- No category
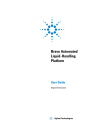
advertisement
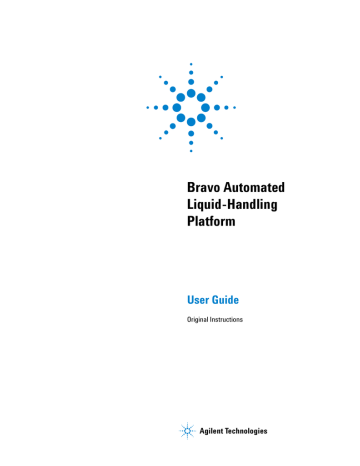
E Diagnostics quick reference
AM Mix task parameters
AM Mix task parameters
About this topic
This topic describes the task parameters for the AM Mix task, which is available only for the Bravo 96AM Head.
The AM Mix task is designed for aspirating and dispensing fluids through
AssayMAP Bravo cartridges that are mounted on the Bravo 96AM Head.
To run the AM Mix task from Diagnostics, see
“Performing a task using Bravo
. To use the task in a protocol, see the
VWorks
Automation Control User Guide
.
Parameter description
The AM Mix task has the following parameters.
Parameter
Location, plate
Location, location
Volume (µL)
Pre- aspirate volume (µL)
Blowout volume (µL)
Liquid class
Description
The labware involved in the Mix task.
The location at which the Mix task occurs.
<auto- select> automatically places the labware at the first- available or appropriate location for the task. If accessories are installed on the deck or shelf, the software uses the accessory configuration information in Bravo Diagnostics or Vertical Pipetting
Station Diagnostics to determine the correct location for the task.
The volume of liquid to be mixed in each well.
The volume of air to be drawn before the pipette tips enter the liquid.
The volume of air to dispense after the main volume has been dispensed while the tips are still in the wells.
Typically, the blowout volume is the same as the pre- aspirate volume.
The pipetting velocity and accuracy.
IMPORTANT
To ensure consistent pipetting, always select a liquid class for liquidhandling tasks.
Override flow rates from liquid class
The option to override the aspirate and dispense velocity in the selected liquid class.
Selecting this option enables you to specify a value for the flow rate without changing the liquid class.
Bravo Automated Liquid-Handling Platform User Guide 281
E Diagnostics quick reference
AM Mix task parameters
Parameter
Aspirate/dispense flow rate (0–500 µL/s)
Mix cycles (0–100)
Dynamic tip extension
(0–20 mm/µL)
Description
The numerical value or the JavaScript variable that will override both the aspirate and dispense velocity in the selected liquid class.
A JavaScript variable enables the value to be assigned later. For example, using a VWorks form, an operator could easily change the flow rate for a mix step in increments from as low as 1 µL/min up to 2000 µL/min or more using the same liquid class.
If the task is included in a VWorks macro, a
JavaScript variable enables you to change the value for the task at the macro level.
IMPORTANT
The software requires that the flow rate value be in microliters per second
(µL/s) at run time. If you want an operator to enter the value in microliters per minute
(µL/min), you can use scripting to convert the values for the software to use.
The number of times to repeat the aspirateand- dispense cycle.
The rate at which the Bravo 96AM Head moves during the aspirate action. The software calculates the distance over which the tips will move without crashing.
Use dynamic tip extension to prevent spills as the pipette tips displace the liquid.
To move the tips:
• At the same rate as the volume change.
Calculate dynamic tip extension (DTE) as follows:
DTE = (well depth)/(well vol) = 1/A, where A is the cross- sectional area of a well with straight walls
• Faster than the volume change.
DTE > 1/A
• Slower than the volume change.
DTE < 1/A
The starting and ending positions can be calculated as follows:
(V aspirated
* DTE) + Distance well bottom
Note: Instead of a negative aspirated volume, the software automatically moves downward toward the well bottom with each aspirate action.
282 Bravo Automated Liquid-Handling Platform User Guide
E Diagnostics quick reference
AM Mix task parameters
Parameter
Well selection
Pipette technique
Aspirate distance
(0–100 mm)
Dispense at different distance
Dispense distance
(0–100 mm)
Perform tip touch
Which sides to use for tip touch
Tip touch retract distance
(–20 to 50 mm)
Tip touch horizontal offset
(–5 to 5 mm)
Description
The wells at which the Mix task occurs.
Click in the parameter box, and then click the Browse button to select the wells in the
Well Selection dialog box.
Use this parameter only if the Bravo 96AM
Head has fewer tips than the number of wells in the microplate, or if you are in single- row or single- column mode.
The pipette location offset you want to use for the Mix task.
The list of pipette techniques are defined in the Pipette Technique Editor.
The distance between the end of the pipette tips and the well botttoms during the aspirate action.
IMPORTANT
The labware definition must be accurate and the teachpoint must be precise in order for the system to position the tips at the correct distance from the well bottom.
The option to dispense at a pipette tip height that is different than the aspirate distance.
Select the check box to enter a value for the dispense distance.
The distance between the tips of the probes, cartridges, or disposable tips and the well bottoms during the dispense action.
The option to touch the tips on one or more sides of the well.
The side or sides of the well to use during tip touch: North, South, East, West, North/
South, West/East, West/East/South/North.
The vertical distance for the tips to rise before touching the sides of the wells.
The horizontal distance the tips move. The value is based on the well diameter specified by the labware definition.
For example, if you set a value of:
• 0, the tips move a horizontal distance equal to the well radius
• > 0, the tips attempt to move past the well radius, which results in a more forceful tip touch
• < 0, the tips move a distance less than the radius of the well, resulting in a lighter tip touch
Bravo Automated Liquid-Handling Platform User Guide 283
E Diagnostics quick reference
AM Mix task parameters
Related information
For information about… See…
Opening Bravo Diagnostics
“Opening Diagnostics” on page 26
Editing the labware classes, liquid library, or pipetting techniques
VWorks Automation Control Setup
Guide
Performing a diagnostic task
Reporting a problem
“Performing a task using Bravo
“Reporting problems” on page 78
284 Bravo Automated Liquid-Handling Platform User Guide
Index
A pendant port, 10 aborting a run,
accessories performing tasks in diagnostics,
pipette controls,
Accessories Hub, installing,
Alignment Station,
pipette head axes,
power entry, 10
Bravo,
delidding,
power switch, 6 pump I/O port, 10
Heated Shaking Station, Inheco Teleshake
95,
removing a pipette head, 63 serial dilution,
Heated Shakingl Station, Inheco Teleshake
95,
serial port, 10 setting up workflow,
Manual Fill Reservoir,
Microplate Vacuum Alignment Station,
shutting down,
starting,
Nested Rack Insert,
Orbital Shaking Station,
stopping a run,
troubleshooting,
overview,
Peltier Thermal Station, Inheco CPAC using the Move command,
Ultraflat,
setting teachpoint for,
C cleaning the device,
Thermal Station (chiller),
Vacuum Filtration Station,
cleaning up after a run, concurrent operation,
Weigh Station,
air requirements, Microplate Vacuum Alignment
Configuration tab configuring autofilling, 156
Station,
quick reference,
Alignment Station,
context-sensitive help,
Approach command, gripper,
creating a profile,
approach height,
Aspirate task parameters,
AssayMAP Bravo Platform, 177
Assemble Vacuum process,
axes illustrated, 7
Jog Teach tab controls,
pipette head,
D
B
Bravo accessories,
axes, illustrated, 7 changing the speed,
cleaning,
described,
disposable pipette heads,
Ethernet port, 10 fixed tip pipette heads,
fuse holder, 10 gripper,
homing,
initializing,
jogging the pipette head,
moving the pipette head manually,
deck, 7
Delidding option,
devices defined,
device file, adding devices,
device file, creating,
device file, saving,
device files defined,
Diagnostics
Approach and Move commands,
changing the speed,
gripper, fine-tuning,
Jog/Teach tab,
jogging the pipette head,
opening,
performing tasks,
pipette head axes,
pipette head controls,
Direct Drive Robot preparing for a run,
disabling all servo motors,
Disassemble Vacuum process,
Dispense task parameters,
Bravo Automated Liquid-Handling Platform User Guide 285
Index
dry runs,
dry runs, described,
E emergency stop,
errors messages,
reporting,
teachpoint,
Ethernet port, 10 external robots,
F fuse holder, 10
G gripper axes of motion, 7 described,
jogging,
H hardware errors,
troubleshooting problems,
hardware overview axes, 7
Heated Shaking Station, Inheco (Teleshake
95),
homing gripper,
pipette head,
I indicator lights, 5 initializing,
IO tab quick reference,
J job roles for readers of this guide,
Jog Teach tab quick reference,
Jog/Teach diagnostics tab, overview,
jogging gripper,
pipette head,
K knowledge base,
L labels serial number,
286
labware gripper, specifying for,
Light Curtain,
M
Magnetic bead option,
maintenance cleaning,
pipette head tipbox stripper pins,
post-run cleanup,
routine,
Manual Fill Reservoir,
Microplate Vacuum Alignment Station setup,
Mix task parameters,
motor fault, troubleshooting,
Move command, gripper,
N
Nested Rack Insert,
Nested Tipbox Insert,
O online help,
Orbital Shaking Station setting up,
Shake task parameters,
P
PDF guide,
Peltier Thermal Station, Inheco (CPAC
Ultraflat),
pendant, 6 pendant port, 10 pin tools perform task using Bravo Diagnostics,
setting teachpoints,
software control,
task parameters,
pipette heads axes,
changing, 63 changing the speed,
controls,
described, 6 disposable,
disposable-tip,
fixed tip,
homing,
initializing,
jogging,
moving manually,
removing, 63 serial dilution,
using the Move command,
Bravo Automated Liquid-Handling Platform User Guide
Index
power entry, 10 power switch, 6 powering off,
powering up,
problems contacting technical support,
troubleshooting hardware,
Processes tab quick reference,
processes, performing in diagnostics,
Profiles tab quick reference,
profiles, creating,
protocol runs performing dry runs,
planning for,
setup guidelines,
protocols post-run cleanup,
Pump I/O port, 10
Pump Reagent task parameters,
R reservoirs configuring autofill, 155
Manual Fill Reservoir,
robot, external,
routine maintenance,
run aborting,
cleaning up after,
preparing for,
S safety
Light Curtain,
serial dilution, compatible pipette heads for,
serial number label,
serial port, 10 service,
setting up workflow,
Shake task parameters,
shutting down,
software
Diagnostics quick reference,
errors,
reporting errors,
version number,
speed, changing,
SRT Bravo Platform,
starting up,
stopping a run,
T tasks, performing in diagnostics,
teachpoints
Bravo Automated Liquid-Handling Platform User Guide
labware,
setting all relative to one,
setting for accessories,
verifying,
y-axis offsets,
technical support,
Thermal Station (chiller),
tie bar, 6 tipbox stripper pins, retracting,
troubleshooting error messages,
hardware problems,
turning off,
U user guides,
V
Vacuum Filtration Station installing and setting up,
task parameters,
version numbers, software,
W
Wash tips task parameters, 252 w-axis described, 7
Home W position controls,
Weigh Station,
configuring reservoir operations, 155 setting up,
workflow setting up the Bravo,
workflows preparing for a run,
preparing for protocol runs,
X x-axis, 7
Y y-axis, 7 y-axis offsets,
Z z-axis, 7 z-axis safe position,
287
Index
288 Bravo Automated Liquid-Handling Platform User Guide
Agilent Technologies
User Guide
G5409-90006
Revision F, June 2015
advertisement
Related manuals
advertisement
Table of contents
- 7 Preface
- 8 About this guide
- 9 Accessing Automation Solutions user information
- 15 Introduction to the Bravo Platform
- 16 Safety notes
- 17 About the Bravo Platform
- 19 Hardware overview
- 23 Connection panel description
- 26 Pipette heads and pin tools
- 29 Software overview
- 31 Setting up the Bravo Platform
- 32 Workflow for setting up the Bravo Platform
- 33 Starting up and shutting down
- 35 Creating or adding a Bravo device
- 40 Opening Diagnostics
- 42 Creating and managing profiles
- 46 Initializing the Bravo Platform
- 50 Setting teachpoints
- 57 Verifying the gripper setup
- 59 Configuring external robot access
- 69 Preparing for a protocol run
- 70 Workflow for preparing a protocol run
- 70 Emergency stops
- 71 Planning for the protocol run
- 72 About performing dry runs
- 73 Maintaining the Bravo Platform
- 74 Routine maintenance
- 75 Cleaning the Bravo Platform
- 76 Cleaning up after a run
- 77 Changing the Bravo head
- 83 Replacing the fuse
- 84 Retracting tip box stripper pins
- 86 Moving the head manually
- 87 Recovering from a head collision
- 89 Troubleshooting hardware problems
- 91 Troubleshooting hardware-related error messages
- 92 Reporting problems
- 95 Using Bravo Diagnostics
- 96 About the Jog/Teach tab
- 98 Homing the pipette head
- 100 Jogging the pipette head
- 102 Changing the pipette head speed
- 103 Using the Move and Approach commands
- 105 Fine-tuning the gripper movements
- 111 Clearing motor faults and checking the head type
- 112 Performing a task using Bravo Diagnostics
- 115 Accessories and platepads
- 116 Accessories overview for the Bravo Platform
- 118 Installing the Accessories Hub
- 121 Setting up a Microplate Vacuum Alignment Station
- 126 Setting up the Orbital Shaking Station
- 132 Using the teach plate to set the teachpoint for an accessory
- 134 Setting up the Vacuum Filtration Station
- 147 Configuring a platepad for delidding
- 148 Installing an Alignment Station
- 150 Setting up a Nested Rack Insert
- 153 Using the Manual Fill Reservoir
- 154 Setting up the Thermal Station
- 157 Setting up thermal and shaking stations (Inheco controller)
- 165 (Bravo SRT only) Setting up an LT tip box location
- 169 Autofilling accessories
- 170 Autofilling station overview and setup workflow
- 171 Configuring an autofilling station for the Bravo Platform
- 176 Setting up a Weigh Station for the Bravo Platform
- 179 Setting up the Barcode Reader
- 180 About setting up the Barcode Reader
- 182 Installing or removing the Barcode Reader
- 183 Creating a profile for the Barcode Reader
- 185 Specifying the Barcode Reader location
- 187 Testing and optimizing barcode scanning
- 193 Setting up the AssayMAP Bravo Platform
- 194 AssayMAP Bravo Platform overview
- 197 Bravo 96AM Head overview
- 202 AssayMAP cartridge overview
- 204 About installing the AssayMAP Bravo Platform
- 205 Installing and using the Bravo 96AM Head
- 213 Installing the 96AM Wash Station
- 217 Setting up the AssayMAP Bravo Platform
- 220 Setting teachpoints for the AssayMAP Bravo Platform
- 223 Verifying and adjusting teachpoints for the accessory locations
- 231 Opening the Protein Sample Prep Workbench
- 232 Requirements for partial-head liquid handling
- 237 Diagnostics quick reference
- 238 Bravo Diagnostics dialog box
- 239 Configuration tab quick reference
- 242 Accessory Diagnostics dialog box
- 243 External Robots tab quick reference
- 244 IO tab quick reference
- 246 Jog/Teach tab quick reference
- 250 Gripper tab quick reference
- 252 Profiles tab quick reference
- 256 Processes tab quick reference
- 259 Aspirate task parameters
- 263 Dispense task parameters
- 265 Dispense to Waste task parameters
- 269 Mix task parameters
- 272 Pump Reagent parameters
- 273 Shake task parameters
- 275 Vacuum Filtration Station task parameters
- 278 Wash Tips task parameters
- 281 Pin Tool task parameters
- 285 AM Aspirate task parameters
- 290 AM Dispense task parameters
- 295 AM Mix task parameters
- 299 Index