, fit, and functions are identical for the two models.
NOTE
The GSU 25B was a prior version of the GSU 25D, all form, fit, and functions are identical for the two models.
19.1 Equipment Description
NOTE
There is no TSO/ETSO applicable to the GSU 25.
The GSU 25 is not supported for installations in type certificated aircraft using the guidance in this installation manual.
The GSU 25 is an LRU that provides AHRS and Air Data information in a single mechanical package. The
GSU 25 interfaces to a remote mounted GMU magnetometer for heading information and also computes
OAT and TAS from inputs provided by the GTP 59. Up to three GSU 25 units may be installed to provide redundancy and cross-checking of attitude, heading, and air data.
The GSU 25 provides the functions in Table 19-1.
Air Data
Table 19-1 GSU 25 Functions
Interfaces
Pressure Altitude
Density Altitude
Vertical speed
Mach Number
CAN (1)
RS-232 (2 TX/2 RX)
OAT Probe (GTP 59)
Magnetometer (GMU 22)
(1 RS-232 TX/ 1 RS-485 RX)
AHRS
Magnetic Heading (with input from GMU magnetometer )
Pitch Angle
Roll Angle
Linear Accelerations
Indicated Airspeed
True Airspeed
Angle of attack
Pitch, Roll, Yaw Rotation Rates
3 axis angular rates
3 axis accelerations
190-01115-01
Rev. AN
G3X/G3X Touch Installation Manual - GSU 25/25B/25C/25D Installation
Page 19-1
Air Data
Outside and total air temperature (via GTP 59)
Table 19-1 GSU 25 Functions
Interfaces AHRS
Figure 19-1 GSU 25 Unit View
19.1.1 Status LED
The GSU 25 has an LED on the outer case that indicates current status. See
190-01115-01
Rev. AN
G3X/G3X Touch Installation Manual - GSU 25/25B/25C/25D Installation
Page 19-2
19.2 General Specifications
See
for power/current specifications, and Section 2.4.1
for dimension/weight specifications.
GSU 25D (011-02929-51 only) HARDWARE MOD LEVEL HISTORY
The following table identifies hardware modification (Mod) Levels for the GSU 25D LRU. Mod Levels are listed with the associated service bulletin number, service bulletin date, and the purpose of the modification. The table is current at the time of publication of this manual (see date on front cover) and is subject to change without notice.
MOD
LEVEL
1
SERVICE
BULLETIN
NUMBER
N/A
SERVICE
BULLETIN
DATE
N/A
PURPOSE OF MODIFICATION
Changed Maximum Pressure Altitude from 30,000 feet to 55,000 feet
190-01115-01
Rev. AN
G3X/G3X Touch Installation Manual - GSU 25/25B/25C/25D Installation
Page 19-3
19.3 Required Equipment
Table 19-2 lists the kits available for the GSU 25.
Table 19-2 GSU 25 Available Equipment
Item
GSU 25C Unit Assembly
GSU 25D Unit Assembly
GSU 25 Connector Kit (contains all items in Table 19-3 and Table 19-4)
Garmin P/N
011-02929-50
011-02929-51
K10-00181-00
Quantity
1
1
1
Table 19-3 Contents of 9 Pin Connector Kit (011-03002-00)
Item
Backshell w/Hdw, Jackscrew, 9/15 pin
CAN Termination Kit
D-Sub, Crimp Socket Connector, 09 CKT
Contact Socket, Mil Crimp, Size 20, 20-24 AWG
Garmin P/N
011-01855-00
011-02887-00
330-00625-09
336-00022-02
Quantity
1
1
1
9
Table 19-4 Contents of 15 Pin Connector Kit (011-03002-01) contains mounting hardware
Item
Backshell w/Hdw, Jackscrew, 15/26 pin
AN3-7A, Bolt
AN960, Cad Plate, #10 Washer
Washer, Int Star, MS35334, #10
D-Sub, Crimp Socket Connector, 15 CKT
Contact Socket, Mil Crimp, Size 20, 20-24 AWG
Garmin P/N
011-01855-01
211-00090-05
212-00035-10
212-00081-03
330-00625-15
336-00022-02
Quantity
1
4
1
15
4
4
19.3.1 Additional Equipment Required
• Wiring: The installer will fabricate cables and supply all wire for system connector kits
011-03002-00 and 011-03002-01.
• Air hoses and fittings to connect pitot air, static air, and AOA air to the GSU 25. The GSU 25 uses a female 1/8 27 ANPT fitting for each of these ports. Use appropriate aircraft fittings to connect to pitot, static, and AOA system lines (per
190-01115-01
Rev. AN
G3X/G3X Touch Installation Manual - GSU 25/25B/25C/25D Installation
Page 19-4
19.4 Unit Installation
Fabrication of a wiring harness is required. Sound mechanical and electrical methods and practices should
be used for installation of the GSU 25. Refer to Section 2.3
for wiring considerations, and to Section 26.14
for pinouts.
The GSU 25 connects to other LRUs in the G3X system using the CAN bus. To provide an optional redundant path for attitude and air data, a secondary RS-232 connection to a single GDU display (typically
PFD1) is also supported. See
for wiring and configuration information.
Connector kits include backshell assemblies. Garmin’s backshell connectors give the installer the ability to quickly and easily terminate shield grounds at the backshell housing. The instructions needed to install the
jackscrew backshell are located in Section 25
.
NOTE
Connection to a GMU magnetometer and GTP 59 is required for ADAHRS 1 but optional for ADAHRS 2 & 3.
NOTE
Ensure that backshell connectors are fully tightened. Loose connectors may cause vibration-related performance issues that are difficult to troubleshoot.
19.4.1 Mounting/Calibration Overview
It is critical that the GSU 25 is mounted in alignment with the centerline of the aircraft. The GSU 25 must be mounted with the connectors aligned within 1.0 degree of either the longitudinal or lateral axis of the
aircraft. (see Section 19.4.1 for complete requirements)
The specification for mounting the GSU 25 such that it is level with respect to pitch/roll of the aircraft is not nearly as restrictive, and must only be within 30.0 degrees in each axis. In most installations, the
GSU 25 is mounted relatively level with respect to the zero waterlines of the aircraft (e.g. longerons), even
requirements
Calibrating the pitch/roll offsets is also a crucial part of the installation (see Section 35.4.7
calibration, while on the ground, the aircraft must be level in both pitch/roll such that it accurately represents the in-cruise attitude of the aircraft. This part of the calibration determines that the displayed measured attitude of the GSU 25 is zero degrees in pitch/roll when the aircraft is in level, coordinated cruise flight. (Note that the PFD allows +/- 5 degrees of pitch offset adjustment in flight. This allows the pilot to adjust the pitch offset while in flight to show a correct attitude indication on the PFD, even if the pitch attitude was slightly off when the on the ground pitch/roll offset calibration was performed.)
190-01115-01
Rev. AN
G3X/G3X Touch Installation Manual - GSU 25/25B/25C/25D Installation
Page 19-5
19.4.2 Mounting Requirements
The GSU 25 contains an extremely sensitive strap-down inertial measurement unit, consider the following when selecting a mounting location:
• The GSU 25 can be oriented remotely in any of 24 orientations ( Figure 19-6
), but must satisfy the mounting alignment requirements along the longitudinal/lateral axes of the aircraft. The unit can be mounted in any of the 4 cardinal directions with the connectors pointing up or down can also be mounted on a vertical surface, with the connectors facing up, down, forward, aft, left, or right.
NOTE
The “Tubes Up” mounting orientations are not recommended as any moisture in the pitot/static/AOA line could drain into the GSU 25 and damage the pressure sensors.
NOTE
Select the “Tubes Forward/Connectors Down” orientation when the GSU 25 is mounted to the back of the GDU 4XX unit.
• Although mounting the GSU 25 to the threaded holes on the back of the GDU 4XX display is not generally recommended due to instrument panel flexing, the “Tubes Forward/Connectors Down” configuration should be selected when this location is used.
• Mount the GSU 25 with the connectors aligned within 1.0 degree of either the longitudinal or lateral axis of the aircraft. The direction of the unit will be accounted for during the calibration procedure as shown in Figure 19-2 .
• The GSU 25 must be mounted rigidly to the aircraft primary structure through strong structural
members capable of supporting substantial loads, see torque specification listed on Figure 19-5 .
• The supporting plate must be rigidly connected.
• The GSU 25 should be mounted within 13 feet (4.0 meters) longitudinally and 6.5 feet (2.0 meters) laterally of the aircraft CG (center of gravity). In cases where the longitudinal distance from the
CG is planned to be greater than 6.5 feet (2.0 meters), it is preferable to mount the GSU 25 forward of the aircraft CG if possible, to enable better acceleration outputs for autopilot use.
• Avoid placing the GSU 25 near sources of vibration or audible noise. Example locations to be avoided include the engine firewall, near large motors or fans, and audible buzzers and speakers.
• Do not mount the GSU 25 in an enclosed area, it should be mounted in a location that provides adequate airflow.
• Avoid areas that are prone to severe vibration. Excessive vibration may result in degraded accuracy.
• Do not use shock mounting to mount the GSU 25. Shock mounts used for other types of inertial systems are not acceptable for the GSU 25 AHRS. The mounting system must have no resonance with the unit installed. The unit and mounting structure must not have any resonance with respect to the aircraft primary structure.
• The wing is not an ideal location to install the GSU 25. Installing a GSU 25 in the wing may exceed the lateral CG boundary for the unit, exposes the unit to potential wing flex (of which any amount is a problem), and may expose the unit to unacceptable levels of acoustic noise resulting from precipitation impacting the leading edge of the wing. These are potential sources of error in the determination of attitude and should be avoided.
190-01115-01
Rev. AN
G3X/G3X Touch Installation Manual - GSU 25/25B/25C/25D Installation
Page 19-6
• The GSU 25 must be leveled to within 30.0° of the in-flight level cruise attitude and an aircraft leveling and offset calibration procedure carried out prior to flight. (This procedure is described in
for GDU 37X systems and Section 35.4.7.2
for GDU 4XX systems.)
• The mounting location for the GSU 25 should be protected from rapid thermal transients, in particular, large heat loads from nearby high-power equipment.
• Avoid placing the GSU 25 within 1 inch of magnetically mounted antennas, speaker magnets, or other strongly magnetic items.
Figure 19-2 AHRS Orientation Selection
19.4.3 Unit Mounting
For final installation and assembly, refer to the outline and installation drawing
and
of this manual.
1. Mount the unit to a suitable mounting location using the hardware in the connector kit (
per the requirements in
.
2. Assemble the wiring harness and backshell connectors
3. Assemble the pneumatic hoses and connectors.
4. Connect backshell connector and hoses.
5. Connect CAN terminator to unit if required (see Section 2.3.1.3.3
NOTE
When mounting the GSU 25 to the airframe, it is important to ensure that fastening hardware is tight for proper unit operation.
190-01115-01
Rev. AN
G3X/G3X Touch Installation Manual - GSU 25/25B/25C/25D Installation
Page 19-7
19.4.4 Pneumatic Plumbing
The GSU 25 has three ports that are connected to the aircraft’s pitot pressure source, static pressure source,
27 ANPT female threads. The mating fitting must have 1/8-27 ANPT male threads.
NOTE
The temporary port plugs attached to the pressure ports on a new GSU 25 are not suitable for flight, remove prior to installation of GSU 25 into aircraft.
Figure 19-3 GSU 25 Air Hose Fitting Locations
Use appropriate air hoses and fittings to connect the pitot and static lines to the unit. Use colored (or well marked) tubing to avoid confusing pitot, static, and AOA plumbing per
. Avoid sharp bends and routing near aircraft control cables. The GSU 25 should not be at the low point of the pneumatic plumbing lines, to avoid moisture or debris collecting at or near the unit. Ensure that no deformations of the airframe surface have been made that would affect the relationship between static air pressure and true ambient static air pressure for any flight condition. Refer to part 43, Appendix E for approved practices while installing hoses and connections.
190-01115-01
Rev. AN
G3X/G3X Touch Installation Manual - GSU 25/25B/25C/25D Installation
Page 19-8
19.4.5 Pneumatic Connections
The following steps should be used to aid in the fabrication of pneumatic hose connections and in attaching the aircraft pitot pressure source and aircraft static pressure source to the GSU 25.
CAUTION
If the AOA port is unused, connect it to the static port to avoid overpressuring (and causing damage to) the internal AOA sensor.
CAUTION
When the GSU 25 is used in conjunction with the GAP 26 pitot/AOA probe to perform Part 43 Appendix E altimeter tests, the probe adapter from the pitot-static tester must completely cover the pitot and AOA ports and drain holes on the GAP
26 to avoid overpressuring (and causing damage to) the internal AOA sensor of the GSU 25. If the GAP 26 is installed but AOA is unused (i.e., the AOA port of the
GAP 26 is not connected to the AOA port of the GSU 25) then the GAP 26 AOA port must be connected to the same pressure port as the pitot port during pitotstatic testing.
*Note: If the AOA is unused and connected to the static port (as described in the preceding Caution statement) it can remain connected to the static port for the pitot-static test.
CAUTION
Use of different colored tubing is recommended for static, pitot, and AOA plumbing to avoid plumbing connection errors. Incorrect plumbing connections will result in erroneous air data information calculated by the GSU 25.
Observe the following cautions when connecting pneumatic lines:
1. Make sure the aircraft static pressure port is plumbed directly to the unit static pressure input port and the aircraft pitot pressure port is plumbed directly to the unit pitot pressure input port. The
AOA port must be plumbed directly to the AOA pressure port or, if unused, directly to the aircraft static port.
2. Seal the threads of pneumatic fittings at the connector ports. Use caution to ensure there are no pneumatic leaks.
3. Use care to avoid getting fluids or particles anywhere within the pneumatic lines connected to the
GSU 25.
The installer must fabricate any additional mounting equipment needed. Use outline and installation
for reference.
190-01115-01
Rev. AN
G3X/G3X Touch Installation Manual - GSU 25/25B/25C/25D Installation
Page 19-9
19.5 Outline and Installation Drawings
190-01115-01
Rev. AN
Figure 19-4 GSU 25 Outline Drawing
G3X/G3X Touch Installation Manual - GSU 25/25B/25C/25D Installation
Page 19-10
190-01115-01
Rev. AN
Figure 19-5 GSU 25 Installation Drawing
G3X/G3X Touch Installation Manual - GSU 25/25B/25C/25D Installation
Page 19-11
>
D
AR
>>>
RW
FO
D
>>
>>
AR
RW
FO
>
AR
>>>
D
RW
FO
>
D
AR
>>>
RW
FO
>
AR
>>>
D
RW
FO
>
D
AR
>>>
RW
FO
>
D
AR
>>>
RW
FO
>
D
AR
>>>
RW
FO
190-01115-01
Rev. AN
Figure 19-6 GSU 25 Orientation Drawings (page 1 of 3)
G3X/G3X Touch Installation Manual - GSU 25/25B/25C/25D Installation
Page 19-12
>
AR
>>>
D
RW
FO
>
AR
>>>
D
RW
FO
>
AR
>>>
D
RW
FO
>
AR
>>>
D
RW
FO
>
AR
>>>
D
RW
FO
>
AR
>>>
D
RW
FO
>
AR
>>>
D
RW
FO
>
AR
>>>
D
RW
FO
190-01115-01
Rev. AN
Figure 19-6 GSU 25 Orientation Drawings (page 2 of 3)
G3X/G3X Touch Installation Manual - GSU 25/25B/25C/25D Installation
Page 19-13
>
AR
>>>
D
RW
FO
>
AR
>>>
D
RW
FO
>
AR
>>>
D
RW
FO
>
AR
>>>
D
RW
FO
>
AR
>>>
D
RW
FO
>
AR
>>>
D
RW
FO
>
AR
>>>
D
RW
FO
>
AR
>>>
D
RW
FO
190-01115-01
Rev. AN
Figure 19-6 GSU 25 Orientation Drawings (page 3 of 3)
G3X/G3X Touch Installation Manual - GSU 25/25B/25C/25D Installation
Page 19-14
20 GSU 73 (SENSOR UNIT) INSTALLATION
The GSU 73 can be installed as part of the G3X system. This section contains general information as well as installation information for the GSU 73. Use this section to mount the GSU 73 unit.
20.1 Equipment Description
NOTE
There is no TSO/ETSO applicable to the GSU 73.
The GSU 73 is intended for the experimental aircraft and LSA (light sport aircraft) markets. The Garmin
GSU 73 Sensor Unit is not a TSO-certified product and has received no FAA approval or endorsement.
The GSU 73 is intended to be used as a part of the G3X system and it is not suitable for installation in typecertificated aircraft.
The GSU 73 is an LRU that provides AHRS and Air Data information as well as an interface to Engine/
Airframe sensors in a single mechanical package. The GSU 73 interfaces to a remote mounted GMU 22 for heading information and also computes OAT and TAS from inputs provided by the GTP 59.
NOTE
The GSU 73 is not compatible with the GMU 11 magnetometer. Installations with a
GSU 73 must also include a GMU 22 connected to the GSU 73.
NOTE
In installations using more than one ADAHRS, the GSU 73 will always be designated as
ADAHRS 1 and the GSU 25 units will be designated as ADAHRS 2, ADAHRS 3, etc.
190-01115-01
Rev. AN
Figure 20-1 GSU 73 Unit View
G3X/G3X Touch Installation Manual - GSU 73 Installation
Page 20-1
20.1.1 Features Summary
Air Data
Pressure Altitude
Density Altitude
Vertical Speed
Mach Number
Indicated Airspeed
True Airspeed
Interfaces
CAN (1)
RS-232 (2 TX/2 RX)
ARINC 429 (4 RX/2 TX)
OAT Probe (GTP 59)
Magnetometer (GMU 22) (1 RS-232 TX/ 1 RS-485 RX)
AHRS
Magnetic Heading
Pitch Angle
Roll Angle
Linear Accelerations
Pitch, Roll, Yaw Rotation Rates
Engine/Airframe
27 Analog Inputs
4 Digital Inputs
4 Discrete Inputs
2 Discrete Outputs
20.2 General Specifications
for power/current specifications, and
for dimension/weight specifications.
GSU 73 HARDWARE MOD LEVEL HISTORY
The following table identifies hardware modification (Mod) Levels for the GSU 73 LRU. Mod Levels are listed with the associated service bulletin number, service bulletin date, and the purpose of the modification. The table is current at the time of publication of this manual (see date on front cover) and is subject to change without notice.
MOD
LEVEL
1
2
SERVICE
BULLETIN
NUMBER
N/A
N/A
SERVICE
BULLETIN
DATE
N/A
N/A
PURPOSE OF MODIFICATION
Improved HSCM accuracy when using +28 V supply
Improved backup capacitor circuit to increase backup time in certain under-voltage conditions
190-01115-01
Rev. AN
G3X/G3X Touch Installation Manual - GSU 73 Installation
Page 20-2
20.3 Required Equipment
Table 20-1 lists the kits available for the GSU 73.
Table 20-1 GSU 73 Available Equipment
Item
Configuration Module w/EEPROM and Jackscrew, Kit
Thermocouple Kit
Unit Assembly, GSU 73
P731 Connector Kit, GSU 73
P732 Connector Kit, GSU 73
*Included in G3X w/GSU 73 LRU Kit (K10-00016-00)
**Included in G3X w/GSU 73 Installation Kit (K10-00017-00)
Garmin P/N
011-00979-20**
011-00981-00**
011-01817-00*
011-01818-00**
011-01818-01**
Quantity
1
1
1
1
1
Table 20-2 Contents of P731 Connector Kit (011-01818-00)**
Item
Sub-Assy,Backshell w/Hdw,Jackscrew
Connector ,Hi Dens, D-Sub, Mil Crimp 62ck
Contact Pin, Mil Crimp, Size 22D
**Included in G3X w/GSU 73 Installation Kit (K10-00017-00)
Garmin P/N
011-01855-03
330-00185-62
336-00021-00
Quantity
1
1
20
Table 20-3 Contents of P732 Connector Kit (011-01818-01)**
Item
Sub-Assy,Backshell w/Hdw,Jackscrew
Garmin P/N
011-01855-04
Connector ,Hi Dens, D-Sub, Mil Crimp 78ck
Contact Pin, Mil Crimp, Size 22D
**Included in G3X w/GSU 73 Installation Kit (K10-00017-00)
330-00185-78
336-00021-00
Quantity
1
1
30
20.3.1 GSU 73 Configuration Module
The GSU 73 configuration module stores a duplicate copy of the AHRS/Magnetometer calibration values which are recorded upon completion of post-installation calibration procedures. The GSU configuration module also provides a reference temperature measurement which is used for calculating thermocouple
temperatures. All thermocouple temperature readouts will be Red-x’d ( Section 36
) if the GSU configuration module is not present.
190-01115-01
Rev. AN
G3X/G3X Touch Installation Manual - GSU 73 Installation
Page 20-3
20.3.2 Additional Equipment Required
• Cables: The installer will fabricate and supply all system cables.
• An example of mounting hardware is: #10-32 pan or hex head screw (4 ea.) and #10-32 selflocking nut (4 ea)
• Air hoses and fittings to connect pitot and static air to the GSU 73. The GSU 73 has a female
1/8 27 ANPT fitting for each pitot and static port. Use appropriate aircraft fittings to connect to pitot and static system lines.
20.4 Unit Installation
Fabrication of a wiring harness is required. Sound mechanical and electrical methods and practices should
be used for installation of the GSU 73. Refer to Section 2.3
for wiring considerations, and to Section 26.15
for pinouts.
Connector kits include backshell assemblies. The backshell assembly houses the configuration module
(P732 only) and a thermocouple reference junction (if applicable). Garmin’s backshell connectors give the installer the ability to quickly and easily terminate shield grounds at the backshell housing. The instructions needed to install the Jackscrew Backshell, Configuration Module, and Thermocouple are located in
190-01115-01
Rev. AN
G3X/G3X Touch Installation Manual - GSU 73 Installation
Page 20-4
20.4.1 Pneumatic Plumbing
The GSU 73 has two ports that are connected to the aircraft’s pitot pressure source and static pressure
threads. The mating fitting must have 1/8-27 ANPT male threads.
Figure 20-2 GSU 73 Air Hose Fitting Locations
Use appropriate air hoses and fittings to connect the pitot and static lines to the unit. Avoid sharp bends and routing near aircraft control cables. The GSU 73 should not be at the low point of the pitot or static plumbing lines, to avoid moisture or debris collecting at or near the unit. Ensure that no deformations of the airframe surface have been made that would affect the relationship between static air pressure and true ambient static air pressure for any flight condition. Refer to part 43, Appendix E for approved practices while installing hoses and connections.
20.4.2 Pneumatic Connections
The following steps should be used to aid in the fabrication of pneumatic hose connections and in attaching the aircraft pitot pressure source and aircraft static pressure source to the GSU 73.
NOTE
Check pneumatic connections for errors before operating the GSU 73. Incorrect plumbing could cause internal component damage. Observe the following cautions when connecting pneumatic lines.
1. Make sure the aircraft static pressure port is plumbed directly to the unit static pressure input port and the aircraft pitot pressure port is plumbed directly to the unit pitot pressure input port.
2. Seal the threads of pneumatic fittings at the connector ports. Use caution to ensure there are no pneumatic leaks.
3. Use care to avoid getting fluids or particles anywhere within the pitot and static lines connected to the GSU 73.
The installer must fabricate any additional mounting equipment needed. Use outline and installation
for reference.
190-01115-01
Rev. AN
G3X/G3X Touch Installation Manual - GSU 73 Installation
Page 20-5
20.4.3 Mounting Requirements
Mount the GSU 73 with the connectors aligned within 1.0 deg of either the longitudinal or lateral axis of the aircraft. The direction of the unit will be accounted for during the calibration procedure as shown in
Figure 20-3 AHRS Orientation Selection
The GSU 73 includes an extremely sensitive strap-down inertial measurement unit. It must be mounted rigidly to the aircraft primary structure, preferably to a metallic structure to conduct heat away from the unit. Do not mount the GSU 73 in an enclosed area, it should be mounted in a location that provides
adequate airflow to comply with the maximum outer case temperature listed in Appendix D.12.1
Do not use shock mounting to mount the GSU 73. Shock mounts used for other types of inertial systems are not acceptable for the GSU 73 AHRS. The mounting system must have no resonance with the unit installed. Excessive vibration may result in degraded accuracy.
The supporting plate must be rigidly connected to the aircraft primary structure through strong structural members capable of supporting substantial loads. Avoid areas that are prone to severe vibration.
The GSU 73 should be mounted within 13 feet (4.0 meters) longitudinally and 6.5 feet (2.0 meters) laterally of the aircraft center of gravity. In cases where the longitudinal distance from the CG is planned to be greater than 6.5 feet (2.0 meters), it is preferable to mount the GSU 73 forward of the aircraft center of gravity if possible, to enable better acceleration outputs for autopilot use. The mounting location for the
GSU 73 should be protected from rapid thermal transients, in particular, large heat loads from nearby highpower equipment.
The GSU 73 must be leveled to within 3.0° of the in-flight level cruise altitude and an aircraft leveling and offset calibration procedure carried out prior to flight. (This procedure is described in
GDU 37X systems and
Avoid placing the GSU 73 within 1 inch of magnetically mounted antennas, speaker magnets, or other strongly magnetic items.
20.4.4 Unit Mounting
For final installation and assembly, refer to the outline and installation drawing Figure 20-4
of this manual.
1. Assemble the wiring harness and backshell connectors.
2. Assemble the pneumatic hoses and connectors.
3. Mount the unit to a suitable mounting location using (4 ea) #10-32 pan or hex head screws
(example) per the requirements in
.
4. Connect backshell connector and hoses.
NOTE
When mounting the GSU 73 to the airframe, it is important to ensure that fastening hardware is tight for proper unit operation.
190-01115-01
Rev. AN
G3X/G3X Touch Installation Manual - GSU 73 Installation
Page 20-6
20.5 Outline and Installation Drawings
190-01115-01
Rev. AN
Figure 20-4 GSU 73 Outline Drawing
G3X/G3X Touch Installation Manual - GSU 73 Installation
Page 20-7
190-01115-01
Rev. AN
Figure 20-5 GSU 73 Orientation Drawings
G3X/G3X Touch Installation Manual - GSU 73 Installation
Page 20-8
21 GTP 59 (TEMPERATURE PROBE) INSTALLATION
This section contains general information as well as installation information for the GTP 59. Use this section to mount the GTP 59.
NOTE
For installations using more than one ADAHRS, ADAHRS 1 must be connected to a
GTP 59, but installing additional GTP 59’s for other GSU 25 ADAHRS units is optional.
An ADAHRS not connected to a GTP 59 will use temperature data supplied by other
ADAHRS as long as both ADAHRS are communicating via the CAN bus.
Figure 21-1. GTP 59
21.1 Equipment Description
The Garmin GTP 59 is an outside mounted temperature probe that provides raw air temperature data. The temperature input device is a three-wire temperature probe interface. OAT Power Out and OAT High are connected internally at the OAT probe.
The GTP 59 is available per the following part number.
Table 21-1 GTP 59 Part Number
Item
GTP 59 OAT Probe Kit
*Included in G3X w/GSU 73 LRU (K10-00016-00)
Garmin Part Number
011-00978-00*
190-01115-01
Rev. AN
G3X/G3X Touch Installation Manual - GTP 59 Installation
Page 21-1
Table 21-2 contains a list of items found in the GTP 59 Outside Air Temperature (OAT) Probe kit
(011-00978-00). The GTP 59 probe has an attached pigtail.
Table 21-2 GTP 59 Outside Air Temperature Kit*
Item
Nut, 5/16”, Hex, Skirt
Screw, 4-40 x .250, PHP, SS/P, w/NYL
Garmin Part Number
210-00055-00
211-60234-08
Washer, Lock, Self-Sealing, 5/16
Contact, Pin, Mil Crimp, Size 22D
GTP 59 OAT Probe
*Included in G3X w/GSU 73 LRU Kit (K10-00016-00)
212-00026-00
336-00021-00
494-00022-XX
Quantity
1
2
1
5
1
21.1.1 Additional Equipment Required
• Cables - The installer will supply all system cables.
21.2 General Specifications
See
Section 21-2 for mounting dimensions.
21.3 Unit Installation
NOTE
The following instructions are general guidance.
NOTE
The GTP 59 is a Resistive Temperature Device (RTD) that detects changing temperature by monitoring small changes in resistance. For optimum accuracy, take care to avoid introducing extra resistance, such as loose, dirty, or corroded connections in the wiring path between the ADAHRS and GTP 59.
Consider the following recommendations when determining the mounting location for the GTP 59:
• Do not mount the GTP 59 where aircraft exhaust gases will flow over it.
• Do not mount the GTP 59 where it would be affected by heated air from the engine or exhaust. On most aircraft this includes any location downstream of the engine compartment.
• The GTP 59 must be exposed to the outside airflow. Do not mount the GTP 59 in a sheltered location where it is not exposed to outside airflow (for example, inside a wing or landing gear bay).
• For best results, do not mount the GTP 59 where it will be directly heated by the sun when the aircraft is parked.
190-01115-01
Rev. AN
G3X/G3X Touch Installation Manual - GTP 59 Installation
Page 21-2
Table 21-3 contains a list of parts needed for the GTP 59 installation and interconnect harness. Refer to
GTP 59 O.A.T. Probe Installation Drawing for wiring and mounting instructions.
Table 21-3 Parts Needed for GTP 59 Installation
Description
Nut
Screw
Washer
Qty. Included
1
2
1
GPN
210-00055-00
211-60234-08
212-00026-00
5 336-00021-00 Contact, Pin, Mil Crimp, Size 22D
Ring Terminal
3-Conductor Cable
OAT Sensor
1 494-00022-XX
1. Prepare the surface. The metal body of the OAT probe should be grounded to the aircraft. The installation requirements vary depending on the airframe material composition.
a) Aluminum airframe: When a mounting location has been found, prepare the inside surface of the aircraft. Remove all paint from the contacting area and clean with a degreaser.
b) Composite airframe: If possible, mount the OAT probe through a grounded metal strap or band. Otherwise, mount the OAT probe in an area of the airframe that has a significant amount of underlying metal foil or mesh. To ensure adequate conductivity, it may be necessary to mount the OAT probe through a metal doubler. Use fasteners that allow a conductive path to the airframe.
2. Mount the OAT probe on the prepared surface. Place the ring terminal (1) over the end of the OAT probe (3). Insert the probe and ring terminal into the hole in the skin of the aircraft. Place the washer (5) over the end of the OAT probe on the outside skin of the aircraft. Thread the nut (4) onto the OAT probe. Holding the OAT probe on the inside, tighten the nut (4) to 100 inch-lbs. 20 inch-lbs.
3. Route the OAT probe cable (2) to the GSU 25/GSU 73.
4. Cut the OAT Probe cable (2) to the required length. Strip back 2.0” to 3.5” of jacket while retaining the shield on the OAT Probe cable (2). Trim away enough to leave 0.5” of shield exposed.
5. Strip back 1/8” (0.125”) of insulation and crimp pins to each of the conductors in the shielded cable.
6. Cut an AWG #16 wire to 3” long. Strip back 0.5” of insulation from this cable. Connect the shield of the OAT Probe cable (2) to the AWG #16 wire.
7. Attach the ring terminal to the backshell, using the screw provided in the OAT Probe Kit and one of the tapped holes on the backshell termination area.
8. Insert newly crimped pins into the D-Sub connector and wires into the appropriate connector housing location as specified by the installation wiring diagrams.
9. Verify that all necessary pins for the GSU 25/GSU 73 have been attached to the cables and snapped into the proper slots of the 78 pin D-Sub connector.
10. Wrap the cable bundle with Silicone Fusion Tape (GPN: 249 00114 00 or similar) at the point where the backshell strain relief and cast housing contact the cable bundle. The smooth side of the backshell strain relief should contact the tape.
190-01115-01
Rev. AN
G3X/G3X Touch Installation Manual - GTP 59 Installation
Page 21-3
21.4 GTP 59 Icing
The GTP 59 OAT probe has no icing protection. If ice accumulates on the GTP 59 OAT probe, its accuracy is unknown. Consequently, air temperature measurements may be incorrect if ice accumulates on the probe. Furthermore, computations dependent upon air temperature measurements may be affected (e.g. true airspeed and delta-ISA).
190-01115-01
Rev. AN
G3X/G3X Touch Installation Manual - GTP 59 Installation
Page 21-4
21.5 Outline and Installation Drawings
190-01115-01
Rev. AN
Figure 21-2. GTP 59 O.A. T. Probe Installation Drawing
G3X/G3X Touch Installation Manual - GTP 59 Installation
Page 21-5
22 GTR 20 (VHF COMMUNICATIONS RADIO) INSTALLATION
This section contains general information as well as installation information for the GTR 20. Use this section to mount the GTR 20 unit. Careful planning and consideration of the suggestions in this section are required to achieve the desired performance and reliability from the GTR 20. The guidance of FAA advisory circulars AC 43.13-1B and AC 43.13-2B, where applicable, may be found useful for making retro-fit installations that comply with FAA regulations.
NOTE
A GTR 20 cannot be installed in a system that also includes a GDU 37X. The GTR 20 will only work with the G3X system that uses the new GDU 4XX displays. The GTR 20 is not supported with G3X installations using GDU 37X displays.
Figure 22-1 GTR 20 Unit View (shown with mounting brackets on ends)
22.1 Equipment Description
The GTR 20 is a transceiver that operates in the 118.000 to 136.975 MHz frequency range. The receiver sensitivity SINAD is greater than 6dB when the RF level is -107 dBm with 30% modulation. The transmitter power is 10 W carrier minimum.
Table 22-1 Available Units
Model
GTR 20
GTR 20
Part Number
011-03007-00
011-03007-10
TX Power (Watt) 8.33 KHz Spacing
10 N/A
10 N/A
25 KHz Spacing
Yes
Yes
190-01115-01
Rev. AN
G3X/G3X Touch Installation Manual - GTR 20 Installation
Page 22-1
CAUTION
The use of ground-based cellular telephones while aircraft are airborne is prohibited by
FCC rules. Due to potential interference with onboard systems, the use of ground-based cell phones while the aircraft is on the ground is subject to FAA regulation 14 CFR §91.21.
FCC regulation 47 CFR §22.925 prohibits airborne operation of ground-based cellular telephones installed in or carried aboard aircraft. Ground-based cellular telephones must not be operated while aircraft are off the ground. When any aircraft leaves the ground, all ground-based cellular telephones on board that aircraft must be turned off. Ground-based cell phones that are on, even in a monitoring state, can disrupt GPS/SBAS performance.
22.1.1 Status LED
The GTR 20 has an LED located in the hole to the right of the D-sub connector (J2001) that indicates its current status. See
for details.
22.2 Equipment Available
22.2.1 Unit Configurations
Model
Table 22-2 GTR 20 Part Numbers
Assembly Part
Number
010-01076-00 GTR 20 unit only
GTR 20 Standard (includes
GTR 20 (New) unit only
GTR 20 (New) Standard
(includes items in Table 22-3)*
*Includes 011-03241-00 connector kit
010-01076-01
010-01076-10
010-01076-11
Unit Only Part
Number
011-03007-00
011-03007-00
011-03007-10
011-03007-10
22.2.2 Additional Equipment Required
(010-01076-00, 010-01076-10).
Table 22-3 Contents of GTR 20 Connector Kit (011-03241-00)
Item
Backshell w/Hdw, Jackscrew,37 Pin
Screw, 8-32 x .312, PHP, SS/P
Washer, Split Lock, Size 8
Washer, Flat, Non-Std, SS, ID .195, OD .354
Conn, Rcpt, D-Sub, Crimp Socket, Commercial, 37 CKT
Contact, Socket, Military Crimp, Size 20
Garmin P/N
011-01855-03
211-60209-09
212-00018-04
212-20065-00
330-00625-37
336-00022-02
Quantity
1
5
5
5
1
37
190-01115-01
Rev. AN
G3X/G3X Touch Installation Manual - GTR 20 Installation
Page 22-2
22.3 General Specifications
See
for power/current specifications, and Table 2-4 for dimension/weight specifications.
22.3.1 COM Specifications
The GTR 20 transmitter meets the requirements of RTCA DO-186B section 2.3 for a class 4 transmitter.
Characteristic
Microphone Input
Modulation Capability
Modulation
Frequency Range
Frequency Tolerance
Output Power
Duty Cycle
Carrier Noise Level
Stuck Mic Time-Out
Demodulated Audio Distortion
Table 22-4 Transmitter Specifications
Specification
Two inputs, standard carbon or dynamic mic with integrated preamp.
The GTR 20 provides a 150 Ω AC input impedance and supplies the microphone with an 11 V bias through 470 Ω +/- 5%.
85% with 150 to 1500 mVRMS microphone input at 1000 Hz. Range can be extended from 20 mVrms to 2500 mVrms with mic gain adjustment.
AM Double sided Emission Designator: 6K00A3E (118 - 136.975 MHz)
118.000 to 136.975 MHz, 25 kHz channel spacing
+/-5 ppm from -20°C to +55°C
10 Watts carrier minimum
20%
At least 35 dB (SNR)
35 seconds time-out, reverts to receive
Less than 25% distortion when the transmitter is at 85% modulation at
350 to 2500 Hz
The GTR 20 receiver meets the requirements of RTCA DO-186B section 2.2 for a class C receiver.
Table 22-5 Receiver Specifications
Characteristic
Frequency Range
Specification
118.000 to 136.975 MHz, 25 kHz channel spacing
Headset Audio Output 60 mW minimum into a 150 Ω load
Audio Response
Audio Distortion
Sensitivity
Squelch
Less than 6 dB of variation between 350 and 2500 Hz
Less than 25% at rated output power
SINAD greater than 6 dB when the RF level is -107 dBm with 30% modulation
Automatic squelch with manual override
190-01115-01
Rev. AN
G3X/G3X Touch Installation Manual - GTR 20 Installation
Page 22-3
22.4 Installation Considerations
22.4.1 COM Antenna
A COM Antenna that meets TSO-C37( ) and C38( ) or TSO-C169( ), 50W, vertically polarized with coaxial cable is recommended but not provided.
CAUTION
To avoid damage to the GTR 20, take precautions to avoid transmitting when no antenna is connected.
22.4.2 Installation Materials
The GTR 20 is intended for use with the standard aviation accessories. The following items are recommended for installation, but not supplied:
• Wire (MIL-W-22759/16 or equivalent)
• Shielded Wire (MIL-C-27500 or equivalent)
• Mounting Hardware - #10 hardware recommended
• Push/Pull (that can be manually reset) Circuit Breaker
• Tie Wraps or Lacing Cord
• Ring Terminals (for grounding)
• Coaxial Cable (RG-400, RG-142B or coaxial cable with 50 Ω impedance meeting applicable aviation regulations should be used.
22.4.3 Cabling and Wiring
Refer to the interconnect examples in
Section 29 for wire gauge guidance.
Use wire and cable meeting the applicable aviation regulation. When routing wire and cable, observe the following precautions:
• Keep as short and as direct as possible
• Avoid sharp bends
• Avoid routing near power sources (e.g. 400 Hz generators, trim motors, etc.) or near power for fluorescent lighting
• Do not route cable near high voltage sources
CAUTION
To avoid damage to the GTR 20, take precautions to prevent Electro-Static Discharge
(ESD) when handling the GTR 20, connectors, and associated wiring. ESD damage can be prevented by touching an object that is of the same electrical potential as the GTR 20 before handling the GTR 20 itself.
NOTE
The GTR 20 connects to the G3X system using the CAN bus. If communication is lost or no
GDU displays are present, the GTR 20 will automatically tune the emergency frequency
(121.500 MHz) and set the COM radio volume to a pre-determined level. See Section
for information on configuring the emergency volume level.
190-01115-01
Rev. AN
G3X/G3X Touch Installation Manual - GTR 20 Installation
Page 22-4
22.5 Antenna Considerations
This section contains mounting location considerations for the antennas required for the GTR 20. For mounting the COM antenna, refer to the aircraft manufacturer’s data.
22.5.1 COM Antenna Location
The GTR 20 COM antenna should be well removed from all projections, engines and propellers. The ground plane surface directly below the antenna should be a flat plane over as large an area as possible (18 inch square, minimum). The antenna should be mounted a minimum of six feet from any DME or other
COM antennas, and four feet from any ADF sense antennas. The COM antenna should also be mounted as far as practical from the ELT antenna. Some ELTs have exhibited re-radiation problems that cause interference with other radios, including GPS. This can happen when the COM (GTR 20 or any other
COM) is transmitting on certain frequencies such as 121.15 or 121.175 MHz, which may cause the ELT output circuit to oscillate from the signal coming in on the ELT antenna coax.
If simultaneous use of two COM transceivers is desired (split-COM or simul-comm), the COM antennas should be spaced for maximum isolation. A configuration of one topside antenna and one bottom side antenna is recommended. The GTR 20 requires a transmit interlock.
Simultaneous COM performance varies significantly across installations and is affected by both the isolation between the COM antennas and the separation of the tuned frequencies. Each installation should be individually examined to determine the expected performance of simultaneous COM.
CAUTION
Garmin recommends the COM antenna be mounted a minimum of six feet from any other
COM antennas. For aircraft which cannot comply with the recommended separation,
COM antenna spacing should never be less than three feet to reduce the chance of damage to the COM receiver. All dual COM installations must use the GTR 20 interlock. An example of direct line of sight is both antennas mounted on the bottom or top surface of the aircraft. For metallic aircraft, it is recommended that one antenna is mounted on the bottom close to the front and the other on the top of the aircraft close to the tail such that the aircraft structure is between the two antennas. For composite aircraft, additional shielding may be needed between top and bottom mounted COM antennas.
NOTE
Canadian installations are required to meet Industry Canada specifications for maximum radiation as documented in Radio Specifications Standard 102 (RSS-102). For more information about RF exposure and related Canadian regulatory compliance, contact:
Manager, Radio Equipment Standards
Industry Canada
365 Laurier Avenue
Ottawa, Ontario
K1A 0C8
In accordance with Canadian Radio Specifications Standard 102 (RSS 102), an RF safety separation distance of 26 cm from the antenna should be maintained for an RF field strength exposure to persons of less than the 10W/m 2 occupational safety limit.
Under Industry Canada regulations, this radio transmitter may only operate using an antenna of a type and maximum (or lesser) gain approved for the transmitter by Industry
190-01115-01
Rev. AN
G3X/G3X Touch Installation Manual - GTR 20 Installation
Page 22-5
Canada. To reduce potential radio interference to other users, the antenna type and its gain should be so chosen that the equivalent isotropically radiated power (e.i.r.p.) is not more than that necessary for successful communication.
The GTR 20 has been approved by Industry Canada to operate with the antenna types listed below. Antenna types not included in this list, having a gain greater than the maximum gain indicated for that type, are strictly prohibited for use with this device.
A COM Antenna that meets TSO-C37( ) and C38( ) or TSO-C169( ), 50W, vertically polarized. Maximum gain of 1 dBi with an impedance of 50 Ω.
22.5.2 Interference of GPS
On some installations, VHF COM transceivers, Emergency Locator Transmitter (ELT) antennas, and
Direction Finder (DF) receiver antennas can re-radiate to the GPS antenna. Placement of the GPS antenna relative to a COM transceiver and COM antenna (including the GTR/ COM antenna), ELT antenna, and
DF receiver antenna is critical.
Use the following guidelines, in addition to others in this document, when locating the GTR 20 and its antenna.
• Locate the GTR 20 as far as possible from all GPS antennas.
• Locate the COM antenna as far as possible from all GPS antennas.
If a COM is found to be radiating, the following can be done:
• Replace or clean VHF COM rack connector to ensure good coax ground.
• Place a grounding brace between the GTR 20 and ground.
• Shield the GTR 20 wiring harness.
190-01115-01
Rev. AN
G3X/G3X Touch Installation Manual - GTR 20 Installation
Page 22-6
22.6 Mounting Considerations
The GTR 20 is designed to mount remotely.
22.6.1 Bracket Installation
The GTR 20 is shipped with the brackets positioned on the ends of the unit. The brackets can be removed from the bottom of the GTR 20 and repositioned by the installer. The GTR 20 mounting brackets can be positioned on the sides or the ends of the GTR 20. The installer determines the orientation and position of the brackets that best suits the installation. See
and Figure 22-3 for bracket positions.
22.6.2 Unit Mounting
Secure the GTR 20 to the airframe in a suitable mounting location using a minimum of four #10 fasteners
(not provided). Hardware is intended to be located in the 4 outermost mounting locations. The center locations in each bracket are additional locations provided for the installer’s convenience.
Do not mount the GTR 20 on the “hot” side (engine side) of the firewall. To reduce interference, route the
GTR 20 wiring harness separately from any COM radio or transponder antenna coax.
No cooling air is required for the GTR 20/200, however, as with all electronic equipment, lower operating temperatures extends equipment life. Reducing the operating temperature by 15° to 20°C (27° to 36°F) reduces the mean time between failures (MTBF).
For final installation and assembly, see Figure 22-2 ,
22.6.3 Antenna Installation and Connections
The GTR 20 requires a standard 50 vertically polarized antenna. Follow the antenna manufacturer’s installation instructions for mounting the antenna.
The antenna should be mounted on a metal surface or a ground plane with a minimum area of 18 inches x
18 inches. Refer to
for installation location considerations.
22.6.4 Antenna Coaxial Cable Installation
The antenna coax cable should be made of RG-142B, RG-400 or a comparable quality 50 coax. See
or follow the BNC connector manufacturer’s instructions for cable preparation/connector installation.
Check that there is ample space for the cabling and mating connectors. Avoid sharp bends in the antenna cable, and routing near aircraft control cables. Route the COM antenna cable as far as possible away from any GPS antenna cables.
Check for insertion loss and Voltage Standing Wave Ratio (VSWR). VSWR should be checked with an inline type VSWR/wattmeter inserted in the coaxial transmission line between the transceiver and the antenna. The VSWR meter should be inserted as close to the transceiver as possible. When rack and harness buildup is performed in the shop, the coax termination may be provisioned by using a 6-inch inline BNC connection. This would be an acceptable place to insert the VSWR meter. Any problem with the antenna installation is most likely seen as high reflected power. A VSWR of 3:1 may result in up to a 50% loss in transmit power. VSWR at the low, mid and high end of the tuning range should be less than 3:1, for best performance VSWR should be less than 2:1. A high VSWR decreases the amount of power radiated by the antenna and increases power supply current and heat dissipated by the radio when the radio is transmitting.
190-01115-01
Rev. AN
G3X/G3X Touch Installation Manual - GTR 20 Installation
Page 22-7
22.7 Mounting, Wiring, and Power Checks
Fabrication of a wiring harness is required. Sound mechanical and electrical methods and practices are
recommended for installation of the GTR 20. Refer to Section 2.3
for wiring considerations, and to Section
for pinouts.
Verify that all cables are properly secured and shields are connected to the shield block of the connectors.
Check the movement of the flight and engine controls to verify there is no interference between the cabling and control systems. Ensure that all wiring is installed as described in
Prior to powering up the unit, the wiring harness must be checked for proper connections to the aircraft systems and other avionics equipment. Point to point continuity must be checked to expose any faults such as shorting to ground. Any faults or discrepancies must be corrected before proceeding.
After accomplishing a continuity check, perform power and ground checks to verify proper power distribution to the GTR 20. Any faults or discrepancies should be corrected at this time. Remove power from the aircraft upon completion of the harness checkout.
The GTR 20 can be installed after completion of the continuity and power checks. The GTR 20 should be secured appropriately, as described in
. The GTR 20 must be connected to the wiring harness
and antenna.
22.7.1 Unit Ground Checks (Normal Mode)
22.7.1.1 TX Interlock Checkout
Connect pins 4 and 5 per Section 29
.
Table 22-6 TX Interlock Connections
Pin Pin Name
4 TX INTERLOCK OUT
5 TX INTERLOCK IN
Description
Active low output that indicates the GTR 20 is transmitting.
This output is normally connected to the TX INTERLOCK IN of other COM radios installed in the aircraft.
Active Low Input that ‘desenses’ (protects) the GTR 20 receiver when another communications radio is transmitting. This input comes from another communication radio's interlock output or MIC KEY line.
22.7.1.2 Antenna Check
If desired, the antenna VSWR can be checked using an inline wattmeter in the antenna coaxial using frequencies near both ends of the band. The VSWR should be less than 2:1. A VSWR of 2:1 will cause a drop in output power of approximately 12%.
22.7.1.3 Receiver/Transmitter Check
Tune the unit to a local VHF frequency and verify the receiver output produces a clear and understandable audio output. Verify the transmitter functions properly by contacting another station and getting a report of reliable communications.
190-01115-01
Rev. AN
G3X/G3X Touch Installation Manual - GTR 20 Installation
Page 22-8
22.7.2 Flight Checks
22.7.2.1 COM Flight Check
After the installation is complete, perform the following required flight checks to ensure satisfactory transceiver performance.
Check the communications transceiver at a range of at least 50 nautical miles: (This check verifies unit receiver sensitivity test and transmitter range)
1. Maintain an altitude of 5000 ft AGL.
2. Select the frequency of a ground station facility at a range of at least 50 nautical miles.
3. Verify that communication (RX and TX) can be established with that facility.
Check the communications receiver by receiving transmission from a ground station in close proximity
(range of less than 10 nautical miles): (This check verifies that the receiver has a high signal to noise ratio when receiving a strong signal.)
1. Select the frequency of a ground station facility at a range of less than 10 nautical miles.
2. Make sure the received audio from that station is clear (no background electrical noise).
3. If possible, perform the preceding steps 1 and 2 for frequencies in the high (~136.XXX MHz), mid
(~127.XXX MHz), and low (~118.XXX MHz) range of the GTR 20.
22.7.3 Noise
As audio signals are routed to and from the GTR 20 (Headset, Microphone, Music, AUX), care must be taken to minimize effects from coupled interference and ground loops.
Interference can be coupled into interconnecting cables when they are routed near large AC electric fields,
AC voltage sources, and pulse equipment (strobes, spark plugs, magnetos, EL displays, CRTs, etc).
Interference can also couple into interconnecting cables by magnetic induction when they are routed near large AC current-carrying conductors or switched DC equipment (heaters, solenoids, fans, autopilot servos, etc).
Ground loops are created when there is more than one path in which return currents can flow, or when signal returns share the same path as large currents from other equipment. These large currents create differences in ground potential between various equipment operating in the aircraft. These differences in potential can produce an additive effect at audio signal inputs.
The GTR 20 audio inputs may detect the desired input signal plus an unwanted component injected by ground differentials, a common cause of alternator-related noise. This can be minimized by isolating all audio jacks from ground.
Terminating shields at just one end (single-point grounding) eliminates another potential ground loop injection point. The single-point grounding method is critical for the installation of various avionics that produce and process audio signals. Single-point, in this context, means that the various pieces of equipment share a single common ground connection back to the airframe.
Good aircraft electrical/charging system ground bonding is important.
The wiring diagrams and accompanying notes in this manual should be followed closely to minimize noise effects.
190-01115-01
Rev. AN
G3X/G3X Touch Installation Manual - GTR 20 Installation
Page 22-9
22.8 Outline and Installation Drawings
Figure 22-2 GTR 20 Outline Drawing (Mounting Brackets on Ends)
190-01115-01
Rev. AN
G3X/G3X Touch Installation Manual - GTR 20 Installation
Page 22-10
Figure 22-3 GTR 20 Outline Drawing (Mounting Brackets on Sides)
190-01115-01
Rev. AN
G3X/G3X Touch Installation Manual - GTR 20 Installation
Page 22-11
190-01115-01
Rev. AN
Figure 22-4 GTR 20 Installation Drawing
G3X/G3X Touch Installation Manual - GTR 20 Installation
Page 22-12
23 GPS/XM ANTENNA INSTALLATION
This section contains general information as well as installation information for GPS, GPS/WAAS, and
XM antennas. Use this section to mount the antenna(s).
In an installation with multiple GDU 37X/4XX units, each GDU can be configured to use its own internal
GPS receiver, or to receive GPS data transmitted by another GDU. A minimum of one GPS antenna is required for installations using more than one GDU 37X/4XX unit, as the GDU will “share” the GPS information with all GDU units. Additional GPS antennas may be used for redundancy, but are not required. See
(for GDU 37X systems) or
(for GDU 4XX systems) for further information.
NOTE
The GPS 20A can only be used with GA 35, GA 36, or GA 37 antennas.
NOTE
GA 35, GA 36 and GA 37 antennas cannot be used with GDU 37X/4XX units.
NOTE
When a GPS 20A (and connected GPS/WAAS antenna) is installed, it can be used as the sole GPS for the system, however it is recommended to install a GPS antenna on at least one of the GDU 37X/4XX units for redundancy.
23.1 Non-Garmin Materials Required
BNC/TNC Coaxial Connectors May be required to terminate the antenna cable, depending upon which antenna is used. Check the antenna installation instructions for detailed information. Example below:
• Connector, BNC/TNC Coaxial, male, crimp (MIL-PRF-39012)
Coaxial Cable, 50Ω - MIL-DTL-17 (i.e. RG-400)
23.2 Non-Garmin Antennas
Table 23-1 lists non-Garmin antennas currently supported by the GDU 37X/4XX. For non-Garmin
antennas, follow the manufacturer’s installation instructions. It is the installer’s responsibility to ensure that their choice of antenna meets FAA standards according to the specific installation.
NOTE
The GPS antenna should provide a gain of 16 to 25 dB. The GDU 37X/4XX supplies power to the antenna at 4.5 V–5V with a maximum current of 50 mA.
190-01115-01
Rev. AN
G3X/G3X Touch Installation Manual - GPS/XM Antenna Installation
Page 23-1
Table 23-1 Supported Non-Garmin Antennas
Model
Comant
2480-201
VHF/GPS*
Comant
420-10 XM only Antenna
Mount Style
Screw Mount,
Teardrop
Footprint
Screw Mount,
ARINC 743
Footprint
Conn
Type
BNC
TNC
TNC
Antenna
Type
VHF
COM,
GPS
XM
Mfr
Comant
Comant
Antenna Part
Number
CI 2480-201
CI 420-10
Garmin Order
*The GPS antenna connector is TNC type. The VHF COM antenna connector is BNC type.
Number
N/A
N/A
23.3 Garmin Antennas
If using a Garmin GA 26C or GA 26XM, refer to the accompanying installation instructions
(190-00082-00 or 190-00522-03). For GA 35, GA 55/55A, or GA 56 or GA 57X antennas, refer to this
section and the outline and installation drawings in Section 23.8
.
Garmin recommends the antennas shown in Table 23-2. However, any equivalent GPS, GPS/WAAS, or
Table 23-2 Supported Garmin Antennas
Model
GA 26C
Part Number
011-00149-04
Description
GPS Antenna
Weight
NA
Mounting Configuration
Flange, Magnetic, or Suction Cup
Mount (for in-cabin mounting)
GA 35*
(used with
GPS 20A only)
GA 36*
(used with
GPS 20A only)
013-00235-00
013-00244-00
GPS/WAAS
Antenna
GPS/WAAS
Antenna
0.47 lbs
(0.21 kg)
0.47 lbs
(0.21 kg)
Thru-mount (Tear-drop form factor)
Thru-mount (ARINC 743 style mount)
GA 37*
(used with
GPS 20A only)
013-00245-00
GPS/WAAS
+ SiriusXM
Antenna
0.50 lbs
(0.23 kg)
Thru-mount (ARINC 743 style mount)
GA 55
GA 55A
GA 56
011-01033-00
011-01153-00
011-00134-00
XM Antenna
XM Antenna
GPS Antenna
0.25 lbs
(0.11 kg)
0.43 lbs
(0.20 kg)
0.24 lbs
(0.11 kg)
Stud mount (Tear-drop form factor)
Thru-mount (ARINC 743 style mount)
Stud mount (Tear-drop form factor)
GA 57X 011-01032-10
GPS/XM
Antenna
0.47 lbs
(0.21 kg)
Thru-mount (ARINC 743 style mount)
*For use with GPS 20A only, cannot be used with GDU 37X/4XX units
190-01115-01
Rev. AN
G3X/G3X Touch Installation Manual - GPS/XM Antenna Installation
Page 23-2
Table 23-3 GPS or GPS/WAAS Antenna Minimum Requirements
Characteristics
Frequency Range
Gain
Noise Figure
Nominal Output Impedance
Supply Voltage
Supply Current
Output Connector
Specifications
1565 to 1585 MHz
16 to 25 dB typical, 40 dB max.
<4.00 dB
50 Ω
4.5 to 5.5 VDC up to 50 mA
BNC or TNC
Table 23-4 XM Satellite Radio Antenna Minimum Requirements
Frequency Range
Gain (Typical)
Noise Figure
Characteristics Specifications
2332.5 to 2345 MHz
24 dB*
<1.2 dB
Nominal Output Impedance
Supply Voltage
Supply Current (maximum)
Operating Temperature Gain
50 Ω
3.6 to 5.5 VDC
55 mA
-50 to +85° C
*For each 1 dB gain over 24 dB, add 1 dB of attenuation into the antenna cable path between the antenna and the GDU.
It is the installer’s responsibility to ensure that their choice of antenna meets FAA standards according to
the specific installation. This installation manual discusses only the antennas listed in Table 23-2
. Other antennas may be acceptable but their installation is not covered by this manual.
There are several critical factors to take into consideration before installing an antenna for a satellite communications system. These factors are addressed in the following sections.
190-01115-01
Rev. AN
G3X/G3X Touch Installation Manual - GPS/XM Antenna Installation
Page 23-3
23.4 Antenna Mounting Considerations
The information in this section does not pertain to in-cabin (internal) mounted antennas such as the
GA 26C, refer to the accompanying installation instructions (190-00082-00).
No special precautions need be taken to provide an electrical bonding path between the GPS Antenna and the aircraft structure.
23.4.1 VHF COM/GPS Interference
On some installation VHF COM transceivers, Emergency Locator Transmitter (ELT) antennas, and
Direction Finder (DF) receiver antennas can re-radiate through the GPS antenna. The GDU does not interfere with its own GPS receiver. However, placement of the GPS antenna relative to a COM transceiver and COM antenna, ELT antenna, and DF receiver antenna is critical.
Use the following guidelines, in addition to others in this document, when locating the GDU and its antennas.
• GPS Antenna—Locate as far as possible from all COM antennas and all COM transceivers, ELT antennas, and DF antennas. The GPS antenna is less susceptible to harmonic interference if a
1.57542 GHz notch filter is installed on the COM transceiver antenna output.
• Locate the GDU as far as possible from all COM antennas.
If a COM antenna is found to be the problem, a 1.57542 GHz notch filter (Garmin P/N 330-00067-00) may be installed in the VHF COM coax, as close to the COM as possible.
If a COM is found to be radiating, the following can be done:
1. Replace or clean the VHF COM rack connector to ensure good coax ground.
2. Place grounding straps between the GDU unit, VHF COM, and a good ground.
3. Shield the VHF COM wiring harness.
190-01115-01
Rev. AN
G3X/G3X Touch Installation Manual - GPS/XM Antenna Installation
Page 23-4
23.4.2 GPS/XM Antenna Mounting Location
The GPS antenna is a key element in the overall system performance and integrity for a GPS navigation system. The mounting location, geometry, and surroundings of the antenna can affect the system performance and/or availability. The following guidance provides information to aid the installer in ensuring that the optimum location is selected for the installation of the GPS antenna. The installation guidelines presented here meet the intent of AC 20-138A section 16. The greater the variance from these guidelines, the greater the chance of decreased availability. Because meeting all of these installations guidelines may not be possible on all aircraft, these guidelines are listed in order of importance to achieve optimum performance. Items 4a - 4c below are of equal importance, and their significance may depend on the aircraft installation. The installer should use their best judgment to balance the installation guidelines.
1. Mount the antenna on top of the aircraft in a location with an unobstructed view of the sky, as close to level as possible with respect to the normal cruise flight attitude of the aircraft. If the normal flight attitude is not known, substitute the waterline, which is typically referenced as level while performing a weight and balance check.
2. The GPS antenna should be mounted in a location to minimize the effects of airframe shadowing during typical maneuvers. Typically mounting farther away from the tail section reduces signal blockage seen by the GPS antenna.
3. The GPS antenna should ideally be located at the opposite end of the aircraft from the COM unit in order to make the GPS less vulnerable to harmonics radiated from the COM itself.
4a. The GPS antenna should be mounted no closer than two feet (edge to edge) and ideally three feet from any VHF COM antenna or any other antenna which may emit harmonic (or other) interference at the L1 frequency of 1575.42 MHz. An aircraft EMC (Electromagnetic
Compatibility) check ( Section 34.4.15.1
for GDU 37X systems or Section 35.4.24.1
GDU 4XX systems) can verify the degradation of GPS in the presence of interference signals. If an EMC check reveals unacceptable interference, insert a GPS notch filter in line with the offending VHF COM or the (re-radiating) ELT transmitter.
NOTE
The separation requirement does not apply to GPS and COM combination antennas, provided the antenna has been tested to meet Garmin’s minimum performance standards.
The separating requirement includes the combination with an XM antenna element as well.
4b. The GPS antenna should be mounted no closer than two feet (edge to edge) and ideally three feet from any antennas emitting more than 25 watts of power. An aircraft EMC check can verify the degradation of GPS in the presence of interference signals.
4c. To minimize the effects of shadowing at 5° elevation angles, the GPS antenna should be mounted no closer than 6 inches (edge to edge) from other antennas, including passive antennas such as another GPS antenna or XM antenna.
5. To maintain a constant gain pattern and limit degradation by the windscreen, avoid mounting the antenna closer than 3 inches from the windscreen.
6. For multiple GPS installations, the antennas should not be mounted in a straight line from the front to the rear of the fuselage. Also varying the mounting location will help minimize any aircraft shading by the wings or tail section (in a particular azimuth, when one antenna is blocked the other antenna may have a clear view).
190-01115-01
Rev. AN
G3X/G3X Touch Installation Manual - GPS/XM Antenna Installation
Page 23-5
Figure 23-1 shows the recommended placement of antennas.
4
190-01115-01
Rev. AN
Figure 23-1 Recommended Antenna Placement
G3X/G3X Touch Installation Manual - GPS/XM Antenna Installation
Page 23-6
23.4.3 Buried Antenna (below the skin covering or glareshield) Mounting
There are potential performance issues related to buried antennas that the kit builder/installer should be aware of prior to electing to install a buried antenna. See also
, Non-structural Installation to
Glareshield.
• Some gain of the antenna may be lost as the signal needs to penetrate through the skin of the aircraft. The loss may not be apparent, but under the some of the worst case signal scenarios signal availability may be affected.
• The materials in some aircraft are not suitable for GPS signals to penetrate, care should be taken to properly modify the aircraft structure to accommodate this. Modifications of this sort are not recommended or inferred by Garmin or the installation of the GDU, and the installer should seek the guidance of the kit manufacture for such modifications.
• XM – FIS antennas may typically be buried without performance impact if the overlying material is fairly transparent to the satellite signal.
Figure 23-2 shows example areas of some mounting locations which have been used. Low satellite
reception and tracking are compromised in these installations due to fuselage and tail blockage. It is not possible to determine the full impact of these locations, however initial flight testing has not shown any significant impact to availability, your results may vary.
Figure 23-2 Carbon/Glass Buried Antenna Area
190-01115-01
Rev. AN
G3X/G3X Touch Installation Manual - GPS/XM Antenna Installation
Page 23-7
Mounting the antenna under the glare shield (Figure 23-3) is a good option for XM – FIS antennas,
although it is not typically the best option for a GPS antenna. This location results in the aft fuselage shading the antenna.
Figure 23-3 Glare Shield Buried Antenna Area
NOTE
Due to the excessive temperature environment and large areas of signal blockage caused by the fuselage, mounting the antenna under the engine cowling (forward of the firewall) is not recommended and likely will not provide adequate GPS reception.
23.4.4 Antenna Doubler/Backing Plate
The antenna installation must provide adequate support for the antenna considering a maximum drag load of 5 lbs. (at subsonic speed). When penetrating the skin with a large hole (i.e. for the coax connector) a doubler plate is required to re-instate the integrity of the aircraft skin. Never weaken the aircraft structure when choosing a mounting area. Make use of any available reinforcements where appropriate.
23.4.5 Antenna Grounding Plane
Although no ground plane is required, the antennas typically perform better when a ground plane is used.
The ground plane should be a conductive surface as large as practical, with a minimum diameter of 8 inches. To use an antenna in aircraft with fabric or composite skin, a ground plane is recommended. It is usually installed under the skin of the aircraft, below the antenna, and is made of either aluminum sheet or of wire mesh.
23.4.6 Antenna Grounding
The antenna is grounded through the mounting hardware and the coax connection. The mounting hardware
(washers and nuts) and doubler plate should make contact with an unpainted grounded surface ensuring proper antenna grounding. It is important to have good conductivity between the coaxial shield and the ground plane. The bottom of the antenna does not need to make contact with the ground plane (i.e. the surface may be painted). The antenna will capacitively couple to the ground plane beneath the paint or aircraft cover.
190-01115-01
Rev. AN
G3X/G3X Touch Installation Manual - GPS/XM Antenna Installation
Page 23-8
23.5 Teardrop Footprint Antenna Installation (GA 35, GA 55, and GA 56)
This section describes the structural mounting of the teardrop footprint antenna installation.
An acceptable installation method is to use Garmin P/N: 115-00846-10 doubler plate with the GA 35 through-hole, or GA 55/GA 56 stud mount antennas. Another acceptable method is to fabricate and install
one of three doublers ( Figure 23-4
,
, and Figure 23-6 ), depending on the thickness of the skin.
The three doubler designs vary only by number of rivets and hole preparation for installation with flush
antenna doubler/backplate.
shows an example of the doubler installed between stringers on the top fuselage skin, just off centerline. The location should be flat, with no gaps between the skin and doubler, to keep from deforming the skin during installation.
Table 23-5 Teardrop Footprint Antenna Doubler Design and Installation
Aircraft Skin Thickness
Doubler Design (Figure)
Number of Rivets Required
0.032” to 0.049”
12
0.049” to 0.051”
16
0.051” to 0.063”
16
Type of Rivets Required 1
Skin Preparation for Rivets
Doubler Preparation for Rivets
Skin Cutout Detail (Figure)
Doubler Installation (Figure)
MS20426AD4-x
Dimple
Countersink
MS20426AD4-x
Dimple
Countersink
MS20426AD4-x
Countersink
None
1 Rivet length determined at installation, dependent on thickness of material (rivet length = grip length +
1.5 * rivet diameter)
Refer to the drawings in Section 23.8
for Garmin Antenna installation drawings.
23.5.1 Preparation of Doubler
1. Use Garmin P/N: 115-00846-10, or refer to Table 23-5 for guidance on selecting the appropriate
doubler drawing based on the thickness of skin at the antenna location. Make the doubler from
2024-T3 Aluminum (AMS-QQ-A-250/5), 0.063” sheet thickness.
2. For installation in aircraft skins of thickness less than 0.051”, countersink the rivet holes in the doubler for use with flush head rivets (MS20426AD4-x).
3. When using Garmin P/N: 115-00846-10 doubler, sixteen rivet holes exist in the part. For installation of Garmin P/N: 115-00846-10 in skins of thickness between 0.032” and 0.049”, only
) are required.
190-01115-01
Rev. AN
G3X/G3X Touch Installation Manual - GPS/XM Antenna Installation
Page 23-9
23.5.2 Teardrop Antenna Installation Instructions
1. Refer to
and the outline and installation drawings in Section 23.8
guidance and selecting the appropriate mounting cutout. Drill or punch the holes to match the mating part (doubler).
2. Install a doubler plate to reinforce the aircraft skin, as required. Refer to Section 23.5.1
for doubler
preparation and Table 23-5 for additional guidance on the doubler installation. Dimple aircraft skin
when the skin thickness is less than 0.051” for installation of flush head rivets. Countersink aircraft skin when the skin thickness is between 0.051” and 0.063” for installation of flush head rivets.
3. For the GA 35, secure the O-ring in the O-ring groove on the underside of the antenna. Place the antenna over the mounting holes, using the four screw holes to align the antenna and insert the supplied four screws ( Figure 23-32 ).
CAUTION
GA 35 serial numbers below 110000 required screws with 80 degree countersink angle and most aviation fasteners (AN509) are NOT compatible. Serial numbers
110000 and higher, AN509 hardware is compatible. Antennas installed with incompatible hardware or screws that have been over tightened will void antenna warranty.
4. For a stud mount teardrop footprint antenna, place the install gasket on top of aircraft skin using
the four screw holes to align the gasket ( Figure 23-35 ,
5. Washers and locking nuts (not provided) are required to secure the antenna. Torque the four #8-32 stainless steel locking nuts 12-15 in-lbs. Torque should be applied evenly across all mounting studs or screws to avoid deformation of the mounting area.
6. Ensure that the antenna base and aircraft skin are in continuous contact with the gasket or o-ring, as appropriate to the antenna model.
7. Seal the antenna and gasket to the fuselage using Dow Corning 738 Electrical Sealant or equivalent. Run a bead of the sealant along the edge of the antenna where it meets the exterior aircraft skin. Use caution to ensure that the antenna connectors are not contaminated with sealant.
CAUTION
Do not use construction grade RTV sealant or sealants containing acetic acid.
These sealants may damage the electrical connections to the antenna. Use of these type sealants may void the antenna warranty.
190-01115-01
Rev. AN
G3X/G3X Touch Installation Manual - GPS/XM Antenna Installation
Page 23-10
23.5.3 Reference Figures
Figure 23-4 Doubler Design, Teardrop Footprint Antenna, Skin Thickness 0.032" to 0.049"
Figure 23-5 Doubler Design, Teardrop Footprint Antenna, Skin Thickness 0.049" to 0.051"
190-01115-01
Rev. AN
G3X/G3X Touch Installation Manual - GPS/XM Antenna Installation
Page 23-11
Figure 23-6 Doubler Design, Teardrop Footprint Antenna, Skin Thickness 0.051" to 0.063"
Figure 23-7 Sample Doubler Location, Teardrop Footprint Antenna, Metal Skin Aircraft
190-01115-01
Rev. AN
G3X/G3X Touch Installation Manual - GPS/XM Antenna Installation
Page 23-12
Figure 23-8 Skin Cutout Detail, Teardrop Footprint Antenna, Skin Thickness 0.032" to 0.049"
Figure 23-9 Skin Cutout Detail, Teardrop Footprint Antenna, Skin Thickness 0.049" to 0.051"
190-01115-01
Rev. AN
G3X/G3X Touch Installation Manual - GPS/XM Antenna Installation
Page 23-13
Figure 23-10 Skin Cutout Detail, Teardrop Footprint Antenna, Skin Thickness 0.051" to 0.063"
Figure 23-11 Doubler Installation, Teardrop Footprint Antenna, Skin Thickness 0.032" to 0.049"
190-01115-01
Rev. AN
G3X/G3X Touch Installation Manual - GPS/XM Antenna Installation
Page 23-14
Figure 23-12 Doubler Installation, Teardrop Footprint Antenna, Skin Thickness 0.049" to 0.051"
Figure 23-13 Doubler Installation, Teardrop Footprint Antenna, Skin Thickness 0.051" to 0.063"
190-01115-01
Rev. AN
G3X/G3X Touch Installation Manual - GPS/XM Antenna Installation
Page 23-15
23.6 ARINC 743 Footprint Antenna Installation (GA 36, GA 37, GA 55A, GA 57X)
This section describes the structural mounting of the ARINC 743 footprint antenna (GA 36, GA 37, GA
55A, GA 57X) installation. One acceptable method is to use Garmin P/N: 115-00846-00 doubler plate.
Another acceptable method is to fabricate and install one of three doublers, Figure 23-14 ,
, or
rivets and hole preparation for installation with flush rivets.
shows installation of the ARINC
743 footprint antenna.
Table 23-6 provides a summary of design and installation details for the antenna doubler.
shows an example of the doubler installed between stringers on the top fuselage skin, just off centerline.
The location should be flat, with no gaps between the skin and doubler, to keep from deforming the skin during installation.
Table 23-6 ARINC 743 Footprint Antenna Doubler Design and Installation
Skin Thickness
Doubler Design (Figure)
Number of Rivets Required
0.032” to 0.049”
12
0.049” to 0.051”
16
0.051” to 0.063”
16
Type of Rivets Required 1
Skin Preparation for Rivets
Doubler Preparation for Rivets
Skin Cutout Detail (GA 55A)
Doubler Installation (Figure)
MS20426AD4-x
Dimple
Countersink
MS20426AD4-x
Dimple
Countersink
MS20426AD4-x
Countersink
None
1 Rivet length determined at installation, dependent on thickness of material (rivet length = grip length +
1.5 * rivet diameter)
23.6.1 Preparation of Doubler
1. Use Garmin P/N: 115-00846-00, or refer to Table 23-6 for guidance on selecting the appropriate
doubler drawing based on the thickness of skin at the antenna location. Make the doubler from
2024-T3 Aluminum (AMS-QQ-A-250/5), 0.063” sheet thickness.
2. For installation in aircraft skins of thickness less than 0.051”, countersink the rivet holes in the doubler for use with flush head rivets (MS20426AD4-x).
3. When using Garmin P/N: 115-00846-00 doubler, sixteen rivet holes exist in the part. For installation of Garmin P/N: 115-00846-00 in skins of thickness between 0.032” and 0.049”, only
the rivets identified for use through the skin cutout detail ( Figure 23-18
) and doubler installation
) are required.
190-01115-01
Rev. AN
G3X/G3X Touch Installation Manual - GPS/XM Antenna Installation
Page 23-16
23.6.2 ARINC 743 Antenna Installation Instructions
1. Refer to
and the outline and installation drawings in Section 23.8
guidance and selecting the appropriate mounting cutout. Drill or punch the holes to match the mating part (doubler).
2. Install a doubler plate to reinforce the aircraft skin, as required. Refer to Section 23.6.1
for doubler
preparation and Table 23-6 for additional guidance on the doubler installation. Dimple aircraft skin
when the skin thickness is less than 0.051” for installation of flush head rivets. Countersink aircraft skin when the skin thickness is between 0.051” and 0.063” for installation of flush head rivets.
3. Secure the O-ring in the O-ring groove (if applicable, per Figure 23-33 ,
underside of the antenna.
4. Place the install gasket (if applicable, per Figure 23-36
or
Figure 23-38 ) on top of aircraft skin
using the four screw holes to align the gasket.
5. Locking nuts and washers (not provided) are required to secure the GA 36 and GA 37 per
(or may use locking nuts installed on doubler plate, if applicable).
GA 55A ( Figure 23-36 ) and GA 57X (
Figure 23-38 ) use locking nuts installed on doubler plate.
Torque the four supplied #10-32 stainless steel screws (Garmin P/N: 211-60212-20, MS51958-67, or equivalent) 20-25 in-lbs. Torque should be applied evenly across all mounting studs to avoid deformation of the mounting area.
6. Ensure that the antenna base and aircraft skin are in continuous contact with the gasket (if applicable).
7. Seal the antenna and gasket to the fuselage using Dow Corning 738 Electrical Sealant or equivalent. Run a bead of the sealant along the edge of the antenna where it meets the exterior aircraft skin. Use caution to ensure that the antenna connectors are not contaminated with sealant.
CAUTION
Do not use construction grade RTV sealant or sealants containing acetic acid.
These sealants may damage the electrical connections to the antenna. Use of these type sealants may void the antenna warranty.
190-01115-01
Rev. AN
G3X/G3X Touch Installation Manual - GPS/XM Antenna Installation
Page 23-17
23.6.3 Reference Figures
Figure 23-14 Doubler Design, ARINC 743 Footprint Antenna, Skin Thickness 0.032" to 0.049"
190-01115-01
Rev. AN
G3X/G3X Touch Installation Manual - GPS/XM Antenna Installation
Page 23-18
Figure 23-15 Doubler Design, ARINC 743 Footprint Antenna, Skin Thickness 0.049" to 0.051"
190-01115-01
Rev. AN
G3X/G3X Touch Installation Manual - GPS/XM Antenna Installation
Page 23-19
Figure 23-16 Doubler Design, ARINC 743 Footprint Antenna, Skin Thickness 0.051" to 0.063”
190-01115-01
Rev. AN
G3X/G3X Touch Installation Manual - GPS/XM Antenna Installation
Page 23-20
Figure 23-17 Sample Doubler Location, ARINC 743 Antenna, Metal Skin Aircraft
Figure 23-18 Skin Cutout Detail, ARINC 743 Footprint Antenna, Skin Thickness 0.032" to
0.049"
190-01115-01
Rev. AN
G3X/G3X Touch Installation Manual - GPS/XM Antenna Installation
Page 23-21
Figure 23-19 Skin Cutout Detail, ARINC 743 Footprint Antenna, Skin Thickness 0.049" to 0.051"
Figure 23-20 Skin Cutout Detail, ARINC 743 Footprint Antenna, Skin Thickness 0.051" to 0.063"
190-01115-01
Rev. AN
G3X/G3X Touch Installation Manual - GPS/XM Antenna Installation
Page 23-22
Figure 23-21 Doubler Installation, ARINC 743 Footprint Antenna, SkinThickness 0.032" to 0.049"
Figure 23-22 Doubler Installation, ARINC 743 Footprint Antenna, SkinThickness 0.049" to 0.051"
190-01115-01
Rev. AN
G3X/G3X Touch Installation Manual - GPS/XM Antenna Installation
Page 23-23
Figure 23-23 Doubler Installation, ARINC 743 Footprint, Skin Thickness 0.051" to 0.063"
190-01115-01
Rev. AN
Figure 23-24 Installation of ARINC 743 Footprint Antenna
G3X/G3X Touch Installation Manual - GPS/XM Antenna Installation
Page 23-24
23.7 Non-Structural Mount Installation
This section provides installation examples and considerations for non-structural mounting of teardrop and
ARINC 743 footprint antennas. Typical installations may be below a non-metallic glareshield, under the composite or fabric skin, or on an external, non-structural surface. Other non-structural installations may exist, but are not presented in this manual.
External mounting of the antenna is preferred, although the antenna can be mounted inside the aircraft.
When mounted internally, the antenna does not have to be aligned with the aircraft forward direction, but should be equal to the aircraft typical cruise attitude.
There should be a solid mechanical base in the mounting area for the antenna, and existing surfaces or brackets may be used with the doubler plate. Alternately, non-structural brackets may be fabricated in the field as necessary to mount the antenna. Brackets should be made of minimum 0.032” thickness aluminum and should span as short a distance as possible.
Some fabric aircraft include aluminum paste in the fabric finishing process, often referred to as “silver coats”. Presence of thick fabric and/or heavy “silver coats” may degrade the signal strength of the antenna.
23.7.1 Generic Non-structural Antenna Installation
GA 55A/GA 57X) antenna. The teardrop footprint antennas (GA 35, GA 55, GA 56 stud mount) can also be installed in this manner.
For mounting the teardrop style antenna (GA 35, GA 55, or GA 56), a doubler plate similar to
or P/N 115-00846-10 can be used with the mounting surface to support the antenna. Rivets used to secure the doubler plate to the mounting surface are optional in a non-structural installation. Screws, washers, and locking nuts as shown in the outline and installation drawings in
are required to secure the
Teardrop style antenna to the mounting surface. Torque the locking nuts to 12-15 in-lbs, torque should be applied evenly across all mounting studs.
A doubler plate similar to
, or P/N 115-00846-00 (ARINC 743 style) can be used with the mounting surface to support the antenna. Rivets used to secure the doubler plate to the mounting surface are optional in a non-structural installation. Locking nuts are required to secure the ARINC 743 antenna
(locking nuts installed on doubler). Torque the four supplied #10-32 stainless steel screws (Garmin P/N:
211-60212-20, MS51958-67, or equivalent) evenly across all mounting screws.
190-01115-01
Rev. AN
G3X/G3X Touch Installation Manual - GPS/XM Antenna Installation
Page 23-25
Figure 23-25 Generic Non-structural ARINC 743 Footprint Antenna Installation
190-01115-01
Rev. AN
G3X/G3X Touch Installation Manual - GPS/XM Antenna Installation
Page 23-26
23.7.2 Non-Structural Installation to Glareshield
Figure 23-26 Example Bracket Antenna Mounting Under Glareshield
Figure 23-27 Example Non-structural Antenna Mounting Under Glareshield
190-01115-01
Rev. AN
G3X/G3X Touch Installation Manual - GPS/XM Antenna Installation
Page 23-27
23.7.3 Non-structural Installation to Airframe
Internal Non-structural Installation
Figure 23-28 and Figure 23-29 show examples of under the fabric skin non-structural mounting of the
antenna to the airframe of a tube-and-fabric aircraft.
installation. The doubler plate and mounting hardware described in the generic installation (
)
the generic installation of the ARINC 743 footprint antenna. The doubler plate is optional for this type of installation with either the Teardrop or the ARINC 743 antenna.
Figure 23-28 Example Teardrop Antenna Installation In Airframe Under Fabric Skin
Figure 23-29 Example ARINC 743 Footprint In Airframe Under Fabric Skin
190-01115-01
Rev. AN
G3X/G3X Touch Installation Manual - GPS/XM Antenna Installation
Page 23-28
External Non-structural Installation
aircraft. The antenna support bracket shown should be made of 2024-T3 Aluminum with a minimum material thickness 0.032” and maximum distance between airframe tubes of 36”. The bracket is installed to the airframe under the fabric, and the antenna is mounted externally to the bracket. The generic installation of the (
) antenna is used, with the antenna support bracket as the mounting surface. Follow the applicable gasketing and sealant instructions in
(ARINC 743 style).
Figure 23-30 Example Non-structural Antenna Mounting On Airframe
190-01115-01
Rev. AN
G3X/G3X Touch Installation Manual - GPS/XM Antenna Installation
Page 23-29
Minimum Distance from Metal Tube Structure Requirements
and the antenna for cases where the antenna sits underneath the fabric in a metal-tube structure aircraft.
Figure 23-31 Example Teardrop Footprint Antenna Mounting Under Fabric Skin
.
Table 23-7 Minimum Distance Required Between Tube Structure and Antenna
Illustrated Case
Top of antenna at or above the center of the tube structure
Top of antenna between the center and bottom of the tube
structure (Figure 23-31, bottom)
Tube Diameter d (in)
0.625
0.75
1.00
1.25
0.625
0.75
1.00
1.25
Minimum
Distance l (in)
3.6
4.3
5.7
7.2
7.2
8.6
11.5
14.3
190-01115-01
Rev. AN
G3X/G3X Touch Installation Manual - GPS/XM Antenna Installation
Page 23-30
23.8 Outline and Installation Drawings
190-01115-01
Rev. AN
Figure 23-32 GA 35 Installation Drawing
G3X/G3X Touch Installation Manual - GPS/XM Antenna Installation
Page 23-31
R
A
D
W
R
O
F
S) 0] (2 HOLE
17.8] 0.70 [
0 [0.
0.80 [20.3]
[58.4] 2.30
2X 1.60 [40.6]
RD WA FOR
DO NOT PAINT
190-01115-01
Rev. AN
Figure 23-33 GA 36 Installation Drawing
G3X/G3X Touch Installation Manual - GPS/XM Antenna Installation
Page 23-32
R
A
D
W
R
O
F
] [58.4
2.30
2X 1.60 [40.6]
HOLES)
80 [20.3] 2X 0.
0 [0.0] (2
0.70 [17.8]
ARD FORW
DO NOT PAINT
190-01115-01
Rev. AN
Figure 23-34 GA 37 Installation Drawing
G3X/G3X Touch Installation Manual - GPS/XM Antenna Installation
Page 23-33
GA 55 STUD MOUNT
011-00134-00
ANTENNA, AVIATION,
GA 55
FORWARD
253-00002-00
GASKET, NEOPRENE
AIRCRAFT SKIN
ON TOP OF FUSELAGE
115-00031-00
BACKING PLATE
4X 210-10004-09
#8-32 SELF LOCKING NUT
1.91 48.5
.22 5.6
4X #8-32 STUD
FORWARD
4.23 107.4
SIDE VIEW
.50 12.7
2.59 65.8
FRONT VIEW
BNC CONNECTOR
3.00 76.2
2X 1.625 41.28
.813 20.64
4X .188 4.78
190-01115-01
Rev. AN
.625 15.88
2.59 [65.8]
BACKING PLATE
OUTLINE
MOUNTING CUTOUT
(ANTENNA OUTLINE)
Figure 23-35 GA 55 Installation Drawing
G3X/G3X Touch Installation Manual - GPS/XM Antenna Installation
Page 23-34
GA 55A FLANGE MOUNT
FORWAR
D
4X 211-60212-20
#10-32 PHP x 1.00[25.4]
TORQUE 20 TO 25 in-lbs
011-01153-00
GA 55A XM ANTENNA
253-00138-00
MOLDED GASKET
AIRCRAFT SKIN
.49 12.3
2.90 73.7
.60 15.2
.80
20.2
FABRICATE AND INSTALL DOUBLER PLATE
AS REQUIRED TO COMPLY WITH APPLICABLE
AIRWORTHINESS REGULATIONS
FORWARD
2.37 60.2
4.70 119.4
.25 6.4
XM
TNC CONNECTOR
190-01115-01
Rev. AN
.70 17.8
2X 0
011-01153-00
ANTENNA OUTLINE
.750
.625
19.05
15.88
2.350 59.69
2X 3.300 83.82
4X .220
5.59
MOUNTING CUTOUT
NOTES:
1. DIMENSIONS: INCHES[mm]
Figure 23-36 GA 55A Installation Drawing
G3X/G3X Touch Installation Manual - GPS/XM Antenna Installation
Page 23-35
GA 56 STUD MOUNT
011-00134-00
ANTENNA, AVIATION,
GA 56
FORWARD
AIRCRAFT SKIN
ON TOP OF FUSELAGE
115-00031-00
BACKING PLATE
4X 210-10004-09
#8-32 SELF LOCKING NUT
1.91 48.5
.22 5.6
4X #8-32 STUD
FORWARD
4.23 107.4
SIDE VIEW
.50 12.7
2.59 65.8
FRONT VIEW
BNC CONNECTOR
190-01115-01
Rev. AN
3.00 76.2
2X 1.625 41.28
.813 20.64
4X .188 4.78
.625 15.88
2.59 [65.8]
MOUNTING CUTOUT
(ANTENNA OUTLINE)
Figure 23-37 GA 56 Installation Drawing
G3X/G3X Touch Installation Manual - GPS/XM Antenna Installation
Page 23-36
FORWARD
4X 211-60212-20 #10-32 PHP x 1.00[25.4]
011-01032-10 GA 57X GPS/XM ANTENNA
FABRICATE AND INSTALL DOUBLER PLATE AS REQUIRED TO COMPLY WITH APPLICABLE AIRWORTHINESS REGULATIONS
011-01032-00 ANTENNA OUTLINE
19.05 15.88
.750 .625
20.3
40.64
2X.800
2X1.600
.6516.5
2X0
190-01115-01
Rev. AN
FORWARD
Figure 23-38 GA 57X Installation Drawing
G3X/G3X Touch Installation Manual - GPS/XM Antenna Installation
Page 23-37
24 ENGINE/AIRFRAME SENSOR INSTALLATION
24.1 Engine/Airframe Sensor Options
inputs. Many of these sensors are included in the Garmin G3X Sensor Kits ( Section 24.2
). Each of the sensors must be correctly installed and configured (
for GDU 4XX systems) prior to use.
NOTE
In addition to the engine sensors listed in Table 24-1, the G3X system can also work with
many other sensors (not listed) that output a compatible signal, refer to the sensor specifications to determine compatibility.
Table 24-1 Compatible Engine/Airframe Input Sensors
SENSOR TYPE
COMPATIBLE
SENSORS
10-29 Vdc input
Amploc KEY100 Hall effect sensor
UMA 1C4 shunt
GARMIN PART
N/A
N/A
NUMBER*
+/- 100 A
NOTES
Bus Current
Other ammeter shunt or
Hall effect sensor types
Rotax 965531
Rotax 966385
50-150C Thermistor (e.g.
VDO 320-XXX series)
909-D0000-00
N/A
N/A
N/A
N/A
+/- 100 A
Uses custom user-defined calibration (millivolts to amps)
Carburetor
Temperature
Type K Thermocouple
MS28034/
MIL-T-7990 RTD
N/A
N/A
UMA 1B10R RTD 494-70005-00
UMA temperature sensors without the "R" designation are not compatible
0-75 psiG
Coolant Pressure
Custom Analog
Parameter
Kavlico P4055-5020-3
Any voltage-output pressure transducer
Any voltage-output sensor
011-04202-20
N/A
N/A
Uses custom user-defined calibration (voltage to pressure)
Uses custom user-defined sensor calibration
*Items with a Garmin part number may be included in a G3X Sensor Kit (
individually from Garmin Dealers
190-01115-01
Rev. AN
G3X/G3X Touch Installation Manual - Engine/Airframe Sensor Installation
Page 24-1
Table 24-1 Compatible Engine/Airframe Input Sensors
SENSOR TYPE
COMPATIBLE
SENSORS
50-150C Thermistor (e.g.
VDO 320-XXX series)
GARMIN PART
N/A
NUMBER*
NOTES
RTD (e.g. UMA 1B3XR series)
N/A
UMA temperature sensors without the "R" designation are not compatible
Custom
Temperature
Rotax 965531 (thermistor) N/A
Rotax 966385 (thermistor) N/A
Type J thermocouple N/A
Type K thermocouple
MS28034 (MIL-T-7990
RTD)
N/A
N/A
Cylinder Head
Temperature
(CHT)
50-150C Thermistor (e.g.
VDO 320-XXX series)
Type J Thermocouple
Type K Thermocouple
(Alcor 86253)
Type K Thermocouple
(other)
Rotax 965531
Rotax 966385
N/A
N/A
494-70000-00
N/A
N/A
N/A
Discrete Inputs
Active High or Low:
Canopy Warning, Gear
Down Reminder, etc.
N/A
Kavlico P4055-5020-4
Pressure Sensor,150 PSIG 011-04202-30
Uses custom user-defined calibration (0-150 psiG pressure to torque)
Engine Torque
Exhaust Gas
Temperature
(EGT)
Any voltage-output torque transducer
Type K thermocouple
(Alcor 86255)
Type K thermocouple
(other)
N/A
494-70001-00
N/A
Uses custom user-defined calibration (voltage to torque)
*Items with a Garmin part number may be included in a G3X Sensor Kit ( Section 24.2
), and are available individually from Garmin Dealers
190-01115-01
Rev. AN
G3X/G3X Touch Installation Manual - Engine/Airframe Sensor Installation
Page 24-2
Table 24-1 Compatible Engine/Airframe Input Sensors
SENSOR TYPE
COMPATIBLE
SENSORS
EI FT-60
EI FT-90
EI FT-180
GARMIN PART
NUMBER*
494-10001-00
N/A
N/A
0-70 gal/hr
0-125 gal/hr
0-250 gal/hr
NOTES
Fuel Flow
(two sensors required for differential fuel flow)
Floscan Series 200
Floscan 231
Any frequency-output fuel flow transducer
N/A
N/A
N/A
0-60 gal/hr
0-90 gal/hr
Uses custom user-defined calibration (0-5 kHz frequency to fuel flow)
0-15 psiG
Fuel Pressure
Kavlico P4055-5020-2
Kavlico P4055-5020-3
Kavlico P4055-75G
UMA EU07D
UMA 1EU35G
UMA 1EU70D
UMA 1EU70G
UMA 1EM2K
Any voltage-output pressure sensor
Any capacitive fuel quantity sensor (requires external conversion to voltage or frequency)
011-04202-10
011-04202-20
N/A
N/A
N/A
N/A
N/A
N/A
N/A
N/A
0-75 psiG
0-75 psiG
0-7 psi differential
0-35 psiG
0-70 psi differential
0-70 psiG
0-2500 psiG
Uses custom user-defined calibration (voltage to pressure)
Uses custom user-defined calibration (voltage or frequency to fuel quantity)
Fuel Quantity
Any resistive fuel quantity sensor
Any voltage-output fuel quantity sensor
Any frequency-output fuel quantity sensor
N/A
N/A
N/A
Uses custom user-defined calibration (voltage to fuel quantity)
Uses custom user-defined calibration (voltage to fuel quantity)
Uses custom user-defined calibration (frequency to fuel quantity)
*Items with a Garmin part number may be included in a G3X Sensor Kit ( Section 24.2
), and are available individually from Garmin Dealers
190-01115-01
Rev. AN
G3X/G3X Touch Installation Manual - Engine/Airframe Sensor Installation
Page 24-3
Table 24-1 Compatible Engine/Airframe Input Sensors
SENSOR TYPE
Manifold
Pressure
Miscellaneous
Pressure
Oil Temperature
COMPATIBLE
SENSORS
Kavlico P4055-30A-E4A
Kavlico P500-30A-E4A
UMA 1EU50A
GARMIN PART
NUMBER*
494-30004-01
N/A
N/A
N/A UMA 1EU70A
Any voltage-output pressure transducer
Kavlico P4055-5020-3 011-04202-20
Kavlico P4055-5020-4
Pressure Sensor,150 PSIG 011-04202-30
UMA 1EM2K
Any voltage-output pressure transducer
N/A
N/A
N/A
Jabiru (VDO 320-021)
Rotax 965531
Rotax 966385
50-150C Thermistor (e.g.
VDO 320-XXX series)
Type K Thermocouple
N/A
N/A
N/A
N/A
N/A
0-30 psiA, 0-60 inches Hg
0-30 psiA, 0-60 inches Hg
0-25 psiA, 0-50 inches Hg
0-35 psiA, 0-70 inches Hg
Uses custom user-defined calibration (voltage to pressure)
0-75 psiG
0-150 psiG
0-2500 psiG
NOTES
Uses custom user-defined calibration (voltage to pressure)
UMA 1B3-2.5R RTD 494-70004-00
UMA temperature sensors without the "R" designation are not compatible
Oil Pressure
MS28034 (MIL-T-7990
RTD)
Jabiru (VDO 360-003)
N/A
N/A
Kavlico P4055-5020-4
Pressure Sensor,150 PSIG 011-04202-30
Rotax 456180 N/A
Rotax 956413
Rotax 956415
UMA 1EU150G
Any voltage-output pressure sensor
N/A
N/A
N/A
N/A
0-150 psiG
0-150 psiG
Uses custom user-defined calibration (voltage to pressure)
*Items with a Garmin part number may be included in a G3X Sensor Kit ( Section 24.2
), and are available individually from Garmin Dealers
190-01115-01
Rev. AN
G3X/G3X Touch Installation Manual - Engine/Airframe Sensor Installation
Page 24-4
Table 24-1 Compatible Engine/Airframe Input Sensors
SENSOR TYPE
Position Sensor
COMPATIBLE
SENSORS
Any trim servo with integrated position potentiometer
Any standalone potentiometer
Electronic Ignition
Jabiru Alternator Output
JPI 4208XX (Slick/Bendix magneto, pressurized)
Rotax Trigger Coil
UMA 1A3C-2
GARMIN PART
N/A
N/A
N/A
N/A
N/A
NUMBER*
NOTES
Uses custom user-defined calibration (voltage to position)
Uses custom user-defined calibration (voltage to position)
1-4 pulses/revolution
Single phase, 6 pulses/revolution
N/A
N/A
N/A
RPM
UMA 1A3C-4
UMA T1A9-1 (Slick magneto)
UMA T1A9-2 (Bendix magneto)
Turbine engine RPM
(requires Sandia ST26 signal converter)
494-50005-00
494-50005-01
N/A
Uses custom user-defined calibration (0-1000 Hz to RPM)
Any frequency-output RPM sensor
N/A
Uses custom user-defined calibration (0-1000 Hz to RPM)
Turbine Inlet /
Outlet /
Interstage
Temperature
(TIT/TOT/ITT)
Type K thermocouple N/A
*Items with a Garmin part number may be included in a G3X Sensor Kit ( Section 24.2
), and are available individually from Garmin Dealers
190-01115-01
Rev. AN
G3X/G3X Touch Installation Manual - Engine/Airframe Sensor Installation
Page 24-5
the MFD Engine Page.
Figure 24-1 EIS Display (Engine Bar)
The following list of gauges, (if configured) are specifically required by FAR 91.205 and will always be displayed on the EIS display (engine bar). Other gauges will be displayed as space permits based on a predefined priority and user selections.
RPM
Fuel Quantity
Oil Temperature Oil Pressure
190-01115-01
Rev. AN
G3X/G3X Touch Installation Manual - Engine/Airframe Sensor Installation
Page 24-6
24.2 Engine Sensor Applications
24.2.1 Lycoming/Continental Engine Applications
6-cylinder Lycoming and Continental piston engines. Refer to Sensor Interface drawings in Section 31
for sensor wiring guidance.
Table 24-2 Contents of G3X Sensor Kit, 4 Cylinder Lycoming/Continental (K00-00512-00)
Item
Fuel Flow Transducer, EI FT-60
Kavlico P4055-5020-4 Pressure Sensor, 150 PSIG
Manifold Pressure Transducer, Powered, 30 psi, Absolute, w/connector, Kavlico P4055-30A-E4A
Type K Thermocouple, 3/8-24 Threaded, CHT, Alcor 86253
Type K Thermocouple, Clamp, EGT, Alcor 86255
RTD, Oil Temperature, UMA 1B3-2.5R
Shunt, Ammeter, +/-50 mV, 100 amps, UMA 1C4
Garmin P/N
494-10001-00
011-04202-30
494-30004-01
494-70000-00
494-70001-00
494-70004-00
909-D0000-00
Quantity
1
1
1
1
1
4
4
Table 24-3 Contents of G3X Sensor Kit, 6 Cylinder Lycoming/Continental (K00-00513-00)
Item
Fuel Flow Transducer, EI FT-60
Kavlico P4055-5020-4 Pressure Sensor, 150 PSIG
Manifold Pressure Transducer, Powered, 30 psi, Absolute, w/connector, Kavlico P4055-30A-E4A
Type K Thermocouple, 3/8-24 Threaded, CHT, Alcor 86253
Type K Thermocouple, Clamp, EGT, Alcor 86255
RTD, Oil Temperature, UMA 1B3-2.5R
Shunt, Ammeter, +/-50 mV, 100 Amps, UMA 1C4
Garmin P/N
494-10001-00
011-04202-30
494-30004-01
494-70000-00
494-70001-00
494-70004-00
909-D0000-00
Quantity
1
1
1
1
1
6
6
For 8-cylinder Lycoming engine applications, refer to Section 24.2.5
.
For retrofit applications, where a G3X system is installed in a completed aircraft with a Lycoming/
Continental engine, refer to
24.2.1.1 Lycoming/Continental RPM
Engine speed for Lycoming and Continental engines may be sensed by an RPM sensor mounted on the mechanical tach drive, a sensor mounted on the magneto, or via the digital tach signal output from an electronic ignition system. Refer to
.
190-01115-01
Rev. AN
G3X/G3X Touch Installation Manual - Engine/Airframe Sensor Installation
Page 24-7
24.2.1.2 Lycoming/Continental Fuel Pressure
Fuel pressure sensors for Lycoming and Continental engines are not included in the Garmin sensor kits, due to differences between pressure ranges for carbureted and fuel-injected engines. For monitoring
Lycoming/Continental engine fuel pressure, select a sensor from Table 24-1
as appropriate:
• Fuel-injected engines typically use the Kavlico P4055-5020-3 sensor (0-75 psiG, Garmin part number 011-04202-20).
• Carbureted engines typically use the Kavlico P4055-5020-2, sensor (0-15 psiG, Garmin part number 011-04202-10)
NOTE
Lycoming EIS display ranges are typically set to correspond with the pressure at the inlet to the fuel injector. Continental EIS display ranges are typically set to correspond to unmetered fuel pressure values.
24.2.1.3 Lycoming iE2
The G3X system is capable of monitoring the following engine parameters from the Lycoming iE2
FADEC digital interface, when connected via a GEA 24:
• RPM
• Manifold pressure
• Oil pressure
• Oil temperature
• Exhaust gas temperature
• Cylinder head temperature
• Turbine inlet temperature
• Fuel pressure
• ECU bus voltage
190-01115-01
Rev. AN
G3X/G3X Touch Installation Manual - Engine/Airframe Sensor Installation
Page 24-8
24.2.2 Rotax Engine Applications
Refer to the Sensor Interface drawings in Section 32 for all Rotax engine applications.
24.2.2.1 Rotax 912
Table 24-4 lists the Garmin sensor kit available for G3X installations with Rotax 912 engines.
Table 24-4 Contents of G3X Sensor Kit, Rotax 912 (K00-00514-00)
Item Garmin P/N
G3X External Components for Rotax 912 RPM Signal (see Table 24-5 ) 011-02348-00
Manifold Pressure Transducer, Powered, 30 psi, Absolute, w/ connector, Kavlico P4055-30A-E4A
Kavlico P4055-5020-2 Pressure Sensor, 15 PSIG
Type K Thermocouple, Clamp, EGT, Alcor 86255
494-30004-01
011-04202-10
494-70001-00
Shunt, Ammeter, +/-50 mV, 100 Amps, UMA 1C4 909-D0000-00
Quantity
1
1
1
2
1
Rotax engine RPM is sensed via a connection to the engine trigger coil. The external components listed in
Table 24-5 are required for use with the GSU 73 (see Figure 32.3).
Table 24-5 Contents of G3X External Components for Rotax 912 RPM Signal Kit
(011-02348-00)
Item
Silicon Diode, 1A, 200V
7.5 V Zener Diode
300 Ω Resistor, 1%, 0.5 W
Garmin P/N
680-00006-D0
682-00012-00
902-A300R-F0
Quantity
2
1
2
190-01115-01
Rev. AN
G3X/G3X Touch Installation Manual - Engine/Airframe Sensor Installation
Page 24-9
24.2.2.2 Rotax 914
Table 24-6 lists the sensors used for G3X installations with Rotax 914 engines. Order all sensors in the
Rotax 912 sensor kit (K00-00514-00) except the 494-30004-03 fuel pressure sensor. Instead, use the
UMA 1EU07D differential fuel pressure sensor.
Table 24-6 Rotax 914 Sensors
RPM
Sensor Type
Manifold pressure
Oil pressure
Oil temperature
Exhaust gas temperature
Details/Part Number
Use Rotax tachometer output along with external components from
011-02348-00 kit
Use Kavlico P4055-30A-E4A (494-30004-01)
Use Rotax-supplied sensor
Use Rotax-supplied thermistor
Use Type K thermocouple (494-70001-00)
Cylinder head temperature Use Rotax-supplied thermistor
Fuel pressure Use UMA 1EU07D differential fuel pressure sensor
Fuel flow Use EI FT-60 (494-10001-00) or Floscan 201B-6
24.2.2.3 Rotax 912iS/915iS
The G3X system is capable of monitoring the following engine parameters from the Rotax 912iS/915iS
FADEC digital interface, when connected to the dedicated FADEC CAN interface on a GEA 24:
• RPM
• Manifold pressure
• Manifold air temperature
• Oil pressure
• Oil temperature
• Exhaust gas temperature
• Coolant temperature
• Fuel flow
• ECU bus voltage
• Throttle position
• Percent Power (Rotax 915iS only)
See
for GEA 24 to Rotax FADEC wiring information.
Fuel pressure for Rotax FADEC engines may be monitored using one of the two following methods:
• Use UMA 1EU70D differential sensor for fuel pressure.
• With a GDU 4XX system, select an appropriate fuel pressure sensor from
appropriate, and configure the sensor to display fuel pressure relative to manifold pressure (see
for information about FADEC engine status display.
190-01115-01
Rev. AN
G3X/G3X Touch Installation Manual - Engine/Airframe Sensor Installation
Page 24-10
24.2.3 Jabiru Engine Applications
Table 24-7 lists the sensors used in G3X installations with Jabiru engines. See
for Jabiru engine sensor wiring information.
Table 24-7 Jabiru Sensors
RPM
Sensor Type
Manifold pressure
Oil pressure
Details/Part Number
Use Jabiru tachometer output from alternator
Use Kavlico P4055-30A-E4A (494-30004-01)
Use Jabiru-supplied VDO pressure sensor, or Kavlico P4055-150G-E4A
(494-0004-00)
Oil temperature
Exhaust gas temperature
Use Jabiru-supplied VDO 50-150°C thermistor, or any compatible RTD such as UMA 1B3XR series
Use Jabiru-supplied Type K thermocouples
Cylinder head temperature Use Jabiru-supplied Type J thermocouples
Fuel pressure Use Kavlico P4055-5020-2 (011-04202-10)
Fuel flow Use EI FT-60 (494-10001-00) or Floscan 201B-6
190-01115-01
Rev. AN
G3X/G3X Touch Installation Manual - Engine/Airframe Sensor Installation
Page 24-11
24.2.4 UL Power Engine Applications
The G3X system is capable of monitoring the following engine parameters from the UL Power FADEC digital interface, when connected to the dedicated FADEC CAN interface on a GEA 24:
• RPM
• Manifold pressure
• Oil pressure
• Oil temperature
• Cylinder head temperature
• Exhaust gas temperature
• Fuel pressure
• Fuel flow
• ECU bus voltage
for information about FADEC engine status display.
For UL Power engine installations that do not support a digital interface to the GEA 24, the engine sensors
shown in Table 24-8 may be used.
Table 24-8 UL Power Sensors
RPM
Sensor Type Details/Part Number
Use ECU tachometer output and select "Electronic Ignition
(2 pulses/revolution)"
Use Kavlico P4055-30A-E4A (494-30004-01) Manifold pressure
Oil Pressure
Oil temperature
Fuel flow
Kavlico P4055-5020-4 Pressure Sensor, 150 PSIG (011-04202-30)
Use UMA 1B3-2.5R RTD (494-70004-00)
Exhaust gas temperature Use Type K thermocouples
Cylinder head temperature Use Type K thermocouples
Fuel Pressure Kavlico P4055-5020-30 (011-04202-20)
Use ECU fuel consumption pulse output and select "Custom" fuel flow configuration. UL Power specifies a pulse frequency of 170 Hz at
72 L/hour, which suggests an initial scale factor of 32176.
190-01115-01
Rev. AN
G3X/G3X Touch Installation Manual - Engine/Airframe Sensor Installation
Page 24-12
24.2.5 Other Piston Engine Applications
In addition to the engines described previously, the G3X system's engine/airframe inputs can be configured for use with a variety of other engine types.
Sensors for Other Piston Engines - Many other piston engines can be monitored using the supported
engine sensors shown in Table 24-1
, along with custom engine sensor configuration as described in
for GDU 37X units, or Section 35.4.32
for GDU 4XX units.
RPM
Sensor Type
Manifold pressure
Oil pressure
Oil temperature
Exhaust gas temperature
Turbine inlet temperature
Carburetor temperature
Fuel pressure
Fuel flow
Coolant pressure
Coolant temperature (or other temperature)
Hydraulic pressure (or other pressure)
Other parameters
Table 24-9 Sensors for Other Piston Engines
Cylinder head temperature
Details/Part Number
Use any supported sensor from
, or select "Custom" configuration and enter frequency-to-RPM calibration
Use any supported sensor from
, or select "Custom" configuration and enter voltage-to-pressure calibration
Use any supported sensor from
, or select "Custom" configuration and enter voltage-to-pressure calibration
Use any supported sensor from
Use Type K thermocouples. Up to 6 cylinders are supported, or up to 12 cylinders in a GDU 4XX system with dual GEA 24 EIS units.
Use Type J or Type K thermocouples. Up to 6 cylinders are supported, or up to 12 cylinders in a GDU 4XX system with dual GEA 24 EIS units.
Use Type K thermocouples
Use any supported sensor from
Use any supported sensor from
, or select "Custom" configuration and enter voltage-to-pressure calibration
Use any supported sensor from
, or select "Custom" configuration and enter pulses-per-gallon calibration
Use any supported sensor from
, or select "Custom" configuration and enter voltage-to-pressure calibration
Use "Custom" temperature configuration with RTD, thermistor, or thermocouple
Use appropriate Kavlico pressure sensor or select "Custom" configuration and enter voltage-to-pressure calibration
Use any supported sensor from
Large Piston Engines - A GDU 4XX system with dual GEA 24 EIS units installed can monitor a single engine with up to 12 cylinders, including radial engines. For large single-engine applications, cylinders
1-6 are connected to GEA 24 #1 and cylinders 7-12 are connected to GEA 24 #2. (see
Twin Piston Engines - A GDU 4XX system with dual GEA 24 EIS units installed can monitor twin piston engines with up to 6 cylinders each (see
190-01115-01
Rev. AN
G3X/G3X Touch Installation Manual - Engine/Airframe Sensor Installation
Page 24-13
24.2.6 Retrofit Engine Applications
When installing a G3X system in a completed aircraft with a typical piston engine, it is generally possible
to reuse a number of the existing engine sensors that may already be present. Consult Section 30
for general engine sensor wiring guidance that can be applied to existing sensors.
RPM
Sensor Type
Manifold Pressure
Oil Pressure
Oil Temperature
Exhaust Gas
Temperature
Cylinder Head
Temperature
Table 24-10 Retrofit Engine Sensors
Notes on Suitability for Reuse
Sensors that provide a digital output signal can be used without modification, if calibration characteristics are known.
Do not connect G3X RPM inputs directly to magneto P-leads.
Sensors that provide a voltage output can be used without modification, if calibration characteristics are known.
Sensors that provide a resistance or current output may require replacement with a supported sensor (e.g. 494-30004-01).
Sensors that provide a voltage output can be used without modification, if calibration characteristics are known.
Sensors that provide a resistance or current output may require replacement with a supported sensor (e.g. 011-04202-30).
Existing sensors are generally likely to require replacement with a supported sensor (e.g. 494-70004-00).
Type K thermocouples can be used without modification. The GEA 24 J242 connector matches the pinout used by certain other engine monitoring systems.
Type J or K thermocouples can be used without modification. The GEA 24
J242 connector matches the pinout used by certain other engine monitoring systems.
Turbine Inlet
Temperature
Type K thermocouples can be used without modification.
Fuel Pressure
Fuel Flow
Bus Current
Fuel Quantity
Sensors that provide a voltage output can be used without modification, if calibration characteristics are known.
Sensors that provide a resistance or current output may require replacement with a supported sensor (e.g. 494-30004-02 or 494-30004-03).
Most sensors that provide a digital output signal can be used without modification, if calibration characteristics are known.
Many existing installations use Floscan or Electronics International fuel flow sensors that are directly supported by the G3X system.
Most shunt-type or Hall-effect sensors can be used without modification, if calibration characteristics are known.
Most sensors that provide a resistance, voltage, or frequency output can be used without modification. New fuel quantity calibration will be performed during G3X system installation.
For capacitive fuel quantity measurement, a third-party capacitance-tofrequency or capacitance-to-voltage converter is required; the G3X system does not support direct connection to capacitive fuel tank probes.
190-01115-01
Rev. AN
G3X/G3X Touch Installation Manual - Engine/Airframe Sensor Installation
Page 24-14
Sensor Type
Control Surface
Position
Table 24-10 Retrofit Engine Sensors
Notes on Suitability for Reuse
Most potentiometer-type sensors can be used without modification. New position calibration will be performed during G3X system installation.
24.2.7 Turbine Engine Applications
Turbine Engines - Many turbine engines can be monitored using the supported engine sensors shown in
, along with custom engine sensor configuration as described in
displays. Turbine engines are not supported by the GDU 37X display.
Torque
Sensor Type
N1 / N2 RPM
Oil pressure
Oil temperature
Turbine inlet or outlet temperature
Table 24-11 Sensors for Turbine Engines
Details/Part Number
Two separate turbine engine RPM gauges can be displayed. Select
"Custom" configuration for GEA 24 RPM1 / RPM2 inputs and enter frequency-to-RPM calibration. A Sandia ST26 tachometer signal converter is typically required to provide proper digital signal conditioning.
Use Kavlico P4055-5020-4 (011-04202-30) for pressures under 150 PSI and enter pressure-to-torque calibration, or select "Custom" and enter voltage-to-torque calibration
Use any supported sensor from Table 24-1 , or select "Custom"
configuration and enter voltage-to-pressure calibration
Use any supported sensor from Table 24-1
Use Type K thermocouple
Fuel pressure
Fuel flow
Hydraulic pressure (or other pressure)
Other parameters
Use supported Kavlico or UMA pressure sensor, or select "Custom" configuration and enter voltage-to-pressure calibration
Use any supported sensor from Table 24-1 , or select "Custom"
configuration and enter pulses-per-gallon calibration
Use any supported sensor from Table 24-1 , or select "Custom"
configuration and enter voltage-to-pressure calibration
Use any supported sensor from Table 24-1
24.2.8 Twin-Engine Applications
A GDU 4XX system using two GEA 24 units can monitor data from two engines with up to 6 cylinders each. Engine #1 is connected to GEA 24 #1, and engine #2 is connected to GEA 24 #2. Data from both engines is presented on the same GDU display. Due to its larger display size, the GDU 46X is preferred over the GDU 45X or GDU 47X for twin-engine applications.
The two GEA 24s in a twin-engine installation use the same input configuration for analog and digital inputs, with a configuration choice to allow data for a particular input to be monitored from both GEA 24s, or from #1 only. The second GEA 24 may also be used to support additional discrete inputs. For information on configuring twin-engine sensor inputs, see
190-01115-01
Rev. AN
G3X/G3X Touch Installation Manual - Engine/Airframe Sensor Installation
Page 24-15
24.2.9 Rotorcraft Applications
Rotorcraft engine monitoring can be accomplished with a GDU 4XX system, using the engine sensor application information in
. Typically, the GEA 24 RPM 1 input is
used to monitor rotor RPM.
Sensor Type
Rotor RPM
Engine RPM
Other engine sensors
Table 24-12 Sensors for Rotorcraft Applications
Details
Select "Custom" configuration for GEA 24 RPM1 input and enter frequencyto-RPM calibration. A Sandia ST26 tachometer signal converter may be required to provide proper digital signal conditioning.
Select appropriate configuration for GEA 24 RPM 2 input as described in
through
.
Select appropriate sensors and configuration as described in
.
A GDU 4XX system using two GEA 24 units can be used to monitor engine information for a twin-engine
rotorcraft, as described in Section 24.2.8
24.2.10 FADEC Engine Status
When used with a digital interface to a FADEC engine, FADEC status and maintenance information can be viewed in configuration mode. To view FADEC status, access the configuration mode System
24-2) will vary based on the configured engine type.
Figure 24-2 Configuration Mode FADEC Interface Status
In normal mode, caution and warning indications from the FADEC interface are displayed in the form of
CAS messages. Refer to the G3X Touch Pilot’s Guide (190-01754-00) for further information.
190-01115-01
Rev. AN
G3X/G3X Touch Installation Manual - Engine/Airframe Sensor Installation
Page 24-16
24.3 Engine Sensor Installation
NOTE
The following sections contain general guidance on engine and airframe sensor installation. This information is provided for reference only. The installer should always follow any installation guidance and instructions provided by the applicable engine, sensor, or kit-plane manufacturer. Additionally, all installation practices should be done in accordance with AC 43.13-1B.
, and Section 33 contain interface drawings for sensor installations using
the Garmin sensor kits, and for other sensor installations.
24.3.1 CHT (Cylinder Head Temperature)
Both Type J and Type K grounded thermocouples are supported for cylinder head temperature (CHT) measurements. Type K thermocouples are more commonly used for CHT.
To maintain measurement accuracy, appropriate thermocouple extension wire must be used to connect the
CHT probe sensor wires directly to the inputs of the GEA 24/GSU 73. To minimize risk of breakage, it is recommended that a high-quality stranded (as opposed to solid) thermocouple wire be used. For Type K thermocouples, one such example of appropriate wire is TT-K-22S Type K thermocouple wire from Omega
Engineering.
Thermocouple extension wire lengths may vary between cylinders for installation convenience; there is no requirement to use the same length of thermocouple extension wire for each engine cylinder. However, for each individual thermocouple lead, the positive and negative wires should be the same length. When attaching thermocouple extension wire with splices or connectors, the connections for an individual pair of positive/negative wires should be located close together to ensure they are exposed to similar ambient temperatures.
NOTE
If ungrounded thermocouples are used, the low side must be connected to a GEA 24/
GSU 73 ground pin.
190-01115-01
Rev. AN
G3X/G3X Touch Installation Manual - Engine/Airframe Sensor Installation
Page 24-17
24.3.1.1 Lycoming/Continental CHT Sensor Installation
Garmin sensor kits for Lycoming and Continental engines include Alcor 86253 Type K thermocouple probes (Garmin P/N 494-70000-00). Refer to Alcor CHT Installation Instructions (P/N 59167) for complete installation details. Engine manufacturer’s guidance should always be consulted for proper location of CHT probes. A finger sized loop should be provided to allow sufficient strain relief of the probe assembly, and care should be taken to ensure that no chafing of the wires occurs.
Figure 24-3 CHT Probe Package
Figure 24-4 CHT Probe Well
190-01115-01
Rev. AN
G3X/G3X Touch Installation Manual - Engine/Airframe Sensor Installation
Page 24-18
Figure 24-5 One Piece CHT Probe Installed
24.3.2 EGT (Exhaust Gas Temperature)
Type K grounded thermocouples are supported for exhaust gas temperature (EGT) measurements.
NOTE
If ungrounded thermocouples are used, the low side must be taken to a GEA 24/ GSU 73 ground pin.
To maintain measurement accuracy, Type K thermocouple extension wire must be used to connect the EGT probe sensor wires directly to the inputs of the GEA 24/GSU 73. To minimize risk of breakage, it is recommended that a high quality stranded (as opposed to solid) thermocouple wire be used. One such example of appropriate wire TT-K-22S Type K thermocouple wire from Omega Engineering.
Thermocouple extension wire lengths may vary between cylinders for installation convenience; there is no requirement to use the same length of thermocouple extension wire for each engine cylinder. However, for each individual thermocouple lead, the positive and negative wires should be the same length. When attaching thermocouple extension wire with splices or connectors, the connections for an individual pair of positive/negative wires should be located close together to ensure they are exposed to similar ambient temperatures.
190-01115-01
Rev. AN
G3X/G3X Touch Installation Manual - Engine/Airframe Sensor Installation
Page 24-19
24.3.2.1 EGT Sensor Installation
General Installation Guidance – Garmin sensors kits include Alcor 86255 Type K thermocouple probes
(Garmin P/N 494-70001-00). Refer to Alcor EGT Installation Instructions (P/N 59180) for complete installation details. Engine manufacturer’s guidance should be consulted and followed for proper location of EGT probes.
Perform the following steps and refer to Figure 24-6
, Figure 24-7 , and Figure 24-8 to install an EGT
sensor.
1. EGT probes (Figure 24-6) should optimally be mounted a minimum 2 inches and a maximum of 4
inches from the cylinder exhaust port flange on a flat portion of the exhaust tube. For highly supercharged engines, the EGT probe should optimally be mounted a minimum 5 inches and a maximum of 7 inches from the cylinder exhaust port flange on a flat portion of the exhaust tube.
To maintain consistent readings across cylinders, all probes should be mounted an equal distance from the exhaust flanges.
2. Carefully center punch the probe hole locations so that the external portion of the probe does not interfere with any other parts of the engine or cowling (
Figure 24-7 ). It may be desirable to angle
the probes towards the rear of the engine to allow efficient wire routing back to the cockpit. If angling the probes towards the rear of the engine, take care to ensure that sufficient clearance is provided to service the spark plugs.
3. Carefully insert probe into the exhaust pipe and tighten the clamp snugly with screwdriver
(35 in-lbs torque max.).
4. Connect the EGT probes to the thermocouple extension wire. Provide strain relief for the assembly by either fastening the probe leads to the valve covers with a clamp, or by tying the extension wire to the intake tubes or other suitable location. A finger-sized loop should be provided to allow appropriate strain relief, and care should be taken to ensure that no chafing of the wires occurs. See
Figure 24-8 for an example of an installed EGT probe.
190-01115-01
Rev. AN
Figure 24-6 EGT Package
G3X/G3X Touch Installation Manual - Engine/Airframe Sensor Installation
Page 24-20
Figure 24-7 Exhaust Pipe Drilled
190-01115-01
Rev. AN
Figure 24-8 Installed EGT Probe Orientation
G3X/G3X Touch Installation Manual - Engine/Airframe Sensor Installation
Page 24-21
24.3.3 Oil Temperature
Oil temperature can be measured using the specific resistance temperature detector (RTD) and thermistor sensors listed in
24.3.3.1 Lycoming/Continental Oil Temperature Sensor Installation
Garmin sensor kits for Lycoming and Continental engines include the UMA 1B3-2.5R platinum RTD probe (Garmin P/N 494-70004-00). This probe is designed for oil temperature probe wells with 5/8-18 threads.
General Installation Guidance – Refer to the applicable engine manual for proper location of the oil temperature sensor. The sensor is usually installed near the oil filter.
1. Cut the safety wire and remove the existing vent plug (Figure 24-9), if installed.
2. To prevent galling of the threads, apply a small amount of engine oil to the probe threads.
3. Ensure that an unused copper crush gasket is present on the probe, and install the probe into the engine (black side of crush gasket down).
NOTE
Crush gaskets can only be used once. A new gasket must be installed any time the probe is removed and installed.
4. Tighten the probe to the torque as specified by the engine manufacturer.
5. Safety-wire the probe to the engine case as appropriate.
6. Connect the supplied connector to the appropriate inputs on the GEA 24/GSU 73 as referenced in the G3X interconnects in
Section 31 . Secure the connector and wire assembly to an appropriate
location in the engine compartment to provide strain relief.
Figure 24-9 Vent Plug Figure 24-10 Oil Temperature
Probe
Figure 24-11 Oil
Temperature Probe Installed
(Crush Gasket Not Shown)
190-01115-01
Rev. AN
G3X/G3X Touch Installation Manual - Engine/Airframe Sensor Installation
Page 24-22
24.3.4 Pressure (Fuel, Manifold, Oil, and Coolant)
Select the pressure sensor from
that is best suited for the aircraft system and installation location. Maximum system operating or surge pressures must not exceed the sensor's rated pressure.
General Mounting Methods – The specified pressure transducers provide for two different mounting options:
Figure 24-12 Pressure Transducer Mounting a) Sensor body secured to the engine mount or firewall via an appropriately sized Adel clamp
(preferred)
OR b) Mounted to a transducer mounting block located on the firewall. UMA sensor mounting may require the use of a stainless steel AN911 fitting (union).
WARNING
The sensor must not be mounted directly to the engine. Mechanical failure of the sensor could result in leaks and loss of pressure.
WARNING
Test all fuel, oil, and coolant pressure sensors for leakage following installation and prior to flight.
Installation Guidance:
1. Hoses and fittings - Fuel and oil hoses installed in the engine compartment should meet TSO-C53a
Type C or D (fire resistant) and rated for the pressure, temperature, and be compatible with the fuel or oil. Sensor hoses must be routed as far away from the aircraft exhaust system as practical and no closer than 6 inches. Fittings should be AN/AS-spec or Mil-spec.
2. Sensors - Do not install sensors directly below fittings or components that may leak flammable fluid. To prevent water from settling in the fuel pressure sensor and causing freeze damage, install sensor with the electrical connector angling upward or with a hose/line with an upward bend that will trap heavier water before entering the sensor.
190-01115-01
Rev. AN
G3X/G3X Touch Installation Manual - Engine/Airframe Sensor Installation
Page 24-23
3. Routing - Line fittings, routing, alignment, bonding, and support spacing should be installed as defined in the aircraft maintenance manual or Section 8-31 of AC 43.13-1B, Aircraft Inspection and Repair
4. Mount the sensor using one of the two methods noted above.
5. Refer to the applicable engine manual to identify the appropriate connecting port on the engine for the parameter being sensed. The male threads on Kavlico sensors are designed to mate with a 1/8”
NPT female thread. The female threads on UMA sensors are designed to mate with a 1/8” NPT male thread. Thread sealant or tape should be used for the NPT threads. To reduce the risk of system contamination, a minimal amount of sealant or tape should be applied leaving at least two threads at the end of the fitting clear of all sealant/tape.
WARNING
The fuel and oil pressure fittings on the engine port should have a restrictor hole where appropriate to minimize potential fluid loss in the event of breakage.
NOTE
A restrictor or snubber fitting (not available from Garmin) may be installed (between the hose and the sensor) to dampen manifold pressure fluctuations. One example is the PS-8G fitting from Omega Engineering.
6. Connect the supplied connector to the appropriate inputs of the GEA 24/GSU 73 as referenced in
the Sensor Interface Drawings in Section 31 through
. Secure the connector and wire assembly to an appropriate location in the engine compartment to provide strain relief.
NOTE
Kavlico P4055 pressure sensors use Packard Metri-Pack 150 connectors.
7. To avoid fuel pressure sensor damage or rupture, verify the aircraft fuel system nominal and surge pressures will not exceed the rated operating pressure of the sensor. Verify that pressure caused by thermal expansion of fuel in the pressure sensor line is not trapped by the fuel shut-off valve or other components.
190-01115-01
Rev. AN
G3X/G3X Touch Installation Manual - Engine/Airframe Sensor Installation
Page 24-24
24.3.5 RPM (Revolutions Per Minute)
24.3.5.1 Lycoming/Continental RPM Sensor Installation
The following two types of mechanical RPM sensors are supported:
UMA 1A3C-2, UMA 1A3C-4 Standard mechanical tach drive sensors
The standard mechanical tach drive sensor is installed on the engine accessory case:
1. Remove the cap from the tachometer drive output (Figure 24-13) from the back of the engine.
2. Insert adapter tang into slotted keyway in sensor drive port.
3. Screw tach sensor onto threaded driver port, ensuring that the adapter tang on the sensor aligns with the slotted keyway in the drive port (Figure 24-14).
4. Connect the supplied connector to the appropriate inputs on the GEA 24/GSU 73 as referenced in the G3X interconnects in Section 31 . Secure the connector and wire assembly to an appropriate location in the engine compartment to provide strain relief.
The body of the sensor unit can be offset slightly to eliminate potential interference with other engine accessories. If the interference cannot be alleviated by offsetting the sensor directly, the builder may either install a magnetic pickup sensor or use a short tachometer drive extension cable to remote mount the sending unit to the engine mount (or other suitable location)
Figure 24-13 Tachometer Drive Output Figure 24-14 Installed Tachometer Sensor
190-01115-01
Rev. AN
G3X/G3X Touch Installation Manual - Engine/Airframe Sensor Installation
Page 24-25
UMA N/T1A9-X, JPI 4208XX - Magnetic pickup tach sensors:
The magnetic pickup tach sensor is installed in the magneto bleed port. It is recommended that it be installed in the non-impulse magneto, but it can be installed in the impulse magneto if only one magneto exists (engines with single electronic ignition). The UMA N/T1A9-X sensors are suitable for nonpressurized magnetos only. JPI 4208XX RPM sensors are available in different versions for both pressurized and non-pressurized magnetos. Given that the bleed port size on Slick and Bendix magnetos differ, the installer should verify that the sensor part number is appropriate for the magneto type.
1. Remove the existing vent plug from the magneto bleed port (Figure 24-15).
2. Lightly apply thread sealer such as Loctite 242 (or equivalent) to the threads of the sensor. Be careful not to apply too much, and ensure sealer is applied only to the threads and not the pickup face itself.
3. Install the sensor into the port ( Figure 24-17 ). The sensor should be installed finger tight plus 1/6 turn. Do not over-tighten.
4. Connect the supplied connector to the appropriate inputs on the GEA 24/GSU 73 as referenced in the G3X interconnects in
Section 31 . Secure the connector and wire assembly to an appropriate
location in the engine compartment to provide strain relief.
Figure 24-15 Magneto Bleed Port
NOTE
There are two plugs on a Slick/Unison 43xx series magneto (Figure 24-16) where the tach
sender could fit. The one closest to the rotating magnet, with the hex-shaped plug, is correct. The one on the opposite side, with a round plug, is incorrect.
CORRECT TACH SENSOR PORT
190-01115-01
Rev. AN
WRONG PORT
CORRECT TACH
SENSOR PORT
WRONG PORT
Figure 24-16 Plugs on Slick/Unison 43XX Magneto
G3X/G3X Touch Installation Manual - Engine/Airframe Sensor Installation
Page 24-26
Figure 24-17 Magneto Tach Sensor Installed
24.3.5.2 Electronic Ignition RPM
For engines with electronic ignition, RPM can be sensed via a digital tach signal output from the electronic ignition system. The G3X system provides configurations for ignition systems that output 1 through 4 pulses per crankshaft revolution, or a custom RPM input configuration may be used to accommodate other types of electronic ignition.
Aircraft with dual electronic ignition systems can connect the tachometer signal output from the second
ignition to the GEA 24/GSU 73 RPM2 input (see Figure 31-2
). The RPM value displayed on the RPM gauge will be the higher of the two RPM signals.
NOTE
Electronic ignition systems with open-collector tachometer signal outputs may require a pull-up resistor between the tachometer signal output and +5VDC or +12VDC.
190-01115-01
Rev. AN
G3X/G3X Touch Installation Manual - Engine/Airframe Sensor Installation
Page 24-27
24.3.5.3 P-Lead RPM Sensing
CAUTION
Only a MOD Level 2 GEA 24 can be connected directly to a P-Lead. Do not connect
MOD Level 1 or MOD Level 0 units directly to a P-Lead. The MOD Level status can be determined by checking the serial tag on the unit.
For a direct connection, the GEA 24 measures the electrical signal generated by the primary magneto coils or “P-Leads” from both engine magnetos. The connections can be made to the magneto P-Lead stud or to the P-Lead wire at the ignition switch as shown in
Figure 31-4 . If the magneto does not have a ring
terminal stud, connect the GEA 24 to the ignition switch. Otherwise, connect it to whichever minimizes the wire length to the GEA 24.
When making a connection directly to a P-Lead, a 400kΩ (±10%) resistor needs to be installed. To prevent
between the P-Lead connection and the resistor must not exceed six inches. Shielded wires must be used.
Use a resistor that is 400K ohm (±10%), 0.5W, rated to maintain resistance and power rating at 150°C, and qualified to MIL-R-10509.
Following the installation of the P-Lead signal wires, verify the continuity of each magneto P-Lead to airframe ground while the ignition key is OFF. If there is evidence of discontinuity in the magneto P-Lead grounding circuit, it must be corrected before further engine maintenance or checks. Continuity can only be measured if the magneto points are open or the wire is disconnected from the magneto. Use a magneto timing light to ensure the ohmmeter will not measure false continuity through the points or coil windings.
WARNING
Do not turn the propeller and stay clear of the propeller arc when installing the P-Lead signal wires.
190-01115-01
Rev. AN
G3X/G3X Touch Installation Manual - Engine/Airframe Sensor Installation
Page 24-28
24.3.6 Fuel Quantity
24.3.6.1 Resistive Type Fuel Quantity Sensors
Resistive type fuel quantity sensors with a 0–500 Ω range are currently supported. Wiring methods vary based on the GEA 24/GSU 73 channel being used. Please see
for proper wiring considerations.
CAUTION
For composite and tube-and-fabric airframe installations that include a GEA 24, it is recommended to install 2 - 2.2 kΩ resistors as shown in
grounding path in the event of lightning strike. This is optional for metal aircraft, either wiring method can be used. The additional components have no effect on GSU 73 fuel inputs. When in-line resistors are installed, use "Voltage" configuration setting, if in-line resistors are not installed, use "Resistive" configuration setting.
24.3.6.2 Capacitive Type Fuel Quantity Sensors
Capacitive fuel quantity sensors require the use of an external transducer to convert capacitance to either a frequency or a voltage.
Fuel quantity transducers that convert capacitance to a voltage of up to 28V may be used, including 0-5V and 0-12V transducers. Examples of this type of transducer include the Skysports and Westach units.
Voltage-output fuel quantity transducers may be connected to any of the four fuel quantity inputs on the
GEA 24, or to any of the four analog fuel quantity inputs on the GSU 73 (FUEL 1/2/3/4).
Fuel quantity transducers that convert capacitance to a frequency of up to 50 kHz may be used. Examples of this type of transducer include the Princeton, Vision Microsystems, and EI P-300C units. The transducer's output waveform must meet the requirements of the GEA 24/GSU 73 digital inputs (see
for the GEA 24 and Section 26.15.8
for the GSU 73). When using a GEA 24, frequencyoutput fuel quantity transducers may be connected to any of the four fuel quantity inputs (FUEL 1/2/3/4).
When using a GSU 73, frequency-output fuel quantity transducers must be connected to the two digital fuel quantity inputs (CAP FUEL 1/2).
NOTE
Vision Microsystems capacitive level senders used with a GSU 73 may require installing a
5 kΩ pull-down resistor at the sensor output.
NOTE
The GEA 24 and GSU 73 can provide +5V or +12V excitation voltage to capacitive fuel quantity transducers. The power supply output pins on the GEA 24 and GSU 73 are designed for low-current transducers only. Transducers that require higher supply currents, including Princeton capacitive fuel quantity transducers, may require power to be supplied from the aircraft electrical bus instead.
190-01115-01
Rev. AN
G3X/G3X Touch Installation Manual - Engine/Airframe Sensor Installation
Page 24-29
24.3.7 TIT (Turbine Inlet Temperature) Sensor
The G3X system supports Type K grounded thermocouples for sensing turbine inlet temperature (TIT), turbine outlet temperature (TOT), or inter-turbine temperature (ITT). This type of sensor is applicable to all turbocharged or turbine engines.
To maintain measurement accuracy, appropriate thermocouple extension wire must be used to connect the
TIT probe sensor wires directly to the inputs of the GEA 24/GSU 73. To minimize risk of breakage, it is recommended that a high-quality stranded (as opposed to solid) thermocouple wire be used. For Type K thermocouples, one such example of appropriate wire is TT-K-22S Type K thermocouple wire from Omega
Engineering. When attaching thermocouple extension wire with splices or connectors, the connections for an individual pair of positive/negative wires should be located close together to ensure they are exposed to similar ambient temperatures.
NOTE
If ungrounded thermocouples are used, the low side must be connected to a GEA 24/
GSU 73 ground pin.
24.3.8 Bus Voltage Monitor
Bus voltage is normally sensed from an external voltage signal connected to a GEA 24/GSU 73 analog
for interface drawings). Optionally, the GEA 24/GSU 73 can be configured to measure bus voltage without requiring an external connection, by sensing the voltage of its power supply
inputs. See Voltage portion of Section 34.4.19.3.2
for GDU 37X systems and Section 35.4.32.14
4XX systems (Volts 1 and Volts 2 Inputs) for configuration guidance.
190-01115-01
Rev. AN
G3X/G3X Touch Installation Manual - Engine/Airframe Sensor Installation
Page 24-30
24.3.9 Bus Current
Electrical current can be sensed by the G3X system either by Hall Effect current sensors or via the use of a traditional ammeter shunt.
24.3.9.1 Ammeter Shunt Installation
The UMA 1C4 ammeter shunt included in Garmin sensor kits (Garmin P/N 909-D0000-00) is a 100 Amp/
50 mv shunt. Other ammeter shunts with different specifications can be supported via calibration
adjustments. See Current portion of Section 34.4.19.3.2
for GDU 37X systems and Section 35.4.32.15
GDU 4XX systems (Volts 1 and Volts 2 Inputs) for configuration guidance.
General Installation Guidance – The ammeter shunt has two holes in the base for mounting with #10 screws. The current-carrying wires are attached to the large 1/4” lugs, while the current sense wires are attached via the use of #8 ring terminals.
Figure 24-18 Ammeter Shunt
NOTE
It is important that no metal portion of the shunt touch any other portion of the aircraft or exposed wiring. Large voltages and current are present in the shunt, and an electrical short or fire could result from inadvertent contact.
The shunt should be installed in-line with the current being sensed. As noted below, the appropriate wire should be cut and attached to each of the large ¼” lugs. A 1A fuse or other form of circuit protection must be installed between the shunt and the applicable GEA 24/GSU 73 inputs to prevent inadvertent damage to the GEA 24/GSU 73. Connect the two sense wires (attached to the #8 terminals) to the appropriate inputs on the GEA 24/GSU 73 as referenced in the G3X interconnects in
. If the ammeter readings are shown with the opposite polarity, check to see if the sense wire connections are reversed.
An alternator ammeter shunt should be installed inline in the alternator output (“B” terminal). A battery ammeter shunt should be installed between the battery positive terminal and the battery contactor.
Depending on the location of the alternator or battery relative to its supported electrical bus, it is typically desirable to install the shunt on the firewall near where the alternator or battery output would normally penetrate the firewall.
190-01115-01
Rev. AN
G3X/G3X Touch Installation Manual - Engine/Airframe Sensor Installation
Page 24-31
24.3.9.2 Hall Effect Current Sensor
Hall Effect current sensors can be used to sense electrical current via induced magnetic fields, without direct connection to high-current conductors.
The default Hall Effect current sensor supported by the G3X system is the AMPLOC KEY100. This sensor outputs 2.5V at zero amps, with a sensitivity of 15.9 mV/Amp up to +/- 100A. Other Hall Effect sensors with different specifications can be supported via calibration adjustments. See Current portion of
for GDU 37X systems and Section 35.4.32.15
for GDU 4XX systems for configuration
guidance.
24.3.10 Fuel Flow
Fuel flow in the G3X system is sensed via a mechanical transducer which converts the movement of fuel to a series of digital pulses.
For engines with a fuel return line, a second flow sensor must be used to measure the quantity of unused fuel that is returned from the engine to the fuel tank. Connect the return fuel flow sensor to the GEA 24/
GSU 73 FUEL FLOW 2 input (see Figure 30-2.1
). The value displayed on the fuel flow gauge will be the difference between the main (supply) fuel flow and secondary (return) fuel flow measurements.
24.3.10.1 K-Factor Adjustment
The number of electrical pulses sensed per gallon of fuel flow is referred to as the K-Factor. The G3X system uses the configured K-Factor to convert pulse frequency to fuel flow. When installing the fuel flow sensor, the installer should take note of number on the tag attached to the sensor (if applicable). This number is the calibrated K-Factor of the sensor. For sensors that are not supplied with a specific calibration value, use the default K-Factor value provided.
Although each fuel flow sensor has a default K-Factor value, aspects unique to each installation will affect the accuracy of the initial K-Factor, and as a result the K-Factor must generally be adjusted up or down for accurate fuel flow measurement.
If the fuel usage reported by the G3X system differs from the actual fuel usage, as measured at the fuel pump (or other trusted method of measurement), use the following formula to calculate a corrected
K-Factor, which can then be used to calibrate the fuel flow.
Corrected K-Factor = ( [G3X reported fuel used] x [previous K-factor] ) / [actual fuel used]
Refer to the K-Factor portion of
for (GDU 37X) or Section 35.4.32.13
(for GDU 4XX) for information on entering K-Factor calibration.
24.3.10.2 Electronics International Fuel Flow Sensor Installation
Garmin sensor kits include the Electronics International FT-60 “red cube” fuel flow sensor (Garmin P/N
494-10001-00). Refer to Electronics International document # 1030032 for FT-60 installation guidance.
The default K-Factor for the FT-60 is 68,000 pulses/gallon. No sensor specific calibration is required for the FT-60, but variations in the installation can affect the K-Factor as described above.
Other Electronics International FT-series fuel flow sensors are also supported; consult the manufacturer for installation guidance.
190-01115-01
Rev. AN
G3X/G3X Touch Installation Manual - Engine/Airframe Sensor Installation
Page 24-32
24.3.10.3 Floscan Fuel Flow Sensor Installation
The information below is taken from the Floscan Series 200 Flow Transducer Application Notes:
1. The inlet and outlet ports in series 200 flow transducers have ¼” NPT threads. Use only ¼” NPT hose or pipe fittings to match. When assembling fittings into the inlet and outlet ports, DO NOT
EXCEED a torque of 15 ft. lbs. (180 inch lbs.), or screw the fittings in more than 2 full turns past hand tight WHICHEVER HAPPENS FIRST. Floscan Instrument Co., Inc. will not be responsible for cracked castings caused by failure to use ¼” NPT fittings, over-torquing the fittings, or assem- bling them beyond the specified depth.
2. A screen or filter should be installed upstream of the flow transducer to screen out debris which could affect rotor movement or settle in the V-bearings. As turbulence upstream of the transducer affects its performance, there should be a reasonable length of straight line between the transducer inlet and the first valve, elbow, or other turbulence producing device.
3. Install the flow transducer with wire leads pointed UP to vent bubbles and ensure that the rotor is totally immersed in liquid. For maximum accuracy at low flow rates, the transducer should be mounted on a horizontal surface.
Some additional mounting considerations should be noted as follows:
1. When installing the NPT fittings into the transducer, use fuel lube such as EZ TURN © or an equivalent thread sealer. Teflon tape should NEVER by used in a fuel system.
2. To minimize inaccuracies caused by turbulence in the fuel flow, the sensor should be mounted with approximately 5-6” of straight tubing before and after the sensor. If special circumstances exist that prevent an extended length of straight tubing before and after the sensor, then a gently curved hose may be acceptable. 45 degree or 90 degree elbow fittings should NOT be used immediately before or after the sensor.
3. Specific sensor mounting location is left to the builder. Ideally, the sensor should be placed prior to the fuel distribution device (carburetor or fuel injection distribution device).
4. On a Continental fuel injected engine, the transducer must be located between the metering unit and the flow divider valve.
5. Sensor wires should be connected to the appropriate inputs on the GEA 24/GSU 73 as referenced
in the G3X interconnects in Section 30
.
The Floscan 201B-6 (201-030-000) fuel flow sensor K-Factor value can range from 28,000 to 31,000 pulses/ gallon.
190-01115-01
Rev. AN
G3X/G3X Touch Installation Manual - Engine/Airframe Sensor Installation
Page 24-33
The G3X default K-Factor for the 201B-6 is 29,500 pulses/gallon. Some Floscan fuel flow sensors come with a tag that lists the K-factor number measured during unit calibration (see Figure 24-19).
NOTE
If the Floscan tag shown in Figure 24-19 is lost, the serial number of the Floscan sensor can be supplied to Floscan to obtain the calibrated K-factor value.
Actual K Factor measured at
16 GPH
Figure 24-19 Example Floscan Fuel Flow Sensor
The tag shown in Figure 24-19 lists a K-Factor of 16-2890. The first two digits (16) represent Gallons Per
Hour, while the last four digits (2890) represent the number of electrical pulses (divided by 10) output by the sensor per gallon of fuel flow. The numbers on the tag are used in determining the K-Factor to be entered as part of the Fuel Flow Calibration described in Section 34.4.19.4 (for GDU 37X) and
(for GDU 4XX). To determine this number, a zero should be added to the four digit number on the tag. In the example above after adding the zero to 2890, the resulting K-Factor to be entered on the Fuel Flow Calibration page would be 28900.
190-01115-01
Rev. AN
G3X/G3X Touch Installation Manual - Engine/Airframe Sensor Installation
Page 24-34
24.3.11 Carburetor Temperature Sensor
24.3.11.1 Lycoming and Continental Engine Sensor Installation
The UMA 1B10R platinum resistance temperature detector (RTD) is applicable to all carbureted
Lycoming and Continental engines that accept a temperature probe with ¼-28 threads.
General Installation Guidance:
1. Locate and remove the threaded ¼-28 brass plug (Figure 24-20 and Figure 24-21) on the side of the carburetor as shown in Figure 24-20. If a threaded plug is not present (as is the case with many older carburetors), consult the engine and/or carburetor manufacturer for instructions on how to drill and tap the lead plug adjacent to the butterfly valve.
2. Install a very small amount of thread lubricant on the probe threads and insert into the carburetor
(Figure 24-22).
3. Connect the supplied connector to the appropriate inputs of the GEA 24/GSU 73 as referenced in
the G3X interconnects in Section 31
. Secure the connector and wire assembly to an appropriate location in the engine compartment to provide strain relief.
Figure 24-20 Carb Temp
Sensor Mounting Location
Figure 24-21 Carb Temp
Sensor Mounting Location w/Screw Removed
Figure 24-22 Carb Temp
Sensor Installed
24.3.12 Position Sensor
In general, most potentiometer-type resistive position sensors can be used with the G3X system. Typically these sensors take the form of a 0–5k Ω or 0–10k Ω variable resistor. Electric trim motors with integrated position potentiometers do not require separate position sensors.
Each position sensor installation will vary widely according to the aircraft, motion being sensed, and mechanical installation. A standalone position sensor should ideally be mounted such that the full travel of the sensor is just slightly greater than the full travel of the control surface.
Refer to the appropriate trim motor or position sensor installation manual and G3X interconnects in
Section 30 for proper wiring connections. Section 34.4.19.3.2 (for GDU 37X systems) and
Section 35.4.27.1 (for GDU 4XX systems) provides calibration instructions.
190-01115-01
Rev. AN
G3X/G3X Touch Installation Manual - Engine/Airframe Sensor Installation
Page 24-35
25 CONNECTOR INSTALLATION INSTRUCTIONS
NOTE
Ensure that backshell connectors are fully tightened. Loose connectors may cause vibration-related performance issues that are difficult to troubleshoot.
25.1 Cable Connector Installation
Coaxial cables are required for antenna connections for GPS, XM, transponder, comm, VHF Nav, ADS-B, and video functions.
1. Route the coaxial cable to the unit location. Secure the cable in accordance with good aviation practices.
2. Trim the coaxial cable to the desired length and install the BNC or TNC connector per the connector manufacturer’s instructions for cable preparation.
25.2 Jackscrew Backshell Assembly
25.2.1 Shield Block Installation Parts
. Parts listed in Table 25-1 are supplied in the LRU Connector Kits (see
). Parts listed in Table 25-2 are to be provided by the installer.
Table 25-1 Parts supplied for a Shield Block Installation ( Figure 25-1 )
Item #
1
6
12
13
14
15
Description
Cast Backshell Housing
Contacts
Clamp
Screw,4-40x.375,PHP,SS/P,w/Nylon
Cover
Screw,4-40x.187,FLHP100,SS/P,w/Nylon
GPN or MIL spec
125-00175-00
336-00094-00
115-01078-04
211-60234-10
115-01079-04
211-63234-06
Item #
2
3
4
5
Table 25-2 Parts not supplied for a Shield Block Installation ( Figure 25-1
)
Description
Multiple Conductor Shielded Cable (2-conductor shown in
)
Drain Wire Shield Termination (method optional)
Braid, Flat (19-20 AWG equivalent, tinned plated copper strands
36 AWG, Circular Mil Area 1000 -1300)
Floating Shield Termination (method optional)
GPN or MIL spec
Parts used depend on method chosen
Parts used depend on method chosen
Parts used depend on method chosen
Parts used depend on method chosen
190-01115-01
Rev. AN
G3X/G3X Touch Installation Manual - Connector Installation Instructions
Page 25-1
Item #
7
8
9
10
11
Table 25-2 Parts not supplied for a Shield Block Installation ( Figure 25-1 )
Description
Ring terminal, #8, insulated, 18-22 AWG
Ring terminal, #8, insulated, 14-16 AWG
Ring terminal, #8, insulated, 10-12 AWG
Screw, PHP, 8-32x.312", Stainless
Screw, PHP, 8-32x.312", Cad Plated Steel
Split Washer, #8, (.045" compressed thickness) Stainless
Split Washer, #8, (.045" compressed thickness) Cad-plated steel
Flat Washer, Stainless, #8, .032" thick, .174"ID, .375" OD
Flat washer, Cad-plated Steel, #8, .032" thick, .174"ID, .375" OD
Silicon Fusion Tape
GPN or MIL spec
MS25036-149
MS25036-153
MS25036-156
MS51957-42
MS35206-242
MS35338-137
MS35338-42
NAS1149CN832R
NAS1149FN832P
-
NOTE
In Figure 25-1, “AR” denotes quantity “As Required” for the particular installation.
190-01115-01
Rev. AN
G3X/G3X Touch Installation Manual - Connector Installation Instructions
Page 25-2
Figure 25-1 Shield Install onto a Jackscrew Backshell (78 pin example)
25.2.2 Backshell Assembly (refer to Figure 25-1)
1. Insert the crimped wire harness contacts (6) into the D-sub connector.
2. Wrap the cable bundle with silicone fusion tape (11) where the strain relief clamps the bundle.
3. Place the smooth side of the backshell strain relief clamp (12) across the cable bundle.
4. Secure strain relief with three 4-40 x 0.375 pan head screws (13).
5. Attach the cover (14) to the backshell using the supplied screws (15).
190-01115-01
Rev. AN
G3X/G3X Touch Installation Manual - Connector Installation Instructions
Page 25-3
6. Install a ring terminal onto the cable shield drains, grouping wires as appropriate for the connector.
See following note.
7. Place the following items on the 8-32 x 0.312 pan head shield terminal screw (8) in the order they are presented.
a) Split washer (9) b) Flat washer (10) c) First ring terminal (7) d) Second ring terminal (if necessary)
8. Insert the pan head shield terminal screw (8) into a tapped hole on the shield block.
NOTE
Each tapped hole on the shield block may accommodate up to two ring terminals. It is preferred that only two wires be terminated per ring terminal. This necessitates the use of a #8 ring terminal, insulated, 14-16 AWG (MS25036-153). If only a single wire is left or if only a single wire is needed for this connector, a #8 ring terminal, insulated, 18-22 AWG
(MS25036-149) can be used. If more wires exist for the connector than two per ring terminal, it is permissible to terminate a maximum of three wires per ring terminal.
9. Secure connector to mating connector on avionics device using the knurled thumb screws. The end of each thumb screw accepts a 3/32” hex wrench (
) to aid in securing the connector.
190-01115-01
Rev. AN
G3X/G3X Touch Installation Manual - Connector Installation Instructions
Page 25-4
25.2.3 Shield Termination Technique – Method A.1 (Standard)
NOTE
For the following steps please refer to Figure 25-1
1. The appropriate number of Jackscrew Backshells will be included in the particular LRU connector kit.
Figure 25-2 Method A.1 for Shield Termination
Backshell
1
2
3
4
5
-
Table 25-3 Shielded Cable Preparations for Garmin Connectors
Number
Std/HD
9/15
15/26
25/44
37/62
50/78
1.25
1.5
1.5
1.5
1.5
2.25
2.5
2.5
2.5
2.5
1.75
2.0
2.0
2.0
2.0
Window
(inches)
2.75
3.0
3.0
3.0
3.0
Window
(inches)
5.25
5.5
5.5
5.5
5.5
Ideal
(inches)
4.25
4.5
4.5
4.5
4.5
2. At one end of a shielded cable (item 2, Figure 25-1 ) measure a distance between “Window Min” to
“Window Max” (Table 25-3) and cut a window (max size 0.35”) in the jacket to expose the shield
(item 4, Figure 25-2). Use caution when cutting the jacket to avoid damaging the individual braids
of the shield. When dealing with a densely populated connector with many cables, it may prove beneficial to stagger the windows throughout the “Window Min” to “Window Max” range. If staggering is not needed the “Ideal Window” length is recommended.
Suggested tools to accomplish the window cut:
• Coaxial Cable Stripper
• Thermal Stripper
• Sharp Razor Blade
190-01115-01
Rev. AN
G3X/G3X Touch Installation Manual - Connector Installation Instructions
Page 25-5
3. Connect a Flat Braid (item 4, Figure 25-2 ) to the shield exposed through the window of the
prepared cable assembly (item 2, Figure 25-1 ) from step 2. The Flat Braid should go out the front
of the termination towards the connector. It is not permitted to exit the rear of the termination and loop back towards the connector (
). Make this connection using an approved shield termination technique.
NOTE
FAA AC 43.13-1B Chapter 11, Section 8 (Wiring Installation Inspection Requirements) may be a helpful reference for termination techniques.
Preferred Method:
Slide a solder sleeve (item 3,
Figure 25-1 ) onto the prepared cable assembly (item 2, Figure 25-1
) and connect the Flat Braid (item 4,
) to the shield using a heat gun approved for use with solder sleeves. It may prove beneficial to use a solder sleeve with a pre-installed Flat Braid versus having to cut a length of Flat Braid to be used. The chosen size of solder sleeve must
accommodate both the number of conductors present in the cable and the Flat Braid (item 4, Figure
Solder Sleeves with pre-installed Flat Braid
A preferred solder sleeve would be the Raychem S03 Series with the thermochromic temperature indicator (S03-02-R-9035-100, S03-03-R-9035-100, S03-04-R-9035-100). These solder sleeves come with a pre-installed braid and effectively take the place of items 3 and 4,
Figure 25-2 . For detailed instructions on product use, reference Raychem installation
procedure RCPS 100-70.
Raychem recommended heating tools:
•HL1802E
•AA-400 Super Heater
•CV-1981
•MiniRay
•IR-1759
Individual solder sleeves and Flat Braid
Solder Sleeves:
Reference the following MIL-Specs for solder sleeves.
(M83519/1-1, M83519/1-2, M83519/1-3, M83519/1-4, M83519/1-5)
Flat Braid:
If the preferred Raychem sleeves are not being used, the individual flat braid selected should conform to ASTMB33 for tinned copper and be made up of 36 AWG strands to form an approximately 19-20 AWG equivalent flat braid. A circular mil area range of 1000 to 1300 is required. The number of individual strands in each braid bundle is not specified. (e.g.
QQB575F36T062)
NOTE
Flat Braid as opposed to insulated wire is specified in order to allow continuing air worthiness by allowing for visual inspection of the conductor.
190-01115-01
Rev. AN
G3X/G3X Touch Installation Manual - Connector Installation Instructions
Page 25-6
Secondary Method:
Solder a Flat Braid (item 4, Figure 25-2 ) to the shield exposed through the window of the prepared
cable assembly (item 2,
). Ensure a solid electrical connection through the use of acceptable soldering practices. Use care to avoid applying excessive heat that burns through the insulation of the center conductors and shorts the shield to the signal wire. Slide a minimum 0.75
inches of Teflon heat shrinkable tubing (item 3, Figure 25-2
) onto the prepared wire assembly and shrink using a heat gun. The chosen size of heat shrinkage tubing must accommodate both the number
of conductors present in the cable and the Flat Braid (item 4, Figure 25-2 ) to be attached.
Teflon Heat Shrinkable Tubing:
Reference the following MIL-Spec for Teflon heat shrinkable tubing (M23053/5-X-Y).
4. At the same end of the shielded cable (item 2, Figure 25-1
) and ahead of the previous shield
termination, strip back “Float Min” to “Float Max” ( Table 25-3
) length of jacket and shield to
optimally.
Preferred Method:
The jacket and shield should be cut off at the same point so no shield is exposed. Slide 0.75 inches
minimum of Teflon heat shrinkable tubing (item 5, Figure 25-2 ) onto the cable and use a heat gun
to shrink the tubing. The chosen size of heat shrinkage tubing must accommodate the number of conductors present in the cable.
Secondary Method:
Leave a max 0.35 inches of shield extending past the jacket. Fold this 0.35 inches of shield back
over the jacket. Slide a solder sleeve (item 5, Figure 25-2
) over the end of the cable and use a heat gun approved for solder sleeves to secure the connection. The chosen size of solder sleeve must accommodate the number of conductors present in the cable.
5. Strip back approximately 0.17 inches of insulation from each wire of the shielded cable (item 2,
the installer to determine the proper length of insulation to be removed. Wire must be visible in the inspection hole after crimping and the insulation must be 1/64 – 1/32 inches from the end of the
contact as shown in Figure 25-3.
6
190-01115-01
Rev. AN
2
Figure 25-3 Insulation/Contact Clearance
G3X/G3X Touch Installation Manual - Connector Installation Instructions
Page 25-7
NOTE
For the item numbers in the following steps 6-13 please refer to Figure 25-1 ..
6. Insert newly crimped pins and wires into the appropriate connector housing location as specified by the installation wiring diagrams.
7. Cut the Flat Braid (item 4) to a length that, with the addition of a ring terminal, will reach one of the tapped holes of the Jackscrew backshell (item 1). An appropriate amount of excess length without looping should be given to the Flat Braid (item 4) to allow it to freely move with the wire bundle.
NOTE
Position the window splice to accommodate a Flat Braid (item 4) length of no more than 4 inches.
8. Guidelines for terminating the newly cutoff Flat Braid(s) (item 4) with insulated ring terminals
(item 7):
• Each tapped hole on the Jackscrew Backshell (item 1) may accommodate only two ring terminals (item 7).
• It is preferred that only two Flat Braid(s) (item 4) be terminated per ring terminal. Two Flat
Braids per ring terminal will necessitate the use of a Ring terminal, #8, insulated, 14-16
AWG (MS25036-153).
• If only a single Flat Braid is left or if only a single Flat Braid is needed for this connector a
Ring terminal, #8, insulated, 18-22 AWG (MS25036-149) can accommodate this single Flat
Braid.
• If more braids exist for this connector than two per ring terminal, it is permissible to terminate three braids per ring terminal. This will necessitate the use of a Ring terminal, #8, insulated, 10-12 AWG (MS25036-156).
9. Repeat steps 2 through 8 as needed for the remaining shielded cables.
10. Terminate the ring terminals to the Jackscrew Backshell (item 1) by placing items on the Pan Head
Screw (item 8) in the following order: Split Washer (item 9), Flat Washer (item 10) first Ring
Terminal, second Ring Terminal (if needed) before finally inserting the screw into the tapped holes on the Jackscrew Backshell. Do not violate the guidelines presented in Step 8 regarding ring terminals.
11. It is recommended to wrap the cable bundle with Silicone Fusion Tape (item 11)
(GPN: 249-00114-00 or a similar version) at the point where the backshell clamp and cast housing will contact the cable bundle.
NOTE
Choosing to use this tape is the discretion of the installer.
12. Place the smooth side of the backshell clamp (item 12) across the cable bundle and secure using the three screws (item 13). Warning: Placing the grooved side of the clamp across the cable bundle may risk damage to wires.
13. Attach the cover (item 14) to the backshell (item 1) using the two screws (item 15).
190-01115-01
Rev. AN
G3X/G3X Touch Installation Manual - Connector Installation Instructions
Page 25-8
25.2.4 Shield Termination Technique - Method A.2 (Daisy Chain)
In rare situations where more braids need to be terminated for a connector than three per ring terminal it is allowable to daisy chain a maximum of two shields together before coming to the ring terminal
Method A.1 are still applicable.
NOTE
The maximum length of the combined braids should be approximately 4 inches.
Figure 25-4 Method A.2 (Daisy Chain) for Shield Termination
190-01115-01
Rev. AN
G3X/G3X Touch Installation Manual - Connector Installation Instructions
Page 25-9
25.2.5 Shield Termination – Method B.1 (Quick Term)
If desired, the drain wire termination (item 3,
) and the floating shield termination (item 5,
) can be effectively combined into a “Quick Term”. This method eliminates the float in the cable insulation and moves the placement of the window which was described by the dimensions “Window
Min” and “Window Max” from Method A. This technique is depicted in
.
NOTE
The original purpose for separating the shield drain termination (item 3, Figure 25-4 )
from the float termination (item 5,
) in Method A was to allow for a variety of
lengths for the drain wires so that the shield drain terminations (item 3, Figure 25-4 )
would not all “bunch up” in the harness and to eliminate loops in the drain wires. If
Method B is chosen, as described in this section, care must be taken to ensure that all drain shield terminations can still be inspected. With connectors which require a large number of shield terminations it may be best to use Method A. This will allow the drain
shield terminations (item 3, Figure 25-4 ) a larger area to be dispersed across.
Using this method, the instructions from Section 25.2.3
(Method A) are followed except that:
1. Step 2 is eliminated
2. Steps 3 and 4 are replaced by the following:
At the end of the shielded cable (item 2,
), strip “Quick Term Min” to “Quick Term
Max” (
Table 25-4 ) length of the jacket to expose the shield. Next trim the shield so that at most
0.35 inches remains extending beyond the insulating jacket. Fold this remaining shield back over the jacket.
Connect a Flat Braid (item 4,
) to the folded back shield of the prepared cable assembly. The flat braid should go out the front of the termination towards the connector. It is not permitted to exit the rear of the termination and loop back towards the connector (
Make this connection using an approved shield termination technique.
NOTE
FAA AC 43.13-1B Chapter 11, Section 8 (Wiring Installation Inspection Requirements) may be a helpful reference for termination techniques.
Preferred Method:
) to the shield using a heat gun approved for use with solder sleeves. It may prove beneficial to use a solder sleeve with a pre-installed Flat Braid versus having to cut a length of Flat Braid to be used. The chosen size of solder sleeve must accommodate both the number of conductors present in the cable and the Flat Braid (item 4,
NOTE
for recommended solder sleeves and flat braid. The same recommendations are applicable to this technique.
190-01115-01
Rev. AN
G3X/G3X Touch Installation Manual - Connector Installation Instructions
Page 25-10
Secondary Method:
Solder a Flat Braid (item 4, Figure 25-5) to the folded back shield on the prepared cable assembly
(item 2, Figure 25-1 ). Ensure a solid electrical connection through the use of acceptable soldering
practices. Use care to avoid applying excessive heat that burns through the insulation of the center conductors and shorts the shield to the signal wire. Slide a minimum of 0.75 inches of Teflon heat
shrinkable tubing (item 3, Figure 25-5) onto the prepared wire assembly and shrink using a heat gun.
The chosen size of heat shrinkage tubing must accommodate both the number of conductors present in
the cable as well as the Flat Braid (item 4, Figure 25-5) to be attached.
Teflon Heat Shrinkable Tubing:
Reference the following MIL-Spec for general Teflon heat shrinkable tubing (M23053/5-X-Y)
Figure 25-5 Method B.1 (Quick Term) for Shield Termination
Backshell Size
1
2
3
4
5
Table 25-4 Shielded Cable Preparations – (Quick Term)
Number of Pins
Std/HD
9/15
15/26
25/44
37/62
50/78
Quick Term Min
(inches)
1.25
1.5
1.5
1.5
1.5
Quick Term Max
(inches)
2.25
2.5
2.5
2.5
2.5
Quick Term
Float (inches)
1.75
2.0
2.0
2.0
2.0
190-01115-01
Rev. AN
G3X/G3X Touch Installation Manual - Connector Installation Instructions
Page 25-11
25.2.6 Shield Termination-Method B.2 (Daisy Chain-Quick Term)
In rare situations where more braids need to be terminated for a connector than three per ring terminal it is allowable to daisy chain a maximum of two shields together before coming to the ring terminal
Method B.1 are still applicable.
NOTE
The maximum length of the combined braids should be approximately 4 inches.
Figure 25-6 Method B.2 (Daisy Chain-Quick Term) for Shield Termination
190-01115-01
Rev. AN
G3X/G3X Touch Installation Manual - Connector Installation Instructions
Page 25-12
25.2.7 Daisy Chain between Methods A and B
In rare situations where more braids need to be terminated for a connector than three per ring terminal and a mixture of Methods A and B have been used, it is allowable to daisy chain a maximum of two shields
for the shield termination technique set forth for Method A and B are still applicable.
NOTE
The maximum length of the combined braids should be approximately 4 inches.
Figure 25-7 Daisy Chain between Methods A and B
25.2.8 ID Program Pins (Strapping)
NOTE
The GDU 37X rear connector (J3701) is electrically isolated. For installations using programming pins, a ground pin must be tied to the connector shell.
ID Program Pins provide a ground reference used by the hardware as a means of configuration for system identification. The following instructions will illustrate how this ground strapping should be accomplished with the Jackscrew Backshell:
1. Cut a 4 inch length of 22 AWG insulated wire.
WARNING
Flat Braid is not permitted for this purpose. Use only insulated wire to avoid inadvertent ground issues that could occur from exposed conductors.
2. Strip back approximately 0.17 inches of insulation and crimp a contact (item 6, Figure 25-3
) to the
4” length of 22 AWG insulated wire. It is the responsibility of the installer to determine the proper length of insulation to be removed. Wire must be visible in the inspection hole after crimping and the insulation must be 1/64 – 1/32 inches from the end of the contact as shown in
.
3. Insert newly crimped pins and wires into the appropriate connector housing location as specified by the installation wiring diagrams.
4. At the end opposite the pin on the 22 AWG insulated wire strip back 0.2 inches of insulation.
5. Terminate this end via the ring terminals with the other Flat Braid per Steps 8 through 11
) pertaining to shield termination. If this ground strap is the only wire to terminate, attach a Ring terminal, #8, insulated, 18-22 AWG (MS25036-149).
190-01115-01
Rev. AN
G3X/G3X Touch Installation Manual - Connector Installation Instructions
Page 25-13
25.2.9 Splicing Signal Wires
NOTE
Figure 25-8 illustrates that a splice must be made within a 3 inch window from outside the
edge of clamp to the end of the 3 inch max mark.
WARNING
Keep the splice out of the backshell for pin extraction, and outside of the strain relief to avoid preloading.
Figure 25-8 shows a two wire splice, but a maximum of three wires can be spliced. If a third wire is
spliced, it is located out front of splice along with signal wire going to pin.
Splice part numbers:
•Raychem D-436-36/37/38
•MIL Spec MIL-S-81824/1
This technique may be used with shield termination methods: A.1, A.2, B.1, B.2, C.1 and C.2.
190-01115-01
Rev. AN
Figure 25-8 D-Sub Spliced Signal Wire illustration
G3X/G3X Touch Installation Manual - Connector Installation Instructions
Page 25-14
25.3 Jackscrew Connector Installation
The D-sub connectors in a G3X/G3X Touch system use metal backshells with a convenient shield block for grounding the cable shields, and knurled jackscrews to attach the connector to the mating connector on the avionics module. The jackscrews should be tightened to 6-8 in. lbs. with a small slotted screwdriver, or
a 3/32” hex tool (preferred, Figure 25-9).
NOTE
It is important to ensure that connectors are fully tightened. Loose connectors may cause vibration-related performance issues that are difficult to troubleshoot.
The connector jackscrews are also pre-drilled to accept safety wire where additional security is desired. It is generally not a requirement to safety wire these connectors, especially when tightened with a hex tool.
Do not tighten more than 8 in. lbs. to prevent damage to the mating hardware.
Figure 25-9 Jackscrew Hex Driver
190-01115-01
Rev. AN
G3X/G3X Touch Installation Manual - Connector Installation Instructions
Page 25-15
25.4 Thermocouple Installation into a Backshell
included in the G3X w/GSU 73 Installation Kit (K10-00017-00).
Table 25-5 Thermocouple Kit GPN 011-00981-00
Item #
1
2
3
Description
3” Thermocouple, K type
Pins #22 AWG
Screw
Qty. Needed
1
2
1
PN or MIL spec
925-L0000-00
336-00021-00
211-60234-08
1. Strip back approximately 0.17 inches of insulation from both the positive and negative
thermocouple leads (item 1, Figure 25-10) and crimp a pin (item 2, Figure 25-10) to each lead. It is
the responsibility of the installer to determine the proper length of insulation to be removed. Wire must be visible in the inspection hole after crimping and the insulation must be 1/64 – 1/32 inches
from the end of the contact as shown in Figure 25-10.
2
1
Figure 25-10 Insulation/Contact Clearance
190-01115-01
Rev. AN
G3X/G3X Touch Installation Manual - Connector Installation Instructions
Page 25-16
NOTE
Refer to
for all item numbers in the following steps 2-5.
2. Insert newly crimped pins and wires (items 1 & 2) into the appropriate connector housing (item 4) location as specified by the installation specific wiring diagram.
3. Place thermocouple (item 1) body onto backshell (item 5) boss. Upon placing the thermocouple
(item 1) body, orient it such that the wires exit downward.
4. Attach thermocouple (item 1) tightly to backshell (item 5) using screw (item 3).
5. Attach cover (item 6) to backshell (item 5) using screws (item 7).
Figure 25-11 Jackscrew Backshell Thermocouple Installation
190-01115-01
Rev. AN
G3X/G3X Touch Installation Manual - Connector Installation Instructions
Page 25-17
advertisement
Related manuals
advertisement
Table of contents
- 24 Section 1 Inventory of Materials
- 24 1.1 Unpacking Unit
- 24 1.2 Required Garmin Equipment
- 24 1.3 Optional Garmin Equipment
- 24 1.4 Optional Garmin LRUs
- 24 1.5 Required non-Garmin Equipment
- 24 1.6 Optional Garmin Equipment (non-LRU)
- 24 1.7 Optional non-Garmin Equipment
- 24 1.8 Optional 3rd Party Sensors/LRUs
- 24 1.9 Garmin Software and Documents
- 25 Section 2 Installation Preparation
- 25 2.1 System Overview
- 25 2.2 Electrical Considerations
- 25 2.3 Wiring/Cabling Considerations
- 25 2.4 Mechanical Considerations
- 25 2.5 LRU/Sensor Installation Information
- 26 Section 3 GAD 27 (Flaps/Lights/Trim Controller) Installation
- 26 3.1 Equipment Description
- 26 3.2 Equipment Available
- 26 3.3 General Specifications
- 26 3.4 Mounting Requirements
- 26 3.5 Unit Installation
- 26 3.6 Outline and Installation Drawings
- 27 Section 4 GAD 29/29B (ARINC 429 Adapter) Installation
- 27 4.1 Equipment Description
- 27 4.2 Equipment Available
- 27 4.3 General Specifications
- 27 4.4 Mounting Requirements
- 27 4.5 Unit Installation
- 27 4.6 Outline and Installation Drawings
- 28 Section 5 GAP 26 (Pitot/AOA Probe) Installation
- 28 5.1 Equipment Description
- 28 5.2 Equipment Available
- 28 5.3 Required Equipment
- 28 5.4 General Specifications
- 28 5.5 Unit Installation
- 28 5.6 Outline and Installation Drawings
- 103 Section 6 GDU 37X (Display Unit) Installation
- 103 6.1 Equipment Description
- 103 6.2 General Specifications
- 103 6.3 Installation Information
- 103 6.4 Unit Installation
- 103 6.5 Antennas
- 103 6.6 Mounting Requirements
- 103 6.7 Outline and Installation Drawings
- 104 Section 7 GDU 45X (Display Unit) Installation
- 104 7.1 Equipment Description
- 104 7.2 General Specifications
- 104 7.3 Installation Information
- 104 7.4 Unit Installation
- 104 7.5 Antennas
- 104 7.6 Mounting Requirements
- 104 7.7 Outline and Installation Drawings
- 105 Section 8 GDU 46X (Display Unit) Installation
- 105 8.1 Equipment Description
- 105 8.2 General Specifications
- 105 8.3 Installation Information
- 105 8.4 Unit Installation
- 105 8.5 Antennas
- 105 8.6 Mounting Requirements
- 105 8.7 Outline and Installation Drawings
- 106 Section 9 GDU 470 (Display Unit) Installation
- 106 9.1 Equipment Description
- 106 9.2 General Specifications
- 106 9.3 Installation Information
- 106 9.4 Unit Installation
- 106 9.5 Antennas
- 106 9.6 Mounting Requirements
- 106 9.7 Outline and Installation Drawings
- 107 Section 10 GEA 24 (EIS Interface) Installation
- 107 10.1 Equipment Description
- 107 10.2 Equipment Available
- 107 10.3 General Specifications
- 107 10.4 Unit Installation
- 107 10.5 Mounting Requirements
- 107 10.6 Outline and Installation Drawings
- 112 Section 11 GI 260 (AOA Indicator) Installation
- 112 11.1 Equipment Description
- 112 11.2 Equipment Available
- 112 11.3 General Specifications
- 112 11.4 Unit Installation
- 112 11.5 Unit Calibration
- 112 11.6 Unit Operation
- 112 11.7 Outline and Installation Drawings
- 113 Section 12 GMC 305 (AFCS Mode Controller) Installation
- 113 12.1 Equipment Description
- 113 12.2 Equipment Available
- 113 12.3 General Specifications
- 113 12.4 Mounting and Wiring Requirements
- 113 12.5 Outline and Installation Drawings
- 114 Section 13 GMC 307 (AFCS Mode Controller) Installation
- 114 13.1 Equipment Description
- 114 13.2 Equipment Available
- 114 13.3 General Specifications
- 114 13.4 Mounting and Wiring Requirements
- 114 13.5 Outline and Installation Drawings
- 115 Section 14 GMC 507 (AFCS Mode Controller) Installation
- 115 14.1 Equipment Description
- 115 14.2 General Specifications
- 115 14.3 Mounting and Wiring Requirements
- 115 14.4 Outline and Installation Drawings
- 116 Section 15 GMU 11 (Magnetometer) Installation
- 116 15.1 Equipment Description
- 116 15.2 General Specifications
- 116 15.3 Equipment Available
- 116 15.4 Unit Installation
- 116 15.5 Outline and Installation Drawings
- 117 Section 16 GMU 22 (Magnetometer) Installation
- 117 16.1 Equipment Description
- 117 16.2 General Specifications
- 117 16.3 Equipment Available
- 117 16.4 Unit Installation
- 117 16.5 Outline and Installation Drawings
- 157 Section 17 GPS 20A (WAAS GPS Position Source) Installation
- 157 17.1 Equipment Description
- 157 17.2 Statement of Compliance (per AC 90-114A CHG1)
- 157 17.3 Equipment Available
- 157 17.4 General Specifications
- 157 17.5 Mounting Requirements
- 157 17.6 Unit Installation
- 157 17.7 Antennas
- 157 17.8 Antenna Cable Requirements
- 157 17.9 Outline and Installation Drawings
- 158 Section 18 GSA 28 (Autopilot Servo) Installation
- 158 18.1 Equipment Description
- 158 18.2 Equipment Available
- 158 18.3 General Specifications
- 158 18.4 Required Equipment
- 158 18.5 Unit Installation
- 158 18.6 Unit Wiring
- 158 18.7 Outline and Installation Drawings
- 159 Installation
- 159 19.1 Equipment Description
- 159 19.2 General Specifications
- 159 19.3 Required Equipment
- 159 19.4 Unit Installation
- 159 19.5 Outline and Installation Drawings
- 160 Section 20 GSU 73 (Sensor Unit) Installation
- 160 20.1 Equipment Description
- 160 20.2 General Specifications
- 160 20.3 Required Equipment
- 160 20.4 Unit Installation
- 160 20.5 Outline and Installation Drawings
- 161 Section 21 GTP 59 (Temperature Probe) Installation
- 161 21.1 Equipment Description
- 161 21.2 General Specifications
- 161 21.3 Unit Installation
- 161 21.4 GTP 59 Icing
- 161 21.5 Outline and Installation Drawings
- 162 Section 22 GTR 20 (VHF Communications Radio) Installation
- 162 22.1 Equipment Description
- 162 22.2 Equipment Available
- 331 22.3 General Specifications
- 331 22.4 Installation Considerations
- 331 22.5 Antenna Considerations
- 331 22.6 Mounting Considerations
- 331 22.7 Mounting, Wiring, and Power Checks
- 331 22.8 Outline and Installation Drawings
- 332 Section 23 GPS/XM Antenna Installation
- 332 23.1 Non-Garmin Materials Required
- 332 23.2 Non-Garmin Antennas
- 332 23.3 Garmin Antennas
- 332 23.4 Antenna Mounting Considerations
- 332 23.5 Teardrop Footprint Antenna Installation (GA 35, GA 55, and GA 56)
- 332 23.6 ARINC 743 Footprint Antenna Installation (GA 36, GA 37, GA 55A, GA 57X)
- 332 23.7 Non-Structural Mount Installation
- 332 23.8 Outline and Installation Drawings
- 333 Section 24 Engine/Airframe Sensor Installation
- 333 24.1 Engine/Airframe Sensor Options
- 333 24.2 Engine Sensor Applications
- 333 24.3 Engine Sensor Installation
- 334 Section 25 Connector Installation Instructions
- 334 25.1 Cable Connector Installation
- 334 25.2 Jackscrew Backshell Assembly
- 334 25.3 Jackscrew Connector Installation
- 334 25.4 Thermocouple Installation into a Backshell
- 334 25.5 Configuration Module Installation into a Backshell
- 334 25.6 P-Lead Resistor Installation (Braid Shield)
- 335 Section 26 LRU Pinouts
- 335 26.1 GAD 27 (Flaps/Lights/Trim Controller)
- 335 26.2 GAD 29/29B (ARINC 429 Adapter)
- 335 26.3 GDU 37X (Display Unit)
- 335 26.4 GDU 4XX (Display Unit)
- 335 26.5 GEA 24 (EIS Interface)
- 335 26.6 GI 260 (AOA Indicator)
- 335 26.7 GMC 305 (AFCS Mode Controller)
- 335 26.8 GMC 307 (AFCS Mode Controller)
- 335 26.9 GMC 507 (AFCS Mode Controller)
- 335 26.10 GMU 11 (Magnetometer)
- 335 26.11 GMU 22 (Magnetometer)
- 335 26.12 GPS 20A (WAAS GPS Position Source)
- 335 26.13 GSA 28 (Autopilot Servo)
- 335 26.14 GSU 25 (AHRS/Air Data Sensor Unit)
- 335 26.15 GSU 73 (Sensor Unit)
- 514 26.16 GTP 59 (Temperature Probe)
- 514 26.17 GTR 20 (VHF Communications Radio)
- 514 26.18 GTX 23 (Mode S Transponder)
- 515 Section 27 G3X w/GSU 25 and/or GAD 29 Interconnect Drawings
- 515 27.1 Core Interconnect Drawings w/GSU 25 and/or GAD
- 515 27.2 External Interconnect Drawings w/GSU
- 516 Section 28 G3X w/GSU 73 Interconnect Drawings
- 516 28.1 Core Interconnect Drawings
- 516 28.2 External Interconnect Drawings w/GSU
- 517 Section 29 G3X w/GTR 20 Interconnect Drawings
- 517 29.1 Notes for Section 29 Drawings
- 517 29.2 Single GTR 20 Interconnect Drawings
- 517 29.3 Dual GTR 20 Interconnect Drawings
- 518 Section 30 Sensor Wiring Examples
- 518 30.1 Notes for Section 30 Drawings
- 518 30.2 Sensor Wiring Examples w/GEA
- 518 30.3 Sensor Wiring Examples w/GSU
- 519 Section 31 Lycoming/Continental Sensor Wiring Examples
- 519 31.1 Notes for Section 31 Drawings
- 519 31.2 GEA 24 - Lycoming/Continental Sensor Drawings
- 519 31.3 GSU 73 - Lycoming/Continental Sensor Drawings
- 520 Section 32 Rotax Sensor Wiring Examples
- 520 32.1 Notes for Section 32 Drawings
- 520 32.2 GEA 24 - Rotax Sensor Drawings
- 520 32.3 GSU 73 - Rotax Sensor Drawings
- 521 Section 33 Jabiru Sensor Wiring Examples
- 521 33.1 Notes for Section 33 Drawings
- 521 33.2 GEA 24 - Jabiru Sensor Drawings
- 521 33.3 GSU 73 - Jabiru Sensor Drawings
- 522 Section 34 GDU 37X Configuration and Post Installation Checkout
- 522 34.1 Recommended Test Equipment
- 522 34.2 Configuration Mode
- 522 34.3 Software Loading Procedure
- 522 34.4 Configuration Pages
- 522 34.5 Garmin Database Updates
- 522 34.6 SiriusXM® Activation Instructions (GDU 375 only)
- 522 34.7 External Interface Configuration (Garmin units only)
- 885 34.8 GDU Splash Screen
- 885 34.9 Checklist Editor
- 886 Section 35 GDU 4XX Configuration and Post Installation Checkout
- 886 35.1 Recommended Test Equipment
- 886 35.2 Configuration Mode
- 886 35.3 Software Loading Procedure
- 886 35.4 Configuration Pages
- 886 35.5 Garmin Database Updates
- 886 35.6 SiriusXM® Activation Instructions (GDU 455/465 only)
- 886 35.7 External Interface Configuration (Garmin units only)
- 886 35.8 Sharing G3X Touch Flight Plans (Crossfill) with External IFR Navigators
- 886 35.9 Checklist Editor
- 887 Section 36 Troubleshooting
- 887 36.1 General Troubleshooting
- 887 36.2 CAN Network Troubleshooting
- 887 36.3 GDU 37X/4XX
- 887 36.4 Air Data Troubleshooting
- 887 36.5 Engine Indication Troubleshooting
- 887 36.6 ADAHRS Troubleshooting
- 887 36.7 Post Installation Calibration Procedures
- 887 36.8 GSU 73 Data Logging
- 887 36.9 Sending Troubleshooting Data to Garmin
- 888 Section 37 Maintenance
- 888 37.1 Inspections/Continued Airworthiness/Maintenance
- 888 37.2 Return to Service Information