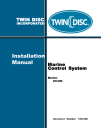
advertisement
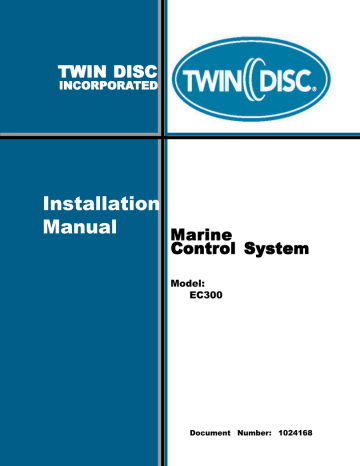
TWIN DISC
INCORPORA
TED
Installation
Manual
Model:
EC300
Document Number: 1024168
NOTICE
Twin Disc, Incorporated makes no warranty or guaranty of any kind, expressed, implied or otherwise, with regard to the information contained within this manual. Twin Disc, Incorporated has developed this manual through research and testing of the information contained therein. Twin Disc, Incorporated assumes no responsibility for any errors that may appear in this manual and shall not be liable under any circumstances for incidental, consequential or punitive damages in connection with, or arising out of, the use of this manual. The information contained within this manual is subject to change without notice.
Document Number
1024168
Revision 2
April, 2008
Marine Control System
Installation Manual
TWIN DISC, INCORPORATED
EXCLUSIVE LIMITED WARRANTY-
PLEASURE CRAFT MARINE TRANSMISSION,
SURFACE DRIVE, and ELECTRONIC CONTROL SYSTEMS
A. Twin Disc, Incorporated warrants all assembled products and parts, (except component products or parts on which written warranties issued by the respective manufacturers thereof are furnished to the original customer, as to which Twin Disc,
Incorporated makes no warranty and assumes no liability) against defective materials or workmanship
for a period of thirty six
(36) months from the date of original shipment by Twin Disc, Incorporated to the original customer, but not to exceed twenty four (24) months or one thousand (1,000) hours of service, whichever occurs first.
This is the only warranty made by Twin
Disc, Incorporated and is in lieu of any and all other warranties, express or implied, including the warranties of merchantability or fitness for a particular purpose and no other warranties are implied or intended to be given by Twin
Disc, Incorporated. This warranty applies only to private, non commercial (non revenue earning) marine pleasure
craft applications.
The original customer does not rely upon any tests or inspections by Twin Disc, Incorporated or on Twin Disc, Incorporated's application engineering. Twin Disc, Incorporated is not responsible for any specific application, installation or performance standard. Any analysis program by Twin Disc, Incorporated based upon customer supplied information is done solely as an accommodation to the customer and is not to be interpreted or construed as an approval for specific application or installation or a guarantee of performance.
B.
The exclusive remedy provided by Twin Disc, Incorporated whether arising out of warranty within the applicable warranty period as specified, or otherwise (including tort liability), shall at the sole option of Twin Disc, Incorporated be either the repair or replacement of any Twin Disc, Incorporated part or product found by Twin Disc, Incorporated to be defective. For all models except MG340 and MG360 this include the labor to perform that work and to remove and reinstall (or equivalent credit). In this context, labor is defined as the flat rate labor hours established by Twin Disc,
Incorporated in the published Twin Disc Flat Rate Schedule, required to remove, disassemble, inspect, repair, reassemble, reinstall and test the Twin Disc, Incorporated product only. Authorized reasonable travel and living expenses will be considered for payment in all model except MG340, MG360 and Electronic Control Systems. Under no circumstances, including a failure of the exclusive remedy, shall Twin Disc, Incorporated be liable for economic
loss, consequential, incidental or punitive damages..
The above warranty and remedy are subject to the following terms and conditions:
1. Complete parts or products upon request must be returned transportation prepaid and also the claims submitted to Twin
Disc, Incorporated within sixty (60) days after completion of the in warranty repair.
2. The warranty is void if, in the opinion of Twin Disc, Incorporated, the failure of the part or product resulted from abuse, neglect, improper maintenance or accident.
3. The warranty is void if any modifications are made to any product or part without the prior written consent of Twin Disc,
Incorporated.
4. The warranty is void unless the product or part is properly transported, stored and cared for from the date of shipment to the date placed in service.
5. The warranty is void unless the product or part is properly installed and maintained within the rated capacity of the product or part with installations properly engineered and in accordance with the practices, methods and instructions approved or provided by Twin Disc, Incorporated.
6. The warranty is void unless all required replacement parts or products are of Twin Disc origin or equal, and otherwise identical with components of the original equipment. Replacement parts or products not of Twin Disc origin are not warranted by Twin Disc, Incorporated.
C. As consideration for this warranty, the original customer and subsequent purchaser agree to indemnify and hold Twin Disc,
Incorporated harmless from and against all and any loss, liability, damages or expenses for injury to persons or property, including without limitation, the original customer's and subsequent purchaser's employees and property, due to their acts or omissions or the acts or omissions of their agents, and employees in the installation, transportation, maintenance, use and operation of said equipment.
D. Only a Twin Disc, Incorporated authorized factory representative shall have authority to assume any cost or expense in the service, repair or replacement of any part or product within the warranty period, except when such cost or expense is authorized in advance in writing by Twin Disc, Incorporated.
E. Twin Disc, Incorporated reserves the right to improve the product through changes in design or materials without being obligated to incorporate such changes in products of prior manufacture. The original customer and subsequent purchasers will not use any such changes as evidence of insufficiency or inadequacy of prior designs or materials.
F. If failure occurs within the warranty period, and constitutes a breach of warranty, repair or replacement parts will be furnished on a no charge basis and these parts will be covered by the remainder of the unexpired warranty which remains in effect on the complete unit.
December 14, 2007 TDWP10099 rev 2008
FLAT RATE SCHEDULE FOR
MARINE PLEASURE CRAFT TRANSMISSION
(Hourly Labor Rate Must be Acceptable to Twin Disc, Incorporated.)
Product Code / Model Series R&R
0450 - MG340 SERIES * Part Only
*
Unit
Rebuild
*
Clutch
Repair
(both packs)
*
R&R
Pump
*
0451 - MG360 SERIES * Part Only
* * * *
0432 - MG5010 & MG5011 SERIES
10 8 2 1
0401 - MG506 SERIES
0435 - MG5050 SERIES
0437 - MG5061 & MG5062V SERIES
0453 - MG5055A SERIES
1706 - MG5065A SERIES
1707 - MG5065SC SERIES
0425 - MG5085 SERIES
0442 - MG5075A SERIES
0443 - MG5075SC SERIES
10
10
10
10
10
10
10
10
10
11
11
11
11
11
11
12
12
12
4
4
4
4
4
4
4
4
4
1
1
1
1
1
1
1
1
1
0476 - MG5082 SERIES
10 12 4 1
0419 - MG5114 SERIES
10 17 5 1
0433 - MG5090 SERIES
10 17 5 1
0489 - MGX5114A SERIES
10 17 5 1
0490 - MGX5114SC SERIES
10 17 5 1
0491 - MGX5114IV SERIES
10 17 5 1
1719 - MGX5095A SERIES
10 17 5 1
1728 - MG5095A SERIES
10 17 5 1
1729 - MG5095SC SERIES
0405 - MG514 SERIES
10
10
17
25
5
6
1
1
0447 - MG5145A SERIES
10 25 6 1
0448 - MG5145SC SERIES
10 25 6 1
0492 - MGX5135A SERIES
10 25 6 1
0494 - MGX5145SC SERIES
10 25 6 1
1704 - MG-5135A SERIES
10 25 6 1
0426 - MG516 & MG5170 SERIES
10 28 8 1
0477 - MG5170 SERIES
10 28 8 1
0412 - MG5200 SERIES
10 32 10 1
0416 - MG518 SERIES
10 32 10 1
0459 - MG6557SC SERIES
10 32 10 1
0461 - MG6557RV SERIES
10 32 10 1
0465 - MG-6619A SERIES
10 32 10 1
0473 - MG-520-1HP SERIES
10 32 10 1
0441 - MG-6650-00-SC SERIES
12 32 16 1
0446 - MG-6848-00-SC SERIES
12 32 16 1
0478 - MG-6690SC SERIES
12 32 16 1
0484 - MGX-61500SC SERIES
12 32 16 1
0485 - MGX-6650 SERIES
12 32 16 1
0487 - MGX-6690SC SERIES
12 32 16 1
0488 - MGX-6848SC SERIES
12 32 16 1
1721 - MGX-6620SC SERIES
12 32 16 1
1737 - MGX-6599A SERIES
December 14, 2007
12
R&R
Valve
*
*
1
1
1
1
1
1
1
1
1
1
1
1
1
1
1
1
1
1
1
1
1
1
1
1
1
1
1
1
1
1
1
1
1
1
1
1
1
1
1
1
1
Rebuild
Valve
*
*
0.5
0.5
0.5
0.5
0.5
0.5
0.5
0.5
0.5
0.5
0.5
0.5
0.5
0.5
0.5
0.5
0.5
0.5
0.5
0.5
0.5
0.5
0.5
0.5
0.5
0.5
0.5
0.5
0.5
0.5
0.5
0.5
0.5
0.5
0.5
0.5
0.5
0.5
0.5
0.5
0.5
32 16 1 1 0.5
TDWP10099A rev 2008
FLAT RATE HOUR ALLOWANCE
MARINE PLEASURE CRAFT SURFACE DRIVE
(Hourly Labor Rate Must be Acceptable to Twin Disc, Incorporated.)
Description of Flat Rate Labor
ASD6 ASD8
ASD
10
ASD
11
ASD1
2
ASD
14
Removal and Reinstallation
Recondition complete unit and test for leaks
2
5
3
6
3
6
3
6
4
6
6
6
ASD
15
8
8
Replace front oil seal
Replace input shaft
Replace input gear/sprocket
Replace Chain
Replace H-Joint
Replace thrust ball
Replace retainer ring
Replace propeller shaft
Replace thrust tube
Replace rear oil seal
Replace steer cylinder
Replace power steer pump
Replace trim pump
Replace Ball Boot
Replace and align driveline
1
1
1
1
2
2
2
2
2
1
1
1
1
2
1
1
3
3
4
2
2
2
3
3
1
1
1
1
2
2
1
3
3
4
2
2
2
3
3
1
1
1
1
2
2
1
3
3
4
2
2
2
3
3
1
1
1
1
2
2
1
3
-
-
3
3
2
3
4
1
1
1
1
2
2
1
4
-
-
3
3
2
4
5
1
1
1
1
2
3
1
4
-
-
3
3
2
4
6
1
1
1
1
2
3
ASD
16
8
8
1
4
-
-
3
3
2
4
6
1
1
1
1
2
3
FLAT RATE HOUR ALLOWANCE
MARINE PLEASURE CRAFT ELECTRONIC CONTROL SYSTEMS
(Hourly Labor Rate Must be Acceptable to Twin Disc, Incorporated.)
* Travel and related expenses are not included as a part of Twin Disc Electronic Control Warranty.
Description of Flat Rate Labor
(hours allowed for function to the right =>)
EC200
EC250
EC300 External Sensor
Removal and Reinstallation and Test
Electronic Control Repair *
* there are no serviceable internal components
3
0
3
0
3
0
1
0
December 14, 2007 TDWP10099B rev 2008
Table of Contents
Twin Disc, Incorporated
Table of Contents
Introduction .........................................................13
General Information .......................................................................... 15
Replacement Parts ............................................................................ 16
Source of Service Information......................................................... 17
Required Tools................................................................................... 18
Basic System Components .............................................................. 19
Additional Materials .......................................................................... 23
Component Installation......................................25
General Component Installation Guidelines .................................. 25
EC300 Control Installation ................................................................ 27
Control Head Installation .................................................................. 28
Single/Dual Lever Control Head Assembly .................................... 29
Side Mount Control Head Assembly (Binnacle/Console Station) 32
Control Head Lever Drag Adjustment............................................. 35
Twin Disc Display Installation .......................................................... 36
Speed Sensor Installation ................................................................ 38
Installation - Magnetic Pick-Up Engine Speed Sensor ................. 40
Installation - Hall Effect Pick-Up Output Speed Sensor ................ 42
Installation - Tachometer Signal Generator ................................... 43
Station Doubler Installation .............................................................. 44
Servo Actuator Installation ............................................................... 46
Servo Actuator Mounting ................................................................. 47
Push-Pull Cable Installation Guidelines ......................................... 48
Push-Pull Cable Installation Kits for Conductive Vessels ........... 49
Push-Pull Cable Installation Kits for Nonconductive Vessels ..... 50
Push-Pull Cable Mounting Bracket and Cable Installation.......... 52
Push-Pull Cable Adjustment for Mechanically Controlled
Push-Pull Cable Adjustment for Mechanically Controlled Valve 56
Push-Pull Cable Final Adjustment ................................................... 57
EC300 Marine Control System Installation Manual #1024168
9
Table of Contents
Twin Disc, Incorporated
Electrical Installation ..........................................59
General Electrical Harness Information ......................................... 59
General Electrical Installation Guidelines ...................................... 60
Control Head Harness (J1, J2, or J3) Installation .......................... 66
Multi-Station Single Lever Control Head Wiring Installation........ 67
Multi-Station Dual Lever Control Head Wiring Installation........... 69
Multi-Station Dual Lever Control Head Wiring Instllation Using
Station Doublers ........................................................................... 73
Service Connector (J4) ..................................................................... 78
Transmission Harness (J5, J6, J7 J8, and J12) Installation ........ 78
Control to Bracket Wiring Installation............................................. 79
Bracket to Transmission Wiring Installation ................................. 81
Neutral Start Interlock Wiring Installation....................................... 82
Engine Throttle Wiring Installation.................................................. 85
Prewired Connection Inspection..................................................... 88
Engine Control Harness (J5) Installation ....................................... 89
Neutral Start Interlock Wiring Installtion ......................................... 91
Electronic Control Module Throttle Wiring .................................... 95
Engine Speed Sensor Harness Installation ................................... 99
Engine Room Analog Harness (J6) Installation ........................... 101
Transmission Oil Temperature Sensor Wiring Installation ....... 103
PWM Driver Harness (J7) Installation ........................................... 104
Two Solenoid Transmission Clutch Control Wiring Installation106
Three Solenoid Transmission Clutch Control Wiring Installation ..
Shaft Brake Wiring Installation....................................................... 108
Stabilizer Disable Wiring Installation............................................. 109
Troll Enable Wiring Installation ...................................................... 110
Bridge Signals Harness (J8) Installation ...................................... 111
Ignition Switch Wiring ..................................................................... 112
Manual Override Switch Wiring ..................................................... 114
Tachometer Output Wiring Installation ......................................... 116
Twin Disc Display Harness (J9) Installation................................. 118
Twin Disc Display Harness Wiring ................................................ 120
Communication Harness (J10) Installation .................................. 122
Dual Engine Communication Harness Installation ..................... 123
Multiple Engine Communication Harness Installation ............... 125
10 EC300 Marine Control System Installation Manual #1024168
Table of Contents
Twin Disc, Incorporated
Servo Actuator Harness (J11) Installation .................................... 127
Servo Actuator Harness Wiring ..................................................... 129
Engine Room Switch Harness (J12) Installation ......................... 133
Transmission Oil Filter Differential Pressure Switch Wiring Installation ............................................................................................. 135
Transmission Oil Pressure Switch Wiring Installation ............... 136
EC300 Control Power and Grounding Harness (J13) Installation ..
....................................................................................................... 137
EC300 Control Power Wiring ......................................................... 138
EC300 Control Bonding Installation.............................................. 147
Engineering Drawings ......................................151
List of Engineering Drawings ........................................................ 151
Morse 33 Series Cable Mounting Dimensions ............................ 153
Servo Actuator Mounting Dimensions ......................................... 154
Twin Disc Display Mounting Dimensions (1018791) .................. 155
Control Head Mounting Template ................................................. 156
Side Mount Lever Mounting Template ......................................... 157
Side Mount Selector Assembly Mounting Template .................. 158
EC300 Control Mounting Dimensions .......................................... 159
EC300 Control Pin Assignments ................................................... 160
System 1 - Single Engine, 1 Station .............................................. 161
System 2 - Twin Engine, 2 Stations Sheet 1 - Port Control ........ 162
System 2 - Twin Engine, 2 Stations Sheet 2 - Starboard Control ....
....................................................................................................... 163
System 3 - Twin Engine, 1 Station with Mechanical Actuators
Sheet 1 - Port Control ................................................................. 164
System 3 - Twin Engine, 1 Station with Mechanical Actuators
Sheet 2 - Starboard Control ....................................................... 165
System Control - EC300 with MAN Engine, Sheet 1 (1024103) . 166
System Control - EC300 with MAN Engine, Sheet 2 (1024103) . 167
Wiring Diagram Sheet 1 - Port Control ......................................... 168
Wiring Diagram Sheet 2 - Starboard Control ............................... 169
11
EC300 Marine Control System Installation Manual #1024168
Table of Contents
Twin Disc, Incorporated
Appendix - A....................................................... A-1
Environmental Specifications ........................................................ A-1
Appendix - B ......................................................B-1
Engine Connection Requirements ................................................ B-1
Transmission State Signals ......................................................... B-11
12 EC300 Marine Control System Installation Manual #1024168
Introduction
Twin Disc, Incorporated
Introduction
Preface
4.
5.
6.
The Twin Disc Incorporated product line of electronic Marine Control Systems provides remote operation of engine throttle and transmission engagement.
The model EC300 Marine Control System is designed for use with current
Electronic Throttle and/or Electric Shift propulsion systems used within the pleasure and work-boat markets. The EC300 Control has many special features which provide flexibility and adaptability for use with the vast majority of engine/ transmission combinations including options such as Engine Sync, Trolling,
Shaft Brake, Mechanical Actuator Output, Transmission Oil Pressure and Oil
Temperature Monitoring, and Helm Display.
The following installation instructions provide the necessary information on
Component Installation, Electrical Installation, and Configuration. Review the entire manual for the options specific to your application, and become familiar with all Customer Supplied materials and tools that may be required. In addition, while the manual is outlined for the general sequence of installation from setup through troubleshooting, a good understanding of all aspects of the installation will help make for a smoother installation process.
The installation procedure is as follows:
1.
Read and understand this manual. Contact the supplier of the system, your local Twin Disc Distributor, or the Twin Disc Incorporated website for help: http://www.twindisc.com
2.
Locate desired positions for Control Heads, Controls and general routing of interconnecting harnessing.
3.
Identify locations for vessel interconnections such as Ignition, Power
Wiring, Electronic Throttle, Electric Shift, Speed Sensing etc. The engine manual, transmission manual, and vessel wiring diagrams may be needed for reference.
Purchase/fabricate any necessary “Customer Supplied” items or tools.
Install system components.
Install harnessing and wiring.
13
EC300 Marine Control System Installation Manual #1024168
Introduction
Twin Disc, Incorporated
7.
8.
Inspect and compare the installation against this manual and applicable system drawings. Correct any discrepancies.
Record all component part numbers and serial numbers. Document all customer supplied and connected wiring. Include wire colors and location in document.
9.
Test the system. Complete any necessary troubleshooting and adjustments. (See configuration Manual)
10.
Sea trial the vessel.
14 EC300 Marine Control System Installation Manual #102
4168
Twin Disc, Incorporated
Introduction
General Information
This publication provides the information necessary for the installation of the
Twin Disc Model EC300 Control System.
The components as supplied with the order meet the codes and standards that were applicable when the order was placed. Applicable codes and standards include:
American Boat & Yacht Council (ABYC) Direct Current (DC) Electrical
Systems on Boats Standard E-9.
American Bureau of Shipping’s (ABS) Rules for Building and Classing
Steel Vessels 2002.
American Bureau of Shipping’s (ABS) Rules for Building and Classing
Steel Vessels Under 90 Meters (295 Feet) 2001.
Russian Maritime Registry Service’s (RMRS) Rules for the Classification and Construction of Sea-Going Ships. Part XI. Electrical Equipment,
Part XV. Automation
Russian Maritime Registry Service’s (RMRS) Rules for Technical
Supervision During Construction of Ships and Manufacture of Materials and Products for Ships. Part IV. Technical Supervision During
Manufacture of Products
The customer is responsible for meeting all currently applicable code and standard requirements for the component installation at the time of installation.
The following instructions cover the typical installation of a single or twin-engine system with one, two, or three control stations as standard equipment.
Additionally, these instructions cover installation of up to eight engine systems with optional accessories and cables.
The EC300 Control System is supplied in response to customer specific applications. Based upon the details of the order, certain features and options that are described in this manual will not be applicable. For specific component information, refer to the system installation drawing supplied for your application.
Restriction Notice:
This document contains proprietary Twin Disc Incorporated information. Neither receipt nor possession thereof confers any rights to reproduce, use or disclose, in whole or in part, any such information without express written authorization from the
Corporate Engineering Control Systems, Twin Disc Incorporated,
Racine, WI 53405.
EC300 Marine Control System Installation Manual #1020607
15
Introduction
Twin Disc, Incorporated
Replacement Parts
Parts List
Engineering assembly drawings are provided in appropriate sections of this manual to facilitate ordering spare or replacement parts. Current system drawings are available from Twin Disc Incorporated or the nearest authorized
Twin Disc Incorporated Distributor.
Ordering Parts
WARNING
All replacement parts or products must be of Twin Disc Incorporated origin or equal, and otherwise identical with components of the original equipment. Use of any other parts or products will void the warranty and may result in malfunction or accident, causing injury to personnel and/or serious damage to the equipment. Twin Disc Incorporated absolves itself of any responsibility resulting from any external, internal or installation changes made in the field without the express written approval of Twin Disc Incorporated.
Renewal parts and service parts kits may be obtained from an authorized Twin
Disc Incorporated distributor or service dealer.
16 EC300 Marine Control System Installation Manual #1024168
Twin Disc, Incorporated
Introduction
Safety
All people installing and operating this unit must employ safe operating practices. Twin Disc Incorporated is not responsible for any personal injury resulting from any unsafe and careless use of hand tools, power tools, lifting equipment, or from any unsafe practices during installation and operation.
Because of the possible danger to people or property from accidents that may result from the use of manufactured products, it is important that correct procedures be followed. Products must be used in accordance with the information specified.
Proper installation procedures must be used. Proper safety devices, such as guards, may be required as specified in applicable codes. Safety devices are not provided by Twin Disc Incorporated nor are they the responsibility of Twin
Disc Incorporated.
Source of Service Information
All information, illustrations and specifications in this manual are based on the latest information at the time of publication. The right is reserved to make changes at any time without notice.
Individual product service bulletins are issued to provide Twin Disc distributors with immediate notice of new service information. These service bulletins are distributed to all Twin Disc EC300 Control distributors throughout the United
States and many foreign countries.
For the latest service information on Twin Disc Incorporated products, contact any Twin Disc distributor or service dealer. For a complete list of Twin Disc
Distributors or Service Dealers, please see our Corporate website at http:// www.twindisc.com. For additional information you may contact Twin Disc
Incorporated Product Service by e-mail at [email protected] or phone at
(800) 558-3208 ext 2727.
EC300 Marine Control System Installation Manual #1024168
17
Introduction
Twin Disc, Incorporated
Required Tools
18
Installation and Set-up may require the following tools:
Electric or pneumatic drill
Assorted drill bits
Center punch
#1 Phillips screwdriver
Screwdriver with a 1/8 in. blade
Wire terminal crimpers
Wire strippers
DC voltmeter or multimeter
Watch with a seconds hand
Tachometer, oscilloscope, or frequency counter for troubleshooting dual engine applications
3/32 in. hex key (Allen) wrench
1/8 in. hex key (Allen) wrench
Deutsch crimp tool (P/N HDT 48-00) for 12 to 24 AWG wire sizes
Torque wrench capable of measuring 4.52 Nm (40 lb-in.) for installing a speed sensor in the flywheel housing and for mounting components
File, rasp, or sandpaper to smooth cut surfaces
500 VDC Megohmmeter for testing power wiring as per ABS requirements.
Laptop with latest MFST software updates
EC300 Communication Kit (Twin Disc p/n 1021108)
EC300 Display Harness and Display (Twin Disc p/n 1018791)
EC300 Marine Control System Installation Manual #1024168
Twin Disc, Incorporated
Introduction
Basic System Components
This section serves as a guide for your pre-installation parts check. Be sure that you have ordered and received all of the basic components necessary for this system installation.
Table 1. Required Components for Typical Applications
Supplied by:
Required Components for Typical Applications
EC300 Control
Qty Qty Qty Qty
1 1 2 2
Single Lever Control Head
(J1, J2, J3)
1
1
2
1
N/A N/A
Dual Lever Control Head
(J1, J2, J3)
N/A N/A
1
2
2
2
Single Lever Station Harness
(J1, J2, J3)
Dual Lever Station Harness
(J1, J2, J3)
Transmission Harness (J5, J6, J7,
J8) EC300 Control to Bracket
1 2
N/A N/A
N/A N/A
1 2
1
3
1
3
2
3
2
3
EC300 Marine Control System Installation Manual #102
4168
19
Introduction
Twin Disc, Incorporated
Transmission Harness (J5, J6, J7,
J8) Bracket to Transmission
1
4
1
4
2
4
2
4
J5 Engine Control Harness
1 1 2 2
J5 Speed Sensor Harness
1 1 2 2
J6 Engine Room Analog Harness
Speed Sensors (See Table 3)
J7 PWM Driver Harness
J8 Misc Bridge Harness
1
2
5
2
5
4
5
1
1
1
2
2
1 2 1
J10 Communication Harness
J13 Power Harness
(See Table 4)
N/A N/A
1 2
1
The Control Head can be ordered with the lever on the left or right side.
2
The Dual Lever Control Head can be replaced with optional Split Single Lever Control Heads, or a
Side Mount Control Head Assembly.
3
Harness Assembly, eliminating the need for individual harnesses. Various harness options are available to accommodate diffferent transmission and control system options.
4
Harness Assembly, eliminating the need for individual harnesses. Various harness options are available to accommodate diffferent transmission and control system options.
5
Quantity indicated is based on the requirement for an input and output speed sensor.
1
1
2
4
5
2
2
1
2
20 EC300 Marine Control System Installation Manual #1024168
Twin Disc, Incorporated
Introduction
Table 2. Optional Components
Supplied by:
Optional Components
Display
Qty Qty Qty Qty
1
1
1
1
2
1,2
2
1,2
J9 Display Harness
1
1
1
1
2
1
2
1
Station Doubler
* * * * * * * *
Servo Actuator
1
3
1
3
2
3
2
3
J11 Servo Harness
1
3
1
3
2
3
2
3
J12 Engine Room Switch Harness
1
4
1
4
2
4
2
4
* *
1
Optional Display. The use of a display will require the installation of a J9 Display Harness.
2
One Per station.
Optional Station Doublers are required in applications requiring more then 3 control stations per
EC300 Control (maximum of 5). J1 connection will not support a Station Doubler.
3
Optional Servo Actuator is required for the operation of mechanical control. Installation of a Servo
Actuator will require the installation of a J11 Servo Harness
4
Optional Oil Filter Differential and Oil Pressure Switches - used to trigger a fault condition when active.
EC300 Marine Control System Installation Manual #1024168
21
Introduction
Twin Disc, Incorporated
Table 3. Typical Speed Sensor Types
Single Output Magnetic Pickup Sensors are available with various thread sizes and connectors.
Dual Output Magnetic Pickup Sensors are available with various thread sizes and connectors.
Tachometer Generator with Drive Tang.
One input speed sensor is required for each engine and one shaft speed sensor is required per transmission. On a dual output speed sensor, one output can be used for EC300 input and the other output can be used for instrumentation. The dual-output pickup can be installed in place of existing pickups if both are electrically compatible.
Note: On multiple engine vessels, each engine must use speed sensors of the same type, model, and part number.
Table 4. Communications Harness Components for Twin Engine Basic Systems
Communications Harness Components *
General Drawing
Supplied by
Component Name
Tw in Disc Customer Qty
Controller
Communications
Harness
Communications
Harness
2
1
1
1
J1939 T-Connector
Receptacle
Terminating Resistor
Plug
2
2
1
2
* Required for multiple engine systems
1
Add one (1) additional component for each additional engine (more than two).
2
Quantity does not change, regardless of the number of engines.
22 EC300 Marine Control System Installation Manual #1024168
Twin Disc, Incorporated
Introduction
Additional Materials
Installation requires the following supplies that are not furnished with the basic control system:
Brackets, fasteners, and other hardware for mounting the components
Note: Use 6.35 mm (0.25 in.) maximum fastener diameter to
mount the control(s).
Wire terminal lugs, cable ties, cable clamps, insulating materials, and other electrical hardware (Refer to General Installation Guidelines for more information about the electrical hardware requirements.)
Hook-Up Wire, stranded copper (19 strands or more); 14 AWG (15 amps max.) unless otherwise specified; rated for 50 VDC, conforming to UL
1426 Cables for Boats or other applicable standards; marked with type/ style, voltage, size, and dry temperature rating; color coded as shown in
Table 5.
Note: Table 5 provides color code requirements for those
vessels subject to American Boat & Yacht Council (ABYC)
Standard E-9 requirements.
Table 5. Power Wire Color Codes as per ABYC Standard E-9
Color Code
Yellow w/Red Stripe
Function
Neutral Start Relay Contacts (J5 pins 9 & 10)
Purple
Yellow (preferred) or Black
Red
Ignition Switch (J8 pin 1)
Battery Negative (-) (J13 pin 3)
Battery Positive (+) (J13 pin 1)
Auxilliary Battery Positive (+) (J13 pin 2)
Green w/Yellow Stripe (preferred) or Green
DC Grounding Conductors or Bonding Only
Starter Solenoid Circuits Greater Than 5 Amps
Relay, Normally Open (NO) Single Pole Single Throw (SPST), coil voltage rating equal to the starter solenoid voltage, contact current rating greater than the starter solenoid current, one (1) required per control, customer supplied.
EC300 Marine Control System Installation Manual #102
4168
23
Introduction
Twin Disc, Incorporated
24 EC300 Marine Control System Installation Manual #1024168
Component Installation
Twin Disc, Incorporated
Component Installation
General Component Installation Guidelines
Ensure a suitable location is chosen for mounting the EC300 Control(s),
Control Head(s), Twin Disc Display(s), and any other components. EC300
Controls should be mounted near the engines in a location reasonably free from direct splash and spray, and protected from mechanical abuse. See
Appendix - A for Environmental Specifications. When selecting the location
for mounting the components, consideration should be given to any pushpull cable routing in order to avoid sharp bends or excessive lengths. The mounting surface should be flat, or shimmed so that the control enclosure is secured without distortion to the bottom plate. Controls should not be mounted on the engines unless they are protected by a heat shield and mounted to a vibration-damped plate.
Choose a location that meets the following criteria:
It is not on any drivetrain component.
It is away from heat sources.
It is clear of service and access areas.
It is away from AC power and high current conductors.
It is protected from submersion or splash.
It will not provide a “step” for personnel.
It is a minimum of 1 m (3.3 ft) away from alternators, generators, communications equipment, and associated wiring.
It is away from high vibration.
It provides easy access for routing, connecting, and adjusting the push-pull cable, if used.
It is convenient for accessing the electrical connections.
Control equipment and displays are to be so placed or protected as to minimize the likelihood of sustaining damage from the condensation of moisture, accumulation of dust, oil vapors, steam, dripping liquids, or from activities around their location.
EC300 Marine Control System Installation Manual #1024168
25
Component Installation
Twin Disc, Incorporated
26
There are other factors to consider when choosing a mounting location for the
EC300 Controls and Servo Actuators.
Push-pull cable installation should meet the following criteria:
Cables should be minimum length possible.
Any cable bends should have no sharp bends. Install with the maximum possible bend radius. Refer to cable manufacturer’s specifications.
Cables must be located away from hot surfaces.
Cables must be clear of service or access areas.
Cables must be Morse Series 33 RED JAKET ® Supreme or equivalent.
Electrical wiring and routing should meet the following criteria:
Wiring must be minimum practical length.
Wiring must be located away from high current conductors and devices.
Wiring must be located away from hot surfaces.
Wiring must be clear of service and access areas.
Wiring should be at least 1 m (3.3 ft) away from communications equipment, antennas, and associated leads.
Wiring should be at least 1 m (3.3 ft) away from alternators, generators, and ignition systems.
Wiring should have drip loops where required, especially at the controls.
Use the correct fasteners and mounting hardware as follows:
Use any fasteners and mounting hardware as supplied from Twin
Disc Incorporated with the component.
Use stainless steel fasteners unless otherwise specified.
Use lock washers as specified.
EC300 Marine Control System Installation Manual #1024168
Twin Disc, Incorporated
Component Installation
EC300 Control Installation
Note: The EC300 Control can be mounted in any orientation on a flat surface.
TWIN DISC
INCORPORATED
MODEL EC300
P/N 1020676
BOM
S/N
VOLTAGE 12-24VDC
J1 J2 J3 J4 J5 J6 J7
J8 J9 J10 J11 J12 J13
Figure 1. Preferred Mounting Arrangement for EC300 Control
1.
Locate a solid, flat surface where the three enclosure mounting feet contact and are parallel to the mounting surface.
2.
Note: All mounting hardware must be corrosion resistant.
If required, fabricate brackets, shims, or spacers in order to provide a flat surface.
3.
Note: Refer to the EC300 Control Mounting Dimensions drawing (1020676) in Engineering Drawings.
Mark and drill three (3) mounting holes for the 6.35 mm (0.25 in.) mounting hardware.
4.
5.
Mount the control using three (3) sets of fasteners and lock washers.
Note: Place lock washers under the mounting screw heads.
Tighten fasteners up to 1.13 Nm (10 lb-in.) maximum.
EC300 Marine Control System Installation Manual #1024168
27
Component Installation
Twin Disc, Incorporated
Control Head Installation
A control station is a location from which the boat can be operated. A control station will consist of one or more Control Heads. Each control station requires the installation of a Control Head and associated wiring harnesses. The control station may consist of a single or dual lever Control Head, multiple
Control Heads, or a side mount Control Head Assembly. There are separate instructions for the single/dual lever Control Head and the side mount Control
Head Assemblies.
Note: Only EC300 Control Heads will work with the EC300
Control. The EC200/250/251 Control Heads are not compatible.
Note: Locate the Control Head(s) where they will not be in direct spray, splash, or submerged.
Note: Chrome plated Control Heads should be polished periodically using a chrome polish to help retard corrosion.
The following subsections make up this section:
Single/Dual Lever Control Head Assembly
Side Mount Control Head Assembly
Drag Adjustment Procedures
28 EC300 Marine Control System Installation Manual #1024168
Twin Disc, Incorporated
Component Installation
Single/Dual Lever Control Head Assembly
The Control Head may be either a single or dual lever version. This installation procedure applies to both versions.
Note: If this is a new installation, ensure that all required components are properly located before cutting the first hole. Other components that may require installation include a display, an ignition switch or instrumentation gauges.
Note: At least 25.4 mm (1 in.) of clearance is required at both ends of the lever travel for the operator’s hands (see
Figure 3). Clearance must be provided beneath the
Control Head to accommodate the base, an electrical connector and a harness. The Control Head should be installed at least 1 m (3.3 ft) away from any communications equipment and associated leads.
1.
Select a mounting location that is flat, readily accessible, permanent, and solid.
154.9
(6.10)
160.8
(6.33)
72.4
(2.85)
PORT
LEVER
N
GEAR SHIFTER IS IN
WHEN INDICATOR ON.
SY
PRESS
CRUISE
TROLL
STATION
N
PORT STBD
TWIN DISC EC300
POWER COMMANDER R
MODE
SELECT
SWITCH
STATION SELECT
INDICATOR LED
(2 PLACES)
127
(5.0)
MINIMUM RECOMMENDED
MAINTENANCE CLEARANCE
NEUTRAL
INDICATOR LED
(2 PLACES)
SYN
C
EXP
RES
S
TRO
LL
CRU
ISE
R
STBD
LEVER
STATION
SELECT
BUTTON
Figure 2. Front View of Dual Lever Control Head With Levers in Neutral
EC300 Marine Control System Installation Manual #1024168
29
Component Installation
Twin Disc, Incorporated
2.
3.
Cut out the Control Head Mounting Template in Engineering Drawings in the back of this manual, and tape it in the desired location.
Note: The template provided with the control is direction specific. Ensure that the “ahead” direction on the template is pointing toward the bow in order to ensure that the forward motion of the lever is directed ahead.
Ensure that the control head location provides clearance for the operator’s hands over the full range of lever travel.
ASTERN DETENT POSITION
AHEAD DETENT POSITION
15 o
15 o
ASTERN
55 o
AHEAD
55 o
30
25.4
(1.0)
72.4
(2.85)
25.4
(1.0)
CLEARANCE REQUIRED
TO AVOID PINCH POINTS
(BOTH SIDES)
127
(5.0)
MINIMUM RECOMMENDED
MAINTENANCE CLEARANCE
Figure 3. Side View of Control Head With Lever Clearance Shown
4.
Center punch the four (4) mounting holes and scribe the base cutout outline.
EC300 Marine Control System Installation Manual #1024168
Twin Disc, Incorporated
Component Installation
5.
Remove the template.
Note: The hole cannot be smaller than shown on the template and must be properly aligned with the mounting holes.
Drill and cut the holes using the template markings.
6.
7.
8.
Check the hole locations with the template.
Remove any splinters or sharp edges from the holes.
9.
Check the fit by carefully placing the Control Head in the hole.
10.
Remove the Control Head from the cutout.
11.
Correct the fit as necessary.
12.
Set drag per Control Head Lever Drag Adjustment. See Control Head
Note: Drag adjustment is provided at each lever. Proper adjustment is necessary to ensure that the lever remains in the intended position without operator assistance.
13.
Install and mount the Control Head using the supplied gasket and four (4) oval head #10 screws or equivalent.
Note: All fastening hardware must be corrosion resistant.
Note: The type of fastener to be used depends on material used for the support. Each Control Head is supplied with stainless steel 38 mm (1.5 in.) screws suitable for mounting in a dash up to 19 mm (0.75 in.) thick. Use the appropriate fastener for the specific installation.
14.
Torque the fasteners to 1.13 Nm (10 lb-in.) maximum.
15.
Install and mount the Control Head using the supplied gasket and four
(4) oval head #10 screws or equivalent.
16.
Torque the fasteners to 1.13 Nm (10 lb-in.) maximum.
Reference Control Head Harness (J1, J2, or J3) Installation for cable installation.
EEC300 Marine Control System Installation Manual #1024168
31
Component Installation
Twin Disc, Incorporated
LEVER
Side Mount Control Head Assembly (Binnacle/Console Station)
The side mount Control Head Assembly consists of a Lever, Interface
Assembly, Interface harness and Selector Assembly. The lever may be supplied by Twin Disc or other sources. Specific lever attachment instructions should be supplied with the lever and the lever must be capable of attaching to the 15.87
mm (0 .625 in.) diameter shaft of the Interface Assembly. The Interface Assembly comes with a mounting plate for sandwiching the console wall between the assembly and the mounting plate. The Selector Assembly mounts directly to the surface of the console.
1.
2.
Locate a position on the side of the console which provides the operator with unrestricted access to the lever(s), while providing full range (70 degrees either side of neutral) of lever motion.
Locate a position on the top or front surface of the console which provides unrestricted access to the Selector Assembly. Confirm that the desired location will allow the Interface Harness to reach between the Interface Assembly and the Selector Assembly.
HARNESS, WIRING
SIDE MOUNT
HARNESS, WIRING
SIDE MOUNT
SELECTOR ASSY
DUAL SIDE MOUNT
N
GEAR SHIFTER IS IN
NEUTRAL POSITION
WHEN INDICATOR ON.
SYNC
EXPRESS
CRUISE
TROLL
N
PORT
STATION
SELECT
STBD
TWIN DISC EC300
POWER COMMANDER
R
LEVER
32
INTERFACE ASSY INTERFACE ASSY
MOUNTING PLATE
HARNESS, WIRING
DUAL LEVER
TO STBD CONTROL TO PORT CONTROL
Figure 4. Side Mount Control Head Assembly
MOUNTING PLATE
EC300 Marine Control System Installation Manual #1024168
Twin Disc, Incorporated
Component Installation
3.
4.
5.
Cut out the Interface Assembly Mounting Template and Selector
Assembly Mounting Template from the Engineering Drawings and tape in the selected positions.
Note: For twin engine applications, the template to mount the
Starboard Interface Assembly is flipped over and then rotated 90 degrees counterclockwise from the Port
Interface Assembly. See Figure 5.
Use the scale marks on the template to verify that the template is the correct size. (Scale = 1:1)
Using the templates, mark all necessary holes and cutouts.
Locate * in Upper
Front Corner of Console
Port
*
Locate * in Upper
Front Corner of Console
*
Starboard
Drawing Not To Scale
7.
8.
Figure 5. Side Mount Interface Assembly Mounting Template Position
6.
Drill and cut the holes using the template markings.
Check the hole locations with the template.
Remove any splinters or sharp edges from the holes.
EC300 Marine Control System Installation Manual #1024168
33
Component Installation
Twin Disc, Incorporated
9.
Check the fit of the holes by carefully inserting the Interface and Selector assemblies.
10.
Correct the fit as necessary.
157.10
(6.185)
46.23
(1.82)
22.22
(.875)
19.04
(.750)
NOMINAL
SCREW, FLAT HEAD
10-32 X 1 1/2
4 PLACES
15.87 ( .625) SHAFT
WITH 3/16" KEYWAY
34
INTERFACE ASSEMBLY
MOUNTING PLATE
CONSOLE
Figure 6. Side Mount Interface Mounting
11.
Install the Selector Assembly using the gasket and stainless steel hardware provided with the unit.
12.
Set drag per Control Head Lever Drag Adjustment. See Control Head
Lever Drag Adjustment on page 33.
Note: Drag adjustment is provided at each lever. Proper adjustment is necessary to ensure that the lever remains in the intended position without operator assistance.
13.
Install the Interface Assembly/Assemblies using the mounting plate and stainless hardware provided.
14.
Connect the Interface Harness between the Interface Assembly and the
Selector Assembly and secure/strain relieve as necessary.
15.
Attach the Lever to the 15.87 mm (0 .625 in.) diameter shaft of the
Interface Assembly, following the instructions provided with the lever.
EC300 Marine Control System Installation Manual #1024168
Twin Disc, Incorporated
Component Installation
Control Head Lever Drag Adjustment
1.
2.
Adjust drag as needed. Refer to Figure 7 and 8 for drag adjustment screw locations.
Access the drag adjustment screw and insert an 1/8 in. hex key wrench into the opening for each lever. Remove the access screw on side mount control heads. See Figure 7 and Figure 8.
3.
Tighten the drag adjustment screw(s) until the desired drag is obtained over the full lever travel.
Note: 0.45 to 0.91 kg (1 to 2 lb) average drag is normally desirable.
DRAG ADJUSTMENT
DRAG ADJUSTMENT
Figure 7. Drag Adjustment Screws for Single/Dual Lever Control Head
REMOVE SCREW
TO ACCESS
DRAG ADJUSTMENT
Figure 8. Drag Adjustment Screws for Side Mount Control Head
Assembly
EC300 Marine Control System Installation Manual #102416
35
Component Installation
Twin Disc Display Installation
Twin Disc, Incorporated
36
3.
4.
1.
2.
5.
Figure 9. Twin Disc Display
Note: Ensure that all items are located for installation on the dash or control panel before cutting the first hole.
Note: One (1) display is provided as an option for each EC300
Control. Multiple displays may be provided to support multiple control stations.
Note: The Twin Disc Display is designed to mount from the front through a 3.2 to 19 mm (0.125 to 0.75 in.) thick panel
or dash. See Twin Disc Display Mounting Dimensions
(1018791) in Engineering Drawings. The mounting
bracket is installed from the rear. Wiring should be connected while the display is accessible.
Locate a position on the dash or control panel for the display.
Using the appropriate cutting tools, cut a 54 mm (2.125 in.) hole.
Round off any sharp edges and remove any burrs.
Remove the mounting bracket and nuts from the rear of the display.
Ensure that the display will fit in the hole.
EC300 Marine Control System Installation Manual #1024168
Twin Disc, Incorporated
Component Installation
6.
Install gasket on display. (See Twin Disc Display Harness (J9) installation for wiring instructions.)
Insert the display in the dash or control panel.
7.
8.
Attach the mounting bracket and tighten the nuts until the display is firmly secured in the dash.
If applicable, repeat steps 1 through 8 for each additional display.
9.
Refer to Twin Disc Display Harness (J9) Installation for display harness wiring installation.
EC300 Marine Control System Installation Manual #1024168
37
Component Installation
Twin Disc, Incorporated
Speed Sensor Installation
Applications with options such as Sync Mode (engine synchronization), Express
Mode, and Troll Mode require the installation of an engine speed sensor and/ or transmission output speed sensor. Engine speed sensors (transmission input) are most often installed on the marine transmission, however in some cases the engine speed sensor is installed on the engine flywheel. The output speed sensor may be installed directly into the transmission or on a bracket near the output shaft with a speed pick-up wheel connected to the output flange.
Only Twin Disc speed sensors are acceptable for the output shaft speed.
There are many types of engine speed sensors available and many will work with the EC300 Control System. This section outlines the installation of the sensors available from Twin Disc Incorporated. Contact Twin Disc, or the nearest distributor, for the possible use of other sensors.
The Speed Sensor is a cylindrical-threaded component that screws into either the engine flywheel housing; the transmission housing; or into a bracket on the output side to sense transmission output speed. It is triggered by the crown of the gear teeth when they pass in close proximity to the end of the speed sensor.
The Speed Sensor produces an output signal of one pulse per gear tooth. The
EC300 Control software converts the individual pulse signals into revolutions per minute (rpm). The number of teeth on the gear must be known in order for the software to be properly configured. This information is either supplied by the engine supplier if flywheel mounted, or Twin Disc Incorporated if connected to transmission.
38 EC300 Marine Control System Installation Manual #1024168
Twin Disc, Incorporated
Component Installation
Single output speed sensors are preferred over dual output (See Figure 10); however dual output speed sensors are acceptable if the outputs are electrically isolated from each other and have the required electrical characteristics.
SINGLE OUTPUT
DUAL OUTPUT
Figure 10. View of Typical Single and Dual Output Speed Sensors
The following sub-sections make up this section.
Installation – Magnetic Pick-up Engine Speed Sensor
Installation – Hall Effect Pick-up Output Speed Sensor
Installation – Tachometer Signal Generator
EC300 Marine Control System Installation Manual #1024168
39
Component Installation
Twin Disc, Incorporated
Installation – Magnetic Pick-up Engine Speed Sensor
Note: Some transmissions have pre-drilled and plugged sensor holes above the primary or secondary shaft transfer gear.
Note: Some engines have pre-drilled and plugged sensor mounting plates in the flywheel housing. Consult the engine manufacturer if a mounting hole must be added.
Additionally, some engines may already have Speed
Sensors installed in the flywheel housings for the engine tachometers. An existing single output sensor may be replaced with a dual output sensor in order to eliminate the need to add additional holes.
1.
Bump the engine starter until the crown (top) of a gear tooth is visible in the center of the hole. See Figure 11.
Crown of
Gear in
Center of Hole
Direction of
Rotation
Engine Flywheel
Housing
Figure 11. View of Tooth Crown through Speed Sensor Mounting Hole
40 EC300 Marine Control System Installation Manual #1024168
Twin Disc, Incorporated
Component Installation
2.
Thread the lock nut onto the sensor and apply anaerobic sealant equivalent to MA908 (Loctite 242) to the threads of the engine speed sensor near the end away from the wires. See Figure 12.
SINGLE OUTPUT
APPLY SEALANT
TO THREADS
DUAL OUTPUT
Figure 12. View of Typical Single and Dual Output Speed Sensors
3.
Thread the sensor into the sensor opening until it just contacts tip of the gear tooth then back sensor out one full turn.
4.
5.
Tighten the lock nut to 4.52 Nm (40 lb-in.) maximum while holding the
Speed Sensor body in place.
If using a dual-output Speed Sensor, reconnect the original signal cable to one of the sensor outputs.
EC300 Marine Control System Installation Manual #1024168
41
Component Installation
Twin Disc, Incorporated
Installation – Hall Effect Pick-up Output Speed Sensor
Note: Some transmissions have predrilled and plugged sensor holes for the purpose of installing output speed sensors.
Note: Some transmissions may need an output speed pickup wheel installed on the output flange and an output speed bracket installed on the transmission housing to facilitate the installation of an output speed sensor. See
Figure 13.
42
SPEED SENSOR
SPEED PICK-UP BRACKET
SPEED PICK-UP WHEEL
CAP SCREWS
CAP SCREWS
SPEED PICK-UP WHEEL
TRANSMISSION OUTPUT FLANGE
Figure 13. Output Speed Sensor, Pick-Up Bracket, and Speed Wheel
1.
Turn the output shaft until the crown of the gear tooth or speed wheel tooth is centered in the sensor hole. See Figure 11.
2.
3.
4.
Thread the lock nut onto the sensor. Apply anaerobic sealant equivalent to MA908 (Loctite 242) to the threads of the engine speed sensor near the end away from the wires. See Figure 12.
Install sensor until contacts tip of gear tooth and back sensor out two full turns.
Tighten the lock nut to 4.52 Nm (40 lb-in.) maximum while holding the
Speed Sensor body in place.
CAUTION
The Hall Effect Pick-Up output speed sensor used for the EC300 Marine
Control System cannot be used to provide signals to other devices on the vessel. The output signal must be connected directly to the EC300
Control.
EC300 Marine Control System Installation Manual #1024168
Twin Disc, Incorporated
Component Installation
Installation – Tachometer Signal Generator
Tachometer signal generators will also work with the EC300 Control System.
See Figure 14. The tachometer signal generator must be capable of generating an AC signal with a frequency that is proportional to speed. Use a generator that provides the highest frequency possible. A minimum of 15 cycles per crankshaft revolution is required. Twin Disc, Incorporated has a 30 pulse per revolution tachometer signal generator available. The output amplitude of the tachometer signal generator must be a minimum of 1.5 volts RMS AC.
Note: The number of pulses per revolution must be known in order for the EC300 control software to be properly configured.
TACHOMETER
GENERATOR
DRIVE TANG
CUSTOMER SUPPLIED
DRIVE FLANGE
Figure 14. View of Tachometer Signal Generator
Note: Mechanical drive components that are necessary to convert an existing tachometer sender drive to a dual tachometer sender drive must be ordered from the accessory supplier identified on the existing tachometer sender.
CAUTION
The tachometer signal generator output used for the EC300 Marine
Control System cannot be used to provide signals to other devices on the vessel. The signal generator output used must be connected directly to the EC300 Control.
Install the tachometer signal generator as per the manufacturer’s instructions.
Reference Engine Control Harness (J5) Installation and Engine Room
Harness (J6) Installation in the Electrical Installation Section of this manual for complete speed sensor wiring information.
EC300 Marine Control System Installation Manual #1024168
43
Component Installation
Twin Disc, Incorporated
Station Doubler Installation
Station Doublers are used for installations requiring four (4) or five (5) Control
Heads per control. One (1) Station Doubler is required if four (4) Control
Heads are used. Two (2) are required for five (5) Control Heads.
Note: The J1 connection will not support a station doubler and must be connected directly to a Control Head.
9.00
(228.6)
8.50
(215.9)
4.56
(115.8)
3.00
(76.2)
CONTROL
3.88
(98.6)
2.98
(75.7)
TWIN DISC
INCORPORATED
EC300 MODEL
P/N
BOM
S/N
VOLTAGE
Figure 15. Station Doubler Top and Side Views
5.0
(127.0)
MINIMUM
RECOMMENDED
MAINTENANCE
CLEARANCE
44 EC300 Marine Control System Installation Manual #1024168
Twin Disc, Incorporated
Component Installation
1.
2.
3.
4.
Locate a solid, flat surface where the mounting pads contact and are parallel to the mounting surface.
Note: All mounting hardware must be corrosion resistant.
If required, fabricate brackets, shims or spacers in order to provide a flat surface.
Mark and drill four (4) mounting holes for the 6.35 mm (0.25 in.) mounting hardware.
Mount the Station Doubler using four (4) sets of fasteners and lock washers.
Note: Place lock washers under the mounting screw heads.
Tighten the fasteners to 1.13 Nm (10 lb-in.) maximum.
5.
Reference Multiple Station Dual Lever Control Head Wiring Installation for harness installation.
EC300 Marine Control System Installation Manual #1024168
45
Component Installation
Twin Disc, Incorporated
Servo Actuator Installation
The EC300 Control System supports one servo actuated device per control.
The EC300 Control Systems can control either a mechanically shifted transmission, a mechanically controlled throttle, or a mechanically controlled troll valve.
The Servo Actuator can be mounted in any orientation on a flat surface. See
Figure 16 for preferred mounting orientation. The Servo Actuator should be located within the reach of the supplied harness and as close to the engine/ transmission as practical.
Note: The Servo Actuator and Push-Pull Cable Installation process should be read and understood prior to installation of Servo Actuator and related components, to ensure all component mounting positions are located properly and all necessary materials are available for the complete installation.
This section contains the following sub-sections:
Servo Actuator Mounting
Push-Pull Cable Installation Guidelines
Push-Pull Cable Installation Kits for Conductive Vessels
Push-Pull Cable Installation Kits for Nonconductive Vessels z z
Push-Pull Cable Installation z
Mechanically Shifted Transmission
Mechanically Controlled Throttle
Mechanically Controlled Troll Valve
Push-Pull Cable Final Adjustment
46 EC300 Marine Control System Installation Manual #1024168
Twin Disc, Incorporated
Component Installation
Servo Actuator Mounting
The Servo Actuator will accommodate a total push-pull cable stroke of 41 to 84 mm (1.6 to 3.3 in.). It will provide a maximum of 24 kg (53 lb) of force at the innermost point on the lever and a maximum of 11.3 kg (25 lb) of force at the outermost point on the lever.
Figure 16. Preferred Mounting Arrangement for Servo Actuator
1.
Locate a solid, flat surface where the mounting rails contact and are parallel to the mounting surface.
Note: Refer to Servo Actuator Dimensional Drawing in
Engineering Drawings for mounting dimensions for your specific actuator.
Note: All mounting hardware must be corrosion resistant.
Note: Neither the engine nor the transmission push-pull cable clamp and bracket are supplied.
2.
3.
Note: Fabricate brackets, shims or spacers as required to provide a flat surface.
Mark and drill the four mounting holes for the 6.35 mm (0.25 in.) mounting hardware.
Mount the Servo Actuator using four sets of fasteners and lock washers.
Note: Use 6.35 mm (0.25 in.) diameter fasteners and place lock washers under the mounting screw heads.
4.
Install the push-pull cable. Refer to Push-Pull Cable Installation for cable installation.
EC300 Marine Control System Installation Manual #1024168
47
Component Installation
Twin Disc, Incorporated
Push-Pull Cable Installation Guidelines
Correct push-pull cable installation will aid in trouble-free operation of the control system. Different installation kits are available. Where possible, quickdisconnect ball joints should be used to assist in push-pull cable adjustments.
Push-pull cable installation should meet the following guidelines:
Cables must be Morse 33 Series RED JAKET ® Supreme or equivalent.
A minimal number of bends should be used.
Bends should use the maximum possible radius where bends are required. Refer to cable manufacturer specifications.
Cables should not be routed near hot surfaces.
Cables should not be routed in service or access areas.
48 EC300 Marine Control System Installation Manual #1024168
Twin Disc, Incorporated
Component Installation
Push-Pull Cable Installation Kits for Conductive Vessels
Quick-disconnect ball joint kits or terminal eye pins with cable clamps for Morse
33 series push-pull cables are available from Twin Disc Incorporated. See
Figure 17 and Figure 18. The dual kit accommodates one end of two cables.
The single kit accommodates one end of one cable. Each Servo Actuator requires a single kit to connect the cable to the Servo Actuator. Refer to Morse
33 Series Cable Mounting Dimensions in Engineering Drawings for additional information.
#10-32 x 0.75 (2)
CLAMP, MORSE P/N 31509
SHIM, MORSE P/N 31538
#12 EXTERNAL TOOTH LOCK WASHER (2)
RETAINER PLATE
Figure 17. Installing Cable Clamp on Servo Actuator for Conductive
Vessels
MORSE BALL JOINT ASSY.
0.218 ID NYLON FLAT WASHER
ACTUATOR ARM
0.218 ID NYLON FLAT WASHER
MORSE LOCK WASHER
MORSE NUT
Figure 18. Installing Ball Joint Assembly for Conductive Vessels
EC300 Marine Control System Installation Manual #1024168
49
Component Installation
Twin Disc, Incorporated
Push-Pull Cable Installation Kits for Nonconductive Vessels
There is a possibility that high-powered electronic equipment used on vessels built in glass reinforced plastic (fiberglass), wood, or other nonconductive material can produce electrical interference that may affect the operation of the servo actuator or EC300 Control. Most secondary current path sources of interference can be eliminated by insuring there are no “loops” through the engine block or transmission via push-pull cables.
CAUTION
If isolation components are used on any component of the EC300
Control System, they must be used on all components.
For nonconductive vessels, isolating installation kits with cable clamps and terminal eye pins must be used to isolate the Servo Actuator from push-pull cables. See Figure 19 and Figure 20. One kit is required to attach the cable to each Servo Actuator. Consult Twin Disc Incorporated or a local distributor for substitutions or alterations. Refer to Morse 33 Series Cable Mounting
Dimensions in Engineering Drawings for additional information.
#8-32 X 0.75 (2)
#8 SHOULDER WASHER (2)
(TEFLON/NYLON)
CLAMP, MORSE P/N 31509
SHIM, MORSE P/N 31538
0.218 ID NYLON FLAT WASHER (2)
ACTUATOR PLATE
0.218 ID NYLON FLAT WASHER (2)
#8-32 STOP NUT (2)
W/NYLON INSERT
Figure 19. Installing Cable Clamp on Servo Actuator for Nonconductive
Vessels
50 EC300 Marine Control System Installation Manual #1024168
Twin Disc, Incorporated
Component Installation
RETAINING RING
NYLON TERMINAL EYE
MORSE P/N 300646
MODIFIED TERMINAL PIN
MORSE P/N 301456
0.250 ID FLAT WASHER
ACTUATOR ARM
0.250 ID FLAT WASHER
MORSE LOCK WASHER
MORSE NUT
Figure 20. Installing Terminal Eye Pin for Nonconductive Vessels
EC300 Marine Control System Installation Manual #1024168
51
Component Installation
Twin Disc, Incorporated
Push-Pull Cable Mounting Bracket and Cable Installation
This section describes how to install the push-pull cable for a mechanically shifted transmission, for a mechanically controlled throttle, and for a mechanically controlled troll valve. See Figures 21 - 25.
Note: Use either a Conductive or Nonconductive Push-Pull
Cable Installation Kit as required by the vessel.
PULL
POSITION
PUSH
POSITION
ADJUSTING CLAMP
CENTERS TRAVEL
TO MATCH CABLE
WITH ACTUATOR
ADJUSTING BALL JOINT POSITION
UP INCREASES CABLE TRAVEL
ADJUSTING BALL JOINT POSITION
DOWN DECREASES CABLE TRAVEL
PUSH-PULL CABLE
CABLE CLAMP
TERMINAL EYE PIN OR
BALL JOINT CONNECTOR
MOUNTING PAD
Figure 21. Servo Actuator Push-Pull Cable Installation
1.
Fabricate a push-pull cable mounting bracket as needed, to attach/clamp the cable to the engine or transmission. The critical dimension is 7.25
inches from centerline of the clamp mounting holes to centerline of the engine/transmission lever. See Figure 22. Secure the bracket to engine/ transmission.
CUSTOMER SUPPLIED
STATIONARY MOUNTING
BRACKET
184.15
(7.25)
52
SERVO ACTUATOR
ENGINE or TRANSMISSION
Figure 22. Push-Pull Cable Mounting Bracket
EC300 Marine Control System Installation Manual #1024168
Twin Disc, Incorporated
Component Installation
CAUTION
Brackets must be located to allow the most direct and unrestricted movement of push-pull cable. Bends, kinks, and tight or multiple radii will cause premature wear and undesirable engine/transmission response.
2.
The Servo Actuator end of the push-pull cable may be adjusted for a range of travel from 1.5-3.5 inch. Loosely attach the cable at the engine/ transmission using a mounting arrangement which allows for a cable travel within the 1.5-3.5 inch range. In rare instances, modifications to the engine/transmission lever are required to meet this range of travel.
(For example: If the travel is less than the 1.5 inch, then the engine/ transmission lever may need to be lengthened, or an additional hole added to the existing lever.) Loosely attach the other end of the pushpull cable to the Servo Actuator. Confirm that the cable travel is within the 1.5-3.5 inch range and tighten the engine/transmission end. Leave the Servo Actuator end loose.
Proceed to the push-pull cable adjustment section for either the mechanically shifted transmission, mechanically controlled throttle, or mechanically controlled troll valve to perform the initial push-pull cable adjustment.
EC300 Marine Control System Installation Manual #1024168
53
Component Installation
Twin Disc, Incorporated
Push-Pull Cable Adjustment for Mechanically Shifted Transmission
The transmission’s gear select actuator is a three-position device: 45 degree left, center, and 45 degree right. See Figure 23. The control will drive the Servo
Actuator to these positions as commanded by ahead, neutral, or astern commands from the control head. The push-pull cable positions the gear select lever in the desired position.
ASTERN
NEUTRAL
AHEAD
ASTERN
NEUTRAL
AHEAD
TRANSMISSION
SERVO ACTUATOR ENGINE
Figure 23. Transmission Gear Select Actuator
1.
Position Control Head lever at the Forward Detent. The Servo Actuator lever will move to the Forward position.
2.
3.
4.
Position the transmission lever to Forward Detent. The attached pushpull cable will move accordingly.
Make note of the push-pull cable position at the Servo Actuator end, comparing the location of the cable to the Servo Actuator lever. Using a piece of tape and pen/marker, mark the Servo Actuator with the position of the cable end.
Repeat with the Control Head lever at the Reverse Detent. The Servo
Actuator will move to the Reverse position.
Note: When you adjust the push-pull cable travel for Forward and Reverse positions, Neutral will automatically be centered. However, you cannot adjust the push-pull cable for Neutral and then assume the Forward and
Reverse positions will be aligned.
Proceed to Push-Pull Cable Final Adjustment.
54 EC300 Marine Control System Installation Manual #1024168
Twin Disc, Incorporated
Component Installation
Push-Pull Cable Adjustment for Mechanically Controlled Throttle
The engine’s throttle actuator is a two-position device with continuous control between the two end positions. The nominal end positions are at 45 degrees left and 45 degrees right. See Figure 24. The control will drive the Servo Actuator between these positions as commanded by the lever position at the Control
Head. The push-pull cable positions the throttle actuator in the corresponding position.
FULL
IDLE
FULL
IDLE
SERVO ACTUATOR
TRANSMISSION
ENGINE
Figure 24. Engine Throttle Actuator
1.
Position Control Head lever at the Neutral Detent. The Servo Actuator lever will move to the idle position.
2.
3.
4.
Position engine lever to Idle. The attached push-pull cable will move accordingly.
Make note of the push-pull cable position at the Servo Actuator end, comparing the location of the cable end to the Servo Actuator lever.
Using a piece of tape and pen/marker, mark the Servo Actuator with the position of the cable end.
Repeat with the Control Head lever in Full Throttle position. The Servo
Actuator lever will move to the full throttle position.
Proceed to Push-Pull Cable Final Adjustment.
EC300 Marine Control System Installation Manual #1024168
55
Component Installation
Twin Disc, Incorporated
Push-Pull Cable Adjustment for Mechanically Controlled Troll Valve
The transmission’s troll valve is a two-position device with nominal positions at
45 degree left and 45 degree right rotation. See Figure 25. The Control will drive the Servo Actuator to these positions as commanded by lever position at the Control Head. The push-pull cable positions the troll valve in the desired position.
CRUISE
TROLL
TROLLING VALVE
CRUISE
TROLL
SERVO ACTUATOR
TRANSMISSION
ENGINE
Figure 25. Transmission Troll Valve Actuator
1.
Position the Control Head lever at the Neutral Detent and the Mode
Select Switch to TROLL. The Servo Actuator will move to the Full
Slip/Troll position.
2.
Position the transmission trolling lever to Full Slip/Troll. The attached push-pull cable will move accordingly.
3.
Make note of the push-pull cable position at the Servo Actuator end, comparing the location of the cable end to the Servo Actuator lever.
Using a piece of tape and pen/marker, mark the Servo Actuator with the position of the cable end.
4.
Repeat steps 1 - 3 with the Control Head Mode Select Switch in CRUISE.
The Servo Actuator will move to the Lockup/Cruise position.
Proceed to Push-Pull Cable Final Adjustment.
56 EC300 Marine Control System Installation Manual #1024168
Twin Disc, Incorporated
Component Installation
Push-Pull Cable Final Adjustment
CAUTION
Final adjustments/alignment of the push-pull cable must be completed with power applied to a functioning control system. All power wiring and Control System checks must be made prior to proceeding with the final adjustments/alignment of the push-pull cable. Disconnect the quick connect on the push-pull cable from the Servo Actuator lever to perform the power wiring and Control System checks.
1.
2.
Power up the Control System and take command at a Control Head.
Use the Control Head closest to where the Servo Actuator is located, or have one person operate the Control Head while another monitors and adjusts the push-pull cable at the Servo Actuator. Move the Control Head levers and the Mode Select Switch to shift the component the Servo
Actuator is connected to. Mark the travel distance of the Servo Actuator lever and the engine/transmission troll lever.
Compare your marks of the positions of the push-pull cable to the
Servo Actuator, with the following diagrams. Use these diagrams and the associated instructions to adjust/align the cable attachment at the Servo Actuator lever. As adjustments are made, repeat step 1 to confirm results of adjustments. Several adjustments and checks may be necessary before achieving final alignment. Final alignment should be when the Servo Actuator lever is unrestricted to move to its positions, while moving the engine/transmission/troll lever to its proper positions without coming bottoming out against the engine/transmission/ troll lever end stops. When the final alignment is complete, tighten all clamps and associated hardware.
A: When the travel of the Servo Actuator lever is wider than the travel of the push-pull cable, adjust by moving the attachment for the cable on the Servo Actuator lever down towards the shaft of the actuator. See Figure 26.
ADJUST BALL JOINT POSITION DOWN RESULT
Figure 26. Adjustment of Cable Attachment
EC300 Marine Control System Installation Manual #1024168
57
Component Installation
Twin Disc, Incorporated
B: When the travel of the Servo Actuator lever is narrower than the travel of the push-pull cable, adjust by moving the attachment for the cable on the Servo Actuator lever up and away from the shaft of the actuator. See Figure 27.
ADJUST BALL JOINT POSITION UP RESULT
Figure 27. Adjustment of Cable Attachment
C: When the travel of the Servo Actuator lever and push-pull cable matches closely, but the cable will not reach to attach to the
Servo Actuator Lever at both ends of travel, move the cable clamp inwards towards the actuator lever. See Figure 28.
ADJUST CABLE/BRACKET INWARD RESULT
Figure 28. Adjustment of Cable Clamp - Short
D: When the travel of the Servo Actuator lever and push-pull cable matches closely, but the cable overshoots the Servo Actuator lever at both ends of travel, moving the cable clamp outwards away from the actuator lever. See Figure 29.
58
ADJUST CABLE/BRACKET OUTWARD RESULT
Figure 29. Adjustment of Cable Clamp - Overshoot
Note: Electrical harness installation for the Servo Actuator is completed in Electrical Installation.
EC300 Marine Control System Installation Manual #1024168
Electrical Installation
Twin Disc, Incorporated
Electrical Installation
General Electrical Harness Information
The EC300 Control System is provided with 13 wiring harness connections
(example J1, J2, or J3). All 13 connections are not used in all applications.
Each of these connections is described separately within this manual. Most harnesses provided by Twin Disc Incorporated are supplied in 609 mm (2 ft) increments.
Note: If a harness needs to be shortened, refer to the installation diagram provided for the system. Shorten the harness on the end identified by the scissors icon.
Twin Disc Incorporated provides harnesses in the following configurations:
Fully prefabricated wiring harnesses with connectors installed on both ends.
Prefabricated wiring harnesses with connectors installed only on the
EC300 end of the harness. The equipment end of the harness is fabricated by the installer at the time of installation with components provided by the customer.
Prefabricated wiring harnesses with connectors installed on the equipment end and terminals installed on the EC300 end of the harness. The terminals on these harnesses will be installed into the
EC300 connector provided by Twin Disc Incorporated.
For Non-Twin Disc components, the wiring harness and equipment end connectors are supplied by the customer with the EC300 connector being supplied by Twin Disc Incorporated. Kits are available from Twin Disc
Incorporated which provide the contact sockets and sealing plugs used in the EC300 connectors.
EC300 Marine Control System Installation Manual #1024168
59
Electrical Installation
Twin Disc, Incorporated
General Electrical Installation Guidelines
CAUTION
Ensure that the EC300 Control Power and Grounding Harness (J13) connector is disconnected before proceeding with the installation of all other harnesses. When making the electrical connections described in this section, ensure that the associated power source is turned off.
The following general electrical installation points apply to all electrical installations.
Read the following guidelines before making any installations and connections.
The installer must follow the EC300 installation diagram provided for the system.
The following guidelines must be met when fabricating electrical harnesses:
Electric harness are to be flame retardant and must comply with the following requirements, as applicable: z
Harnesses constructed to IEC Publication 60092 standards are to comply with the flammability criteria of IEC Publication
60332-3, Category A/F or A/F/R.
z
Harnesses constructed to IEEE 1580-2001 are to comply with the flammability criteria contained therein.
z
Harnesses constructed to other standards, where accepted by ABS, are to comply with the flammability criteria of IEC
Publication 60332-3, category A/F or A/F/R (depending on the intended installation), or other acceptable standards.
z
Flame retardant marine harnesses which have not passed the bunched harness flammability criteria as per IEC Publication
60332-3 may be considered, provided that the harness is treated with approved flame retardant material or the installation is provided with approved fire stop arrangements.
60 EC300 Marine Control System Installation Manual #1024168
Twin Disc, Incorporated
Electrical Installation
z
Maximum current carrying capacities of harnesses conforming to IEC Publication 60092-353 are to be in accordance with the values given in 4-8-3/Table 6 of ABS Rules for Building and
Classing Steel Vessels 2002. These values are applicable for harnesses installed double-banked on cable trays, in cable conduits or cable pipes. The values, however, are to be reduced for installations where there is an absence of free air circulation around the harnesses. See 4-8-2/7.7.1 and Note 4 of 4-8-3/
Table 6 in the ABS document.
z
The rated temperature of the harness’s insulating material is to be at least 10°C (18°F) higher than the maximum ambient temperature likely to be in the space where the harness is installed.
z
Harness constructions shall use stranded copper (19 strands or more); rated for 50 VDC, conforming to UL 1426 Cables for Boats or other applicable standards; should not be more than 3.6 m
(12 ft) long; should be marked with type/style, voltage, size, and dry temperature rating; and should be color coded as shown in
Table 6.
Table 6. Power Wire Color Codes as per ABYC Standard E-9
Color Code
Yellow w/Red Stripe
Function
Neutral Start Relay Contacts (J5 pins 9 & 10)
Purple
Yellow (preferred) or Black
Red
Ignition Switch (J8 pin 1)
Battery Negative (-) (J13 pin 3)
Battery Positive (+) (J13 pin 1)
Auxilliary Battery Positive (+) (J13 pin 2)
Green w/Yellow Stripe (preferred) or Green
DC Grounding Conductors or Banding Only
EC300 Marine Control System Installation Manual #1020607
61
Electrical Installation
Twin Disc, Incorporated
62
The following guidelines must be met when routing electrical wiring harnesses:
CAUTION
Keep the EC300 system harnesses away from antenna wires and AC power wires. Do not route the EC300 control harnesses in the same trough or conduit as antenna or AC power wires.
Wiring harnesses must be located away from high current conductors and devices. Harnesses must be at least 1 m (3.3 ft) away from communications equipment, antennas and associated wiring.
Wiring harnesses must be located away from hot surfaces or highrisk fire areas.
Wiring harnesses must be clear of service areas, access areas, or other spaces where it may be exposed to mechanical damage. Where this cannot be avoided, special measures are to be made for effective protection of the harnesses.
CAUTION
Do not add additional wire to any harness. Longer harnesses may require thicker conductors.
Do not splice or substitute different types of wire into the harnesses.
Increased length may require increased wire size.
Any splices must meet the requirements of the applicable standards or specifications.
Harnesses are available in varying lengths in 0.6 m (2 ft) increments.
Wiring harnesses must be the minimum practical length. Wiring harnesses should never be installed in a manner which results in more than 609 mm (24 in.) of excess length.
Wiring harnesses should have service/drip loops at each connection point as required to minimize water drainage toward the connector.
Loops should be tied down so that they do not move freely when the boat is in motion. Excess motion can cause the harnesses to fatigue and break.
Wiring harness bend radius should be at least eight harness-diameters unless otherwise permitted. RMRS requires greater than ten harnessdiameters.
Wiring harnesses are to be secured in such a manner that stresses are not transmitted to the connector terminal.
EC300 Marine Control System Installation Manual #102
4168
Twin Disc, Incorporated
Electrical Installation
Wiring harnesses must be supported or secured every 406 mm (16 in.) maximum with the appropriate hardware except if the harness is enclosed in rigid duct, conduit, or other enclosure. The distance between harness supports are to be suitably chosen according to the type of harness and the degree of vibration the installation is likely to be subjected to. For horizontal runs where harnesses are laid on tray plates, individual support brackets or hanger ladders, the distance between the fixing points may be up to 914 mm (36 in.), provided that there are supports with maximum spacing as specified above.
Increased support will be required for wiring harness runs on weather decks where forces from sea water washing over the deck is expected.
Alternatively, harness support systems complying with a recognized standard other than IEC 60092-352 may be used where the installed harness must also comply with that standard. Specifically, harness support systems meeting the requirements of IEEE 1580-2001 may be used where IEEE 1580-2001 harnesses are installed.
Some applicable codes and standards (notably RMRS) require different spacing for harness supports. The following table shows RMRS spacing requirements.
Table 7. RMRS Wire Fastening Points
E x t e r n a l d i a m e t e r o f c a b l e , m m
O ve r
- - -
8
1 3
2 0
3 0
U p t o
8
1 3
2 0
3 0
- - -
D i s t a n c e b e t w e e n fa s t e n i n g p o i n t s fo r c a b l e s , m m
W i t h o u t W i t h
W i t h m i n e r a l a r m o u r
2 0 0
2 5 0
3 0 0
3 5 0
4 0 0 a r m o u r
2 5 0
3 0 0
3 5 0
4 0 0
4 5 0 i n s u l a t i o n
3 0 0
3 7 0
4 5 0
4 5 0
4 5 0
Metallic wire harness clamps or supports are required if the failure of the support could cause a hazardous condition in the engine room, machinery rooms, or passageways.
Clamps and supports shall not have sharp edges or rough surfaces that could damage the insulation. Special protective measures such as tape or other wrapping are required for metallic clamps or supports.
Clips, saddles, and straps are to have surface area and sufficient width as to not cause damage to the insulation.
Non-metallic clamps and supports must be resistant to oil, gasoline, and water and shall have a temperature range of -34 to 121°C (-30 to
250°F). They shall be flame retardant in accordance with IEC
Publication 60092-101. Where used for wire harnesses that are not routed on top of horizontal cable trays, suitable metal clips or straps are to be added at regular intervals not exceeding 2 m (6.6 ft) in order to prevent the release of wire harnesses during a fire.
Do not use wire staples.
EC300 Marine Control System Installation Manual #1024168
63
Electrical Installation
Twin Disc, Incorporated
64
Where wire harnesses pass through watertight or fire-rated bulkheads or decks, the penetrations are to be made through the use of approved stuffing tubes, transit devices, or pourable materials in order to maintain the watertight or firetight integrity of the bulkheads or decks. These devices or materials must not damage the harness. Where cable conduit pipe or equivalent is carried through decks or bulkheads, arrangements are to be made to maintain the integrity of the water or gas tightness of the structure.
Wiring harnesses are not to be installed behind, or imbedded in, structural insulation. They may, however, pass through such insulation at right angles. Wiring conduit or recesses integral with B or C class fire-walls may be used for installing harnesses if the fire-walls are of an approved type and the installation prevents the propagation of smoke through the conduit.
When harnesses pass through non-watertight bulkheads, decks or structural members, the length of the bearing surface for the harness is to be at least 6.4 mm (0.25 in.). All burrs and sharp edges are to be removed.
No harness is allowed to penetrate the collision bulkhead.
To avoid possible signal interference, signal wire harnesses occupying the same wireway or conduit with power harnesses are to be effectively shielded.
The following guidelines must be met when making wiring connections:
All electrical connections must be made within waterproof enclosures or shall be watertight. Connections must be watertight if they can be immersed in water.
The connectors have a resilient insert that seals to the insulation of each wire in the connector. Do not attempt to fit two wires into any of the connector positions. Sealing plugs are provided for unused positions of the connector in order to insure the sealed nature of the connected harness assembly. Do not discard these white plastic plugs since they must be inserted into the unused positions.
For harness kits that require field termination by the installer, tape and secure the ends of any unused wires.
Note: Wire harnesses supplied by Twin Disc Incorporated will not include any unused wires.
EC300 Marine Control System Installation Manual #1024168
Twin Disc, Incorporated
Electrical Installation
Terminals must not damage the conductor.
Metals used for connections shall be corrosion resistant.
Terminal lugs shall be ring lug or captive spade styles and shall be sized to match the terminal and the conductor. Shanks shall be insulated unless used on a grounded conductor. Crimp lugs must be of equal or greater current rating than the wire.
Wire harnesses stripped of insulation are to be sealed using heat shrink tubing in combination with insulating compound or sealing devices.
The installer must provide suitable wire harness and crimping tools.
An appropriate tool for Deutch contacts is the Deutsch crimper
(P/N HDT 48-00). Use all tools and materials in accordance with manufacturer’s instructions.
Crimps must be made with a tool designed to operate with the lug/ contact. Crimps shall be able to hold 13.6 kg (30 lb) for one minute.
Aluminum or unplated steel shall not be used for fasteners.
Twist-on connectors, such as wire nuts, shall not be used.
Solder may not be the only means of connection between two or more conductors or between a conductor and a connector.
Any friction connectors or soldered connectors at components must meet the component manufacturer’s requirements as well as the applicable standards.
No more than four conductors may be terminated at any single stud.
Wires shall have sufficient freedom of movement to allow for removal, dressing, and tension relief.
To avoid electromagnetic interference caused by circulating currents, the conductive shield and wire harness armor of signal harnesses is to be grounded only at one end of the wire harness.
To connect a harness to an EC300 Control, align the plug orientation keys with the EC300 Control’s receptacle and push the plug in until it snaps in place.
EC300 Marine Control System Installation Manual #1024168
65
Electrical Installation
Twin Disc, Incorporated
Control Head Harness (J1, J2, or J3) Installation
The Control Head Harness (J1, J2, and J3) provides the main interface between the Control Head and the EC300 Controller. The vessel will have one or more
Control Heads located at the vessel control stations with either single lever or dual lever heads.
The Control Head Harnesses (J1, J2, and J3) are fully pre-fabricated and plug into the J1, J2, and J3 connector at the EC300 or the station doubler if used.
The J1, J2, or J3 connectors contain all contacts and sealing plugs that are required to fill the connector. Sealing plugs must be installed into all unused connector contact positions in order to maintain the integrity of the connector.
Refer to General Electrical Installation Guidelines for harness routing criteria prior to proceeding with this section.
This section contains the following sub-sections:
Multi-Station Single Lever Control Head Wiring Installation
Multi-Station Dual Lever Control Head Wiring Installation
Split Single Lever Control Heads in Twin Engine Installations
Multi-Station Dual Lever Control Head Wiring Installation Using Station
Doublers
66 EC300 Marine Control System Installation Manual #1024168
Twin Disc, Incorporated
Electrical Installation
Multi-Station Single Lever Control Head Wiring Installation
This section is applicable to single engine applications with up to three Single
Lever Control Heads. See Figure 30.
CONTROL STATION 1
PORT
CONTROL STATION 2
PORT
CONTROL STATION 3
PORT
CIRCULAR
CONNECTOR
HARNESS, WIRING
PORT LEVER
3 PLACES
TWIN DISC
INCORPORATED
MODEL EC300
P/N 1020676
BOM
S/N
VOLTAGE 12-24VDC
6
J1
7 6
J2
7 6
J3
7
J4 J5 J6 J7
1 12 1 12 1 12
J8 J9 J10 J11 J12 J13
Figure 30. Single Engine Single Lever Control Head Wiring
EC300 Marine Control System Installation Manual #1024168
67
Electrical Installation
Twin Disc, Incorporated
Each single lever harness is designed to connect to the Control Head at one end, and to the EC300 Control’s J1, J2, or J3 connector at the other end. Use
Connector J1 if only one Single Lever Control Head is used. Use Connectors
J1 and J2 if two Single Lever Control Heads are used.
Install the Control Head harness as follows:
2.
3.
Note: The Control Head may be removed from the dash if this facilitates making the connection. If it is removed, then reinstall it after the connections have been made.
Note: Provide enough length in the harness to allow removal of the Control Head in the future.
Refer to General Electrical Installation Guidelines for harness routing criteria.
1.
Connect the circular connector end of the Control Head harness to the
Control Station 1 (main/most used) Single Lever Control Head.
Note: Align the large connector key with the large keyway and push the connector into place. Then, turn the connector’s collar until the engagement snap is felt.
Ensure that the Single Lever Control Head is firmly mounted.
Route the Control Head harness to the EC300 Control.
4.
5.
6.
7.
Connect the Control Head Harness plug to the J1 receptacle of the
EC300 Control.
If applicable, repeat Steps 1 through 4 for connecting additional Control
Stations using J2 for the second Control Head and J3 for the third Control
Head.
If J2 and/or J3 are not used, install a connector kit into these receptacles to seal the connector. See System Drawing for Connector Plug Kit p/n.
Secure all harnesses to a supporting structure with clamps or cable ties at 406 mm (16 in.) intervals.
68 EC300 Marine Control System Installation Manual #1024168
Twin Disc, Incorporated
Electrical Installation
Multi-Station Dual Lever Control Head Wiring Installation
This section is applicable to dual engine applications with up to three Dual
Lever Control Heads. See Figure 31.
CONTROL STATION 1
PORT STBD
CONTROL STATION 2
PORT STBD
CONTROL STATION 3
PORT STBD
CIRCULAR
CONNECTOR
HARNESS, WIRING
PORT LEVER
3 PLACES
STARBOARD CONTROL PORT CONTROL
TWIN DISC
INCORPORATED
MODEL EC300
P/N 1020676
BOM
S/N
VOLTAGE 12-24VDC
TWIN DISC
INCORPORATED
MODEL EC300
P/N 1020676
BOM
S/N
VOLTAGE 12-24VDC
6
J1
7 6
J2
7 6
J3
7
J4 J5 J6
J7
1 12 1 12 1 12
J8 J9
2
1
J10
3
4
J11 J12 J13
6
J1
7 6
J2
7 6
J3
7
J4 J5 J6 J7
1 12 1 12 1 12
J8 J9
2
1
J10
3
4
J11 J12 J13
1020614
RECEPTACLE
T CONNECTOR (J1939)
2 PLACES
CONNECTOR
TERMINATING RESISTOR
2 PLACES
HARNESS, WIRING
COMMUNICATION
1020615
1020614
HARNESS, WIRING
CONTROLLER COMMS
2 PLACES
Figure 31. Dual Engine Dual Lever Control Head Wiring
Install the Control Head harnesses as follows:
Note: Each dual lever harness consists of two separate harnesses joined together at the Control Head end. At the EC300 end, one harness end is marked PORT and the other harness end is marked STARBOARD. The harness end(s) marked PORT must route to the port control. The STARBOARD harness end(s) must route to the starboard control. Use receptacle J1 at both controls if only one Dual Lever Control Head is used. Use receptacles J1 and J2 if two Dual Lever Control Heads are used. Use the same “J” number receptacles from each
Dual Lever Control Head at both the port and the starboard controls.
EC300 Marine Control System Installation Manual #1024168
69
Electrical Installation
70
Twin Disc, Incorporated
2.
3.
4.
5.
Note: The Control Head may be removed from the dash if this facilitates making the connection. If it is removed, then reinstall it after the connections have been made.
Note: Provide enough length in the harness to allow removal of the Control Head in the future.
Refer to General Electrical Installation Guidelines for harness routing criteria.
1.
Connect the circular connector end of the dual lever harness to the
Control Station 1 (main/most used) Dual Lever Control Head.
Note: For each Control Head connector, align the large connector key with the large keyway and push the connector into place. Then, turn the connector’s collar until the engagement snap is felt.
Ensure that the Dual Lever Control Head is firmly mounted.
Route the harness marked “PORT” to the EC300 Port Control.
Connect the Dual Lever Control Head Harness plug to the J1 receptacle of the “PORT” EC300 Control.
Route the harness marked “STARBOARD” to the EC300 Starboard
Control.
6.
7.
8.
9.
Connect the Dual Lever Control Head Harness plug to the J1 receptacle of the “STARBOARD” EC300 Control.
If applicable, repeat steps 1 through 6 for connecting additional Control
Stations using J2 for the second Control Head and J3 for the third Control
Head.
If J2 and/or J3 are not used, install a connector kit into these receptacles to seal the connector. See System Drawing for Connector Plug Kit p/n.
Secure all harnesses to a supporting structure with clamps or cable ties at 406 mm (16 in.) intervals.
Note: It is desirable, especially on single station vessels, to route the port and starboard harnesses as far apart as possible.
This minimizes the odds of both harnesses being accidently damaged at the same time allowing continued, but reduced, control of the vessel.
EC300 Marine Control System Installation Manual #1024168
Twin Disc, Incorporated
Electrical Installation
Split Single Lever Control Head Stations in Twin Engine Installations
Some dual-engine installations use split Single Lever Control Heads at control stations rather than Dual Lever Control Heads. For such installations, one split lever harness and one dual lever harness are used. See Figure 32.
PORT STBD
TO EC300
STARBOARD CONTROL
STARBOARD
1020617
HARNESS, WIRING
DUAL LEVER
PORT
TO EC300
PORT CONTROL
1021458
HARNESS, WIRING
SPLIT LEVER
Figure 32. View of Split Single Lever Harness Wiring
Install the Control Head harnesses as follows:
Note: The Control Heads may be removed from the dash if this facilitates making the connection. If they are removed, then reinstall them after the connections have been made.
Note: Provide enough length in the harness to allow removal of the Control Heads in the future.
EC300 Marine Control System Installation Manual #1024168
71
Electrical Installation
72
Twin Disc, Incorporated
2.
3.
Refer to General Electrical Installation Guidelines for harness routing criteria.
1.
Connect the female circular connector end of the Split Lever harness with the two circular connectors to the port Single Lever Control Head.
Note: For each Control Head connector, align the large connector key with the large keyway and push the connector into place. Then, turn the connector’s collar until the engagement snap is felt.
4.
Route the Split Lever harness to the Starboard Control Head.
Connect the circular connector end of the Split Lever harness to the starboard Single Lever Control Head.
Connect the circular connector end of the Dual Lever harness to the male circular connector of the Split Lever harness at the Port Single
Lever Control Head.
5.
6.
7.
Ensure that the port and starboard single lever Control Heads are firmly mounted.
Route the Dual Lever harness to the EC300 Port Control and Starboard
Control.
Note: It is desirable, especially on single station vessels, to route the port and starboard harnesses as far apart as possible.
This minimizes the odds of both harnesses being accidently damaged at the same time allowing continued, but reduced, control of the vessel.
Connect the Dual Lever Harness plug labeled “Port” to the J1 receptacle of the Port EC300 Control.
8.
9.
Connect the Dual Lever Harness plug labeled “Starboard” to the J1 receptacle of the Starboard EC300 Control.
If applicable, repeat steps 1 through 6 for connecting additional Control
Stations using J2 for the second Control Head and J3 for the third Control
Head.
10.
If J2 and/or J3 are not used, install a connector kit into these receptacles to seal the connector. See System Drawing for Connector Plug Kit p/n.
11.
Secure all harnesses to a supporting structure with clamps or cable ties at 406 mm (16 in.) intervals.
EC300 Marine Control System Installation Manual #1024168
Twin Disc, Incorporated
Electrical Installation
Multi-Station Dual Lever Control Head Wiring Installation Using Station Doublers
This section is applicable to multiple engine applications with more than three
(3) Dual Lever Control Heads per EC300 Control. Each EC300 Control can directly accept up to three Control Head inputs. Using Station Doublers, a total of five Control Head inputs can be supported. Each Station Doubler combines the signals from two separate Control Heads and routes the combined signals to each of the EC300 Controls at J2 or J3. See Figures 33 and 34.
Figure 33 shows five Control Heads and two Station Doublers. The control head not connected to a station doubler must be connected to J1.
PORT STBD
CONTROL STATION 1
PORT STBD
CONTROL STATION 2
PORT STBD
CONTROL STATION 3
PORT STBD
CONTROL STATION 4
PORT STBD
CONTROL STATION 5
STARBOARD
STATION
A
STBD
STATION
B
PORT
STARBOARD
1020617
PORT
STATION
A
PORT
STATION
B
HARNESS, WIRING
DUAL LEVER
7 PLACES
STARBOARD
PORT
STATION
A
STBD
STATION
B
CIRCULAR
CONNECTOR
7 PLACES
BOX, JUNCTION
STATION DOUBLER
2 PLACES
STARBOARD
1020617
PORT
STATION
A
PORT
STATION
B
PORT CONTROL STARBOARD CONTROL
TWIN DISC
INCORPORATED
MODEL EC300
P/N 1020676
BOM
S/N
VOLTAGE 12-24VDC
6
J1
7 6
J2
7 6
J3
7
J4 J5 J6 J7
1 12 1 12 1 12
J8 J9
2
1
J10
3
4
J11 J12 J13
TWIN DISC
INCORPORATED
MODEL EC300
P/N 1020676
BOM
S/N
VOLTAGE 12-24VDC
6
J1
7 6
J2
7 6
J3
7
J4 J5 J6 J7
1 12 1 12 1 12
J8 J9
2
1
J10
3
4
J11 J12 J13
1020614
RECEPTACLE
T CONNECTOR (J1939)
2 PLACES
CONNECTOR
TERMINATING RESISTOR
2 PLACES
HARNESS, WIRING
COMMUNICATION
1020615
1020614
HARNESS, WIRING
CONTROLLER COMMS
2 PLACES
Figure 33. Typical Five Station Dual Lever Control Head Wiring
EC300 Marine Control System Installation Manual #1024168
73
Electrical Installation
Twin Disc, Incorporated
Note: Station Doublers may also be used on single-engine
Single Lever Control Head applications if more than three
Control Heads are required. Single Lever Control Head
Station-to-Doubler harnesses are used in place of the dual lever station-to-doubler harnesses. A port station-todoubler harness is used with a Port Control Head. A starboard station-to-doubler harness is used with a
Starboard Control Head.
PORT STBD
CONTROL STATION 1
PORT STBD
CONTROL STATION 2
74
TO STBD
CONTROL
TO PORT
CONTROL
BOND WIRE
WITH RING LUG
BOX, JUNCTION
STATION DOUBLER
STATION
A
STBD
STATION
B
STARBOARD STARBOARD
1020617
PORT PORT
HARNESS, WIRING
DUAL LEVER
3 PLACES
STATION
A
PORT
STATION
B
Figure 34. Station Doubler Connection Using Dual Lever Control Heads
Install the Control Head harnesses as follows:
Note: The Doubler-to-Station Harness routes between the
Control Head and the Station Doubler. The Doubler-to-
Control Harness routes between the Station Doubler and the EC300 Control (J2 or J3).
Note: The Control Head may be removed from the dash if this facilitates making the connection. If it is removed, then reinstall it after the connections have been made.
EC300 Marine Control System Installation Manual #1024168
Twin Disc, Incorporated
Electrical Installation
Note: Provide enough length in the harness to allow removal of the Control Head in the future.
Refer to General Electrical Installation Guidelines for harness routing criteria.
Control Station 1
1.
Connect the circular connector end of a Doubler-to-Station harness to the Dual Lever Control Head.
Note: For each Control Head connector, align the large connector key with the large keyway and push the connector into place. Then, turn the connector’s collar until the engagement snap is felt.
Ensure that the Dual Lever Control Head is firmly mounted.
2.
3.
4.
5.
Route the Doubler-to-Station harness to the Station Doubler.
Connect the Doubler-to-Station harness plug marked “PORT” into the receptacle marked “STATION A” on the “PORT” end of the Station
Doubler.
Connect the Doubler-to-Station harness plug marked “STARBOARD” into the receptacle marked “STATION A” on the “STBD” end of the Station
Doubler.
Control Station 2
6.
Connect the circular connector end of a Doubler-to-Station harness to the Dual Lever Control Head.
7.
8.
Ensure that the Dual Lever Control Head is firmly mounted.
Route the Doubler-to-Station harness to the Station Doubler.
9.
Connect the Doubler-to-Station harness plug marked “PORT” into the receptacle marked “STATION B” on the “PORT” end of the Station
Doubler.
10.
Connect the Doubler-to-Station harness plug marked “STARBOARD” into the receptacle marked “STATION B” on the “STBD” end of the Station
Doubler.
EC300 Marine Control System Installation Manual #1024168
75
Electrical Installation
Twin Disc, Incorporated
Doublers to EC300 Control
11.
Connect the circular connector end of a Doubler-to-Control harness to the receptacle on the Station Doubler marked “CONTROL”.
12.
Route the harness marked “PORT” to the EC300 Port Control.
Note: It is desirable, especially on single station vessels, to route the port and starboard harnesses as far apart as possible.
This minimizes the odds of both harnesses being accidently damaged at the same time allowing continued, but reduced, control of the vessel.
13.
Connect the Doubler-to-Control Harness plug to the J2 receptacle of the Port EC300 Control.
14.
Route the harness marked “STARBOARD” to the EC300 Starboard
Control.
15.
Connect the Doubler-to-Control Harness plug to the J2 receptacle of the Starboard EC300 Control.
16.
If applicable, repeat steps 1 through 15 to connect two additional Dual
Lever Control Heads through a second Station Doubler to the J3 receptacles of the EC300 Port and Starboard Controls.
17.
If J2 and/or J3 are not used, install a connector kit into these receptacles to seal the connector. See System Drawing for Connector Plug Kit p/n.
18.
Secure all harnesses to a supporting structure with clamps or cable ties at 406 mm (16 in.) intervals.
76 EC300 Marine Control System Installation Manual #1024168
Twin Disc, Incorporated
Electrical Installation
Bonding Wire
19.
Route a bond wire from the vessel bonding system to the selected mounting pad on each Station Doubler. See Figure 33.
Note: The bonding conductor must be 14 AWG stranded copper wire. It must be colored green with a yellow stripe
(preferred) or green in order to comply with ABYC standards.
20.
Install a ring lug on the doubler end of the wire.
Note: The ring lug must be properly sized for both the wire and the mounting fastener.
21.
Remove the mounting fastener at the bonding connection.
22.
Remove any paint at the mounting connection in order to ensure electrical contact.
23.
Insert the bonding wire’s ring lug on the Station Doubler.
24.
Reinstall and tighten fasteners up to 1.13 Nm (10 lb-in.) maximum.
EC300 Marine Control System Installation Manual #1024168
77
Electrical Installation
Service Connector (J4)
Factory Use Only
Twin Disc, Incorporated
Transmission Harness (J5, J6, J7 J8, and J12) Installation
Note: The J5, J6, J7, J8, and J12 wiring harnesses may be installed as one harness (standard) or individual harnesses. If your installation includes individual harnesses, proceed to the installation instructions for each harness. When completed with the Transmission Harness installation proceed to the J9 Harness installation procedure and omit the J12 installation procedure.
The Transmission Harness is a fully prefabricated harness that combines the wiring for the J5, J6, J7, J8 and J12 harnesses and connections. It consists of
2 separate harness assemblies. A Control to Bracket Harness (Figure 35) and a Bracket to Transmission Harness (Figure 36). Various harness options are available to accommodate different transmission and control system options.
The Control to Bracket harness connects to the EC300 and is routed to the mating circular connector mounted on the transmission bracket. The transmission is supplied with the Bracket to Transmission harness prewired.
The J5 wiring for engine throttle is available at the bracket and must be fabricated and wired by the customer. The Transmission Harness connectors contain all contacts and sealing plugs that are required to fill the connector contact positions. Sealing plugs must be installed into all unused connector contact positions in order to maintain the integrity of the connector.
Refer to General Electrical Installation Guidelines for harness routing criteria before proceeding with this section.
This section contains the following sub-sections:
Control to Bracket Wiring Installation
Bracket to Transmission Wiring Installation z
Neutral Start Interlock Wiring Installation z
Engine Throttle Wiring Installation z
Prewired Connection Inspection
78 EC300 Marine Control System Installation Manual #1024168
Twin Disc, Incorporated
Electrical Installation
Control to Bracket Wiring Installation
The Control to Bracket wiring provides wiring connections to interface the transmission and engine with the EC300 Control. See Figure 35.
J5
J8
J6
1022894
TWIN DISC
INCORPORATED
MODEL EC300
P/N 1020676
BOM
S/N
VOLTAGE 12-24VDC
J1 J2
1
8
J8
4
5
J9
J3 J4
6
J5
7
4
J6
5
6
J7
7
J10
1
J11
12
1
3
8
1
4
1
J12
6
J13
12
CHASSIS
J7
J12
Figure 35. Control to Bracket Harness Assembly
EC300 Marine Control System Installation Manual #1024168
79
Electrical Installation
Twin Disc, Incorporated
7.
8.
Refer to General Electrical Installation Guidelines for harness routing criteria.
1.
2.
3.
4.
5.
Align the J5 harness connector with the J5 receptacle of the EC300
Control and push it in until it snaps into place.
Align the J6 harness connector with the J6 receptacle of the EC300
Control and push it in until it snaps into place.
Align the J7 harness connector with the J7 receptacle of the EC300
Control and push it in until it snaps into place.
Align the J8 harness connector with the J8 receptacle of the EC300
Control and push it in until it snaps into place.
Align the J12 harness connector with the J12 receptacle of the EC300
Control and push it in until it snaps into place.
6.
Ensure that sealing plugs are installed in all empty connector positions of each connector.
Route the Control to Bracket Harness to the transmission.
Secure all harnesses to a supporting structure with clamps or cable ties at 406 mm (16 in.) intervals.
80 EC300 Marine Control System Installation Manual #1024168
Twin Disc, Incorporated
Electrical Installation
Bracket to Transmission Wiring Installation
Marine transmissions with this option will come from the factory with the Bracket to Transmission harness prefabricated and installed. The installer will need to fabricate and install the J5 Neutral Start Interlock and Engine Throttle wiring.
The Neutral Start Interlock connector is supplied by Twin Disc Incorporated.
The installer will need to provide the wires and terminate them to the connector and to the neutral start interlock connections on the engine. The Bracket to
Transmission harness provides the wires (approximately 3 m [10 ft] long) which the installer will need to terminate to the Engine Throttle Input. See Figure 36.
FWD
REV
1022881
TEMP
INPUT SPEED
THROTTLE
OUTPUT SPEED
CHASSIS
MANUAL OVERRIDE 1
MANUAL OVERRIDE 2
Figure 36. Bracket to Transmission Harness Assembly
NEUTRAL START
The following criteria must be met when installing engine control harness wiring:
The Neutral Start Interlock wires must be 14 AWG stranded copper wire.
All other wires must be a minimum of 18 AWG stranded copper wire.
Before installing the Neutral Start Interlock Wiring, plan if the Engine
Throttle harnesses and/or the Engine Speed Sensor Harness are to be installed. Consider the harness routing for each component to consolidate wire routing.
Refer to General Electrical Installation Guidelines for harness routing
criteria prior to proceeding with this section.
EC300 Marine Control System Installation Manual #1024168
81
Electrical Installation
Twin Disc, Incorporated
Neutral Start Interlock Wiring Installation
The EC300 Control is designed to ensure that a control head is in command and that the lever is in the neutral detent position before an engine can be started. All EC300 Control Systems include a Neutral Start Interlock feature for prevention of start-in-gear situations. The Neutral Start Interlock is a relay contact inside of the EC300 Control. The relay contact closes only when the system ignition is turned on, a Control Head is selected, and the lever for the selected
Control Head is in the neutral position.
Neutral Start Interlock Wiring Requirements
Normally, the boat wiring routes the start command wire from the key switch or engine control panel through the EC300 Control’s Neutral Start Interlock. If a bypass or override switch is desired, contact Twin Disc Incorporated or a local distributor for information related to specific installation requirements. Damage or injury that is caused by improper installation is not the responsibility of Twin
Disc Incorporated or its distributors.
CAUTION
Bypassing of the neutral start interlock may cause damage or injury.
Twin Disc Incorporated and its distributors are not responsible for the results of any improper wiring. Contact Twin Disc Incorporated or a local distributor for recommendations related to any engine-room start switch.
Two contacts are provided in the Transmission harness connector kit for the neutral start interlock wiring. The Neutral start connector pins A and B are for use with commonly available DC engine system voltages (12/24 VDC nominal).
Pin C is blank and will have a sealing plug installed to maintain the integrity of the connector.
82 EC300 Marine Control System Installation Manual #1024168
Twin Disc, Incorporated
Electrical Installation
Install the Neutral Start Interlock portion of the Transmission harnesses as follows
(See Figure 37):
BRACKET TO TRANSMISSION HARNESS
MANUAL OVERRIDE 1
MANUAL OVERRIDE 2
NEUTRAL START
PIN A
PIN B
PIN C = BLANK
BRACKET TO TRANSMISSION HARNESS
MANUAL OVERRIDE 1
START SWITCH
NEUTRAL START RELAY CONTACT - N.O. (14 AWG)
NEUTRAL START RELAY CONTACT - COM. (14 AWG)
YELLOW/RED
WIRE
YELLOW/RED
WIRE
BATT+
BATT-
STARTER SOLENOID
BATT-
BATT+
NEUTRAL START WITH RELAY
(USED WHEN STARTER RELAY SOLENOID IS 5 AMPS DC OR GREATER)
MANUAL OVERRIDE 2
PIN A
NEUTRAL START
PIN B
PIN C = BLANK
NEUTRAL START RELAY CONTACT - N.O. (14 AWG)
NEUTRAL START RELAY CONTACT - COM. (14 AWG)
YELLOW/RED
WIRE
YELLOW/RED
WIRE
START SWITCH
BATT+
STARTER SOLENOID
BATT-
NEUTRAL START WITHOUT RELAY
(USED WHEN STARTER RELAY SOLENOID IS LESS THAN 5 AMPS DC)
Figure 37. Neutral Start Interlock Schematic Bracket to Transmission
Harness
A Neutral Start Interlock Relay must be used for isolation if the starter relay/ solenoid current exceeds 5 amps DC. Use an isolation relay if the starter solenoid/relay current is unknown or if no means to measure the current is available.
Note: The EC300 Control’s neutral start interlock contacts and any hardwired transmission neutral interlock must be wired in series with the vessel’s starting circuit. If a hardwired transmission neutral start switch is present, then modify the following installation procedures to accommodate the switch.
The exact nature of the customer wiring will depend upon whether or not a relay is required. It will also depend upon the nature of the customer’s existing wiring.
The following steps assume that the Ignition Switch (start switch), the Starter
Solenoid, and the Neutral Start Relay (if used) are already installed.
EC300 Marine Control System Installation Manual #1024168
83
Electrical Installation
Twin Disc, Incorporated
Refer to General Electrical Installation Guidelines for harness routing criteria.
This section assumes an existing connection between the engine starting switch at the helm and the engine starting circuit. If a connection does not exist, it may be desirable to install this circuit before continuing.
1.
Remove the locking wedge from the Neutral Start Deutsch connector.
Note: The Neutral Start connector is provided in the
Transmission harness connector kit.
2.
Note: Refer to the EC300 System Installation Drawings in the
Engineering Drawings Section for pin numbering information.
Disconnect the wire coming from the start switch at the helm from the start relay/solenoid.
A.
Remove any existing terminals from the end of the wire and crimp the supplied Deutsch contact (P/N 0462-209-16141) using the
Deutsch HDT crimp tool (P/N HDT 48-00).
3.
4.
Note: The Deutsch 14 AWG contact (P/N 0462-209-16141) can be identified by a green band.
B.
Route the wire from the start relay/solenoid to the Neutral Start connector of the Bracket to Transmission harness and insert it into pin A of the connector.
Using 14 AWG wire, make a connection from pin B of the Neutral Start connector to the start relay/solenoid.
A.
Crimp a supplied Deutsch contact (P/N 0462-209-16141) using the Deutsch HDT crimp tool (P/N HDT 48-00) and insert it into pin B of the Neutral Start connector.
B.
Route this wire to the start relay/solenoid and terminate it at the start relay/solenoid using an appropriate connector.
When both pins and the seal plug have been inserted in the connector body, then insert the locking wedge.
5.
Align the harness connectors and push it in until it snaps into place.
6.
Secure all harnesses to a supporting structure with clamps or cable ties at 406 mm (16 in.) intervals.
84 EC300 Marine Control System Installation Manual #1024168
Twin Disc, Incorporated
Electrical Installation
Engine Throttle Wiring Installation
These signals interface with the engine Electronic Control Module’s (ECM’s) throttle input. The engine control module can also be referred to as the Electronic
Control Unit (ECU), Electronic Engine Control (EEC), or other similar names.
The engine manufacturer provides specific engine control manuals that detail the requirements for the throttle signal and power supply connections. The
Bracket to Transmission Harness has three pins for throttle control. Table 8 lists the pin functions.
Table 8. Engine Control Pin Functions
Pin
J5 Pin 1
J5 Pin 2
Signal Name
ECM Power Supply
Throttle Signal
Function
Power supply for the Throttle Signal. It is most often a power supply coming from J8 pin 2. In some cases it may be power coming from the
ECM. This signal is to be used as the power source for the throttle signal output.
The throttle position output signal. Depending upon the engine manufacturer, this signal can be a programmed voltage or current. The throttle signal is directed by the position of the lever at the active control head. It can also be a pulse train with programmable low and high levels with variable frequency or pulse widths. This is configured by the Twin Disc distributor or at the factory.
J5 Pin 3 ECM Power Supply
Common
The common return path and reference point for engine throttle circuit.
J5 Pin 4 Transmission State 1 A solid-state switch output that goes active when the transmission is in neutral. This wire is used only for specific engines. See page B-12 in Appendix B for additional information
J5 Pin 5 Transmission State 2 A solid-state switch output that goes active when the transmission is not in neutral. This wire is used only for specific engines. See page B-
12 in Appendix B for additional information
J5 Pin 6 Transmission State
Return
The return signal for the transmission state signal. This wire is used only for specific engines. See page B-12 in Appendix B for additional information
EC300 Marine Control System Installation Manual #1020607
85
Electrical Installation
Twin Disc, Incorporated
The EC300 Control System currently supports the following types of electronic engine controls:
Table 9. Engines Supported
Engine Manufacturer
Caterpillar
Cummins
Cummins
Detroit Diesel
Detroit Diesel
Deutz
Deutz
Iveco
Iveco
John Deere
MAN
MTU
Scania
Volvo Penta
Volvo Penta
Engine Name in MFST
Caterpillar
Cummins Centry/Celect
Cummins Quantum
Detroit Diesel Voltage
Detroit Diesel Frequency
Deutz Type 1
Deutz Type 2
Iveco PWM
Iveco Voltage
John Deere
MAN Current
MTU
Scania
Volvo Penta EVC B
Volvo Penta EVC C
Voltage
Voltage
Voltage
Current
Current
Voltage
Current
Current
Carrier
Voltage
Current
Voltage
Voltage
Current
Voltage
Voltage
Modulation
PWM
Amplitude
Amplitude
Amplitude
Frequency
PWM
Amplitude
PWM
Amplitude
Amplitude
Amplitude
Amplitude
Amplitude
Amplitude
Amplitude
If the specific engine is not listed, contact Twin Disc Incorporated or a local distributor for custom information and support.
Note: All EC300 Control configuration is performed by Twin Disc
Incorporated or its local distributor.
Refer to Appendix - B for detailed electrical installation requirements for the engines listed.
86 EC300 Marine Control System Installation Manual #1020607
Twin Disc, Incorporated
Electrical Installation
4.
5.
Install the Engine Throttle Wiring portion of the Bracket to Transmission harnesses as follows:
Refer to General Electrical Installation Guidelines for harness routing criteria.
1.
Identify the wiring requirements from the installation drawing and from appendix -B for the specific engine installation.
2.
3.
Locate the necessary connecting points on the engine control module or engine control wiring circuits.
Route the throttle harness portion of the Bracket to Transmission harness to the engine.
Connect the throttle harness wires at the engine end.
Secure all harnesses to a supporting structure with clamps or cable ties at 406 mm (16 in.) intervals.
EC300 Marine Control System Installation Manual #1024168
87
Electrical Installation
Twin Disc, Incorporated
Prewired Connection Inspection
The transmission is supplied with the Bracket to Transmission harness prewired for all connections other than the the neutral start and engine throttle circuits.
The remaining connections have been completed at the factory based upon the options ordered.
Verify that the connections are securely connected and have not been damaged during transmission installation. See Figure 38.
FWD
REV
1022881
TEMP
INPUT SPEED
THROTTLE
OUTPUT SPEED
CHASSIS
MANUAL OVERRIDE 1
MANUAL OVERRIDE 2
Figure 38. Bracket to Transmission Harness Assembly
NEUTRAL START
To complete the wiring harness installation proceed to the Twin Disc Display
Harness (J9) Installation, Communication Harness (J10) Installation, Servo
Actuator Harness (J11) Installation, and EC300 Control Power and Grounding
Harness (J13) Installation. Skip only those procedures that do not apply to your installation.
88 EC300 Marine Control System Installation Manual #1024168
Twin Disc, Incorporated
Electrical Installation
Engine Control Harness (J5) Installation
The Engine Control Harness (J5) provides wiring connections for the Neutral
Start Interlock, Engine Throttle (if applicable), and Engine Speed Sensor. The
EC300 J5 12 pin Deutsch connector, as well as the Engine Speed Sensor harness, are supplied by Twin Disc Incorporated. The Neutral Start Interlock and Engine Throttle harness are customer supplied, field fabricated, and plug into the J5 connector when not using the Twin Disc transmission harness. The
J5 connector kit contains all contacts and sealing plugs that are required to fill the connector contact positions. Sealing plugs must be installed into all unused connector contact positions in order to maintain the integrity of the connector.
The Neutral Start Interlock wiring and Engine Throttle wiring (if applicable) should be fabricated and routed to the EC300 Control prior to installing the Engine
Speed Sensor Harness. See Figure 39 and Figure 40.
The following criteria must be met when installing engine control harness wiring:
The Neutral Start Interlock wires must be 14 AWG stranded copper wire.
All other wires must be a minimum of 18 AWG stranded copper wire.
Before installing the Neutral Start Interlock Wiring, plan if the Engine
Throttle harnesses and/or the Engine Speed Sensor Harness are to be installed. Consider the harness routing for each component to consolidate wire routing.
Refer to General Electrical Installation Guidelines for harness routing criteria prior to proceeding with this section.
This section contains the following sub-sections:
Neutral Start Interlock Wiring Installation
Engine Throttle Wiring Installation
Engine Speed Sensor Wiring Installation
EC300 Marine Control System Installation Manual #1024168
89
Electrical Installation
Twin Disc, Incorporated
HARNESS, WIRING
ENGINE THROTTLE
CUSTOMER SUPPLIED
CUSTOMER SUPPLIED WIRE
ECM POWER SUPPLY
CONNECT FROM J8-2 TO J5-1
THROTTLE SIGNAL TO ENGINE CONTROL MODULE
THROTTLE COMMON FROM ENGINE CONTROL MODULE
NEUTRAL START RELAY CONTACT - N.O. (14 AWG)
J5-2
J5-3
J5-9
TO ENGINE
CONTROL MODULE
SEE APPENDIX
FOR SPECIFIC
ENGINE CONNECTIONS
START SWITCH
BATT+
NEUTRAL START RELAY CONTACT - COM. (14 AWG)
J5-10
1020706
HARNESS, WIRING
ENGINE SPEED SENSOR
SEE ENGINE SPEED SENSOR HARNESS INSTALLATION SECTION
ENGINE
SPEED
SENSOR
BATT-
STARTER SOLENOID
TO START MOTOR
BATT+
CONNECTOR KIT
ENGINE THROTTLE
TWIN DISC
INCORPORATED
MODEL
P/N
BOM
S/N
VOLTAGE
EC300
12-24VDC
6 7
1 12
Figure 39. Engine Control Harness (J5)
90 EC300 Marine Control System Installation Manual #1024168
Twin Disc, Incorporated
Electrical Installation
Neutral Start Interlock Wiring Installation
The EC300 Control is designed to ensure that a control head is in command and that the lever is in the neutral detent position before an engine can be started. All EC300 Control Systems include a Neutral Start Interlock feature for prevention of start-in-gear situations. The Neutral Start Interlock is a relay contact inside of the EC300 Control. The relay contact closes only when the system ignition is turned on, a Control Head is selected, and the lever for the selected
Control Head is in the neutral position.
Neutral Start Interlock Wiring Requirements
Normally, the boat wiring routes the start command wire from the key switch or engine control panel through the EC300 Control’s Neutral Start Interlock. If a bypass or override switch is desired, contact Twin Disc Incorporated or a local distributor for information related to specific installation requirements. Damage or injury that is caused by improper installation is not the responsibility of Twin
Disc Incorporated or its distributors.
CAUTION
Bypassing of the neutral start interlock may cause damage or injury.
Twin Disc Incorporated and its distributors are not responsible for the results of any improper wiring. Contact Twin Disc Incorporated or a local distributor for recommendations related to any engine-room start switch.
Two contacts are provided in the Engine throttle connector kit (J5) for the neutral start interlock wiring. Connector J5 pin 9 and connector J5 pin 10 are for use with commonly available DC engine system voltages (12/24 VDC Nominal).
Install the Neutral Start Interlock portion of the Engine Control harnesses as follows (See Figure 40):
EC300 Marine Control System Installation Manual #1024168
91
Electrical Installation
Twin Disc, Incorporated
HARNESS, WIRING
ENGINE THROTTLE
CUSTOMER SUPPLIED
CUSTOMER SUPPLIED WIRE
ECM POWER SUPPLY
CONNECT FROM J8-2 TO J5-1
ENGINE CONTROL MODULE
SEE ENGINE CONTROL HARNESS INSTALLATION SECTION
NEUTRAL START RELAY CONTACT - N.O. (14 AWG)
NEUTRAL START RELAY CONTACT - COM. (14 AWG)
HARNESS, WIRING
ENGINE SPEED SENSOR
SEE ENGINE SPEED SENSOR HARNESS INSTALLATION SECTION
J5-9
J5-10
MANUAL OVERRIDE
SWITCH
START SWITCH
BATT+
BATT-
STARTER SOLENOID
BATT-
BATT+
CONNECTOR KIT
ENGINE THROTTLE
6 7
1
NEUTRAL START WITH RELAY
(USED WHEN STARTER RELAY SOLENOID IS 5 AMPS DC OR GREATER)
HARNESS, WIRING
ENGINE THROTTLE
CUSTOMER SUPPLIED
CUSTOMER SUPPLIED WIRE
ECM POWER SUPPLY
CONNECT FROM J8-2 TO J5-1
ENGINE CONTROL MODULE
SEE ENGINE CONTROL HARNESS INSTALLATION SECTION
NEUTRAL START RELAY CONTACT - N.O. (14 AWG)
NEUTRAL START RELAY CONTACT - COM. (14 AWG)
HARNESS, WIRING
ENGINE SPEED SENSOR
SEE ENGINE SPEED SENSOR HARNESS INSTALLATION SECTION
J5-9
J5-10
MANUAL OVERRIDE
SWITCH
START SWITCH
BATT+
STARTER SOLENOID
BATT-
CONNECTOR KIT
ENGINE THROTTLE
6 7
1
NEUTRAL START WITHOUT RELAY
(USED WHEN STARTER RELAY SOLENOID IS LESS THAN 5 AMPS DC)
Figure 40. Neutral Start Interlock Schematic J5 Harness
92 EC300 Marine Control System Installation Manual #1024168
Twin Disc, Incorporated
Electrical Installation
3.
4.
A Neutral Start Interlock Relay must be used for isolation if the starter relay/ solenoid current exceeds 5 amps DC. Use an isolation relay if the starter solenoid/relay current is unknown or if no means to measure the current is available.
Note: The EC300 Control’s neutral start interlock contacts and any hardwired transmission neutral interlock must be wired in series with the vessel’s starting circuit. If a hardwired transmission neutral start switch is present, then modify the following installation procedures to accommodate the switch.
The exact nature of the customer wiring will depend upon whether or not a relay is required. It will also depend upon the nature of the customer’s existing wiring.
The following steps assume that the Ignition Switch (start switch), the Starter
Solenoid, and the Neutral Start Relay (if used) are already installed.
Refer to General Electrical Installation Guidelines for harness routing criteria.
This section assumes an existing connection between the engine starting switch at the helm and the engine starting circuit. If a connection does not exist, it may be desirable to install this circuit before continuing.
1.
Disconnect the wire coming from the start switch at the helm from the start relay/solenoid and connect it to J5 pin 9.
2.
5.
Make a connection from J5 pin 10 to the start relay/solenoid using 14
AWG wire.
Route both yellow with a red stripe wires to the EC300 Control.
For the yellow with a red stripe wire from the start switch at the helm, crimp the supplied Deutsch contact (P/N 0462-209-16141) using the
Deutsch HDT crimp tool (P/N HDT 48-00).
Note: The Deutsch 14 AWG contact (P/N 0462-209-16141) can be identified by a green band.
Remove the locking wedge from the Deutsch connector.
EC300 Marine Control System Installation Manual #1024168
93
Electrical Installation
Twin Disc, Incorporated
6.
Insert the wire coming from the start switch at the helm into pin 9 of the
J5 connector.
Note: The J5 connector is provided in the Engine throttle connector kit.
7.
Note: Refer to the EC300 System Installation Drawings in the
Engineering Drawings Section for pin numbering information.
For the yellow with a red stripe wire from the starter relay/solenoid, crimp the supplied Deutsch contact (P/N 0462-209-16141) using the Deutsch
HDT crimp tool (P/N HDT 48-00).
8.
9.
Insert the wire coming from the start relay/solenoid into pin 10 of the J5 connector.
When all pins have been inserted in the connector body, then insert the
Deutsch locking wedge.
10.
Ensure that sealing plugs are installed in all empty connector positions.
11.
Align the harness connector with the J5 receptacle of the EC300 Control and push it in until it snaps into place.
12.
Secure all harnesses to a supporting structure with clamps or cable ties at 406 mm (16 in.) intervals.
94 EC300 Marine Control System Installation Manual #1024168
Twin Disc, Incorporated
Electrical Installation
Electronic Control Module Throttle Wiring
These signals interface with the engine Electronic Control Module’s (ECM’s) throttle input. The engine control module can also be referred to as the Electronic
Control Unit (ECU), Electronic Engine Control (EEC), or other similar names.
The engine manufacturer provides specific engine control manuals that detail the requirements for the throttle signal and power supply connections. The
Engine Control Harness (J5) has six pins for throttle control. Table 10 lists the pin functions.
The engine control output can consist of three signals as follows:
The throttle control signal
An optional signal indicating the transmission is in neutral
An optional signal indicating the transmission is not in neutral
Table 10. Engine Control Pin Functions
Pin
J5 Pin 1
J5 Pin 2
Signal Name
ECM Power Supply
Throttle Signal
Function
Power supply for the Throttle Signal. It is most often a power supply coming from J8 pin 2. In some cases it may be power coming from the
ECM. This signal is to be used as the power source for the throttle signal output.
The throttle position output signal. Depending upon the engine manufacturer, this signal can be a programmed voltage or current. The throttle signal is directed by the position of the lever at the active control head. It can also be a pulse train with programmable low and high levels with variable frequency or pulse widths. This is configured by the Twin Disc distributor or at the factory.
J5 Pin 3 ECM Power Supply
Common
The common return path and reference point for engine throttle circuit.
J5 Pin 4 Transmission State 1 A solid-state switch output that goes active when the transmission is in neutral. This wire is used only for specific engines. See page B-12 in Appendix B for additional information
J5 Pin 5 Transmission State 2 A solid-state switch output that goes active when the transmission is not in neutral. This wire is used only for specific engines. See page B-
12 in Appendix B for additional information
J5 Pin 6 Transmission State
Return
The return signal for the transmission state signal. This wire is used only for specific engines. See page B-12 in Appendix B for additional information
EC300 Marine Control System Installation Manual #1024168
95
Electrical Installation
Twin Disc, Incorporated
96
The EC300 Control System currently supports the following types of electronic engine controls:
Table 11. Engines Supported
Engine Manufacturer
Caterpillar
Cummins
Cummins
Detroit Diesel
Detroit Diesel
Deutz
Deutz
Iveco
Iveco
John Deere
MAN
MTU
Scania
Volvo Penta
Volvo Penta
Engine Name in MFST
Caterpillar
Cummins Centry/Celect
Cummins Quantum
Detroit Diesel Voltage
Detroit Diesel Frequency
Deutz Type 1
Deutz Type 2
Iveco PWM
Iveco Voltage
John Deere
MAN Current
MTU
Scania
Volvo Penta EVC B
Volvo Penta EVC C
Voltage
Voltage
Voltage
Current
Current
Voltage
Current
Current
Carrier
Voltage
Current
Voltage
Voltage
Current
Voltage
Voltage
Modulation
PWM
Amplitude
Amplitude
Amplitude
Frequency
PWM
Amplitude
PWM
Amplitude
Amplitude
Amplitude
Amplitude
Amplitude
Amplitude
Amplitude
If the specific engine is not listed, contact Twin Disc Incorporated or a local distributor for custom information and support.
Note: All EC300 Control configuration is performed by Twin Disc
Incorporated or its local distributor.
Refer to Appendix - B for detailed electrical installation requirements for the engines listed.
Harness Fabrication and Wiring Procedure
Note: The connector kit supplied for Engine Control Harness
J5 has enough contacts and plugs necessary to fill the connector. Use only the contacts that are needed. Unused connector positions must have a sealing plug inserted in order to maintain the environmental integrity of the connector.
EC300 Marine Control System Installation Manual #102
4168
Twin Disc, Incorporated
Electrical Installation
5.
6.
7.
8.
Install the Engine Throttle Wiring portion of the Engine Control harnesses as follows:
Refer to General Electrical Installation Guidelines for harness routing criteria.
1.
Identify the wiring requirements from the installation drawing and from appendix -B for the specific engine installation.
2.
Locate the necessary connecting points on the engine control module or engine control wiring circuits.
3.
4.
Make a suitable interface harness containing the necessary conductors.
Note: The throttle signal wires must be 18 AWG stranded copper wire. All other wires must be a minimum of 18 AWG stranded copper wire.
Connect the engine harness at the engine end.
Note: It may be desirable to complete any other terminations for this harness before securing the harness.
Route the engine harness to the associated EC300 Control.
Crimp the supplied Deutsch pin (P/N 0462-209-16141) using the
Deutsch HDT crimp tool (P/N HDT 48-00) for the Engine Control Harness
J5 connector on the wires.
Remove the locking wedge from the Deutsch connector.
Insert the wires into the proper position in the J5 connector.
Note: Refer to the EC300 System Installation Drawings in the
Engineering Drawings Section for pin numbering information.
Note: The J5 connector is provided in the Engine throttle connector kit.
Note: Ensure that the pin to wire crimp is uniform and complete.
Ensure that the pin is locked into in the connector.
EC300 Marine Control System Installation Manual #1024168
97
Electrical Installation
Twin Disc, Incorporated
9.
When all pins have been inserted in the connector body, then insert the
Deutsch locking wedge.
10.
Ensure that sealing plugs are installed in all empty connector positions.
11.
Align the harness connector with the J5 receptacle of the EC300 Control and push it in until it snaps into place.
12.
Secure all harnesses to a supporting structure with clamps or cable ties at 406 mm (16 in.) intervals.
98 EC300 Marine Control System Installation Manual #1024168
Twin Disc, Incorporated
Electrical Installation
Engine Speed Sensor Harness Installation
The Engine Speed Sensor Harness is a prefabricated wiring harnesses with connectors installed on the equipment end and terminals installed on the EC300 end of the harness. The terminals on these harnesses will be installed into the
EC300 connector (J5) provided by Twin Disc Incorporated. The Neutral Start
Interlock wiring and Engine Throttle wiring (if applicable) should be fabricated and routed to the EC300 prior to installing the Engine Speed Sensor Harness.
CAUTION
The engine speed sensor signal must connect only to the EC300 Control.
If another speed sensor signal is required, use engine speed sensor doublers or dual output engine speed sensors. Note that a tachometer output is available from the EC300 Control.
Install the Engine Speed Sensor Harness Wiring portion of the Engine Control harnesses as follows (See Figure 41):
HARNESS, WIRING
ENGINE THROTTLE
SEE ENGINE CONTROL HARNESS
INSTALLATION SECTION
HARNESS, WIRING
ENGINE SPEED SENSOR
1020706
ENGINE
SPEED
SENSOR
SIGNAL
SENSOR RETURN
J5-11
J5-12
RED/GRN STRIPE
GRN/RED STRIPE
A
B
CONNECTOR KIT
ENGINE THROTTLE
TWIN DISC
INCORPORATED
MODEL EC300
P/N 1020676
BOM
S/N
VOLTAGE 12-24VDC
J1 J2 J3 J4
6
J5
7
J6
1 12
J7
J8 J9
J10 J11
J12 J13
Figure 41. Engine Speed Sensor Harness Wiring
EC300 Marine Control System Installation Manual #1024168
99
Electrical Installation
Twin Disc, Incorporated
5.
6.
7.
8.
Refer to General Electrical Installation Guidelines for harness routing criteria.
1.
Remove the locking wedge from the J5 Deutsch connector.
2.
Insert the red with a green stripe wire into position 11 of the J5 connector.
3.
4.
9.
Insert the green with a red stripe wire into position 12 of the J5 connector.
Note: Refer to the EC300 System Installation Drawings in the
Engineering Drawings Section for pin numbering
information.
When both pins have been inserted in the connector body, then insert the Deutsch locking wedge.
Ensure that sealing plugs are installed in all empty connector positions.
Align the harness connector with the J5 receptacle of the EC300 Control and push it in until it snaps into place.
Route the Engine Speed Sensor Harness to the Engine Speed Sensor.
Plug the 2-pin connector of the Engine Speed Sensor Harness into the
Engine Speed Sensor receptacle.
Secure all harnesses to a supporting structure with clamps or cable ties at 406 mm (16 in.) intervals.
100 EC300 Marine Control System Installation Manual #1024168
Twin Disc, Incorporated
Electrical Installation
Engine Room Analog Harness (J6) Installation
The Engine Room Analog Harness Connector (J6) provides analog inputs from a transmission oil temperature sensor and a transmission output speed sensor.
The oil temperature sensor is not applicable in all installations. The Engine
Room Analog harness is fully pre-fabricated and plugs into the J6 connector at the EC300 Control and directly into the temperature sensor and output speed sensor at the other end. The J6 connector contains all contacts and sealing plugs that are required to fill the connector. Sealing plugs must be installed into all unused connector contact positions in order to maintain the integrity of the connector.
This section contains the following sub-sections:
Transmission Oil Temperature Sensor Wiring Installation
Transmission Output Speed Sensor Wiring Installation
HARNESS, WIRING
ENGINE ROOM ANALOG
TRANS OIL
TEMP SENSOR
TRANSMISSION
OUTPUT SENSOR
TWIN DISC
INCORPORATED
MODEL EC300
P/N 1020676
BOM
S/N
VOLTAGE 12-24VDC
J1 J2 J3 J4
J5
4
J6
5
J7
1 8
J8
J9 J10 J11
J12 J13
J6-6
J6-8
J6-7
J6-3
J6-4
J6-5
J6-1
J6-2
X
X
X
SENSOR + EXCITATION
SENSOR RETURN
SIGNAL
RED
BLACK
ORANGE
SIGNAL
SENSOR RETURN
RED/GRN STRIPE
GRN/RED STRIPE
A
B
C
TRANSMISSION
OUTPUT
A
B
TRANS OIL TEMP
Figure 42. Engine Room Analog Harness (J6) Wiring Diagram
EC300 Marine Control System Installation Manual #1024168
101
Electrical Installation
Twin Disc, Incorporated
Transmission Oil Temperature Sensor Wiring Installation
Install the wiring for a Transmission Oil Temperature Sensor as follows (See
Figure 42):
Refer to General Electrical Installation Guidelines for harness routing criteria.
1.
Align the Engine Room Analog Harness connector with the J6 receptacle of the EC300 Control and push it in until it snaps into place.
2.
Route the Engine Room Analog Harness to the associated transmission.
Note: The Transmission Oil Temperature Sensor cable is part of the Engine Room Analog harness. Cable ties may be removed for routing purposes.
3.
4.
Install the Transmission Oil Temperature Sensor cable’s receptacle onto the transmission oil temperature sensor’s plug.
Secure all harnesses to a supporting structure with clamps or cable ties at 406 mm (16 in.) intervals.
Note: It may be desirable to complete any other terminations for this harness before securing the harness.
102 EC300 Marine Control System Installation Manual #1024168
Twin Disc, Incorporated
Electrical Installation
Transmission Output Speed Sensor Wiring Installation
Install the wiring for a Transmission Output Speed Sensor as follows (See Figure
42):
Refer to General Electrical Installation Guidelines for harness routing criteria.
1.
Align the Engine Room Analog Harness connector with the J6 receptacle of the EC300 Control and push it in until it snaps into place.
2.
3.
Route the Engine Room Analog Harness to the associated transmission.
Note: The Transmission Output Speed Sensor cable is part of the Engine Room Analog harness. Cable ties may be removed for routing purposes.
Install the Transmission Output Speed Sensor cable’s plug into the
Transmission Output Speed Sensor’s receptacle.
4.
Secure all harnesses to a supporting structure with clamps or cable ties at 406 mm (16 in.) intervals.
Tooth Count
Note: The EC300 Control must be configured with the correct tooth count for the specific transmission installed. Obtain the correct tooth count information from the manufacturer’s literature or count the teeth.
EC300 Marine Control System Installation Manual #1024168
103
Electrical Installation
Twin Disc, Incorporated
PWM Driver Harness (J7) Installation
The PWM Driver Harness (J7) provides solenoid driver outputs for transmission gear selection and other functions. Not all of these outputs are used in any specific application. The following sections provide instructions for the installation of the PWM Driver Harness.
The PWM Driver harness is fully pre-fabricated and plugs into the J7 connector at the EC300 Control and directly into the solenoid connectors at the other end.
The J7 connector contains all contacts and sealing plugs that are required to fill the connector. Sealing plugs must be installed into all unused connector contact positions in order to maintain the integrity of the connector.
This section contains the following sub-sections:
Two Solenoid Transmission Clutch Control Wiring Installation
Three Solenoid Transmission Clutch Control Wiring Installation
Shaft Brake Wiring Installation
Stabilizer Disable Wiring Installation
Troll Enable Wiring Installation
104 EC300 Marine Control System Installation Manual #1024168
Twin Disc, Incorporated
Electrical Installation
J5
HARNESS, WIRING
PWM DRIVERS
J12
J6
6
J7
7
1
J13
12
NEUT.
REV
FWD
REV
FWD
REV
FWD
TROLL
FWD
REV
J7-6
J7-3
J7-5
J7-2
J7-4
J7-1
J7-7
J7-10
J7-8
J7-11
J7-9
X
X
X
X
X
J7-12 X
BROWN/LIGHT BLUE STRIPE
LIGHT BLUE/BROWN STRIPE
PURPLE/YELLOW STRIPE
YELLOW/PURPLE STRIPE
GREEN/RED STRIPE
RED/GREEN STRIPE
F
E
D
C
B
A
NEUTRAL
REVERSE
FORWARD
J7-6
J7-3
J7-5
J7-2
J7-4
J7-1
J7-7
J7-10
J7-8
J7-11
X
X
X
X
J7-9
X
J7-12 X
X
X
PURPLE/YELLOW STRIPE
YELLOW/PURPLE STRIPE
GREEN/RED STRIPE
RED/GREEN STRIPE
J7-6
J7-3
J7-5
J7-2
J7-4
X
X
J7-1
J7-7
J7-10
X
X
J7-8
J7-9
X
J7-11
X
X
J7-12 X
PURPLE/YELLOW STRIPE
YELLOW/PURPLE STRIPE
GREEN/RED STRIPE
RED/GREEN STRIPE
B
A
D
C
D
C
B
A
REVERSE
FORWARD
REVERSE
FORWARD
J7-9
J7-12
J7-8
J7-11
J7-8
J7-11
J7-6
J7-3
J7-5
J7-2
J7-4
X
X
J7-1
J7-7
J7-10
J7-8 X
J7-11
X
J7-9
X
J7-12
X
PURPLE/YELLOW STRIPE
YELLOW/PURPLE STRIPE
GREEN/RED STRIPE
RED/GREEN STRIPE
LIGHT BLUE/BROWN STRIPE
BROWN/LIGHT BLUE STRIPE
B
A
B
A
D
C
REVERSE
FORWARD
TROLL
RED
BLACK
RED
BLACK
RED
BLACK
SHAFT BRAKE
STABILIZER
DISABLE
TROLL
ENABLE
Figure 43. PWM Driver Harness Wiring Diagram
EC300 Marine Control System Installation Manual #1024168
105
Electrical Installation
Twin Disc, Incorporated
Two Solenoid Transmission Clutch Control Wiring Installation
Install the wiring for a two-solenoid transmission as follows (See Figure 43):
Note: Refer to the transmission manufacturer’s technical manual as required to identify the solenoids. If the solenoids are not clearly identified, make the connections on a temporary basis until testing can confirm the selection.
3.
4.
Refer to General Electrical Installation Guidelines before proceeding with this section.
1.
Connect the PWM Driver harness to the forward and reverse solenoid connectors.
2.
Route the PWM Driver harness to the EC300 Control.
Note: It may be desirable to complete any other terminations for this harness before securing the harness.
Ensure that sealing plugs are installed in all empty connector positions.
5.
Align the harness connector with the J7 receptacle of the EC300 Control and push it in until it snaps into place.
Secure all harnesses to a supporting structure with clamps or cable ties at 406 mm (16 in.) intervals.
106 EC300 Marine Control System Installation Manual #1024168
Twin Disc, Incorporated
Electrical Installation
Three Solenoid Transmission Clutch Control Wiring Installation
Install the wiring for a three-solenoid transmission as follows (See Figure 43):
Note: Refer to the transmission manufacturer’s technical manual as required to identify the solenoids. If the solenoids are not clearly identified, make the connections on a temporary basis until testing can confirm the selection.
Refer to General Electrical Installation Guidelines before proceeding with this section.
1.
2.
Connect the PWM Driver harness to the forward, neutral, and reverse solenoid connectors.
Route the PWM Driver harness to the EC300 Control.
3.
4.
5.
Note: It may be desirable to complete any other terminations for this harness before securing the harness.
Ensure that sealing plugs are installed in all empty connector positions.
Align the harness connector with the J7 receptacle of the EC300 Control and push it in until it snaps into place.
Secure all harnesses to a supporting structure with clamps or cable ties at 406 mm (16 in.) intervals.
EC300 Marine Control System Installation Manual #1024168
107
Electrical Installation
Twin Disc, Incorporated
108
Shaft Brake Wiring Installation
Install the wiring for a shaft brake solenoid as follows (See Figure 43):
Note: The connector kit supplied for the PWM Driver Harness has enough contacts and plugs necessary to fill the connector. Use only the contacts that are needed. Unused connector positions must have a sealing plug inserted in order to maintain the environmental integrity of the connector.
Refer to General Electrical Installation Guidelines before proceeding with this section.
1.
2.
3.
Connect the red wire to the signal lead for the Shaft Brake Solenoid.
Connect the black wire to the return lead for the Shaft Brake Solenoid.
Route the red and black wires to the EC300 Control.
Note: It may be desirable to complete any other terminations for this harness before securing the harness.
4.
5.
Remove the locking wedge from the Deutsch connector.
Insert the red wire into position 9 of the J7 connector.
Note: Refer to the EC300 System Installation Drawings in the
Engineering Drawings Section for pin numbering information.
Note: The J7 connector is part of the PWM Driver Harness.
Insert the black wire into position 12 of the J7 connector.
6.
7.
When all pins have been inserted in the connector body, reinsert the
Deutsch locking wedge into the front of the connector body.
Ensure that sealing plugs are installed in all empty connector positions.
8.
9.
Align the harness connector with the J7 receptacle of the EC300 Control and push it in until it snaps into place.
10.
Secure all harnesses to a supporting structure with clamps or cable ties at 406 mm (16 in.) intervals.
EC300 Marine Control System Installation Manual #1024168
Twin Disc, Incorporated
Electrical Installation
Stabilizer Disable Wiring Installation
Install the wiring for a stabilizer disable solenoid as follows (See Figure 43):
1.
2.
3.
Note: The connector kit supplied for the PWM Driver Harness has enough contacts and plugs necessary to fill the connector. Use only the contacts needed. Unused connector positions must have a sealing plug inserted to maintain the environmental integrity of the connector.
Refer to General Electrical Installation Guidelines before proceeding with this section.
Connect the red wire to the signal lead for the Stabilizer Disable input.
Connect the black wire to the return lead for the Stabilizer Disable input.
Route the red and black wires to the EC300 Control.
Note: It may be desirable to complete any other terminations for this harness before securing the harness.
Remove the locking wedge from the Deutsch connector.
4.
5.
Insert the red wire into position 8 of the J7 connector.
Note: Refer to the EC300 System Installation Drawings in the
Engineering Drawings Section for pin numbering information.
Note: The J7 connector is part of the PWM Driver Harness.
Insert the black wire into position 11 of the J7 connector.
6.
7.
8.
When all pins have been inserted in the connector body, reinsert the
Deutsch locking wedge into the front of the connector body.
Ensure that sealing plugs are installed in all empty connector positions.
9.
Align the harness connector with the J7 receptacle of the EC300 Control and push it in until it snaps into place.
10.
Secure all harnesses to a supporting structure with clamps or cable ties at 406 mm (16 in.) intervals.
EC300 Marine Control System Installation Manual #1024168
109
Electrical Installation
Twin Disc, Incorporated
110
Troll Enable Wiring Installation
Install the wiring for a troll enable solenoid as follows (See Figure 43):
Note: The connector kit supplied for the PWM Driver Harness has enough contacts and plugs necessary to fill the connector. Use only the contacts that are needed. Unused connector positions must have a sealing plug inserted in order to maintain the environmental integrity of the connector.
Refer to General Electrical Installation Guidelines before proceeding with this section.
1.
2.
3.
Connect the red wire to the signal lead for the Troll Enable Solenoid.
Connect the black wire to the return lead for the Troll Enable Solenoid.
Route the red and black wires to the EC300 Control.
Note: It may be desirable to complete any other terminations for this harness before securing the harness.
4.
5.
Remove the locking wedge from the Deutsch connector.
Insert the red wire into position 8 of the J7 connector.
Note: Refer to the EC300 System Installation Drawings in the
Engineering Drawings Section for pin numbering information.
Note: The J7 connector is part of the PWM Driver Harness.
Insert the black wire into position 11 of the J7 connector.
6.
7.
When all pins have been inserted in the connector body, reinsert the
Deutsch locking wedge into the front of the connector body.
Ensure that sealing plugs are installed in all empty connector positions.
8.
9.
Align the harness connector with the J7 receptacle of the EC300 Control and push it in until it snaps into place.
10.
Secure all harnesses to a supporting structure with clamps or cable ties at 406 mm (16 in.) intervals.
EC300 Marine Control System Installation Manual #1024168
Twin Disc, Incorporated
Electrical Installation
Bridge Signals Harness (J8) Installation
The Bridge Signals Harness (J8) provides wiring connections for the Ignition
Switch, Manual Override Switch, and Tachometer. Not all of these features may be used in any specific application. The Bridge Signals Harness (J8) is field fabricated. The J8 connector kit is provided by Twin Disc Incorporated and consists of the EC300 J8 connector and all contacts and sealing plugs for the connector. The equipment end of the harness is fabricated by the installer at the time of installation with components provided by the customer. Sealing plugs must be installed into all unused connector contact positions in order to maintain the integrity of the connector.
Note: EC300 Bridge Signals Harness (J8) also may contain wiring for other features. Route the harness to the most convenient location serving all the applicable connections.
This section contains the following sub-sections:
Ignition Switch Wiring
Manual Override Switch Wiring
Tachometer Output Wiring Installation
CUSTOMER SUPPLIED WIRE
ECM POWER SUPPLY
CONNECT FROM J8-2 TO J5-1
NOTE: NOT FOR USE WITH
CAT ENGINE APPLICATIONS
MANUAL OVERRIDE
SWITCH
IGNITION SWITCH
+12/24 VDC
J8-1
J8-2
TACHOMETER OUTPUT SIGNAL
TACHOMETER RETURN SIGNAL
J8-3
J8-4
J8-5
J8-6
HARNESS, WIRING
BRIDGE SIGNALS
CUSTOMER SUPPLIED
J1 J2 J3 J4 J5 J6 J7
1
8
J8
4
5
J9
TWIN DISC
INCORPORATED
MODEL EC300
P/N 1020676
BOM
S/N
VOLTAGE 12-24VDC
J10 J11 J12 J13
CONNECTOR KIT
BRIDGE SIGNALS
Figure 44. Bridge Signals Harness (J8) Connections
EC300 Marine Control System Installation Manual #1024168
111
Electrical Installation
Twin Disc, Incorporated
Ignition Switch Wiring
Ignition switch wiring is accomplished through the Bridge Signals Harness (J8) that connects to the J8 receptacle at the EC300 Control. The ignition signal turns on power to the EC300 Control. The control will not function unless this terminal is connected to a DC signal source from the load side of the ignition switch.
Note: The following instructions refer to a combination ignition switch which has an ON position and a START position.
For this type of ignition switch installation, power to the
EC300 Control must not be interrupted when starting the engine. If a common master power switch is used to enable separate START push-buttons, then use this master ON switch as this signal source.
Install the Ignition Switch Wiring portion of the Bridge Signals harnesses as follows (See Figure 44):
CAUTION
The DC voltage from the ignition switch to J8, Pin 1 must be from the same source as the voltage used by the EC300 Control. It must not be interrupted when the engine is started.
Refer to General Electrical Installation Guidelines before proceeding with this section.
1.
Connect the wire to be used for the ignition wiring to the load side of the ignition switch.
2.
3.
Route the wire to the EC300 Control.
Note: It may be desirable to complete any other terminations for this harness before securing the harness.
Remove the locking wedge from the Deutsch connector.
112 EC300 Marine Control System Installation Manual #1024168
Twin Disc, Incorporated
Electrical Installation
4.
5.
6.
7.
8.
Insert the wire into position 1 of the J8 connector.
Note: Refer to the EC300 System Installation Drawings in the
Engineering Drawings Section for pin numbering information.
Note: The J8 connector is part of the Bridge Signals Harness.
When all pins have been inserted in the connector body, reinsert the
Deutsch locking wedge into the front of the connector body.
Ensure that sealing plugs are installed in all empty connector positions.
Align the harness connector with the J8 receptacle of the EC300 Control and push it in until it snaps into place.
Secure all harnesses to a supporting structure with clamps or cable ties at 406 mm (16 in.) intervals.
EC300 Marine Control System Installation Manual #1024168
113
Electrical Installation
Twin Disc, Incorporated
Manual Override Switch Wiring
The Manual Override switch is used to disable the forward and reverse solenoid drivers when the manual override valve is open. The Manual Override switch is a normally closed contact. In the event the manual override valve is manually activated, the switch contacts will open and the EC300 control will go into a controller neutral condition and no longer power the forward and reverse solenoids. If used, the Manual Override Switch should be installed per Manual
Override Switch Installation.
Install the Manual Override Switch input wiring portion of the Bridge Signals harnesses as follows (See Figure 44):
WARNING
Twin Disc Incorporated strongly recommends that the Manual Override
Switch is properly wired if the transmission is equipped with a manual override valve. Failure to properly wire the Manual Override Switch may cause catastrophic gear failure if the Manual Override Valve and the forward or reverse solenoid are inadvertently activated at the same time.
Refer to General Electrical Installation Guidelines before proceeding with this section.
1.
Connect the customer supplied wire to either screw terminal on one of the manual override valve switches.
2.
3.
4.
Connect the other customer supplied wire to the other screw terminal on the manual override valve switch.
Note: The manual override valve has screw terminals on both sides for two separate connections. One side is for the
J8 Manual Override switch connection and the other side for the J5 neutral start switch connection.
Route the two wires to the EC300 Control.
Note: EC300 Bridge Signals Harness (J8) also may contain wiring for other features. Route the harness to the most convenient location serving all the applicable connections.
Remove the locking wedge from the Deutsch connector.
114 EC300 Marine Control System Installation Manual #1024168
Twin Disc, Incorporated
Electrical Installation
5.
Insert one of the wires into position 3 of the J8 connector.
Note: Refer to the EC300 System Installation Drawings in the
Engineering Drawings Section for pin numbering information.
Note: The J8 connector is part of the Bridge Signals Harness.
Insert the other wire into position 4 of the J8 connector.
6.
7.
When all pins have been inserted in the connector body, reinsert the
Deutsch locking wedge into the front of the connector body.
Ensure that sealing plugs are installed in all empty connector positions.
8.
9.
Align the harness connector with the J8 receptacle of the EC300 Control and push it in until it snaps into place.
10.
Secure all harnesses to a supporting structure with clamps or cable ties at 406 mm (16 in.) intervals.
Note: It may be desirable to complete any other terminations for this harness before securing the harness.
EC300 Marine Control System Installation Manual #1024168
115
Electrical Installation
Twin Disc, Incorporated
Tachometer Output Wiring Installation
The tachometer output circuit is used to drive a tachometer indicator. This signal can be used to drive a tachometer at the helm indicating either engine or propeller speed.
Install the tachometer output wiring portion of the Bridge Signals harnesses as follows (See Figure 44):
3.
4.
5.
Refer to General Electrical Installation Guidelines before proceeding with this section.
1.
Note: EC300 Bridge Signals Harness (J8) also may contain wiring for other features. Route the harness to the most convenient location serving all the applicable connections.
Connect one customer supplied wire to the signal input connection on the tachometer.
2.
Connect the other customer supplied wire to the return connection on the tachometer.
Route the two wires to the EC300 Control.
Remove the locking wedge from the Deutsch connector.
Insert the wire connected to the tachometer signal input into position 5 of the J8 connector.
6.
Note: Refer to the EC300 System Installation Drawings in the
Engineering Drawings Section for pin numbering
information.
Note: The J8 connector is part of the Bridge Signals Harness.
Insert the wire connected to the tachometer signal return into position 6 of the J8 connector.
116 EC300 Marine Control System Installation Manual #1024168
Twin Disc, Incorporated
Electrical Installation
7.
When all pins have been inserted in the connector body, reinsert the
Deutsch locking wedge into the front of the connector body.
Ensure that sealing plugs are installed in all empty connector positions.
8.
9.
Align the harness connector with the J8 receptacle of the EC300 Control and push it in until it snaps into place.
10.
Secure all harnesses to a supporting structure with clamps or cable ties at 406 mm (16 in.) intervals.
Note: It may be desirable to complete any other terminations for this harness before securing the harness.
EC300 Marine Control System Installation Manual #1024168
117
Electrical Installation
Twin Disc, Incorporated
Twin Disc Display Harness (J9) Installation
The Twin Disc Display Harness Assembly consists of a communication harness, two adapter harnesses, two J1939 T-Connectors, and two J1939 terminating resistors. The J1939 CAN Harness adapts the Communications Harness to the display’s 3-pin receptacle via a J1939 T-Connector. The Multiple Display
Adapter Harness adapts the Communications Harness to the control’s J9 receptacle via a J1939 T-Connector. The Communication Harness has identical
T-Connectors at each end. Each end is supplied with a pre-installed terminating resistor. Do not remove the J1939 terminating resistors.
The Display Power Harness connects between the 8 - pin receptacle of the
Multiple Display Adapter Harness and the 6 - pin receptacle of the display. The black wire at the display end of the harness connects to the circular connector of the Control Head.
This section contains the following sub-sections:
Twin Disc Display Harness Wiring
Note: The purchase and installation of the Twin Disc Display is an option. If physical installation is impractical, the display may be stored and only used temporarily during configuration and troubleshooting. The following assumes that the display has been installed.
118 EC300 Marine Control System Installation Manual #1024168
Twin Disc, Incorporated
Electrical Installation
TO CONTROL HEAD
DISPLAY
HARNESS, WIRING
DISPLAY POWER
1020718
HARNESS, WIRING
J1939 CAN
CONNECTOR
TERMINATING RESISTOR
2 PLACES
CONNECTOR
J1939 T CONNECTOR
2 PLACES
J1939-CAN H
J1939-CAN L
J1939-CAN SHIELD
A
B
C
RED/GRN STRIPE
GRN/RED STRIPE
+12/+24V VDC POWER
BATTERY GROUND
BACKLIGHT CONTROL
NOT FOR CUSTOMER USE
STATION ACTIVE
NOT FOR CUSTOMER USE
1
2
3
4
5
6
WHITE
BLACK
BLACK
120
A B C
A B C
C B A
C B A
TO CONTROL HEAD
PIN E FOR PORT
PIN J FOR STBD
TWIN DISC
INCORPORATED
MODEL EC300
P/N 1020676
BOM
S/N
VOLTAGE 12-24VDC
J1 J2 J3 J4 J5 J6 J7
J8
4
3
J9
6
1
J10 J11 J12 J13
HARNESS, WIRING
MULTIPLE DISPLAY ADAPTER
A
A
B
B
C
C
GRN/RED STRIPE
RED/GRN STRIPE
1020615
HARNESS, WIRING
COMMUNICATION
C C
B B
A A
A A
B B
C C
C
B
A
C
B
A
120
RED/GRN STRIPE
GRN/RED STRIPE
BLACK
WHITE
2
3
6
J9
4
5
1
Figure 45. Display Harness J9 Installation
6 8 5 7 4 2 3 1
EC300 Marine Control System Installation Manual #1024168
119
Electrical Installation
Twin Disc, Incorporated
120
Twin Disc Display Harness Wiring
Install the Twin Disc Display Harness Assembly and the Display Power Harness as follows (See Figure 45):
Refer to General Electrical Installation Guidelines before proceeding with this section.
1.
Align the 3-pin plug of the J1939 Can harness with the 3-pin receptacle of the Twin Disc Display and push together until the lock snaps into place.
2.
3.
Install a J1939 T-Connector into the remaining 3-pin plug of the J1939
Can harness.
Install a 3-pin plug of the Communications harness into the J1939 T-
Connector.
4.
5.
Align the 6-pin plug of the Display Power harness with the 6-pin receptacle of the Twin Disc Display and push together until the lock snaps into place.
Route the short black wire to the Control Head.
7.
8.
6.
9.
Access the Control Head connector.
Note: The Control Head may be removed from the dash if this facilitates making the connection. If it is removed, then reinstall it after the connections have been made.
Disconnect the Control Head harness from the Control Head.
Install the short black wire of the Display Power harness into the Control head receptacle (position E for a port lever application, position J for a starboard lever application).
Route the Display Power harness and the Communications harness to the EC300 Control.
10.
Install a J1939 T-Connector into the 3-pin plug of the Multiple Display
Adapter harness.
11.
Install the 3-pin plug of the Communications harness into the J1939 T-
Connector
EC300 Marine Control System Installation Manual #1024168
Twin Disc, Incorporated
Electrical Installation
12.
Remove the 8-pin receptacle from the Multiple Display Adapter harness located near the J9 connector at the EC300 Control.
13.
Remove the locking wedge from the Multiple Display Adapter harness’s plug.
14.
Install the white wire of the Display Power harness into position 2, 7, or
8 of the 8-pin plug of the Multiple Display Adapter harness.
15.
Install the black wire of the Display Power harness into position 4, 5, or
6 of the 8-pin plug of the Multiple Display Adapter harness.
16.
Install a J1939 terminating resistor into the J1939 T-Connector receptacle located at each end of the Twin Disc Display Communications
Harness Assembly.
Note: Terminating resistors must be installed at each end of the
Twin Disc Display Communication Harness Assembly for the communications to work properly.
17.
Repeat steps 1 through 16 for each additional Twin Disc Display.
18.
When all pins have been inserted in the connector body, install the locking wedge into the Multiple Display Adapter harness 8-pin plug.
19.
Install the 8-pin receptacle onto the Multiple Display Adapter harness’s
8-pin plug.
20.
Align the Multiple Display Adapter harness 6-pin connector with the J9 receptacle of the EC300 Control and push it in until it snaps into place.
21.
Secure all harnesses to a supporting structure with clamps or cable ties at 406 mm (16 in.) intervals.
EC300 Marine Control System Installation Manual #1024168
121
Electrical Installation
Twin Disc, Incorporated
Communication Harness (J10) Installation
The Communications Harness (J10) provide the main interface between two or more EC300 Controllers. The vessel may have one or more EC300
Controllers located in or near the engine room. The Communication Harnesses
(J10) are fully pre-fabricated and plug into the J10 connector at each EC300.
The J10 connectors contains all contacts and sealing plugs that are required to fill the connector. Sealing plugs must be installed into all unused connector contact positions in order to maintain the integrity of the connector.
Cruise mode and Express mode support a feature in which the speed of all engines in the system can be synchronized. For the synchronization feature to function, information must be passed between all controllers in the system. A communication harness assembly is required to be connected between all
EC300 Controls. A typical harness assembly consists of 2 controller harnesses;
1 communication harness; 2 T-connector receptacles; and 2 terminating resistors. The harnesses are available in various lengths and are terminated with the proper connectors.
This section contains the following sub-sections:
Dual Engine Communication Harness Installation
Multiple Engine Communication Harness Installation
122 EC300 Marine Control System Installation Manual #1024168
Twin Disc, Incorporated
Electrical Installation
Dual Engine Communication Harness Installation
A Communication Harness Assembly is required to connect the two EC300
Controllers on a dual engine installation. This prefabricated harness assembly comes with connectors at both ends. Connect the communication harness to the EC300 Controller at each end. The main communications harness must be terminated at each end. The terminators are installed in the T-Connectors as part of the prefabricated harness assembly.
PORT CONTROL STARBOARD CONTROL
TWIN DISC
INCORPORATED
MODEL EC300
P/N 1020676
BOM
S/N
VOLTAGE 12-24VDC
J1 J2 J3 J4 J5 J6 J7
TWIN DISC
INCORPORATED
MODEL EC300
P/N 1020676
BOM
S/N
VOLTAGE 12-24VDC
J1 J2 J3 J4 J5 J6 J7
J8 J9
2
1
J10
3
4
J11 J12 J13 J8 J9
2
1
J10
3
4
J11 J12 J13
1020614
COMMS +
1
COMMS -
2
COMMON
3
4
X
CONNECTOR
TERMINATING RESISTOR
2 PLACES
RED/GRN STRIPE
GRN/RED STRIPE
DH
A A
B
C
B
C
C
B
C
B
A A
C C
B B
A A
HARNESS, WIRING
COMMUNICATION
1020615
CONNECTOR
J1939 T CONNECTOR
2 PLACES
GRN/RED STRIPE
RED/GRN STRIPE
C
B
A
C
B
A
1020614
HARNESS, WIRING
CONTROLLER COMMS
2 PLACES
DH
A A
B B
C C
C
B
A
C
B
A
120
RED/GRN STRIPE
GRN/RED STRIPE
X
1
2
3
4
Figure 46. Dual Engine Communication Harness Assembly J10
Installation
EC300 Marine Control System Installation Manual #1024168
123
Electrical Installation
Twin Disc, Incorporated
Install the Communication Harness Assembly as follows (See Figure 46):
Note: The specific application may have different lengths for each segment of communication harness. Use the correct segments.
Refer to General Electrical Installation Guidelines before proceeding with this section.
1.
Install a J1939 T-Connector receptacle on the 3-pin plug of each
Controller Comms Harness.
2.
3.
4.
5.
Align the Controller Comms Harness connector with the J10 receptacle of each EC300 Controller and push it in until it snaps into place.
Connect the Communication Harness between the EC300 Controllers by installing the 3-pin plugs into the J1939 T-Connector receptacles located on the Controller Comms Harness at each EC300 Controller.
Install a J1939 Terminating Resistor into the J1939 T-Connector receptacle located at each end of the Communication Harness Assembly.
Note: Terminating resistors must be installed at each end of the communication harness assembly for the communications to work properly.
Secure all harnesses to a supporting structure with clamps or cable ties at 406 mm (16 in.) intervals.
124 EC300 Marine Control System Installation Manual #1024168
Twin Disc, Incorporated
Electrical Installation
Multiple (more than two) Engine Communication Harness Installation
For installations that contain three or more engines, multiple communications harnesses and multiple J1939 T-Connectors are required. The T-connector allows daisy chaining to the J10 connector at each EC300 Controller. Each communications harness is connected to the EC300 Controller through a short controller communications harness. The main communications harness must be terminated at each end. The terminators are installed in the T-Connectors as part of the prefabricated harness assembly.
PORT CONTROL PORT INBOARD CONTROL STARBOARD CONTROL
TWIN DISC
INCORPORATED
MODEL EC300
P/N 1020676
BOM
S/N
VOLTAGE 12-24VDC
J1 J2 J3 J4 J5 J6 J7
J8 J9
2
1
J10
3
4
J11 J12 J13
TWIN DISC
INCORPORATED
MODEL EC300
P/N 1020676
BOM
S/N
VOLTAGE 12-24VDC
J1 J2 J3 J4 J5 J6 J7
J8 J9
2
1
J10
3
4
J11 J12 J13
TWIN DISC
INCORPORATED
MODEL EC300
P/N 1020676
BOM
S/N
VOLTAGE 12-24VDC
J1 J2 J3 J4 J5 J6 J7
J8 J9
2
1
J10
3
4
J11 J12 J13
CONNECTOR
TERMINATING RESISTOR
2 PLACES
CONNECTOR
J1939 T CONNECTOR
3 PLACES
1020615
HARNESS, WIRING
CONTROLLER COMMS
3 PLACES
HARNESS, WIRING
COMMUNICATION
2 PLACES
1020615
Figure 47. Multiple (more than two) Engine Communication Harness
Assembly J10 Installation
EC300 Marine Control System Installation Manual #1024168
125
Electrical Installation
Twin Disc, Incorporated
Install the Communication Harness Assembly as follows (See Figure 47):
Note: The specific application may have different lengths for each segment of communication harness. Use the correct segments.
Refer to General Electrical Installation Guidelines before proceeding with this section.
1.
Install a J1939 T-Connector receptacle on the 3-pin plug of each
Controller Comms Harness.
2.
3.
4.
Align the Controller Comms Harness connector with the J10 receptacle of each EC300 Controller and push it in until it snaps into place.
Connect the Communication Harness between the EC300 Controllers by installing the 3-pin plugs into the J1939 T-Connector receptacles located on the Controller Comms Harness at each EC300 Controller.
Install a J1939 Terminating Resistor into the J1939 T-Connector receptacle located at the far ends of the routing path for the
Communication Harness Assembly.
Note: Terminating resistors must be installed at each end of the communication harness assembly for the communications to work properly.
5.
Secure all harnesses to a supporting structure with clamps or cable ties at 406 mm (16 in.) intervals.
126 EC300 Marine Control System Installation Manual #1024168
Twin Disc, Incorporated
Electrical Installation
Servo Actuator Harness (J11) Installation
Note: The Station Transfer Signal feature will not be available
for EC300 Control Installations with Servo Actuators.
The Servo Actuator Harness (J11) provides the interface between the EC300
Controller and the Servo Actuator. The Servo Actuator Harness is pre-fabricated and plugs into the J11 Connector at the EC300 and into the 12-pin connector at the servo actuator. The Servo Actuator Power Harness is fabricated by the installer at the time of installation with components provided by the customer.
The J11 Connector contains all contacts and sealing plugs that are required to fill the connector. Sealing plugs must be installed into all unused connector contact positions in order to maintain the integrity of the connector.
This section contains the following sub-sections:
Servo Actuator Harness Wiring
The following criteria must be met when installing Servo Actuator harness wiring:
Battery positive and negative power wires must be 14 American Wire
Gauge (AWG) minimum (15 amps max.).
Note: A fuse or circuit breaker is required at the battery or power
distribution point for cable protection. The Servo Actuator is internally protected.
Refer to General Electrical Installation Guidelines for harness routing guidelines.
Power distribution wiring must be insulated. Caps or boots are required at all terminals in order to prevent accidental shorts.
The main power wires to the power/interface connector (battery + and battery -) must be routed directly to the battery or a primary distribution panel within 1 m (3.3 ft) of the battery, but not the starter feed.
Special requirements apply to vessels with gasoline, liquid petroleum gas (LPG), or Marine Compressed Natural Gas (CNG) engines or to vessels with hazardous areas. Power routing and wiring must meet all applicable codes and standards. Circuit components may have to be rated as Ignition Protected as per SAE J1171 External Ignition Protection of Marine Electrical Devices, UL 1500 Ignition Protection Test to Marine
Products, and the electrical system requirements for boats in Title 33
CFR 183.410(a).
EC300 Marine Control System Installation Manual #1024168
127
Electrical Installation
Twin Disc, Incorporated
Do not connect the Servo Actuator's battery + or - power input directly to the engine or any of its electrical components.
Connect the servo power wires to the battery for the engine controlled by the Servo Actuator. Port engine servos should be connected to the
“port” battery. Starboard engine servos should be connected to the
“starboard” battery.
Use a good quality connector to connect the power wires to the battery or bus bar and check the wires to be sure they are secure. Do not use simple spring-loaded connectors.
DC Distribution must be a two-wire system. Battery return wiring must be routed to the battery and not to the bonding system or the metallic hull. The negative side of the battery must be connected to ground if the system is to be grounded.
The electrical load added by the Servo Actuator System is not large.
Current is limited to 15 amps at either 12 or 24 VDC. However, in some circumstances, this may require an increase in the capacity of the power distribution system, larger batteries, and/or larger grounding conductors.
The customer is responsible for meeting the applicable code and standard requirements.
128 EC300 Marine Control System Installation Manual #1024168
Twin Disc, Incorporated
Electrical Installation
Servo Actuator Harness Wiring
Install the Servo Actuator Harness as follows (See Figure 48):
2.
3.
Refer to General Electrical Installation Guidelines before proceeding with this section.
1.
Align the Servo Actuator harness connector with the J11 receptacle of the EC300 Controller and push it in until it snaps into place.
Route the Servo Actuator harness to the Servo Actuator.
Remove the locking wedge from the Servo Actuator connector.
4.
Make a suitable interface harness containing the necessary conductors.
Note: The wires must be a minimum of 14 AWG stranded copper
wire.
5.
6.
Install the primary battery positive wire into pin 4 of the servo actuator connector.
If used, install the auxiliary battery positive wire into pin 5 of the servo actuator connector.
Install the ground wire into pin 6 of the servo actuator connector.
7.
8.
When all pins have been inserted in the connector body, reinsert the locking wedge into the front of the connector body.
Ensure that sealing plugs are installed in all empty connector positions.
9.
10.
Align the harness connector with the connector on the Servo Actuator and push it in until it snaps into place.
11.
Route the primary positive and the ground wires to the Port battery and connect to the battery.
12.
If used, route the auxiliary positive wire to the Starboard battery and connect to the battery.
13.
Repeat Steps 1 through 12 for any remaining Servo Actuators that may be used on other EC300 Controllers.
EC300 Marine Control System Installation Manual #1024168
129
Electrical Installation
Twin Disc, Incorporated
14.
Secure all harnesses to a supporting structure with clamps or cable ties at 406 mm (16 in.) intervals.
TWIN DISC
INCORPORATED
MODEL EC300
P/N 1020676
BOM
S/N
VOLTAGE 12-24VDC
J1 J2 J3 J4 J5 J6 J7
130
J8 J9 J10
2
1
J11
3
4
J12 J13
14 AWG
5 AMP
+
PORT
BATTERY
-
FUSE/HOLDER SUPPLIED
WITH ACTUATOR HARNESS
INSTALL NEAR BATTERY
14 AWG
14 AWG
5 AMP
TO STBD BATT+
HARNESS, WIRING
ACTUATOR
PIN 4 = PRIMARY BATT+
PIN 5 = AUXILIARY BATT+
PIN 6 = GROUND
J11-1
J11-2
J11-3
J11-4 X
CUSTOMER SUPPLIED HARNESS
ACTUATOR POWER
RED
BLACK
ORANGE
11
2
3
POWER SIGNAL
POSITION SIGNAL
POSITION REFERENCE
ACTUATOR
Figure 48. Wiring the Servo Actuator
EC300 Marine Control System Installation Manual #1024168
Twin Disc, Incorporated
Electrical Installation
Station Transfer Signal Wiring Installation
3.
4.
5.
Note: The Station Transfer Signal feature will not be available
for EC300 Control Installations with Servo Actuators.
The station transfer signal output circuit is used to alert ships personnel that control of the ship’s propulsion system is being transferred from one control station to another via an audible device.
The EC300 station transfer signal output can drive up to one amp of current at a voltage approximately equal to the controller power supply. If the audible device requires higher current or a different voltage, an appropriately sized, customer supplied relay must be used.
Install the station transfer signal output wiring harnesses as follows (See Figure
49).
1.
2.
Note: this installation guide covers only direct connection of the
audible device to the EC300 controller.
Connect one customer supplied wire to the positive signal input of the audible device.
Connect the other customer supplied wire to the negative signal input of the audible device.
6.
Route the two wires to the EC300 Control.
Remove the locking wedge from the J11 Deutsch connector.
Insert the wire for the positive signal input of the audible device into pin
1 of the J11 connector.
Insert the wire for the negative signal input of the audible device into pin
4 of the J11 connector.
7.
Note: Refer to the EC300 System Installation Drawings in the
Engineering Drawings Section for pin numbering information.
When all pins have been inserted in the connector body, reinsert the
Deutsch locking wedge into the front of the connector body.
EC300 Marine Control System Installation Manual #1024168
131
Electrical Installation
Twin Disc, Incorporated
8.
Ensure that sealing plugs are installed in all empty connector positions.
9.
Align the harness connector with the J11 receptacle of the EC300
Control.
10.
Secure all harnesses to a supporting structure with clamps or cable ties per applicable codes and standards.
Note: It may be desirable to complete any other terminations of this harness before securing the harness.
132
Figure 49. Wiring the Station Transfer Signal
EC300 Marine Control System Installation Manual #1024168
Twin Disc, Incorporated
Electrical Installation
Engine Room Switch Harness (J12) Installation
The Engine Room Switch Harness (J12) provides digital inputs from a transmission oil filter switch, and a transmission oil pressure switch. Not all of these available inputs may be used in any specific application. This instruction does not cover the physical installation of these sensors. Refer to the applicable manufacturer’s literature if it is necessary to install these components.
The Engine Room Switch Harness (J12) is pre-fabricated and plugs into the
J12 connector at the EC300 Control. The equipment end of the harness is fabricated by the installer at the time of installation with components provided by the customer. The J12 connector contains all contacts and sealing plugs that are required to fill the connector. Sealing plugs must be installed into all unused connector contact positions in order to maintain the integrity of the connector.
This section contains the following sub-sections:
Transmission Oil Filter Differential Pressure Switch Wiring
Transmission Oil Pressure Switch Wiring
EC300 Marine Control System Installation Manual #1024168
13
3
Electrical Installation
Twin Disc, Incorporated
TWIN DISC
INCORPORATED
MODEL EC300
P/N 1020676
BOM
S/N
VOLTAGE 12-24VDC
J1 J2 J3 J4 J5 J6 J7
J8 J9 J10 J11
3
1
J12
4
6
J13
HARNESS, WIRING
ENGINE ROOM SWITCH
OIL
FILTER
OIL
PRESSURE
TRANS
(J12-1) RED/GRN STRIPE
(J12-2) GRN/RED STRIPE
(J12-3) YEL/PUR STRIPE
(J12-4) PUR/YEL STRIPE
Figure
50. Transmission Switch Harness Wiring Diagram
13
4
EC300 Marine Control System Installation Manual #1024168
Twin Disc, Incorporated
Electrical Installation
Transmission Oil Filter Differential Pressure Switch Wiring Installation
Install the wiring connections for a Transmission Oil Filter Differential Pressure
Switch as follows (See Figure 49):
Note: The Transmission Oil Filter Differential Pressure Switch
Cable is part of the Engine Room Switch harness. Cable ties may be removed for routing purposes.
Refer to General Electrical Installation Guidelines before proceeding with this
section.
1.
Align the harness connector with the J12 receptacle of the EC300
Control and push it in until it snaps into place.
2.
4.
Route the Engine Room Switch Harness to the Transmission Oil Filter
Differential Pressure Switch area.
Terminate the red with green stripe “OIL FILTER” J12 pin 1 wire to either screw terminal for the Transmission Oil Filter Differential Pressure Switch.
5.
6.
Terminate the green with red stripe “OIL FILTER” J12 pin 2 wire to the other screw terminal for the Transmission Oil Filter Differential Pressure
Switch.
Note: Refer to Figure 50 for detailed information about the conductors. Refer to the transmission manufacturer’s technical manual for any recommendations for terminating the wires. Refer to Wire Connections for other requirements.
Secure all harnesses to a supporting structure with clamps or cable ties at 406 mm (16 in.) intervals.
Note: It may be desirable to complete any other terminations for this harness before securing the harness.
EC300 Marine Control System Installation Manual #1024168
13
5
Electrical Installation
Twin Disc, Incorporated
Transmission Oil Pressure Switch Wiring Installation
Install the wiring connections for a Transmission Oil Pressure Switch as follows
(See Figure 49):
Note: The Transmission Oil Pressure Switch cable is part of the
Engine Room Switch harness. Cable ties may be removed for routing purposes.
Refer to General Electrical Installation Guidelines before proceeding with this section.
1.
If not already completed, align the harness connector with the J12 receptacle of the EC300 Control and push it in until it snaps into place.
2.
4.
If not already completed, route the Engine Room Switch Harness to the
Transmission Oil Pressure Switch area.
Terminate the light blue with brown stripe “OIL PRESSURE SWITCH”
J12 pin 3 wire to either screw terminal on the Transmission Oil Pressure
Switch.
5.
6.
Terminate the brown with light blue stripe “OIL PRESSURE SWITCH”
J12 pin 4 wire to the other screw terminal on the Transmission Oil
Pressure Switch.
Secure all harnesses to a supporting structure with clamps or cable ties at 406 mm (16 in.) intervals.
Note: It may be desirable to complete any other terminations for this harness before securing the harness.
13
6
EC300 Marine Control System Installation Manual #1024168
Twin Disc, Incorporated
Electrical Installation
EC300 Control Power and Grounding Harness (J13) Installation
The Control Power and Grounding Harness (J13) provides operating power for the EC300 Controller. This harness is field fabricated and plugs into the J13 connector at the EC300 Controller via the 6-pin Deutsch connector. The EC300
J13 connector is supplied by Twin Disc Incorporated and the wiring harness and equipment end connectors are supplied by the customer. The J13 connector kit (6-pin Deutsch connector) contains all contacts and sealing plugs that are required to fill the connector contact positions. Sealing plugs must be installed into all unused connector contact positions in order to maintain the integrity of the connector.
This section contains the following sub-sections:
EC300 Control Power Wiring
EC300 Control Bonding Installation
EC300 Marine Control System Installation Manual #1024168
137
Electrical Installation
Twin Disc, Incorporated
138
EC300 Control Power Wiring
Note: Using switched power to the EC300 Control is not
recommended. However, if standards or agencies require that all electronic circuits have on-off control, then use the same switched power that also feeds the engine controller.
CAUTION
Controller power or grounding connections can not be made at any conductor through which motor starting current flows. Do not use a connection directly on the engine or starter. Locate the connection as close to the battery as practical.
CAUTION
Use the same source of power for the EC300 Control as used for the electronically controlled engine, if applicable. Ensure that the circuit current rating is adequate for combined load of the EC300 Control and the engine controller.
CAUTION
Obtain power either from primary distribution for the engine or directly from the batteries. Primary distribution is the first location to which the heavy-duty battery wires connect. Do not connect downstream of any secondary circuit breaker or fuse.
Power Wiring Requirements
The following criteria must be met when installing power distribution wiring for
US installations:
Low voltage conductors must comply with SAE standards J1127 Battery
Cable or J1128 Low Tension Primary Cable. The insulation temperature rating must meet the requirements of SAE J378 Marine Engine Wiring or UL 1426 Cables for Boats.
Electric cables must be constructed of stranded copper conductors, thermoplastic, elastomeric or other insulation, moisture-resistant jackets, and, where applicable, armor and outer-sheathing are to be in accordance with IEC Publication 60092-353, IEEE 1580-2001 or other marine standards acceptable to the American Bureau of Shipping (ABS).
All electrical cables for power circuits are to have insulation suitable for a conductor temperature of not less than 60°C (140°F).
EC300 Marine Control System Installation Manual #1024168
Twin Disc, Incorporated
Electrical Installation
Battery positive and negative power wires must be 14 American Wire
Gauge (AWG) minimum (15 amps max.).
Approved fuses or manual-reset trip-free circuit breakers must be used for the EC300 Control System power distribution wiring as per the applicable codes or standards. The fuse or circuit breaker rating must be 15 amps.
Note: A fuse or circuit breaker is required at the battery or power
distribution point for cable protection. The EC300 Control is internally protected.
A 15A fuse and fuse holder are supplied in the Power Connector Kit
(J13).
All fuses must meet the general provisions of Article 240 of the National
Electrical Code or IEC 92-202, as appropriate, and have an interrupting rating sufficient to interrupt the maximum asymmetrical RMS short-circuit current at the point of application. Each fuse must provide for ready access to test the condition of the fuse.
Unless otherwise permitted, the fuse or circuit breaker must be located within 178 mm (7 in.) of the point at which the power conductor is connected.
Note: If the wire is continually sheathed or enclosed and if
connected directly to a battery terminal, the distance may be up to 1,829 mm (72 in.).
Power distribution wiring must be insulated. Caps or boots are required at all terminals in order to prevent accidental shorts.
Special requirements apply to vessels with gasoline, liquid petroleum gas (LPG), or Marine Compressed Natural Gas (CNG) engines or to vessels with hazardous areas. Power routing and wiring must meet all applicable codes and standards. Circuit components may have to be rated as Ignition Protected as per SAE J1171 External Ignition Protection of Marine Electrical Devices, UL 1500 Ignition Protection Test to Marine
Products, and the electrical system requirements for boats in Title 33
CFR 183.410(a).
The main power wires to the power/interface connector (battery + and battery -) must be routed directly to the battery or a primary distribution panel within 1 m (3.3 ft) of the battery, but not the starter feed.
EC300 Marine Control System Installation Manual #1024168
139
Electrical Installation
Twin Disc, Incorporated
Do not connect the EC300 Control’s battery + or - power input directly to the engine or any of its electrical components.
Connect the EC300 control power wires to the battery for the engine controlled by the EC300 Control. Port engine controls should be connected to the “port” battery. Starboard engine controls should be connected to the “starboard” battery.
Use a good quality connector to connect the power wires to the battery or bus bar and check the wires to be sure they are secure. Do not use simple spring-loaded connectors.
DC Distribution must be a two-wire system. Battery return wiring must be routed to the battery and not to the bonding system or the metallic hull. The negative side of the battery must be connected to ground if the system is to be grounded.
The electrical load added by the EC300 Control System is not large.
Current is limited to 15 amps at either 12 or 24 VDC. However, in some circumstances, this may require an increase in the capacity of the power distribution system, larger batteries, and/or larger grounding conductors.
The customer is responsible for meeting the applicable code and standard requirements.
140 EC300 Marine Control System Installation Manual #1024168
Twin Disc, Incorporated
Electrical Installation
Install the control power wiring as follows (See Figure 51 and Figure 52):
The EC300 Control operates on voltages between 10 and 28 VDC. DC to DC converters must be used for other system voltages. Power wiring must be a twisted pair of 14 AWG stranded copper wire.
Note: Figure 51 and Figure 52 show auxiliary batteries as is
required by certain codes and standards. If redundant (port and starboard) batteries are present, then use the port battery for the port controller’s main battery connection on J13 pin 1. Use the starboard battery for the auxiliary connections on J13 pin 2. Reverse the connector assignments for the starboard EC300 Control.
Note: Figure 51 and Figure 52 both show two single batteries.
This is typical for 12 VDC systems using 12 VDC batteries. The 24 VDC system typically connects two 12
VDC batteries in series to obtain 24 VDC. 6 VDC batteries can also be connected in series to achieve either 12 VDC or 24 VDC. Batteries can also be connected in parallel in order to increase the available battery current. Using a multimeter, test the voltage of each battery and across all batteries if multiple batteries are used so as not to exceed the voltage limits for the EC300 Control.
EC300 Marine Control System Installation Manual #1024168
141
Electrical Installation
Twin Disc, Incorporated
PORT CONTROL
TWIN DISC
INCORPORATED
MODEL EC300
P/N 1020676
BOM
S/N
VOLTAGE 12-24VDC
J1 J2 J3 J4 J5 J6 J7
15 AMP
J8 J9 J12
3
1
J13
4
6
J10 J11
CONNECTOR KIT
INSERT SEALING PLUG IN
CONTACT POSITIONS 4-6
J13-3
J13-1
HARNESS, WIRING
POWER
CUSTOMER SUPPLIED
POWER COMMON (14 AWG)
PRIMARY POWER INPUT (14 AWG)
-
PORT
BATTERY
+
NEGATIVE CONTROL LEADS
MUST BE CONNECTED TO
SAME SINGLE POINT
FROM STARBOARD
EC300 CONTROL
(IF USED)
-
STBD
BATTERY
+
HOOKING UP PORT CONTROL
TO STARBOARD BATTERY
IS OPTIONAL
TO STARBOARD
EC300 CONTROL
(IF USED)
15 AMP
FUSE AND HOLDER ARE SUPPLIED
WITH CONNECTOR KIT
INSTALL AS CLOSE TO BATTERY AS POSSIBLE
J13-2
AUXILIARY POWER INPUT (14 AWG)
Figure 51. Power Wiring Diagram for Unswitched Engine Powering
Applications
142 EC300 Marine Control System Installation Manual #1024168
Twin Disc, Incorporated
Electrical Installation
PORT CONTROL
TWIN DISC
INCORPORATED
MODEL EC300
P/N 1020676
BOM
S/N
VOLTAGE 12-24VDC
J1 J2 J3 J4 J5 J6 J7
NEGATIVE CONTROL LEADS
MUST BE CONNECTED TO
SAME SINGLE POINT
-
PORT
BATTERY
+
J10 J11 J12
3
1
J13
4
6
J8 J9
CONNECTOR KIT
INSERT SEALING PLUG IN
CONTACT POSITIONS 4-6
SWITCH
15 AMP
J13-3
J13-1
HARNESS, WIRING
POWER
CUSTOMER SUPPLIED
POWER COMMON (14 AWG)
PRIMARY POWER INPUT (14 AWG)
FUSE AND HOLDER ARE SUPPLIED
WITH CONNECTOR KIT
INSTALL AS CLOSE TO BATTERY AS POSSIBLE
SWITCH 15 AMP
J13-2
AUXILIARY POWER INPUT (14 AWG)
FROM STARBOARD
EC300 CONTROL
(IF USED)
-
STBD
BATTERY
+
HOOKING UP PORT CONTROL
TO STARBOARD BATTERY
IS OPTIONAL
TO STARBOARD
EC300 CONTROL
(IF USED)
Figure 52. Power Wiring Diagram for Switched Engine Powering
Applications
EC300 Marine Control System Installation Manual #1024168
143
Electrical Installation
Twin Disc, Incorporated
144
Figure 53. Redundant Power Distribution
Note: Some applicable codes and standards (notably RMRS)
require completely redundant wiring between the EC300 controller and the auxiliary power supply. Figure 53 shows the connections for redundant power distribution.
EC300 Marine Control System Installation Manual #1024168
Twin Disc, Incorporated
Electrical Installation
2.
3.
Refer to General Electrical Installation Guidelines before proceeding with this section.
1.
Install two fuses or circuit breakers at the battery positive or engine controller power distribution connections.
Route power wiring to the fuses or circuit breakers.
Temporarily remove the fuses or open the circuit breakers.
Note: Power wiring must be a twisted pair of 14 AWG stranded
copper wire.
CAUTION
Ensure that the EC300 Control power wiring is electrically identical to that used for any associated engine controller.
4.
5.
Connect the first red wire going to EC300 Control Connector J13 Pin 1 to the load side of Main Battery fuse or circuit breaker.
Note: If no auxiliary battery is present, do not install a wire to
J13 Pin 2. Pin 2 should be plugged.
Connect the second red wire going to EC300 Control Connector J13
Pin 2 to the load side of the Auxiliary Battery fuse or circuit breaker.
CAUTION
The two batteries and the EC300 Controller’s negative power connection must be made at the same point.
6.
7.
8.
Connect the yellow (preferred) or black wire going to EC300 Control
Connector J13 Pin 3 to the DC Grounding Bus or the DC Negative Bus as is applicable.
Route the EC300 Control Power and Grounding Harness (J13) to the associated EC300 Control.
Note: The Deutsch contacts (14 AWG) (P/N 0462-209-16141)
have a green band.
Using the Deutsch crimping tool (P/N HDT 48-00), crimp the wires to the Deutsch contacts (14 AWG) (P/N 0462-209-16141).
EC300 Marine Control System Installation Manual #1024168
145
Electrical Installation
Twin Disc, Incorporated
9.
Assemble the J13 Deutsch Mating Connector (P/N DT06-6S-P012).
See Figure 51 and Figure 52.
10.
Ensure that sealing plugs are installed in all empty connector positions.
11.
Secure all harnesses to a supporting structure with clamps or cable ties at 406 mm (16 in.) intervals.
Note: For vessels complying with American Bureau of Shipping
(ABS) Rules for Building and Classing Steel Vessels 2002 or Rules for Building and Classing Steel Vessels Under
90 Meters (295 Feet) 2001, insulation resistance of power and lighting cables is to be measured. Appliances connected to the circuits may be disconnected for this test. Each power and each lighting circuit is to have an insulation resistance between conductors and between each conductor and earth of not less than 0.4 Megohms for loads less than 25 amps.
12.
Ensure that the power harness conductors for J13 pin 1 through J13 pin
6 are disconnected at both ends.
13.
Using a 500 VDC Megohmmeter or equivalent, measure the resistance between each of the following sets of conductors: z z
J13 pin 1 and Earth or Bonding System
J13 pin 2 and Earth or Bonding System z
J13 pin 3 and Earth or Bonding System
14.
Verify that all measurements are greater than or equal to 0.4 Megohms.
Note: Leave EC300 Control Power and Grounding Harness
(J13) disconnected from the EC300 Control until all wiring has been completed.
146 EC300 Marine Control System Installation Manual #1024168
Twin Disc, Incorporated
Electrical Installation
EC300 Control Bonding Installation
The EC300 Control enclosure connects directly to the surface on which it is mounted. For both conductive and nonconductive vessels, the bonding connection is also made in order to ensure that the metallic enclosure is bonded.
Bonding provides a means of making a controlled path for the removal of electrical noise that could be introduced to the EC300 Control through the wiring by inductive interference from motors or generators or by electromagnetic interference from radar or radios. Applicable codes may prevent bonding connections to the battery negative. Some codes do require that the bonding connection and battery negative are connected at one point only. Other codes require that there be no connection between the bonding system and the battery negative. Install the bonding system as per the applicable code.
CAUTION
The bonding wire used for the EC300 Control must be connected to the same bonding system as used for the engine. Ground the EC300 Control bonding wire to the negative battery terminal only if the engine is grounded to the negative battery terminal.
Bonding Requirements
The EC300 Control must be bonded. If used, the Servo Actuator and accessories must also be bonded.
Note: EC300 Control System components including Controllers,
Servo Actuators, and Accessories that have designated bond points should be mounted on isolating platforms like plywood, starboard, PVC boxes, etc.
Note: Insulated push-pull cable mounting hardware may be
necessary to satisfy bond/isolation requirements, especially if the engine block is not grounded to the battery negative. See Push-Pull Cable Installation Kits for
Nonconductive Vessels.
The following criteria must be met when making bonding connections:
The EC300 Control must be directly bonded to battery negative, bond rails, or hull plates. If the engine is grounded to the battery negative terminal, then the EC300 Control’s bond connection should also be to the battery negative. If the vessel or engine has an independent bonding system, then the control should be bonded to the independent bonding system.
EC300 Marine Control System Installation Manual #1024168
147
Electrical Installation
Twin Disc, Incorporated
Bond wires must be connected to one of the unpainted mounting surfaces of the EC300 Control, the Station Doubler, and the Servo Actuator. Any paint must be removed in order to make the bonding connection. The bond wire must be terminated with a ring lug that fits the fastener used to mount the component.
The bonding conductor must be 14 AWG stranded copper wire with insulation that is colored green with yellow stripe (preferred) or green to comply with ABYC standards.
Install the EC300 Control bonding connection as follows (See Figure 54 and
Figure 55):
1.
If EC300 is used with Twin Disc Transmission and the Transmission
Harness Series, connect green chassis wire from the transmission harness to one of the unpainted mounting feet of the EC300.
J5
J8
1022894
J6
J7
J12
148
CHASSIS
Figure 54. Master Control Harness (J5, J6, J7, J8, J12, and Chassis
Wire) Diagram
EC300 Marine Control System Installation Manual #1024168
Twin Disc, Incorporated
Electrical Installation
2.
If the EC300 is not wired with transmission harness series, route a bond wire, connected to the vessel bonding system, to one of the unpainted mounting feet of each of the EC300 controls.
Note: If no vessel bonding system is present, the EC300 must be grounded to the engine block.
BONDING SYSTEM
BOND WIRE
WITH RING LUG
MOUNTING FOOT
3 PLACES
TWIN DISC
INCORPORATED
MODEL EC300
P/N 1020676
BOM
S/N
VOLTAGE 12-24VDC
J1 J2 J3 J4 J5 J6 J7
J8 J9 J10 J11 J12 J13
Figure 55. EC300 Control Bond Connection Diagram
3.
Install a ring lug on the control end of the wire.
Note: The ring lug must be properly sized for both the wire and
the mounting fastener.
EC300 Marine Control System Installation Manual #1024168
149
Electrical Installation
Twin Disc, Incorporated
4.
5.
6.
7.
Remove the mounting fastener at the bonding connection.
Remove any paint at the mounting connection in order to ensure electrical contact.
Insert the bonding wire’s ring lug on the EC300 Control.
Reinstall and tighten fasteners up to 1.13 Nm (10 lb-in.) maximum.
150 EC300 Marine Control System Installation Manual #1024168
Twin Disc, Incorporated
Engineering Drawings
Engineering Drawings
List of Engineering Drawings
The following pages include the generic engineering drawings that are applicable to the EC300 Control System. These generic drawings are listed below. Application specific drawings may also be applicable and are supplied separately.
Note: Any part numbers listed in the following engineering
drawings are for reference only. Please refer to your bill of materials for part numbers specific to your application.
Morse 33 Series Cable Mounting
Servo Actuator Mounting Dimensions
Twin Disc Display Mounting Dimensions
Control Head Mounting Template
Side Mount Lever Mounting Template
EC300 Marine Control System Installation Manual #10
24168
1
51
Engineering Drawings
Twin Disc, Incorporated
EC300 Control Mounting Dimensions
EC300 Control Mounting Dimensions
System 1 - SingleEngine, 1 Station
System 2 - Twin Engine, 2 Stations
System 2 - Twin Engine, 2 Stations
System 3 - Twin Engine, 1 Station with
System 3 - Twin Engine, 1 Station with
System Control - EC300 with MAN Engine,
System Control - EC300 with MAN Engine,
1
52
EC300 Marine Control System Installation Manual #102
4168
Twin Disc, Incorporated
Morse 33 Series Cable Mounting Dimensions
69.9
(2.75)
Engineering Drawings
184.1
(7.25)
FABRICATE BRACKET LEVER
TO PROVIDE DIMENSIONS SHOWN
25.4
(1.00)
CABLE CLAMP
SHIM
EC300 Marine Control System Installation Manual #1024168
153
Engineering Drawings
Servo Actuator Mounting Dimensions
Twin Disc, Incorporated
154 EC300 Marine Control System Installation Manual #1024168
Twin Disc, Incorporated
Twin Disc Display Mounting Dimensions (1018791)
Engineering Drawings
EC300 Marine Control System Installation Manual #1024168
155
Engineering Drawings
Control Head Mounting Template
Twin Disc, Incorporated
156 EC300 Marine Control System Installation Manual #1024168
Twin Disc, Incorporated
Side Mount Lever Mounting Template
Engineering Drawings
EC300 Marine Control System Installation Manual #1024168
157
Engineering Drawings
Side Mount Selector Assembly Mounting Template
Twin Disc, Incorporated
158 EC300 Marine Control System Installation Manual #1024168
Appendix - A
Twin Disc, Incorporated
Appendix - A
Environmental Specifications
Table 13. Environmental Specifications
Parameter
Supply Voltage
Operating Temperature
Storage Temperature
Vibration
Minimum Value
10.5 Volts
-18º C (0º F)
-40º C (-40º F)
Maximum Value
30.0 Volts
70º C (158º F)
80º C (176º F)
7.5g (20-20,000 Hz)
The EC300 meets or exceeds ABS requirements and ABYC recommendations for electrical transients, electromagnetic compatibility, chemical resistance, flame resistance, corrosion resistance, submersion in liquids, dust tolerance and electrostatic discharge.
EC300 Marine Control System Installation Manual #1024168
A-1
Appendix - A
Twin Disc, Incorporated
A-2 EC300 Marine Control System Installation Manual #1024168
Twin Disc, Incorporated
Appendix - B
Appendix - B
Engine Connection Requirements
Caterpillar Engine Connection Requirements
This throttle signal configuration is known as a PWM or Duty Cycle. The EC300 sets the throttle signal duty cycle to approximately 9% at idle and 92% at full throttle. Generally, the EC300 is connected to the engine control at the connections designated for the “Primary Throttle Position Sensor” or “TPS”.
Depending on the model and harnessing provided, the EC300 Engine Harness
(J5) will either be connected to the “Primary Throttle Position Sensor” connector, or directly to the Customer Connector. See Table 14 and Table 15. Refer to the engine manufacturer’s literature to resolve any discrepancies.
Table 14. Engine Connections at Caterpillar’s TPS Connector
EC300 Engine
Harness J5
J5 Pin 1
EC300 Signal
Decsription
TPS Connector
ECM Power Supply A (note 1)
Engine Signal Description
Switched Positive (ECM Power)
J5 Pin 2 Throttle Signal C Primary Throttle Position Signal
J5 Pin 3 ECM Power Supply
Common
B (note 1) Negative Battery (ECM Power)
1) The battery positive connection to J5-1 should be switched and from ECM wiring.
2) The battery negative connection to J5-3 should be from ECM wiring - not battery bus.
Table 15. Engine Connections at Caterpillar’s Customer Connector
EC300 Engine
Harness J5
J5 Pin 1
EC300 Signal
Decsription
Customer
Connector
ECM Power Supply Pin 30
J5 Pin 2
J5 Pin 3
Throttle Signal
ECM Power Supply
Common
Pin 10
Pin 2
Engine Signal Description
Battery Positiove (switched)
Primary Throttle
Battery Negative
EC300 Marine Control System Installation Manual #1024168 B-1
Appendix - B
Twin Disc, Incorporated
Cummins Engine Connection Requirements
Vary with Type (Series) of Engine
Cummins Centry Engine Connection Requirements
The EC300 supports the Cummins Centry Type 8 engine controller. This controller is used on QSK, QSM-11, 485, 480C, and KTA type engines. The
KTA engine is configured for a current loop interface. All other types are voltage interfaces. The EC300 supplies approximately 1.1 volts at idle and 3.95 volts at full throttle when configured as a Cummins voltage output and 5.5 ma at idle and 19.8 ma at full throttle when configured as a Cummins current loop output.
All Cummins installations require pin one of J5 on the EC300 controller to be connected to J8, pin 2. A three pin GM Packard Weather Pack connector
(12010717) mates with the Cummins OEM throttle connector.
Table 16. Engine Connections at Cummins 50 pin Connector
EC300 Engine
Harness J5
J5 Pin 1
EC300 Signal
Decsription
Customer OEM
Connector
ECM Power Supply J8, Pin 2
J5 Pin 2
J5 Pin 3
Throttle Signal
ECM Power Supply
Common
Pin B
Pin A
Engine Signal Description
Throttle Position (Throttle)
V Throttle Return (GND)
B-2 EC300 Marine Control System Installation Manual #1024168
Twin Disc, Incorporated
Appendix - B
Cummins Quantum Voltage Type Engine Connection Requirements
This throttle signal configuration is a DC voltage. The EC300 throttle signal is set to approximately 0.1.1 VDC at idle and 3.95 VDC at full throttle. This configuration is typically used with Cummins QSM-11, 485C and QSK models with Quantum series engine controls. Generally, the EC300 is connected to the engine control at the connections designated for the throttle or throttle pot.
Depending on the model and harnessing, the EC300 wiring will connect to the
“Throttle” or the “OEM” connector. See Table17 and Table 18. Refer to the engine manufacturer’s literature to resolve any discrepancies.
Table 17. Engine Connections at the Cummins Throttle Harness Stub
EC300 Engine
Harness J5
J5 Pin 1
EC300 Signal
Decsription
Customer OEM
Connector
ECM Power Supply J8, Pin 2
J5 Pin 2 Throttle Signal DD Pin B
Engine Signal Description
Throttle Position (Throttle)
J5 Pin 3 ECM Power Supply
Common
DD Pin A
Note: Not all QSK Throttle Pot Connectors are "DD".
V Throttle Return (GND)
Table 18. Engine Connections at the Cummins Quantum QSM-11 Engine with Voltage Control
EC300 Engine
Harness J5
J5 Pin 1
EC300 Signal
Decsription
OEM Connector
QSM-11
ECM Power Supply DD Pin C
Engine Signal Description
V Throttle (VTP)
J5 Pin 2
J5 Pin 3
Throttle Signal
ECM Power Supply
Common
DD Pin B
DD Pin A
Throttle Position (Throttle)
V Throttle Return (GND)
EC300 Marine Control System Installation Manual #1024168 B-3
Appendix - B
Twin Disc, Incorporated
Detroit Diesel Frequency Engine Connection Requirements
for Frequency Control
Table 19. Engine Connections at the Detroit Diesel Engine
EC300 Engine
Harness J5
J5 Pin 1
EC300 Signal
Decsription
Engine Connector
ECM Power Supply J8, Pin 2
J5 Pin 2
J5 Pin 3
Engine Signal Description
Throttle Signal
ECM Power Supply
Common
MIM Plug
DRC 16-24S Pin 14
MIM Plug
DRC 16-24S Pin 15
Series 60 Wiper
Series 60 RTN
Detroit Diesel Voltage Engine Connection Requirements
for Voltage Control
Table 20. Engine Connections at the Detroit Diesel Engine
EC300 Engine
Harness J5
J5 Pin 1
EC300 Signal
Decsription
Engine Connector
ECM Power Supply J8, Pin 2
J5 Pin 2
J5 Pin 3
Engine Signal Description
Throttle Signal
ECM Power Supply
Common
MIM Plug
DRC 16-24S Pin 14
MIM Plug
DRC 16-24S Pin 15
Series 60 Wiper
Series 60 RTN
B-4 EC300 Marine Control System Installation Manual #1024168
Twin Disc, Incorporated
Appendix - B
Deutz Type 1 Engine Connection Requirements
for Voltage Control
Table 21. Engine Connections at the Deutz Type 1 Engine
EC300 Engine
Harness J5
J5 Pin 1
EC300 Signal
Decsription
Engine Connector
ECM Power Supply J8, Pin 2
J5 Pin 2 Throttle Signal B8
J5 Pin 3 ECM Power Supply
Common
A7
1) Remove wiring from signal input range transformer.
Engine Signal Description
DSC 1005 60V
X4 Pin 81 (note 1) Signal
X4 Pin 82 (note 1) Ground
Deutz Type 2 Engine Connection Requirements
for 4-20mA Loop Control
Table 22. Engine Connections at the Deutz Type 2 Engine
EC300 Engine
Harness J5
J5 Pin 1
EC300 Signal
Decsription
Engine Connector
Engine Signal Description
W/RSC 671
ECM Power Supply Terminal F of Gov From 5550/5570 Governor via Diode
J5 Pin 2 Throttle Signal Terminal 4 of Speed
Control
From 671 Speed Control
J5 Pin 3 ECM Power Supply
Common
Terminal 5 of Speed
Control
From 671 Module Speed Control
Note: Verify that terminal F of the speed control is switched power (battery +) that will be turned off when the boat is not in use.
EC300 Marine Control System Installation Manual #1024168 B-5
Appendix - B
Twin Disc, Incorporated
Iveco PWM Engine Connection Requirements
for Pulse Width Modulation Control
Table 23. Engine Connections at the Iveco Engine
EC300 Engine
Harness J5
J5 Pin 1
EC300 Signal
Decsription
Engine Connector
ECM Power Supply A (note 1)
Engine Signal Description
Switched Positive (ECM Power)
J5 Pin 2 Throttle Signal C Primary Throttle Position Signal
J5 Pin 3 ECM Power Supply
Common
B (note 1) Negative Battery (ECM Power)
1) The battery positive connection to J5-1 should be switched and from ECM wiring.
2) The battery negative connection to J5-3 should be from ECM wiring - not battery bus.
Iveco Voltage Engine Connection Requirements
for Voltage Control
Table 24. Engine Connections at the Iveco Engine
EC300 Engine
Harness J5
J5 Pin 1
EC300 Signal
Decsription
Engine Connector
ECM Power Supply J8, Pin 2
Engine Signal Description
J5 Pin 2 Throttle Signal S1 Pin B Throttle Pot Wiper
J5 Pin 3 ECM Power Supply
Common
S1 Pin A Sensor Return
Note: Connections should be made as close to the Engine Control Unit (ECU) as possible.
B-6 EC300 Marine Control System Installation Manual #1024168
Twin Disc, Incorporated
Appendix - B
John Deere Engine Connection Requirements
This throttle signal configuration is a DC voltage. The EC300 throttle signal is set to approximately 0.50 VDC at idle to 4.50 VDC at full throttle. This configuration is similar to the voltage types explained above; however, see the engine manual for complete details on interconnections for throttle input to the engine harness/engine control.
Table 25. Engine Connections at the John Deere Engine
EC300 Engine
Harness J5
J5 Pin 1
EC300 Signal
Decsription
Engine Connector
W/SE4/ECU
ECM Power Supply J8, Pin 2
J5 Pin 2 Throttle Signal S1 Pin B
Engine Signal Description
Throttle Pot Wiper
J5 Pin 3 ECM Power Supply
Common
S1 Pin A Sensor Return
Note: Connections should be made as close to the Engine Control Unit (ECU) as possible.
EC300 Marine Control System Installation Manual #1024168 B-7
Appendix - B
Twin Disc, Incorporated
MAN Current Engine Connection Requirements
for 4-20mA Loop Control
This throttle configuration is a current loop and is set to approximately 3.8 mA at idle and 20.3 mA at full throttle. See the MAN engine manual for complete details on interconnections for throttle input to the engine harness/engine control.
Table 26. Engine Connections at the MAN Engine with Current Control
EC300 Engine
Harness J5
J5 Pin 1
EC300 Signal
Description
Engine Connector
ECM Power Supply J8 Pin 2
Engine Signal Description
Ignition Return
J5 Pin 2
J5 Pin 3
J5 Pin 9
J5 Pin 10
Throttle Signal X9 Pin 9 4-20 MA (+)
Throttle Common X9 Pin 10 and to J8
Pin 6
4-20 MA (-)
Battery (-) from T531
Neutral Start Interlock Neutral Start Relay
Contact (normally open)
Neutral Start Relay
Contact (common)
X9 Pin 7
X9 Pin 8 Neutral Start Interlock
Table 27. Previous Engine Connection Diagram (NOW OBSOLETE)
EC300 Engine
Harness J5
J5 Pin 1
EC300 Signal
Decsription
Engine Connector
(note 1)
ECM Power Supply X9 Pin 7
Engine Signal Description
Battery from T515
J5 Pin 2 Throttle Signal X9 Pin 9 4-20 MA (+)
J5 Pin 3 ECM Power Supply
Common
X9 Pin 10 and Pin 8
4-20 MA (-)
Battery (-) from T531
Note: Wiring may be required inside MAN engine control to get switched battery (+) (terminal 15) to wiring side of connector X9 Pin 7.
Note: The connections shown in table 27 are OBSOLETE and should NOT be used. They are shown only for reference.
MAN has indicated the engine warranty will become void if controller connections use MAN power or common references.
B-8 EC300 Marine Control System Installation Manual #1024168
Twin Disc, Incorporated
Appendix - B
MTU Engine Connection Requirements
for 4-20mA Loop Control
This throttle signal configuration is a current loop and is set to approximately
3.8 mA at idle and 20.3 mA at full throttle. This configuration is similar to the
Cummins current loop explained above; however, see the engine manual for complete details on interconnections for throttle input to the engine harness/ engine control.
Table 28. Engine Connections at the MTU Engine
EC300 Engine
Harness J5
J5 Pin 1
EC300 Signal
Decsription
Engine Connector
Engine Signal Description
ECM Power Supply LOP 1 Terminal 91 + 24 VDC
W/EL55 (MOEL)
J5 Pin 2 Throttle Signal LOP 1 Terminal 83 I in 4-20 MA
J5 Pin 3 ECM Power Supply
Common
LOP 1 Terminal 84 GRND
Note: Connections are for MDEC (ECS 5) version only. Check wiring diagram for engine to verify connection terminal numbers for other controls.
EC300 Marine Control System Installation Manual #1024168 B-9
Appendix - B
Twin Disc, Incorporated
Scania Engine Connection Requirements
This throttle signal configuration is a DC voltage and is set to approximately
0.35 VDC at idle and 3.10 VDC at full throttle. This configuration is similar to the voltage types explained above; however, see the engine manual for complete details on interconnections for throttle input to the engine harness/engine control.
Table 29. Engine Connections at the Scania Engine
EC300 Engine
Harness J5
J5 Pin 1
EC300 Signal
Decsription
Engine Connector
ECM Power Supply J8, Pin 2 TPSE
Engine Signal Description
W/DEC 2
J5 Pin 2 Throttle Signal C36-12 TPSS
J5 Pin 3 ECM Power Supply
Common
Switched Power
C36-11
C36-9
TPSR Ye
+24V Remote Throttle Validation
Note: The +24V signal to C36-9 must be provide to prevent "set" Throttle Limp Home mode.
B-10 EC300 Marine Control System Installation Manual #1024168
Twin Disc, Incorporated
Appendix - B
Transmission State Signals
The EC300 provides complimentary transmission state signal outputs. These are optically isolated outputs capable of sinking or sourcing 50 mA of current, depending on the wiring configuration. The transmission in neutral output allows current to flow when the EC300 is commanding the transmission to neutral; the transmission in gear output is off in this state. Likewise, the transmission in gear output allows current to flow when the EC300 has engaged either the forward or reverse clutch; the transmission in neutral output is off in this state.
The options below depict the various wiring options for these outputs.
Refer to you enginie throttle interface specifications to see if these functions are compatable with your engine. These functions are set up by an Authorized
Twin Disc Distributor or at the factory.
OPTION 1
EC300
J5-4
+V
OPTION 2
EC300
J5-5
+V
J5-6
TO DRIVE DEVICE J5-6 TO DRIVE DEVICE
TRANSMISSION IN NEUTRAL,
SOURCING OUTPUT
TRANSMISSION IN GEAR,
SOURCING OUTPUT
OPTION 3
EC300
J5-4
J5-6
TO DRIVE DEVICE
COMMON
OPTION 4
EC300
J5-5
J5-6
TRANSMISSION IN NEUTRAL,
SINKING OUTPUT
TRANSMISSION IN GEAR,
SINKING OUTPUT
Figure 91. Transmission State Signal Output Diagram
TO DRIVE DEVICE
COMMON
EC300 Marine Control System Installation Manual #1024168 B-11
Appendix - B
Twin Disc, Incorporated
B-12 EC300 Marine Control System Installation Manual #1024168
#102
4168 R2 4/08
TWIN DISC, INCORPORATED RACINE, WISCONSIN 53403, U.S.A. 262-638-4000/262-638-4482 (FAX) WWW.TWINDISC.COM
advertisement
* Your assessment is very important for improving the workof artificial intelligence, which forms the content of this project
Related manuals
advertisement
Table of contents
- 13 Introduction
- 13 Preface
- 15 General Information
- 16 Replacement Parts
- 17 Safety
- 17 Source of Service Information
- 18 Required Tools
- 19 Basic System Components
- 23 Additional Materials
- 25 Component Installation
- 25 General Component Installation Guidelines
- 27 EC300 Control Installation
- 28 Control Head Installation
- 29 Single/Dual Lever Control Head Assembly
- 35 Control Head Lever Drag Adjustment
- 36 Twin Disc Display Installation
- 38 Speed Sensor Installation
- 40 Installation - Magnetic Pick-Up Engine Speed Sensor
- 42 Installation - Hall Effect Pick-Up Output Speed Sensor
- 43 Installation - Tachometer Signal Generator
- 44 Station Doubler Installation
- 46 Servo Actuator Installation
- 47 Servo Actuator Mounting
- 48 Push-Pull Cable Installation Guidelines
- 49 Push-Pull Cable Installation Kits for Conductive Vessels
- 50 Push-Pull Cable Installation Kits for Nonconductive Vessels
- 52 Push-Pull Cable Mounting Bracket and Cable Installation
- 55 Throttle
- 57 Push-Pull Cable Final Adjustment
- 59 Electrical Installation
- 59 General Electrical Harness Information
- 60 General Electrical Installation Guidelines
- 66 Control Head Harness (J1, J2, or J3) Installation
- 67 Multi-Station Single Lever Control Head Wiring Installation
- 69 Multi-Station Dual Lever Control Head Wiring Installation
- 71 tions
- 73 Station Doublers
- 78 Service Connector (J4)
- 78 Transmission Harness (J5, J6, J7 J8, and J12) Installation
- 79 Control to Bracket Wiring Installation
- 81 Bracket to Transmission Wiring Installation
- 82 Neutral Start Interlock Wiring Installation
- 85 Engine Throttle Wiring Installation
- 88 Prewired Connection Inspection
- 89 Engine Control Harness (J5) Installation
- 91 Neutral Start Interlock Wiring Installtion
- 95 Electronic Control Module Throttle Wiring
- 99 Engine Speed Sensor Harness Installation
- 101 Engine Room Analog Harness (J6) Installation
- 103 Transmission Oil Temperature Sensor Wiring Installation
- 104 PWM Driver Harness (J7) Installation
- 108 Shaft Brake Wiring Installation
- 109 Stabilizer Disable Wiring Installation
- 110 Troll Enable Wiring Installation
- 111 Bridge Signals Harness (J8) Installation
- 112 Ignition Switch Wiring
- 114 Manual Override Switch Wiring
- 116 Tachometer Output Wiring Installation
- 118 Twin Disc Display Harness (J9) Installation
- 120 Twin Disc Display Harness Wiring
- 122 Communication Harness (J10) Installation
- 123 Dual Engine Communication Harness Installation
- 125 Multiple Engine Communication Harness Installation
- 127 Servo Actuator Harness (J11) Installation
- 129 Servo Actuator Harness Wiring
- 133 Engine Room Switch Harness (J12) Installation
- 135 lation
- 136 Transmission Oil Pressure Switch Wiring Installation
- 138 EC300 Control Power Wiring
- 147 EC300 Control Bonding Installation
- 151 Engineering Drawings
- 151 List of Engineering Drawings
- 153 Morse 33 Series Cable Mounting Dimensions
- 154 Servo Actuator Mounting Dimensions
- 155 Twin Disc Display Mounting Dimensions (1018791)
- 156 Control Head Mounting Template
- 157 Side Mount Lever Mounting Template
- 158 Side Mount Selector Assembly Mounting Template
- 159 EC300 Control Mounting Dimensions
- 160 EC300 Control Pin Assignments
- 161 System 1 - Single Engine, 1 Station
- 162 System 2 - Twin Engine, 2 Stations Sheet 1 - Port Control
- 164 Sheet 1 - Port Control
- 165 Sheet 2 - Starboard Control
- 168 Wiring Diagram Sheet 1 - Port Control
- 169 Wiring Diagram Sheet 2 - Starboard Control