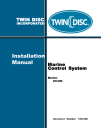
advertisement
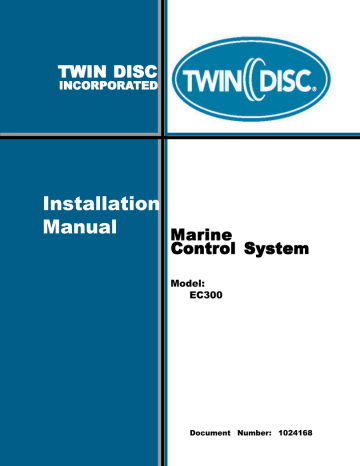
Engineering Drawings
Side Mount Selector Assembly Mounting Template
Twin Disc, Incorporated
158 EC300 Marine Control System Installation Manual #1024168
Appendix - A
Twin Disc, Incorporated
Appendix - A
Environmental Specifications
Table 13. Environmental Specifications
Parameter
Supply Voltage
Operating Temperature
Storage Temperature
Vibration
Minimum Value
10.5 Volts
-18º C (0º F)
-40º C (-40º F)
Maximum Value
30.0 Volts
70º C (158º F)
80º C (176º F)
7.5g (20-20,000 Hz)
The EC300 meets or exceeds ABS requirements and ABYC recommendations for electrical transients, electromagnetic compatibility, chemical resistance, flame resistance, corrosion resistance, submersion in liquids, dust tolerance and electrostatic discharge.
EC300 Marine Control System Installation Manual #1024168
A-1
Appendix - A
Twin Disc, Incorporated
A-2 EC300 Marine Control System Installation Manual #1024168
Twin Disc, Incorporated
Appendix - B
Appendix - B
Engine Connection Requirements
Caterpillar Engine Connection Requirements
This throttle signal configuration is known as a PWM or Duty Cycle. The EC300 sets the throttle signal duty cycle to approximately 9% at idle and 92% at full throttle. Generally, the EC300 is connected to the engine control at the connections designated for the “Primary Throttle Position Sensor” or “TPS”.
Depending on the model and harnessing provided, the EC300 Engine Harness
(J5) will either be connected to the “Primary Throttle Position Sensor” connector, or directly to the Customer Connector. See Table 14 and Table 15. Refer to the engine manufacturer’s literature to resolve any discrepancies.
Table 14. Engine Connections at Caterpillar’s TPS Connector
EC300 Engine
Harness J5
J5 Pin 1
EC300 Signal
Decsription
TPS Connector
ECM Power Supply A (note 1)
Engine Signal Description
Switched Positive (ECM Power)
J5 Pin 2 Throttle Signal C Primary Throttle Position Signal
J5 Pin 3 ECM Power Supply
Common
B (note 1) Negative Battery (ECM Power)
1) The battery positive connection to J5-1 should be switched and from ECM wiring.
2) The battery negative connection to J5-3 should be from ECM wiring - not battery bus.
Table 15. Engine Connections at Caterpillar’s Customer Connector
EC300 Engine
Harness J5
J5 Pin 1
EC300 Signal
Decsription
Customer
Connector
ECM Power Supply Pin 30
J5 Pin 2
J5 Pin 3
Throttle Signal
ECM Power Supply
Common
Pin 10
Pin 2
Engine Signal Description
Battery Positiove (switched)
Primary Throttle
Battery Negative
EC300 Marine Control System Installation Manual #1024168 B-1
Appendix - B
Twin Disc, Incorporated
Cummins Engine Connection Requirements
Vary with Type (Series) of Engine
Cummins Centry Engine Connection Requirements
The EC300 supports the Cummins Centry Type 8 engine controller. This controller is used on QSK, QSM-11, 485, 480C, and KTA type engines. The
KTA engine is configured for a current loop interface. All other types are voltage interfaces. The EC300 supplies approximately 1.1 volts at idle and 3.95 volts at full throttle when configured as a Cummins voltage output and 5.5 ma at idle and 19.8 ma at full throttle when configured as a Cummins current loop output.
All Cummins installations require pin one of J5 on the EC300 controller to be connected to J8, pin 2. A three pin GM Packard Weather Pack connector
(12010717) mates with the Cummins OEM throttle connector.
Table 16. Engine Connections at Cummins 50 pin Connector
EC300 Engine
Harness J5
J5 Pin 1
EC300 Signal
Decsription
Customer OEM
Connector
ECM Power Supply J8, Pin 2
J5 Pin 2
J5 Pin 3
Throttle Signal
ECM Power Supply
Common
Pin B
Pin A
Engine Signal Description
Throttle Position (Throttle)
V Throttle Return (GND)
B-2 EC300 Marine Control System Installation Manual #1024168
Twin Disc, Incorporated
Appendix - B
Cummins Quantum Voltage Type Engine Connection Requirements
This throttle signal configuration is a DC voltage. The EC300 throttle signal is set to approximately 0.1.1 VDC at idle and 3.95 VDC at full throttle. This configuration is typically used with Cummins QSM-11, 485C and QSK models with Quantum series engine controls. Generally, the EC300 is connected to the engine control at the connections designated for the throttle or throttle pot.
Depending on the model and harnessing, the EC300 wiring will connect to the
“Throttle” or the “OEM” connector. See Table17 and Table 18. Refer to the engine manufacturer’s literature to resolve any discrepancies.
Table 17. Engine Connections at the Cummins Throttle Harness Stub
EC300 Engine
Harness J5
J5 Pin 1
EC300 Signal
Decsription
Customer OEM
Connector
ECM Power Supply J8, Pin 2
J5 Pin 2 Throttle Signal DD Pin B
Engine Signal Description
Throttle Position (Throttle)
J5 Pin 3 ECM Power Supply
Common
DD Pin A
Note: Not all QSK Throttle Pot Connectors are "DD".
V Throttle Return (GND)
Table 18. Engine Connections at the Cummins Quantum QSM-11 Engine with Voltage Control
EC300 Engine
Harness J5
J5 Pin 1
EC300 Signal
Decsription
OEM Connector
QSM-11
ECM Power Supply DD Pin C
Engine Signal Description
V Throttle (VTP)
J5 Pin 2
J5 Pin 3
Throttle Signal
ECM Power Supply
Common
DD Pin B
DD Pin A
Throttle Position (Throttle)
V Throttle Return (GND)
EC300 Marine Control System Installation Manual #1024168 B-3
Appendix - B
Twin Disc, Incorporated
Detroit Diesel Frequency Engine Connection Requirements
for Frequency Control
Table 19. Engine Connections at the Detroit Diesel Engine
EC300 Engine
Harness J5
J5 Pin 1
EC300 Signal
Decsription
Engine Connector
ECM Power Supply J8, Pin 2
J5 Pin 2
J5 Pin 3
Engine Signal Description
Throttle Signal
ECM Power Supply
Common
MIM Plug
DRC 16-24S Pin 14
MIM Plug
DRC 16-24S Pin 15
Series 60 Wiper
Series 60 RTN
Detroit Diesel Voltage Engine Connection Requirements
for Voltage Control
Table 20. Engine Connections at the Detroit Diesel Engine
EC300 Engine
Harness J5
J5 Pin 1
EC300 Signal
Decsription
Engine Connector
ECM Power Supply J8, Pin 2
J5 Pin 2
J5 Pin 3
Engine Signal Description
Throttle Signal
ECM Power Supply
Common
MIM Plug
DRC 16-24S Pin 14
MIM Plug
DRC 16-24S Pin 15
Series 60 Wiper
Series 60 RTN
B-4 EC300 Marine Control System Installation Manual #1024168
Twin Disc, Incorporated
Appendix - B
Deutz Type 1 Engine Connection Requirements
for Voltage Control
Table 21. Engine Connections at the Deutz Type 1 Engine
EC300 Engine
Harness J5
J5 Pin 1
EC300 Signal
Decsription
Engine Connector
ECM Power Supply J8, Pin 2
J5 Pin 2 Throttle Signal B8
J5 Pin 3 ECM Power Supply
Common
A7
1) Remove wiring from signal input range transformer.
Engine Signal Description
DSC 1005 60V
X4 Pin 81 (note 1) Signal
X4 Pin 82 (note 1) Ground
Deutz Type 2 Engine Connection Requirements
for 4-20mA Loop Control
Table 22. Engine Connections at the Deutz Type 2 Engine
EC300 Engine
Harness J5
J5 Pin 1
EC300 Signal
Decsription
Engine Connector
Engine Signal Description
W/RSC 671
ECM Power Supply Terminal F of Gov From 5550/5570 Governor via Diode
J5 Pin 2 Throttle Signal Terminal 4 of Speed
Control
From 671 Speed Control
J5 Pin 3 ECM Power Supply
Common
Terminal 5 of Speed
Control
From 671 Module Speed Control
Note: Verify that terminal F of the speed control is switched power (battery +) that will be turned off when the boat is not in use.
EC300 Marine Control System Installation Manual #1024168 B-5
Appendix - B
Twin Disc, Incorporated
Iveco PWM Engine Connection Requirements
for Pulse Width Modulation Control
Table 23. Engine Connections at the Iveco Engine
EC300 Engine
Harness J5
J5 Pin 1
EC300 Signal
Decsription
Engine Connector
ECM Power Supply A (note 1)
Engine Signal Description
Switched Positive (ECM Power)
J5 Pin 2 Throttle Signal C Primary Throttle Position Signal
J5 Pin 3 ECM Power Supply
Common
B (note 1) Negative Battery (ECM Power)
1) The battery positive connection to J5-1 should be switched and from ECM wiring.
2) The battery negative connection to J5-3 should be from ECM wiring - not battery bus.
Iveco Voltage Engine Connection Requirements
for Voltage Control
Table 24. Engine Connections at the Iveco Engine
EC300 Engine
Harness J5
J5 Pin 1
EC300 Signal
Decsription
Engine Connector
ECM Power Supply J8, Pin 2
Engine Signal Description
J5 Pin 2 Throttle Signal S1 Pin B Throttle Pot Wiper
J5 Pin 3 ECM Power Supply
Common
S1 Pin A Sensor Return
Note: Connections should be made as close to the Engine Control Unit (ECU) as possible.
B-6 EC300 Marine Control System Installation Manual #1024168
Twin Disc, Incorporated
Appendix - B
John Deere Engine Connection Requirements
This throttle signal configuration is a DC voltage. The EC300 throttle signal is set to approximately 0.50 VDC at idle to 4.50 VDC at full throttle. This configuration is similar to the voltage types explained above; however, see the engine manual for complete details on interconnections for throttle input to the engine harness/engine control.
Table 25. Engine Connections at the John Deere Engine
EC300 Engine
Harness J5
J5 Pin 1
EC300 Signal
Decsription
Engine Connector
W/SE4/ECU
ECM Power Supply J8, Pin 2
J5 Pin 2 Throttle Signal S1 Pin B
Engine Signal Description
Throttle Pot Wiper
J5 Pin 3 ECM Power Supply
Common
S1 Pin A Sensor Return
Note: Connections should be made as close to the Engine Control Unit (ECU) as possible.
EC300 Marine Control System Installation Manual #1024168 B-7
Appendix - B
Twin Disc, Incorporated
MAN Current Engine Connection Requirements
for 4-20mA Loop Control
This throttle configuration is a current loop and is set to approximately 3.8 mA at idle and 20.3 mA at full throttle. See the MAN engine manual for complete details on interconnections for throttle input to the engine harness/engine control.
Table 26. Engine Connections at the MAN Engine with Current Control
EC300 Engine
Harness J5
J5 Pin 1
EC300 Signal
Description
Engine Connector
ECM Power Supply J8 Pin 2
Engine Signal Description
Ignition Return
J5 Pin 2
J5 Pin 3
J5 Pin 9
J5 Pin 10
Throttle Signal X9 Pin 9 4-20 MA (+)
Throttle Common X9 Pin 10 and to J8
Pin 6
4-20 MA (-)
Battery (-) from T531
Neutral Start Interlock Neutral Start Relay
Contact (normally open)
Neutral Start Relay
Contact (common)
X9 Pin 7
X9 Pin 8 Neutral Start Interlock
Table 27. Previous Engine Connection Diagram (NOW OBSOLETE)
EC300 Engine
Harness J5
J5 Pin 1
EC300 Signal
Decsription
Engine Connector
(note 1)
ECM Power Supply X9 Pin 7
Engine Signal Description
Battery from T515
J5 Pin 2 Throttle Signal X9 Pin 9 4-20 MA (+)
J5 Pin 3 ECM Power Supply
Common
X9 Pin 10 and Pin 8
4-20 MA (-)
Battery (-) from T531
Note: Wiring may be required inside MAN engine control to get switched battery (+) (terminal 15) to wiring side of connector X9 Pin 7.
Note: The connections shown in table 27 are OBSOLETE and should NOT be used. They are shown only for reference.
MAN has indicated the engine warranty will become void if controller connections use MAN power or common references.
B-8 EC300 Marine Control System Installation Manual #1024168
Twin Disc, Incorporated
Appendix - B
MTU Engine Connection Requirements
for 4-20mA Loop Control
This throttle signal configuration is a current loop and is set to approximately
3.8 mA at idle and 20.3 mA at full throttle. This configuration is similar to the
Cummins current loop explained above; however, see the engine manual for complete details on interconnections for throttle input to the engine harness/ engine control.
Table 28. Engine Connections at the MTU Engine
EC300 Engine
Harness J5
J5 Pin 1
EC300 Signal
Decsription
Engine Connector
Engine Signal Description
ECM Power Supply LOP 1 Terminal 91 + 24 VDC
W/EL55 (MOEL)
J5 Pin 2 Throttle Signal LOP 1 Terminal 83 I in 4-20 MA
J5 Pin 3 ECM Power Supply
Common
LOP 1 Terminal 84 GRND
Note: Connections are for MDEC (ECS 5) version only. Check wiring diagram for engine to verify connection terminal numbers for other controls.
EC300 Marine Control System Installation Manual #1024168 B-9
Appendix - B
Twin Disc, Incorporated
Scania Engine Connection Requirements
This throttle signal configuration is a DC voltage and is set to approximately
0.35 VDC at idle and 3.10 VDC at full throttle. This configuration is similar to the voltage types explained above; however, see the engine manual for complete details on interconnections for throttle input to the engine harness/engine control.
Table 29. Engine Connections at the Scania Engine
EC300 Engine
Harness J5
J5 Pin 1
EC300 Signal
Decsription
Engine Connector
ECM Power Supply J8, Pin 2 TPSE
Engine Signal Description
W/DEC 2
J5 Pin 2 Throttle Signal C36-12 TPSS
J5 Pin 3 ECM Power Supply
Common
Switched Power
C36-11
C36-9
TPSR Ye
+24V Remote Throttle Validation
Note: The +24V signal to C36-9 must be provide to prevent "set" Throttle Limp Home mode.
B-10 EC300 Marine Control System Installation Manual #1024168
Twin Disc, Incorporated
Appendix - B
Transmission State Signals
The EC300 provides complimentary transmission state signal outputs. These are optically isolated outputs capable of sinking or sourcing 50 mA of current, depending on the wiring configuration. The transmission in neutral output allows current to flow when the EC300 is commanding the transmission to neutral; the transmission in gear output is off in this state. Likewise, the transmission in gear output allows current to flow when the EC300 has engaged either the forward or reverse clutch; the transmission in neutral output is off in this state.
The options below depict the various wiring options for these outputs.
Refer to you enginie throttle interface specifications to see if these functions are compatable with your engine. These functions are set up by an Authorized
Twin Disc Distributor or at the factory.
OPTION 1
EC300
J5-4
+V
OPTION 2
EC300
J5-5
+V
J5-6
TO DRIVE DEVICE J5-6 TO DRIVE DEVICE
TRANSMISSION IN NEUTRAL,
SOURCING OUTPUT
TRANSMISSION IN GEAR,
SOURCING OUTPUT
OPTION 3
EC300
J5-4
J5-6
TO DRIVE DEVICE
COMMON
OPTION 4
EC300
J5-5
J5-6
TRANSMISSION IN NEUTRAL,
SINKING OUTPUT
TRANSMISSION IN GEAR,
SINKING OUTPUT
Figure 91. Transmission State Signal Output Diagram
TO DRIVE DEVICE
COMMON
EC300 Marine Control System Installation Manual #1024168 B-11
Appendix - B
Twin Disc, Incorporated
B-12 EC300 Marine Control System Installation Manual #1024168
#102
4168 R2 4/08
TWIN DISC, INCORPORATED RACINE, WISCONSIN 53403, U.S.A. 262-638-4000/262-638-4482 (FAX) WWW.TWINDISC.COM
advertisement
Related manuals
advertisement
Table of contents
- 13 Introduction
- 13 Preface
- 15 General Information
- 16 Replacement Parts
- 17 Safety
- 17 Source of Service Information
- 18 Required Tools
- 19 Basic System Components
- 23 Additional Materials
- 25 Component Installation
- 25 General Component Installation Guidelines
- 27 EC300 Control Installation
- 28 Control Head Installation
- 29 Single/Dual Lever Control Head Assembly
- 35 Control Head Lever Drag Adjustment
- 36 Twin Disc Display Installation
- 38 Speed Sensor Installation
- 40 Installation - Magnetic Pick-Up Engine Speed Sensor
- 42 Installation - Hall Effect Pick-Up Output Speed Sensor
- 43 Installation - Tachometer Signal Generator
- 44 Station Doubler Installation
- 46 Servo Actuator Installation
- 47 Servo Actuator Mounting
- 48 Push-Pull Cable Installation Guidelines
- 49 Push-Pull Cable Installation Kits for Conductive Vessels
- 50 Push-Pull Cable Installation Kits for Nonconductive Vessels
- 52 Push-Pull Cable Mounting Bracket and Cable Installation
- 55 Throttle
- 57 Push-Pull Cable Final Adjustment
- 59 Electrical Installation
- 59 General Electrical Harness Information
- 60 General Electrical Installation Guidelines
- 66 Control Head Harness (J1, J2, or J3) Installation
- 67 Multi-Station Single Lever Control Head Wiring Installation
- 69 Multi-Station Dual Lever Control Head Wiring Installation
- 71 tions
- 73 Station Doublers
- 78 Service Connector (J4)
- 78 Transmission Harness (J5, J6, J7 J8, and J12) Installation
- 79 Control to Bracket Wiring Installation
- 81 Bracket to Transmission Wiring Installation
- 82 Neutral Start Interlock Wiring Installation
- 85 Engine Throttle Wiring Installation
- 88 Prewired Connection Inspection
- 89 Engine Control Harness (J5) Installation
- 91 Neutral Start Interlock Wiring Installtion
- 95 Electronic Control Module Throttle Wiring
- 99 Engine Speed Sensor Harness Installation
- 101 Engine Room Analog Harness (J6) Installation
- 103 Transmission Oil Temperature Sensor Wiring Installation
- 104 PWM Driver Harness (J7) Installation
- 108 Shaft Brake Wiring Installation
- 109 Stabilizer Disable Wiring Installation
- 110 Troll Enable Wiring Installation
- 111 Bridge Signals Harness (J8) Installation
- 112 Ignition Switch Wiring
- 114 Manual Override Switch Wiring
- 116 Tachometer Output Wiring Installation
- 118 Twin Disc Display Harness (J9) Installation
- 120 Twin Disc Display Harness Wiring
- 122 Communication Harness (J10) Installation
- 123 Dual Engine Communication Harness Installation
- 125 Multiple Engine Communication Harness Installation
- 127 Servo Actuator Harness (J11) Installation
- 129 Servo Actuator Harness Wiring
- 133 Engine Room Switch Harness (J12) Installation
- 135 lation
- 136 Transmission Oil Pressure Switch Wiring Installation
- 138 EC300 Control Power Wiring
- 147 EC300 Control Bonding Installation
- 151 Engineering Drawings
- 151 List of Engineering Drawings
- 153 Morse 33 Series Cable Mounting Dimensions
- 154 Servo Actuator Mounting Dimensions
- 155 Twin Disc Display Mounting Dimensions (1018791)
- 156 Control Head Mounting Template
- 157 Side Mount Lever Mounting Template
- 158 Side Mount Selector Assembly Mounting Template
- 159 EC300 Control Mounting Dimensions
- 160 EC300 Control Pin Assignments
- 161 System 1 - Single Engine, 1 Station
- 162 System 2 - Twin Engine, 2 Stations Sheet 1 - Port Control
- 164 Sheet 1 - Port Control
- 165 Sheet 2 - Starboard Control
- 168 Wiring Diagram Sheet 1 - Port Control
- 169 Wiring Diagram Sheet 2 - Starboard Control