PRODUCT MAINTENANCE. EKOM DK50 2V, DK50 Plus Mobile, DK50 2V/M MOBILE, DK50 2V S, DK50 PLUS
Add to My manuals104 Pages
advertisement
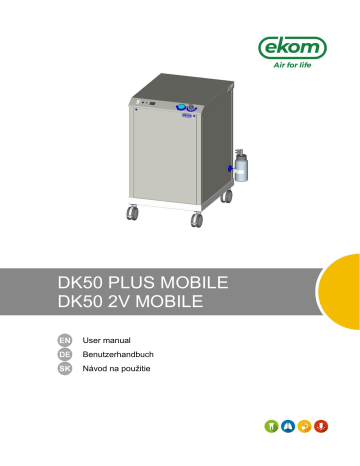
PRODUCT MAINTENANCE
PRODUCT MAINTENANCE
16. PRODUCT MAINTENANCE
The operator should carry out device checks regularly in the intervals defined by applicable regulations. Test results must be recorded.
The device has been designed and manufactured to keep its maintenance to a minimum. For correct and reliable operation of the compressor perform the following operations:
Risk of servicing by persons without required qualification.
Repair works beyond standard maintenance (see chapter.16.1) may only be
performed by a qualified technician (organization authorized by the manufacturer) or manufacturer’s customer service.
Standard maintenance works (see chapter 16.1) may only be carried out by
a trained operator.
Only use spare parts and accessories approved by the manufacturer.
Risk of injury and damage to the device.
Before any maintenance work, it is necessary to:
- check, if it is possible to disconnect compressor from the supplied equipment, so that there is no risk of damage to a person using the given appliance or any other material damages
- switch off the compressor
- disconnect it from the mains (pull out the mains plug)
- vent the compressed air from the air tank
Risk of injury when venting the compressed air.
Protect eyesight – wear goggles when venting the compressed air from the compressor pneumatic system (air tank).
Risk of burn.
Pump components (head, cylinder, pressure hose) have high temperature during and shortly after compressor operation
– do not touch these components!
Let the device cool before any product maintenance, service or connection/ disconnection of pressurized air!
The removed grounding conductor during service must be connected back to the original position after completing the service.
NP-DK50 PLUS, 2V-MOBILE-A-4_12-2019-MD 28 12/2019
PRODUCT MAINTENANCE
16.1. Maintenance intervals user
Qualified professional
12/2019 29 NP-DK50 PLUS, 2V-MOBILE-A-4_12-2019-MD
PRODUCT MAINTENANCE
16.2. Check of product operation
Check pump condition – the pumps must operate evenly without excessive vibrations or noise. If there is any negative result, find the cause of the given condition or call service engineers.
Check fans operation (visually) – the fans must be operating when the fans are running. If there is a negative result, look for the cause of the given condition or call service engineers.
Check if the power cord and pneumatic hoses are not damaged. Replace the damaged parts or call service engineers.
Check ambient temperature – ambient temperature must be below temperature limit (40°C).
Improve cooling in the room if the temperature is higher.
Compressor with air dryer - open the plug on the condensate collecting bottle and drain the condensate,
16.3. Check of pneumatic connections leakage and device inspection
Leakage check
Check pneumatic connections of the compressor when the compressor is operating – pressurizing.
Use a leakage analyser or soapy water to check all connections for leaks. Tighten or release the connection where leaks are found.
Device inspection
Check condition of the compressor pump – even operation, appropriate noise level.
Check fans operation – fans must be running in the defined cycles of the compressor operation.
Check function of the temperature switch (B2) – heat the temperature switch to temperature abov e 40°C (e.g. using a heat gun – Be careful, do not operate with high temperature on plastic components in the surrounding, it can cause deformation of plastic materials). Fan
EV1 (and EV2 for a compressor with dryer) starts up once the temperature reaches 40°C – the compressor must be under voltage.
Check filters condition – filters must be undamaged and sufficiently clean.
Check condition of the pump itself, check if there is no dirt inside the crankcase or clearance in the crankshaft.
Replace any defective parts if there are any failures.
16.4. Check of electrical connections
Risk of electric shock.
Check electrical connections on the device disconnected from the mains.
Check mechanical function of the main switch.
Check if the power cable and conductors are not damaged.
Visually check if cables are connected to the terminal box.
Check all screw connections of the green-yellow PE grounding conductor.
NP-DK50 PLUS, 2V-MOBILE-A-4_12-2019-MD 30 12/2019
PRODUCT MAINTENANCE
16.5. Condensate drain
Risk of slipping on a wet floor in case of the collecting vessel overflow.
Compressors without dryers
(Fig. 1 and Fig. 5) During regular operation is condensate automatically drained through automatic
drain (autodrain) which is catched into a condensate collection vessel. Pull the vessel out of the holder and pour out the condensate.
Compressors with air dryer
Condensate from compressors with air dryers is automatically drained into the condensate collection vessel.
Monitor the level in the vessel using the 1 l or
2 l markings (depending on the volume of the vessel), and empty at least once a day
Fig. 5: Check of condensate collection vessel
Before the following checks it is required:
16.6. Check of safety valve
When the compressor is operated for the first time, make sure that the safety valve is working properly.
Turn the screw (2) on the safety valve (1) several rotations to the left until the safety valve releases air.
Let the safety valve vent for only a few seconds.
Turn the screw (2) to the right until it seats, closing the valve.
12/2019
Fig. 6: Check of safety valve
Risk of pressure increase when safety valve is damaged.
Safety valve must not be used to depressurize the air tank. It could damage the safety valve function. The valve is set to the maximum allowed pressure, it is tested and marked.
Safety valve setting must not be adjusted.
31 NP-DK50 PLUS, 2V-MOBILE-A-4_12-2019-MD
PRODUCT MAINTENANCE
Risk of injury when compressed air is vented.
Protect your eyesight when checking the safety valve – wear protective goggles.
16.7. Inlet filter and pre-filter replacement
Pull out the rubber plug (2) by hand.
Remove the dirty inlet filter (1).
Insert a new filter and mount the rubber plug.
Fig. 7: Inlet filter replacement
Pull out the pre-filter by hand (3)
Replace the element and re-insert
Fig. 8: Inlet pre-filter replacement
16.8. Replacement of filter element
Remove the hose (1) from the quick connector.
Use a wrench (2) to release the filter vessel (3) and remove.
Pull down on the filter element (4) to remove.
Insert a new filter element.
Re-install the filter vessel.
Gently tighten the filter vessel with the wrench.
Re-install the hose on the quick connector.
NP-DK50 PLUS, 2V-MOBILE-A-4_12-2019-MD 32 12/2019
advertisement
Related manuals
advertisement
Table of contents
- 6 GENERAL INFORMATION
- 6 CONFORMITY WITH THE REQUIREMENTS OF THE EUROPEAN UNION
- 6 SYMBOLS
- 7 DEVICE USE
- 8 GENERAL SAFETY INSTRUCTION
- 9 STORAGE AND TRANSPORT
- 10 PRODUCT DESCRIPTION
- 10 VARIANTS
- 10 PRODUCT FUNCTION
- 14 TECHNICAL DATA
- 18 INSTALLATION
- 18 INSTALLATION CONDITIONS
- 18 COMPRESSOR ASSEMBLY
- 19 PNEUMATIC CONNECTION
- 19 ELECTRICAL CONNECTION
- 19 COMMISSIONING
- 20 PNEUMATIC AND ELECTRICAL DIAGRAMS
- 26 OPERATION
- 27 SWITCHING ON THE COMPRESSOR
- 27 SWITCHING OFF THE COMPRESSOR
- 28 PRODUCT MAINTENANCE
- 33 LONG-TERM SHUTDOWN
- 33 DISPOSAL OF DEVICE
- 33 TROUBLESHOOTING
- 35 REPAIR SERVICE
- 98 ANNEX
- 98 INSTALLATION RECORD
- 37 ALLGEMEINE INFORMATIONEN
- 37 KONFORMITÄT MIT DEN ANFORDERUNGEN DER EU
- 37 SYMBOLE
- 38 NUTZUNG DES GERÄTS
- 39 ALLGEMEINE SICHERHEITSANWEISUNGEN
- 40 LAGERUNGS- UND TRSANSPORTBEDINGUNGEN
- 41 PRODUKTBESCHREIBUNG
- 41 MODELLE
- 41 PRODUKTFUNKTION
- 45 TECHNISCHE DATEN
- 49 INSTALLATION
- 49 INSTALLATIONSBEDINGUGEN
- 49 ZUSAMMENBAU DES KOMPRESSOR
- 50 ELEKTRISCHER ANSCHLUSS
- 50 INBETRIEBNAHME
- 57 BETRIEB
- 58 EINSCHALTEN DES KOMPRESSORS
- 58 AUSSCHALTEN DES KOMPRESSORS
- 59 PRODUKTWARTUNG
- 64 LANGFRISTIGE AUßERBETRIEBNAHME
- 64 ENTSORGUNG DES GERÄTS
- 65 FEHLERBEHEBUNG
- 66 INFORMATIONEN ZU REPARATURBETRIEBEN
- 98 ANHANG
- 99 INSTALLATIONSPROTOKOLL
- 68 VŠEOBECNÉ INFORMÁCIE
- 68 POŽIADAVKAMI SMERNÍC EURÓPSKEJ ÚNIE
- 68 POUŽITÉ SYMBOLY
- 69 POUŽITIE ZARIADENIA
- 70 ZÁKLADNÉ BEZPEČNOSTNÉ POKYNY
- 71 PREPRAVNÉ PODMIENKY
- 72 POPIS VÝROBKU
- 72 VARIANTY
- 72 FUNKCIA VÝROBKU
- 76 TECHNICKÉ ÚDAJE
- 80 INŠTALÁCIA
- 80 INŠTALAČNÉ PODMIENKY
- 80 ZOSTAVENIE KOMPRESORA
- 81 PNEUMATICKÉ PRIPOJENIE
- 81 ELEKTRICKÉ ZAPOJENIE
- 81 PRVÉ UVEDENIE DO PREVÁDZKY
- 82 PNEUMATICKÉ A ELEKTRICKÉ SCHÉMY
- 88 OBSLUHA
- 89 ZAPNUTIE KOMPRESORA
- 89 VYPNUTIE KOMPRESORA
- 90 ÚDRŽBA VÝROBKU
- 95 ODSTAVENIE
- 95 LIKVIDÁCIA PRÍSTROJA
- 95 VYHĽADÁVANIE PORÚCH A ICH ODSTRÁNENIE
- 97 INFORMÁCIE O OPRAVÁRENSKEJ SLUŽBE
- 98 PRÍLOHA
- 100 ZÁZNAM O INŠTALÁCII