Draper Roller Maintenance. MacDon D50 & D60
Add to My manuals160 Pages
MacDon D50 & D60 Harvest Headers are designed to serve a dual function in your grain, hay, and specialty crop harvesting operation. Teamed with your self-propelled windrower power unit and optional hay conditioner, the D50 and D60 Harvest Headers will cut and lay crop into uniform fluffy windrows. Windrowing allows starting the harvest earlier, protects the crop from wind damage, and gives you more flexibility in scheduling combine time.
advertisement
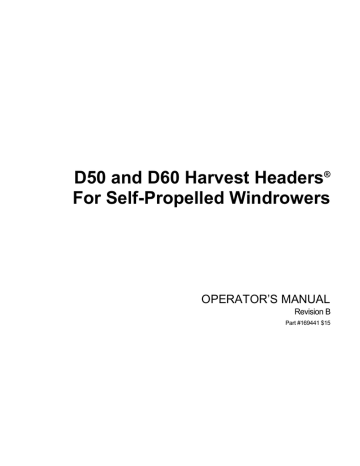
SECTION 8. MAINTENANCE AND SERVICING
The draper rollers have non-greaseable bearings.
The external seal should be checked every 200 hours (or more frequently in sandy conditions), to obtain the maximum bearing life.
DANGER
Engage header lift cylinder stops and reel props before working under header or reel.
a. Raise header and reel, and engage cylinder and reel stops. b. On deck shift headers, position deck so drive roller is easily accessible. c. Loosen and uncouple draper. Refer to Section
8.8.2 Replacing Split Draper.
DANGER
Engage header lift cylinder stops and reel props before working under header or reel.
Refer to illustrations opposite. a. Position roller in deck arms, and secure forward end with bolt (C) and washer. Do not tighten at this time. b. Apply SAE Multi-Purpose grease to motor shaft, locate motor on roller arm, and engage motor shaft into roller. c. Secure motor with bolts (B), and tighten. d. Push roller against shoulder on motor shaft, and hand-tighten the two set screws (A). Torque set screws to 20 ft·lbf (27 N·m). e. Torque bolt (C) to 70 ft·lbf (95 N·m). f. Re-attach draper. Refer to Section 8.8.2
Replacing Split Draper. g. Adjust draper tension. Refer to Section 8.8.1
Draper Tension Adjustment. h. Re-adjust hydraulic motor hoses if required, and tighten hose clamps. i. Run machine, and adjust tracking if required.
Section 8.8.4 Draper Alignment.
A
B d. Loosen the two set screws in access hole (A) in the drive roller hub at motor end. e. Remove the two bolts (B) that hold hydraulic motor to arm, and pull motor off roller.
C f. Remove bolt (C) at forward end of roller, and remove roller from deck.
Form 169441
114
Revision B
8.8.5.3 Idler Roller Removal
DANGER
Engage header lift cylinder stops and reel props before working under header or reel.
a. Raise header and reel, and engage cylinder and reel stops. b. On deck shift headers, position deck so idler roller is easily accessible. c. Loosen and uncouple draper. Refer to Section
8.8.2.1 Draper Removal.
B
SECTION 8. MAINTENANCE AND SERVICING
A
8.8.5.4 Idler Roller Installation
See illustration opposite. a. Position stub shaft in idler roller in forward arm
(B) on deck. b. Push on roller to deflect forward arm slightly so that stub shaft at rear of roller can be slipped into rear arm (C). c. Install bolts (A) with washers, and torque to
70 ft·lbf (93 N·m). d. Re-attach draper. Refer to Section 8.8.2
Replacing Split Draper. e. Adjust draper tension. Refer to Section 8.8.1
Draper Tension Adjustment. f. Run machine and adjust tracking if required.
Section 8.8.4 Draper Alignment.
8.8.5.5 Draper Roller Bearing/Seal
Replacement
NOTE
Seal (D) not included in D50 header.
a. Remove roller assembly. Refer to Section 8.8.5.1
Drive Roller Removal or Section 8.8.5.3 Idler
Roller Removal.
C
F
E
D
A d. Remove bolts (A) and washer at ends of idler roller. e. Spread roller arms (B) and (C), and remove roller. b. Remove bearing assembly (E) and seal (D) from roller tube (F) as follows:
Form 169441
115
1. Attach a slide hammer to threaded shaft.
2. Tap out the bearing assembly. c. Clean inside of roller tube (F). Check tube for wear or damage. Replace if necessary.
(continued next page)
Revision B
SECTION 8. MAINTENANCE AND SERVICING
d. Install bearing and seal as follows:
1. Install bearing assembly (E) into roller by pushing on outer race of bearing. The bearing is fully positioned when the 0.55 inch
(14 mm) dimension is achieved. See illustration below.
E
0.55 - 0.59 in.
(14 - 15 mm)
0.12 - 0.16 in.
(3 - 4 mm)
D
2. Apply grease in front of bearing. Refer to
Section 8.3.4 Recommended Fluids and
Lubricants. e. Install seal (D) as follows:
1. Locate seal at roller opening, and position a flat washer (1.0 inch I.D. X 2.0 in. O.D.) on seal.
2. Using a suitable socket to locate on the washer, tap seal into roller opening until it seats on the bearing assembly. The seal is fully positioned when the 0.12 in. (3 mm) dimension is achieved. See illustration above. f. Re-install roller assembly. Refer to Section 8.8.5
Draper Roller Maintenance.
Form 169441
116
Revision B
advertisement
Key Features
- Cuts and lays crop into uniform fluffy windrows
- Allows starting the harvest earlier
- Protects the crop from wind damage
- Gives you more flexibility in scheduling combine time
- Designed for self-propelled windrowers
- Optional hay conditioner available
Related manuals
Frequently Answers and Questions
What is the purpose of MacDon D50 & D60 Harvest Headers?
What types of crops can be harvested with MacDon D50 & D60 Harvest Headers?
Do MacDon D50 & D60 Harvest Headers work with all self-propelled windrowers?
Can I use a hay conditioner with MacDon D50 & D60 Harvest Headers?
advertisement
Table of contents
- 3 INTRODUCTION
- 4 MODEL AND SERIAL NUMBER
- 8 SAFETY
- 8 SAFETY ALERT SYMBOL
- 8 SIGNAL WORDS
- 8 SAFETY SIGNS
- 8 Safety Sign Installation
- 9 Safety Sign Locations
- 18 GENERAL SAFETY
- 20 DEFINITIONS
- 21 COMPONENT IDENTIFICATION
- 22 SPECIFICATIONS
- 24 OPERATION
- 24 OWNER/OPERATOR RESPONSIBILITIES
- 24 OPERATIONAL SAFETY
- 25 HEADER ATTACHMENT/DETACHMENT
- 25 Attachment
- 26 Detachment
- 28 BREAK-IN PERIOD
- 28 PRE-SEASON CHECK
- 29 DAILY START-UP CHECK
- 29 SHUTDOWN PROCEDURE
- 30 HEADER CONTROLS
- 30 HEADER LIFT CYLINDER LOCK-OUTS
- 31 REEL PROPS
- 32 HEADER SET-UP
- 36 HEADER OPERATING VARIABLES
- 36 Cutting Height
- 38 Header Float
- 39 Header Angle
- 40 Reel Speed
- 41 Ground Speed
- 42 Draper Speed
- 42 Knife Speed
- 45 Reel Height
- 45 Reel Fore-Aft Position
- 50 Reel Tine Pitch
- 52 Crop Dividers and Rods
- 55 DELIVERY OPENING/DECK SHIFT
- 55 Delivery Opening - D
- 57 DOUBLE WINDROWING
- 57 Hydraulic Deck Shift
- 57 Manual Deck Shift
- 59 WINDROW TYPES
- 60 HAYING TIPS
- 60 Curing
- 60 Topsoil Moisture
- 60 Weather And Topography
- 60 Windrow Configuration
- 60 Driving on Windrow
- 60 Raking And Tedding
- 61 Chemical Drying Agents
- 62 DRAPER DEFLECTORS
- 62 Deflector Replacement
- 62 Deflector Rework
- 63 HEADER LEVELLING
- 63 UNPLUGGING CUTTERBAR
- 64 UPPER CROSS AUGER
- 65 TRANSPORTING HEADER
- 65 On The Windrower
- 65 Towing
- 66 Converting from Transport to Field Position
- 71 Converting from Field to Transport Position
- 73 STORAGE
- 74 MAINTENANCE AND SERVICING
- 74 PREPARATION FOR SERVICING
- 74 RECOMMENDED SAFETY PROCEDURES
- 75 MAINTENANCE SPECIFICATIONS
- 75 Recommended Torques
- 77 Roller Chain Installation
- 77 Sealed Bearing Installation
- 78 Recommended Fluids and Lubricants
- 78 Conversion Chart
- 79 ENDSHIELDS
- 79 Hinged
- 81 Non-Hinged
- 82 LUBRICATION
- 82 Greasing Procedure
- 82 Lubrication Points
- 88 Oiling Requirements
- 89 Hoses and Lines
- 90 Hydraulic Schematics
- 94 ELECTRICAL
- 95 SICKLE AND SICKLE DRIVE
- 95 Sickle Sections
- 96 Sickle Removal
- 96 Sickle Head Bearing Replacement
- 97 Sickle Installation
- 97 Spare Sickle (Single Knife Headers)
- 98 Sickle Guards
- 101 Sickle Hold-Downs
- 102 Sickle Drive Belts - Non-Timed Drive
- 103 Sickle Drive Belts - Timed Drive
- 108 Wobble Box
- 111 DRAPERS
- 111 Draper Tension Adjustment
- 112 Replacing Split Draper
- 113 Replacing Endless Draper
- 115 Draper Alignment
- 116 Draper Roller Maintenance
- 119 Deck Height
- 120 REEL AND REEL DRIVE
- 120 Reel Clearance to Cutterbar
- 121 Reel Frown Adjustment
- 122 Reel Centering
- 123 Reel Drive Chain - D
- 128 Reel Drive Sprocket - D
- 130 Reel Drive U-Joint - D
- 131 Reel Drive Motor - D
- 133 Reel Speed Sensor
- 134 Reel Tines
- 136 Tine Tube Bushings
- 140 TRANSPORT SYSTEM
- 140 Wheel Bolt Torque
- 140 Axle Bolts
- 140 Tire Inflation
- 141 MAINTENANCE SCHEDULE
- 141 Break-In Inspections
- 142 Interval Maintenance
- 143 Maintenance Record
- 144 TROUBLESHOOTING
- 144 CROP LOSS AT CUTTERBAR
- 145 CUTTING ACTION AND SICKLE COMPONENTS
- 147 REEL DELIVERY
- 149 HEADER AND DRAPERS
- 150 CUTTING EDIBLE BEANS
- 153 WINDROW FORMATION
- 154 OPTIONS AND ATTACHMENTS
- 154 CUTTERBAR POLY
- 154 ADJUSTABLE SKID SHOES WITH POLY COVER
- 154 STUB GUARD CONVERSION KIT
- 154 STABILIZER WHEELS
- 154 STABILIZER/TRANSPORT WHEELS
- 155 LODGED CROP REEL FINGER KIT
- 155 VERTICAL KNIFE MOUNTS
- 155 UPPER CROSS AUGER KIT
- 155 REEL ENDSHIELD KIT
- 155 DOUBLE DRAPER DRIVE
- 156 DRAPER EXTENSION KIT
- 156 RICE DIVIDER KIT
- 156 KNIFE HEAD SHIELD
- 156 SWATH FORMING RODS
- 156 HYDRAULIC DECK SHIFT
- 156 DOUBLE WINDROW ATTACHMENT
- 157 HAY CONDITIONER
- 157 ROCK RETARDER KIT
- 157 HYDRAULIC REEL FORE-AFT POSITIONER
- 158 UNLOADING AND ASSEMBLY